Низколегированная сталь это: Низколегированная сталь: основные характеристики | Полезные статьи о металлопрокате
alexxlab | 05.07.2023 | 0 | Разное
Низколегированная сталь и ее особенности
Одним из самых востребованных видов металлопродукции является легированная сталь. Легированием металла называют процесс введения полезных элементов в состав при плавке. Легированный сплав обладает рядом полезных характеристик, которые проявляются в зависимости от количества легирующих элементов. Различают низко-, средне- и высоколегированные сплавы, для которых характерно содержанием примесей соответственно до 2,5%, от 2,5% до 10%, и от 10% до 50%.
Из чего состоит низколегированная сталь
Для легирования стали на производстве применяют недорогие элементы: марганец, кремний. Для придания продукту определенных свойств в состав сплавов также могут входить титан, хром, медь, ванадий и молибден.
Разберем подробнее свойства некоторых из них:
- кремний – единственный неметаллический элемент, который используют в процессе легирования. Он придаёт сплаву прочность пропорционально своему содержанию;
- хром и цинк известны тем, что хорошо защищают получившийся сплав от возникновения коррозии;
- ванадий придаёт стали однородность структуры;
- медь повышает пластичность сплава.
Впрочем, её избыточное содержание негативно сказывается на качестве – метал начинает налипать на смежные конструкции;
- молибден – его применение повышает термостойкость сплава.
Использование этих и других элементов для легирования делает такую сталь выгодной для применения в практически каждой сфере промышленности и хозяйства.
Используемая маркировка
Обозначение марки низколегированной стали состоит из комбинации цифр и букв, которые обозначают элемент и его количество в сплаве. Первые две цифры в маркировке указывают на количество углерода в сотых долях процента. Далее идёт обозначение введенных в состав легирующих элементов.
Важно отметить, что процентное содержание добавок указывается лишь в том случае, когда оно достигает значения больше единицы. Порядок указания элементов выстроен таким образом, чтобы показать в правильной последовательности их значимость, поэтому сперва указывают добавки, которые наиболее влияют на свойства сплава, а затем другие Также в наименовании указывается степень раскисления стали.
Разберем маркировку на примере: 18ХГТ. Здесь видим наличие 18 процентов углерода с хромом, марганцем и титаном; каждого не более 1%.
Обработка низколегированной стали
Обработка низколегированного металлопроката обычно не производится, но по специальному заказу могут проводить обработку в отожженном или нормализованном состоянии, либо сразу после прокатки.
Выполняют обработку двух типов: термическую и механическую.
В первом случае металлопрокат подвергают отпуску при температурах до 660 градусов по Цельсию – это позволяет снять сварочное напряжение швов. Стоит отметить, что термообработка должна проводиться с соблюдением правил по отношению к каждому виду нелегированного металла.
Механическая обработка производится чаще термической. Выполняют гибку, штамповку, резку и вальцовку. Параметры режущих инструментов подбираются согласно параметрам стали, которая подвергается обработке.
Такие процедуры позволяют повысить прочность конструкции, увеличить вязкость металла, а также снизить его чувствительность к надрезу и изгибу.
Где применяют такую сталь?
Низколегированные стали обладают характеристиками, которые позволяют их применять в практически каждой сфере промышленности и хозяйства.
Основные из них:
- строительство. Низколегированные марки применяются для сооружения конструкций, которые подвержены давлению и другим механическим силам, часто воздействующим на строение. Чаще всего это гражданские объекты, но встречаются и ангары с преобладанием высоких температур, а также строения, которые подвержены агрессивным условиям окружающей среды;
- машиностроение. Из низколегированных сталей здесь выполняются элементы несущих каркасов грузовых автомобилей, а также лонжероны легковых транспортных средств;
- вагоностроение. Конструкция вагонов содержит балки, которые как раз выполняются из низколегированных марок стали. Они способны выдерживать большие нагрузки, устойчивы к вибрации, а также имеют высокую прочность, что позволяет таким вагонам выдерживать крупные грузы;
- мостостроение.
Устойчивость к коррозии, способность выдерживать угловые нагрузки и давление делает эту марку стали необходимой для возведения мостовых сооружений;
- нефтегазовая промышленность. В процессе возведения магистральных путепроводов сталь должна обладать прочностью на изгиб, чтобы выдерживать неравномерную нагрузку, оказываемую трубными конструкциями.
Также эту марку стали активно используют в химической промышленности и приборостроении.
Низколегированная сталь: особенности, классификация, маркировка
- Главная >
- Блог >
- Низколегированная сталь: особенности, классификация, маркировка
06.02.2023
Время чтения: 10 минут
Редакция сайта VT-Metall
Сохранить статью:
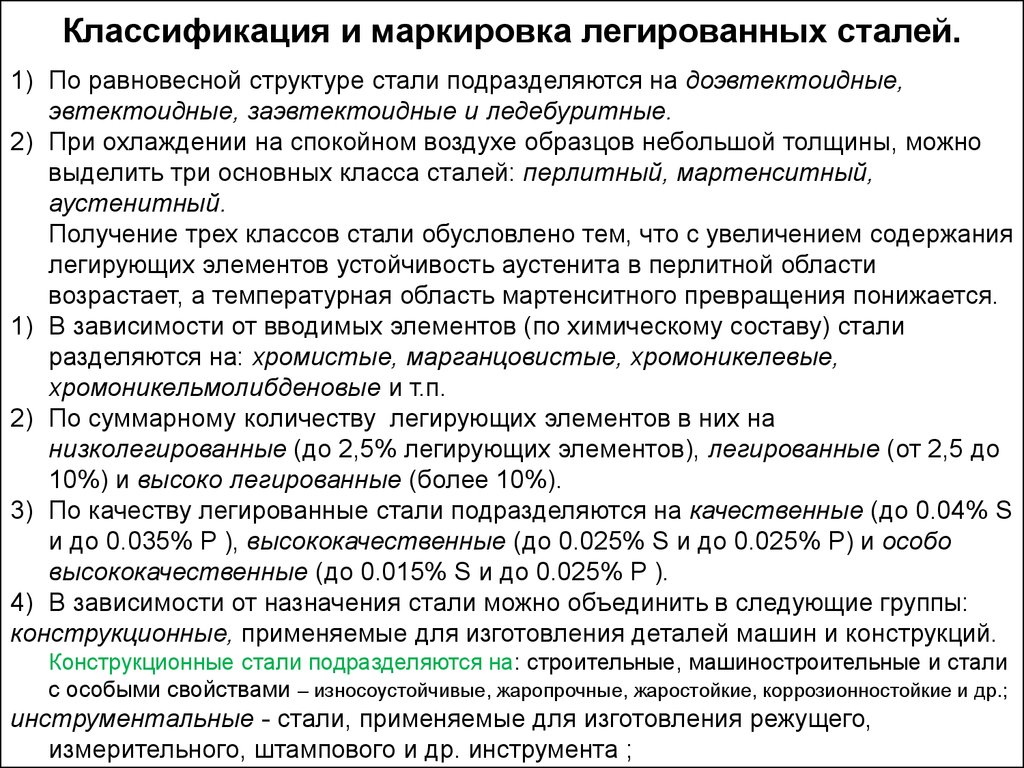
Какой она бывает? Существует несколько видов такой стали. Классифицируют их по различным параметрам, но основными считаются два: качество материала и его химический состав, полученный в результате введения тех или иных легирующих элементов.
