Недостатки метода роквелла: Недостатки:
alexxlab | 03.05.2023 | 0 | Разное
Недостатки:
Метод можно применять только для материалов с твердостью до 650 HBW.
Твёрдость по Бринеллю зависит от нагрузки (обратный размерный эффект – reverse indentation size effect).
При вдавливании индентора по краям отпечатка из-за выдавливания материала образуются навалы и наплывы, что затрудняет измерение как диаметра, так и глубины отпечатка.
Из-за большого размера тела внедрения (шарика) метод неприменим для тонких образцов.
Преимущества:
Зная твёрдость по Бринеллю, можно быстро найти предел прочности и текучести материала, что важно для прикладных инженерных задач
2. Так как метод Бринелля — один из самых старых, накоплено много технической документации, где твёрдость материалов указана в соответствии с этим методом.
Данный метод является более точным по сравнению с методом Роквелла на более низких значениях твёрдости (ниже 30 HRC).
Также метод Бринелля менее критичен к чистоте подготовленной под замер твёрдости поверхности.
2)Твердость по Роквелу d=1,59 мм
Измерение твёрдости по относительной глубине проникновения индентора было предложено в 1908 году венским профессором Людвигом (Ludwig) в книге «Die Kegelprobe» (дословно «испытание конусом»)[1]. Метод определения относительной глубины исключал ошибки, связанные с механическими несовершенствами системы, такими как люфты и поверхностные дефекты.
Твердомер
Роквелла, машина для определения
относительной глубины проникновения,
был изобретен уроженцами штата Коннектикут Хью
М. Роквеллом (1890—1957) и Стэнли П. Роквеллом
(1886—1940). Потребность в этой машине была
вызвана необходимостью быстрого
определения эффектов термообработки
на обоймах стальных подшипников. Метод
Бринелля, изобретенный в 1900 году в
Швеции, был медленным, не применимым
для закалённых сталей, и оставлял слишком
большой отпечаток, чтобы рассматриваться
какнеразрушающий.
Ме́тод Рокве́лла является методом проверки твёрдости материалов. Из-за своей простоты этот метод является наиболее распространённым и основан на проникновении твёрдого наконечника в материал и измерении глубины проникновения.
Формулы для определения твёрдости:
Чем твёрже материал, тем меньше будет глубина проникновения наконечника в него. Чтобы при большей твёрдости материала не получалось большее число твёрдости по Роквеллу, вводят условную шкалу глубин, принимая за одно её деление глубину, равную 0.002 мм. При испытании алмазным конусом предельная глубина внедрения составляет 0.2 мм, или 0.2 / 0.002 = 100 делений, при испытании шариком — 0.26 мм, или 0.26 / 0.002 = 130 делений. Таким образом формулы для вычисления значения твёрдости будут выглядеть следующим образом:
а) при измерении по шкале А (HRA) и С (HRC):
Разность представляет
разность глубин погружения индентора
(в миллиметрах) после снятия основной
нагрузки и до её приложения (при
предварительном нагружении).
б) при измерении по шкале B (HRB):
HR (H/)-шарик
HRC, (H/)
3)Твердость по Виккерсу(hv,h/)
Метод Виккерса — метод измерения твёрдости металлов и сплавов по Виккерсу. Регламентируется ГОСТ 2999-75 и ISO 6507.[1]
Сущность метода заключается во вдавливании в испытуемый материал правильной четырёхгранной алмазной пирамиды с углом 136° между противоположными гранями.
Основным недостатком метода является зависимость измеряемой твердости от приложенной нагрузки или глубины внедрения индентора (явление размерного эффекта, часто называемого в англоязычной литературе indentation size effect). Особенно сильно эта зависимость проявляется при малых нагрузках.
Пластичность-св-во деформирваться под воздействием внешних сил без разрушения и сохраняет новую форму после прекращения работы действия внешних сил.
Параметры:
Относительное удлинение = -длина разрушения
Относительное сжатие
TKl- коффициент расширения
TKl==
Прочность–способность
материала сопротивляться действию
внешних сил не разрушаясь.
