Обработка лазером металла – Обработка металла лазером: преимущества и особенности технологии
alexxlab | 17.06.2020 | 0 | Разное
Обработка металла лазером: преимущества и особенности технологии
Вопросы, рассмотренные в материале:
- Где преимущественно применяется технология обработки металла лазером
- Какие существуют способы обработки металла лазером
- Какое оборудование используется для лазерной обработки металлов
- Каковы особенности лазерной обработки различных видов металла
Научно-технический прогресс позволил сократить долю ручного труда в производстве. Благодаря разработке передовых инновационных технологий процесс металлообработки стал автоматизированным. Обработка металла лазером позволяет повысить сложность, скорость и точность производственных операций. Из этой статьи вы узнаете об особенностях и преимуществах этой современной технологии.
История технологии обработки металла лазером
В инновационной технологии обработки металла лазером воплотились все передовые достижения академической физики. Оптический квантовый генератор или лазер был открыт во второй половине XX века. Лазерное устройство лавинообразно генерирует фотоны с одинаковой энергией, направленностью движения и поляризацией и преобразует энергию накачки (световую, электрическую, тепловую, химическую и др.) в энергию монохроматического когерентного света. Этот удивительный оптический прибор излучает мощный узконаправленный пучок интенсивного света.
Открытие было высоко оценено физиками и инженерами. В 1962 году, после испытания первого лабораторного квантового генератора, американская фирма «Спектра физикс» разработала и представила на рынке коммерческие лазеры. Это был настоящий революционный прорыв в лазерных технологиях. Позже были созданы различные типы и модификации лазера – от микроприборов до гигантских установок. Например, длина лазерной установки «Нова» в Национальной лаборатории Лоуренса Ливермора в США составляет 137 м, а ее суммарная мощность – 1014 Вт. Лазерное оборудование широко используется в научных и производственных областях.
Уже в 70–80 годы XX века началось интенсивное развитие лазерных технологий, которые с большим успехом применялись в обработке металла: сварке, закалке, наплавке, маркировке, резке. С помощью лазерного оборудования изготавливались различные детали и элементы конструкций: прокладки, кронштейны, дисковые пилы, панели, щитки для приборов, двери, декоративные решетки.
Изобретение кинематических сложных роботов-манипуляторов и гибких оптоэлектронных лучепроводов позволило расширить возможности лазерной металлообработки. В современном производстве с помощью лазера осуществляется резка пространственных металлоизделий.
Сегодня обработка металла лазером – это высокоэффективный технологический процесс. Лазерные станки являются высокотехнологичным современным оборудованием благодаря уникальным свойствам лазера: высокой мощности излучения – до 108-109 Вт/см2 в непрерывном режиме и до 1016-1017 Вт/см2 в импульсном.
Лазерный луч легко управляется автоматизированными системами. Мощное излучение мгновенно нагревает и прожигает сфокусированную зону. При охлаждении металла заготовка не деформируется и сохраняет свою форму. Область резки очищается от продуктов сгорания способом продувки с использованием технологического газа: кислорода, азота, воздуха.
В каких сферах применима обработка металла лазером
Открытие лазера можно назвать одним из самых значимых научно-технических достижений XX века. Разработка универсальных лазерных технологий способствовала рождению современных направлений научной и технической оптики, появлению новых промышленных отраслей.
Лазерные технологии применяются не только для обработки различных материалов, они стали незаменимым элементом специализированных информационных систем, широко используются в науке, медицине, при создании военной техники.
Рекомендовано к прочтению
Лазерная резка, в отличие от механического метода, является более эффективным и экономически выгодным способом раскроя любых металлических листов. Такой метод металлообработки не наносит вреда материалам, полностью исключает деформацию, не требует дальнейшей постобработки.
При обработке металла лазером снижается расход материалов. Современные лазерные станки оснащены специальными программами, которые автоматически помогут рассчитать наиболее экономичный способ раскроя материала.
Лазерная металлообработка является универсальной и востребованной в различных производственных областях: строительстве, машиностроении, станкостроении. С помощью лазера можно изготовить не только крупные массивные детали, но и хрупкие декоративные элементы.
Преимущества и недостатки обработки металла лазером
Лазерная обработка является самым эффективным и высококачественным способом резки различных металлов. Весь технологический процесс раскроя автоматизирован и выполняется по заданным критериям. Лазер хорошо режет любые металлы с различными показателями теплопроводности.
Высокая энергетическая мощность лазерного луча обеспечивает расплавление металла в области резки. Но при этом полностью исключается даже минимальная деформация заготовки, так как зона термического воздействия очень ограничена. Эта особенность позволяет использовать лазерную технологию для обработки мягких металлов.
Преимущества обработки метала лазером:
- Полностью исключается механическое воздействие на заготовку или деталь. Лазерная технология позволяет резать мягкие, хрупкие материалы без риска деформации.
- Возможность обрабатывать твердые сплавы.
- Высокая точность раскроя и реза. Кромка в зоне резки очень ровная, отсутствуют наплывы, заусеницы и другие дефекты.
- Не требуется последующая дополнительная обработка готовых изделий.
- Есть возможность вырезать заготовки и детали даже самой сложной геометрической формы.
- Простота и легкость управления оборудованием. Рисунок детали выполняется в чертежной программе и переносится в компьютер лазерного оборудования для выполнения резки.
- Высокая производительность. Обработка металла лазером происходит в 10 раз быстрее, чем резка с помощью газовой горелки.
- Высокая скорость раскроя тонколистового проката.
- Максимальная экономия расходных материалов за счет компактного размещения деталей на листе.
- Экономическая эффективность. Снижение затрат при изготовлении небольших партий деталей, так как отсутствует необходимость изготовления форм для прессования или литья.
Недостатки обработки метала лазером:
- Высокая стоимость оборудования.
- Низкая эффективность обработки металлов и сплавов с высокими отражающими свойствами: алюминием, нержавеющей сталью.
- Допустимая максимальная толщина металлического листа – 20 мм.
Виды обработки металла лазером
В современном промышленном производстве все чаще применяются лазерные установки. С помощью этой уникальной технологии осуществляется резка, формовка, стыковка материалов. Лазерным лучом можно нанести покрытие или изменить свойства различных материалов: металла, пластмассы, древесины, бумаги и металла.
Наиболее востребованными лазерными технологиями являются: прямое лазерное спекание (DMLS), лазерная и лазерно-механическая гибка, лазерная резка и лазерное сверление, лазерная сварка.
1. Прямое лазерное спекание металлов.
Технология прямого лазерного спекания позволяет быстро изготовить образцы любых металлических деталей без ограничения в геометрической форме. Таким способом изготавливаются металлические формообразующие вставки пресс-форм для литья полимеров под давлением.
Для выполнения прямого лазерного спекания в компьютер вводятся данные в трех измерениях. С помощью высокотемпературного лазерного луча металлический порошок равномерно и постепенно наплавляется вдоль контура заготовки в соответствии с 3D-данными. Готовые детали отличаются высокой прочностью и могут выдерживать максимальные механические нагрузки.
Прямое лазерное спекание применяется для обработки таких сплавов и металлов, как:
- высококачественная сталь;
- инструментальная сталь;
- титан;
- алюминий.
2. Лазерная гибка металлов.
С помощью технологии лазерной гибки осуществляется загибание заготовки. Лазерный луч нагревает зону обработки на плоской металлической пластине. Поверхность, не прогретая лазером, препятствует расширению металла в месте нагрева. Под действием возникшего механического напряжения пластина сгибается. Происходит пластическая деформация металла, вследствие которой пластина после охлаждения сохраняет новую форму.
При выполнении лазерно-механической гибки место сгиба сначала нагревается с помощью лазерного луча, а затем осуществляется механический загиб пластины. Эта технология позволяет уменьшить механическое воздействие в процессе гибки и увеличить относительное удлинение при разрыве металла. Такая обработка металла лазером дает возможность получить больший угол при меньших радиусах изгиба.
3. Лазерная резка металлов.
Технология лазерной резки позволяет с помощью лазерного луча выполнить термическую резку металлических листов или трехмерных заготовок: труб, профилей.
Метод лазерной резки используется в случае, если необходимо быстро и с высокой точностью произвести обработку геометрически сложных, двух- или трехмерных заготовок, сделать трехмерные вырезы в труднодоступных зонах, выполнить бесконтактную резку. Скорость обработки составляет от 10 до 100 и более м/мин. Лазерная резка, по сравнению с вырубкой в штампе, является экономически выгодным способом изготовления даже небольшого количества заготовок.
В производстве могут использоваться комбинированные установки, оснащенные фокусированным лазером высокой мощности для лазерной резки и вырубной головкой для вибрационной высечки и вырубки в штампе. На таком оборудовании можно выполнить две операции – лазерную резку и вырубку в штампе. В таких устройствах обычно применяется углекислотный (газовый), твердотельный или волоконный лазер.
4. Лазерное сверление металлов.
Обработка металла лазером осуществляется без снятия стружки. С помощью лазерного луча внутрь заготовки локально передается мощный поток энергии. В зоне лазерного воздействия материал ионизируется, превращается в пар (плазму) и испаряется. Чтобы исключить образование наплавления по краю отверстия, образовавшаяся плазма отбрасывается в сторону под давлением, которое возникает между внешней средой заготовки и местом сверления.
- Одноимпульсное лазерное сверление.
Отверстие сверлится за один импульс лазерного излучения. У способа одноимпульсного сверления есть свои недостатки: большая энергозатратность импульса; ограничение толщины заготовки, в которой делаются отверстия; коническая форма отверстий из-за постепенного ослабления тепловой энергии при передаче внутрь материала.
- Ударное лазерное сверление.
Отверстие сверлится за несколько импульсов лазерного излучения – лазер несколько раз бьет в одну и ту же точку на заготовке. При каждом импульсе материал испаряется и вытесняется из отверстия под действием испарившейся составляющей. В результате многоимпульсной обработки металла лазером получаются более глубокие (около 100 мм) отверстия, чем при одноимпульсном сверлении.
К преимуществам этого способа сверления можно отнести следующие возможности: сделать отверстия под углом к поверхности заготовки; просверлить отверстия в материалах повышенной твердости, получить качественный результат сверления. Недостатком является более длительный процесс выполнения технологической операции.
- Лазерное трепанирование (вырезание отверстий).
Отверстие любого диаметра сверлится лазерным лучом, который пульсирует и вращается. После высверливания в заготовке первого отверстия рядом с ним с некоторым перекрытием делается другое. Как показывает практика, наиболее соответствующим является перекрытие от 50 до 80 % площади отверстия.
- Ударное сверление вращающимся лазерным лучом (лазерным «спиральным сверлом»).
Этот способ сверления по принципу выполнения очень похож на ударное лазерное сверление, разница лишь в том, что лазерный луч дополнительно вращается. Лазерное «спиральное сверло» снимает с заготовки материал в виде стружки-спирали. Метод ударного сверления вращающимся лучом позволяет добиться высокого качества обработки металла лазером.
5. Лазерная сварка металлов (LBW).
Лазерная сварка применяется для соединения нескольких металлических деталей. Лазерный луч является концентрированным источником тепловой энергии. Такая сварка отличается большой глубиной и высокой скоростью выполнения сварочной операции. В результате получается тонкий и качественный сварной шов. Технология лазерной сварки часто используется в машиностроении.
Для электронно-лучевой (EBW) и лазерной сварки характерна высокая плотность энерговыделения (в среднем 1 МВт/см2). Тепловая мощность луча обеспечивает большую скорость нагрева и быстрое охлаждение рабочей зоны. Термическое влияние лазера распространяется на небольшие области заготовки.
Для сварки используются только лучи небольшого диаметра, размер лазерного пятна варьируется от 0,2 мм до 13 мм. Энергетические затраты зависят от глубины проникновения луча и положения фокальной точки. Чем больше глубина проникновения, тем выше энергозатратность. При расположении фокальной точки ниже поверхности заготовки расходуется максимальное количество энергии.
Выбор непрерывного или пульсирующего лазерного луча зависит от свойств свариваемых заготовок. Для соединения тонких материалов (например, лезвия бритвы) выбирают импульсы длительностью порядка миллисекунд, а для выполнения глубокой сварки необходим непрерывный лазерный луч.
Лазерную сварку называют универсальной технологией, так как с ее помощью можно выполнить соединение деталей из различных металлов и сплавов: алюминия, титана, сталей (нержавеющих, углеродистых, высокопрочных низколегированных).