Вопросы, рассмотренные в материале:
- Преимущества низколегированных типов стали
- Критерии качества НЛС
- Влияние легирующих элементов на свойства НЛС
- Классификация НЛС
- Маркировка низколегированной стали
- Варианты обработки низколегированной стали
- Сварка НЛС
- Применение низколегированной стали
Преимущества низколегированных типов стали
Содержание легирующих элементов в такой стали относительно невысоко, однако даже в малых концентрациях добавки позволяют в разы улучшить некоторые характеристики металла (предел текучести, износостойкость, сопротивляемость механическому старению) в сравнении с обычными углеродистыми сплавами.
Наличие легирующих элементов в составе сплава кратно повышает его коррозионную стойкость. К примеру, сетка мясорубки, через отверстия которой выходит нарубленный ножами фарш, обычно выполнена именно из низколегированной стали. При относительно невысокой стоимости такой металл не покрывается пятнами ржавчины уже через несколько недель эксплуатации, как это происходит с обычными углеродистыми сплавами, из которых изготовлены, к примеру, простые гвозди.
Востребованность низколегированной стали (НЛС) обусловлена ее свойствами – такие сплавы отличает хорошая обрабатываемость, устойчивость к воздействию низкой температуры и значительно меньшая склонность к холодному растрескиванию, чем у обычных углеродистых. Закаленному низколегированному стальному сплаву присущи высокая прочность, ударная вязкость и твердость. Степень раскисления металла может быть различной, но наиболее популярны спокойные разновидности НЛС.
Критерии качества НЛС
Физические характеристики низколегированных марок стали в значительной степени обусловлены процентной долей таких вредных примесей, как сера, от концентрации которой напрямую зависит ломкость металла, и фосфор.
В высококачественных стальных сплавах содержание примесей не должно по весу превышать 0,02–0,03 %, а сталь обыкновенного качества может содержать до 0,05 % серы и фосфора. Высокое качество, например, раритетных советских сверл, сохраняющееся, несмотря на многолетнее использование для сверления даже толстого металла, обусловлено именно крайне высокой степенью очистки сплава от серы.
Получить стальной сплав, полностью очищенный от примеси серы, к сожалению, можно исключительно в лаборатории.
Благодаря развитию металлургических технологий в наши дни сталь с высоким содержанием вредных примесей используется в промышленности все реже. Низколегированные типы стали, согласно нормам ГОСТ 19281–2014, выпускаются в виде толстых листов, универсального широкополосного проката или рулонов. Для нужд судостроительной промышленности НЛС выпускают в тонких или толстых листах, широких отрезах и фасонных заготовках.
Также из низколегированной стали изготавливается прокат периодического профиля классов А и Ап для армирования сборных железобетонных конструкций и монолитного железобетона согласно ГОСТ 5781-82 и 10884-94.
Влияние легирующих элементов на свойства НЛС
Общая процентная доля легирующих элементов в стальных сплавах должна составлять не более 2,5 % (по некоторым источникам – 5 %). Сказанное не относится к углероду, который к таким добавкам не относится.
Вводя в расплав те или иные металлы, можно добиться улучшения отдельных характеристик стали. Легирование производят с помощью добавления:
- ванадия – улучшает структуру металла, делая его более однородным и не позволяя расслаиваться в ходе термической обработки и пластического деформирования;
- молибдена – делает сплав жаростойким и жаропрочным;
- ниобия – сплав становится более прочным;
- вольфрама – соединяясь с азотом, повышает теплопроводность металла;
- титана – повышает износостойкость стали;
- никеля и кремния – делают металл более упругим и повышают его ударную вязкость;
- марганца – увеличивает прочность без ухудшения пластичности;
- алюминия – уменьшает образование окалины;
- хрома – делает сплав более твердым, прочным и устойчивым к коррозии;
- кобальта – не только повышает пластичность и прочность стального сплава, но и улучшает его магнитные свойства.
Рекомендуем статьи
- Чем отличаются металлы от неметаллов: физические и химические свойства
- Сталь Х12МФ: характеристики, состав, производство
- Как полировать сталь: промышленные и бытовые методы обработки
Виды стали, легированные кобальтом, неслучайно часто используют для изготовления сверл и фрез самого высокого качества – такие инструменты отличаются долговечностью и стойкостью к нагрузкам на излом. Выдающиеся характеристики – причина более высокой стоимости, чем у изделий из быстрорежущих типов стали.
Классификация НЛС
Существует несколько вариантов классификации НЛС, в основе которых лежат:
- химический состав (введенные в состав легирующие добавки) – сталь может быть никелевой, хромоникелевой, молибденовой, хромомолибденовой и т. д.;
- термическая обработка – НЛС может быть закаленной и отпущенной (мартенситной), нормализованной и отпущенной, отожженной и т.
д.;
- свариваемость.
Видов низколегированной стали огромное множество, что обусловлено разнообразием вариантов соотношения в сплаве легирующих добавок и режимов термообработки.
Сказанное выше объясняет наличие определенных «нахлестов», которые можно обнаружить в представленной выше классификации НЛС. Специалисты предпочитают разделять такие сплавы на четыре категории:
Низколегированные мартенситные стали
Высокую прочность такой низколегированной стали (ее еще называют улучшаемой) дополняют минимальный предел текучести 690 МПа, хорошая ударная вязкость, пластичность, коррозионная стойкость и свариваемость. Сплавы этой группы широко используют для выпуска плит, листового металла, прутка, профилированного проката и поковок. Из низколегированных мартенситных типов стали изготавливают ответственные элементы крупногабаритных металлоконструкций, землеройную, шахтную технику и т. д.
