Никелевое покрытие: Никелевое покрытие
alexxlab | 18.03.2023 | 0 | Разное
1.2 Никелевые покрытия
Никель – серебристо-серый твердый металл с едва заметным желтоватым блеском. Он имеет очень высокую износостойкость. Разновидности никеля с более высоким содержанием фосфора имеют исключительную устойчивость к коррозии. Никель часто используется в качестве металлической подложки благодаря своим выравнивающим, сглаживающим и изолирующим свойствам. Он повышает устойчивость металлов к «агрессии» со стороны таких солей как цианид меди или серебра. Как уже было сказано, никель – твердый металл с низкой пластичностью. Поэтому он не рекомендуется в тех случаях, когда требуется обеспечить определенную гибкость покрытия.
Различают 2 вида покрытия никелем – химическое и электрохимическое.
Химическое никелирование – применяют для покрытия никелем деталей любой конфигурации. Химически восстановленный никель обладает высокой коррозионной стойкостью, большой твердостью и износостойкостью, которые могут быть значительно повышены при термической обработке (после 10-15 мин.
NiCl2 + NaH2PO2 + H2O → NaH2PO3 + 2HCl + Ni
Одновременно происходит гидролиз гипофосфита натрия. Степень полезного использования гипофосфита принимают около 40%.
Восстановление никеля из его солей гипофосфитом самопроизвольно начинается только на металлах группы железа, катализирующих этот процесс. Для покрытия других каталитически неактивных металлов (например, меди, латуни) необходим контакт этих металлов в растворе с алюминием или другими более электроотрицательными, чем никель, металлами. Для этой цели используют активирование поверхности обработкой в растворе хлористого палладия (0,1 – 0,5 г/л) в течение 10-60 с. На некоторых металлах, таких, как свинец, олово, цинк, кадмий, никелевое покрытие не образуется даже при использовании метода контактного нанесения и активирования.
Состав раствора и режим никелирования:
Состав электролита (г/л) и режим работы | Электролит щелочной |
Никель хлористый NiCl2 | 20-30 |
Натрия гипофосфит Na(PH2O2) | 15-25 |
Натрий лиомннокислый Na3C6H5O7 | 30-50 |
Аммоний хлористый NH4 | 30-40 |
Аммиак водный 25% Nh4 | 70-100 мл/л |
pH | 8-9 |
Температура, ° | 80-90 |
Скорость осаждения | 10-15 мкм/час |
Покрытия, полученные в кислых растворах, отличаются меньшей пористостью, чем из щелочных растворов (при толщине выше 12 мкм покрытия практически беспористые). Из кислых растворов химического никелирования рекомендуется следующий состав и режим никелирования:
Состав электролита (г/л) и режим работы | Электролит кислый |
Никель сернокислый NiSO4 | 20-30 |
Натрий уксуснокислый CH3COONa | 10-20 |
Натрия гипофосфит Na(PH2 O2) | 20-25 |
Тиомочивина CS(NH2)2 | 0.03 |
Кислота уксусная (ледяная) CH3COOH | 6-10 мл/л |
pH | 4,3-5,0 |
Температура, ° | 85-95 |
Скорость осаждения | 10-15 мкм/час |
Химическое никелирование осуществляют в стеклянных, фарфоровых или железных эмалированных ваннах. В качестве материала подвесок применяют углеродистую сталь.
Гальваническое никелирование – позволяет получать из различных электролитов либо матовые малопористые либо блестящие декоративные покрытия. В зависимости от толщины покрытия они обеспечивают различные степени антикоррозионной защиты, хорошую устойчивость поверхности к истиранию и невысокий коэффициент температурного расширения. Прочность на растяжение и жесткость при этом относительно низкие, а внутреннее напряжение – сравнительно высокое. Поэтому такие покрытия не рекомендуется использовать для технических целей, предполагающих возможное изгибание и деформацию детали.
Сульфатные электролиты никелирования.
В практике гальваностегии наиболее распространены электролиты на основе сульфата никеля, поскольку эта соль очень хорошо растворима в воде (до 400 г/л).
В качестве депассиваторов анодов в эти растворы вводят хлорид никеля, который препятствует запассивированию анодов и прекращению электролиза. В роли буферного соединения чаще всего используют борную кислоту. Можно так же использовать соли уксусной кислоты. Для электролитов с низким значением pH более эффективны добавки буферных соединений в виде фторида натрия и других фторидов.
Сульфатные электролиты никелирования имеют высокий выход по току: 90-100%
Составы электролитов для матового никелирования и режимы работы:
Состав электролита (г/л) и режим работы | Элект-т № 1 | Элект-т № 2 | Элект-т № 3 | Элект-т № 4 | Элект-т № 5 | Элект-т № 6 |
Никеля сульфат NiSO4 | 140-200 | 150-200 | 140-150 | 300-350 | 400 | 240 |
Никеля хлорид NiCl2 | 30-40 | – | – | 45-60 | – | 30 |
Натрия хлорид NaCl | – | 10-15 | 5-10 | – | – | – |
Борная кислота H3BO3 | 25-40 | 25-30 | 25-30 | 30-40 | 25-40 | |
Натрия сульфат NaSO4 | 60-80 | 40-50 | 40-50 | – | – | – |
Магния сульфат MgSO4 | – | 50-60 | 25-30 | – | – | – |
Натрия фторид NaF | – | – | – | – | 2-3 | – |
Янтарная к-та НООС-СН2-СН2-СООН | – | – | – | – | – | 30 |
Натрия лаурилсульфат C12H25SO4Na | – | – | – | – | – | 0,05-0,1 |
pH | 5,2-5,8 | 5,0-5,5 | 5,0-5,5 | 1,5-4,5 | 2-3 | 2,5-3,5 |
Температура, ° | 20-55 | 20-30 | 20-35 | 45-65 | 50-60 | 50-60 |
Катодная плотность тока, А/дм2 | 0,5-2,0 | 0,5-2,0 | 0,5-2,0 | 2,5-10 | 5-10 | 5-30 |
Электролит № 1 – предусмотрен ГОСТ 9. 305-84.
