Отпуск закалка: Что такое закалка, отпуск стали и цвета побежалости
alexxlab | 14.01.2019 | 0 | Разное
Закалка и отпуск в кустарных условиях – Кузнечное дело
Существует несколько способов закалки,один из них закалка с сомоотпуском,применяется она когда нужно закалить только часть детали или инструмента,например лезвие топора,стамески,зубила,боёк молотка.Производится она следующим образом- Нагреваем под закалку часть подлежащая закалке на длинне 30-40мм,выдержка в огне при достижении закалочной температуры небольшая и опускается в воду или масло примерно на длине 15-20мм на 5-10 секунд(возможно и больше для крупного инструмента),затем действуя быстро вынимаем из охладителя и быстро за 2-3 секунды не дольше куском наждачного камня зачищаем охлаждённую часть,тепло двигаясь из неохлаждённой части инструмента начинает производить отпуск и соответственно появляются цвета побежалости,дождались нужный цвет(на это требуется как правило от 3х до 30секунд) охлаждаем окончательно.Вся эта процедура проделывается в темпе,зевать некогда,поэтому вода,брусок наждака и тому подобное должно находиться на расстоянии вытянутой руки.Зубило и кернер перед закалкой затачивается окончательно плюс зачищается на точиле начисто та часть что будет греться(то есть 30-40мм),чтобы легче и быстрее после закалки зачистить .Топор и стамеску перед закалкой затачиваем не до остроты ,а что бы осталась тупая кромка примерно в 1мм,кроме того на лезвии не должно быть зазубрин.Отвёртку , шило,нож подобным образом отпустить не получится,поэтому их закаливают полностью ,а для отпуска применяют другие приёмы,делается это так-В горне греется подходящий брусок металла до 600-700 градусов ,на наковальню ложится кирпич,сверху него разогретый брусок ,клещами берём шило ,отвёртку или нож(предварительно закаленные и зачищеные до блеска) и перемещаем предмет предназначенный для отпуска по разогретому,следить нужно внимательно за цветами побежалости,чтобы отпуск(цвет побежалости) по всей длинне был равномерным.Этим же приёмом пользуемся в случае если при закалке с самоотпуском не удалось равномерно по всей длине отпустить лезвие топора например.
Как осуществляется закалка и отпуск стали
Закалка и отпуск стали проводятся с целью придания сплаву максимальной твердости, прочности и упругости. Обработанный металл обладают лучшими свойствами, чем обыкновенный материал, лучше переносит работу в неблагоприятных условиях и в агрессивных средах. Основной способ закалки состоит в нагревании стали до определенной температуры и поддержании достигнутого уровня в течение установленного времени, а затем резком охлаждении материала. Это позволяет подготовить металл к последующей эксплуатации.
Структура стали после закалки приобретает аустенитный вид. Это означает, что атомы углерода внедряются в кристаллическую решетку железа, что придает сплаву максимальную устойчивость связей и, как следствие, повышенную прочность на износ. Такой способ обработки является одним из самых дешевых методов продления эксплуатационного цикла использования стальных изделий. Он не требует применения дорогостоящих материалов, которые внедряют в сплав для улучшения физических и химических свойств.
Закалка стали производится на том же оборудовании, что и выплавка, поэтому нет необходимости в покупке новых производственных линий или открытии дополнительных заводов. Этот метод был открыт человечеством еще в древние времена. Кузнецы, изготавливая различные изделия, нагревали их при помощи простейших плавильных печей, а затем резко опускали в емкость с холодной водой. Это делало продукцию намного прочнее. Современные виды закалки стали сделали огромный скачок в плане технологий, но суть осталась прежней.
Режимы закалки сталей
Существует несколько режимов закалки сталей. Каждый режим используется для обработки металла под конкретную отрасль производства. Все способы имеют свои достоинства и недостатки, и на текущий момент нет какого-либо универсального метода, лишенного слабых сторон. Поэтому рассмотрим все варианты. Первый подразумевает закалку углеродистой стали с применением одного охладителя. Это самый простой способ, так как не требует соблюдения каких-либо особых условий. Его недостатком является очень сильное закалочное напряжение, которое испытывает металл при обработке. Если неправильно рассчитать температурный режим, то закалка может привести к разрушению сплава.
Второй метод подразумевает охлаждение металла в двух разных средах. Сначала нагретую сталь кладут в воду, где охлаждают до 300 градусов по Цельсию, а затем переносят в масло, где она проходит окончательное охлаждение. Это позволяет значительно снизить напряжение, но метод имеет сложную реализацию, так как трудно рассчитать, когда именно необходимо менять среду охлаждения.
Ступенчатая закалка применяется для небольших предметов. Она делается в несколько этапов. На первом горячее изделие помещают в расплав солей или металлов, который имеет температуру на 50 градусов выше точки начала мартенситного превращения. А когда температуры сплава и среды уравняются, сталь переносят в воду, где она окончательно остывает. Этот метод дает очень хорошие результаты, но требует дополнительных затрат на создание технологических условий.
Изотермическая закалка также подразумевает использование в качестве охлаждающей среды не воды или масла, а расплава солей или щелочей. Но в отличие от предыдущего метода здесь материал проходит полный цикл охлаждения в расплаве. Твердость стали после закалки такого типа является наивысшей, так как аустенит переходит в состояние цементита. Это означает, что атомы углерода еще более глубоко внедряются в структуру железа, создавая очень прочные межмолекулярные связи.
Последний способ – закалка с самоотпуском. Он подразумевает, что нагретую деталь помещают в охлаждающую среду, но не дают ей полностью остыть. Изделие вынимают из охладителя, вследствие чего поверхность снова нагревается за счет сохраненной внутренней теплоты. Такой способ позволяет получать особый вид стали, который сочетает твердость на поверхности и вязкость внутри. Все перечисленные режимы закалки стали используются в равной мере в зависимости от необходимости.
Частичная закалка стали
Также существуют методы частичной закалки одного изделия, когда определенная часть должна быть тверже остального металла. В частности такой обработке подвергается лезвие катаны и многих других режущих инструментов. Для правильной закалки очень важным условием является соблюдение правильного температурного режима на всех технологических этапах. Его выбор зависит от марки обрабатываемой стали и процентном соотношении различных примесей в сплаве.
Температура закалки стали должна быть на 30-50 градусов выше точки мартенситного превращения. Такой уровень позволяет достичь оптимальной активности атомов углерода, которые начинают перемещаться и внедряться в железо на межмолекулярном уровне. Быстрое охлаждение используется, чтобы сохранить этот эффект, так как при постепенной потере температуры углерод постепенно возвращается в исходное состояние и закалка не сохраняется.
Кроме перечисленных режимов существуют также отдельные виды обработки. Один из них – это поверхностная закалка стали. Она подразумевает обработку лишь верхних слоев металла без манипуляций с внутренним строением. Технология абсолютно идентична полной закалке, но необходимость нагрева лишь поверхностного слоя заставляет корректировать способы.
Способы повехностной закалки стали
Существует 4 основных метода поверхностной закалки: с индукционным нагревом при помощи высокочастотного тока, с электроконтактным нагревом, с нагревом при помощи газопламенных горелок и закалку при помощи использования электролитического раствора. Для обработки мелких деталей зачастую используют последний метод.
Для средних изделий применяются первые два, а для крупногабаритных элементов лучше всего подходит нагрев при помощи газовых горелок. Для охлаждения используют те же жидкости, что и при полной закалке. В редких случаях, для особо крупных конструкций применяются газовые холодильные установки. И последний вид обработки называется неполной закалкой стали. Он подразумевает медленное охлаждение нагретого материала, в результате чего часть атомов углерода успевают покинуть молекулярную сетку железа и вернуться к нормальному состоянию.
