Литье под давлением металла: Литье металлов под давлением
alexxlab | 11.04.2023 | 0 | Разное
Литье под давлением: особенности технологии, область применения
Литье под давлением — это процесс, в рамках которого с помощью автоматизированного оборудования изготавливаются детали с тонкими стенками из цветных металлов, пластмассы и стали. Данная технология отличается высокой производительностью. При создании деталей жидкий расплав, полученный из указанных материалов, с высокой скоростью подается в специальную пресс-форму, после чего под действием давления получается отливка заданной конфигурации.
Особенности технологического процесса
В рамках данного процесса используются специальные стальные пресс-формы, предназначенные для заливки расплавленного материала, который под воздействием высокого давления кристаллизуется, приобретая заданную конфигурацию.
Данное устройство представляет собой литейную оснастку, в конструкции которой предусматриваются подвижные и неподвижные детали. Первые перемещаются по направляющим цилиндрам, вторые крепятся на стационарной плите.
Перед началом технологического процесса подвижная часть пресс-формы плотно фиксируется к неподвижным с помощью гидроцилиндра. Затем, чтобы предотвратить перемещение этих деталей, последние крепятся посредством специальных замков. После заливки и застывания расплавленного материала подвижную часть устройства сдвигают в сторону. Полученная под высоким давлением заготовка удаляется из оборудования с помощью механических толкателей.
Перед началом процесса внутренние детали, которые контактируют с расплавленным материалом, предварительно обрабатываются специальной разделительной смазкой. Данный состав применяется для исключения негативного влияния высоких температур на стальные детали оборудования и беспрепятственного отделения созданных заготовок от стенок.
Литье под давлением ведется в автоматическом режиме с использованием промышленных установок. Основным узлом данного оборудования считается камера, в которой происходит прессование материала. Этот элемент конструкции бывает двух типов: холодный и горячей.
Процесс изготовления деталей в таком оборудовании сводится к следующему: после заполнения установки металлом запускается поршень, который, двигаясь внутри цилиндра, нагнетает расплав в пресс-форму. После заполнения последней внутри камеры увеличивается давление. Это происходит за счет повышения усилия на поршень, что приводит к кристаллизации металла.
Горячая камера пресс-форм представлена в виде ванны, расположенной в чугунном тигле, который в ходе создания заготовок постоянно подогревается. В таких установках также используется поршень, который двигаясь выталкивает расплав из тигля. Далее металл поднимается по специальному каналу с подогреваемым мундштуком (предупреждает затвердевание материала), через который поступает в пресс-форму. По окончании процесса остатки расплава возвращаются в ванну.
Пресс-формы с горячей камерой применяются при создании заготовок из сплавов цинка и магния.
Температура нагрева материала
Температура, до которой нагревается материал, подбирается с учетом двух параметров: марка сплава и геометрических параметров создаваемой детали. Несоблюдение этого правила ведет к серьезным последствиям. Из-за перегрева материала при заливки пресс-формы вылетают брызги, которые перекрывают отверстия для вентиляции, вследствие чего нарушается газоотведение, что ведет к появлению пор в заготовке после затвердевания последней.
Превышение допустимой температуры ведет к увеличению продолжительности кристаллизации металла, из-за чего на завершение технологического процесса уходит больше времени. Это приводит к росту нагрузки на оборудования, что повышает износ пресс-формы. В подобных условиях увеличиваются риски приваривания металла к внутренним стенкам. Вследствие этого растет вероятность повреждения детали при выталкивании.
Данный технологический процесс предполагает выполнение прессовки при минимальной температуре. Цветные металлы можно нагревать на 10-300 градусов выше той отметки, по достижении которой сплав начинает затвердевать. При этом, если техническое задание требует изготовление деталей с тонкой стенкой, температура нагрева увеличивается. При создании отливок простой конфигурации применяется обратный подход. В подобных случаях материал нагревается до температуры, немного превышающей точку плавления.
Если в ходе данного технологического процесса изготавливаются детали высокой прочности, то металл заливают в пресс-форму в твердо-жидком состоянии. Такой подход позволяет добиться следующих результатов:
- исключить появление усадочного эффекта в создаваемой заготовке;
- уменьшить негативное влияние высокой температуры на оборудование;
- сократить продолжительность процесса затвердевания отливки;
- снизить риски приваривания металла к внутренним стенкам.
