Обработка графита на токарном станке: Токарная обработка графита | tokarnaja-obrabotka.ru
alexxlab | 26.04.2023 | 0 | Разное
Токарная обработка графита | tokarnaja-obrabotka.ru
Токарная обработка графита от ООО “Токарная обработка” на okuma B400, 16К20, 1К63, ДИП500 и токарных автоматах. Срок изготовления от 3х дней. Отправьте запрос с чертежами на электронную почту: [email protected]
Наша компания уже многие годы работает в сфере механической обработки и оказывает услуги по токарной обработке графита. Особое внимание уделяется чистоте обработки графита, потому как довольно сложно добиться получения из такого материала деталей высокого качества.
Для расчета стоимости токарной обработки графита пошлите запрос с чертежами на электронную почту: [email protected] Ответим на любые вопросы: 8 3439 38 00 81, 8 3439 38 98 01, доставка по всей России.
Технология обработки графита.Графит отлично поддается обработке на нашем высокотехнологичном токарном оборудовании нового поколения. Графит является слоистым материалом, который не обладает высокой прочностью. Именно поэтому очень важно использовать правильный режущий инструмент и минимизировать зажимное усилие. Если не правильно выбрать режим токарной обработки графита, то на деталях могут появиться сколы и трещины. Наши специалисты имеют отличный опыт в изготовлении таких деталей и всегда подбирают оптимальный режим работы, что в свою очередь гарантирует получение изделий высокого качества.
Все оборудование, на котором выполняется токарная обработка графита, оснащено специальными зажимными устройствами, исключающими риски повреждения деталей. В процессе обработки наши сотрудники учитывают все показатели. Возникновение центробежной силы влияет на степень зажимного усилия, и деталь необходимо закрепить так, чтобы она не треснула и не вылетела. Необходимо обеспечить оптимальный уровень зажимного усилия, при котором деталь из графита не будет повреждена.
Наше оборудование оснащено специализированными цанговыми патронами со специальными кулачками, поверхность которых покрыта пластинами из стеклотекстолита. Все кулачки изготовлены из легковесного металла. Это позволяет избежать воздействия центробежной силы на зажимное усилие. Накладки на кулачках изготовлены из армированного стекловолокна и поверхность залита эластичным пластиком. Применение таких кулачков обеспечивает отличную фиксацию детали в патроне и исключает возможность повреждения заготовки из графита. Материал, из которого изготовлены такие кулачки, имеет высокий коэффициент трения, что позволяет при небольшом зажимном усилии передать крутящий момент.
Некоторые модели токарного оборудования на нашем предприятии оснащены многокулачковыми патронами. Кулачки в таких патронах двигаются попарно и связаны специальными маятниковыми мостами. На таком оборудовании осуществляется токарная обработка деталей из графита, так как такие патроны позволяют хорошо закрепить деталь и исключить возможность ее вылета или повреждения. Зажимное усилие распределяется по всей поверхности детали. В таких патронах деталь отлично центрируется для того, чтобы не возникало даже малейшей вибрации, которая тоже в процессе обработки может привести к разрушению детали.
Как правило, из графита изготавливают детали несложных геометрических форм. Это могут быть цилиндры, стержни или плиты. Наше оборудование позволяет изготовить детали любой формы, а специалисты при обработке всегда учитывают все свойства этого материала. Необходимо понимать, что на деталях из графита не должно присутствовать большого количества отверстий или сложных сечений, наличие которых повышает хрупкость изделия и может привести к быстрой поломке.
Перед выполнением токарной обработки графита, наши высококвалифицированные мастера детально изучают техническое задание, после чего подбирают необходимый режущий инструмент. Обработка графита требует использования специализированного высококачественного инструмента, который хорошо заточен. Большое внимание уделяется снятию припуска с детали. В процессе обработки необходимо минимизировать воздействие режущего инструмента на поверхность заготовки из графита, чтобы избежать появления трещин и надломов. Для этого специалисты перед обработкой создают специальные программы, где учитываются оптимальные обороты и режимы подачи режущего инструмента. Если требуется снять большой слой с заготовки, то работа выполняется за несколько циклов.
