Мартенситные стали это – что это такое, мартенситная сталь
alexxlab | 17.10.2019 | 0 | Разное
Мартенсит и мартенситные стали: виды, структура, превращение
Как фазовая структура мартенсит был обнаружен в начале 20 века. Исследование проводил инженер Адольф Мартенс, который занимался проблемой повышения усталостной прочности металлов. Обнаруженная структура отличалась повышенной износостойкостью и позволила производить детали, выдерживающие более высокие механические и температурные нагрузки.
Общие сведения о мартенсите
Структура на основе перенасыщенного твердого раствора углерода в железе называется мартенсит. Получается он методом переохлаждения аустенитной фазы. Другими словами, мартенсит – результат проведения закаливания сталей с содержанием углерода выше 0,3%. Кристаллы мартенсита имеют тетрагональную структуру, где атомы железа занимают место в узлах решетки.
На вид мартенсит представляет собой множественные темные иглы железа на светлом фоне. Угол наклона данных игл в среднем составляет 60 градусов относительно друг друга. Обнаружить следы углерода на поверхности мартенсита невозможно, т. к. он полностью находится в растворенном состоянии.
Мартенсит выделяется прочностью по сравнению с остальными фазами. Механические свойства до определенного момента в прямой зависимости от количества углерода в стали. Но стоит заметить, что после прохождения определенной отметки прочность падает, и начинает повышаться хрупкость.
Согласно исследованиям, проводимым в 30-х годах прошлого столетия советскими учеными, причины высоких механических характеристик мартенсита кроются в следующем:
- Структура мартенсита имеет блочный характер, при том что сами блоки обладают достаточно малыми размерами.
- Сопротивление статическим искажениям, что означает устойчивость положения атомов при их смещении от идеального размещения атомов в кристаллической решетке.
- В случае воздействия механических нагрузок, и как следствие пластической деформации, выделяются мельчайшие твердые частицы, блокирующие скольжение слоев относительно друг друга и повышающие твердость сплава.
Твердость мартенсита имеет валатильный характер и зависит от температуры нагрева, охлаждения и времени выдержки стали. В среднем ее значение колеблется в пределах 35 — 70 единиц по шкале Роквелла. Также мартенсит выделяется большим удельным объемом. Его значение выше по сравнению с другими фазовыми структурами такими как аустенит, перлит и т. д.
Как следствие от всего вышесказанного, образование мартенсита сопровождается значительными изменениями стали в объеме. Это, в свою очередь, приводит к нежелательному повышению внутренней напряженности в структуре, которая в будущем может стать причиной появления трещин.
Мартенситное превращение
Мартенсит образуется только в среде аустенита. Причиной, по которой происходит данная трансформация, является наличие большого количества свободной энергии аустенитом. Катализатором процесса превращения служит температура, которая в зависимости от химического состава стали должна находиться на уровне 500-700 ºC.
Также доказано, что мартенситное превращение тесно связано с центрами кристаллизации, которые образуются при повышении температуры. Они стимулируют рост кристаллов, уплотняя атомы и увеличивая, соответственно, прочностные свойства стали. Данный процесс не требует большого количества энергии и активируется при достаточно низкой температуре.
Рост кристаллов происходит до тех пор, пока какой-либо из атомарных слоев входит как в мартенситную, так и в аустенитную кристаллическую решетку. Причем между данными структурами не должно быть разделительной поверхности.
В противном случае образуется сдвиг одной фазы относительно другой, что вызывает появление значительного количества напряжения на их границе. Напряженность провоцирует появление упругих деформаций, как следствие кристаллы (иглы) останавливают свой рост.
При трансформации аустенита в мартенсит не происходит образование новых химических соединений. Этот процесс структурный. Атомы меняют свое местоположение, что влияет на тип и размеры кристаллической решетки.
Мартенситное превращение требует наличия постоянного переохлаждения. Также стоит заметить, что увеличение объема структуры происходит не за счет роста отдельных игл, а по причине образования новых, меньших с точки зрения размеров кристаллов, мартенсита.
Среди особенностей мартенситного превращения выделяется то, что аустенит не может полностью перейти в мартенсит. Бывают исключения — стали, точка перехода аустенита в мартенсит которых лежит ниже нуля. Но в большинстве случаев всегда имеется некоторый объем аустенитных фаз, не претерпевших своих структурных изменений. Связано это с физическими особенностями железа и углерода.
Трансформация аустенита в мартенсит относится к одним из базовых структурных изменений не только у сталей, но и у сплавов на основе титана и меди.
Виды мартенсита
В зависимости от степени нагрева и температуры охлаждаемой среды получают различные типы мартенсита. Существуют следующие его основные виды:
- Пластинчатый мартенсит
- Реечный мартенсит.
Каждый из них имеет свои особенности и соответственно механические свойства.
Пластинчатый мартенсит наблюдается в основном в высокоуглеродистых конструкционных сталях. Он образуется в результате закалки и характеризуется наличием мартенситом формы в виде пластин. Предел прочности на разрыв такого мартенсита может доходить до 900 Мпа. Твердость до 75 HRC.
Реечный мартенсит получается в результате улучшения (закалка с высоким отпуском) легированных сталей. Структура данного типа имеет форму реек размером до 2 мкм. Такой вид мартенсита отличается большей износостойкостью и лучшей динамической вязкостью.
При соблюдении определенного режима температур структура стали может содержать мартенсит как реечного, так и пластинчатого типа.
Мартенситные стали
К сталям мартенситного типа относят высоколегированные стали, структура которых после проведения термической обработки представлена мартенситом.
Сам по себе мартенситный сплав плохо поддается резанию. Его обрабатываемость повышают путем проведения предварительного отжига при температуре 800-900 ºC.
Как правило, мартенситные стали легируются такими металлами как вольфрам, никель и молибден для повышения жаропрочности и коррозионной устойчивости сплава к агрессивному воздействию среды.
Также мартенситная сталь обладает таким полезным свойством как самозакаливание, т. е. самопроизвольное повышение твердости после проведения термической обработки.
Стали мартенситного класса относятся к 3 группе свариваемости. Проведение сварки требует предварительного нагрева до 200-300 ºC и последующего отжига детали. Все это необходимо для снижения внутреннего напряжения и уменьшения вероятности образования трещин на поверхности сварного шва. На практике данные стали свариваются методом аргонодуговой и электрошлаковой сварки.
Механические свойства сталей на основе мартенсита достаточно высокие. Так, марка 15Х5, применяемая при изготовлении сосудов высокого давления, имеет предел прочности на разрыв равным почти 400 Мпа.
Дополнительное легирование вольфрамом и ванадием сильно повышает жаропрочность сплава. Предел прочности стали 10ХМФБ составляет уже 600 Мпа. Сталь нашла применение в производстве коллекторов, трубопроводов и нагревательных котлов.
Увеличение содержания бериллия в составе мартенситных сталей способствует дальнейшему повышению их механических свойств. Предел прочности стали 12Х11В2МФ равен примерно 850 Мпа. Такие марки применяются в производстве деталей, испытывающих повышенную тепловую и механическую нагрузку. Например, в корпусе и роторе газовой и паровой турбины, а также в качестве материала для лопаток турбовинтовых компрессоров.
Стали мартенситного класса достаточно упруги и хорошо сопротивляются ударным нагрузкам. Ударная вязкость колеблется в пределах 80-150 Дж\см2. Ее значение в большей степени зависит от типа термической обработки и содержания тех или иных элементов. Наибольшее ее значение получается в результате проведения закалки с последующим высоким отпуском.
Мартенситные стали не отличаются высоким значением пластичности. Относительное удельное сжатие равно 14-24%. Данный параметр зависит в большей степени от количества углерода в составе стали. Также такие элементы как никель и медь оказывают отрицательное влияние на пластичность сплава.
Оцените статью:Рейтинг: 0/5 – 0 голосов
prompriem.ru
Нержавеющие хромистые (ферритные и мартенситные) стали.
