Плотность стали низкоуглеродистой: Плотность стали: справочные таблицы, метод определения
alexxlab | 26.12.1991 | 0 | Разное
Низкоуглеродистая сталь – марки, свойства, применение
Низкоуглеродистая сталь – марки, свойства, применение- Обновлено 10 октября 2020 г.
Большая часть производства в той или иной степени применяют низкоуглеродистую сталь. Строительство, машиностроение, станкостроение – вот неполный список отраслей, где она активно применяется.
Состав по ГОСТ
Сталь – это сплав железа с углеродом, процент содержания последнего при этом не должно превышать 2,14%. Все что выше этого значения – уже чугун. Низкоуглеродистая сталь отличается пониженным содержанием углерода, что откладывает свой отпечаток как на механические, так технологические свойства.
Существует несколько стандартов, которые регулируют состав углеродистых сплавов. Среди них наиболее востребованы ГОСТ 380-2005 и ГОСТ 1050-90. Согласно им низкоуглеродистой может называться сталь, которая включает в себя:
- Углерод (до 0,25%). Он позволяет термически упрочнять сталь, в результате чего твердость и временное сопротивление металла может увеличиться в несколько раз.
- Кремний (до 0,35%) Он улучшает механические характеристики, особенно, это касается ударной вязкости и прочности. Также увеличение кремния в сплаве положительно сказывается на свариваемости.
- Марганец (до 0,8%) относится к группе полезных примесей. По своему молекулярному строению схож с кислородом и активно вступает с ним химическую связь, что препятствует образованию оксида железа. Сталь, легированная марганцем, более однородна по составу, лучше справляется с динамическими нагрузками, становиться податливей к термическому упрочнению.
- Сера (до 0,06%) – вредная примесь. Делает металл красноломким, усложняет обработку давлением: ковкой, прокаткой и т.д. Снижает плотность сварного шва. Повышает отпускную хрупкость.
- Фосфор (до 0,08%) ответственен за появление хладноломкости. Искажает кристаллическую структуру стали. Снижает ее ударную вязкость. Ухудшает прочность и выносливость металла. Но не всегда фосфор является вредной примесью. В некоторых случаях его добавление оправдано, т.
к. он увеличивает податливость металла резанию. Но все равно, общее количество его не должно превышать 0,1%.
- Кислород – самый нежелательный элемент в составе стали. Введение 0,001% кислорода способно снизить прочность металла на 50%. Препятствует обработки сплава режущим инструментом.
- Азот. После попадания его в металл, образует нитриды железа – очень хрупкое соединение, которое снижают как прочностные, так и технологические свойства сплава.
Особенности низкоуглеродистых сталей
Низкоуглеродистая сталь по сравнению с другими сталями крайне пластична. Их относительно удельное сопротивление на сжатие составляет 23-35% в зависимости от процента содержания углерода в составе. Чем его больше, тем пластичность ниже.
Все марки низкоуглеродистых сталей имеют первую категорию свариваемости.
Процесс сварки не требует сложных подготовительных операций: прогрева поверхности, обезжиривания и т. д. Сварной шов получается плотным, при работе на сжатие по прочности сравним с цельным металлом. Пониженная углеродистая сталь поддается всем видам сварки: от обычной электродуговой до вакуумной в среде инертных газов.
Низкоуглеродистая сталь не обладает повышенными прочностными характеристиками. Временное сопротивление на разрыв для нее колеблется в пределах 320-450 МПа. То же самое можно сказать относительно твердости. Без дополнительного упрочнения твердость стали составляет 22-23 единиц по шкале Роквелла.
Низкоуглеродистые марки не поддаются закалке в силу малого содержания углерода в составе. Среди немногочисленных вариантов улучшения сталям своих механических свойства выделяют цементацию. Это разновидность химико-термического упрочнения, при котором поверхность металла принудительно насыщают углеродом, что делает металл более твердым и износостойким. Помимо этого, в качестве механического упрочнения хорошо зарекомендовали себя разного рода наклепы, обкатка роликами и прочее.
Классификация и марки
Существует несколько основных критериев по которым подразделяются углеродистые марки. Одним из самых важных среди них являются условия проведения раскисления. Выделяют следующие низкоуглеродистые стали:
- Спокойные. Включает минимальное содержание в составе окиси железа, что делает процесс выплавки «спокойным» – без бурного выделения углекислоты с зеркала металла. Возможным это стало благодаря введению раскислителей: алюминий, марганец и кремний. Все выходящие газы скапливаются в усадочной раковине, которая впоследствии обрубается, что в результате дает плотный и однородный металл.
- Кипящие. Раскисляются одним марганцем. Имеют увеличенное количество оксида железа в составе. Процесс плавки сопровождается выделением углекислого газа, что создает впечатление будто металл кипит. Эти стали менее прочны и менее однородны по химическому составу, но при этом стоят дешево и имеют низкий процент отходов в производстве.
- Полуспокойные.
Помимо марганца для удаления кислорода дополнительно применяют алюминий. По характеристикам эта углеродистая сталь представляет собой что-то среднее между кипящими и спокойными сплавами.
Помимо степени раскисления низкоуглеродистые марки также классифицируются по наличию неметаллических включений в своем составе. Исходя из этого они различаются на:
- Обыкновенного качества;
- Качественные машиностроительные.
Рассмотрим каждый пункт более подробно.
Стали обыкновенного качества. К ним не предъявляются строгие требования как к выбору шихты, так и к плавке и разливке. Фосфора в них допускается не более 0,08%, а серы не более 0,06%. Разливают такой сплав в крупногабаритные слитки, поэтому для них характерно появление зональной ликвации.
Сталь обыкновенного качества идет на производство разного рода горячекатаного металлопроката: прутки ГОСТ 4290-90, швеллеры ГОСТ 8240-97, балки ГОСТ 8239-95, уголки ГОСТ 8509-95 и прочие. Этот прокат служит материалом для производства разного рода болтовых, клепочных и сварных металлоконструкций. В станкостроении из нее производят малоответственные детали не требующие проведения термобработки: оси, вальцы, зажимы и т.д.
Исходя из гарантированности указанных свойств сталь обыкновенного качества бывает:
- Группы «А». Поставка происходит по механическим характеристикам, химический состав при этом не нормируется. Маркируется «Ст» и цифрой от 0 до 6. (Ст.6, Ст.5 и т.д.). С увеличением цифры возрастает и прочность выбранного сплава.
- Группы «Б». Такие металлы идут с нормированным химсоставом. В маркировке дополнительно прописывается способ получения сплава.
- Группы «В». Здесь в сталях регулируются одновременно прочностные характеристики и химсостав. В маркировке дополнительно указывается буква В.
Качественные машиностроительные стали производятся в более строгих условиях выплавки. Обладают меньшим количеством вредных образований в химсоставе: сера до 0,04%, фосфор до 0,04%. Маркируются надписью «сталь» и цифрой, указывающей количество карбидов в сотых долях процента.