Таким образом, образуется частично закаленный металл. Такой тип обработки применяется, когда необходимо специально оставить в структуре материала слабые места. Этот подход используется в автомобильной промышленности для создания так называемой контролируемой деформации при аварии. Он разработан специально для уменьшения травматизма пассажиров и снижения количества смертельных случаев.
Закалка, отжиг, отпуск — Сделай сам – портал самодельщиков
Часто приходится сталкиваться с необходимостью повысить прочность и твердость металла или готового изделия, иногда же, наоборот, желательно сделать металл более мягким, легче поддающимся обработке. И в том, и в другом случае нужный эффект достигается термической обработкой, заключающейся в нагреве материала до определенной температуры с последующим быстрым (или медленным) охлаждением. Таким образом, путем изменения режима термической обработки удается получать различные физико-механические свойства металлов. К основным операциям термической обработки относят отжиг, нормализацию, закалку и отпуск (рис.).
Режимы термической обработки: ПЗ и ПО – полные закалка и отжиг; НЗ и НО – неполные закалка и отжиг; ВО, СО и НО – высокий, средний и низкий отступ соответственно
Как известно, термической обработке с целью изменения структуры и свойств подвергают многие металлы и их сплавы. Например, чтобы восстановить пластичность сплава на основе меди, подвергнутого холодной деформации, сплав подвергают отжигу. Правда, другой вид термической обработки – закалка для многих медных сплавов невозможен. Но здесь мы не будем говорить о термообработке цветных металлов, а рассмотрим (очень коротко!) технологию термической обработки стали (ее основных видов). Сразу поясним, что сплавы на основе железа (то есть стали), содержащие от 0,02 до 0,8% углерода, называют доэвтектоидными, сталь с 0,8% – эвтектоидной, а сплавы, где присутствует от 0,8 до 2,14%С – заэвтектоидными. Еще в тексте упомянуты температуры АС1 и АС3, значения которых для конкретной марки стали можно найти в любом соответствующем справочнике.
Отжиг заключается в нагреве стали (доэвтектоидной – выше температуры АС3, а заэвтектоидной – выше температуры АС1) с последующим медленным охлаждением вместе с печью. Если нагреть доэвтектоидную сталь выше АС1, но ниже АС3, то полной перекристаллизации металла не произойдет. Такую термическую обработку называют неполным отжигом, который применяют для улучшения обрабатываемости резанием доэвтектоидных сталей (см. таблицу 1). Подобный отжиг конструкционных легированных сталей проводят при 750…770°С с последующим охлаждением со скоростью 30…60°С/ч, причем чем выше легированность стали, тем медленнее ее охлаждение. Отжиг снижает твердость и повышает вязкость стали, улучшает ее обрабатываемость и стабилизирует физические свойства.
Таблица 1. Режимы отжига
Нормализация отличается от отжига повышенной скоростью охлаждения, которое проводят не в печи, а на воздухе (спокойном или движущемся). Нормализацию осуществляют для размельчения зерна металла и повышения прочности последнего. Эффект, получаемый от нормализации, зависит от состава стали. Для низкоуглеродистых сталей нормализацию применяют вместо отжига. Нормализация с целью размельчения зерен обеспечивает большую производительность при последующей обработке металла резанием, а также позволяет получить более чистую поверхность обрабатываемых деталей. Нормализацию с последующим высоким отпуском (при температуре 600…650°С) часто используют для исправления структуры легированных сталей, применяя ее вместо полного отжига, так как производительность этих двух операций (нормализации и отпуска) выше, чем одного отжига.
Закалка заключается в нагреве стали на 30…50°С выше температур АС3 (для доэвтектоидных сталей) или АС1 (для заэвтектоидных сталей), некоторой выдержке металла при соответствующей температуре для завершения фазовых превращений и последующем его охлаждении со скоростью выше критической. При нагреве стали выше температуры АС3 закалку называют полной, при нагреве выше АС1 (на 30…50°С) – неполной. Неполную закалку (НЗ) для доэвтектоидных сталей, как правило, не применяют, а используют ее главным образом при термической обработке инструментальных сталей (см. таблицу 2). Охлаждение углеродистых сталей проводят чаще всего в воде, а легированных – в масле или в других средах. Закалка не является окончательной операцией термической обработки. Дело в том, что в результате закалки сталь приобретает хрупкость и в ней возрастают внутренние напряжения. Чтобы избавиться от того и другого, сталь после закалки обязательно отпускают. Инструментальную сталь, в основном, подвергают подобной термообработке (закалке и отпуску) для повышения твердости, износостойкости и прочности, а конструкционную – как для увеличения прочности и твердости, так и для придания ей достаточной высокой пластичности и вязкости.
Таблица 2. Режимы закалки
Охлаждение при закалке не должно вызывать закалочных дефектов: трещин, деформаций, коробления и возникновения высоких растягивающих остаточных напряжений в поверхностных слоях. Чаще всего для закалки используют кипящие жидкости: воду, водные растворы солей и щелочей, масла. Вода как охлаждающая среда имеет существенные недостатки: с одной стороны, высокая скорость охлаждения воды нередко приводит к образованию закалочных дефектов; с другой стороны, с повышением температуры ее закалочная способность резко ухудшается. Наиболее высокой и равномерной охлаждающей способностью отличаются холодные 8…12%-ные водные растворы соли или едкого натра, которые хорошо зарекомендовали себя на практике.
Легированные стали закаливают в минеральном масле. Преимуществом масла является небольшая скорость охлаждения, что снижает возможность возникновения закалочных дефектов. К недостаткам масла следует отнести повышенную его способность воспламеняться (температура вспышки 165…300°С), а также довольно высокую стоимость. Температуру масла поддерживают в пределах 60…90°С (вязкость масла в этом случае оказывается минимальной).
Отпуск стали заключается в нагреве закаленной стали до температуры ниже АС1, выдержке при заданной температуре и последующем охлаждении с определенной скоростью. Отпуск является окончательной операцией термической обработки, в результате которой сталь приобретает оптимальные механические свойства (см. таблицу 3). Кроме того, отпуск полностью или частично устраняет внутренние напряжения, возникающие при закалке. Эти напряжения снимаются тем полнее, чем выше температура отпуска.
Таблица 3. Режимы отпуска
Скорость охлаждения после отпуска в значительной степени влияет на значение остаточных напряжений в металле. Чем медленнее протекает охлаждение, тем меньше становятся остаточные напряжения. По этой причине изделия сложной формы во избежание их коробления после отпуска при высоких температурах следует охлаждать медленно, а изделия из легированных сталей, склонных к отпускной хрупкости, после отпуска при 500…650°С во всех случаях следует охлаждать быстро. Различают три вида отпуска: низкий, средний и высокий.
Низкий (низкотемпературный) отпуск проводят с нагревом до 250°С. При этом снижаются внутренние напряжения в металле, повышается его прочность и немного улучшается вязкость, причем все это осуществляется без заметного снижения твердости стали. Закаленная сталь, содержащая 0,5…1,3% углерода, после низкого отпуска сохраняет твердость в пределах HRC 58. ..63, а следовательно, характеризуется высокой износоустойчивостью. Однако такое изделие (если оно не имеет вязкой сердцевины) не выдерживает значительных динамических нагрузок. Низкотемпературному отпуску подвергают режущий и измерительный инструмент из углеродистых и низколегированных сталей, а также детали, претерпевшие поверхностную закалку, цементацию. Продолжительность отпуска обычно 1…2,5 ч.
