Основные части токарного станка: Устройство токарного станка
alexxlab | 04.04.1989 | 0 | Разное
Описание функций и назначения основных узлов токарного токарно фрезерного центра. Референция в Спб
Токарные обрабатывающие центры заняли прочное место на современном металлообрабатывающем производстве. Сегодня на практике доказана экономическая целесообразность их использования при обработке деталей сложной конструкции с высокой точностью и заготовок серийными партиями. Работа на многофункциональных токарно-фрезерных центрах требует меньшего количества операций перестановки заготовки, соответственно менее сложной оснастки, меньше ручных настроек, меньше обслуживания благодаря высокой степени автоматизации и технологической оснащенности.
Отличия от классического токарного с ЧПУ
(может быть 1 пункт или сразу несколько)
– наличие управляемого поворота патрона
– гидравлический патрон и пиноль, стружкосборник и телескопическая защита направляющих в базовом оснащении
– наличие приводного инструмента – через осевой или радиальный блок возможно выполнение операций фрезерования
В связи с особенностями эксплуатации, к токарным обрабатывающим центрам предъявляется ряд специфических требований, несоблюдение которых значительно снижает их эффективность.
Точность. Вся конструкция станка и каждый узел в отдельности должны иметь повышенную размерную точность. Погрешности базирования и закрепления, возникающие при установке заготовок в приспособлениях, должны быть сведены к минимуму.
Жесткость. Для возможности использования полной мощности станка на черновых операциях узлы станка должны иметь повышенную жесткость. В то же время, их конструкция должна обеспечить получение высокой точности на чистовых операциях.
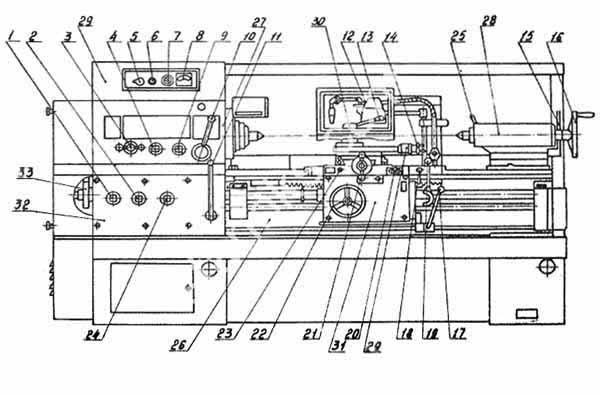
Многофункциональность.
Универсальность, переналаживаемость приспособлений. Станки с ЧПУ, в отличие от станков-автоматов, обладают высокой гибкостью, так как переналадка их может заключаться лишь в смене УП и переналадку оснастки – приспособлений и инструмента. Поэтому, для сокращения простоя станков приспособления должны обеспечивать возможность их быстрой переналадки или смены.
На примере токарного обрабатывающего центра собственного производства ТС1720Ф4 рассмотрим особенности конструкции узлов станка и конструкции в целом.
1 Станина
2 Салазки
3 Суппорт
4 Передняя бабка
5 Задняя бабка
6 Шпиндель
7 Привод продольной подачи
8 Привод поперечной подачи
9 Бак СОЖ
10 Транспортёр для удаления стружки
11 Кабинет
12 Шкаф с электроаппаратурой
13 Головка револьверная 12-ти позиционная с приводным инструментом
14 Пульт управления с системой ЧПУ
16 Система подачи и сбора СОЖ
17 Гидравлическая система
18 Тележка для стружки
Жесткость ТС1720Ф4 и точность обработки обеспечивается продуманной конструкцией и качеством изготовления узлов станка. Станина, отлитая из высокопрочного чугуна с высокими показателями демпфирования вибрации, задает общую жесткость конструкции. Угол ее наклона в 300 позволяет эффективно использовать пространство рабочей зоны: разместить револьверную голову большей емкости, увеличить диаметр обрабатываемой заготовки, обеспечить свободное стружкоотведение и доступ к инструменту и заготовке. Точность изготовления детали напрямую зависит от перемещения подвижных узлов станка. В токарно-фрезерном центре ТС1720Ф4 применены высокоскоростные направляющие качения повышенной жесткости и ШВП от ведущего мирового производителя HIWIN. Направляющие данного типа за счет применения роликов обеспечивают минимальное сопротивление движению исполнительного механизма, достигая максимальной скорости перемещения 20000 мм/мин, в то время как шарико-винтовые пары, благодаря применению гаек с предварительным натягом и большему диаметру ходового винта, отличаются высокими точностью останова, износостойкостью и жесткостью.
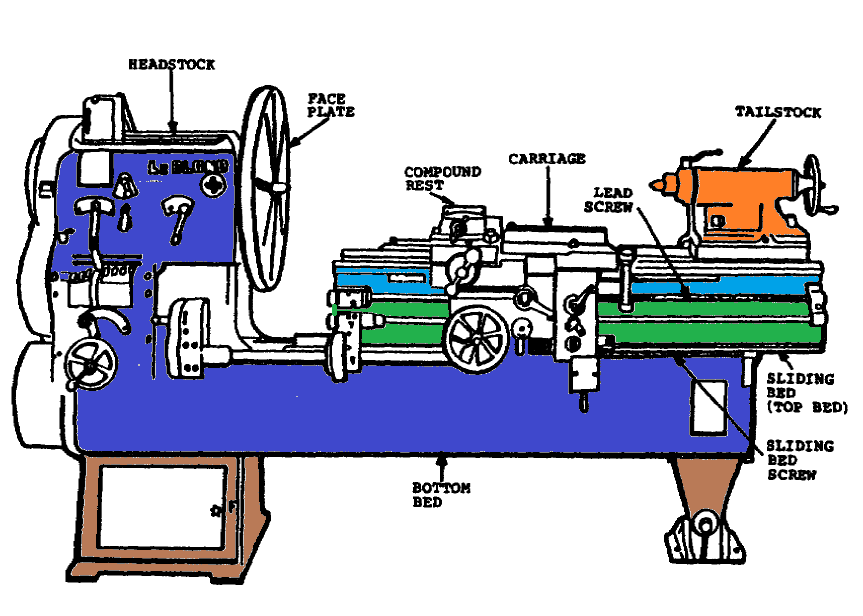
Значительная часть (70-75 %) обрабатываемых на токарных станках видов деталей (фланцы, валы, стаканы) требуют отличных от токарных методов обработки, к которым относятся сверление, резьбонарезание метчиком, фрезерование боковых поверхностей и канавок. Практическая реализация данной задачи привела к созданию управляемого ЧПУ привода шпинделя и револьверной головки с приводными позициями.
В нашем токарном центре непосредственно на шпинделе устанавливается датчик контроля позиции. Во время работы он с дискретностью 0,001о определяет угол поворота детали и скорость вращения. В сочетании с эффективным гидравлическим тормозом шпинделя он позволяет выполнять обработку по оси С. Контролируемая комбинация перемещений по осям Х и С, при применении приводного инструмента, позволяют выполнять высококачественную контурную фрезерную обработку.
Инструментальный магазин – револьверная головка – является еще одним рабочим органом станка, к которому предъявляются повышенные требования к прочности, жесткости и точности позиционирования, так как она воспринимает силы резания.

ТС1720Ф4 оснащен 12-ти позиционной револьверной головкой с возможностью применения приводного инструмента в радиальном и аксиальном направлении. Система крепления инструментальных блоков – VDI30. Она отвечает требованиям быстрой смены инструмента и надежного крепления. Индексация револьверной головки по кратчайшему пути и гидравлический привод зажима максимально сокращают время смены инструмента в процессе работы.
При фрезеровании и нарезании резьбы гребенкой, при точении многогранников или фрезеровании винтовых канавок применяется синхронизация вращения инструмента и заготовки. Также следует отметить, что для автоматизированной непрерывной работы токарного центра целесообразна установка систем управления и контроля ресурса режущего инструмента, позволяющая автоматически, например, перед обработкой следующей детали, не дожидаясь критического износа инструмента, заменять его дубликатом из другой позиции револьверной головки и контроля точности полученной заготовки.

