Литье стали – процесс, способы, методы – Жить Просто
alexxlab | 29.03.2020 | 0 | Разное
Литые диски или штампованные: все «за» и «против»
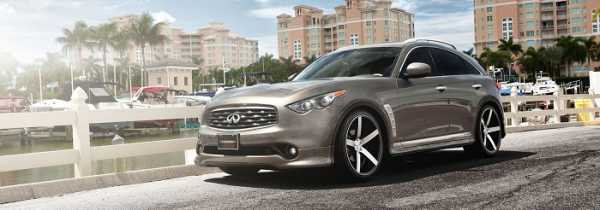
(Голосов: 1, Рейтинг: 5) |
Вопросы, рассмотренные в материале:
- Чем литые диски отличаются от штампованных
- Каковы сильные и слабые стороны литых и штампованных дисков
- На каком типе автомобильных дисков все же остановиться
- Что думают автолюбители о том, какие диски лучше
Чаще всего в комплектации автомобилей эконом-класса идут штампованные диски. В более дорогих машинах они литые. С чем это связано? Складывается впечатление, что в первом случае на колесах экономят, поэтому они хуже. В то время как литье считается более качественным изделием и его могут позволить себе лишь люди обеспеченные. Давайте выясним, что же лучше – литые диски или штампованные.
Чем литые диски отличаются от штампованных
Вопрос о том, какой вариант предпочтительнее – литые или штампованные диски – зимой особенно актуален. Большинство автовладельцев убеждены, что «штамповка» лучше, так как литье под воздействием морозов становится хрупким. Споры о том, какая модель качественнее, не поддерживают только те, у кого есть оба комплекта. В таких случаях хозяева машин меняют резину вместе с дисками в зависимости от сезона. То есть в летнее время они используют красивое литье, а зимой ездят на более практичных штампованных дисках. Для начала разберемся в особенностях обоих вариантов.
- Штампованные диски
Штампованные диски вырезают из листового металла, а затем отдельные куски сваривают и покрывают краской. Такие изделия стоят дешевле литых аналогов. Вместе с тем они более прочные и менее подвержены деформации. Если на «штамповке» появляется вмятина, её довольно просто выправить. Ещё один плюс – подобные диски легко выдерживают низкие температуры.
В отличие от литых дисков штампованные выглядят малопривлекательно и весят гораздо больше. С другой стороны непрезентабельный внешний вид частично компенсируется колпаками.
Литые модели ещё называют «титанами», их производят из алюминиевого сплава, который отливают в специальную форму. Иногда диски вырезают из цельного листа алюминия. Литье выглядит красиво, оно легкое и при этом прочное. Титаны выдерживают низкие температуры, но на морозе становятся менее крепкими. Если летом поломку можно быстро исправить, то в зимнее время разрушенное колесо восстановить не удастся.
Оба вида дисков уже давно соперничают друг с другом, и это связано не только с сезонными различиями. Своих поклонников имеют и литые, и штампованные диски. Разница между этими двумя типами колес, конечно, существует. Мы постараемся быть объективными и понять, каковы достоинства и недостатки обоих комплектов.
Сильные и слабые стороны литых и штампованных дисков
Каждый автовладелец имеет свое мнение относительно того, какой диск лучше. Это вполне закономерно, так как идеальных вариантов не существует. И даже литье, имеющее много плюсов, все же не лишено некоторых недостатков.
1. Прочность
У титанов есть одно важное преимущество – невероятно высокая прочность. Причина в том, что для производства литья используют материал прекрасного качества – алюминий. Легкое и надежное сырье сегодня используется в аэрокосмической отрасли. В то же время штамповку изготавливают из стали, которая легко деформируется даже из-за небольшого физического воздействия.
Однако прочность и твердость материала не считается таким уж большим преимуществом. Хотя литые диски устойчивы к ударам средней мощности, они могут лопнуть при более серьезном воздействии, причем колеса потом невозможно будет восстановить. И даже если появится только вмятина, все равно диски уже нельзя отремонтировать.
2. Работа подвески
Какой диск тяжелее: литой или штампованный? Как правило, литье весит меньше на 20-50% процентов, но тут многое зависит от размера, дизайна и других характеристик. Благодаря небольшой массе изделия нагрузка на подвеску при движении по хорошему дорожному покрытию снижается. Из-за этого интенсивность толчков и ударов ослабевает, а звуки, раздающиеся из-под днища на неровной дороге, становятся менее громкими. Все это делает езду на машине более комфортной.
Однако не стоит забывать, что штамповка из-за своей пластичности поглощает много энергии и не передает её на подвеску. А жесткое литье ускоряет износ ходовой части, если постоянно ездить по дороге со значительными неровностями или вовсе по бездорожью. По этой причине не советуем ставить титаны на коммерческие машины, солидные внедорожники и транспортные средства, которые используются в тяжелых условиях.
3 Тормозной механизм
Если вы внимательно рассмотрите литые диски, то заметите, что у них чаще всего есть тонкие спицы, приоткрывающие внутреннюю сторону колеса. В штамповке спиц нет, и колеса являются цельными элементами с маленькими отверстиями, уменьшающими массу. Благодаря особенностям конструкции литых дисков к тормозной системе поступает гораздо больше воздуха, и они лучше охлаждаются. Это качество свидетельствует о надежности и эффективности функционирования изделия, и в опасной ситуации шансы удачно затормозить повышаются.
