Накатки резьбы: Накатка резьбы – Profiroll Technologies
alexxlab | 16.05.2023 | 0 | Разное
Накатка резьбы – Profiroll Technologies
Накатка резьбы и профилей
Накатка резьбы и профилей роликами является самым универсальным и точным способом накатывания резьбы. При накатке резьбы на 2-роликовых станках заготовка располагается между накатными инструментами на специальном поддерживающем устройстве – накатном ноже или роликовой опоре. Оба ролика вращаются синхронно в одном направлении, как минимум один из них имеет радиальную подачу для внедрения в заготовку, при этом путем пластического деформирования происходит формирование требуемого профиля резьбы на заготовке.
Параметры влияющие на усилие при накатывании
- Прочностные характеристики материала
- Коэффициент деформации
- Площадь контакта
Накатывание с радиальной подачей роликов
Известно также как «накатка на врез». Применяется для накатки коротких резьб, длина резьбы ограничена шириной накатных роликов. В процессе накатки формообразующий инструмент с негативным профилем внедряется в заготовку и формирует требуемый профиль, при правильном подборе параметров осевое перемещение заготовки отсутствует. Требуемое усилие при накатывании зависит от шага, длины резьбы и свойств материала.
Явным преимуществом накатывания с радиальной подачей является скорость процесса.
‘; nomaps[nomaps.length] = ‘
Воспроизводя видео на Youtube, вы соглашаетесь с условиями Youtube. Это также передает релевантные пользователю данные на YouTube / Google и сохраняет файлы cookie.
‘;
Накатывание резьбы методом радиальной подачи. Деталь: резьбовая шпилька М56х4. Резьбонакатной станок: PR 60e PRS
Накатывание кольцевыми роликами с осевой подачей
Известно также как «накатка на проход». Применяется в случаях, когда длина требуемой резьбы превышает ширину накатных роликов. Особенность конструкции роликов: наличие заходной, калибрующей, и выходной частей. Накатные ролики имееют «кольцевой» профиль с требуемым шагом и наклоняются в станке на угол подьёма α и направление накатываемой резьбы.
Накатывание скорректироваными роликами с осевой подачей
Накатные ролики с коррекцией по углу подьема резьбы, в отличии от кольцевых роликов, имеют многозаходной винтовой профиль. Сумма угла подьема профиля накатного инструмента и наклона шпинделей накатного станка равна углу подьёма резьбы α накатываемой детали. В зависимости от конструкции, возможна высокоскоростная осевая накатка (HDU) или накатка с пониженной осевой скоростью (TDU) прецизионных или глубоких профилей.
Применение роликов с коррекцией по углу подьема резьбы позволяет также оптимтизировать процесс накатки по усилию. В оптимальном случае возможно накатывание крупных резьб на относительно небольших станках.
‘; nomaps[nomaps.length] = ‘
Воспроизводя видео на Youtube, вы соглашаетесь с условиями Youtube. Это также передает релевантные пользователю данные на YouTube / Google и сохраняет файлы cookie.
‘;
Накатывание резьбы методом осевой подачи. Деталь: полнорезьбовая шпилька с трапецеидальной резьбой TR 110. Резьбонакатной станок с ЧПУ: PR 100 CNC/AC
Оборудование для накатки резьбы на гайки
НА ШУРУПЫ И САМОРЕЗЫ НА ГАЙКИ НА БОЛТЫ, ВИНТЫ, ШПИЛЬКИ НА МИКРОВИНТЫ НА ШПИЛЬКИ И ПРУТКИ НА ТОНКИЕ ИЗДЕЛИЯ С НЕСТАНДАРТНЫМ ПРОФИЛЕМ НА СПЕЦИАЛЬНЫЕ ДЕТАЛИ НА ТРУБЫ
- общая информация о
нарезании резьб на гайки - 4-шпиндельные
гайконарезные станки - 2-шпиндельные
резьбонарезные автоматы - 1-шпиндельные
гайконарезные автоматы - Универсальные
гайконарезные станки - Гайконарезные автоматы
для ГЛУХИХ гаек - резьбонарезные станки для
ДЛИННЫХ КОЛЕСНЫХ гаек - гидравлические станки
для обжима гаек
Общая информация о получении резьбы на гайках
К самым распространенным крепежным изделиям можно отнести гайки. Они являются важной частью резьбовых соединений и применяются в различных их видах.