Сталь 08 и 10 применяются в ответственных узлах машиностроения. Из них производят втулки, змеевики, прокладки и т.д. Перед использованием все детали обязательно подвергаются цементации или любому другому химико-термическому упрочнению.
Стали 15, 20, 25 используются для узлов, работающих на износ и не испытывающих повышенных механических нагрузок: рычаги, шестерни, толкатели клапанов и т.д.
Способы получения
Выделяют следующие низкоуглеродистые стали в зависимости от способа выплавки:
- Конверторные печи. Металл плавиться за счет химической теплоты экзотермических реакций. Удаление излишнего углерода происходят при продувке кислорода сквозь зеркало металла. Плюсом такого способа является высокая производительность. Минусом – повышенная концентрация азота на выходе.
- Мартеновские печи. В рабочей камере сжигается жидкое топливо. Необходимая температура плавки достигается за счет теплоты отходящих газов.
При таком способе сплав получается более раскисленным и с меньшим содержанием неметаллических примесей.
- Электропечи. Обладают более совершенным способом выплавки. Все качественные марки низкоуглеродистой стали выплавляются только таким методом.Достоинством здесь выступает простота регулировки теплового режима и возможность использования шлаков и флюсов. Минус – значительные затраты электроэнергии.
Низкоуглеродистая сталь в большей степени востребована машиностроением и, особенно, строительством. Именно эти отрасли обеспечивают ее постоянным спросом вот уже на протяжении нескольких десятков лет. И ссудя по обширно обустраивающимся городам и развивающейся промышленности потребность в углеродистой стали будет только увеличиваться.
Оцените статью:
Рейтинг: 0/5 – 0 голосов
Ещё статьи по теме:
Холоднокатаная сталь
Рельсовая сталь
Редкоземельные металлы
Марка: Ст3сп — она же Ст3 или Ст.![]() | |||||||
Класс: Сталь конструкционная углеродистая обыкновенного качества | |||||||
Использование в промышленности: несущие элементы сварных и несварных конструкций и деталей, работающих при положительных температурах |
Химический состав в % стали Ст3сп | ||
C | 0,14 — 0,22 | |
Si | 0,15 — 0,3 | |
Mn | 0,4 — 0,65 | |
Ni | до 0,3 | |
S | до 0,05 | |
P | до 0,04 | |
Cr | до 0,3 | |
N | до 0,008 | |
Cu | до 0,3 | |
As | до 0,08 | |
Fe | ~97 |
Зарубежные аналоги марки стали Ст3сп | ||
США | A284Gr.![]() | |
Германия | 1.0038, 1.0116, DC03, Fe360B, Fe360D1, RSt37-2, RSt37-3, S235J0, S235J2G3, S235JR, S235JRG2, St37-2, St37-3, St37-3G | |
Япония | SS330, SS34, SS400 | |
Франция | E24-2, E24-2NE, E24-3, E24-4, S235J0, S235J2G3, S235J2G4, S235JRG2 | |
Англия | 1449-2723CR, 1449-3723CR, 3723HR, 40B, 40C, 40D, 4360-40B, 4360-40D, 4449-250, 722M24, Fe360BFU, Fe360D1FF, HFS3, HFS4, HFW3, HFW4, S235J2G3, S235JR, S235JRG2 | |
Евросоюз | Fe37-3FN, Fe37-3FU, Fe37B1FN, Fe37B1FU, Fe37B3FN, Fe37B3FU, S235, S235J0, S235J2G3, S235JR, S235JRG2 | |
Италия | Fe360B, Fe360BFN, Fe360C, Fe360CFN, Fe360D, Fe360DFF, Fe37-2, S235J0, S235J2G3, S235J2G4, S235JRG2 | |
Бельгия | FE360BFN, FE360BFU, FED1FF | |
Испания | AE235BFN, AE235BFU, AE235D, Fe360BFN, Fe360BFU, Fe360D1FF, S235J2G3, S235JRG2 | |
Китай | Q235, Q235A, Q235A-B, Q235A-Z, Q235B, Q235B-Z, Q235C | |
Швеция | 1312, 1313 | |
Болгария | BSt3ps, BSt3sp, Ew-08AA, S235J2G3, S235JRG2, WSt3ps, WSt3sp | |
Венгрия | Fe235BFN, Fe235D, S235J2G3, S235JRG2 | |
Польша | St3S, St3SX, St3V, St3W | |
Румыния | OL37.![]() | |
Чехия | 11375, 11378 | |
Финляндия | FORM300H, RACOLD03F, RACOLD215S | |
Австрия | RSt360B |
Свойства и полезная информация: |
Твердость материала: HB 10 -1 = 131 МПа Свариваемость материала: без ограничений Флокеночувствительность: не чувствительна Склонность к отпускной хрупкости: не склонна |
Механические свойства стали Ст3сп при Т=20oС | |||||||
Прокат | Размер | Напр.![]() | σв(МПа) | sT (МПа) | δ5 (%) | ψ % | KCU (кДж / м2) |
Сталь горячекатан. | 20 — 40 | 380-490 | 25 |
Особенности стали Сс3сп и электрошлаковая сварка: углеродистые стали — самый распространенный конструкционный материал. По объему применения стали этого класса превосходят все остальные. К углеродистым относятся стали с содержанием 0,1-0,7% С, при содержании остальных элементов не более: 0,8% Мn, 0,4% Si, 0,05% Р, 0,05% S, 0,5% Си, 0,3% Сг, 0,3% Ni. В табл. 9.1 приведен химический состав и механические свойства сталей, нашедших применение при изготовлении сварных конструкций с использованием электрошлаковой сварки.
По способу производства различают мартеновскую и конвертерную стали, по степени раскисления (в порядке возрастания) кипящую, полуспокойную и спокойную.
Спокойные углеродистые стали поступают в промышленность в виде отливок и поковок по ГОСТ 977-75, в виде горячекатаной стали обыкновенного качества по ГОСТ 380-71, качественных конструкционных горячекатаных сортовых сталей по ГОСТ 1050-74. Главным отличительным признаком этих сталей является содержание в них углерода.
Прочностные характеристики углеродистых сталей повышаются с увеличением содержания углерода, при этом их свариваемость ухудшается, так как возрастает опасность образования горячих трещин в шве. При содержании свыше 0,5% С стали практически не свариваются электрошлаковой сваркой без специальных приемов.
Чувствительность к горячим трещинам в шве возрастает с увеличением жесткости свариваемых конструкций. Предварительный и сопутствующий подогрев могут существенно снизить опасность появления трещин даже при сварке жестких стыков (например, на участке замыкания кольцевого шва). Одним из радикальных средств по предотвращению горячих трещин служит снижение скорости подачи электродной проволоки.
