Освидетельствование баллонов – Освидетельствование газовых баллонов: бытовых, автомобильных
alexxlab | 08.10.2019 | 0 | Разное
Освидетельствование газовых баллонов: бытовых, автомобильных
Для хранения и транспортирования сжатых и сжиженных газов применяют емкости, выполненные из металла или композитных материалов. Эти сосуды рассчитаны на то, что газ будет храниться в них под определенным давлением. Так, ГОСТ 15860-84 определяет, что рабочее давление в емкости с пропаном не должно превышать 1,6 МПа. Существуют и емкости, рассчитанные на более высокое давление в 5 МПа. Все емкости, применяемые для хранения газов должны проходить испытания и периодические освидетельствования.
Контроль пригодности газового баллонаЦель проведения испытаний и освидетельствования газового баллона – это контроль над его техническим состоянием и принятие решение о его дальнейшей эксплуатации или утилизации.
Поверка газового баллона
Освидетельствование газового баллона – это мероприятие, которое необходимо в первую очередь его владельцу. Освидетельствование может гарантировать то, что баллон безопасен в эксплуатации и может быть использован по назначению, в противном случае их эксплуатация недопустима. Существует единый порядок освидетельствования, во время ее проведения проводят осмотр поверхностей баллонов на предмет обнаружения повреждения поверхности.
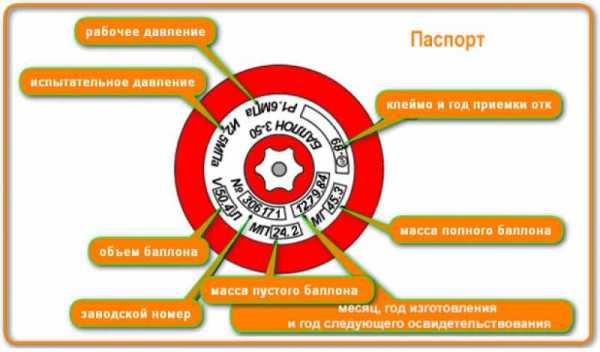
Срок службы газового баллона
Выполняют проверку качества маркировки и окраски на предмет соответствия требованиям ГОСТ, состояния крана. Кроме того, в процессе аттестации проводят гидравлические испытания емкостей для хранения газов. Результаты осмотра и проведенных испытаний заносят в паспорт, сопровождающий изделие все время его эксплуатации.
Без проведения подобных мероприятий заправка и эксплуатации емкостей для хранения и перевозки газа недопустимы. Обследование баллонов и вынесение заключения по ним может выполнять только организация, которая имеет все необходимые разрешения и полномочия от соответствующих государственных надзорных органов.
Сосуды для хранения газов должны проходить аттестацию один раз в несколько лет. Срок проведения зависит от нескольких параметров – от материала, например, если баллоны изготовлены из легированной или углеродистой стали, то им достаточно проходить через эту процедуру один раз в пять лет. Баллоны, устанавливаемые на автомобили в составе ГБО, должны проходить аттестацию в три или пять лет.
Баллоны, которые работают в стационарных условиях и предназначены для хранения инертных газов проходят необходимые освидетельствования один раз в десять лет.
Обозначенные сроки освидетельствования должны строго соблюдаться. Все дело в безопасности. Если емкости предназначены для хранения и перевозки пропаном, ацетиленом или другим взрывоопасным газом любой дефект на наружной поверхности баллона может привести к непоправимым последствиям.
Как только возникают сомнения в работоспособности емкости для хранения газа необходимо вывести ее из оборота и приобрести, или арендовать новый.
Период допустимой эксплуатации
ГОСТ 949-73 определил то, что для баллонов, выполненных из стали и рабочим давлением до 19,6 МПа составляет 20 лет.
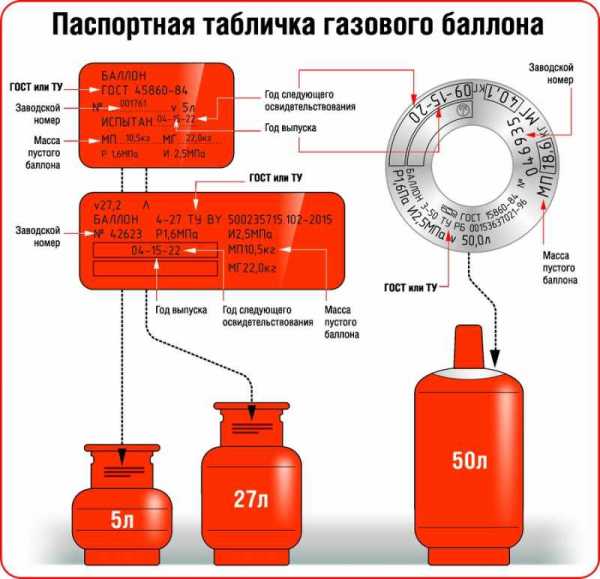
Период допустимой эксплуатации
Периодичность проведения проверки годности баллонов
Транспортировка и эксплуатация технических газов связано со значительной опасностью. Это обусловлено не столько их взрывоопасностью или воспламеняемостью, а, сколько наличием высокого давления в сосудах, предназначенных для их хранения и доставки к месту потребления.
При таких условиях даже самый незначительный дефект может оказаться причиной серьезного происшествия. Именно поэтому огромную роль играет своевременное освидетельствование и необходимое обслуживание баллонов.
Процесс освидетельствования и восстановления емкостей для промышленных газов
Нормативной документацией, а именно «Правилами обустройства и эксплуатации сосудов…» назначена регулярность проведения освидетельствования технического состояние сосудов для газов.
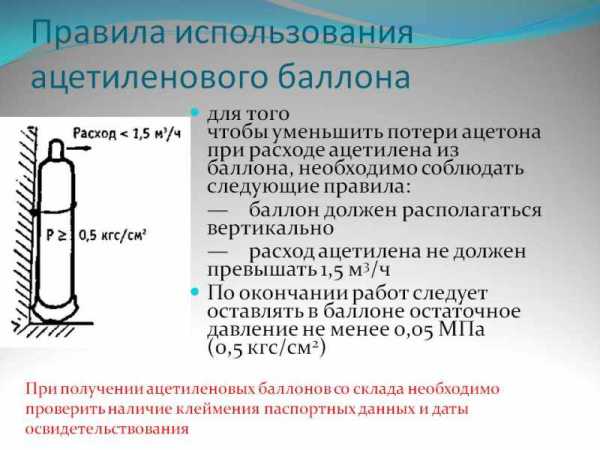
Правила использования ацетиленовых баллонов
К примеру, освидетельствование баллонов для ацетилена проводится один раз в пять лет. В то время, как масса, находящаяся внутри баллона, должна проверятся как минимум один раз в 2 года. Кстати, на баллоне должна быть нанесена отметка о сроках проведения освидетельствования, результате осмотра пористой массы и указаны сроки следующего освидетельствования баллона.
В соответствии с техническими условиями, к эксплуатации допускают только те емкости, которые прошли все необходимые испытания и об этом сделаны все соответствующие записи. Новые сосуды, проходят необходимый цикл испытаний во время приемки продукции службой технического контроля.
По истечении сроков освидетельствования баллоны должны проходить переосвидетельствование, то есть полное освидетельствование технического состояния. При этом те, которые переосвидетельствование не прошли должны быть изъяты из оборота и отправлены на вторичную переработку (утилизацию).
Емкости, на которых обнаружены исправимые дефекты, то они подлежат ремонту и после выполнения требуемых работ, проведения надлежащих испытаний могут быть возвращены в эксплуатацию.
Порядок проведения очередных испытаний баллонов
Очередные испытания баллонов проводят, руководствуясь РД 03112194-1094-03 и РД 03112194-1095-03. Сотрудники, которые выполняют такую работу, должны пройти соответствующие курсы и обладать надлежащими знаниями и навыками.
Очередные испытания проводят в следующей последовательности:
- Приемка емкостей. На этом этапе освидетельствования выполняется проверка комплектности баллона, выполняется осмотр внешней поверхности. Одновременно с этим выполняют проверку даты последнего осмотра и опрессовки. При необходимости должна быть выполнена очистка внутренней поверхности емкости.
- Обследование внутренней части емкости проводят с применением специализированного оборудования.
- Выполняют демонтаж арматуры и ее проверку. Кроме того, в процессе осмотра может быть выполнена установка технологических деталей, без которых невозможно провести гидравлические испытания.
После проведения гидравлических испытаний (опрессовки) необходимо просушить сосуд от следов реагента. Вернуть на место демонтированную арматуру.
Баллон необходимо подготовить к грунтовке и покраске. Для этого его подвергают пескоструйной обработке. После нанесения покрытия соответствующего цвета и ее просушки на поверхность баллона необходимо выполнить маркировку в соответствии с нормативной документацией. Окончание работ по освидетельствованию оформляется соответствующим актом. Общее время на выполнение всех указанных работ составляет 3 – 5 часов. В это время входят и подготовительные и основные операции.