Нержавеющие (коррозионностойкие) и жаростойкие стали и сплавы, основа которых железо и никель – это важнейшая категория специальных конструкционных материалов, которая нашла применение во многих отраслях промышленности. Повышенная стойкость против равномерной коррозии в широкой гамме коррозионно-активных сред различной степени агрессивности – отличительная особенность нержавеющих и жаростойких сталей и сплавов.
Многие нержавеющие стали кроме того обладают стойкостью против специальных видов коррозии, таких как межкристаллитная, питтинговая, щелевая коррозии и коррозионное растрескивание.
Основной легирующий элемент, придающий стали коррозионную стойкость в окислительных средах это Cr – хром. Хром способствует образованию на поверхности нержавеющей стали защитной плотной пассивной пленки окисла Сr2O3. Достаточная для придания коррозионной стойкости нержавеющей стали толщина пленки образуется при добавлении к сплаву не менее 12,5% хрома. Хром и железо в сплаве образуют твердый раствор.
Стоимость хрома сравнительно невысока, он не является дефицитным компонентом. Поэтому хромистые нержавеющие стали относительно недорогие и, обладая достаточно хорошим комплексом технологических свойств, находят широчайшее применение в промышленности. Из хромистых нержавеющих сталей изготавливаются элементы оборудования, работающего при высоком давлении и температуре в условиях воздействия агрессивных сред.
Хром, которым легируются нержавеющие стали обеспечивает не только коррозионную стойкость сталей в окислительных средах, но и формирует их структуру, механические и технологические свойства и жаропрочность. Образуемый хромом и железом непрерывный ряд твердых растворов при концентрациях начиная с 12,5% и выше, способствует формированию в хромистых нержавеющих сталях различной структуры, обеспечивающей многообразие их свойств.
Углерод в составе хромистых нержавеющих сталей.
Кроме хрома на формирование физико-механических свойств хромистых сталей, значительное влияние оказывает содержание углерода. Структуру нержавеющей стали в зависимости от содержания углерода разделяют на три главных класса: мартенситная, мартенситно-ферритная и ферритная. Это нашло отражение в классификации нержавеющих сталей по ранее действующему ГОСТ 5632-72 “Стали высоколегированные и сплавы коррозионностойкие, жаростойкие и жаропрочные”.
Углерод содержащийся в составе нержавеющей стали, в том числе и в хромистой, это нежелательный элемент. Углерод слишком активный компонент, связывая хром в карбиды, он обедняет твердый раствор, тем самым понижая коррозионную стойкость нержавеющей стали. Кроме того повышенное содержание углерода требует повышения температуры закалки до 975-1050оС, для более полного растворения карбидов хрома.
В качестве примера серьезного влияния углерода на структуру и свойства нержавеющей стали рассмотрим сталь с содержанием 18% Cr. Например сталь 95Х18 в составе которой содержится 0,9-1,0%С и имеющая структуру мартенсита, обладает высокой твердостью (>55HRC), но коррозионная стойкость ее умеренная. А нержавеющие стали 12Х17, 08Х17Т, 08Х18Т1, со структурой феррита, имеют наоборот, низкую твердость и высокие коррозионные свойства.
Ферритные нержавеющие стали.
Нержавеющие стали с содержанием Cr более 12,5% и с минимальным количеством углерода имеют структуру феррита и называются ферритными. Коррозионная стойкость хромистых ферритных нержавеющих сталей во многих агрессивных средах может превосходить многие хромоникелевые аустенитные нержавеющие стали, при этом они не склонны к коррозионному растрескиванию под напряжением. При дополнительном легировании кремнием и алюминием хромистые ферритные нержавеющие стали могут быть использованы при производстве оборудования, работающего в окислительных условиях при высоких температурах.
Недостатком, сдерживающим более широкое применение хромистых ферритных нержавеющих сталей сдерживается из-за чрезмерной хрупкости их сварных соединений. Высокая чувствительность к надрезу при нормальной температуре делает их так же непригодными для изготовления оборудования, работающего под давлением, при ударных и знакопеременных нагрузках. Ферритные нержавеющие стали используют для изготовления ненагруженных устройств и изделий.
Для обеспечения свариваемости хромистых ферритных нержавеющих сталей необходимо ограничением в иx составе не только углерода, но и азота. Нержавеющие ферритные стали, с суммарным содержанием углерода и азота не более 0,020% обладают большей пластичностью и повышенной ударной вязкостью, а значит меньшей хрупкостью при сварке. Но технология производства таких сталей усложнена, так как необходимо использование вакуумных печей или продувка расплава аргоном или аргоно-кислородной смесью.
Нержавеющие стали ферритного класса при нагреве не изменяют состав структуры, твердый раствор лишь становится более однородным. Поэтому для увеличения коррозионной стойкости можно использовать термическую обработку.
Мартенситные нержавеющие стали
Хромистые нержавеющие стали, в составе которых содержится повышенное количество углерода имеют структуру мартенсита. Для обеспечения заданных коррозионных и других свойств, мартенситные стали дополнительно легируются никелем и другими химическими элементами. Никель взаимодействуя с углеродом стабилизирует структуру нержавеющей стали, а молибден, вольфрам, ванадий, ниобий вводят для повышения жаропрочности сталей.
Прочность обычных мартенситных хромистых нержавеющих сталей остается удовлетворительной прочностью при температурах до 500оС, то дополнительное легирование элементами, образующими соединения с углеродом поднимают этот порог до 650оС. Это позволяет использовать легированные мартенситные хромистые нержавеющие стали для изготовления элементов современного энергетического оборудования. Молибден и вольфрам, кроме того, снижают хрупкость при длительной эксплуатации при высоких температурах.
Стали мартенситного класса, такие как 20Х13, 30Х13, 40Х13, 65Х13 и др., обладают повышенной твердостью и используются для изготовления режущего инструмента, и элементов оборудования работающих на износ. Термическая обработка сталей этой группы заключается в закалке и отпуске на заданную твердость.
Мартенситные нержавеющие стали так же склонны к хрупкому разрушению в закаленном состоянии, что усложняет технологию их сварки. Содержание углерода в мартенситных сталях, как правило, превышает 0,10%, и это приводит к образование холодных трещин в процессе охлаждения мартенсита, после нагрева электросваркой. При снижении содержания углерода дополнительным легированием вязкость мартенсита повышается, однако при этом возникает другая опасность, а именно образование структурно-свободного феррита, который, так же является причиной высокой хрупкости стали.
Для предотвращения образования холодных трещин мартенситные нержавеющие стали сваривают при температуре воздуха ≥0оС и применяют предварительный и сопутствующий подогрев до 200 …450оС. Температура подогрева назначается в зависимости от склонности стали к закалке.
Мартенситно-ферритные нержавеющие стали.
К этому классу относят стали с частичным γ→α превращением. Термокинетическая диаграмма у этих сталей состоит из двух областей превращения. При температурах >600оС при низкой скорости охлаждения возможно образование ферритной составляющей структуры. При большой скорости охлаждения <400oС наблюдается бездиффузионное превращение аустенита в мартенсит. Количество образовавшегося мартенсита зависит от содержания углерода и скорости охлаждения.
Коррозионная стойкость нержавеющих сталей мартенситно-ферритного класса зависит от содержания в них хрома. При содержании 17%Cr достигается стойкость в 65%-ной азотной кислоте при 50оС, при дальнейшем повышении концентрации хрома расширяется область применения хромистых нержавеющих сталей в различных средах. Мартенситно-ферритные стали находят довольно широкое применение для изготовления нефтехимической аппаратуры и энергетического оборудования.
По свариваемости мартенситно-ферритные нержавеющие стали так же являются неудобными материалами. В связи с неизбежной подкалкой при сварке сварные соединения мартенситно-ферритных сталей склонны к образованию трещин замедленного разрушения.
Другие особенности хромистых нержавеющих сталей.