Параметры :
-сигма
= (H/)
=
Связь между результатами проверки на твёрдость и прочностными характеристиками материалов исследовались такими учёными-материаловедами, как Н. Н. Давиденков, М. П. Марковец и др. Используются методы определения предела текучести по результатам проверки на твёрдость вдавливанием. Такая связь была найдена, например, для высокохромистых нержавеющих сталей после различных режимовтермообработки. Среднее отклонение для конического алмазного индентора составляло всего +0,9 %. Были проведены исследования по нахождению связи между значениями твёрдости и другими характеристиками, определяемыми при растяжении, такими как предел прочности (временное сопротивление), относительное сужение и истинное сопротивление разрушению.
Лабораторная работа №2 – Лабораторная работа №2 Определение твердости материалов методом Бринелля –
скачать (139.9 kb.)
- Смотрите также:
- Лабораторная работа №1 Определение твердости металлов методами бринелля и роквелла (Документ)
- Лабораторная работа – Биохимия крови (Лабораторная работа)
- Лабораторная работа №19 по курсу общей физики.
Определение коэффициента Пуассона воздуха акустическим методом (Документ)
- Лежава А. Г., Барсуков В. Г (Документ)
- Лабораторная работа №3 «Определение фенола в воде методом высокоэффективной жидкостной хроматографией с электрохимическим детектированием» (Документ)
- Определение твердости металлов 2 часа (Документ)
- Вычислительная математика, с практическими заданиями в среде MathCAD (Документ)
- Лабораторная работа №2-7 Определение показателя адиабаты воздуха методом Клемана-Дезорма (Документ)
- Материаловедение изделий из кожи (Документ)
- Лабораторная работа №1 – Задачи одномерной оптимизации (Лабораторная работа)
- Лабораторная работа эм7 «Определение удельного заряда электрона методом магнитной фокусировки» (Документ)
- Свидунович Н.А., Окатова Г.П., Куис Д.В. Лабораторный практикум с использованием металлографического комплекса (Документ)
Лабораторная работа №2
Определение твердости материалов методом Бринелля
Цель работы:
1) ознакомиться с методами определения твердости;
2) приобрести практические навыки в работе с приборами для измерения твердости;
3) определить твердость трех образцов и рассчитать предел прочности этих образцов.
Материалы и оборудование:
Сталь;
Твердомер Роквелла и Бринелля.
Измерение твердости НВ по Бринеллю
Таблица 1
№ образца |
Материал |
Нагрузка, кг |
Диаметр шарика, мм |
№ отпечатка |
Диаметр отпечатка, мм |
НВ среднее по образцу | ||||
Измерение |
Среднее | |||||||||
1 |
2 | |||||||||
1 |
Сталь |
3000 |
10 |
1 |
3. ![]() |
3.05 |
3.05 |
401 | ||
2 |
2.9 |
2.9 |
2.9 |
444 | ||||||
3 |
2.9 |
2.9 |
2.9 |
444 |
429.7HB
Измерение твердости по Роквеллу HR_
Тип наконечника – шарик, нагрузка – 100 кг, шкала – красная
Тип наконечника – конус, нагрузка – 150 кг, шкала – черная
Таблица 2
№ образца |
Результаты измерения |
Среднее значение по образцу |
Обозначение единиц твердости |
Число НВ |
Материал | ||
1 |
2 |
3 | |||||
2 |
50. ![]() |
51.5 |
51.0 |
50.85 |
HRC |
495 |
Сталь |
3 |
77.0 |
77.5 |
78.0 |
77.5 |
HRB |
137 |
Al |
Обобщенная таблица результатов измерений и вычисление предела прочности
Таблица 3
№ образца |
Метод замера |
Число твердости по результатам замеров (НВ,HRC,HRB) |
НВ (после перевода по таблице или формуле) |
Материал |
Формула для расчета предела прочности |
Предел прочности | |
кг/мм2 |
МПа | ||||||
1 |
HB |
429. ![]() |
429.7 |
Сталь |
σв = 0,362 × НВ | ||
2 |
HRC |
50.85 |
495 |
Сталь |
σв = 0,362 × НВ | ||
3 |
HRB |
77.5 |
137 |
Al |
σв = 0,26 × НВ |
КОНТРОЛЬНЫЕ ВОПРОСЫ
Что называется твердостью? Методы определения твердости.
Твердостью называется сопротивление, оказываемое испытуемым телом внедрению в него другого более твердого тела.
Твердость определяют методом вдавливания с достаточно большой нагрузкой. Методы Роквелла и Бринелля.
Сущность процессов, происходящих в металле при определении твердости методом вдавливания.