Но есть и минус – узлы, расположенные под колесами, плохо защищены. А значит, внутрь легко может попасть камень или другой предмет, особенно если машина движется с небольшой скоростью.
Рекомендуем
«Какой размер колес лучше, и есть ли «золотая середина»? » Подробнее4. Внешний вид
У литых и штампованных дисков разница есть и во внешнем виде. Штамповку делают из стандартного металлопроката, поэтому она имеет классическую форму и лишена каких-либо декоративных элементов. У литья бывает разное количество спиц, толщина которых также варьируется. Литые диски могут быть массивными (такой дизайн подходит для внедорожников) или ажурными (которые хорошо смотрятся в спортивных машинах).
При всем многообразии вариантов литья, которые встречаются на отечественном рынке, в случае поломки купить всего один аналогичный диск будет проблематично. Однако эта проблема решается благодаря интернет-магазинам.
5. Устойчивость
Если у штампованного диска повредить грунтовку, он начнет ржаветь. Коррозия усиливается, если ездить по дорогам, обработанным антигололёдным веществом. У литья нет такого недостатка, так как алюминий не боится влаги, даже если на нем появляются царапины, трещины и прочие повреждения.
Однако некоторые литые модели все же не так устойчивы к внешним воздействиям. Если в составе изделия есть много магния, то контакт с водой может повлиять на прочность колеса.
Что может повредить стандартные алюминиевые элементы:
- Электрохимическая коррозия, которая появляется, когда на колесо попадает большое количество соли. Такое происходит постоянно, поскольку именно солью у нас борются со льдом.
- Чрезмерный нагрев при откручивании замерзших болтов в холодное время года.
- Хранение в неподобающих условиях.
- Технические свойства автомобиля
Благодаря маленькому весу колесо становится более инертным, и в результате для того, чтобы машина развила нужную скорость, требуется гораздо меньше усилий. Это улучшает динамические показатели колеса, снижает количество времени, которое необходимо для разгона.Также в сравнении с автомобилем на штамповке, у транспортного средства на литье топливо расходуется медленнее. Но помните, что когда машина выезжает на бездорожье, преимущества у штамповки.
6. Целевое назначение
Отличия литых дисков от штампованных существенны, и у каждого варианта есть свои достоинства и недостатки. Так, модели из легкого сплава лучше использовать для скоростной езды по хорошему дорожному покрытию. Как правило, если ездить на таких колесах по плохой дороге, они быстро приходят в негодность и не подлежат ремонту. Штамповку же гораздо легче восстановить. С поломкой можно справиться, вооружившись лишь кувалдой или молотком.
По этой причине штампованные диски часто ставят на недорогие автомобили, внедорожники и коммерческие транспортные средства. Комплекты различаются и по цене. Легкосплавные стоят в 1,5-3 раза дороже.
На каком типе автомобильных дисков остановиться
На какие параметры обращать внимание, выбирая литые или штампованные диски?Есть три основных момента:
- условия, в которых вы собираетесь эксплуатировать автомобиль;
- марка и класс машины;
- активное использование в теплое или холодное время года.
Если вы планируете ездить на одном комплекте ободьев круглый год, то учитывая дороги в России, рекомендуем поставить штампованные модели из стали. Так вы гарантированно не выбросите деньги на ветер.
В идеале же лучше иметь два разных комплекта, чтобы в зависимости от сезона сделать замену литых дисков на штампованные. Напомним, что для лета подходят обода из легкого сплава, а зимой лучше использовать модель из стали. Из-за неубранного снега дорога покрывается наледью и образуются выбоины. Когда вы выезжаете на обочину или плотно прижимаетесь к бордюру, наледь по краям проезжей части царапает титановые диски.
Какие еще моменты стоит принять во внимание, выбирая литые или штампованные диски:
- Если вы передвигаетесь по полям на внедорожнике, не тратьте деньги на литье. На автомобили бизнес и премиум класса, которые ездят по хорошему покрытию, наоборот, не ставьте штамповку, это выглядит неуместно.
- Не используйте титаны на микроавтобусах, который эксплуатируют для коммерческих перевозок. Колеса быстро износятся.
Литые диски, конечно, имеют массу преимуществ. Но российский авторынок они не завоевали даже наполовину. Точно также дела обстоят в странах бывшего СССР: здесь штамповка считается практичнее алюминиевых дисков. Ситуация может измениться, если дорожное покрытие станет более качественным.
