Оборудование плазменное напыление металла – Плазменное напыление металла: оборудование, фото, видео
alexxlab | 24.06.2020 | 0 | Разное
Плазменное напыление металла: оборудование, фото, видео
Виды и применение процессов плазменного напыления металлов
Плазменное напыление (или, другими словами – диффузионная металлизация) эффективный способ изменения физико-механических свойств, а также структуры основной поверхности. Поэтому он часто используется с декоративными целями, и для увеличения стойкости конечного продукта.
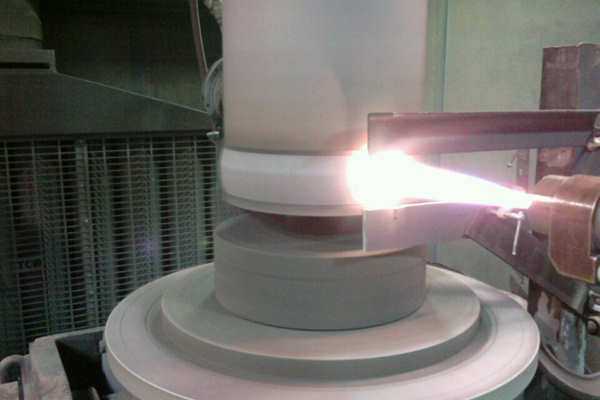
Принцип плазменного напыления
Как и традиционные методы поверхностных покрытий, при диффузионной металлизации происходит осаждение на поверхности металла слоя другого металла или сплава, который обладает необходимыми для последующего применения детали свойствами – нужным цветом, антикоррозионной стойкостью, твёрдостью. Отличия заключаются в следующем:
- Высокотемпературная (5000 — 6000 °С) плазма значительно ускоряет процесс нанесения покрытий, который может составлять доли секунд.
- При диффузионной металлизации в струе плазмы в поверхностные слои металла могут диффундировать также химические элементы из газа, где проводится обработка. Таким образом, регулируя химический состав газа, можно добиваться комбинированного поверхностного насыщения металла атомами нужных элементов.
- Равномерность температуры и давления внутри плазменной струи обеспечивает высокое качество конечных покрытий, чего весьма трудно достичь при традиционных способах металлизации.
- Плазменное напыление отличается чрезвычайно малой длительностью процесса. В результате не только повышается производительность, но также исключается перегрев, окисление, прочие нежелательные поверхностные явления.
Рабочие установки для реализации процесса
Поскольку чаще всего для инициации высокотемпературной плазмы используется электрический разряд – дуговой, искровой или импульсный – то применяемое для такого способа напыления оборудование включает:
- Источник создания разряда: высокочастотный генератор, либо сварочный преобразователь;
- Рабочую герметизированную камеру, где размещается подвергаемая металлизации заготовка;
- Резервуар для газа, в атмосфере которого будет производиться формирование высокотемпературной плазмы;
- Насосной или вакуумной установки, обеспечивающей необходимое давление для прокачки рабочей среды или для создания требуемого разрежения;
- Системы управления за ходом протекания процесса.
Работа плазмотрона, выполняющего плазменное напыление, происходит так. В герметизированной камере закрепляется напыляемая деталь, после чего между поверхностями рабочего электрода (в состав которого входят напыляемые элементы) и заготовкой возбуждается электрический разряд. Одновременно через рабочую зону с требуемым давлением прокачивается жидкая или газообразная среда. Её назначение – сжать зону разряда, повысив тем самым объёмную плотность его тепловой мощности. Высококонцентрированная плазма обеспечивает размерное испарение металла электрода и одновременно инициирует пиролиз окружающей заготовку среды. В результате на поверхности образуется слой нужного химического состава. Изменяя характеристики разряда – ток, напряжение, давление – можно управлять толщиной, а также структурой напыляемого покрытия.
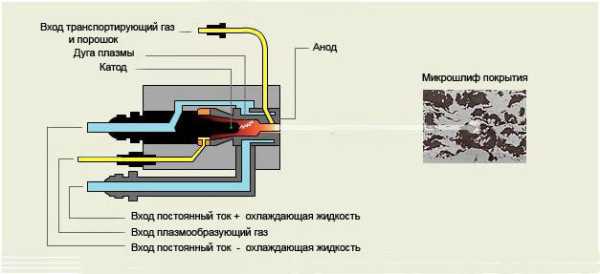
Схема плазменного напыления
Аналогично происходит и процесс диффузионной металлизации в вакууме, за исключением того, что сжатие плазмы происходит вследствие разницы давлений внутри и вне её столба.
Технологическая оснастка, расходные материалы
Выбор материала электродов зависит от назначения напыления и вида обрабатываемого металла. Например, для упрочнения штампов наиболее эффективны электроды из железо-никелевых сплавов, которые дополнительно легируются такими элементами, как хром, бор, кремний. Хром повышает износостойкость покрытия, бор – твёрдость, а кремний – плотность финишного покрытия.
При металлизации с декоративными целями, главным критерием выбора металла рабочего электрода является конфигурация напыляемой поверхности, а также её внешний вид. Напыление медью, например, производят электродами из электротехнической меди М1.
Важной структурной составляющей процесса является состав среды. Например, при необходимости получить в напыляемом слое высокостойкие нитриды и карбиды, в газе должны присутствовать органические среды, содержащие углерод или азот.
Последующая обработка готового покрытия
В силу особенностей процесса плотность напылённого слоя и прочность его сцепления с основным металлом не всегда бывают достаточными для обеспечения долговечности покрытия. Поэтому часто после обработки деталь подвергается последующему поверхностному оплавлению с использованием кислородно-ацетиленового пламени, либо в термических печах. Как следствие, плотность покрытия возрастает в несколько раз. После этого продукцию шлифуют и полируют, применяя твердосплавный инструмент.
С учётом последующей доводки изделия, толщину слоя металла после обработки принимают не менее 0,8 — 0,9 мм.
Для придания детали окончательных прочностных свойств её закаливают и отпускают, применяя технологические режимы, рекомендуемые для основного металла.
Плазменное напыление повышает теплостойкость, износостойкость и твёрдость изделий, увеличивает их способность противодействовать коррозионным процессам, а напыление с декоративными целями значительно улучшает внешний вид деталей.
Ограничениями технологии диффузионного плазменного напыления считаются чрезмерная сложность конфигурации заготовки, а также относительная сложность используемых установок.
При невысоких требованиях к равномерности образующегося слоя можно использовать и более простые установки, конструктивно напоминающие сварочные полуавтоматы. В этом случае плазменное напыление производится в воздушном пузыре, который образуется при обдуве зоны обработки компрессором. Электроды, в составе которых имеется напыляемый металл, последовательно перемещаются по контуру изделия. Для улучшения сцепления напыляемого металла с основой внутрь зоны напыления вводится также присадочный материал.
Процесс напыления металлического порошка на токарном станке
Если вы нашли ошибку, пожалуйста, выделите фрагмент текста и нажмите Ctrl+Enter.
stankiexpert.ru
Плазменное напыление. Принцип, оборудование плазменного напыления
Содержание страницы
Итак, в чем же состоит принцип плазменного напыления? Во всех устройствах плазменного напыления порошок приобретает температуру и скорость в струе горячего газа, создаваемого плазматроном. В свою очередь, плазматрон или плазменный генератор – это устройство, изобретенное в 1920-х годах, в котором электрическая дуга, горящая между катодом и анодом в ограниченном объеме (сопле), раздувается инертным газом и создает факел высокотемпературного восстановительного пламени.
Чем же так привлекателен этот принцип для решения задач термического напыления? Именно тем, что пламя плазматрона очень горячее и всегда строго восстановительное; присутствие кислорода в плазматроне категорически не допускается из-за быстрого, в противном случае, разрушения материалов электродов (парциальное давление кислорода в плазмообразующих газах определяется их чистотой и должно быть не выше 0,004%). Факел пламени плазматрона, при грамотном его применении, может не только восстановить активную металлическую поверхность из оксидных пленок на напыляемых частицах, но даже и очистить от оксидов саму поверхность субстрата. Подобную возможность предоставляет исключительно метод плазменного напыления.