Электролиты № 2, 4 – для стационарных ванн.
Электролит № 3 – для колокольных и барабанных ванн.
Электролит № 6 – для получения осадков никеля при высоких плотностях тока.
Для получения блестящих никелевых покрытий применяют специальные блескообразующие добавки, которые в свою очередь обладают эффектом микровыравнивания катодной поверхности, делая ее относительно ровной и блестящей. Так же блескообразующие добавки понижают питингообразование, улучшая тем самым качество получаемого покрытия.
Составы электролитов для блестящего никелирования и режимы работы:
Состав электролита (г/л) и режим работы | Элект-т № 1 | Элект-т № 2 | Элект-т № 3 | Элект-т № 4 | Элект-т № 5 | Элект-т № 6 |
Никеля сульфат NiSO4 | 250-300 | 250-300 | 100-350 | 200-250 | 250-300 | 250-300 |
Никеля хлорид NiCl2 | 50-60 | – | 30-200 | – | 30 | – |
Натрия хлорид NaCl | – | 10-15 | – | 10-15 | – | 10-15 |
Борная кислота H3BO3 | 25-40 | 30-40 | 30-50 | 30 | 30 | 25-40 |
Натрия фторид NaF | – | – | – | – | – | 5-6 |
1,4-бутиндиол C4H6O2 | 0,2-0,5 | 0,2-3,0 | – | 0,2-0,3 | – | – |
Сахарин C7H5NO3S | 0,7-1,2 | – | 0,3-2,0 | – | 1-2 | – |
Фталимид C8H5NO2 | 0,08-0,12 | – | – | – | – | – |
Формальдегид HCHO | – | – | – | – | – | 0,4-0,8 |
Хлорамин Б C6H5SO2N(NaCl)•H2O | – | 1-2 | – | – | – | |
Кумарин C9H6O2 | – | – | – | – | 0,2-1,0 | – |
Пропаргиловый спирт C3H4O | – | – | – | – | 0,056-0,112 | – |
Паратолуолсульфамид | – | – | 2,0 | – | – | – |
2,6-нафталиндисульфокислота C10H6(SO3H)2 | – | – | – | – | – | 2-4 |
1,5-нафталиндисульфокислота C10H6(SO3H)2 | – | – | – | 1,5-2,0 | – | – |
Моющее средство «Прогресс» | – | 0,1-0,2 | 0,1-0,2 | 0,1-0,2 | – | – |
Сульфонол | – | – | – | – | – | 0,015 |
НИБ-3, мл/л | – | – | 0,3-10,0 | – | – | – |
Выравнивающая композиция | – | – | 0,03-0,15 | – | – | – |
pH | 4-5 | 4-5 | 3-5 | 4,5-,5,5 | 4,0-4,5 | 5,8-6,0 |
Температура, ° | 55+(-5) | 50+(-5) | 55+(-5) | 45+(-5) | 50+(-10) | 45+(-5) |
Катодная плотность тока, А/дм2 | 3-8 | 2-5 | 2-8 | 2-4 | 1-10 | 3-5,0 |
Все добавки, входящие в состав никелевых электролитов, за исключением кумарина, растворяются в подогретом электролите или горячей воде. Кумарин растворяется в ледяной уксусной кислоте или борной кислоте в соотношении 1:4.
Большинство электролитов блестящего никелирования содержат серосодержащие добавки. Это приводит к снижению коррозионной стойкости блестящих никелевых покрытий по сравнению с матовыми, механически полированными осадками, полученными из электролитов без добавок.
Фторборатные электролиты никелирования.
Эти электролиты обладают хорошими буферными свойствами и большей устойчивостью по сравнению с некоторыми сульфатными электролитами никелирования. Выход по току в этих электролитах достигает 100%. Осаждение можно вести при высоких плотностях тока – до 20 А/дм2.
Состав раствора и режим осаждения:
Состав электролита (г/л) и режим работы | Электролит |
Фторборат никеля Ni (BF4)2 | 300-400 |
Хлорид никеля NiCl2 | 10-15 |
Борная кислота H3BO3 | 10-30 |
pH | 2,7-3,5 |
Температура, ° | 10-20 |
Катодная плотность тока, А/дм2 | 10-15 |
Электролит выделяется высокой интенсивностью процесса, меньшей напряженностью и большей эластичностью осадков (по сравнению с сульфатными электролитами), что определяет целесообразность его применения в гальванопластике. Микротвердость осадков, полученных из данного электролита, достигает 3,0 – 3,5 ГПа.
Сульфаматные электролиты никелирования.
Сульфаматные электролиты образуют покрытия с минимальными внутренними напряжениями, поэтому их применяют для нанесения толстых слоев осадков никеля в гальванопластике, а так же при металлизации диэлектриков по проводящему слою. Выход по току 100%.
