Методы определения твердости металлов: Методы определения твердости металла | Speranza
alexxlab | 18.04.2023 | 0 | Разное
Классификация методов определения твердости металлов и их сплавов при проведении обследований зданий и сооружений
А.Л. Фролов, эксперт,
А.М. Аллаберганов, эксперт,
ООО «ПСК «Высота»
Д.А. Киселев, эксперт
М.А. Агеева, эксперт
Э.Т. Мышко, эксперт
ООО «Диаформ».
Объем проводимых обследований зданий и сооружений увеличивается с каждым годом, что является следствием ряда факторов: физического и морального их износа, перевооружения и реконструкции производственных зданий промышленных предприятий, реконструкции малоэтажной старой застройки, изменения форм собственности и резкого повышения цен на недвижимость, земельные участки и др. Особенно важно проведение обследований после разного рода техногенных и природных воздействий (пожары, землетрясения и т.п.), при реконструкции старых зданий и сооружений, что часто связано с изменением действующих нагрузок, изменением конструктивных схем и необходимостью учета современных норм проектирования зданий.
Исключительно важное значение имеют обследование и оценка технического состояния строительных конструкций и зданий, в целом поврежденных пожаром, и установление причин недостаточной эффективности противопожарных мероприятий.
Одним из основных свойств материала, определяюших надежность и долговечность конструкций, является твердость. Количественная оценка твердости позволяет сделать выводы о виде примененных сплавов в конструкциях, их характеристиках и степени повреждения, что является дополнительным критерием обоснования выводов о техническом состоянии зданий и сооружений при проведении обследования.
Понятие твердости известно человечеству с давних времен. В 1881 г. один из основоположников теории твердости Генрих Герц отмечал, что твердость – “это настолько общепонятное свойство, что каждый считает, что знает о твердости не меньше, чем сам я” [1]. Он же ввел одно из первых понятий твердости, которую рассматривал как нагрузку, соответствующую началу пластической деформации при вдавливании шара в плоскость.
Поскольку измерение твердости является значительно менее трудоемкой операцией, чем большинство других видов механических испытаний, и не сопровождается разрушением изделия, этот вид испытаний широко распространен в промышленности. Измерения твердости используются при контроле технологических процессов, определении эксплуатационных характеристик изделий, выборе режимов механической обработки и т. д. Это неразрушающий метод контроля, основной способ оценки качества термической обработки изделия. О твердости судят либо по глубине проникновения индентора (метод Роквелла), либо по величине отпечатка от вдавливания (методы Бринелля, Виккерса, микротвердости). Во всех случаях происходит пластическая деформация материала.
В основу классификации методов определения твердости положено разделение методов по диапазонам в зависимости от применяемых нагрузок и, соответственно, глубин внедрения индентора в исследуемый материал. В результате проведенных дискуссий, в 2002 г. в международном стандарте ISO 14577 было закреплено распределение методов определения твердости по диапазонам, которое приведено в табл. 1.
Таблица 1. Распределение методов определения твердости по диапазонам
Наименование диапазона |
Величина применяемых нагрузок на индентор F, H |
Глубина внедрения индентора в исследуемый материал h, мкм |
Макродиапазон |
2≤F≤30000 |
не регламентирована |
Микродиапазон |
F<2 |
h>0,2 |
Нанодиапазон |
не регламентирована |
h≤0,2 |
Макродиапазон включает в себя все методы определения твердости, при осуществлении которых используются нагрузки на индентор от 2 до 30000 Н.
К микродиапазону относятся методы, для реализации которых применяются нагрузки меньше 2 Н, а глубина внедрения индентора при этом больше 0,2 мкм. Нанодиапазон характеризуется любыми методами определения твердости, при которых глубина внедрения индентора не превышает 0,2 мкм. Стремительно развивающееся в последнее время наноиндентирование часто выходит за пределы 0,2 мкм глубины внедрения индентора. Поэтому такую твердость материала правильнее называть микротвердостью, а не нанотвердостью, как часто приводится в современных публикациях. Вышеуказанный стандарт ориентирован преимущественно на определение твердости при нагруженном инденторе, т.е. с учетом упругой и пластической составляющих твердости.
Одним из универсальных способов определения твердости практически всех материалов является метод измерения твёрдости вдавливанием шарика (твердость по Бринеллю).