В отношении плазменного напыления существует, в среде теоретиков и практиков термического напыления, ряд предрассудков, которые, в большинстве случаев, связаны не с процессом как таковым, а с недопониманием сути процесса напыления, недостатками конструкций конкретных устройств и с неправильным их применением. Обсудим эти предрассудки:
1. “Пламя плазмы слишком горячее и пригодно поэтому, только для напыления тугоплавких металлических и оксидных керамических материалов. Слишком высокая температура приводит к испарению части порошка и разрушению карбидов хрома и вольфрама”.
Действительно, температура плазмы может достигать 20.000°C и более, что много выше, чем, например, температура ацетиленокислородного пламени (около 3000°C). Однако, температура пламени имеет очень мало общего с температурой напыляемых частиц. Не углубляясь в физику взаимодействия горячего газа с твердыми частицами, скажем только, что это взаимодействие очень сложное и зависит от большого количества параметров, в числе которых не только температура газа, его скорость, длина факела и размер частиц, но и химические составы газа и частиц. К тому же, решающее значение для передачи тепла от факела к частицам имеет не абсолютная температура пламени, а его светимость. Так, например, более горячее, но почти невидимое водородно-кислородное пламя нагревает частицы гораздо хуже, чем более холодное, но яркое (из-за светящихся нано частиц углерода) ацетилено-кислородное пламя. Светимость факела плазмы зависит от состава плазмообразующего газа, от размера и состава частиц, проходящих сквозь него. Интересно, что во многих случаях эта светимость меньше, чем у ацетиленокислородного пламени и ее приходится увеличивать разными способами, только чтобы придать частицам хотя бы минимальную необходимую температуру. Так как длина пламени газопламенных устройств также часто превышает длину факела плазмы, получается «парадокс»: грубозернистые металлические порошки нагреваются в устройствах порошкового газопламенного напыления сильнее, чем в более мощных и «горячих» устройствах плазменного напыления.
2. “Скорость частиц при плазменном напылении недостаточна для получения плотных покрытий”.
Скорость потока газа и частиц в нем определяется не принципом образования пламени, а исключительно конструкцией устройства. В настоящее время существуют промышленные устройства плазменного напыления с соплом Лаваля, обеспечивающие частицам сверхзвуковую скорость.
3. “Для напыления металлов годятся только дорогостоящие установки вакуумного плазменного напыления, а установки атмосферного плазменного напыления непригодны из-за окисления металлических частиц”.
Подобное утверждение приходится, как ни странно, слышать довольно часто, даже от людей, практически занимающихся плазменным напылением, особенно применительно к покрытиям из MCrAlY для лопаток газовых турбин. На самом же деле, в этом утверждении происходит типичная подмена понятий: чисто металлические покрытия из легкоплавких никелевых сплавов, полученные вакуумным плазменным напылением (VPS), действительно лучше атмосферно напыленных (APS), но не из-за окисления частиц в плазме, а совсем по другой причине, о которой будет рассказано в разделе, посвященном вакуумному плазменному напылению. Окисление же металлических частиц в обоих этих способах происходит одинаково.
Устройства атмосферного плазменного напыления ничем не отличаются от устройств вакуумного плазменного напыления. Разница не в самих устройствах, а в способе организации процесса напыления: атмосферное напыление проводится на воздухе, а при вакуумном напылении и плазматрон, и напыляемая деталь находятся в вакуумной камере под разряжением. Понятно, что атмосферное напыление гораздо доступнее и дешевле вакуумного, к тому же для больших деталей вакуумное напыление становится просто невозможным из-за нереального размера вакуумной камеры. Сами же плазматроны могут использоваться как для атмосферного, так и для вакуумного напыления.
Чтобы понятнее объяснить особенности плазменного напыления, перейдем к рассмотрению разных конструкций, существующих на сегодняшний день.
Установки плазменного напыления
Устройства плазменного напыления отличаются большим разнообразием конструкций. Будем рассматривать их от самых «традиционных» до самых «продвинутых».
Наиболее распространенные устройства, – это устройства с одним катодом и одним анодом, и с вводом порошка снаружи короткого сопла, перпендикулярно к оси пламени.
Принцип действия таких устройств показан на схеме (рисунок 28):
Рис. 28. Принцип плазменного напыления.
Как видно из схемы, короткое сопло плазматрона одновременно является анодом. Порошок вводится снаружи сопла перпендикулярно оси пламени, в непосредственной близости от дуги.
Самое популярное устройство этого типа, – плазматрон 3MB фирмы Sulzer Metco, который, с небольшими модификациями, существует уже больше 40 лет. На рисунке 29 представлены актуальные модели этой серии с максимальной мощностью 40 кВт.
Рис. 29. Плазматрон 3MB.
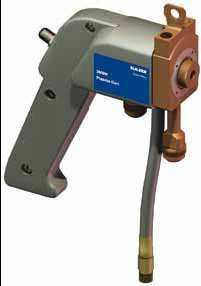
Несколько более новое и мощное (55 кВт) однокатодное устройство, – плазматрон F4, показанный на рисунке 30.
Рис. 30. Плазматрон F4.
Устройство 9MB, – один из самых мощных однокатодных плазматронов традиционного типа (80 кВт при токе 1000 А и напряжении 80 В) производится также фирмой Sulzer Metco (рисунок 31):
Рис. 31. Плазматрон 9MB
Традиционные однокатодные плазматроны других фирм мало отличаются от плазматронов Sulzer Metco: все они работают при относительно малом расходе газов, низком (< 100 В) напряжении и большом (до 1000 А) токе дуги. Ни один из традиционных плазматронов не позволяет достичь частицам скорости звука.
Достоинством плазматронов с небольшим расходом газов является возможность придания частицам очень высокой температуры (> 4000°C) из-за относительно долгого времени их пребывания в горячей зоне пламени рядом с дугой. Столь высокие температуры частиц позволяют расплавить практически любые керамические и металлические материалы.
Развитие техники плазменного напыления в последние двадцать лет идет по пути увеличения скорости частиц. Для придания частицам большей скорости необходимо увеличить давление плазмообразующих газов перед соплом, что автоматически приводит к повышению расхода газов и росту напряжения дуги.
Современное, мощное (до 85 кВт, ток до 379 А, напряжение до 223 В) устройство с одним катодом и анодом – это плазматрон 100HE американской фирмы Progressive Technologies Inc., который, благодаря большому давлению и расходу плазмообразующих газов, позволяет достичь скоростей частиц – близких к скорости звука (рисунок 32):
Рис. 32. Плазматрон 100HE.
Из-за высокой скорости плазмообразующего газа уменьшается время пребывания частиц в горячей зоне пламени и, соответственно, их температура. Для противодействия этому необходимо увеличивать мощность дуги и использовать в плазмообразующем газе большое количество водорода, который, благодаря процессу диссоциации-ассоциации молекул, удлиняет горячую зону пламени. Таким образом, плазматрон 100HE реализует температуру частиц, с размером 20-30 мкм, выше 2300°C при скорости около 250 м/сек, что делает возможным напылять покрытия из Cr3C2 – NiCr, Cr
Вторым направлением развития, в комбинации с увеличением расхода газов, является деление одной дуги на три части, которое позволяет улучшить стабильность и равномерность факела пламени, уменьшить износ электродов и увеличить суммарную мощность пламени. Типичным примером такого устройства является новейший плазматрон TriplexProTM-210 фирмы Sulzer Metco с одним анодом и тремя катодами, максимальной мощностью 100 кВт (рисунок 33):
Рис. 33. Плазматрон TriplexProTM.
1 – задняя часть корпуса; 2 – анодный стек; 3 – передняя часть корпуса; 4 – изолятор; 5 – накидная гайка; 6 – три катода в керамическом блоке; 7 – элемент анодного стека; 8 – канал плазмы; 9 – насадка с тремя порошковыми дюзами.
Технология Triplex от Sulzer Metco вошла в практику термического напыления в 90-х годах. Эти устройство обладают, по сравнению с плазматронами с одной дугой, существенно большим ресурсом и стабильностью результатов напыления. Для многих коммерческих порошков плазматроны Triplex позволяют также улучшить производительность и КПД напыления при сохранении качества покрытия.
