Механизированная наплавка: технология для различных деталей, режимы, особенности выполнения
alexxlab | 26.10.1988 | 0 | Разное
технология для различных деталей, режимы, особенности выполнения
21.07.2021
Частично механизированная сварка (наплавка) – это простой метод выполнения сварочных работ с высокой эффективностью. Да и затраты он несет небольшие. Вот почему способ стал популярен одновременно и у профессионалов на крупных производствах, и у частников, занимающихся подсобными работами. Да и даже новички, которым необходимо выполнить единичное действие у себя на даче, в загородном доме или на собственном складе, чаще всего используют именно такую методику. Ведь она выгодно отличается быстрым усвоением, легкой реализацией. И что еще важнее, является вполне экономичным выбором.
В этом обзоре мы конкретно разберемся в сути, видах техники, различных сопутствующих приемах, необходимом оборудовании. А также выявим все ключевые преимущества и недостатки подобной системы.
Что называют технологией частично механизированной сварки наплавки
Для начала разберемся со смежными понятиями. Ручной вариант – это работа, подразумевающая участие человека на всех этапах процесса. Он самостоятельно погружает необходимую конструкцию или деталь, производит плавление, сменяет электроды. Участие каких-то программ не подразумевается. В автоматическом варианте же деятельность сварщика отсутствует по определению. Его роль заключается лишь в расположении объекта на крепежах. То есть, это может выполнить и непрофессионал.
Полуавтоматический режим совмещает две эти функции. Погрузка и размещение осуществляется самостоятельно, так же как и движение сварочным аппаратом. Но подача электродов уже становится автоматической. Это легче, ведь не нужно переживать за корректность размещения проволоки, следить за настройками. Определять уровень газа, подачу электроэнергии. Все сделает «умное» оборудование за работника.
Благодаря этому для «любительской» работы обычно приобретают такое оборудование. Чтобы минимизировать возможность ошибки. А как известно, в этой сфере она может стоить дорого.
Особенности технологии частично механизированной сварки наплавки
Пройдемся по всему алгоритму детально.
- • В первую очередь происходит обработка рабочей поверхности. Необходимо устранить возможные дефекты, возникшие при прокате металла. Это не самая редкая ситуация, брак поступает часто. Поэтому лучше перестраховаться. Для исправления деформации возможно применить плавление.
- • Наносится разметка на сталь. Определяются участки, где будет проходить резка, выбирается режим работы.
- • Резка объекта. После нее нужно в обязательном порядке зачистить кромки. Дуговая сварка предполагает ровную поверхность. Соответственно, кромки подрезаются, если дефекты слишком сильные. А дальше для выравнивания обрабатываются абразивом. Нужен инструмент высокой твердости, иначе металл он просто не возьмет.
- • Следующим этапом нужно выбрать конкретный режим.
Для этого определяется сила и полярность тока, на котором будет работать оборудование. Важно учесть температуру в окружающей среде. В помещении это сделать просто. Она кардинальным образом изменяться не будет. А вот на свежем воздухе есть нюансы. Резкое похолодание – это редкость. А вот неожиданно вышедшее солнце из-за туч прямыми лучами способно повысить температуру на десять и выше градусов.
- • Выбираем число подходов, сразу строго фиксируем эту цифру и следуем ей. А также определяем пространственное положение шва.
- • Теперь необходимо заземлить деталь, которую будем плавить.
- • Только после этого подключаем электрический ток. Аппарат при соприкосновении с объектом начнет пропускать электричество. А значит, и кромка детали, и сам электрод ввиду сильного термического фактора будут плавиться. В итоге, обе масса смешиваются в единое целое. После плавления шлак начинает стремиться вверх, выступая наружу, создавая защитную пленку. Остается лишь подождать остывания и затвердевания.
И новенький шов готов.
Также выполнение частично механизированной наплавки может происходить одним из двух способов. Левый вариант – это процесс, при котором сварочный аппарат передвигается слева направо, соответственно. Пруток же двигается параллельно перед горелкой. Двигать лучше всего под прямым углом ко шву, некоторыми зигзагами.
Второй вариант – правый. Перемещение оборудование происходит в обратную сторону. Пламя направляется на ванну с металлическим шлаком. В итоге по времени этот способ изрядно проигрывает. Ведь остывание шва становится куда более длительным процессом, он постоянно заново подогревается. Но фактически, это более качественный вариант. Он обуславливается более прочным соединением. Да и расход газа существенно сокращается. Так что можно говорить и о какой-то экономии.
Режимы
Отдельных строго регламентированных параметров нет. Существует масса ГОСТов под каждый конкретный тип работ и аппаратуру. Но общие методы можно выделить через некоторые аспекты. Один из них – энергия. Электрический ток – это главный двигатель процесса. А значит, его источник или блок обладает принципиальным значением. Сам узел подачи энергии может строиться на двух различных принципах. Первый – это трансформаторный. Это уже зарекомендованный стандарт, который сейчас становится морально устаревшим. Но, плюсы очевидны, трансформатор легко заменить или починить, если он выйдет из строя. То есть, преимуществом выступает примитивность.
Второй вариант – инертный преобразователь. Более прогрессивная модель, которая сейчас ставится почти на каждое оборудование для полуавтоматической сварки на рынке. Электрическая дуга в этом методе становится значительно более стабильной. Горение поддерживается постоянно, даже если питание начинает проседать. Таким образом, уменьшается возможность внешних факторов повлиять на качество работы. Кроме того, КПД тоже возрастает. При наименьших затратах энергии выдается стабильный поток, способный полностью обеспечить нужды сварщика.
Подключать же аппаратуру нужно к источнику с разным напряжением. Все зависит от параметров устройства. По традиции для любительских нужд приобретаются небольшие модели, работающие от сети в 220В. И с одной фазой. А вот если говорить про крупное производство, то там для повышения эффективности используются иные источники. И в большинстве случаев, трехфазные.
Если разбирать режимы частично механизированной наплавки, нельзя обойти своим вниманием такой вид, как сварка в среде защитных газов. Главный критерий – универсальность. Соединения практически любых металлов легко формируются этим методом. Да и процесс можно осуществлять не только в заводском помещении со специально выверенной температурой и газовой средой, но и на свежем воздухе.
Для реализации понадобится оборудование со съемным газовым баллоном. А также с двигателем, подающими механизмами и самой кассетой, в которой хранится проволока. В большей части аппаратов всего два механизма подачи, но если подразумевается серьезная нагрузка, логично приобрести более мощный тип. В нем роликов может быть четыре, шесть и даже больше.
Это простая и доступная технология. Но громоздкий газовый баллон иногда мешает работе, если подразумевается постоянное движение от объекта. Также стоит учесть, что благодаря невысокой цене газа, этот вид еще и экономичен.
Для работ повышенной сложности принято использовать иную технологию, под флюсом. Также идеально подходит для соединения легированной стали или алюминия, для сплавов железа и никеля. Хотя и в работе с обычными соединениями показывает отличный результат. Подходит для выполнения частично механизированной наплавки различных деталей медного типа на производстве.
Флюс – это порошкообразный материал, марганец в своей основе. Он подается вместе с электродом, поэтому при проходе электрического тока происходит плавление сразу двух металлов. Полученная смесь работает гораздо лучше и эффективнее. Порошок бывает плавленым и неплавленным. Последний – стандартный, стоит дешевле, но менее результативен. А первый – это материал после сильной термической обработки, иногда смесь с керамическим происхождением в форме крошки.