Какие диски лучше – литые или штампованные: мнения автолюбителей
«Литые диски или штампованные лучше? Безусловно, титаны. Их масса меньше, поэтому мотор быстрее раскручивает диски. Они более прочные, «убить» штамповку намного легче, чем литье. Внешне модели из легкого сплава выглядят круче. На Ниву, конечно, качественные литые диски я не смог купить, но на остальные машины всегда ставил литье». (Олег)
«Это зависит от того, какая у вас цель. Если хотите улучшить дизайн авто, то тут я согласен, можете вообще что угодно ставить. Если вам нужно сделать колеса более жёсткими, прочными и тяжелыми, тогда вот мой совет. Литье крепче и тверже, но ненамного, а стоит дороже штамповки раза в три. Помню случай из жизни: однажды по пути на Ахтубу въехал на скорости 160 км/ч на асфальтированную ступеньку (шел ремонт дороги, и там, где заканчивался новый асфальт, высота была больше на 10 см, предупреждающий знак отсутствовал). Красивые легкосплавные диски, конечно, разбились. До шиномонтажа я кое-как доехал, но восстанавливать убитое литье – выкидывать деньги на ветер. Похожая ситуация произошла, когда ехали на штампованных дисках, но тут я пару раз ударил молотком и можно было ехать куда угодно». (Андрей)
«Мне нравятся стальные диски, они более пригодны для дорог в нашей стране. Был случай, когда в пути лопнула шина, запаски с собой не было, но на диске производства Германии я смог проехать 75 км. После реставрации он был в ходу еще пару лет». (smoc)
«Вкратце могу сказать вот что. Во-первых, литье – это больше украшение для машины, в эксплуатации оно слабенькое. Во-вторых, у штампованных дисков оптимальное соотношение цена-качество. И в-третьих, кованные модели хороши для осторожных водителей, а не для тех, кто собирает все ямы на пути». (Александр)
Рекомендуем
«Какой размер шин лучше: для лета, зимы, бездорожья» Подробнее«Литые диски или штампованные? Литье крепче, да и выглядит лучше, чем штампованные изделия, так как его делают из алюминия. Это влияет на разгон, на торможение, на мягкость хода и долговечность подвески. Есть и недостатки, конечно: высокая цена на изделие и обслуживание в случае повреждения. Если диски плохого качества, то они облезают при минусовых температурах. У штамповки все наоборот». (ivandrey)
«Литые или штампованные диски? Зимой и весной, когда тает снег, а дороги превращаются в терку, стоит пренебречь дизайном и ездить на штампованном комплекте, потому что он намного лучше рихтуется. У каждого автолюбителя свой подход при выборе дисков. Не имеет особого смысла сравнивать обе модели, так как каждая имеет свои достоинства и недостатки. Водители должны сами решать, какие диски приобретать». (kirich23)
rad-star.ru
Мероприятия в литейной отрасли
Лето стремительно катится к завершению, период отпусков тоже, осенью традиционно начинается активная пора деловых мероприятий в литейной отрасли.
С 9 по 13 сентября в Казани пройдет ХIV международный съезд литейщиков и международная выставка «Литье-2019».
Ожидается прибытие порядка 700 участников из России, Казахстана, Украины, Беларуси, Монголии, Германии, Италии , США, Англии, Турции, Чехии, Китая, Бразилии и других стран.
Готовится насыщенная программа. Будут доклады, презентации, обсуждения, обмен мнениями.
Секция№ 1 «Черные и цветные сплавы». Плавильные агрегаты, технология плавки и внепечной обработки, шихтовые материалы, модифицирование, рафинирование и фильтрация, охрана труда и техника безопасности, технико-экономические и экологические показатели. Механические и эксплуатационные свойства сплавов, дефекты в отливках и
методы их предотвращения, контрольно-измерительная техника.
Секция № 2 «Изготовление литейных форм и стержней». Оборудование для изготовления форм и стержней, выбивки и очистки отливок. Технологические процессы изготовления форм из песчано-глинистых и холоднотвердеющих смесей, изготовления стержней по горячей и холодной оснастке, краски и связующие материалы, литниковые системы, оснастка, технико-экономические и экологические показатели.
Секция № 3 «Специальные виды литья». Литье по выплавляемым и газифицируемым моделям, центробежное, кокильное, непрерывное литьё, литье под низким и высоким давлением. Компьютерное моделирование литейных процессов, 3D—технологии, технико-экономические и экологические показатели.
Город Рязань приглашает профессионалов 10-13 сентября принять участие в международном XIV Конгрессе «Кузнец-2019» «Состояние и перспективы развития технологических процессов обработки металлов давлением и оборудования кузнечно-прессового машиностроения в современных условиях»
Ожидаются выступления специалистов обработки металлов давлением, представителей науки и высшей школы, машиностроительных и металлургических предприятий России и зарубежья.
Мероприятие направлено на обмен информацией, опытом и инновационными проектами по оборудованию, современным технологиям в области обработки металлов давлением, которые являются актуальными для
кузнечно-штамповочных производств и других отраслей промышленности.
В программе значится посещение ОАО «Тяжпрессмаш» — предприятия с более чем полувековой историей.
Конгресс в Красноярске «Цветные металлы и минералы»- один из крупнейших российских горно-металлургических форумов.
Он состоится 16-20 сентября.
В рамках конгресса пройдут три конференции:
Конференция «Алюминий Сибири — ICSOBA»:
- Бокситы
- производство глинозема
- получение алюминия
- углеродные материалы
- литье, обработка давлением, рециклинг
- аддитивные технологии.
Конференция «Золото Сибири»:
- минерально-сырьевая база цветных и благородных металлов.
Конференция «Металлургия цветных, редких и благородных металлов»:
- технологии обогащения руд цветных и благородных металлов
- металлургия цветных, редких и благородных металлов.
В рамках конгресса состоятся семинары, круглые столы, экскурсии на производства края, Международный чемпионат по технологической стратегии «Metal Cup».
pmet.ru
типы, устройство. Пресс-форма для литья – Жить Просто
Как показывает практика, обычные литниковые системы в современном исполнении позволяют произвести окончательное формообразование готового изделия с четкими контурами. В некоторых случаях используются специальные конструкции, когда металл проходит длительную и сложную трансформацию. Такие агрегаты оснащены круговым коллектором, улучшающим условия заполнения.