В производстве крепежных изделий используются несколько технологий изготовления гайки – точение, горячая штамповка, холодная штамповка и др. Все технологии придают изделию определенную форму (круглая, четырехугольная, шестигранная), но основная составляющая гайки – это резьба, которая является основой для создания крепежных соединений.
Нарезание резьбы – операция, выполняемая со снятием стружки или методом накатывания, в результате которой образуются винтовые канавки на поверхностях. Наиболее распространенным и универсальным способом получения внутренних резьб гаек является обработка резанием.
К ней относятся:
- нарезание внутренних резьб метчиками
- точение внутренних резьб резьбовыми резцами и гребенками
- резьбофрезерование внутренних резьб дисковыми и червячными фрезами
- нарезание внутренних резьб резьбонарезными головками
- вихревая обработка внутренних резьб
- накатывание внутренних резьб резьбонакатными головками
- накатывание (выдавливание) внутренних резьб бесстружечными метчиками.
Видов гаек и размеров гаек очень много, поэтому видов оборудования для нарезки / накатки резьбы на гайки тоже много. Как же производителю выбрать способ нарезания резьбы? Нарезание резьбы метчиками, накатка на гайконарезном станке, фрезерование или токарная обработка? Лишь путем проб и ошибок – если один из способов не приносит удовлетворительного результата, нужно пробовать другой. Всем способам нарезания резьбы на гайки присущи свои достоинства, свои недостатки и своя сфера применения. Самое главное: решая взяться за нарезку резьбы, посмотрите на имеющиеся станки и подсчитайте стоимость инструментов, время цикла резки и сроки эксплуатации инструментов.
Нарезание резьбы на гайки метчиками
- применение гаечных метчиков для нарезания резьбы на гайки это самый распространённый и наименее затратный способ на начальном этапе производства
- гаечные метчики могут быть использованы при обработке практически любого материала твердостью вплоть до 65 HRC
- гаечные метчики могут нарезать резьбу в отверстиях глубиной более трёх диаметров самого инструмента
- гаечные метчики обычно работают намного быстрее, чем резьбонарезные фрезы с одной режущей кромкой
- нарезание резьбы гаечными метчиками это продолжительный процесс.
- нарезка резьбы гаечными метчиками возможна в отверстиях диаметром не более 16 мм. При нарезании резьбы в отверстиях большего диаметра у станка может просто не хватить мощности для поворота гаечного метчика, контактирующего с заготовкой.
- при нарезании резьбы гаечными метчиками производится большое количество стружки, которую нужно эффективно отводить. В противном случае стружка образовывает заторы вокруг метчика, забивает канавки метчика, что может привести к обламыванию метчика в отверстии. Алюминий, углеродистые и нержавеющие стали являются наиболее сложными материалами для контроля отвода стружки.
- при нарезании резьбовых отверстий диаметром 6 мм и менее существует проблема отвода стружки, так как пространство очень ограничено, а инструменты маленького размера относительно хрупкие.
- поскольку диаметр и шаг резьбы всегда остаются неизменными, один и тот же гаечный метчик не может использоваться для нарезания отверстий разного размера.
- при нарезке резьбы в гайках гаечными метчиками требуется смазка
Накатывание резьбы на гайки бесстружечными метчиками на гайконарезных автоматах
Достоинства и недостатки накатки гаечной резьбы
- является наиболее высокопроизводительным способом получения резьбы на гайках
- накатные метчики не режут, а деформируют материал, поэтому стружка при этом процессе не образуется и отсутствует вероятность возникновения заторов стружки
- накатывание резьбы бесстружечными метчиками (метчиками-раскатниками) обеспечивает высокое качество получаемой резьбы на гайках
- накатанная резьба прочнее резьбы, получаемой нарезкой, так как зернистый по своей структуре металл подвергается сдавливанию, что делает его более однородным
- твёрдость заготовки при такой обработке ограничивается как правило 40 HRC
- поскольку накатка резьбы подразумевает пластическую деформацию, материал должен быть пластичен или обладать низким коэффициентом растяжения
- накатные метчики требуют больший крутящий момент и большую мощность от станка, кроме того, инструмент должен быть крепче зажат в державке станка.
Для пластической деформации металла требуется приложить большую силу, чем при его резке.