Большой опыт токарно-фрезерной обработки, работы с графитом, высокая квалификация нашего персонала, наличие современного оборудования и качественной оснастки гарантируют выполнение токарных работ высокого качества. Наши клиенты всегда остаются довольными и своевременно получают качественные детали из графита. Работы выполняются на станках с прогрессивным программным управлением, что максимально ускоряет и автоматизирует процесс, а также позволяет нам снизить стоимость выполнения работ. Все клиенты могут в любое время проконсультироваться у наших специалистов по всем интересующим вопросам. В случае необходимости, наши инженеры всегда помогут создать чертежи и техническое задание, учитывая все пожелания клиента.
3 правила фрезерной обработки графита
Чтобы правильно обрабатывать графит, нужно обязательно учитывать его свойства. Иначе никак.
Графит от природы очень прочный материал, однако при неправильном обращении с ним легко подвержен образованию сколов и трещин. Хрупкость сильно осложняет обработку данного металла. Однако если следовать советам технологов компании ТИГРОТЕХ, то все получится.
Износ инструмента
Из-за того, что графит является одним из самых абразивных материалов, обрабатывающий инструмент довольно быстро стачивается и выходит из строя.
Можно, конечно, пробовать фрезеровать графит фрезами из быстрорежущей стали. Однако такой инструмент долго не проработает, а качество обработанной поверхности будет оставлять желать лучшего.
Другое дело – фрезы из твердых сплавов с покрытием из поликристаллического алмаза PSD. Алмазное покрытие придает инструменту высокую стойкость даже при сильном абразивном износе.
Алмазные фрезы для ЧПУ Zamus Gra-Mate от южнокорейского производителя Widin идеально подходят для фрезерования графита. Слой из синтезированного алмаза толщиной 18-20 микрон увеличивает длительность эксплуатации данного инструмента в 10-30 раз. Однако, необходимо учитывать, что фрезы с алмазным напылением плохо реагируют на перегрев. При высоких температурах на режущих кромках образуются небольшие сколы и трещины. Чтобы избежать возникновения проблем, лучше всего вести обработку графита на высоких скоростях – от 20 до 40 тысяч оборотов в минуту.
Опасная пыль
Хотя графит намного мягче стали, обрабатывать его намного сложнее. И вот почему.
Во время фрезерования материал превращается не в стружку, как это случается, например, в случае обработки стали, а в порошкообразную пыль. Образованные частицы, хоть и мелкие, но сохраняют абразивные свойства. Пыль летит на оборудование и представляет огромную опасность для основных узлов фрезерного станка.
Кроме того, графитовая пыль является довольно опасной и для человеческого здоровья, поэтому на оператора станка также воздействуют негативные последствия обработки этого материала.
Не стоит забывать, что графитовая пыль, как и любая другая, может быть взрывоопасной.
Чтобы не рисковать здоровьем работника, а также не подвергать станок риску выхода из строя, очень важно устанавливать специальные системы для улавливания и сбора пыли.
Обработка на сухую
Применение смазочно-охлаждающей жидкости значительно облегчило бы предыдущую проблему с устранением графитовой пыли, но… Графит стоит обрабатывать насухую. Более того, необходимо удалить всю влагу из материала еще до начала фрезерования.
Графит является пористым материалом, который поглощает влагу. Если не учитывать это свойство, то проблем не миновать.
Если влага не будет удалена до начала обработки, то она будет перегреваться во время фрезерования и расширяться. В результате образуется трещина на обрабатываемой поверхности, что испортит деталь. Поэтому перед тем, как работать с графитом, просто поместите графит в сушильную камеру на несколько часов.
В компании ТИГРОТЕХ вы можете купить фрезы по графиту Zamus Gra-Mate по цене производителя Widin. Актуальную стоимость и данные по наличию можно узнать в нашем каталоге.
Для помощи в подборе звоните по телефону +7 (495) 642-31-30 или пишите на почту [email protected].