Средний (среднетемпературный) отпуск ведут при температуре 350…500°С. Применяют этот отпуск, главным образом, при термообработке сталей для пружин и рессор. В результате подобного отпуска обеспечиваются высокие пределы упругости и выносливости металла. Твердость стали HRC 39…44.
Высокий (высокотемпературный) отпуск осуществляют при температуре 500…600°С. Высокий отпуск обеспечивает у стали наилучшее соотношение прочности и вязкости.
Термическую обработку, состоящую из закалки и высокого отпуска, называют улучшением. Обычно улучшению подвергают среднеуглеродистые конструкционные стали, к которым предъявляются высокие требования по пределам текучести и выносливости, а также по ударной вязкости. Улучшение значительно повышает конструктивную прочность стали, уменьшая чувствительность к концентраторам напряжений, развитию трещин, снижает температуру верхнего и нижнего порога хладколомкости. Отпуск при температуре 550…600°С почти полностью снимает остаточные напряжения, возникающие при закалке.
Уже многие годы при термообработке стальных изделий я пользуюсь приведенными таблицами, составленными в студенческие годы при написании курсового проекта. Думаю, что они могут быть полезными и другим мастеровым людям.
В заключение немного о маркировке и классификации сталей по назначению. Единой мировой системы маркировки сталей не существует. В России марки углеродистой стали обыкновенного качества обозначаются буквами Ст и номером (Ст0, Ст1, Ст2 и т.д.). В данном случае цифры обозначают порядковый номер стали. В зависимости от особенностей производства эти стали получают тот или иной индекс. Например, СтГпс – полуспокойная сталь с повышенным содержанием Mn. Качественные углеродистые стали маркируют двузначными числами, показывающими среднее содержание в них С в сотых долях процента: 05, 08, 45 и т.д. Инструментальные углеродистые стали обозначают буквой У с цифрами (У7, У8, У10 и т.д.), где цифры – содержание углерода в десятых долях процента. Обозначение легированных сталей включает в себя буквы, указывающие, какие компоненты входят в состав стали, и цифры, характеризующие их содержание. Заметим, что первые цифры марки обозначают среднее содержание в стали С, причем у конструкционных сталей это содержание дано в сотых долях процента, а у инструментальных и нержавеющих – в десятых долях процента. Так, сталь марки 3X13 содержит 0,3%С и 13%Cr. При этом, если содержание легирующего элемента не превышает 1,5%, то цифра за соответствующей буквой не ставится. О применении тех или иных сталей можно судить по таблице 4.
Таблица 4. Классификация сталей по назначению и рекомендуемые режимы окончательной термической обработки
закалка с отпуском – это… Что такое закалка с отпуском?
- закалка с отпуском
3.3.3 закалка с отпуском (quenching and tempering): Термообработка, состоящая из упрочнения закалкой, за которой следует отпуск стали. Упрочнение закалкой предполагает аустенизацию, за которой следует охлаждение при таких условиях, когда аустенит переходит в мартенсит и, возможно, в бейнит.
Отпуск предполагает нагревание один или более раз до температуры, не превышающей температуру рекристаллизации (Ас1), а также выдержку при этой температуре, затем охлаждение с заданной скоростью так, чтобы структура изменилась и были достигнуты требуемые свойства.
Буквенное обозначение данного условия поставки – Q.
3.
3.3 закалка с отпуском (quenching and tempering): Термообработка, включающая упрочнение стали закалкой, с последующим отпуском.
Примечание 1 – Упрочнение закалкой предполагает аустенизацию стали, за которой следует охлаждение при таких условиях, когда аустенит переходит в более или менее полный мартенсит и возможно бейнит.
Примечание 2 – Отпуск стали предполагает нагревание один или более раз до температуры, которая меньше нижней температуры рекристаллизации (Ac1), а также поддержание этой температуры, за которой следует охлаждение с заданной скоростью так, чтобы структура модифицировалась и были достигнуты требуемые свойства.
Примечание 3 – Буквенное обозначение данного условия поставки – Q.
Словарь-справочник терминов нормативно-технической документации. academic.ru. 2015.
- закалка и отпуск
- закалка с последующим высоким отпуском
Смотреть что такое “закалка с отпуском” в других словарях:
Закалка (металлургия) — Закалка вид термической обработки материалов (металлы, их сплавы, стекло), заключающийся в их нагреве выше критической температуры (температуры изменения типа кристаллической решетки, т. е. полиморфного превращения, либо температуры, при которой… … Википедия
закалка (стали) с последующим отпуском — — [http://slovarionline.ru/anglo russkiy slovar neftegazovoy promyishlennosti/] Тематики нефтегазовая промышленность EN tempering … Справочник технического переводчика
закалка с последующим отпуском — — [http://slovarionline.ru/anglo russkiy slovar neftegazovoy promyishlennosti/] Тематики нефтегазовая промышленность EN temper … Справочник технического переводчика
закалка и отпуск — 4.10 закалка и отпуск (quenching and tempering): Термообработка, включающая закалочное упрочнение с последующим отпуском.
Источник: ГОСТ Р ИСО 3183 2009: Трубы стальные для трубопроводов нефтяной и газовой промышленности. Общие технические… … Словарь-справочник терминов нормативно-технической документации
закалка с последующим высоким отпуском — 3.5 закалка с последующим высоким отпуском; Q + Т: Нагрев горячекатаной стали до температуры выше температуры Ас3на 30 °С 100 °С с последующим быстрым охлаждением (закалка), затем нагрев закаленной стали ниже температуры Ас1, выдержка при этой… … Словарь-справочник терминов нормативно-технической документации
Закалка — термическая обработка материалов, заключающаяся в их нагреве и последующем быстром охлаждении с целью фиксации высокотемпературного состояния материала или предотвращения (подавления) нежелательных процессов, происходящих при его… … Большая советская энциклопедия
закалка с прокатного нагрева с последующим высоким отпуском — 3.7 закалка с прокатного нагрева с последующим высоким отпуском; Qпн + Т: Прокатка стали при температурах выше температуры Аr3с последующим ускоренным охлаждением до значений температуры ниже температуры завершения γ ® αпревращений и нагревом… … Словарь-справочник терминов нормативно-технической документации
закалка — термическая обработка металла, заключающаяся в его нагреве и последующем быстром охлаждении. В результате закалки происходит фиксация высокотемпературного состояния металла и подавляются нежелательные процессы, происходящие при его медленном… … Энциклопедия техники
Объёмно-поверхностная закалка — Эта статья или раздел носит ярко выраженный рекламный характер. Это не соответствует правилам Википедии. Вы можете помочь проекту … Википедия
Объемно-поверхностная закалка — (металлов) это современная технология закалки стали. Данная технология разработана ведущими российскими учеными, является новым словом в области упрочнения металлов.