Предыдущая статья
Следующая статья
Получить консультацию
по инструменту, методам обработки, режимам или подобрать необходимое оборудование можно связавшись с нашими менеджерами или отделом САПР
Также Вы можете подобрать и приобрести режущий инструмент и оснастку к станку, производства Тайваня, Израиля
Отправляя заявку, вы соглашаетесь с политикой конфиденциальности
Проработать технологию, подобрать станок и инструмент
Заглавная страница
КАТЕГОРИИ: Археология ТОП 10 на сайте Приготовление дезинфицирующих растворов различной концентрации Техника нижней прямой подачи мяча. Франко-прусская война (причины и последствия) Организация работы процедурного кабинета Смысловое и механическое запоминание, их место и роль в усвоении знаний Коммуникативные барьеры и пути их преодоления Обработка изделий медицинского назначения многократного применения Образцы текста публицистического стиля Четыре типа изменения баланса Задачи с ответами для Всероссийской олимпиады по праву Мы поможем в написании ваших работ! ЗНАЕТЕ ЛИ ВЫ? Приготовление дезинфицирующих растворов различной концентрации Практические работы по географии для 6 класса Организация работы процедурного кабинета Изменения в неживой природе осенью Уборка процедурного кабинета Сольфеджио. Все правила по сольфеджио Балочные системы. |
⇐ ПредыдущаяСтр 13 из 16Следующая ⇒ Токарные станки предназначены для получения из заготовок различных деталей, имеющих форму тел вращения. Если на станке имеется устройство для нарезания резьбы, то такой станок называется токарно-винторезным. На рис. 3 изображен общий вид то карновинторезного станка модели 1К62, указаны основные части, узлы и органы управления . Станина 4 массивное чугунное основание, на котором смонтированы все основные узлы станка. Верхняя часть станины имеет две плоские и две призматические направляющие, по которым могут перемещаться подвижные узлы стайка. Станина установлена на двух тумбах. Передняя бабка I .-чугунная коробка, внутри которой расположен главный рабочий орган станка шпиндель, представляющий собой полый вал, на правом конце которого крепятся приспособления, зажимающие заготовку, например патрон. Шпиндель получает вращение от расположенного в левой тумбе электродвигателя через клиноременную передачу и систему зубчатых колес и муфт, размещенных внутри передней бабки. Суппорт 6 устройство для закрепления резца, обеспечения движения подачи, т. е. перемещения резца в различных направлениях. Движения подачи могут осуществляться вручную и механически. Механическое движение подачи суппорт получает от ходового винта и ходового вала. Фартук 5 система механизмов, преобразующих вращательное движение ходового винта и ходового вала в прямолинейное движение суппорта. Коробка подач 3 механизм, передающий вращение ходовому винту и ходовому валу и изменяющий величину подачи. Вращательное движение в коробку подач передается от шпинделя с помощью реверсивного механизма и гитары со сменными зубчатыми колесами. Гитара 2 предназначается для настройки станка на требуемую подачу подбором соответствующих сменных зубчатых колес. Задняя бабка 7 предназначена для поддерживания правого конца длинных заготовок в процессе обработки, а также закрепления сверл, зенкеров и разверток.
Фрезерование поверхностей заключается в снятии стружки вращающимися многолезвийными инструментами — фрезами, режущие кромки зубьев которых находятся в прерывистом контакте с обрабатываемым материалом. Различают следующие основные виды фрезерования: 1) осевое цилиндрическое фрезерование цилиндрическими, дисковыми и концевыми фрезами; 2) торцовое фрезерование торцовыми, дисковыми и концевыми фрезами; 3) двустороннее фрезерование дисковыми, концевыми и торцовыми фрезами; 4) трехстороннее фрезерование концевыми и шпоночными фрезами; 5) комбинированное фрезерование наборами фрез; 6) фасонное фрезерование фасонными цилиндрическими и концевыми фрезами. Фрезерование применяют для обработки поверхностей различных форм (плоскостей, фасонных поверхностей и др.). Чаще всего фрезерованием обрабатывают плоскости. Для этой цели применяют цилиндрические или торцовые фрезы. Первые бывают с прямыми (рис. 109, а) или с винтовыми (рис. При применении фрез последнего вида фрезерование протекает более плавно и спокойно вследствие постепенного врезания зубьев в металл. Торцовые фрезы подразделяются на хвостовые и насадные (рис. 109, в). Последние при их значительных размерах делают с вставными зубьями (фрезерные головки, см. рис. 109, г), что позволяет расходовать меньше дорогих инструментальных сталей и заменять, в случае надобности, отдельные зубья фрезы, корпус которой делается из относительно дешевой стали (например, стали 45). Для фрезерования пазов применяют дисковые, а также концевые цилиндрические фрезы. Дисковые фрезы подразделяются на следующие виды: двусторонние, трехсторонние и пазовые (рис. 109, в—ж). Первые имеют зубья на периферии и на одном из торцов; вторые, кроме того, и на втором торце. Регулируемые трехсторонние фрезы состоят из двух половин, между которыми помещают прокладки для регулировки толщины фрезы, уменьшающейся после ее заточки. Пазовые фрезы имеют зубья только на периферии. Для фрезерования углублений, канавок, фасонных поверхностей применяют угловые фасонные фрезы, которые могут быть насадными и хвостовыми (рис. 109, е). Существуют также особые фрезы для нарезания зубчатых профилей, нарезания резьб и др. (рис. 109, ж, з, и). Для изготовления фрез применяют быстрорежущие стали (Р18, Р9), сталь 9ХС, а также оснащают фрезы пластинками из твердых сплавов.
Геометрическая форма каждого зуба фрезы в принципе сходна с геометрической формой токарного резца, однако условия работы зубьев фрез хуже, чем токарных резцов, вследствие прерывистого контакта зубьев фрезы с обрабатываемой поверхностью. Резание металла при фрезеровании протекает менее спокойно, чем при постоянном контакте режущей кромки резца с обрабатываемой поверхностью, что имеет место при точении. Геометрические параметры зуба фрезы показаны на рис. 110; здесь передний угол γ = 5 ÷ 15°, задний угол α = 10 ÷ 30° и угол заострения β. У фрез, оснащенных пластинками из твердых сплавов, часто передние углы имеют отрицательное значение, а угол заострения β получается до 90°. Чем больше этот угол, тем прочнее зуб фрезы и лучше условия теплоотвода в тело инструмента. Скорость резания v при фрезеровании равна окружной скорости вращения инструмента. Глубина резания t — это слой металла, снимаемый за один проход (рис. 111). Рис. 111. Схема фрезерования Шириной фрезерования В называют длину части поверхности, находящуюся в контакте с режущими элементами фрезы и измеряемую в направлении, перпендикулярном подаче. Подача — это перемещение обрабатываемой заготовки относительно инструмента или, наоборот, фрезы относительно заготовки. sмин=sоб * n =sz * z *n мм/мин, гдеz — число зубьев фрезы; n — число оборотов фрезы в минуту; n = (1000*v) / π*d об/мин; гдеv — скорость резания в м/мин; d— диаметр фрезы в мм. Скорость резания зависит от обрабатываемого материала, условий обработки, глубины резания, подачи, стойкости фрезы и т. д. и назначается по нормативам режима резания или подсчитывается по эмпирическим формулам.
При фрезеровании инструментами с периферическими зубьями стружка имеет вид запятой (рис. 112). Ее толщина не равномерна и изменяется по мере поворота зуба относительно обрабатываемой поверхности. Рис. 113. Попутное (а) и встречное (б) фрезерование Различают попутное (по подаче) и встречное (против подачи) фрезерование. В первом случае (рис. Чаще применяют второй способ, при котором толщина стружки постепенно увеличивается и достигает наибольшего значения при выходе зуба фрезы из контакта с обрабатываемой поверхностью. Площадь поперечного сечения стружки в каждый момент резания — величина переменная. Силы резания, действующие на зубья фрезы, имеют различные направления и разную величину в зависимости от направления подачи по отношению к направлению вращения фрезы, т. е. от способа фрезерования (встречное или попутное), а также от рода фрезерования (торцовыми фрезами или фрезами с периферическими зубьями). При встречном фрезеровании цилиндрическими фрезами сила резания Р, действующая на каждый зуб фрезы, может быть разложена на две составляющих: касательную к фрезеPz и радиальную Рy, направленную к центру фрезы. Касательная сила создает крутящий момент M = (Pz* d )/2 кГмм, где d — диаметр фрезы в мм.