Лазерная сварка, как и электронно-лучевая, отличается высоким качеством. Но высокая скорость охлаждения при сваривании высокоуглеродистых сталей может привести к растрескиванию шва. Скорость сварки зависит от количества затраченной энергии, типа заготовок и толщины металла. Газовые лазеры обладают высокой мощностью и преимущественно используются для крупносерийного производства в автомобилестроении.
Какое оборудование используется для обработки металла лазером
Оборудование для лазерной металлообработки различается по источникам излучения и выходной мощности, которая определяет металлический материал. Твердотельные (на гранате с неодимом Nd:YAG) квазинепрерывные и импульсно-периодические лазерные источники с выходной мощностью от 100 до 300 Вт предназначены для обработки черных металлов и нержавеющей стали. Газовые непрерывные СО2 лазерные источники с выходной мощностью до 2500 Вт используются для обработки черных металлов легированных сталей и некоторых других видов сплавов.
В комплект оборудования для обработки металла лазером входит:
- лазер, оснащенный системой охлаждения и системой питания;
- координатный стол для крепления заготовки;
- компьютерная система управления координатным столом;
- устройство подачи технологического газа;
- вентиляционная система.
Для обработки металла используется лазер с очень большой мощностью излучения. Чтобы предупредить его перегрев, лазерная установка оснащена двухконтурной водяной системой охлаждения или холодильным компрессором на фреоне. Выбор источников питания лазера зависит от практикоориентированных технологических задач. Трансформаторные схемы питания способны выдерживать большие нагрузки, обеспечивают непрерывную работу и считаются более надежными. При минимальных мощностях используются импульсные блоки питания.
Координатный стол – это высокоточное автоматизированное оборудование, оснащенное портальной схемой. Заготовка, неподвижно закрепленная на координатном столе, режется лазерным лучом, который перемещается по координате. Но могут быть и другие схемы. Например, при резке Nd:YAG лазерный луч перемещается по одной координате, а стол с закрепленной заготовкой двигается по другой координате.
Промышленная компьютерная система для управления координатным столом оснащена различными аппаратными устройствами: приводом, датчиками и т. д. Все поставленные задачи выполняются с помощью программного обеспечения, в состав которого входят:
- Программа ввода исходных данных (электронных чертежей) в графических редакторах AutoCad, CorellDraw, Adobe Illustrator и др. Используются следующие форматы данных: *.plt, *.ai, *.dxf, *.cf2.
- Программа управления поворотом, масштабированием, размножением исходного файла (электронного чертежа) по рабочему полю стола.
- Программа настройки параметров лазерной обработки и режима врезки, автоматического учета ширины реза, определения внутренних и внешних контуров, корректировки режима резки непосредственно в технологическом процессе.
- Программа настройки параметров координатного привода и рабочей среды оператора, генерации (рисования) простейших геометрических форм.
- Программа подключения внешних устройств, управления лазерным излучателем, обеспечения связи с внешней локальной сетью.
При выполнении лазерной резки используется различный технологический газ – кислород для щадящей резки черных металлов, инертный газ азот для нержавеющей стали. При прожигании материала лазерным лучом образуются газообразные и аэрозольные продукты распада. Их удаление осуществляется с помощью специальной вентиляции, которая является обязательным элементом любой промышленной установки для обработки металла лазером.
Для того чтобы лазерный луч попадал точно в цель, оборудование оснащено системой зеркал «летающая оптика». Альтернативой является комплекс деформируемых зеркал, в котором сочетаются стационарные и «портальные» схемы. Луч, прежде чем попасть в сфокусированную точку, отражается в зеркалах и дважды меняет траекторию движения. И хотя в такой системе отсутствует сложная механика, к ее главным недостаткам можно отнести трудности в управлении зеркальными поверхностями.
Современная лазерная установка – это сложный механизм, отличающийся простотой управления. Лазерное оборудование обеспечивает высокую скорость и точность металлообработки.
Компьютерное оснащение позволяет полностью исключить фактор человеческой ошибки, способствует экономичному расходу материалов, гарантирует высокое качество каждого готового изделия.
Полная автоматизация всех операций обеспечивает постоянство сфокусированных лучей. Вся энергия с помощью линз совмещается в один мощный лазерный луч, который при соприкосновении с материалом нагревает поверхность в зоне линии разреза. В то же время остальная область заготовки остается холодной. В результате обработки детали не деформируются, на их поверхности отсутствуют какие-либо дефекты.
Особенности обработки различных видов металла лазером
1. Лазерная обработка алюминия.
Алюминиевые заготовки обрабатываются по заданному автоматизированному шаблону. На начальном этапе в программу загружаются исходные данные – электронные чертежи будущей детали. К выполнению этого процесса не привлекаются узкие специалисты. С помощью компьютера рассчитывается наиболее рациональное расположение формы детали на металлическом листе. Процент излишков сведен к минимуму.
Резка стали и деревообработка являются наиболее востребованными технологиями в промышленном производстве.
В сфокусированную на заготовке точку вместе с лазерным лучом подается поток воздуха, который увеличивает энергию излучения, удаляет продукты плавления и шлаки.
Алюминий – мягкий материал, обладающий высокой теплопроводностью. Он быстро поглощает тепловую энергию лазера. Для многих небольших производственных цехов это свойство металла является проблемой, так как для работы с ним необходим мощный лазер.
Особенности обработки алюминия лазером:
- невысокая производственная скорость, так как высокоскоростные установки не обеспечивают необходимый контроль деформации заготовки;
- отсутствует прямой контакт с материалом в процессе всей операции, лазерный луч прожигает поверхность алюминиевого листа;
- продувная зона обеспечивает полную очистку контура;
- при правильно загруженном чертеже автоматизированная установка позволяет изготовить детали самой сложной формы;
- при работе с алюминием ошибки исключены, система ЧПУ полностью контролирует весь технологический процесс.
При обработке мягкого металла лазером к крепежным элементам предъявляются особые требования, это особенно актуально для устаревших лазерных установок. Для лазерной резки не требуется закрепление заготовок – деталь кладется на координатный стол, а лазерная установка автоматически выполняет все операции в соответствии с введенными данными, загруженными электронным чертежом.
2. Обработка нержавеющей стали.
Нержавеющая сталь обладает высокой сопротивляемостью к любому виду физического и энергетического воздействия. Поэтому обработка этого сплава является непростым энергозатратным процессом.
Особенности обработки нержавеющей стали лазером:
- Раскрой материала осуществляется бесконтактным способом, в результате этого полностью исключается даже самая незначительная деформация деталей.
- Даже при высокой сопротивляемости материала отсутствует фактор погрешности.
- При лазерной резке листовой стали не образуются дефекты, такие как: заусеницы, отслоение краев, заусениц, деформация кромки края.
- Сокращение временных затрат, следовательно, и снижение стоимости выполнения работ.
- Показатель мощности лазерного оборудования не должен иметь каких-либо ограничений по толщине материала или заготовок. Раскрой любого стального листа осуществляется равномерно, в соответствии с электронным чертежом.
Основным преимуществом обработки нержавеющей стали лазером является высокое качество деталей и длительный период их эксплуатации.
Нержавеющая сталь устойчива к коррозии и процессам окисления. Лазер нисколько не снижает физические характеристики нержавеющих сплавов.
3. Обработка лазером меди и латуни.
Чтобы обеспечить правильный раскрой листов меди, необходимо выставить правильные параметры установки ЧПУ, именно от этого будет зависеть качество изготовленных деталей. Резка выполняется на низких скоростях и при максимальной мощности лазера. Несоблюдение технологических правил отразится на конечном результате – нарушится структурная целостность заготовки, произойдет деформация кромок.
Для лазерной резки латуни нет необходимости в особой настройке программы, достаточно выставить стандартные параметры ЧПУ. Лазерная технология гарантирует изготовление деталей высокого качества. В процессе обработки металла лазером не нарушаются физические свойства материала, исключается деформация изделий и образование дефектов. Подобную резку можно по праву назвать современной технологией ювелирной металлообработки.
Почему следует обращаться к нам
Мы с уважением относимся ко всем клиентам и одинаково скрупулезно выполняем задания любого объема.
Наши производственные мощности позволяют обрабатывать различные материалы:
- цветные металлы;
- чугун;
- нержавеющую сталь.
При выполнении заказа наши специалисты применяют все известные способы механической обработки металла. Современное оборудование последнего поколения дает возможность добиваться максимального соответствия изначальным чертежам.
Для того чтобы приблизить заготовку к предъявленному заказчиком эскизу, наши специалисты используют универсальное оборудование, предназначенное для ювелирной заточки инструмента для особо сложных операций. В наших производственных цехах металл становится пластичным материалом, из которого можно выполнить любую заготовку.
Преимуществом обращения к нашим специалистам является соблюдение ГОСТа и всех технологических нормативов. На каждом этапе работы ведется жесткий контроль качества, поэтому мы гарантируем клиентам добросовестно выполненный продукт.
Благодаря опыту наших мастеров на выходе получается образцовое изделие, отвечающее самым взыскательным требованиям. При этом мы отталкиваемся от мощной материальной базы и ориентируемся на инновационные технологические наработки.
Мы работаем с заказчиками со всех регионов России. Если вы хотите сделать заказ на металлообработку, наши менеджеры готовы выслушать все условия. В случае необходимости клиенту предоставляется бесплатная профильная консультация.
vt-metall.ru
Лазерная обработка
- Подробности
Создано: 17 декабря 2012
Просмотров: 9379
Сферы применения лазерной обработки разнообразны, например: обработка материалов с помощью лазерной обработки, обработка военной техники, информатика, медицина, связь и др. Сферы лазерной обработки материалов подразумевает:
- резку листа;
- закалку;
- наплавку;
- сварку;
- обработка, такая как: гравировка и маркировка, а также многие иные технологические операции.
С помощью лазерной обработки материалов можно обеспечивать высокую точность и производительность, экономят электроэнергию и материалы.
Лазерная обработка материалов
Помимо механической резки в промышленности используется с помощью лазерной обработки, основанной на электрофизическом, электрохимическом и физико-химическом воздействий. А именно – плазменная резка и ацетиленокислородная резка, которые обеспечивают более высокую эффективность и производительность, если сравнивать их с механическими методами.
Но при всем этом они не обеспечивают потребной точности и чистоты реза, из-за чего в большинстве случаев обрабатываемому материалу требуется последующая механическая обработка. Электроэрозионная резка позволяет получать рез малой ширины и высокого качества, однако характеризуется достаточно низкой производительностью, что для любого предприятия – не целесообразно.
Сфокусированное лазерное излучение при лазерной обработки дает возможность лазерной обработки осуществлять практически любые сплавы и металлы, причем совершенно независимо от их теплофизических характеристик. При лазерной обработки абсолютно отсутствует механическое воздействие на материал. Вследствие чего можно выполнять лазерную обработку материала с высочайшей точностью, в том числе нежестких и легкодеформируемых деталей.
Благодаря невероятно огромной мощности излучения лазера обеспечивается не только качество, но и весьма и весьма высокая производительность самого процесса реза.
Лазеры
В твердотельном лазере накачка активного элемента реализовывается высоковольтными разрядными лампами, либо импульсными либо непрерывными, а длина волны излучения составляет – 1 мкм. Режим генерации лазера, также может быть или непрерывным или импульсным. Еще данный лазер оснащен режимом гигантского импульса Q-switch.
Лазеры c диодной накачкой. Накачка осуществляется мощными светоизлучающими диодами замес-то высоковольтной газоразрядной лампы. Лазеры достаточно дорогие в цене, но зато в их системе отсутствуют высокие напряжения. Ресурс диодных линеек гораздо значительнее ресурса газоразрядной лампы, к тому же лазеры c диодной накачкой лучше управляются непосредственно от электронных систем, что крайне важно.
CО2-лазеры – газовые. Основа данных лазеров – это смеси газов CО2-He-N2. Длина волны излучения составляет – 10 мкм. При этом возбуждение смеси CО2-лазера осуществляется различными видами электрического разряда (соответственно в газах). Самыми компактными и эффективными являются – щелевые (slab) лазеры, накачка которых производится высокочастотным разрядом. При помощи импульсных лазеров можно резать любую сталь, титан, алюминиевые сплавы, причем рез получается, весьма высокого качества. Также возможна с помощью лазерной обработки обработка и медных сплавов, но эффективность резки подобных материалов напрямую зависит от химических составляющих.
Лазеры-CО2 пригодны не только для лазерной обработки металлов и всяких сплавов, этими лазерами можно разрезать и практически любой неметаллический материал. Однако для ряда материалов сложной структуры, например: ДСП, граниты, бакелитовые фанеры все же не рекомендуется применять лазерную резку. Как правило, для лазерной обработки металлов необходим достаточно высокий уровень мощности (не менее 500 Вт), для разрезания цветных металлов еще больше – 1000 Вт и более.