Состав раствора и режим осаждения:
Состав электролита (г/л) и режим работы | Электролит |
Сульфамат никеля (NH2SO3)2Ni | 300-400 |
Хлорид никеля NiCl2 | 10-15 |
Борная кислота HBO3 | 25-40 |
Сахарин C7H5NO3S | 0,5-1,5 |
Лаурил (додецил) сульфат натрия C12H25SO4Na | 0,1-1,0 |
pH | 3-4,5 |
Температура, ° | 40-55 |
Катодная плотность тока, А/дм2 | 1-12 |
Черное никелирование.
Процесс черного никелирования заключается в получении покрытий черного цвета. Покрытие обладает более высокой твердостью и прочностью по сравнению с оксидными пленками и широко используется для отделки различных изделий. Толщина слоя черного никелирования обычно не превышает 0,5-0,7 мкм. Осадки обладают не высокой коррозионной стойкостью и не высокой адгезией к поверхности стальных изделий, поэтому предварительно необходимо нанесение на деталь медного или никелевого покрытия.
Составы растворов и режим осаждения:
Состав электролита (г/л) и режим работы | Электролит №1 | Электролит №2 | Электролит №3 | Электролит №4 |
Никеля сульфат NiSO4 | 50 | 75 | 50 | 50 |
Цинка сульфат ZnSO4 | 25 | 25 | 25 | 25 |
Никель-аммония сульфат (NH4)2SO4•NiSО4 | – | 45 | – | – |
Аммония сульфат (Nh5)2SO4 | 15 | – | 15 | 15 |
Калия роданид KCNS | 32 | – | 25 | 30 |
Натрия роданид NaCNS | – | 15 | – | – |
Борная кислота H3BO3 | – | 25 | – | – |
Натрия ацетат CH3COONa | – | – | – | 15 |
Лимонная кислота H3C6H5O7 | – | – | 2 | – |
pH | 4,5-5,5 | 5,6-5,9 | 5,2-5,5 | 4,5-5,5 |
Температура, ° | 18-25 | 40-50 | 18-25 | 30-40 |
Катодная плотность тока, А/дм2 | 0,1-0,15 | 1,0-1,3 | 0,1 | 0,1-0,3 |
Чтобы предупредить пассивирование катодных контактов необходимо протравливать их в 50% растворе серной кислоты после каждой загрузки. Для повышения коррозионной стойкости черные никелевые покрытия необходимо промасливать или покрывать бесцветным лаком.
Свойства и область применения никелевых покрытий | Никелирование
Никель является металлом подгруппы железа, который получил в гальванотехнике наиболее широкое применение.
По сравнению с меднением, латунированием, серебрением и др. никелирование получило промышленное применение значительно позднее, но уже с конца XIX столетия этот процесс стал наиболее распространенным методом «облагораживания» поверхности металлических изделий. Лишь в двадцатые годы текущего столетия широкое применение получил другой процесс — хромирование, который, казалось, вытеснит никелирование. Однако оба эти процесса — никелирование и хромирование для защитно-декоративных целей применяются комбинированно, т. е. изделия сперва никелируют и затем покрывают тонким слоем хрома (десятые доли микрона). Роль никелевого покрытия при этом не умаляется, напротив к нему предъявляются повышенные требования.
Широкое распространение никелирования в гальванотехнике объясняется ценными физико-химическими, свойствами электролитически осажденного никеля. Хотя в ряде напряжений никель стоит выше водорода, вследствие сильно выраженной склонности к пассивированию, однако он оказывается достаточно стойким против атмосферного воздуха, щелочей и некоторых кислот. По отношению к железу никель имеет менее электроотрицательный потенциал, следовательно, основной металл — железо — защищается никелем от коррозии лишь при отсутствии пор в покрытии.
Никелевые покрытия, полученные из растворов простых солей, имеют весьма тонкую структуру, и так как в то же время электролитический никель прекрасно принимает полировку, то покрытия могут быть доведены до зеркального блеска. Это обстоятельство позволяет широко применять никелевые покрытия для декоративных целей. При введении в электролит блескообразователей удается получать в слоях достаточной толщины блестящие никелевые покрытия без полировки. Структура нормальных никелевых осадков чрезвычайно тонка, и ее трудно выявить даже при сильном увеличении.
Чаще всего при никелировании преследуют две цели: защиту основного металла от коррозии и декоративную отделку поверхности. Такие покрытия широко применяют для наружных частей автомобилей, велосипедов, различных аппаратов, приборов, хирургических инструментов, предметов домашнего обихода и т. д.
С электрохимической точки зрения никель может быть охарактеризован как представитель металлов группы железа. В сильнокислой среде осаждение этих металлов вообще невозможно — на катоде выделяется почти один водород. Мало того, даже в растворах, близких к нейтральным, изменение рН влияет на выход по току и свойства металлических осадков.
Явление отслаивания осадка, больше всего присущее никелю, также в сильной степени связано с кислотностью среды. Отсюда и вытекает первейшая забота о соблюдении надлежащей кислотности и регулировании ее при никелировании, так же как выбор надлежащей температуры для правильного ведения процесса.
Первые электролиты для никелирования готовили на основе двойной соли NiSO4(NH4)2SO4·6H2O. Эти электролиты были впервые исследованы и разработаны профессором Гарвардского университета Исааком Адамсом в 1866 г. По сравнению с современными высокопроизводительными электролитами с высокой концентрацией никелевой соли электролиты с двойной солью допускают плотность тока, не превышающую 0,3—0,4 А/дм2. Растворимость двойной никелевой соли при комнатной температуре не превышает 60—90 г/л, в то время как семиводный сульфат никеля при комнатной температуре растворяется в количестве 270—300 г/л. Содержание металлического никеля в двойной соли 14,87%, а в простой (сернокислой) соли 20,9%.