Правила хранения
Баллоны, предназначаемые для технических газов, хранят на основании требований безопасности, которые определены в «Правилах эксплуатации сосудов под давлением ПБ 03-576-03».
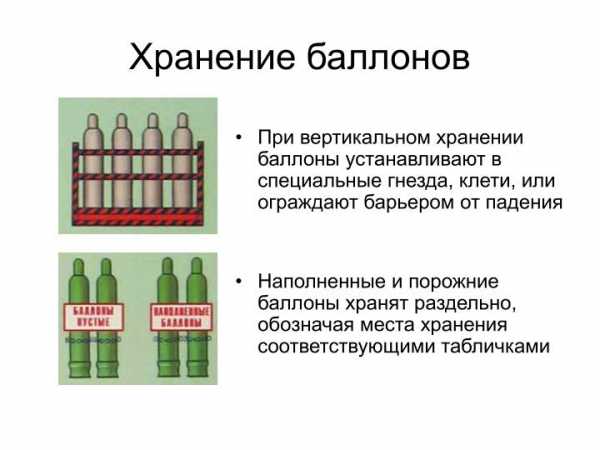
Хранение баллонов
В частности, весь рабочий и инженерно-технический персонал должен пройти должный теоретический и практический инструктаж. Сосуды, содержащие газ, хранят или в отдельных помещениях (зданиях), или допустимо их хранение и на открытом пространстве, но в этом случае, они должны быть ограждены от воздействия осадков и солнца.
Между тем хранить в одном помещении (здании) емкости с кислородом и горючими газами запрещено!
Емкости с газом могут быть установлены, для дальнейшей эксплуатации, не ближе чем на один метр к источникам тепла. Если для обогрева применяют открытый огонь, то расстояние до баллона не должно быть меньше 5 метров.
Виды и устройство вентилей
Несмотря на то, что все баллоны для хранения и перевозки газов отличаются друг от друга формой, цветом покрытия, объемом и многими другими характеристиками все они имеют одинаковое устройство. Баллон включает в свой состав – кран, бак и пр. Краны могут отличаться друг от друга конструктивными особенностями и материалами, которые были использованы для их производства. Кроме, их разделяют по типу применения – одни применяют для кислорода, другие для пропана, третьи для ацетилена. Соответственно на их поверхность наносят покрытия следующего типа:
- синее;
- красное
- белое.
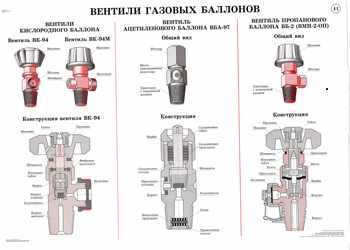
Вентили газовых баллонов
Типовой газовый кран состоит из:
Корпуса, выполненного в виде тройника, состоящего из трех штуцеров, на каждом из них нарезана резьба. На некоторых моделях в корпус вмонтирован предохранительный клапан. Главная задача этого устройства стравливание излишнего давления, возникшего в баллоне.
Штуцера, расположенного внизу предназначенного для присоединения крана к емкости для хранения газа. К верхнему крепится регулирующих маховик (штурвал). К боковому штуцеру присоединяют внешние коммуникации или выполняют закачку газа. Корпус и основные детали выполняют из латуни или стали.
Краны, применяемые для негорючих газов, выполняют с правой резьбой на штуцерах, для тех, которые используют для горючих газов, нарезают левую.
Ремонт вентиля газового баллона
Основные неисправности газовых кранов
На самом деле конструкция газового крана не отличается сложностью и особо в нем ломаться нечему. Но и тем не менее в силу ряда причин, он может или начать пропускать газ или полностью выйти из строя. Одна из причин его поломок – это небрежное отношение со стороны персонала. Например, прикладывание излишних усилий при открывании или закрывании. Это может привести или к срыву резьбы или поломке штока.
Кроме этого, попадание в регулятор посторонних частиц может привести к тому, что они не дадут полностью закрыть затвор, а это неизбежно приведет к утечке газа. В любом случае при малейшем подозрении на наличие дефектов в корпусе или механизме газового крана, баллон необходимо изымать с рабочего места или бытового помещения и отправить его на ремонт.
Да, бесспорно, газовый кран, можно снять с баллона и самостоятельно его осмотреть и при необходимости его продуть или отремонтировать, но нельзя забывать о том, что любая работа с газовым баллоном несет в себе потенциальную опасность. Именно поэтому еден строгий запрет на демонтаж газовых кранов самостоятельно в кустарных условиях. Если есть даже небольшая возможность передать ремонт газового крана в мастерскую, то лучше так и сделать.
Меры предосторожности при замене
Замена вентиля на газовом баллоне должна проводиться с соблюдением определенных мер безопасности, среди них такие, как:
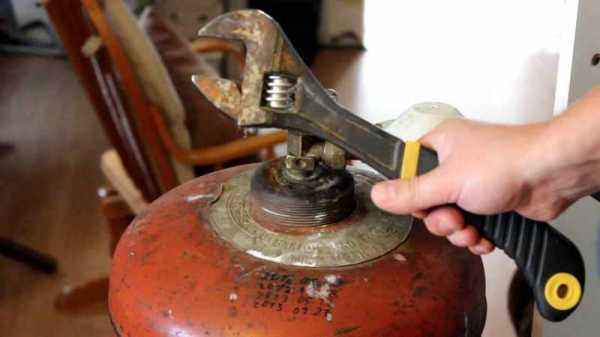
Замена вентиля газового баллона
- Удалить из сосуда остатки газа. Газ допустимо стравливать только на открытом пространстве. Исключение можно сделать только для азота, кислорода и ряда других.
- Рабочее место, на котором будут выполнять работы должно хорошо проветриваться.
- Маховик надо откручивать плавно и с небольшой скоростью.
- Замену вентиля можно выполнять только после уравнивания давления снаружи и в баллоне.
При установке вентиля на штатное место в баллоне необходимо использовать фум-ленту и другие типы герметиков, которые обеспечивают надежность соединения. Надо отметить, что уплотнители любого типа могут создавать определенные сложность при извлечении вентиля. Для облегчения этой задачи допустимо использовать строительный фен.
Выполнять нагрев арматуры, устанавливаемой на баллон допустимо только после стравливания содержимого емкости.
Пошаговая инструкция по замене вентиля
Новый регулировочный клапан не фиксируется к баллону на чистую резьбу. Обязательно необходимо применять уплотнительные материал: герметики или фум-ленту.
Проверка герметичности и завершение работ
По окончании работ по замене вентиля на газовом сосуде необходимо выполнить проверку герметичности вновь собранных соединений. Для этого используют способ, проверенный десятилетиями – нанесение мыльной пены.
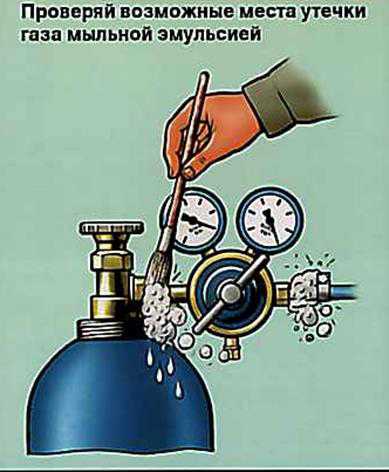
Проверка герметичности и завершение работ
Если стыки собраны некачественно, то в месте утечки газа будут образовываться пузыри и поэтому нужно будет выполнить работу, по сборке по новой.
Зачем делать ремонт газового баллона
Делать или не делать ремонт газовых баллонов определяют на стадии их обследования. В процессе освидетельствования проводят осмотр внешней и внутренних полостей баллона.
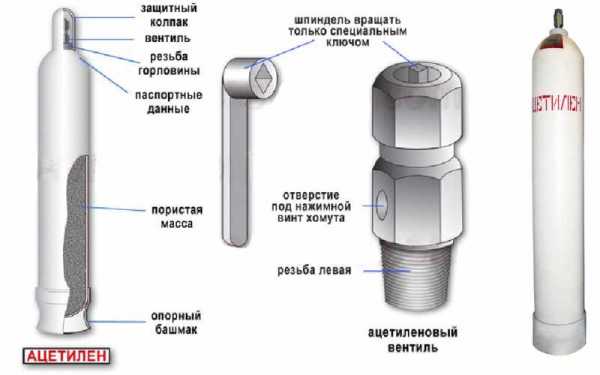
Места для осмотра в газовых баллонах при проверки
Кроме того, осматривают состояние опорного башмака, если его состояние не в состоянии обеспечить вертикальную установку баллона, то эксплуатировать его недопустимо.
