Подшипник вращения: Подшипник вращения | Справочник конструктора-машиностроителя
alexxlab | 23.10.1986 | 0 | Разное
Подшипник вращения | Справочник конструктора-машиностроителя
?Самоустанавливающиеся шариковые подшипники ( шарикоподшипники ) располагают два ряда шаров со сферической дорожкой качения на внешнем кольце.
Эта особенность конструкции обеспечивает самоустанавливаемость подшипников, позволяет им выдерживать перекосы вала относительно туловища.
Поэтому такие подшипники особенно спокойны в узелках, где возможны перекосы вследствиепогрешностей при установке или из – за изгибов вала.
2А587-8
Классификация подшипников качения осуществляется на основе следующих симптомов : По облику тел качения Шариковые, Роликовые ( игольчатые, если ролики тонкие и высокие ) ;
По образу воспринимаемой нагрузки Радиальные ( нагрузка вдоль оси вала не допускается ).
Радиально – настойчивые, настойчиво – лучевые.
Воспринимают нагрузки как вдоль, так и поперек оси вала.
Часто нагрузка вдоль оси только одного течения.
Настойчивые ( нагрузка поперек оси вала не допускается ).
Обеспечивают подвижность вдоль оси, вращение вокруг оси не нормируется или нельзя.
Встречаются рельсовые, телескопические или вальные линейные подшипники.
Шариковые винтовые передачи.
Обеспечивают сопряжение винт – гайка через тела качения.
По количеству линий тел качения Однорядные, Двухрядные, Многорядные ;
По способности компенсировать несоосность вала и втулки Самоустанавливающиеся.
Несамоустанавливающиеся.
На рис.1 с целью упрощения чертежа не показаны мелкие некоторые иные детали конструкции такого магнитного подшипника.
Главнаяотличительная особенность предлагаемого обыкновенного и изящноготехнического решения заключается в своеобразной комбинации магнитов по двум осям координат для автоматической компенсации как осевых, так и лучевых нагрузок на валу этого подшипника.
В случае использованиявысоких технологий правильного изготовления конструкции подобного бесконтактного подвеса с соблюдением минимальных зазоров вдоли миллиметра между магнитамии с применением современных магнитов типа « самарий – кобальт » такие магниты могут совершенно действительно использованы в динамических порядках нагрузок на валу в автотранспорте до 200 киловатт механической мощности.
магнитный Более эффективный дисковый, который был помянут для бесконтактной передачи значительного вращающего момента с ведущего вала на ведомый вал показан на рис.2.
Он заключается из двух параллельных дисков 1, 2, сделанных из каждого немагнитного материала, рабочих больших вечных магнитов 3, 4, размещенных на этих дисках – раазноименными полюсами навстречу друг другу.
Коэффициент редукции скорости ведущего и ведомого валов 5, 6 подобного бесконтактного редуктора устанавливается соотношением числа магнитов на этих дисках.

Кроме того, такой магнитный редуктор имеет кпд практически единицу.
Уже сейчас реально создание магнитных компактных бесконтактных редукторов на мощности от сотен ватт до 60 кВт, поскольку сила взаимного притяжения современных магнитов из сплавов типа « самарий – кобальт » на расстоянии долей мм достигает тысяч ньютонов С дальнейшим усовершенствованием магнитных материалов и постоянных магнитов магнитный редуктор вполне может передать до 100 – 150 кВт механической мощности.
T + A SACD 1250 R black Компания T + A представила четыре проигрывателя дисков, которые способны воспроизводить наиболее важнее музыкальные и видео форматы.
Благодаря этим новшествам было завоевано значительное улучшение качества механических компонентов, а также улучшение свойств чтения и воспроизведения дисков.
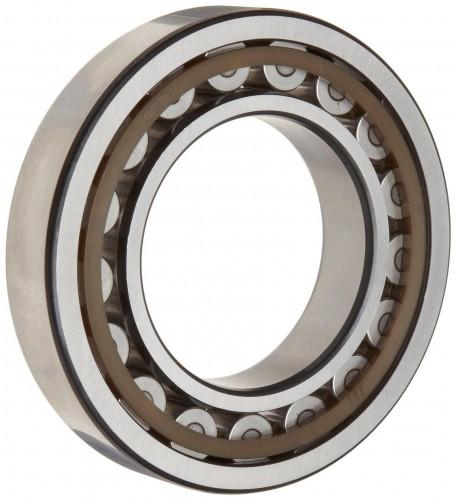
Дисковый механизм оборудован компонентами высочайшего качества : двигателями увеличенной надежности от Mabuchi, подшасси с превосходным затух
Подшипники являются наиболее разболтанным и хорошим элементом многих агрегатов от автомобиля до космического кораблика и ракеты.
Однако механические подшипники почти исчерпали собственное развитие.
Они располагают быстрейший износ, требуют регулярного ухода и летучи.
Кроме того, механическое
бесконтактные Известны электромагнитные подшипники вращения.
Однако это довольно непростые и ценные приспособления.
Я знаю вообще два типа подшипников : качения ( как в машинке, йо – йо и т д ) и скольжения ( область применения авиация, продовольственная промышленность ).
Качение – – в нем используются тела качения ( шары или ролики ).
Подшипник скольжения может представлять собой что угодно, хоть лыжи по снегу.
Подобно варианту – гидростатические ( смазка залита между кольцами ) и гидродинамическая ( смазку подают под давлением например насосом, и разжимают кольца, т.е. кольца вообще не соприкасаются ).
Считается, что на огромных скоростях здорово действуют на скольжении + смазка охлождает подшипник, к какому классу отнести магнитный я не знаю, спрос какого размера его можно сделать?
И на схеме видно что вместо духовного кольца выходит вал ?!
для присоединения его нужны муфты?
Подшипники ASB ( производства SNR ) серийно устанавливаются на следующие машины : Группа FIAT : Alfa – Romeo 145, 146, 147, 155, 156, 166, Fiat Seicento, Palio, Punto PSA : Citroen C3, C5, C8, Peugeot 206, 307, 807 Renault : Megane 2, Laguna, Espace IV, Trafic 2, Logane Группа VW : Audi A2, Seat Arosa, Leon, Skoda Fabia, VW Lupo, Polo ( производство FAG попатенту SNR ), Golf V, Passat, Octavia, Touran ( производство NSK попатенту SNR ), Touareg, Audi B8 BMW : Mini Porsche : Cayenne Ford : Focus, Mondeo ( FAG попатенту SNR ) Rover : 75 Volvo : S80 ( FAG попатенту SNR ) Продажа подшипников > >
Для верной работы шарикоподшипников, на них всегда необходима влиять определенная минимальная нагрузка.
Это особенно важно, когда подшипники работают при высочайших скоростях, когда силы инерции шариков и сепаратора, а также трение в смазочном материале могут оказывать отрицательное влияние на условия качения в подшипнике и вызвать проскальзывание шариков по дорожке качения, что приводит к повреждению дорожки качения.
Где купить химические реактивы.
принцип работы, скорость вращения и значение маркировок 608, Z, ZZ, RS. И какой ABEC выбрать
Подшипники: принцип работы, скорость вращения и значение маркировок 608, Z, ZZ, RS. И какой ABEC выбрать
Держитесь. Это очень сложная тема. Большая и неоднозначная. Маркировки в заголовке – это маленькая часть существующих подшипников: их много, для разных сфер жизни от простейших игрушек до космических кораблей. А мы рассмотрим те, что используются в самокатах, роликах и скейтбордах, ведь мы их продаём, а вы их покупаете) Это подшипники ABEC 608.
Лирика, которую можно пропустить, но лучше прочитать. Мы не делаем подшипники. В нашем распоряжении данные из необъятного интернета, а также логика и здравый смысл для изучения и систематизации этих данных. Мы попытались быть максимально объективными и перепроверяли всё, что перепроверяется. Но в теме всё равно остались туманные моменты: они не попали под научные стандарты и остались «на кончиках пальцев». Вы почувствуете эти моменты.
При этом статья даёт чёткое понимание заявленных в заголовке маркировок, всё честно.
Это дочитают не все. Мы попытались написать интересно и легко. Если вам будет тяжело читать, мы поймём и попробуем писать легче. А вы поймёте, как было непросто всё это писать.
Переходим к первому разделу, – он самый простой и короткий. Погнали)
Роль подшипников и принцип работы
Подшипники обеспечивают вращение с наименьшим сопротивлением. Главная задача подшипника – снизить силу трения поверхностей, став посредником между ними. На примере самокатов это будет внутренняя поверхность колеса и внешняя часть оси, на которую это колесо надевается.
Чтобы лучше это понять, посмотрим на три следующие фотографии.
Это подшипники ABEC-9 608 RS ждут своего применения в самокате
Это вид внутри. Внешнее кольцо и внутреннее движутся относительно друг друга благодаря шарикам
А вот один из тех подшипников уже стоит в центре самокатного колеса. Подшипник впрессовывается так, чтобы внешнее кольцо подшипника максимально плотно прилегало к колесу, а внутреннее – к оси. Так не будет скольжения между поверхностями, но колесо при этом будет вращаться на оси.
Отверстие в центре подшипника (оно же – отверстие в центре колеса) – это место, в которое войдёт ось.
Раз мы заговорили о размерах подшипников и их применении в самокатах, то остановимся подробнее на этой теме. Это и будет первая маркировка из заголовка статьи.
Маркировка 608
Метка 608 – это один из элементов более крупной категории: 6000. Это показатель того, на какую нагрузку рассчитаны подшипники, какой у них тип и размер. За каждый из этих показателей отвечает своя цифра (или число).
Цифра 6 означает «шариковый однорядный радиально-упорный подшипник». То есть внутри подшипника используются шарики, а не валики, лежат в один ряд, а не в два, и сам подшипник рассчитан на давление по радиусу, а не на ось.
Цифра 0 (вторая слева) означает, что это особо лёгкая серия подшипников. Они применяются в том числе в скейтах, роликах и самокатах. Это показатель нагрузки, которую выдерживает подшипник. За это отвечает его ширина. Модели других серий – шире или тоньше и выдерживают, соответственно, больше либо меньше нагрузки:
- 6800 – ещё легче
- 6900 – сверхлёгкая серия
- 6000 – наша особо лёгкая серия
- При этом 6200 – это просто лёгкая серия, готовая к более большому давлению
- А 6300 – средняя серия, готовая к тяжёлым нагрузкам
- А есть ещё 16000. Единица перед «6000» значит, что это та же самая модель, с той же допустимой нагрузкой, что и наша 6000, только зауженная, тонкая.
Система обозначений неудобная. Специалисты по подшипникам говорят, что многие показатели проще запомнить, чем понять. Почему 6800 легче, чем 6300? Как 6000 и 16000 могут быть рассчитаны на одинаковую нагрузку, если у них разная ширина? Не известно. Мы не задавались этим вопросом, так как он уже не по нашей теме.
Во введении мы предупреждали, что тема сложная и неоднозначная))
Цифра 8 означает внутренний размер.
В подписи к фото 3 мы сказали, что прилегание поверхностей должно быть максимально плотным. Такая плотность обеспечивается в том числе совпадением размеров подшипника и места для подшипника. Число 608 означает, что размер внутреннего отверстия подшипника равен 8 мм.
Вот несколько размеров серии 6000:
- в начале этого списка идут подшипники меньшего диаметра: 7 мм, 6 мм и т.д.
- 608 – внутренний диаметр (в.д.) 8 мм. Наш основной изучаемый размер.
- 609 – в.д. 9 мм
- 6000 – в.
д. 10 мм
- 6001 – в.д. 12 мм
- 6002 – в.д. 15 мм
- 6003 – в.д. 17 мм
- 6004 – в.д. 20 мм
- 6005 – в.д. 25 мм
- 6006 – в.д. 30 мм
- Это не весь список. Дальше подшипники увеличиваются на 5 мм с каждым шагом, доходя до 500 мм, то есть до 50 см. Представьте полуметровый подшипник, внутрь которого почти поместится крышка канализационного люка.
И это тоже не конец. Дальше подшипники продолжают расти, но уже с другими обозначениями:
Это подшипник Huisman для корабельного крана. Размер подшипника: 30 метров, что равно 12-этажному зданию. Точки снаружи и внутри круга – люди.
Грузоподъёмность подшипника. Её тонкости и переоценённая значимость.
Согласно данным европейского производителя подшипников Motion & Control NSK, грузоподъёмность подшипников серии 6000 – это 201 КГс в статике и 465 КГс в динамике.
Тонкость в том, что 1 кг – это 1 килограмм, а 1 КГс – это 1 килограмм-сила, то есть усилие, которое одно тело, весом в 1кг, оказывает на другое тело. То есть это просто давление весом без дополнительно приложенного усилия. При этом конвертеры величин ставят знак «равно» между 1 кг и 1 КГс.
В чём переоценённость «грузоподъёмности» скейтерских, самокатных и роликовых подшипников?
В том, что надо смотреть не на максимальную нагрузку подшипника, а на максимальную нагрузку самоката (или скейта, колёсной рамы роликов) в целом. Если у райдера сломается руль или погнётся дека, то ему будет не до мыслей «а ведь подшипник-то выдержал», потому что самокат всё равно пришёл в негодность. А максимальная нагрузка самокатов, обычно, от 50 до 110 кг., то есть меньше, чем у подшипников.
Мы не разбирались в том, есть ли разница между «грузоподъёмностью» и «макс.нагрузкой», потому что это не нужно для раскрытия темы. Если вы покупаете самокат или скейт:
- известного бренда
- с хорошей репутацией
- средней или высокой ценовой категории
то этой покупкой вы избавляете себя от переживаний. Раз в этой модели используется определённый подшипник, значит технологи всё рассчитали и продумали. (Только если подшипник не бракованный, но для этого есть гарантия).
Да, систематизация маркировок неудобная. Но маркировка – это удобный способ сокращения информации + стандартизация
Стандартизация означает, что все производители могут продавать свои подшипники по всему миру: и производители, и продавцы и покупатели говорят на одном языке – маркировочном.
Но тут тоже не всё так просто, потому что типов маркировок тоже несколько, в зависимости от страны производства. Иногда маркировки перекликаются между собой. Рассмотрим 3 примера:
- ГОСТ 1000800
- ISO 6800
- ISO 61800
Всё это одинаковые подшипники. Просто первый из России, второй из Японии, а третий из Европы. И это не весь список аналогов. Возможно, когда-то появится (или уже есть) система стандартов для подшипниковых стандартов.
А что касается удобства сокращения – тут без оговорок. Маркировка экономит очень много букв и места:
Формулировку слева на подшипник не нанесёшь
В этой иллюстрации мы использовали маркировку Z, что значит закрытость подшипника. Стало быть, пора осветить эту тему подробнее, тем более, что с маркировкой 608 (и немного вокруг неё) разобрались.
Маркировки Z, ZZ, RS и 2RS
Буквы Z и ZZ
Они означают закрытость подшипника: если в маркировке 1 буква Z, значит у подшипника одна закрытая сторона. Если стоит ZZ, то подшипник закрыт полностью – с обоих боков. Это позволяет заполнять внутреннюю часть подшипников смазывающим веществом. Смазки снижают трение, нагрев и разрушение подшипников, увеличивая их срок службы и обеспечивая более мягкий и плавный ход. Также боковые заглушки защищают внутреннюю часть подшипника от пыли, грязи и влаги.
Z = металлическая стенка с одной стороны
Обозначения RS или 2RS (он же 2RSH)
Это так же показатель закрытости подшипника, но уже с резиново-каучуковой шайбой поверх металлической заглушки. Такая заглушка даёт повышенную защиту от пыли и влаги. Буквы RS значат, что закрыта одна сторона, а 2RS или 2RSH значат, что закрыты обе стороны.
Модели RS (а может и 2RS, в зависимости от того, есть ли у них стенка с другой стороны). Разных марок, цветов заглушки и класса ABEC
Свойства и применение
Открытые подшипники используются в стерильных и просто чистых условиях: там, где они не могут забиться грязью или начать работать неравномерно из-за пыли. Открытые подшипники проще и дешевле изготовить, а так же они хоть на пару грамм, но меньше весят. Иногда это важно.
Закрытые подшипники созданы для грязных условий, например, в самокатах: они работают на улице, в нескольких сантиметрах от земли. Открытый подшипник в этих условиях заклинит через несколько метров езды.
Ещё эти показатели влияют на скорость вращения. По мнению блогеров, которые сидят на форумах про механику, электронику, ЧПУ и станкостроение, подшипники с металлическими стенками (Z и ZZ) подходят там, где нужна большая скорость вращения, чтобы резиновый уплотнитель не создавал трение, затормаживая собой движение. Например для фрезерных станков с оборотами 8 тысяч в минуту. А прорезиненные подходят там, где такая большая скорость не достигается, например, в катании на самокатах со скоростью около 2500 оборотов в минуту.
Как прокомментировать мнение блогеров из предыдущего абзаца? Звучит логично, и можно было бы потратить время на проверку этой информации, но, к счастью, для нас это уже уход от основной темы. Тем более, что бывают подшипники RS и 2RS с бесконтактным креплением уплотнителя, то есть не затормаживающие вращение.
Главное, что тема букв раскрыта, и можно переходить к последнему разделу.
ABEC
ABEC – это и маркировка подшипника и аббревиатура American Bearing Engineering Committee, то есть «американская ассоциация производителей подшипников». Это большая серьёзная компания, в которую входят мировые производители подшипников из Америки, Европы и Японии. Чтобы быть частью этой организации, надо делать такие подшипники, которые соответствуют конкретным требованиям, о которых поговорим дальше.
Число ABEC – это показатель точности сборки подшипника.
Сама надпись «abec» на подшипнике значит, что он – прецизионный. То есть «обладающий высокой точностью или созданный с соблюдением высокой точности параметров; высокоточный». А цифры означают степень этой точности параметров. Удобнее будет смотреть в таблице, где заодно указаны и другие стандарты + их аналоговость:
Теперь мы знаем, что ABEC-7 соответствует ISO (International Standards Organisation) 492-P4 и ГОСТу 520 класса 4: у всех более чем высокая точность изготовления – прецизионная.
(Да, получается, что это прецизионные подшипники прецизионной точности сборки…)
Разберёмся, что это значит.
Abec 1. Это стандартный уровень точности. Не низкий и не плохой, а стандартный, которому соответствует множество подшипников мира.
Abec 3. Повышенный класс точности. Используется в станках и в автомобилях – в ступицах и генераторах. Бывает в недорогих роликах.
Abec 5 и 7 – золотая середина. Их рассмотрим отдельно ниже.
Abec 9. Подшипники ещё более высокой точности. Здесь не используем слово «высочайшей», потому что в продаже уже появились ABEC-11. В их вращении минимизированы трения и вибрации.