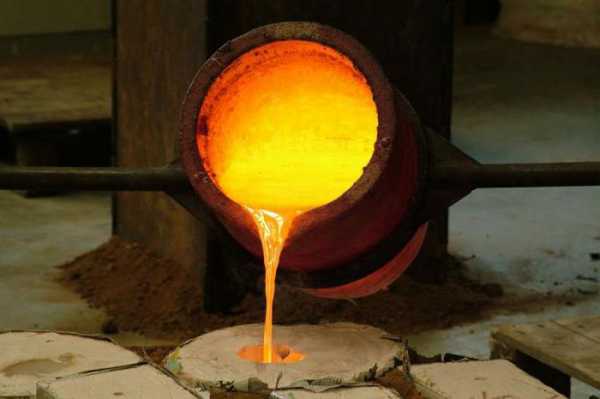
Боковые модификации
Боковые литниковые системы оснащены питателями, которые располагаются под прямым углом к входному литнику. Такой тип часто используется в формах с одним и несколькими рабочими гнездами.
Питатель при подходе к рабочей полости имеет уменьшенную толщину, агрегирует с впускным элементом, сечение которого влияет на количество проходящего метала по полости формы. В питателях бокового типа сырье перемещается по плоскости разъема с последующим заполнением нижней части рабочей камеры. При этом происходит блокирование вентиляционных каналов, что затрудняет удаление воздуха. В связи с этим боковые литниковые системы наиболее эффективны при изготовлении неглубоких заготовок.
Если переместить полость в подвижную часть агрегата, поступающий под давлением металл также будет препятствовать удалению воздушных пузырьков из глубины. Стоит отметить, что при литье деталей с большими центральными стержнями, расположенными перпендикулярно, возможно появление ряда дефектов.
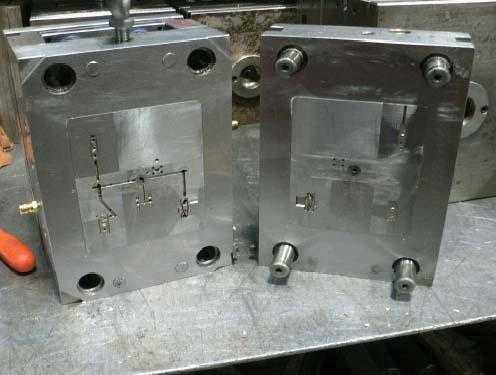
Особенности работы бокового литника
Размещение бокового питателя по касательной линии позволяет нивелировать лобовой удар и завихрения. Отливка имеет широкий элемент, который установлен перпендикулярно стержню, а также присутствуют крупные воздушные подключения. В итоге отсутствует воздушная пористость и встречные струи.
С касательными литниками наиболее качественно получается кольцевое литье, при условии, что ширина детали соразмерна с аналогичным показателем рабочего элемента. Нерационально использовать подобный механизм при отливе кольцевых заготовок со ступенчатым диаметром и сплошных деталей. Связано это с тем, что при вращении металла он завихряется, а это негативно влияет на заполнение центральной части, образуя в ней пробелы. Для решения проблемы применяют литник с более широким диаметром.
Расчет литниковой системы требует учета ширины впускного коллектора и его размещения. Эти факторы влияют на качество отливки. Стоит отметить, что при расположении литника возле широкой части заготовки металл будет поступать широкой струей, завихряясь и преждевременно заполняя вентиляционные гнезда. Если система смонтирована с узкой стороны детали, сырье будет течь по стенкам без существенного завихрения.
Литниковые системы центрального типа
Центральные вариации применяются для отливки плоских заготовок, у которых предусмотрено свободное центральное поле (рамы, кольца). Также они используются для выпуска коробчатых и цилиндрических деталей с открытой центральной полостью.
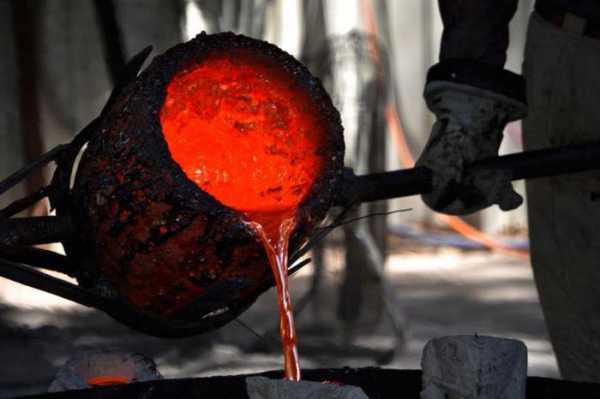
Подобная особенность конструкции позволяет смонтировать ходовой литник по центру оси с торцовой стороны. При этом может использоваться несколько питателей. Центральные отверстия применяются при производстве деталей с полостями, днище которых имеет отверстие. Через него пропускается стержень, трансформирующийся в рассекатель. Этот элемент может проходить строго по центру или со смещением, что дает возможность поместить форму в полости несимметрично к ходовому элементу.
Среди преимуществ центральных литниковых систем для литья под давлением отмечается следующее:
- Имеется возможность заполнения рабочей полости несколькими питателями без образования встречных струй металла.
- Конструкция имеет одинаковый температурный режим всех рабочих поверхностей, что обеспечивает исключение деформаций поверхности.
- Гарантируется существенное сокращение пути металла без добавочной струи из камеры сжатия.
- Обеспечивается равное направление поступления металла и извлечения воздуха.
Для корректной работы агрегата и устранения завихрений струя должна направляться параллельно центровому стержню и стенкам формы.