- отверстие под накатывание резьбы должно быть просверлено более точно, чем таковое отверстие под нарезании резьбы
- полученные путем пластической деформации материала, не подходят для некоторых отраслей промышленности, таких как медицинская и авиационно-космическая. При накатке резьбы внутренний диаметр не идеален, авиационно-космическая отрасль не допускает такой U-образный профиль на внутреннем диаметре резьбы.
Токарная обработка резьбы
Токарная обработка является ещё одним способом нанесения внутренней резьбы. При этом используются либо сменные твердосплавные пластины, либо миниатюрный инструмент наподобие расточного резца. Обработка производится на многоосевых или токарных станках. Нарезание резьбы на токарных станках выполняется в единичном и мелкосерийном производстве.
- нарезание резьбы на токарных станках подходит для целого ряда материалов вплоть до очень твердых или абразивных
- нарезание резьбы на токарных станках подходит для отверстий глубиной до 3 его диаметров при использовании инструмента со стальными державками, и даже глубиной в 4-5 диаметров при использовании инструмента с державками из твердых сплавов
- возможно нарезание различных видов резьб при соответствующей настройке вращения шпинделя с перемещением суппорта, углом воздействия режущего инструмента и частотой оборотов детали
- скорость нарезания резьбы на токарном станке очень маленькая.
Использование высокопроизводительных режимов при нарезании резьбы приводит к повышенной нагрузке на элементы шпиндельного узла.
- для получения точной резьбы необходимо выдержать жесткие требования по подаче, шагу резьбы, соосности инструмента и отверстия.
- большая трудоёмкость операции нарезания резьбы
- отвод стружки является большой проблемой при нарезании внутренней резьбы на токарных станках, особенно остро проблема проявляется при нарезании резьбы в глухих отверстиях
- требуется СОЖ
Нарезание резьбы гайконарезными головками
Гайконарезная головка представляет собой сложный механизм, оснащенный комплектом гребенок, выполняющих роль зубьев метчиков, имеющих режущие и направляющие резьбовые профили.
- гайконарезные головки могут использоваться для нарезания резьбы любого типа
- нарезание резьбы гайконарезными головками, применяемыми на автоматических станках, значительно производительнее (в 3—4 раза), чем нарезание плашками, так как благодаря автоматическому раскрыванию обратного свинчивания их не требуется.
- гайконарезные головки не требуют реверсирования, так как в конце рабочего хода гребенки автоматически убираются внутрь корпуса
- в одном корпусе головки допускается установка гребенок различных размеров, что повышает универсальность инструмента
- повышенная точность резьбы
- подходит для серийного и массового производства
- высокая стойкость и долговечность – вставные гребенки имеют большее количество переточек
- размеры получаемой резьбы можно легко регулировать и при необходимости нарезать в два прохода
- резьбовой профиль гребенок образуется шлифованием, что обеспечивает хорошее качество режущих и калибрующих профилей и, как следствие, улучшается точность и шероховатость поверх-ностей резьбового профиля нарезаемой резьбы
- высокая цена
- при нарезании резьб гайконарезными головками станок должен отвечать установленным для него нормам точности. Особенно важно соблюдение требований по биению шпинделя и соосности детали и гайконарезной головки
Нарезание внутренней резьбы фрезами
Для нарезания резьбы применяются цельные твердосплавные фрезы и сменные твердосплавные пластины (стальное тело фрезы с карбидными вставками). Многовитковые резьбонарезные фрезы нарезают резьбу сразу на всю глубину за один полный поворот фрезы. Одновитковые фрезы нарезают один виток резьбы за оборот.
- фрезы для нарезания резьбы подходят для обработки материала прочностью до 65 HRC
- резьбонарезные фрезы имеют большой диапазон применения, их диаметр начинается от 1.5 мм и заканчивается самыми большими размерами
- одна и та же резьбонарезная фреза может применяться для отверстий, имеющих различный диаметр, но одинаковый шаг резьбы
- фреза с одной режущей кромкой может быть использована для обработки отверстий различных диаметров, а также и нарезания резьбы различного шага
- фреза одной и той же геометрии, но с одним или двумя слоями различных покрытий, позволяет обрабатывать множество разнообразных материалов
- одновитковая резьбонарезная фреза может быть применена для обработки глухих и сквозных отверстий, а также для нарезания правой и левой резьбы
- одновитковая фреза может работать на большой глубине, вплоть до 20 диаметров
- так как фреза имеет плоскую нижнюю поверхность, она может нарезать резьбу в непосредственной близости от днища глухого отверстия, и даже если фреза сломается, это не приведет к выбраковыванию детали
- фреза для нарезания резьбы может быть совмещена в одном корпусе с другими инструментами для сверления отверстий, тем самым образовывая комбинированный инструмент, который может одновременно сверлить, делать фаски и нарезать резьбу
- отвод стружки обычно не является проблемой при нарезании резьбы фрезами
- цикл обработки фрезой обычно дольше цикла обработки метчиками
- использование фрез для нарезания резьбы в гайках требует специальной программы для станка
- использование фрез для нарезания резьбы на гайки требует постоянного контроля оператора.