Фирмой GTV GmbH выпущено, в обход патента Sulzer Metco на трехкатодные плазматроны, устройство GTV Delta с одним катодом и тремя анодами, которое, в принципе, является ухудшенной компиляцией TriplexPro (рисунок 34):
Рис. 34. Плазматрон GTV Delta.
Последнее, третье направление развития – это отказ от радиального ввода порошка в пользу гораздо более рационального – осевого. Ключевой элемент конструкции плазматрона с осевым вводом порошка – Convergens был изобретен в 1994 году американцем Люсьеном Богданом Дэльча (Delcea, Lucian Bogdan).
В настоящее время существует только одно подобное устройство, – плазматрон Axial III, максимальной мощностью 150 кВт, производства канадской фирмы Mettech, которое объединяет собой все три направления развития (большой расход газов, три дуги и осевой ввод порошка). Установки плазменного напыления с плазматроном Axial III производятся и распространяются также немецкой фирмой Thermico GmbH.
На рисунках 35, 36 и 37 изображено само устройство Axial III и его конструктивная схема:
Рис. 35. Плазматрон Axial III.
Рис. 36. Вид на устройство Axial III со стороны сопла.
Рис. 37. Принципиальная схема Axial III.
Все современные установки плазменного напыления являются автоматическими, то есть, управление источниками тока, системой водяного охлаждения и расходом газов регулируется системой ЧПУ с визуализацией и сохранением рецептов на компьютере. Так, например, плазматрон Axial III поставляется фирмой Thermico GmbH в комплекте с компьютеризированной системой управления, самостоятельно проводящей зажигание дуг и выход на рабочий режим, выбор рецептов напыления, и осуществляющей контроль всех основных параметров: расхода трех плазмообразующих газов (аргона, азота и водорода), токов дуг, параметров системы водяного охлаждения. Эта же автоматическая система управляет и порошковым питателем.
О порошковом питателе Thermico нужно сказать особо. Это, наиболее «продвинутое» на сегодняшний день в мире устройство позволяет не только постоянно регулировать массовый расход порошка и расход несущего газа (азота или аргона), но и допускает использование тонкозернистых порошков с плохой сыпучестью, непригодных, например, для питателей фирмы Sulzer Metco.
Автор лично, в течение долгого времени работал с плазматроном Axial III и может из своего опыта сказать, что несмотря на некоторые конструктивные недоработки, этот плазматрон представляет собой самое прогрессивное устройство термического напыления, объединяющее достоинства высокоскоростного напыления с высокой температурой строго восстановительного пламени. Главное же достоинство Axial III состоит в осевом вводе порошка.
Достоинства осевого ввода порошка
Осевой ввод порошка – это качественный скачок в технике плазменного напыления. Дело тут не только в том, что при осевом вводе значительно уменьшаются потери порошка, но и в том, что открываются возможности напыления совсем других порошковых материалов, непригодных для радиального ввода. Так как этот аспект является принципиально важным для понимания следующих разделов, остановимся на нем подробнее.
Итак, что же происходит при радиальном вводе порошка в струю пламени на выходе из сопла? Перечислим недостатки такого ввода:
- Для радиального ввода пригодны только очень узкофракционные порошки, для которых необходимо точно подбирать давление несущего газа. Что это значит?: При недостаточном давлении несущего газа частицы порошка будут «отскакивать» от струи пламени, при слишком высоком давлении несущего газа они будут «простреливать» это пламя насквозь; если же порошок состоит из частиц разного размера, то подобрать «правильное» давление несущего газа в принципе невозможно: самые мелкие частицы будут всегда «отскакивать», а самые крупные – всегда «простреливать», то есть, ни тех ни других частиц в напыляемом покрытии не будет, а будут только какие-то «средние» частицы. Особенно трудно вводятся мелкозернистые порошки из-за их повышенного рассеяния несущим газом (типичное облако пыли вокруг факела).
- При радиальном вводе порошка нельзя использовать в порошковой смеси не только частицы разных размеров, но и разных плотностей (разных масс) по той же причине: более тяжелые частицы пролетают сквозь пламя легче более легких. Таким образом, попытка использования сложных порошковых смесей приведет к искажению состава покрытия по сравнению с составом порошковой смеси.
- Увеличение скорости плазмообразующих газов усложняет радиальный ввод порошка, так как дополнительно сужаются интервалы необходимых давлений несущего газа и распределения частиц по размерам. На практике это означает следующее: чем выше скорость пламени, тем меньше КПД напыления при радиальном вводе порошка. Ввести же весь порошок в пламя без потерь невозможно ни при каких обстоятельствах.
- Расположение порошковых дюз рядом с горячей зоной пламени вызывает их разогрев, компенсирующийся только охлаждением газом, несущим порошок. Если же скорости охлаждающего газа недостаточно для охлаждения, то частицы порошка могут налипать на края отверстия дюз, образуя натеки. Налипшие куски периодически отрываются от дюзы, попадают в пламя и вызывают характерный дефект – «плевание», приводящий к образованию грубых пористых включений в покрытии. Так как скорость истечения несущего газа строго связана с параметрами пламени (см. пункт 1), то возникает проблема: для некоторых порошков просто не существует параметров, убирающих эффект «плевания», особенно если эти порошки легкоплавкие и/или мелкозернистые.
Переход на осевое введение порошка позволяет полностью избавиться от вышеперечисленных проблем:
- Давление и скорость несущего газа больше не привязаны к параметрам пламени и порошка. Единственное условие, – давление несущего газа должно быть несколько выше давления плазмообразующего газа в сопле в месте ввода порошка. За счет осевого ввода, любой порошок полностью захватывается пламенем.
- Всегда можно подобрать такое давление несущего газа, при котором «плевания», связанного с налипанием порошка на край отверстия порошковой дюзы происходить не будет.
- Возможно использование порошковых смесей любой сложности и фракционного состава. Частицы разных размеров будут приобретать различные скорости и температуры, но все, в итоге, примут участие в образовании покрытия. То, что мелкие частицы при осевом вводе в пламя плазмы становятся значительно горячее крупных, открывает новые возможности для дизайна порошковых смесей. Созданию таких полифракционных композиций посвящена основная часть этой книги.
Автору очень повезло, что в его распоряжении в течение многих лет находился плазматрон Axial III с осевым вводом порошка. Если бы не это, то создание новых многокомпонентных покрытий было бы просто невозможно.
Сводная таблица устройств термического напыления
Для обобщения, прямого сравнения и систематизации всех способов термического напыления сопоставим свойства типичных устройств, а также их примерные цены в одной таблице (таблица 2):
Таблица 2. Сравнение устройств термического напыления.