В материал вдавливается стальной шарик, и значения твердости определяют по величине поверхности отпечатка, оставляемого шариком. Шарик вдавливают с помощью пресса.
Испытуемый образец устанавливают на столике 1 в нижней части неподвижной станины пресса (рис. 2), зашлифованной поверхностью кверху. Поворотом вручную маховика 2 по часовой стрелке столик поднимают так, чтобы шарик мог вдавиться в испытуемую поверхность. В прессах с электродвигателем вращают маховик 2 до упора и нажатием кнопки включают двигатель 5. Последний перемещает коромысло и постепенно вдавливает шарик под действием нагрузки, сообщаемой привешенным к коромыслу грузом. Эта нагрузка действует в течение определенного времени, обычно 10—60 с, в зависимости от твердости измеряемого материала, после чего вал двигателя, вращаясь в обратную сторону, соответственно перемещает коромысло и снимает нагрузку.
В образце остается отпечаток со сферической поверхностью (лунка). Диаметр отпечатка измеряют лупой, на окуляре которой нанесена шкала с делениями, соответствующими десятым долям миллиметра. Диаметр отпечатка замеряют с точностью до 0,05мм (при вдавливании шарика диаметром 10мм и 5мм) в двух взаимно перпендикулярных направлениях. Для определения твердости следует принимать среднюю из полученных величин.
Число твердости по Бринеллю НВ вычисляют по уравнению.
Однако получение постоянной и одинаковой зависимости между Р и d, необходимое для точного определения твердости, достигается только при соблюдении определенных условий. При вдавливании шарика на разную глубину, т. е. с разной нагрузкой для одного и того же материала, не соблюдается закон подобия между получаемыми диаметрами отпечатка. Наибольшие отклонения наблюдаются, если шарик вдавливается с малой нагрузкой и оставляет отпечаток небольшого диаметра или вдавливается с очень большой нагрузкой и оставляет отпечаток с диаметром близким к диаметру шарика. Поэтому твердость материалов измеряют при постоянном соотношении между величиной нагрузки Р и квадратом диаметра шарика D2. Это соотношение должно быть различным для материалов разной твердости.
В процессе вдавливания наряду с пластической деформацией измеряемого материала происходит также упругая деформация вдавливаемого шарика. Величина этой деформации, искажающей результаты определения, возрастает при измерении твердых материалов. Поэтому испытания вдавливанием шарика ограничивают измерением металлов небольшой и средней твердости (для стали с твердостью не более НВ =
Известное влияние оказывает также длительность выдержки металла под нагрузкой. Легкоплавкие металлы (свинец, цинк, баббиты), имеющие низкую температуру рекристаллизации, испытывают пластическую деформацию не только в момент вдавливания, но и в течение некоторого времени после приложения нагрузки. С увеличением выдержки под нагрузкой пластическая деформация этих металлов практически стабилизируется.
Для металлов с высокими температурами плавления влияние продолжительности выдержки под нагрузкой незначительно, что позволяет применять более короткие выдержки (10 — 30 с).
При измерении твердости шариком определенного диаметра и с установленными нагрузками на практике пользуются заранее составленными таблицами, указывающими число НВ в зависимости от диаметра отпечатка и соотношения между нагрузкой Р и поверхностью отпечатка F. При указании твердости НВ иногда отмечают принятые нагрузку и диаметр шарика.
Однако этот способ не позволяет:
а) испытывать материалы с твердостью более НВ 450;
б) измерять твердость тонкого поверхностного слоя (толщиной менее 1—2 мм), так как стальной шарик продавливает этот слой и проникает на большую глубину. Толщина измеряемого слоя (или образца) должна быть не менее 10-кратной глубины отпечатка.