Виды ремонта газового баллона в частности, ремонт пропановых баллонов
Ремонт газовых баллонов выполняют на основании данных полученных при освидетельствовании в частности. В частности, при проведении восстановительно-ремонтных работ заменяют, вентили, заменяют башмак, выполняют ремонт горловины и пр.
Кроме того, разумеется, при необходимости, на поверхности сосуда наносят дополнительные надписи. Но надо всегда помнить о том, что иногда безопаснее приобрести новый баллон, чем продолжать эксплуатировать старый.
Чаще всего ремонту подлежат пропановые баллоны. Это связано в первую очередь с тем, что эти баллоны имеют широкое применение и в промышленности, и в быту. Но, владельцы бытовых баллонов, должны быть готовы к тому, что они ремонту не подлежат.
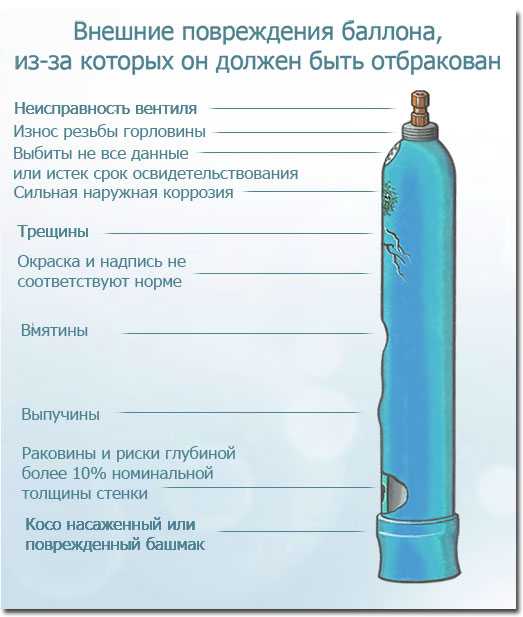
Внешние ддеффекты газового баллона для отбраковывания
Случаи, при которых газовые баллоны не обменивают и к дальнейшему использованию непригодны.
Если на поверхностях баллона выявлены дефекты поверхности, которые превышают 10% от площади поверхности, то такое оборудование ремонту не подлежит и, должно быть, утилизировано.
Если вы нашли ошибку, пожалуйста, выделите фрагмент текста и нажмите Ctrl+Enter.
stankiexpert.ru
Освидетельствование баллонов
Освидетельствование баллонов производится наполнительными станциями или испытательными пунктами при наличии у них:
–помещений для проведения работ;
– технических средств, обеспечивающих возможность проведения освидетельствования;
– приказа о назначении ответственных лиц за освидетельствование;
– подготовленных специалистов;
– инструкции по проведению ТО;
– клейма с шифром, зарегистрированного в органах РТН круглой формы диаметром 12 мм.
Величина пробного давления и время выдержки под пробным давлением устанавливаются изготовителем по ГОСТам и ТУ, пробное давление должно быть не менее чем полуторное рабочее давление.
Освидетельствование включает:
– проверку массы вместимости;
– гидравлическое испытание.
Проверка массы и вместимости бесшовных баллонов до 12 л включительно и свыше 55 л, а также сварных баллонов независимо от вместимости не производится.
При удовлетворительных результатах организация, в которой проведено освидетельствование, выбивает на баллоне своё клеймо круглой формы диаметром 12 мм, дату проведённого и следующего освидетельствования (в одной строке с клеймом0, Клеймо должно иметь шифр, присвоенный органом РТН.
Результаты ТО баллонов вместимостью более 100 л заносятся в паспорт, клейма в этом случае на баллонах не ставятся.
Результаты освидетельствования записываются в журнал испытаний.
Баллоны у которых выявлены трещины, вмятины, отдулины, раковины и риски глубиной более 10% номинальной толщины стенки, надрывы и выщербления, износ резьбы горловины и отсутствуют некоторые паспортные данные, должны быть выбракованы.
Баллоны, у которых обнаружена косая или слабая насадка башмака, к дальнейшему освидетельствованию не допускаются до перенасадки башмака.
Ёмкость баллона определяют по разности между весом баллона, наполненного водой, и весом порожнего баллона или при помощи мерных бачков.
Состояние пористой массы в баллонах для ацетилена проверяется на наполнительных станциях не реже чем через 24 месяца.
Баллоны для ацетилена наполненные пористой массой при освидетельствовании испытывают азотом под давлением 35 кгс/см2 . Чистота азота должна быть не менее 97% по объёму. При проверке пористой массы ставится клеймо с буквами «Пм», удостоверяющее проверку пористой массы.
Запрещается эксплуатация баллонов, на которых выбиты не данные, предусмотренные Правилами.
Бесшовные стандартные баллоны вместимостью от 12 до 55 л при уменьшении массы на 7,5% и выше, а также при увеличении их вместимости более чем на 1% бракуются и изымаются из эксплуатации.
Забракованные баллоны независимо от их назначения должны быть приведены в негодность путём нанесения насечек на резьбе горловины или просверления отверстия на корпусе.
Освидетельствование баллонов должно производиться в отдельных, специально оборудованных помещениях при температуре не ниже 12о С.
Наполненные газом баллоны, находящиеся на длительном хранении, при наступлении очередных сроков периодического освидетельствования подвергаются освидетельствованию в выборочном порядке в количестве не менее 5 шт. из партии до 100 баллонов, 10 шт. – из партии до 500 баллонов и 20 шт. – партии свыше 500 баллонов.
При удовлетворительных результатах освидетельствования срок хранения баллонов устанавливается лицом, проводившим освидетельствование, но не более чем 2 года. Результаты выборочного освидетельствования оформляются соответствующим актом.
При неудовлетворительных результатах освидетельствования производится повторное освидетельствование в таком же количестве.
В случае неудовлетворительных результатов при повторном освидетельствовании дальнейшее хранение все партии баллонов не допускается.
studfiles.net
ТЕХНОЛОГИЧЕСКИЕ ОПЕРАЦИИ | ТИП БАЛЛОНА КПГ/CNG 1,2,3,4 | ТРЕБОВАНИЯ НОРМАТИВНЫХ ДОКУМЕНТОВ (ОБЯЗАТЕЛЬНОЕ/НЕОБЯЗАТЕЛЬНОЕ) |
Откачка газа из баллона перед освидетельствованием | 1,2,3,4 | Необязательно |
Продувка инертным газом | 1,2,3,4 | Обязательное (Приказ Ростехнадзора от 25.03.2014 №116 пункт №500) |
Мойка и осмотр наружной поверхности баллонов | 1,2,3,4 | Обязательное (Приказ Ростехнадзора от 25.03.2014 №116 пункт №393, 493, 500, 501) |
Вывинчивание и завинчивание вентиля в баллон | 1,2,3,4 | Обязательное (Приказ Ростехнадзора от 25.03.2014 №116 пункт №477) |
Осмотр и промывка внутренней поверхности баллона | 1,2,3,4 | Обязательное (Приказ Ростехнадзора от 25.03.2014 №116 пункт №116, 393, 493, 500, 501) |
Осмотр и очистка внутренней поверхности баллона | 1,2 | Обязательное (Приказ Ростехнадзора от 25.03.2014 №116 пункт №500) |
Определение массы и вместимости баллона | 1,2,3 | Обязательное (Приказ Ростехнадзора от 25.03.2014 №116 пункт №493, 393, 503) ГОСТ Р 51753-2001 пункт 10 |
Гидравлические испытания на прочность конструкции баллона | 1,2,3,4 | Обязательное (Приказ Ростехнадзора от 25.03.2014 №116 пункт №493, 393, 169, 395, 504, 177, 179, 180, 181, 184, 185, 186) ГОСТ Р 51753-2001 пункт 10 |
Определение остаточной деформации конструкции баллона | 1,2,3,4 | Обязательное Рабочие инструкции по освидетельствованию баллонов разработанные заводами изготовителями баллонов основаны на требованиях ГОСТ Р 51753-2001, ГОСТ ISO 11439-2014 |
Сушка внутренней поверхности баллонов после гидроиспытаний | 1,2,3,4 | Необязательно |
Очистка наружной поверхности баллона | 1 | Необязательно |
Испытание на герметичность баллона соединения вентиль/баллон | 1,2,3,4 | Обязательное (Приказ Ростехнадзора от 25.03.2014 №116 пункт №396) Рабочие инструкции по освидетельствованию баллонов, основаны на требованиях ГОСТ Р 51753-2001 |
Испытание на герметичность баллона | 4 | Обязательное ГОСТ Р 51753-2001 10.1 |
Маркировка баллона | 1,2 | Обязательное (Приказ Ростехнадзора от 25.03.2014 №116 пункт №490, 494)
|
gassc.com
Техническое обслуживание и освидетельствование газовых баллонов
Категория:
Газобаллонные автомобили
Публикация:
Техническое обслуживание и освидетельствование газовых баллонов
Читать далее:
Техническое обслуживание и освидетельствование газовых баллонов
В процессе эксплуатации газобаллонных автомобилей наружная окраска баллонов из-за попадания на их поверхность влаги, грязи, песка разрушается, что способствует коррозии металла и уменьшает прочность баллонов. Особенно это относится к баллонам, расположенным на раме близко к колесам автомобиля.