Свойства и характеристики | * Способы термического напыления | |||||||
1 | 2 | 3 | 4 | 5 | 6 | 7 | 8 | |
Использование порошка или проволоки | проволока | порошок | проволока | порошок | порошок | порошок | проволока | порошок |
Максимальная скорость напыляемых частиц, м/сек | 100 | 50 | 200 | 800 | 1200 | 1000 | 100 | 400 |
Максимальная температура напыляемых частиц, °C | 2800 | 2500 | 1700 | 1500 | 600 | 1200 | > 4000 | > 4000 |
Размер частиц, образующих покрытие, мкм | 0,1 – 1000 | 10 – 150 | 0,1 – 1000 | 10 – 100 | 10 – 100 | 10 – 100 | 0,1 – 1000 | 1 – 50 |
КПД напыления по напыляемому материалу | — | + | — | +++ | +++ | +++ | — | ++ |
КПД напыления по расходу энергии | – | +++ | — | — | — | — | ++ | – |
Минимальная пористость покрытия, об.% | 10-15 | 10-25 | 5-10 | 2-3 | < 1 | < 1 | 5-10 | 0,5-3 |
Термическая мощность устройств, кВт | 10-30 | 10-50 | 30-100 | 50-250 | 30-85 | < 20 | 20-150 | 25-150 |
Производительность напыления, кг/час | 2-5 | 5-10 | 2-5 | 5-10 | 10-20 | < 1 | 10-30 | 2-5 |
Распространенность коммерческих устройств и запчастей на мировом рынке | Много устройств | Много устройств | Мало устройств | Много устройств | Мало устройств | Нет устройств | Много устройств | Много устройств |
Мобильность устройств | +++ | +++ | – | – | +++ для Dymet, – для остальных | — | +++ | – для APS — для VPS |
Шумность устройств | — | +++ | — | — | — | — | — | — |
Эмиссия паров и тонкой пыли | — | ++ | — | ++ | +++ | ++ | — | – |
Цена отдельных устройств, € | 2.000- 5.000 | 2.000- 3.000 | 10.000- 20.000 | 10.000- 50.000 | 10.000- 80.000 | нет | 10.000- 20.000 | 5.000- 30.000 |
Цена автоматизированных установок без периферии, € | нет | 30.000- 50.000 | нет | 100.000- 250.000 | 100.000- 250.000 | нет | нет | 100.000- 250.000 |
Цена автоматизированных установок с периферией «под ключ»: звукозащитной кабиной, фильтровентиляционной установкой, роботом и т.д., € | нет | 100.000- 500.000 | нет | 200.000- 600.000 | 200.000- 600.000 | нет | нет | 200.000- 600.000 для APS 1.000.000 и более для VPS |
Сравнительная стоимость эксплуатации с учетом расходных материалов (кроме порошков и проволок), ресурса устройств и запасных частей, €/час | 10-15 | 5-15 | 30-60 | 40-100 | 40-100 | > 100 | 5-30 | 30-150 |
* Нумерация способов:
- Газопламенное напыление проволокой
- Газопламенное напыление порошком
- Сверхзвуковое газопламенное напыление проволокой
- Сверхзвуковое газопламенное напыление порошком (HVOF и HVAF)
- Холодное напыление порошком
- Детонационное напыление порошком
- Электродуговое напыление проволокой
- Плазменное напыление порошком (APS и VPS)
Просмотров: 253
extxe.com
Плазменное напыление: описание технологии, назначение
Несущая поверхность детали иногда требует доработки: изменения структуры или свойств механических и физических параметров. Провести такое преобразование можно, используя плазменное напыление. Процесс является одним из видов диффузии, при которой происходит металлизация внешнего слоя изделия. Для осуществления такой обработки применяют специальное оборудование, способное превращать металлические частички в плазму и с высокой точностью переносить ее на объект.
Свойство покрытий, полученных путем диффузионной металлизации, отличается высоким качеством. Они имеют хорошую адгезию к основанию и практически составляют с последним единое целое. Универсальность метода заключается в том, что нанести можно абсолютно любые металлы, а также другие материалы, например полимеры.
Получить напыление способом плазменного переноса частиц можно только в условиях производственных цехов на заводах и фабриках.
Сущность и назначение плазменного напыления металлов
Суть процесса плазменного напыления заключается в том, что в струю из плазмы, которая имеет сверхвысокие температуры и направлена на обрабатываемый объект, подают дозированное количество частиц металла. Последние расплавляются и, увлекаемые струей, оседают на поверхности детали. К плазменному напылению прибегают в следующих случаях:
- Создание защитного слоя на изделии. Это может быть механическое усиление, когда на менее прочное основание наносят более прочный металл. С помощью диффузионной металлизации также можно увеличить сопротивляемость детали коррозионному воздействию, если наносить пленку из оксидов или металлов, мало подверженных окислению.
- Восстановление изношенных деталей. В этом случае за счет нового слоя покрытия можно убрать дефекты разрушения поверхности, чтобы придать изделию первоначальное состояние. В качестве материала напыления здесь используют металл, идентичный материалу основания.
Плазменное напыление отличается от других видов напыления рядом особенностей:
- Благодаря тому что плазма воздействует на исходное основание при помощи сверхвысоких температур (5000–6000 градусов по Цельсию), процесс протекает в ускоренном режиме. Иногда достаточно долей секунд, чтобы получить заданную толщину напыления.
- Диффузионная металлизация позволяет наносить как монослой на поверхность, так и делать комбинированное напыление. При помощи плазменной струи можно дополнять диффундируемый металл элементами газа, необходимыми для насыщения слоя элементарными частицами нужных химических элементов.
- При плазменном напылении практически отсутствует эффект дополнительного окисления основного металла. Это связано с тем, что реакция протекает в среде инертных газов без привлечения кислорода.
- Финальное покрытие обладает высоким качеством за счет идеальной однородности и равномерности проникновения атомов напыляемого металла в слой основания.
Методом диффузионной металлизации плазменного типа можно получать слои толщиной от нескольких миллиметров до микрон.
Технология и процесс напыления
При газоплазменном напылении металлов основой рабочей газовой среды являются инертные газы азот или аргон. Дополнительно по необходимости технологического процесса к основным газам может быть добавлен водород. Между катодом, в качестве которого выступает электрод в виде остроконечного стержня внутри горелки, и анодом, коим является подвергаемое водяному охлаждению сопло из меди, в процессе работы возникает дуга. Она прогревает до необходимой температуры рабочий газ, который обретает состояние плазменной струи.
Одновременно в сопло подается металлический материал в виде порошка. Этот металл под воздействием плазмы превращается в субстанцию с высокой способностью к проникновению в поверхностный слой обрабатываемого изделия. Распыляемый под давлением расплавочный материал оседает на основании.
Современные плазменные горелки имеют КПД в пределах 50–70 %. Они позволяют работать с любыми металлами, в том числе и тугоплавкими сплавами. Плазменное напыление – полностью управляемый процесс, позволяющий регулировать скорость подачи плазмы, мощность и форму струи.
В случае восстановления формы детали путем плазменного напыления технологический процесс имеет следующие этапы:
- Подготовка напыляемого материала. Суть процесса заключается в сушке порошка в специальных шкафах при температуре 150–200 градусов по Цельсию. При необходимости порошок также просеивают через сито для получения однородных по размеру гранул.
- Подготовка подложки или основания. На этом этапе с поверхности детали удаляют все посторонние включения. Это могут быть окислы либо различные загрязнения масляными веществами. Для лучшего сцепления основание может быть подвергнуто дополнительному процессу образования шероховатости. Если на изделии имеются участки, которые не следует подвергать напылению, их закрывают специальными экранами.
- Напыление слоя металла и операции по заключительной обработке полученной поверхности.
К подложке напыляемый материал может доходить в твердом состоянии, в пластичной форме либо в жидком виде. Это определяется режимом технологического процесса.
Применяемое оборудование
Стандартный комплект установки плазменного напыления включает в себя:
- Источник электрического питания. Его назначение – питать схему формирования высоковольтного разряда и всех систем.
- Блок формирования разряда. В зависимости от устройства схемы может генерировать искровые разряды, импульсные высокочастотные напряжения либо сплошную электрическую дугу.
- Резервуары хранения газа – это чаще всего обычные газовые баллоны.
- Камеру, где непосредственно происходит напыление. Внутрь такого герметичного резервуара помещают обрабатываемую заготовку и плазмотрон.
- Установку вакуумного типа с насосом. В задачи этого агрегата входит создание требуемого разряжения в камере и образование тягового потока для подачи рабочей среды.
- Плазмотрон – устройство, которое снабжено соплом для подачи рабочей среды и системой приводов для перемещения сопла в пространстве.
- Систему дозирования напыляемого порошка. Служит для точной подачи необходимого количества напыляемого материала в единицу времени.
- Охлаждающую систему. В задачу этого элемента входит отвод лишнего тепла от области сопла, через которое проходит раскаленная плазма.
- Аппаратную часть. Она включает в себя компьютер, который управляет всем процессом плазменного напыления.
- Систему вентиляции. Она служит для отвода отработанных газов из рабочей камеры.
Современные установки диффузионной металлизации имеют специальное программное обеспечение, позволяющее путем введения заданных параметров проводить полностью автономную операцию обработки изделия. В задачи оператора входит установка детали в камеру и задание точных условий проведения процесса.