Поверхностные слои металла, находящиеся под наконечником и вблизи него, пластически деформируются. После снятия нагрузки остается отпечаток.
Преимущества измерений твердости по сравнению с другими способами определения механических свойств.
Для измерения твердости не требуется изготовление специальных образцов, как это необходимо для определения предела прочности, характеристик пластичности и вязкости. Поэтому, при необходимости 100 % контроля деталей на механические свойства, твердость можно измерять на готовых деталях, которые затем использовать по назначению.
Измерение твердости проводится быстро. Например, при вдавливании по методу Роквелла за 30-60 секунд, а по методу Бринелля за 1-3 минуты.
Твердость можно измерять на деталях небольшой толщины, а также в очень тонких слоях, не превышающих (для некоторых способов измерения) десятых долей миллиметра, например, в поверхностных слоях цементированной, азотированной или закаленной стали.
Какие свойства металлов (механические и технологические) можно определить по значениям твердости?
По значениям твердости можно определять и некоторые пластические свойства металлов. Твердость, определенная вдавливанием, характеризует также предел выносливости некоторых металлов, в частности меди, дуралюмина и сталей в отожженном состоянии.
Приборы для замера твердости.
Твердомер Роквелла и Бринелля, лупа Бринелля.
Метод Бринелля.
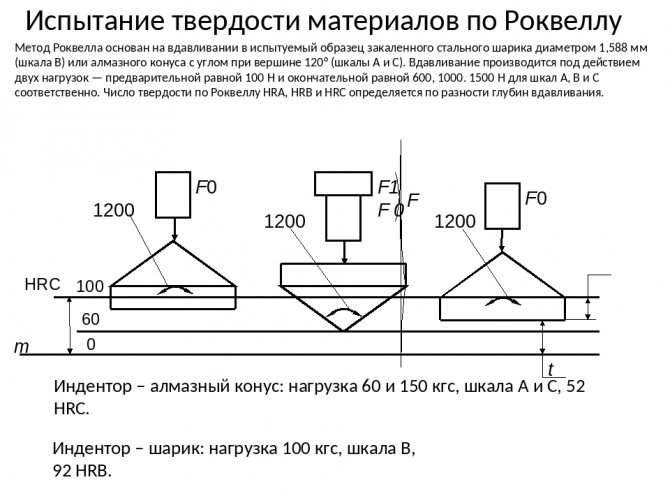
При испытании твердости по Бринеллю в испытуемый материал под определенной нагрузкой Р (от 62,5 до 3000 кг) вдавливается стальной закаленный шарик диаметром D (2,5; 5 или 10 мм. Шарик оставляет на поверхности металла отпечаток, по величине которого судят о твердости испытуемого металла.
Числом твердости по Бринеллю называется отношение нагрузки Р, передаваемой через шарик на образец, к площади поверхности образовавшейся при этом лунки F. Эта величина обозначается НВ и равняется отношению нагрузки Р к площади отпечатка F. Размерность твердости НВ – кг/мм2
Порядок замера твердости по Бринеллю
Для замера твердости испытуемый образец ставят на столик, расположенный на подъемном винте.

устанавливают съемные грузы. В зависимости от количества этих грузов нагрузка на образец может изменяться от 62,5 до 3000 кг.
Для подачи на шарик основной нагрузки включить электромотор, нажав на кнопку на корпусе прибора.
После автоматического отключения электромотора опустить столик вращением маховика.
Замерить с помощью лупы Бринелля диаметр отпечатка по схеме, приведенной на рис.2. На рис. 1 dопт = 3,5 мм.
По найденному диаметру отпечатка, пользуясь таблицей (см. приложение) или формулой (2), найти число твердости по Бринеллю (НВ) в кг/мм2.
