Микрометр схема: Микрометр, микрометрический глубиномер, микрометрический нутромер
alexxlab | 12.09.2020 | 0 | Разное
Микрометр – что за инструмент и как им пользоваться? + видео
Иногда измерение линейных размеров какого-нибудь предмета требует от нас точности, которую не может позволить себе доступная нам канцелярская линейка, тогда на помощь приходит микрометр. Разнообразие принципов работы этого инструмента дает возможность совершенствовать точность измерений, и это устройство освоит даже начинающий мастер.
Устройство микрометра и точность измерений
Предельная точность была критически необходима еще в XVI веке в оружейном деле, позже принцип этого несложного механизма стали применять в геодезии, а официально прибор вышел в таком виде, каким мы его сейчас знаем, в середине XIX века. Устройство микрометра довольно простое в механическом смысле, рабочими являются винт и гайка. А вот сами измерения снимаются со сложной и тщательно выверенной шкалы, причем не одной.
Почему этот инструмент имеет такое название? Чаще всего, диапазон размеров, которые может с достоверной точностью определить этот прибор, лежит в области микрон. 1 мкм (микрон) это не что иное, как 0,001 мм, вы даже представить не можете, насколько это мелкие параметры. Но такие мелочи меряются редко, чаще точность составляет около 50 мкм (погрешность при этом 2-9 мкм), что также довольно мелко для человеческого глаза, но уже крайне важно для некоторых точных сборочных работ или настроек.
Способов измерения этим инструментом может быть два – абсолютный и относительный (контактный). При первом способе мы прикладываем разъем прибора непосредственно к предмету, выставляем согласно его геометрии зажимы и смотрим на шкалу, где сразу же определяем размер в мкм. Относительный способ измеряет какие-либо параметры рядом находящихся предметов или границ, а потом математически вычисляется искомый параметр.
Микрометр механический – особенности прибора
Традиционно мы привыкли наблюдать в работе микрометр механический, хотя сегодня даже небольшое усовершенствование в виде электронной индикации вполне доступно и значительно упрощает использование. Но об этом приборе чуть позже, а сейчас разберем основные особенности механики. Состоит он из двух ясно различимых частей: ручки (стебель, барабан и трещотка) и выемки для размещения измеряемой детали (полукруг с опорной стойкой и направленным на нее микрометрическим винтом).
Сам процесс измерения заключается в ручном закручивании ручки, чтобы сомкнуть винт. Как только эти элементы сошлись вокруг детали, крутят трещотку для подгонки, потом она начинает прокручиваться, это означает, что параметр замерен, остается снять показания на шкалах, которые расположены на стебле и барабане. Некоторые модели инструмента снабжены стопорным механизмом, чтобы зафиксированная величина не сбилась, пока вы будете записывать значение в журнал или сравниваете размер с другой деталью.
Электронный микрометр – в чем преимущество?
Мы уже упомянули, что электронный микрометр – это всего лишь немного усовершенствованный механический инструмент, но что же нам это дает на практике? Использование электронной индикации и возможности более точной калибровки привело к увеличению точности и удобству замеров этим прибором. Так он может показывать размеры с точностью до 1 мкм с погрешностью до 0,1 мкм. Многие инструменты обладают встроенной калибровкой.
Электронное табло, которым оснащен этот инструмент, может быть настроено на несколько систем отсчета, например, миллиметры или дюймы. Также там производитель размещает полезные индикации, вроде уровня заряда батареи. Для снижения энергопотребления механизм запрограммирован на определенное время бездействия, после которого самостоятельно отключается, чаще всего это 5 минут.
Как пользоваться микрометром – простые рекомендации
Изучив всю познавательную информацию о новом для вас приборе, самое время разобраться, как пользоваться микрометром, чтобы измерения были максимально точными, насколько позволяет имеющийся у вас инструмент.
Как пользоваться микрометром – пошаговая схема
Шаг 1: Проверка и калибровка
Время от времени, а также сразу после покупки, следует проверить ваш инструмент на наличие дефекта при измерении. В случае сбитой шкалы можно провести регулировку, для этого в комплекте всегда идет ключ. Для проверки точности прибора делается простая операция – смыкаются измерительные плоскости без детали. Когда винт упирается в противоположную плоскость, индикатор электронного микрометра должен показать 0. В механическом приборе барабан должен практически полностью закрыть стебель, его скошенный край обязан остановиться ровно на нулевой отметке шкалы стебля, а ноль барабана должен совпасть с продольным штрихом стебля.
Перед измерением обязательно выдержите деталь и инструмент для измерения в одном температурном режиме (в одном помещении) хотя бы 3 часа.
Шаг 2: Фиксация детали
Внешне кажется, что все просто на этом этапе, вставляй деталь и зажимай, что есть мочи. Но это не совсем так, прибор высокоточный, и любое усилие исказит ваши результаты, а еще страшнее, если это собьет тонкую настройку всей системы. Но для предотвращения самодеятельности в приборе придуманы специальные механизмы. Сначала вы доводите винт до детали, расположенной возле второй измерительной плоскости, простым вращением барабана. Как только почувствовали упор, пора немного сместиться по рукоятке и продолжить вращать трещотку, это самый крайний вращательный элемент. Как только вы услышали характерный щелчок, потом второй и третий – самое время остановиться. Это значит, что деталь надежно зафиксирована, и три щелчка об этом вас известили.
Шаг 3: Снимаем показания шкал
Электронный прибор покажет вам все на индикаторе, тут разбираться не нужно, где искать заветные цифры. А вот с механикой нужно приловчиться. Начинаем снимать измерения с самого крупного разряда цифр, заканчивая самым мелким. Первым делом смотрим на шкалу стебля, это та часть рукоятки, которая оставалась все это время неподвижной. На ней имеются две шкалы, но они для удобства восприятия находятся на одной оси, просто деления снизу обозначают миллиметры (каждое деление равняется 1 мм), а сверху – половинки миллиметра (шаг 0,5 мм).
В том месте, где остановился край барабана, смотрим, сколько делений по нижней (пусть 6) шкале осталось видимыми, так мы узнаем первую цифру (6 мм). Если край барабана поравнялся с каким-то делением верхней шкалы, то цифра после запятой будет 5, если деление спряталось, то пока что после запятой стоит ноль, но следом рассматриваем шкалу барабана, где найдем сотые доли миллиметра, которые и приплюсуются к десяткам. Например, на верхней шкале мы половинчатое деление не увидели, следовательно, пока что у нас 6,0 мм. Но на барабане с горизонтальным штрихом стебля совпала цифра 22, тогда 6,0 0,22=6,22 мм. Если бы штрих на верхней шкале стебля был виден, то было бы 6,5 мм, и уже к нему прибавляли бы 0,22, получилось бы 6,72 мм.
Для подсчета приведен общий случай для самого распространенного в хозяйстве вида этого прибора.
Но для каждого инструмента значение штрихов будет определяться его классом точности, поэтому сначала посмотрите, что значит разметка на шкалах, а потом начинайте подсчеты.
Оцените статью: Поделитесь с друзьями!
главная основы элементы примеры расчетов любительская технология общая схемотехника радиоприем конструкции для дома и быта связная аппаратура телевидение справочные данные измерения обзор радиолюбительских схем в журналах обратная связь
Реклама |
В журнале “Радио” номер 7 , страница 43 за 1971 год была опубликована схема электронного микрометра для измерения диаметра обмоточного провода от 0,2 до 1,6 миллиметра: Схема представляет собой высокочастотный генератор на частоту около 15 мегагерц, собранный на транзисторах Т1 и Т2 и измерительный блок. ![]() Во время положительных полупериодов ток протекает через диод Д2, контур L3С6С7, переменный резистор R5 и микроамперметр, а во время отрицательных полупериодов – через диод Д1, переменные резисторы R6,R5 и микроамперметр. Катушка L3 служит датчиком микроамперметра. Эта катушка, а также конденсаторы С6 и С7 образуют контур, резонансная частота которого несколько меньше частоты генератора. Для того, чтобы измерить диаметр провода, его вводят внутрь катушки L3. Индуктивность катушки, а следовательно и частота настройки контура, и ток, протекающий по ветви Д2-L3-С6С7- R5- микроамперметр, изменяются и стрелка последнего отклоняется от нуля. ![]() Катушка L1 намотана на полистироловом каркасе диаметром 10 миллиметров в один слой, ширина намотки 10 миллиметров. Катушка содержит 21 виток провода ПЭВ – 0,31 мм с отводом от середины. Катушка L2 намотана поверх катушки L1 и содержит 10 витков того же провода. Катушка L3 намотана на керамическом каркасе с внешним диаметром 4, внутренним 2 миллиметра. Катушка намотана в один слой, ширина намотки 10 миллиметров, и содержит 42 витка, провод ПЭВ – 0,2 мм. Все детали микрометра собраны на плате с размерами 65 на 45 миллиметров, которая прикреплена к лицевой панели прибора перпендикулярно с таким расчетом, чтобы один из торцов катушки L3 проходил в отверстие, сделанное в панели. ![]() Налаживание прибора сводится к подбору емкостей конденсаторов С2 и С7 с таким расчетом, чтобы частота генератора была несколько выше резонансной частоты измерительного контура L3С6С7 и установке стрелки микроамперметра на последнее деление шкалы при помощи резистора R5. Шкалу микроамперметра градуируют непосредственно в долях миллиметра при помощи эталонных отрезков провода (измеряем микрометром). Перед измерениями необходимо, нажав кнопку Кн1, установить стрелку микроамперметра на нуль при помощи резистора R6. Далее вставляем отрезок измеряемого провода во внутрь катушки и, нажав кнопку выключателя питания, производим измерение. |
микрометр
Министерство образования АР Крым
Таврический
Национальный Университет им. Вернадского
Исследование физического прибора
МИКРОМЕТР
Выполнил: студент 1 курса
физического факультета гр. Ф-111
Потапов Евгений
Симферополь-2010
План:
1. Название. 2. Принцип действия. 3. Схема устройства прибора -основные части -их размещение -взаимодействие 4. Эксплуатационные характеристики. 5. Правила пользования. 6. Область применения прибора.