Процесс никелирования весьма чувствителен к примесям в электролите и в анодах. Совершенно очевидно, что малорастворимую в воде соль легче освободить в процессе кристаллизации и промывки от вредных примесей, например сульфатов меди, железа, цинка и др. , чем более растворимую простую соль. В значительной степени по этой причине электролиты на основе двойной соли имели доминирующее применение во второй половине XIX и в начале XX столетия.
Борная кислота, которая в настоящее время рассматривается как весьма существенный компонент для буферирования электролита никелирования и электролитического рафинирования никеля, была впервые предложена в конце XIX — начале XX в.
Хлориды были предложены для активирования никелевых анодов в начале XX столетия. К настоящему времени в патентной и журнальной литературе предложено большое разнообразие электролитов и режимов для никелирования, по-видимому, больше, чем по какому-либо другому процессу электроосаждения металлов. Однако без преувеличения можно сказать, что большая часть современных электролитов для никелирования представляет собой разновидность предложенного в 1913 г. профессором Висконзинского университета Уоттсом на основании детального исследования влияния отдельных компонентов и режима электролита. Несколько позднее в результате усовершенствования им было установлено, что в концентрированных по никелю электролитах, при повышенной температуре и интенсивном перемешивании (1000 об/мин) можно получать удовлетворительные в толстых слоях никелевые покрытия при плотности тока, превышающей 100 А/дм2 (для изделий простой формы). Эти электролиты состоят из трех основных компонентов: сульфата никеля, хлорида никеля и борной кислоты. Принципиально возможна замена хлорида никеля хлоридом натрия, но, по некоторым данным, такая замена несколько снижает допустимую катодную плотность тока (возможно из-за уменьшения общей концентрации никеля в электролите). Электролит Уоттса имеет следующий состав, г/л:
240 — 340 NiSO4 · 7H2O, 30—60 NiCl2 · 6H2O, 30 — 40 H3ВO3.
Из других электролитов, которые в последнее время все больше привлекают к себе внимание исследователей и находят промышленное применение, следует назвать фторборатные, позволяющие применять повышенную плотность тока и сульфаматные, обеспечивающие возможность получения никелевых покрытий с меньшими внутренними напряжениями.
В начале тридцатых годов текущего столетия, и в особенности после второй мировой войны, внимание исследователей было приковано к разработке таких блескообразователей, которые позволяют получать блестящие никелевые покрытия в слоях достаточной толщины не только на отполированной до блеска поверхности основного металла, но и на матовой поверхности.
Разряд ионов никеля, как и других металлов подгруппы железа, сопровождается значительной химической поляризацией и выделение этих металлов на катоде начинается при значениях потенциалов, которые намного отрицательнее соответствующих стандартных потенциалов.
Выяснению причин этой повышенной поляризации посвящено много исследований и было предложено несколько далеко не совпадающих объяснений. По одним данным, катодная поляризация при электроосаждении металлов группы железа резко выражена лишь в момент начала выделения их, при дальнейшем повышении плотности тока потенциалы меняются незначительно. С повышением температуры катодная поляризация (в момент начала выделения) резко снижается. Так, в момент начала выделения никеля при температуре 15° С катодная поляризация равна 0,33 В, а при 95° С 0,05 В; для железа катодная поляризация снижается с 0,22 В при 15° С до нуля при 70° С, а для кобальта с 0,25 В при 15° С до 0,05 В при 95° С.
Высокую катодную поляризацию в момент начала выделения металлов группы железа объясняли выделением этих металлов в метастабильной форме и необходимостью затраты дополнительной энергии для перехода их в устойчивое состояние. Такое объяснение не является общепризнанным, имеются и другие взгляды на причины большой катодной поляризации, при которой происходит выделение металлов группы железа, и связанную с поляризацией мелкокристаллическую структуру.
Другие последователи приписывали особую роль водородной пленке, образующейся в результате совместного разряда ионов водорода, затрудняющей процесс агрегации мелких кристаллов и приводящей к образованию мелкодисперсных осадков металлов группы железа, а также защелачиванию прикатодного слоя и связанным с этим выпадением коллоидных гидроокисей и основных солей, которые могут соосаждаться с металлами и затруднять рост кристаллов.
Некоторые исходили из того, что большая поляризация металлов группы железа связана с большой энергией активации при разряде сильно гидратированных ионов, расчеты других показали, что энергия дегидратации металлов группы железа примерно такая же, как энергия дегидратации таких двухвалентных ионов металлов как медь, цинк, кадмий, разряд ионов которых протекает с незначительной катодной поляризацией, примерно в 10 раз меньшей, чем при электроосаждении железа, кобальта, никеля. Повышенную поляризацию металлов группы железа объяснили и сейчас объясняют адсорбцией чужеродных частиц; поляризация заметно снижалась при непрерывной зачистке катодной поверхности.
Этим не исчерпывается обзор различных взглядов на причины повышенной поляризации при электроосаждении металлов группы железа. Можно, однако, принять, что за исключением области малых концентраций и высоких плотностей тока, кинетика этих процессов может быть описана уравнением теории замедленного разряда.
Вследствие большой катодной поляризации при сравнительно небольшом перенапряжении водорода процессы электроосаждения металлов группы железа чрезвычайно чувствительны к концентрации ионов водорода в электролите и к температуре. Допустимая катодная плотность тока тем выше, чем выше температура и концентрация ионов водорода (чем ниже водородный показатель).