Продолжаем углубляться. Держитесь, осталось немного))
Подшипник состоит из частей. Чем выше число ABEC, тем меньше радиальное и осевое биение этих частей. В этой системе ещё много параметров, но нам важны именно эти два. Они показывают, насколько внешнее и внутреннее кольцо «люфтят», то есть движутся вверх-вниз и вправо-влево относительно друг друга без особых усилий:
- Abec-5. Осевое биение внутреннего кольца– 8 тысячных миллиметра
- Abec-9. Осевое биение внутреннего кольца – 1 тысячная миллиметра
- Они отличаются друг от друга в 8 раз, но почувствуете ли вы это, катаясь по бугристому асфальту в ветреную погоду, если речь идёт о тысячных миллиметра…
- Abec-3 и 1.
Осевое биение не указано. Видимо, его погрешность столь велика, что американский подшипниковый комитет не стал снисходить до такого уровня неточностей. Или на это есть какая-то другая причина.
Официально, чем выше эта цифра, тем меньше зазоры между частями подшипника, то есть выше защита от пыли, грязи и влаги. Тем меньше вибраций и биений частей подшипника друг об друга. Тем плавнее и тише вращение: без ощущения металлического трения.
Значит, он должен быть долговечнее? На деле оказывается иначе. Рассмотрим два пункта:
- Чем выше число абек, тем сложнее получается подшипник. А сложные механизмы больше подвержены поломке и требуют более щадящих условий эксплуатации. Возможно, это связано с тем, что больший люфт 5х и 7х абеков выступает компенсатором ударной нагрузки.
- На поверхностях подшипника есть неровности. На первый взгляд, кажется, что поверхность идеально гладкая, и то же говорят ощущения, если провести пальцем. Но если посмотреть под микроскопом, то в металле колец и шариков будут неровные холмики и ямки.
Их трение друг об друга, умноженное на скорость вращения, и на условия эксплуатации, и на беспощадное время, приводят к появлению и развитию трещин в металле, а потом – к негодности.
Тут мы сталкиваемся с очередной неоднозначностью: непонятно, в какой момент параметры подшипников играют на сохранение и долговечность, а в какой – на разрушение. То есть возникает 2 вопроса:
Чем больше люфт – тем больше размах биения частей или тем дальше друг от друга части, которые могут биться?
Чем больше люфт – тем больше риск попадания посторонних частиц или тем больше вероятность, что они не задержатся внутри подшипника и не будут его разрушать?
Вместо ответа приведём факт из тусовки райдеров:
9е абеки выходят из строя значительно быстрее 5х и 7х.
ABEC 5 и 7 – золотая середина.
Сравнивая категории подшипников, правильнее говорить не только и не столько о характеристиках скорости, ударопрочности и общей долговечности, а больше о том, под какие цели больше подходит каждое сочетание этих характеристик ABEC. 5е и 7е подшипники не так чувствительны к ударам, как 9е, но обладают большей плавностью хода, чем 3е.
Инерция и скорость вращения подшипника
Какой подшипник быстрее? Попытаемся ответить на этот вопрос, исходя из уже прочитанной выше информации.
Каждое лето несколько раз в неделю наши покупатели выдвигаю версию, что чем выше число ABEC, тем быстрее крутится подшипник. Но в официальных выкладках по характеристикам ABEC не указана скорость. Там сказано, что чем выше число, тем выше точность исполнения: тем меньше вибраций, биений. С одной стороны, показатель скорости не упоминается. Но с другой, чем меньше биений, тем более ровный ход и тем выше КПД вращения. Вроде звучит логично.
Истина где-то посередине.
В этом случае корректнее говорить не про скорость, а про инерцию, то есть как долго самокат проедет после одного отталкивания. Да и скорость наверняка будет хоть чуть-чуть больше, если работа подшипника будет гладкой.
Но если мы добавим к этому степень гладкости и фактуру асфальта/бетона/рампы, на которых мы катаемся, нашу усталость и наличие/отсутствие ветра, то мысли об уровне ABEC могут потеряться окончательно: катаясь по неровной дороге вы вряд ли подумаете «ох, что-то седьмой абек не вывозит, тут уже девятый нужен».
Мнение райдера.
Высокий класс скорее нужен для точных приборов и медицинского оборудования, а в плане катания между 5м и 7м Абеками нет разницы. Это мнение Андрея Апрельского, который в том числе снимает обзоры на подшипники и катается на скейтбордах комплит 27 penny+oxelo из пластика, а также на деревянной доске 22` своей сборки. Но ярые фанаты катания и трюков могут не согласиться, на что имеют полное право, и мы их понимаем, поддерживаем и даём возможность купить трюковый самокат с подшипником ABEC-9.
Докопаться до истины – важно. Но наслаждаться катанием – важнее
Что сказать в качестве итога. Разбираться в подобных темах – значит стремиться к идеалу. Это хорошо: мы ценим это и пытаемся проделать этот путь вместе с вами. При этом всегда важно понять, когда пора остановиться:
- например, когда углубление в тему перестаёт быть интересным, обессиливает и заставляет потеть и нервничать
- или когда приходит понимание, что разница играет роль только в «вакууме», то есть в лабораторных условиях, оторванных от реальности
Вот выбираете вы между 3м и 7м абеком. И 7й конечно идёт плавнее. 3й тоже нормально идёт, но 7й легче стартует и более инерционный – дольше едет после отталкивания…
А если не знать, где какой, то есть не быть предвзятым? Разницу почувствуют не все.
Не нужно вникать в термин «непостоянство ширины внутреннего кольца подшипника в тысячных долях миллиметра», если вам от этого становится дурно. Вам это не нужно. Это термин из мрачных НИИ, очень далёкий от молодых и бодрых девчонок и парней, крутящих бэкфлипы на рампе под современную музыку.
Что делать
- Если вы непрофессиональный райдер, и вы просто тусуетесь с друзьями в вашем райончике, при этом не хотите много тратить, то берите 5й абек
- Тот же совет подойдёт начинающим райдерам, которые хотят сэкономить: 5й абек
- Если не профи, но можете себе позволить поднять планку, то берите 7й абек
- Тот же совет подойдёт начинающим, которые хотят войти в райдерство на повышенном уровне: 7й абек
- Ну а если вы претендуете на профессионализм в дисциплине, и у вас есть доступ к площадкам с хорошим покрытием, а также свободные деньги, то для вас 9й абек
- В любом случае кайфуйте от катания и от жизни)
А это древний подшипник Леонардо Да Винчи. Деревянный
Наверное, отлично бы подошёл к этому самокату (шутка)
Предельная частота вращения подшипников Московского Подшипникового Завода №7 (ООО “МПЗ-7”).
Под предельной понимают наибольшую допустимую частоту вращения, при превышении которой не может быть обеспечен расчетный ресурс подшипника. Для оценки предельной частоты вращения используют скоростной параметр (DPWn), наименьшие значения которого в зависимости от типа подшипника и вида смазочного материала приведены в табл. 79. Подбором конструкции, условий нагружения, смазывания и охлаждения значения скоростного параметра могут быть увеличены в 1,5-3 раза.
nпр = ( DPWn ) K / DPW
Здесь К – коэффициент, учитывающий влияние воспринимаемой подшипником нагрузки, оцениваемой по значению ресурса Ln, рис. 32. Как видно, для крупных подшипников nпр существенно снижается с увеличением габаритных размеров.
Для подшипников сверхлегких и особолегких серий диаметров предельная частота вращения может быть увеличена на 10% по сравнению с рассчитанной по формуле.
79. Значения скоростного параметра Dm, л
Тип подшипника | Значения Dpw n, мм об/мин, для смазочного материала | |
пластичного | жидкого | |
Шариковый: | ||
радиальный однорядный | 4,5·105 | 5,5·105 |
радиальный однорядный с защитными шайбами | 4,0·105 | – |
радиальный однорядный с уплотнениями | 4,0·105 | – |
радиальный сферический двухрядный | 4,0·105 | 5,5·105 |
радиально-упорный однорядный с углом контакта до 26° | 4,0·105 | 5.![]() |
упорный однорядный | 1,3·105 | 1,8·105 |
Роликовый: | ||
радиальный с короткими цилиндрическими роликами | 3,5·105 | 4,0·105 |
конический однорядный | 2,5·105 | 3,0·105 |
конический двухрядный | 2,0·105 | 2,5·105 |
конический четырехрядный | 1,5·105 | 2,0·105 |
Примечания: 1. Значения приведены для подшипников со стальным штампованным сепаратором, работающих при температуре не выше 100 °С.
2. При угле контакта 36° для радиально-упорных шариковых подшипников скоростной параметр снижается на 25%.
Тип подшипника определяет кинематику и потери на трение. Наиболее быстроходными являются прецизионные радиальные и радиально-упорные шарикоподшипники легких и сверхлегких серий. Подшипники тяжелых серий менее быстроходны. Для нормальных частот вращения применяют в основном подшипники класса точности 0 со стальными штампованными сепараторами.
В таблицах технических характеристик приводят значения предельных частот вращения для подшипников класса точности 0 с обычными для данных типов конструкциями сепараторов.
При повышенных частотах используют подшипники высокой точности с массивными, в основном латунными, бронзовыми текстолитовыми сепараторами. Для высокоскоростных узлов ведущие фирмы уже производят подшипники с телами качения из керамических материалов, которые вследствие малой плотности и высокой прочности, термо- и износостойкости, коррозионной стойкости являются весьма перспективными. В подшипниках с шариками из керамики на основе нитрида кремния Si3N4 меньше тепловыделение (вследствие меньшего коэффициента трения), меньшие центробежные нагрузки от тел качения, что позволяет повысить в 1,5-2 раза ресурс высокоскоростных узлов различных машин.
При проектировании быстроходного узла следует учитывать изменение зазора в подшипнике, возникающее вследствие перепада температур между наружным и внутренним кольцами. Уменьшение зазора может быть особенно значительным вследствие повышенного скольжения при быстром разгоне подшипника с пластичным смазочным материалом.
Рис. 32. Зависимость коэффициента K, учитывающего влияние нагрузки, от ресурса Lh и диаметра Dpw
Для повышения предельной частоты вращения решающее значение имеют смазочный материал и охлаждение подшипника. Желательно, чтобы подшипник работал в условиях жидкостного трения. Если используют пластичный смазочный материал или минеральное масло с вязкостью при
рабочей температуре не ниже 12 мм2с, а скоростной параметр (Dpw n) ≥ 300000 мм х об/мин, то наличие гидродинамического режима обеспечено заведомо.
Смазочный материал высокоскоростных подшипников должен обладать пониженной вязкостью и хорошими антикоррозионными свойствами.
Способы его подвода могут быть различны: циркуляционное смазывание, масляным туманом и др.
Необходимым условием достижения высокой частоты вращения является правильно выбранный предварительный натяг. При недостаточных натягах неизбежна повышенная вибрация, а при чрезмерно больших – повышенное тепловыделение, неоправданное снижение ресурса подшипника.
Показатели качества
В табл. 80 перечислены основные показатели качества подшипников качения, номенклатура которых установлена ГОСТ 4.479-87.
» Шарикоподшипник с четырёхточечным контактом – два в одном
Шарикоподшипник с четырёхточечным контактом (рис. 1) способен выдерживать осевые нагрузки в обоих направлениях в сочетании с радиальной нагрузкой определённой величины и обеспечивает очень жёсткий допуск на осевую фиксацию вала. Такой подшипник также может использоваться в условиях ограниченного пространства, поскольку его можно воспринимать как два однорядных радиально-упорных шарикоподшипника, объединённых в один. В результате такой подшипник прекрасно подходит для использования в промышленных редукторах, приводах локомотивов, компрессорах и других агрегатах.
Особенности конструкции и технические характеристики
Стандартные шарикоподшипники SKF с четырёхточечным контактом, также известные как подшипники QJ, состоят из цельного наружного кольца, разъёмного внутреннего кольца и сепаратора, центрируемого по наружному кольцу. Конструкция колец имеет ряд отличительных особенностей (рис. 2). Так, наружное кольцо имеет конструктивное сходство с наружным кольцом радиальных шарикоподшипников, но отличается величиной поперечного сечения и геометрией дорожек качения. Дорожка качения радиального шарикоподшипника имеет кольцевую геометрию.
Наружное кольцо шарикоподшипника с четырёхточечным контактом имеет две симметричные дорожки качения, которые пересекаются в центре кольца в одной точке. Такую форму ещё называют «готической аркой». Центры окружностей двух дорожек качения имеют незначительное смещение в осевом направлении (рис. 2). Внутреннее кольцо разделено на две половины и имеет в основе тот же конструктивный принцип, что и наружное кольцо. Это даёт определённое преимущество по сравнению с конструкцией радиальных шарикоподшипников. Конструкция дорожек качения наружного кольца позволяет устанавливать угол контакта (стандартный – 35°) и величину осевого зазора независимо друг от друга. Другими словами, существует возможность добиться определённой величины осевого зазора без изменения величины угла контакта (определяется как отношение радиуса кривизны дорожки качения и диаметра шарика).
Для подшипника с углом контакта 35° требуются высокие заплечики дорожки качения. Такой подшипник с цельным внутренним кольцом, в отличие от разъёмной конструкции, невозможно собрать с использованием максимального количества шариков. Стандартная процедура сборки подшипника включает три операции:
- вставка сепаратора в наружное кольцо,
- запрессовка шариков в сепаратор,
- вставка половин внутреннего кольца с каждой из сторон.
Внутренние кольца не являются самоудерживающимися. Чтобы предотвратить рассыпание подшипника во время транспортировки или погрузочно-разгрузочных работ, в его отверстие помещают пластиковую вставку.
Теоретически один шарик имеет четыре разных точки контакта с кольцами (рис. 3). Но такое положение шарика возникает только при воздействии радиальной нагрузки. В реальных условиях зачастую на подшипник действует исключительно осевая нагрузка (рис. 4а), которая передаётся только в двух точках контакта в диагональном положении. В случае изменения направления осевой нагрузки две точки контакта перемещаются в противоположное положение. Именно по этой причине подшипники данного типа способны выдерживать осевые нагрузки в обоих направлениях. Также возможны условия, при которых возникают комбинированные нагрузки с преобладанием осевой составляющей (рис. 4b). Чтобы обеспечить аналогичный эффект с помощью однорядных радиально-упорных шарикоподшипников, необходимо установить два подшипника по O-образной или X-образной схеме. Это означает, что применение шарикоподшипников с четырёхточечным контактом позволяет разрабатывать более компанктные узлы и обеспечивает экономию пространства. Два однорядных радиально-упорных шарикоподшипника могут быть заменены одним шарикоподшипником с четырёхточечным контактом. Важным условием является то, что для нормальной работы шарикоподшипника с четырёхточечным контактом должна преобладать осевая нагрузка. SKF рекомендует соотношение нагрузок Fa/Fr > 1,27.
В стандартном исполнении шарикоподшипники SKF с четырёхточечным контактом оснащаются механически обработанным латунным сепаратором оконного типа (суффикс обозначения MA) (рис. 1a) или литым сепаратором оконного типа из полиэфирэфиркетона (суффикс обозначения PHAS) (рис. 1b). Оба сепаратора центрируются по наружному кольцу. Это позволяет увеличить допустимую частоту вращения. Специальная конструкция симметричного сепаратора в свою очередь позволяет разместить максимальное количество крупных шариков.
На рис. 5 приведены основные характеристики подшипников SKF серии QJ.
Нагрузка, номинальный ресурс и частота вращения
Принимая во внимание компактную конструкцию шарикоподшипника с четырёхточечным контактом может показаться, что номинальная грузоподъёмность согласованного комплекта двух однорядных радиально-упорных шарикоподшипников может быть сравнительно выше. На рис. 6 представлено сравнение номинальной грузоподъёмности подшипников QJ серий диаметра 2 и 3 и согласованных комплектов радиально-упорных шарикоподшипников серий 72 B и 73 B соответственно. На рисунке видно, что грузоподъёмность шарикоподшипника с четырёхточечным контактом практически не уступает грузоподъёмности соответствующего комплекта радиально-упорных шарикоподшипников. Таким образом с помощью шарикоподшипника с четырёхточечным контактом можно сэкономить до 50 % пространства в осевом направлении.
Также необходимо учитывать номинальный ресурс. Ключевым фактором здесь является эквивалентная динамическая нагрузка, рассчитываемая следующим образом:
P = 0,60×Fr + 1,07×Fa
для шарикоподшипника с четырёхточечным контактом (угол контакта 35°),
P = 0,57×Fr + 0,93×Fa
для согласованного комплекта радиально-упорных шарикоподшипников (угол контакта 40°).
Очевидно, что величина эквивалентной динамической нагрузки на шарикоподшипник с четырёхточечным контактом будет выше, главным образом, за счёт меньшего угла контакта. При этом более низкий номинальный ресурс в значительной степени компенсируется преимуществами компактной конструкции.
На рис. 7 сравнивается предельная частота вращения подшипников серии QJ 2 и QJ 3 с предельной частотой вращения согласованных комплектов подшипников серий 72 B и 73 B. На рисунке видно, что в первом случае номинальная частота вращения выше приблизительно на 70 %. Это может объясняться меньшим углом контакта подшипников (35° по сравнению с 40°), конструкцией и материалом сепараторов (цельные, латунь или полиэфирэфиркетон), центрированием сепараторов по наружному кольцу и специальными окнами сепаратора для смазки.
Конструкция сопряжённых компонентов
Во многих случаях шарикоподшипник с четырёхточечным контактом используется в сочетании с радиальным подшипником, например, цилиндрическим роликоподшипником. В этом случае важно, чтобы шарикоподшипник с четырёхточечным контактом воспринимал только осевую нагрузку. Таким образом, наружное кольцо шарикоподшипника с четырёхточечным контактом не должно быть зафиксировано в осевом и радиальном направлениях, а должно устанавливаться с радиальным зазором (от 1 до 2 мм) в корпусе (рис. 8). В противном случае наружное кольцо подшипника не сможет компенсировать перемещения из-за нагрева, что вызовет дополнительные нежелательные нагрузки на подшипник. Чтобы предотвратить вращение наружного кольца, на наружных кольцах большинства подшипников предусмотрены два фиксирующих паза, которые позволяют соединить наружное кольцо с корпусом с помощью штифта (рис. 8). Если осевой фиксации наружного кольца избежать невозможно, наружное кольцо должно быть, по крайне мере, точно отцентрировано при монтаже.
Также важно, чтобы две половины внутреннего кольца всегда были зафиксированы в осевом направлении.