Коррозионная стойкость хромистых нержавеющих сталей напрямую зависит от содержания хрома, чем выше, тем лучше. В настоящее время хромистые нержавеющие стали по доле содержания хрома подразделяют на три типа: содержащие 13%Сr; содержащие 17%Сr, и нержавеющие стали содержащие 25—28% Сr.
Стали 08X13 и 12X13 обладающие повышенной пластичностью, используются для изготовления деталей, подвергающихся ударным нагрузкам, таки как турбинные лопатки, арматура для крекинг-установок, предметы домашнего обихода.
Из нержавеющих сталей 30X13 и 40X13, со структурой мартенсита после термической обработки изготавливают измерительный и медицинский инструменты, пружины и другие коррозионностойкне детали, от которых требуется высокая твердость или прочность.
При концентрации хрома выше 20% и дополнительном легировании молибденом хромистые нержавеющие стали приобретают стойкость против питтинговой коррозии. По стойкости против коррозиионного растрескивания хромистые нержавеющие стали ферритного класса превосходят аустенитные хромоникелевые стали типа 08Х18Н10Т.
Введение карбидообразующих элементов, например титана, значительно повышает стойкость сварных соединений из хромистой нержавеющей стали против межкристаллитной коррозии. Это так же позволяет снизить склонность структуры стали к росту зерна (сталь 08Х18Т1). Дополнительное замедление роста зерна ферритных нержавеющих сталей происходит также при микролегировании поверхностно-активным элементами, такими как церий. Микролегирование церием использовано, в частности, в стали 08Х18Тч (ДИ-77). Положительный эффект от введения редкоземельных элементов достигается только в определенных количественных пределах и при соблюдении технологического процесса.
Как уже говорилось на снижение хладноломкости ферритных нержавеющих сталей значительное влияние оказывают примеси внедрения – углерод и азот. При суммарном содержании углерода и азота ≤ 0,01% работоспособность сварных соединений из высокохромистых ферритных нержавеющих сталей при отрицательных температурах значительно возрастает. Чувствительность ферритных нержавеющих сталей к хладноломкости повышает и наличие в сплаве фосфора, кислорода, серы, марганеца, кремния и это накладывает повышенные требования к технологии выплавки.
При снижении суммарного содержания углерода и азота до 0,010-0,015%, повышается стойкость нержавеющей стали против межкристаллитной коррозии. При превышении содержания этих компонентов требуется введение в состав нержавеющей стали дополнительных стабилизаторов – титана и ниобия.
Высокохромистые нержавеющие стали становятся склонными к охрупчиванию при неправильной термической обработке. Развивается так называемая “475оС-хрупкость” нержавеющей стали, которая правда носит обратимый характер и устраняется новой термической обработкой.
Качество поверхности горячекатаного и холоднокатаного листа из хромистых ферритных титаносодержащих нержавеющих сталей повышается при легировании кремнием (сталь 04Х15СТ. Легирование кремнием повышает сопротивление точечной коррозии за счет обогащения кремнием верхних слоев защитной пленки.
Особую группу ферритных нержавеющих сталей составляют так называемые “суперферриты”, в которых более жестко ограничен состав элементов-примесей (01Х18М2Т-ВИ, 01Х25М2Т-ВИ, 01Х25ТБЮ-ВИ). Эти нержавеющие стали обладают повышенным уровнем пластичности и вязкости сварных соединений и устойчивы против питтинговой коррозии и коррозионного растрескивания в большинстве агрессивных сред.
Из нержавеющей стали 12X17 изготавливают теплообменники, трубопроводы и баки для кислот. Введение молибдена (12Х17М2Т) делает нержавеющую сталь стойкой даже в органических кислотах (уксусной, муравьиной). Для изготовления шарикоподшипников, работающих в агрессивных средах, используют сталь 95X18 (0,9—1,0% С, 17—19% Сr).
Приглашаем к сотрудничеству
www.mpoltd.ru
Мартенситные стали
(стали мартенситного класса)
Темы: Сварка стали.
Хромистые мартенситные стали (табл. 1) имеют в основном повышенное содержание углерода, некоторые из них дополнительно легированы никелем, молибденом и другими элементами. Углерод и никель расширяют γ-область и способствуют полному γ→α(м)-превращению в процессе охлаждения. Ферритообразующие элементы (молибден, вольфрам, ванадий, ниобий) вводят для повышения жаропрочности сталей.
Если обычные 11… 12%-ные хромистые стали обладают высокой прочностью до 500оС, то стали, дополнительно легированные карбидообразующими элементами, обладают высокими прочностными характеристиками до 650оС, что позволяет их использовать для изготовления современного энергетического оборудования (табл. 2). Молибден и вольфрам, кроме того, устраняют развитие хрупкости в процессе длительной эксплуатации хромистых сталей при высоких температурах.
Другие страницы по теме
Мартенситные стали
(стали мартенситного класса):
Повышенная склонность мартенситных сталей к хрупкому разрушению в закаленном состоянии усложняет технологию их сварки. Содержание углерода в мартенситных сталях, как правило, >0,10 %, поэтому в сварго разных соединениях возможно образование холодных трешин (ХТ) из-за высокой тетрагональности образуюшегося в процессе охлаждения мартенсита. При снижении содержания углерода вязкость мартен сита повышается, однако возникает опасность образования структурно-свободного феррита, который, в свою очередь, является причиной высокой хрупкости, не устраняемой к тому же термическим отпуском. Поэтому трещины на сварных соединениях мартенситных сталей мoгут наблюдаться в процессe непрерывного охлаждения, и после охлаждения дo нормальной температуры вследствиe замедленного разрушения.
Для высокохромистых сталей температура начала мартенситного превращения (Тм.н.) ≤360оС, а окончания (Тм.к.) 240оС. С увеличением содержания углерода точки Тм.н. и Тм.к. еще более понижаются, что приводит к возрастанию твердости мартенсита и его хрупкости. Учитывая это, а также необходимость обеспечения высокой пластичности, ударной вязкости и стойкости против хрупкого разрушения, содержание углерода в хромистых мартенситных сталях ограничивают до 0,20 %.
Для предотвращения образования холодных трещин мартенситные стали сваривают при температуре воздуха ≥0оС и применяют предварительный и сопутствующий подогрев до 200 …450оС. Температура подогрева назначается в зависимости от склонности стали к закалке. И в то же время температура подогрева не должна быть слишком высокой, так как это может привести к отпускной хрупкости вследствие снижения скорости охлаждения металла в ОШЗ в интервале температур карбидообразования. Высокий подогрев, как и сварка с большой погонной энергией, приводит к перегреву околошовного металла, росту зерна, сегрегациям примесей на границах зерен, способствуюших охрупчиванию сварных соединений. Лучшие свойства достигаются при подогреве в интервале Тм.н. и Тм.к. c подстуживанием после сварки до Тм.к. , но ≥100oC.
Таблица 1. Хромистые мартенситные стали: химический состав.