Разработка этой технологии это результат более чем 10 летнего труда… … Википедия
Слесарно-монтажный ручной инструмент / Hand tools UNIOR | Каталог UNIOR 2014 Профессиональный ручной инструмент (Всего 522 стр.) | |||||
203 Каталог UNIOR 2014 Профессиональный инструмент Стр.203 | |||||
Термическая обработка (закалка и отпуск) термообработку осуществляют для улучшения структуры стали, повышения твёрдости и вязкости инструмента и придания прочих свойств, требуемых для обеспечения работы при очень высоких нагрузках. 18. Пескоструйная обработка очистка поверхности перед последующим хромированием важна для обеспечения качества и длительной защиты поверхности. 19. Хромирование захваты съёмника покрывают тонким и прочным слоем диоксида хрома, что защищает их от воздействия коррозии,делает более износостойкими. При этом инструмент приобретает привлекательный внешний вид. СБОРКА 20. Окончательная сборка окончательную сборку инструмента осуществляет обученный и высококвалифицированный персонал, что обеспечивает функциональность и высокое качество съёмников Unior. Длительный срок эксплуатации Съёмники UNIOR изготовлены из качественной конструкционной стали.Кованые захваты и траверса обладают повышенной прочностью. Ходовой винт подвергают специальной термохимической обработке. Простота в использовании Съёмники UNIOR позволяют произвести безопасный и максимально быстрый демонтаж подшипников, втулок и шестерёнок. J Отличительные особенности съёмников UNIOR полированная поверхность винт целиком подвергнут закалке с высоким отпуском материал конструкционная углеродистая сталь захваты устанавливаются в двух позициях захваты, корпус, винт кованые хромирование или цинковое покрытие Съёмники с двумя захватами 204 205 Съёмники с тремя захватами 205 206 Съёмники с пятью захватами и экстракторы Специальные съёмники 206 207 207 211 | |||||
См. ![]() | |||||
Отклонения размеров / Fit tolerance table | Соотношение твердостей Таблица / Hardness equivalent table | ||||
Типы резьб / Thread types and applications | Аналоги сталей / Workpiece material conversion table | ||||
Отверстия под резьбу / Tap drill sizes | Обороты в скорость / Surface speed to RPM conversion | ||||
Перевод дюймов в мм / Inches to mm Conversion table | Перевод единиц в систему СИ / SI unit conversion table | ||||
UNIOR | |||||
| |||||
Каталог UNIOR 2015 Инструмент (450 страниц) | |||||
Каталог UNIOR 2014 Инструмент (522 страницы) | |||||
Каталог UNIOR 2010 Инструмент (268 страниц) | |||||
Каталоги ручного инструмента / Hand tools catalogs | |||||
Каталог UNIOR 2014 Профессиональный ручной инструмент (Всего 522 стр.) | |||||
| |||||
200 | 201 Вставки, биты 6715Е6,3 Переходник ф j магнитный 1/4 -6,3 L 603028 E6.3 (1/4 ) 77 32 Отвёртка ударная с набором вставок размеры ящика: 197x 105 x 38 + | 202 | 204 | 205 | 206 Съёмники с тремя захватами щ Съёмник с двумя перемещающимися захватами материал: конструкционная углеродистая сталь кованый, целиком подвергнут закалк |
Закалка Отпуск – Энциклопедия по машиностроению XXL
Таким образом, к четырем основным видам термической обработки (отжиг I рода, отжиг II рода, закалка, отпуск) могут быть добавлены две сложные обработки.
Конструкционные стали подвергают двойной упрочняющей термической обработке — закалке + отпуску, причем среднеуглеродистые — обычно высокому отпуску (улучшению), низкоуглеродистые — низкому. [c.370]
В низкоуглеродистой стали после закалки получается достаточно пластичный мартенсит. Отпуск при 15(f снимает (конечно, только частично) внутренние напряжения и несколько повышает пластичность. В лучших сортах низкоуглеродистых легированных сталей при такой термической обработке (закалка + отпуск при 150°С) достигается высокий комплекс [c.372]
Марка сталл Отжиг Закалка Отпуск [c.417]
В конструктивно-технологической группе деталей в качестве условий при выборе операций учитывают разновидности термической обработки, например для ступенчатых валов нормализацию, улучшение, закалку, отпуск и др. для корпусных деталей из чугуна — искусственное старение и т. д. Эти операции назначаются в технологический маршрут при выполнении условий, вытекающих из технических требований на изготовление детали. Условия, характеризующие шероховатость обрабатываемых поверхностей, определяются характером производства. Например, при обработке наружных цилиндрических поверхностей валов выполнение условия, обе- [c.97]
Коррозионная стойкость хромистых сталей зависит также от режимов термической их обработки. Наиболее распространенным видом термической обработки, обеспечивающим высокую сопротивляемость коррозии хромистых сталей, содержащих хром в количестве около 13%, является закалка с отпуском. При нагреве сталей рассматриваемого типа до высоких температур (950—1000°С) достигаются условия, при которых карбиды хрома переходят в твердый раствор. Если фиксировать это состояние быстрым охлаждением (в масле или на воздухе), то углерод удерживается в твердом растворе. Следующий за процессом закалки отпуск при низкой температуре лишь снимает напряжения закалочного происхождения, незначительно изменяя основную структуру, и таким образом общая сопротивляемость стали коррозионным разрушениям сохраняется.
[c.216]
Основными видами термической обработки, различно изменяющими структуру и свойства стали и назначаемыми в зависимости от требований, предъявляемых к полуфабрикатам (отливки, поковки, прокат п т, д.) и готовыми изделиями, являются отжиг, нормализация, закалка, отпуск. [c.191]
С Мп 51 Прочие легирующие элементы закалка отпуск [c.186]
Нормализация Закалка, отпуск [c.255]
ЗОХГС (закалка, отпуск 680 С) 1,34 — 0,01 1,2 — [c.620]
Нормализация Закалка. Отпуск [c.70]
Нормализация Закалка. Отпуск 100—300 До 100 315 490 315 490 570 655 14 16 35 45 34 59 167-207 212—248 [c.76]
Листы и полосы (Образцы поперечные) Листы после закалки, отпуска (Образцы поперечные) От 10 до 32 вкл. 325 450 21 [c.99]
Листы после закалки, отпуска (Образцы поперечные) От 10 до 60 вкл. 49 29 [c.108]
После закалки, отпуск [c.118]
Пруток диаметром 115 мм. Закалка. Отпуск [c.135]
Поковки. Закалка. Отпуск До 100 395 395 615 17 45 59 187—229 [c.136]
Поковки. Закалка. Отпуск 100—300 До 100 395 490 395 490 615 655 15 16 40 45 54 59 187—229 212—248 [c.139]
I группу составляют простые углеродистые стали. Их обычно применяют в нормализованно.м состоянии или без термической обработки. О том, какие при этом получаются свойства, говорилось выше (см. главу XVI, п. 1). В некоторых случаях для деталей диаметром 10—15 мм, в которых может быть по. у-чена более или менее удовлетворительная прокаливаемость и относительно небольшое коробление, может быть применена углеродистая сталь с улучшающей термической обработкой (закалка отпуск при 500—650°С). [c.386]
При обычной термической обработке (закалка + отпуск) прочность определяется содержанием углерода н температурой отпуска.