Сверление Сверление — вид механической обработки материалов резанием, при котором с помощью специального вращающегося режущего инструмента (сверла) получают отверстия различного диаметра и глубины, или многогранные отверстия различного сечения и глубины. Назначение сверления Сверление – необходимая операция для получения отверстий в различных материалах при их обработке, целью которой является:
Сверление цилиндрических отверстий, а также сверление многогранных (треугольных, квадратных, пяти- и шестигранных, овальных) отверстий выполняют с помощью специальных режущих инструментов — свёрл.
Операции сверления производятся на следующих станках:
И на ручном оборудовании:
Для облегчения процессов резания материалов применяют следующие меры:
Виды сверления [править]
Охлаждение при сверлении [править] Большой проблемой при сверлении является сильный разогрев сверла и обрабатываемого материала из-за трения. В месте сверления температура может достигать нескольких сотен градусов Цельсия. При сильном разогреве материал может начать гореть или плавиться. Многие стали при сильном разогреве теряют твердость, в результате режущие кромки стальных свёрл быстрее изнашиваются, из-за чего трение только усиливается, что в итоге приводит к быстрому выходу свёрл из строя и резкому снижению эффективности сверления. Аналогично, при использовании твердосплавного сверла или сверла со сменными пластинами, твердый сплав при перегреве теряет твердость, и начинается пластическая деформация режущей кромки, что является нежелательным типом износа. Для борьбы с разогревом применяют охлаждение с помощью охлаждающих эмульсий или смазочно-охлаждающих жидкостей (СОЖ). При сверлении ручным инструментом сверление время от времени прерывают и окунают сверло в емкость с жидкостью. 18) Шлифовáние — механическая или ручная операция по обработке твёрдого материала (металл, стекло, гранит, алмаз и др. Типы шлифовального инструмента [править]
Хонингование — вид абразивной обработки материалов с применением хонинговальных головок (хонов). В основном применяется для обработки внутренних цилиндрических поверхностей путём совмещения вращательного и возвратно-поступательного движения хона с закреплёнными на нём раздвижными абразивными брусками с обильным орошением обрабатываемой поверхности смазочно-охлаждающей жидкостью. Один из видов чистовых и отделочных обработок резанием. Позволяет получить отверстие с отклонением от цилиндричности до 5 мкм и шероховатостью поверхности Ra=0,63÷0,04. Хонингование наружных поверхностей осуществляется на специализированных станках (горизонтально-хонинговальных) или модернизированных (шлифовальных, горизонтально-расточных), производительность при этом по сравнению с суперфинишированием в 2—4 раза выше вследствие бо́льшего количества брусков и бо́льших давлений. Области применения хонингования [править] Обработка отверстий в различных деталях в том числе в деталях двигателя (отверстий блоков цилиндров, гильз цилиндров, отверстий кривошипной и поршневой головок шатунов, отверстий шестерен) и т. д. Хонинговочная сетка является побочным эффектом этого высокоточного метода шлифования. По её характеру можно судить о правильности обработки, точности соблюдения технологии. Особенно это актуально при работе ручным инструментом. Она также способствует лучшему смазыванию при работе пары трения . При обработке хонингованием обеспечивается стабильное получение точных отверстий и требуемых параметров шероховатости обработанной поверхности. Инструмент для хонингования При хонинговании используют бруски изготовленный методом прессования на керамической и бакелитовой основе. Абразивным материалом являются белый электрокорунд марок 23А, 24А, 25А и зеленый карбид кремния марок 63С, 64С, а также в качестве абразива используется алмаз и эльбор. 1 2 3 1 а) в) 3 1 б) г)
25)
Ковка — это высокотемпературная обработка различных металлов (железо, медь и её сплавы, титан, алюминий и его сплавы), нагретых до ковочной температуры. Для каждого металла существует своя ковочная температура, зависящая от физических (температура плавления, кристаллизация) и химических (наличия легирующих элементов) свойств. Для железа температурный интервал 1250–800 °С, для меди 1000–650 °С, для титана 1600—900 °С, для алюминиевых сплавов 480–400 °С. Различают:
Изделия и полуфабрикаты, получаемые ковкой, называют поковкой. При ковке в штампах металл ограничен со всех сторон стенками штампа. При деформации он приобретает форму этой полости (см. При свободной ковке (ручной и машинной) металл не ограничен совсем или же ограничен с одной стороны. При ручной ковке непосредственно на металл или на инструмент воздействуют кувалдой или молотом. Свободную ковку применяют также для улучшения качества и структуры металла. При проковке металл упрочняется, завариваются так называемые несплошности и размельчаются крупные кристаллы, в результате чего структура становится мелкозернистой, приобретает волокнистое строение. Машинную ковку выполняют на специальном оборудовании — молотах с массой падающих частей от 40 до 5000 кг или гидравлических прессах, развивающих усилия 2–200 МН (200–20000 тс), а также на ковочных машинах. Изготовляют поковки массой 100 т и более. Для манипулирования тяжёлыми заготовками при ковке используют подъёмные краны грузоподъёмностью до 350 т, кантователи и специальные манипуляторы. Ковка является одним из экономичных способов получения заготовок деталей. При ковке используют набор кузнечного инструмента, с помощью которого заготовкам придают требуемую форму и размеры. Основные операции ковки [править]
Ковка может быть горячей и холодной. Горячая ковка создаётся методом нагревания металла и придания ему нужной формы. В то же время холодная ковка создается без нагрева металла. При помощи сгиба либо вручную, либо на специальном станке, также в создании узора участвует болгарка (обрезание концов квадратного либо круглого прута), и сварочный аппарат, который собирает детали узора вместе. Область применения ковки — мелкосерийное и единичное производство. Достоинства ковки:
Недостатки ковки:
Горячая объёмная штамповка — это вид обработки металлов давлением, при которой формообразование поковки из нагретой заготовки осуществляют с помощью специального инструмента — штампа. Течение металла ограничивается поверхностями полостей (а также выступов), изготовленных в отдельных частях штампа, так что в конечный момент штамповки они образуют единую замкнутую полость (ручей) по конфигурации поковки. В качестве заготовок для горячей штамповки применяют прокат круглого, квадратного, прямоугольного профилей, а также периодический. При этом прутки разрезают на отдельные (мерные) заготовки, хотя иногда штампуют из прутка с последующим отделением поковки непосредственно на штамповочной машине. Применение объемной штамповки оправдано при серийном и массовом производстве. При использовании этого способа значительно повышается производительность труда, снижаются отходы металла, обеспечиваются высокие точность формы изделия и качество поверхности. Штамповка в открытых штампах характеризуется переменным зазором между подвижной и неподвижной частями штампа. В этот зазор вытекает часть металла – облой, который закрывает выход из полости штампа и заставляет остальной металл заполнить всю полость. В конечный момент деформирования в облой выжимаются излишки металла, находящиеся в полости, что позволяет не предъявлять высокие требования к точности заготовок по массе. Штамповкой в открытых штампах можно получить поковки всех типов. Штамповка в закрытых штампах характеризуется тем, что полость штампа в процесс деформирования остается закрытой. Зазор между подвижной и неподвижной частями штампа постоянный и небольшой, образование в нем облоя не предусмотрено. Устройство таких штампов зависит от типа машины, на которой штампуют. Например, нижняя половина штампа может иметь полость, а верхняя – выступ (на прессах), или верхняя – полость, а нижняя – выступ (на молотах).