Так как фреза стачивается в процессе нормального износа, оператору необходимо измерять допустимые отклонения в размерах резьбы, следить за износом инструмента и регулировать режущий процесс, чтобы подстроится под текущий износ инструмента и сохранить правильные размеры получаемой резьбы.
- при использовании фрезы для нарезания резьбы силы резания не сбалансированы. При нарезании резьбы большой длины создается большое давление на боковую поверхность фрезы, так как на нее воздействует большая радиальная сила. Это может приводить к проблемам в виде отскакивания режущей кромки от заготовки и появлению на ней сколов, и даже к обламыванию фрез небольшого диаметра
Шлифование для нарезания высокопрецизионной резьбы на гайки
Нарезание резьбы методом шлифования позволяет нарезать высокопрецизионные внутренние резьбы. Типичными деталями, которые производятся методом внутреннего шлифования, являются резьбоизмерительные калибры, гайки для обычных и шариковых винтовых передач. Нарезание внутренней резьбы методом шлифования производится на специализированных станках.
- при помощи одного станка можно вышлифовывать широкое разнообразие внутренних видов резьбы
- типичные размеры, обеспечивающие экономически выгодный процесс шлифования, варьируются от 10 до 533 мм
- нарезание внутренней резьбы методом шлифования является очень точным процессом
- требуется узкоспециализированное дорогостоящее оборудование
- требуется отвод / смыв стружки при нарезании внутренней резьбы методом шлифования
- для эффективного нарезания внутренней резьбы методом шлифования станок должен обладать жесткостью конструкции, точным перемещением по осям, способностью выполнять точные циклические перемещения и наличие прецизионных шпинделей с датчиками контроля температуры
Что такое накатка резьбы? | Helix Linear Technologies
Накатка резьбы — это процесс ковки металла, при котором резьба формируется путем пропускания материала под высоким давлением через набор закаленных штампов закаленных штампов. В резьбонакатном станке плашки скошены или наклонены друг относительно друга, поэтому их оси не параллельны. Перекос отвечает за перемещение материала через штампы в так называемом процессе сквозной подачи. Накатные гребенки предназначены для управления скоростью подачи проходящего через них материала, которая регулирует время пребывания прокатываемого материала в плашках и устанавливает скорость формирования резьбы. Прокатные штампы являются неотъемлемой частью процесса проектирования штампов, учитывая разнообразие размеров резьбы, глубины, формы и прокатываемого материала.
Каковы преимущества накатывания резьбы?
Накатка резьбы — это экономичный способ изготовления прецизионных ходовых винтов. Он идеально подходит для изготовления длинных резьб. Прецизионные нити можно наматывать со скоростью несколько футов в минуту. Однако операции механической обработки и шлифования являются гораздо более медленными процессами для создания резьбы и более сложными при нарезании резьбы большой длины из-за возможностей станка и отношения длины к диаметру.
Дополнительные преимущества накатывания резьбы включают:
Экономия времени – Независимо от глубины резьбы, накатка производит окончательную резьбу за один проход через плашки, в то время как процессы нарезания и шлифования могут потребовать нескольких проходов для достижения полной глубина резьбы. При производстве многозаходной резьбы разница во времени еще более значительна. Многие ходовые винты могут иметь от двух до четырех заходов, а некоторые – до шестнадцати заходов. Все заходы формируются сразу в процессе накатки резьбы, независимо от количества заходов. Однако при использовании методов механической обработки или шлифования все заходы производятся по отдельности, что увеличивает время изготовления резьбы. В дополнение к экономии времени нарезание резьбы по отдельности может привести к ошибкам при переходе от резьбы к резьбе или шагу шага.