Области применения
Возможность использования шарикоподшипников с четырёхточечным контактом следует рассматривать в тех случаях, когда конструкция имеет ограниченное пространство, при наличии больших осевых нагрузок в обоих направлениях или при высокой частоте вращения. Подобные условия могут возникать в насосах, тормозах-замедлителях, компрессорах, промышленных редукторах или автомобильных коробках передач, тяговых двигателях и рулевых колонках.
Винтовые компрессоры (рис. 9а) применяются во многих отраслях промышленности для сжатия различных газов при относительно высоком давлении. Перепад давления между двумя концами ротора компрессора приводит к возникновению осевых нагрузок, которые могут восприниматься шарикоподшипниками с четырёхточечным контактом. Узкий зазор между двумя роторами, а также между роторами и корпусом компрессора требует наличия жёсткой конструкции подшипников и малых осевых зазоров.
Тормоза-замедлители (рис. 9b) преобразуют кинетическую энергию грузового автотранспорта в тепло. Для этого требуются высокоскоростные подшипники, которые способны выдерживать быстрые изменения частоты вращения.
Использование многофазных насосов (рис. 9с) позволяет повышать эффективность эксплуатации нефтяных месторождений по сравнению с традиционными методами. Насосы устанавливаются на дне моря и увеличивают давление подачи газонефтяной смеси. Это обуславливает очень высокие требования к надёжности насосов.
Редукторы ветряных турбин (рис. 9d) передают энергию главного вала, вращающегося с очень низкой частотой (порядка 18 об/мин), на генератор, частота вращения которого выше приблизительно в 100 раз. При вращении с высокой частотой косозубые колёса вала вызывают большие осевые нагрузки. В этом случае применяется комбинация цилиндрического роликоподшипника и шарикоподшипника с четырёхточечным контактом.
В области железнодорожного транспорта (рис. 9e) существуют два основных варианта применения данных подшипников. В редукторах и тяговых двигателях, как правило, используют комбинацию цилиндрических роликоподшипников и шарикоподшипников с четырёхточечным контактом. Подшипники тяговых двигателей должны быть защищены от повреждений, возникающих в результате прохождения электрического тока. Надёжным решением в данном случае является использование изолированных подшипников INSOCOAT с электроизоляционным покрытием.
INSOCOAT является зарегистрированной торговой маркой SKF Group.
Береги подшипник смолоду!
Береги подшипник смолоду!
Даже высококачественные подшипники не будут работать долго, если не обслуживать их соответствующим образом. Нарушение правил эксплуатации приводит к выходу подшипника из строя раньше положенного срока. А простой электрооборудования в ремонтный период влечет за собой убытки предприятия. Этого можно избежать, если своевременно получить сигнал о некорректной работе подшипникового узла электродвигателя и принять соответствующие меры.
Как определить состояние подшипникового узла?
Определить состояние подшипника в процессе эксплуатации поможет мониторинг основных рабочих характеристик.
-
Уровень и характер шумов определяются с помощью звукоулавливающих приборов и наблюдений.
-
Уровень вибрации измеряется анализатором частотного спектра, но такой метод требует владения технологией вибродиагностики.
«Русэлпром» рекомендует
решить задачу измерения уровня вибрации путем установки датчика контроля вибрации. Эта опция предоставляет максимально точные данные о работе подшипникового узла в оперативном режиме.
«Русэлпром» рекомендует
установить датчики контроля температуры подшипникового узла для своевременного получения информации о её повышении до опасных значений.
Важно! Решение об установке датчиков необходимо принять на этапе заказа электродвигателя.
-
Состояние смазочного материала. Следите, чтобы смазка была чистой, не содержала посторонних включений. Также она не должна быть слишком густой, чтобы не замедлять процесс вращения.
О нарушении в работе механизмов часто свидетельствуют несколько признаков одновременно, так как основные рабочие характеристики подшипника – шум, вибрация, температура – взаимосвязаны.
О чем свидетельствуют результаты мониторинга?
Превышение уровня шума
Может иметь электромагнитные или механические причины. Неисправность подшипника относится к группе механических шумов. По характеру этого шума можно установить вид неисправности:
-
cвистящий шум указывает на отсутствие смазочного материала;
-
скрежет свидетельствует о загрязнении смазки, наличии твердых частиц в ней, поломке сепаратора или задевании вала за крышки подшипника. Такой же характер шума возникает в начале разрушения рабочей поверхности втулки или вала;
-
стук в подшипнике возникает при сильном разрушении поверхности втулки или вкладыша, разрушении поверхности кольца, шарика или ролика. Причиной стука также может быть ослабление посадки внутреннего кольца на валу или наружного кольца в подшипниковом щите.
При появлении повышенного уровня шума подшипник нужно разобрать и внимательно осмотреть, выявить причины нарушения работы и принять соответствующие меры по их устранению.
«Русэлпром» рекомендует
не вскрывать электродвигатель, если не истек срок его гарантии. По всем вопросам нарушения работы привода обращаться к специалистам завода-изготовителя.
Повышенная вибрация
Самое опасное для подшипника явление. Его возникновение может быть связано с нарушением работы самого подшипника или с неисправностью других частей электродвигателя.
Если причина связана с подшипником, то вибрация сопровождается шумом и перегревом. Необходимо разобрать механизм, определить его состояние и заменить подшипник, если он критически поврежден.
Если вибрация продолжается и после замены подшипника, причина связана с другими частями электродвигателя. Её необходимо найти и устранить.
Перегрев подшипникового узла
Он может возникать по разным причинам. Вот основные из них:
-
в системе смазки – загрязнение системы, загустение смазочного вещества, недостаток или отсутствие смазки, избыток смазки;
-
загрязнение подшипника – попадание в механизм инородных тел.
В обоих случаях нужно промыть систему смазки и подшипник, просушить детали механизма, пополнить систему новой смазкой, собрать подшипниковый узел и протестировать его работу.
«Русэлпром» рекомендует
тщательно подбирать смазочный материал. От этого зависит стабильная работа не только подшипникового узла, но и всего двигателя.
-
превышение допустимой нагрузки электродвигателя – следует остановить работу механизма и дать остыть.
-
чрезмерный износ, разрушение подшипника – следует разобрать подшипниковый узел, внимательно осмотреть механизм, выявить причины разрушения, устранить их, а затем заменить подшипник на новый.
Как определить причины неисправной работы подшипника?
Передовые предприятия отказались от системы планово-предупредительных ремонтов. Установка датчиков мониторинга позволяет оперативно отслеживать состояние оборудования и разбирать электродвигатель только в случае выявления признаков его некорректной работы.
Для подробного анализа нарушения работы подшипникового узла нужно провести его ревизию – разобрать.
Ревизия подшипникового узла наглядно демонстрирует состояние механизма и его пригодность к дальнейшей эксплуатации. Порядок действий:
- Открыть электродвигатель и разобрать подшипник. На этом этапе нужно обратить внимание на состояние смазки: её количество, густоту, загрязненность.
- Очистить подшипник от старой смазки бензином или керосином.
- Внимательно осмотреть поверхности самого подшипника и смежных деталей на наличие повреждений.
- Оценить пригодность к дальнейшей эксплуатации подшипника. Для этого нужно учесть: степень повреждения подшипника, условия эксплуатации, режим его работы.
«Русэлпром» рекомендует
установить связь со специалистами завода-изготовителя вашего электродвигателя. Вы получите не только оперативное компетентное решение технических задач, но и внесёте свой вклад в улучшение качества продукции.
Если ревизия показала небольшие повреждения, необходимо определить причину по характеру повреждений и устранить её. Затем произвести замену смазочного материала и собрать механизм. После сборки следует сначала протестировать электродвигатель, запустив его вхолостую. Если уровень шума и вибрации не превышают допустимые пределы, не происходит чрезмерный нагрев, электрическую машину можно соединять с приводимым механизмом и продолжать работу устройства.
В таблице перечислены основные виды повреждений подшипников, возможные причины их возникновения и меры по устранению причин неисправной работы механизма в целом.
Откалывание мелких частиц материала подшипника от гладкой поверхности дорожки качения или элементов качения в результате явления усталости при качении, в связи с чем возникают участки с шероховатой и крупнозернистой структурой поверхности.![]() |
|
|
|
Тусклые или мутные пятна на поверхности вместе с незначительным общим износом.![]() |
|
|
|
Образование на дорожках качения и поверхностях тел качения линейных ударов. Происходит это явление при легких (незначительных) заклиниваниях по каким-либо причинам тел качения в гнезде сепаратора (например, скольжения из-за избыточного, или недостаточного количества смазки или неправильного выбора ее марки).![]() |
|
|
|
Размазывание является поверхностным дефектом, который возникает при наличии малых закаливаний между элементами подшипника, вызванных разрывом слоя смазки и/или скольжением. Образование шероховатости на поверхности происходит вместе с оплавлением поверхности. | |
|
|
Образование мелких частей, которые отламываются в результате чрезмерной нагрузки или ударной нагрузки, действующей локально на часть угла ролика или бортика кольца с дорожкой качения.![]() |
|
|
|
Трещины на кольце с дорожкой качения и на элементах качения. Продолжение эксплуатации подшипника в таком состоянии приводит к еще большим трещинам и расколам. | |
|
|
Повреждения сепаратора включают в себя деформации сепаратора, разлом и износ.![]() |
|
|
|
Если инородные частицы попадают в зону контакта качения, происходит выщербливание на поверхности дорожки качения или поверхности элементов качения.![]() |
|
|
|
Поверхность тел качения или поверхностей дорожек качения имеет матовый цвет и на них имеются ямки (лунки) от инородных тел. | |
|
|
Износ представляет собой повреждение поверхности вследствие трения скольжения на поверхности дорожки качения, элементов качения, края ролика, поверхности буртика, ячеек сепаратора и т.![]() |
|
|
|
Износ происходит вследствие периодического скольжения между двумя поверхностями. Истирание возникает на поверхности посадки, а также на поверхности контакта между дорожкой качения и элементами качения. Фреттинг-коррозия (истирание) является альтернативным термином для описания красновато-коричневых или черных частиц износа | |
|
|
Подобно различным типам истирания, ложное бринеллирование представляет собой образование выбоин, имеющих сходство с вмятинами Бринелля, и происходит вследствие износа, вызванного вибрациями и колебаниями в точках контакта между элементами качения и дорожкой качения.![]() |
|
|
|
Ползучесть представляет собой явление, при котором имеет место относительное скольжение на поверхностях посадки и, в связи с этим, возникает зазор на посадочных поверхностях. Ползучесть приводит к глянцеватому внешнему виду поверхности, иногда с образованием задиров или износом. | |
|
|
Если происходит резкий перегрев в процессе вращения, подшипник изменяет цвет.![]() |
|
|
|
Когда через подшипник проходит электрический ток, происходят дуговой пробой и горение тонкого слоя смазки в точках контакта между дорожкой и элементами качения.![]() |
|
|
|
Ржавчина и коррозия подшипников представляют собой пятна на поверхностях колец и элементов качения и могут встречаться с интервалом, соответствующим шагу элементов качения на кольцах или по всей поверхности подшипника. | |
|
|
Царапины в виде прямых линий на поверхности дорожек качения или элементов качения, образовавшиеся в период монтажа или демонтажа подшипника.![]() |
|
|
|
Изменение цвета сепаратора, элементов качения и дорожки качения происходит в результате реакции смазочного материала и материала элементов подшипника при высокой температуре. | |
|
|
По статистике, всего 1% всех подшипников отрабатывает заложенный срок службы. Всё потому, что этот срок рассчитывается при эксплуатации электрической машины в идеальных условиях. Как же создать эти идеальные условия и продлить жизнь механизма?
- проводите регулярный осмотр подшипникового узла и электродвигателя в целом, как в состоянии покоя, так и в процессе эксплуатации. Датчики контроля вибрации и температуры подшипника, заложенные во время производства электрической машины, помогут своевременно выявить признаки неисправной работы механизма и принять меры по устранению причин неисправностей;
- соблюдайте чистоту механизма подшипника: вытирайте вытекшее масло чистыми салфетками, плотно закрывайте крышку электродвигателя, чтобы избежать попадания пыли, влаги и инородных предметов;
- следите за состоянием смазки в механизме, поддерживайте её оптимальное количество, своевременно производите замену;
- используйте правильно подобранные качественные смазочные материалы, храните их в чистом сухом месте;
- монтаж и демонтаж механизма подшипникового узла производите осторожно с использованием специальных инструментов, которые должны быть максимально чистыми, как и руки мастера.
Следуя этим советам, вы убережете подшипник – от поломки, электродвигатель – от внезапного выхода из строя, а производство – от простоя и неминуемых убытков. Так что, береги подшипник смолоду!
Если у вас возникли вопросы, наши специалисты готовы на них ответить. Звоните:
8 (495) 600-42-53 доб. 3292 – Дмитрий Гаврилюк, инженер технической дирекции,
8 (812) 462 88 38 – Юрий Михалёв, инженер по оборудованию.
8 (800) 301-35-31, 8 (495) 788-28-27 – контакт-центр.
Также читайте:
Электродвигатели 7AVE – энергосберегающие решения концерна «Русэлпром»
Особенности обозначений ГОСТ и МЭК (IEC)
10 простых советов по продлению срока службы двигателя
3 вопроса о покупке электродвигателя
Проблемы подшипников качения | Спектральная вибродиагностика
Русов В.А.
“Диагностика дефектов вращающегося оборудования по вибрационным сигналам” 2012 г.
3.1. Диагностика дефектов уровня «подшипник»
К уровню «подшипник» относятся все дефекты опорных подшипников агрегатов, и самих опорных стоек. Поскольку наибольшее распространение в практике нашли подшипники качения и скольжения, в данном разделе рассматриваются особенности диагностики дефектов именно этих типов подшипников.
Подшипники
качения различных типов и марок, шариковые и роликовые, радиальные и радиально
– упорные, однорядные и двухрядные и т. д. широко применяются во вращающемся оборудовании
различного назначения. Без преувеличения можно сказать, что большая часть
ремонтов оборудования, особенно малой и средней мощности, производится по причине
дефектов опорных подшипников качения. Поэтому вопросы оперативной оценки технического
состояния таких подшипников, диагностики возникающих в них дефектов, а также
прогнозирования возможности их дальнейшей эксплуатации, занимают одно из самых важных
мест в работе служб вибрационной диагностики.
В данной главе сделан достаточно краткий обзор основных диагностических методов, применяемых для оценки качества подшипников, определения дефектов на различных стадиях развития, расчета остаточного ресурса подшипников качения. Причина краткости описания проста – каждый из перечисленных ниже методов требует для своего полного описания отдельной книги.
3.1.1.1. Основные признаки и особенности развития дефектов
Наличие дефекта в подшипнике качения легко выявляется несколькими способами. Дефект может быть диагностирован «на слух», по форме вибрационного сигнала, по спектру, по СКЗ сигнала, по спектру огибающей вибрационного сигнала, с использованием «пик-фактора», «эксцесса», и другими методами.
Во
вступительном разделе мы рассмотрим различные особенности и признаки возникновения,
развития и диагностики дефектов подшипников качения, акцентируя внимание на тех
особенностях, которые нам понадобятся далее, для описания того или иного метода
диагностики подшипников. Это позволит уменьшить дублирование описательной
информации, которую необходимо приводить при описании каждого метода
диагностики дефектов.
Характерная форма вибрационного сигнала, в данном случае, зарегистрированного на опоре с подшипником качения, имеющем достаточно развитый дефект состояния, для примера, приведена на рисунке 3.1.1.1. На этом рисунке хорошо видны две наиболее характерные, и важные для диагностики, составляющие сигнала вибрации – фоновая, и импульсная.
Фоновое, или среднее значение уровня вибросигнала, регистрируемого на подшипнике качения, характеризуется каким – то усредненным значением, например среднеквадратичным значением виброскорости. Это значение вибрации достаточно просто может быть замерено при помощи обычных виброметров.
В
моменты прохождения через «несущую», нагруженную зону подшипника качения,
дефектного элемента, или элементов, на вибросигнале появляется четко выраженный
амплитудный пик, некий энергетический импульс. Параметры этого импульса
определяются видом, локализацией и степенью развития дефекта подшипника. Каждый
такой ударный импульс обладает четырьмя основными диагностическими параметрами.
Это максимальная амплитуда импульса, частота свободных (заполняющих) колебаний,
скорость затухания амплитуды этих колебаний, и частота повторения импульсов.
Наиболее
важным параметром, характеризующим степень развития дефекта подшипника,
является амплитуда ударного импульса. Для измерения этого параметра импульса в
приборах вибрационного контроля должны быть предусмотрено использование
высокочастотных датчиков измерения вибрации и применения специальных пиковых
детекторов или достаточно высокочастотных АЦП. Это обусловлено тем, что ударные
импульсы имеют сравнительно высокую частоту. Локализация дефекта, место его
расположения, обычно уточняется по частоте следования импульсов, для чего
используются спектральные методы.
Если диагностику состояния опорных подшипников качения проводить по параметрам временных вибрационных сигналов, то основное внимание следует уделить двум. Это, во-первых, количественное значение общего уровня фона вибрации и, измеренное лучше в размерности СКЗ, во-вторых, это соотношение между уровнями фона вибрации и амплитудами пиковых значений в вибрационном сигнале.
В самом общем случае изменение технического состояния подшипника качения, возникновение и развитие в нем дефектов, за весь период его службы можно, разделить на пять основных этапов. Эти этапы схематически показаны на рис. 3.1.1.2. На этом рисунке по вертикали отложен уровень вибрации в размерности виброскорости (мм/сек), а по горизонтальной оси отложено относительное время эксплуатации подшипника.
Обобщенное
техническое состояние подшипника, на каждом этапе его эксплуатации,
определяется зоной между двумя линиями вибрационных уровней. Нижняя линия соответствует
значению фонового уровня вибрации, определенному в размерности СКЗ виброскорости,
а верхняя линия соответствует усредненной амплитуде ударных импульсов, возникающих
при работе подшипника качения.
Как
мы уже отмечали, этапов, характеризующих изменение технического состояния
подшипников качения, можно выделить пять. На первом этапе, на рисунке это зона до
границы с отметкой «1», общее техническое состояние подшипника будем считать
идеальным. Эту зону можно считать не зоной наличия дефектов, а зоной их
первичного возникновения. Дефекты еще не оказывают влияния на вибрации подшипников,
все имеющее место увеличение вибрации обусловлено естественным износом
поверхностей качения подшипников. На этом этапе пики вибрации превышают уровень
фона незначительно, а сам «фоновый уровень» вибрации, в данном случае это СКЗ
виброскорости, значительно меньше нормируемых значений тревожного и аварийного
уровней, принятых для данного класса оборудования.