Преимущества и недостатки. Масса слитков составляет от 200 кг до 350т. Наибольшее распространение имеют слитки массой более 1 т. Для ковки применяются слитки многогранные (чаще всего шести восьмигранные) или цилиндрические. По способу изготовления поковок различают свободную ковку и горячую объёмную штамповку. Горячая объёмная штамповка – это вид обработки материалов давлением, при котором формообразование поковки из нагретой заготовки осуществляют с помощью специального инструмента – штампа. Течение металла ограничивается поверхностями плоскостей, изготовленных в отдельных частях штампа, так что в конечный момент штамповки они образуют единую замкнутую плоскость (ручей) по конфигурации поковки. В качестве заготовок для горячей штамповки в подавляющем большинстве случаев применяют прокат круглого квадратного, прямоугольного профилей, а также периодический. При этом прутки разрезают на отдельные заготовки, хотя иногда штампуют и от прутка с последующем отделением поковки непосредственно на штамповочной машине. Заготовки отрезают от прутка различными способами: на кривошипных пресс-ножницах, газовой резкой и т д. По сравнению с ковкой штамповка имеет ряд преимуществ. Горячей объёмной штамповкой можно получать без напусков поковки сложной конфигурации, которые ковкой изготовить без напусков нельзя, при этом допуски на штамповочную поковку в 3 – 4 раза меньше, чем на кованную. В следствии этого значительно сокращается объём последующей механической обработки, штамповочные поковки обрабатывают только в местах сопряжения с другими деталями, и эта обработка может сводиться только к шлифованию. Производительность штамповки значительно выше – составляет десятки и сотни штамповок в час. В то же время штамповочный инструмент штамп – дорогостоящий инструмент и является пригодным только для изготовления какой то одной, конкретной поковки. В связи с этим штамповка экономически целесообразна лишь при изготовлении достаточно больших партий одинаковых поковок. Кроме того, для объёмной штамповке поковок требуется гораздо больше усилий деформирования, чем для ковки таких же поковок. Поковки массой в несколько сот килограммов для штамповки считается крупными. В основном штампуют поковки массой 20 – 30 килограмм. Но благодаря созданию мощных машин в отдельных случаях штампуют поковки массой до трёх тонн. Горячей объёмной штамповкой изготовляют заготовки для ответственных деталей автомобилей, тракторов, сельскохозяйственных машин, самолётов, железнодорожных вагонов, станков и так далее. Конфигурация поковок чрезвычайно разнообразна, в зависимости от неё поковки обычно разделяются на группы. Например, штампованные поковки, можно разделить на 2 группы: удлинённой формы, характеризующиеся большим отношением длинны к ширине, и круглые или квадратные в плане. Наличие большого разнообразия форм и размеров штампованных поковок, а также сплавов, из которых их штампуют, обуславливает существование различных способов штамповки. Так как характер течения металла в процессе штамповки определяется типом штампа, то этот признак можно признать основным для классификации способов штамповки. В зависимости от типа штампа выделяют штамповку в открытых штампах и в закрытых штампах. Штамповка в открытых штампах характеризуется переменным зазором между подвижным и неподвижным частями штампа. В этот зазор вытекает заусенец (облой), который закрывает выход из полости штампа и заставляет металл целиком заполнить всю полость. В конечный момент формирования заусенец выжимаются излишки металла, находящийся в плоскости, что позволяет не предъявлять особо высоких требований к точности заготовок по массе. Заусенец затем обрезается в специальных штампах. Штамповкой в открытых штампах получают поковки всех типов. Штамповка в закрытых штампах характеризуется тем, что полость штампа в процессе деформирования остаётся закрытой. Зазор между подвижной и не подвижной частями штампа при этом постоянный и большой, так что образование заусенца в нём не предусматривается. Устройство таких штампов зависит от типа машины, на которых штампуют. Закрытый штамп может быть с одной или двумя взаимно перпендикулярными плоскостями разъёма, то есть состоять из трёх частей. При штамповке в закрытых штампах надо строго соблюдать равенство объёмов заготовки и поковки, иначе при недостатке металла не заполняются углы полости штампа, а при избытке размер поковки по высоте будет больше нужного. Значит процесс получения заготовки усложняется, поскольку отрезка заготовок должна сопровождаться высокой точностью. Существенным преимуществом штамповки в закрытых штампах является уменьшение расхода металла, поскольку нет отхода заусениц. Поковки полученные в закрытых штампах имеют более благоприятную микроструктуру, так как волокна обтекают контур поковки, а не прорезаются в месте выхода металла заусениц. штамповке в закрытых штампах металл деформируется в условиях всестороннего неравномерного сжатия при больших зажимающих напряжениях, чем в открытых штампах. Это позволяет получить большие степени деформации и штамповать малопластичные сплавы. К закрытой штамповке можно отнести штамповку выдавливанием и прошивкой, так как штамп в этих случаях выполняют по типу закрытого и отхода металла заусениц не предусматривает. Деформирование металла при горячей штамповке вдавливанием и прошивкой происходит так же, как при холодном прямом и обратном выдавливании. ⇐ Предыдущая78910111213141516Следующая ⇒ Читайте также: Техника прыжка в длину с разбега Организация работы процедурного кабинета Области применения синхронных машин Оптимизация по Винеру и Калману |
Последнее изменение этой страницы: 2016-08-01; просмотров: 704; Нарушение авторского права страницы; Мы поможем в написании вашей работы! infopedia. |
Виртуальная тетрадь по технологии 6 класс
Токарный станок по обработке древесины предназначен для изготовления цилиндрических, конических и сферических деталей путем снятия резцами стружки с заготовки. Основными частями станка являются: электродвигатель, клиноременная передача, передняя бабка, задняя бабка, подручник и станина.
От электродвигателя (2) через клиноременную передачу (1) вращение передается шпинделю (3). К шпинделю крепятся приспособления для закрепления заготовки. Резец при точении перемещают вручную, опирая его на подручник (5). Передняя бабка (4) служит опорой левому концу, задняя бабка (6) правому концу заготовки, подручник – режущему инструменту и руке.
Пуск станка производят при помощи черной кнопки пульта управления (7), остановку производят красной кнопкой (при длительном нажатии на красную кнопку – срабатывает электрический тормоз).
Для закрепления заготовки применяют различные приспособления. Для закрепления заготовок небольшого диаметра и длиной до 150 мм (кубки, солонки) применяют патрон (1). Для точения деталей большого диаметра и небольшой толщины (тарелки, шкатулки) применяют планшайбу (2). При обработке длинной заготовки (подсвечник) ее закрепляют между трезубцем (3) и задней бабкой.
Изготовление заготовки цилиндрической формы на токарном станке.
На торцах заготовки находят центры. Если заготовка имеет в сечении форму квадрата, то проводят диагонали (для нахождения центра у круглых заготовок имеется приспособление – центроискатель), полученные центры накалывают шилом или пробивают кернером. Рубанком строгают ребра, придавая заготовке форму восьмигранника. С одной стороны делают ножовкой пропил для трезубца и закрепляют ее в станке.
Основными инструментами для точения служат резцы: рейер (полукруглая стамеска) – для чернового точения и протачивания канавок и майзель (косая стамеска) – для чистового точения, отрезания и подрезания заготовок. Токарную стамеску держат двумя руками, передвигая по подручнику. За первый проход снимают стружку толщиной 1…2 мм серединой лезвия рейера. Дальнейшее точение выполняют боковыми частями лезвия при движении стамески как влево, так и вправо. После 2…3 мин работы следует остановить станок и проверить крепление заготовки и зазор между заготовкой и подручником (2-3 мм). Когда остается снять 3…4 мм, начинают чистовое точение. Майзель ставят на ребро тупым концом вниз. Стружку срезают серединой и нижней частью лезвия.
Контроль диаметра детали производят в нескольких местах штангенциркулем после остановки станка. Прямолинейность поверхности проверяют линейкой или угольником на просвет.
До отрезания детали ее обрабатывают наждачной бумагой, полируют бруском более твердой древесины (при вращении детали). Разметку по длине делают карандашом по линейке или штангенциркулю, выключив станок.