Принципиальное отличие метода определения твердости по Роквеллу от рассмотренного выше измерения по Бринеллю состоит в том, что твердость определяют по глубине
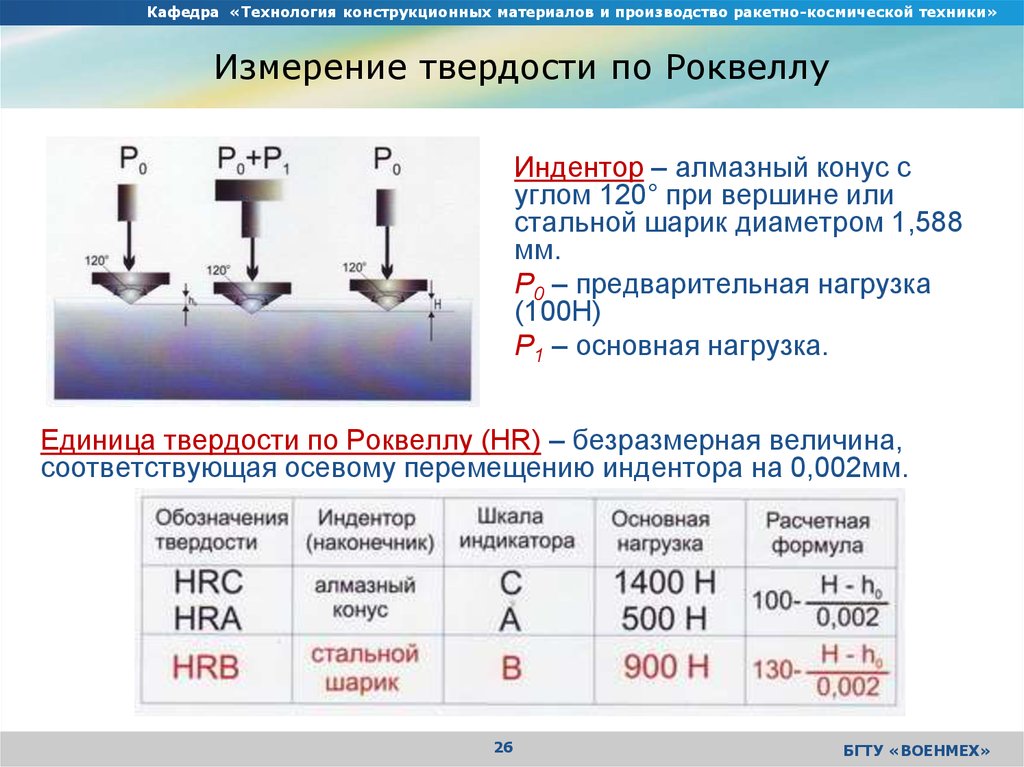
Этот метод имеет то преимущество перед измерениями по Бринеллю, что позволяет изменять нагрузку в широких пределах, без изменения значений твердости, так как при вдавливании конуса сохраняется закон подобия, а условия деформации под вершиной конуса с увеличением давления не изменяются.
Нагружение осуществляется в два этапа. Сначала прикладывается предварительная нагрузка Р0 (10 кт·с) для плотного соприкосновения наконечника с образцом. Затем прикладывается основная нагрузка Р1. В течение некоторого времени действует общая рабочая нагрузка Р. После снятия основной нагрузки определяют значение твердости по глубине остаточного вдавливания наконечника h под нагрузкой.
Прибор измеряет глубину отпечатка алмазного конуса (стального шарика) или, точнее, разность между глубиной отпечатков, полученных от вдавливания наконечника под действием основной нагрузки и от вдавливания под предварительной нагрузкой. Числа твердости по Роквеллу возрастают с увеличением твердости материала, что позволяет сравнить числа Роквелла с числами Бринелля. Однако числа твердости по Роквеллу можно пересчитать на числа твердости по Бринеллю с помощью специальных диаграмм и таблицы, построенных на основании многочисленных экспериментальных работ. Зависимость между этими числами не имеет линейного характера.
Измерение твердости по Роквеллу требует меньше времени (30—60 с), чем по Бринеллю, причем результат измерения виден на шкале (он указан стрелкой). Кроме того, измерение твердости по Роквеллу оставляет меньший отпечаток на поверхности детали.
Твердость очень тонких слоев металла (толщиной менее 0,3 мм) с указанными нагрузками 60 и 150 кт·с измерять нельзя, так как алмазный конус проникает на глубину, превышающую толщину этих слоев, и указывает, следовательно, твердость нижележащих областей. Вместе с тем с увеличением твердости измеряемого материала глубина отпечатка уменьшается, вследствие чего понижается точность измерения (особенно для металлов с твердостью более HRC 60).