Среднеуглеродистые высокопрочные типы стали
Конструкционные виды стали этой группы обладают очень высокой прочностью в сочетании с минимальным пределом текучести, достигающим 1 380 МПа.
Шарикоподшипниковые типы стали
Для изготовления подшипников используют сплавы высокой твердости с углеродистостью порядка 1 %. Содержание 0,4–1,65 % хрома придает металлу хорошую прокаливаемость при охлаждении маслом. Низколегированная сталь, содержащая 0,1–0,2 % углерода, применяется реже, так как поверхностным слоям приходится придавать необходимую твердость с помощью цементации, что значительно усложняет технологический процесс.
Хромомолибденовые теплостойкие виды стали
Содержание хрома в таких сплавах колеблется от 0,5 до 9 %, молибдена – от 0,5 до 0,1 %, а углеродистость не превышает 0,2 %. Для улучшения характеристик металла используют нормализацию с отпуском, закалку с отпуском или отжиг. Из хромомолибденовых типов стали изготавливают детали нефтегазового, химического, атомного оборудования, трубы, теплообменники и сосуды высокого давления.
Маркировка низколегированной стали
Низколегированные стали (согласно ГОСТ) маркируются буквенными обозначениями и цифровыми индексами. Для обозначения легирующих элементов пользуются следующими буквами кириллицы:
Маркировка начинается цифровым обозначением содержания углерода в сотых долях процента, если числовое обозначение отсутствует – углеродистость сплава выше 1 %. Далее цифрами обозначают процентную долю легирующих элементов. Если содержание добавки менее 1 %, цифру не ставят. К примеру, в стальном сплаве марки 18ХГТ содержится 0,18 % углерода, а содержание хрома, марганца и титана для каждого элемента ≤ 1 %.
Первыми буквами в маркировке обозначают сортамент, к примеру, магнитные, хромистые или нержавеющие типы стали – это Ж, Х или Е. Буквы С – хромоникелевые сплавы с выраженной коррозионной стойкостью, Р – быстрорежущие виды стали, Ш – шарикоподшипниковые, А – автоматные, Э – электротехнические, а Л – литейные. К примеру, АС35Г2 – маркировка автоматной стали, легированной свинцом, содержащей 0,35 % углерода и около 2 % марганца.
Буквами ТО или Н обозначают типы стали, механические характеристики которых были улучшены, соответственно, термической обработкой или нагартовкой. ГОСТ и специализированная справочная литература содержат точное описание химического состава тех или иных сплавов.
Варианты обработки низколегированной стали
Для того чтобы повысить прочность, пластичность, коррозионную стойкость и устойчивость к воздействию отрицательной температуры, низколегированные типы стали могут подвергаться термообработке – закалке с отпуском. Для снятия остаточных напряжений и снижения твердости сварных швов в конструкциях используется отпуск при температуре около +645 °C.
Режим обработки подбирается в зависимости от назначения, конструкции изделий и химического состава сплава. Такая обработка требуется, к примеру, при изготовлении труб, подвергающихся в ходе эксплуатации действию давления, высокой температуры и агрессивных веществ.
Часто для обработки НЛС пользуются термомеханическими методами – холодным пластическим деформированием с последующим отжигом. Ковка позволяет добиться необходимой мелкозернистости, а отжиг приводит к рекристаллизации и формирует мелкодисперсную структуру. С помощью таких комбинированных технологий можно избавиться даже от мельчайших неоднородностей в кристаллической решетке металла и снизить его хрупкость.
Сварка НЛС
Детали из низколегированной стали хорошо поддаются сварке в силу своих физико-химических характеристик, обусловленных содержанием углерода около 0,2 % и легирующих элементов до 2,5 %.
Содержание кремния (около 1,05 %) делает металл прочным и упругим, однако большое количество образующегося при сварке шлака может затруднять процесс. Наличие в составе сплава марганца (около 1,7 %) повышает закаливаемость, но также осложняет сваривание заготовок. Присутствие других легирующих элементов, таких как молибден, хром и ванадий, не лучшим образом сказывается на прочности сварных соединений.
Хорошая закаливаемость низколегированных типов стали – причина, по которой их чаще всего приходится сваривать в нагретом состоянии или посредством нежесткого режима термической обработки (в противном случае возможна только контактная точечная сварка). При использовании инвертора необходимо выставлять ток примерно на 12,5 % ниже, чем для обычных низкоуглеродистых сплавов. При этом необходимо прилагать к стержню электрода большее усилие (приблизительно на 30), чем для работы с обычным металлом.
Для сварки низколегированных типов стали можно использовать электродуговую, точечную и газовую сварку. Для сваривания деталей с помощью инвертора рекомендуется использовать электроды Э-50А, а для работы газовой сваркой применять присадочную проволоку.
Оптимальный метод для сваривания деталей из низколегированной стали – ручная электродуговая сварка, которую можно использовать с металлом любой толщины и при любой температуре окружающего воздуха. В процессе соединения элементов конструкций из НЛС посредством сварки возможно формирование горизонтальных, вертикальных и потолочных швов.
Применение низколегированной стали
Благодаря высоким эксплуатационным характеристикам НЛС широко применяют для:
- Изготовления сварных металлоконструкций в производстве автомобилей, станков, ж/д вагонов и в тяжелом сельскохозяйственном машиностроении.
- Производства оборудования для нефтедобывающей промышленности. Вследствие применения НЛС снижается масса элементов конструкции, сокращаются затраты металла и труда, а значит, и стоимость готовой продукции.
- Сооружения конструкций, подвергающихся при эксплуатации переменным динамическим нагрузкам и перепадам температуры.
- Производства паровых турбин – используются термостойкие сплавы с легирующими добавками (молибден, молибден и хром, хром, молибден и ванадий), которые также придают металлу устойчивость к серьезным пневмонагрузкам.
- Строительства трубопроводов – трубы из низколегированной стали, содержащей хром, кремний и марганец, обладают высокой прочностью, упругостью и эффективно сопротивляются упругой деформации.