Применение центральных литников
Рассматриваемые приспособления применяются исключительно в формах с одним рабочим гнездом. Отливка тонкостенных заготовок требует монтажа нескольких питателей. Для работы с толстостенной деталью и слабой обтекаемостью достаточно будет одного элемента. Он устанавливается по касательной с впускным отсеком, что позволяет при поступлении металла с одной стороны максимально убрать воздушные примеси.
Обработка крупных заготовок коробчатой и корпусной конфигурации проводится с применением нескольких питателей центрального типа. Это позволяет обеспечить питание всех отдаленных участков рабочей полости, а также исключить возникновение сплошной струи, вызывающей расслаивание сырья. Суммарное значение питателей увеличивается, а плюсы центральной литьевой формы проявляются, если сечение входного элемента будет превышено настолько, чтобы обеспечить питание рабочей полости без возникновения перебоев струи жидкого металла на каждом питателе.
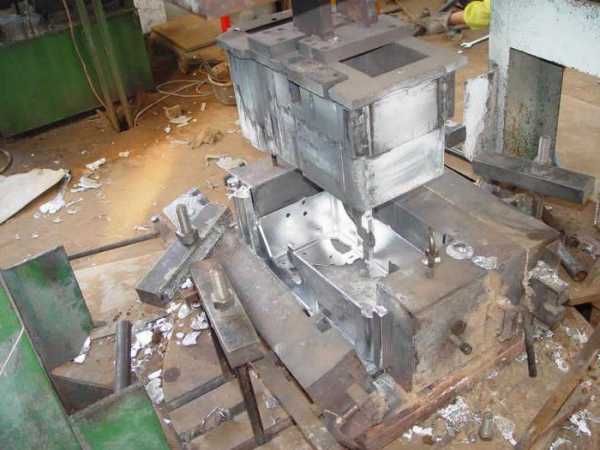
Прямые питатели
Центральные питатели без рассекателей используются для отливки конструкций, конфигурация которых не позволяет установку боковых аналогов. В данном случае элементы литниковой системы монтируются непосредственно на деталь, служат также в качестве питателя. Прямые модификации резонно применять для отлива толстостенных компактных заготовок, которые обрабатываются при малых скоростях питателями большого сечения.
liveprosto.ru
история, производство, продукция – Жить Просто
Более 80 лет ООО «ПК «Бежицкий сталелитейный завод» поставляет отечественному железнодорожному машиностроению качественные стальные отливки. Без его продукции не обходится производство пассажирских, грузовых, специализированных вагонов, составов электропоездов и метрополитена. Продукция поставляется под брендом «Бежицкая сталь».
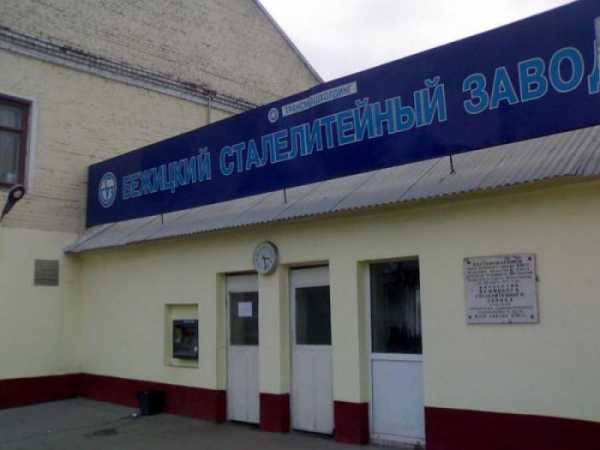
Основание
По решению правительства в 1931 году в городке Бежица Брянской области, на заболоченном лесистом участке, началось возведение сталелитейного цеха брянского завода «Красный профинтерн». К концу 1934 года были отстроены мартеновский корпус, пожарное отделение, котельная, вспомогательные помещения. 28 сентября 1935 года бригады Бориса Лактюхова и Петра Гаврилова выполнили первую опытную плавку. Спустя 2 месяца металл варили уже в 3-х мартеновских печах. Также на Бежицком сталелитейном заводе была построена уникальная сталеплавильная электропечь. Из первой порции стали были отлиты бюст И.В. Сталина и памятная доска.
В 1938 году филиал был реорганизован в самостоятельное производство – Орджоникидзеградский сталелитейный завод. С началом военных действий правительство постановило в срочном порядке эвакуировать основные технологические мощности и часть специалистов на Урал – в Нижний Тагил. На новой площадке началось изготовление танков серии Т-34 и их модификаций.
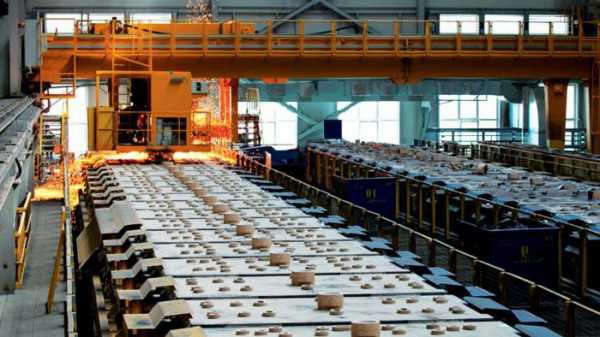
Послевоенное развитие
Спустя месяц после освобождения Бежицы заводчане приступили к восстановлению полуразрушенных цехов и монтажу оборудования. Первую послевоенную сталь сварили 25 декабря 1945 года. В 1948 на завод пришел талантливый руководитель А.Ф. Аверин. Под его началом, спустя полтора года, Бежицкий сталелитейный завод вышел на довоенный уровень производства.