Металл с включениями твердой фазы прессуется исключительно в установках с холодной камерой. Это объясняется тем, что при изготовлении деталей из данного материала в другом оборудовании повышаются риски застывания расплава в подводящем канале. В частности, в ходе литья под давлением алюминия объем твердых частиц должен составлять 40-60% при условии, если пресс-формы беспрепятственно заполняется, а качество отливки остается на высоком уровне.
Скорость подачи расплавленного материала
Скорость, с которой поршень спрессовывает расплавленный материал, определяется с учетом характеристики сплава и геометрии изготавливаемой детали:
- Деталь простой формы и с толстыми стенками. В этом случае не требуется быстрая прессовка расплава.
- Деталь сложной геометрической формы и с тонкими стенками. При создании подобной заготовки расплав прессуется с высокой скоростью. Такое требование объясняется тем, что жидкий материал должен успеть заполнить все полости до начала затвердевания.
Превышение допустимой скорости прессовки приводит к тому, что подаваемая струя разлетается на мелкие капли, вследствие чего в расплав попадает воздух. В случае если в конструкции предусматривается недостаточное количество каналов, предназначенных для отвода газов, либо те закупорены, в отливаемой заготовке останутся пустоты. Во избежание подобных последствий литье под давлением проводится в вакууме, в который помещается пресс-форма.
То, с какой скоростью проводится прессовка, определяет качество отливок и продолжительность срока службы оборудования. Если расплав подается слишком быстро, то из-за этого смазка, которой обработана ванна, смывается. Из-за этого металл прикипает к внутренним стенкам, что при выталкивании приводит к повреждению заготовки.
При слишком медленной скорости ухудшается качество детали. В этом случае металл начинает затвердевать до того момента, как будет увеличено давление внутри оборудования. Во избежание описанных последствий расплавленный материал подается в пресс-форму со скоростью 10-50 м/с. Меньший параметр выбирается при создании заготовок из стали и медных сплавов. Расплавленные олово и цинк подаются с большей скоростью.
Давление на расплав при затвердевании
После заполнения пресс-формы металлом на поршень многократно увеличивается давление. Материал испытывает такое воздействие до того момента, пока не затвердеет. Благодаря давлению:
- увеличивается плотность заготовки;
- улучшаются механические характеристики отливки;
- исключается образование усадочных дефектов;
- повышается качество отливки;
- снижается риск появления брака;
- растет чистота поверхности металлической детали.
Усилие прессования определяется в зависимости от требований, предъявляемых к прочностным характеристикам детали: чем выше второй параметр, тем больше должно быть давление. Данный показатель также зависит от типа сплавов:
- алюминиевые прессуются под давлением 40-200 МПа;
- на основе магния — 40-180 МПа;
- цинковые — 10-50 МПа.
Чем толще стенка изготавливаемой детали, тем выше должно быть давление при кристаллизации.
Температура нагрева пресс-формы
Перед подачей расплава пресс-форма нагревается до температуры, определяемой в зависимости от типа сплава и толщины стенок:
- цинковые — 120-1600 градусов;
- на основе магния — 200-2400 градусов;
- алюминиевые — 180-2500 градусов;
- на основе стали — 200-2800 градусов;
- латунные — 280-3200 градусов.
При изготовлении деталей с тонкими стенками пресс-форма прогревается до верхней границы указанных диапазонов, с толстыми — до нижней. Это обусловлено тем, что в первом случае такой подход позволяет предупредить затвердевание металла до заполнение формы, во втором — увеличить скорость застывания материала.
К достоинствам литья под давлением относится следующее:
- детали получаются с низкой шероховатостью и высокой точностью исполнения;
- детали не требуют механической обработки после окончания прессовки;
- процесс можно полностью автоматизировать;
- процесс отличается высокой производительностью.
К недостаткам данной технологии относят сложность и высокую стоимость оборудования, необходимого для литья под давлением. Поэтому этот метод изготовления деталей не применяется при мелко- и среднесерийном производстве. Также данную технологию не используют при литье тугоплавких металлов (плавятся при температуре выше, чем сталь). Кроме того, такой метод не подходит для создания крупных отливок из-за неравномерного затвердевания материала.