При производстве металлопроката, предназначенного для эксплуатации в широком диапазоне температуры (от -70 до +450 °C), широко применяются НЛС марки 09Г2С и аналогичные сплавы. Такой металл используется для изготовления паровых котлов, емкостей и аппаратов высокого давления, элементов ответственных сварных металлоконструкций для химической, нефтедобывающей и нефтеперерабатывающей промышленности, судостроения, машиностроения и т. д.
Также из таких типов стали производят бесшовные горячекатаные и электросварные трубы большого диаметра и контейнеры для перевозки тяжелых грузов.
Благодаря описанным особенностям низколегированные типы стали пользуются постоянно растущим спросом – с 1955-го по 1970-й их выплавка выросла примерно на 1 600 %! Из всего объема производимой в мире стали порядка 13 % приходится именно на НЛС.
Читайте также
20.04.2023
Электродуговая сварка: преимущества и недостатки, виды и особенности
Подробнее
17.04.2023
Шлифовка металла: методы, виды
Подробнее
13.04.2023
Структура стали после закалки: виды и технологии термообработки
Подробнее
10.04.2023
Сварочная ванна: советы по ее идеальной отработке
Подробнее
07.04.2023
Какие соединения относятся к резьбовым: разновидности и функции
Подробнее
04.04.2023
Высокоуглеродистая сталь и ее особенности
Подробнее
31.03.2023
Температура закалки стали: какой должна быть
Подробнее
29.03.2023
Плазмотрон: устройство, виды, задачи
Подробнее
Низкоуглеродистая сталь | Низколегированные стали
Углеродистые и низколегированные стали являются рабочими лошадками мира механики. Ни один другой класс материалов не обладает таким широким спектром механических свойств, как экономически. Углеродистые стали представляют собой сплавы железа, углерода, марганца и кремния.
Низколегированные стали аналогичны углеродистым сталям, но содержат дополнительные легирующие элементы, такие как хром, молибден и т. д., для улучшения реакции на термообработку. При термообработке в этой группе материалов возможен предел прочности от 60 до 300 тысяч фунтов на квадратный дюйм. Используя специализированные процессы термообработки, можно создавать детали с особыми свойствами в разных областях одной и той же детали. Примером этого может быть первая термическая обработка отливки до очень жесткого состояния для повышения ударопрочности, а затем применение второй термической обработки для упрочнения поверхности, чтобы сделать поверхность износостойкой.
IC 1010 (отожженный)
IC 1020 (отожженный)
IC 1020 (нормализованный)
IC 1025 (отожженный)
IC 1030 (отожженный)
IC 1030 (закаленный)
IC 1035 (отожженный)
IC 1035 (закаленный)
IC 1045 (отожженный)
IC 1045 (закаленный)
IC 1050 (отожженный)
IC 1050 (закаленный)
IC 1060 (отожженный)
IC 1060 (закаленный)
IC 4130 (отожженный)
IC 4130 (закаленный)
IC 4140 (отожженный)
IC 4140 (закаленный)
IC 4150 (отожженный)
IC 4150 (закаленный)
IC 4330 (отожженный)
IC 4330 (закаленный)
IC 4340 (отожженный)
IC 4340 (закаленный)
IC 4620 (отожженный)
IC 4620 (закаленный)
IC 52100 (отожженный)
IC 52100 (закаленный)
IC 6150 (отожженный)
IC 6150 (закаленный)
IC 8620 (отожженный)
IC 8620 (закаленный)
IC 8625 (закаленный)
IC 8630 (отожженный)
IC 8630 (закаленный)
IC 8640 (отожженный)
IC 8640 (закаленный)
WCB (нормализованный)
Низколегированная сталь – IspatGuru
Низколегированная сталь
- satyendra
- 8 сентября 2021 г.
- 0 комментариев
- легированная сталь, легирующие элементы, закалка стали, подшипниковая сталь, углеродистая сталь, электротехническая сталь, прокаливаемость, жаропрочная сталь, сталь HSLA, низколегированная сталь, пружинная сталь, атмосферостойкая сталь,
Низколегированные стали
Легирующие элементы добавляются в стали по разным причинам, включая повышение коррозионной стойкости и/или улучшение механических свойств при низких или повышенных температурах. Легирующие элементы также используются для улучшения прокаливаемости закаленной и отпущенной стали.
Термин «легированная сталь» используется для тех сталей, которые имеют в своем составе помимо углерода другие легирующие элементы. Легированные стали производятся путем соединения сталей с одним или несколькими другими легирующими элементами. Обычно это металлы. Их намеренно добавляют, чтобы придать стали определенные свойства, которых нет у простых углеродистых сталей.
Существует большое количество легирующих элементов, которые можно добавлять в сталь. Общее количество легирующих элементов в легированных сталях (кроме микролегированных сталей) может варьироваться от 1 % до 50 %. Общие легирующие элементы включают марганец, никель, хром, молибден, ванадий, кремний и бор. Менее распространенные легирующие элементы включают алюминий, кобальт, медь, церий, ниобий, титан, вольфрам, олово, цинк, свинец, сурьму и цирконий.
Любая сталь, которая содержит более 1,65 % марганца, 0,60 % кремния и 0,60 % меди или определенное минимальное количество любого другого элемента, называется «легированной» сталью. Легированные стали обычно делятся на два класса, а именно (i) низколегированные стали и (ii) высоколегированные стали. Их делят по составу, основанному на содержании легирующих элементов.
Введение легирующих элементов в стали улучшает ряд свойств легированных сталей по сравнению с углеродистыми сталями. Этими свойствами являются прочность, твердость, ударная вязкость, коррозионная стойкость, износостойкость, прокаливаемость, обрабатываемость, термостойкость, огнестойкость, твердость в горячем состоянии и т. д. Легированные стали могут нуждаться в термической обработке для достижения некоторых из этих улучшенных свойств.
Легированные стали обычно бывают трех типов. Это микролегированные стали, низколегированные стали и высоколегированные стали. Микролегированные стали — это тип легированных сталей, которые содержат небольшое количество легирующих элементов (обычно в диапазоне от 0,05 % до 0,15 %). Эти стали также иногда называют высокопрочными низколегированными сталями. Разница между низколегированными сталями и высоколегированными сталями несколько условна.
Некоторые люди определяют низколегированные стали как те стали, которые содержат легирующие элементы до 4 %, в то время как согласно другому второму определению низколегированные стали содержат легирующие элементы до 8 %. Стали с содержанием легирующих элементов выше этого количества относятся к категории высоколегированных сталей.