Помимо развития технологической части, значительное внимание руководство уделяло повседневной жизни работников. Для них возводилось жилье, объекты соцкультбыта, проводились культурно-развлекательные мероприятия. Всего за 3 года на окраине Бежицы вырос новый микрорайон малоэтажной застройки.
В 1966 году место директора занял однофамилец предыдущего руководителя Е.К. Аверин. Как и предшественник, он многое сделал для технического перевооружения Бежицкого сталелитейного завода. Правительственными наградами за трудовые достижения отмечены многие сталелитейщики. В советский период предприятие работало на пределе мощностей. С началом перестройки и ломкой хозяйственных связей объем работ снизился. В 90-е БСЗ был акционирован.
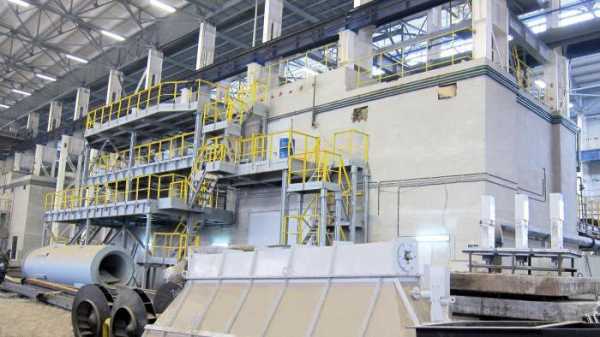
Новый этап
В 2002 году ПК «Бежицкий сталелитейный завод» вошел в состав «Трансмашхолдинга». Этот шаг позволил получить доступ к инвестициям, выйти на новые сбытовые рынки, работать в кооперации с профильными предприятиями железнодорожного машиностроения.
В 2005 году БСЗ возглавил В.В. Воронин. За последующие годы реализована очередная программа технического перевооружения. Старое оборудование частично заменено новыми автоматизированными компьютеризированными комплексами.
Важным достижением стало оборудование участка мелкосерийных отливок в формах из холоднотвердеющих смесей. Затем последовала комплексная реконструкция литейного цеха №3, запущены новейшие линии механообработки крупного литья. Построены новые инфраструктурные объекты.
Сегодня структура производства включает цеха:
- литейный;
- специализированный;
- механосборочный;
- механообработки.
Также на заводе действуют 11 вспомогательных участков и цехов. Качество изделий контролируется работниками сертифицированной заводской лаборатории. При конструировании новых узлов применяется технология 3-D проектирования. На формовочной линии установлено оборудование компании Kunkel-Wagner. Автоматизированные комплексы позволяют проводить работу по заданным параметрам. Таким образом исключается влияние так называемого «человеческого фактора».
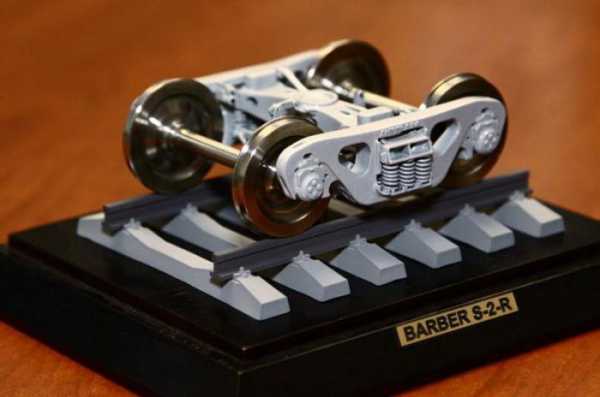
Бежицкий сталелитейный завод: продукция
БСЗ многие годы остается безоговорочным лидером в производстве стальных отливок для железнодорожной отрасли. Ассортимент предприятия насчитывает порядка 300 наименований стального литья повышенной надежности для производства и ремонта вагонов всех типов.
В цехах выпускают конечную продукцию:
- каркасы тележек;
- балки надрессорные;
- балочки центрирующие;
- люльки;
- башмаки;
- валики подъемника;
- замкодержатели;
- корпуса букс;
- автосцепки;
- кронштейны;
- упоры передние, задние;
- поглощающие аппараты;
- центра колесные;
- тяговые хомуты и много другое.
За 80 лет работы Бежицкий сталелитейный завод выпустил 6,47 млн. тонн стали. Освоено и сертифицировано производство надрессорных балок к тележкам серии Barber с осевой нагрузкой 25 тонн.
liveprosto.ru
”Ижсталь” модернизирует литейные мощности – Союз-Литье
Завод «Ижсталь» (входит в Группу «Мечел») увеличил энергомощность литейного цеха. Это повысит объем производства качественной литейной продукции из специальных марок стали, которой завод обеспечивает добывающие предприятия Группы «Мечел» для установки на экскаваторах и другой горной технике.
Завод ввел в эксплуатацию новую кабельную трассу 6кВ для одновременной работы имеющихся сталеплавильных печей. Протяженность трассы превысила 1200 метров, специалисты предприятия проложили более 20 тонн кабеля.