Здесь особенно эффективны так называемые щелевые CО2-лазеры, обеспечивающие «суперимпульсный» режим излучения по сравнению с другими CО2-системами. То есть световой поток состоит из импульсов имеющих частоту 10-20 кГц, а не непрерывен. Таким образом, при средней мощности, к примеру, в 500 Вт – в импульсе мощность составляет 1000-1500 Вт. Что крайне важно при лазерной обработки металлов, так как ширина реза уменьшается в разы, кроме того уменьшается порог начала резки и существенно улучшается качество лазерной обработки в целом.
Неметаллические материалы твердотельные лазеры режут значительно сквернее газовых, но при этом имеют неоспоримое преимущество при резке непосредственно металлов – из-за того, что волна длиной в 1 мкм отражается хуже, нежели волна длиной в 10 мкм. Алюминий и медь для волны длиной в 10 мкм – практически идеально отражающая среда.
Технология
На сегодняшний день аналогичное по основным параметрам, качеству и набору опций оборудование стоит примерно одинаково. А поскольку современные системы лазерной обработки, которые представлены на российском рынке известными мировыми производителями такими как: Mazak (Япония), PrimaIndustrie (Италия), Bystronic (Швейцария), Trumpf (Германия) очень сходны, то естественно имеет смысл остановиться на характеристиках и общих свойствах присущих данным системам. Проще говоря, сформулировать совместные тенденции развития технологий лазерной обработки, а так же основные признаки лазерного комплекса предназначенного для резки материалов современного поколения.
За последние годы технологии лазерной обработки подверглись весьма значительным усовершенствованиям, например: увеличение толщины разрезаемого материала и производительности (т. е. скорости его разрезания). Сегодняшние крупные лазерные установки для резки различных материалов оснащаются CO2-лазерами обладающими мощностью до 6 кВт. Конечно, у типовых лазерных установок мощность лазера не превышает 4 кВт, но, тем не менее, это позволяет им резать листовую сталь толщиной до 19 мм (в отдельных случаях даже до 25 мм). Чтобы разрезать пластины из коррозионно-стойкой стали толщиной до 12 мм, для лазерной резки используют азот, который закачивается под высоким давлением.
Постепенно повышается и скорость лазерной обработки. К примеру, если на типовом лазерном оборудовании низкоуглеродистую оцинкованную листовую сталь толщиной 1,63 мм разрезают со скоростью составляющей 12,7 м/мин, то на современных лазерных установках эту же сталь, но толщиной более 2 мм, режут со скоростью 20 м/мин и даже свыше того. Кроме всего прочего, скорости быстрых перемещений рабочих элементов подобного лазерного оборудования достигают до 100 м/мин. Следовательно, производительность таких установок при лазерном сверлении листов толщиной в 2 мм достигает 3-4 отверстия в секунду, что, безусловно, является отличным показателем.
Стоит отметить еще одну тенденцию развития лазерных установок – автоматизация. Автоматизация в той или иной степени применяется в подавляющем большинстве лазерных установок. Здесь можно выделить устройства для загрузки листов крупных габаритов, загрузочно-разгрузочные системы, специальные башенные накопители, где заготовки сортируют по типу материала и толщине. Традиционно управление такого лазерного оборудования осуществляется при помощи ЧПУ, и на основе персональных компьютеров.
Стоит отметить, что при повторяемости +0,05 мм точность лазерной резки достигает 0,1 мм, причем высокое качество реза стабильное, поскольку зависит исключительно от постоянства скорости передвижения лазерного луча, у которого параметры остаются неизменны. Обычно лазерные установки компонуются так: стол, где устанавливаются листовые заготовки, подвижной портал УЧПУ для управления режущей головкой и самой головкой, причем следует отметить, что некоторые лазерные установки оснащают двумя режущими головками. Однако подобная компоновка применима только для разрезания небольших деталей.
Подавляющее большинство современных лазерных установок изготавливаются с маневренным лазерным лучом или «летающей» оптикой. При этом материал, который режется, остается совершенно неподвижным, потому как все делает перемещаемый по материалу лазерный луч, осуществляя запрограммированные резы. Сам лазер располагается на раме установки либо же рядом с ней (в данном случае непосредственно система подачи луча концентрирует его по осям Y и Х).
Установки с «летающей» оптикой предназначаются для обработки заготовок размером от 1,2 х 2,4 до 3 х 7,8 м. Оборудованы такие лазерные установки двумя спутниками, при этом каждый из них расположен непосредственно на личном рабочем столе. Данные спутники совместно со столами после отреза одной заготовки меняются своими местами, тем самым снимают со спутника отрезанную заготовку. Такая конструкция позволяет обеспечивать максимальное время применения лазерного луча, следовательно, использовать и максимальную производительность всей установки в целом.
Продолжают выпускать и лазерные установки комбинированного типа. В подобном оборудовании заготовка устанавливается на столе с передвижением по оси Х, а сама лазерная головка перемещается при лазерной обработки, как правило, по оси Y. Хотя они и гораздо проще по конструкции, но, тем не менее, они не обладают такой производительностью какая у лазерных установок с «летающей» оптикой. К примеру, скорость позиционирования при лазерной обработки в 3-10 раз выше, грузоподъемность вдвое, а при добавлении второго стола сменная производительность делается выше аж на 50-100% – разница очевидна.
Чрезвычайно важным фактором для лазерной обработки какого-либо материала является прошивка начального отверстия. Некоторые лазерные установки при помощи процесса летающей прошивки обладают возможностью получать до 4-х отверстий в секунду в холоднокатаной стали с толщиной 2 мм. Получение одного отверстия в листовом металлопрокате из горячекатаной стали большей толщины (до 19,1 мм) при лазерной обработки реализовывают с помощью силовой прошивки приблизительно за 2 с. Использование этих методов лазерной обработки позволяет увеличивать производительность и эффективность лазерной обработки до уровня, который имеют вырубные пресса с ЧПУ.
interlaser.ru
Лазерная резка металла – технология обработки лазером
Лазерная резка – инновационная технология обработки металлических заготовок, которая применяется в производственных масштабах компаний, а также умещается в небольших частных мастерских. Благодаря уникальной установке, продуцирующей лазер, на определенном участке материала создает фигурные формы деталей.
Способ лазерной обработки подходит для каждого металлического материала, но индивидуальные особенности конкретного сырья все-таки имеются.
В чем заключается изюминка технологии?
Исходя из названия метода обработки, основное действие выполняется специальным лазером. Дорогостоящее оборудование фокусирует луч на маленькой площади, в результате чего образуется неимоверное количество энергии.
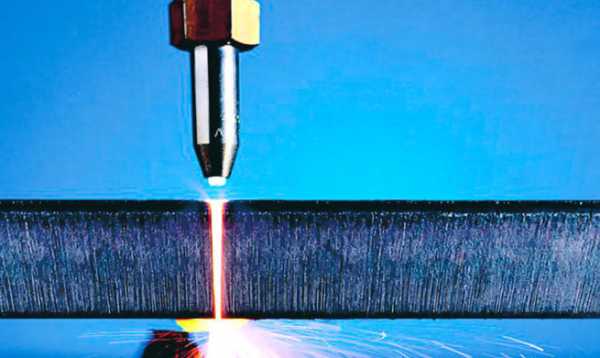
Лазерная резка металла
Под воздействием высокоплотного излучения происходит разрушение любого металла – он плавится, сгорает, иногда моментально испаряться.
Рассматривая характеристики лазерного воздействия, выделяют следующие аспекты процесса:
- отличительной чертой луча в сравнении с обычными световыми волнами является постоянная длина и частота продуцируемой волны. Это свойство обеспечивает отличную фокусировку с помощью системы линз на любой имеющейся поверхности;
- направленность луча всегда поддерживается в высокой концентрации, усиливает эффективность маленький угол рассеивания энергии;
- когерентность – способность сосредоточить в одной области множество однотипных процессов, ведущих к преобразованию материала. Суммарная мощность установки увеличивается за счет полного резонанса, всех происходящих внутри лазера процессов.
Подобные особенности обуславливают энергетическое постоянство, благодаря чему лазерная резка металла считается уникальным высокоэффективным методом получения необходимых деталей.
Тонкости технологического процесса
Современная лазерная установка – идеал оборудования, одновременно воплощающий скорость, невероятную точность обработки и простоту управления сложной машиной.
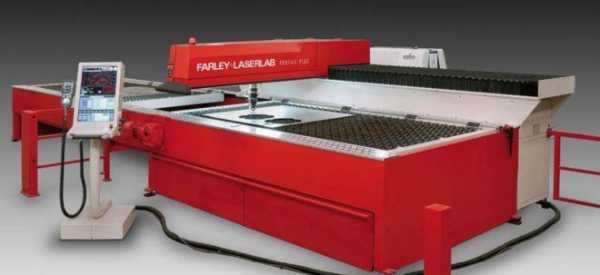
Многоцелевое устройство для лазерной резки
Благодаря внедрению компьютерного оснащения стало возможным устранить фактор человеческой ошибки, избегать излишков, обеспечить качество каждой выпущенной детали.
Работающая автоматизированная машина поддерживает постоянство сфокусированных лучей, совмещая линзами всю энергию в одном мощном потоке – лазере. При соприкосновении с поверхностью происходит нагревание исключительно намеченной линии разреза, при этом остальная часть заготовки остается незадействованной в процессе. Отсутствует лишняя деформация, чрезмерного нагревания всей детали с дальнейшим повреждением особо уязвимых областей не происходит.
Технология лазерной резки металла позволяет работать с мягкими сплавами и тонкими листами заготовок. Способы выполнения обработки подразделяются на два типа:
- лазерную резку плавлением детали;
- выполнение обработки путем испарения.
Плавление наиболее распространенный и дешевый способ достижения результата. Воздействие фокусированных лазерных волн на металл приводит к его нагреванию. Высокая температура на определенном участке становится причиной расплавления детали, а при равномерном смещении луча получают желаемую форму.
Если воздействие луча чрезмерное и энергия достигает второго физического рубежа – молекулы материала начинают закипать. При кипении наблюдается мгновенное испарение частичек детали.
На заметку: процесс испарения считается наиболее эффективным и точным методом обработки. Но для поддержания запредельного уровня энергии требуется множество ресурсов и производственных мощностей. Резку металла лазером по методу испарения считают дорогостоящим этапом производства, он существенно увеличивает себестоимость конечного результата.
Новый лазер – преимущества внедрения технологии
Создание некоторых важных элементов производственных машин и любого профессионального оборудования требует максимальной точности обработки металлических заготовок.
Достигнуть требуемого высокого результата позволяет лазерная резка металла, обладающая весомыми преимуществами в сравнении с известными альтернативными методами обработки:
- автоматизированный программный контроль качества и заложенный алгоритм работы позволяют увеличить точность резки, это является предпосылкой создания сложных элементов;
- скорость процесса существенно превосходит остальные способы;
- лазерное воздействие ограничивает чрезмерный перегрев заготовки, мягко разрезает материал;
- производительность любой лазерной установки обеспечивает заблаговременное выполнение крупных срочных заказов;
- температурному нагреву подвержена исключительно область разреза;
- допускается выполнение контурной резки любой сложности;
- объемы излишков регламентирует компьютер. Программа рассчитывает наиболее рациональное расположение всех необходимых форм;
- отверстия характеризуются минимальным диаметром, равным 0,5 мм.
Лазерную обработку металлов приравнивают к передовым производственным технологиям, что заставляет многих заказчиков уходить от старых производителей деталей к современным методикам.
Если компания внедряет этот метод обработки, то существенно возрастает качество выпускаемой продукции, появляется возможность выполнения индивидуальных заказов.
Резка алюминия – основные нюансы и характеристики процесса
Обработка алюминиевых заготовок происходит по определенному автоматизированному шаблону. В программу загружаются чертежи будущей детали, этот процесс позволяет избежать дорогостоящего привлечения узких специалистов. Дополнительная экономия заключается в рациональном расположении формы детали на имеющейся заготовке, снижается процентное количество излишков.
Распространенным производственным действием считается лазерная резка стали, а также работа с деревянными материалами.