Углеродистые стали в настоящее время сваривают проволочными электродами, электродами большого сечения или плавящимися мундштуками. Наиболее широко применяют проволочные электроды и плавящиеся мундштуки.
Наиболее целесообразный путь повышения прочности металла шва заключается в увеличении содержания марганца, поскольку это не сопровождается снижением технологической прочности металла шва. Марганец увеличивает склонность металла к закалке и упрочняет феррит. Так, при легировании металла шва 1,5% Мn (0,12-0,14% С) достигаются те же прочностные характеристики, что и при 0,22-0,24% С (0,5-0,7% Мn). Металл шва в первом случае обладает большей стойкостью против кристаллизационных трещин и против перехода в хрупкое состояние. Положительное влияние на прочность оказывают также небольшие добавки в металл шва никеля, хрома и других легирующих элементов.
Для электрошлаковой сварки углеродистых сталей чаще всего используют флюс АН-8 и сварочные проволоки марок Св-08, Св-08А, Св-08 ГА, Св-08Г2С, Св-10Г2 (ГОСТ 2246-70). Так, при
сварке сталей 15, 15Л, Ст2 равнопрочные соединения могут быть получены при использовании проволок Св-08 и Св-08А. При сварке низкоуглеродистой стали СтЗ применяют проволоку Св-08ГС.
Краткие обозначения: | ||||
σв | — временное сопротивление разрыву (предел прочности при растяжении), МПа | ε | — относительная осадка при появлении первой трещины, % | |
σ0,05 | — предел упругости, МПа | Jк | — предел прочности при кручении, максимальное касательное напряжение, МПа | |
σ0,2 | — предел текучести условный, МПа | σизг | — предел прочности при изгибе, МПа | |
δ5,δ4,δ10 | — относительное удлинение после разрыва, % | σ-1 | — предел выносливости при испытании на изгиб с симметричным циклом нагружения, МПа | |
σсж0,05 и σсж | — предел текучести при сжатии, МПа | J-1 | — предел выносливости при испытание на кручение с симметричным циклом нагружения, МПа | |
ν | — относительный сдвиг, % | n | — количество циклов нагружения | |
sв | — предел кратковременной прочности, МПа | R и ρ | — удельное электросопротивление, Ом·м | |
ψ | — относительное сужение, % | E | — модуль упругости нормальный, ГПа | |
KCU и KCV | — ударная вязкость, определенная на образце с концентраторами соответственно вида U и V, Дж/см2 | T | — температура, при которой получены свойства, Град | |
sT | — предел пропорциональности (предел текучести для остаточной деформации), МПа | l и λ | — коэффициент теплопроводности (теплоХотСтилость материала), Вт/(м·°С) | |
HB | — твердость по Бринеллю | C | — удельная теплоХотСтилость материала (диапазон 20o — T ), [Дж/(кг·град)] | |
HV | — твердость по Виккерсу | pn и r | — плотность кг/м3 | |
HRCэ | — твердость по Роквеллу, шкала С | а | — коэффициент температурного (линейного) расширения (диапазон 20o — T ), 1/°С | |
HRB | — твердость по Роквеллу, шкала В | σtТ | — предел длительной прочности, МПа | |
HSD | — твердость по Шору | G | — модуль упругости при сдвиге кручением, ГПа |
_ _ _ _ _ _ _ _ _ _ _ _ _ _ _ _ _ _ _ _ _ _ _ _ _ _ _ _ _ _ _ _ _ _ _ _ _ _ _ _ _ _ _ _ _ _ _ _ _ _ _ _ _ _ _ _ _ _ _ _ _ _ _ _ _ _ _ _ _ _ _ _ _ _ _ _ _ _ _ _ _ _ _ _ _ _ _ _ _ _ _ _ _ _ _ _ _ _ _ _ _ _ _ _ _ _ _ _ _ _ _ _ _ _ _ _ _ _ _ _ _ _ _ _ _ _ _ _ _ _ _ _ _ _ _ _ _ _ _ _ _ _ _ _ _ _ _ _ _ _ _ _ _ _ _ _ _ _ _ _ _ _ _ _ _ _ _ _ _ _ _ _ _ _ _ _ _ _ _ _ _ _ _ _ _ _ _ _ _ _ _ _ _ _ _ _ _ _ _ _ _ _ _ _ _ _ _ _ _ _ _ _ _ _ _ _ _ _ _ _ _ _ _ _ _ _ _ _ _ _ _ _ _ _ _ _ _ _ _ _ _ _ _ _ _ _ _ _ _ _ _ _ _ _ _ _ _ _ _ _ _ _ _ _ _ _ _ _ _ _ _ _ _ _ _ _ _ _ _ |
ГОСТ 6727-80 МЕЖГОСУДАРСТВЕННЫЙ СТАНДАРТ ПРОВОЛОКА ИЗ
НИЗКОУГЛЕРОДИСТОЙ
ТЕХНИЧЕСКИЕ УСЛОВИЯ
ИПК
ИЗДАТЕЛЬСТВО СТАНДАРТОВ
МЕЖГОСУДАРСТВЕННЫЙ СТАНДАРТ
Дата введения 01.01.83 Настоящий стандарт распространяется на проволоку из низкоуглеродистой стали холоднотянутую периодического профиля класса Вр-1 для армирования железобетонных конструкций. (Измененная редакция, Изм. № 2, 3). 1.1. (Исключен, Изм. № 3). 1.2. Основные параметры и размеры проволоки должны соответствовать указанным в табл. 1. Обозначения размеров проволоки приведены на чертеже. Таблица 1 мм
Примечание Номинальный шаг вмятин s и
радиус сопряжения поверхности вмятин с выступами R
являются справочными величинами для конструирования профилирующего инструмента
и на проволоке не проверяются. (Измененная редакция, Изм. № 2, 3). 1.3. Радиус сопряжения поверхности вмятин с выступами R для проволоки всех диаметров должен быть равен (2,5 ± 0,5) мм. Допускается относительное смещение противоположных вмятин до 0,5 S и расположение их по винтовой линии оси проволоки. (Измененная редакция, Изм. № 2). 1.4. Разность размеров а и а1 не должна превышать поля допуска на размер а. Пример условного обозначения проволоки номинальным диаметром 3,0 мм: Проволока 3 Bp1 ГОСТ 6727-80. (Измененная редакция, Изм. № 3). 2.1. Проволока должна изготовляться в соответствии с требованиями настоящего стандарта по технологическому регламенту, утвержденному в установленном порядке. Проволока должна изготовляться из катанки по ОСТ 14-15-193. (Измененная редакция, Изм. № 1, 2). 2.2. Механические свойства проволоки должны соответствовать
указанным в табл. Таблица 2