Уважаемые посетители сайта: специалисты и технологи по плазменному напылению! Поддержите тему статьи в комментариях. Будем благодарны за конструктивные замечания и дополнения, которые расширят обсуждаемый вопрос.
wikimetall.ru
обзор видов обработки и оборудования
Напыление металла – это технология изменения структуры поверхности изделия с целью приобретения определенных качеств, повышающих эксплуатационные характеристики. Обработку выполняют путем нанесения однородного металлического слоя на деталь или механизм. В качестве расходного материала используют специальные порошковые составы, которые подвергают термической обработке и придают им значительное ускорение. При ударном соприкосновении с поверхностью частицы осаждаются на плоскости.
Технология появилась в начале XX века в качестве альтернативы традиционным способам поверхностной модификации металлов. По мере изучения и развития методов напыления металлических изделий была образована отдельная отрасль – порошковая металлургия. Это технология получения порошков для изготовления из них различных изделий.
В современной промышленности напыление металлов считается одним из самых экономичных способов обработки. По сравнению с объемным легированием технология дает возможность получить необходимые эксплуатационные свойства поверхности при меньших затратах.
Сущность и назначение напыления металлов
Нанесение защитных покрытий на металл необходимо для многих отраслей промышленности. Цель напыления изделий – повышение базового эксплуатационного ресурса заготовки. Защитный слой обеспечивает надежную защиту от следующих вредных факторов:
- воздействия агрессивных сред;
- вибрационных и знакопеременных нагрузок;
- термического воздействия.
Состав многокомпонентного порошка подбирают исходя из требуемых эксплуатационных качеств.
Использование нескольких составляющих повышает риск получения неоднородного покрытия ввиду расслаивания защитного слоя. Для решения этой проблемы используют специальные материалы канатного типа, где порошок фиксируется пластичной связкой.
В процессе напыления поток частиц направляют на поверхность металла. При взаимодействии с поверхностью распыляемые элементы деформируются, что обеспечивает надежный контакт с изделием. Качество адгезии с заготовкой зависит от характера взаимодействия частиц с подложкой, а также процедуры кристаллизации защитного слоя.
Способы напыления, применяемое оборудование
На заре развития технологии обработка изделий осуществлялась с помощью сопла горелки и обычного компрессора, которые обеспечивали нагрев расходного материала и скоростной перенос на осаждаемую поверхность. По мере развития технологии были разработаны новые методы получения защитного покрытия. Следующим этапом развития стало использование электродугового оборудования. Конструкция такого металлизатора проволочного типа была разработана в 1918 году.
Существует два вида процесса напыления:
- Газодинамическое. Обработка осуществляется мельчайшими частицами, размер которых не превышает 150 мкм.
- Вакуумное. Процедура протекает в условиях пониженного давления. Образование защитного слоя происходит в процессе конденсации напыляемого материала на базовой поверхности.
Рассмотрим основные способы обработки, а также особенности используемого оборудования для напыления.
Напыление в магнетронных установках
Технология магнетронной вакуумной металлизации основана на действии диодного газового разряда в скрещенных полях. В процессе работы установки в плазме тлеющего заряда образуются ионы газа, которые воздействуют на распыляемое вещество. Основными элементами магнетронной системы являются:
- анод;
- катод;
- магнитный узел.
Функция последнего элемента заключается в локализации плазмы у основания распыляемого вещества – катода. Любая магнитная система состоит из центральных и периферийных магнитов постоянного действия. На катод подают постоянное напряжение от источника питания. Под действием тока происходит распыление мишени при условии, что заряд будет стабильно высоким на протяжении всей процедуры.
Преимущества магнетронного метода:
- высокая производительность;
- точность химического состава осажденного вещества;
- равномерность покрытия;
- отсутствие термического воздействия на обрабатываемую заготовку;
- возможность использования любых металлов и полупроводниковых материалов.
С помощью установок получают тонкие защитные пленки в среде специального газа. Напыляемым материалом могут выступать металлы, полупроводники или диэлектрики. Скорость образования слоя зависит от силы тока и давления рабочего газа.
Ионно-плазменное напыление
Одна из разновидностей вакуумного напыления металла на поверхность. Метод является следующим этапом развития технологии термического осаждения, которая основана на нагреве исходных материалов до точки кипения с их дальнейшей конденсацией на заготовках.
В состав принципиальной схемы оборудования для ионно-плазменного насаждения входят следующие элементы:
- анод;
- катод-мишень;
- термокатод;
- камера;
- заготовка.
Алгоритм действия установки:
- В камере создается пониженное давление.
- На термокатод, который является вспомогательным источником электронов, подается ток.
- Вследствие нагрева возникает термоэлектронная эмиссия.
- В камеру подают инертный газ. Наибольшей популярностью пользуется аргон.
- Между анодом и термокатодом возникает напряжение, которое инициирует образование плазменного тлеющего заряда.
- На катод подают мощный заряд.
- Положительные ионы воздействуют на распыляемый материал-мишень.
- Распыленные атомы осаждаются на заготовке в виде тонкого покрытия.
Ионно-плазменное осаждение используют в качестве декоративных или защитных покрытий, которые характеризуются высокой плотностью и прочностью, а также отсутствием изменений в стереохимическом составе.
Для изменения цвета изделия в технологический цикл добавляют реактивные газы: кислород, ацетилен, азот или углекислоту.
Плазменное напыление
Один из самых эффективных – метод диффузионной металлизации. Особенности технологического процесса:
- Рабочая температура плазмы может достигать 6000 ºC. Это способствует высокой скорости осаждения состава на поверхности. Длительность процесса – десятые доли секунды.
- Существует возможность изменения структурного состава поверхности заготовки. Вместе с горячей плазмой в верхние слои изделия могут диффундировать отдельные химические элементы.
- Плазменная струя отличается неизменными показателями давления и температуры. Это положительно влияет на качество напыления.
- Благодаря малому времени обработки заготовка не подвергается вредным поверхностным факторам, таким как перегрев или окисление.
В качестве источника энергии для образования плазмы используют искровой, импульсный или дуговой разряд.
Лазерное напыление
Лазерное напыление металла применяют для достижения следующих целей:
- повышения прочности поверхностного слоя;
- восстановления геометрии изделия;
- снижения коэффициента трения;
- защиты от коррозионных процессов.
В отличие от прочих методов металлизации источником тепла является энергия излучения лазера. Высокая точность фокусировки позволяет добиться концентрации энергии точно в зоне работы. Это снижает термическое воздействие на заготовку, что позволяет избежать изменения геометрии изделия и дает возможность осуществить напыление практически любого материала.
Благодаря высокой скорости охлаждения в поверхностном слое металла образуются структуры с высокой твердостью, что повышает эксплуатационные характеристики детали.
Вакуумное напыление
Вакуумное напыление металла – эффективный и универсальный способ металлизации поверхности. С помощью данного метода можно обрабатывать практически любое изделие. За время технологического цикла с материалом происходит ряд превращений:
- испарение;
- конденсация;
- адсорбция;
- кристаллизация.
Производительность процесса зависит от многих факторов: структуры заготовки, типа наносимого материала, скорости потока заряженных частиц и многих других.
Вакуумные установки отличаются принципом действия. Существует непрерывное, полунепрерывное, а также периодическое оборудование.
Порошковое напыление
Порошковое напыление металлов полимерными материалами является наиболее эффективным способом получения высококачественного покрытия с декоративными или защитными свойствами.
Порошок для распыления представляет собой смесь каучука и цветного пигмента. Его наносят на поверхность с помощью специального электростатического пистолета. При этом порошок приобретает заряд, который способствует эффективному сопряжению с заготовкой.
Для получения качественного покрытия необходимо тщательно подготовить поверхность. Суть процедуры заключается в очистке заготовки от загрязнений и следов коррозии с последующим обезжириванием.
Для использования технологии в промышленных масштабах используют специальные покрасочные линии автоматического или ручного действия.