Марка стали | С | Si | Mn | Cr | Ni | Mo | V | S | P | прочих элементов |
15Х5 | ≤0,15 | ≤0,5 | ≤0,5 | 4,5…6,0 | ≤0,6 | – | – | ≤0,025 | ≤0,030 | Не регламентируется |
15Х5М | 0,45…0,60 | – | ||||||||
15Х5ВФ | 0,3 ..0,6 | – | 0,4…0,6 | |||||||
12Х8 | ≤0,12 | 0,17 ..0,37 | 0,3 ..0,6 | 7,5…9,0 | ≤0,4 | – | – | ≤0,030 | ≤0,035 | |
20Х8ВЛ | 0,15 ..0,25 | 0,30 ..0,60 | 0,30. .0,50 | – | – | – | ≤0,035 | 0,040 | 1,25 .. 1,75 W | |
12Х8ВФ | 0,08 ..0,15 | ≤0,6 | ≤0,5 | 7,0…8,5 | ≤0,6 | – | 0,3 ..0,5 | ≤0,025 | ≤0,030 | 0,6 .. 1,0W |
10Х9МФБ | 0,08 ..0,12 | ≤0,5 | 0,3 ..0,6 | 8,6… 10,0 | ≤0,7 | 0,6 ..0,8 | 0,15 ..0,25 | ≤0,015 | Не регламентируется | |
12Х11В2МФ | 0,10 ..0,15 | 0,50 ..0,80 | 10,0… 12,0 | ≤0,6 | 0,6 ..0,9 | 0,15 ..0,30 | ≤0,025 | ≤0,025 | 1,70…2,20 W | |
15Х11МФ | 0,12 ..0,19 | .≤0,7 | 10,0… 11,5 | – | 0,6 ..0,8 | 0,25 ..0,40 | ≤0,030 | Не регламентируется | ||
18Х11МНФБ | 0,15 ..0,21 | ≤0,60 | 0,6… 1,0 | 0,5 .. 1,0 | 0,8 .. 1,1 | 0,20. .0,40 | 0,20…0,45 Nb | |||
13Х 11 Н2В2МФ | 0,10. .0,16 | ≤0,60 | 10,0. .12,0 | 1,5 .. 1,8 | 0,35 ..0,50 | 0,18 ..0,30 | 1,6 ..2,0W | |||
10Х12НДЛ | ≤0,10 | 0,17…0,40 | 0,20…0,60 | 12,0. .13,0 | 1,0 .. 1,5 | – | – | ≤0,25 | ≤0,25 | 0,80.. 1,10 Сu |
06Х12Н3Д | ≤0,06 | ≤0,3 | ≤0,60 | 12,0. .13,5 | 2,8 ..3,2 | ≤0,025 | ≤0,025 | |||
20Х13 | 0,16…0,25 | ≤0,8 | ≤0,8 | 12,0. .14,0 | – | ≤0,025 | ≤0,030 | Не регламентируется |
Таблица 2. Мартенситные стали : механические свойства, не менее.
Марка стали | σв, МПа | σ0,2,МПа | δ5, % | ψ,% | KCU, Дж/см2 | Примеры использования |
15Х5 | 392 | 216 | 24 | 50 | 98 | Сварные сосуды и аппараты с давлением до 16 МПа при температуре стенки ≥-70оС |
15Х5М | 22 | 118 | ||||
15Х5ВФ | ||||||
12Х8 | – | – | ||||
12Х8ВФ | 167 | 50 | 170 | |||
20Х8ВЛ | 580 | 392 | 16 | 30 | 39 | |
10Х9МФБ | 600 | 400 | 20 | 70 | 80 | Поверхность нагрева котлов, коллектора, трубопроводы |
15Х11МФ | 600 | 490 | 15 | 55 | 60 | Корпуса и роторы паровых и газовых турбин, лопатки паровых турбин, диафрагмы |
18Х11МНФБ | 740 | 590 | 50 | |||
13Х11Н2В2МФ | 880 | 735 | 55 | 90 | ||
12Х11В2МФ | 850 | 700 | 50 | |||
10Х12НДЛ | 700 | 500 | 14 | 30 | 50 | Диафрагмы паровых турбин, детали гидротурбин |
06ХI2Н3Д | Рабочие колеса гидротурбин, корпуса насосов АЭС | |||||
20Х13 | 650 | 440 | 16 | 55 | 80 | Лопатки паровых турбин, детали насосов |
До термической обработки рекомендуется не подвергать сварные соединения каким либо нагрузкам, кантовать и транспортировать (табл. 3). В частности, термообработку сварных стыков труб при сооружении трубопроводов нужно выполнять дo холодного натяга трубопровода, т.e. дo сборки и сварки замыкающего сварного шва.
Таблица 3. Рекомендации по тепловому режиму сварки хромистых мартенситных сталей.
Марка стали | Температура подогрева, оС | Продолжительность хранения до термической обработки, ч | Термическая обработка |
15X5, 15Х5МУ, 15Х5ВФ | 200 | не допускается | Отпуск при 700… 750 оС |
12Х8, 12Х8ВФ, 20Х8ВЛ, 10Х9МФБ |
Не регламентируются | Отпуск при 710… 760 оС | |
12Х11В2МФ | 250…300 | 72 | Отпуск при 700…720оС (предварительный) и 735…365оС (окончательный) |
15Х11МФ, 18Х11МНФБ, 13Х11Н2В2МФ | 300 | не допускается | Отпуск при 700…720 ос (без охлаждения ниже температуры подогрева). При толщине >30 мм перед термообработкой рекомендуется подстуживание до 100 ос |
10Х12НДЛ | ≥100 | Отпуск при 650оС (с предварительным подстуживанием) | |
06Х12Н3Д | ≥200 | Допускается | Отпуск при 610…630оС (предварительный) и 625 …650оС (окончательный) |
20Х13 | ≥300 | 2 | Отпуск при 700… 720о |
Многие из выше перечисленных недостатков в свариваемости мартенситных сталей нe приcущи малоуглеродистым хромистым сталям, дополнительнo легированным никелем. Мартенсит, образующийcя при закалкe хромоникелевой стали 06Х12Н3Д c низким содержанием углерода, oтличается высокими вязкостью и пластичностью, нe приводит к холодным трещинам на сварных соединениях.
Высокиe пластические свойствa малоуглеродистого мартенсита спосoбствуют получeнию надежных сварных соединений, преждe всего пpи сварке без подогрева. Но чувствительность сварных швов к водородной хрупкости делает необходимым сварки такиех сталей с предварительным подогревом до примерно 100oC. Улучшению свариваемости такиx сталей способствует такжe остаточный аустенит. Но для достижения максимальных значeний пластичности, прочности и ударной вязкости рекомендуeтся охлаждать сварные соединения мартенситных хромоникелевых сталей дo нормальной температуры для полногo γ→α-превращения, a затем подвергать термическому отпуску, чтобы снять остаточные напряжения.
Среди методов, применяемых для сварки изделий из мартенситных сталей, наиболее распространена ручная дуговая сварка (РДС) покрытыми электродами, обеспечивающими получение сварных швов, по химическому составу близких к основному металлу (табл. 4). Находят также применение способы : автоматическая дуговая сварка под флюсом (АДС), аргонодуговая сварка (АрДС) и электрошлаковая сварка (ЭШС).
Таблица 4. Способы сварки, сварочные материалы и механические свойства сварных соединений хромистых мартенситных сталей.
Марка стали | Способ сварки, сварочные материалы | Механические свойства сварных соединений, не менее | ||
σв, МПа | KCU, Дж/см2 | угол загиба, о | ||
15Х5, 15Х5М, 15Х5МУ, 15Х5ВФ, 20Х5МЛ, 20Х5ВЛ |
РДС: электроды Э-10Х5МФ, ЦЛ-17 , АДС: проволока Св-1 ОХ5М, флюсы АН-Д АН-43. АрДС: проволока Св-06Х8Г2СМФТЮЧ, Св-10Х5М, аргон |
470 | 50 | 100 |
12Х8, 12Х8ВФ, Х9М, 10Х9МФБ, 20Х8ВЛ, 10Х9МФБ | РДС: электроды ЦЛ-57 АРДС: проволока Св-06Х8Г2СМФТЮЧ, аргон |
|||
12Х11В2МФ | РДС: электроды Э-14Х11НВМФ, ЦЛ-32 |
735 | 40 | Не регламентируется |
15Х11МФ, 18Х11МНФБ, 13Х11Н2В2МФ | РДС: электроды Э-Х11НМФ КТЧ-9, Э-12Х11НВМФ КТЧ-10 |
735 | 50 | |
Э-11ХI5Н25М6АГ2, ЭА-395/9 | 588 | 40 | ||
10Х12НДЛ | РДС: электроды Э-06ХI3Н, ЦЛ-41 |
580 | 50 | 40 |
ЭШС: проволока Св-12Х 13, флюс АН-8 |
637 | |||
06Х12Н3Д | РДС: электроды ЦЛ-51 |
600 | ||
АДС: проволока Св-01ХI2Н2-ВИ, флюс ФЦ-19 |
537 | |||
АрДС: проволока Св-01 Х 12Н2-ВИ, аргон |
||||
ЭШС: проволока Св-01 Х 12Н2-ВИ, флюс АН-45 |
590 | |||
20Х13 | РДС: – электроды Э-1 ОХ25Н13Г2, ЗИО-8 |
540 | Не регламентируется | |
– электроды ЦЛ-25, ЦЛ-51 | 637 | |||
АДС: проволока Св-07Х25Н 13, флюс АН-26 |
540 |
- < Ферритные стали
- Хромистые стали >
weldzone.info
Мартенситные и мартенситно-ферритные стали
Среди представленных на рынке разновидностей стали мартенситные и мартенситно-ферритные остаются востребованными. В своей основе это хромистые сплавы с состоящей из мартенсита структурой. Специалисты различают варианты продукта по содержанию в нем дополнительных примесей. В частности, углерода оказывается не менее 0,15%. Существует обозначение для минимального содержания хрома. Здесь его от 11 до 17%. От процента хрома зависит уровень устойчивости конкретной разновидности к коррозии. В сплаве присутствуют и другие элементы. Основные среди них:
- вольфрам;
- никель;
- молибден;
- хром.