Высококачественная отделка – В процессе прокатки получается превосходное полированное покрытие. Воронение — это механическая полировка, которая улучшает качество поверхности, так как штампы сжимают и формируют прокатанный материал. Обработка поверхности важна, потому что многие гайки, соединяющие ходовой винт, изготовлены из пластика, а высококачественная отделка обеспечивает повышенную износостойкость. Вороненая отделка также снижает коэффициент трения, повышая общую эффективность на 8-9%. Кроме того, точность и чистота этого процесса обеспечивают оптимальную производительность, делая ходовые винты более гладкими и долговечными.
Прочность материала – В процессе прокатки материал не удаляется, и это изменяет физические свойства материала, что приводит к упрочнению металла. Это условие обеспечивает более прочную резьбу и улучшает поверхностную твердость ходового винта. Более жесткая поверхность повышает износостойкость и хорошо работает с гайками из других материалов.
Без шва – Помимо дополнительной прочности прокатанного материала, еще одним преимуществом накатывания резьбы является отсутствие шва на вершине резьбы. Ходовые винты низкого качества, не требующие точности, прокатываются для контроля диаметра шага, но допускают колебания основного диаметра. Этот вариант обнажает шов в верхней части нити, от едва заметного до более существенного. Хотя эта практика увеличивает срок службы штампа, она приводит к изменению основного диаметра и не является оптимальной для пластиковых гаек на центрирующей резьбе, где может быть контакт на этой поверхности. Прецизионная накатка нити закрывает этот шов благодаря дизайну и повышенному давлению. Этот процесс заполнения штампов снижает срок службы штампа, но повышает общую точность диаметра, отделки и внешнего вида продукта.
Материал для накатки резьбы и подготовка
Резьба может быть накатана с использованием нержавеющей стали, углеродистой стали, алюминия, титана или других стержневых материалов. Нержавеющая сталь обычно используется для прокатки ходовых винтов. Тем не менее, материалы для конкретного применения могут быть выбраны для удовлетворения конкретных требований проекта. Хотя некоторая регулируемость процесса прокатки может позволить использовать одни и те же прокатные штампы для нескольких различных материалов, новые штампы могут потребоваться при наличии различий в твердости, пластичности и пластичности материалов.
Выражение «мусор на входе, мусор на выходе» точно применимо к процессу точной накатки резьбы. Диаметр и округлость заготовки, подаваемой через штампы, имеют существенное значение. Отдельная операция бесцентрового шлифования стержневой заготовки требуется для контроля жестких допусков на диаметр заготовки и круглость стержня. Обе спецификации должны соответствовать размеру 0,0002 дюйма или 5 микронам. инструментальная сталь. Точность готовой матрицы в значительной степени зависит от качества червячной плиты. Обычно для улучшения отделки после механической обработки необходим процесс полировки или притирки. набор.
Резьбонакатные плашки проходят термообработку для достижения большей твердости, чем накатываемый материал. Термическая обработка завершается после зубофрезерования, что может повлиять на окончательную точность. Использование подходящего материала и процесса термообработки значительно увеличивает срок службы штампов, особенно в штампах, которые накатывают резьбу с мелким шагом или очень крупную резьбу (большой угол наклона спирали). Обе крайности резьбы по своей сути создают большую нагрузку на матрицы.
Шлифовка штампов, как правило, более точна, и могут быть получены более жесткие допуски. Процесс шлифования обеспечивает лучшую чистоту поверхности без вторичной полировки. Кроме того, штампы шлифуются после закалки, что устраняет некоторую непредсказуемость или изменчивость процесса термообработки.
Типы резьбонакатных систем
Резьбонакатные системы обычно делятся на три категории: плоские вальцы, системы с двумя и тремя матрицами.
Плоские вальцы – Плоские вальцы используются для высокоскоростных и неточных операций, таких как нарезание резьбы в крепежных деталях, механических винтах и болтах.
Трехбойковая прокатка – Трехбойковая прокатка обеспечивает высокую точность прокатки и круглость. Тем не менее, это может быть недопустимо при производстве ходовых винтов малого диаметра из-за ограничения того, насколько близко три матрицы могут располагаться друг к другу. Могут помочь матрицы меньшего диаметра, но все еще существуют ограничения по размеру. Кроме того, из-за размеров оправки оборудования и соображений износа/срока службы матрицы меньшего размера часто создают дополнительные проблемы.