Твердость и другие свойства, анализируемые в процессе ее определения разными методами, как правило, рассчитываются по формулам, включающим глубину внедрения индентора в испытуемую поверхность в той или иной степени. Основные критерии оценки твердости, в зависимости от показателя степени глубины внедрения индентора, условно можно разделить на 3 группы:
1. Критерии оценки твердости 1-й степени, когда в формуле расчета твердости применяется :
2. Критерии оценки твердости 2-й степени, когда в формуле расчета твердости применяется
3. Критерии оценки твердости 3-й степени, когда в формуле расчета твердости применяется
К критериям первого уровня можно отнести характеристики, по которым с определенными допущениями оценивается твердость, т.е. способность материала сопротивляться при внедрении в него индентора: диаграмма индентирования, работа индентирования, ползучесть, вязкоупругое восстановление материала, твердость по Роквеллу, твердость по Шору. Физическая сущность критериев оценки твердости первого уровня представлена в табл. 2.
Таблица 2. Критерии оценки твердости 2-й степени
Название критерия |
Сущность критерия |
Диаграмма индентирования |
Показывает зависимость глубины внедрения индентора от нагрузки на индентор |
Работа индентирования |
Равна площади под нагрузочной ветвью диаграммы индентирования |
Твердость по Шору |
Показывает зависимость глубины внедрения индентора от максимальной нагрузки |
Твердость по Роквеллу |
Равна относительному изменению глубины внедрения индентора при равных нагрузках в условных единицах и характеризует пластическую составляющую твердости при минимальной предварительной нагрузке |
Ползучесть |
Показывает изменение глубины внедрения индентора в процессе нагрузки под действием постоянной максимальной нагрузки в определенном интервале времени |
Вязкоупругое восстановление отпечатка в процессе разгрузки |
Показывает изменение глубины внедрения индентора в процессе разгрузки при выдержке в определенном интервале времени с нагрузкой, равной 10-20% от максимальной |
К критериям второго уровня оценки твердости относятся: твердость по Бринеллю, твердость по Виккерсу, микротвердость, среднее контактное давление, поверхностная твердость, твердость по Мартенсу, твердость индентирования, твердость по Мейеру. Физическая сущность критериев оценки твердости второго уровня представлена в табл. 3.
Таблица 3. Критерии оценки твердости 2-й степени
Название критерия |
Сущность критерия |
Твердость по Бринеллю |
Отношение нагрузки к площади поверхности сферического отпечатка |
Твердость по Виккерсу |
Отношение нагрузки к площади поверхности пирамидального отпечатка |
Микротвердость по ГОСТ 9450-76 |
Отношение нагрузки, величиной до 2 Н, к площади поверхности пирамидального отпечатка |
Твердость по Мейеру |
Отношение нагрузки к площади проекции поверхности отпечатка |
Твердость индентирования |
Отношение максимальной нагрузки к площади проекции контакта индентора и материала |
Среднее контактное давление |
Отношение нагрузки к площади проекции контакта индентора и материала во всех точках нагрузочной ветви диаграммы индентирования |
Твердость по Мартенсу |
Отношение фиксированной нагрузки к площади внедренной в материал части индентора |
Поверхностная твердость |
Отношение нагрузки к площади внедренной в материал части индентора во всех точках нагрузочной ветви диаграммы индентирования |
Физическая сущность критериев оценки твердости второго уровня представлена в табл. 3.
Таблица 3. Критерии оценки твердости 2-й степени
Название критерия |
Сущность критерия |
Твердость по Русселю |
Отношение нагрузки к объему восстановленного отпечатка |
Твердость по Холлнагелю |
Отношение нагрузки к объему восстановленного отпечатка |
Твердость по Шпету |
Отношение максимальной нагрузки к произведению поверхности и глубины восстановленного отпечатка |
Твердость по Мартелго |
Отношение работы к объему восстановленного отпечатка |
Объемная твердость |
Отношение нагрузки к объему внедренной в материал части индентора во всех точках нагрузочной ветви диаграммы индентирования |
Третий уровень оценки твердости характеризуют такие критерии: твердость по Русселю, твердость по Холлнагелю, объемная твердость, твердость по Мартелю, твердость по Шпету.
Выводы
Общепринятая классификация способов расчета твердости, основанная на уровне прилагаемой нагрузки и глубине индентирования, не отражает современного понимания этого свойства и не учитывает весь объем информации, получаемой при испытаниях. В данной статье предложен новый подход к разделению существующих методов определения механических характеристик материалов, которые могут быть получены в процессе испытаний на твердость. Такая классификация возможна только на основании особенностей применяемых расчетных методик с учетом показателя степени глубины внедрения индентора в материал.
Литература:
1. Григорович В.К. Твердость и микротвердость металлов / В.К. Григорович. − М.: Наука, 1976. −230 с.