Во время работы эти гранулы активно плавятся. Смешиваются с остальным шлаком и попадают в сварочную ванночку. Но при этом флюс поднимается, создает на поверхности специальный защитный слой. Он полностью предохраняет от контакта с кислородной средой. А значит, полученный шов будет до остывания защищен. И получится более крепким и качественным. Затвердевший порошок превращается в наслоение. Удалить его можно без всяких проблем скребком с молотком или иным инструментом. После пары ударов слой трескается и разваливается. Примечательно то, что остатки допустимы к повторной процедуре. Покупать в следующий раз придется меньше флюса.
И провести очистку нужно в обязательном порядке. Ведь слой визуально скрывает под собой шов. И непонятно, получился ли он на запланированном уровне качестве. Или нуждается в доработке, переделке.
Оборудование
Главными аспектами, присущими полуавтоматической сварке, как мы уже говорили, является отсутствие необходимости ив подачи электрода. Менять его в держателе не нужно. «Умный» механизм все сделает самостоятельно.
Машинный вариант оборудования не предполагает наличие этого элемента. Там используется проволока, которую нужно лишь запустить. Отрегулировать придется интенсивность подачи. А значит и мощность аппарата. Ну и также настройке подвергается расстояние от проволоки до объекта.
На современном рынке представлено множество устройств, отличающихся как по параметрам, так и по уровню качества. Разумеется, ценовой вопрос имеет значение.
Впрочем, также одной из причин актуальности таких устройств является легкое освоение. Если на производстве зачастую работают профессионалы с высоким разрядом, то среди частников зачастую уровень подготовки ниже.
Какой бы товар вы ни выбрали для себя, всегда будут существовать несколько аспектов, которые неизменны для каждого. Это общие характеристики всех линеек продукции.
Рассмотрим подробнее:
- • Горелка. Естественно, она присутствует во всех типах оборудования. В том числе среди ручного или полностью автоматического.
- • Кабель и шланг. С помощью этих проводников для работы поступает электрической ток, газ и новые электроды, которые необходимо плавить.
Как уже отмечалось, последние могут быть заменены проволокой.
- • Управляющий блок. Зачастую содержит несколько индикаторов, сигнализирующих о состоянии аппарата, наличия подключении к источникам. А также запас расходных элементов. Если случится повреждение или перегрузка, индикаторы сообщают об этом.
- • Блок питания. В тех вариантах, когда нет подключения напрямую к сети. Да и даже в этом случае зачастую напряжение подается через этот элемент.
- • Резервуар с газом. Его габариты могут отличаться в различном диапазоне. Чем серьезнее нужды, тем больше размер баллона.
Иногда стандартный комплект оборудования снабжается некоторыми новыми частями. Ограничительные экраны, специальные вытяжки для работы в помещении, стойки для расположения «рукава». А также специальные подвижные платформы или просто тележки без бортов, чтобы перемещать баллон с газом. Особенно если он весьма крупный.
Назначение плавки
Обозначенная методика используется в массе различных сфер. Широко востребована как на крупном производстве, так и для каких-то небольших частных работ. Во многих случаях, если ландшафт на территории неудобный, даже стандартный подвод воды из источника к своему дому без предварительной сварки подвести проблематично.
Основные же отрасли, где метод применяется особо широко, это:
- • Соединение магистралей. Все пути, которыми подается газ, вода и так далее. Зачастую центральные линии сплошь состоят из металла. И только отводы на воды организовываются из полипропилена или полиэтилена.
- • Резервуары для содержания потенциально опасных жидкостей. Нефть, как вариант.
- • Практически все основные несущие конструкции из металла в сфере строительства жилых домов. Как многоэтажных, так и частных. Сюда же относится и железобетон.
- • Мосты, ворота, ограждения, элементы заборов.
- • Корпусные части крупных судов.
- • А также все металлических изделий. Перечислить каждую сферу невозможно.
И не стоит забывать, что плавление – это лучший способ ремонта габаритных металлических изделий. А также часто применяется для восстановления различного транспорта. В большей части для техники сельскохозяйственного назначения.
Преимущества
Давайте пройдемся по основным плюсам, которые можно найти в способе полуавтоматической сварки.
- • Скорость исполнения.
- • Возможность без проблем соединять тонкие конструкции и детали.
- • Применяется в универсальных положениях, вертикально или горизонтально, без разницы.
- • Снижения риска деформирования объекта.
- • Выше КПД по сравнению с ручной.
- • Подходит для новичков.
Недостатки
При наличии плюсов, избежать минусов полностью никогда не удается.
- • Значительно возрастает риск пробития газовой защиты при работе на свежем воздухе.
- • Существует шанс, что расплавленный электрод немного разлетится.
- • На максимальной мощности аппарат использовать не рекомендуется. Или постоянно охлаждать, он весьма быстро нагревается.
Как видно, минусом меньше. Но они тоже довольно ощутимые.
Итоги
Эта методика сейчас полностью вытесняет ручное производство. Разумеется, она быстрее, эффективнее, проще и безопаснее. КПД выше в несколько раз. Но полностью автоматический метод, разумеется, приносит более серьезные результаты. В противовес, это и дороже. И если крупные заводы ориентируются на такой подход, то небольшие фирмы со средним потоком производства больше тяготеют к полуавтомату. Для частников же частично механизированная наплавка различных деталей – это единственный способ быстро и выгодно выполнять свою деятельность. А если вы все-таки решили приобрести специальное оборудование, то обращайтесь в нашу компанию «Сармат». Мы предоставляем широкую линейку технического обеспечения для механической обработки.
Механизированная наплавка | Обслуживание и ремонт автомобиля
Процесс наплавки происходит при горении электрической дуги между электродной проволокой и деталью под слоем сыпучего флюса.
Оборудование для наплавки
Автоматическую наплавку под слоем флюса производят на специальных установках, основными элементами которых являются токарный станок с наплавочной головкой вместо резцедержателя и источник питания дуги. Для снижения частоты вращения шпинделя токарный станок переоборудуют, вмонтировав между двигателем привода станка и ведомым шкивом понижающий редуктор, рассчитанный на вращение детали со скоростью 2-5 об/мин.
Для автоматической наплавки под слоем флюса коленчатых валов разработаны специальные установки, не требующие доработки. Одна из них — ОКС-5523 — работает в полуавтоматическом режиме. Особенностью этой установки является бесступенчатое регулирование скоростей наплавки и наличие универсальных центросместителей.
В качестве источников тока при автоматической наплавке используют преобразователи ПСГ-500, ПСУ-500-2, выпрямители ВС-600, ВКС-500-1 и др. Для подачи электродной проволоки в зону наплавки используют наплавочные головки А580М, ОКС-1031Б, ОКС-1252А и др.
Электродная проволока
В качестве электрода при автоматической наплавке деталей под слоем флюса применяют пружинную проволоку 2-го класса диаметром 1,6-2,0 мм с содержанием углерода 0,7-0,8%. При восстановлении деталей находят также применение проволоки следующих марок: низкоуглеродистые сварочные Св-0,8 и Св-0,8А; легированные сварочные Св-18ХГС и Св-08Г2С; углеродистые наплавочные Нп-50 и Нп-80; легированная наплавочная Нп-ЗОХГСА, высоколегированная наплавочная Нп-2Х14.
При выборе проволоки необходимо учитывать, что наплавленный металл должен быть близок по химическому составу к основному металлу.