Область применения
Литье под давлением позволяет создавать тонкостенные изделия толщиной от 1 мм со сложной геометрией из пластика и следующих сплавов:
- медных;
- алюминиевых;
- цинковых;
- на основе магния;
- на основе стали.
В связи с этим литье под давлением нашло применение в приборо-, автомобиле-, самолето- и станкостроении, при производстве бытовой техники и элементов для смесителей. Также данная технология используется при создании продукции из синтетических материалов (полиэтилена, полипропилена и других).
Литье стали под давлением – zavod-litja.ru
Литье стали под давлением это способ производства металлических отливок, при котором они изготовляются в пресс-форме с давлением до 700 МПа. Обычно при таком методе литья используются сплавы, созданные с применением:
- магния,
- алюминия,
- цинка,
- меди,
- и других металлов.
Работа с цветными металлами обусловлена возможностью литья при незначительной температуре жидкого металла. Литьё под давлением даёт возможность изготавливать изделия, применяемые в сантехнике, машиностроении (блоки двигателя и карбюратора) и прочих областях промышленности. Масса изделий, создаваемых таким способом литья, может варьироваться от нескольких грамм до сотни килограмм.
Пришлите ваши чертежи или эскизы на [email protected]
Либо звоните 8-800-250-88-72. Доставка по России и СНГ!!!
Литье стали под давлением
Процесс литья осуществляется на специализированном оборудовании, которое включает в себя линейные машины и камеры прессования. Могут быть и горячими и холодными. Камеры оснащены специальными стержнями, создающими внутренние полости изделий и механизмами выталкивания. При литье учитываются факторы способствующие повышению прочности и точности отливок. С помощью них мы предлагаем все виды литья из черных и цветных металлов от 1кг.
Холодный способ литья
При создании отливок в холодной камере, на первом этапе создания заготовок в литейную машину вручную или автоматически помещается определённое количество сплава. Там он подвергается воздействию пресса и постепенно подаётся по литниковым каналам с помощью поршня в оформляющую полость, которая плотно закрывается.
Остатки жидкого металла не поместившиеся в форму застывают в отдельной камере, и после удаляется за ненадобностью. После того отливка в полости остыла и затвердела, удаляются подвижные стержни, которые создавали внутреннюю полость изделия, и заготовка выталкивается наружу специальными механизмами.
Пришлите ваши чертежи или эскизы на [email protected]
Либо звоните 8-800-250-88-72.
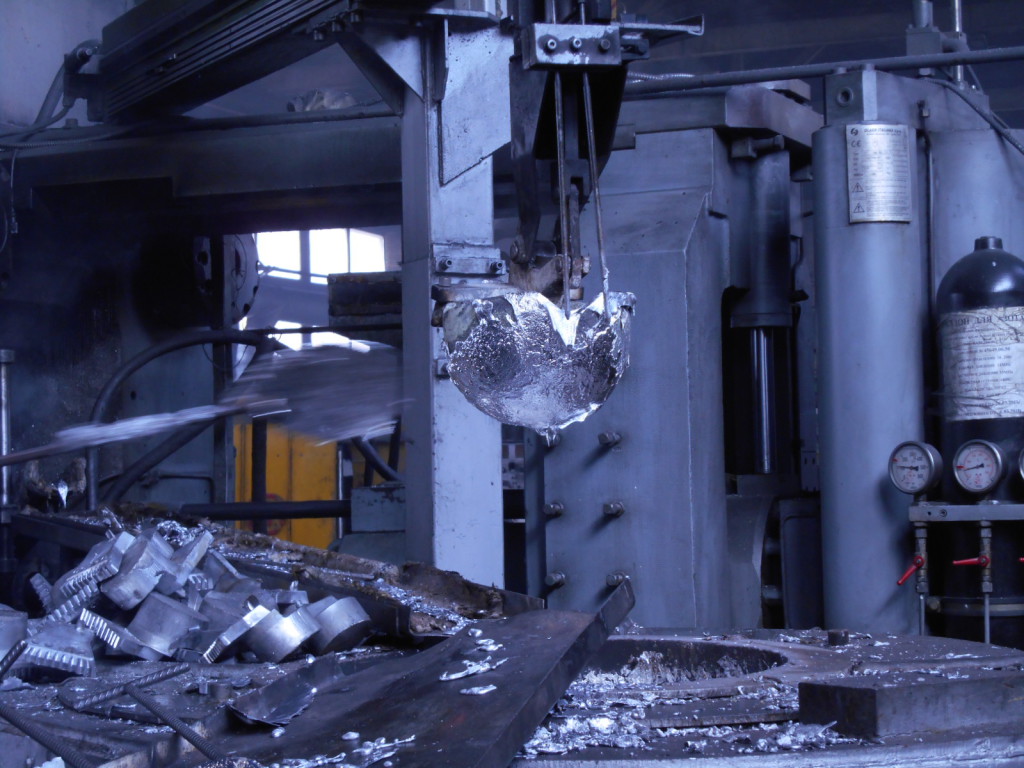
Горячий способ литья
При создании заготовок горячим методом, сплав самотёком поступает из тиля печи в камеру для прессования. Как только камера заполнилась, срабатывает реле, которое выставляется на определённый промежуток времени. За это время поршень давит на неостывший жидкий металл и тот по литниковым трубкам отправляется в формирующую полость станка, где сплав затвердевает и кристаллизируется, так происходит процесс литья стали под давлением.