Советы от профессионала — Tri-Gemini
Советы и рекомендации Тони Мухи по уникальным характеристикам обрабатываемости графита , и другие различные графитовые формы. Они производят все: от аэродинамических электродов для компонентов реактивных двигателей до электродов в форме собачьей кости для производства кормов для домашних животных. За это время сотрудники нашего отдела нестандартных электродов столкнулись и решили почти все возможные проблемы, которые вы можете себе представить или с которыми вы можете столкнуться в своей работе. Судя по нашему большому опыту, вы можете догадаться, что мы разработали ряд технологий и методов обработки графита, которые доказали свою эффективность и рентабельность. Мы хотели бы поделиться с вами некоторыми из этих «хитростей».
Распиловка
Графит поставляется в виде необработанных блоков различных размеров, некоторые из которых имеют размеры до 24 x 24 x 72 дюйма, поэтому можно с уверенностью предположить, что потребуется распиловка определенного типа. пил мы используем стандартное полотно из углеродистой стали шириной 1-1/2 дюйма с 2-1/2 или 3 зубьями на дюйм, работающее со скоростью полотна 1800 футов в минуту. Вы обнаружите, что это хорошая отправная точка для большинства приложений.
На небольших вертикальных ленточных пилах, используемых для более тонкого пропила, эффективной комбинацией является полотно из углеродистой стали шириной 5/8 дюйма с числом зубьев от 4 до 8 на дюйм, работающее от 2000 до 2600 футов в минуту.
При выборе пильного диска важно использовать диск с максимально узким пропилом, но с достаточной прочностью луча для предотвращения прогиба , Узкий пропил не только экономит дорогой материал, но и уменьшает количество сколов на стороне выхода пропила. Сниженное усилие резания узкого пропила будет особенно ценно при пилении тонких профилей, неправильной формы или круглых, при зажиме поверхность ограничена
Несколько слов о биметаллических и твердосплавных полотнах: несмотря на то, что эти полотна обладают многими преимуществами по сравнению с полотнами из углеродистой стали при работе со сталью, они не дают значительных преимуществ при работе с графитом. По нашему опыту, их стоимость не оправдывает их использования даже при трехкратном увеличении срока службы лезвия.
Сверление
Сверление не только одна из древнейших операций механической обработки, но и до сих пор самая преобладающая – 60% всего времени обработки затрачивается на сверление отверстий. А поскольку для большинства графитовых электродов требуются отверстия заподлицо, мы хотели бы поделиться некоторыми успехами, достигнутыми нами благодаря достижениям в технологии режущего инструмента.
Большинство производителей сверл предлагают инструменты с высокой спиралью, широкой фаской и параболической канавкой. Параболическая форма канавки имеет прочное поперечное сечение с большим объемом канавки за режущими кромками. Эта форма позволяет быстро удалить графитовую пыль из точки контакта и обеспечивает исключительную производительность при сверлении глубоких отверстий (3 дюйма и более). Добавление покрытия к инструменту (например, TiN) увеличивает срок службы сверла и помогает уменьшить износ, приводящий к конусообразным отверстиям. Комбинация нитритного покрытия, большой спирали и параболической формы позволила нам увеличить как глубину сверления, так и скорость подачи, тем самым сократив время цикла сверления.
Если несколько лет назад наиболее подходящими были сверла из быстрорежущей стали с покрытием, то сегодня для крупносерийных работ по бурению необходимо использовать как минимум твердосплавные сверла с покрытием… и даже сверла с алмазными наконечниками. Их дополнительные затраты более чем окупаются за счет увеличения срока службы, постоянного диаметра отверстий и сокращения количества смен инструмента.
Подачи для сверл диаметром 1/32” и меньше начинаются от 0,0015” до 0,002” дюйма/об.
Подачи для сверл диаметром от 1/32 дюйма до 1/8 дюйма, от 0,001 до 0,003 дюйма/об и от 0,003 дюйма до 0,007 дюйма/об. для больших диаметров. Чтобы предотвратить «выдувание» или «выкрашивание» сквозного отверстия, обязательно используйте еще один кусок графита под заготовкой, чтобы сверло могло переходить в аналогичный материал с постоянной скоростью подачи.