(Измененная редакция, Изм. 2.3. На поверхности проволоки не должно быть трещин, плен, закатов, раковин. Допускаются риски и царапины глубиной не более половины предельных отклонений на размер а и налет ржавчины. (Измененная редакция, Изм. № 3). 2.4. Проволока изготовляется в мотках массой 500-1500 кг. Допускается изготовление проволоки в мотках массой 20-100 кг. Каждый моток должен состоять из одного отрезка проволоки. Проволока должна быть свернута в мотки неперепутанными рядами. (Измененная редакция, Изм. № 2). 2.5. Линейная плотность проволоки должна соответствовать указанной в табл. 3. Таблица 3
Расчетная площадь поперечного сечения и теоретическая
линейная плотность проволоки приведены в приложении 2. (Измененная редакция, Изм. № 2, 3). 3.1. Проволоку принимают партиями. Партия должна состоять из проволоки, оформленной одним документом о качестве, в котором следует указывать: – товарный знак или наименование и товарный знак предприятия-изготовителя; – условное обозначение проволоки; – результаты испытаний; – количество мотков; – номер партии; – массу нетто партии; – изображение государственного Знака качества для проволоки высшей категории качества. (Измененная редакция, Изм. № 1, 2, 3). 3.2. Размер а, разность размеров а и а1 и качество поверхности проволоки проверяют на каждом мотке. (Измененная редакция, Изм. № 3). 3.3. Для проверки механических свойств проволоки и параметров профиля проволоки от партии должно быть отобрано 3 % мотков, но не менее 5 мотков. (Измененная редакция, Изм. № 2). 3.4. При получении неудовлетворительных результатов
испытаний хотя бы по одному из показателей проводят повторные испытания на
удвоенной выборке. 4.1. Для каждого вида испытаний отбирают по одному образцу с одного конца мотка. 4.2. Качество поверхности проволоки контролируется невооруженным глазом. 4.3. Размеры а и а1 проволоки измеряют микрометром по ГОСТ 6507. Величина разности размеров а и а1 определяется как среднее арифметическое значение трех измерений, проведенных на участке длиной 1 м. (Измененная редакция, Изм. № 2, 3). 4.4. Параметры профиля проволоки определяют как среднее арифметическое трех измерений, проведенных на участке длиной 1 м с каждой стороны. Глубина вмятин h измеряется микрометром по ГОСТ 6507, оборудованным специальной пяткой (обязательное приложение 1). Длина выступа b измеряется отсчетным микроскопом МПБ-2, изготовленным по технической документации. При разногласиях в измерении параметров профиля
проволоки контроль проводится по линейной плотности проволоки (табл. Линейная плотность проволоки определяется как частное от деления массы двух образцов длиной 1 м, взвешенных с погрешностью до 0,001 кг, на их длину, измеренную с погрешностью до 0,001 м. (Измененная редакция, Изм. № 2, 3). 4.5. Испытание проволоки на растяжение проводят по ГОСТ 12004. 4.6. Испытание проволоки, на перегиб проводят по ГОСТ 1579. Проволока диаметром 3,0 и 4,0 мм испытывается на валиках диаметром 20 мм, а диаметром 5,0 мм – на валиках диаметром 30 мм. При испытании проволоки образец зажимается так, чтобы вмятины были обращены к губкам прибора. 4.5, 4.6 (Измененная редакция, Изм. № 2). 4.7. Глубину рисок и царапин определяют удалением их зачисткой с последующим сравнительным измерением в зачищенном и незачищенном местах. (Измененная редакция, Изм. № 2, 3). 5.1. Каждый моток массой 500-1500 кг должен быть
равномерно перевязан по окружности не менее чем в четырех местах, а моток
массой 20-100 кг – не менее чем в трех местах. По требованию потребителя моток массой 500-1500 кг должен иметь промежуточные вязки, расположенные внутри мотка. В качестве увязочных материалов применятся катанка по ОСТ 14-15-193 или термически обработанная проволока по нормативно-технической документации. Концы мотка должны быть аккуратно уложены и легко находимы. (Измененная редакция, Изм. № 2, 4). 5.1a. Мотки проволоки массой 20-100 кг связывают в бухты. Масса грузового места не должна превышать 1500 кг. По согласованию изготовителя с потребителем допускается увеличение массы грузового места. Грузовые места формируют в транспортные пакеты по ГОСТ 24597 и ГОСТ 21650. (Введен дополнительно, Изм. № 2). 5.2. К каждому мотку (бухте) должен быть прочно прикреплен ярлык, на котором указывают: – товарный знак или наименование и товарный знак предприятия-изготовителя; – условное обозначение проволоки; – номер партии; – клеймо технического контроля; – изображение государственного Знака качества для
проволоки высшей категории качества. (Измененная редакция, Изм. №1, 2). 5.3. Проволоку перевозят транспортом всех видов в соответствии с правилами перевозки грузов, действующими на транспорте данного вида. Размещение и крепление грузов в транспортных средствах, перевозимых по железной дороге, должно соответствовать техническим условиям погрузки и крепления грузов, утвержденными Министерством путей сообщения СССР. Транспортирование по железной дороге проводится повагонными и малотоннажными или мелкими отправками. Допускается транспортирование проволоки в универсальных контейнерах по ГОСТ 15102, ГОСТ 20435, ГОСТ 22225. 5.4. Хранение проволоки – по условиям 5 ГОСТ 15150. 5.3, 5.4. (Измененная редакция, Изм. № 2). 5.5. Транспортирование проволоки, отправляемой в районы Крайнего Севера и районы, приравниваемые к ним, проводится по ГОСТ 15846. (Измененная редакция, Изм. № 3). 5.6. Транспортная маркировка – по ГОСТ 14192. (Введен дополнительно, Изм. № 2). Специальная пятка к микрометру типа МК по ГОСТ 6507 для измерения глубины вмятин Материал – сталь ШХ15, У10А, У12А.