Флюс
Приготавливают флюс так: на 10 весовых частей флюса АН-348-А берут 0,5 части порошкового графита и 0,4 части порошкового феррохрома №6 и, тщательно их смешав, вливают в массу 0,5 части жидкого стекла. Графит (ЭУТ-1, ЭУБ или ЭУН) должен быть предварительно просеян через сито с размером ячеек 0,05-0,07 мм. Феррохром просеивают через сито, имеющее на 1 см2 около 1000 отв. Затем массу снова перемешивают, пока вся она не станет увлажненной. Приготовленную массу устанавливают в электропечь и прокаливают 3-3,5 ч при 550-600°С. После остывания флюс разбивают тщательно в порошок и просеивают через сито с 9 отв/см2.
К полученной массе добавляют 10 частей отдельно прокаленного и просеянного чистого флюса АН-348-А и всю массу тщательно перемешивают. В таком виде флюс применяют для наплавки стальных деталей, требующих высокую твердость поверхностного слоя. Если в качестве электродной проволоки применяют пружинную проволоку 2-го класса, то при наплавке деталей под флюсом указанного состава твердость металла достигает 52-62 HRC. Для обеспечения такой твердости при наплавке сварочной проволокой Св-08 флюс должен иметь несколько другой состав: (в процентах по массе) стандартный флюс АН-348-А — 95,5; графит порошковый — 2,5; феррохром № 6 порошковый — 2.
Приготовленный флюс должен храниться в сухом помещении. В случае длительного перерыва в работе и увлажнения флюса его перед применением необходимо прокалить.
Подготовка к наплавке
Перед наплавкой восстанавливаемая поверхность должна быть тщательно очищена. Зачистку производят шлифовальной шкуркой (лентой) при вращении детали в центрах станка. Если деталь раньше восстанавливалась вибродуговой наплавкой, то перед наплавкой под слоем флюса ранее наплавленный слой необходимо сошлифовать.
Остатки смазки с электродной проволоки снимают резиновыми шайбами с проколотыми отверстиями. Шайбы устанавливают перед входом проволоки в наплавочную головку.
Отверстия, выходящие на поверхность наплавки, заглушают графитовой пастой, замешанной на жидком стекле, или графитовыми стержнями. Операцию выполняют за сутки до наплавки с тем, чтобы паста успела затвердеть.
Деталь в патроне должна быть надежно закреплена. Биение наплавляемой поверхности не должно превышать 1,5 мм.
Режимы наплавки
На качество наплавки оказывают влияние ток и напряжение, скорость подачи электродной проволоки и вращения детали, вылет проволоки и ее положение по отношению к детали.
При наплавке необходимо стремиться к тому, чтобы хорошее формирование валиков не сопровождалось глубоким проваром основного металла. Основное влияние на глубину провара оказывают сила тока и напряжение, чем они выше, тем глубже провар.
При большом вылете электродной проволоки возрастает сопротивление цепи, что приводит к нарушению процесса наплавки. А слишком большой вылет (свыше 25 мм) делает наплавку просто невозможной.
На форму и размеры наплавляемых валиков большое влияние оказывает скорость наплавки. Слишком большая скорость приводит к уменьшению ширины валика и к плохому сплавлению электродного металла с основным.
При наплавке флюс должен равномерно и достаточно толстым слоем покрывать сварочную ванну и конец электродной проволоки на протяжении всего процесса наплавки. Малейшее открытие ванны и дуги приводит к разбрызгиванию электродного металла и образованию дефектов в виде пор и раковин. Для того чтобы флюс лучше удерживался на поверхности детали, электродную проволоку подают на деталь с некоторым смещением от зенита.
В процессе наплавки под слоем флюса могут быть различные неполадки, снижающие качество. Причинами резкого изменения ширины и высоты наплавляемого валика являются большой вылет электродной проволоки из мундштука, износ выходного отверстия наконечника мундштука или неравномерная подача электродной проволоки (из-за пробуксовки подающих роликов, заедания и пр.). Чаще всего неравномерная подача проволоки вызывается слабым прижимом роликов или их износом.
При нарушении устойчивости горения дуги необходимо проверить прежде всего контакт проволоки с токосъемником (наконечником мундштука). С течением времени отверстие наконечника изнашивается, в результате чего увеличивается вылет проволоки.
Если поверхность наплавленного металла получается недостаточно гладкой, то следует увеличить силу тока или уменьшить подачу суппорта. Чтобы поверхность наплавки была наиболее гладкой образующий валик должен на треть перекрывать ранее наплавленный.
5.6.2. Механизированная сварка и наплавка.
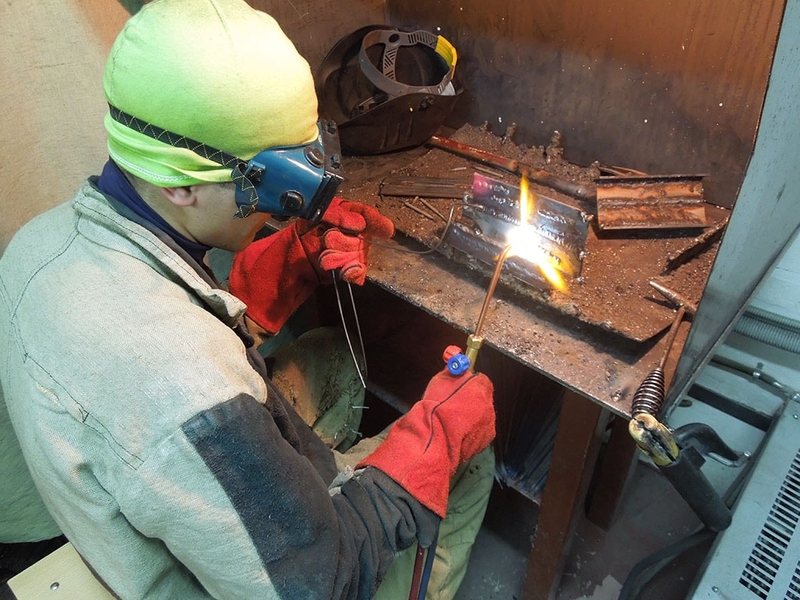
5.6.2. Механизированная сварка и наплавка
Оборудование для механизированной сварки и наплавки. Для механизированной сварки и наплавки применяют автоматы, полуавтоматы для сварки плавящимся электродом и специальное наплавочное оборудование, выпускаемое для наплавки под слоем флюса и вибродуговой (табл. 5.58—5.60).
Для наплавки деталей используют переоборудованные токарные станки, которые снабжают аппаратами для механизированной подачи электродной проволоки к месту наплавки и для управления процессом горения дуги.
При наплавке под слоем флюса станок оборудуют устройством для механизированной подачи флюса. При вибродуговой наплавке в комплект станка входят резервуар для охлаждающей жидкости и насос для подачи ее на деталь. Для уменьшения частоты вращения шпинделя станка применяют червячный редуктор.
Таблица 5.58
Автоматы для наплавки
Таблица 5. 59
Головки для вибродуговой наплавки
* Для ОКС-1252А сечение электрода (ленты) 10х0,5 мм, для ОКС-6569 диаметр порошковой проволоки 2–2,5 мм.
Таблица 5.60
Полуавтоматы для сварки плавящимся электродом
Примечание. С – сплошная проволока, И – порошок.