Название:
Микро́метр — универсальный инструмент (прибор), предназначенный для измерений линейных размеров абсолютным контактным методом в области малых размеров с высокой точностью (до 2 мкм), преобразовательным механизмом которого является микропара винт — гайка.
Принцип действия:
Действие микрометра
основано на перемещении винта
вдоль оси
при вращении его в неподвижной гайке. Перемещение пропорционально углу
поворота винта вокруг оси . Полные
обороты отсчитывают по шкале,
нанесённой на стебле микрометра, а доли
оборота — по круговой шкале, нанесённой
на барабане. Оптимальным является
перемещение винта в гайке лишь на длину
не более 25 мм
из-за трудности изготовления винта с
точным шагом на большей длине. Поэтому
микрометр изготовляют несколько
типоразмеров для измерения длин от 0 до
25 мм, от 25 до 50 мм и т. д. Для
микрометров с пределами измерений от
0 до 25 мм при сомкнутых измерительных
плоскостях пятки и микрометрического
винта нулевой штрих шкалы барабана
должен точно совпадать с продольным
штрихом на стебле, а скошенный край
барабана — с нулевым штрихом шкалы
стебля. Для измерений длин, больших
25 мм, применяют микрометр со сменными
пятками; установку таких микрометров
на ноль производят с помощью установочной
меры, прикладываемой к микрометру, или
концевых
мер.
Измеряемое изделие зажимают между
измерительными плоскостями микрометра.
Обычно шаг винта равен 0,5 или 1 мм и
соответственно шкала на стебле имеет
цену деления 0,5 или 1 мм, а на барабане
наносится 50 или 100 делении для получения
отсчёта 0,01 мм.
Схема устройства прибора:
Микрометр состоит из стальной скобы , к которой присоединяется трубка , имеющая внутреннюю винтовую нарезку. При работе, микрометр держат так, чтобы скоба была обращена к работающему, а трубка располагалась справа от нее.
В трубку входит винт, скрепленный с гильзой и выходящий наружу в виде стержня
.
Если шаг винта равен мм, то при одном обороте винт и связанная
с ним гильза перемещаются вправо или влево на мм. Следовательно, расстояние между
концом стержня и упором можно отсчитать по положению гильзы
.
На трубке нанесен масштаб, позволяющий отсчитать, на сколько целых делений отодвинулась гильза от нулевого положения. На самой гильзе нанесены деления, дающие возможность оценить, на какое расстояние отошла гильза от ближайшего целого деления слева на трубке . Если гильза по окружности разделена на делений, то при повороте гильзы на одно деление сама гильза перемещается поступательно на мм.
Эксплуатационные характеристики:
Характеристики некоторых микрометров, выпускаемых в СССР
Тип микрометра | Пределы измерений, мкм | Погрешность, мкм |
Гладкий Рычажный Листовой Трубный Зубомерный Настольный | от 0 до 600 от 0 до 2000 от 0 до 5; 10; 25 от 0 до 10: 25 от 0 до 100 от 0 до 10: 20 | ± (2—10) ± (3—4) ± 4 ± 4 ± 5 ± (2—3) |
Правила пользования:
Прежде, чем
пользоваться микрометром, нужно проверить
правильность его установки на нуль. Для
этого поворачивают гильзу до тех пор, пока стержень не коснулся упора
.
Завинчивание следует производить,
пользуясь головкой
,
поворачивающейся с некоторым трением,
что исключает возможность сильного
нажима на измеряемый предмет и обеспечивает
постоянный нажим при измерениях. Если
конец стержня касается вплотную упора
,
то в случае правильной установки прибора,
обрез гильзы должен совпадать с нулевым делением
основного масштаба и нулевое деление
гильзы должно точно совпадать с нулевой чертой
на трубке
.
После проверки правильности установки
прибора следует:
а) определить шаг винта, т.е. расстояние, на которое перемещается винт и гильза за один оборот;
б) рассчитать, на какую долю миллиметра передвинется гильза при повороте на одно деление и приступить к измерениям.
Для определения
длины тела, следует поместить его между
выступами и
,
и вращать гильзу при помощи головки до тех пор, пока измеряемое тело не будет
зажато между выступами и
. После этого отсчитать число целых
делений на трубке до гильзы и число делений, на которое повернулась
гильза
.
Зная цену деления гильзы
,
подсчитать, на какую долю миллиметра
отодвинута гильза от ближайшего левого
деления на трубке
.
Сумма обоих отсчетов определит искомую
длину.
Область применения прибора:
В зависимости от конструкции (формы корпуса или скобы, в которую встраивается микропара, формы измерительных поверхностей) или назначения (измерение толщины листов, труб, зубьев зубчатых колёс) микрометры разделяют на гладкие, рычажные, листовые, трубные, проволочные, призматический, канавочные, резьбомерные, зубомерные и универсальные.
Микрометры
выпускаются ручные и настольные, в том
числе со стрелочным отсчётным
устройством.
Микрометрические пары используются
также в глубиномерах,
нутромерах
и других измерительных средствах.
Наибольшее распространение имеют
гладкие
микрометры.
Настольные микрометры (в том числе со
стрелочным отсчётным устройством)
предназначаются для измерения маленьких
деталей (до 20 мм), их часто называют
часовыми микрометрами.
6
Как правильно пользоваться микрометром:видео,технология измерений
На рынке сейчас встречается множество типов и моделей данного устройства, но принцип их действия и правила пользования микрометром почти всегда остаются одинаковыми, так как исключение составляют лишь электронные модели. Механические же делаются по одному и тому же принципу, но с различными особенностями, в зависимости от измеряемых предметов.
Устройство микрометра
Прежде чем разобраться, как мерить микрометром, нужно узнать устройство данного прибора. Стандартные модели состоят из таких составляющих как:
фото:устройство микрометра
- Скоба – эта деталь должна быть достаточно жесткой, так как даже небольшая деформация может привести к большим ошибкам измерения и, соответственно, прибор можно будет считать сломанным из-за погнутой скобы;
- Пятка – зачастую она запрессована в сам корпус, но встречаются и модели со сменной пяткой.
Такие варианты встречаются у микрометров, диапазон измерения которых составляет от 500 до 800 мм;
- Винт микрометрический – его вращение происходит путем перемещения вращающейся трещотки;
- Стопорное устройство – данный элемент выполняется в виде зажима винтового. Его используется для фиксации винта микрометрического, когда происходит снятие показаний или очередная настройка прибора;
- Стебель – на этом элементе имеются две шкалы: основная и дополнительная. На основной показано количество целых миллиметров измеряемой детали. На дополнительной показывается количество половин миллиметров;
- Барабан – эта деталь показывает отсчет десятых и сотых долей миллиметра. Для шкалы стебля барабан является указателем;
- Трещотка – с ее помощью происходит вращение винта микрометрического, а также регулируется усилие, которое прикладывается к измерительной поверхности микрометра;
- Эталон – эта деталь находится вне самого устройства, но является его неотъемлемой частью, так как она служит для поверки, перед тем как производить измерение микрометром.