Процесс воздействия поршня регулируется реле. После того как реле заканчивает работать, металл начинает остывать в формирующей полости, а застыв, автоматически выталкивается из неё. У полученной заготовки отрезается облой или заливы, а затем её механически обрабатывают на специальном оборудовании и при необходимости осуществляют термообработку.
Огромный объем продукции в кратчайшие сроки
Литьё под давлением обычно осуществляется на высокой скорости, что позволяет создавать большой объём продукции. На качество полученных изделий влияет множество факторов, которые определяются не только конструкторским решением или использованием определенной технологии, но и:
- маркой сплава,
- формой отливки,
- литниковой системой,
- способностью оборудования поддерживать нужную температуру металла,
- прочими особенностями производства.
Изготовление отливок центробежным литьем под давлением предполагает высокую точность соответствия завяленным габаритам (4-7 класс). Также оно позволяет быстро создавать изделия и обеспечивает чёткость рельефа поверхности отливки и её чистоту (заготовка до 45кг. будет выполнена с точностью 6-8 класса). Станок литья под давлением способен создавать в минуту до 50 изделий, а при использовании многогнездовых форм за одну заливку можно производить от 15 деталей и больше.
Пришлите ваши чертежи или эскизы на [email protected]
Либо звоните 8-800-250-88-72. Доставка по России и СНГ!!!
Данный способ литья позволяет производить высококачественные детали, которые используются в оргтехнике и бытовой технике. Полученные изделия также применяются в двигателях внутреннего сгорания, сантехнике, печатных станках и пр.
Процесс литья предполагает несколько этапов
Пресс-форма или литейная форма обычно стальная. Для того чтобы отливки соответствовали заявленным характеристикам и габаритам подбирается специальная оформляющая плоскость, которая придаёт рельеф внешней поверхности изделий и помогает избежать искажений размеров.
В пресс-форме наличествуют специальные подвижные стержни, изготовленные из металла, задача которых создать внутреннюю полость при литье стали под давлением. Также пресс-форма включает и выталкиватели – механизмы удаляющие заготовку из полости. Литейные машины делятся на два типа: с холодными и горячими камерами, в которых происходит прессование. Холодные камеры прессования работают со сплавами из алюминия, меди и магния. Давление в этих камерах может достигать 700 МПа. В горячих камерах прессования используются в основном сплавы с наличием цинка. В эти камеры помещается расплав, который при движении поршня на небольшой скорости загружается в оформляющую плоскость.
Литье под давлением | Обзор процесса литья под давлением
Литье под давлением — это производственный процесс, при котором расплавленный металл заливают или нагнетают в стальные формы. Формы, также известные как инструменты или штампы, изготавливаются из стали и разрабатываются специально для каждого проекта. Это позволяет создавать каждый компонент с точностью и воспроизводимостью. Алюминий, цинк и магний являются наиболее часто используемыми сплавами для литья под давлением.