Ранее в дополнение к имеющейся в цехе пятитонной печи для производства крупнотоннажного чугунного литья установили две печи постоянного тока емкостью 1,4 тонны каждая для производства качественных отливок из легированных марок стали. Производительность малотоннажных печей составляет около 800 тонн литья в год. Это расширило номенклатуру литейного цеха до 1500 наименований отливок, большинство из которых – детали для горнодобывающей техники, в том числе – карьерных экскаваторов. Малотоннажное литье также востребовано при проведении ремонтов металлургического оборудования.
В перспективе планируется приобрести дополнительные формовочные машины и смеситель холодных твердеющих смесей, что повысит производительность и улучшит качество литейной продукции.
«Перед нами стоит важная задача: обеспечить потребность горнодобывающих предприятий Группы в качественном литье. Поэтому техперевооружению литейного цеха уделяется самое пристальное внимание», – отметил управляющий директор ПАО «Ижсталь» Сергей Козеннов.
***
ПАО «Ижсталь»
Управление делами администрации
и общественных отношений
Андрей Дюгуров
lityo.com.ua
Литейное производство | Курганский Арматурный Завод
Литейное производство ООО «Курганский арматурный завод» – специализированное предприятие по изготовлению стальных и чугунных заготовок.
Завод оснащён современным технологическим оборудованием. Контроль химического состава сплавов осуществляется в экспресс лаборатории в процессе плавки, качество формовочных смесей приборами земельной лаборатории. Плавка чугуна и сталей осуществляется в индукционных печах фирмы «Inductotherm» (Англия) ИПП-1 емкостью 1т., GW-45 емкостью 0,45т.
- Габариты опок в свету минимальная 400 х 300, максимальная 1800 х 1600 мм
- Имеет мощности по термической обработке углеродистых и нержавеющих сталей, печи оборудованные КИП, работающие на газовом топливе с объемом загрузки 15 тонн и 2 тонны.
Наше предприятие сотрудничает с предприятиями Урала, Сибири и Дальнего Востока.
Имеет сертификаты ИСО 9001-2000 и Сертификаты АPI (Американского института нефти).
Основной продукцией предприятия являются:
- Отливки из серого чугуна марки СЧ-20 ГОСТ 1412-85 развесом от 40 до 1500 кг.
- Отливки из углеродистых сталей марки ст.25Л; 20ГЛ; 30ХМЛ; 35Л; 40Л; 45Л; 20Х5МЛ развесом от 5 до 750 кг.
- Отливки из нержавеющих сталей марки 12Х18Н9ТЛ; 12Х18Н12М3ТЛ; 110Г13Л развесом от 5 до 750 кг.
- Отливки из хладостойкой стали марки ХМ25Л ТУ развесом от 5 до 750 кг.
В литейном производстве освоены следующие технологии литья:
- Чугунное литье в песчаные формы с использованием стержней ЖСС (СО2– процесс) и ХТС (альфа-сет процесс на автоматической линии производства фирмы Omega Foundry Machinery Ltd (Англия))
- Чугунные отливки из марки СЧ-20 для использования в народном хозяйстве, арматурное литье. Отливки с гарантированной герметичностью и механическими свойствами материала.
- Стальное литье в жидкостекольные формы со стернями из ХТС:
- Литье в жидкостекольные формы из сталей 25Л; 20ГЛ; 20Х5МЛ; 30ХМЛ; 20Х13; ХМ25Л; 35Л; 40Л; 20Г1ФЛ; 12Х18Н9ТЛ; 12ХН12М3ТЛ, развес литья от 2,0 – 120,0 кг.
- Точное стальное литье по выплавляемым моделям:
- Литье по выплавляемым моделям из сталей 25Л; 20ГЛ; 20Х5МЛ; 30ХМЛ; 20Х13; ХМ25Л; 35Л; 40Л; 20Г1ФЛ; 12Х18Н9ТЛ; 12ХН12М3ТЛ, развес литья от 0,2 – 5,0 кг.
Отливки, изготавливаемые СЧЛЗ, используются в условиях экстремальных температурных нагрузок, в агрессивных средах, в оборудовании, требующем повышенной надежности и длительной безотказной работы.
Примеры использования отливок:
- Отливки арматуры из стали 12Х18Н9ТЛ и 12Х18Н12М3ТЛ используются в условиях сероводородной среды, стойкие к сероводородному растрескиванию с рабочим давлением от 16 до 250 кгс/см.куб. с условным проходом Ду от 50 до 500 мм. Отливки испытанные номинальным давлением воздухом. Гарантированная герметичность и механические свойства материала;
- Отливки из стали ХМ25Л используются в условиях крайнего севера с рабочим давлением от 16 до 250 кгс/см.куб. с условным проходом Ду от 50 до 300 мм. Отливки испытанные номинальным давлением воздухом. Гарантированная герметичность и механические свойства материала.
Литейное производство ООО «Курганский арматурный завод» приглашает к сотрудничеству! Мы будем рады установить с Вами партнерские отношения.
kurgan-armatura.ru
производство и применение – Жить Просто
Производство этого вида стали занимает главенствующее место среди прочих магнитных материалов. Сталь электротехническая — это сплав железа с кремнием, доля которого составляет от 0,5% до 5%. Широкую популярность изделий данного вида можно объяснить высокими электромагнитными и механическими свойствами. Изготавливают такую сталь из широко распространенных компонентов, дефицита в которых нет. Это объясняет ее низкую стоимость.