Сталь считается низколегированной, если какой-либо определенный диапазон или определенное минимальное количество любого из следующих элементов указан или требуется в пределах признанной области конструкционных легированных сталей: алюминий, бор, хром (до 3,99 % ), кобальт, ниобий, молибден, никель, титан, вольфрам, ванадий, цирконий или любой другой легирующий элемент, добавляемый для получения желаемого эффекта легирования. Низколегированные стали обычно имеют ферритно-перлитную, перлитную или бейнитную структуру.
Термин «низколегированная сталь» используется для отличия стали от высоколегированной стали. Низколегированные стали представляют собой категорию черных металлов, механические свойства которых превосходят простые углеродистые стали в результате добавления легирующих элементов. К высоколегированным сталям относятся стали с высокой степенью трещиностойкости, мартенситностареющие стали, аустенитные марганцевые стали, инструментальные стали и нержавеющие стали.
Низколегированная сталь является важным материалом в экономическом и оборонном контексте. Механические свойства низколегированных сталей зависят от внутренней организации микроструктуры, а внутренняя организация зависит от влияния таких важных факторов, как легирующие элементы и параметры процесса. Низколегированные стали содержат никель, молибден и хром, которые улучшают свариваемость, ударную вязкость и предел текучести материала.
Требования к химическому составу низколегированной стали соответствуют различным стандартам. Низколегированные стали могут быть пригодны для некоторых конструкционных применений. Остаточные легирующие элементы могут влиять на механические свойства горячекатаной стали. Легирующие элементы также влияют на прокаливаемость и механические свойства закаленных и отпущенных сталей.
Несмотря на добавление легирующих элементов, низколегированные стали не обязательно плохо поддаются сварке. Тем не менее, точное знание того, какой тип низколегированной стали имеет решающее значение для достижения хорошей целостности сварного шва, равно как и правильный выбор присадочного металла. При сварке низколегированных сталей предварительный подогрев и последующая термообработка обычно не требуются.
Для многих основной функцией легирующих элементов в низколегированных сталях является повышение прокаливаемости для оптимизации механических свойств и ударной вязкости после термической обработки. Однако в некоторых случаях добавки легирующих элементов используются для уменьшения ухудшения состояния окружающей среды при определенных условиях эксплуатации.
Применение низколегированных сталей сильно различается во многих отраслях промышленности. Применение этих сталей варьируется от военной техники, землеройной и строительной техники, трубопроводов повышенной проходимости, сосудов под давлением и трубопроводов, нефтяных буровых платформ и так далее. Несколько распространенных низколегированных сталей используются для изготовления корпусов кораблей, подводных лодок, мостов и внедорожников.
Благодаря добавлению определенных легирующих элементов низколегированные стали обладают точным химическим составом и обеспечивают лучшие механические свойства, чем многие обычные низкоуглеродистые стали или простые углеродистые стали. Легирующий элемент в низколегированной стали обычно составляет от 1 % до 4 % и добавляется в зависимости от его способности придавать очень специфические свойства. Например, добавление молибдена повышает прочность материала, никеля повышает ударную вязкость, а хром повышает жаропрочность, твердость и коррозионную стойкость. Марганец и кремний, другие распространенные легирующие элементы, обладают превосходными свойствами раскисления.
Как и для простых углеродистых сталей, для низколегированных сталей существует установленная система классификации обозначений. Классификация основана на основном легирующем элементе (элементах) в стали. Эти основные элементы включают углерод, марганец, кремний, никель, хром, молибден и ванадий. Каждый элемент по отдельности или в сочетании с другими элементами придает стали определенные свойства и характеристики.
Низколегированные стали можно классифицировать в соответствии с (i) химическим составом, таким как никелевые стали, никель-хромовые стали, молибденовые стали, хромомолибденовые стали и т. д., и (ii) термической обработкой, такой как закалка и отпуск, нормализация и закалка, отжиг и т. д., и (iii) в зависимости от свариваемости.
Поскольку в низколегированных сталях возможно большое разнообразие химических составов, а также из-за того, что некоторые стали можно использовать в более чем одном состоянии термообработки, существует определенное совпадение в классификации низколегированных сталей. Следовательно, классифицировать низколегированные стали довольно сложно. Обычно используются четыре основные группы низколегированных сталей. Эти группы включают (i) низкоуглеродистые закаленные и отпущенные стали, (ii) среднеуглеродистые сверхвысокопрочные стали, (iii) жаропрочные хромомолибденовые стали и (iv) подшипниковые стали.
Низкоуглеродистые закаленные и отпущенные стали сочетают в себе высокий предел текучести (от 350 МПа до 1035 МПа) и высокую прочность на растяжение с хорошей ударной вязкостью, пластичностью, коррозионной стойкостью или свариваемостью. Различные типы низкоуглеродистых закаленных и отпущенных сталей имеют различные комбинации этих характеристик в зависимости от их предполагаемого использования. Некоторые из этих сталей используются в военных целях для брони, в основном в виде пластин. Кроме того, некоторые из этих сталей также производятся в виде поковок или отливок.
Низколегированные стали обычно не используются без соответствующей термической обработки. Безусловно, самый большой тоннаж низколегированных сталей относится к типу, который имеет номинальное содержание углерода в диапазоне от 0,25 % до 0,55 %. Если для науглероженных деталей используется низколегированная сталь, номинальное содержание углерода обычно не превышает 0,2 %. Различные комбинации и количества марганца, кремния, никеля, хрома, молибдена, ванадия и бора обычно присутствуют в этих сталях для улучшения свойств закаленного и отпущенного сплава.
Микроструктура (отпущенный мартенсит или бейнит), полученная путем закалки и отпуска низколегированных сталей, характеризуется хорошей ударной вязкостью, то есть способностью деформироваться без разрушения при заданном уровне прочности. Основное явление получения благоприятной микроструктуры путем термической обработки также возможно в простых углеродистых сталях, хотя в основном в тонких срезах. Таким образом, наиболее важным эффектом легирующих элементов в низколегированной стали является индуцирование образования мартенсита или бейнита и сопутствующих улучшенных свойств в больших сечениях. Уровень твердости или прочности этих структур зависит от содержания углерода в продуктах превращения, а не от присутствующих легирующих элементов.