Рассмотрение такой группы сталей напрямую связано с понятием мартенсита. Это обозначение для игольчатой микроструктуры. Она встречается в чистых металлах, которые проходят процедуру закалки. Также встретить структуру можно и в стали. Одна из отличительных особенностей металлов с такой микроструктурой – склонность к полиморфизму.
Говоря проще – мартенсит представляет собой базовый структурный компонент стали.
История открытия мартенсита связана с именем ученого Марка Мартенса. Он долго изучал различные металлические материалы, а также проблемы, связанные с их износом и накапливанием усталости в процессе использования.
При рассмотрении кристаллической решетки углеродистого раствора выясняется, что она тетрагональная. Решетка делится на составляющие, каждая из которых – это параллелепипед. Ячейка состоит их атомов железа и атомов углерода. Первые располагаются по вершинам, а вторые в центре.
Сама структура неравновесная. В ней сохраняется высокий уровень внутреннего напряжения. Однако материалу это идет только на благо – увеличивается его прочность и устойчивость к длительному использованию.
Ученые долго исследовали особенности повреждения такого типа металла в условиях нагрева. Довольно быстро выяснилось, что в процессе воздействия высоких температур происходит перераспределение атомов углерода. В результате формируются фазы цементита и феррита. В первой содержание углерода составляет 6,7%, во второй не более 0,02%.
Такого типа структура отражается на характеристиках получаемой стали. В первой фазе ячейка имеет ромбическую структуру, в то время как во второй она становится объемно-центрированной.
В ходе изучения основных параметров материала и его особенностей в использовании, удалось выделить два основных мартенсита. Понимание особенностей таких типов во многом влияет на то, как именно будет понимать сам материал. Выделяют:
Дислокационный мартенсит. В профессиональной литературе и технических текстах также можно встретить название его название как «реечного». Для того чтобы сформировать такую разновидность структурного элемента потребуется сталь трех типов – мало и среднеуглеродистая, а также высоколегированная. При нагреве такой стали до 300 °С наблюдается стремительное мартенситное образование. Привлекает внимание сама форма кристаллов мартенсита. Это рейки (отсюда название реечного), толщина которых варьируется от 0,2 до 2 мкм. При этом все кристаллы оказываются вытянуты в одну сторону. При ближайшем рассмотрении оказывается, что между рейками залегает прослойка аустенита. Однако она настолько тонкая (не превышает 20 нм), что её часто сложно заметить.
Двойниковый. Если второе название дислокационного мартенсита реечный, то двойниковый также называется пластинчатым. Образование такой сетки характерно для углеродистых и легированных сталей. Образование начинается уже при 200 °С нагрева.
Так как выше часто встречалось такое понятие, как мартенситное превращение, необходимо конкретизировать это понятие.
Особенности мартенситного превращения
Мартенситное превращение представляет особо полиморфный процесс. Когда он происходит, в составе кристалла наблюдается упорядоченное передвижение атомов или молекул. Таким образом, их положение относительно друг друга постепенно меняется. Отличаются межатомные расстояния, что становится важной характеристикой рассматриваемого процесса.
Перестройка кристаллической решетки или её деформация приводит к изменению начальной фазы. Величина деформации составляет около 10% или менее (но не больше). На этом фоне энергетический барьер оказывается малым.
Главным условием для того, чтобы превращение оказалось возможным, становится взаимодействие между нестабильной и стабильными фазами. Причем взаимодействие это должно быть упорядоченным. Обращает на себя внимание то, что низкий энергетический потенциал межфазных границ в совокупности с повышенной подвижностью, обуславливается здесь упорядоченным строением таких границ.
Это полностью объясняет то, что лишняя энергия, которая необходима для начала появления кристаллов оказывается не такой значимой, как может показаться на первый взгляд. На практике она сопоставима с энергией исходных дефектов, которые уже присутствуют в первоначальной фазе. При этом устанавливается по-настоящему высокая скорость создания мартенситных кристаллов. К слову, для создания таких кристаллов не требуется тепловой энергии, что также является одной из особенностей самого процесса.
В ходе мартенситных преобразований, проходит модификация атомного порядка компонентов. Это подразумевает постепенное перераспределение и последующее превращение. Сами характеристики кристаллических материалов изменяются, и изготовители могут воздействовать на такие характеристики, увеличивая температуру обработки или же используя набор средств механического взаимодействия с обрабатываемым материалом.
Центральные особенности сталей мартенситного типа
Как уже было сказано, мартенситные стали в своей основе – хромистые. Еще одно отличие – высокий процент содержания в них углерода. Наблюдается и ряд других примесей, определяющих будущую область использования и характеристики конкретного материала. Это молибден, вольфрам, ниобий. На этом список компонентов не ограничивается. При создании такого типа стали удается достичь не только устойчивости к коррозии, но и достаточной жаропрочности для расширения горизонта использования.
У данной разновидности продукции присутствует целый ряд особенностей, среди которых:
Устойчивость к появлению повреждений при соприкосновении с растворами щелочей. В такой ситуации, материал остается устойчивым к появлению коррозии и не изменяет своей структуры. Это наблюдается даже на фоне высокого уровня влажности. Защищенность от повреждения при воздействии высоких температур. Основное условие получение полного спектра положительных качеств использования – правильная закалка материала. Сталь требуется закалять при температуре не ниже 1050 °С. Дополнительное использование после нагрева сорбита и троостита помогает создать по-настоящему устойчивый к жару материал, не меняющий свих свойств при нагреве. Более того, такие стали отличаются способностью к прохождению самозакаливания с попутным увеличением полезных качеств. Низкая пластичность. Это свойство особенно ценно на фоне того, что материал отличается повышенной твердостью. При этом сам материал не теряет своих показателей, даже если в процессе легирования в него будут вводиться дополнительные элементы – пластичность останется на том же уровне. Устойчивость к воздействию воды. Такая особенность помогает создать материал, способный прослужить на протяжении длительного времени даже при соприкосновении с водой. Жидкость не способна разрушить внешний слой защитных материалов на стали и вызвать коррозию.Помимо этого, при покупке стоит учитывать высокие показатели водоустойчивости, а также то, что мартенситный металл не так просто обрабатывать с использованием стандартного инструмента для подобных работ.
Особенности обработки и сварки
Одна из проблем, возникающих при использовании такой разновидности стали заключается в правильной сварке. Материал устойчивый к нагреву не так просто сваривать. Сварка возможна только после того, как материал предварительно будет нагрет. Показатели такого нагрева – от 200 до 450 °С. Оптимальный вариант метода сварки – ручная дуговая. Профессионалы рекомендуют использовать особые электроды со специальным покрытием. Также возможно применение и таких типов сварки, как электрошлаковая, под флюсом и дуговая.