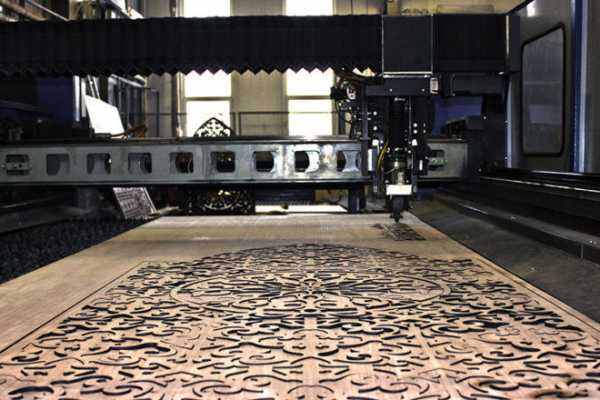
Лазерная резка по дереву
В процессе обработки алюминиевых листов совместно с основным лазерным лучом в сфокусированную зону подается поток воздуха, он увеличивает общую энергию луча, а также служит своеобразным мусоропроводом для образующихся шлаков и продуктов плавления.
Мягкий алюминий характеризуется высокой теплопроводностью, это позволяет ему отлично поглощать энергию лазера. Эта особенность является камнем преткновения многих рядовых производственных цехов, поскольку лишь профессиональный высокомощный лазер способен справиться с этим материалом.
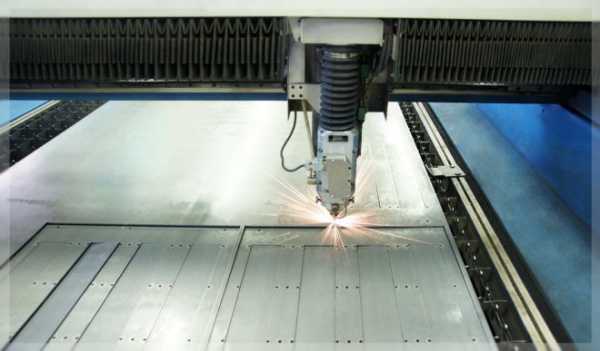
Станок с мощным лазером для резки алюминия
Основными нюансами в работе с алюминиевыми заготовками являются:
- небольшие производственные скорости – высокоскоростные установки не контролируют образование на поверхности заготовки деформаций;
- в процессе работы отсутствует прямой контакт с материалом, лазер просто прожигает поверхность алюминия;
- продувная зона обеспечивает полную очистку контура, эта функция весьма актуальна при дальнейшем сваривании;
- автоматизированная установка при правильно заложенном чертеже справляется с неимоверно сложным проектом детали.
- алюминий не приемлет исправлений – человеческий фактор полностью исключается за счет системы ЧПУ.
При обработке мягких металлов часто появлялся фактор статического влияния крепежных элементов, особенно устаревших производственных машин, но лазерная резка нержавеющей стали не требует закрепления заготовок. Достаточно просто положить заготовку в рабочую зону, а машина выполнит все необходимые операции в точности с заявленным электронным чертежом.
Лазерный станок с ЧПУ
Выполнение резки других материалов
Сложное выполнение художественной резки, раскройка рядовых материалов при работе с автоматизированной лазерной машиной ЧПУ становятся довольно обычной заводской работой. Кроме алюминиевых листов, подобные установки легко справляются с несколькими видами металла:
- нержавеющими материалами;
- листами из других материалов;
- стальными заготовками;
- латунью.
Работа с нержавейкой приравнивается к сложным энергозависимым проектам, поскольку материал отличается высокой сопротивляемостью к любому типу энергетического и физического воздействия. Мощный лазер и компьютеризированная начинка установки позволяют получить сложные фигуры и уникальные детали, прочность которых будет на высоком уровне.
Обработка нержавеющей стали
Лазерная резка нержавейки получила особую популярность. Особенностями процесса обработки нержавейки выступают:
- вся раскройки материала производится бесконтактным способом, что исключает даже минимальную деформацию деталей в местах воздействия машины;
- даже при работе с этим сложных материалов отсутствует фактор погрешности;
- лазерная резка материала исключает шансы образования отслоения краев, заусениц, а кромка края не деформируется;
- общие временные затраты существенно ниже, что обуславливает небольшое снижение стоимости подобных услуг;
- показатель мощности лазера не имеет ограничений по толщине заготовок из нержавейки. Любой лист материала будет равномерно разрезан с учетом заложенного чертежа.
Достоинством процесса лазерной обработки нержавеющих материалов считается отсутствие какого-либо влияния на качественные свойства детали, это не снижает длительность эксплуатационного периода.
Этот материал обладает уникальной защитой от коррозии, а прошлые технологические процессы всегда способствовали снижению способности противостоять окислению. Лазер не способен снижать физические свойства.
Медь и латунь – обработка материала лазером
Для обеспечения раскройки медных листов требуется правильно выставить параметры установки ЧПУ, что во многом предопределяет качество конечных форм. Выполнять резку необходимо на низких скоростях и при максимальной мощности луча. Только такое соотношение условий позволит создать идеальный требуемый продукт. Пренебрежение технологичными нюансами приводит к деформированию кромок и нарушению структурной целостности.
Латунь, как материал, не требует определенной скрупулезной настройки программы резки, допускается проведение раскройки при стандартных параметрах оборудования. Но именно лазерная методика обработки гарантирует отсутствие любых структурных повреждений. Нарушения физических свойств, перегрева детали в процессе работы не происходит. Лазерная резка металла – современный способ ювелирной обработки материалов.
Видео: Лазерная резка стали
promzn.ru
Лазерная обработка металлов – Слесарное дело
В последнее время в различных технологиях промышленного производства все чаще применяется лазер. Так, лазерные установки могут применяться для формовки, резки, стыковки и изменения свойств самых разнообразных материалов, таких как древесина, пластмассы, бумага и металлы, а также для нанесения на них различных покрытий.
К важнейшим технологиям лазерной обработки металлов относятся: 1) прямое лазерное спекание (DMLS), 2) лазерная и лазерно-механическая гибка, 3) лазерная резка и лазерное сверление, а также 4) лазерная сварка.
1) Прямое лазерное спекание металлов – это технология быстрого изготовления металлических прототипов, которая обладает большим потенциалом для прямого изготовления металлических формообразующих вставок пресс-форм, применяемых для литья пластмасс под давлением, а также для прямого изготовления образцов и прототипов различных деталей.
В технологии прямого лазерного спекания металлов используются 3D-данные, в соответствии с которыми осуществляется постепенное наплавление металлического порошка вдоль контура заготовки с помощью высокотемпературного лазерного луча. Модели, изготовленные по этой технологии, обладают высокой прочностью и способны выдерживать большие механические нагрузки.
Данная технология может применяться для спекания следующих материалов:
– высококачественная сталь
– инструментальная сталь
– титан
– алюминий.
2) Лазерная гибка металлов – это загибание заготовки с помощью лазерного луча. При нагревании металлической пластины с помощью лазерного луча в каком-то ограниченном месте эта пластина стремится расшириться в месте нагрева, чему препятствует холодная поверхность, которая не нагревалась лазерным лучом. В результате возникают механические напряжения, под действием которых плоская пластина сгибается. При этом происходят пластические деформации металла. Благодаря этому пластина остается деформированной, т.е. сохраняет приданную ей новую форму даже после охлаждения.
Лазерно-механическая гибка металлов – это технология, в которой используется предварительный нагрев места сгиба с помощью лазерного луча и последующее механическое загибание заготовки. Благодаря этому достигается уменьшение механического усилия гибки, и увеличение относительного удлинения при разрыве металла заготовки. Это позволяет обеспечить больший угол при меньших радиусах изгиба.
3) Лазерная резка металлов – это технология термической резки листового металла, а также трехмерных заготовок, например, труб или профилей, с помощью лазерного луча.
Этот метод применяется в тех случаях, когда сложная геометрия заготовки (двух- или трехмерная) требует точной и быстрой обработки (как правило, со скоростью от 10 до более 100 м/мин), изготовления трехмерных вырезов (в том числе в труднодоступных местах) или/и бесконтактной обработки почти без приложения усилий. По сравнению с альтернативными технологиями, такими как вырубка в штампе, лазерная резка экономически приемлема уже при очень маленьких партиях обрабатываемых заготовок.
Однако также существуют комбинированные установки, в которых преимущества лазерной резки сочетаются с достоинствами вибрационной высечки и вырубки в штампе. Такие установки позволяют выполнять как операции с вырубной головкой, так и лазерную резку любых контуров. Применение в них находят фокусированные лазеры высокой мощности, чаще всего углекислотный (газовый) лазер, но при этом все больше применяется и твердотельный лазер, а также более эффективный, хорошо фокусируемый волоконный лазер.
Лазерное сверление металлов – это технология обработки без снятия стружки, при которой с помощью лазера внутрь заготовки локально передается настолько большое количество энергии, что материал в месте воздействия лазера ионизируется и испаряется. Ионизированный пар (вернее плазма) отбрасывается в сторону за счет разницы давлений между внешней средой заготовки и местом лазерного сверления. При этом наплавление металла по краю отверстия является нежелательным.
а) Одноимпульсное лазерное сверление
Лазерный луч включается однократно и просверливает материал за один импульс. Недостатком этого вида лазерного сверления являются малая максимальная толщина просверливаемого материала и большая потребляемая энергия импульса. Кроме того, получаемые отверстия имеют явную коническую форму, так как передача тепловой энергии внутрь материала сильно ослабевает с увеличением глубины отверстия.
б) Ударное лазерное сверление
Лазерный луч в несколько импульсов бьет в одно и то же место на заготовке и при этом при каждом импульсе испаряет некоторое количество материала. При этом расплавленный материал вытесняется из отверстия под действием испарившейся составляющей материала. Это позволяет получать значительно более глубокие отверстия, чем при одноимпульсном лазерном сверлении (около 100 мм). К другим преимуществам этого метода относятся возможность выполнения отверстий под углом к поверхности заготовки, более высокое качество сверления и возможность обработки даже чрезвычайно твердых материалов. Недостатком является более длительный процесс сверления.
в) Лазерное трепанирование (вырезание отверстий)
Пульсирующий лазерный луч вращается и таким образом может «вырезать» отверстия любого диаметра. После того, как пробито первое отверстие в материале, рядом с ним с некоторым перекрытием выполняется следующее отверстие. При этом на практике наиболее оптимальным оказалось перекрытие в 50-80 % площади отверстия.
г) Ударное сверление вращающимся лазерным лучом (сверление лазерным «спиральным сверлом»)
Этот метод лазерного сверления действует по тому же принципу, что и ударное лазерное сверление, но с дополнительным вращением лазерного луча. Благодаря этому материал заготовки снимается в виде спиралевидной стружки. При этом качество сверления выше по сравнению с лазерным трепанированием.
4) Лазерная сварка металлов (LBW) – это технология сварки, применяемая для соединения нескольких металлических деталей с помощью лазерного луча. При этом лазерный луч служит в качестве концентрированного источника тепловой энергии, обеспечивая тонкий сварной шов, большую глубину и высокую скорость сваривания. Часто эта технология используется в крупносерийном производстве, например, в автомобильной промышленности.
Как и электронно-лучевая сварка (EBW), лазерная сварка характеризуется высокой плотностью энерговыделения (порядка 1 МВт/см2), что обеспечивает малые зоны термического влияния, а также высокую скорость нагрева и охлаждения. Диаметр пятна лазерного луча может варьироваться от 0,2 мм до 13 мм, правда, для сварки применяются лишь лучи малых диаметров. При этом глубина проникновения луча пропорциональна количеству затраченной энергии, но также зависит от положения фокальной точки и увеличивается до максимума, когда фокальная точка расположена чуть ниже поверхности заготовки.
Непрерывный или пульсирующий лазерный луч может использоваться в зависимости от свойств свариваемых заготовок. Так, импульсы длительностью порядка миллисекунд используются для сваривания тонких материалов, таких как лезвия бритв, а непрерывный лазерный луч применяется для выполнения глубокой сварки.
Лазерная сварка является универсальной технологией, пригодной для сваривания углеродистых сталей, высокопрочных низколегированных сталей, нержавеющих сталей, алюминия и титана. Из-за высокой скорости охлаждения возникает проблема растрескивания при сваривании высокоуглеродистых сталей. Качество лазерной сварки высокое, сходное с качеством электронно-лучевой сварки. Скорость сварки пропорциональна количеству затраченной энергии, но также зависит от типа и толщины заготовок. Благодаря высокой допустимой мощности газовых лазеров они особенно хорошо подходят для крупносерийного производства. Так, лазерная сварка является доминирующей технологией сварки в автомобильной промышленности.
< Предыдущая | Следующая > |
---|
slesario.ru
4 способа улучшить кромку при лазерной резке
Качество красок в лазерной резке значительно улучшилось за десятилетия, и многие из этих улучшений исходят из четырех областей: лучшие материалы, сопла, контроль процесса и качество луча.