2. Энциклопедический словарь / под ред. Н.Н. Арсеньева, Е.Е. Петрушевского: Изд-во Ф.А. Брокгауз, И.А. Эфрон. –С.Пб.: Типогр. Акц. о-ва “Изд. дело”. − Брокгауз − Эфрон. − 1890 − 1907. − Т.х32а. − 1901. − С. 706-707.
Специализированный журнал “Промышленность и безопасность” – www. pbperm.ru
Короткая ссылка на новость: https://a-economics.ru/~EAZwI
Методы определения твердости металлов и способы ее повышения
Дата публикации: 02.06.2022
Содержание:
- Твёрдость металлов и сплавов: основные термины и понятия
- Основные методы закалки металла
- Диффузионные методы закалки металла
- Науглероживание и карбонитрирование
- Азотирование и нитрокарбюризация
Закалка металлов и сплавов (упрочнение поверхности) — это процесс, включающий в себя широкий спектр технологических методов, который используется для повышения износостойкости деталей без воздействия на более мягкую и прочную внутреннюю часть. Увеличение твёрдости металла полезно при изготовлении таких деталей, как кулачковая или кольцевая шестерня, подшипники или валы, рабочие органы плугом и культиваторов, которые должны иметь очень твёрдую поверхность для сопротивления износу, а также жёсткую внутреннюю поверхность для сопротивления ударам, возникающим во время эксплуатации. Твёрдость металлов и сплавов играет основную роль в процессе закалки.
Твёрдость металлов может характеризоваться как сопротивление проникновению, царапанию, резанию или истиранию. В зависимости от того, какое из перечисленных выше обстоятельств является наиболее интересным в конкретном случае, используются различные виды испытаний на твёрдость. Компоненты, влияющие на твёрдость металлов, включают микроструктуру, размер зерна, деформационное упрочнение и т. д. Обычно увеличение твёрдости металла до желаемого уровня осуществляется методом термической обработки или закалки.
Когда металлы подвергаются термической обработке, это влияет на их микроструктуру и позволяет легко изменять уровень твёрдости. Для определения твёрдости металлов широко используются следующие методы:
Испытание на твёрдость. Используется стальной шарик, который вдавливается в образец под действием различной нагрузки, которая поддерживается в течение 15-30 секунд. Затем рассчитывается число твёрдости по Бринеллю. Оно основано на площади вдавливания. Обычно это делается с помощью микроскопа. Если диаметр вмятины больше, это соответствует более низкому числу Бринелля и более мягкому материалу.
Испытание на твёрдость по Роквеллу. Проникающие элементы, используемые в твердомере Роквелла, варьируются от очень маленьких алмазных наконечников до стального шарика диаметром 3-4 см. Маленькие наконечники обычно используются для более твёрдых материалов, которые демонстрируют большую устойчивость к вдавливанию. Для различных материалов используются различные шкалы силы.
Существует два совершенно разных подхода к различным методам поверхностной закалки:
- Методы, предполагающие намеренное наращивание или добавление нового слоя.
- Методы, предусматривающие модификацию поверхности и подповерхности без намеренного наращивания или увеличения размеров детали.
Методы первой группы включают использование тонких плёнок, покрытий или накладок на сварные швы которые обычно становятся менее рентабельными при увеличении объёмов производства, особенно когда необходимо повысить прочность всей поверхности деталей. Усталостные характеристики плёнок, покрытий и накладок также могут быть ограничивающим фактором, в зависимости от прочности связи между основой и дополнительным слоем.
ДИФФУЗИОННЫЕ МЕТОДЫ ЗАКАЛКИ МЕТАЛЛА
Методы упрочнения диффузией включают несколько вариантов упрочняющих элементов (таких как углерод, азот или бор) и технологического метода, используемого для обработки и транспортировки упрочняющих элементов к поверхности детали. Технологические методы воздействия предполагают использование упрочняющих элементов в таких формах, как газ, жидкость или ионы. Эти вариации процесса естественным образом приводят к различиям в типичной глубине и твёрдости корпуса. Факторы, влияющие на пригодность конкретного метода диффузии, включают тип стали, желаемую твёрдость корпуса, глубину корпуса, желаемый профиль корпуса и стоимость.