Общее действие легирующих элементов, растворенных в аустените, заключается в снижении скорости превращения аустенита при докритических температурах. Поскольку желательные продукты превращения в этих сталях (мартенсит и низший бейнит) образуются при низких температурах, существенное значение имеет пониженная скорость превращения. Таким образом, заготовки можно охлаждать медленнее или закаливать большие заготовки в данной среде без превращения аустенита в нежелательные высокотемпературные продукты (перлит или верхний бейнит). Эта функция, снижающая скорость превращения и, таким образом, облегчающая окончательное превращение в мартенсит или низший бейнит, известна как прокаливаемость, наиболее важный эффект легирующих элементов в закаливаемых сталях. Повышая прокаливаемость, легирующие элементы значительно расширяют потенциал улучшенных свойств для больших сечений, необходимых для многих применений.
Многие кривые прокаливаемости служат для иллюстрации того принципа, что независимо от состава отпущенные стали одинаковой твердости имеют примерно одинаковую прочность на растяжение. Максимальная (после закалки) твердость термообработанной стали зависит в первую очередь от содержания углерода. Легирующие элементы мало влияют на максимальную твердость, которая может быть достигнута в стали, но они существенно влияют на глубину, до которой эта максимальная твердость может быть достигнута в детали определенного размера и формы.
Таким образом, для конкретного применения одним из первых решений, которое необходимо принять, является уровень содержания углерода, необходимый для получения желаемой твердости. Следующим шагом является определение того, какое содержание сплава обеспечивает надлежащую реакцию упрочнения при соответствующем размере сечения. Это не означает, что отпущенные мартенситные стали одинаковы во всех отношениях, независимо от состава, поскольку содержание сплава определяет различия в сохранении прочности при повышенных температурах, в сопротивлении истиранию, в сопротивлении коррозии и даже в определенной степени, в жесткости. Однако сходство достаточно заметно, чтобы можно было достаточно точно прогнозировать механические свойства по твердости, а не по составу, тем самым оправдывая акцент на прокаливаемости как наиболее важной функции легирующих элементов.
Среднеуглеродистые сверхвысокопрочные стали представляют собой конструкционные стали, предел текучести которых может превышать 1380 МПа. Некоторые из этих сталей имеют обозначения, данные в различных стандартах, в то время как некоторые другие стали имеют собственный состав. Формы продукции для этих сталей включают заготовки, прутки, стержни, поковки, листы, трубы и сварочную проволоку.
Хромомолибденовые низколегированные стали представляют собой жаропрочные стали, содержащие от 0,5 % до 9 % хрома и от 0,5 % до 1 % молибдена. Содержание углерода обычно ниже 0,2 %. Хром обеспечивает улучшенную стойкость к окислению и коррозии, а молибден повышает прочность при повышенных температурах. Эти стали обычно производятся в нормализованном и отпущенном, закаленном и отпущенном или отожженном состояниях. Хромомолибденовые стали широко используются в нефтяной и газовой промышленности, на ископаемых топливах и на атомных электростанциях.
Подшипниковые стали используются для изготовления шариковых и роликовых подшипников. Самая популярная подшипниковая сталь содержит около 1 % углерода и 1,5 % хрома. Испытания шарикоподшипников, проведенные Штрибеком в 1901 году на такой стали, показали ее пригодность для применения и, по-видимому, были приняты около 120 лет назад для подшипников компанией Fichtel & Sachs из Швайнфурта в 1905 году и по сей день остаются ключевой сталью в производстве. подшипников с прогрессивным улучшением усталостных характеристик, достигаемым в основном за счет улучшения чистоты по отношению к неметаллическим включениям. Он представляет собой большую часть подшипниковой стали, производимой ежегодно. В Таблице 1 приведены номинальные составы некоторых подшипниковых сталей.
Таб.1 Номинальные составы некоторых подшипниковых сталей | ||||||||||||||||||||
Сл. № | Марка | Номинальный состав, % | ||||||||||||||||||
Углерод | 9024 802 Марганец 9024 0179 Кремний | Хром | Никель | Молибден | ||||||||||||||||
Высокоуглеродистые подшипниковые стали | ||||||||||||||||||||
1 | AISI 52100 | 1,04 | 0,35 | 0,25 | 1,45 908853 908242 9 | |||||||||||||||
2 | ASTM A 485-1 | 0,97 | 1,10 | 0,60 | 1,05 | |||||||||||||||
3 | ASTM A 485-3 | 1,02 | 0,78 | 0,22 | 1,30 | |||||||||||||||
4 | ТБС-9 | 0,95 | 0,65 | 0,22 | 0,50 | 0,25 максимум | 0,12 | |||||||||||||
5 | SU 1,02 | Менее 0,50 | 0,25 | 1,05 | Менее 0,25 | Менее 0,08 | ||||||||||||||
6 | 105Cr6 | 0,97 | 0,32 | 0,25 | 1,52 | 3 | 0285 | Науглероживание подшипниковой стали | ||||||||||||
1 | 4118 | 0,20 | 0,80 | 0,22 | 0,50 | 924 0,11 0,11 8 | 2 | 5120 | 0,20 | 0,80 | 0,22 | 0,80 | 8 9 | 8620 | 0,20 | 0,80 | 0,22 | 0,50 | 0,55 | 0,20999 4 | 4620 | 0,20 | 0,55 | 0,22 | 1,82 | 0,25 |
5 | 4320 | 0,25 9025 0,20 9024 2 | 0,22 | 0,50 | 1,82 | 0,25 | ||||||||||||||
6 | 3310 | 0,1 0,52 | 0,22 | 1,57 | 3,50 | |||||||||||||||
7 | SCM420 | 9 2075 0,20 9024 2 | 0,25 | 1,05 | 0,22 | |||||||||||||||
8 | 20MnCr5 | 0,17-0,22 | 1,1-1,4 | 0,4 максимум | 1,0219.
Как видно из таблицы, есть две категории сталей, которые Применение в большинстве подшипников. Первая категория состоит из тех сталей, которые имеют высокое содержание углерода (около 1 % углерода) и закалены по всему сечению до мартенситного или бейнитного состояния. Вторая категория сталей состоит из науглероженных сталей с низким содержанием углерода (от 0,1 % C до 0,2 % углерода) и цементируемых. Эти стали имеют мягкую сердцевину, но прочные поверхностные слои, нанесенные с помощью таких процессов, как поверхностная или индукционная закалка. Подшипниковые стали также можно разделить в широком смысле на классы, предназначенные для нормальной эксплуатации, эксплуатации при высоких температурах или эксплуатации в коррозионных условиях. На рис. 1 показана микроструктура высокоуглеродистых и науглероженных подшипниковых сталей.