Влияние кремния
Данная составляющая во взаимодействии с железом образует плотный раствор с высоким удельным сопротивлением, величина которого зависит от того, какой процент кремния в сплаве. При воздействии его на чистое железо оно теряет свои магнитные свойства.
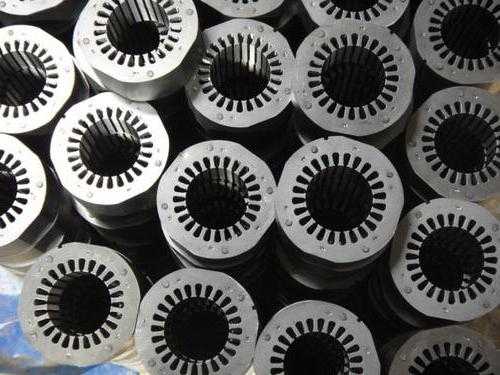
А вот при воздействии на техническое, наоборот, сказывается положительно. Проницаемость железа возрастает и происходит улучшение стабильности металла. Благоприятное действие кремния (Si) можно объяснить следующим образом. Под влиянием этого элемента происходит переход углерода в графит из состояния цементита, который обладает меньшими магнитными свойствами. Элемент Si оказывает нежелательное воздействие на снижение индукции. Влияние его распространяется на теплопроводность и на плотность железа.
Примеси в составе
В своем составе сталь электротехническая может содержать и другие компоненты: серу, углерод, марганец, фосфор и прочие. Самый вредный из них — углерод (С). Он может находиться в форме как цементита, так и графита. Это по-разному влияет на сплав, так же, как и процент содержания углерода. Чтобы избежать нежелательных включений элемента С, нельзя сталь быстро охлаждать для следующего старения и стабилизации.
Отрицательное воздействие на свойства материала оказывают следующие компоненты: кислород, сера, марганец. Они снижают его магнитные качества. Техническое железо в своем составе обязательно имеет примеси. Здесь их приходится учитывать в совокупности, не так, как для чистого железа.
Можно улучшить свойства стали, применив очистку от примесей. Но такой метод не всегда выгоден на масштабном производстве. А вот с помощью холодной прокатки листовая электротехническая сталь образует в своей структуре магнитные свойства. Это позволяет добиться лучших результатов. Но обязательно необходим дальнейший обжиг.
Холодная прокатка
На протяжении длительного времени считали, что кремний увеличивает хрупкость стали. Производство проходило в основном с помощью горячей прокатки. Рентабельность холодной прокатки была низкой.
Только после того, как было обнаружено, что холодная обработка вдоль направления повышает магнитные свойства материала, она получила широкое применение. Другие направления показали себя только с худшей стороны. Холодная прокатка благотворно повлияла на механические свойства, а также на улучшение качества листовой поверхности, повысила его волнистость и дала возможность штампования.
Отличительные свойства, которые получила сталь электротехническая за счет применения холодной обработки, можно объяснить образованием в ней кристаллографической текстуры. Она отличается несколькими степенями. Они, в свою очередь, зависят от того, при какой температуре проходит прокатка, также от толщины необходимого листа и от того, в какой степени он обжат.
Себестоимость листа одной толщины горячекатаной стали в 2 раза ниже, чем холоднокатаной.
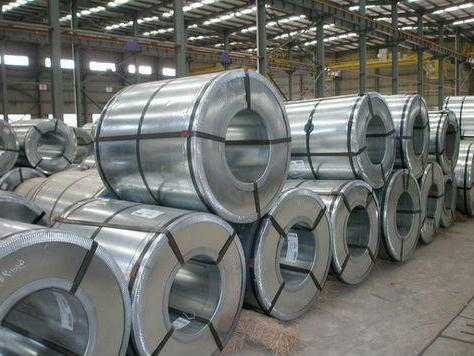
Но данное отрицательное качество полностью компенсируется низкими теплопотерями (их меньше примерно раза в два), высоким качеством и возможностью хорошей штамповки холоднокатаного сплава. Различие в этих сталях — содержание кремния. Его количество составляет от 3,3% до 4,5% соответственно.
ГОСТ
Производители выпускают всего два вида стали, которые соответствуют по ГОСТу.
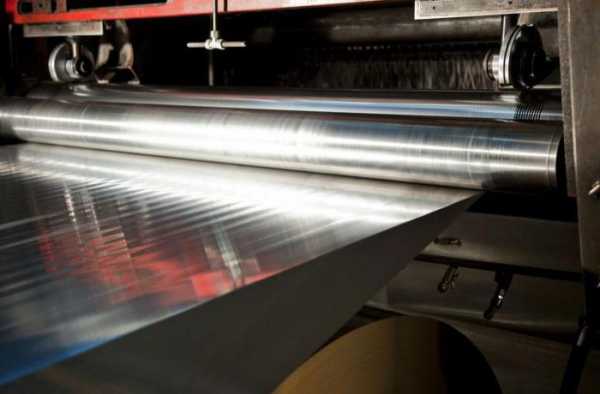
Первый вид — 802—58 «Электротехническая тонколистовая». Второй — сталь электротехническая ГОСТ 9925—61 «Лента холоднокатаная рулонная из электротехнической стали».
Маркируется буквой «Э», за ней идет номер, цифры которого имеют определенное значение:
Цифра ноль следом за второй цифрой означает, что сталь текстурированная. Если стоят два ноля, то она мало текстурированная.
В конце маркировки можно встретить следующие буквы:
Делится сплав по области применения на три вида:
liveprosto.ru