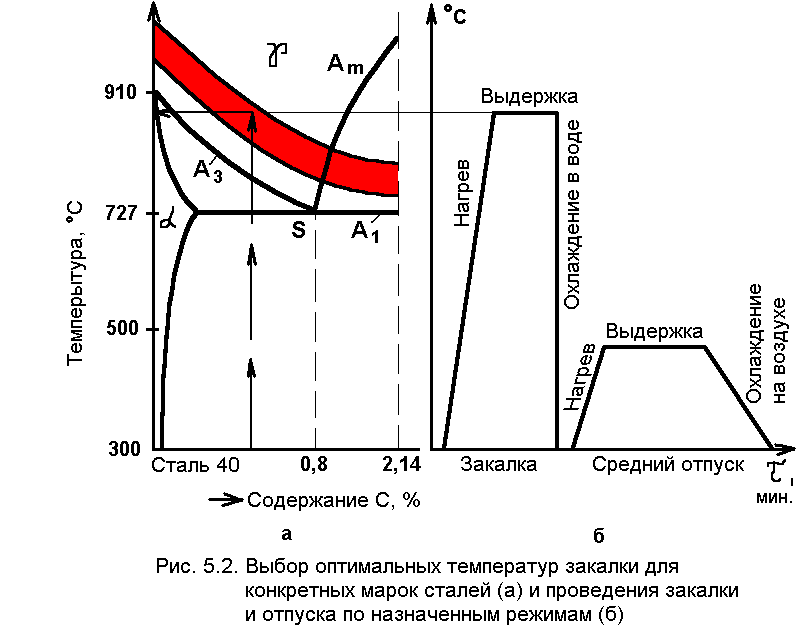
В качестве примера приведем сталь, содержащую 0,3%С, 9% Ni, 4% Со, обладающую после обычной термической обработки (закалка + отпуск 200°( ) при прочности (сгв), равной 160 кгс/,мм , высоким комллоксом пластических и вязких. свойств 1)) = 60 /о, Г5о = —ПО°С, йр =2,5 кгс-м/см , что равноценно стали 18Х2Н4ВА, яо при прочности ее. Ов= 130 кгс/мм . [c.392]
Поскольку термпчгской обработкой закалка + отпуск 600°С невозможно значительно повысить прочностные свойства СтЗ, то в тех случаях, когда необходимо иметь более высокий предел текучести, применяют легированные стали. Эти стали обычно называют низколегированными, или строительными сталями повышенной прочности, В отличие от конструкционных легированных сталей, строительные стали повышенной прочности у потребителей не подвергаются термической обработке, т. е. структура и служебные характеристики формируются при производстве сталей. [c.401]
В закаленной стали тетрагональность мартенсита и внутренние напряжения создают 1начительную хрупкость, поэтому после закалки отпуск является обязательной операцией. Температура отпуска определится величиной рабочей твердости, которой должен обладать инструмент. Рекомендуемая температура отпуска для некоторых видов инструмента некоторых видов показана в табл. 46.
[c.413]
Отжиг, закалка и отпуск инструментальной стали
Инструментам, которые оказались сломанными, неосторожно поврежденными нагревом или были подвергнуты переделке, требуется восстановление рабочих качеств поверхности или режущего края.
Сначала инструмент нужно отжечь путем его нагрева до вишнево-красного каления. Эта температура еще называется “критической”. Ее можно определить, поднося магнит к нагреваемому докрасна изделию. Когда исчезает притяжение, температура отжига достигнута. Затем сталь следует медленно охладить на воздухе. Мягкую сталь обрабатывать несложно.
Нагрев металла до “критической температуры” с последующим быстрым охлаждением в воде или масле приводит к повышению твердости металла. Металл становится твердым, но одновременно слишком хрупким, чтобы инструментом можно было работать.
Если поверхность металла очистить и заполировать, можно будет заметить тонкие переходы цветов (цвета побежалости), обусловленные образованием оксидной пленки, которые могут служить индикатором температуры.
Нагревать нужно осторожно и на некотором удалении от рабочей кромки. Наблюдайте за изменением цветов по мере их продвижения вдоль инструмента. В тот момент, когда нужный цвет достигнет рабочей кромки, быстро охладите инструмент в воде или масле.
Отпуск углеродистой стали: сопоставление цвета побежалости с температурой
Температура | Цвет | Отпускаются | |
°F | °С | ||
200° | 93° | Нет цвета | |
400° | 204° | Очень бледный желтый | |
430° | 221° | Желтый | Клинки бритв |
440° | 227° | Светлый соломенно-желтый | Клинки штихелей |
450° | 232° | Соломенно-желтый | Шаберы |
460° | 238° | Насыщенный соломенно-желтый | |
470° | 243° | Темно-желтый | Инструменты для обработки дерева и зубила |
490° | 254° | Коричнево-желтый | Сверла |
500° | 260° | Коричневый | |
510° | 266° | Коричнево-фиолетовый | |
530° | 277° | Пурпурный | Пунзелы и инструменты для чеканки |
540° | 282° | Фиолетовый | |
550° | 288° | Темно-голубой | Пружины |
560° | 293° | Голубой | |
570° | 299° | Васильково-голубой | |
600° | 316° | Ярко-голубой | Зубила для горячей обработки |
620° | 327° | Серо-голубой | |
630° | 332° | Сине-зеленый до серого |
Закалка – Закалка и отпуск
Закалка – это процесс термообработки при низких температурах (ниже A1), обычно выполняемый после нейтральной закалки, двойной закалки, атмосферной цементации, нитроцементации или индукционной закалки для достижения желаемого соотношения твердость / вязкость.
Преимущества
Максимальная твердость марки стали, которая достигается закалкой, придает материалу низкую вязкость. Отпуск снижает твердость материала и увеличивает ударную вязкость.Благодаря отпуску вы можете адаптировать свойства материалов (соотношение твердости / вязкости) к конкретному применению.
Применение и материалы
Темперирование можно разделить на три основные группы:
- Низкотемпературный (160-300 ° C): используется для цементируемых деталей и инструментальных сталей для холодной обработки. Обычно требования к твердости составляют около 60 HRC.
- Закалка пружинных сталей (300-500 ° C): используется для пружинных сталей или аналогичных применений. Обычно требования к твердости составляют около 45 HRC.
- Высокотемпературная (500 ° C или выше): используется для закаленной и отпущенной стали, инструментальной стали для горячей обработки и быстрорежущей стали. Твердость будет варьироваться от 300HB до 65HRC в зависимости от материала.
Подробности процесса
Температура отпуска может варьироваться в зависимости от требований и марки стали от 160 ° C до 500 ° C или выше. Закалка обычно выполняется в печах, которые могут быть оборудованы опцией защитного газа. Защитный газ предотвратит окисление поверхности во время процесса и в основном используется при более высоких температурах.Для некоторых типов сталей большое значение имеет время выдержки при температуре отпуска; увеличенное время выдержки будет соответствовать более высокой температуре. В зависимости от марки стали в определенных температурных интервалах может возникать такое явление, как отпускная хрупкость. Обычно следует избегать отпуска в пределах этого температурного интервала. Эти области показаны в каталогах стали поставщиков стали, а также указаны наиболее подходящие температуры в зависимости от требований к твердости.
Что такое закалка? | Metal Supermarkets
Закалка – это процесс термообработки, который изменяет механические свойства (обычно пластичность и твердость) и снимает внутренние напряжения стали.Отпуск позволяет углю, захваченному мартенситной микроструктурой, диспергироваться и позволяет снять внутренние напряжения со стали, которые могли быть созданы в результате предыдущих операций.
Процесс закалки
Отпуск выполняется путем повышения температуры стали до заданного значения ниже ее более низкой критической температуры, обычно после операции закалки. По достижении этой температуры она сохраняется в течение определенного времени. Точная температура и время зависят от нескольких факторов, таких как тип стали и требуемые механические свойства.
Чтобы довести сталь до критической температуры, необходимо использовать какое-либо нагревательное устройство. Обычные устройства включают газовые печи, электрические печи сопротивления или индукционные печи. Часто этот нагрев выполняется в вакууме или с помощью инертного газа, чтобы защитить сталь от окисления. Как только печь достигает желаемой температуры, наступает время выдержки. По истечении времени выдержки печь выключают, и стали дают остыть с заданной скоростью.
Почему сталь закаляется?