Источниками питания для автоматической и полуавтоматической сварки или наплавки деталей служат сварочные преобразователи, трансформаторы и выпрямители (табл. 5.61—5.63).
Таблица 5.61
Сварочные преобразователи для автоматической и полуавтоматической сварки
* Снабжен реостатом дистанционного управления сварочного тока.
Таблица 5.62
Сварочные трансформаторы для автоматической дуговой сварки под флюсом
Таблица 5.63
Сварочные выпрямители для автоматической сварки
*ПВ– 65 %.
** Питание полуавтомата типа А-765.
Материалы для механизированной сварки и наплавки. Для механизированной сварки применяют стальную холоднотянутую калиброванную проволоку (табл. 5.64) и проволоку порошковую сварочную, а для механизированной наплавки – проволоку стальную наплавочную (табл. 5.65), а также порошковую проволоку и ленту. Для сварки и наплавки под слоем флюса используют плавленые флюсы.
Таблица 5.64
Проволока стальная сварочная (ГОСТ 2246—70*)
Таблица 5.65
Проволока стальная наплавочная* (ГОСТ 10543—98)
* Проволока диаметром 1–4 мм.
Технологические особенности механизированной сварки и наплавки.
Механизированные способы сварки и наплавки позволяют в широких пределах регулировать состав и свойства наплавленного металла при обеспечении его высоких качеств.
При сварке под слоем флюса дуга устойчиво горит в том случае, если плотность тока на электроде составляет не менее 25 А/мм2. Дальнейшее уменьшение плотности тока вызывает прерывистое горение дуги и плохое формирование шва. Шаг наплавки следует выбирать так, чтобы валики перекрывались на 1/2—1/3 их ширины. При бол ьшем шаге наплавки поверхность получается неровной, и соответственно возрастает трудоемкость последующей механической обработки детали. Режимы наплавки деталей под слоем флюса приведены в табл. 5.66.
Вибродуговую наплавку проводят в среде охлаждающей жидкости, в атмосфере воздуха (без защиты дуги и охлаждения детали), в потоке воздуха, под слоем флюса, в среде водяного пара, в защитных газах с одновременной подачей охлаждающей жидкости.
При вибродуговой наплавке в среде охлаждающей жидкости наплавляемый металл подвергается резкому охлаждению, поэтому в наплавленном слое могут появляться мелкие закалочные трещины, что приводит к снижению усталостной прочности деталей.
Вибродуговую наплавку в атмосфере воздуха (без подачи охлаждающей жидкости на деталь) применяют при ремонте деталей, твердость рабочих поверхностей которых не превышает 300 НВ. Наибольшее распространение способ получил при ремонте резьбовых соединений, а также деталей, изготовленных из чугуна.
Вибродуговую наплавку в потоке воздуха ведут с подачей его из воздушной магистрали непосредственно в зону горения дуги, расходуя его в пределах 15–30 л/мин. Наплавленный в потоке воздуха металл содержит значительное количество азота и кислорода и сравнительно мало пор.
Применение флюса при вибродуговой наплавке способствует повышению качества шва и более равномерному нагреву и охлаждению детали. Деформации наплавленных деталей в 5–6 раз меньше деформации деталей, наплавленных вручную.
Таблица 5.66
Режимы наплавки деталей под слоем флюса
Вибродуговая наплавка в среде водяного пара рекомендуется при ремонте деталей, твердость наплавляемых поверхностей которых находится в пределах 200–400 НВ. При наплавке по этому способу в зону горения дуги от парообразователя подают водяной пар. Применение водяного пара в качестве защитной среды диктуется доступностью и легкостью получения его на ремонтных предприятиях.
Технология вибродуговой наплавки деталей включает в себя подготовку деталей к наплавке, выбор режимов наплавки и наплавочных материалов, наплавку.
Рекомендуемые режимы вибродуговой наплавки деталей в среде жидкости:
Напряжение, В……………………………………………………………………. 12—18
Сила тока, А……………………………………………………………………….. 130—300
Индуктивное сопротивление (витки дросселя РСТЭ-34) ………….. 4—10
Диаметр электродной проволоки, мм………………………………………… 1,3—3
Скорость подачи электродной проволоки, м/мин……………………… 1,16—3
Высота слоя, мм …………………………………………………………………….. 0,3—3
Подача, мм/об……………………………………………………………………….. 2–4,5
Коэффициент переноса металла ………………………………………………. 0,85—0,9
Данный текст является ознакомительным фрагментом.
Сварка по-дамасски
Сварка по-дамасски При изготовлении булата и дамасской стали большую роль играли процессы диффузии (перемещения) углерода из жидких, полужидких или твердых масс высокоуглеродистой стали в частицы малоуглеродистого железа, обеспечивающие сварку этих разнородных
7.
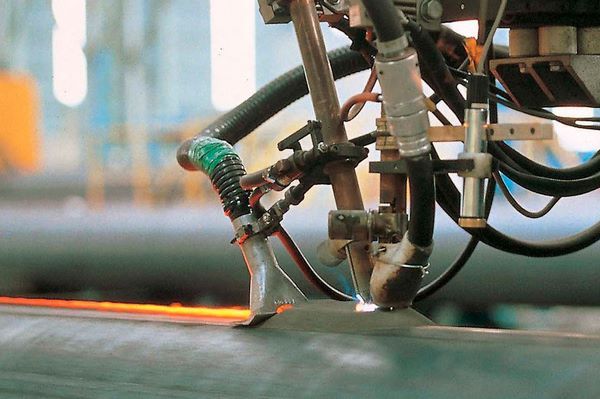
7.2. ЭЛЕКТРИЧЕСКАЯ СВАРКА 7.2.1. ЭЛЕКТРИЧЕСКАЯ ДУГОВАЯ СВАРКА Электрическая дуговая сварка была изобретена в России. Н.Н. Бенардос 6 июля 1885 г. подал заявку и получил привилегию Департамента торговли и мануфактур № 11982 (1886 г.) на способ «соединения и разъединения металлов
5.6.3. Газовая сварка
5.6.3. Газовая сварка При сварке стальных деталей используют присадочную проволоку Св-08, Св-08А, Св-12ГС в виде прутков длиной 0,8 м. При сварке стальных деталей пропан-бутан-кислородным пламенем применяют проволоку Св-12ГС и Св-08Г2С с повышенным содержанием углерода и
механизированный керамогранит | Корпорация творческих материалов
Mechanized излучает индустриальную эстетику благодаря минималистичному подходу к бетону. Коллекция с линейной поверхностью и нейтральной палитрой идеально подходит для архитектурных проектов.
Креативные функции:
- Двенадцать размеров | 12″x24″ до 63″x126″
- Четыре варианта отделки | Бучардированная, высокой плотности, шлифованная, матовая
- Профилированные панели
- Асфальтоукладчики
- Фарфор
- Сделано в Италии
Исключительные декоры делают эту выдающуюся коллекцию, которая действительно преображает пространство, а также позволяет облицовывать стены и продолжать дизайн снаружи.
Механизированные изделия считаются «соответствующими LEED», поскольку они имеют Декларации экологических продуктов (EPD), Декларации продуктов для здоровья® (HPD) и содержат переработанные материалы. Каждый из этих компонентов может способствовать начислению кредитных баллов в соответствии с рейтинговой системой LEED V4.
Посмотреть другие продукты, отвечающие требованиям LEED!