Преимущества литья под давлением
Литье под давлением может иметь значительные преимущества по сравнению с другими производственными процессами, которые часто приводят к значительной экономии средств не только в цене самой детали, но и в общей стоимости производства. Когда вы отливаете деталь, вы можете создавать сложные формы сетки, включая наружную резьбу и сложные внутренние элементы с минимальными углами уклона, что сводит к минимуму вторичные операции. Вы также можете комбинировать несколько деталей в одну деталь, исключая сборочные операции и снижая трудозатраты, а также получая дополнительные преимущества упрощенного управления запасами и большей согласованности компонентов.
Другие преимущества:
- Различная толщина стенки
- Более жесткие допуски
- Меньше шагов от сырья до готовой детали
- Быстрое время производственного цикла
- Сокращение брака материалов
- Долгий срок службы инструмента, особенно для обработки цинка и магния
Сплавы для литья под давлением
Цинк, алюминий и магний являются тремя основными сплавами для литья под давлением. Обычно это цветные металлы, а их механические свойства сильно различаются, чтобы соответствовать практически каждому типу применения, который может понадобиться производителю. Литые под давлением сплавы не только выдерживают высокие рабочие температуры, но и полностью пригодны для вторичной переработки. Литые под давлением сплавы также имеют:
- Хорошая коррозионная стойкость
- Высокая прочность и твердость
- Высокая теплопроводность
- Высокая электропроводность
- Выдающиеся свойства экранирования электромагнитных и радиопомех
- Хорошие отделочные характеристики
По отдельности каждый литой сплав предлагает множество преимуществ, которых может не предложить другой. Это одна из замечательных особенностей литья под давлением, вы не должны быть ограничены, когда дело доходит до выбора правильного металла.
Процесс литья под давлением
Не существует единого процесса, подходящего для любого проекта. Каждый проект уникален, поэтому Dynacast предлагает множество решений для всех нужд литья под давлением. Это гарантирует, что правильный процесс всегда используется для правильного приложения. В Dynacast мы предлагаем три различных типа процессов литья под давлением.
Горячая камера
Используется для цинка, некоторых сплавов магния и других легкоплавких сплавов, литье под давлением с горячей камерой является отличным вариантом для сплавов, которые не легко разрушают и разрушают металлические горшки, цилиндры и плунжеры.
Холодильная камера
Лучше подходит для металлов с высокой точкой плавления, таких как алюминий.
Сборка литого металла
За последние 50 лет мы разработали и усовершенствовали наши инновационные; одноэтапное производственное решение, литьевая металлическая сборка. IMA превосходит большинство клеев, используемых для соединения и сборки мелких деталей, и снижает производственные затраты.
Многоползунковое и обычное литье под давлением
Компания Dynacast предлагает два различных типа оснастки: многоползунковую и обычную. Каждый из них имеет свои уникальные преимущества, и наши опытные инженеры могут помочь решить, какой инструмент лучше всего подходит для каждого проекта.
Преимущества многоползунковой оснастки
Наша запатентованная технология многоползунковой оснастки предлагает ряд уникальных преимуществ, в том числе:
- Форма сетки впервые
- Устраняет второстепенные операции, такие как сборка и механическая обработка
- Сложная геометрия и жесткие допуски на более высоких скоростях
- Минимальное отклонение от детали к детали по сравнению с обычными многогнездными штампами
- Компактный инструмент, менее подверженный изменению линии разъема и его отрицательному влиянию на допуски на размеры готовой детали
Преимущества обычных инструментов
Традиционные инструменты для литья под давлением имеют одну или несколько полостей. Инструмент разработан, чтобы быть эффективным и сократить второстепенные операции, что помогает снизить затраты. К другим преимуществам обычных инструментов для литья под давлением относятся:
- Матрицы, предназначенные для эффективного управления крупносерийным производством
- Литье под давлением в форме сетки, конструкция которого направлена на исключение вторичных операций
- Матрицы со стальными распорками для увеличения срока службы инструмента
- Эффективное производство с правильно спланированными линиями охлаждения и подачи воды
Global Die Castings
Dynacast является мировым производителем как обычных, так и многокомпонентных прецизионных литых компонентов. Наши инженеры предлагают проектные решения для различных отраслей, включая бытовую электронику, автомобилестроение, здравоохранение и многое другое. Когда наши инженеры участвуют в проекте на ранней стадии, они могут помочь разработать инструмент и деталь специально для массового производства. Все наши клиенты получают понимание и опыт на всех этапах проекта. Свяжитесь с нашей командой инженеров, чтобы запросить предложение сегодня.