Для электроосаждения металлов группы железа нет нужды прибегать к растворам комплексных солей — эти металлы вполне удовлетворительно кристаллизуются на катоде из растворов простых солей, чаще всего сернокислых или хлористых, более доступных и более экономичных, чем комплексные соли.
- Влияние кислотности на работу никелевых электролитов
- Структура и механические свойства никелевых осадков
- Анодный процесс и никелевые аноды
- Защита от коррозии и механического износа
- Гальванопластика
- Вредные примеси
- Блестящее никелирование
- Двухслойные никелевые покрытия
- Толстые никелевые покрытия
- Покрытие «черным никелем»
- Химическое никелирование
- Электроосаждение кобальта и его сплавов
- Блестящие кобальтовые покрытия
- Электролитическое осаждение железа
- Сульфатные электролиты железнения
- Хлористые электролиты
- Фторборатные электролиты
Химическое никелирование | MIL-C-26074, ASTM B733 и AMS 2404
Химическое никелирование — это процесс совместного осаждения никель-фосфорного сплава без необходимости подачи внешнего электрического тока. Процесс химического никелирования происходит в результате химического восстановления ионов никеля в растворе химического никеля на металлическую подложку, а не осаждения ионов под действием приложенного тока. В результате химическое осаждение никеля лишено многих проблем, связанных с традиционным электролитическим никелем, включая наросты на кромках и неоднородное покрытие. Химическое никелевое покрытие чрезвычайно однородно, устойчиво к коррозии и эрозии и обеспечивает превосходную смазывающую способность.
Advanced Plating Technologies, компания из Милуоки, штат Висконсин, производит химическое никелирование в соответствии со стандартами MIL-C-26074, ASTM B733 и AMS 2404, а также большинством спецификаций компании. Компания APT предлагает химическое никелирование корпусов, стеллажей и вибраций практически на любую металлическую подложку, включая практически любые сплавы железа, меди и алюминия, а также многие экзотические сплавы. APT обеспечивает химическое никелирование в различных технически ориентированных отраслях, включая медицину, нефть и газ, передачу/распределение электроэнергии и оборонную промышленность.
Химическое никелирование – обзор
Химическое никелирование предлагается компанией Advanced Plating Technologies как для типа IV со средним содержанием фосфора (6-9% P), так и для типа V с высоким содержанием фосфора (10-14%). Содержание фосфора в химическом никеле существенно влияет на свойства покрытия, включая твердость, коррозионную стойкость и магнетизм. Ниже приведен краткий обзор химического никелирования, предоставляемого APT:
- Возможны допуски наплавки до +/- 0,0001 дюйма
- Толщина покрытия в диапазоне от 0,0001 дюйма на сторону до тяжелого покрытия методом химического никелирования более 0,005 дюйма на сторону
- Термическая обработка, предназначенная для повышения адгезии и твердости наплавленного никеля и может быть проведена без обесцвечивания наплавленного металла
- APT предлагает семейство HP+™ высокоэффективного химического никелирования, которое включает в себя молекулярный герметик для повышения коррозионной стойкости и смазывающей способности сухой пленки
- Запатентованное семейство черного химического никелирования – Tacti-black ® химический никель
- Селективное химическое никелирование с использованием как традиционных, так и специально разработанных методов селективного покрытия
- APT может сочетать химическое никелирование с порошковым покрытием для электронных шасси и корпусов
- Предлагается широкий ассортимент подложек, включая медное покрытие или электролитическое никелирование для создания многослойных дуплексных систем для улучшения коррозионных характеристик (см.
раздел «Что вызывает окисление или «ржавение» металлов» в разделе «Темы покрытия» нашей технической библиотеки).
Химическое никелирование – что такое химическое осаждение?
Химическое никелирование представляет собой уникальный процесс нанесения покрытия, который не требует внешнего источника электронов для осаждения, как при традиционном электролитическом покрытии. Скорее, химический никель представляет собой никель-фосфорный сплав, нанесенный химическим восстановлением (реакцией) из гипофосфита на каталитическую подложку без приложения внешнего тока. Поскольку во время осаждения не подается ток, покрытия методом химического никелирования свободны от обычной неоднородности традиционных электролитических покрытий и могут покрывать даже чрезвычайно сложные геометрические формы с превосходной однородностью (см.: В чем отличия химического никеля от традиционного электролитического никеля в нашей Технической документации). раздел “Темы библиотечного покрытия”).
Любая часть детали, одинаково смачиваемая раствором химического никеля, будет покрыта однородно, включая внутренние или внутренние элементы. Важно отметить, что для поддержания постоянной скорости осаждения требуется непрерывный поток раствора. Таким образом, глухие отверстия с небольшим внутренним диаметром труб или фитингов часто имеют меньшую толщину покрытия. Соосажденный фосфор в покрытии химическим никелированием увеличивает смазывающую способность по сравнению с традиционным никелевым покрытием, а процентное содержание фосфора в покрытии также влияет на такие свойства покрытия, как магнетизм, коррозионная стойкость и твердость. Кроме того, последующее спекание при температурах выше 500°F может перевести отложения никеля химическим способом из аморфного состояния после нанесения покрытия в кристаллическую структуру, что значительно повысит твердость.
Химическое никелирование – свойства осаждения
Нажмите, чтобы загрузить RU Технические данные
Обратитесь к списку ниже, чтобы узнать о различиях между осаждением химического никеля со средним и высоким содержанием фосфора, а также с запатентованными вариантами химического никелирования APT HP+™. Выберите PDF-файл технических данных по химическому никелированию справа, чтобы просмотреть полный список физических, механических и электрических свойств осажденного химического никеля.