- Технический >
- Механизированные изображения >
Цвета
Темно-серый
Светло-серый
Слоновая кость
Серо-коричневый
Шалфей
Мокко
Шалфовый + темно-серый, большой
Шалфовый + темно-серый, малый
Темно-серый + светло-серый, большой
Темно-серый + светло-серый, малый
Серо-коричневый + цвет слоновой кости, большой
Taupe + Ivory Small
Mocha+ Taupe Large
Mocha+ Taupe Small
Oval Deco 12″x12″x10mm | Матовый
Темно-серый
Светло-серый
Слоновая кость
Серо-коричневый
Шалфей
Мокко
1″x1″ Лист мозаики на 12″ 12″ | Матовый
Темно-серый + Светло-серый + Шалфей
Слоновая кость + Мокко + Серо-коричневый
Мозаика в произвольном порядке на листе 6’x24″x10 мм | Матовый
Светло-серый
Дуговой декор 62 x 62 x 10 мм | Матовый
Размер
-
8″x32″ -
12 x 24 дюйма -
24 x 24 дюйма -
16″x32″ -
24 x 48 дюймов -
32 x 32 дюйма -
48 x 48 дюймов -
32″x63″ – 32″x95″ – 48″x95″ – 63″x63″ – 63″x126″
Подробные сведения о размерах, отделке и толщине см. в разделах
Загрузить таблицу размеров
Отделка
-
2 “x 24” x 10 мм Закругленный конец | Полированный или матовый -
2 “x 32” x 6 мм Закругленный конец | Матовый -
Лестница 13 x 48 x 10 мм | Отточенный или матовый -
Угол лестницы 13 x 48 x 10 мм | Влево или вправо | Полированный или матовый -
13 “x 48” x 10 мм, угол лестницы закрытый | Полированный или матовый
Обзор
Корпус | Неглазурованный фарфор |
---|---|
Страна происхождения | Италия |
Бюджетная цена За квадратный фут. Только для бюджетных целей. Применяется для полевой плитки (не мозаики, отделки, декора). Общее среднее использование коллекции – некоторые предметы немного меньше или немного больше, чем диапазон. | 4-11 долларов |
Время выполнения заказа Оценено на основе средних значений.![]() | 6-8 недель |
Наличие на складе | Импорт/заводской склад |
Толщина | НЕСКОЛЬКО | Информацию о размерах, отделке и толщине см. в документе | .
Смотреть | Бетон, Бетон (минимальный) |
Отделка | Бучардированная, высокой плотности, шлифованная, матовая |
Технические характеристики
Название теста | Метод испытаний | Результат теста |
---|---|---|
Водопоглощение | ISO 10545-3 | 0,08% |
Стойкость к истиранию | ISO 10545-6 | 140 мм 2 |
Прочность на разрыв | ISO 10545-4 | 50 Н/мм 2 |
ДКОФ | DCOF Акутест | ≥0,42 |
Загрузка
Механизированный лист
Механизированные изображения
Креативные дополнения для механизированных изделий
Mozzafiato
Mozzafiato в переводе с итальянского означает «захватывающий дух», что идеально описывает эту коллекцию редкого мрамора.
Кольцевая развязка
Карусель — это современная интерпретация древнего котто.
Улей
Стекло для улья представляет собой игру размеров с плоскими и рельефными поверхностями.
Работы по техническому обслуживанию PennDOT
Хотя бригады PennDOT являются обычным явлением на 40 000 миль дорог Пенсильвании и 25 000 мостов, многие из наших клиентов могут не осознавать объем работы, которую мы выполняем. Серия Maintenance First была разработана, чтобы пролить свет на операции, которые PennDOT выполняет круглый год в рамках нашей миссии по созданию эффективной транспортной системы. Вы также можете увидеть
как образуются выбоины (PDF) .
ПЕРЕЙТИ К: Обработка поверхности |
Резка плеча |
Оценка плеча |
Замена и очистка труб |
Механизированное исправление |
Исправление вручную |
Заделка швов и трещин |
Зимние операции |
Управление растительностью |
Штриховая живопись |
Техническое обслуживание и очистка мостов |
Подписание

Обработка поверхности
Эта операция по техническому обслуживанию, широко известная как «смазка и стружка», используется как способ продлить срок службы дорог с низкой интенсивностью движения еще на три-пять лет.
Это действие выполняется, когда температура превышает 60 градусов, как правило, в период с апреля по октябрь. Для обработки поверхности требуется подметальная машина, маслораспределитель, камнедробилка, катки, многочисленные самосвалы и бригада, состоящая примерно из 18 человек.
Операция начинается с уборки проезжей части от мусора. Затем масло разбрызгивается на дорогу, сразу же поверх масла наносится слой мелкого камня. Затем его укатывают на место, при этом весь рыхлый заполнитель сметается с проезжей части после затвердевания.
Обычно требуется около двух дней, чтобы камни полностью сцепились с затвердевшим асфальтом. Автомобилистам следует снижать скорость на дорогах до тех пор, пока камень не сцепится с асфальтом.
Эта поддерживающая обработка герметизирует поверхность дороги, предотвращая проникновение воды, и восстанавливает трение поверхности, повышая сцепление с дорогой.
Нажмите, чтобы открыть PDF. (PDF для печати)Обрезка обочин
Обрезка обочин удаляет лишний материал и мусор с немощеных обочин. Это улучшает дренаж и позволяет воде уходить с проезжей части.
Для этого процесса требуется такое оборудование, как грейдеры, грузовики, метлы, ленточные или колесные погрузчики и катки. Рабочие двигаются вперед, чтобы обнаружить и пометить или удалить объекты, которые потенциально могут повредить оборудование, такие как указатели, стекло и большие камни.
Грейдер следует за рабочими, срезает лишний материал с обочины и складывает его в штабель для подбора погрузчиком. Его загружают в грузовик для перевозки на место заправки. Следующей частью операции является подметание лишнего материала, оставшегося на проезжей части. Наконец, каток следует за операцией погрузки, чтобы уплотнить или стабилизировать открытый грунт.
Это важная операция по техническому обслуживанию шоссе. Когда дренажные системы не работают должным образом, вода скапливается на проезжей части, создавая условия для обледенения зимой и ослабляя дорожное покрытие, вызывая выбоины.
Нажмите, чтобы открыть PDF. (PDF для печати)Профилирование обочины
Профилирование обочин включает в себя формирование и стабилизацию обочин грунтовых дорог.
Эта операция технического обслуживания обычно программируется в период с апреля по ноябрь. Бригада по планировке плеч включает около 10 рабочих, которые управляют грейдерами, самосвалами, катком и щеткой.
PennDOT выравнивает обочины, чтобы устранить уклон между проезжей частью и обочиной и позволить воде стекать с дорожного покрытия. Если позволить образоваться и остаться на обочине колеи, вода может проникнуть внутрь и повредить край тротуара.
Внешний край обочины срезан по направлению к дороге. Затем отрезанный материал повторно сортируется по обочине, чтобы заполнить углубления и колеи. Затем материал сметается с проезжей части и уплотняется катком.
Замена и очистка труб
Для поддержания эффективного потока воды вокруг дорог штата замена и очистка труб имеют важное значение. Управление потоком воды является одним из наиболее важных аспектов содержания тротуаров. Неконтролируемый поток воды повредит как поверхность тротуара, так и область под тротуаром, что приведет к ухудшению состояния.