Зона «1-2» на рисунке 3.1.1.2. В этой зоне, начиная с границы «1», в подшипнике появляется и начинает развиваться какой-либо дефект, который сопровождается ударными вибрационными импульсами, амплитуда который быстро растет по величине. «Разрушающая энергия» импульсов затрачивается на «углубление» дефекта в рабочих поверхностях подшипника, в результате чего происходит еще большее увеличение энергии импульсов. Уровень фона вибрации по своей величине при пока этом почти остается неизменным, т. к. дефект носит локальный характер и на общем состоянии подшипника пока не сказывается. Повторим, что это зона возникновения дефекта в процессе эксплуатации.
Зона
«2-3». Начиная с границы «2» ударные импульсы в подшипнике достигают по своей
энергии, применительно к графику это увеличение по амплитуде, практически максимального
значения. Дальше амплитуда импульсов уже растет немного. Количественное значение
максимума энергии импульсов определяется типом подшипника и условиями его эксплуатации.
Выделяющаяся в подшипнике энергия импульсов уже столь велика, что ее достаточно
не только «для углубления», но и для расширения зоны дефекта. На данной стадии процесс
саморазвития дефекта начинает идти более быстро. Одновременно с этим и уровень
фона тоже растет достаточно монотонно. Можно сказать, что дефект набирает силу,
готовиться к решающему нападению.
Зона
«3-4». Это зона перехода дефекта подшипника от стадии «сильный дефект» к полной
деградации. Процесс начинается с границы «3». Геометрическая зона развития дефекта
здесь уже столь велика, что подшипник начинает «терять» свое основное назначение
– обеспечивать вращение поддерживаемого вала с минимальным трением. Возрастают потери
в подшипнике на вращение ротора и, как результат, увеличивается энергия,
выделяющаяся в подшипнике, растет уровень фона. Это уже этап саморазрушения
подшипника.
Зона «4-5». Это последний этап развития дефекта, когда он охватил уже весь подшипник, вернее говоря все то, что осталось от подшипника. Уровень фона вибрации практически сравнялся с уровнем пиков, точнее говоря, весь вибрационный сигнал состоит из пиков. Работы подшипников качения в этой зоне следует избегать, хотя, если говорить точнее, она уже просто невозможна.
Все эти вышеперечисленные этапы ухудшения состояния подшипника свойственны практически всем видам дефектов, имеющих место в любых разновидностях подшипников. В зависимости от ряда конструктивных и эксплуатационных параметров подшипников могут наблюдаться различия в длительности описанных этапов, в интенсивности вибрационных процессов в них, но общая картина развития дефектов не меняется.
Есть
и другие характерные признаки наличия дефектов в подшипниках качения.
При работе подшипника с дефектами на поверхностях качения в спектре вибрационного сигнала появляются характерные составляющие, гармоники, с собственными частотами, по которым можно достаточно корректно выявить место нахождения дефекта. Численные значения частот этих гармоник зависят от соотношения геометрических размеров элементов подшипника, и конечно однозначно связаны с оборотной частоты вращения ротора контролируемого механизма.
В
нагруженном подшипнике качения можно дифференцировать четыре основные, характерные,
применяемые для диагностики частоты – гармоник. Это гармоники (от оборотной
частоты) вызываются специфическими процессами на внешней обойме подшипника, на внутренней
обойме подшипника, связаны с работой сепаратора подшипника, и с частотой
вращения тел качения – шаров или роликов. Рассмотрим, для упрощения без промежуточных
математических выкладок, формулы для расчета этих частот.
Частота обкатывания тел качения по внешней обойме подшипника, часто в литературе обозначаемая как BPFO:
Fн = Nтк / 2 х F1 ( 1 – Dтк / Dc х cosj )
где: Nтк – количество тел качения в одном ряду подшипника;
F1 – оборотная частота вращения ротора;
Dтк – диаметр тела качения;
Dc – средний диаметр сепаратора;
j - угол контакта тела качения с обоймой.
Частота обкатывания тел качения по внутренней обойме – BPFI:
Fв = Nтк / 2 х F1 ( 1 + Dтк / Dc х cos j )
Частота работы сепаратора – FTF:
Fс = 1 / 2 х F1 ( 1 – Dтк / Dc х cos j )
Частота работы (вращения) тел качения – BSF:
Fтк = 1 / 2 х F1 х Dтк / Dc ( 1 – Dтк2 / Dc2 х cos2 j )
Как
видно из этих формул, для точного определения характерных гармоник работы
подшипника качения достаточно 4 первичных параметров, три из которых являются
конструктивными, а четвертый определяется рабочей частотой вращения ротора.
Данные формулы расчета характерных подшипниковых частот являются достаточно простыми, но не всегда удобными для практики. Сложность заключается в том, что они включают в себя угол контакта тел качения с обоймами. Этот параметр не всегда известен точно и в процессе работы подшипника, по мере износа рабочих поверхностей подшипника, может изменять свое значение.
В практике удобнее использовать более простые формулы, не включающие в себя этот угол, в результате, естественно, менее точные, чаще всего приемлемые для практической диагностики. Приведем и эти формулы:
Частота обкатывания тел качения по внешней (наружной) обойме – BPFO:
Fн = F1 ( Nтк / 2 – 1,2 )
Частота обкатывания тел качения по внутренней обойме – BPFI:
Fв = F1 ( Nтк /2 + 1,2 )
Частота работы сепаратора – FTF:
Fс = ( 1 / 2 – 1,2 / Nтк )
Частота вращения тел качения – BSF:
Fтк = ( Nтк / 2 – 1,2 / Nтк )
Алгоритм использования этих формул достаточно прост – если в спектре вибрационного
сигнала появляются гармоники с такими частотами, то можно говорить о дефектах в
соответствующем элементе подшипника. Так это можно трактовать теоретически,
практически же все выглядит сложнее.
Использовать эти формулы, опираясь на анализ «прямых спектров» (классических спектров Фурье от всего сигнала) следует очень осторожно, достоверность диагностики с их использованием может быть не высокой. Достаточно часто даже при наличии в подшипнике явного дефекта в вибросигнале характерные частоты могут полностью отсутствовать, иметь сдвиг по частоте, или иметь очень малый уровень.
3.1.1.2. Методы диагностики дефектов подшипников
Для
оценки технического состояния и диагностики дефектов подшипников качения
разными авторами и компаниями разработано достаточно много различных методов.
Естественно, что все эти методы, различные по своим теоретическим предпосылкам,
имеют разную трудоемкость, требуют различного приборного обеспечения и могут
применяться для различных целей. Конечно, итоговая информация, полученная в
результате использования этих методов, имеет различную информативность и
достоверность.
В данном разделе мы попытаемся, очень обзорно и поверхностно, рассмотреть и сравнить основные методы, чаще всего применяемые в практике. В основе сравнения будем использовать параметр, который назовем как практическая применимость и эффективность. При этом будем систематизировать эти методы исходя только из основных, базовых, теоретических предпосылок, возможности применения их на различных этапах развития дефектов подшипников.
В самом общем случае оценка технического состояния и поиск дефектов подшипников качения может производиться при четырех наиболее распространенных методов, по следующим диагностическим параметрам:
1. По величине СКЗ виброскорости
Данный метод позволяет выявлять дефекты подшипников
на последних стадиях, начиная, примерно, с середины третьего этапа развития дефекта,
когда общий уровень вибрации значительно вырастает. Данный метод диагностики
прост, имеет нормативную базу, требует минимальных технических затрат и не
требует специального обучения персонала, применяется при диагностике
«массового» и сравнительно недорогого вращающегося оборудования.
2. Диагностика дефектов подшипников качения по спектрам вибрационных сигналов
Данный метод применяется на практике достаточно часто, хотя и не обладает
высокой чувствительностью, но он позволяет выявлять, наряду с диагностикой
подшипников, большое количество других дефектов вращающегося оборудования. Этот
метод позволяет начинать диагностику дефектов подшипников примерно с середины
второго этапа, когда энергия резонансных колебаний вырастет настолько, что
будет заметна в общей картине частотного распределения всей мощности
вибросигнала. Для реализации данного метода необходим хороший измерительный прибор
достаточно высокого уровня, и специально подготовленный персонал.
3. Диагностика дефектов по соотношению пик / фон вибросигнала
Основы метода иллюстрируются рисунком 3.1.1.1. Этот метод разрабатывался несколькими компаниями и имеет много различных, примерно одинаковых по эффективности, практических модификаций. Это метод HFD (High Frequency Detection – метод обнаружения высокочастотного сигнала), метод SPM (Shock Pulse Measurement – метод измерения ударных импульсов), метод SE (Spike Energy - метод измерения энергии импульса), а также еще несколько других, но менее известных методов. Лучшие разновидности данного метода позволяет выявлять дефекты подшипников качения на достаточно ранних стадиях, начиная примерно с конца первого этапа развития. Приборы, реализующие данный метод диагностики дефектов достаточно просты и дешевы.
4. Диагностика дефектов подшипников качения по спектру огибающей вибрационного сигнала
Данный метод позволяет выявлять дефекты подшипников на самых ранних стадиях,
начиная примерно с середины первого этапа. Теоретически данный метод диагностики
дефектов подшипников качения может базироваться и на анализе акустических сигналов,
и на анализе вибрационных сигналов. В первом случае метод называется SEE (Spectral Energy Emitted – анализ излучаемой спектральной энергии), и для своей работы использует специальный
датчик акустического излучения. Чаще всего для такой диагностики используют акустические
детекторы утечек различных модификаций, работающие в диапазоне частот до 100
кГц. В этом случае измерение акустических параметров производится дистанционно,
с некоторого удаления от контролируемого подшипника. Если для измерения
вибрационных сигналов используются «обычные контактные датчики вибрации», то
применение этого метода не требует использования специального оборудования. Развитием
данного метода много занимались российские диагносты, в настоящее время
считается уже классическим методом для анализа вибросигналов с подшипников качения.
Все вышеперечисленные методы диагностики дефектов подшипников качения различаются не только теоретическими предпосылками, положенными в их основу. Они различаются типом используемого диагностического оборудования, его стоимостью, необходимой подготовкой персонала и конечно своей эффективностью. Практически всегда справедливо простое правило – чем на более ранней стадии, и чем более достоверно необходимо обнаруживать дефекты подшипников, тем дороже это стоит.
Кроме
того всегда следует помнить и учитывать, что диагностика состояния подшипников
является только частью общего диагноза по оборудованию. Полный анализ состояния
оборудования обычно проводится по спектрам вибросигналов, поэтому при выборе
метода диагностики подшипников качения предпочтение следует отдавать
диагностике по спектрам огибающей, что делает этот метод практически универсальным.
При таком подходе полный набор технических средств, предназначенный для
диагностики состояния оборудования, будет минимальным по объему и стоимости.
В случае, если стандартная спектральная диагностика данного типа оборудования постоянно не проводится, то для ранней диагностики состояния подшипников качения весьма эффективно применение методов, основанных на сравнении уровней фона и пика вибросигнала. Эти методы обладают достаточной для стандартной практики работы специалистов по вибрационной диагностике достоверностью. Очень большим достоинством этих методов является то, что для своей реализации они не требуют дорогих и специализированных виброметров.
Для
того, чтобы при наличии явного дефекта в подшипнике необходимо выполнение
целого ряда различных требований. Эти требования обусловлены конструктивными,
эксплуатационными, и методическими особенностями проведения диагностики
подшипников качения различными методами.
Основное требование к конструкции подшипникового узла следующее – должен существовать хороший акустический контакт между зоной установки подшипника качения, и возможным местом установки измерительного датчика. Здесь использован термин «акустический контакт» по той причине, что большая часть интересующих нас вибрационных частот находится в зоне акустической слышимости. Конечно, более правильно было бы говорить о передаче вибрационных сигналов от контролируемого подшипника к датчику, но в данном случае это равноценно.
Измерение параметров технического состояния контролируемого подшипника должны проводиться в определенных условиях:
- Контролируемый подшипник должен быть
нагружен достаточным усилием, чтобы «дефект мог проявиться» в измеряемых
вибрационных сигналах. При невыполнении этого условия диагностика в режиме «on-line» становится
бессмысленной.
- Дефектная зона подшипника качения должна периодически проходить через зону нагрузки подшипника.
- Желательно, чтобы в контролируемом оборудовании не было других источников вибрационных сигналов с частотой, равной частоте дефектов, или их влияние было ослаблено в зоне контроля.
Используемое для диагностики измерительное оборудование должно обладать определенными свойствами:
- Частотные параметры измерительного датчика должны охватывать весь возможный диапазон частот, которые могут возникнуть в контролируемом подшипнике, и который представляет «диагностический интерес».
- Регистратор и анализатор вибрационных сигналов,
используемый для анализа «прямых спектров» подшипников качения, должен
обеспечивать, после обработки, получение спектра вибросигнала с разрешением не
меньше 1600 – 3200 линий.
Эти требования относятся ко всем методам диагностики подшипников качения по спектрам и спектрам огибающей, которые базируются на использовании вышеприведенных формул расчета подшипниковых частот.
В завершение данного общего раздела, касающегося общих вопросов диагностики, хочется коснуться важного методического вопроса, связанного с диагностикой «тихоходных подшипников». Такие подшипники в больших количествах используются в бумагоделательных машинах, в различных конвейерных линиях и подъемных механизмах.
Смысл
рассматриваемого вопроса достаточно прост, он заключается в том, чтобы определить,
какими частотными параметрами должны обладать измерительные приборы, предназначенные
для диагностики таких подшипников качения, и каковы особенности такой диагностики.
Например, если нужно диагностировать подшипник, частота вращения которого равна
0,2 Гц, т. е. если контролируемый подшипник делает один оборот за пять секунд,
то какими должны быть частотные свойства используемого диагностического
прибора, измерительного датчика? В каком частотном диапазоне должны
производиться измерения, чтобы полученной информации хватило для проведения
корректной диагностики подшипника.
Для ответа на этот вопрос обратимся к рисунку 3.1.1.3., на котором показан временной сигнал, зарегистрированный на дефектном подшипнике, имеющем раковину на внутренней обойме.
Приведенная
на рисунке вибрационная картина понятна и наглядна. Один раз в пять секунд
дефектная зона внутренней обоймы попадает в нагруженную зону подшипника, и при
прохождении через дефектную зону тел качения возникают динамические удары.
После каждого удара в дефектной зоне возникают свободные затухающие колебания с
частотой около 2 кГц. В приведенном примере мы имеем «серии» из трех ударов, т.
е. за время прохождения дефектной зоны в нее «попадают» три тела качения
подшипника. Это «рафинированная» вибрационная картина реального дефекта,
достаточно часто встречающегося в практике.
Вопрос стоит следующим образом, какими частотными свойствами должен обладать измерительный датчик, и в каком диапазоне частот мы должны провести измерения, чтобы, например, диагностировать дефект в данном подшипнике при помощи прямых спектров.
Для
начала определимся с тем, какая зона нашего вибрационного сигнала представляет
для нас интерес, от этого зависит многое. Очевидно, что если речь идет о
повторяющихся импульсах, то мы должны включить в рассмотрение не менее 2-3
оборотов контролируемого ротора, а в идеале 4-5, чтобы было можно уверенно
диагностировать дефекты сепаратора подшипника качения. Это связано с тем, что
частота гармоники дефектного сепаратора обычно чуть меньше 0,5 Гц, т. е. такой
дефект «обкатывается» один раз за два оборота ротора. Если мы включим в
рассмотрение 4 оборота ротора, то получим, что мы должны зарегистрировать
вибрационный сигнал, длительность которого равняется 20 секунд.
Выше мы уже говорили, что частота свободных колебаний после динамических ударов, в нашем примере, равняется 2 кГц. Чтобы корректно зарегистрировать и диагностировать эту гармонику на спектре мы должны вести регистрацию с частотой не менее 5 кГц, а лучше больше, например, хотя бы 6 кГц. Это логично вытекает из правила Найквиста.
Теперь
становится понятным, что одна регистрация вибрационного сигнала на тихоходном
подшипнике должна производиться с частотой 6 кГц, и длительностью 20 секунд.
Итоговая длина одной выборки должна составлять не менее 120 тысяч отсчетов АЦП.
Такими возможностями обладают далеко не все приборы регистрации вибрационных сигналов,
в том числе самые лучшие, это специфическое требование. Для 95% процентов
приборов, имеющихся на современном рынке, максимальная длина выборки сигнала не
превышает 8192 отсчета.
Второй важный вопрос, а каков частотный диапазон измерительного датчика, предназначенного для диагностики тихоходных подшипников качения? Что самое парадоксальное, многие утверждают, что чем ниже этот диапазон, тем лучше. А какой же диапазон необходим для диагностики подшипника, сигнал с которого приведен на нашем рисунке? При опросе 90% специалистов сказали, что необходим датчик с нижней граничной частотой от 0,05 Гц, и даже ниже.
Когда
мы акцентировали внимание на том, что основная диагностическая частота составляет
2 кГц, это есть частота свободных колебаний конструкций «вокруг подшипника»
после динамических ударов в зоне дефекта, даже после этого не все изменили свои
требования к частотным свойствам измерительного датчика. Еще раз подчеркнем,
что все эти рассуждения справедливы только для диагностики подшипников качения,
для диагностики подшипников скольжения требования другие, более стандартные.
Заключим данные рассуждение следующим. Диагностику тихоходных подшипников качения следует проводить при помощи «импульсных» методов. Диагностика с использованием «прямых» спектров практически невозможна, а с использованием спектров огибающей вибрационного сигнала весьма сомнительна.
3.1.1.3. Диагностика дефектов по общему уровню вибрации
Данный
способ оценки технического состояния и диагностики дефектов в подшипниках
вообще, и в подшипниках качения в частности, входит в широко распространенную
простейшую практику оценки общего технического состояния вращающегося оборудования
по общему уровню вибрационного сигнала. Такая диагностика производится техническим
персоналом без специальной вибрационной подготовки. Для проведения такой
диагностики дефектов подшипников качения вполне достаточно использования простейшего
виброметра, измеряющего общий уровень вибрации.
Как уже говорилось выше, такая диагностика дефектов подшипников качения позволяет определять дефекты только на самой последней стадии их развития, когда они уже приводят или уже привели к деградации состояния подшипников, повышению общего уровня вибрации. Диагностику дефектов подшипников по величине СКЗ виброскорости, а только для такой размерности вибрационного сигнала существуют критерии технического состояния оборудования, можно интерпретировать уже как предаварийную.