Технология использования микрометра
Зная устройство прибора, можно более подробно узнать, как пользоваться микрометром. Схема действий здесь весьма проста, но нужно правильно придерживаться порядка выполнения операций. Для этого требуется:
- Первым делом нужно установить измеряемый предмет между такими частями как пятка и микрометрический винт. При этом нужно вращать барабан, чтобы шпиндель был максимально близко к измеряемому предмету. Держать инструмент требуется левой рукой за изолированную часть дуги. В ином случае, она может нагреться от тепла тела, так что показания будут неверными;
- Шпиндель понемногу следует приблизить вплоть до соприкосновения с поверхностью измеряемого предмета. Если смотреть с торца, где сделана нарезка, то крутить нужно против часовой стрелки. Это нужно делать, пока деталь не зайдет в зазор торцов. После этого можно продолжать вращение до упора о часовой стрелке. При закручивании следует держаться за нарезку на конце барабана.
Когда концы упрутся в поверхность, во время вращения будет идти звук, как от трещотки;
- Точный размер замеряется при помощи шкалы нониуса на барабане. Когда вы снимите данные, то нужно перевести микрометры в миллиметры;
- После снятия точных размеров можно вращать все в обратном направлении, чтобы освободить деталь из зажимов.
Определение показаний прибора
Наличие нескольких шкал на одном устройстве создает трудности для тех, кто не знает, как пользоваться микрометром. Главное, правильно анализировать показания каждой шкалы:
фото:как правильно пользоваться микрометром
Указатель для шкалы «2» на стебле является торец барабана. Для круговой шкалы «3» указателем является продольный штрих «1». Шкала с цифрами показывает количество миллиметров. Ее верхняя часть без цифр – половины. Для снятия показаний отмечается последний полный штрих нижней шкалы прибора (на рисунке – черта зеленого цвета). Он указывает на целое число миллиметров.
Далее следует глянуть, есть ли справа от него на верхней шкале еще одна черта (на рисунке отмечена синим цветом). Если такова имеется, то добавляется еще 0,5 мм к имеющемуся значению. Когда идет подсчет показаний круговой шкалы «3», то в расчет берут то значение, которое совпадает с продольным штрихом на шкале «1». Чтобы более детально понять, как пользоваться микрометром видеоурок поможет получить более полное представление о данном процессе.
Таким образом, если вы поняли, как правильно пользоваться микрометром, то можно легко подсчитать сумму на втором рисунке. 17 мм на нижней шкале + 0,5 мм на верхней + 0,25 мм на барабане. Таким же образом можно понять, сколько микрометров в миллиметре, так как шкала показывает сотые доли. Итого: на нижнем рисунке микрометр показывает 17,75 мм.
Проверка точности и калибровка
Естественно, что все снятия показаний производятся при помощи поверенного устройства, показывающего точные данные. Для проверки точности используют эталоны, которые идут в комплекте. Дело в том, что для каждого предела измерений и соответствующей модели применяются свои детали. Таким образом, эталон имеет определенную длину, которая вписывается в заданный предел. Если при измерении микрометр показал нужные данные, то им можно пользоваться в дальнейшем. Но желательно делать поверку перед каждым использованием.
Учитывая все правила и предписания, здесь точно узнаете, как пользоваться микрометром, вне зависимости от его модели и диапазона измерений.
Интересует аренда склада Одесса? Заходите на knin.com.ua и выбирайте помещение. Очень низкие цены!
МИКРОМЕТРЫ РЫЧАЖНЫЕ ТИПА МР ,МРИ ГОСТ 4381-87
Угол /2 должен быть не более 20°. Конструкцией микрометра должен быть обеспечен гарантированный зазор между барабаном и стеблем.
2.1.7. Микрометры должны иметь стопорное устройство для закрепления микрометрического винта.
2.1.8. Микрометры должны иметь устройство, арретирующее подвижную пятку.
2.1.9. Конструкцией микрометров должна быть обеспечена возможность установки их в нулевое положение при соприкасании измерительных поверхностей между собой или с установочной мерой. При таком совмещении начальный штрих шкалы стебля должен быть виден целиком, но расстояние от торца конической части барабана до ближайшего края штриха не должно превышать 0,1 мм.
2.1.10. (Исключен, Изм. N 1).
2.1.11. Измерительная поверхность микрометрического винта должна быть плоской. Измерительная поверхность подвижной пятки микрометров с верхним пределом измерений до 300 мм должна быть плоской, а свыше 300 мм — сферической.
2.1.12. Радиус сферы подвижной пятки микрометров с верхними пределами измерений более 300 мм должен быть 80 — 120 мм.
2.1.13. Измерительные поверхности микрометров должны быть оснащены твердым сплавом. По заказу потребителя микрометры следует изготовлять с закаленными измерительными поверхностями. Твердость закаленных измерительных поверхностей должна быть не ниже 61 .
2.1.14. Параметр шероховатости измерительных поверхностей микрометров — Ra <= 0,04 мкм по ГОСТ 2789.
2.1.15. Допуск плоскостности измерительных поверхностей микрометров с верхним пределом измерений до 100 мм — 2 интерференционные полосы, а свыше 100 мм — 3 интерференционные полосы. Допускаются завалы на расстоянии 0,2 мм от краев измерительных поверхностей для микрометров с верхним пределом измерения до 50 мм и на расстоянии 0,5 мм — для микрометров с верхним пределом измерения свыше 50 мм.
2.1.16. Допуск соосности микрометрического винта и пятки микрометров с пределами измерений до 50 мм — 0,1. (Измененная редакция, Изм. N 1).
2.1.17. У микрометров типа МР при нажиме на измерительные стержни (микрометрической головки и отсчетного устройства) в направлении, перпендикулярном к оси с усилием 1 Н, изменение показаний по шкале отсчетного устройства не должно превышать 1/2 деления.
2.1.18. Измерительный механизм микрометров должен работать плавно.
2.1.20. Установочные меры длиной до 275 мм следует изготовлять с двумя плоскими поверхностями, а свыше 275 мм — с одной плоской и одной сферической поверхностями.
2.1.21. Допускаемые отклонения длины от номинальных размеров, суммарный допуск плоскостности и параллельности, а также допуск плоскостности измерительных поверхностей установочных мер — по табл. 3.
2.1.22. Допуск биения измерительных поверхностей относительно оси установочной меры длиной более 275 мм не должен превышать половины допуска на размер. При проверке биения меру следует устанавливать на две опоры в точках, расположенных на расстоянии 0,21 L от концов меры, где L — длина установочной меры.
2.1.23. Измерительные поверхности установочных мер должны быть закалены. Твердость измерительных поверхностей установочных мер должна быть не ниже 61 .
2.1.24. Параметр шероховатости измерительных поверхностей установочных мер для микрометров с верхним пределом измерений до 100 мм — Ra <= 0,04 мкм, а свыше 100 мм — Ra <= 0,08 мкм по ГОСТ 2789.
2.1.25. Наружные поверхности микрометров и установочных мер, за исключением подвижной пятки, микрометрического винта и измерительных поверхностей, должны иметь противокоррозионное покрытие. На наружных поверхностях микрометров и установочных мер не должно быть дефектов, влияющих на эксплуатационные характеристики.
2.1.26. Наружные поверхности скоб микрометров и установочные меры номинальной длиной 50 мм и более (за исключением концевых мер длины класса точности 1 по ГОСТ 9038) должны быть теплоизолированными.
2.1.27. Средняя наработка микрометров на отказ должна составлять не менее 550000 условных измерений.
Примечание. Под условным измерением понимают однократное возвратно-поступательное перемещение подвижной пятки в пределах участка шкалы, на котором нормируют погрешность.
2.1.27.1. Критерием отказа является невыполнение требований пп. 2.1.2 и 2.1.4 (в части предела допускаемой погрешности).
2.1.28. (Исключен, Изм. N 1).
2.1.29. Полный средний срок службы микрометров — не менее 6 лет.
2.1.30. (Исключен, Изм. N 1).
2.1.30.1. Критерий предельного состояния микрометров — предельное состояние отсчетного устройства, обусловленное предельным износом или поломкой контактных элементов рычажной системы или узла подвески измерительного рычага.
2.1.31. Среднее время восстановления работоспособного состояния микрометров — не более 4 ч (включая время на поверку микрометров после восстановления).
2.1.32. (Исключен, Изм. N 1).
2.2. Комплектность
2.2.1. В комплект микрометра должны входить: сменные пятки к микрометрам с верхним пределом измерения свыше 150 мм — 1 комплект; установочные меры к микрометрам с верхним пределом измерения до 300 мм — 1 шт., свыше 300 до 1000 мм — 2 шт., свыше 1000 мм — 4 шт.; центровочные гильзы для микрометров с верхним пределом измерения свыше 300 мм — 1 комплект; ключ для регулирования микрометров (если предусмотрен конструкцией).