Рис. 1
Рис. 1 Микроструктура высокоуглеродистых и науглероженных подшипниковых сталей
Низколегированные стали обычно требуют особого ухода при их производстве. Они более чувствительны к термическим и механическим воздействиям, управление которыми осложняется неодинаковым действием различных химических составов. Для обеспечения наиболее удовлетворительных результатов потребители обычно консультируются с производителями стали относительно обработки, механической обработки, термообработки или других операций, которые будут использоваться при изготовлении стали, механических операций, которые необходимо использовать при изготовлении стали, механических свойств, которые необходимо получить, и условия службы, для которых предназначены готовые изделия.
Существует несколько низколегированных сталей, которые не предназначены только для прочности при комнатной температуре. Эти стали обладают дополнительными важными свойствами, такими как коррозионная стойкость, жаростойкость и формуемость. Некоторые из популярных низколегированных сталей описаны ниже.
Конструкционные легированные стали – Эти легированные стали имеют низкое содержание легирующих элементов. Суммарное содержание легирующих элементов в этих сталях колеблется от 0,25 % до примерно 6 %. Этот класс легированных сталей используется при строительстве мостов, зданий, кораблей, автомобильных рам, железных дорог и т. д. Конструкционные легированные стали используются для таких деталей машин, как валы, шестерни, рычаги, болты, пружины, поршневые пальцы и шатуны. и т. д.
Никелевая сталь . Средняя сталь в условиях низких температур имеет более высокую прочность, но низкое удлинение и ударную вязкость, что повышает вероятность хрупкого разрушения. Если сталь требуется в условиях низких температур, то она должна иметь превосходную ударную вязкость при низких температурах, что очень важно. Никелевая сталь подходит для работы при низких температурах. Сталь для низкотемпературной эксплуатации изготавливается путем добавления от 2,5 % до 3,5 % никеля в углеродистую сталь для повышения ее ударной вязкости при низких температурах. Никель может укрепить ферритовую матрицу, одновременно снижая Ar3 (температура третьего превращения), что способствует образованию мелкого зерна. В дополнение к нормализующей обработке в процессе производства низколегированной низкотемпературной служебной стали закалка и отпуск также являются частью обработки для улучшения механических свойств.
Атмосферостойкая сталь – Все низколегированные стали имеют тенденцию ржаветь в присутствии влаги и воздуха. Эта ржавчина представляет собой пористый оксидный слой, который может удерживать влагу и кислород и способствовать дальнейшей коррозии. Скорость образования ржавчины зависит от доступа кислорода, влаги и атмосферных загрязнений к поверхности металла. Атмосферостойкие стали представляют собой низколегированные стали с повышенной коррозионной стойкостью. Эти стали работают, контролируя скорость, с которой кислород в атмосфере может реагировать с поверхностью металла.
Атмосферостойкие стали с содержанием углерода менее 0,2 %, к которым в качестве легирующих элементов добавляют в основном медь, хром, никель, фосфор, кремний и марганец в количестве не более 3 % до 5 %. Повышенная коррозионная стойкость атмосферостойкой стали по сравнению с мягкой сталью или простой углеродистой сталью обусловлена образованием в слабоагрессивных средах компактного и хорошо прилипающего слоя продуктов коррозии, известного как патина. Это определение атмосферостойкой стали, однако, не осталось неизменным, а эволюционировало по мере разработки новых составов атмосферостойкой стали для достижения улучшенных механических свойств и/или противостояния все более агрессивным атмосферным условиям с точки зрения коррозии, особенно в морской среде.
В 1968 году стандарт ASTM A-242 представил две спецификации для атмосферостойких сталей: одна с высоким содержанием фосфора (менее 0,15 %), а другая с более низким содержанием фосфора (максимум 0,04 %). Последняя в конечном итоге была заменена атмосферостойкой сталью стандарта ASTM A-588 (таблица 2). Эта сталь обладает меньшей стойкостью к атмосферной коррозии из-за меньшего содержания фосфора, но по этой же причине лучше сваривается.
Табл. 1 Химический состав обычно используемых атмосферостойких сталей | ||||||||||||||||||||||||||||||||||||||||||||||||||||||||
Элементы / Тип стали | Блок | ASTM A-242 (COR-TEN A) | ASTM гр. A (COR-TEN B)||||||||||||||||||||||||||||||||||||||||||||||||||||||
Типичная концентрация | 0 Типовая концентрация 90 Углерод (C) | % | 0,15 максимум | 0,019 максимум | Кремний (Si) | % | 0,3–0,65 | Марганец (Mn) | % | % | максимум | 0,8-1,25 | Фосфор (P) | % | 0,015 максимум | 0,15 максимум | 0,04 максимум | 0,04 максимум | Сера (S) 90s | % 05 | Менее 0,05 | Медь (Cu) | % | 0,2 минимум | 0,25-0,4 | 0,25-0,4 | 0,3-0,4 | % | 0,5-0,8 | 0,4 -0,65 | 0,6-1,0 | Никель (Ni) | % | 0,5-0,65 | 0,4 максимум | 3 0,4 43 | Ванадий (V) | % | 0,02- 0,10 | |
Высокопрочная сталь с высоким пределом текучести – В эту серию низколегированных сталей добавлены марганец, никель, хром, молибден и т. д. Эти элементы могут увеличить прочность ферритовой матрицы, улучшить склонность к закалке и позволить лучше контролировать размер зерна. Этот тип стали в состоянии сварки может соответствовать требованиям высокой прочности, коррозионной стойкости или улучшенной ударной вязкости и другим механическим свойствам. Этот тип стали имеет хорошую свариваемость с пределом текучести в диапазоне от 480 МПа до 830 МПа и пределом прочности при растяжении в диапазоне от 620 МПа до 1030 МПа.
Низколегированные стали с жаропрочными свойствами. Примером низколегированной стали, которая используется из-за ее высокотемпературных свойств, является сталь ротора турбины ASTM A 470. Эти стали используются в паровых турбинах для производства электроэнергии и обычно содержат комбинации никеля, хрома, молибдена и/или ванадия. Пример микроструктуры роторной стали ASTM A 470 показан на рис. 2.