Двухвалковая прокатка – Двухвалковая прокатная система обеспечивает превосходные результаты и наибольшую гибкость при прокатке высокоточных ходовых винтов и уменьшении диаметров. Еще одним преимуществом системы с двумя штампами является снижение затрат на инструмент. По мере увеличения диаметра ходового винта увеличиваются и соответствующие штампы, используемые для их прокатки. Изготовление комплекта из двух штампов дешевле, чем из трех штампов. В системе с двумя головками требуется лезвие для поддержки материала во время его прокатки. Однако этот компромисс намного перевешивает его преимущества.
Helix Linear Technologies предлагает широчайший диапазон диаметров ходовых винтов, ходов и форм резьбы. Мы производим все наши резьбонакатные плашки собственными силами и специализируемся на специальных формах резьбы, разработанных для удовлетворения конкретных требований наших клиентов. Эти внутренние возможности позволяют нам быстро проектировать и производить прокатные штампы, что в некоторых случаях приводит к получению прокатного материала в течение одной недели.
Прецизионно катаные ходовые винты предлагают инженерам и проектировщикам машин высококачественные и экономичные решения для удовлетворения их требований к линейному перемещению. Свяжитесь с инженером по применению Helix Linear Technologies сегодня для консультации.
Компания Superior Thread Rolling Company Когда вы отправляете нам заказ на поставку, STR будет управлять всем производственным процессом для вас, от закупки сырья до проверки первого изделия AS9102.
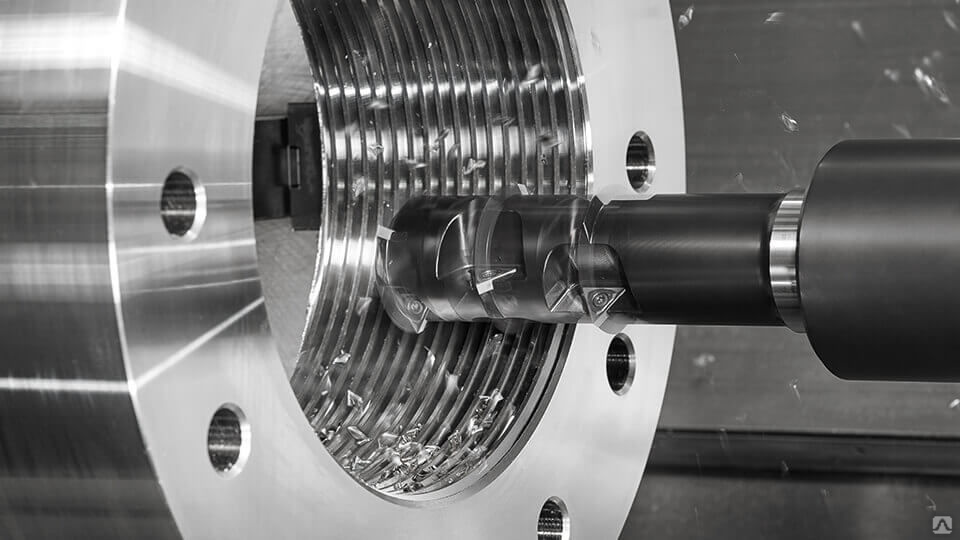
Ваш менеджер по работе с клиентами использует ERP-систему Superior для отслеживания статуса вашего заказа в режиме реального времени. Они будут вашим единственным контактным лицом на протяжении всего процесса, что сделает общение с STR простым и точным.
Компания Superior Thread Rolling производит полные детали для всех крупных авиакосмических компаний Prime и Tier 1 в мире. Мы используем бережливые ячейки с ЧПУ и поток единичных изделий, чтобы снизить производственные затраты и время выполнения заказа, обеспечивая при этом стабильное качество. Мы также можем предложить хранить запасы для вас, чтобы вы получали только то количество, которое вам нужно, когда они вам нужны.
Узнайте больше о наших комплексных услугах по производству!
- • com/wp-content/uploads/Manufactured-Parts-1024×768.jpg” data-bg-alt=”Manufactured Parts”> •
← →
Thread Rolling
Superior Thread Rolling — ведущий в мире поставщик услуг по накатыванию резьбы. Наш 70-летний опыт обеспечивает прочную основу для решения ваших самых сложных задач по нарезанию резьбы. Компания Superior продолжает лидировать в отрасли по накатыванию резьбы с максимально возможной производительностью. Команда инженеров, инспекторов, инженеров по качеству и менеджеров по работе с клиентами поддерживает лучшую команду экспертов по накатыванию резьбы в отрасли.