- Химическое никелевое покрытие с высоким содержанием фосфора (> 10% P, тип V): Полублестящий внешний вид, немагнитный, пригоден для пайки при правильном выборе флюса, отличная коррозионная стойкость, низкое напряжение осаждения после покрытия, отлично подходит для тяжелых конструкций, Rc 48 -55 (с покрытием), 66-70 (с термообработкой), аморфная структура после покрытия.
- Среднее содержание фосфора Химическое никелирование (6-9% P, тип IV): Внешний вид от полублестящего до блестящего, магнитный, паяется при правильном выборе флюса, хорошая коррозионная стойкость, умеренное напряжение отложений после покрытия, не рекомендуется для тяжелых конструкций , Rc 58–62 (после покрытия), 66–70 (с термообработкой), полукристаллическая структура после покрытия.
- HP+™ Электрохимическое никелирование: Запатентованный процесс, предлагаемый APT, в котором молекулярный герметик из редкоземельных металлов наносится на химический никель с высоким или средним содержанием фосфора для повышения коррозионной стойкости и смазывающей способности сухой пленки. Сопротивление контакта немного увеличится, и этот процесс не рекомендуется для пайки или других применений соединения. Все остальные свойства депозита остаются такими же, как указано выше.
Химическое никелирование – возможности передовых технологий нанесения покрытий
Технические характеристики:
MIL-C-26074
ASTM B733
AMS 2404
ISO 4527
Большинство спецификаций компании
Отдел:
Средний фосфорный электрольесс. Электрольесс
Высокий фосфол. с высоким или средним содержанием фосфора
Подложки с покрытием:
Черные металлы: Все сплавы черных металлов, включая мягкую, нержавеющую, закаленную и инструментальную сталь
Медь: Все медные сплавы, включая чистую медь, медные сплавы, включая теллур и бериллий, латунь, никель-серебро
Алюминий: Все алюминиевые сплавы, включая деформируемые, литые и специальные сплавы (MIC-6) , чистый никель (никель 200), кобальт-хром (MP35N), ковар, монель, хасталлой, монель, свинец 42 дюйма x 20 дюймов (медь и сталь)
Подставки:
Медная
Электролитическое никель
Тепловые обработки:
Опрессование водорода
.
Листовое покрытие (химически фрезерованные/протравленные листы)
Сегментированные полосы (лады)
Химическое никелирование – Технические характеристики
Двумя наиболее распространенными услугами по химическому никелированию, сертифицированными Advanced Plating Technologies, являются MIL-C-26074, ASTM B733 и AMS 2404. APT также может сертифицировать услуги по химическому никелированию по ISO 4527 и AMS 2405, а также к большинству специфических для компании услуг по химическому никелированию. характеристики никеля. Краткое описание услуг по химическому никелированию в соответствии со спецификациями MIL, ASTM и AMS выглядит следующим образом: не считается термической обработкой).
Класс 2: Термическая обработка для получения требуемой твердости. Может использоваться на всех металлах, не подверженных нагреву до 500F и выше. Требуемая твердость может быть получена в соответствии с следующим графиком:
° F температурный часов
500 4 или более
550 2 или более
650 1–1,5
750* 0,5 до 1*
* График обжига составляет 750F в течение от 0,5 до 1 часа, так как это обеспечивает наиболее полный и стабильный во времени переход от аморфной к кристаллической структуре отложений для достижения высокой твердости.
Класс 3: алюминиевые сплавы без термообработки и бериллиевые сплавы, обработанные для улучшения адгезии никелевого покрытия. Покрытые нетермообрабатываемые алюминиевые детали должны нагреваться от 1 до 1,5 часов при температуре 375°F +/- 15°F для улучшения адгезии никелевого покрытия.
Класс 4: алюминиевые сплавы, термообрабатываемые, обработанные для улучшения адгезии никелевого покрытия. Термообрабатываемые алюминиевые сплавы с покрытием должны нагреваться от 240°F до 260°F в течение 1-1,5 часов для улучшения адгезии никелевого покрытия.