Закалка стали после процесса закалки позволяет достичь среднего уровня твердости и прочности.Это достигается за счет диффузии углерода внутри микроструктуры стали. Когда сталь закаляется, она может стать чрезмерно хрупкой и твердой. Однако, когда сталь не закалена, она может не обладать прочностью или стойкостью к истиранию, необходимой для предполагаемого применения. Отпуск также улучшает обрабатываемость и формуемость закаленной стали и может снизить риск растрескивания или разрушения стали из-за внутренних напряжений.
Когда используется темперирование?
- Закалка чаще всего используется после операции закалки.Нагревание углеродистой стали и быстрая закалка могут сделать ее слишком твердой и хрупкой. Закалка может частично восстановить его пластичность.
- Отпуск может снизить твердость и снять напряжение свариваемого компонента. Сварные швы могут образовывать локализованную зону, которая затвердевает из-за высокой температуры процесса сварки. Это может привести к нежелательным механическим свойствам и остаточным напряжениям, которые могут способствовать водородному растрескиванию. Темперирование помогает предотвратить это.
- Упрочненные материалы часто требуют отпуска.Материалы могут упрочняться в результате таких процессов, как штамповка, гибка, формовка, сверление или прокатка. Упрочненные материалы имеют большое количество остаточных напряжений, которые можно уменьшить с помощью процесса отпуска.
Metal Supermarkets – крупнейший в мире поставщик мелкосерийного металла с более чем 85 обычными магазинами в США, Канаде и Великобритании. Мы эксперты по металлу и обеспечиваем качественное обслуживание клиентов и продукцию с 1985 года.
В Metal Supermarkets мы поставляем широкий ассортимент металлов для различных областей применения.В нашем ассортименте: нержавеющая сталь, легированная сталь, оцинкованная сталь, инструментальная сталь, алюминий, латунь, бронза и медь.
Наша горячекатаная и холоднокатаная сталь доступна в широком диапазоне форм, включая пруток, трубы, листы и пластины. Мы можем разрезать металл в точном соответствии с вашими требованиями.
Посетите одно из 85 наших офисов в Северной Америке сегодня.
В чем разница между отпуском и отжигом?
Закалка и отжиг – это оба метода термической обработки металла.Целью термической обработки является намеренное изменение физических (и химических) свойств металла с целью его подготовки к производству. Термическая обработка может повлиять на многие свойства металлического изделия, включая прочность, твердость, формуемость, пластичность, пластичность и обрабатываемость.
Отжиг и отпуск: термическая обработка металлических изделий
Обычно на термическую обработку металла влияют три переменных:
- Температура, до которой он нагревается
- Продолжительность выдержки при этой температуре
- Способ или скорость охлаждения
В зависимости от типа металла, подвергаемого термообработке, и желаемого результата эти переменные будут меняться.Но, тем не менее, эффективная термообработка требует точного контроля над всеми тремя.
Несмотря на то, что существует множество методов термической обработки металла, сегодня я расскажу только о двух из них: отжиг и отпуск.
Процесс отжига
Как работает отжиг?
При отжиге металл нагревается до идеальной температуры, а затем выдерживается при этой температуре в течение заданного периода времени. Скорость охлаждения для отжига находится на медленном конце спектра.Например, если вы готовили что-то в духовке и вместо того, чтобы извлекать это по окончании времени приготовления, вы позволяли ему остыть в духовке, это похоже на отжиг.
Основная причина, по которой металлический продукт подвергается отжигу, состоит в том, чтобы уменьшить его твердость / сделать его более мягким. Таким образом, его будет легче обрабатывать. Кроме того, некоторые металлы подвергаются отжигу для увеличения электропроводности.
Три этапа отжига
Процесс отжига включает три отдельных этапа:
- Восстановление
- Рекристаллизация
- Рост зерна
Давайте подробнее рассмотрим, что происходит на каждом этапе.
Этап отжига 1: восстановление
Первым этапом процесса отжига является восстановление. Во время восстановления металл нагревается. Обычно используемым нагревательным устройством является печь – для отжига металла можно использовать газовые, электрические и индукционные печи. Целью стадии восстановления является нагрев металла до температуры, при которой его внутренние структуры расслабляются.
Этап отжига 2: рекристаллизация
Второй этап процесса отжига – рекристаллизация. Во время рекристаллизации металл нагревается еще больше.Оптимальным вариантом является достижение температуры, превышающей температуру рекристаллизации металлов, но без превышения температуры плавления.
Когда материал удерживается в этой зоне наилучшего восприятия, новые зерна могут начать развиваться во внутренней структуре металла без образования ранее существовавших напряжений.
Этап отжига 3: рост зерен
Третья стадия процесса отжига – рост зерна. На этой заключительной стадии те зерна, которые начали развиваться на второй стадии, способны полностью развиваться.Контролируя процесс охлаждения и поддерживая определенную скорость, рост зерна приведет к получению более пластичного и менее твердого материала.
Процесс закалки
Как работает закалка?
Закалка – это термообработка, которая улучшает вязкость твердых, хрупких сталей, чтобы они сохраняли свои свойства во время обработки. Для отпуска требуется, чтобы металл был нагрет до температуры ниже так называемой нижней критической температуры – в зависимости от сплава эта температура может составлять от 400 до 1300 ° F.
Когда достигается более низкая критическая температура стали, эта температура поддерживается в течение заданного времени. Тип обрабатываемой стали определяет критическую температуру и время выдержки материала при этой температуре.
Другие переменные, влияющие на отпуск, включают продолжительность выдержки металла при критической температуре и скорость охлаждения. Оба эти фактора влияют на механические свойства материала.
Визуальный эффект закалки
Также известно, что закалка влияет на цвета, которые появляются на поверхности стали. Эти цвета, которые могут варьироваться от светло-желтого до оттенков синего, используются для обозначения окончательных свойств стали. Например, наши улучшенные пружинные стали – 1075 и 1095 – имеют синий цвет, но из-за явных различий в контакте с углеродом их оттенок синего и другие физические свойства различаются. Вы можете просмотреть подробное сравнение здесь.
Закалка и отпуск ножевой стали – Sandvik Materials Technology
Закалка – это способ сделать сталь ножа более твердой.Если сначала нагреть ножевую сталь до 1050–1090 ° C (1922–1994 ° F), а затем быстро охладить (закалить)), ножевая сталь станет намного тверже, но при этом станет более хрупкой.
Для уменьшения хрупкости материал закаливают, обычно нагревая его до 175–350 ° C (347–662 ° F) в течение 2 часов, что приводит к твердости 53–63 HRC и хорошему балансу между сохранением резкости, шлифуемость и вязкость.
Закалка должна проводиться в течение разумного периода времени после затвердевания, предпочтительно в течение часа или около того.Жизненно важно, чтобы лезвие остыло до комнатной температуры перед началом отпуска. В противном случае превращение в мартенсит будет прервано, и результаты упрочнения могут ухудшиться.
Более высокая температура отпуска дает несколько более мягкий материал с более высокой вязкостью, тогда как более низкая температура отпуска дает более твердый и несколько более хрупкий материал, как показано на рисунке ниже.
Кемпинговый нож или нож для выживания, например, можно закалить при температуре 350 ° C (662 ° F), чтобы он мог выдерживать грубое обращение, не ломаясь.С другой стороны, если ожидается, что нож будет иметь острую кромку, его можно вместо этого закалить при 175 ° C (347 ° F) для максимальной твердости.