Критерии
технического состояния, и степени развития дефектов в данном методе полностью
ориентированы на соответствующие нормативные значения уровней вибрации,
принятые для данного механизма. Дефектным в этом методе диагностики считается
такой подшипник качения, вибрации которого превысили общую норму для агрегата,
это является признаком дефектного состояния контролируемого подшипника качения.
При таком пороговом повышении значения уровня вибрации, замеренной на опорном
подшипнике, обслуживающему персоналу необходимо принимать решение о возможности
дальнейшей работы агрегата или об остановке оборудования и замене подшипника.
Первые признаки дефекта подшипника данным методом диагностики обнаруживаются при обследовании оборудования персоналом достаточно поздно, примерно за несколько месяцев, недель или даже дней, что зависит от целого ряда особенностей работы данного подшипника, до момента полного выхода подшипника из строя. Несмотря на такое позднее обнаружение дефектов, и несколько скептическое отношение к этому методу специалистов со стажем, такой метод диагностики состояния подшипников качения достаточно широко используется в практике и дает неплохие результаты в тех случаях.
Максимальными преимуществами метод обладает в случаях, когда:
- Основной задачей проведения
диагностического обследования оборудования является только предотвращение аварий и их последствий,
пусть даже диагностическая информация о наличии дефекта будет получена на
достаточно позднем этапе.
- Останов оборудования для замены подшипника могут быть выполнены в любое время, без какого – либо ущерба для работы контролируемой установки и технологического цикла всего предприятия, без нарушения общего процесса.
- Если цикличность проведения ремонтных работ на контролируемом оборудовании такова, что оставшийся срок службы подшипника с диагностированным дефектом, пусть даже минимальный, всегда превышает оставшееся время работы до его вывода в ремонт по другим причинам.
Достоинством
такого, самого простейшего метода диагностики дефектов подшипников качения по
общему уровню вибрации, является так же и то, что для его применения не
требуется практически никакого дополнительного обучения обслуживающего, а часто
и эксплуатационного персонала. Кроме того стоимость технического оборудования,
необходимого для данного метода диагностики, минимальна.
Если на предприятии ранее не велись какие-либо работы по вибрационной диагностике, то данный метод диагностики обеспечивает наибольшую эффективность при своем внедрении. Применение всех других методов диагностики подшипников качения всегда требует больших начальных материальных затрат, и дает экономический эффект только на более поздних стадиях работы.
В заключении по данному вопросу следует сказать, что неожиданно высокую эффективность может иметь диагностика дефектов подшипников качения наиболее простым способом – «на слух». Для этого необходимо наличие какого-либо устройства для прослушивания подшипников, например типа стетоскопа, или виброметра с подключаемыми наушниками. Если ничего даже этого нет, то можно воспользоваться любой сухой деревянной палочкой достаточных размеров.
Если
приложить ее одним концом к контролируемому подшипнику, а вторым концом к уху, то
при наличии дефекта в подшипнике можно очень явственно услышать высокий, негромкий,
приятный звон, называемый иногда «бронзовыми колокольчиками». Стоит только один
раз его услышать, и спутать его уже будет нельзя ни с чем. Достоверность
диагностики дефектных подшипников таким методом очень велика.
3.1.1.4. Диагностика дефектов подшипников по спектрам сигналов
Большинство специалистов по вибрационной диагностике, если они начинают заниматься подшипниками качения, ожидают наибольшей достоверности и наибольшего эффекта при внедрении диагностики по классическим спектрам вибрационных сигналов. Такие спектры, в отличие от спектров огибающей вибрационного сигнала, также используемых для диагностики подшипников качения, достаточно часто называют «прямыми», и этот термин мы тоже будем применять.
К
сожалению, чаще всего именно здесь их оптимистическим ожиданиям не суждено будет
сбыться. Мало того, что сама процедура диагностики является достаточно сложной
и противоречивой, достоверность большинства практических диагнозов по состоянию
подшипников качения, полученных при использовании таких «прямых» спектров вибрационных
сигналов, является неожиданно низкой. Метод, предназначенный для решения самых
сложных диагностических задач вращающегося оборудования, не дает хороших
результатов при диагностике «копеечных» подшипников качения!
«Неожиданность»
такого парадокса запрограммирована заранее и заложена в особенностях диагностики
по спектрам вибрационных сигналов. Ошибки диагнозов заранее прогнозируемы и
заключаются в том, что классический спектр есть, по своему определению,
распределение мощности исходного временного вибросигнала в частотной области.
По этой, причине появление на спектре характерных гармоник того или иного элемента
подшипника качения, следует ожидать только в том случае, когда дефект
разовьется до такой степени, когда мощность его гармоник будет соизмерима с
мощностью «механических» гармоник, связанных с небалансом, расцентровкой.
Только в этом случае на спектре можно уверенно диагностировать «подшипниковые»
гармоники, когда они будут иметь не только большую амплитуду, но и существенную
мощность.
Для того, чтобы повысить чувствительность данного диагностического метода к «подшипниковым гармоникам» с малой мощностью, применяются различные способы, например, амплитуды гармоник в анализируемых спектрах представляются в логарифмическом масштабе. Это конечно помогает, но до определенного значения, когда гармоники уже начинают маскироваться общим «белым шумом», который в вибрационных сигналах имеет значительную амплитуду.
В
соответствии с приведенной в начале главы градацией развития дефектов подшипников
качения на этапы можно сказать, что диагностика по спектрам вибрационных сигналов
может уверенно выявлять дефекты подшипников качения, начиная только с конца
первого этапа их развития, а чаще с середины второй зоны. Причем даже на этом
уровне диагностика по «прямым» спектрам вибрационных сигналов является делом
достаточно непростым, и имеет ряд специфических особенностей.
Ниже мы попытаемся рассмотреть эти особенности, значительно усложняющие диагностику дефектов подшипников качения по прямым спектрам.
Начнем с требований, которые предъявляются к приборам регистрации и анализа вибрационных сигналов. Используемый для диагностики подшипников качения измерительный прибор должен обязательно иметь высокое частотное разрешение, не менее, чем 3200 линий в спектре. В противном случае произойдет «размазывание» мощности узкого ударного пика дефекта по достаточно широкой спектральной полосе, что приведет к резкому занижению амплитуды характерной подшипниковой гармоники, что однозначно исказит результаты проводимой диагностики. Как мы уже писали раньше, таких приборов находится в эксплуатации не так много, обычно частотное разрешение приборов значительно меньше.
Вполне
понятно, что раз диагностика подшипников качения, чаще всего, ведется на
анализе динамических процессов, то измерения необходимо вести в размерности
виброускорения, в котором эти процессы более значимы. Хотя в некоторых методах
диагностики необходимо анализировать энергетическую составляющую колебаний, для
чего следует пользоваться измерениями в размерности виброскорости.
Далее обратимся к основным особенностям проявления дефектов подшипников в исходных вибрационных сигналах, и в получаемых на их основе «прямых» спектрах мощности. Таких характерных особенностей существует несколько.
- Во-первых, это наличие на зарегистрированном сигнале вибрации явно выраженных периодических ударных процессов. Каждый удар, возникающий при обкатывании зоны дефекта телами качения подшипника, характеризуется целым набором параметров – максимальной амплитудой удара, частотой возникающих свободных колебаний, и скоростью затухания этих колебаний.
- Во-вторых, это наличие в спектре вибрационного сигнала большого количества «нецелых»
компонент, или, беря за базу оборотную частоту поддерживаемого ротора, гармоник
с дробными номерами.
Частоты этих нецелых гармоник определяются подшипниковыми соотношениями. Кроме того, при определенных типах дефектов подшипников эти гармоники сами создают свои семейства и гармоники на частотах взаимного биения, которые еще больше усложняют процедуру диагностики.
- В-третьих, это наличие в спектре вибрационного сигнала широкополосных «поднятий», своеобразных энергетических горбов вблизи подшипниковых частот, и частот собственных резонансов элементов механической конструкции. Идентифицировать причину возникновения этих горбов на спектре, а также связать их параметры с первичными дефектами подшипников качения очень сложно.
Рассмотрим
сначала форму ударных импульсов, возникающих при ударных воздействиях от
дефектов подшипников, возникающих в вибрационном сигнале. Для этого рассмотрим
простейший пример вибрационного сигнала, приведенный на рисунке 3. 1.1.4., зарегистрированного
на дефектном подшипнике качения. После каждого удара в дефектной зоне подшипника
возникают свободные резонансные колебания, которые обычно затухают по
экспоненциальному закону.
Вероятность появления таких ударных периодических импульсов, имеющих весьма характерный вид, сопровождающих процесс обкатывания дефекта подшипника, близка к 100 %. Для описания формы этих процессов особенностей даже придуман специальный термин – «золотая рыбка». Наличие импульсов такой формы в вибрационном сигнале является надежным диагностическим признаком для выявления дефектов подшипников.
Частота
следования этих «золотых рыбок», точнее говоря их плавников и хвостиков, во
временном сигнале должна достаточно точно соответствовать частоте,
характеризующей дефект того или иного элемента подшипника. Интенсивность «золотых
рыбок», степень их выраженности, превышения над общим фоном вибрации, зависит
от степени развития дефекта. Пример такого вибросигнала с двумя «золотыми
рыбками» приведен на нашем рисунке. Сразу же обратим внимание читателя на то,
что «на один оборот ротора» может приходиться различное количество ударных
импульсов, частота их следования определяется не оборотной частотой ротора, а
расчетными «подшипниковыми» частотами.
В реальных вибрационных сигналах «золотая рыбка» не бывает такой красивой, чаще всего форма ее является более «лохматой». У нее имеются различные «дополнительные плавники», располагаемые сверху, или снизу. Ударные импульсы могут следовать один за другим, часто даже наслаиваясь друг на друга. Все это зависит от реальной частоты следования ударов от дефектов, и от собственных резонансных свойств механической конструкции или ее отдельных элементов.
Вторая, основная диагностическая особенность
заключается в наличии специфического проявлении дефектов подшипников качения в
«прямых» спектрах вибрационных сигналов. Непосредственно при проведении диагностики
можно выявить три типа возможных, наиболее часто встречающихся типа спектров
вибросигналов, соответствующих различным этапам развития дефектов.
Диагностическая стадия 1
Первые признаки дефектов на спектре вибросигналов появляются тогда, когда дефект подшипника, возникнув, разовьется до такого уровня, что выделяемая им энергия (в золотых рыбках) станет сравнительно заметной в общей энергии вибрации подшипника, т. е. будет представлена на спектре. Применительно к вышеописанному разделению на этапы развития дефектов, приведенному на рисунке 3.1.1.1., это примерно конец первого этапа – начало второго. По срокам это бывает примерно несколько месяцев с момента начала развития дефекта. Пример спектра первой стадии приведен на рис. 3.1.1.5.
В
этом спектре, наряду с первыми, механическими, гармониками оборотной частоты
вращения ротора, появляется пик на характерной частоте дефекта того или иного
элемента подшипника. На этой стадии развития дефекта характерная «подшипниковая»
гармоника уже хорошо видна на спектре, что позволяет достаточно точно выявлять
дефектный элемент, особенно если представлять амплитуду гармоник в логарифмическом
масштабе.
По своей амплитуде пик характерной гармоники уже соизмерим с амплитудой первой или второй гармоник оборотной частоты ротора, но по своей мощности еще много уступает им. На спектре это выражается тем, что пик подшипниковой гармоники является очень узким. Дефект появился, но еще не является сильно развитым, динамические удары при обкатывании дефекта есть, но амплитуда и энергия их еще не очень значительна.
Эта
стадия, соответствующая специфическому проявлению дефектов подшипников в
спектрах вибрационных сигналов, и завершается тогда, когда амплитуда
характерной гармоники достигает своего максимума, примерно равного амплитуде
оборотной гармоники, и уже больше не растет. Она если и будет превышать
оборотную гармонику, то не на много, не более 30%. Причина этого проста –
энергия подшипниковых гармоник автоматически «вносится» преобразованием Фурье – FFT в состав оборотной гармоники. Как
следствие срабатывает логическое правило, говорящее о том, что одно слагаемое
не может быть больше итоговой суммы.
Диагностическая стадия 2
Следующая стадия развития дефекта подшипника качения начинается тогда, когда на спектре рядом с подшипниковой гармоникой, очень близко, появляется первая пара боковых гармоник, располагающихся слева и справа.
Появление
боковых гармоник обозначает, что начался этап пространственного расширения зоны
дефекта в подшипнике вдоль поверхностей качения, что иллюстрируется рисунком
3.1.1.6. В этой зоне дефект имеет уже такие размеры (глубину), что при
«проваливании» тела качения в зону дефекта он смещается настолько, что основную
нагрузку по поддержке вала механизма уже берут на себя рядом расположенные тела
качения. «Ступенька», с которой «прыгает» тело качения в зоне дефекта,
практически не может быть очень большой, ее величина зависит от общей степени
износа подшипника качения. В результате увеличение амплитуды динамических
импульсов больше не происходит. Вся энергия этих импульсов теперь уходит не на
углубление, а уже на расширение зоны дефекта, возникающее за счет постепенного
«раскрашивания» границ зоны дефекта.
На
этой стадии диагностики дефектов подшипников по спектрам вибрационных сигналов значительно
увеличивается «вклад дефекта» в общую вибрацию контролируемого механизма.
Подшипниковая гармоника увеличивает свою мощность до такого значения, что
становится соизмерима с основными механическими гармониками – первой и второй.
Результатом наличия в вибросигнале двух, как минимум, гармоник – синхронной и
несинхронной примерно одинаковой мощности возбуждает в агрегате частоты биений.
Эти частоты биений проявляются в спектре в виде боковых полос вблизи
характерной подшипниковой гармоники. По мере роста мощности подшипниковой
гармоники с расширением зоны дефекта число боковых полос и их мощность
постепенно возрастает.
Дальнейшее развитие дефекта приводит уже к появлению новых семейств гармоник,, уже от самой характерной подшипниковой частоты. Обычно появляются гармоники с номером два и три от основной частоты подшипникового дефекта. Рядом с каждой такой гармоникой слева и справа тоже будут иметь место боковые частоты, число пар которых может быть достаточно большим. Чем более развит дефект, тем больше боковых гармоник и у гармоник частоты дефекта.
Гармоники
от подшипниковых частот с большим номером, чем три, регистрируются достаточно
редко. Это происходит по той причине, что хотя более высокочастотные гармоники
и возникают, но мы не можем их зарегистрировать на внешней поверхности подшипниковых
опор. Чем выше частота возникающих колебаний, тем более интенсивно это колебание
будет затухать внутри подшипниковой опоры, на участке от места возникновения до
места установки первичного измерительного датчика.
Пример спектра вибросигнала подшипника качения с таким уровнем развития дефекта показан на рисунке 3.1.1.7. На этом спектре есть две гармоники от характерной частоты подшипникового дефекта, первая и вторая. Вокруг каждой гармоники расположено по две пары боковых гармоник, расположенных слева и справа.
Износ подшипника, обладающего таким набором характерных гармоник в спектре, уже очевиден. Пространственно он может простираться почти по всей рабочей поверхности подшипника, он уже стал групповым, захватив несколько элементов подшипника. Подшипник нуждается в замене или к такой процедуре нужно интенсивно готовиться.
Хочется
завершить описание этого этапа развития дефекта в подшипнике качения небольшим,
но методически важным сравнением, связанным с использованием общего подхода к
диагностике дефектов вращающегося оборудования. При внимательном рассмотрении
видно, что такой состав гармоник подшипниковой частоты, который показан на
рисунке 3.1.1.7., если не брать во внимание боковые гармоники, очень похож на
состав гармоник оборотной частоты ротора, имеющий место при наличии
механического ослабления в роторе, так же называемого люфтом, описанном в
соответствующем разделе.
Такое совпадение типов дефектов реально есть и на самом деле. Появление на спектре гармоник подшипниковой частоты говорит именно о развитии механического ослабления, так как при такой степени развития дефекта фиксация ротора в дефектном подшипнике становится уже недостаточно точной. Следствием такого совпадения проявления дефектов является примерное равенство наборов основных гармоник, возникающих в обоих случаях – при общем ослаблении ротора, и при ослаблении в опорном подшипнике.
Диагностическая стадия 3
Это
последняя стадия развития дефектов подшипника. В конце этой стадии подшипник
уже полностью деградировал и перестал исполнять свои прямые функции -
обеспечивать вращение валов при минимальных затратах на трение. Потери на
трение в подшипнике велики, и вращение ротора затруднено.
Развитие
дефекта подшипника на этой стадии, при диагностике его по спектрам вибрационных
сигналов, проходит следующим образом. Износ подшипника достигает такой стадии,
когда характерная частота дефекта, из-за очень большого расширения зоны дефекта,
становится нестабильной, такая же участь постигает боковые гармоники. Наложение
многих семейств гармоник, каждое из которых состоит из основной частоты и
боковых гармоник, создает достаточно сложную картину. Если в этих семействах
основные гармоники различаются по частоте немного, то сумма всех этих частот
представляет собой общее поднятие спектра, «энергетический горб», захватывающий
такой диапазон частот, куда входят все гармоники всех семейств от всех уже
существующих дефектов подшипника качения.
На общем фоне «энергетического горба» могут выделяться отдельные гармоники, но обычно все они носят случайный характер, как по частоте, так и по амплитуде, и уже практически ничего конкретного не отражают. Они просто увеличивают мощность, сосредоточенную в этом частотном диапазоне спектра.
Практически
вся мощность вибрационного сигнала сосредоточена не в зоне наиболее значимых механических
гармоник, с первой по десятую, а в зоне характерных гармоник, соответствующих
имеющим место дефектам диагностируемого подшипника качения. Правда на этом
этапе таких дефектов уже много, и это понятно, подшипника уже практически нет,
есть «сплошной дефект» всех элементов подшипника. Для иллюстрации этой стадии
на рисунке 3.1.1.8. приведен спектр вибросигнала. На рисунке достаточно хорошо
видны все вышеперечисленные особенности диагностирования третьей стадии развития
дефекта.
Кроме того в диапазоне гармоник, свойственных механическому ослаблению и увеличенному зазору в подшипнике поднимается лес целых гармоник оборотной частоты. Все они по своим параметрам соответствуют вышеназванным механическим причинам. Причины возникновения таких гармоник вполне понятна, в контролируемом подшипнике велики все зазоры, о чем мы уже писали немного раньше. Только на этом этапе мы имеем механическое ослабление не на уровне дефектов тел качения, а на уровне увеличения зазоров в опорных подшипниках. В результате и возникают множественные гармоники оборотной частоты ротора.
Диагностическое заключение о техническом состоянии такого подшипника качения очень простое – он нуждается в скорейшей замене, т. к. возможность возникновения аварийной ситуации с контролируемым оборудованием очень велика.