Марка A — минимальная толщина покрытия 0,0010 дюйма
Марка B — минимальная толщина покрытия 0,0005 дюйма
Марка C — минимальная толщина покрытия 0,0015 дюйма
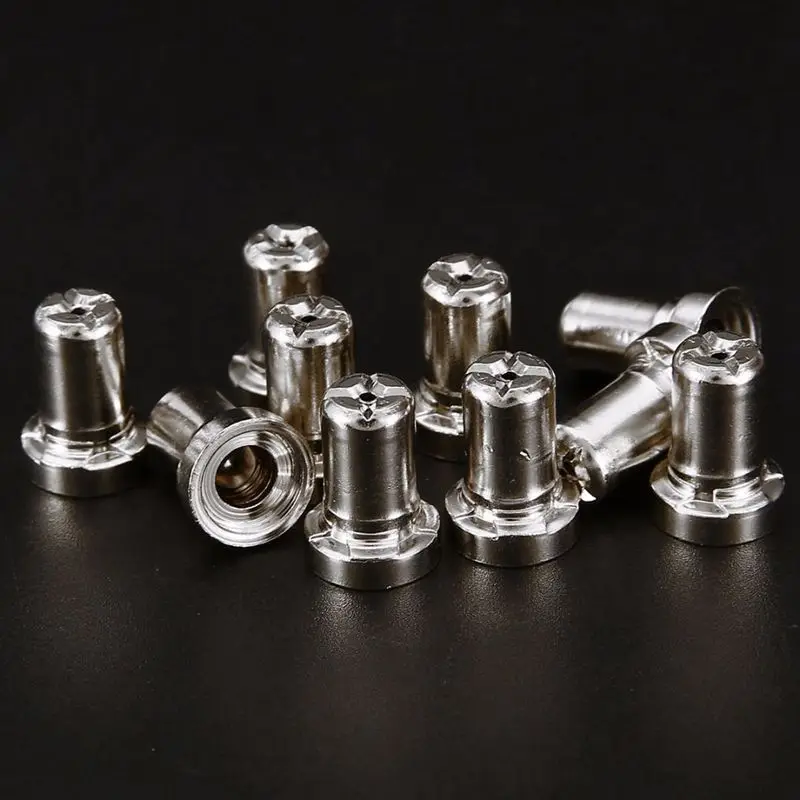
Тип I: Фосфор не требуется
Тип II: 1-3% фосфора (низкое содержание фосфора)
Тип III: 2-4% фосфора (низкое содержание фосфора)
Тип IV: 5-9% фосфора (среднее содержание фосфора)
Тип V: 10% или более фосфора (высокое содержание фосфора) фосфор)
SC0: Минимальная толщина 0,000004,
SC1: Легкая работа 0,0002, минимум
SC2: Легкая работа, 0,0005, минимум
SC3: Средняя нагрузка, 0,001, минимум
SC4: Тяжелая работа, 0,003, минимум 900 автокаталитического никелевого покрытия зависит
Шероховатые, неоднородные поверхности требуют более толстого покрытия
, чем гладкие поверхности, для достижения максимальной коррозионной стойкости и минимальной пористости
.
Класс 1: после напыления, без термической обработки.
Класс 2: Термическая обработка при температуре от 260 до 400°C (500-752°F) для получения минимальной твердости 850 HK100.
Класс 3: Термическая обработка при температуре от 180 до 200°C (356-392°F) в течение 2-4 часов для улучшения адгезии покрытия к стали и для уменьшения водородного охрупчивания.
Класс 4: Термическая обработка при температуре от 120 до 130 °C (248–266 °F) в течение не менее 1 часа для повышения адгезии термообрабатываемых (со старением) алюминиевых сплавов (таких как 7075) и науглероженной стали.
Класс 5: Термическая обработка при температуре от 140 до 150 °C (284–302 °F) в течение не менее 1 часа для улучшения адгезии покрытия к алюминию, алюминиевым сплавам без старения, меди, медным сплавам и бериллию.
Класс 6: Термическая обработка при температуре от 300 до 320 °C (572–608 °F) в течение не менее 1 часа для улучшения адгезии покрытия для титановых сплавов.
Примечание. AMS 2404 заменяет собой AMS-MIL-C-26074, в котором используются обозначения классов прочности для передачи требований к толщине. См. 8.13 для полной перекрестной ссылки из выноски AMS-MIL-C-26074 на технически идентичные положения в рамках этой спецификации (AMS 2404), чтобы соответствовать требованиям заказа на поставку.
Класс 1: За исключением снятия водородного охрупчивания, без термической обработки после нанесения покрытия.
Класс 2: Термическая обработка при температуре 450 °F (232 °C) или выше для упрочнения покрытия.
Класс 3: Термическая обработка при 375 °F (191 °C) для улучшения адгезии к нетермообрабатываемым алюминиевым и бериллиевым сплавам.
Класс 4: Термическая обработка при температуре 250 °F (121 °C) для улучшения адгезии к термообрабатываемым алюминиевым сплавам.
1.3.1 Если не указан конкретный класс, должен поставляться класс 1.
3.1.1 Обработка для снятия напряжений – Стальные детали с твердостью 40 HRC или выше, которые были отшлифованы после термической обработки, должны быть очищены от поверхностных загрязнений и должным образом сняты напряжения перед подготовкой к нанесению покрытия. Если не указано иное, температура снятия напряжения должна быть не ниже 275°F (135°C) в течение не менее пяти часов для деталей с твердостью 55 HRC или выше или не ниже 375°F (191°C) в течение не менее четырех часов для остальных частей.
3.3.2.1 Если указан класс 2, детали должны быть нагреты до выбранной температуры в диапазоне от 450 до 800°F и выдержаны в течение времени, достаточного для повышения твердости наплавленного металла. См. 3.4.4 и 8.6. Снятие водородного охрупчивания (3.3.1) можно не проводить, если отверждение класса 2 достигается в течение четырех часов после нанесения покрытия.
3.3.2.2 Если указан класс 3, детали должны быть нагреты до 375°F +/- 15°F в течение от 1 до 1,5 часов.
3.3.2.3 Если указан класс 4, детали должны быть нагреты до 250°F +/- 10°F в течение от 1 до 1,5 часов.
3.4.1 Толщина
Если не указано иное, минимальная толщина никелевого покрытия должна составлять 0,0010 дюйма для сплавов на основе алюминия, 0,0005 дюйма для сплавов меди, никеля, кобальта, титана и бериллия и 0,0015 дюйма для сплавов на основе железа.
3.4.4 Твердость
Класс покрытия 2 должна быть не ниже 800 HK100 или эквивалента, определенного в соответствии с ASTM E384.
3.4.7 Состав
Компетентная инженерная организация может указать диапазон содержания фосфора в месторождении. Если указано, состав месторождения должен быть определен методом, приемлемым для компетентной проектной организации.