Температуры отпуска ниже 175 ° C (347 ° F) следует использовать только в исключительных случаях, когда предъявляются экстремальные требования к высокой твердости, поскольку очень низкие температуры отпуска приводят к очень хрупкому материалу. Точно так же следует избегать отпуска при температурах выше 350 ° C (662 ° F), поскольку это может привести к хрупкости и снижению коррозионной стойкости.Обратите внимание, что если закаленное лезвие подвергается воздействию температур выше температуры отпуска (например, во время шлифования), свойства ножа будут ухудшены.
Правильно выполненная закалка приведет к хорошему балансу между твердостью, ударной вязкостью и коррозионной стойкостью готового лезвия ножа.
Дополнительные сведения о закалке
Учебное пособие: Процесс отпуска
Закалка
Закалка – это процесс, выполняемый после закалки.Детали, закаленные закалкой, часто бывают слишком хрупкими. Эта хрупкость вызвана преобладанием мартенсита. Эта хрупкость устраняется отпуском. В результате отпуска достигается желаемое сочетание твердости, пластичности, ударной вязкости, прочности и структурной стабильности. Не следует путать закалку с закалкой проката – эта закалка является показателем степени выполненной холодной работы.
Механизм отпуска зависит от стали и температуры отпуска. Преобладающий мартенсит представляет собой несколько нестабильную структуру.При нагревании атомы углерода диффундируют из мартенсита с образованием осадка карбида и одновременного образования феррита и цементита, который является стабильной формой. Например, инструментальные стали теряют от 2 до 4 баллов твердости по шкале С Роквелла. Несмотря на то, что приносится в жертву небольшая прочность, ударная вязкость (измеряемая по ударной вязкости) существенно увеличивается. Пружины и подобные детали должны быть намного жестче – они закалены до гораздо меньшей твердости.
Закалка производится сразу после закалки.Когда после закалки сталь остынет примерно до 40 ° C (104 ° F), она готова к отпуску. Деталь повторно нагревается до температуры от 150 до 400 ° C (от 302 до 752 ° F). В этой области образуется более мягкая и жесткая структура троостита. В качестве альтернативы, сталь можно нагреть до температуры от 400 до 700 ° C (от 752 до 1292 ° F), что приведет к более мягкой структуре, известной как сорбит. Он имеет меньшую прочность, чем троостит, но большую пластичность и вязкость.
Нагрев для отпуска лучше всего осуществлять путем погружения деталей в масло, для отпуска до 350 ° C (662 ° F), а затем нагревания масла вместе с деталями до соответствующей температуры.Нагревание в ванне также гарантирует, что вся деталь будет иметь одинаковую температуру и подвергнуться одинаковому отпуску. Для температур выше 350 ° C (662 ° F) лучше всего использовать ванну с нитратными солями. Соляные ванны можно нагревать до 625 ° C (1157 ° F). Независимо от ванны, важно постепенно нагревать ее, чтобы избежать растрескивания стали. После достижения желаемой температуры детали выдерживают при этой температуре около 2 часов, затем вынимают из ванны и охлаждают на неподвижном воздухе.
Аустемперирование
Austempering – это метод закалки.Деталь не закаляется мартенситным превращением. Вместо этого материал закаливают выше температуры, когда мартенсит образует MS, около 315 ° C (600 ° F). Его выдерживают до этой температуры, пока вся часть не достигнет этой температуры. Поскольку деталь выдерживается дольше при этой температуре, аустенит превращается в бейнит. Бейнит достаточно твердый, поэтому отпадает необходимость в дальнейшем отпуске, а склонность к растрескиванию значительно снижается.
Закалка
Мартенситный отпуск аналогичен аустемперированию, за исключением того, что деталь медленно охлаждается посредством мартенситного превращения.Структура представляет собой мартенсит, который необходимо закалить так же, как и мартенсит, который образуется в результате быстрой закалки. Самым большим преимуществом закалки по сравнению с быстрой закалкой является меньшая деформация и тенденция к растрескиванию.
Sinotech предлагает исключительно широкий спектр вторичных процессов , которые применяются к металлам, сформированным в горячих или холодных процессах. Sinotech ‘ Инженеры по качеству поставщиков определяют доступность процесса на металлообрабатывающем предприятии, а также качество.Если внутренние вторичные процессы не соответствуют стандартам Sinotech, то процессы выполняются на проверенных Sinotech и квалифицированных сторонних предприятиях вторичной обработки. Sinotech провела аудит, квалифицировала и работала с QS-9000 и сертифицированными ISO предприятиями вторичной обработки в Китае, Тайване и Корее более 12 лет. Sinotech стремится управлять вашим проектом на месте и доставлять вам детали по более низким ценам, но с таким же качеством, обслуживанием и условиями, как у местного поставщика.
Закалка и отпуск в одной камере
Закалка закаленных сталей – один из важнейших процессов термообработки, используемых при производстве деталей. Индукционный отпуск обеспечивает твердость и механические свойства, аналогичные тем, которые получаются при обычном отпуске в печи. Развитие производства ячеек привело к объединению индукционной закалки и отпуска в той же производственной ячейке, где выполняются другие производственные операции, такие как резка стали, шлифование, механическая обработка и сверление.Таким образом, детали производятся полностью, включая термообработку в ячейке, по одной детали за раз. Это поддается бережливому производству. Временные циклы закалки и отпуска имеют гораздо меньшую продолжительность, чем другие процессы в ячейке. Оптические пирометры часто используются для измерения температуры поверхности деталей, достигаемой во время закалки и отпуска, и хранятся в компьютере для использования в расчетах статистического контроля процесса (SPC).
Способы закалки
Существует пять методов индукционной закалки: однократная, непрерывная прогрессивная, вертикальная развертка, конвейерная закалка и закалка в провисе.
Одиночный нагрев или статический нагрев для отпуска лучше всего использовать для коротких деталей или там, где требуется закалка в узкой зоне. В этом методе используются отдельные источники питания и катушки как для процесса закалки, так и для процесса отпуска. Перед запуском цикла отпуска заготовке необходимо дать полностью остыть до температуры ниже 150 ° F.
Непрерывная прогрессивная обработка используется для обработки закаленных и отпущенных прутков и труб (см. Рисунок 1). Детали длиной от 8 до 24 футов обычно обрабатываются встык.Эти индукционные системы распространены в крупных производственных цехах. При этом связка незакаленных стержней, трубы или трубок индексируется для положительного привода, и отдельные части проходят через серию индукционных катушек с контролируемой скоростью движения. Детали слегка поворачиваются при перемещении через змеевики, пока не достигнут температуры аустенитизации (приблизительно 1700 ° F), а затем проходят через серию закалочных камер для охлаждения. После охлаждения они проходят через ряд низкочастотных индукционных катушек меньшей мощности с той же скоростью поступательного движения.После нагрева для отпуска заготовки индексируются на столе медленного охлаждения, а затем в окончательную сборку. Усовершенствованные компьютерные средства управления в сочетании с оптическими пирометрами обеспечивают повторяемость процесса, поскольку все рецепты процесса и контрольные пределы хранятся в компьютере для каждого типа и диаметра материала.
Изображение 1: Сплошной пруток постепенно нагревается с помощью серии индукционных катушек до температуры аустенизации перед закалкой и отпуском.Вертикальное сканирование обычно используется для индукционной закалки заготовки за один проход.Второе сканирование затем используется для индукционного отпуска после того, как температура заготовки стабилизируется ниже 150 ° F. Закалка не включается во время цикла отпуска, чтобы позволить теплу проникнуть глубже, чем в исходном цикле закалки. Второй проход для закалки использует только около 30 процентов мощности, используемой для закалки, и более медленную (30-50 процентов) скорость сканирования, чем при закалке.