2.2.2. К микрометру должен быть приложен паспорт по ГОСТ 2.601, включающий инструкцию по эксплуатации.
2.3. Маркировка
2.3.1. Маркировка микрометров — по ГОСТ 13762.
2.3.2. На установочной мере должен быть нанесен номинальный размер; для мер свыше 300 мм — штрихи на расстоянии 0,21 L от концов мер, где L — длина установочной меры.
2.3.3. В паспорте микрометров при их сертификации проставляется национальный знак соответствия по ГОСТ 28197. (Измененная редакция, Изм. N 1).
2.4. Упаковка
2.4.1. Упаковка микрометров — по ГОСТ 13762.
2.4.2. Микрометры должны быть упакованы в деревянный или пластмассовый футляр. Микрометры с верхним пределом измерения от 1000 до 2000 мм допускается укладывать в футляры, закрывающие только измерительную часть и установочные меры. (Измененная редакция, Изм. N 1).
2.4.3. Микрометры в упаковке для транспортирования должны выдерживать: транспортную тряску ускорением 30 м/с2 при частоте 80 — 120 ударов в минуту; перепад температур от минус (50 +/- 3) °C до плюс (50 +/- 3) °C и относительную влажность (95 +/- 3)% при температуре 35 °C.
3. ПРИЕМКА
3.1. Для проверки соответствия микрометров требованиям настоящего стандарта проводят государственные испытания, приемочный контроль, периодические испытания и испытания на надежность.
3.2. Государственные испытания — по ГОСТ 8. 383 и ГОСТ 8.001.
3.3. При приемочном контроле каждый микрометр следует проверять на соответствие требованиям пп. 1.2 (в части поверки измерительного усилия и его колебания), 2.1.2 (за исключением проверки изменений показаний микрометра от изгиба скобы), 2.1.4, 2.1.5.2, 2.1.6, 2.1.6.2 — 2.1.7, 2.1.9 — 2.1.11, 2.1.14 — 2.1.22, 2.1.24 — 2.1.26.
3.4. Периодические испытания проводят не реже раза в три года на не менее трех микрометрах из числа прошедших приемочный контроль на соответствие всем требованиям настоящего стандарта, кроме пп. 2.1.27 — 2.1.31.
Если при испытаниях обнаружено, что изделия соответствуют всем требованиям настоящего стандарта, то результаты периодических испытаний считают положительными.
3.5. Подтверждение показателей надежности (пп. 2.1.27 — 2.1.31) проводят не реже раза в три года по программе испытаний на надежность, разработанной в соответствии с ГОСТ 27.410 <*>.
———————————
<*> В части раздела 2 заменен ГОСТ 27. 301.
Допускается совмещение испытаний на надежность с периодическими испытаниями.
3.4, 3.5. (Измененная редакция, Изм. N 1).
4. МЕТОДЫ КОНТРОЛЯ И ИСПЫТАНИЙ
4.1. Проверка микрометров должна проводиться по ГОСТ 8.411.
4.2. При проверке влияния транспортной тряски используют ударный стенд, создающий тряску ускорением 30 м/с2 при частоте 80 — 120 ударов в минуту.
Микрометры в упаковке крепят к стенду и испытывают при общем числе ударов 15000. После испытаний погрешность микрометров не должна превышать значений, указанных в табл. 2.
Допускается проводить испытания микрометров транспортированием на грузовой машине со скоростью от 20 до 40 км/ч на расстояние 100 км по грунтовой дороге.
4.3. Воздействие климатических факторов внешней среды при транспортировании проверяют в климатических камерах в следующих режимах: при температуре минус (50 +/- 3) °C, затем плюс (50 +/- 3) °C и далее при влажности (95 +/- 3)% при температуре 35 °C. Выдержка в климатической камере по каждому виду испытаний — не менее 2 ч. После испытаний погрешность микрометров и допускаемое изменение показаний от изгиба скобы не должны превышать значений, указанных в п. 2.1.2. (Измененная редакция, Изм. N 1).
4.4. (Исключен, Изм. N 1).
5. ТРАНСПОРТИРОВАНИЕ И ХРАНЕНИЕ
5.1. Транспортирование и хранение микрометров — по ГОСТ 13762.
6. УКАЗАНИЯ ПО ЭКСПЛУАТАЦИИ
6.1. Применение рычажных микрометров на месте эксплуатации должно соответствовать паспорту на микрометры.
7. ГАРАНТИИ ИЗГОТОВИТЕЛЯ
7.1. Изготовитель гарантирует соответствие микрометров требованиям настоящего стандарта при соблюдении условий эксплуатации, транспортирования и хранения. Гарантийный срок хранения микрометров — 24 мес со дня выпуска. Гарантийный срок эксплуатации — 12 мес со дня ввода микрометров в эксплуатацию в период гарантийного срока хранения. (Измененная редакция, Изм. N 1).
Рычажный микрометр – Большая Энциклопедия Нефти и Газа, статья, страница 4
Рычажный микрометр
Cтраница 4
Устройство рычажного микрометра такое же, как и обычного микрометра, с той лишь разницей, что у него отсутствует трещотка.
[47]
Измерение рычажным микрометром производится следующим образом. Проверяемая деталь вводится между его измерительными поверхностями. Медленно вращают микрометрическую головку до появления стрелки в поле шкалы в скобе. Далее точно совмещают штрих на барабане микрометрической головки с продольным штрихом на стебле. [48]
В рычажных микрометрах и скобах ( рис. 6.5) при измерении чувствительная пятка /, перемещаясь, воздействует на рычаг 2, зубчатый сектор которого поворачивает зубчатое колесо 3 и стрелку, неподвижно укрепленную на его оси. Пружина 4 постоянно прижимает колесо 3 к зубчатому сектору, устраняя таким образом мертвый ход. У рычажной скобы микровинт 5 не имеет отсчетного устройства, оно есть на микровинте рычажного микрометра. [49]
В рычажных микрометрах или скобах ( рис. 39, а) при измерении чувствительная пятка /, перемещаясь, действует на рычаг 2; зубчатый сектор поворачивает колесо 3 и стрелку, укрепленную неподвижно на его оси. Пружина 4 постоянно прижимает колесо 3 к зубчатому сектору, устраняя, таким образом, мертвый ход.
[51]
Так как рычажные микрометры оснащены стрелочным отсчетным устройством, то их микрометрическая пара не имеет трещотки. При непосредственном измерении размеров измерительную пятку микрометра доводят до соприкосновения с деталью ( вращая винт) и добиваются положения, при котором один из штрихов барабана совпадает с каким-либо штрихом на стебле. В это время стрелка отсчетного устройства не находится в крайнем положении. Целые значения размера берутся по микропаре, а дробные – по стрелочному от-счетному устройству. [52]
ЛИЗя с Рычажный микрометр по рычажной системе нижним качающим – ничем не отличается от рычажной скобы. При вращении барабана микрометра и достижении размера эталона стрелка устанавливается на нуль. При проверке размеров изделия вращать барабан не нужно. В случае использования микрометра для абсолютного измерения барабан микрометра вращают до тех пор, пока стрелка не установится на нуле. Показания снимают, как у обычного микрометра.
[53]
Серийно выпускают рычажные микрометры типа МР ( ГОСТ 4381 – 80) с диапазоном измерения – 25 мм, ценой деления отчетного устройства 2 мкм, диапазоном показаний не менее 0 14 мм, измерительным усилием – 6 0 1 0 Н и допускаемой погрешностью 1 мкм. [55]
Измерительная цепь рычажного микрометра представляет собой соединение механизмов микрометра и рычажной скобы, причем отсчет миллиметров, их десятых и сотых долей производится обычным способом по микрометру, когда стрелка отсчетного устройства находится вблизи нулевой отметки шкалы, а тысячные доли отсчитывают по той же шкале, когда барабан микрометра довернут до положения, при котором ближайшая отметка его круговой шкалы совпадает с продольным штрихом шкалы стебля.
[56]
Наружный вид рычажного микрометра представлен на рис. 7.12, а его кинематическая схема на рис. 7.13. Там же имеются его описание и основные зависимости, характеризующие работу механизма. [57]
При относительных измерениях рычажный микрометр настраивают по блоку концевых мер требуемого размера, путем перемещения микрометрического винта. [58]
В СССР выпускаются рычажные микрометры трех типов: МР ( микрометр рычажный) с пределами измерения О-25 и 25 – 50 мм, они находят применение в основном в индивидуальном и мелкосерийном производстве для измерения наружных размеров; МРЗ с пределами измерения 0 – 20 и 20 – 45 мм, служащие для измерения длины общей нормали зубчатых колес, и МРИ с пределами измерения до 2000 мм, оснащенные измерительными головками. [59]
В отличие от рычажных микрометров и скоб на микрокаторе не устанавливают предварительно поле допуска, а сразу же определяют отклонения. Каждый указатель микрокатора перемещается самостоятельно.