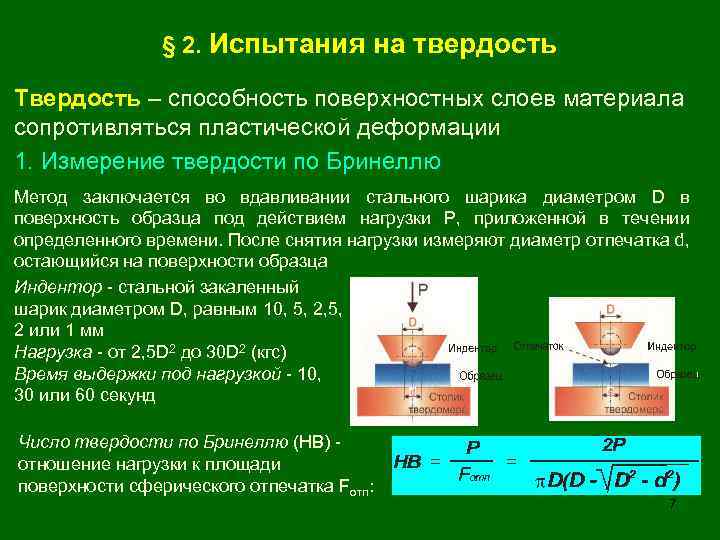
Недостатки метода Бринелля
На прессе Бринелля нельзя испытывать твердость тонкого материала, поскольку стальной шарик продавливает этот слой. Толщина испытуемого должна быть не меньше 10-кратной глубины отпечатка.
Невозможность производить испытания металлов, имеющих твердость более 450 ед. по Бринеллю, так как при этом деформируется сам шарик, и результаты испытания будут неточными.
Преимущества метода Бринелля
Преимуществами этого метода являются: простота, достаточная точность, минимальные требования к чистоте поверхности по сравнению с другими методами, а также наличие устойчивой связи НВ с величиной σв.
Прибор для замера твердости по Роквеллу. Как обозначается твердость по Роквеллу? Применяемые наконечники и нагрузки, правило выбора. Порядок измерения твердости. Шкалы, по которым производится отсчет.
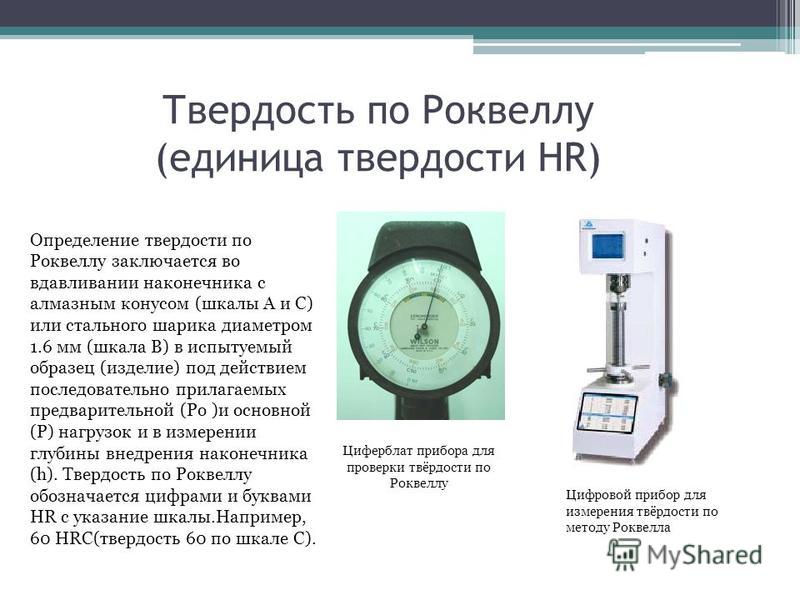
Испытание твердости металлов по способу Роквелла в соответствии с ГОСТ 9013-59 производится вдавливанием в испытуемый образец алмазного конуса с углом при вершине 120 ° или стального закаленного шарика D = 1,59 мм (1/16″) под действием двух последовательно прилагаемых нагрузок – предварительной (10 кг) и общей (предварительная + основная) в 60; 100 или 150 кг. Предварительное нагружение производят для того, чтобы исключить влияние упругой деформации и различной степени чистоты измеряемой поверхности на результаты измерений.
О твердости материала судят не по диаметру отпечатка, а по глубине лунки, образующейся после вдавливания конуса или шарика, величина которой определяется в ходе испытаний по разности глубин вдавливания индентора под действием двух последовательно приложенных нагрузок (предварительной и основной). Эта разность характеризует твердость испытуемого материала по Роквеллу (HR).
Для численной характеристики твердости введена условная шкала с цифрами, нанесенными в порядке, обратном перемещению индентора в момент приложения нагрузки, причем внедрение наконечника на 0,002 мм соответствует перемещению стрелки индикаторной головки на одно деление. Число твердости по Роквеллу есть отвлеченное число. Оно сопровождается буквами HRC, HRB или HRA в зависимости от условий испытания (используемого индентора и общей нагрузки). Числа твердости по Роквеллу, выраженные в условных единицах, связываются с углублением конуса или шарика формулами (3), (4).