8.6 Следующие тепловые обработки были использованы для достижения твердости класса 2:
° F Температура часов
450 4, минимум
500 4, минимум
550 2, минимум
650 1 до 1,5
750* от 0,5 до 1*
* Предпочтительный и конфразирующий переход с высокой высокой склонностью. от аморфной до кристаллической структуры отложений для достижения высокой твердости.
8.13 Спецификации AMS-MIL-C-26074 и его предшественников поощряют использование обозначений класса для указания толщины следующим образом:
Марка A Не менее 0,0010 дюйма
Марка B Не менее 0,0005 дюйма
Марка C Не менее 0,0015 дюйма
Химическое никелирование: все, что вам нужно знать
1 апреля 2020 г.
Химическое никелирование
(ENP) представляет собой автокаталитическое химическое восстановление покрытия из никелевого сплава (наиболее распространенным является никель-фосфорный), используемого для отделки поверхности. Этот процесс завершается без электрического тока, который обычно используется при гальванике. ENP осаждается путем восстановления ионов никеля химическим восстановителем, таким как гипофосфит натрия.
В процессе ENP наносится очень ровный слой никель-фосфорного сплава, содержание фосфора в котором обычно составляет от 2% до 14%. Это покрытие обеспечивает ряд преимуществ для деталей, включая коррозионную стойкость, повышенную твердость, износостойкость и защиту поверхности от истирания. При более высоком содержании фосфора покрытие становится аморфным, что означает отсутствие границ зерен, создающих очаги коррозии, что делает его идеальным для защиты от коррозии. Однако чем выше содержание фосфора в наплавке, тем ниже твердость наплавки. Ванны ENP с низким содержанием фосфора обеспечивают самую твердую отделку с самой низкой защитой от коррозии из-за кристаллической природы наплавки.
Для чего используется химическое никелирование?
Химическое никелированиеуниверсально и имеет множество преимуществ. Он используется для защиты деталей от естественного износа, истирания и коррозии, а также придает поверхности твердость для всех типов применений в различных условиях. Химическое никелирование чаще всего используется в следующих отраслях:
- Аэрокосмическая промышленность
- Строительство
- Электроника
- Машиностроение
- Нефть и газ
Примеры промышленных деталей, которые могут быть обработаны с помощью ENP, включают приводные валы, электрические и механические инструменты, инженерное оборудование, задвижки для нефтяных месторождений, клапанные насосы и многое другое.
Преимущества химического никелирования
Процесс химического никелирования предлагает различные преимущества по сравнению с традиционным гальванопокрытием, которые делают его надежной обработкой поверхности:
Защита от коррозии
Химическое никелирование менее пористое, чем гальваническое никелевое покрытие, что делает его чрезвычайно твердым и коррозионно-стойким к обычным агрессивным средам, таким как соленая вода, углекислый газ, кислород и сероводород.
Экономичность
Поскольку для производства самого покрытия не используется электричество, это эффективный и точный процесс, что делает его рентабельным для многих применений. Эта прочная высококачественная отделка может быть выполнена с меньшими капитальными затратами, чем стандартное гальваническое покрытие, и с меньшим количеством оборудования. Покрытие продлевает срок службы деталей, обеспечивая дополнительную экономию затрат на срок службы вашего оборудования.
Однородность
В процессе ENP на детали наносится очень ровное покрытие. Из-за автокаталитического характера этого процесса нет сильноточных или слаботочных областей, которые приводят к избыточному или недостаточному покрытию критических областей вашей детали. Толщину инженерных покрытий можно строго контролировать, не допуская образования наростов на кромках. С помощью этого процесса можно равномерно нанести покрытие даже сложной геометрии.
Твердость
Существует несколько различных типов ванн ENP с различным содержанием фосфора: низкое (2-4%), среднее (5-9%) и высокое (10-14%). Решение о том, какую ванну использовать, зависит от конечного применения. EN с низким содержанием фосфора (2-4%) обеспечивает наибольшую твердость при самой низкой защите от коррозии, а EN с высоким содержанием фосфора (10-14%) обеспечивает наибольшую защиту от коррозии при минимальном уровне твердости. Многие клиенты выбирают фосфор среднего уровня (5-9%), что обеспечивает лучшее из обоих миров.
Что такое процесс химического никелирования?
Для успешной обработки поверхности необходимо выполнить определенные шаги перед нанесением покрытия ENP. К ним относятся следующие шаги:
- Предварительная обработка – Поверхность деталей тщательно очищается с помощью различных химикатов для удаления остатков машинных/охлаждающих масел, смазок и даже отпечатков пальцев.
- Активация поверхности – После завершения тщательной очистки подложка активируется другим химическим веществом, например кислотой, для удаления оксидов и активации поверхности.
- Покрытие – После очистки и активации детали помещают в ванну ENP на время, достаточное для получения необходимой толщины покрытия.
- Инспекция – После нанесения покрытия детали, покрытые ENP, отбираются и испытываются в соответствии с требованиями спецификаций или внутренними стандартами, не содержащими требований.
Прочие факторы:
- Текстура поверхности : Неровные металлические поверхности, такие как заусенцы, не могут быть эффективно покрыты. Все заусенцы, неровности поверхности, сварочные брызги или острые края должны быть удалены или сглажены.
- Очистка : Все металлические поверхности должны быть полностью очищены от грязи, масла, жира или остатков процессов очистки.
- Активация поверхности : Покрытие ENP может быть выполнено на большинстве подложек. Его можно наносить непосредственно на сталь, но для других материалов могут потребоваться дополнительные действия для обеспечения адгезии.