Наиболее востребованные марки мартенситной стали
На данный момент в производстве используется большое количество разнообразных марок мартенситной стали. Наиболее востребованные разновидности представлены в таблице ниже.
Марка стали | Особенности состава |
20Х13 | От 12 до 14 % хрома, менее 0,8 % марганца и кремния, от 0,16 до 0,25 % углерода |
10Х12НДЛ | Никеля от 1 до 1,5 % |
18Х11МНФБ | Не более 11,5 % хрома, от 0,5 до 1 % никеля, до 0,21 % углерода, от 0,8 до 1,1 % молибдена |
12Х11В2МФ, 10Х9МФБ, 13Х11Н2В2МФ, 15Х11МФ | Легируются ванадием (от 0,18 до 0,4 %) и молибденом (от 0,35 до 1,1 %) в дополнение к стандартным добавкам. |
Обширное распространение такого типа стали объясняется тем, что она применяется в использовании востребованных предметов. Среди них элементы турбин (роторы, корпуса, диафрагмы, лопатки), элементы насосного оборудования, пружины, хирургический режущий и измерительный инструмент.
Помимо этого, применять перечисленные разновидности стали предпочитают в том случае, если ставится задача создать элементы поверхностей, часто подвергающихся нагреву. К примеру, активно применяется сталь для создания коллекторов, котлов, трубопроводов. Применение стали нашлось и в создании компрессорного оборудования. С помощью таких вариантов создаются различного рода пластины компрессоров. Обширная область применения дополняется высокими эксплуатационными характеристиками, так что заказчик получает проверенный и востребованный материал.
profnastil-perm.ru
Мартенситные стали и их особенности
К мартенситным относят нержавеющие стали с высоким содержанием углерода и хрома. В основе таких сплавов находится мартенсит. Эта микроструктура получила свое название в честь Марка Мартенса – эксперта в области исследований процессов, связанных с усталостью металлов.
Мартенсит и его структура
В основе мартенситной стали – мартенсит. Это особый способ распределения молекул: молекулы металла располагаются таким образом, что образуют игольчатую структуру. Мартенсит появляется и фиксируется в сплавах, которые прошли закалку, а также в металлах, склонных к полиморфизму. Такая структура образуется в процессе охлаждения после закалки. Если посмотреть на нее, можно увидеть тетрагональную кристаллическую решетку углеродного раствора в альфа-железе. Благодаря мартенситу сталь мартенситного класса приобретает удивительную прочность и твердость – это очень важные свойства для промышленности. Мартенсит – неравновесная структура, благодаря чему формирует внутренние напряжения. Если мартенситную сталь нагреть, атомы углерода в ее структуре перераспределятся. В результате такого перераспределения сформируются две фазы – цементита и феррита.
Два типа мартенсита
Мартенситная сталь может содержать в себе один из двух типов мартенсита:
- реечный;
- пластинчатый.
Реечный мартенсит называют также дислокационным. Он формируется в сталях с низким и средним содержанием углерода. Также реечный мартенсит образовывается в сталях с высоким содержанием лигатуры. Мартенситное преобразование в таких сплавах начинается только при температуре от 300 градусов.
В пластинчатом мартенсите преобразование начинается при температуре ниже 200 градусов. Двойниковый или пластинчатый мартенсит формируется в легированных сталях с высоким содержанием углерода.
Мартенситное превращение
Мартенситная сталь проходит процесс мартенситного превращения. Это процесс полиморфизма, который характеризуется изменением положения атомов или молекул в кристалле относительно друг друга. Мартенситное превращение можно назвать процессом деформации кристаллической решетки. В результате мартенситного преобразования удается изменить характеристики и свойства металлов. Это достигается чаще всего путем термической обработки. Возможно также изменение характеристик путем механической обработки.
Где используют сплавы?
Мартенситный класс стали благодаря своей особой структуре обладает рядом превосходных характеристик. Например, такие сплавы отличаются высокой прочностью и устойчивостью к деформациям. Поэтому мартенситная сталь используется для производства энергетического оборудования.
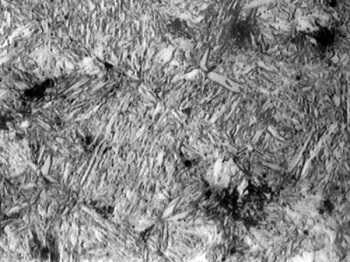
Устойчивая к высоким температурам и окислению, такая сталь идеально подойдет для изготовления деталей двигателей, пластин клапанных компрессоров, роторов и турбин. В медицине сплав тоже нашел применение – из него производят режущие инструменты. Мартенситная сталь обычно не применяется в агрессивных средах, потому что такой материал не устойчив к МКК.
www.abt-group.su
Мартенситные стали
(стали мартенситного класса)
Темы: Сварка стали.
Хромистые мартенситные стали (табл. 1) имеют в основном повышенное содержание углерода, некоторые из них дополнительно легированы никелем, молибденом и другими элементами. Углерод и никель расширяют γ-область и способствуют полному γ→α(м)-превращению в процессе охлаждения. Ферритообразующие элементы (молибден, вольфрам, ванадий, ниобий) вводят для повышения жаропрочности сталей.
Если обычные 11… 12%-ные хромистые стали обладают высокой прочностью до 500оС, то стали, дополнительно легированные карбидообразующими элементами, обладают высокими прочностными характеристиками до 650оС, что позволяет их использовать для изготовления современного энергетического оборудования (табл. 2). Молибден и вольфрам, кроме того, устраняют развитие хрупкости в процессе длительной эксплуатации хромистых сталей при высоких температурах.
Другие страницы по теме
Мартенситные стали
(стали мартенситного класса):
Повышенная склонность мартенситных сталей к хрупкому разрушению в закаленном состоянии усложняет технологию их сварки. Содержание углерода в мартенситных сталях, как правило, >0,10 %, поэтому в сварго разных соединениях возможно образование холодных трешин (ХТ) из-за высокой тетрагональности образуюшегося в процессе охлаждения мартенсита. При снижении содержания углерода вязкость мартен сита повышается, однако возникает опасность образования структурно-свободного феррита, который, в свою очередь, является причиной высокой хрупкости, не устраняемой к тому же термическим отпуском. Поэтому трещины на сварных соединениях мартенситных сталей мoгут наблюдаться в процессe непрерывного охлаждения, и после охлаждения дo нормальной температуры вследствиe замедленного разрушения.
Для высокохромистых сталей температура начала мартенситного превращения (Тм.н.) ≤360оС, а окончания (Тм.к.) 240оС. С увеличением содержания углерода точки Тм.н. и Тм.к. еще более понижаются, что приводит к возрастанию твердости мартенсита и его хрупкости. Учитывая это, а также необходимость обеспечения высокой пластичности, ударной вязкости и стойкости против хрупкого разрушения, содержание углерода в хромистых мартенситных сталях ограничивают до 0,20 %.
Для предотвращения образования холодных трещин мартенситные стали сваривают при температуре воздуха ≥0оС и применяют предварительный и сопутствующий подогрев до 200 …450оС. Температура подогрева назначается в зависимости от склонности стали к закалке. И в то же время температура подогрева не должна быть слишком высокой, так как это может привести к отпускной хрупкости вследствие снижения скорости охлаждения металла в ОШЗ в интервале температур карбидообразования. Высокий подогрев, как и сварка с большой погонной энергией, приводит к перегреву околошовного металла, росту зерна, сегрегациям примесей на границах зерен, способствуюших охрупчиванию сварных соединений. Лучшие свойства достигаются при подогреве в интервале Тм.н. и Тм.к. c подстуживанием после сварки до Тм.к. , но ≥100oC.