Рис. 2 Микроструктуры стали с высокотемпературными свойствами и двухфазной стали
Низколегированные стали с формуемостью – Некоторые стали предназначены для оптимальной формуемости при листовом прокате. Обычная сталь, указанная как качество волочения, является специальной спокойной сталью. Эта холоднокатаная листовая сталь с низким содержанием углерода имеет определенное содержание алюминия. Алюминий соединяется с азотом в стали с образованием осадков нитрида алюминия в процессе отжига. Эти выделения нитрида алюминия играют важную роль в развитии специфической кристаллографической текстуры в листе, которая способствует глубокой вытяжке. Другим типом стали, используемой для применений, требующих оптимальной формуемости, является сталь без пор. В этой листовой стали с очень низким содержанием углерода элементы внедрения, углерод и азот, сочетаются с карбидо- и нитридообразующими элементами, такими как титан и ниобий. Сталь «освобождается» от этих промежуточных элементов, которые ухудшают формуемость.
Двухфазные низколегированные стали – Двухфазные низколегированные стали относятся к классу высокопрочных сталей, которые используются в тех случаях, когда предел текучести стали увеличивается во время самого процесса штамповки. Двухфазные стали состоят из двух фаз, а именно из мягкой ферритовой матрицы и дисперсной второй фазы мартенсита (от 5 % до 30 %). В дополнение к мартенситу могут существовать небольшие количества бейнита и остаточного аустенита (рис. 2). Мягкая ферритная фаза обычно непрерывна, что придает этим сталям превосходную пластичность. Когда эти стали деформируются, деформация концентрируется в менее прочной ферритной фазе, окружающей островки мартенсита, создавая уникальную высокую скорость деформационного упрочнения, характерную для этих сталей.
Двухфазная сталь ведет себя как композиционный материал, в котором ферритовая матрица обеспечивает высокую способность к холодной штамповке, а мартенсит является упрочняющим элементом. Правильная пропорция между двумя фазами обеспечивает непрерывный предел текучести, низкий предел текучести, высокое значение удлинения, гладкую кривую текучести с высоким коэффициентом деформационного упрочнения, а также лучшую пластичность и формуемость. Микроструктура стали обеспечивает хорошее сочетание высокой прочности на растяжение, низкого отношения предела текучести к прочности на растяжение и очень высокой скорости начального деформационного упрочнения с хорошими значениями относительного удлинения. Двухфазная сталь хорошо поддается формованию, что обеспечивает большую гибкость при проектировании деталей. Прочность формованной детали намного выше, чем у высокопрочной низколегированной стали, особенно при очень низкой деформации. Высокая скорость начального деформационного упрочнения и высокая прочность на растяжение придают двухфазной стали очень высокую способность поглощать энергию, что делает эти стали пригодными для использования в конструкционных и армирующих конструкциях.
Низколегированные стали, упрочняемые обжигом – Сталь, упрочняемая обжигом, представляет собой сталь, которая демонстрирует способность к значительному увеличению прочности за счет сочетания деформационного упрочнения во время формирования детали и старения под действием деформации во время последующего термического цикла, такого как операция обжига краски. . Закаливаемые стали предназначены для повышения прочности во время цикла окраски и сушки при производстве автомобилей. Эти стали содержат элементы, образующие соединения, выпадающие в осадок при температурах спекания краски. Эти выделения упрочняют сталь.
Сталь, упрочняемая обжигом, была разработана для повышения прочности во время цикла обжига краски при производстве автомобилей. Эти стали содержат элементы, образующие соединения, выпадающие в осадок при температурах спекания краски. Эти выделения упрочняют сталь. Эти стали содержат достаточное количество углерода и/или азота в растворе, чтобы вызвать деформационное старение. Как правило, стали, закаливаемые в печи, представляют собой раскисленные алюминием стали с достаточным количеством алюминия для соединения с азотом в виде нитрида алюминия.
В сталях, упрочняемых термическим обжигом, используется низкое содержание растворенного углерода для обеспечения управляемого углеродного деформационного старения для увеличения предела текучести формованных автомобильных панелей, что повышает устойчивость к вмятинам или позволяет уменьшить толщину. Деформация возникает из-за штамповки, а старение ускоряется за счет обжига краски. Закаливаемые стали содержат достаточное количество перенасыщенного растворенного углерода, так что реакция старения обычно увеличивает предел текучести штампованной панели на 27–55 МПа.
Среднеуглеродистые сверхвысокопрочные низколегированные стали – Семейство среднеуглеродистых низколегированных сверхвысокопрочных сталей включает марку 4130, марку повышенной прочности 4140 и марку более глубокой закалки, повышенную прочность 4340. Несколько модификаций базовой стали 4340. были разработаны марки стали. В одной модификации содержание кремния увеличивается для предотвращения охрупчивания, когда сталь отпускается при низких температурах для достижения требуемой очень высокой прочности. В некоторые марки стали добавляется ванадий в качестве измельчителя зерна для повышения ударной вязкости, а содержание углерода немного снижается для улучшения свариваемости. Одна марка стали содержит ванадий, немного больше углерода, хрома и молибдена, чем 4340, и немного меньше никеля. Другими менее широко используемыми сталями, которые могут быть включены в это семейство, являются стали марок 6150 и 8640.
Среднеуглеродистые низколегированные сверхвысокопрочные стали легко поддаются горячей штамповке, обычно при температурах в диапазоне от 1065°С до 1230°С. в извести, золе или другом изоляционном материале. Перед механической обработкой обычной практикой является нормализация при температуре от 870°C до 925°C и отпуск при температуре от 650°C до 675°C, или отжиг путем охлаждения в печи от 815°C до 845°C до приблизительно 540°C, если сталь глубокой воздушной закалки. Эти обработки придают достаточно твердую структуру, состоящую из среднего и мелкого перлита. В этом состоянии сталь имеет рейтинг обрабатываемости около 50 % по сравнению со сталью для свободного резания.
Легированная пружинная сталь – Эти пружинные стали используются в условиях высоких напряжений и ударных или ударных нагрузок. Эти стали могут выдерживать более широкий температурный диапазон, чем пружинные стали с высоким содержанием углерода, и используются либо в отожженном, либо в предварительно отпущенном состоянии. Кремний является ключевым элементом в большинстве легированных пружинных сталей. Типичный образец легированной пружинной стали содержит 1,5–1,8 % кремния, 0,7–1 % марганца и 0,52–0,6 % углерода.