НАУГЛЕРОЖИВАНИЕ И КАРБОНИТРИРОВАНИЕ
Науглероживание — это добавление углерода к поверхности низкоуглеродистой стали при температуре обычно между 850 и 980 ºC, при которой аустенит с его высокой растворимостью для углерода является стабильной кристаллической структурой. Закалка металлов и сплавов осуществляется, когда высокоуглеродистый поверхностный слой закаливается для формирования мартенситного слоя с хорошим сопротивлением износу и усталости, наложенного на прочную сердцевину из низкоуглеродистой стали. Из различных диффузионных методов наиболее широко используется газовое науглероживание, за которым следуют газовое азотирование и карбонитрирование.
АЗОТИРОВАНИЕ И НИТРОКАРБЮРИЗАЦИЯ
Азотирование — это поверхностно-упрочняющая термическая обработка, при которой азот вводится в поверхность стали при температуре от 500 до 550 °C, пока она находится в ферритном состоянии. Поскольку азотирование не включает нагрев до фазы аустенита с закалкой для образования мартенсита, основная цель закалки металла данным методом заключается в создании минимального искажения и точного контроля размеров.
Типы испытаний на твердость – Тестер твердости
Главная> Типы тестирования
Основы тестирования на твердость
Основы испытания на твердость
Тестирование на твердость Rockwell
Тест на твердость 9.
Измерение твердости по Виккеру
Измерение твердости по Виккеру
Измерение твердости по Либу
Измерение твердости по Либу
Измерение твердости — это самый простой, быстрый и экономичный метод оценки механических характеристик металлов. Качество твердости – это способность материала выдерживать ограничение другим твердым материалом. Для испытательного материала твердость означает включающие свойства эластичности, прочности, пластичности, износостойкости, ударной вязкости и других физических величин при определенном напоре, а также испытательной нагрузке. Основная цель этого испытания на твердость – определить применимость объекта или эффект размягчения или упрочнения объекта для использования. Поскольку испытание на твердость может воспроизвести изменение свойств металла при различном химическом составе, микроструктуре, а также в условиях термообработки, испытание на твердость можно широко использовать для изучения свойств металлов, контроля качества этапа термообработки, а также расширение новых материалов.
Существует два основных метода определения твердости металлов. Одним из них является метод медленного и безударного статического испытания. Здесь определение твердости зависит от глубины вмятины, размера области вмятины или площади выступа вмятины. Статические методы испытаний включают Роквелла, Бринелля, Виккерса, Лееба, Бэббита, Векслера и т. д. Среди них Роквелла, Бринелля и Лееба — три широко используемых метода определения твердости. Шкала Роквелла является наиболее часто используемой мерой при тестировании продукции. Согласно текущей статистике, твердомер Роквелла определяет около 70 % твердости металла. Другим типом метода тестирования является метод динамического тестирования, который звучит динамично, поскольку создает более эффективную тестовую силу. К этому типу относятся испытания на твердость по Шору и по Либу. Метод динамических испытаний обычно используется для определения твердости больших неподвижных заготовок.
Наша компания является экспертом в области определения твердости и предлагает приборы для измерения твердости по Бринеллю, Виккерсу, Роквеллу и Леебу. Они оценивают в реальных условиях, отбрасывая эффекты вибрации, прогиб детали из-за грязи, влияние оператора, окалины, а также изгиб образца под нагрузкой.
Здесь вы найдете основную информацию о различных типах испытаний, а также о методах определения твердости. Чтобы найти дополнительную информацию, перейдите по ссылке ниже, где вы найдете подробные сведения об их принципах работы, а также об их преимуществах. Если вы хотите приобрести твердомер, пожалуйста, нажмите кнопку «Спросите наших экспертов» внизу страницы. Наши инженеры свяжутся с вами в ближайшее время.
Основы измерения твердости
Здесь вы найдете более подробную информацию об измерении твердости, причинах проведения этого испытания, а также о различных соображениях, таких как размер образца, толщина и т. д.
Подробнее
Испытание на твердость по Роквеллу Твердость по Роквеллу определяет глубину пластической деформации отпечатка и измеряется в 0,002 мм как единица твердости. Использование различных отпечатков, а также испытательных усилий в тесте на твердость по Роквеллу показывает, что в различных комбинациях они эквивалентны соответствующим шкалам Роквелла. Есть три обычно используемые шкалы, где их приложения включают почти все обычно используемые металлы.
Знать о методе испытаний Роквелла и о том, как он измеряется.