Тем не менее, улучшенный инструмент и повышенная производительность не предотвращают некоторые простые ошибки, и сверление на глубину, превышающую канавки, является одной из наиболее серьезных ошибок, которые вы можете совершить. Графит очень быстро заполняет канавки сверла. Если сверло периодически не вынимается из отверстия для очистки канавок (засверливание), графит быстро перемещается по хвостовику сверла, вызывая его заедание в отверстии. Это приводит либо к поломке инструмента, либо к поломке графитовой заготовки, либо к тому и другому.
Если вам необходимо просверлить канавки, потратьте несколько минут, чтобы отшлифовать зазор на наружном диаметре. хвостовика сверла. Чтобы предотвратить заедание, достаточно отшлифовать диаметр хвостовика до размера, на 0,004–0,005 дюйма меньше диаметра сверла. В этом может заключаться разница между выполнением требований клиента в срок и началом с нуля.
Мы сознательно стремимся перенести как можно больше процессов обработки с ручных операций на наше оборудование с ЧПУ по очевидным причинам повышения производительности и экономии. Токарная обработка не является исключением. Постоянный размерный размер от детали к детали и сокращение участия оператора — все это преимущества станков с ЧПУ. . Из-за абразивных свойств графита было принято использовать высококачественные твердосплавные вставные инструменты с покрытием TiN. Это необходимо для компенсации быстрой эрозии режущей кромки, вызванной абразивностью графита. Например, типичная скорость вращения шпинделя для 2″ диам. стержень из графита средней твердости и плотности составляет 800 об/мин как для черновых, так и для чистовых проходов. Подачи обычно составляют 0,015″/оборот для черновой обработки и 0,004–0,006″/оборот при чистовой обработке. Как правило, глубина резания от 0,015 до 0,025 дюйма обеспечивает лучшую отделку, чем глубина реза от 0,005 дюйма. Это связано со структурой графита, из-за которой он откалывается при введении инструмента. По этой же причине рекомендуется использовать инструмент с положительным передним углом и радиусом вершины не менее 1/64 дюйма.
Однако все всегда меняется! Так, в течение последних нескольких лет наши токарные станки с ЧПУ оснащались алмазным инструментом. Этот шаг был наиболее продуктивной и экономически эффективной мерой, которую мы инициировали в области токарной обработки. Мы используем вставки из алмазной пленки, изготовленные по технологии химического осаждения из газовой фазы (CVD). Эти пластины позволили нам увеличить все наши скорости резания и подачи, в то же время достигая в большинстве случаев лучшего качества поверхности, чем мы получаем с твердосплавными пластинами с покрытием TiN. Нередки случаи, когда пластины CVD демонстрируют срок службы в 25–30 раз больше, чем твердосплавные, до замены или повторной притирки.
Другим и, возможно, лучшим преимуществом инструмента с алмазным наконечником является его способность поддерживать одинаковый размер от детали к детали. Меньшее «время простоя», посвященное подгонке размера путем регулировки смещения инструмента, и меньшее «время простоя», посвященное поддержанию чистоты поверхности путем замены пластин, приводит к увеличению «времени безотказной работы» для обеспечения стабильной работы.
Фрезерование
Фрезерование 2-D и 3-D графитовых электродов значительно расширилось за последние несколько лет. Стандартная оснастка для наших фрез была исключительно твердосплавной. Высокоскоростные и кобальтовые инструменты использовались только тогда, когда диаметр, длина или особая форма резца делали стоимость карбида непомерно высокой. Чтобы увеличить возможности для допусков и сложных требований к контролю, Tri-Gemini инвестировала в ряд высокоскоростных мельниц Mikron. Скоростные фрезерные центры должны быть оснащены алмазной оснасткой, чтобы удовлетворить потребность в оснастке достаточно цепкой ручкой, обеспечивающей повышенную скорость.
При обычном (невысокоскоростном) фрезеровании графита большинство людей склонны устанавливать слишком низкие обороты шпинделя и скорость подачи. Поднимите эти обороты — вы увидите разницу! Если вы хотите быть немного осторожным, начните с увеличения числа оборотов на 10%, но не забудьте также увеличить скорость подачи. Если нагрузка стружки на зуб недостаточна, графит будет действовать на инструмент почти как полирующий агент. Перемещайте инструмент через заготовку, но не со скоростью, которая создает чрезмерное давление на инструмент. Нагрузка на стружку примерно 0,005”/зуб/об. для черновой обработки и .002”/зуб/об. для чистовой обработки являются эффективными отправными точками для фрезерования.