Замена труб — круглогодичная работа. Как правило, труба устанавливается перед ремонтом или уплотнением поверхности дорожного покрытия. Стандартная бригада труб состоит из мастера, трех операторов оборудования и четырех дополнительных членов бригады. Оборудование включает в себя кабину экипажа, экскаватор-погрузчик, два самосвала, компрессор и каток. Из-за своей долговечности и простоты в обращении большинство заменителей труб изготавливаются из пластика, а остальные разделены между металлом и бетоном.
Операции по замене труб состоят из резки или распиловки дорожного покрытия, создания траншеи в основании дорожного покрытия, установки трубы, заполнения траншеи, уплотнения насыпного материала и замены поверхности дорожного покрытия.
Очистка труб в основном производится в летние месяцы путем промывки их водой. Большинство труб очищаются с помощью высокоскоростного очистителя канализации. Чтобы обеспечить попадание воды в трубу, необходимы дополнительные меры, такие как очистка канавы, вырезание обочины и выравнивание обочины, что позволяет воде течь по ее естественному дренажному пути.
Нажмите, чтобы открыть PDF. (PDF для печати)Механизированный ремонт
Механизированный ремонт используется для ремонта ограниченных участков проезжей части с обширными выбоинами, большими площадями с трещинами на дорожном покрытии и впадинами. Это также улучшает гладкость дорожного покрытия.
Это техническое обслуживание обычно проводится летом, но может выполняться и в другое время года, если позволяют дорожные и погодные условия. Бригаде обычно требуется от 13 до 15 рабочих, несколько самосвалов, асфальтоукладчик, каток и устройство для нанесения липкого слоя.
Механизированное ямочное заделывание включает шесть конкретных этапов — разметку области, которую необходимо залатать, очистку территории с помощью метлы для уборки улиц, заполнение любых больших дыр или низких участков латательным материалом, уплотнение материала, нанесение слоя асфальта на отмеченную область и уплотнение участка катком.
Если бы рабочие не выполняли механизированные ремонтные работы, поврежденное дорожное покрытие еще больше ухудшилось бы, что вынудило бы PennDOT полностью восстановить дорогу или выполнить другие, более дорогостоящие ремонтные работы.
Заделка ям вручную
Заделка ям вручную чаще всего называется заделкой выбоин.
В большинстве случаев заделка выбоин производится весной, когда температура постоянно держится выше нуля. Зимой, если позволяет погода, бригады латают выбоины с помощью холодного пластыря.
Холодный участок представляет собой асфальт, смешанный с мылом, водой и мелкими камнями. Мыло и вода позволяют материалу оставаться гибким, поэтому бригады могут работать с ним. Материал холодного пластыря просто помещается в выбоину с помощью лопаты, а затем уплотняется. После того, как мыло и вода испарятся, материал станет твердым. Хотя это предназначено для временного ремонта, холодные ремонтные работы могут длиться два или более года.
Горячая смесь — это постоянная заплатка для выбоины, для которой требуется смесь чистого асфальта и мелкозернистого камня, нагретая примерно до 300 градусов по Фаренгейту. Выбоина вырезается под прямым углом, очищается, а затем обрабатывается липким слоем асфальта, который действует как клей. После нанесения выравнивающего слоя горячую смесь помещают в выбоину и уплотняют катком или другим приспособлением. Если бы выбоины не были отремонтированы, дорожное покрытие раскололось бы и потребовало бы более дорогостоящих корректирующих мероприятий.
Заделка швов и трещин
Заделка швов используется для герметизации стыков на бетонных дорогах, а заделка трещин используется для герметизации трещин на асфальтовых дорогах.
Герметизация трещин предотвращает просачивание воды через трещины на асфальтированной дороге, что может привести к выбоинам и разрушению дорожного покрытия. Герметизация швов предотвращает отложение камней или других твердых материалов между плитами на бетонном проезжей части. Если значительное количество материала попадет в стыки, дорога не сможет расширяться и сжиматься при изменении температуры и в конечном итоге сломается в стыках, или плита может деформироваться.
Заделка трещин обычно выполняется с марта по ноябрь в зависимости от погодных условий. Герметизация швов обычно выполняется с апреля по июнь и с сентября по ноябрь. Этот временной интервал используется, потому что суставы полностью открыты. Для обоих видов работ требуется около восьми рабочих, самосвал, нагревательный котел для герметика и устройство для нанесения герметика.
Эти работы по техническому обслуживанию включают удаление мусора из трещины или стыка, подлежащего герметизации, а затем нанесение жидкого битумного материала.
Нажмите, чтобы открыть PDF. (PDF для печати)Зимние работы
Зимние работы включают удаление снега и льда, а также нанесение противогололедных материалов на все дороги и мосты штата. В центре зимних операций задействованы опытный оператор и самосвал, оснащенный разбрасывателем соли, снегоуборочным плугом, а часто и скребковым плугом.
Во время суровых зимних штормов PennDOT также направляет по крайней мере одного механика в каждый гараж, чтобы позаботиться о любых серьезных отказах или поломках оборудования.
Чтобы предотвратить образование льда на дорожном покрытии, грузовики PennDOT посыпают смесью соли, чтобы растопить лед, и небольших камней, называемых противоскользящими, для обеспечения сцепления. В некоторых сельских районах PennDOT ограничит использование соли и увеличит количество противоскольжения, нанесенного на дорожное покрытие, поскольку полная эффективность соли зависит от интенсивности движения.
Во время шторма PennDOT сначала вспахивает и посыпает солью основные автомагистрали, а затем переезжает на менее посещаемые сельские дороги. Во время сильных зимних бурь оборудование часто перенаправляется с назначенных сельских маршрутов, чтобы в первую очередь помочь вспашке дорог с более интенсивным движением.
Еще одно оружие, которое PennDOT имеет в своем зимнем арсенале, — это защита от обледенения. Защита от обледенения, по сути, включает обработку дороги рассолом (соленой водой) до того, как начнут выпадать замерзающие осадки. Водная часть рассола испаряется, а оставшаяся соль помогает предотвратить прочное сцепление льда с дорожным покрытием.
PennDOT также имеет 62 объекта по всему штату, способных производить собственный рассол. В среднем за последние пять лет было использовано более 9 миллионов галлонов противообледенительного материала. Чтобы узнать больше о зимних операциях PennDOT, посетите
Зимний раздел нашего сайта.
Управление растительностью
Управление растительностью украшает дороги штата, делает их более безопасными, доступными и украшает пейзаж.
Скашивание, опрыскивание пестицидами и выборочное прореживание деревьев являются процессами, составляющими программу управления.
PennDOT скашивает около 112 000 акров ежегодно с мая по октябрь. Как часто косят дороги, определяется их интенсивностью движения и установленным ограничением скорости, а также высотой роста.
В местах, где косилки не могут безопасно передвигаться, на придорожную растительность наносится гербицид. Использование гербицидов более рентабельно, чем вырубка или обрезка деревьев. Гербициды контролируют обширную корневую систему инвазивных растений. Все три вида деятельности поддерживают видимость на обочинах.
Типичная бригада по обрезке деревьев состоит из мастера, оператора оборудования и четырех-пяти членов бригады. Оборудование для прореживания деревьев включает в себя кабину экипажа, самосвал, измельчитель веток, цепные пилы и другие ручные инструменты по мере необходимости. Для скашивания PennDOT использует 228 принадлежащих департаменту тракторных косилок и контрактных косилок.
Особое внимание уделяется уходу за растительностью в течение вегетационного периода и продолжается в течение зимы, когда уборка снега не требуется.