Расчетная площадь поперечного сечения и теоретическая линейная плотность проволоки
ПРИЛОЖЕНИЕ 2. ИНФОРМАЦИОННЫЕ ДАННЫЕ 1. РАЗРАБОТАН И ВНЕСЕН Министерством черной металлургам СССР РАЗРАБОТЧИКИ Е.М. Киреев, К.Г. Залялютдинов, Х.Н. Белалов, Н.А. Галкина, Т.А. Коршунова, К.В. Михайлов, В.И. Бондаренко, В.М. Скубко 2. УТВЕРЖДЕН И ВВЕДЕН В ДЕЙСТВИЕ Постановлением Государственного комитета СССР по стандартам от 15.05.80 № 2108 3. ВЗАМЕН ГОСТ 6727-53 4. ССЫЛОЧНЫЕ НОРМАТИВНО-ТЕХНИЧЕСКИЕ ДОКУМЕНТЫ
5. Ограничение срока действия снято по протоколу 2-93 Межгосударственного Совета по стандартизации, метрологии и сертификации (ИУС 2-93) 6. ИЗДАНИЕ (май 2003 г.) с Изменениями № 1, 2, 3, 4, утвержденными в декабре 1984 г., июне 1987 г., октябре 1988 г., феврале 1990 г. (ИУС 3-85, 10-87, 1-89, 5-90) ___________________________________________________________________________________________________________________________ Переиздание (по состоянию на апрель 2008 г.) СОДЕРЖАНИЕ
|
Низкоуглеродистая сталь – малоуглеродистая сталь
Типичные области применения низкоуглеродистой стали включают компоненты автомобильных кузовов, конструктивные элементы (например, двутавровые балки, швеллеры и уголки) и листы, используемые в трубопроводах и зданиях.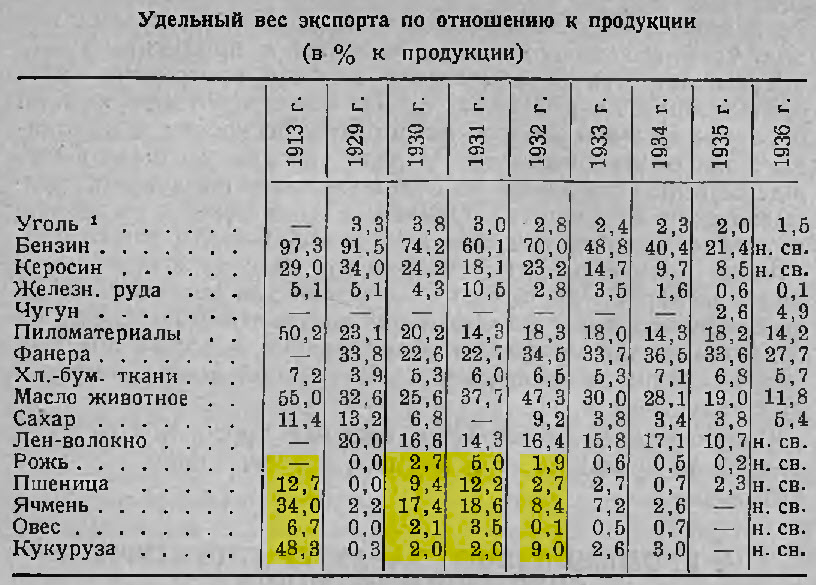
Низкоуглеродистая сталь , также известная как мягкая сталь , в настоящее время является наиболее распространенной формой стали, поскольку ее цена относительно низкая. В то же время он обеспечивает свойства материала, приемлемые для многих приложений. Низкоуглеродистая сталь содержит примерно 0,05–0,25% углерода делает его ковким и пластичным . Мягкая сталь имеет относительно низкую прочность на растяжение , но она дешева и легко формуется; поверхностная твердость может быть увеличена за счет науглероживания.
Типичные области применения включают компоненты автомобильных кузовов, конструкционные формы (например, двутавровые балки, швеллеры и уголки) и листы, используемые в трубопроводах и зданиях. Например, сталь A36 является обычной конструкционной сталью в Соединенных Штатах. Например, листы низкоуглеродистой стали, используемые для изготовления кузовов автомобилей, подвергаются различным операциям формовки, включая глубокую вытяжку. Микроструктуры состоят из ферритных и перлитных составляющих. Следовательно, эти сплавы относительно мягкие и слабые, но обладают выдающейся пластичностью и ударной вязкостью. Кроме того, они поддаются механической обработке, сварке и из всех сталей являются наименее дорогими в производстве. Плотность этого металла 7861,09.3 кг/м³ (0,284 фунта/дюйм³), а прочность на растяжение составляет не более 500 МПа (72500 фунтов на кв. дюйм).
Цена на низкоуглеродистую сталь
Нелегко узнать точную стоимость различных материалов, потому что она сильно зависит от многих переменных, таких как:
- тип продукта, который вы хотели бы купить
- количество продукта
- точный тип материала
Цены на сырье меняются ежедневно и в основном определяются спросом, предложением и ценами на энергию. двутавровые балки, швеллеры и уголки), а также листы, используемые в трубопроводах и зданиях.
Однако, как правило, нержавеющая сталь стоит в четыре-пять раз больше, чем углеродистая сталь с точки зрения затрат на материалы. Углеродистая сталь стоит около 500 долларов США за тонну , а нержавеющая сталь стоит около 2000 долларов США за тонну . Чем больше легирующих элементов содержит сталь, тем она дороже. Основываясь на этом правиле, логично предположить, что аустенитная нержавеющая сталь 316L и мартенситная нержавеющая сталь с 13% Cr будут стоить меньше, чем дуплексная нержавеющая сталь с 22% Cr и 25% Cr. Стали на основе никеля, вероятно, будут стоить примерно столько же, сколько дуплексные нержавеющие стали. Многочисленные виды стали, от низкоуглеродистой до высокоуглеродистой, и широкий диапазон оценок нержавеющей стали сильно различаются по стоимости. Например, Inconel 600 (зарегистрированная торговая марка Special Metals), который относится к семейству аустенитных сплавов на основе никеля и хрома 9.Суперсплавы 0003, стоят около 40000 долларов США за тонну .
Свойства низкоуглеродистой стали – ASTM A36
Свойства материала являются интенсивными свойствами , что означает, что они не зависят от количества массы и могут варьироваться от места к месту в системе в любой момент. Материаловедение включает в себя изучение структуры материалов и связывание их с их свойствами (механическими, электрическими и т. д.). Как только материаловед узнает об этой корреляции структура-свойство, он может приступить к изучению относительных характеристик материала в данном приложении. Основными факторами, определяющими структуру материала и, следовательно, его свойства, являются входящие в его состав химические элементы и то, как он был обработан до конечной формы.
Механические свойства низкоуглеродистой стали – ASTM A36
Материалы часто выбирают для различных применений, поскольку они имеют желаемое сочетание механических характеристик. Для конструкционных приложений свойства материалов имеют решающее значение, и инженеры должны их учитывать.
Прочность низкоуглеродистой стали – ASTM A36
В механике материалов прочность материала – это его способность выдерживать приложенную нагрузку без разрушения или пластической деформации. Прочность материалов учитывает взаимосвязь между внешними нагрузками , приложенными к материалу, и результирующей деформацией или изменением размеров материала. Прочность материала – это его способность выдерживать приложенную нагрузку без разрушения или пластической деформации.
Предел прочности при растяжении
Предел прочности при растяжении низкоуглеродистой стали составляет от 400 до 550 МПа.