HRC = 100 – ((h-h0)/0,002) (3)
HRB = 130 – ((h-ho)/0,002) (4), где
h0 – глубина внедрения наконечника в испытуемый образец под действием предварительной нагрузки;
h – глубина внедрения наконечника под действие общей нагрузки.
На циферблате индикатора (рис.1) имеются две шкалы – красная внутренняя и черная наружная.
Рис. 1. Индикатор
Красной шкалой пользуются при испытаниях на твердость шариком: она смещена относительно нулевого положения черной шкалы на 30 делений. Необходимость смещения вызвана тем, что глубина вдавливания при стандартных нагрузках на шарик получается более 0,2 мм, т.е. стрелка при вдавливании делает поворот более чем на 100 делений.
Черной шкалой пользуются при испытании на твердость алмазным наконечником: ее нулевое положение совпадает с начальным положением стрелки.
При вдавливании стального шарика нагрузка составляет 100 кг, отсчет ведут по красной шкале. Твердость обозначают HRB.
При вдавливании алмазного конуса нагрузка составляет 150 кг, отсчет ведут по черной шкале. Твердость обозначают HRC.
При вдавливании алмазного конуса при нагрузке 60 кг и замере твердости алмазным конусом отсчет ведут по черной шкале, а твердость обозначают HRA.
Измерения алмазным конусом с нагрузкой 150 кг (HRC) проводят:
а) для материалов с твердостью более НВ 450;
б) для материалов средней твердости более НВ 230, как более быстрым способом определения, оставляющим, кроме того, меньший след на измеряемой поверхности, чем при испытаниях по Бринеллю;
в) для определения твердости тонких поверхностных слоев (не менее 0,5 мм).
Измерения алмазным конусом с нагрузкой 60 кг (HRA) применяют для очень твердых металлов (более НВ 700), например, твердых сплавов, когда вдавливание алмазного конуса с большой нагрузкой может вызвать выкрашивание алмаза, а также для измерения твердых поверхностных слоев толщиной 0,3-0,5 мм.
Порядок замера твердости по Роквеллу
Визуально проверить соответствие индентора и нагрузки, установленных на приборе:
(HRC: индентор – конус, общая нагрузка 150 кг, шкала черная; HRB: индентор – шарик, общая нагрузка 100 кг, шкала красная).
Установить образец на столик, расположенный на подъемном винте.
Дать предварительную нагрузку, поднимая столик с образцом поворотом маховика и следя за движением стрелок (большой и маленькой) на шкале прибора. Предварительную нагрузку контролировать по маленькой стрелке прибора: она должна встать вертикально и указывать на красную точку.

Поворотом шкалы совместить нуль черной шкалы с концом большой стрелки (для любого варианта: HRC, HRB, HRA).
Подать на индентор основную нагрузку ручным нажатием на педаль прибора и дождаться окончания выдержки (прибор с электромотором, длительность выдержки контролируется автоматически).
После снятия основной нагрузки при сохранении предварительного поджатая по показаниям большой стрелки записать результат измерения HRC (по черной шкале) или HRB (по красной шкале).
Разгрузить образец поворотом маховичка.
Преимущества метода Роквелла
Метод Роквелла получил широкое применение в лабораторной и производственной практике. Он позволяет замерять твердость на готовых деталях, так как на поверхности остается отпечаток очень малой величины, который не влияет на работу детали.
Этим методом можно проверять металлы очень мягкие и очень твердые, а также измерять твердость очень тонких деталей и поверхностных слоев. Данный метод отличается высокой производительностью.
Недостатки метода Роквелла
Недостатками этого метода являются необходимость соблюдения параллельности проверяемых поверхностей, относительно низкая точность измерений по сравнению с другими методами и необходимость более тщательной подготовки поверхностей.
Как определить предел прочности материалов, твердость которых измерена на приборе Бринелля или Роквелла. Для каких материалов можно произвести такое определение?