Нажмите, чтобы открыть PDF. (PDF для печати)Окраска линий
Каждый год бригады по окраске линий PennDOT наносят на автомагистрали более 1,6 миллиона галлонов желтой и белой краски для разметки, чтобы помочь автомобилистам.
Этого количества краски достаточно, чтобы заполнить 470 надземных плавательных бассейнов глубиной четыре фута и диаметром 12 футов. PennDOT начинает красить линии дорожного движения в начале лета. К тому времени, когда эта операция будет завершена в октябре, бригады PennDOT нанесут более 114 000 миль линий, чего достаточно, чтобы совершить почти пять оборотов вокруг земного шара.
PennDOT красит в основном разделительные линии дорог и автомагистралей, но также красит некоторые временные полосы для полиции штата, дорожные указатели STOP и некоторые знаки железнодорожных переездов.
Погода для покраски должна быть теплой и сухой, так как дождь, высокая влажность или температура ниже 50 градусов по Фаренгейту увеличивают нормальное время высыхания на 90-120 секунд.
Оборудование покрасочных бригад линии PennDOT нагревает краску примерно до 110 градусов по Фаренгейту, а затем распыляет материал на дорогу. Пока краска еще влажная, автоматически наносятся шарики из переработанного стекла для обеспечения отражающей способности.
По оценкам PennDOT, компания использует около 11 миллионов фунтов стеклянных бусин для рисования каждый год.
Нажмите, чтобы открыть PDF. (PDF для печати)Техническое обслуживание и чистка мостов
В Пенсильвании находятся одни из старейших мостов в стране, средний возраст которых превышает 50 лет. Профилактическое обслуживание чрезвычайно важно для продления срока службы сооружений как в Пенсильвании, так и в стране.
Плохое состояние конструкций является одной из самых острых транспортных проблем страны. Хорошая программа профилактического обслуживания может увеличить срок службы моста.
PennDOT инспектирует мосты большинства штатов не реже одного раза в два года. Основываясь на результатах осмотра или конструктивных нуждах, бригады PennDOT производят замену мостов или структурный ремонт стальных или бетонных компонентов. Некоторые округа PennDOT отливают и строят свои собственные балки зимой, чтобы использовать их для строительства летом.
Уборка мостов является важным элементом государственной программы профилактического обслуживания мостов. Палуба и основание должны содержаться в чистоте, дренажные системы должны быть свободны от мусора. PennDOT предписывает ежегодно очищать большинство мостов.
PennDOT очищает более 16 000 мостов каждый год.
Базовая бригада по очистке мостов состоит из мастера, оператора оборудования и четырех членов бригады. Необходимое оборудование включает кабину экипажа, самосвал, подметальную машину и промывочную машину.
Подписание
Самый важный способ передачи информации о безопасности на дорогах нашим клиентам — это дорожные знаки.
В большинстве операций округа PennDOT есть единая бригада вывесок — бригадир вывесок и помощник, — которые устанавливают знаки вдоль дорог штата; в нескольких крупных округах есть дополнительные бригады. PennDOT несет ответственность за проверку установленных знаков и определение необходимости замены знака из-за возраста, вандализма, повреждения или по другим причинам. Работы определены, вывески производятся в государственной мастерской вывесок, и после завершения вывески планируются к установке.
В Пенсильвании около 1,3 миллиона государственных вывесок. Магазин вывесок PennDOT ежегодно производит около 85 000 вывесок. Знаки изготавливаются из алюминиевых заготовок, покрытых световозвращающей пленкой высокой интенсивности. После нанесения защитного покрытия для сообщения вывески наносятся трафаретные или вырезанные символы.
Подавляющее большинство — 95 процентов — заказов на печать выполняются в течение 14 дней с момента получения заказа.
Обработка поверхностей с высоким коэффициентом трения (HFST) — Безопасность
Обработка поверхности с высоким коэффициентом трения (HFST)
Обработка поверхности с высоким коэффициентом трения (HFST) — это обработка дорожного покрытия, которая резко и немедленно снижает количество аварий, травм и смертельных случаев, связанных с проблемами трения, например:
- трение дорожного покрытия во влажных условиях и/или
- Высокие требования к трению из-за скорости автомобиля и/или геометрии проезжей части.
905:00 Исследовательский отчет, опубликованный FHWA, показывает, что HFST, по оценкам, снижает количество аварий на мокрой дороге на 83 процента, а общее количество аварий – на 57 процентов.
HFST включает в себя нанесение очень высококачественного заполнителя на дорожное покрытие с использованием полимерного связующего для восстановления и/или поддержания трения дорожного покрытия в существующих или потенциально опасных местах аварии. Более высокое сцепление с дорожным покрытием помогает автомобилистам сохранять лучший контроль как в сухих, так и в мокрых условиях вождения.
Хотя HFST не подходит для мощения коридоров, это подход, который был продемонстрирован на национальном и международном уровнях и обеспечил значительное увеличение трения при точечном применении. Для проверки улучшенного трения после установки использовалось самое современное оборудование для измерения трения.
Особенности
- Посетите страницу Примеры использования и заслуживающие внимания практики , чтобы получить информацию о реальных применениях HFST.
- HFST Часто задаваемые вопросы, технические характеристики и дополнительные ресурсы доступны на странице часто задаваемых вопросов, ссылок и других ресурсов.
Что нового
- Обработка поверхности с высоким коэффициентом трения — Карманное руководство по установке и проверке
- Версия для планшетов
- Версия для мобильных телефонов
- Обработка поверхностей с высоким коэффициентом трения — часто задаваемые вопросы — обновление 2022
- Обработка поверхности с высоким коэффициентом трения — Руководство по выбору места и установке
- Ресурсы для обработки поверхности с высоким коэффициентом трения
Концепция применения противоскользящей обработки поверхности была впервые оценена в Соединенном Королевстве в 1967 для Большого Лондонского Совета. Город реализовал программу по улучшению перекрестков путем нанесения покрытия с высокой устойчивостью к скольжению на более чем 800 перекрестках и в других потенциально проблемных местах. Исследование проекта, озаглавленное «Расположение и обращение с опасными местами заноса в городах» (отчет об исследованиях TRB 623, 1976 г. ), показало снижение количества аварий на 31 процент. Эта технология появилась в Соединенных Штатах несколько десятилетий спустя, но использовалась в основном для герметизации настилов мостов. Только в начале 2000-х различные поставщики HFST начали продавать эту обработку в качестве контрмеры безопасности для транспортных отделов штата и местных агентств. На приведенной ниже карте показано состояние внедрения HFST на кривых в США по состоянию на декабрь 2017 г.
Табличная версия карты
Следующие ссылки приведут вас к разделам этой страницы, описывающим дополнительную информацию о HFST и поддерживающих программах FHWA:
Вернуться к началу
Описание технологии
Последние достижения в понимании требований к трению дорожного покрытия, рецептуре эпоксидной смолы и прочному заполнителю производства повышают безопасность в критических местах с повышенным риском аварий на бетонных и асфальтовых покрытиях. В доступных продуктах HFST используются наполнители, устойчивые к полировке и истиранию, а также уменьшающие аквапланирование на мокрой поверхности.
Крупный план типичного заполнителя, используемого в качестве покрытия поверхности, демонстрирующий угловатость и размер.
Обработка может производиться как вручную, так и механическим способом. Скорость полностью механизированной установки HFST аналогична другим операциям по укладке дорожного покрытия. Доступны различные типы систем HFST в зависимости от типов заполнителей, связующих систем и методов нанесения.