Здесь
мы подошли к самому главному в диагностике любого оборудования любым методом.
Каковы финальные и промежуточные критерии для оценки технического состояния
подшипника качения? Как оценить уровень развития выявленного дефекта – на
основании сравнении амплитуд конкретных гармоник, или анализируя иные параметры
гармоник характерных подшипниковых частот. К сожалению, в очередной раз
вынуждены разочаровывать нашего читателя, таких однозначных для практики
значений нет, или, если говорить еще более точно, нам они неизвестны.
В
практике диагностам чаще всего приходится оперировать терминами типа «больше –
меньше», или «более развитый дефект – менее развитый». Все зависит от очень
многих параметров – от типа подшипника, особенностей его монтажа, величины
технологической нагрузки на подшипник, и от много другого. Говоря иными
словами, уровень дефекта подшипника в каждом механизме свой, уникальный. На величину
порога каждого дефекта даже сказывается выбранное место для установки датчика,
удаление от места возникновения дефекта. Например, в самом простейшем случае, дефект
внутренней обоймы подшипника качения менее заметен в вибрационном сигнале, чем
дефект его внешней обоймы.
Определение истинного уровня недопустимого развития дефекта подшипников качения, точнее говоря определение истинной степени развития каждого дефекта каждого подшипника, чаще всего представляет наибольшую сложность, и значительно увеличивает трудоемкость использования метода диагностики по прямым спектрам. Нет ничего полезнее и важнее, чем практический опыт, накопленный по результатам диагностических измерений и сравнения их с результатами, полученными в процессе ремонтных работ.
В заключение по данному вопросу хотелось бы немного повторить уже сказанное, дополнив его некоторыми специфическими признаками:
- Все подшипниковые частоты обычно модулируются частотой вращения ротора, что
приводит к возникновению вокруг них характерных боковых гармоник.
По мере углубления дефекта число боковых гармоник растет. Дополнительная мощность вибрации от дефекта оказывается сосредоточенной не в основной гармонике дефекта, а вокруг нее, причем в достаточно широком диапазоне частот.
- Достаточно часто бывает, что реальные частоты характерных гармоник от отдельных элементов подшипника не соответствуют рассчитанным значениям, причем по мере «углубления и расширения зоны дефектов» это отличие может увеличиваться.
- Чаще всего при значительных степенях развития дефектов на спектре возникают «энергетические
горбы» – участки с общим поднятием уровня, имеющие большое количество случайных
пиков. Такие «горбы» могут возникнуть как вблизи характерной частоты, так и
вблизи частоты резонанса конструкции или ее отдельного элемента. Часто «энергетический
горб» бывает в двух местах спектра, и на характерной частоте и на резонансной.
Достаточно часто, при развитом дефекте, сама гармоника характерной частоты, вокруг которой появился и вырос «энергетический горб», на спектре отсутствует. Иногда число «горбов» может быть три или даже больше.
3.1.1.5. Диагностика с использованием пик – фактора
В данном разделе кратко рассмотрим те методы диагностики подшипников качения, в которых идет анализ наличия дефектов подшипников по соотношению на временных вибросигналах пиков и общего уровня «фона» вибрации. Одна из таких временных зависимостей, по которым может выполниться такая диагностика, приведена в начале данного раздела на рисунке 3.1.1.1.
В
силу устоявшейся практической привычки мы называем эти, во многом достаточно
разные методы диагностики подшипников качения, общим наименованием – «диагностикой
по пик – фактору», хотя разработчики многих компаний придумали разновидностям этого
метода иные названия. Применяемый нами диагностический признак «пик – фактор»
не является единственным и полностью общепринятым в практике, но в силу того,
что оно хорошо отражает физический смысл этого метода, мы используем его
преимущественно.
Как уже говорилось выше, этот метод диагностики подшипников качения имеет несколько достаточно широко известных разновидностей. Эти разновидности разрабатывались разными компаниями, в них несколько по-разному производят сравнение уровней пика и фона вибросигнала. В одном методе для сравнения берется амплитуда пика, в другом энергия, фоновый уровень также может рассчитываться по-разному.
Мы уже называли основные разновидности этого метода:
- Диагностика с использованием СКЗ вибрационного сигнала и пиковых значений – классический метод диагностики по пик фактору.
- Диагностика с использованием соотношения
эксцесса вибрационного сигнала и общего уровня.
- Метод HFD (High Frequency Detection – метод обнаружения высокочастотного сигнала).
- Метод SPM (Shock Pulse Measurement – метод измерения ударных импульсов).
- Метод SE (Spike Energy - метод измерения энергии импульса).
Лучшие разновидности данного метода позволяет выявлять дефекты подшипников качения на достаточно ранних стадиях, начиная примерно с конца первого этапа развития. Приборы, реализующие данный метод диагностики дефектов достаточно просты и дешевы.
При
более общем взгляде на все эти методы видно, что они, в силу одинакового теоретического,
методического и даже приборного подхода к решению проблемы, имеют примерно и
одинаковую трудоемкость, и почти одинаковую достоверность поставленных диагнозов.
Для этих методов нужна примерно одинаковая техническая база – специализированные
переносные виброметры с встроенными двумя типами детекторов вибросигналов – детектором
среднего уровня вибросигнала и пиковым детектором.
Использование обобщенного количественного соотношения двух величин по типу – «средний уровень – пик» позволяет диагносту определять дефекты подшипника на достаточно ранних стадиях их развития, что является несомненным достоинством применения такого подхода к диагностике.
Каждая из известных нам компаний-разработчиков диагностических методов по своему, с использованием собственного опыта, решила проблему нормирования этапов развития диагностируемых дефектов, но практическое представление этих наработок примерно одинаково – это специальные таблицы или номограммы, достаточно удобные для практического использования. Какого – либо обобщающего исследования, сравнивающего эти методы между собой нет, да и очевидно быть не может. Все они примерно с равным успехом применяются в практике.
Вопросы
методики практического проведения замеров вибрации в этих методах не имеют
достаточно подробного описания. Это является результатом того, что эти
достаточно простые методы диагностики ориентированы на использование
персоналом, не обладающим специальной диагностической подготовкой. Поэтому сама
технология проведения замеров должна быть очень простой, не «затуманенной»
сложными теоретическими выкладками.
Мы не будем заниматься сравнением всех этих методов диагностики подшипников качения по «пик – фактору» между собой, не будем выискивать достоинства и недостатки как самих методов, так и компаний-разработчиков. Это уже специальный, можно даже сказать коммерческий вопрос, выходящий за пределы основных задач, решаемых данным методическим руководством.
Будет
лучше, когда каждый конкретный пользователь сам примет свое решение по данному
вопросу, какой из методов диагностики подшипников качения с использованием «пик
– фактора» ему нравится больше всего, и с успехом использует его на практике.
Тем более, такой диагностикой чаще всего занимаются не специалисты, которые,
как мы надеемся, читают эту книгу.
3.1.1.6. Диагностика дефектов подшипников по спектрам огибающей
Метод диагностики состояния вращающегося оборудования при помощи спектров огибающей вибрационного сигнала получил максимальное прикладное развитие благодаря его применению именно для ранней диагностики технического состояния подшипников качения. Основы метода диагностики дефектов подшипника качения по спектру огибающей и особенности его практического применения достаточно подробно описаны выше, и поэтому не будем здесь все это повторять.
Если
говорить кратко и очень просто, суть этого метода заключается в детектировании
высокочастотных хвостиков «золотых рыбок» (смотри рисунок 3.1.1.4), и получения
спектра от полученной огибающей высокочастотного сигнала. Полученная кривая,
огибающая исходный вибрационный сигнал, является более информативной для
диагностики дефектов подшипников качения, чем исходный сигнал, так как она
принудительно «избавлена» от ненужной высокочастотной информации. По этой
причине на спектре от данной кривой более явно представляются гармоники,
соответствующие характерным подшипниковым частотам, математические формулы,
предназначенные для расчета которых также приведены выше, в начале данного
раздела.
Процедура проведения регистрации огибающей вибрационного сигнала достаточно сложна. Она должна учитывать несколько специфических особенностей, позволяющих повысить чувствительность метода.
- Во-первых,
регистрация производится не во всем частотном диапазоне, в котором может
работать измерительный прибор, а только в узкой его полосе. Поскольку первые применения
данного метода чаще всего проходили с использованием аппаратуры компании «Брюль &
Къер», которая наряду с созданием приборов вибрационного контроля занималась
акустическими измерениями, для определения параметров полос частот
использовались октавные определения.
В настоящее время стандартом для расчета огибающей сигнала считается использование треть октавных фильтров, или близких к ним.
- Во-вторых, достаточно сложным является выбор необходимой полосы частот, перестройка которой осуществляется при помощи управляемых фильтров высокого порядка. С одной стороны, в этой полосе частот должны быть максимальны высокочастотные колебания, которые возникают после динамических ударов в зоне дефекта подшипника. С другой стороны, в выбранной полосе частот должны быть минимальны колебания, связанные с другими причинами, приводящими к увеличенным вибрациям в зоне опорных подшипников.
Как
вы уже догадались, практически для каждого контролируемого подшипника этот
вопрос приходится решать отдельно. Слишком от многих конструктивных и
эксплуатационных параметров это зависит.
Мы достаточно подробно описываем этот вопрос потому, что от правильного его решения во многом зависит точность и достоверность проводимой диагностики дефектов подшипников качения.
Далее мы приведем, причем уже в конечном виде, общей таблицей, практически полный перечень дефектов, которые можно диагностировать в подшипниках качения при помощи спектральных методов – по классическим спектрам и спектрам огибающей. Всего в этой таблице приведено 15 наиболее часто встречающихся причин повышенной вибрации – дефектов подшипников с различной локализацией.
Все
дефекты в таблице представлены в определенном хронологическом порядке, связанным
с этапами «жизненного цикла» подшипника качения в оборудовании. Сначала идут дефекты,
связанные с монтажом подшипников, с которыми приходится встречаться уже на
этапе ввода оборудования в эксплуатацию. Далее идут дефекты смазки, т. е.
эксплуатации подшипников. За ними следуют проблемы, связанные уже с износом рабочих
поверхностей подшипников. Замыкают таблицу явно выраженные и уже сильно
развитые дефекты элементов подшипников типа, «скол» и «раковина» на
поверхностях качения.
В графе «тип сигнала» указывается параметр,
при помощи которого наиболее эффективно проводить диагностику каждого дефекта.
Это может «прямой» спектр, спектр огибающей сигнала, или их комбинация. В графе
«основная частота» указывается или оборотная гармоника, или подшипниковые гармоники,
являющиеся основными при диагностике. В следующей графе указывается, на какие
гармоники от основной частоты следует обращать основное внимание. И в последней
графе «порог» указывается уровень модуляции вибрационного сигнала основной
диагностической гармоникой. Этот параметр рассчитывается по стандартным
формулам обработки сигналов, которые следует взять из теории анализа модулированных
радиосигналов.
N | Дефект подшипника | Тип сигнала | Основная частота | Гармоники | Порог |
1. Проблемы монтажа подшипников качения | |||||
1 | Перекос наружного кольца при посадке | Спектр + огибающая | 2 х Fн | k=1,2 | 16 % |
2 | Неоднородный радиальный натяг | Спектр + огибающая | k x F1 | k=1,2 | 13 % |
3 | Проскальзывание в посадочном месте | Огибающая | k x F1 | k=1,2,3 | 9 % |
4 | Ослабление крепления подшипника | Спектр | k x F1 | k=0.![]() |
13 % |
5 | Задевания подшипнике и уплотнениях | Спектр | k x F1 | k=0.5,1,1.5, 2,2.5,3 | 13 % |
6 | Обкатывание наружного кольца | Спектр + огибающая | F1 | 16 % | |
2. Проблемы смазки | |||||
7 | Проблемы смазки | Фон вибрации | – | – | 20 dB |
3. Проблемы износа подшипников качения | |||||
8 | Увеличенные зазоры в подшипнике | Спектр | k x F1 | k=1,2,3,4,5,6.![]() |
13 % |
9 | Износ поверхности наружного кольца | Огибающая | Fн | – | 16 % |
10 | Износ поверхности тел качения | Огибающая | Fc или F1-Fс | k=1,2,3 | 15 % |
11 | Износ поверхности внутреннего кольца | Огибающая | kxF1 | k=1,2,..6 | 13 % |
12 | Дефект группы поверхностей трения | Огибающая | Fн + Fв Fн+F1 | k=1,2,.![]() |
16 % |
4. Критические дефекты подшипников качения | |||||
13 | Раковины (сколы) на наружном кольце | Огибающая | k x Fн | k=1,2,3 | 16 % |
14 | Раковины (сколы) на внутреннем кольце | Огибающая | k x Fв | k=1,2,3 | 15 % |
15 | Раковины (сколы) на телах качения | Огибающая | k x Fтк | k=1,2,3 | 15 % |
Проблемы
изготовления и монтажа подшипников можно отнести к нулевому этапу развития дефектов
подшипников, когда эксплуатация подшипника еще даже не началась. Проблемы
смазки и начальные этапы износа соответствуют первому этапу, когда дефекты поверхностей
качения только зарождаются.
Сильный износ и зона углубления физических дефектов подшипников относятся ко второму этапу развития дефектов в подшипниках. Как уже говорилось выше, третий этап развития дефектов в подшипниках, начало их деградация, диагностируется уже любым методом.
Для иллюстрации возможностей диагностики дефектов подшипников качения, приведем несколько характерных спектров огибающей вибросигнала, свойственных нескольким наиболее характерным дефектам.
На
рисунке 3.1.1.9. приведен спектр огибающей вибрационного сигнала с подшипника
качения, имеющего значительную раковину на наружном кольце. На приведенном спектре
может иметься достаточно много гармоник, иногда даже более десяти. Все они, по своей
частоте, кратны частоте обкатывания наружного кольца подшипника качения, т. е.
являются ее гармониками. Других, значительных, характерных гармоник на данном
спектре просто нет, поэтому вибрационная диагностика данного дефекта подшипников
качения не вызывает значительных трудностей, диагностическая картина дефекта здесь
достаточно простая.
На следующем спектре огибающей вибрационного сигнала, приведенном на рисунке 3.1.1.10., следует диагностировать дефект типа раковина на внутреннем кольце. Здесь также имеются гармоники характерной частоты – частоты внутреннего кольца, но здесь есть существенное отличие. Характерные гармоники имеют боковые полосы, сдвинутые на частоту вращения ротора. Появление боковых полос объяснялось выше с физической точки зрения.
Можно
привести еще одно объяснение причин появления боковых гармоник, с другой точки
зрения. Дефект на внутреннем кольце не постоянно находится в нагруженной зоне
подшипника. В течении одного оборота ротора он то находится в нагруженной зоне,
то выходит из нее. Таким образом, дефект внутреннего кольца модулируется
частотой вращения ротора. При внимательном рассмотрении спектра на рис. 3.1.1.10.
возникает впечатление, что дефект модулируется синусоидой, по которой и
располагаются амплитуды основных и боковых гармоник. Данный дефект
диагностируется тоже достаточно просто.
Мы не будем приводить примеров спектров огибающих для других дефектов подшипников качения. Все они достаточно просты и могут быть легко дифференцированы после небольших рассуждений. Вся сложность проведения диагностики дефектов по спектру огибающей заключается в получении этих спектров, а дальше все уже достаточно просто.
Уровень
дефекта на диагностических спектрах огибающей определяется по величине
модуляции огибающей данного вибросигнала характерной гармоникой.
Диагностируемые дефекты принято характеризовать в данном методе диагностики
уровнями – слабый, средний и сильный. Нормированию подлежит порог сильного
дефекта, в долях от которого в дальнейшем рассчитываются пороги среднего и слабого
уровней. Порог среднего уровня дефекта чаще всего считают равным половине от
величины порога сильного дефекта. Порог слабого уровня дефекта обычно
определяют в 20 процентов от уровня порога сильного дефекта.
Самым ответственным считается корректное определение уровня порога сильного дефекта. При этом приходиться учитывать три аспекта работы подшипника и способа проведения замера вибрации:
- Чем больше размер подшипника, тем более высоким должен быть уровень порога сильного дефекта. Большой подшипник «звенит» сильнее.
- Чем выше рабочая частота вращения ротора
механизма, тем выше должен быть уровень порога сильного дефекта.
При быстром вращении от подшипника больше шума.
- Измерительный датчик должен располагаться как можно ближе к контролируемому подшипнику. При удалении датчика часть полезной информации затухает в конструкции и уровень порога сильного дефекта необходимо понижать.
Для каждого нового конкретного типа оборудования, точнее говоря, даже для каждого подшипника в каждом оборудовании, уровень порога сильного дефекта реально приходиться каждый раз подбирать сугубо индивидуально, не рассчитывать, а именно подбирать.
Величина
порога сильного дефекта во многом зависит от удаленности элемента с дефектом от
измерительного датчика. Пороги дефектов внутреннего кольца подшипника всегда
ниже порогов дефектов наружного кольца. Это объясняется увеличением затухания полезной
составляющей вибросигнала на более длинном пути передачи, включая дополнительные
зазоры в подшипнике.
Для справки напомним, что для примера усредненные, наиболее часто встречающиеся, значения уровней порогов сильных дефектов приведены выше в таблице, где перечислены диагностируемые в подшипниках качения дефекты. В зависимости от примененного способа диагностики дефектов подшипника в таблице имеется две разновидности единиц, в которых нормируется уровень сильного порога.
При
использовании для диагностики дефекта подшипника классических спектров
вибросигналов уровень порога сильного дефекта может быть задан в долях от
нормированного допустимого значения виброскорости на данном подшипнике или так
же в процентах модуляции. При сравнении с нормой необходимо использовать не
полное, абсолютное значение виброскорости на данном подшипнике, а только ту ее
часть, которая наведена диагностируемым дефектом. Это несколько сложнее, но в
конечном итоге более точно.
При определении качества смазки за базу для сравнения берется общий уровень «фоновой» вибрации исправного подшипника с хорошей смазкой. При повышении общего уровня «фона» вибрации в десять раз, т. е. на 20 dB, качество смазки считается неудовлетворительным.
Еще раз хочется напомнить, что в таблице приведены только общие, усредненные значения уровней порогов сильных дефектов. У конкретных подшипников возможен разброс этих значений на ± 40 % или даже несколько больше. Все зависит от типа подшипника и условий его работы.
Сам
факт диагностирования того или иного дефекта подшипника несет в себе полезную
информацию, но эта информация мало применима для практики. Обслуживающий персонал
больше интересует вопрос о возможности дальнейшей практической эксплуатации
оборудования с дефектным подшипником и тех ограничениях, которые накладывает
обнаруженный дефект на возможности использования оборудования. Очень важным для
практики является вопрос о сроках проведения очередного ремонта. Все эти вопросы
относятся уже к сфере, относящейся к системе обслуживания оборудования.