Для подрезания торцов майзель ставят острым углом вниз и по риске делают неглубокий надрез. Затем, отступив немного вправо или влево
(в зависимости от того, какой торец подрезают), наклоняют стамеску и срезают на конус часть заготовки. Эту операцию повторяют несколько раз, пока не оста-нется шейка диаметром 8…10 мм. Далее деталь снимают со станка, отрезают ее концы ножовкой. Торцы зачищают. Точение деталей выполняют по технологическим картам.
Так же предлагаю к вашему вниманию презентацию “История создания токарного станка”
Токарный станок
Итак, история токарных станков уходит в далекую древность. Они использовались для изготовления деталей прялок, столов, стульев, посуды и т.д.А сейчас мы подробно рассмотрим технологию точения древесины на токарном станке по дереву.
youtube.com/embed/8luyM2iVM2w” allowfullscreen=””/>Теперь пришло время проверить свои знания по общей теме “Токарная обработка древесины”
В приложении размещены интересные тренажёры , имитирующие работу токарного станка. Скачайте swf-файлы к себе на компьютер и откройте с помощью браузера Google Chrome. Теперь вы тоже можете потренироваться в работе на токарном станке. Удачи!
Практическая работа
Найдите в Интернете историю развития токарных станков. Подготовьте презентацию на эту тему. Работу разместите в виртуальной тетради.
youtube.com/embed/kYyJ6RM1jVg” allowfullscreen=””/>23 Различные части токарного станка и их функции
Сегодня мы собираемся обсудить различные части токарного станка , которые полезны для выполнения операций на токарном станке.
Токарные станки более универсальны, чем все остальные станки.
Он в основном используется для обработки круглых поверхностей, таких как цилиндрические или конические, но также может использоваться для изготовления плоских поверхностей, сверления отверстий, обработки пазов и многих других видов работ.
Итак, не теряя времени, приступим.
Parts of Lathe Machine
There are following parts are used in the lathe machine:
- Bed
- Guideways
- Headstock
- Spindle
- Carriage
- Saddle
- Cross slide
- Compound Rest
- Составной суппорт
- Резцедержатель
- Фартук
- Задняя бабка
- Патрон
- Лицевая пластина
- Центр
- Корма для подачи
- СВОЙСТВЕННЫЙ ВИНТ
- Ноги
- Чипс
- Ручное колесо
- Скоровой контроллер
- Bull Gear
- Sleeve

Детали токарного станка |
Станина
Станина является основным корпусом станка.
К нему прикручены все основные компоненты.
Обычно изготавливается из чугуна из-за его высокой прочности на сжатие.
Изготавливается методом литья и крепится болтами к полу.
Его верхняя часть состоит из направляющих станины или V-образных направляющих, которые прецизионно обработаны и используются для направления и выравнивания других частей токарного станка.
Направляющие
Направляющие обеспечивают движение задней бабки и каретки на станине.
Передняя бабка
Передняя бабка — это основная часть корпуса, которая размещается с левой стороны кровати.
Служит удерживающим устройством для зубчатых цепей, шпинделей, приводных шкивов и т.д.
Механизм передней бабки приводится в действие электродвигателем, вращающим шпиндель.
Также изготовлен из чугуна.
Шпиндель
Основная часть токарного станка, удерживающая и вращающая патрон.
Изготавливается из качественной легированной стали с термообработкой.
Резьба, конусы и т. д. выполнены на одном конце шпинделя, к которому можно прикрепить удерживающие устройства.
Каретка
Расположена между передней и задней бабками.
Используется для удержания и перемещения стойки инструмента вдоль станины к передней бабке или от нее.
Скользит по направляющим.
Также изготовлен из чугуна.
Состоит из шести основных частей:
- Седло
- Поперечный суппорт
- Составной упор
- Составной суппорт
- Стойка инструмента
- Фартук
Седло
Представляет собой Н-образную отливку, установленную на направляющих токарного станка, поддерживает поперечный салазок, обеспечивающий перемещение резцедержателя.
Поперечные салазки
Поперечные салазки — это часть каретки, позволяющая перемещать резцедержатель под прямым углом к направляющим станины во время обработки.
Поперечные салазки перемещаются винтом подачи.
Составной упор
Составной упор — это деталь, соединяющая поперечный суппорт и составной суппорт.
Составной упор монтируется поверх поперечного салазка.
Он имеет круглое основание, на котором сделаны градусные деления.
Питание не подается, но управляется вручную.
Определённую глубину резания можно установить вращением винта подачи составного упора.
После установки в соответствии с требованиями составной ползун прочно фиксируется на основании.
Составная направляющая
Составная направляющая крепится к составной опоре с помощью соединения типа «ласточкин хвост».
Составные суппорты используются для резки углов или конусов, которые нельзя обрезать вращением передней бабки.
Стойка для инструмента
Крепится болтами к каретке в верхней части составного суппорта.
Используется для жесткого удержания инструментов в правильном положении.
Фартук
Фартук находится на тележке.
Состоит из всех управляющих и движущихся механизмов вагона.
Фартук крепится к седлу с помощью механизмов подачи, обеспечивающих автоматическую подачу в каретку.
Маховик фартука можно вращать для перемещения каретки вручную вместе с станиной станка.
Задняя бабка
Задняя бабка представляет собой отливку, расположенную с правой стороны станины.
Его функция заключается в поддержке свободного конца заготовки или работы во время обработки.
Может скользить по направляющим станины и фиксироваться в любом положении.
Задняя бабка предназначена для следующих целей:
- Для поддержки свободных концов длинных заготовок при выполнении токарных операций.
- Для удержания режущих инструментов, таких как сверлильные патроны, сверла, развертки и т. д.
- Точение внешнего конуса методом смещения.
Патрон
Это важный инструмент, который используется для удержания и вращения заготовки.
Самый маленький кусок заготовки можно удерживать в патроне.
Планшайба
Планшайба крепится к шпинделю токарного станка и может быть установлена на месте для выполнения токарной операции.
Центр
Центр — это часть токарного станка, которая используется для поддержки длинных заготовок между передней и задней бабками для выполнения токарной операции.
Центр, который входит в шпиндель передней бабки и вращается вместе с заготовкой, называется подвижным центром.
Центр, который используется в шпинделе задней бабки и который не вращается, называется мертвой точкой.
Вал подачи
Изготовлен из высококачественной легированной стали.
Проходит по всей длине станины и устанавливается под ходовым винтом.
Имеет шпоночный паз, из которого можно передавать движения каретке механизма подачи.
При подключении механической подачи она обеспечивает поперечное перемещение инструмента.
Ходовой винт
Используется для нарезания резьбы.
Ходовой винт расположен на нижней стороне станины и используется для автоматического перемещения каретки во время нарезания резьбы.
Изготовлен из сплава хорошего качества и выполнен из трапецеидальной резьбы.
Ноги
Ноги используются для переноски всех нагрузок машины.
Крепятся болтами к полу, что предотвращает вибрацию.
Поддон для чипсов
Поддон для чипсов устанавливается на нижней стороне кровати.
Его основная функция – убирать всю стружку, удаляемую заготовкой.
Маховик
Это маховик, который приводится в действие вручную для перемещения поперечных салазок, каретки, задней бабки и других частей, содержащих маховик.
Регулятор скорости
Регулятор скорости расположен на передней бабке и управляет скоростью вращения шпинделя.
Bull Gear
Изготовлен из чугуна.
Используется для медленных и быстрых скоростей с помощью заднего штифта выпуклой шестерни и фиксируется «шпонкой» на полом шпинделе.
Втулка
Втулка устанавливается внутри задней бабки, которую можно перемещать вперед и назад для установки или удаления мертвой точки.
Спецификация токарного станка
Размер токарного станка указан в соответствии с:
- Высота центров.
- Качели
- Расстояние между центрами
- Длина станины
- Максимальный диаметр стержня
- Качели на каретке
Итак, здесь мы должны знать о деталях токарного станка .
Надеюсь, вам понравится.
Часто задаваемые вопросы, относящиеся к частям токарного станка
Какая часть токарного станка используется для автоматического перемещения каретки во время нарезания резьбы?
Часть токарного станка, которая используется для автоматического перемещения каретки во время нарезания резьбы, представляет собой ходовой винт.