Рисунок 1
Достижения в системах управления, мониторинг процесса и качество луча улучшают режущие кромки даже в чрезвычайно толстом материале.
Лазеры стали настоящей рабочей лошадкой по обработке металлов, и они никогда не были более производительными. Они вырезают детали на беспрецедентных скоростях, что делает автоматизацию обработки материалов еще более важной. Вся высокая скорость резания в мире может не оказывать существенного влияния на общее время цикла, если лазер простаивает в течение длительного времени, ожидая, что операторы будут загружать листы и выгружать детали.
Подобное мышление также относится к качеству кромок. Качество кромки, конечно, субъективно. Механик будет смотреть на лазерную резку и обнаруживать, что качество кромки не очень хорошее. С другой стороны, сварщик может смотреть на ту же самую часть и видеть гладкое, последовательное, качественное преимущество. Несмотря на это, требования к приложениям диктуют то, что считается «качеством», лазер может закончить резку пакета деталей в мгновение ока, но что делать, если эти части необходимо отправить на вторичную операцию снятия заусенцев?
Резка со скоростями в столькими дюймами в минуту велика, но общее время цикла может не сильно измениться, если детали попадают в заторможенное узкое место удаления грата. Чтобы обеспечить лучший рез, операторы исторически должны были изменять параметры программы резки, такие как скорость резки вокруг острых углов, но иногда они обнаруживали, что это заняло больше времени, чем просто отправка всего прогона через систему удаления грата.
С конца 1990-х и начала 2000-х годов многое изменилось. Режущие лазеры эволюционировали до такой степени, что во многих случаях даже толстые части, выходящие со стола резки, могут пропускать вторичные операции снятия грата — не требуется ручная настройка параметров резания. Эти улучшения были достигнуты главным образом благодаря достижениям в четырех областях: качество материала, технология сопел, контролю процесса и качеству луча (см. Рисунки 1 и 2).
- Улучшенный материал
В течение последних 15 лет более мощные лазеры позволили изготовителям разрезать более толстый материал, но иногда ухудшалось качество края. Вначале трудно было получить толстый материал с гладкой поверхностью фрезеровки и соответствующей композицией состава металла, которая бы позволила лазеру разрезать ровный гладкий край.
Производители стального проката видели рост спроса и начали выпускать более подходящий для лазерной лазерный резки материал. Сегодня для предприятий, обрабатывающих 0,5-дюймовую и даже более толстую сталь, легко доступны материалы для лазерного качества уровня фрезеровки.
- Лучшие сопла
Способность мощных лазерных машин вырезать более толстые материалы вынуждали режущие сопла также совершенствоваться. Усовершенствования включали соосные проточные сопла для резки стали кислородом. При резке кислородом поток вспомогательного газа очень низкий — от 0,5 до 2,0 кубических футов в минуту. Коаксиальные или двойные форсунки допускают плавный и постоянный поток газа в разрез, что обеспечивает хорошее качество кромок в стали толщиной от 0,5 до 1,25 дюйма.
Эта технология не ограничивалась кислородной резкой. Азотная газовая резка стала более популярной благодаря мощной лазерной способности разрезать на высоких скоростях тонкие материалы. Резка азотом оставляла свободную от оксида кромку, которая была готова к сварке или окраске.
Недостаток азота заключался в том, что для удаления материала требовался очень высокий расход газа, поэтому ему требовалось сопло большого диаметра и подача азота под высоким давлением для резки на более высоких скоростях и в более толстых материалах. Чтобы решить эту проблему, усовершенствования сопел помогли создать оптимальную динамику потока. Углы конуса внутри сопла создавали коаксиальный поток для резки под высоким давлением с наименьшим количеством турбулентности в самой зоне резки. Эти исследования и разработки сыграли огромную роль в разрешении лазерам разрезать детали с использованием азота, оставив их без шлаков и с последовательным и гладким краем.
- Лучшее управления процессом
По мере того как лазеры становились более мощными и начали резать более толстые материалы, становилось все труднее достичь свободной от шлаков, с хорошим качеством кромок деталей. Специалисты по лазерной резке увидели это и начали заставлять контроллеры больше, чем просто запускать программу; Они сделали обработку более простой и надежной без необходимости использования опытного оператора.
Фигура 2
Сегодняшние лазеры могут вырезать разнообразные толщины во многих материалах и обеспечить чрезвычайно хорошее качество кромки, гладкое и достаточно однородное, чтобы его не нужно было отправлять через вторичную операцию снятия грата.
Высокомощные лазеры имели возможность резки тонких материалов с высокой скоростью, используя азот в качестве вспомогательного газа, оставляя без оксида края. Однако вначале некоторые из этих частей по-прежнему нуждались в вторичной операции по удалению небольших кусков шлака, оставшихся на острых углах, когда все еще на высокой мощности, лазер замедлялся, чтобы сделать резкий поворот. Чтобы устранить вторичное снятие заусенцев, программистам пришлось бы сменить режим работы лазера, чтобы использовать меньшую мощность, скорость и частоту на каждом углу. Это заняло много времени на стороне программирования, и поэтому вскоре они поняли, что более эффективно очищать края после резки, а не тратить время на программирование.
Сегодняшние контроллеры автоматизируют все это. Они подсчитывают величину мощности, скорости и частоты, чтобы понижаться в зависимости от скорости, с которой режущая голова движется в угол, и повышаться, когда она разгоняется за углом. Это позволяет избежать перегрева и препятствует образованию грата ков в углах (см. Рис. 3).
Тем не менее, лазер не может достичь хорошего качества кромок без хорошей прошивки. Старые машины сработали с запрограммированным временем пирсинга. Если пирсинг не пробивал материал в запрограммированный промежуток времени, машина все же начинала резать, только для создания плохих и, возможно, непригодных для использования деталей. Таким образом, операторы устанавливали чрезмерно длинные периоды пирса, чтобы обеспечить проникновение насквозь. Это добавило много секунд для каждого пирса, что продлевало общее время цикла для прогона.
В старых системах фактическая резка также выполнялась заданной программой, которая не могла адаптироваться к непредвиденным изменениям условий резания. Если в результате работы создавались бтакованные детали, операторы по-прежнему обнаруживали, что выбрасывают детали с плохими краями и вырезают дополнительные детали.
Именно здесь мониторинг процесса помог заполнить нужную ситуацию. Используя датчики света, встроенные в машину, контроллеры теперь контролируют лазерную резку в реальном времени. Мониторинг процесса позволяет машине «смотреть» пирсинг и резку, а также корректировать, чтобы процесс мог продолжаться для обрабатывать используемых деталей. При контроле пирса контроллер наблюдает за пирсом, ощущает, когда он проходит через материал, и только затем начинает резку деталей.
Мониторинг процесса также включает обнаружение разгара кромок и образования плазмы. Используется при резке стали с кислородом, чтобы детектировать разгара кромок от перегрева, когда материал горит неустойчиво, что приводит к плохому качеству кромок. Контроллер видит это и делает необходимые корректировки, чтобы слегка охладить разрез, временно уменьшая мощность и замедляя работу, прежде чем продолжить с большей скоростью.
Подобно обнаружению разгара кромок, плазменная детекция используется с резкой азота. При резке нержавеющей стали или углеродистой стали азотом лазер расплавляет сталь, а вспомогательный азотный газ эвакуирует расплавленный материал, оставляя свободный от оксида край. Однако, если лазер слишком быстро режет, он поворачивает на резкий угол, или его фокус немного уходит, вы рискуете «потерять срез» — получить непрорез- и создаете непригодные детали.
Когда это происходит, азот и расплавленный материал создают плазму. Датчик обнаружения плазмы обнаруживает эту частоту света и подсчитывает, что рез скоро будет потерян, прервется. В этот момент машина замедляет скорость подачи на заданное расстояние до того, как будет возвращаться обратно без потери разреза. Результат: система продолжает производить хорошие детали с чистыми краями.
- Новые лазеры, новые параметры луча
OEM-производители потратили миллионы долларов в исследования и разработки, чтобы улучшить качество лазерного луча. Благодаря лучшему лучу лазер позволяет более стабильно и качественно отрезать сталь, нержавеющую сталь и алюминий. На протяжении десятилетий большая часть этой работы была сфокусирована на CO2-лазерах, но в последние годы R & D также подтолкнула исследования и разработки для твердотельных лазеров, включая волоконный лазер и, в последнее время, технологию с прямыми диодами.
CO2-лазер изменил технологию изготовления металла. Он добрался до нас, где мы находимся сегодня. Волоконный лазер зарекомендовал себя следующим поколением лазерной резки для промышленности. Благодаря более низкой стоимости обслуживания, простоте эксплуатации и возможности резки на гораздо более высоких скоростях, чем CO2-лазер, волоконный лазер является самым быстрорастущим вариантом для многих новых лазерных покупок. Он производит кромку в тонких материалах, очень похожих на высококачественные края, которые производит лазер СО2; но по мере увеличения толщины материала качество краев уменьшается.
Рисунок 3
Контроллеры используют мониторинг процесса для обнаружения характеристик пирсинга и резки в реальном времени. Они вносят необходимые изменения, чтобы обеспечить наилучшее качество кромки, даже вокруг острых углов. Лучше излучение, сопла, контроль процесса и материал обеспечивают качество.
Качество лазерного луча измеряется произведением параметров излучения или BPP (beam parameter product). Лазеры CO2 обычно имеют BPP от 8 до 9 мм • мрад, что позволяет лазеру резать сталь, нержавеющую сталь и алюминий с очень хорошим качеством кромок.
Волоконные лазеры обычно имеют BPP от 1 до 3 мм • мрад, что позволяет лазерам резать очень быстро в более тонких материалах, но качество кромок в более толстых материалах ухудшается.
Именно поэтому CO2-лазер был выбором производителей, которые обрабатывают более толстые материалы. Однако появляется новая технология, которая изменяет свойства луча волоконного лазера, позволяя ему резать толстую мягкую сталь с тем же качеством, что и CO2, даже с половинной мощностью. Это позволит изготовителям приобретать волоконный лазер для обработки их полного диапазона типов материалов и толщин без специальной оптики и без изменения объектива.
Способность эмулировать качество кромки CO2 на волоконных машинах была и продолжает выполняться путем использования Специальных линз и зеркал, которые изменяют ширину реза, позволяя большему количеству вспомогательного газа проникать в разрез и уменьшать плотность мощности пятна. Однако, изменяя значение BPP, волоконный лазер может достичь качества луча CO2-лазера с правильной настройкой луча и без необходимости в дополнительных настройках и расходных материалах. Взглянув в будущее, новая технология, без сомнения, добавит еще одну морщину на лазер Рынок резки. Некоторые производители разработали твердотельные системы, известные как лазеры с прямым диодом, которые обеспечивают дополнительную эффективность и уникальные преимущества для обработки. Хотя пока неясно, как эта технология повлияет на текущие варианты лазера, она уже показала способность производить превосходное качество краев.
Лазерная Технология всегда меняется. Более быстрые, более эффективные системы продолжают появляться — и еще больше впереди.
Источник: http://www.thefabricator.com/article/lasercutting/4-ways-to-a-better-laser-cut-edge
Ранее по теме:
Поделиться ссылкой:
- Нажмите, чтобы поделиться на Twitter (Открывается в новом окне)
- Нажмите здесь, чтобы поделиться контентом на Facebook. (Открывается в новом окне)
- Нажмите, чтобы поделиться в Google+ (Открывается в новом окне)
- Нажмите, чтобы поделиться на LinkedIn (Открывается в новом окне)
- Нажмите, чтобы поделиться в Telegram (Открывается в новом окне)
- Нажмите, чтобы поделиться записями на Pocket (Открывается в новом окне)
- Нажмите, чтобы поделиться в Skype (Открывается в новом окне)
- Нажмите, чтобы поделиться записями на Tumblr (Открывается в новом окне)
- Нажмите, чтобы поделиться в WhatsApp (Открывается в новом окне)
- Нажмите, чтобы поделиться записями на Pinterest (Открывается в новом окне)
- Нажмите, чтобы поделиться на Reddit (Открывается в новом окне)
Похожие записи
xn--80akfo2a.xn--p1ai
Материалы для лазерной обработки | Статьи компании «ЮСТО»
Акрил (оргстекло). “Классический” материал для лазерной резки. Режется очень хорошо до толщины 10 мм. Хорошо наносится и любой вид лазерной гравировки. Пожалуй, лучше всех остальных материалов отвечает требованиям лазерной обработки. Связано это в основном с тем, что при лазерном воздействии практически отсутствует плавление материала, в основном идет испарение и удаление паров сжатым воздухом, который подается в зону обработки. Заметное оплавление поверхности реза происходит только при небольшой скорости резки и минимальной подаче воздуха – лишь бы не допустить возгорания материала. Тогда мы имеем то, что называют “зеркальной кромкой” реза. При работе с молочным и цветным акрилом этот эффект выражен слабее.