Для обеспечения безопасной эксплуатации баллонов и продления срока их службы необходимо периодически окрашивать их наружные поверхности масляной или эмалевой краской красного цвета.
Перед покраской баллоны должны быть тщательно вымыты, очищены от грязи и просушены. Окраска баллонов по мере необходимости производится в специальной мастерской, непосредственно на автомобиле, без демонтажа запорной арматуры и газопроводов, при отсутствии в них газа.
Рекламные предложения на основе ваших интересов:
Автомобильные баллоны как для СНГ, так и СПГ являются сосудами высокого давления, на которые распространяются «Правила устройства и безопасной эксплуатации сосудов, работающих под давлением», утвержденные Госгортехнадзором СССР. Однако следует отметить, что автомобильные баллоны в силу специфики их использования не подлежат регистрации в местных органах Госгортехнадзора и поэтому надзор за их правильной технической эксплуатацией и хранением целиком возложен на автотранспортные предприятия.
Автомобильные баллоны должны подвергаться периодическому освидетельствованию: баллоны для сжиженных нефтяных газов не реже чем через 2 года; баллоны для сжатого природного газа, изготовленные из углеродистой стали, не реже чем через 3 года; баллоны для сжатого природного газа, изготовленные легированной стали, не реже чем через 5 лет (постановление Госгортехнадзора СССР от 24.12.85 № 53). Освидетельствование баллонов производится на специализированных пунктах. Перед освидетельствованием баллоны должны быть освобождены от газа, продегазированы азотом или инертным газом, демонтированы с автомобиля и вместе с запорной арматурой и переходниками, комплектно, по маркам автомобилей направлены на испытательные пункты.
Освидетельствование баллонов включает в себя следующие операции:
— осмотр наружной и внутренней поверхностей баллонов; гидравлические испытания пробным давлением, превосходящим в 1,5 раза рабочее давление;
— проверку герметичности соединений горловины баллона с газовой арматурой.
Кроме этого, у баллонов, предназначенных для сжатого природного газа, при освидетельствовании производится проверка массы и объема.
Баллоны, у которых при осмотре наружной и внутренней поверхностей выявлены трещины, вмятины, раковины и риски глубиной более 10% от номинальной толщины стенки, надрывы, вы-щербления, износ резьбы, и баллоны, у которых отсутствуют некоторые паспортные данные, выбраковываются без проведения гидравлических испытаний.
Масса баллонов для СПГ определяется методом взвешивания, а их емкость по разности масс баллона, наполненного водой и порожнего. При потере массы более 7,5% от указанной на баллоне или увеличении их емкости более 2% баллоны выбраковываются. Выбраковка баллонов производится нанесением насечек на резьбе горловины баллона или просверливанием отверстий на корпусе, что исключает возможность их дальнейшего использования.
Гидравлические испытания баллонов для сжиженных нефтяных газов проводят под давлением 2,4 МПа (24 кгс/см2), создаваемым гидравлическим прессом. Перед испытаниями с баллонов снимают арматуру и на ее место устанавливают заглушки, а сами баллоны полностью заливают водой. Под пробным давлением баллоны выдерживают в течение 1 мин, затем давление снижают до рабочего (16 кгс/см2), осматривают баллон снаружи и обстукивают сварные соединения. Баллоны считаются выдержавшими гидравлические испытания, если не обнаружено признаков разрыва, течи, потения в сварных соединениях и на поверхности металла, видимых остаточных деформаций.
После гидроиспытаний баллоны просушивают и устанавливают арматуру. Затем баллоны в сборе с арматурой подвергают пневматическим испытаниям с целью проверки герметичности Резьбовых соединений и вентилей.
Для этого баллоны заполняют воздухом или инертным газ0 под давлением 1,6 МПа (16 кгс/см2) и опускают в ванну с во дой. Время выдержки 2 мин. Появление пузырьков воздуха н” допускается. Если они все же есть, то после удаления воздуХа (инертного газа) из баллона пытаются устранить неисправность и проводят повторное пневмоиспытание. Если же причиной не-герметичности является недоброкачественность резьбы, то баллон бракуется.
Результаты освидетельствования с указанием выявленных и устраненных неисправностей отмечаются в паспорте баллона. На стенке баллона выбивают дату (месяц и год) произведенного и последующего испытания и ставят клеймо (круглой формы 0 12 мм) организации, проведшей освидетельствование.
Если в процессе эксплуатации газобаллонного автомобиля возникает необходимость произвести замену арматуры баллона или отдельных ее узлов, то после ремонта проводят внеочередные пневматические испытания без регистрации в паспорте баллона.
Гидравлические испытания баллонов для сжатого природного газа проводят под давлением 30 МПа (300 кгс/см2) на специальной установке. Время выдержки под давлением должно быть не менее 2 мин. Баллон считается выдержавшим гидравлические испытания, если не обнаружено течи, слезок, потения на поверхности баллона, признаков разрыва или видимых остаточных деформаций.
После гидравлических испытаний баллон сушат, устанавливают баллонные переходники и вентили. Затем его опрессовывают сжатым воздухом при давлении 20 МПа (200 кгс/см2) для проверки герметичности резьбовых соединений и вентилей.
При достижении удовлетворительных результатов освидетельствования баллоны клеймят, окрашивают, комплектуют по маркам автомобилей и передают на склад готовой продукции.
Баллоны для сжатого природного газа для проведения их освидетельствования доставляются на специализированный пункт из автотранспортных предприятий комплектно в сборе с переходниками и вентилями .с указанием модели автомобиля или его модификации, с которого они демонтированы, а также с заглушками на переходниках, препятствующих попаданию влаги внутрь баллона и повреждению резьбы вентилей и переходников в процессе транспортировки.
Возврат освидетельствованных баллонов потребителю производится обезличенно, но в той же комплектности, что и принятых на освидетельствование. Восполнение выбракованных баллонов должно производиться за счет обменного фонда испытательного пункта.
Рекламные предложения:
Читать далее: Текущей ремонт газовой аппаратуры
Категория: – Газобаллонные автомобили
Главная → Справочник → Статьи → Форум
stroy-technics.ru
1.6.3. Техническое освидетельствование баллонов-сосудов
Условия эксплуатации баллонов-сосудов
на предприятиях общего машиностроения
характеризуются высокой стабильностью
состава рабочей среды и инертностью ее
по отношению к металлу сосуда. Исследования
надежности и безопасности в эксплуатации
баллонов-сосудов проводились на сосудах,
бывших в эксплуатации 10-19 лет. Результаты
исследования подтвердили неизменность
механических свойств металла и циклическую
долговечность сосуда. Исходя из этого,
был установлен срок* технического
освидетельствования стационарно
установленных баллонов-сосудов емкостью
от 100 до 400 л, работающих под давлением
до 35 МПа (350 кгс/см)
сжатого воздуха или азота с точкой росы
ниже минус 35°С, замеренной при давлении
150 кгс/см
,-
через 30 лет с момента их установки.
________________________
* Решение Госгортехнадзора СССР от 19.04.1973 г., № 06-13-10а/494.
По истечении 30-летнего срока эксплуатации баллоны-сосуды подвергаются выборочному техническому освидетельствованию (внутреннему осмотру и гидравлическому испытанию) в количестве 2,5%, но не менее двух от общего числа баллонов-сосудов, присоединенных к одному коллектору и работающих в одинаковых условиях. Положительные результаты выборочного технического освидетельствования распространяются на всю партию (группу) баллонов, для которых устанавливается очередное техническое освидетельствование через 10 лет. Если результаты выборочного технического освидетельствования отрицательны, то вся (группа) партия баллонов-сосудов подлежит внутреннему осмотру и гидравлическому испытанию.
1.7. Дополнительные требования по проведению испытаний при техническом освидетельствовании сосудов и аппаратов блоков разделения воздуха
Расположенные внутри кожуха блока
разделения воздуха сосуды и аппараты
(в дальнейшем – сосуды) с рабочим давлением
выше 0,07 МПа (0,7 кгс/см)
подлежат техническим освидетельствованиям
в соответствии с правилами [1]. Однако
проведение технического освидетельствования
в том виде, как это изложено выше, связано
со значительными трудностями. Поэтому,
исходя из условий эксплуатации указанных
сосудов, их конструктивного и материального
исполнения, а также их размещения в
кожухе, Минхимпром СССР утвердил
инструкцию И 928-74 [77], которая является
дополнением к правилам [1] в части
требований к проведению периодических
и досрочных испытаний при техническом
освидетельствовании сосудов.