Вопрос прогнозирования остаточного ресурса подшипника качения во многом напоминает прогнозирование общего остаточного ресурса оборудования, но и имеет свои индивидуальные особенности. Не вдаваясь в подробности, рассмотрим основные проблемы, возникающие при расчете остаточных ресурсов подшипников.
Это:
- Каждый подшипник имеет свои уникальные физические особенности, приводящие к специфическим внутренним процессам. Поэтому каждый подшипник должен описываться своей математической моделью.
- Каждый подшипник должен описываться двумя
различными моделями – одна должна описывать общие процессы износа подшипника
без дефектов, а другая должна описывать процессы развития внутренних дефектов.
- Время полного развития дефектов, находящихся на разных элементах подшипника, например не внешнем кольце или на сепараторе, различно. Для дефектов каждого элемента подшипника должна существовать своя математическая модель.
Даже из этого простого перечисления особенностей математического описания физических процессов в подшипнике качения видно, насколько сложна задача прогнозирования остаточного ресурса подшипника по итогам проведения вибрационной диагностики.
Первоначально
состояние подшипника «контролируется» при помощи достаточно стабильной модели
нормального износа, когда в нем отсутствуют внутренние дефекты. Так
продолжается до момента выявления в подшипнике какого-либо дефекта. Здесь
приходится отказываться от нормальной модели и переходить к моделям развития
дефектов. Очень важной задачей, решаемой при переходе от нормальной модели к
контролю состояния по модели развития дефекта, является как можно более точное
определение времени зарождения дефекта. Чем точнее оно будет определено, тем
более достоверными будут дальнейшие прогнозы по величине остаточного ресурса
подшипника.
Максимальная скорость развития разных дефектов различна, поэтому контролировать следует развитие всех возможных дефектов, даже когда один из них только что зародился, а другой уже достаточно развит. Никогда нельзя заранее сказать, какой из дефектов раньше всех разовьется до недопустимого уровня и послужит причиной смены подшипника качения при ремонте.
Периодичность
проведения диагностических измерений вибрации зависит от максимальной скорости
развития дефекта подшипника в данном оборудовании. В практических случаях
замеры могут проводиться через интервал времени от нескольких часов до одного
года. При нормальной эксплуатации типового оборудования и проведении замеров
примерно через шесть месяцев удается выявить большую часть дефектов на
достаточно ранней стадии и предупредить аварии.
После выявления первых признаков зарождающегося дефекта интервал времени между двумя измерениями необходимо сократить. В зависимости от локализации дефекта интервал времени между замерами сильно меняется. Он минимален при дефектах тел качения, которые могут развиваться очень быстро.
Подшипник подлежит замене или ежедневному наблюдению при наличии в нем двух сильных дефектов.
Для
обеспечения необходимой точности расчета остаточного ресурса и даты проведения
ремонта в расчетах необходимо применение математических моделей с порядком не ниже
третьего – четвертого. Если вспомнить, что один подшипник описывается не менее,
чем десятком математических моделей, то становятся представимыми те
математические затраты, необходимые для корректного прогнозирования параметров
эксплуатации подшипника качения. А таких подшипников на предприятии в работе
может одновременно находиться в работе несколько тысяч.
Процедура контроля состояния многих подшипников на предприятии становится возможной только при использовании компьютеров, в которых создаются и работают базы данных по подшипникам и современные экспертные системы диагностики.
Приборы нашего производства для диагностики подшипников качения
- ДПК-Вибро – компактный виброметр, прибор оперативной диагностики подшипников качения
- Vibro Vision-2 – анализатор вибросигналов с расширенными функциями диагностики подшипников качения
Обзор типов и модификаций для применения в движении
Основными компонентами радиального шарикоподшипника являются наружное кольцо, внутреннее кольцо, сепаратор и шарики.Изображение предоставлено NTN Corporation
Подшипники вращения являются обычными компонентами систем движения. Они используются в редукторах, двигателях, шкивах, вентиляторах, насосах — практически каждый раз, когда вал вращается, подшипники качения уменьшают трение и поддерживают радиальные или осевые нагрузки.
Классификация подшипников вращения начинается с типа подшипника, воспринимающего нагрузку — шарикового или роликового. Следующей отличительной чертой шариковых и роликовых подшипников является основное направление нагрузки, которое может выдержать подшипник, — радиальное или осевое (также известное как упорное). Далее шарикоподшипники классифицируются по конфигурации наружного кольца, а роликоподшипники далее классифицируются по форме роликов.
Несмотря на то, что существуют десятки вариантов подшипников качения, включая конструкции, предназначенные для конкретных сред, монтажных конфигураций и областей применения, здесь рассматриваются наиболее распространенные категории.
Подшипники вращения
Подшипники вращения классифицируются по тому, используют ли они шарики или ролики, а затем по типу нагрузки, на которую они рассчитаны: радиальная или осевая (упорная). Дальнейшая классификация шарикоподшипников основана на конфигурации наружного кольца, тогда как роликовые подшипники дополнительно классифицируются по форме роликов.

Шариковые подшипники — Радиальные
Радиально-упорные шарикоподшипники обычно используются парами или в двухрядной конструкции (показано здесь), чтобы выдерживать осевые нагрузки в обоих направлениях.Изображение предоставлено: SKF
В семействе шарикоподшипников радиальные шарикоподшипники являются самым простым типом, с дорожками качения, которые почти соответствуют или соответствуют диаметру шариков. Этот тип подходит для радиальных нагрузок и для осевых нагрузок в любом направлении, хотя их грузоподъемность относительно мала по сравнению с другими типами подшипников. Для более высокой грузоподъемности при относительно небольшой занимаемой площади радиальные шарикоподшипники обычно доступны в двухрядной конструкции с двумя рядами шариков вместо одного.
Радиально-упорные шарикоподшипники сконструированы таким образом, что линия, соединяющая точки контакта внутреннего кольца, шарика и наружного кольца, проходит радиально под углом к подшипнику. Угол контакта увеличивает грузоподъемность, но это означает, что подшипник может выдерживать осевую нагрузку только в одном направлении, поэтому эти подшипники обычно используются парами или в двухрядной конструкции (по сути, это два радиально-упорных подшипника, установленных вплотную друг к другу). чтобы выдерживать осевые нагрузки в обоих направлениях.
Шариковые подшипники с четырехточечным контактом — это одинарные радиально-упорные подшипники, рассчитанные на высокие осевые нагрузки в обоих направлениях. Они также могут выдерживать комбинированные осевые и радиальные нагрузки, если преобладает осевая составляющая.
Шариковые подшипники — упорные
Упорные шариковые подшипники состоят из двух относительно тонких колец подшипника (иногда называемых подшипниковыми пластинами или шайбами) с дорожками качения, рассчитанными на восприятие осевых нагрузок в одном или обоих направлениях. Радиальные нагрузки, как правило, недопустимы для упорных подшипников, а скоростные возможности ограничены (в некоторых случаях от 20 до 30 процентов от их аналогов радиальных подшипников).
Роликовые подшипники — радиальные
Роликовые подшипники, такие как показанный здесь цилиндрический роликоподшипник, имеют более высокую радиальную грузоподъемность, чем шарикоподшипники, благодаря использованию роликов для поддержки нагрузки.Изображение предоставлено: NSK Ltd.
Подшипники качения с роликами, поддерживающими нагрузку, имеют более высокую грузоподъемность и более высокую жесткость, чем шарикоподшипники аналогичных размеров. Тип нагрузки, которую они могут выдержать, зависит в первую очередь от формы ролика.
Цилиндрические роликоподшипники может выдерживать высокие радиальные нагрузки, в то время как двухрядные цилиндрические версии имеют чрезвычайно высокую радиальную грузоподъемность и высокую жесткость в радиальном направлении. Хотя стандартные цилиндрические роликовые подшипники не способны воспринимать осевые нагрузки, некоторые конструкции включают внутренние ребра или буртики, которые позволяют им воспринимать относительно небольшие осевые нагрузки в одном или обоих направлениях.
В игольчатых роликоподшипниках используются длинные тонкие ролики, длина которых в три-десять раз превышает диаметр. Они имеют хорошую радиальную грузоподъемность, но основное преимущество конструкции иглы заключается в том, что она имеет тонкое поперечное сечение для применений, где требуется высокая радиальная грузоподъемность, но пространство ограничено.
В отличие от цилиндрических и игольчатых роликоподшипников, конические роликоподшипники , в которых для поддержки нагрузки используются конические ролики, могут выдерживать осевые нагрузки в одном направлении. Конические роликоподшипники можно рассматривать как роликовую версию радиально-упорного шарикоподшипника, и, как и их аналоги шарикоподшипников, конические роликоподшипники часто используются парами или в двухрядной конструкции для противодействия осевым силам, возникающим в подшипник при приложении радиальной нагрузки. Коническая конструкция также улучшает характеристики качения и снижает трение внутри подшипника.
Сферические роликовые подшипники используют бочкообразные ролики и имеют две внутренние дорожки качения, наклоненные под углом к оси подшипника, и одну внешнюю дорожку качения сферической формы. Это дает им возможность самовыравнивания, очень высокую допустимую радиальную нагрузку и способность выдерживать осевые нагрузки в обоих направлениях.
Роликовые подшипники — упорные
Конические упорные роликовые подшипники имеют чистое движение качения, поэтому они выделяют меньше тепла и меньше изнашиваются.Упорные версии роликоподшипников, как правило, соответствуют прочностным характеристикам своих радиальных аналогов, но с возможностью осевой (осевой) нагрузки.
Цилиндрические упорные роликоподшипники могут воспринимать высокие осевые нагрузки и способны выдерживать ударные нагрузки, хотя радиальные нагрузки недопустимы.
Аналогично, упорные игольчатые роликоподшипники могут выдерживать высокие осевые нагрузки, но в гораздо меньшем форм-факторе из-за использования игольчатых подшипников.
Упорные конические роликоподшипники могут быть однонаправленными или двунаправленными, что указывает на то, могут ли они воспринимать осевые нагрузки в одном или обоих направлениях. Как и их радиальные аналоги, конические упорные роликоподшипники имеют «чистое» движение качения, что означает меньшее выделение тепла и меньший износ.
Сферические упорные роликоподшипники могут воспринимать очень высокие осевые нагрузки и малые или умеренные радиальные нагрузки, а также могут выдерживать некоторые перекосы.
Для получения дополнительной информации о подшипниках качения посетите наш дочерний сайт: Bearingtips.com.
Подшипники вращения Выбор и применение для ваших приложений движения
Подшипники играют ключевую роль почти во всех системах движения. В Motion Solutions мы понимаем это лучше, чем любая другая компания в этой области. В конце концов, мы начинали как консультант по подшипникам, и подшипники были одними из первых продуктов, которые мы продавали. Надлежащий выбор подшипников и их реализация по сей день входят в число наших основных компетенций. Для нашей клиентской базы это имеет решающее значение, потому что выбор подшипника может повлиять на производительность системы.
Одна из самых больших ошибок, которую допускают OEM-производители, заключается в том, что они с самого начала разрабатывают проект без учета подшипников. Изношенный подшипник может привести к смещению системы, что может увеличить износ привода. Это, в свою очередь, усложняет работу двигателя. Конечным результатом может стать ранний отказ двигателя, который приведет к часам или даже дням простоя и будет повторяться, если проблема с подшипниками не будет решена. Производители оборудования должны иметь план с самого начала.
Подшипник должен выдерживать нагрузку не только по величине, но и по направлению. Тип подшипника, который может выдерживать радиальную нагрузку, может не выдержать, например, осевой нагрузки или их комбинации. Рабочий цикл важен, как и скорость.
Много дискуссий идет о размерах двигателя, но правильный размер подшипников не менее важен. Недостаточный размер может привести к преждевременному отказу, но чрезмерный размер увеличивает как стоимость, так и занимаемую площадь, не обеспечивая измеримой выгоды. Наконец, в конструкции должно быть достаточно места для размещения подшипника. В конце концов, лучший в мире подшипник не поможет, если он не подходит.
Наша команда инженеров имеет большой опыт проектирования систем и выбора подшипников. Воспользуйтесь их опытом, чтобы выбрать лучший подшипник для вашего применения.
Шариковые подшипники
Шариковые подшипники используют шарики в качестве тел качения. Целью шарикоподшипника является уменьшение трения при вращении и поддержка радиальных и осевых нагрузок. В шарикоподшипниках используются уплотнения, удерживающие смазку и не допускающие попадания частиц, что продлевает срок службы. Прецизионные шарикоподшипники используются в высокопроизводительных приложениях на различных рынках, включая автоматизацию, аэрокосмическую промышленность, робототехнику, здравоохранение и станкостроение.
Радиальные шарикоподшипники
Радиальные шарикоподшипники — это рабочие лошадки, широко доступные в различных размерах, материалах и ценах. Они могут работать на очень высоких скоростях и обеспечивают хороший отвод тепла. Добавление сепараторов помогает разделять шарики, уменьшая трение и повышая эффективность. Радиальные шарикоподшипники имеют меньшую грузоподъемность, чем радиально-упорные подшипники, из-за угла контакта и меньшего количества шариков. Это важно иметь в виду — перегрузка может привести к повреждению поверхности, такому как бринеллирование, растрескивание или истирание, что приведет к преждевременному выходу из строя.
Радиально-упорные шарикоподшипники
Не каждая нагрузка является чисто осевой или чисто радиальной. Радиально-упорные подшипники предназначены для гибридных радиально-осевых нагрузок. Внешняя дорожка качения имеет приподнятый буртик для поддержки нагрузки поперек угла контакта. Угол контакта увеличивает грузоподъемность подшипника, позволяя ему выдерживать большую нагрузку в направлении тяги.
Одиночный радиально-упорный подшипник может воспринимать усилие только в одном направлении. В результате эти подшипники почти всегда используются парами, при этом отдельные подшипники ориентированы с противоположными углами контакта, так что между двумя подшипниками система может поддерживать осевое усилие в обоих направлениях. Точные детали конфигураций различаются: подшипники могут располагаться спиной к спине, лицом к лицу, в тандеме или по отдельности на противоположных концах вала. Ориентация «спина к спине» лучше всего подходит для поддержки моментных нагрузок. Ориентация «лицом к лицу» допускает смещение, что делает ее подходящей для таких задач, как поддержка конца шарико-винтовой передачи. Тандемные подшипники устанавливаются в одну сторону, что ограничивает их выдерживание осевой нагрузки только в одном направлении, но почти в два раза большей величины; потребуется дополнительный подшипник, чтобы воспринимать тягу в противоположном направлении.
Выбор материала сепаратора дает дополнительные степени свободы. В радиально-упорных подшипниках обычно используются пластмассовые или фенольные сепараторы. Фенольные сепараторы, как правило, несколько прочнее пластиковых и лучше удерживают смазку в течение более длительного срока службы.
Упорные шарикоподшипники
Во многих областях применения предъявляются высокие требования к размерам и весу. Подшипники тонкого сечения обеспечивают плавное движение в очень узком форм-факторе. Из-за своего размера они имеют меньшую грузоподъемность. Следует соблюдать осторожность при определении размера.
Подшипники тонкого сечения
Современное производство делает акцент на максимальном повышении эффективности рабочего оборудования (OEE) и увеличении времени безотказной работы. Мониторинг состояния является важным инструментом для достижения этой цели. Данные о состоянии дают представление о состоянии, работе и производительности оборудования, объектов и даже производимой продукции. Обычно это включает в себя такие факторы, как температура, давление, влажность, вибрация, ток или напряжение. Например, повышение температуры двигателя может указывать на разрушение смазки. Появление всплеска в частотном спектре вибрации насоса может указывать на эрозию лопастей. Повышенное потребление тока может указывать на изношенные подшипники или шестерни. Благодаря этим типам информации группы технического обслуживания могут более эффективно устранять неисправности, а также в первую очередь помогать предотвращать их.
Роликовые подшипники
Роликовые подшипники используют ролики вместо шариков для разделения движущихся частей. Ролики доступны в различных формах, включая линейные и выпуклые. Они обеспечивают лучшее распределение нагрузки, что позволяет им выдерживать более высокие нагрузки. Они очень хороши для применений, требующих высокой жесткости. Компромисс заключается в том, что большая площадь контакта также снижает эффективность.
Конические роликоподшипники
Конические роликоподшипники имеют форму усеченного конуса. Такая форма позволяет им более эффективно справляться со смешанной нагрузкой. С другой стороны, увеличенная площадь контакта роликов снижает эффективность.
Игольчатые роликоподшипники
Игольчатые роликоподшипники представляют собой цилиндрические роликоподшипники, очень длинные для своего диаметра. Такое высокое соотношение сторон позволяет им выдерживать большие радиальные нагрузки при очень компактных форм-факторах. Корпуса делятся на механически обработанные (прецизионные) и штампованные (вытяжные). Игольчатые подшипники со штампованным наружным кольцом минимизируют размеры; для приложений с очень ограниченным пространством доступны игольчатые подшипники без внутреннего корпуса.
Упорные подшипники
Упорные подшипники рассчитаны на высокие осевые нагрузки. Вместо использования двух концентрических дорожек качения, которые обычно встречаются в подшипниках, они используют форм-фактор блина, состоящий из двух плоских тороидальных дорожек качения, прижатых друг к другу, чтобы окружить ролики, ориентированные радиально от центра. Эта конфигурация позволяет упорному подшипнику выдерживать высокую осевую нагрузку без повреждений.
Проблема вращения наружного кольца
Фото: Getty Images / nantonov
На первый взгляд может показаться, что подшипник качения с вращением внутреннего кольца (вала) или вращением наружного кольца на самом деле не так уж и много разные по характеристикам подшипников. Чтобы дать некоторое представление, большинство применений подшипников с вращением внутреннего кольца (более 95 процентов).
Таким образом, конструкция стандартного подшипника ориентирована на применение с вращением внутреннего кольца. Большинство может не думать, что вращение внутреннего или наружного кольца имеет значение, но подшипники с вращением на наружном кольце обычно менее надежны, чем подшипники с вращением на внутреннем кольце. Ниже приведены случаи и связанные с ними проблемы.
Подшипники с тремя дорожками качения
Подшипники с тройными дорожками качения, которыми я занимался в течение многих лет, — это подшипники с тройными дорожками качения, которые использовались в некоторых специально разработанных валках газетной бумажной фабрики, которые имели три кольца и два набора роликов. Набор внутренних роликов имеет вращающееся внешнее кольцо, а набор внешних роликов имеет вращающееся внутреннее кольцо. Посмотрев в конце 1980-х годов видео о том, как смазка течет через внутреннее кольцо, установленное в лаборатории. Это было частью исследования проблем с комплектом внутренних подшипников, которые беспокоили многих пользователей.