На кромке реза обычно наблюдается тонкая полосатая структура, которая практически до конца неустранима и вызвана физическим процессами, протекающими в зоне реза. Но не надо путать эту тонкую структуру с зубцами большей амплитуды, которые есть следствие недостатков в оборудовании.
При резке акрила толщиной более 5-8мм надо учитывать термические напряжения, которые могут возникать в материале, особенно в режиме “зеркального реза”, и взаимодействовать с собственными внутренними напряжениями.
Полистирол режется медленнее и хуже, чем акриловое стекло. Резка полистирола идет через расплав материала. Поэтому на кромках реза неизбежно появление облоя. При небольшой подаче сжатого воздуха кромка реза почти прозрачна, но облой значителен. При увеличении подачи воздуха облой уменьшается, но кромки реза становятся шершавыми, а решетка технологического стола и вентиляция забиваются тонкими нитями, выдуваемыми из зоны реза. После резки практически каждого листа заготовки необходимо чистить стол и вентиляционную решетку. Резка полистирола возможна, но очень трудоемка.
Полиэфирное стекло (ПЭТ, ПЭТФ, ПЭТГ). Полиэфирное стекло хорошо режется лазером, но хуже акрила. Небольшой облой практически неизбежен. Поверхность реза также может быть близкой к зеркальной, но периодическая неровность поверхности реза всегда присутствует и несколько сильней выражена, чем у акрила.
Стиролакронитрил (САН)- сравнительно новый полимерный материал, используемый в рекламных технологиях, хорошо режется лазером. Качество реза примерно среднее между акрилом и полистиролом.
Зеркальные и фольгированные пластики режутся в общем также как и основной материал, но есть и определенные проблемы, связанные с возможностью повреждения зеркального слоя. Многое зависит от типа и марки металлизированного пластика, способа нанесения металлизированного слоя и (или) защитного слоя краски. Во всех случаях для уменьшения вероятности возгорания и повреждения зеркала требуется более интенсивных поддув воздуха. Кроме того, во избежание повреждения зеркального слоя часто целесообразно вести резку таких пластиков вверх зеркальным слоем. Поэтому желательно для каждого типа материала провести пробные резы.
Поликарбонат плохо режется лазером и только небольших толщин, до 1-2мм. Край реза зеркально-коричневый, с выраженным облоем и заметной периодической структурой. Возможна резка сотового поликарбоната толщиной 4-6мм, но с весьма низким качеством реза.
Слоистые пластики – текстолит, гетинакс и т.п. Режутся лазером очень плохо и только малой толщины. Во многом это связано со слоистой структурой материала и характеристиками используемой полимерной связки.
Полипропилен, капролон и др. литые полимерные материалы, в т.ч. термореактивные можно вполне прилично резать до толщин 5-10мм. Но очень многое зависит от конкретной марки материала и его производителя. Поэтому обязательно проведение пробных резов.
Фторопласт можно резать лазером, но только при очень хорошей вытяжке. Объемный характер поглощения лазерного излучения во фторопласте определяет весьма специфический, взрывной, характер процесса резки.
Облицовочные пластики и термопласты. Большинство режется только при небольшой толщине (до 1-2мм). Качество реза может быть вполне приличным, но трудоемкость резки велика. Обязательно проведение пробных резов на каждой партии материала.
Пенопласты и поролоны режутся без проблем. Возможна резка, как с оплавлением поверхности кромок, так и практически без ее оплавления. Но при большой толщине материала (более 20-25мм) проявляется значительная “бочкообразность” лазерного реза, т.е. края реза перестают быть перпендикулярными поверхности. При резке поролона есть трудности с внутренними напряжениями в материале в результате которых может исказиться контур резки.
Дерево и шпон хорошо режутся до толщины 10-15 мм, в зависимости от типа древесины. Требуется интенсивный поддув для удаления продуктов горения. Хорошо режутся сосна, ель, осина, тополь. Значительно хуже береза, тем более бук или дуб. Чем тверже и плотнее древесина, тем трудней она режется. лазером. Характер резки вдоль и поперек волокон различен. Общая проблема сучки, при наличии которых отличного качества реза добиться очень трудно. Край реза от светло-коричневого до почти черного, слегка обугленный. Чем толще и тверже древесина, тем темнее кромки реза.
Фанера. Хорошо режется до толщины 8-10мм. Резка фанеры сильно зависит от сорта древесины, вида клея и способа обработки. Лучше всего режется обессмоленная фанера из древесины хвойных пород. Березовая фанера режется хуже. Еще хуже фанера с формальдегидными смолами. Поверхность реза всегда темная. Режим и качество резки конкретного сорта фанеры определяются экспериментальным путем.
Картон, пенокартон, бумага, ткани прекрасно режутся лазером. Край реза слегка желтоватый или коричневый. Для тонкий материалов проблемой является их ровная укладка и удержание на плоскости. Резка в несколько слоев практически не используется, т.к. в этом случае крайне трудно избежать внедрения продуктов распада между слоями и их загрязнения.
Кожа хорошо режется лазером до толщины 3-4мм. Требуется интенсивный поддув. Цвет и степень обугленности краев реза очень сильно зависит от типа кожи. Обязательно проведение пробных резов. Еще проблема – ровная укладка на поверхности стола раскроя.
МДФ и ПСБ хорошо режутся лазером до толщины 8-10мм. Но характеристики материала (тип связки, плотность прессовки) очень сильно варьируются в зависимости от его марки и конкретного производителя. Поэтому обязательно проведение пробных резов. Край реза ровный, от светло- до темно коричневого, слегка обугленный. Обязателен интенсивный поддув сжатого воздуха.
Ламинированная ДВП хорошо режется лазером до толщины 10-12мм. Торцевая поверхность реза от светло- до темно-коричневого цвета, в зависимости от толщины. Требуется интенсивный поддув воздуха.
ДСП режется лазером отвратительно из-за своей рыхлой структуры и особенностей используемой полимерной связки (эпоксидные или формальдегидные смолы). В принципе можно резать ДСП толщиной 6мм. Край реза неровный, темно-коричневый, местами черный.
Резина и линолеум хорошо режутся лазером. Но при этом в тонком (порядка 0,1мм) слое вокруг кромок реза теряется вулканизация. Для некоторых сортов резины возможно обугливание по торцевой поверхности реза. Остается специфический запах, выветривающийся со временем.
Поранит, гипсокартон, слюду можно, и довольно успешно, резать лазером. Лазерная резка прокладок из паротита практикуется очень часто. Скорость резки определяется толщиной материала. Вообще высокотемпературные и композитные материалы резать лазером можно, если только эти материалы не боятся термических напряжений.
Искусственный камень. Возможность резки зависит прежде всего от типа используемой связки. Почти наверняка будет хорошо резаться искусственный камень толщиной 10-12мм, если он на акриловой основе. Торцевая поверхность реза гладкая, матовая. В остальных случаях необходим пробный рез.
Камень резать лазером в принципе можно, но очень неэффективно. Лучше и не пробовать.
Стекло, керамику резать лазером возможно, но сложно. Хотя некоторые виды настенной керамической плитки режутся вполне удовлетворительно. Но обычный для стекла и керамик механизм термораскалывания, который используется при их резке, дает положительные результаты только при больших партиях совершенно однотипного материала. Кроме того, малые радиусы кривизны контура реза все равно исключаются, а скорость резки весьма невелика.
Вспененные ПВХ пластики. Возможна резка вспененных ПВХ пластиков толщиной до 15 мм. При большей толщине материала край реза начинает обугливаться. Резка идет при интенсивной подаче сжатого воздуха. Облой (заусенец на отливке или штамповке) очень мал или практически отсутствует, т.к. процесс резки в основном идет через сухую возгонку материала.
Торцевая поверхность реза имеет коричневый цвет, светлеющий со временем. Чем больше толщина материала, тем темнее кромка реза. Цвет кромки определяется парами ПВХ, которые образуются в процессе лазерной резки и впитываются в пористую поверхность реза. Коричневый торец сохраняется даже при резке литых, в т.ч. прозрачных, ПВХ пластиков. Удаление цвета механической зачисткой или мойкой возможно только частично, так как пары проникают вглубь материала. Детали после резки имеют специфический запах, исчезающий со временем.
Неприятной особенностью резки ПВХ являются пары хлора, которые также выделяются при резке, пусть и в крайне ограниченном количестве и вызывают коррозию всех стальных деталей станка.
www.yusto.ru
6.3. Лазерная обработка
В 1951 г. Басовым Н.Г., Прохоровым А.М. и другими учеными, получившими позднее Нобелевскую премию, был предложен прибор, названный мазером (microwave amplification by stimulated emission of radiation) – микроволновый усилитель электромагнитных волн за счет вынужденного излучения, в диапазоне сантиметровых волн. На этом принципе усиления был разработан первый твердотельный рубиновый лазер (light amplification by stimulated emission of radiation), работающий в оптическом диапазоне длин волн.
Технологии обработки материалов с использованием лазеров дают возможность осуществления процессов, недоступных большинству других технологий при полной автоматизации и высокой производительности процессов.
Создание технологических лазеров мощностью в несколько киловатт непрерывного излучения и пиковой мощностью импульсного излучения (длительностью 10-8…10-6 с) в сотни мегаватт позволяет достичь при фокусировке этого излучения интенсивностей до 108 Вт/см2 в непрерывном режиме и до 1012 Вт/см2 в импульсном режиме.
В термических видах технологических процессов (резке, пробивке отверстий, закалке, наплавке, сварке и др.) применяется лазерное излучение при интенсивности 104…107 Вт/см2.
При действии лазерного луча на поверхность металла, происходит преобразование энергия его электромагнитной волны в тепловую энергию электронов решетки в тонком слое глубиной 10-6 см за время 10-11 с.
Лазерная обработка материалов производится без изоляции образцов в вакууме. При лазерной обработке отсутствует последующее рентгеновское излучение от образца.
В основе работы лазера лежат три фундаментальных явления, происходящих при взаимодействии электромагнитных волн с веществом, а именно – процессы спонтанного и вынужденного излучения и процесс поглощения.
Если в некоторой физической среде существуют два энергетических уровня 1 и 2 с энергиями Е1 и Е2 (Е1 < Е2), из которых уровень 1 принят в качестве основного, то можно предположить, что атом (или молекула) вещества находится первоначально в состоянии, соответствующем уровню 2 (рис. 6.17). Поскольку Е2 > Е1, атом будет стремиться перейти на уровень 1. Следовательно, из атома должна выделиться соответствующая разность энергий Е2 – Е1. Когда эта энергия освобождается в виде электромагнитной волны, процесс называют спонтанным излучением. При этом частота υ излученной волны определяется из формулы Планка:
h υ = Е2 – Е1,
где h – постоянная Планка.
Рис. 6.17. Схематическое представление процессов: а) спонтанное излучение,
б) вынужденное излучение, в) поглощение
Таким образом, спонтанное излучение характеризуется испусканием фотона с энергией при переходе атома с уровня 2 на уровень 1. Заметим, что спонтанное излучение – только один из двух возможных путей перехода атома из одного состояния в другое. Переход может происходить также и без излучения. В этом случае избыток энергии Е2 – Е1 выделяется, в какой-либо иной форме (например, разность энергии может перейти в кинетическую энергию окружающих молекул).
Имеется вероятность того, что падающая волна (рис. 6.17, а) вызовет переход атома с уровня 2 на уровень 1. При этом разность энергии Е2 – Е1 выделится в виде электромагнитной волны, которая добавится к падающей (рис. 6.17, б), такое явление называется вынужденным излучением.
Между процессами спонтанного и вынужденного излучения имеется существенное отличие. В случае спонтанного излучения атом испускает электромагнитную волну, фаза которой не имеет определенной связи с фазой волны, излученной другим атомом. Более того, испущенная волна может иметь любое направление распространения. В случае же вынужденного излучения, поскольку процесс инициируется падающей электромагнитной волной, излучение любого атома добавляется к этой волне в той же фазе. Падающая волна определяет также направление распространения испущенной волны.