Другим аспектом, на который следует обратить внимание при фрезеровании, является выкрашивание графита на стороне выхода реза. Хотя снижение скорости подачи в конце резания и обеспечение остроты фрезы помогает уменьшить выкрашивание, попробуйте «попутное фрезерование»! «Восхождение» значительно снижает выход стружки. Я бы рекомендовал попутное фрезерование только при использовании оборудования с ЧПУ или тех станков, которые оснащены «ШВП». Попутное фрезерование может выполняться безопасно и эффективно, поскольку «шариковые винты» не имеют люфта, как в ручных машинах, оснащенных ходовыми винтами.
Необходимо решить проблему удаления стружки и пыли! Следите за тем, чтобы зона резки была чистой и не содержала графитовой крошки и пыли. Удалите пыль/стружку с помощью вакуума или сжатого воздуха, или и того, и другого. Мы обнаружили, что, очищая зону реза от стружки/пыли, мы можем делать более глубокие пропилы и при этом сохранять отличное качество отделки. Не допускайте попадания в зону резания смазочных и охлаждающих жидкостей. Мы рекомендуем всегда обрабатывать всухую. Стружка/пыль, смешанные с жидкостью, имеют тенденцию собираться и прилипать к канавкам фрезы, что приводит к ухудшению качества обработки, не говоря уже о том, что суспензия абразивного графита может вызвать преждевременный износ всех движущихся частей вашего оборудования. Учитывая тот факт, что графит изначально грязный, кому действительно нужно тратить свое время, вычищая ведра липкой черной грязи? Тематическое исследование Farr по установке оборудования для удаления пыли является отличным источником информации по этому вопросу и доступно здесь.
Появление высокопроизводительного фрезерования подняло планку в области фрезерования. Высокая частота вращения шпинделя приводит к снижению давления инструмента при резке. Пониженное давление инструмента позволяет фрезеровать очень тонкие ребра и использовать концевые микрофрезы (диаметром менее 0,020 дюйма) без поломки инструмента. Улучшенная реакция станка, обновленное программное обеспечение с улучшенными возможностями, обеспечивающими более качественную обработку поверхности, алмазный инструмент со сроком службы в десять-пятнадцать раз больше, чем у твердосплавных, усовершенствованные системы крепления заготовок и автоматическая работа — все это объединилось, чтобы переместить зону фрезерования на более видное место внутри. изготовление электродов. Устройства смены поддонов на столе фрезерного станка помогают поддерживать производительность фрезерного станка во время резки, а не во время загрузки приспособлений. Несколько областей настройки используются для одновременного выполнения различных заданий с небольшим связыванием программ. Все дело в производительности и экономичности.
SFM = Поверхностные футы в минуту Фреза Прибл. Диапазон SFM
об/мин = оборотов в минуту 1592 Diamond: 500-2000
SFM = (об/мин x диаметр инструмента X Pi) / 12 )
об/мин = (SFM x 12) / (Диаметр инструмента X Pi)
Черновая обработка
1 1 Чип 0: Нагрузка 900 .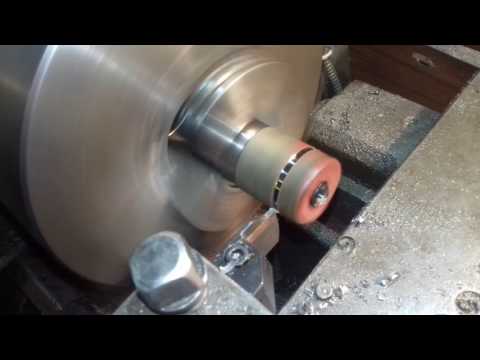
Подача = (об/мин x количество стружки на зуб x количество зубьев) средний зернистость, средняя твердость и открытая структура. Общим требованиям отвечает «зеленое колесо» с обозначением GC 60 h21 V. Средняя глубина резания на черновых проходах обычно находится в диапазоне от 0,010 до 0,020 дюйма, тогда как глубина на чистовых проходах колеблется от 0,0002 до 0,002 дюйма. Средняя подача с поверхности составляет 45-55 футов/мин.