В соответствии с указанной инструкцией сосуды блоков разделения воздуха подлежат:
а) гидравлическому испытанию на прочность пробным давлением с предварительным внутренним осмотром в доступных местах – не реже одного раза в 8 лет, если они работают при переменном режиме давления и температуры (регенераторы-вымораживатели и др.), а также другие сосуды, имеющие фланцевые соединения на корпусе и съемные внутренние устройства (адсорберы, фильтры и др.).
Регенераторы, изготовленные из углеродистых сталей, подвергают гидравлическому испытанию пробным давлением с предварительным внутренним осмотром не реже одного раза в два года;
б) пневматическому испытанию на прочность пробным давлением (взамен гидравлического испытания в связи с трудностью удаления влаги из сосудов и возникновением больших напряжений от веса воды в фундаментах и в самих сосудах, а также невозможности проведения внутренних осмотров по конструктивным особенностям) с внешним и внутренним осмотрами в доступных местах, если они работают в условиях стабильных температур и давлений (ректификационные колонны, конденсаторы, переохладители, подогреватели, азотные, кислородные и детандерные теплообменники и т. д.) – не реже одного раза в 8 лет;
в) пневматическому испытанию на плотность рабочим давлением периодически, не реже одного раза в 4 года, при полных отогревах без выемки изоляции и демонтажа трубопроводов.
Гидравлическое испытание на прочность пробным давлением в связи с трудностями удаления влаги, перегрузкой сосуда или фундамента или по конструктивным особенностям может быть заменено пневматическим испытанием тем же давлением по согласованию с местными органами госгортехнадзора.
Первичное техническое освидетельствование сосудов, находившихся в бездействии более одного года или более трех лет складской консервации, производят до монтажа в соответствии с требованиями правил [1]. Испытаниям сосудов на прочность (как гидравлическим, так и пневматическим) предшествуют полный отогрев блока, выемка изоляции из блока и отсоединение всех трубопроводов, обвязывающих испытываемый сосуд или группу сосудов в местах фланцевых соединений.
Для пневматического испытания применяют
воздух с относительной влажностью при
окружающей температуре не более 60%, с
содержанием масла не более 10 мг/м.
Таким же требованиям должен отвечать
воздух, применяемый для продувки и
просушки сосудов после гидравлического
испытания.
Вода, применяемая для гидравлических испытаний, должна удовлетворять требованиям к питьевой воде по ГОСТ 2874-82 [19].
Гидравлические испытания с предварительным внутренним осмотром сосудов производят в соответствии с требованиями правил [1, 4, 6]. После гидравлических испытаний сосуды тщательно сушат и продувают.
Пневматическим испытаниям на прочность предшествуют подготовительные работы. Производятся тщательный внешний и в доступных местах внутренний осмотры сосуда. Сосуд допускается к пневматическому испытанию на прочность на основании акта технического осмотра (составляется при исправном состоянии и положительном заключении по результатам осмотра), рабочей схемы и мероприятий по технике безопасности. Пневматическое испытание проводят для каждого сосуда отдельно. Группа сосудов, имеющих общую обвязку трубопроводов без разъемных соединений в составе высокого, среднего или низкого давления, может быть пневматически испытана на прочность пробным давлением совместно.
До начала пневматических испытаний на кожухе блока открывают и полностью снимают предохранительные мембраны для обеспечения свободного выхода возможных утечек воздуха из испытываемого сосуда. С этой же целью на кожухе блока снимают 2-3 люка со стороны наружной стены здания.
Если сосуды испытывают поочередно, все обвязывающие испытываемый сосуд трубопроводы отсоединяют, в том числе и импульсные линии после вентилей. На штуцерах сосуда устанавливают заглушки, а импульсные линии перекрывают своим вентилем. Заглушки должны соответствовать пробному давлению и иметь хвостовики.
Если испытывают несколько сосудов, входящих в систему одного рабочего давления, имеющих общие обвязочные трубопроводы и арматуру, то их отсоединяют от системы сосудов более низкого давления имеющимися вентилями. При наличии фланцевых соединений на трубопроводах, соединяющих две системы разного рабочего давления, между фланцами устанавливают заглушки с хвостовиками. В этом случае сосуды и трубопроводы смежной системы соединяют с атмосферой через полностью открытые вентили, установленные на ней. Установленные на испытываемой системе импульсные трубки надежно перекрывают своими вентилями. Имеющийся на сосуде предохранительный клапан отсоединяют, а на фланце патрубка сосуда устанавливают заглушку.
Собирают схему пневматических испытаний в соответствии с принципиальной, приведенной на рис. 1.23. Аналогичная схема применяется и при испытании группы сосудов. Диаметр трубопровода 9 для аварийного сброса воздуха из испытываемого сосуда принимают не менее диаметра трубопровода 10, подводящего воздух в испытываемый сосуд, но не менее 20 мм. Условный проход запорного вентиля 8 на трубопроводе 9 принимают равным или больше диаметра трубопровода. На трубопроводе сжатого воздуха от источника давления устанавливают редукционный клапан 6, отрегулированный на испытательное давление, и запорный вентиль 7. Между редукционным клапаном 6 и запорным вентилем 7 устанавливают предохранительный клапан 4, отрегулированный на открытие при давлении на 2-3% больше испытательного давления (пробного). Предохранительный клапан, его установка и пропускная способность должны удовлетворять требованиям правил [1]. Измерение давления в сосуде производят по контрольному манометру 5 по ГОСТ 8625-77Е [26] класса точности 0,4-1. Контроль давления в трубопроводе подвода воздуха в сосуд осуществляют по проверенному рабочему манометру 11. Выбирая манометры, исходят из того, чтобы их шкала была больше в 1,2-1,5 раза испытательного давления, предел измерения которого должен находиться в средней трети шкалы.
Рис. 1.23. Принципиальная схема пневматического испытания на прочность сосудов и аппаратов блока разделения воздуха: 1 – испытываемый сосуд; 2 – кожух блока разделения воздуха; 3 – стена зданий; 4 – предохранительный клапан; 5 – контрольный манометр; 6 – редукционный клапан; 7 – запорный вентиль подачи воздуха; 8 – запорный вентиль сброса воздуха; 9 – трубопровод сброса воздуха; 10 – трубопровод подачи воздуха; 11 – рабочий манометр
Обращают внимание на недопустимость установки между манометром и сосудом запорного органа. Все трубопроводы и арматура, используемые в схеме пневматического испытания, рассчитывают на давление, превышающее испытательное не менее чем на 50%. Для обеспечения безопасности во время испытаний запорную и регулирующую арматуру, предохранительный клапан и манометры выводят в безопасное место, доступное для обслуживания и наблюдения. На время нагружения сосуда пробным давлением не занятых в испытаниях людей удаляют из помещения в безопасное место.
Подъем давления в сосуде начинают путем медленного открытия запорного вентиля 7 на трубопроводе от источника давления. По манометру следят за плавным нарастанием давления. Для проверки плотности испытательной схемы и сосуда предусматривают несколько остановок при промежуточных и рабочих давлениях в соответствии с инструкцией предприятия по проведению испытания. Обязательные остановки предусматривают для сосудов:
с рабочим давлением выше 0,5 МПа (5 кгс/см)
– при промежуточном давлении, равном
половине рабочего;
с рабочим давлением выше 10 МПа (100 кгс/см)
– через каждые 5 МПа (50 кгс/см
).
Повышение давления производят в соответствии с графиком:
#G00-0,1 МПа (0-1 кгс/см
)
15-20 мин
0,1-1,0 МПа (1-10 кгс/см
)
60-90 мин
1,0-5,0 МПа (10-50 кгс/см
)
80-90 мин
5,0-10,0 МПа (50-100 кгс/см
)
30-40 мин
Плотность соединений при промежуточных и рабочем давлении проверяют галоидными течеискателями или обмазкой их мыльным раствором. В случае обнаружения неплотностей испытание прекращают, давление в сосуде плавно снижают до атмосферного, после чего устраняют причины утечек. При необходимости выполнения ремонтных работ для устранения утечек они должны выполняться в соответствии с требованиями правил [1]. Сведения о выявленных дефектных и выполненных работах по их устранению записывают в ремонтный журнал. После устранения выявленных дефектов и контроля качества выполненных при этом работ испытания проводят повторно.
Если при промежуточных и рабочем давлениях не будет обнаружено утечек и видимых деформаций, давление в сосуде плавно поднимают до пробного, величина которого определяется в соответствии с правилами [1]. Пробное давление в сосуде поддерживают постоянным с помощью вентиля 7 в течение 5 минут, после чего вентиль 7 закрывают и открывают вентиль 8 сброса давления воздуха из сосуда, которым регулируют плавное снижение давления в сосуде до рабочего.