Какая часть токарного станка имеет силовой механизм?
Подающий стержень — это часть токарного станка, обеспечивающая силовой механизм.
Какая часть токарного станка состоит из следующих частей: поперечных салазок, фартука и резцедержателя?
Каретка представляет собой часть токарного станка, состоящую из седла, поперечного суппорта, составного упора, составного суппорта, инструментальной стойки и фартука.
Какова функция составного люнета в токарном станке?
Основная функция заключается в обеспечении определенной глубины резания вращением винта подачи составного упора.
Какова функция поперечного скольжения на токарном станке?
Основной функцией поперечного суппорта является резка под углом или конусом, который нельзя обрезать вращением передней бабки.
Как называется часть токарного станка, которая используется для поддержки тупика длинного обрабатывающего вала, а также для поддержания осевого выравнивания обрабатывающего вала?
Часть токарного станка, которая используется для поддержки тупика длинного обрабатывающего вала, а также для поддержания осевого выравнивания обрабатывающего вала, называется мертвой точкой.
Какая часть токарного станка изготовлена из Н-образного чугуна на направляющих станины?
Седло – это часть токарного станка, обрабатывающая ч-образный чугун на направляющих станины.
Какова функция седла токарного станка?
Его основная функция заключается в поддержке поперечных салазок, обеспечивающих перемещение резцедержателя.
Какова функция ходового винта в токарном станке?
Основная функция ходового винта заключается в автоматическом перемещении каретки во время нарезания резьбы.
Какую функцию выполняет фартук токарного станка?
К седлу крепится фартук с механизмами подачи, обеспечивающими автоматическую подачу в каретку.
Какова функция ножки токарного станка?
Основная функция опоры токарного станка заключается в том, что она несет полную нагрузку станка и передает ее на землю. Вот почему он прикручен к полу, что предотвращает вибрацию.
Какова функция задней бабки токарного станка?
Его основная функция заключается в поддержке свободного конца заготовки или работы во время обработки.
15 различных частей токарного станка и их функции
Связанный: Что такое токарный станок?
Детали токарного станкаНиже приведены детали токарного станка:
Детали токарного станка- Передняя бабка : Передняя бабка обычно располагается с левой стороны станка и оснащена шестернями, патронами, шпинделями , рычаги управления скоростью передачи и регуляторы подачи. Он устанавливался в фиксированном положении на внутренних путях, как правило, на левом конце. Используя патрон, он вращает работу.
- Задняя бабка: Ее также иногда называют передней бабкой или кукольной головой. Обычно располагается с правой стороны станка, заготовка поддерживается на конце. Устанавливается на внутренних направляющих станины и может перемещаться в любом положении передней бабки в соответствии с длиной заготовки. К нему будет установлено дополнительное приспособление для токарной обработки конуса.
- Станина: Основные части токарного станка, Обычно изготавливаются из чугуна. Предусмотрена тяжелая жесткая рама, на которой крепятся все основные узлы. все части прикручены к станине. Он включает в себя переднюю бабку, заднюю бабку, каретки и другие детали.
- Каретка : Каретка расположена между передней и задней бабками и содержит фартук, седло, составную опору, поперечный суппорт и резцедержатель. Двигается по внешним путям. Используется для монтажа и перемещения большинства режущих инструментов.
- Патрон позволяет устанавливать сложные детали некруглой, квадратной или треугольной формы.
- Стержень подачи: Ходовой винт используется для автоматического перемещения каретки во время нарезания резьбы. Используется для соединения коробки подачи и коробки скольжения и передачи скорости и мощности коробки подачи на коробку скольжения, так что коробка скольжения достигает продольного линейного движения.
- Ходовой винт: Винт специально предназначен для сгибания различных резьб. При гибке других поверхностей заготовки вместо шурупов используют только гладкие шурупы. Учащиеся должны различать световой винт и ходовой винт, основываясь на содержимом слайд-бокса.
- Поддон для стружки: Находится в нижней части станка. Поддон для стружки используется для сбора стружки, образующейся во время работы токарного станка.
- Маховик: Это колесо, которое приводится в действие вручную для перемещения поперечных салазок, каретки, задней бабки и других частей, имеющих маховик.
- Охлаждающее устройство : Охлаждающее устройство в основном использует насос охлаждающей воды для подавления щелевой жидкости в резервуаре для воды и распыления ее на место резки, промывки стружки и снижения температуры резки.
Сглаживает поверхность, увеличивая срок службы инструмента. Качество обработки поверхности заготовки.
- Ноги : Это опоры, на которые переносится весь вес машины. Преобладающий метод — использование литых ножек. Обе ножки прочно закреплены на полу через опорные точки, чтобы предотвратить вибрацию машины.
- Ползунковый блок: Это блок управления подачей токарного станка. Он снабжен механизмом, который превращает вращательное движение светового стержня и ходового винта в поступательное движение резцедержателя.
- Коробка передач: внутри передней бабки, обеспечивающая несколько скоростей с геометрическим передаточным числом за счет перемещения рычагов.
- Шпиндель: Отверстие в передней бабке, к которому можно подавать прутковый материал, что позволяет обрабатывать валы, длина которых до двух раз превышает длину между центрами токарного станка, с одного конца за раз.
- Поперечные салазки : Устанавливаются на поперечных салазках каретки и используют маховик для подачи инструментов в заготовку.
- Стойка для инструмента : Для установки держателей инструментов, в которых зажимаются режущие насадки.
- Направляющие : Для обеспечения точного перемещения задней бабки и каретки на станине, устанавливаются снаружи или внутри.
- Фартук: Прикрепляется к передней части каретки, имеет механизм и органы управления для перемещения каретки и поперечных салазок.
Какие основные части токарного станка?
Несмотря на то, что существуют различные типы токарных станков, большинство из них имеет несколько основных деталей, облегчающих их работу.
- Кровать.
- Передняя бабка
- Задняя бабка
- Каретка
- Ножки.
- Поперечный салазок
- Седло.
- Фартук.
Что является частью токарного станка?
Основные части токарного станка, все детали крепятся болтами к станине. Он включает в себя переднюю бабку, заднюю бабку, каретки и другие детали. Каретка: Каретка расположена между передней и задней бабками и содержит фартук, седло, составную опору, поперечный суппорт и инструментальную стойку.
Каковы 6 основных компонентов токарного станка?
Токарный станок состоит из шести основных частей. Это станина, узел передней бабки, главный шпиндель, задняя бабка, каретка и устройства защиты от перегрузок.
Что такое торцовка на токарном станке?
Торцовка на токарном станке использует торцовочный инструмент для резки плоской поверхности перпендикулярно оси вращения заготовки. Торцовочный инструмент устанавливается в резцедержатель, который опирается на каретку токарного станка. Затем инструмент будет подаваться перпендикулярно оси вращения детали, когда она вращается в кулачках патрона.
Что не является частью токарного станка?
Объяснение: Оправка не является частью токарного станка.
Какой инструмент используется в токарном станке?
Токарные станки можно разделить на разные категории. Наиболее распространенные классификации включают: Использование: токарный инструмент, расточный инструмент, инструмент для снятия фаски, инструмент для нарезания канавок и т. д. Материал: инструмент из быстрорежущей стали, инструмент из карбида, алмазный диск, другие материалы и т. д.
Размер токарного станка ?
Общий размер составляет примерно 15-дюймовые качели с расстоянием между центрами от 36 до 48 дюймов. Многие токарные станки инструментального цеха используются для производства специальных инструментов и штампов из-за высокой точности станка.
Читайте также
- Токарный станок: Детали, типы и применение
6 Основные части токарного станка | Станки
РЕКЛАМА:
Описание различных частей токарного станка приведено ниже:
Часть № 1. Кровать: Опирается на широкие колонны коробчатого сечения и изготовлена из чугуна. Его верхняя поверхность либо зачищена, либо отшлифована, предусмотрены направляющая и скользящая поверхности. Кровать состоит из двух тяжелых металлических направляющих, идущих вдоль, с направляющими или V-образными формами на них. Он жестко поддерживается поперечными подпругами. Внешние направляющие обеспечивают опорные и скользящие поверхности для каретки, а внутренние направляющие – для задней бабки.