Фасонное шлифование требует круга с более мелкой зернистостью, а круги с зернистостью 100 будут работать очень хорошо, если вы останетесь со средней твердостью. При погружении эти круги очень хорошо сохраняют свою форму, и даже малые радиусы могут быть зачищены без поломки круга. Чаще одевайте колесо, чтобы оно оставалось острым! Несмотря на то, что колесо не ломается, оно наполняется и блестит. Круг с глазурью не только теряет эффективность шлифования, но и выделяет много тепла, что может привести к деформации заготовки.
Круги средней твердости с зернистостью 46 или больше не рекомендуются. Они имеют тенденцию терять часть своего песка во время шлифовальных операций, что вызывает образование рубцов на графите.
Каждая конкретная операция обработки имеет свои собственные переменные: размер обрабатываемой детали, зажимные устройства, состояние режущих инструментов, точность станка, допуски, которые необходимо выдерживать, количество изготавливаемых деталей, безопасность оператора, сбор пыли, и т. д. И хотя у каждой работы есть свои факторы, определяющие подход, который вы будете использовать при обработке, попробуйте немного поэкспериментировать самостоятельно. Небольшой опыт в сочетании с готовностью к экспериментам создадут ваши собственные «хитрости».
Обработка графита на заказ в Tri-Gemini
Узнайте больше здесь
Электроды точно по вашим спецификациям; графитовые или металлические, а также графитовые компоненты для приложений, не связанных с электроэрозионной обработкой. Услуги по исправлению доступны для многократного использования одного и того же блока графита.
Все, что вы хотели знать о жидкости для электроэрозионной обработки
Решение проблем обработки графита
Графит широко используется в электроэрозионной обработке. Однако графит обладает особыми характеристиками, которые затрудняют его обработку. Он прочный, но в то же время мягкий и ломкий, и при неправильном обращении может расколоться. Кроме того, графит является абразивным веществом, вызывающим необычно высокий износ инструмента.
В этом сообщении блога мы рассмотрим проблемы обработки графита и предложим решения для этого довольно уникального процесса.
Электроды могут иметь небольшие ребра и элементы, для которых требуются инструменты малого диаметра, а графит обычно обрабатывается без охлаждающей жидкости и на высоких скоростях. Это делает идеальный обрабатывающий центр с высокой скоростью вращения шпинделя и оптимальными системами пылеудаления.
Крайне важно иметь хорошую чистоту поверхности электродов перед погружением штампа, чтобы свести к минимуму время на стенде после этого.
Общие проблемы и решения1. Истирание и связанный с этим износ инструмента: Поскольку графитовые материалы, используемые для электроэрозионной обработки, чрезвычайно абразивны, инструменты изнашиваются быстрее, чем обычно. Для достижения наилучших результатов при обработке графита используйте инструмент из карбида со специальным покрытием.
InovaTool и The Leading Edge предлагают широкий ассортимент твердосплавных инструментов с алмазным покрытием, устойчивых к износу, что делает их идеальными для решения этой задачи.
Для обработки графита рекомендуется использовать алмазное покрытие CVD для увеличения срока службы и производительности инструмента. Это покрытие наносится непосредственно на твердосплавные инструменты, повышая твердость и создавая слой покрытия, который в пять раз толще, чем алмазное покрытие PVD.
2. Сухая обработка: Обработка без СОЖ и на высоких скоростях создает много пыли. Сжатый воздух можно использовать для уменьшения износа инструмента и предотвращения его преждевременного выхода из строя. Сильная вакуумная система внутри станка обязательна для удаления пыли из рабочей зоны.
3. Геометрия заготовки: Электроды для электроэрозионной обработки могут представлять собой сложные детали с элементами, которые нелегко создать с помощью обычных инструментов и обычных фрезерных станков. Эти электроды могут иметь небольшие, глубокие и хрупкие элементы, которые очень сложно создать. Надлежащие режущие инструменты, работающие с правильными режимами резания, со специальной геометрией и покрытиями, могут помочь справиться с этой задачей.