Инструменты для литья под давлением | Литой дизайн
За более чем 80 лет работы мы изготовили более 300 000 уникальных штампов. Все наши штампы и оборудование для литья под давлением стандартизированы во всем мире, и мы глобально координируем наши инструментальные ресурсы. Это означает, что независимо от того, где находится ваше производство, мы поддерживаем вас от концепции, быстрого прототипирования, оснастки и предпроизводственных испытаний до полномасштабного производства. Мы предлагаем два типа процессов оснастки: многоползунковую и обычную.
Свяжитесь с нашей командой сегодня, чтобы узнать о преимуществах Dynacast.
Многоцелевой инструмент для литья под давлением
Наша запатентованная многоползунковая технология была впервые изобретена в 1936 году. С тех пор мы постоянно совершенствуем наши инструменты и машины, чтобы предложить самый передовой процесс литья под давлением. Многоползунковый инструмент предназначен для использования четырех (или более) перпендикулярных суппортов в инструменте, что позволяет нам создавать более сложные и точные отливки. Многокомпонентное литье под давлением предлагает ряд уникальных преимуществ, в том числе:
- Форма сетки в первый раз, исключающая вторичные операции, такие как сборка и механическая обработка
- Сложная геометрия и жесткие допуски на высокой скорости для производительности мирового уровня и снижения общих затрат
- Минимальное отклонение от детали к детали по сравнению со стандартными многогнездными штампами
- Более компактные инструменты, менее подверженные изменению линии разъема и его отрицательному влиянию на допуски на размеры готовой детали
Обычная оснастка для литья под давлением
Обычный инструмент для литья под давлением поставляется с одной полостью (одна деталь за цикл) или несколькими полостями (более одной детали за цикл). Наш традиционный инструментальный процесс разработан только с двумя направляющими, а не с четырьмя, что обеспечивает клиентам эффективность производства и снижение затрат. Когда вы выбираете Dynacast в качестве компании по литью под давлением, вы получаете:
- Качественные матрицы, которые эффективно справляются с большими объемами производства
- Внимание к конструкции штампов, добавление столько функций детали, сколько необходимо, чтобы избежать вторичных операций. Наша цель всегда чистая форма с первого раза
- Тщательное планирование для отказа от механической обработки и снижения затрат
- Прогностический анализ износа для увеличения срока службы наших штампов. Наши разработчики инструментов предсказывают, какая часть штампа может изнашиваться, и вставляют ее в виде отдельного стального элемента
- Тщательно спланированные линии подачи воды и охлаждения обеспечивают эффективное производство
Разработка и производство инструментов Dynacast
Все наши инструменты начинаются с проектирования для производства, когда мы беседуем с нашими клиентами, чтобы убедиться, что любые недостатки детали могут быть проверены и исправлены до того, как инструмент будет построен. Изменение элементов штампа на передней части поможет улучшить конечную деталь, а также повысит общее качество инструмента. На этом этапе проектирования мы также можем предсказать, где инструмент будет изнашиваться, и создать съемные вставки для инструмента, которые могут сэкономить время и затраты на техническое обслуживание. Мы разрабатываем наши инструменты для работы с минимальным временем простоя.
Инструментальное подразделение Dynacast состоит примерно из 25 производителей инструментов, 95% из которых работают с Dynacast более 25 лет. Их знания и опыт имеют огромное значение для наших клиентов. Они не только производят лучшие инструменты для литья под давлением, но и работали с тысячами клиентов практически из каждой отрасли и могут изменить решения, если в процессе производства возникнут какие-либо проблемы.
Свяжитесь с нашей командой инженеров, чтобы запросить расценки, или запланируйте личную встречу, чтобы узнать больше о наших инструментах для литья под давлением.