Три основных блока, установленных на кровати:
РЕКЛАМА:
я. Передняя бабка,
ii.Задняя бабка и
III. Карета.
Зачищенные или отшлифованные направляющие и скользящие поверхности на станине токарного станка обеспечивают точность выравнивания этих трех узлов. Передняя бабка неподвижно закреплена на станине, задняя бабка регулируется по положению для размещения заготовок разной длины. Каретку можно перемещать между передней и задней бабками вручную или с помощью электропривода.
РЕКЛАМА:
Станина токарного станка изготовлена из высококачественного специального чугуна, обладающего высокими вибропоглощающими свойствами. Станина токарного станка жестко закреплена на ножке шкафа и концевой ножке, а на нее насажены все остальные детали. (См. рис. 12.2).
Верхняя поверхность станины обработана точно. Важными соображениями при проектировании станины токарного станка являются ее жесткость, выравнивание и точность. При его использовании следует соблюдать все меры предосторожности, чтобы избежать образования царапин, зазубрин и вмятин от падающих инструментов/гаечных ключей, и его следует регулярно смазывать, чтобы избежать коррозии.
Станина токарного станка, являющаяся основным направляющим элементом для точной механической обработки, должна быть достаточно жесткой, чтобы предотвратить отклонение под действием сил резания; должен быть массивным с достаточной глубиной и шириной для поглощения вибраций; должны быть рассчитаны на сопротивление скручивающим напряжениям, возникающим из-за равнодействующей двух сил; должны быть выдержаны естественным образом, чтобы снять напряжение, возникающее во время литья.
РЕКЛАМА:
На рис. 12.3 (а) показано сечение типичной станины токарного станка. Можно отметить, что в то время как верхние поверхности принимают на себя вес передней бабки, каретки и задней бабки, узкие поверхности, такие как буква «G», действуют как направляющие поверхности для движения каретки и задней бабки.
На рис. 12.3 (б) показаны некоторые альтернативные варианты расположения направляющих и опор. Важно отметить, что направляющие поверхности не должны располагаться слишком далеко друг от друга во избежание эффекта бокового ветра или заедания.
Концевая передача станины:
РЕКЛАМА:
Движение шпинделя передней бабки также передается на редуктор подачи через зубчатую передачу в конце станины. Затем привод передается через коробку передач; выборочно к ходовому винту или подающему валу, в зависимости от того, используется ли станок для нарезки винтов или плоского точения.
Положение торцевого зацепления обеспечивает постоянную зависимость между скоростью перемещения каретки и скоростью вращения шпинделя, как бы последняя ни изменялась. Предусмотрено также реверсирование направления траверсы каретки в конце зацепления станины. Скорость перемещения каретки на станине регулируется с помощью зубчатой передачи на конце станины в сочетании с редуктором подачи.
Большинство современных токарных станков имеют реверсивный механизм, встроенный в переднюю бабку и приводимый в действие отдельным рычагом. В некоторых токарных станках ходовой винт и вал подачи могут вращаться постоянно в одном направлении, а реверсирование седловой траверсы достигается за счет реверсивной передачи в фартуке.
Изменения скорости подачи, обычно необходимые для токарной обработки или нарезания резьбы, могут быть сделаны в редукторе подачи, но когда необходимо нарезать специальную резьбу, может потребоваться изменить передаточное отношение зубчатого зацепления на конце станины.
Деталь № 2. Головка:РЕКЛАМА:
Он поддерживает главный шпиндель в подшипниках и правильно его выравнивает. В нем также находится необходимый передаточный механизм с рычагами переключения скоростей для получения разных скоростей. Конический шкив, шестерни или их комбинация могут использоваться для изменения скорости вращения шпинделя.
Аксессуары, устанавливаемые на шпиндель передней бабки:
1. Трехкулачковый патрон
2. Четырехкулачковый патрон
3. Токарный центр и токарная собачка
4. Цанговый патрон
5. Лицевая панель
6. Магнитный патрон.
Комплектная передняя бабка состоит из отливки передней бабки, расположенной на направляющих станины с левой стороны от оператора, полого шпинделя, в котором подвижный центр жестко удерживается конусом, и необходимых шестерен и механизмов для получения различные скорости вращения.
Центральная линия передней бабки параллельна направляющим как в горизонтальной, так и в вертикальной плоскостях. На всех современных токарных станках используется полноприводная шпиндельная бабка. Однако там, где критерием являются большая простота и низкая стоимость, можно использовать шпиндельную бабку с конусным приводом. Передняя бабка с редуктором может приводиться либо непосредственно от линейного вала, либо от независимого двигателя, при этом привод передается на главный приводной шкив постоянной скорости.
Передняя бабка также включает в себя автономный механизм сцепления и тормоза, с помощью которого шкив при необходимости может быть соединен с валом в передней бабке. Обычно предусмотрены устройства, обеспечивающие автоматическое торможение шпинделя при свободном вращении шкива.
Скользящая передача обычно используется для получения различных изменений скорости, шестерни устанавливаются на многошпиндельных валах и перемещаются по ним в осевом направлении с помощью внешних рычагов управления через селекторный механизм.
Отдельный редуктор переключения скоростей расположен под передней бабкой для снижения скорости, чтобы иметь разные скорости подачи для нарезания резьбы и автоматических боковых перемещений каретки. Подающий вал используется для большинства токарных операций, а ходовой винт используется для нарезания резьбы и т. д.
Это полый цилиндрический вал, через который могут проходить длинные тонкие детали. Конец шпинделя, обращенный к задней бабке, называется носом шпинделя. Носик шпинделя имеет отверстие под конус Морзе (самоблокирующийся конус) и резьбу снаружи. Конус Морзе используется для размещения токарного центра или цангового патрона и резьбовой части для патрона или планшайбы. Конструкция шпинделя токарного станка и его подшипников является важной особенностью, так как упор режущего инструмента имеет тенденцию отклонять шпиндель.
В передней бабке используются антифрикционные подшипники, а шпиндель, изготовленный из высокопрочной стали, соответствующим образом закаленной и отпущенной, опирается на роликовые подшипники. Передние подшипники шпинделя воспринимают как осевые, так и радиальные нагрузки на шпиндель, а задний подшипник сконструирован таким образом, что шпиндель может перемещаться в осевом направлении относительно передних подшипников, допуская расширение и сжатие. Передний подшипник выполнен регулируемым с помощью фланцевой пластины и предварительно нагружен в сборе, чтобы избежать любой возможности люфта во время резки с последующей вибрацией.
Носик шпинделя предназначен для быстрой установки и снятия на нем патронов и приспособлений, а также для их точного и надежного позиционирования. Для этого используется носовая часть шпинделя винтового типа с двумя установочными цилиндрическими поверхностями спереди и сзади и резьбой между ними. Выступ носовой части шпинделя сведен к минимуму для защиты от изгиба.
Шпиндель выполнен полым для пропуска длинных стержней. На передней стороне имеется конусное гнездо для установки приводного центра, который вращается вместе со шпинделем. Различные планшайбы и патроны крепятся к фланцу носовой части шпинделя болтами или шпильками и позиционируются с помощью конической втулки.
Деталь № 4. Задняя бабка: Представляет собой подвижную отливку, расположенную напротив передней бабки на направляющих станины.
Используется для двух целей:
(i) Для поддержки другого конца изделия при механической обработке и
(ii) Для удержания инструмента для выполнения таких операций, как сверление, развертывание, нарезание резьбы и т. д.
Содержит мертвые точки, регулировочный винт и маховик.
Корпус задней бабки регулируется на основании, которое установлено на направляющих станины и может перемещаться вперед и назад. Цель создания корпуса, регулируемого на основании, состоит в том, чтобы обеспечить средства для выравнивания центра, установленного в подвижном шпинделе, с центром передней бабки или для смещения этого центра, чтобы можно было поворачивать конусы.