Продукты HFST можно приобрести у многочисленных производителей и подрядчиков. Методы применения и спецификации могут различаться в зависимости от того, как продукт используется для лечения.
Вернуться к началу
Надлежащее использование и расположение
Поддержание надлежащего коэффициента сцепления с дорожным покрытием имеет решающее значение для безопасного вождения. В таких местах, как крутые горизонтальные повороты и там, где транспортные средства могут чрезмерно тормозить, поверхности дорожного покрытия могут преждевременно полироваться, тем самым уменьшая имеющееся трение дорожного покрытия. Это снижение трения может привести к тому, что транспортные средства потеряют управление или занесутся, когда они ускоряются, резко поворачивают или чрезмерно тормозят. HFST может восстановить безопасный уровень трения на полированном дорожном покрытии.
Кроме того, по сравнению с транспортными средствами, движущимися по прямому участку дороги, транспортным средствам, движущимся по горизонтальным кривым, требуется большее боковое (боковое) трение, а транспортным средствам на перекрестках требуется большее продольное трение. В этих областях может потребоваться большее, чем обычно, трение дорожного покрытия.
Технология HFST уникальна своей способностью решать проблемы, характерные для конкретного объекта, и может также быть полезна на:
- подходах к перекресткам с высокой интенсивностью движения,
- Пересадочные рампы,
- Мосты и
- Выбранные участки межгосударственных трасс.
Это новшество может помочь DOTS штата, округам, городам, племенам и федеральным земельным агентствам по всей стране улучшить разногласия в точках размещения.
Вернуться к началу
Преимущества
Благодаря перечисленным ниже преимуществам, проекты усовершенствования HFST были хорошо восприняты общественностью и выборными должностными лицами.
HFST снижают количество аварий, травм и смертельных исходов.
В 1997 году компания Transit New Zealand провела обзор международных исследований уровней устойчивости покрытия к скольжению и впоследствии опубликовала результаты в отчете под названием «Исследования уровней сопротивления скольжению на мокрой дороге для сети автомобильных дорог штата Новая Зеландия». В отчете сделан вывод о том, что реализация политики противоскольжения дала соотношение выгод и затрат, равное 40. Исследования политики противоскольжения до и после внедрения показали, что количество аварий на мокрой дороге снизилось на 30 процентов.
В настоящее время сообщаются данные об авариях с объектов внедрения в США для горизонтальных кривых, которые были обработаны с помощью HFST в середине-конце 2000-х годов. Эти данные подтверждают зарубежный опыт, в котором сообщается о значительном сокращении числа дорожно-транспортных происшествий после установки HFST.
В настоящее время проводится дополнительный анализ снижения аварийности в рамках исследования FHWA «Оценка малозатратных улучшений безопасности» . В штате Кентукки было установлено и измерено 25 дополнительных приложений HFST, и по крайней мере через год на этих объектах было зафиксировано снижение количества сбоев на 69.процент.
HFST относительно дешевы по сравнению с геометрическими улучшениями .
Государственные DOT сообщают, что стоимость HFST варьируется от 25 до 50 долларов за квадратный ярд. Хотя это не дешево, долговечность HFST компенсирует первоначальную высокую стоимость, поскольку срок службы обработки составляет не менее 10 лет.
Департамент транспорта Южной Каролины добился 80-процентной экономии средств после использования HFST на участке проезжей части в одну милю по сравнению с повторным выравниванием того же участка. Для получения дополнительной информации см. тематическое исследование HFST, связанное с опытом DOT Южной Каролины 905:00 .
Кроме того, соотношение выгод и затрат является высоким, поскольку сокращение количества аварий продолжается в течение многих лет.
HFST прочны и долговечны.
HFST обеспечивают устойчивое и долгосрочное решение в местах, где недостаточное трение является фактором, способствующим авариям, а качество существующего дорожного покрытия хорошее. Ожидаемый жизненный цикл HFST составляет примерно 10 лет.
HFST настраиваются в соответствии с конкретными государственными и местными требованиями безопасности .
Агентства могут использовать HFST там, где это может быть наиболее полезным, как показывают исследования и их собственный опыт, например:
- Двухполосные городские или сельские горизонтальные кривые,
- Участки с крутым уклоном или вблизи него,
- Участки при перестроениях и слияниях или рядом с ними, и
- Сельские и городские перекрестки.
HFST дают измеримые результаты .
Недавнее исследование, проведенное Департаментом транспорта Южной Каролины до и после серии горизонтальных криволинейных установок, показало, что соотношение выгод и затрат составляет примерно 24:19.0003
Кентукки поместил HFST на 26 горизонтальных кривых, и на сегодняшний день в этих местах наблюдается среднее сокращение с 6,2 до 1,9 аварий в год. Для получения дополнительной информации обратитесь к тематическому исследованию HFST, связанному с опытом Kentucky Transportation Cabinet .
Кроме того, в отчете 617 Национальной совместной программы исследований автомобильных дорог (NCHRP) указывается снижение числа аварий на 20 процентов для всех аварий на перекрестках.
HFST оказывают незначительное воздействие на окружающую среду и минимальное влияние на трафик.
Как правило, длина установки HFST очень короткая и оказывает очень незначительное воздействие на окружающую среду, особенно по сравнению с перестройкой дорог. Кроме того, обработка часто может быть применена в течение нескольких часов, вызывая минимальные задержки движения и эффекты по сравнению с обычным проектом покрытия дорожного покрытия. Для получения дополнительной информации обратитесь к тематическому исследованию HFST, связанному с опытом Caltran.
Вернуться к началу
Every Day Counts – Обработка поверхности с высоким коэффициентом трения
Инициатива Every Day Counts (EDC) Федерального управления автомобильных дорог предназначена для выявления и внедрения инноваций, направленных на сокращение сроков реализации проектов, повышение безопасности наших дорог и улучшение экологической устойчивости.
Чтобы гарантировать быстрое получение преимуществ от использования HFST на большом проценте рынка США, инициатива EDC разработала агрессивную программу для быстрого ускорения развертывания и внедрения HFST. В рамках последующей инициативы EDC2 был создан план реализации, служащий дорожной картой для быстрого и успешного внедрения HFST, включая техническое руководство и помощь, бенчмаркинг, маркетинг и коммуникации, обучение и демонстрацию проектов, которые будут освещать передовой опыт.
Посетите веб-сайт EDC 2012 HFST для получения дополнительной информации о программе и ресурсах EDC2 HFST.
Вернуться к началу
Программа усовершенствования поверхности на горизонтальных кривых (SEaHC)
FHWA начала активно продвигать HFST в 2008 году с создания национальной демонстрационной программы – SEaHC. Программа SEaHC предусматривала помощь в выборе площадки для HFST, установку HFST и долгосрочную помощь в измерении трения и текстуры для ограниченного числа экспериментальных государств. По состоянию на 31 марта 2014 г. в рамках демонстрационной программы FHWA SEaHC система HFST была установлена в 10 штатах, а всего по стране было установлено 23 установки.
Хотя HFST может применяться к широкому спектру дорожных сценариев, эта национальная демонстрация сосредоточена на местах, которые были определены FHWA как наиболее выгодные — горизонтальные кривые. Программа завершится промежуточными и окончательными отчетами, в которых задокументировано достигнутое за трехлетний период снижение аварийности до и после для всех площадок, включенных в программу.