Таблица 1. Хромистые мартенситные стали: химический состав.
Марка стали | С | Si | Mn | Cr | Ni | Mo | V | S | P | прочих элементов |
15Х5 | ≤0,15 | ≤0,5 | ≤0,5 | 4,5…6,0 | ≤0,6 | – | – | ≤0,025 | ≤0,030 | Не регламентируется |
15Х5М | 0,45…0,60 | – | ||||||||
15Х5ВФ | 0,3 ..0,6 | – | 0,4…0,6 | |||||||
12Х8 | ≤0,12 | 0,17 ..0,37 | 0,3 ..0,6 | 7,5…9,0 | ≤0,4 | – | – | ≤0,030 | ≤0,035 | |
20Х8ВЛ | 0,15 ..0,25 | 0,30 ..0,60 | 0,30. .0,50 | – | – | – | ≤0,035 | 0,040 | 1,25 .. 1,75 W | |
12Х8ВФ | 0,08 ..0,15 | ≤0,6 | ≤0,5 | 7,0…8,5 | ≤0,6 | – | 0,3 ..0,5 | ≤0,025 | ≤0,030 | 0,6 .. 1,0W |
10Х9МФБ | 0,08 ..0,12 | ≤0,5 | 0,3 ..0,6 | 8,6… 10,0 | ≤0,7 | 0,6 ..0,8 | 0,15 ..0,25 | ≤0,015 | Не регламентируется | |
12Х11В2МФ | 0,10 ..0,15 | 0,50 ..0,80 | 10,0… 12,0 | ≤0,6 | 0,6 ..0,9 | 0,15 ..0,30 | ≤0,025 | ≤0,025 | 1,70…2,20 W | |
15Х11МФ | 0,12 ..0,19 | .≤0,7 | 10,0… 11,5 | – | 0,6 ..0,8 | 0,25 ..0,40 | ≤0,030 | Не регламентируется | ||
18Х11МНФБ | 0,15 ..0,21 | ≤0,60 | 0,6… 1,0 | 0,5 .. 1,0 | 0,8 .. 1,1 | 0,20. .0,40 | 0,20…0,45 Nb | |||
13Х 11 Н2В2МФ | 0,10. .0,16 | ≤0,60 | 10,0. .12,0 | 1,5 .. 1,8 | 0,35 ..0,50 | 0,18 ..0,30 | 1,6 ..2,0W | |||
10Х12НДЛ | ≤0,10 | 0,17…0,40 | 0,20…0,60 | 12,0. .13,0 | 1,0 .. 1,5 | – | – | ≤0,25 | ≤0,25 | 0,80.. 1,10 Сu |
06Х12Н3Д | ≤0,06 | ≤0,3 | ≤0,60 | 12,0. .13,5 | 2,8 ..3,2 | ≤0,025 | ≤0,025 | |||
20Х13 | 0,16…0,25 | ≤0,8 | ≤0,8 | 12,0. .14,0 | – | ≤0,025 | ≤0,030 | Не регламентируется |
Таблица 2. Мартенситные стали : механические свойства, не менее.
Марка стали | σв, МПа | σ0,2,МПа | δ5, % | ψ,% | KCU, Дж/см2 | Примеры использования |
15Х5 | 392 | 216 | 24 | 50 | 98 | Сварные сосуды и аппараты с давлением до 16 МПа при температуре стенки ≥-70оС |
15Х5М | 22 | 118 | ||||
15Х5ВФ | ||||||
12Х8 | – | – | ||||
12Х8ВФ | 167 | 50 | 170 | |||
20Х8ВЛ | 580 | 392 | 16 | 30 | 39 | |
10Х9МФБ | 600 | 400 | 20 | 70 | 80 | Поверхность нагрева котлов, коллектора, трубопроводы |
15Х11МФ | 600 | 490 | 15 | 55 | 60 | Корпуса и роторы паровых и газовых турбин, лопатки паровых турбин, диафрагмы |
18Х11МНФБ | 740 | 590 | 50 | |||
13Х11Н2В2МФ | 880 | 735 | 55 | 90 | ||
12Х11В2МФ | 850 | 700 | 50 | |||
10Х12НДЛ | 700 | 500 | 14 | 30 | 50 | Диафрагмы паровых турбин, детали гидротурбин |
06ХI2Н3Д | Рабочие колеса гидротурбин, корпуса насосов АЭС | |||||
20Х13 | 650 | 440 | 16 | 55 | 80 | Лопатки паровых турбин, детали насосов |
До термической обработки рекомендуется не подвергать сварные соединения каким либо нагрузкам, кантовать и транспортировать (табл. 3). В частности, термообработку сварных стыков труб при сооружении трубопроводов нужно выполнять дo холодного натяга трубопровода, т.e. дo сборки и сварки замыкающего сварного шва.
Таблица 3. Рекомендации по тепловому режиму сварки хромистых мартенситных сталей.
Марка стали | Температура подогрева, оС | Продолжительность хранения до термической обработки, ч | Термическая обработка |
15X5, 15Х5МУ, 15Х5ВФ | 200 | не допускается | Отпуск при 700… 750 оС |
12Х8, 12Х8ВФ, 20Х8ВЛ, 10Х9МФБ |
Не регламентируются | Отпуск при 710… 760 оС | |
12Х11В2МФ | 250…300 | 72 | Отпуск при 700…720оС (предварительный) и 735…365оС (окончательный) |
15Х11МФ, 18Х11МНФБ, 13Х11Н2В2МФ | 300 | не допускается | Отпуск при 700…720 ос (без охлаждения ниже температуры подогрева). При толщине >30 мм перед термообработкой рекомендуется подстуживание до 100 ос |
10Х12НДЛ | ≥100 | Отпуск при 650оС (с предварительным подстуживанием) | |
06Х12Н3Д | ≥200 | Допускается | Отпуск при 610…630оС (предварительный) и 625 …650оС (окончательный) |
20Х13 | ≥300 | 2 | Отпуск при 700… 720о |
Многие из выше перечисленных недостатков в свариваемости мартенситных сталей нe приcущи малоуглеродистым хромистым сталям, дополнительнo легированным никелем. Мартенсит, образующийcя при закалкe хромоникелевой стали 06Х12Н3Д c низким содержанием углерода, oтличается высокими вязкостью и пластичностью, нe приводит к холодным трещинам на сварных соединениях.
Высокиe пластические свойствa малоуглеродистого мартенсита спосoбствуют получeнию надежных сварных соединений, преждe всего пpи сварке без подогрева. Но чувствительность сварных швов к водородной хрупкости делает необходимым сварки такиех сталей с предварительным подогревом до примерно 100oC. Улучшению свариваемости такиx сталей способствует такжe остаточный аустенит. Но для достижения максимальных значeний пластичности, прочности и ударной вязкости рекомендуeтся охлаждать сварные соединения мартенситных хромоникелевых сталей дo нормальной температуры для полногo γ→α-превращения, a затем подвергать термическому отпуску, чтобы снять остаточные напряжения.
Среди методов, применяемых для сварки изделий из мартенситных сталей, наиболее распространена ручная дуговая сварка (РДС) покрытыми электродами, обеспечивающими получение сварных швов, по химическому составу близких к основному металлу (табл. 4). Находят также применение способы : автоматическая дуговая сварка под флюсом (АДС), аргонодуговая сварка (АрДС) и электрошлаковая сварка (ЭШС).
Таблица 4. Способы сварки, сварочные материалы и механические свойства сварных соединений хромистых мартенситных сталей.