Осевая регулировка мертвой точки подвижного шпинделя в корпусе задней бабки предусмотрена с помощью маховика, который крепится к винту, зацепляющему гайки в задней части подвижного шпинделя. Его можно расположить в любом положении в корпусе с помощью рычага. Шпиндель расточен или отшлифован до конического калибра по центру, который может быть фиксированного или вращающегося типа.
На рис. 12.6 показан эскиз задней бабки. Перемещают шпиндель 4 задней бабки в корпусе 1 вращением винта 5 маховиком 7. Шпиндель фиксируется в положении рычагом управления 3. На шпинделе установлен конический хвостовик 2. Задняя бабка перемещается по направляющим станка вручную или с помощью седла.
Задняя бабка может быть заблокирована с помощью рычага 6, который соединен со штоком 8 и рычагом 9. Давление зажима можно регулировать с помощью гайки 11 и винта 12. Большее усилие при зажиме можно приложить с помощью гайки 13 и винта 14, удерживающего рычаг 10 против кровати.
Деталь № 5. Каретка (рис. 12.7):Расположен между передней и задней бабками. Он устанавливается на станине и скользит по направляющим станины и может быть зафиксирован на станине в любом желаемом положении путем затягивания стопорного винта каретки. Его можно перемещать вручную с помощью маховика или с помощью механической подачи.
Состоит из седла и фартука и скользит по направляющим между передней и задней бабками. Он имеет форму буквы H и перекинут через станину токарного станка, чтобы нести поперечный салазок, составную опору и опору для инструмента, а также прикреплен к внешним направляющим и прикреплен к станине. Он также несет составной остаток.
Седло, несущее поперечный суппорт и резцедержатель, можно зафиксировать в любом положении при выполнении операции наплавки. При повороте каретка приводится в движение подающим валом, который вращает шестерню, установленную в отливке в передней части каретки (фартуке).
Это соединение входит в зацепление со стойкой вдоль передней части кровати, так что оно тянет себя и каретку вдоль кровати. При нарезании винтов движение каретки достигается за счет зацепления разрезной гайки над ходовым винтом, который затем вращается по отношению к вращению шпинделя.
Обеспечивает три движения инструмента:
(i) Продольная подача — сквозное движение каретки.
(ii) Поперечная подача — за счет движения поперечного суппорта.
(iii) Угловая подача — за счет движения верхнего ползуна.
Состоит из следующих 5 основных частей:
(а) Фартук
(б) Седло
(c) Составной упор, состоящий из вертлюга и верхней направляющей
(d) Поперечный суппорт
(e) Стойка для инструментов
(а) Фартук (рис. 12.8):
Крепится к седлу и висит над передней частью кровати. Он содержит шестерни и муфты для передачи движения от подающего стержня к каретке, а также разрезную гайку, которая входит в зацепление с ходовым винтом при нарезании резьбы. Он преобразует вращательное движение подающего вала или ходового винта в поступательное движение каретки в продольном направлении на станине или поперечных салазок в поперечном направлении на каретке.
Ходовой винт соединен с кареткой с помощью разрезной гайки, закрепленной в фартуке, а подающий вал обычно приводит в движение каретку через червячную передачу. Широко используются два типа фартуков: один тип включает червячный механизм, а другой – фрикционные или кулачковые муфты.
Фартук крепится к переднему положению седла лицом к оператору. Он состоит из маховика для перемещения седла, шестерни для зацепления со рейкой для перемещения седла, рычага для включения автоматической подачи седла, муфты автоматической подачи, разрезной гайки (полугайки) и ходового винта. В нем находится управление кареткой и поперечным скольжением.
Он содержит элементы управления для передачи движения от подающего стержня или ходового винта к каретке и поперечным салазкам. В нем находятся шестерни, рычаги, маховики и муфты для управления кареткой вручную или с помощью автоматической подачи. Предусмотрен рычаг для зацепления разрезной гайки для нарезания резьбы.
(б) Седло:
Изготовлен из Н-образного литья. Как правило, он имеет V-образную направляющую и плоскую направляющую с одной стороны для установки на направляющие станины станка. Он также помогает седлу скользить по направляющим станины с помощью маховика. Другая сторона седла снабжена патрубком «ласточкин хвост» для размещения поперечного суппорта со стрелой.
(c) Составной упор:
Поддерживает резцедержатель и режущий инструмент в различных положениях. На поперечных салазках он может поворачиваться на любой угол в горизонтальной плоскости; его основание градуировано соответствующим образом. Составной упор необходим при точении углов и растачивании коротких конусов, а также при точении углов и форм на формовочных инструментах.
(d) Поперечный суппорт:
Он оснащен ласточкиным хвостом с внутренней стороны с одной стороны и собран на верхней части седла с его ласточкиным хвостом с наружной резьбой. Между седлом и крестовиной «ласточкин хвост» предусмотрена коническая клинья, чтобы обеспечить необходимую посадку для перемещения поперечного суппорта на седле.
На верхней поверхности поперечных суппортов имеются Т-образные пазы, позволяющие фиксировать задний резцедержатель или приспособление для подачи СОЖ. Передняя сторона градуирована в градусах для облегчения поворота составного упора на нужный угол.
Составной упор состоит из шарнирного соединения и верхнего салазка и устанавливается на поперечный салазок.
Вертлюгмонтируется непосредственно на поперечном суппорте и может поворачиваться в любую сторону, чтобы придать компаунду нужный угол. Он снабжен патрубком типа «ласточкин хвост» на верхней поверхности.
Верхняя направляющая снабжена ласточкиным хвостом с внутренней резьбой и монтируется на вертлюге с коническим удлинителем для регулировки. Верхний салазок может скользить по вертлюгу с помощью прецизионного винтового стержня и перемещается вручную.
С помощью верхнего салазка стойка инструмента может перемещаться горизонтально, перпендикулярно или под углом к одной оси направляющих станины в зависимости от положения вертлюга.
(д) Инструментальный пост:
Используется для крепления различных держателей режущих инструментов. Держатели опираются на клин, форма которого в нижней части соответствует вогнутому кольцу (сегментного типа), что позволяет регулировать высоту режущей кромки путем наклона инструмента. (См. рис. 12.12)
Фиксируется на верхней направляющей. Он получает свое движение за счет движения седла, поперечного скольжения и верхнего скольжения.
Обычно используются три типа резцедержателей:
1. Кольцо и коромысло.
2. Быстросменный резцедержатель.
3. Стойка с квадратной головкой.
Стойка для инструмента с кольцом и коромыслом состоит из круглой стойки с прорезью для размещения инструмента или держателя инструмента, кольца, коромысла и зажимного винта для инструмента. Одна сторона кольца плоская, а другая сферическая, на которой сидит коромысло. Инструмент зажимается на коромысле. Высота кончика инструмента регулируется с помощью кольца и коромысла.
Четырехпозиционный резцедержатель позволяет удерживать четыре отдельных держателя инструмента, которые можно поворачивать в различные положения.
Держатель инструмента с квадратной револьверной головкой показан на рис. 12.13. Коническая оправка 3 с резьбовым концом закрепляется в посадочном отверстии верхнего ползуна 5. На конус надевается квадратная револьверная головка 6.
При повороте рукоятки 4 по часовой стрелке ее выступ 2 опускается на резьбу оправки 3 и давит через проставку 1 и упорный подшипник на револьверную головку, заставляя ее плотно сидеть на конусе. При затягивании револьвер удерживается от вращения шариком, зажатым между поверхностями, образованными прорезью в основании шпинделя и отверстием в револьвере.
Для изменения положения инструмента рукоятку 4 поворачивают против часовой стрелки. Бобышка 2 поднимается по резьбе оправки 3, освобождая турель 6. Одновременно бобышка 2 поворачивает турель 6 с помощью фрикционных элементов, которые входят в зацепление с кольцевой выемкой на нижней стороне бобышки. Фрикционные элементы крепятся к башне шпильками 7.
Подпружиненный шар, вставленный в отверстие, не препятствует вращению башни.
Если рукоятка 4 при затягивании занимает неудобное положение, необходимую регулировку можно произвести, изменив толщину проставки 1.