Напыление металла – одна из самых эффективных технологий модификации поверхности. Обработка позволяет получить покрытие с декоративными или защитными качествами, которые повышают эксплуатационные свойства изделия. А что вы думаете о данной технологии? Какой метод считаете наиболее перспективным? Напишите ваше мнение в блоке комментариев.
wikimetall.ru
Плазменное напыление – АО Плакарт
Плазменное напыление (APS, Air Plasma Spray, воздушно-плазменное напыление) – материал (порошок) будущего покрытия подается в плазматрон и нагревается до плавления и переносится на поверхность плазменным потоком.
Особенность плазменного напыления – высокая температура плазменной струи (до 20 – 22 тыс. градусов Цельсия), высокая скорость перемещения частиц в струе (до 500 м/с). Нагрев поверхности при этом не более 200 град.
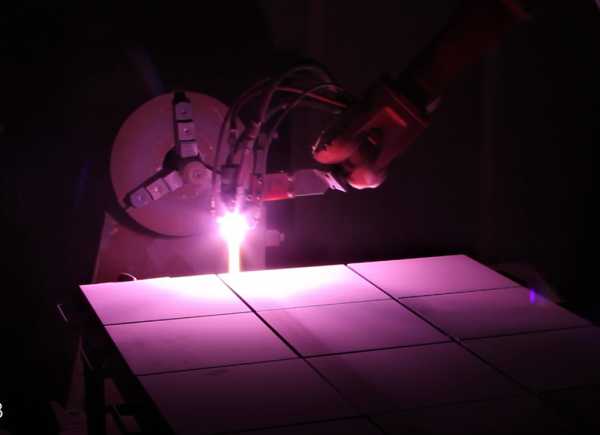
С помощью установок атмосферного плазменного напыления Плакарт P-1000 можно наносить:
- износостойкие;
- коррозионностойкие;
- теплозащитные;
- уплотнительные;
- антифрикционные покрытия;
Плазменные установки Плакарт обеспечивают нанесение покрытий из широкого спектра керамических и металлических порошковых материалов на практически любые внешние и внутренние поверхности отверстий глубиной до 1000мм и диаметром более 125 мм. Плазменные покрытия внесены в конструкторскую документацию на многих отраслевых (авиационных, турбостроительных и пр.) предприятиях и институтах
Преимущества технологии воздушно-плазменного напыления:
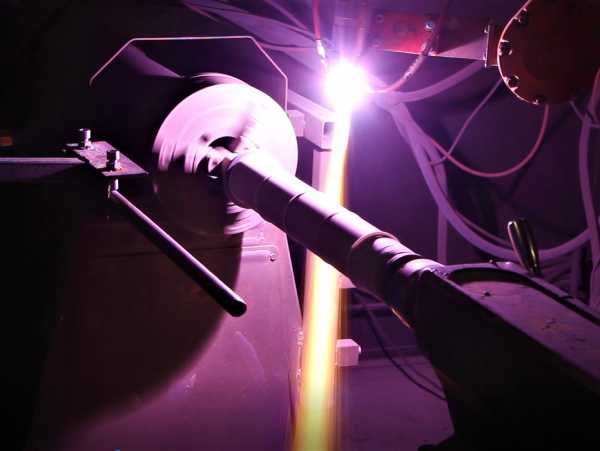
- независимость нанесения покрытия от геометрии поверхности: стабильное качество покрытия обеспечивается как на плоских ровных поверхностях (листы, плиты), так и на крупногабаритных объектах и изделиях сложной формы;
- покрытие (металлы, твердые сплавы, керамику, металлокерамику, полимеры) можно наносить на металлы, пластик, и даже на не терпящие воздействия экстремально высоких температур. При этом практически не происходит деформации основного материала, на который напыляется покрытие;
- равномерное стабильное качество покрытия обеспечивается и на большой площади, и на ограниченных участках больших деталей;
- возможно напыление многослойного покрытия толщиной в несколько миллиметров, что очень важно при восстановлении геометрии изношенных деталей.
Покрытия, наносимые плазменным напылением, отличаются хорошей равномерностью, стабильностью, высокими плотностью и адгезией.
Установка плазменно-порошкового напыления Plakart Р-1000 предназначена для нанесения износостойких, коррозионностойких, теплозащитных, уплотнительных, антифрикционных и других покрытий, придающих рабочей поверхности деталей новые свойства и увеличивающие их рабочий ресурс. Большой выбор отработанных технологий напыления на данной установке позволяет получать хорошо повторяемые покрытия высокого качества.
В установке Plakart P-1000 в качестве плазмообразующего газа используется аргон и водород. При необходимости, в качестве плазмообразующих могут использоваться различные газовые смеси, азот, гелий (доп. опция) и др.
www.plakart.pro
Напыление металлов – все способы и необходимое оборудование
Напыление металлов позволяет улучшить характеристики деталей, работающих в условиях, связанных сильным изнашиванием и механическими концентрированными нагрузками. Металлизация поверхностей повышает устойчивость и увеличивает срок службы. Кроме решения технических задач, напыление используется во время производства декоративных изделий, бижутерии, в пищевой, фармацевтической и химической промышленностях. Для напыления могут применяться различные металлы, конкретный выбор зависит от технического задания.
Химическое хромирование
Используется для обработки деталей со сложной геометрической формой, процесс основан на восстановлении хрома из растворов солей при помощи гипофосфита натрия. Осадок имеет серый цвет, блеск приобретается после полирования. Химическое хромирование протекает в ваннах с таким составом растворов.
Состав растворов для химического хромирования
- Фтористый хром, г — 17
- Хлористый хром, г — 1,2
- Лимоннокислый натрий, г — 8,5
- Гипофосфит натрия, г — 8,5
- Вода, л — 1
- Температура, °С — 70-87
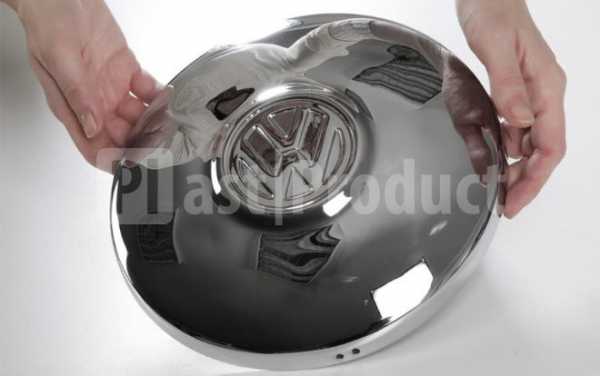
Хромированная деталь
Скорость процесса хромирования может достигать 2,5 мкм/ч, для изготовления ванн используется устойчивый пластик. Металлизация сопровождается выделением ядовитых химических соединений, растворы негативно влияют на кожу людей. Во время производства работ следует соблюдать правила техники безопасности, для очистки воздушной среды устанавливается принудительная вентиляция. Мощность вентиляции рассчитывается исходя из объема помещения или рабочей зоны с учетом минимальной кратности обмена.
На промышленных предприятиях монтируется вентиляция пластиковая, она позволяет выдерживать рекомендованные технологические параметры при минимальных финансовых потерях. Для промышленного хромирования химическим методом применяются специально разработанные растворы с улучшенными показателями.
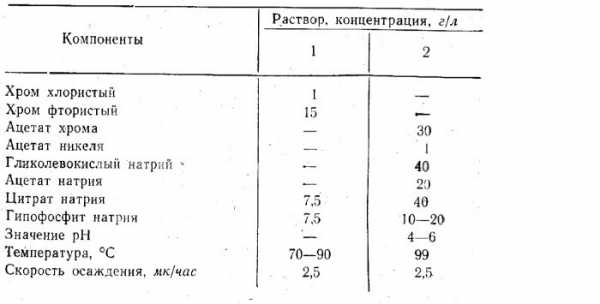
Промышленные растворы для химического хромирования
При приготовлении растворов первым растворяется хлористый хром. Затем согласно схеме могут растворяться лимонно-кислый натрий и фтористый хром. Для ускорения химических процессов в состав добавляется щавелевая кислота. Ионы хрома образуют с ней химически активный ион, скорость покрытия возрастает до 7 мкм/ч и более. Процентное содержание ингредиентов корректируется технологами с учетом поставленных конечных задач по обработке деталей.