Под рабочим давлением сосуд выдерживается не менее 3 часов до выравнивания температуры воздуха в сосуде с температурой окружающей среды. За это время проверяют плотность соединений и осматривают сосуд для выявления возможных видимых деформаций. Температуру воздуха в сосуде и окружающей среды контролируют специальными термопарами либо ртутными термометрами, устанавливаемыми в имеющиеся в сосуде гильзы или укрепленными на стенке сосуда. После выравнивания температуры воздуха в сосуде с температурой окружающей среды и при отсутствии течей и видимых деформаций устанавливают в сосуде давление, точно равное рабочему (по манометру 5). Затем отключают сосуд от источника давления и устанавливают заглушку между трубопроводом и запорным вентилем и наблюдают за падением давления. Величину падения давления определяют по формуле:
,
где – величина падения давления за один час,
в % испытательного давления;
– сумма манометрического и барометрического
давления в начале испытания, МПа;
– то же, в конце испытания, МПа;
– абсолютная температура воздуха в
сосуде в начале испытания, К;
– то же в конце испытания, К;
– продолжительность испытания, ч.
Продолжительность испытания (выдержка) при периодическом техническом освидетельствовании принимают равной 4 часам.
Сосуд признается выдержавшим пневматическое испытание на прочность и пригодным к дальнейшей эксплуатации, если в нем не окажется признаков разрыва, не обнаружится пропуска воздуха через сварные или паяные швы, нет видимых остаточных деформаций после испытания и падение давления в нем за один час не превышает 0,1%.
Результаты испытания сосуда с указанием начальных и конечных температур и давлений, а также длительности испытаний заносят в ремонтный журнал и в специальный акт за подписью лиц, проводивших испытание. Результаты освидетельствования сосуда оформляют в соответствии с правилами [1].
Пневматические испытания сосудов блоков разделения воздуха рабочим давлением проводят для проверки плотности систем высокого, среднего или низкого давлений. Испытания проводят по инструкции, составленной в соответствии с ОСТ 26-04-538-79 [42], но без выемки изоляции и без демонтажа обвязывающих трубопроводов.
Сосуды считаются выдержавшими периодические испытания на плотность, если падение давления при испытании систем высокого, среднего или низкого давления находится в пределах, установленных ОСТ 26-04-538-79 для третьей тепловой опрессовки. Если падение давления превышает установленные нормы, то блок частично или полностью освобождают от изоляции, выявляют и устраняют утечки в трубопроводах, арматуре, сосудах. В том случае, когда выявлены утечки через сварные или паяные соединения или через трещины в корпусе сосуда, производят его ремонт с соблюдением правил [1] c последующим испытанием на прочность и плотность в составе той системы (высокого, среднего или низкого давления), в которую он входит.
studfiles.net
Техническое освидетельствование баллонов
Настоящая методика распространяется на стальные бесшовные баллоны, предназначенные для хранения, транспортирования и использования кислорода, азота, углекислоты, сжатого воздуха вместимостью 40 л на рабочее давление 14,7 МПа, изготовленные по ГОСТ 949.
Методика определяет перечень и последовательность операций, порядок и периодичность проведения технического освидетельствования, а также нормы браковки и требования к ремонту баллонов.
- Общие положения.
- Методика разработана в соответствии с требованиями ПБ 10-115 и ГОСТ 949.
- Целью проведения технического освидетельствования является проверка технического состояния баллона, соответствия его ПБ 10-115, ГОСТ 949 и определение возможности дальнейшей эксплуатации.
- Освидетельствование баллонов должно производиться на наполнительной станции или испытательном пункте, имеющем разрешение органов Госгортехнадзора России на выполнение этих работ.
- Организация, производящая освидетельствование баллонов, должна иметь:
– производственные помещения и технические средства, обеспечивающие возможность качественного проведения освидетельствования;
– приказ о назначении в организации лиц, ответственных за проведение освидетельствования из числа специалистов имеющих соответствующую подготовку;
– методику технического освидетельствования баллонов, разработанную или утвержденную ОАО «РосНИТИ»;
– инструкции по проведению технического освидетельствования баллонов, разработанные на базе методики и утвержденные руководителем организации;
– клеймо с шифром, присвоенное данной организации, и зарегистрированное в органах Госгортехнадзора. - К работам по техническому освидетельствованию и ремонту баллонов могут быть допущены лица не моложе 18 лет, прошедшие медицинское освидетельствование, обученные по соответствующей программе и аттестованные.
- Контрольно- измерительные приборы, инструменты и средства контроля, необходимые для проведения технического освидетельствования, должны проходить метрологическую проверку в соответствии с требованиями нормативной документации.
- Приемка баллонов в ремонт и техническое освидетельствование.
- В ремонт и техническое освидетельствование должны быть направлены баллоны, которые имеют:
– истекший срок периодического освидетельствования;
– неисправность вентиля;
– нарушенную герметичность соединения баллон-вентиль;
– неисправность или отсутствие кольца на горловине;
– неисправность или отсутствие башмака;
– неудовлетворительную окраску наружной поверхности. - Не подлежат освидетельствованию и должны быть выбракованы баллоны, у которых отсутствует хотя бы одно из следующих, установленных ПБ 10-115 ГОСТ 949, паспортных клейм:
– товарный знак завода изготовителя;
– номер баллона;
– фактическая масса порожнего баллона, с точностью до 0,2 кг;
– дата (месяц, год) изготовления и год следующего освидетельствования;
– рабочее давление Р, МПа;
– пробное давление Рпр, МПа;
– фактическая вместимость баллона, с точностью до 0,3 л;
– клеймо ОТК изготовителя круглой формы диаметром 10 мм;
– вид термообработки (N, V). - Технология и правила безопасности проведения ремонтных работ, связанных с неисправностью вентиля, кольца горловины, башмака, должны быть установлены инструкциями, утвержденными руководителем организации, выполняющей эти работы.
- Выбракованные при освидетельствовании баллоны должны быть приведены в негодность путем нанесения насечек на резьбу горловины или сверления отверстия в корпусе и списаны в установленном порядке.
- Периодичность проведения технического свидетельствования баллонов, изготовленных по ГОСТ 949 – 5 лет.
- Дата проведения освидетельствования должна быть указана в паспортной таблице на каждом баллоне.
- Срок службы или возможность дальнейшей эксплуатации баллонов определяется по результатам технического освидетельствования.
- В ремонт и техническое освидетельствование должны быть направлены баллоны, которые имеют:
- Техническое освидетельствование баллонов.
- Последовательность технологических операций.
- Техническое освидетельствование баллонов должно состоять из следующих последовательных операций:
– подготовка баллонов;
– осмотр наружной и внутренней поверхностей баллонов;
– проверка массы и вместимости баллонов;
– гидравлическое испытание баллонов;
– установка вентилей;
– клеймение баллонов;
– оформление результатов технического освидетельствования.
- Техническое освидетельствование баллонов должно состоять из следующих последовательных операций:
- Подготовка баллонов.
- Баллоны, поступившие на участок освидетельствования, должны быть освобождены от рабочей среды.
- Демонтаж вентилей производят после освобождения баллонов от газа.
- Баллоны с неисправными вентилями, из которых невозможно выпустить газ, должны поступать на специально оборудованный пост, где демонтаж вентилей производят по инструкции, утвержденной руководителем организации, проводящей освидетельствование.
- Демонтированные вентили проверяют, при этом исправные вентили передают для дальнейшего использования, а неисправные отправляют в ремонт или бракуют. Вентиль после ремонта должен быть проверен на герметичность.
- Освобожденные от вентилей баллоны должны быть продуты воздухом.
- Наружная и внутренняя поверхности баллонов, освобожденных от вентилей, должны быть очищены от грязи, продуктов коррозии, промыты водой. Жирные и масляные пятна должны быть удалены с помощью растворителя. Резьба горловины должна быть очищена металлической щеткой или метчиком. На наружной и внутренней поверхности баллонов, передаваемых для осмотра, не допускается наличие жирных или масляных пятен, грязи продуктов коррозии.
- Осмотр наружной и внутренней поверхностей баллонов.
- Осмотр наружной и внутренней поверхностей баллонов проводят с целью выявления дефектов, снижающих прочность баллонов, и выявления отклонений от требований ПБ 10-115 и ГОСТ 949.
- Осмотру подвергают 100% наружной и внутренней поверхности баллона, резьбу горловины.
- При осмотре наружной поверхности баллонов используют лупу до 10-ти кратного увеличения. Для определения размеров выявленных дефектов используют универсальные измерительные инструменты – линейки ГОСТ 427, штангенциркули ГОСТ 166, штангенглубиномеры ГОСТ 162 и другие.
- При осмотре внутренней поверхности баллонов используют освещение электрической лампой напряжением не выше 12 В, которую вводят в баллон, или эндоскоп.