[60]
Страницы: 1 2 3 4
Механический измерительный инструмент – Слесарно-инструментальные работы
Механический измерительный инструмент
Категория:
Слесарно-инструментальные работы
Механический измерительный инструмент
Механическими называются инструмент и приборы, передающие при помощи промежуточных передач на шкалу увеличенные отклонения в размерах у измеряемой детали. Такое увеличение отклонений достигается в этих приборах зубчатыми или рычажными механизмами.
Рис. 1. Часовой индикатор: а — внешний вид; б — внутреннее устройство.
Индикатор часового типа (рис. 1), являющийся одним из таких механических инструментов, действует при помощи зубчатого механизма. Подобный индикатор имеет две шкалы и используется для измерения величины отклонений, не превышающих одного миллиметра. Большая шкала индикатора разделена на 100 частей, каждая из которых соответствует 0,01 мм. Малая шкала инструмента позволяет отсчитывать перемещения измерительного штифта, доходящие до 5—10 мм, в зависимости от особенностей конструкции механизма. Установка шкалы индикатора в нулевое положение достигается вращением от руки его наружной обоймы.
В этой конструкции индикатора, через всю его длину во втулках проходит измерительный штифт с зубчатой рейкой, нарезанной на поверхности штифта. В нижнем конце штифта установлен наконечник с шариком, образующим измерительную поверхность. Зубья рейки измерительного штифта соединяются с шестерней, сидящей на одной оси с большой шестерней, передающей в свою очередь движение шестеренке и, следовательно, стрелке. Поворот маленькой стрелки, указывающей перемещение и мерительного штифта в миллиметрах, производится шестерней.
Измерительное давление индикатора создается пружиной и, действующей на направляющую планку. Мертвый ход в узлах механизма устраняет пружина, стремящаяся повернуть все зубчатые соединения в одном и том же направлении.
Пределы измерения индикатором еще более ограничены, чем это указывается на его циферблате. Поэтому не следует пользоваться индикатором для определения отклонений, превышающих 1 мм, так как при пользовании всей шкалой увеличиваются погрешности измерения.
Чтобы произвести измерение индикатором, его укрепляют на измерительном столике, штангенрейомусе или универсальной стойке и дают измерительному штифту натяжение, позволяющее пользоваться срединой шкалы индикатора. Небрежное отношение к индикатору, резкое перемещение штифта, удары, боковое давление на штифт, попадание абразивной пыли в механизм быстро приводят индикатор в негодность.
Область применения индикаторов весьма обширна и они служат главной конструктивной частью многих индикаторных измерительных приборов: глубиномеров, нутромеров, шагомеров, зубомеров и т. д.
Примером такой конструкции прибора для точных измерений диаметров отверстий может служить применение индикатора часового типа для внутренних измерений. Для этой цели на его нижнюю направляющую втулку надеваются специальные наконечники, превращающие боковое давление на измерительный штифт индикатора в давление, направленное вдоль его оси. Такой прибор называется индикаторным нутромером или прибором для внутренних измерений. Индикаторный нутромер при настройке его по точному микрометру позволяет производить относительные измерения диаметров отверстий с точностью 0,01 — 0,015 мм. Обычно нутромер имеет два колка, один из которых подвижен и передает отклонения индикатору через рычаг или наклонную плоскость. Колки у прибора — сменные.
Индикаторные нутромеры изготавливаются комплектами: каждым комплектом можно производить измерения диаметров отверстий в одном из следующих пределов: от 6 до 18, от 18 до 35, от 35 до 50, от 50 до 100, от 100 до 160, от 160 до 250, от 250 до 450 и так до 1000 мм.
Также широко распространены, особенно при изготовлении приспособлений, другие типы индикаторов: рычажные с пределом измерения + 0,1 мм и рычаж. но-зубчатые с пределом измерения + 0,5 мм.
Индикаторы рычажные и рычажно-зубчатые отличаются малыми габаритными размерами и удачно приспособлены для передачи боковых давлений. Эта особенность делает их незаменимыми при определении отклонений в труднодоступных местах или при измерении расстояний между отверстиями (расстояния от боковой стенки одного отверстия до боковой стенки другого).
Принцип действия рычажно-зубчатого индикатора находит применение и в конструкции рычажного микрометра. Рычажный микрометр или микрометр-индикатор представляет собой микрометр, в скобе которого находится рычажно-зубчатое индикаторное устройство. Индикаторное устройство микрометра выполняет роль его трещотки и служит указателем давления измерительных плоскостей на деталь. Поэтому при измерениях таким микрометром во всех случаях следует сохранять нулевое положение стрелки. Нулевому положению стрелки индикатора должно соответствовать нулевое деление на барабане.
Как видно из схемы, индикаторное устройство действует следующим образом. Пятка микрометра все время находится под давлением пружины и, таким образом, нажимая на рычаг, отводит его сектор в крайнее положение. ‘Если между пяткой и шпинделем поместить деталь, размер которой несколько больше расстояния между ними, пятка, преодолев усилие пружины, переместится влево. Это даст возможность малому плечу рычага, получившему свободу, также повернуться влево при помощи шестерни, находящейся под действием пружины. Стоящая на оси шестерни стрелка отметит на циферблате это перемещение пятки микрометра. Индикаторное устройство микрометра позволяет пользоваться им для определения предельных отклонений как скобой после установки шпинделя по блоку концевых мер в нулевое положение, отмечаемое стрелкой индикатора, и после закрепления его стопором. После этого указатели предельных отклонений (не показанные на схеме) устанавливаются на свои места и измеряемый предмет пропускается между измерительными плоскостями. Если при этом стрелка окажется между указателями, то размер детали находится в пределах установленного допуска.
В том случае, если нужно узнать фактический размер этого предмета, то к показаниям на шкалах стебля и барабана добавляют (или вычитают в зависимости от того, в какой стороне находится стрелка) величину отклонения стрелки индикатора. Чтобы не испортить микрометр при измерении размера между двумя плоскостями, его пятку отводят влево, нажимая пальцем на кнопку, действующую на рычаг.
Рычажным микрометром производятся измерения отклонений, не превышающих + 0,02 мм.
Вершиной той точности, которая может быть достигнута при использовании измерительных устройств с механическим рычагом, является процесс измерения миниметром.
Рис. 2. Индикаторный нутромер. а-общий вид; б – конструкция наконечника.
Рис. 3. Индикаторы: а – рычажный; б – рычажно-зубчатый.
Рис. 4. Рычажный микрометр (схема).
Опоры рычажного устройства миниметра имеют ноже-образную форму и уже только эта особенность его конструкции позволяет получить очень малое плечо рычага (около 0,1 мм), а, следовательно, и большое передаточное отношение прибора. В связи с
этим основание стрелки миниметра снабжается двумя V-образными вырезами на нижней и верхней плоскостях. В эти вырезы сверху упирается неподвижная призма, а снизу —- тыльная сторона измерительного штифта. Штифт, двигаясь вверх, наклоняет основание стрелки и, таким образом, передает свое перемещение, увеличенное во много раз стрелкой, на шкалу. Перемещение кончика стрелки будет больше перемещения измерительного штифта в столько раз, во сколько плечо L больше плеча.
На шкалах миниметров не существует нулевых делений и в качестве таковых принимаются любые деления шкалы, разделенной в узкошкальном миниметре на 20 частей, а в широкошкальном — на 60 частей. Цена делений миниметров, нанесенная на их шкале, может быть различной: 0,01, 0,005, 0,002 и 0,001 мм.
При проверке плоских и цилиндрических предметов миниметр укрепляется на стойке с плоским измерительным столиком. Из него кладут блок концевых мер и вместе с головкой миниметра 5 опускают кронштейн до соприкосновения измерительного штифта 8 с поверхностью блока. Закрепив в таком положении кронштейн, переходят к точной установке столика с помощью микрометрического винта. Настройка считается законченной, когда стрелка остановится в нулевом положении, а столик будет закреплен винтом. Отрегулировав, таким образом, прибор и удалив блок, кладут на измерительный столик проверяемую деталь. Во время измерения плоских деталей измерительный штифт приподнимают рычажком, чтобы не повредить штифт, и опускают осторожно на проверяемую плоскость. Цилиндрические детали просто прокатываются по поверхности столика.