Конвейер темперирования использует змеевик канального типа с очень низкой плотностью мощности в течение длительного периода времени (см. Изображение 2).Катушка использует отдельный источник питания и более низкую частоту, чем используется для закалки. После того, как деталь затвердеет и температура детали выровняется с температурой закалочной среды, деталь поступает на конвейер с контролируемой скоростью поступательного движения и повторно нагревается до требуемой температуры отпуска. Обычно на конвейере в шпильке или канальном змеевике одновременно нагревается более одной детали, при этом питание остается включенным. Низкая удельная мощность позволяет выравнивать температуру по всей детали за счет теплопроводности.
Изображение 2: Канальная катушка использует отдельный низкочастотный источник питания для одновременного нагрева нескольких деталей, пока детали перемещаются вперед по конвейеру.Закалка провисания (оставляющая остаточное тепло от процесса закалки в заготовке) регулярно используется в одиночных дробилках большого диаметра и в горизонтальных сканерах. При однократном упрочнении больших деталей в детали присутствует значительное количество тепла. Объем и время закалки распылением контролируются для получения полностью трансформированной микроструктуры, в которой закалка прекращается и позволяет теплу от субкорпуса возвращаться к упрочненному корпусу для снижения напряжения и твердости.
Например, штоки цилиндров из углеродистой стали SAE 1045 подвергаются индукционной закалке с использованием горизонтального сканера. Типичная глубина корпуса составляет от 1,5 до 2,5 мм. Поступательное движение стержня через закалку со скоростью до 3 дюймов в секунду позволяет контролировать температуру на выходе стержня в диапазоне 350 ° F для снижения твердости после закалки с 64 до 60 HRC. В этом методе используется остаточное тепло, и дальнейший отпуск не требуется. Жесткий контроль температуры закалки, давления закалки и потока закалки осуществляется с помощью компьютера и ПЛК.Чем больше диаметр, тем легче контролировать температуру на выходе. Сложнее контролировать стержни меньшего диаметра, потому что они имеют меньше общего остаточного тепла и, следовательно, меньшее окно процесса.
В чем разница между отпуском и отжигом?
Закалка и отжиг – это процессы термической обработки, которые изменяют физические и химические свойства металлов, чтобы подготовить их к производству. Разница между этими двумя процессами связана с температурой и скоростью охлаждения, при этом отпуск происходит при более низких температурах, но с более быстрым временем охлаждения.
Обе термообработки используются для обработки стали, хотя отжиг дает более мягкую сталь, с которой легче работать, а отпуск дает менее хрупкую версию, которая широко используется в строительстве и промышленности.
Чтобы понять разницу между процессами, важно сначала понять преимущества нагрева стали как метода обработки металла.
Что такое термообработка?
Термическая обработка используется для изменения физических и механических свойств металлов без изменения их формы.Нагревание металла увеличивает желаемые характеристики, позволяя проводить дальнейшую обработку.
К распространенным причинам термической обработки относятся:
- Повышенная пластичность
- Повышенная эластичность
- Повышенная формуемость
- Повышенная твердость
- Улучшенная обработка
- Повышенная сила
- Повышенная вязкость
Воздействие на термически обработанные металлы определяется тремя факторами:
- Удельная температура нагрева металла до
- Продолжительность выдержки металла при этой температуре
- Используемый процесс охлаждения
Эффективная термообработка требует, чтобы все три фактора контролировались независимо от типа обрабатываемого металла и желаемых результатов.
Что такое процесс закалки?
Закалка – это процесс, при котором металл точно нагревается до температуры ниже критической, часто на воздухе, в вакууме или в инертной атмосфере. Точная температура варьируется в зависимости от степени твердости, которую необходимо уменьшить. Высокие температуры уменьшат твердость и увеличат эластичность и пластичность, но могут вызвать снижение текучести и прочности на разрыв. Более низкие температуры сохранят большую часть твердости, но уменьшат хрупкость.
Закалка требует постепенного нагрева металла для предотвращения растрескивания. После достижения желаемой температуры она поддерживается в течение фиксированного периода времени. Приблизительный ориентир для этого предлагает один час на дюйм толщины, хотя это зависит от типа обрабатываемого металла. Тепло снимает внутренние напряжения в металле, после чего металл подвергается быстрому охлаждению на воздухе.
Визуальная оценка закалки
Можно получить визуальное представление о влиянии отпуска на сталь, оценивая цвета, которые появляются на поверхности закаленной стали.Цвета варьируются от светло-желтого до различных оттенков синего, в зависимости от таких факторов, как контакт с углеродом. Это позволяет оценить окончательные свойства стали.
Приложения для закалки
Как упоминалось выше, отпуск используется для повышения ударной вязкости сплавов железа, включая сталь. Отпуск обычно проводят после закалки, чтобы уменьшить излишнюю твердость, поскольку необработанная сталь очень твердая, но слишком хрупкая для большинства промышленных применений.
Отпуск может изменить пластичность, твердость, прочность, структурную стабильность и ударную вязкость.
Что такое процесс отжига?
Отжиг включает нагрев металла до заданной температуры перед охлаждением материала с медленной и контролируемой скоростью. Металл помещается в печь, достаточно большую, чтобы воздух мог циркулировать вокруг заготовки.
Металл нагревают до температуры, при которой возможна рекристаллизация. Это вызывает любые дефекты, вызванные деформацией или ремонтом. После того, как металл выдерживается при требуемом нагреве в течение фиксированного периода времени, он очень медленно охлаждается до комнатной температуры.Низкая скорость охлаждения обеспечивает максимальную мягкость и улучшает микроструктуру. Это можно сделать, просто выключив духовку и оставив металл внутри остыть естественным образом, или погрузив нагретый материал в песок, золу или другое вещество с низкой теплопроводностью.
Отжиг можно разбить на три этапа; восстановление, перекристаллизация и рост зерен:
Восстановление
Стадия восстановления – это когда металл нагревается так, что внутренние структуры материала расслабляются.
Перекристаллизация
По мере увеличения нагрева металл достигает температуры, при которой происходит рекристаллизация, позволяя новым зернам развиваться во внутренней структуре металла без образования напряжений. Температура для этого должна быть выше температуры рекристаллизации металла, но ниже температуры плавления.
Рост зерна
Контролируемая скорость охлаждения способствует развитию зерен, образовавшихся во время рекристаллизации, в результате получается более пластичный и менее твердый материал.
Приложения для отжига
Отжиг в основном используется для снижения твердости / увеличения мягкости металла, однако его также можно использовать для увеличения электропроводности. Этот процесс позволяет металлу достаточно размягчиться для холодной обработки, улучшить обрабатываемость и восстановить пластичность.
Это важно для нескольких применений, поскольку без отжига холодная обработка может вызвать растрескивание. В процессе отжига снимаются механические напряжения, возникающие при механической обработке или шлифовании, что позволяет обрабатывать металл дальше.
Этот процесс обычно используется для стали, но также может применяться для металлов, включая алюминий, латунь и медь.
Различия между закаленной и отожженной сталью
Хотя оба процесса представляют собой термическую обработку, они следуют разным правилам для получения разных результатов для разных целей.
Закаленная сталь используется там, где первостепенное значение имеют прочность, ударная вязкость и эластичность. Сюда входят крупномасштабные строительные работы, промышленное оборудование и автомобильные трансмиссии.Закалка делает эти применения возможными и снижает любую связанную с ними опасность.
При отжиге получаются более мягкие металлы, которые можно использовать для изделий, которым не требуется выдерживать значительные нагрузки. Сюда входят многие предметы домашнего обихода и другие повседневные товары.