Предел прочности при растяжении — максимум на инженерной кривой напряжения-деформации. Это соответствует максимальному напряжению , выдерживаемому растянутой конструкцией. Предельная прочность на растяжение часто сокращается до «предельной прочности» или «предела прочности». Если это напряжение применяется и поддерживается, в результате произойдет перелом. Часто это значение значительно превышает предел текучести (на 50–60 % превышает предел текучести для некоторых типов металлов). Когда пластичный материал достигает предела прочности, он испытывает сужение, когда площадь поперечного сечения локально уменьшается. Кривая напряжение-деформация не содержит более высокого напряжения, чем предел прочности. Несмотря на то, что деформации могут продолжать увеличиваться, напряжение обычно уменьшается после достижения предела прочности. Это интенсивное свойство; следовательно, его значение не зависит от размеров испытуемого образца. Однако это зависит от других факторов, таких как подготовка образца, наличие или отсутствие поверхностных дефектов, температура тестовой среды и материала. Предел прочности при растяжении варьируется от 50 МПа для алюминия до 3000 МПа для очень высокопрочной стали.
Предел текучести
Предел текучести низкоуглеродистой стали составляет 250 МПа.
Точка текучести — это точка на кривой напряжения-деформации, которая указывает предел упругого поведения и начало пластического поведения. Предел текучести или предел текучести — это свойство материала, определяемое как напряжение, при котором материал начинает пластически деформироваться. Напротив, предел текучести – это место, где начинается нелинейная (упругая + пластическая) деформация. Перед пределом текучести материал упруго деформируется и возвращается к своей первоначальной форме после снятия приложенного напряжения. Как только предел текучести пройден, некоторая часть деформации будет постоянной и необратимой. Некоторые стали и другие материалы демонстрируют явление, называемое явлением предела текучести. Пределы текучести варьируются от 35 МПа для низкопрочного алюминия до более 1400 МПа для высокопрочной стали.
Модуль упругости Юнга
Модуль упругости Юнга низкоуглеродистой стали составляет 200 ГПа.
Модуль упругости Юнга представляет собой модуль упругости при растяжении и сжатии в режиме линейной упругости при одноосной деформации и обычно оценивается испытаниями на растяжение. Вплоть до предельного напряжения тело сможет восстановить свои размеры при снятии нагрузки. Приложенные напряжения заставляют атомы в кристалле перемещаться из своего равновесного положения, и все атомы смещаются на одинаковую величину и сохраняют свою относительную геометрию. Когда напряжения снимаются, все атомы возвращаются в исходное положение, и остаточная деформация не возникает. Согласно Закон Гука, напряжение пропорционально деформации (в упругой области), а наклон модуль Юнга . Модуль Юнга равен продольному напряжению, деленному на деформацию.
Твердость низкоуглеродистой стали – ASTM A36
Твердость по Бринеллю низкоуглеродистой стали составляет примерно 120 МПа.
В материаловедении твердость способность выдерживать вдавливание поверхности ( локализованная пластическая деформация ) и царапая . Твердость , вероятно, является наиболее плохо определенным свойством материала, поскольку она может указывать на устойчивость к царапанию, истиранию, вдавливанию или даже сопротивляемость формованию или локальной пластической деформации. Твердость важна с инженерной точки зрения, потому что сопротивление износу при трении или эрозии паром, маслом и водой обычно увеличивается с увеличением твердости.
Испытание на твердость по Бринеллю является одним из испытаний на твердость при вдавливании, разработанных для определения твердости. В тестах Бринелля жесткий, 9Сферический индентор 0003 вдавливается под определенной нагрузкой в поверхность испытуемого металла. В типичном испытании используется шарик из закаленной стали диаметром 10 мм (0,39 дюйма) в качестве индентора с усилием 3000 кгс (29,42 кН; 6614 фунтов силы). Нагрузка поддерживается постоянной в течение заданного времени (от 10 до 30 с). Для более мягких материалов используется меньшее усилие; для более твердых материалов вместо стального шарика используется шарик из карбида вольфрама .
Испытание дает численные результаты для количественного определения твердости материала, которая выражается числом Число твердости по Бринеллю – HB . Число твердости по Бринеллю обозначается наиболее часто используемыми стандартами испытаний (ASTM E10-14[2] и ISO 6506–1:2005) как HBW (H по твердости, B по Бринеллю и W по материалу индентора, вольфрамовому сплаву). (вольфрам) карбид). В прежних стандартах HB или HBS использовались для обозначения измерений, выполненных стальными инденторами.
Число твердости по Бринеллю (HB) представляет собой нагрузку, деленную на площадь поверхности вдавливания. Диаметр вдавления измеряют с помощью микроскопа с наложенной шкалой. Число твердости по Бринеллю вычисляется по уравнению:
Широко используются различные методы испытаний (например, Бринелля, Кнупа, Виккерса и Роквелла). В некоторых таблицах коррелируются значения твердости по различным методам испытаний, где корреляция применима. Во всех шкалах высокое число твердости соответствует твердому металлу.
Тепловые свойства низкоуглеродистой стали – ASTM A36
Термические свойства материалов относятся к реакции материалов на изменения их температуры и приложение тепла. Когда твердое тело поглощает энергию в виде тепла, его температура повышается, а его размеры увеличиваются. Но различные материалы реагируют на воздействие тепла по-разному .
Теплоемкость, тепловое расширение и теплопроводность часто имеют решающее значение при практическом использовании твердых тел.
Температура плавления низкоуглеродистой стали – ASTM A36
Температура плавления низкоуглеродистой стали составляет около 1450°C.
В общем, плавление является фазовым переходом вещества из твердого состояния в жидкое. Точка плавления вещества — это температура, при которой происходит это фазовое превращение. Точка плавления также определяет состояние, при котором твердое тело и жидкость могут существовать в равновесии.
Теплопроводность низкоуглеродистой стали – ASTM A36
Низкоуглеродистая сталь представляет собой многоэлементное вещество, в основном железо, с добавками углерода и примесей. Теплопроводность кованого железа составляет около 50 Вт/(м·К).
Характеристики теплопередачи твердого материала измеряются с помощью свойства, называемого теплопроводность , k (или λ), измеренная в Вт/м.K . Он измеряет способность вещества передавать тепло через материал за счет теплопроводности. Обратите внимание, что закон Фурье применяется ко всем веществам, независимо от их состояния (твердое, жидкое или газообразное). Поэтому он также определен для жидкостей и газов.
Теплопроводность большинства жидкостей и твердых тел зависит от температуры, а для паров она также зависит от давления. В общем:
Большинство материалов практически однородны. Поэтому обычно мы можем написать k = k (T) . Аналогичные определения связаны с теплопроводностями в направлениях y и z (ky, kz), но для изотропного материала теплопроводность не зависит от направления переноса, kx = ky = kz = k.
Ссылки:
Материаловедение:
Министерство энергетики США, Материаловедение. Справочник по основам Министерства энергетики, том 1 и 2. Январь 1993 г.
Министерство энергетики США, материаловедение. Справочник по основам Министерства энергетики, том 2 и 2. 19 января.93.