Между числом твердости по Бринеллю НВ и пределом прочности при разрыве (σв) в кг/мм2 существует следующее примерное соотношение:
Для стали с НВ = 125-175 σв = 0,343 × НВ
Для стали при НВ более 175 σв = 0,362 × НВ
Для алюминиевого литья σв = 0,26 × НВ
Для бронзы и латуни отожженной σв = 0,55 × НВ
Для бронзы и латуни наклепанной σв = 0,40 × НВ
Для серого чугуна σв = 1/6 × (НВ-40)
Для цинкового сплава σв = 0,09 × НВ
Для вычисления предела прочности исследуемого материала необходимо выбрать расчетную формулу в зависимости от марки этого материала и произвести расчет, подставив в формулу значение твердости НВ.
Полученное значение σв выражается в кг/мм2. Для перевода этого значения в МПа необходимо его умножить на 9,8. Так 100 кг/мм2 = 980 МПа.
На каком приборе можно определить твердость крупных образцов или деталей и на каком тонких (от 0,5 до 2 мм) с твердостью до 230 НВ, то же с твердостью до 450 НВ, то же с твердостью выше 450НВ.
Твердость крупных и тонких деталей на твердомере Роквелла, а на прессе Бринелля нельзя испытывать твердость тонкого материала, поскольку стальной шарик продавливает этот слой. Толщина испытуемого должна быть не меньше 10-кратной глубины отпечатка.
На каком приборе можно замерить твердость тонких поверхностных слоев?
Твердомер Роквелла
Лабораторная работа №2
Эксперимент по определению твердости по Роквеллу и его преимущества
Содержание
- Что такое твердость по Роквеллу?
- Эксперимент по определению твердости по Роквеллу
- Преимущества
- Недостатки
- Разница между твердостью по Роквеллу и по Бринеллю
Часто задаваемые сомнения
- Что такое испытание на твердость по Роквеллу?
- Как проверить твердость?
- что означает число твердости по Роквеллу?
Введение
Что такое твердость по Роквеллу?
Перед этим вот определение термина, который мы будем использовать в этом посте.
Твердость
(существительное)
- Качество или состояние твердости.
- Это мера сопротивления локальной пластической деформации.
- Изменение межузельных атомов и плотность дислокаций контролируют его.
Твердость по Роквеллу — это не что иное, как значение для конкретного материала, полученное с помощью твердомера по Роквеллу.
Это значение обозначается как «ЧСС». Обозначение «HR» читается как твердость по Роквеллу.
Хью М. изобрел этот процесс. Роквелл и Стэнли П. Роквелл. До изобретения существовало несколько машин, но была потребность в неразрушающем методе.
Неразрушающий метод
- Обозначается NDT (неразрушающий контроль)
- Это метод осмотра и тестирования образца без каких-либо повреждений, чтобы его можно было использовать для дальнейшего процесса, если он окажется в порядке.
Первая машина для испытания стальных колец подшипников.
Эксперимент по определению твердости по Роквеллу
Испытание на твердость по Роквеллу,
- Метод, используемый для расчета твердости материала.
- Способ узнать значение HRC.
- Это процедура дифференциальной глубины.
Принципиальная теория важна.
- Держите деталь под алмазным индентором в указанном месте на станке.
- Приложите к объекту небольшую нагрузку (около 3 кгс). Удерживайте индентор в этом положении в течение заданного времени. Установите шкалу, которая следует за движением индентора, в исходное положение.
- Измерьте глубину вмятины по показаниям шкалы.
- Теперь увеличьте нагрузку до основной нагрузки (около 150 кгс).
- После определенного времени выдержки снова запишите показания на весах.
- Медленно отпустите нагрузку и снова доведите ее до минимального значения нагрузки.
- Как и в шаге 1, удерживайте нагрузку в течение некоторого времени и запишите значение глубины.
- Полностью отпустите нагрузку.
Существует 30 различных типов шкал Роквелла, в которых используются различные инденторы и значения усилия.
Прочтите: Все об электрическом изоляторе: Электрический разъединитель
Выбор шкалы зависит от размера, формы и материала образца, а также других важных факторов, влияющих на конечный результат.
Время задержки обычно составляет несколько секунд, например, 5 секунд, выберите из стандартной таблицы.
Образец упруго восстанавливается после снятия основной нагрузки (незначительная нагрузка все еще действует) и останавливается на высоте «h».
Следующая формула вычисляет число твердости по Роквеллу.
Значение твердости по Роквеллу = Н – ч
Где N — константа из стандартных таблиц, специфичных для шкал твердости, которые мы используем в эксперименте.