Ученится больше
ТЕСТРИТЕЛЬНЫЕ ТАРКОСТИ VICKERSВИКЕРС противоположные поверхности, вдавливая в поверхность образца под определенной нагрузкой F, выдерживая его в течение статического периода времени после разгрузки, измеряя диагональную длину d отпечатка и, наконец, вычисляя площадь поверхности отпечатка, а также среднее давление на его площадь поверхности обозначает значение твердости металла по Виккерсу, обозначенное символом HV.
Узнать больше
Измерение твердости по Бринеллю Поскольку он был впервые предложен шведом Дж. А. Бринелля, этот прибор получил название твердости по Бринеллю. Закаленный стальной шарик диаметром D вдавливается в измеряемую металлическую поверхность с грузом размера P, удерживается в течение определенного периода времени, а затем разгружается. Соотношение нагрузки P и площади поверхности вдавливания F представляет собой значение твердости по Бринеллю, обозначаемое как HB.
Узнать больше
Измерение твердости по Леебу Определяется как удельная масса тела под действием силы упругости при определенном скоростном воздействии на поверхность образца, при ударе на расстоянии 1 мм от поверхности образца скорость отскока, а также расчетная скорость удара ценить.Подробнее
Нужна помощь?
Вы говорите нам, чего хотите, и мы сообщаем вам наше решение.
Спросите у наших экспертов
Спросите у наших экспертов
ИСПЫТАНИЯ НА ТВЕРДОСТЬ МАТЕРИАЛОВ
Испытания на твердость являются одним из наиболее часто используемых в промышленности методов определения качества таких материалов, как металлы. В этом посте мы объясним, из чего состоят эти тесты, каковы наиболее распространенные типы и как они проводятся в химических лабораториях.
Номер:
- Что такое испытания на твердость?
- Как измеряется твердость материалов?
- Scratch hardness tests
- Mohs scale
- Martens hardness test
- Penetration hardness tests
- Brinell hardness test
- Vickers hardness test
- Rockwell hardness test
- When are hardness tests performed?
Что такое испытания на твердость?
Испытания или испытания на твердость – это исследования, проводимые на различных материалах для оценки их стойкости к царапанью или проникновению других веществ . В целом, чем выше поверхностная твердость деталей, тем лучше их поведение в отношении износа, истирания или деформации при взаимодействии с окружающей средой.
Как измеряется твердость материалов?
Испытания на твердость можно отличить в зависимости от того, измеряют ли они устойчивость к царапанию или проникновению. В обоих случаях на поверхность образца наносят определенные материалы для оценки его твердости. Различие между различными модальностями заключается в характере используемых процедур.
Испытания на твердость при царапании
Шкала Мооса
Это первый метод измерения твердости материалов. Он работает с числовой шкалой, состоящей из 10 минералов , каждый из которых представляет степень твердости. Различные вещества классифицируются на шкале в зависимости от количества минералов, которые могут поцарапать их поверхность. Однако это несколько неточный метод, который не работает с металлами.
Испытание на твердость по Мартенсу
В этом типе испытания поверхности надрезаются алмазным конусом, приводимым в действие фиксированной силой , что делает его пригодным для более стойких веществ. Твердость материалов рассчитывается путем измерения ширины царапины, оставленной острием алмаза.
Испытания на твердость при пенетрации
Испытания на твердость по Бринеллю
Может использоваться с чрезвычайно мягкими материалами и железными металлами, если его поверхность не является сферической или цилиндрической. Инспекторный объект представляет собой небольшой стальной шарик (1-10 мм), который прикладывается с нагрузкой определенной силы для каждого типа материала. Твердость определяется путем измерения диаметра отпечатка с помощью микроскопической лупы.
Испытание на твердость по Виккерсу
В данном случае индентор представляет собой четырехугольную алмазную пирамиду с углом 136° между противоположными гранями . Это означает, что его можно использовать на сферических поверхностях и материалах с большей твердостью, чем тесты Бринелля. Окончательный результат достигается путем деления используемой силы на площадь метки, полученной индукцией.
Испытание на твердость по Роквеллу
Это наиболее распространенное исследование для определения твердости металлов из-за его простоты и легкости в использовании. Испытания на твердость по Роквеллу выполняются с помощью машины, которая измеряет глубину проникновения на поверхность образца , оставляя меньшую площадь, чем остальные процедуры.