Уильям Д. Каллистер, Дэвид Г. Ретвиш. Материаловедение и инженерия: введение, 9-е издание, Wiley; 9 издание (4 декабря 2013 г.), ISBN-13: 978-1118324578.
Эберхарт, Марк (2003). Почему все ломается: понимание мира по тому, как он разваливается. Гармония. ISBN 978-1-4000-4760-4.
Гаскелл, Дэвид Р. (1995). Введение в термодинамику материалов (4-е изд.). Издательство Тейлор и Фрэнсис. ISBN 978-1-56032-992-3.
Гонсалес-Виньяс, В. и Манчини, Х.Л. (2004). Введение в материаловедение. Издательство Принстонского университета. ISBN 978-0-691-07097-1.
Эшби, Майкл; Хью Шерклифф; Дэвид Себон (2007). Материалы: инженерия, наука, обработка и дизайн (1-е изд. ). Баттерворт-Хайнеманн. ISBN 978-0-7506-8391-3.
Дж. Р. Ламарш, А. Дж. Баратта, Введение в ядерную технику, 3-е изд., Prentice-Hall, 2001, ISBN: 0-201-82498-1.
Мягкая сталь | Металлургия для чайников
Что такое мягкая сталь?
Мягкая сталь представляет собой тип стального сплава, основным компонентом которого является большое количество углерода. Сплав представляет собой смесь металлов и неметаллов, предназначенную для получения определенных свойств. Сплавы позволяют компенсировать недостатки чистого металла добавлением других элементов. Чтобы понять, что такое мягкая сталь, нужно знать, из каких сплавов состоит сталь. Итак, давайте посмотрим, что мы подразумеваем под сталью, что поможет нам понять, что такое мягкая сталь, а также понять свойства мягкой стали.
Балка из мягкой стали
Термин «мягкая сталь» также применяется в коммерческих целях к углеродистым сталям, на которые не распространяются стандартные спецификации. Содержание углерода в этой стали может варьироваться от очень низкого уровня до примерно 0,3%. Как правило, можно ожидать, что коммерческая «мягкая сталь» легко поддается сварке и имеет приемлемые характеристики холодного изгиба, но указывать «мягкую сталь» технически неуместно и не следует использовать в качестве термина в технике.
Сталь – это любой сплав железа, содержащий от 0,2% до 2,1% углерода, в качестве упрочняющего агента. Помимо углерода, в состав стальных сплавов входит множество металлических элементов. Кроме железа и углерода, в стали используются хром, марганец, вольфрам и ванадий. Все эти элементы наряду с углеродом действуют как отвердители. То есть они препятствуют возникновению дислокаций внутри кристаллов железа и препятствуют скольжению слоев решетки относительно друг друга. Это то, что делает сталь тверже железа.
Листовая мягкая сталь
Различие между мягкой сталью и твердой сталью можно разделить по тому, существует ли у них предел текучести. Поскольку твердая сталь не имеет явного предела текучести, пластичность хуже, чем у мягкой стали. Мягкая сталь имеет очень очевидный предел текучести и большой коэффициент удлинения. Твердая сталь имеет высокую прочность, но ее пластичность не очень хорошая. Пластичность вида стали напрямую влияет на подгонку конструкции, поэтому для арматурной стали следует выбирать мягкую сталь.
Варьируя количество этих упрочняющих добавок, можно получить разные сорта стали. Пластичность, твердость и предел прочности при растяжении низкоуглеродистой стали зависят от количества углерода и других упрочняющих агентов, присутствующих в сплаве. Количество углерода является решающим фактором, определяющим твердость стального сплава. Стальной сплав с высоким содержанием углерода — это мягкая сталь, которая на самом деле намного тверже и прочнее железа. Хотя повышенное содержание углерода увеличивает твердость стального сплава, оно вызывает снижение его пластичности.
Мягкая сталь является наиболее распространенной формой стали, поскольку ее цена относительно низка, а свойства материала приемлемы для многих областей применения. Низкоуглеродистая сталь содержит примерно 0,05–0,15% углерода, а мягкая сталь содержит 0,16–0,29% [1] углерода, поэтому она не является ни хрупкой, ни пластичной. Мягкая сталь имеет относительно низкую прочность на растяжение, но она дешевая и ковкая, твердость поверхности можно повысить за счет науглероживания.
Часто используется, когда требуется большое количество стали, например, в качестве конструкционной стали. Плотность мягкой стали составляет примерно 7,85 г/см3 (7850 кг/м3 или 0,284 фунта/дюйм3), а модуль Юнга составляет 210 000 МПа (30 000 000 фунтов на кв. дюйм). Низкоуглеродистые стали страдают от биения предела текучести, когда материал имеет два предела текучести. Первая точка текучести (или верхняя точка текучести) выше второй, и доходность резко падает после достижения верхней точки текучести. Если низкоуглеродистая сталь нагружена только до некоторой точки между верхним и нижним пределом текучести, то на поверхности могут образоваться полосы Людера.
Мягкая сталь также может быть описана как сталь, которая не является нержавеющей сталью. Мягкая сталь отличается от нержавеющей стали содержанием хрома. Нержавеющая сталь содержит намного больше хрома, чем обычная углеродистая или мягкая сталь. Вот подборка свойств мягкой стали и ее использования в различных областях техники:
- Давайте посмотрим, что делает состав мягкой стали. Помимо максимального предела 2% углерода при производстве углеродистой стали, пропорции марганца (1,65%), меди (0,6%) и кремния (0,6%) являются фиксированными, а пропорции кобальта, хрома, ниобия, молибдена, титан, никель, вольфрам, ванадий и цирконий – нет.
- Большое количество углерода отличает мягкую сталь от других типов стали. Углерод делает мягкую сталь прочнее и жестче, чем другие типы стали. Однако твердость достигается за счет снижения пластичности этого сплава. Атомы углерода закрепляются в междоузлиях решетки железа и делают ее прочнее.
- То, что известно как самый мягкий сорт углеродистой стали или «мягкая сталь», обычно представляет собой углеродистую сталь со сравнительно небольшим содержанием углерода (от 0,16% до 0,19%).
%). Он обладает ферромагнитными свойствами, что делает его идеальным для производства электрических устройств и двигателей.
- Расчетная средняя плотность мягкой стали промышленного класса составляет 7,85 г/см3. Его модуль Юнга, который является мерой его жесткости, составляет около 210 000 МПа.
- Мягкая сталь является самой дешевой и наиболее универсальной формой стали и подходит для любого применения, требующего большого количества стали.
- Большое количество углерода также делает мягкую сталь уязвимой для ржавчины. Естественно, люди предпочитают нержавеющую сталь мягкой стали, когда им нужна технология без ржавчины. Мягкая сталь также используется в строительстве в качестве конструкционной стали. Он также широко используется в автомобилестроении.
Итак, вот некоторые свойства мягкой стали и ее применение. Использование мягкой стали распространяется почти на все виды промышленного применения и промышленного производства.