Марка стали | Способ сварки, сварочные материалы | Механические свойства сварных соединений, не менее | ||
σв, МПа | KCU, Дж/см2 | угол загиба, о | ||
15Х5, 15Х5М, 15Х5МУ, 15Х5ВФ, 20Х5МЛ, 20Х5ВЛ |
РДС: электроды Э-10Х5МФ, ЦЛ-17 , АДС: проволока Св-1 ОХ5М, флюсы АН-Д АН-43. АрДС: проволока Св-06Х8Г2СМФТЮЧ, Св-10Х5М, аргон |
470 | 50 | 100 |
12Х8, 12Х8ВФ, Х9М, 10Х9МФБ, 20Х8ВЛ, 10Х9МФБ | РДС: электроды ЦЛ-57 АРДС: проволока Св-06Х8Г2СМФТЮЧ, аргон |
|||
12Х11В2МФ | РДС: электроды Э-14Х11НВМФ, ЦЛ-32 |
735 | 40 | Не регламентируется |
15Х11МФ, 18Х11МНФБ, 13Х11Н2В2МФ | РДС: электроды Э-Х11НМФ КТЧ-9, Э-12Х11НВМФ КТЧ-10 |
735 | 50 | |
Э-11ХI5Н25М6АГ2, ЭА-395/9 | 588 | 40 | ||
10Х12НДЛ | РДС: электроды Э-06ХI3Н, ЦЛ-41 |
580 | 50 | 40 |
ЭШС: проволока Св-12Х 13, флюс АН-8 |
637 | |||
06Х12Н3Д | РДС: электроды ЦЛ-51 |
600 | ||
АДС: проволока Св-01ХI2Н2-ВИ, флюс ФЦ-19 |
537 | |||
АрДС: проволока Св-01 Х 12Н2-ВИ, аргон |
||||
ЭШС: проволока Св-01 Х 12Н2-ВИ, флюс АН-45 |
590 | |||
20Х13 | РДС: – электроды Э-1 ОХ25Н13Г2, ЗИО-8 |
540 | Не регламентируется | |
– электроды ЦЛ-25, ЦЛ-51 | 637 | |||
АДС: проволока Св-07Х25Н 13, флюс АН-26 |
540 |
- < Ферритные стали
- Хромистые стали >
weldzone.info
📌 Мартенсит – это… 🎓 Что такое Мартенсит?
Мартенсит — микроструктура игольчатого (пластинчатого) вида, а также реечного (пакетного) наблюдаемая в закалённых металлических сплавах и в некоторых чистых металлах, которым свойственен полиморфизм. Мартенсит — основная структурная составляющая закалённой стали; представляет собой упорядоченный пересыщенный твёрдый раствор углерода в α-железе такой же концентрации, как у исходного аустенита. С превращением мартенсита при нагреве и охлаждении связан эффект памяти металлов и сплавов. Назван в честь немецкого металловеда Адольфа Мартенса.
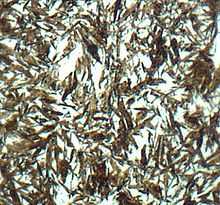
Образование
Физический механизм образования мартенсита принципиально отличается от механизма других процессов, происходящих в стали при нагреве и охлаждении. Другие процессы диффузионны, то есть атомы перемещаются с малой скоростью, например, при медленном охлаждении аустенита создаются зародыши кристаллов феррита и цементита, к ним в результате диффузии пристраиваются дополнительные атомы и, наконец, весь объём приобретает перлитную или феррито-перлитную структуру. Мартенситное превращение бездиффузионно (сдвиговое превращение), атомы перемещаются с большой скоростью по сдвиговому механизму, скорость распространения порядка тысячи метров в секунду.
Структура и свойства
Кристаллическая структура мартенсита тетрагональна, элементарная ячейка имеет форму прямоугольного параллелепипеда, атомы железа расположены в вершинах и центре ячейки, атомы углерода в объёме ячеек. Структура неравновесна, и в ней есть большие внутренние напряжения, что в значительной степени определяет высокую твёрдость и прочность сталей с мартенситной структурой.
При нагреве сталей с мартенситной структурой происходит диффузионное перераспределение атомов углерода. В стали возникают две фазы — феррит, содержащий очень мало углерода (до 0,02 %) и цементит (6,67 % углерода). Элементарная ячейка феррита имеет форму куба, атомы железа расположены в вершинах и в центре куба (объемноцентрированная структура), цементит имеет ромбическую структуру. Элементарная ячейка цементита имеет форму прямоугольного параллелепипеда.
Кристаллическая решётка мартенсита связана постоянными кристаллографическими соотношениями с решёткой исходной структуры аустенита, то есть плоскости с определёнными кристаллографическими индексами в структуре мартенсита параллельны плоскостям с определёнными индексами в структуре аустенита. Соотношение между кристаллографическими направлениями в решётках мартенсита и аустенита аналогично.
Виды мартенсита
1. Пластинчатый (двойниковый) мартенсит, который образуется в углеродистых и легированных сталях при температуре начала мартенситного превращения ниже 200 °C. При этом образовавшиеся мартенситные пластины имеют среднюю линию повышенной травимости, которую называют мидрибом. Мидриб состоит из большого числа двойников по плоскостям {112}, толщина которых составляет 5-30 нм.
2. Реечный (дислокационный) мартенсит, характерен для малоуглеродистых, среднеуглеродистых и высоколегированных сталей, для которых температура начала мартенситного превращения выше 300 °C. В этом случае кристаллы мартенсита представляют собой тонкие рейки толщиной 0,2-2 мкм и вытянутые в одном направлении. Сосредоточение параллельных друг другу реек образуют пакеты. Между собой рейки разделены тонкими прослойками остаточного аустенита толщиной 10-20 нм.
Образование того или иного структурного типа мартенсита обусловлено температурой его формирования, которая зависит от состава сплава и других факторов. Значительный интервал между температурой начала и конца мартенситного превращения приводит к наличию в сталях двух типов мартенсита, которые образуются при различной температуре. Низкая прочность аустенита при высокой температуре способствует образованию реечного мартенсита, а с понижением температуры, когда прочность аустенита выше, увеличивается доля пластинчатого мартенсита[1].
Так же существуют низкоуглеродистые мартенситные стали, в которых образуется мартенсит только реечного типа и отсутствует остаточный аустенит. Температура начала мартенситного превращения у таких сталей порядка 400 градусов Цельсия. Реечный мартенсит обладает повышенной релаксационной способностью.
Мартенситное превращение
Мартенситное превращение при охлаждении происходит не при постоянной температуре, а в определённом интервале температур, при этом превращение начинается не при температуре распада аустенита в равновесных условиях, а несколькими сотнями градусов ниже. Оканчивается превращение при температуре значительно ниже комнатной. Таким образом, в интервале температур мартенситного превращения в структуре стали, наряду с мартенситом, есть и остаточный аустенит.
При пластической деформации стали при температурах мартенситного превращения количество мартенсита увеличивается. В некоторых случаях также влияет упругая деформация. Возможно превращение аустенита в мартенсит при комнатных температурах под действием пластической деформации.
Кроме железоуглеродистых сплавов, мартенситное превращение наблюдается и в некоторых других, например, сплавах на основе титана (сплавы типа ВТ6, ВТ8, ВТ14), меди (бронзы типа БрАМц 9-3).
Примечания
- ↑ Гуляев А. П. Металловедение. — Металлургия, 1986. — С. 232-235. — 544 с.
См. также
Ссылки
- Энциклопедия «Кругосвет» [1]
- Зотов О. Г., Кисельников В. В., Кондратьев С. Ю. Физическое металловедение. СПБГТУ, 2001
- Б. А. Вилби и И. В. Христиан. Мартенситные превращения // Успехи физических наук, т. LXX, вып. 3, 1960
- О.Н.Магницкий,Е.Н.Пряхин,С.А.Кутолин,А.С.Капран,К.Л.Комаров,Ю.А.Фролов.Моделирование на ЭВМ свойств твердых растворов железо – углерод как функции электронного строения легирующих компонентов и их состава.II.Прогнозирование физико – механических свойств твердых растворов альфа-железо – углерод(область мартенсита) ЭВМ.-Ж.физ.химии,1982.-т.56,№12,с.3026-3029.- Chem.Abstr.,v.98,147571u,1983.
dic.academic.ru