Если величина измеряемого предмета соответствует размеру блока концевых мер. стрелка укажет то деление, на которое прибор был настроен. Если измеряемый предмет окажется больше, то стрелка отойдет вправо, если же меньше—влево. Допускаемые отклонения размеров проверяемых деталей обычно отмечаются особыми указателями, перемещаемыми по шкале.
Рис. 5. Миниметр:
1 — основание стрелки; 2 — неподвижная призма; 3 — измерительный штифт; 4 — шкала; 5 — головка миниметра; 6 — рычажок; 7 — кронштейн; 8 — измерительный штифт; 9 — столик; 10— зажим; 11 — микрометрический винт.
Реклама:
Читать далее:
Оптико-механические измерительные приборы
Статьи по теме:
Соберите метрики автоматического выключателя Spring Cloud Resilience4J с помощью микрометра
- 2 минуты на чтение
В этой статье
В этом документе объясняется, как собирать метрики прерывателя цепи Spring Cloud Resilience4j с помощью внутрипроцессного агента Java Application Insights. С помощью этой функции вы можете отслеживать показатели автоматического выключателя resilience4j из Application Insights с помощью Micrometer.
Мы используем демонстрацию «пружинное облако-автоматический выключатель», чтобы показать, как это работает.
Предварительные требования
Создание и развертывание приложений
Следующая процедура создает и развертывает приложения.
- Клонируйте и создайте демонстрационный репозиторий.
git clone https://github.com/spring-cloud-samples/spring-cloud-circuitbreaker-demo.git
cd spring-cloud-circuitbreaker-demo && mvn чистый пакет -DskipTests
- Создание приложений с конечными точками
az spring-cloud app create --name resilience4j --assign-endpoint \
-s $ {asc-service-name} -g $ {asc-resource-group}
az spring-cloud app создать --name reactive-resilience4j --assign-endpoint \
-s $ {asc-service-name} -g $ {asc-resource-group}
- Развертывание приложений.
az развертывание приложения Spring-Cloud -n resilience4j \
--jar-path ./spring-cloud-circuitbreaker-demo-resilience4j/target/spring-cloud-circuitbreaker-demo-resilience4j-0.0.1.BUILD-SNAPSHOT.jar \
-s $ {service_name} -g $ {resource_group}
az Spring-Cloud развертывание приложения -n reactive-resilience4j \
--jar-path .
/spring-cloud-circuitbreaker-demo-reactive-resilience4j/target/spring-cloud-circuitbreaker-demo-reactive-resilience4j-0.0.1.BUILD-SNAPSHOT.jar \
-s $ {service_name} -g $ {resource_group}
Примечание
Включите необходимую зависимость для Resilience4j:
<зависимость>
io.github.resilience4j resilience4j-микрометр <зависимость>org.springframework.cloud пружинное облако-пускатель-выключатель-resilience4j Код клиента должен использовать API
CircuitBreakerFactory
, который реализован как bean-объектСледующие 2 зависимости конфликтуют с вышеуказанными пакетами resilient4j. Убедитесь, что заказчик их не включил.
<зависимость>
org.springframework.cloud весеннее облако-стартер-сыщик <зависимость>org.springframework.cloud весеннее облако-стартер-застежка-молния
Перейдите к URL-адресу, предоставленному приложениями шлюза, и получите доступ к конечной точке из spring-cloud-circuit-breaker-demo следующим образом:
/ получить
/ get / delay / {секунды}
/ get / fluxdelay / {секунды}
Найдите метрики Resilence4j на портале
Выберите блейд Application Insights на портале Azure Spring Cloud и щелкните Application Insights .
Выберите Metrics на странице Application Insights . Выберите azure.applicationinsights из пространства имен Metrics .
Также выберите метрики resilience4j_circuitbreaker_buffered_calls со средним значением .
Выберите resilience4j_circuitbreaker_calls metrics и Average .
Выберите resilience4j_circuitbreaker_calls metrics и Average .Щелкните Добавить фильтр , а затем выберите имя createNewAccount .
Выберите resilience4j_circuitbreaker_calls metrics и Average . Затем нажмите Применить разбиение и выберите вид .
Выберите resilience4j_circuitbreaker_calls , ` resilience4j_circuitbreaker_buffered_calls и resilience4j_circuitbreaker_slow_calls метрик со средним .
См.
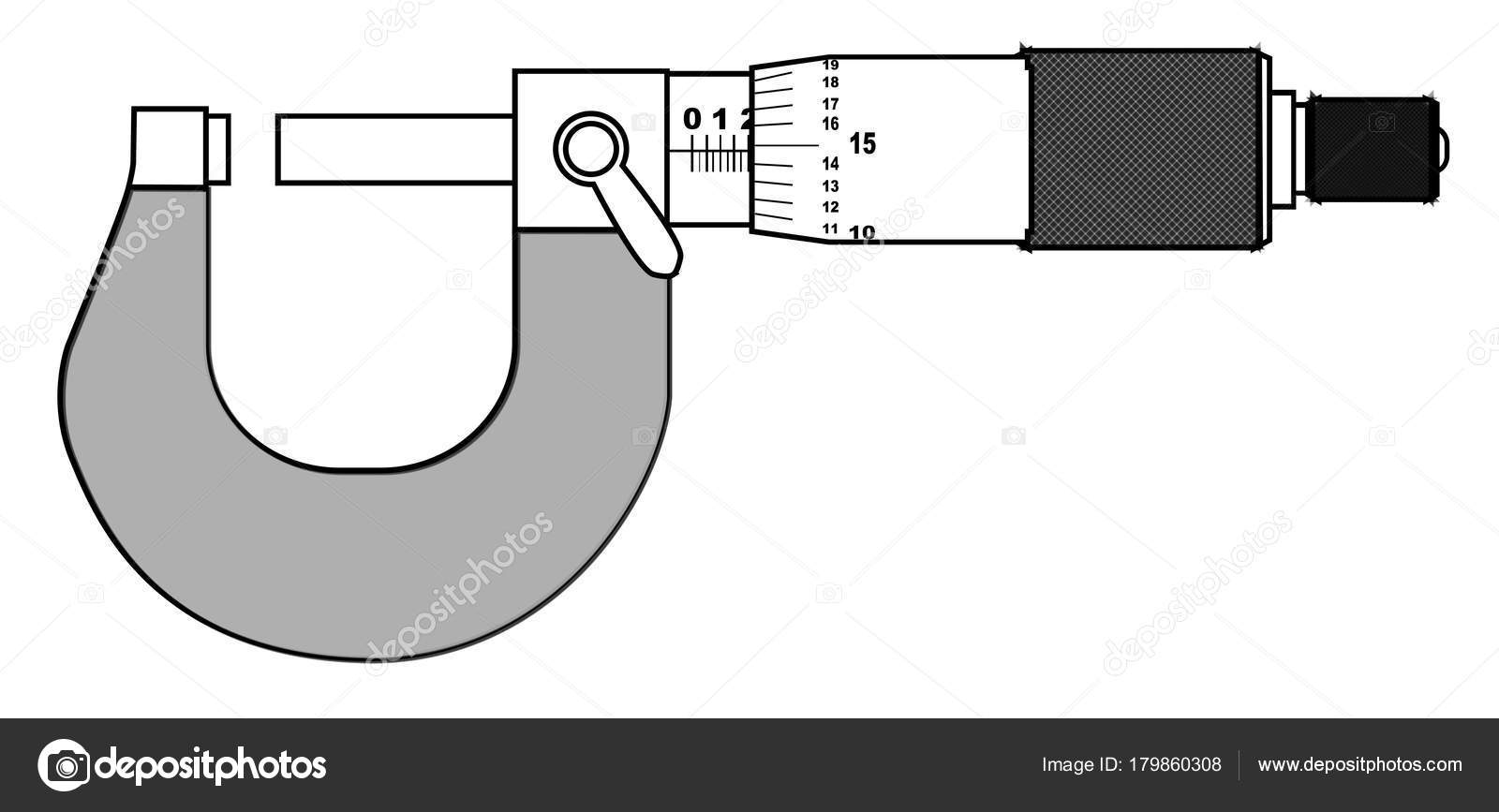
Resilience4j | Предоставьте JMX метрики автоматического выключателя с помощью микрометра | Простой пример – его пакет All Binary
com.itsallbinary.resilience4j.tutorial;
import io.github.resilience4j.circuitbreaker.CircuitBreaker;
import io.github.resilience4j.circuitbreaker.CircuitBreakerRegistry;
import io.github.resilience4j.micrometer.tagged.TaggedCircuitBreakerMetrics;
импорт io.микрометр.кор.инструмент.Часы;
импорт io.micrometer.core.instrument.MeterRegistry;
импорт io.micrometer.jmx.JmxMeterRegistry;
открытый класс CircuitBreakerMetricsJMX {
public static void main (String [] args) {
/ *
* Реестр микрометров с базовыми конфигурациями JMX. На основе структуры, которую вы используете
*, например Spring и т. Д., Вы можете использовать реестр счетчиков, предоставленный этой структурой
*.