Если атом первоначально находится на основном уровне 1, то атом будет оставаться на нем до тех пор, пока на него не подействует какое-либо внешнее возмущение. При воздействии на физическую среду электромагнитной волна с частотой υ (рис. 6.17, в) существует вероятность того, что атом перейдет на верхний уровень 2. Разность энергий Е2 – Е1, требующаяся для того, чтобы атом совершил переход, берется из энергии падающей электромагнитной волны. В этом случае происходит процесс поглощения.
На языке фотонов эти процессы описываются следующим образом.
1. В процессе спонтанного излучения атом, испуская фотон, переходит с уровня 2 на уровень 1.
2. В процессе вынужденного излучения падающий фотон вызывает переход 2→1, в результате чего мы получаем два фотона (падающий плюс испущенный).
3. В процессе поглощения падающий фотон просто поглощается, вызывая переход 1→2.
Как показал А. Эйнштейн, это означает, что вероятности вынужденного излучения и поглощения равны друг другу. Число атомов в единице объема, находящихся на данном энергетическом уровне, будем называть населенностью N этого уровня.
Рассмотрим в какой-либо среде два произвольных энергетических уровня 1 и 2 с соответствующими населенностями N1 и N2 (рис. 6.18). Пусть в этой среде в направлении оси 2 распространяется плоская волна с интенсивностью, соответствующей плотности потока фотонов F. Тогда, изменение плотности потока, обусловленное как процессами вынужденного излучения, так и процессами поглощения, в слое dz.
Если удастся достигнуть неравновесного состояния, для которого N2 > N1, то среда будет действовать как усилитель. Среда, в которой осуществлена инверсия населенностей, называется активной средой.
Рис.6.18. Изменение плотности потока фотонов dF при прохождении плоской электромагнитной волны через слой вещества толщиной dz
Если частота перехода υ = (Е2 – Е1)/h соответствует оптическому диапазону, то усилитель называется лазером. Практически, слово лазер широко используется не только для частот видимого диапазона, но и для частот, лежащих в инфракрасном, ультрафиолетовом и даже в рентгеновском диапазонах.
Для того чтобы усилитель превратить в генератор, необходимо ввести положительную обратную связь. В лазере обратную связь обычно получают размещением активной среды между двумя зеркалами с высоким коэффициентом отражения (например, между плоскопараллельными зеркалами, как показано на рис. 6.19).
Рис. 6.19. Схема устройства лазера
В этом случае плоская электромагнитная волна, распространяющаяся в направлении, перпендикулярном зеркалам, будет поочередно отражаться от них, усиливаясь при каждом прохождении через активную среду. Если одно из двух зеркал сделано частично прозрачным, то на выходе системы можно выделить пучок полезного излучения. В лазерах генерация возможна лишь при выполнении порогового условия, когда инверсия населенностей N2 – N1 – приближается к некоторому критическому значению, называемому критической инверсией. Как только достигнута критическая инверсия, генерация разовьется из спонтанного излучения: действительно, будут усиливаться фотоны, которые спонтанно испускаются вдоль оси резонатора. Этот механизм и лежит в основе лазерного генератора, называемого обычно просто лазером.
Наиболее важными свойствами лазерного пучка являются: а) направленность; б) монохроматичность; в) когерентность; 4) яркость.
Направленность является следствием того, что активная среда помещена в плоскопараллельный резонатор. В таком резонаторе могут поддерживаться только такие электромагнитные волны, которые распространяются вдоль оси резонатора или в очень близком к ней направлении.
Монохроматичность. Это свойство определяется двумя обстоятельствами: а) усиливаться может электромагнитная волна только с частотой υ, определяемой выражением ; б) поскольку устройство из двух зеркал образует резонатор, генерация может возникать только на резонансных частотах этого резонатора.
Когерентность. Для любой электромагнитной волны можно определить пространственную и временную когерентность, или согласованное протекание во времени нескольких колебательных или волновых процессов. Если разность фаз двух колебаний остается постоянной во времени или меняется по строго определенному закону, то колебания называются когерентными.
Если эта разность фаз остается равной нулю в любой момент времени t, то говорят, что между двумя точками имеется полная когерентность. Если такое условие выполняется для любых пар точек волнового фронта, то данная волна характеризуется полной пространственной когерентностью.
Если же это имеет место лишь для определенного интервала времени τ, такою, что 0 < τ < τ0, то волна характеризуется частичной временной когерентностью с временем когерентности τ0. На рис 6.20 в качестве примера показана электромагнитная волна с временем когерентности τ0, которая имеет вид синусоидального электрического поля со скачкообразным изменением фазы через интервалы времени τ0.
Рис. 6.20. Пример электромагнитной волны
со временем когерентности порядка τ0
Яркость В какого-либо источника электромагнитных волн определяется как мощность P излучения, испускаемого с единицы поверхности S источника в единичный телесный угол d. На рис. 6.21 показана яркость источника электромагнитного излучения, испускаемая элементом поверхности dS, в направлении ОО’ под углом θ между направлением ОО’ и нормалью n к поверхности.
Лазер даже небольшой мощности (например, несколько милливатт) имеет яркость, которая на несколько порядков превосходит яркость обычных источников. Это свойство является следствием высокой направленности лазерного пучка.
Рис. 6.21. Поверхностная яркость источника
электромагнитного излучения в точке О
Лазеры разделяются по их активной физической среде. Существуют газовые, жидкостные и твердотельные лазеры.
Газовые лазеры выделяются среди остальных типов лазеров способностью работы в широком спектральном интервале длин волн (от субмиллиметрового диапазона до ультрафиолетового). Они имеют пять разновидностей: газоразрядные, газодинамические, плазмодинамические, химические и электроионизационные.
Наибольшее применение в лазерных технологиях нашли газоразрядные лазеры на углекислом газе, наиболее эффективно работающих на волне с длиной λ = 10,6 мкм.
Активная среда лазеров на углекислом газе представляет собой смесь газов СО2 + N2 + Не. Молекулы СО2 возбуждаются ударами электронов в газовом разряде, причем для увеличения мощности добавляют молекулярный азот (N2). При этом происходит резонансная передача энергии от возбужденных молекул N2 молекулам СО2. Соотношение давлений СО2 и N2 обычно выбирается в пределах 1/1—1/5 при суммарном рабочем давлении в несколько сотен паскалей. Добавление в смесь гелия (Не) способствует более быстрому обеднению нижнего лазерного уровня и повышению выходной мощности излучения.
Лазеры на СО2 имеют коэффициент полезного действия (КПД) до 40%. На величину эффективности преобразования энергии накачки в энергию когерентного излучения влияет температура активной среды. Повышение температуры приводит к увеличению населенности нижнего лазерного уровня. Повышение мощности генерации достигается за счет эффективного охлаждения активной среды и быстрой прокачки смеси газов через рабочую полость.
На рис. 6.22 представлена схема устройства СО2-лазера с поперечным возбуждением.
Рис. 6.22. Схема устройства СО2-лазера с поперечной прокачкой
В случае лазеров с поперечной прокачкой не возникает ограничения по давлению сверху. Однако поднять давление выше 50-100 мм ртутного столба нелегко, поскольку увеличение давления требует соответствующего повышения напряжения разряда. Данное осложнение можно преодолеть, если пустить разрядный ток в направлении, перпендикулярном оси резонатора как показано на рис. 6.23.
В твердотельных лазерах активными центрами являются ионы Cr3+ или ионы редкоземельных элементов, введенные в кристаллическую физическую среду. В качестве рабочего вещества используют твердые тела типа синтетического рубина.
Синтетический рубин представляет собой искусственно выращенный кристалл оксида алюминия А12О3, в который вводятся и равномерно распределяются по объему атомы хрома Сr в количестве 0,05% от массы кристалла. Примесь хрома придает рубину характерный розово-красный цвет. Атомы хрома в кристалле рубина являются оптически активными центрами и генерируют когерентное излучение в видимой части спектра с длиной волны λ=0,6943 мкм (красный цвет).
Рис. 6.23. Схема устройства СО2 – лазера с поперечным возбуждением
Твердотельные полупроводниковые лазеры подразделяют на инжекционные, лазеры с электронной или оптической накачкой. Они обладают: а) миниатюрностью, обусловленной очень большим усилением; б) большим КПД; в) возможностью широкополосной внутренней модуляции излучения по цепи накачки; г) перестройкой длины волны излучения в широком диапазоне.
В соответствии с методами создания инверсии населенностей уровней, полупроводниковые лазеры подразделяют на инжекционные, лазеры с электронной или оптической накачкой.
Наиболее распространены полупроводниковые инжекционные лазеры. В них генерация когерентного излучения происходит при вынужденной рекомбинации избыточных носителей заряда в областях, прилегающих к полупроводниковому переходу с энергией кванта, близкой к ширине запрещенной зоны.
Если температура полупроводника такова, что заштрихованная область V соответствует полностью заполненным энергетическим состояниям (рис. 6.24, а), то при попадании электронов Eg из валентной зоны Fv в зону проводимости Fc в течение интервала времени ~10-13 с электроны «переместятся» на ее самый нижний уровень. Это означает, что между валентной зоной Fv и зоной проводимости Fc возникнет инверсия населенностей hv (рис. 6.24, б). Поскольку электроны стремятся перейти из зоны С в зону V, то при помещении такого полупроводника в соответствующий резонатор, можно получить генерацию лазерного излучения.
В качестве полупроводникового инжекционного лазера наибольшее распространение получили диоды на кристаллах арсенида галлия (GаАs). Применяют полупроводниковые лазеры для оптической накачки твердотельных лазеров.
Рис. 6.24. Принцип действия полупроводникового лазера
В технологиях машиностроения лазеры применяют для следующих видов обработки материалов: а) лазерная резка; б) лазерная закалка; в) лазерное легирование; г) лазерная сварка. Оборудование для выполнения этих операций может быть различно как по составу, так и по назначению. По составу лазерное технологическое оборудование может быть технологическим лазером (ТЛ), лазерной технологической установкой (ЛТУ) и лазерным технологическим комплексом (ЛТК).
Технологический лазер – это источник лазерного излучения, соответствующий заданным техническим требованиям с необходимым комплектом запасных частей. ТЛ является основным компонентом лазерного технологического оборудования.
Лазерная технологическая установка – это технологический лазер с внешним оптическим трактом, комплектом внешней оптики и соответствующим числом запасных частей. В некоторых случаях в ЛТУ имеется манипулятор изделий, работа которого не связана с работой технологического лазера.
ЛТУ предназначены в основном для создания специализированных комплексов на предприятиях заказчика. В настоящее время технологические лазеры поставляются только в комплекте лазерных технологических установок.
Лазерный технологический комплекс – это ЛТУ, снабженная манипулятором изделия или оптики, вспомогательное технологическое оборудование и система управления для проведения технологических операций. Все части ЛТК функционально связаны между собой для выполнения технологического процесса. Практически только при наличии ЛТК можно успешно выполнять те или иные технологические операции в достаточном объеме.
В случае применения автоматизированного манипулятора изделия или оптики и наличия соответствующих систем связи между системами управления манипулятором и лазером комплекс считается автоматизированным технологическим комплексом (АЛТК).
По назначению и способности выполнять то или иное количество операций всю гамму лазерного технологического оборудования подразделяют на универсальное, специализированное и специальное. Соответственно, оно используется в единичном, серийном и массовом производстве.
Специализированные ЛТК создаются на основе одного отработанного технологического процесса при обработке одной детали и предназначен для предприятий, выпускающих ограниченную номенклатуру изделий крупными сериями. При замене технологического процесса большая часть такого оборудования, в частности манипулятор изделия или оптики, подлежат замене.
Специальные ЛТК создаются для решения специальных единичных крупных задач разового исполнения.
Универсальные ЛТК и АЛТК являются общепромышленным оборудованием и предназначены для выполнения целого ряда операций или для обработки нескольких деталей. Обычно универсальные ЛТК используются в серийном и мелкосерийном производстве, и при смене технологического процесса они сохраняют свой состав и основные функции.
Лазерная резка металлов позволяет относительно просто, в автоматическом режиме, изготавливать сложные детали из листовых заготовок без образования стружки при их минимальных тепловых деформациях. Лазерная резка экономически выгодна и технически целесообразна из-за гибкости процессами исключения подготовительных работ (конструкторских и подготовки производства), присущих традиционной технологии получения подобных деталей – холодной листовой штамповке. Скорость резки обратно пропорциональна толщине материала и прямо пропорциональна мощности падающего лазерного излучения при величинах, превышающих определенный порог.
Для реализации технологии лазерной резки в настоящее время созданы различные лазерно-технологические системы, оснащенные лазерными излучателями (газовыми и твердотельными), работающими как в непрерывном, так и в импульсных режимах.