Узнайте больше о том, почему накатанные резьбы лучше!
Инжиниринг — Проектирование для обеспечения технологичности
Накатка резьбы — это не тот процесс, с которым большинство конструкторов сталкиваются ежедневно. Изготовленные на заказ детали, для которых требуется накатка резьбы, должны быть спроектированы должным образом с учетом ограничений процесса, при этом обеспечивая максимальную прочность детали. Мы являемся экспертами в проектировании для обеспечения технологичности аэрокосмических крепежных изделий и накатанной резьбы.
Наш инженерный персонал всегда готов помочь вам в вашем следующем проекте.
Узнайте больше о проектировании накатанной резьбы!
CNC-обработка
Superior Thread Rolling строит станки Lean CNC Cells в соответствии с потребностями наших клиентов. Эти бережливые ячейки используют поток единичных изделий для оптимизации пропускной способности при одновременном снижении вариаций, что приводит к меньшему количеству деталей, не соответствующих допускам. Мы будем рады обработать поставленный вами материал и вернуть детали для окончательной обработки или объединить наши услуги по механической обработке с нашими услугами по накатыванию резьбы в одном заказе!
Узнайте больше о наших бережливых ячейках с ЧПУ и потоке штучных изделий!
Бесцентровое шлифование
Превосходное бесцентровое шлифование резьбы позволяет выполнять большинство работ при подготовке к накатыванию резьбы. Мы также можем отшлифовать дополнительные поверхности на ваших деталях, такие как хвостовик болта, и мы будем рады обслужить вас только для шлифовки! Команда инженеров Superior Thread Rolling имеет опыт и знания в области выполнения требований после шлифовки в аэрокосмической промышленности, которые могут включать в себя снятие напряжения, травление ниталом или магнитную проверку. Мы можем выполнить эти операции после шлифовки и для вас!
Узнайте больше о наших возможностях измельчения!
Накатка галтелей и полировка
Superior Thread Rolling предлагает накатку галтелей и полировку как отдельные услуги или вместе с заказом услуг по накатыванию и/или шлифованию резьбы.
Угловая прокатка — это процесс холодной обработки, обычно используемый на нижней поверхности болта, который увеличивает прочность и усталостную долговечность детали.
Воронкообразная прокатка — это процесс холодной обработки для обработки канавок или поднутрений в детали. Полировка наименьшего диаметра с вашей стороны может увеличить прочность и усталостную долговечность вашего компонента.
Узнайте больше о преимуществах холодной обработки деталей!
Накатка
Superior Thread Rolling предлагает накатку как отдельную услугу или в сочетании с заказом чистового шлифования или накатки резьбы. Накатка — это процесс холодной обработки, при котором материал смещается (без резки!) в заданный узор. Накатка обычно используется для облегчения захвата деталей, а также может использоваться для создания помех в узлах с запрессовкой.
Узнайте больше о наших возможностях и схемах накатки!
Удаление заусенцев
При прорезании шпоночного паза или отверстия в резьбе, особенно в накатанной резьбе, правильное удаление заусенцев абсолютно необходимо для функционирования и производительности детали. Команда Superior Thread Rolling по удалению заусенцев является экспертом в области удаления заусенцев с резьбовых деталей. Сочетание услуг по удалению заусенцев с услугами по накатыванию резьбы и механической обработке позволяет производить детали с надлежащей посадкой, формой и функциями.
Узнайте больше о наших возможностях удаления заусенцев!
Хонингование
Superior Thread Rolling специализируется на производстве деталей с жесткими допусками, и многие из них имеют внутренние элементы, требующие хонингования. Хонингование — это специальный процесс, в котором используются абразивы для медленного удаления материала из отверстия, что позволяет нам соблюдать более жесткие допуски, чем то, на которое способен станок с ЧПУ.
Узнайте больше о наших возможностях хонингования!
Управление цепочками поставок
Superior Thread Rolling специализируется на деталях, требующих термообработки, гальванического покрытия, покрытия и испытаний. Наше расположение в аэрокосмическом производственном центре Лос-Анджелеса в сочетании с нашими долгосрочными отношениями с поставщиками позволяет нам предоставлять услуги внешней обработки на месте, сокращая время обработки и предоставляя нашим клиентам готовый продукт в соответствии с вашим ASL (Список утвержденных поставщиков).