- Баллон, на поверхности которого выявлены трещины, плены, раковины, должен быть выбракован. Баллон, на поверхностях которого выявлены вмятины, риски, коррозионные повреждения и другие дефекты глубиной более 10% от номинальной толщины стенки, должен быть выбракован. Значения номинальной толщины стенки баллонов указаны в таблице 1 ГОСТ 949. Номинальная толщина стенки баллонов вместимостью 40 л на рабочее давление 14,7 МПа, изготовленных по ГОСТ 949 из:
– легированной стали – 5,2 мм;
– углеродистой стали – 6,8 мм.
Баллон, у которого выявлены надрывы, выщербления или износ резьбы горловины, должен быть выбракован. Износ резьбы горловины контролируют калибрами по ГОСТ 24998. - На верхней сферической части баллона должны быть выбиты и отчетливо видны паспортные данные, указанные в 2.2. Баллон, у которого отсутствует хотя бы одно из паспортных данных, должен быть выбракован.
- Наружная поверхность баллона должна быть окрашена масляной, эмалевой или нитрокраской:
– голубого цвета – для кислородных баллонов;
– черного цвета – для углекислотных баллонов;
– черного цвета – для баллонов со сжатым воздухом;
– черного цвета с коричневой полосой – для азотных баллонов;
На цилиндрической части баллона должна быть надпись:
– черного цвета «КИСЛОРОД» или «КИСЛОРОД МЕДИЦИНСКИЙ» – для кислородных баллонов;
– желтого цвета «УГЛЕКИСЛОТА» – для углекислотных баллонов;
– белого цвета «СЖАТЫЙ ВОЗДУХ» – для баллонов со сжатым воздухом;
– желтого цвета «АЗОТ» – для азотных баллонов; - При осмотре баллонов проверяют исправность и надежность крепления кольца горловины и башмака.
- Баллон с неисправным или ослабленным кольцом на горловине допускается к дальнейшему освидетельствованию после закрепления кольца или его замены. Закрепление ослабленных или насадка новых колец производится зачеканкой вручную или раздачей торцевой поверхности горловины кольцевым пуансоном на прессе усилием 500-600 Н по инструкции утвержденной руководителем организации, проводящей освидетельствование. Глубина вдавливания пуансона в металл горловины баллона 1 -2 мм. Эскиз кольца горловины приведен на рисунке А. 1 приложения А.
- Баллон с косой или слабой насадкой башмака или неисправным башмаком допускается к дальнейшему освидетельствованию после перенасадки башмака по инструкции, утвержденной руководителем организации, проводящей освидетельствование. Неисправный башмак снимают с баллона на прессе или сбивают вручную. Насадку башмака производят на горизонтальном прессе усилием 800-1000 Н, предварительно нагревая заготовку башмака до температуры от 900 до 1000 °С. Заготовку башмака нарезают из бракованных баллонов или труб диаметром 219 мм с толщиной стенки от 5,2 до 8,9 мм ГОСТ 8732. Длина заготовки (125 +5) мм. Башмак должен быть плотно насажен на баллон с зазором между опорной плоскостью башмака и днищем баллона не менее 10 мм. Допускается перекос опорной поверхности башмака относительно нормали к образующей корпуса баллона не более 7 мм.
- Производить ремонт кольца горловины и башмака разрешается только после выпуска газа, демонтажа вентиля и продувки баллона воздухом.
- Баллон с неотремонтированным кольцом или башмаком к дальнейшему освидетельствованию не допускается и при невозможности ремонта должен быть выбракован.
- Проверка массы и вместимости баллонов.
- Проверка массы и вместимости баллонов проводится с целью определения величины уменьшения массы или увеличения вместимости баллона относительно первоначальных, указанных в паспортной таблице, за счет разрушения или физико-химического превращения металла (коррозии и т.п.).
- Определение фактической массы производят взвешиванием пустого баллона с точностью до 0,2 кг.
- Определение фактической вместимости производят взвешиванием по разности масс пустого и наполненного водой баллона и последующего расчета объема воды по ее массе.
Наполнение баллона водой производят до первых витков резьбы основания горловины. Температура воды, используемой для определения вместимости, должна быть (20 5) °С. При использовании воды с температурой выше указанной, ее объем определяют с учетом температурного расширения, т.е. умножают на температурный коэффициент. Значения температурных коэффициентов приведены в таблице 1.Таблица 1
Температура воды, °С 30 40 50 60 70 80 90 Температурный коэффициент 1,0043 1,0078 1,0121 1,0171 1,1228 1,0292 1,0361 - При уменьшении массы на 7,5% и выше, а также увеличении вместимости более чем на 1,5%, баллон бракуют.
- Гидравлическое испытание баллонов.
- Гидравлическое испытание проводят с целью проверки прочности баллона.
- Баллон нагружают пробным гидравлическим давлением равным полуторному рабочему со скоростью не более 1,0 МПа/с. Температура воды, используемой для гидроиспытания, должна быть от 5 до 40 °С. Разность температур стенки баллона и окружающего воздуха во время испытаний не должна вызывать конденсации влаги на поверхности баллона. При заполнении водой воздух из баллона должен быть удален полностью.
- Давление при гидроиспытании контролируют двумя манометрами одного типа, предела измерений, одинаковой цены делений и одного класса точности не ниже 1,5.
- Время выдержки баллона под пробным давлением должно быть не менее 1 мин. В течение этого времени падение давления в баллоне не допускается. После выдержки давление в баллоне снижают до рабочего и производят осмотр наружной поверхности.
- Баллон считают выдержавшим гидроиспытание если не обнаружено течи, трещин, слезок, потения, видимых остаточных деформаций, падения давления по манометрам.
- Внутренняя поверхность баллона, выдержавшего гидроиспытание, должна быть осушена горячим сухим воздухом. Наличие влаги в баллоне не допускается.
- Баллон, не выдержавший испытание на прочность, выбраковывают.
- Установка вентилей.
- В баллонах, переданных для установки вентилей, не допускается наличие влаги, грязи, продуктов коррозии, жирных и масляных пятен.
- Баллоны и вентили должны быть обезжирены по инструкции утвержденной руководителем организации, проводящей освидетельствование.
Для обезжиривания могут применяться растворители: хладон 113 ГОСТ 23844, хладон 114 ГОСТ 15899 и другие. - После обезжиривания баллоны и вентили должны быть просушены и продуты воздухом или азотом до полного исчезновения запаха растворителя.
- Установка вентилей должна производиться с применением уплотнителя по инструкции, утвержденной руководителем организации, выполняющей освидетельствование.
- Должен применяться уплотнитель, загорание которого в кислороде исключено. Не допускается использование уплотнителя с наличием масла или жира.
- Усилие затяжки, обеспечивающее герметичность резьбового соединения баллон-вентиль, должно соответствовать для резьбы W 27,8 – от 300 до 400 н.м.
На вентиле, установленном в горловину баллона, должно оставаться от 2 до 5 запасных ниток над торцом горловины.
- Клеймение баллонов.
- При удовлетворительных результатах освидетельствования, организация, выполнявшая его, выбивает на корпусе баллона одной строкой свое клеймо, дату проведенного и дату следующего освидетельствования.
- Окраска и осушка баллонов.
- При неудовлетворительном покрытии наружная поверхность баллона должна быть окрашена масляной, эмалевой или нитрокраской:
– голубого цвета – для кислородных баллонов;
– черного цвета – для углекислотных баллонов;
– черного цвета – для баллонов со сжатым воздухом;
– черного цвета с коричневой полосой – для азотных баллонов; - На цилиндрической части корпуса баллона наносят масляной, эмалевой или нитрокраской надпись:
– черного цвета «КИСЛОРОД» или «КИСЛОРОД МЕДИЦИНСКИЙ» – для кислородных баллонов;
– желтого цвета «УГЛЕКИСЛОТА» – для углекислотных баллонов;
– белого цвета «СЖАТЫЙ ВОЗДУХ» – для баллонов со сжатым воздухом;
– желтого цвета «АЗОТ» – для азотных баллонов;
На длину не менее 1/3 окружности. Высота букв надписи должна быть 60 мм. - Окраска баллонов, находящихся под давлением, не допускается.
- Окрашенные баллоны должны находиться на участке до полного высыхания нанесенного покрытия.
- При неудовлетворительном покрытии наружная поверхность баллона должна быть окрашена масляной, эмалевой или нитрокраской:
- Оформление результатов технического освидетельствования.
- Лицо, проводившее освидетельствование, записывает его результаты в журнал испытаний.
- В журнал испытаний должны быть занесены следующие сведения:
– товарный знак изготовителя;
– номер баллона;
– дата (месяц, год) изготовления баллона;
– дата проведенного и следующего освидетельствования;
– масса, выбитая на баллоне, кг;
– масса, установленная при освидетельствовании, кг;
– вместимость, выбитая на баллоне, л;
– вместимость, установленная при освидетельствовании, л;
– рабочее давление Р, МПа;
– пробное давление Рпр, МПа;
– отметка о пригодности баллона;
– подпись лица, проводившего освидетельствование.