* /
MeterRegistry meterRegistry = new JmxMeterRegistry (s -> null, Clock. SYSTEM);
// Сервисный клиентский объект для вызова сервиса.
ExternalService externalService = новый ExternalService ();
/ *
* Автоматический выключатель с конфигурациями по умолчанию. Ниже приведены значения по умолчанию.
*
* DEFAULT_SLIDING_WINDOW_TYPE = SlidingWindowType.COUNT_BASED; -> Изменение состояния
* произойдет в зависимости от количества неудачных вызовов.
*
* DEFAULT_RECORD_EXCEPTION_PREDICATE -> Все исключения, записанные как отказы
*
* DEFAULT_MINIMUM_NUMBER_OF_CALLS = 100 DEFAULT_SLIDING_WINDOW_SIZE = 100; ->
* Минимальное количество вызовов для записи до принятия решения об открытии.
*
* DEFAULT_FAILURE_RATE_THRESHOLD = 50% -> Из записанных вызовов, если 50% вызовов
* являются ошибочными, то отключается автоматический выключатель
*
* DEFAULT_WAIT_DURATION_IN_OPEN_STATE = 60 секунд -> Подождите столько времени в
* открытое состояние перед переходом в полуоткрытое.
*
* DEFAULT_PERMITTED_CALLS_IN_HALF_OPEN_STATE = 10 -> Посчитайте эти многочисленные вызовы в
* полуоткрытом, чтобы решить, может ли автоматический выключатель быть полностью разомкнутым. *
*
*
* /
CircuitBreakerRegistry circuitBreakerRegistry = CircuitBreakerRegistry.ofDefaults ();
CircuitBreaker circuitBreaker = circuitBreakerRegistry.circuitBreaker (“externalService”);
// Реестр выключателей Bing в реестр микрометров.
TaggedCircuitBreakerMetrics.ofCircuitBreakerRegistry (circuitBreakerRegistry) .bindTo (meterRegistry);
for (int i = 0; i <500; i ++) {
System.out.println (“>> Счетчик вызовов =” + (i + 1));
попробуйте {
// Звоните в службу каждые 1 секунду.
Thread.sleep (1000);
// Украсить служебный вызов в выключателе
String status = circuitBreaker.executeSupplier (() -> externalService.callService ());
System. out.println (“\ t >> Статус вызова:” + статус);
} catch (исключение e) {
e.printStackTrace ();
System.err.flush ();
} finally {
// Распечатайте важную метрическую статистику для наблюдения за поведением выключателя.
System.out.println (“\ t >> Количество успешных вызовов:”
+ circuitBreaker.getMetrics (). GetNumberOfSuccessfulCalls () + “| Количество неудачных вызовов:”
+ circuitBreaker.getMetrics (). getNumberOfFailedCalls () + “|% отказов:”
+ circuitBreaker.getMetrics (). getFailureRate () + “| Состояние:” + circuitBreaker.getState ());
}
}
}
}
микросервисов – интеграция Resilience 4j и Prometheus
Как интегрировать Resilience-4J и Prometheus с микросервисами.
Я интегрировал микросервисы с устойчивостью 4j, а также с Prometheus.Моя проблема в том, что в Prometheus я не получаю никаких запросов на устойчивость, заполняются только HTTP и другие, которые идут по умолчанию.
Пожалуйста, помогите
Шаги, которые я реализовал до сих пор, перечислены ниже ...
1> созданы микросервисы
2> Интегрируйте микросервисы с Resilience 4j, выполнив следующие шаги
i> зависимость в файле pom.xml
ii> создан отдельный класс модуля автоматического выключателя и модуля повторной попытки.
iii> После этого я добавил Прометея, добавив его банку
который...
<зависимость>
io.микрометр
микрометр-реестр-прометей
3> В Prometheus Dashboard запросы / матрицы устойчивости не заполняются.
ie # HELP resilience4j_circuit-breaker_calls Статистика вызовов автоматического выключателя
# TYPE resilience4j_circuit-breaker_calls gauge
resilience4j_circuit-breaker_calls {name = "backendB", call_result = "успешно",} 0,0
resilience4j_circuit-breaker_calls {name = "backendB", call_result = "failed",} 0.0
Пожалуйста, помогите. Заранее спасибо
Я также добавил ниже зависимости для интеграции устойчивости 4j и Prometheus …
<зависимость>
io.github.resilience4j
resilience4j-metrics
0.16.0
<зависимость>
io.github.resilience4j
resilience4j-prometheus
<версия> 0.16.0
нужны матрицы устойчивости на панели инструментов Prometheus.
Схема фазовой автоподстройки частоты для прецизионного емкостного микрометра
MATEC Web of Conferences 68 , 12006 (2016)Схема фазовой автоподстройки частоты для прецизионного емкостного микрометра
Шуцзе Ли 1 и Сян Дэн 2
1 Школа механики, электроники и управления, Пекинский университет Цзяотун, Пекин, 100044, P.R. China
2 Beijing Fei Na Ying Chuang Measurement, Control Technology & Instrumentation Co., LTD, Пекин, 100098, P. R. Китай
Абстрактные
Высокоточный бесконтактный микрометр обычно делится на три категории: микрометр индуктивности, микрометр емкости и микрометр оптического интерферометра. Емкостной микрометр широко используется, потому что он имеет высокое соотношение производительности и цены. С повышением уровня автоматизации точность емкостного микрометра требуется все выше и выше.Как правило, емкостной микрометр состоит из датчика емкости, схемы преобразования емкости / напряжения и схем модуляции и демодуляции. Однако из-за наличия в цепи резисторов, конденсаторов и других компонентов может произойти фазовый сдвиг несущего сигнала и модулированного сигнала. В этом случае конкретное значение фазового сдвига определить невозможно. Следовательно, ошибка, вызванная фазовым сдвигом, не может быть устранена. Это снизит точность микрометра. В этой конструкции, чтобы исключить влияние фазового сдвига, используется схема фазовой автоподстройки частоты (ФАПЧ). В ходе эксперимента функция отслеживания фазы и частоты входного сигнала достигается с помощью схемы фазовой автоподстройки частоты. Этот метод обработки сигналов также может быть применен к системе томографии электрического сопротивления клубней и другим схемам прецизионного измерения.
Это статья в открытом доступе, распространяемая в соответствии с условиями лицензии Creative Commons Attribution License 4.0, которая разрешает неограниченное использование, распространение и воспроизведение на любом носителе при условии правильного цитирования оригинальной работы.
■ | Все авторские права на список деталей остаются собственностью Mitutoyo Corporation. |
■ | Возможно, вы не сможете просмотреть список деталей, если в настройках Adobe Acrobat Reader на вашем ПК не установлен флажок «Отображать PDF в браузере».![]() * Adobe является зарегистрированным товарным знаком Adobe Systems Incorporated. |
■ | Вы можете просмотреть список деталей в виде файла PDF, но вы не можете распечатать или сохранить файл (файл доступен только в формате только для чтения). |
■ | «X», «Y», «Y1» и пустые записи для классификации продаж в списке деталей имеют следующие значения. X: Детали, которые мы не поставляем и не продаем. Y или Y1: Детали, которые могут быть заменены и отрегулированы только обслуживающим персоналом Mitutoyo или ее авторизованных поставщиков, обладающих специальными знаниями. Пусто: детали, доступные для покупки. |
■ | Внешний вид, технические характеристики и другие аспекты деталей, включенных в список деталей, могут быть изменены, и мы можем прекратить производство и продажу этих деталей без уведомления.![]() |
■ | Список деталей включает в себя некоторые детали, доставка которых занимает несколько дней, детали, которые больше не продаются, и детали, которые мы не можем продать. |
■ | Корпорация Mitutoyo не несет ответственности за работу и точность в случае замены вами приобретенной детали. |
■ | По вопросам относительно запчастей обращайтесь в магазин, в котором вы приобрели запчасть. |
■ | Чтобы приобрести деталь, сообщите в магазин номер детали. |
Превосходная точность – как оптическое измерение расстояния с точностью до микрометра становится более надежным
Лазерные датчики расстояния Baumer OM70 с возможностью выбора диапазонов фокусировки для повышения надежности.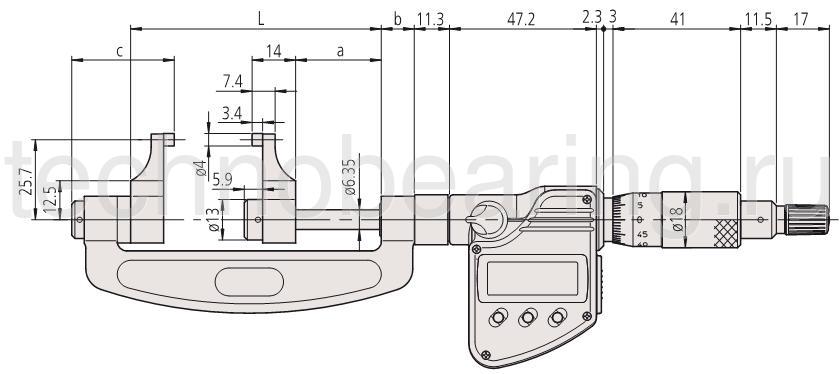
Лазерные датчики расстояния обеспечивают высокоточное измерение расстояния и положения с разрешением менее одного микрометра.Однако на практике возникают интерференционные эффекты, которые могут снизить воспроизводимость оптических измерений расстояния. Благодаря введению выбираемых диапазонов фокусировки лазерные датчики расстояния Baumer OM70 обеспечивают значительно лучшую локальную повторяемость и, таким образом, обеспечивают более надежные результаты измерений и более высокую надежность процесса для автоматизированных измерительных задач.