Для получения расчетного покрытия необходимо выполнять следующие требования:
- Качественная подготовка поверхностей. Детали очищаются механическим и химическим способами, при необходимости поверхности шлифуются.
- Оборудование должно обеспечивать максимальную автоматизацию процесса для исключения вредного влияния человеческого фактора.
- Постоянный контроль за состоянием раствора, фильтрование, поддержание заданной концентрации, своевременная замена катода.
Нарушение рекомендованной технологии может становиться причиной отслоений покрытий или образования глубоких раковин. Необходимость исправления дефектов приводит к значительному увеличению себестоимости производства.
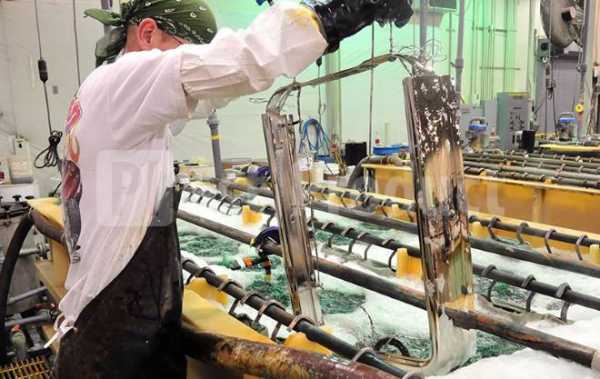
Линия химического хромирования
Визуальный контроль химических процессов производится за счет определения количества выделяемого водорода, технологи рекомендуют для улучшения процесса одновременно покрывать детали из нескольких металлов. Слишком интенсивное выделение водорода может становиться причиной появления раковин, скорость процесса регулируется в каждом конкретном случае.
Газоплазменное напыление
Газоплазменное напыления позволяет получать чистое покрытие с высокими показателями адгезии. Процесс протекает при температурах до +50 000°С, скорость струи оставляет 500 м/с, температура поверхности обрабатываемой детали составляет не более +200°С.
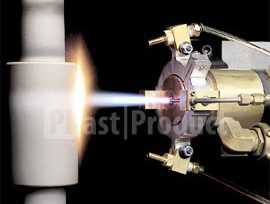
Газоплазменное напыление металлов
Шероховатость поверхности напыляемых деталей до 60 Rz, зона обдува должна на 2–5 мм превышать номинальный размер напыляемого участка. Для работы используются порошки одной фракции по размерам, необрабатываемые участки детали закрываются специальными экранами. Перед процессом поверхность деталей предварительно прогревается до рабочих технологических температур.
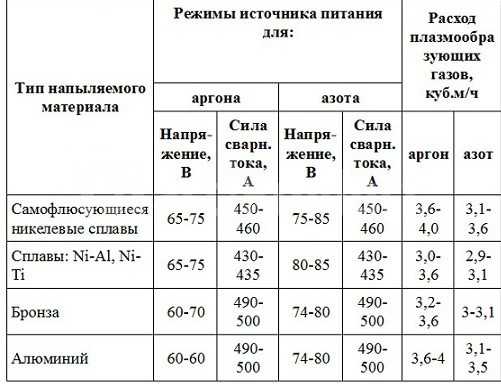
Режимы работы оборудования при газоплазменном напылении
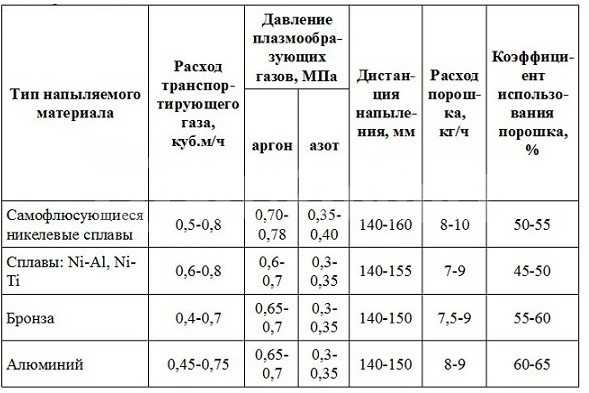
Технология напыления
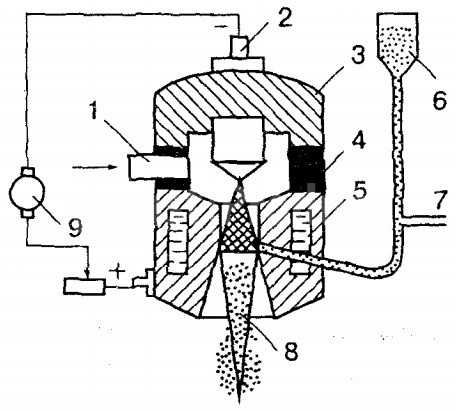
Схема оборудования для напыления
Оборудование для порошкового напыления состоит из подвода газа (1), катода плазмотрона (2), корпуса катода (3), теплоизолятора (4), корпуса анода (5), порошкового питателя (6), подвода газа-носителя (7), плазменной дуги (8) и источника питания (9).
Газоплазменное напыление допускает финишную обработку покрытий для улучшения характеристик деталей, в таком случае толщина покрытия должна учитывать механическую шлифовку.
Напыление в вакууме
Перенос напыляемых металлов выполняется при разрежении 10-2 Па, напыление может быть катодным, магнетронным или ионно-плазменным. Вакуум увеличивает прочность сцепления поверхностей. Оборудование для технологии может быть многокамерным или многопозиционным однокамерным. Первые линии состоят из нескольких установок, в каждой из которых выполняется определенное напыление металлов, агрегаты между собой соединены технологическими линиями для транспортировки деталей. Многопозиционные имеют несколько отдельных постов для напыления в одном объеме. Вакуумное напыление производится по следующим этапам:
- Создание вакуума заданной глубины. Мощные компрессоры откачивают воздух из камеры, металлизация контролируется автоматическими приборами.
- Распыление покрывающего материала. В зависимости от особенностей процесса напыление металлов может выполняться несколькими способами.
- Транспортировка деталей в зависимости от их состояния.
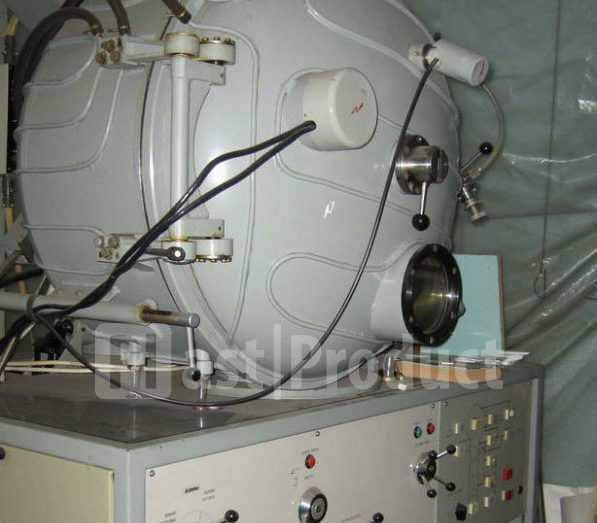
Установка вакуумного напыления
Технологические определенияВакуумное напыление – сложный технологический процесс, зависящий от нескольких параметров:
- Критическая температурная точка напыления. Выше этого значения весь объем направляемых частиц отражается от поверхности детали, напыление металлов приостанавливается. Параметр зависит от металла детали, состояния ее рабочей поверхности и свойств напыляемых материалов.
- Критическая плотность давления. Минимальная плотность, при которой осадочная пленка адсорбируется и становится неспособной принимать атомы металла, напыление прекращается. Контроль критической плотности в установках выполняется непрерывно, при необходимости параметры условий корректируются. В зависимости от состава пленки могут быть моно- или поликристаллическими и аморфными.
Для повышения производительности вакуумное оборудование комплектуется механизмами автоматизированной транспортировки деталей в камеру и из нее, экранами и манипуляторами, заслонками и прочими механизмами. Напыление осуществляется в полуавтоматическом режиме.