Преимущества
- Его легче проводить, чем любой другой тип теста.
- Результаты более точны, чем на других машинах.
- Это занимает меньше времени – Быстро.
- Образец можно будет использовать после теста.
- Прибор может тестировать металлы, а также некоторые пластмассы.
Недостатки
- Не подходит для тонких материалов.
- Точность для более мягких материалов низкая, так как тест полностью зависит от отпечатка индентора.
Разница между твердостью по Роквеллу и по Бринеллю
Ниже приведена сравнительная таблица твердости по Роквеллу и твердости по Бринеллю 9.0030
Роквелл | Бринелль |
Это быстро и легко выполнить. | Это отнимает много времени. |
Глубина измеряется. | Измеряется диаметр слепка. |
Используются сравнительно небольшие нагрузки. | В этом методе используются нагрузки около 3000 кгс. |
Это неразрушающий метод. Образец можно использовать после испытания, так как создается очень маленький оттиск. | Это деструктивный метод. Производимое впечатление больше, чем у Rockwell. |
Материал с шероховатой поверхностью дает ошибки. | Материал с грубой или шероховатой поверхностью может быть проверен точно. |
Значение твердости считывается непосредственно на шкале. | Требуется оптическая оценка. |
Подробнее
Новое сообщение Старый пост Дом
Подписаться на: Опубликовать комментарии (Atom)
Испытание на твердость по Роквеллу и все, что вам нужно о нем знать
В сфере производства устоялось мнение, что определенный объект так же хорош, как и материалы, из которых он сделан. Таким образом, специалисты по производству должны убедиться, что каждый компонент, материал и обработка материала, используемые для создания определенного устройства или машины, будут прочными и долговечными.
Здесь в игру вступает испытание на твердость по Роквеллу, поскольку оно было специально разработано для измерения долговечности материала. Система предназначена для испытаний в соответствии со стандартом ASTM E18. Но прежде чем вы решите инвестировать в твердомер по Роквеллу, вам нужно понять несколько вещей, связанных с тестом.
Что такое испытание на твердость по Роквеллу?
Испытание на твердость по Роквеллу на самом деле является одним из нескольких испытаний, направленных на оценку совместимости материала в качестве компонента с объектом на основе их прочности и долговечности. Другие тесты в серии включают методы Кнупа, Бринелля и Виккерса.
Концепция теста на твердость по Роквеллу по существу аналогична его аналогам. Образец материала подается либо на цифровой, либо на ручной твердомер по Роквеллу, который затем сбрасывает заданную нагрузку, заканчивающуюся индентором, на поверхность. Тогда прочность материала будет определяться характером отпечатка, оставленного на образце.
Однако метод Роквелла сильно отличается от методов Кнупа, Виккерса и Бринелля в одном аспекте. В то время как другие измеряют прочность по размеру или ширине оставшейся вмятины, метод Роквелла измеряет прочность по глубине. Обоснование метода Роквелла заключается в том, что долговечность материала лучше оценивается по его способности сохранять структурную целостность при повреждениях, которые не являются просто поверхностными. Вот почему этот метод широко используется в области металлургии и машиностроения, где целостность материала нельзя просто наблюдать на уровне поверхности.
Как проводится тест?
Как уже было сказано, испытание на твердость по Роквеллу в основном аналогично другим методам в том смысле, что прочность измеряется посредством приложения нагрузки к материалу. Однако тест Роквелла делает это иначе.
Сначала к поверхности прикладывается небольшая нагрузка, которая определяет нулевое положение. Как только нулевое положение установлено, к материалу прикладывается большая основная нагрузка, которая вызывает вдавливание.
При этом малая нагрузка сохраняется на протяжении всего теста. Некоторые варианты теста требуют, чтобы основная нагрузка оставалась на материале до тех пор, пока вмятина, которую он сделал, не станет достаточно глубокой.
После снятия основной нагрузки измеряется глубина проникновения, начиная с нулевого положения. Как и во всех испытаниях на твердость, прочность материала обратно пропорциональна нанесенному ему повреждению. Таким образом, в соответствии с методом Роквелла материалы имеют тенденцию иметь более высокую оценку по шкале твердости, если отпечаток, оставленный на них, находится ближе к поверхности.
Почему метод Роквелла надежен?