Вам также может понравиться
Что такое чугун? Чугун обычно содержит 2-4 мас.![]() | Что такое костяной фарфор? Посуда из костяного фарфора существует уже… | Фазы железо-углерод Влияние температуры на кристаллическую структуру … | Что такое нержавеющая сталь? Скульптура в стиле ар-деко из нержавеющей стали… |
1018 – Специальная сталь Ellwood
Найдите наш широкий выбор сталей от нас и наших дочерних компаний
Загрузить 1018 Спецификация
Мягкая/низкоуглеродистая сталь AISI 1018 обладает отличной свариваемостью, образует однородный и твердый корпус и считается лучшей сталью для науглероженных деталей. Мягкая/низкоуглеродистая сталь AISI 1018 обеспечивает хороший баланс ударной вязкости, прочности и пластичности. Горячекатаная сталь AISI 1018 обладает более высокими механическими свойствами, а также имеет улучшенные характеристики обработки и твердость по Бринеллю.
Специальные средства производственного контроля используются для подготовки поверхности, химического состава, процессов прокатки и нагрева. Все эти процессы позволяют получить продукт высочайшего качества, который подходит для таких производственных процессов, как сварка, ковка, сверление, механическая обработка, холодное волочение и термообработка.
ПРИМЕНЕНИЕ
- Используется в процессах гибки, опрессовки и штамповки.
- Науглероженные детали, в том числе червяки, шестерни, штифты, штифты, некритические компоненты инструментов и комплектов штампов, держатели инструментов, шестерни, детали машин, храповики, штифты и штифты цепи, изготовлены из мягкой/низкоуглеродистой стали AISI 1018.
- Широко используется для крепления, монтажных пластин и распорок.
- Подходит для применений, не требующих высокой прочности легированных сталей и высокоуглеродистых материалов.
- Обеспечивает высокую твердость поверхности и мягкую сердцевину таким деталям, как червяки, собачки, штифты, вкладыши, детали машин, специальные болты, трещотки, штифты цепей, клинья для смазочного инструмента, стяжные стержни, анкерные штифты, шпильки и т.
д.
- Используется для улучшения процессов сверления, механической обработки, нарезания резьбы и пробивки отверстий.
- Используется для предотвращения растрескивания при сильных изгибах.
ХИМИЧЕСКИЙ СОСТАВ
Элемент | Содержимое |
Углерод, C | 0,14 – 0,20 % |
Железо, Fe | 98,81 – 99,26% (в остатке) |
Марганец, Mn | 0,60 – 0,90% |
Фосфор, P | ≤ 0,040% |
Сера, S | ≤ 0,050% |
ФИЗИЧЕСКИЕ СВОЙСТВА
Физические свойства | Метрическая система | Имперский |
Плотность | 7,87 г/куб.см | 0,284 фунт/дюйм 3 |
МЕХАНИЧЕСКИЕ СВОЙСТВА
Механические свойства | Метрическая система | Империал |
Твердость по Бринеллю | 126 | 126 |
Твердость по Кнупу (пересчитанная из твердости по Бринеллю) | 145 | 145 |
Твердость по Роквеллу B (в пересчете на твердость по Бринеллю) | 71 | 71 |
Твердость по Виккерсу (пересчитанная из твердости по Бринеллю) | 131 | 131 |
Прочность на растяжение, максимальная | 440 МПа | 63800 фунтов на кв.![]() |
Прочность на растяжение, предел текучести | 370 МПа | 53700 фунтов на кв. дюйм |
Удлинение при разрыве (50 мм) | 15,0 % | 15,0 % |
Уменьшение площади | 40,0 % | 40,0 % |
Модуль упругости (типично для стали) | 205 ГПа | 29700 тысяч фунтов на квадратный дюйм |
Объемный модуль (типично для стали) | 140 ГПа | 20300 тысяч фунтов на квадратный дюйм |
Коэффициент Пуассона (типичный для стали) | 0,290 | 0,290 |
Обрабатываемость (на основе стали AISI 1212. 100% обрабатываемость) | 70 % | 70 % |
Модуль сдвига (типично для стали) | 80,0 ГПа | 11600 тыс.фунтов/кв.дюйм70 % |
ЭЛЕКТРИЧЕСКИЕ СВОЙСТВА
Электрические свойства | Метрическая система | Английский | Комментарии |
Удельное электрическое сопротивление при 0°C (32°F) | 0,0000159 Ом-см | 0,0000159 Ом-см | в отожженном состоянии |
при 100 °C/ 212 °F | 0,0000219 Ом-см | 0,0000219 Ом-см | в отожженном состоянии |
при 200 °C/392 °F | 0,0000293 Ом-см | 0,0000293 Ом-см | отожженное состояние |
Механическая обработка
Обрабатываемость мягкой/низкоуглеродистой стали AISI 1018 составляет 78% от B1112.
Свариваемость
Мягкая/низкоуглеродистая сталь AISI 1018 может быть мгновенно сварена всеми обычными способами сварки. Сварка не рекомендуется для мягкой/низкоуглеродистой стали AISI 1018, когда она карбонитрирована и науглерожена.
В процессе сварки должны использоваться низкоуглеродистые сварочные электроды, а последующий и предварительный нагрев не требуются. Предварительный нагрев может быть выполнен для сечений более 50 мм. Снятие напряжения после сварки также имеет свои преимущества, такие как процесс предварительного нагрева.
Термическая обработка
Термическая обработка мягкой/низкоуглеродистой стали AISI 1018 состоит из следующих процессов:
Нормализация
- Мягкая/низкоуглеродистая сталь AISI 1018 должна быть нагрета до 890°C – 9940°C – 9940°C – 9940°C C, а затем охлаждают в неподвижном воздухе.
Ковка
- Этот процесс требует нагревания в диапазоне от 1150°C до 1280°C, а мягкая/низкоуглеродистая сталь AISI 1018 выдерживается до тех пор, пока температура не станет постоянной.
- 900°C — минимальная температура, необходимая для процесса ковки.
- После этого процесса сталь охлаждают на воздухе.
Отпуск
- Мягкая/низкоуглеродистая сталь AISI 1018 подвергается отпуску при температуре от 150°C до 200°C для повышения прочности корпуса. Этот процесс практически не влияет на твердость.
- Возникновение шлифовальных трещин уменьшается, когда мягкая/низкоуглеродистая сталь AISI 1018 подвергается отпуску при вышеуказанной температуре.
Отжиг
- Мягкая/низкоуглеродистая сталь AISI 1018 нагревается до 870°C – 910°C и охлаждается в печи
Снятие напряжения
- 500°C – 700°C требуется для снятия напряжения в мягкой/низкоуглеродистой стали AISI 1018, которая затем охлаждается в неподвижном воздухе.
Цементация
- Этот процесс требует нагревания до 780°C – 820°C.