- Последовательность технологических операций.
- Требования безопасности.
- Все работы, связанные с ремонтом и техническим освидетельствованием баллонов, должны проводиться в полном соответствии с Правилами ПБ 10-115 и настоящей методикой.
- При выполнении работ по освидетельствованию баллонов следует строго соблюдать последовательность операций в соответствии с настоящей методикой.
- Помещение, в котором проводят работы по освидетельствованию баллонов, должно быть оборудовано средствами контроля загазованности воздушной среды и вытяжной вентиляцией.
- Категорически запрещается:
– находиться во время испытаний вблизи стендов посторонним лицам;
– производить вблизи стендов какие-либо работы, не относящиеся к освидетельствованию баллонов;
– подтягивать соединения на гидравлическом стенде без снижения давления до атмосферного.
ozon51.ru
Техническое освидетельствование газовых баллонов
Категория:
Газобалонное оборудование
Публикация:
Техническое освидетельствование газовых баллонов
Читать далее:
Техническое освидетельствование газовых баллонов
В процессе эксплуатации ГБА наружная окраска баллонов из-за попадания на их поверхность влаги, грязи, песка разрушается, что способствует коррозии металла и уменьшает прочность баллонов. Особенно это относится к баллонам, расположенным на раме близко к колесам автомобиля.
Для безопасной эксплуатации баллонов и продления срока службы необходимо периодически окрашивать их наружные поверхности масляной или эмалевой краской красного цвета. Перед окраской баллоны следует тщательно вымыть, очистить от грязи и просушить. Окраску баллонов по мере необходимости выполняют в специальной мастерской, непосредственно на автомобиле, без демонтажа запорной арматуры и трубопроводов, при отсутствии в них газа.
Газовые баллоны для ГБА (как для СНГ, так и для СПГ) являются сосудами, выдерживающими высокое давление, на которые распространяются «Правила устройства и безопасной эксплуатации сосудов, работающих под давлением», утвержденные Госгортехнадзором СССР. Однако следует отметить, что эти баллоны в силу специфики их использования не подлежат регистрации в местных органах Госгортехнадзора, и поэтому надзор за их правильной технической эксплуатацией и хранением целиком возложен на АТП. Баллоны для ГБА, работающем на СПГ, изготовленные из углеродистой стали, подвергаются периодическому освидетельствованию не реже чем через З.года, а изготовленные из легированной стали — не реже чем через 5 лет (постановление Госгортехнадзора СССР от 24.12.85, № 53). Разрешение на техническое освидетельствование баллонов выдается местными органами Госгортехнадзора СССР после проверки ими наличия производственных помещений, технических средств, обеспечивающих возможность качественного освидетельствования; специально назначенных приказом по станции ТО лиц, ответственных за проведение освидетельствования, из числа инженерно-технических работников, имеющих соответствующую подготовку; инструкции по проведению технического освидетельствования баллонов. При выдаче разрешения на техническое освидетельствование баллонов органы надзора должны зарегистрировать клеймо с соответствующим шифром, присвоенным данной станции ТО и проставляемым на прошедших проверку баллонах. Перед освидетельствованием баллоны должны быть освобождены от газа, продегазированы азотом или инертным газом, демонтированы с автомобиля и вместе с запорной арматурой и переходниками, комплектно по маркам автомобилей направлены на испытательный пункт.
Рекламные предложения на основе ваших интересов:
Освидетельствование баллонов включает в себя следующие операции:
— осмотр наружной и внутренней поверхности баллонов;
— гидравлические испытания пробным давлением, превосходящим в 1,5 раза рабочее;
— проверку герметичности соединений горловины баллона с газовой арматурой. Кроме того, для баллонов, предназначенных для использования СПГ, при освидетельствовании необходимо проверить их массу и вместимость.
Баллоны, у которых при осмотре наружной и внутренней поверхности выявлены трещины, вмятины, раковины и риски глубиной более 10% от номинальной толщины стенки, надрывы, выщербления, износ резьбы, а также отсутствие некоторых паспортных данных, выбраковываются без проведения гидравлических испытаний. Массу баллонов для СПГ определяют методом взвешивания, а их вместимость — по разности масс наполненного водой и порожнего баллона. При потере массы более 7,5% от указанной на баллоне или увеличении их вместимости более 2% баллоны выбраковываются, на резьбу их горловин наносят насечки, просверливают отверстие на корпусе, что исключает возможность их дальнейшего использования.
Гидравлические испытания баллонов для СПГ проводят под давлением 30 МПа (300 кгс/см2) на специальном стенде для гидравлического испытания баллонов (СГИБ). Время выдержки под давлением — не менее 1 мин. Баллон считается выдержавшим гидравлическое испытание, если не обнаружены течь, слезки, потение на поверхности баллона, признаки разрыва или видимые остаточные деформации. После гидравлического проводят пневматические испытания баллонов на том же стенде. Баллоны опрессовывают сжатым воздухом под давлением 20МПа (200 кгс/см2) для проверки герметичности резьбовых соединений и вентилей; продолжительность испытания не более 1 мин.
Рис. 1. Стенд для гидравлического испытания баллонов вместимостью 50 л.
1 — пневмоцилиндры; 2 — тиски; 3 —механизм поворота; 4 — колонка поворотная; 5 — головка ключа; 6 — приводной вал; 7 — электропривод; 8 — пульт управления; 10 — ванна; 11 — пневмоцилиндр; 12 — фиксатор.
Результаты освидетельствований с указанием выявленных и устраненных неисправностей отмечают в паспорте баллона. На стенке баллона выбивают дату (месяц и год) проведенного и последующего испытания и ставят клеймо (круглой формы диаметром 12 мм) организации, проведшей освидетельствование. Если в процессе эксплуатации возникает необходимость замены арматуры баллона, это осуществляют с помощью механического ключа с электроприводом типа ЭПВ. Такой электропривод состоит из взрывобезопасного электродвигателя, червячного редуктора с дублером для ручного управления, путевого выключателя и клеммной коробки во взрывобезопасном исполнении. В крайних случаях выключение электропривода осуществляют путевым выключателем; для ограничения крутящего момента и автоматического отключения электродвигателя имеется механический моментный выключатель.
Замена в условиях АТП переходников, вентилей или манометра высокого давления на баллонах должна производиться в соответствии с действующей нормативно-технической документацией и включать в себя обязательную проверку герметичности и прочности соединений при рабочем давлении 20 МПа (200 кгс/см2) без регистрации в паспорте баллона.
Баллоны для СПГ для проведения их освидетельствования доставляются на специализированный пункт из АТП комплектно, в сборе с переходниками и вентилями, с указанием моделей автомобиля или его модификации, с которого они демонтированы, а также с заглушками на переходниках, препятствующих попаданию влаги внутрь баллона и повреждению резьбы вентилей и переходников в процессе транспортировки. Возврат освидетельствованных баллонов потребителю производится обезличенно, но в той же комплектности, что и принятых на освидетельствование. Восполнение выбракованных баллонов должно производиться за счет обменного фонда испытательного пункта.
Для механизации трудоемких работ по снятию, установке и транспортировке баллонов для ГБА применяют специальное грузоподъемное устройство (модель Н-702), принципиальная схема которого приведена на рис. 3. Оно состоит из кронштейна, захватного устройства и противовеса. Все устройство подвешивают к электромеханической тали с помощью крюка. Газовый баллон 5 вставляют в захватное устройство торцевой частью и переносят к автомобилю, предварительно закрепив прижимом. Баллон вставляют в специальное отверстие ближайшего продольного бруса и подают вперед, насколько позволяет кронштейн, затем устройство освобождают и дальнейшее продвижение в отверстие второго продольного бруса осуществляют вручную.
Рис. 2. Ключ механический К.МВБП для вентилей баллонов.
1 — станина; 2 — пост управления; 3 — кран управления; 4 — устройство для крепления баллона; 5 — пневмотиски; 6 — головка ключа; 7 — электропривод с редуктором.
Рис. 3. Грузоподъемное устройство для газовых баллонов.
1 — противовес; 2 — кронштейн; 3 — крепежный винт с ручкой; 4 — захватное устройство; 5 — баллон высокого давления.
При незначительных подъемах торца баллона или его вращении рекомендуется применять вороток с удлиненной ручкой. При установке баллонов необходимо выдержать определенное расстояние от горловины баллонов до стенок продольных брусьев. После этого баллоны закрепляют хомутами с помощью стяжных болтов с гайками. Под гайку устанавливают плоскую и пружинную шайбу.
Грузоподъемное устройство можно применять и для погрузки, и для разгрузки баллонов на складе готовой продукции.
Рекламные предложения:
Читать далее: Текущий ремонт газовой аппаратуры
Категория: – Газобалонное оборудование
Главная → Справочник → Статьи → Форум
stroy-technics.ru