В некоторых случаях предпочтительнее измерять прочность материалов с помощью твердомера по Роквеллу. Это связано с рядом преимуществ, перечисленных ниже.
1. Подготовка материала не требуется
В некоторых тестах образец материала должен быть отшлифован, отшлифован, разрезан и отполирован, чтобы получить наиболее точные показания. По сути, для таких тестов, как метод Кнупа и Виккерса, поверхность образца должна быть как можно более плоской с минимальными изменениями или без них.
В методе Роквелла, поскольку измеряется глубина отпечатка, нет необходимости подвергать образец различным процессам, чтобы сделать тест точным. Именно поэтому метод Роквелла используется при тестировании неочищенных материалов, таких как руда.
2. Без оптической оценки
При использовании метода Роквелла значение твердости считывается напрямую, поскольку большинство твердомеров, использующих этот метод, не используют диагональные шкалы для измерения твердости. Это верно, если вы выберете цифровой твердомер по Роквеллу, так как значения сразу же отображаются на экране после нескольких секунд обработки.
При отсутствии оптической оценки вероятность того, что оператор сделает ошибку в показаниях, значительно снижается.
3. Экономичность
Поскольку твердомеры по Роквеллу не нуждаются в сложных оптических системах оценки, они имеют довольно короткие циклы испытаний. Это позволит повысить эффективность процесса тестирования, когда операторы смогут быстро переходить от одного образца к другому.
Добавьте к этому тот факт, что тестеры Роквелла значительно дешевле других приборов, метод Роквелла обеспечивает довольно экономичный процесс. И это не единственный способ, которым метод Роквелла помогает операторам экономить на затратах.
4. Неразрушающий характер
Несмотря на то, что тест оставляет значительный отпечаток на материале, метод Роквелла является неразрушающим и неинвазивным процессом. После каждого испытания сам образец можно использовать для других целей.
Это означает, что метод Роквелла может эффективно помочь операторам сократить количество отходов. Если ваша мастерская также перерабатывает сырье, это может помочь снизить эксплуатационные расходы.
Насколько точна система определения твердости по Роквеллу?
Система определения твердости по Роквеллу RockGen была разработана для проверки уровня твердости металла на основе вмятин, которые они оставляют на испытуемом материале в соответствии со шкалой Роквелла. Машина способна измерять разрешение материала с точностью до 0,001 дюйма. Твердомеры NextGen по Роквеллу гарантированно обеспечивают одну из самых высоких точности на рынке. Измерение твердости по Роквеллу рассчитывается путем применения предварительного силового испытания, называемого предварительной нагрузкой, в течение определенного периода времени, называемого временем выдержки.
По истечении указанного периода времени будет применена дополнительная нагрузка, также известная как основная нагрузка. Теперь приложено полное усилие, и измерения глубины отпечатка производятся от точки отсчета до конечной глубины пенетратора после того, как он подвергся основной нагрузке. Расстояния между двумя отпечатками известны как значения твердости по Роквеллу.
Сколько тестов предусмотрено для обычных тестовых весов Роквелла?
Твердомер по Роквеллу имеет множество различных шкал в зависимости от применения прибора на различных материалах. Существует в общей сложности 30 шкал твердости по Роквеллу, которые можно использовать для определения твердости и ее значения. При испытании на обычных весах Роквелла используется предварительная нагрузка 10 кгс и основная нагрузка 50 кгс, 100 кгс или 150 кгс. Поверхностные весы Роквелла предназначены для материалов толщиной 0,15 мм или 0,0006 дюйма, для которых используется предварительная нагрузка 3 кгс и основная нагрузка 15 кгс, 30 кгс или 45 кгс.
Каковы ограничения испытательных систем Rockwell?
Испытательные системы Rockwell Testing зависят от тестируемого материала, включая твердость, толщину, расположение отпечатков и ограничения масштаба тестируемых материалов. Испытываемый материал должен быть как минимум в 10 раз толще, чем отпечаток Роквелла, когда он сделан из материала.
Твердомеры NextGen по Роквеллу входят в число ведущих машин Rockwell Manufacturing и могут предоставить вам все опции, необходимые вашей компании, включая машины Rockwell Twin Digital Testing. Модель Twin является одним из самых популярных наших продуктов, позволяющих оператору тестировать как обычные, так и поверхностные шкалы Роквелла на одном приборе.