Использование вакуумного оборудования позволяет получать напыление металлов с максимальным коэффициентом адгезии, увеличивается скорость протекания процесса, покрытия отличаются повышенной твердостью и химической устойчивостью. Недостаток – высокая энергоемкость процесса. Кроме того, вакуумное напыление не рекомендуется использовать для деталей со сложным профилем поверхностей.
plast-product.ru
Плазменное напыление как способ защиты изделий диффузной металлизацией
Металлизация – эффективный способ придать конечному продукту дополнительные технические и эксплуатационные характеристики. Плазменное напыление представляет собой совершенный вариант диффузной обработки металлических поверхностей для создания качественного покрытия из другого металла или сплава. Диффузная металлизация позволяет улучшить твердость, прочность, цвет и антикоррозийные свойства исходной детали.
Отличительные особенности диффузного напыления
При работе с металлическими поверхностями часто возникает необходимость придать конечному продукту дополнительные характеристики, чтобы расширить область применения детали. Можно защитить металлическую поверхность от воздействия влаги, высокой температуры и агрессивной химической среды. Плазменное напыление имеет ряд особенностей, которые отличают процесс металлизации от других вариантов обработки металлических поверхностей:
- Ускоренный процесс нанесения покрытий благодаря высокотемпературному воздействию на обрабатываемую поверхность – порядка 5000-6000° C. Технологически напыление может длиться доли секунд для получения необходимого результата.
- Плазменная обработка металлов позволяет создать на поверхности комбинированный слой. Диффундировать можно не только металлические частицы, но и элементы газа из плазменной струи. В итоге металл насыщается атомами нужных химических элементов.
- Традиционная металлизация протекает неравномерно и характеризуется длительностью технологического процесса и возможными окислительными реакциями. Струя высокотемпературной плазмы создает равномерную температуру и давление, обеспечивая высокое качество финальных покрытий.
- При помощи плазменной струи перенос частиц металла и атомов газа происходит мгновенно. Процесс относится к области сварки с применением порошков, стержней, прутков и проволоки. Перенесенные частицы образуют слой толщиной от нескольких микрон до миллиметров на поверхности твердого тела.
к содержанию ↑Современная диффузная металлизация предполагает использование более сложного оборудования, чем в случаях, когда применяют газоплазменное оборудование. Для организации процесса диффузной обработки требуется одновременно наличие газовой и электрической аппаратуры.
Оборудование для диффузного воздействия
Ионно-плазменное напыление по поверхности металлов проводится с использованием высокотемпературной технической плазмы – совокупности большого количества частиц (квантов света, положительных ионов, нейтральных частиц, электронного газа). Под воздействием высокой температуры за счет электрических разрядов в газах происходит интенсивная термоионизация частиц, которые сложно взаимодействуют друг с другом и окружающей средой. Благодаря этому различают плазму, ионизированную слабо, умеренно и сильно, которая, в свою очередь, бывает низкотемпературной и высокотемпературной.
Создать необходимые условия для протекания процесса плазменной ионизации и обработки металлических покрытий помогает специальное оборудование – плазменные установки. Обычно для работы используется дуговой, импульсный или искровой электрические разряды.
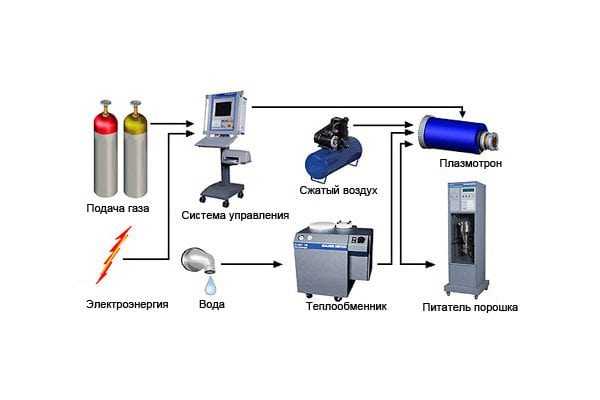
Для реализации технологического процесса требуются следующие установки:
- Генератор высокочастотного типа (можно использовать сварочный преобразователь) – служит источником разряда.
- Герметизированная камера, в которую помещают детали для нанесения покрытий методом плазменного напыления.
- Газовый резервуар. В его атмосфере выполняется ионизация частиц под действием электрического разряда.
- Установка, создающая давление газа. Можно использовать вакуумную или насосную аппаратуру.
- Система, при помощи которой можно качественно изменять токовые характеристики, давление, напряжение, тем самым увеличивая или уменьшая толщину напыляемых покрытий.
Как происходит плазменное напыление: в герметизированной камере фиксируют обрабатываемую деталь, создают электрический разряд, прокачивают рабочую среду с необходимым давлением и напыляемыми порошковыми элементами. Образуется высокотемпературная плазма, которая переносит частицы порошков вместе с газовыми атомами на поверхность некоторой детали. При проведении диффузной металлизации в вакууме, в атмосфере инертного газа или при пониженном давлении можно увеличить скорость движения частиц и получить боле плотный и высокоадгезивный тип покрытий.
Поскольку напыляемым материалом может служить практически любой сплав или металл, ионно-плазменное напыление широко используют в различных отраслях промышленности, а также для проведения ремонтно-восстановительных работ. Любой металл в виде порошков подается в плазменные установки, где под воздействием высокотемпературной плазмы расплавляется и проникает в обрабатываемую металлическую поверхность в виде тонкого слоя напыления. Сферы применения диффузной металлизации:
- детали для авиационной, космической и ракетной промышленности;
- машиностроительное оборудование и энергетическая отрасль;
- металлургическая и химическая отрасль промышленности;
- нефтедобывающая, нефтеперерабатывающая и угольная отрасль;
- транспортная сфера и производство приборов;
- ремонт и реставрация машин, оборудования, изношенных деталей.
Когда струя плазмы и порошков проходит по электродуге и осаживается на обрабатываемой поверхности, образованный слой приобретает важные качественные и эксплуатационные характеристики:
- жаростойкость;
- жаропрочность;
- коррозийную устойчивость;
- электроизоляцию;
- теплоизоляцию;
- эрозийную прочность;
- кавитационную защиту;
- магнитные характеристики;
- полупроводниковые свойства.
к содержанию ↑Ввод напыляемых порошков в установки осуществляется с плазмообразующим или транспортируемым газом. Плазменное напыление позволяет получать различные типы покрытий без ограничения по температуре плавления: металлы, комбинированные сплавы, карбиды, оксиды, бориды, нитриды, композит. Материал, который обрабатывается в установках, не подвергается структурным изменениям, но поверхность изделия приобретает необходимые качественные характеристики. Напылять можно комбинированные слои (мягкие и твердые), тугоплавкие покрытия, различные по плотности составы.
Для нанесения на металлическую поверхность некоторого слоя напыления в условиях высокотемпературной плазменной среды в качестве формирующих покрытий используют не только порошковые составы. В зависимости от того, какими свойствами должна обладать обработанная поверхность, используют следующие особенности плазменной металлизации:
- Наплавление высокоуглеродистой или легированной проволокой под флюсом. Для восстановления поверхностей используют наплавку в установках стержневым или пластинчатым электродом.
- Наплавка по порошковому слою под флюсом используется для реставрации деталей с обширными деформациями по окружности с толщиной слоя более 2 мм.
- Установки для напыления пропускают в качестве плазмообразующих газов аргон, азот, водород, гелий либо их смеси. Необходимо обеспечить отсутствие кислорода, чтобы исключить окисление наплавляемых покрытий.
Наиболее часто этот вид обработки используют для восстановления различных деталей при ремонте автомобильных двигателей. Так, при помощи диффузной металлизации удается восстановить отверстия коренных опор в блоках цилиндров (распространенная поломка), устранить износ головок цилиндров, реставрировать поршни из алюминиевого сплава, коленчатые валы из высокопрочного чугуна, ролики, катки.
При использовании ионно-плазменного напыления значительно возрастает износостойкость сложных узлов оборудования, механизмов и установок. Диффузная металлизация – это эффективный метод реставрации изношенного и усталого металла, а также оптимальный процесс для задания металлическим поверхностям необходимых прочностных и эксплуатационных характеристик.
kraska.guru