Преимущества лазерной резки перед традиционными способами заключается в следующем:
– отсутствие механического контакта с обрабатываемым объектом;
– возможность концентрирования энергии луча в пятно размером до десятых долей миллиметра;
– транспортировка излучения на большие расстояния;
– возможность автоматизации процесса резки;
– возможность быстрой перестройки производства на другие типоразмеры.
ЛТК с манипуляторами изделия со сложным перемещением обычно создаются на базе двух координатных столов, на которые могут устанавливаться различные ротационные системы. Могут также применяться в качестве манипуляторов промышленные роботы.
По характеру манипулятора оптики можно выделить системы с перемещением оптических элементов по линейной и вращательной траектории. ЛТК с манипуляторами оптики со сложной траекторией получили название «лазер-робот».
ЛТК смешанного типа включают перемещение оптики и детали как по линейным, так и по сложным траекториям.
Имеются многоцелевые ЛТК, которые сконструированы таким образом, что могут после некоторой переналадки выполнять несколько операций, например резку, сварку и закалку. В том случае, когда переналадка при переходе с одной операции на другую происходит автоматически, универсальный комплекс имеет название «лазерный обрабатывающий центр» (ЛОЦ). Сейчас распространение получили ЛОЦ на базе твердотельных лазеров.
По форме обрабатываемых изделий ЛТК предназначаются для обработки плоских деталей (резка и сварка листовых материалов) и для обработки тел вращения (резка и сварка труб, закалка валов).
Разновидностью ЛТК для обработки плоских деталей являются комплексы для лазерной резки листовых материалов, в которых стол является неподвижным, а листы перемещаются по столу по двум координатам с помощью специальных захватных устройств. Для перемещения листа обычно используется электропривод с двигателями постоянного тока в сочетании с шариковинтовыми парами.
На рис. 6.25 приведена схема ЛТК, которая включает СО2-лазер мощностью 600 Вт с апертурой пучка 12 мм и расходимостью 2 мрад. Перемещение по осям X и Y 1250и1000 мм, скорость обработки до 24 м/мин, точность вырезки деталей 0,2 мм, максимальная масса листа 60 кг.
Расход гелия составляет 50…100 л/ч, азота 10…20 л/ч, СО2 5…10 л/ч, режущего газа 1,5…2 м3/ч, сжатого газа 1 м3/ч, воды 1000 л/ч. Полная масса АЛТК 5,2 т, занимаемая площадь 30 м2. Потребляемая мощность 15 кВт.
Рис. 6.25. Схема АЛТК для лазерной резки листовых материалов: 1 – частично отражающее зеркало; 2 – резонатор; 3 – полностью отражающее зеркало; 4 – выходящий луч; 5 – отклоняющее зеркало; 6 – фокусирующая линза; 7 – узел лазерной резки; 8 – отсос газа; 9 – отвод жидкости; 10 – выход деталей; 11 – сепаратор; 12 – кассета;
13 – зажим заготовки; 14 – система перемещения
Оптический тракт АЛТК показан на рис. 6.26. Для поддержания постоянного расстояния от сопла до поверхности разрезаемого материала оптическая головка перемещается по оси Z в пределах до 600 мм. Поддержание постоянного зазора осуществляется автоматически с помощью емкостного датчика, подключенного к системе обратной связи. Вследствие этого можно резать металлические листы со значительной волнистостью. Все оптические элементы имеют водяное охлаждение.
Рис. 6.26. Схема внешнего оптического тракта АЛТК: 1 – отклоняющие зеркала; 2 – лазерный луч; 3 – оптическая головка; 4 – подача газа;
5 – фокусирующая линза; 6 – емкостный датчик; 7 – обрабатываемый материал; 8 – рабочий стол
Комбинированные системы включают в свой состав кроме ТЛ другие машины и инструменты. Наибольшее распространение получили АЛТК для резки, в которых кроме лазера имеется револьверный режущий или вырубной пресс небольшой мощности. Такие АЛТК получили название лазер-пресс.
По конструкции манипулятора эти АЛТК относятся к двухкоординатным системам, поскольку листы при обработке перемещаются с помощью специальных захватных устройств по двум координатам. Комбинация лазера и пресса в одном комплексе существенно расширяет возможность каждого из этих инструментов. При обработке листовых материалов это дает эффект существенного повышения производительности.
Например, лазер-пресс в листе длиной 1500 мм вырубает за 5 секунд 14 отверстий диаметром 10…20 мм, 5 овальных пазов с максимальным линейным размером 100 мм высекает за 20 секунд и вырезает фасонный контур по длине листа за 30 секунд. В результате один лист обрабатывается за 65 секунд, тогда как на листоштамповочном прессе только высечка фасонного контура выполняется за 80 секунд. Кроме того, при резке на лазере-прессе сокращается время на загрузку и разгрузку, так как все операции осуществляют на одном станке.
В АЛТК «лазер-пресс» (рис. 6.27) оптическая головка и зажим вырубного пресса размещены в одной станине. Отрицательное влияние динамики операций вырубки на юстировку оптического тракта лазера уменьшено за счет того, что во время штамповки оптическая система поднимается на воздушной подушке.
Рис. 6.27. Схема АЛТК «лазер-пресс»
Обрабатываемый лист зажимается в координатной направляющей с помощью гидравлических захватных устройств. Для обеспечения постоянства расстояния от фокусирующей системы до плоскости реза резак плотно прижимается к листу, причем на прижимаемой плоскости резака имеются шарики для обеспечения движения листа; такие же шарики вмонтированы в поверхность стола. Как и в АЛТК 2-координатного типа (см. рис. 6.25), в станине стола имеются сепаратор и система отсоса отработанных газов, что также способствует получению высокого качества реза.
Для штамповки АЛТК (рис. 6.27) оборудован гидравлическим устройством. Инструменты для вырубки (штампы) используют при изготовлении сквозных отверстий простой формы с небольшим диаметром. Для листового материала, плохо обрабатываемого лазером (например, из алюминия и меди) предусмотрены штампы для вибрационной высечки. Кроме того, выполняются операции вытяжки и отбортовки.
Комплект инструментов для штамповки и вибрационной высечки состоит из штампа, матрицы и съемника; они устанавливаются оператором в магазине за 15 с. Установка инструмента в захват головки пресса производится автоматически по команде от ЧПУ. Магазин имеет 15 позиций с максимальным диаметром инструмента 76 мм. Пресс работает от привода эксцентрикового типа.
Лазерные гибкие производственные системы (ГПС), в отличие от АЛТК, включают в свой состав автоматизированный склад листового материала, робот для загрузки и выгрузки листа, АЛТК с набором сменных оптических головок, датчиков и вспомогательных технологических приспособлений и центральную систему управления.
ГПС (рис. 6.28) включает в свой состав СО2-лазеры мощностью 5 и 10 кВт, а также твердотельный полупроводниковый инжекционный ИАГ-лазер мощностью 300 Вт.
Рис. 6.28. Схема ГПС с 4 лазерными позициями.
Лазерный обрабатывающий модуль (см. рис. 6.28) имеет три рабочие позиции. На рабочей позиции с CO2 – лазером мощностью 10 кВт установлены две обрабатывающие головки для резки и сварки листов толщиной до 20 мм.
На рабочей позиции с лазерным осциллятором на CO2 (см. рис. 6.28) мощностью 10 кВт имеется одна обрабатывающая головка для лазерной закалки торцевых поверхностей валов и шестерен, внутренних поверхностей в валах, поверхностей зубьев шестерен. Головка оснащена сканером, колеблющим луч с частотой 120 Гц. На рабочей позиции ИАГ – лазера (см. рис. 6.28) имеются две обрабатывающие головки: одна предназначена для размягчения металла при токарной обработке, а вторая – для снятия заусенцев с зубьев.
Лазерная закалка характеризуется «жестким» термическим циклом и значительным перегревом. Таким образом, сущность закалки состоит в бездиффузионном превращении при быстром охлаждении гранецентрированной кубической решетки аустенита в искаженную объемно-центрированную кубическую решетку мартенсита.
Закалка предполагает не только быстрый нагрев зоны обработки излучением лазера выше температуры фазового перехода, но и его охлаждение со скоростью больше критической. Самоохлаждение при лазерной закалке происходит за счет передачи тепла от нагретого поверхностного слоя вглубь детали. Также используются охлаждающие среды. Если максимальная температура в области, нагреваемой лазерным лучом, не превышает температуры плавления металла, то все фазовые переходы происходят в твердом состоянии и качество механической обработки поверхности остается прежним.
Схема лазерной закалки со сканированием представлена на рис. 6.29. Оптимальность режима термообработки со сканированием характеризуется производительностью процесса.
Режим закалки со сканированием должен обеспечивать необходимую глубину упрочнения слоя при отсутствии на поверхности локальных оплавленных участков.
Чаще всего лазерную закалку применяют для деталей, работающих в парах трения, так как в результате этой закалки значительно повышается износостойкость и улучшаются поверхностные свойства деталей. Наилучшие результаты по износостойкости имеют поверхности с сеткой закаленных лазером дорожек, занимающей 20…25% всей площади для перлитных чугунов и 5…10 % для ферритных чугунов.
Рис. 6.29. Схема лазерной закалки со сканированием: 1 – лазерный пучок, 2 – фокусирующая система, 3 – сканатор с колеблющимся по некоторому закону зеркалом, 4 – обрабатываемый материал, 5 – сечение закаленной дорожки, Р0 – мощность лазерного излучения, r – радиус лазерного пучка на поверхности материала, σ – площадь сечения лазерного пучка, d – амплитуда сканирования, S – площадь зоны нагрева, zзак – глубина зоны закалки, v – скорость перемещения обрабатываемого материала относительно зоны нагрева
Лазерное легирование принципиально отличается от закалки из жидкого состояния тем, что изменяется химический состав упрочненного слоя. На деталях, выполненных из простых конструктивных материалов можно создавать локальные области с высокими служебными характеристиками, вместо того, чтобы эти детали целиком изготовлять из дефицитных сплавов.
Используя лазерное легирование, можно внести дефицитные компоненты в тонкий слой на локальном участке изделия, повысив при этом износостойкость, коррозионную стойкость, контактную выносливость и другие служебные характеристики. Схема процесса лазерного легирования показана на рис. 6.30.
Рис. 6.30. Схема процесса лазерного легирования: 1 – образец, движущийся со скоростью v, 2 – легированная дорожка, 3 – ванна расплава, 4 – лазерный пучок, 5 – фокусирующая система, 6- защитный газ, 7 – легирующая обмазка
Образец с тонким слоем легирующей обмазки при движении под лазерным лучом локально оплавляется, легирующие компоненты переходят в объем жидкой ванны металла, которая затем кристаллизуется. При этом происходят взаимосвязанные процессы тепломассопереноса и микрометаллургические процессы.
В качестве легирующих добавок используются три основные группы веществ: неметаллы, металлы и сплавы, карбиды. Легирующие вещества поступают в зону легирования, как непосредственно в процессе лазерной обработки в виде вдуваемого порошка или подаваемой проволоки, так и предварительно наносятся на поверхность металла (гальваническим осаждением, плазменно-вакуумным напылением), а затем расплавляются лазерным лучом.
Легирование малоуглеродистых сталей углеродом приводит к формированию мелкозернистой структуры из мартенсита и остаточного аустенита (при этом микротвердость достигает 9000 МПа), а азотом – к азотистому мартенситу, остаточному аустениту и нитридам железа. Небольшое содержание бора увеличивает микротвердость до (6…12).103 МПа.
При легировании чистыми металлами (Со, Сr, Ni, Мn, Мо, W, Тi, V и т.д.) происходит формирование пересыщенных твердых растворов и образование интерметаллидов, приводящих также к повышению в несколько раз микротвердости в зонах легирования.
Лазерная сварка является методом сварки плавлением, т.е. соединяющиеся детали сплавляются под воздействием лазерного излучения. Особенностями являются высокая плотность мощности, а при импульсной сварке – быстрое охлаждение с коротким временем воздействия.
ТЛ применяются для точечной и шовной сварки. Шовная сварка может происходить непрерывно или в режиме точечной сварки внахлестку.
Сваривание деталей происходит при значительно меньших плотностях мощности, чем резка. Это объясняется тем, что при сварке необходимы только разогрев и плавление материала, то есть необходимы плотности мощности, еще недостаточные для интенсивного испарения (105 -106 Вт/см2), при длительности импульса около 10-3-10-4 сек.
ТЛ для сварки способны сваривать разнородные металлы, производить минимальное тепловое воздействие за счет малого размера лазерного пятна, а также сваривать тонкие проволоки диаметром менее 20 мкм.
studfiles.net