Точность повторения для оптически сложных поверхностей
Разрешение в техническом паспорте лазерного датчика расстояния, часто используемое в качестве шкалы точности, является значением, которое может быть достигнуто только в том случае, если положение точки измерения на объект не меняется.Однако, как только поперечное положение точки измерения изменяется, локальная повторяемость имеет решающее значение для точности результата измерения. Эта повторяемость всегда хуже разрешения. Локальная повторяемость оптической измерительной системы сильно зависит от однородности измеряемой поверхности объекта. Поскольку существуют поверхности с различной структурой, это значение очень сложно определить на практике. Небольшие изменения в цвете отражательной способности или структуре поверхности могут существенно повлиять на результат измерения.Высококонтрастные покрытия, матовые или оцинкованные металлические поверхности, природные материалы с цветовой структурой, такие как камень или дерево, изменение цвета в черно-белом или протравленные печатные платы являются примерами таких оптически сложных поверхностей.
Диапазон фокусировки увеличивает надежность
Степень, в которой влияние неоднородных поверхностей влияет на результат измерения, зависит от размера лазерного пятна, отраженного от объекта. Чем меньше размер пятна, тем меньше влияние неоднородных поверхностей на результаты измерений.Поскольку свет лазерного диода в датчике должен фокусироваться через линзу, размер пятна изменяется в пределах диапазона измерения. Наименьшее лазерное пятно достигается в точке фокусировки оптической системы. Таким образом, наиболее надежные результаты измерений получаются, когда измеряемый объект измеряется в области вокруг точки фокусировки датчика – в диапазоне фокусировки.
Различные приложения – Различные датчики
Чтобы охватить объекты разных размеров, геометрии объектов и возможных ситуаций установки на промышленных предприятиях, важно выбрать датчик, который лучше всего подходит для требуемого расстояния до объекта и размера объекта и что гарантирует требуемую точность измерения.Лазерные датчики расстояния OM70 от Baumer доступны в 6 различных диапазонах измерения от 70 до 1500 мм. Выбираемые диапазоны фокусировки доступны для диапазонов измерения 70, 140, 250, 600 и 1000 мм. Выбирая датчик, который точно покрывает важное расстояние в приложении с диапазоном фокусировки, надежность результата измерения может быть значительно улучшена даже с оптически очень требовательными поверхностями. Если измеренные значения оцениваются при калибровке во всем диапазоне измерения, следует выбрать вариант датчика с диапазоном фокусировки в конце диапазона измерения.
OM70 – непревзойденная точность
Высокопроизводительные датчики расстояния OM70 от Baumer сочетают в себе высокоточную технологию измерения и простоту использования в сфере автоматизации. Благодаря разрешающей способности до 0,7 мкм и отклонению от линейности до 0,06% датчики обеспечивают надежное измерение компонентов, а также высокоточное позиционирование объектов или захватов. Датчики гарантируют чрезвычайно высокую стабильность процесса, несмотря на колебания температуры или изменяющиеся условия внешней освещенности, и позволяют измерять расстояния до 1500 мм.
Лазерный микрометр диаметраDDM-2025L с дисплеем
Описание
Лазерный микрометр диаметра DDM-2025L с дисплеем Лазерный датчик диаметра, также называемый оптическим микрометром, лазерным обнаружением, определением диаметра и измерением диаметра. Лазерный измеритель диаметра, высококачественная лазерная технология со специальным бесконтактным и неразрушающим принципом измерения для измерения диаметра, идеальная система для контроля качества, оптимизации процесса и стабильности.
В лазерном измерителе диаметра серии DDM диаметр рассчитывается путем дифракционного анализа непосредственно из теневого изображения, этот измеритель отличается широким диапазоном измерения, высокой точностью, длительным сроком службы и стабильной работой.
Лазерный монитор DDM 2025 – это бесконтактный лазерный измеритель диаметра, это лазерный прибор для измерения диаметра, используемый для онлайн-измерения диаметра, выходной цифровой сигнал диаметра соответствует обнаруженному диаметру кабеля.
Устройство определения диаметра кабеля – это один из видов лазерного измерителя диаметра кабеля или провода, основанный на методе измерения диаметра лазером, это одно из лучших устройств для измерения диаметра.
DDM2025 поставляется с монитором и контроллером DSP-4A, монитор DSP-4A предлагает удаленный дисплей и выход сигнала управления PI.
Особенности лазерного измерителя диаметра серии DDM.
Очень короткое время экспозиции
Метод измерения изображения CCD с использованием лазерных источников света
Обработка данных DSP
Технические параметры (спецификации)
Номер модели | DDM-2025L | DDM-2050L | DDM-2100L | DDM-25XY | DDM-50XY |
Диаметр продукта | 0.1 ~ 25 мм | 0,1 ~ 48 мм | 0,5 ~ 95 мм | 0,1 ~ 25 мм | 0,1 ~ 48 мм |
Точность | ± 2 мкм | ± 2 мкм | ± 5 мкм | ± 2 мкм | ± 2 мкм |
Время воздействия | 200 мкСм | 200 мкСм | 200 мкСм | 200 мкСм | 200 мкСм |
Скорость измерения 600 | 600 измерений / сек / ось | 600 измерений / сек / ось | 600 измерений / сек / ось | 600 измерений / сек / ось | |
Интерфейсы | RS-485 | RS-485 | RS-485 | RS-485 | RS-485 |
Источник питания | 220 В переменного тока ± 10%, 50/60 Гц, 15 ВА | 220 В переменного тока ± 10%, 50/60 Гц, 15 ВА | 220 В переменного тока ± 10% , 50/60 Гц, 15 ВА | 220 В переменного тока ± 10%, 50/60 Гц, 15 ВА | 220 В переменного тока ± 10%, 50/60 Гц, 15 VA |
Размеры | 408 x 180 x 82 мм | 408 x 180 x 82 мм | 504 x 203 x85 мм | 355 x 330 x 82 мм | 355 x 330 x 82 мм |
DDM используется для онлайн-измерения диаметра электрических проводов и кабелей, оптоволоконных кабелей, трубок и проводов. Типичные области применения: измерение внешнего диаметра тонкой проволоки, обнаружение выступа наружного диаметра и опускания шейки на сверхвысокой скорости, измерение внешнего диаметра в суровых условиях. Все методы обработки цифровых изображений и специализированные сверхбольшие интегральные схемы, обеспечивающие высокое качество изображения. стабильность, компактный размер и низкое энергопотребление.
Интерфейс связи RS-485, позволяющий легко подключить контроллер к промышленному компьютеру, ПЛК и сенсорной панели.
Положение устья
Лазерный измеритель диаметра серии DDM может быть установлен до или после охлаждающего желоба.Когда он установлен перед охлаждающим желобом, можно получить оптимизированный регулирующий эффект за счет своевременной обратной связи из-за близости измерительной головки к экструдеру. Но в это время пластиковое покрытие не затвердевает, поэтому установленное номинальное значение должно быть соответствующим. Когда он устанавливается после охлаждающего желоба, измеренное значение представляет собой реальный диаметр провода или кабеля.