На видео показана эффективность подачи масла в подшипник, который имел дополнительные вводы смазки во внутреннее кольцо подшипника. В то время все основные производители подшипников работали над решением проблемы. Одним из решений было увеличить подачу масла к проблемному комплекту роликов (что демонстрировалось на видео). Это было сделано для того, чтобы решить типичную диагностику неадекватной смазки, типичную для того, что наблюдалось.
Реклама
Другим решением этой проблемы было изменение конструкции внутреннего подшипникового узла на более узкий подшипник с роликами меньшего размера. Хотя это решение не учитывало предполагаемый вид отказа, оно устраняло более тонкую проблему, а именно проскальзывание роликов. Эта проблема связана с тем, как «катится» сферический ролик, когда внешнее кольцо вращается вокруг роликов и неподвижного внутреннего кольца, и, что более важно, когда это вращение внешнего кольца связано с угловым смещением.
Происходит следующее: направление движения ролика начинает отклоняться от направления качения, поскольку внутреннее и внешнее кольца становятся более несоосными. Это произошло с бумажной фабрикой, которая использовала один и тот же подшипник с тремя дорожками качения в двух разных машинах, и их надежность в одном приложении была хуже, чем в другом. При исследовании применений валок с меньшей надежностью имел большее всасывание, что могло вызвать больший изгиб вала, поддерживающего внутреннее кольцо самого внутреннего стационарного кольца. Эта разница в выравнивании самого внутреннего кольца была связана с меньшей надежностью, которая была вызвана разницей в направлении прокатки и траектории прокатки.
В качестве визуализации понаблюдайте за задними колесами 18-колесного прицепа, когда он поворачивает за угол. Шина вращается, но направление ее вектора находится под углом к направлению качения, в результате чего она скользит по дороге. По сути, это то, что происходило с роликами во внешнем кольце вращающегося сферического роликоподшипника. При использовании менее массивного ролика эффект скольжения ролика по дорожке снижается и снижается до такой степени, что скользящее движение не приводит к сцеплению с поверхностью, что и было основной причиной проблемы.
Герметичные подшипники
В приведенном выше примере считалось, что проблема связана со смазкой, но это не так, это не означает, что смазка и конкретно консистентная смазка не затрагиваются. При вращении наружного кольца смазка всегда выбрасывается на наружную обойму подшипника, и даже когда он не перекатывается в зоне контакта, на него действует центростремительная сила вращения. В отличие от случая, когда внутреннее кольцо вращается, на смазку, находящуюся на заплечиках внешней обоймы, действует только сила тяжести.
Центростремительная сила, действующая на смазку, вытягивает масло из смазки. Вращение наружного кольца приводит к постоянному центрифугированию смазки. Если нет уплотнения или средств удержания, смазка сама вытечет из подшипника. Даже при наличии уплотнения отделенное масло может проникать через уплотнение, так как типичные уплотнения, встроенные в подшипник, не предназначены для уплотнения на границе раздела наружного кольца, они предназначены для уплотнения на границе раздела внутреннего кольца и под давлением центростремительной силы вполне вероятно, что отделенное масло будет просачиваться через поверхность раздела уплотнение/наружное кольцо.
Таким образом, на фабриках по производству газетной бумаги есть два применения, в которых это проблематично: канатные шкивы и расправляющие валки. Оба имеют вращение по внешнему кольцу и оба имеют низкую надежность. Шариковые подшипники в канатных шкивах могут прослужить два года, тогда как тот же подшипник в электродвигателе может прослужить 10 лет. Другое приложение, разбрасыватель, растягивает лист бумаги, чтобы предотвратить появление складок. Хотя подшипнику требуется больше смазки для смазывания вращающихся подшипников наружного кольца, пользователи неохотно добавляют дополнительную смазку, так как когда они это делают, она выталкивается из подшипника на готовый лист бумаги, превращая его в отходы.
Вращающееся кольцо подшипника играет важную роль в работе подшипника. Применениям с вращением наружного кольца следует уделить особое внимание с точки зрения частоты повторного смазывания и точности центровки. Нельзя просто предполагать, что подшипник будет работать с той же надежностью, что и другие устройства, использующие тот же подшипник. MRO
___________
Дуглас Мартин (Douglas Martin) работает инженером по тяжелому машиностроению в Ванкувере. Он специализируется на проектировании вращающегося оборудования, анализе отказов и смазке. Свяжитесь с ним по электронной почте [email protected].
Понимание механических подшипников — урок для студентов
В мире производства и машиностроения, где широко используются машины, подшипник является механическим компонентом, который почти неизбежен. Термин образован от глагола «нести». Подшипники можно найти во всех видах машин, но в основном они выполняют свою работу под землей.
Механический компонент ограничивает относительное движение между двумя частями до требуемого движения. подшипники могут быть спроектированы так, чтобы обеспечивать свободное линейное перемещение подвижных частей или свободное вращение вокруг неподвижной оси. Он может предотвратить движение, контролируя векторы нормальных сил, действующих на движущиеся части.
Читать Все, что вам нужно знать о механической пружине
Основная функция подшипника — способствовать вращению объектов и уменьшать механическое трение между ними. Сегодня мы рассмотрим определение, функции, детали, классификацию, типы, принцип работы и схему подшипников, используемых в механике.
Содержание
- 1 Что такое подшипник?
- 2 Каковы функции подшипников?
- 3 Какие бывают типы подшипников?
- 3.1 Шариковые подшипники:
- 3.2 Конические роликовые подшипники:
- 3.3 Подпишитесь на нашу рассылку новостей
- 3.4 Упорные шариковые подшипники:
- 3.5 Упорные роликовые подшипники: 3 4 03 4?
- 4.0.1 Посмотрите видео, чтобы получить полное представление о работе подшипников:
- 4.1 Пожалуйста, поделитесь!
Подшипник — это механическая деталь, обеспечивающая линейное или вращательное движение и уменьшающая трение между двумя объектами. Это облегчает движение, снижает усталость и повышает скорость и эффективность между частями.
Поскольку валы, которые необходимы для вращения, используются в различных типах машин, подшипники должны быть частью, обеспечивающей их большие преимущества. Механическая часть широко используется в автомобилях, самолетах, электрогенераторах, холодильниках, кондиционерах, пылесосах, а также в бытовой технике. Судя по списку применений этого подшипника, мы, люди, не можем без них обойтись.
Ниже приведены функции подшипников в различных областях применения:
Помимо обеспечения бесперебойной работы машин, подшипники выполняют следующие две основные функции.
- Уменьшение трения и обеспечение легкого вращения
Поскольку трение является наиболее частым явлением между двумя вращающимися валами, особенно при отсутствии смазки. Между деталями используются подшипники, чтобы сделать вращение более плавным. Обратите внимание, что некоторые подшипники допускают смазку. Потребление энергии сокращается, так как трение уменьшается.
- Подшипник защиты части, поддерживающей вращение и удерживающей положение вала t
Еще одно основное назначение механического компонента — выдерживать большое усилие между вращающимся валом и частью, поддерживающей вращение. Подшипники поддерживают точное положение вращающегося вала.
Читать: Техническое обслуживание
Какие бывают типы подшипников?Различные типы подшипников подразделяются на два: радиальные подшипники (кронштейн вращающегося вала) и упорные подшипники (поддерживающие осевую нагрузку).
Эти типы подшипников работают с различными осевыми и радиальными нагрузками. Однако их отличие в том, что перпендикулярная опора намного прочнее других типов. Ниже приведены различные типы подшипников, предназначенных для восприятия осевых или радиальных нагрузок:
Шариковые подшипники:Шариковые подшипники рассчитаны на то, чтобы выдерживать как радиальные, так и осевые нагрузки. Они используются в различных приложениях различных размеров, поскольку подшипники получают номенклатуру, основанную на телах качения, и имеют равные доли с шарикоподшипниками.
Эти типы подшипников широко используются в автомобильной промышленности для таких деталей, как рулевое управление, силовая передача, карданный вал и т. д. Их также можно увидеть в бытовой технике и других промышленных машинах.
Шариковые подшипники могут выдерживать меньший вес, а также они имеют уникальную конструкцию, способную выдерживать нагрузки, и имеют уникальную структуру. Части шарикоподшипника включают внутреннюю обойму, внешнюю обойму, шарик качения и сепаратор.
Внутреннее кольцо входит в состав вращающегося вала, который стремится вращать ось, а внешнее кольцо установлено на корпусе. Шарик качения передает нагрузку через ось, а сепаратор предотвращает столкновение шариков с другими.
Конические роликоподшипники:Конические роликоподшипники рассчитаны на большие осевые и радиальные нагрузки. Они широко используются в автомобилестроении благодаря тому, что на них можно поднимать тяжелые грузы, не разрушая колеса. Эти типы подшипников обычно начинаются с серийного номера «3».
Детали конического роликоподшипника включают внутреннее и наружное кольца, между которыми расположены конические ролики. Внутреннее кольцо с телом качения образует узел, который индивидуально насаживается на наружное кольцо.
Коническая поверхность расширяется, чтобы обеспечить зацепление в одной точке на валу подшипника. Это указывает на то, что условия качения тел качения оптимизированы.
Осевая грузоподъемность этого подшипника определяется углом контакта, который соответствует углу внешней поверхности дорожки качения.
Присоединяйтесь к нашему информационному бюллетеню
Упорные шариковые подшипники:Упорные шариковые подшипники могут выдерживать осевые нагрузки при низких скоростях и малом весе. На барных стульях принято удерживать сиденье, так как оно содержит элементы качения. Слово «толчок» указывает на передачу осевых нагрузок или осевых нагрузок. Шариковый упорный подшипник обычно начинается с серии «5».
Упорный роликовый подшипник: Упорный роликовый подшипник может выдерживать большие осевые нагрузки, которые часто используются в трансмиссии автомобиля для поддержки косозубых шестерен. Осевая нагрузка воспринимается подшипником.
Работа подшипника довольно проста и понятна. Он состоит из шарика и внутренней части на внешней гладкой поверхности, по которой катится. Шарик имеет тот же вес, что и груз, и сила груза позволяет подшипнику вращаться.
Посмотрите видео, чтобы получить полное представление о том, как работает подшипник: В заключение отметим, что подшипник — это отличный компонент, цель которого — обеспечить простое рациональное и прямолинейное перемещение между двумя объектами. Мы рассмотрели различные типы подшипников, которые, как мы говорим, делятся на два типа; радиальный и упорный подшипник.
Это все для этой статьи. Надеюсь, вам понравилось чтение, если да, пожалуйста, прокомментируйте, поделитесь и порекомендуйте этот сайт другим студентам технических специальностей. Спасибо!
Сферические роликоподшипники уменьшают трение и обеспечивают более плавное вращение
Автор Бен Уоллс
ДОПОЛНИТЕЛЬНОЕ СОДЕРЖАНИЕ: 6 РЕШЕНИЙ ДЛЯ ПОДШИПНИКОВ, КОТОРЫЕ ЭКОНОМЯТ ВАМ ВРЕМЯ И ДЕНЬГИ подшипниковые решения.
Подшипники являются неотъемлемой частью промышленного оборудования. Целью подшипника является регулирование движения движущейся части и уменьшение трения.
Однако существует несколько типов подшипников, каждый из которых имеет свое назначение со своими преимуществами и недостатками.
Сферический роликоподшипник представляет собой подшипник качения, обеспечивающий вращение с низким коэффициентом трения и компенсирующий несоосность между валом и корпусом.
Bearings Manufacturing Company стремится быть поставщиком мирового класса модифицированных и изготовленных шариковых и роликовых подшипников. По этой причине мы работали со всеми типами роликовых подшипников в различных областях применения во всех отраслях промышленности.
Итак, если вы ищете сферический роликоподшипник для своего следующего проекта, какой следующий лучший шаг?
Вы можете связаться с торговым представителем по поводу ваших потребностей в подшипниках или отправить запрос в службу поддержки. Мы можем производить, модифицировать и ремонтировать большинство шариковых и роликовых подшипников.
А пока продолжайте читать, чтобы узнать больше о сферических роликоподшипниках.
Мы подумали, что было бы целесообразно создать серию постов, включающую основные типы подшипников качения, которые могут вам понадобиться для ваших проектов. Это второй пост из пяти частей. Если вы пропустили, вот первая статья — Что такое цилиндрические роликовые подшипники и как они используются?
Что такое сферические роликоподшипники?
Сферические роликоподшипники обеспечивают универсальность движения в двух направлениях. Его основная функция — уменьшить трение между компонентами, допуская несоосность.
Имеются два сферических роликоподшипника, негерметичные/открытые подшипники и герметизированные.
Оба подшипника рассчитаны на высокие нагрузки; тем не менее, закрытые подшипники выигрывают от использования корпуса, который помогает продлить срок их службы. Высокоэффективное двухкромочное уплотнение удерживает смазочные материалы и не пропускает загрязняющие вещества.
Понимание обоих типов подшипников и того, что необходимо для конкретного применения, имеет важное значение при поиске поставщиков.
Каковы преимущества использования сферических роликоподшипников?
- Подшипники уменьшают трение и обеспечивают более плавное вращение.
- Допускает угловое смещение. Сферические роликоподшипники являются самоустанавливающимися, что позволяет компенсировать несоосность.
- Подшипники поддерживают вращающуюся ось в отверстии внутреннего кольца.
- Подшипники обладают выдающейся грузоподъемностью при радиальных и комбинированных нагрузках в одном направлении благодаря множеству сферических роликов.
- Сферические роликоподшипники могут работать на средних и высоких скоростях.
- Сферические роликовые подшипники требуют меньшего обслуживания.
- Подшипники известны увеличенным сроком службы.
- Они обеспечивают пониженный уровень шума и вибрации.
Сферические роликовые подшипники Применение
Сферические роликоподшипники используются в чрезвычайно тяжелых условиях эксплуатации в очень сложных условиях.
Подшипники используются в приложениях, склонных к смещению или отклонению вала (изгибу вала при определенных обстоятельствах, таких как осевая нагрузка). Известно, что они допускают несоосность между валом и корпусом.
Сферические роликоподшипники, способные справляться с несоосностью, предназначены для различных механических применений.
Этот подшипник ежедневно используется в горнодобывающем, строительном, текстильном оборудовании и т.д. . .
«Сферические роликоподшипники имеют широкий спектр применения.
Они используются в приложениях, где возникают большие нагрузки, средние и высокие скорости и возможная несоосность. Примеры: внедорожники, насосы, механические вентиляторы, морские силовые установки, ветряные турбины. и коробки передач». [источник]
Подведение итогов
Сферические роликоподшипники отличаются длительным сроком службы в сочетании с высоким уровнем надежности. Они минимизируют трение и сохраняют шум и вибрацию во время работы.
Эти бочкообразные сферические ролики уменьшают трение внутри подшипника и позволяют подшипнику компенсировать угловое смещение.
В BMC вы получаете универсальное решение для ваших потребностей в подшипниках, включая модификацию, производство и ремонт.
Мы помогли дистрибьюторам и производителям по всему миру приобрести подшипники и продукты для передачи мощности, в которых они нуждались.
Поговорите сегодня с одним из наших экспертов по подшипникам, чтобы сообщить нам, что вам нужно, и мы поможем вам начать работу.
п.с. Следите за новостями о наших конических роликоподшипниках , если вам нужен подшипник, который можно адаптировать для поддержки высоких радиальных или осевых нагрузок (или и того, и другого).
Автор
Бен Уоллс
Обладая 15-летним опытом, Бен может работать с широким спектром ручных шлифовальных станков и станков с ЧПУ. Он досконально понимает и ежедневно применяет теорию измельчения, постоянное совершенствование и разработку процессов. Кроме того, Бен специализируется на модификации, ремонте и производстве подшипников.
Функции предотвращения вращения – блог igus
Подшипники скольжения
Ларс Бутеншон | 27. Ноябрь 2018 г.
Во втором эпизоде этой серии я показал вам несколько вариантов осевой фиксации подшипников, чтобы они не выскальзывали из отверстий в корпусе. В этом эпизоде я хочу показать вам, как сделать простую функцию предотвращения вращения и зачем она вам вообще нужна.
Зачем вам функция предотвращения вращения?
Поврежден подшипник.
Система подшипников скольжения обычно работает следующим образом: запрессовка в отверстие корпуса удерживает подшипник на месте. Подшипник поддерживает движущийся вал. Низкий коэффициент трения по внутреннему диаметру подшипника скольжения позволяет валу легко вращаться. Поскольку подшипник скольжения обычно значительно дешевле вала, он предназначен для использования в качестве изнашиваемой детали. Это означает, что вам просто нужно время от времени заменять подшипник скольжения, а не более дорогой вал.
Вот почему многие металлические подшипники скольжения покрыты тонким слоем ПТФЭ по внутреннему диаметру. Внешний металлический слой служит основой подшипника, а слой ПТФЭ обеспечивает плавную работу вала. Пластиковые подшипники более гибкие. Они обеспечивают возможность скольжения как по внутреннему, так и по внешнему диаметру. Так что не имеет значения, вращается ли вал внутри них или сам подшипник вращается в корпусе. Теоретически.
Продолжать вращаться – но где?
В действительности, однако, не имеет значения, вращается ли подшипник скольжения вокруг вала в корпусе или если подшипник остается неподвижным, а валы вращаются внутри него. Обычно валы оптимизированы для скольжения. Отверстий в корпусе нет. Наоборот: в большинстве случаев качество обработки отверстий в корпусе обходится довольно дешево. Это простые отверстия, просверленные в куске металла. Либо вырезаны лазером, либо штампованы. Создание отверстий с гладким внутренним диаметром обходится дорого, а материал, окружающий отверстие, обычно представляет собой дешевую конструкционную сталь или листовой металл. Все эти обстоятельства в значительной степени представляют собой набор запретов для изнашиваемых или скользящих компонентов. И именно поэтому вы не хотите, чтобы ваш подшипник вращался с валом в отверстии корпуса. В то время как сам подшипник не будет иметь проблем с работой по внешнему диаметру, поверхность, по которой он будет работать, будет.
На самом деле обе поверхности скольжения в системе подшипников имеют одинаковое значение. Если металлическая поверхность скольжения слишком шероховатая и абразивная, подшипник будет сильно изнашиваться, что приведет к более частым простоям или даже к повреждению подшипниковой системы. И именно поэтому вы захотите выбрать классический запрессовываемый невращающийся подшипник скольжения с вращающимся валом внутри. И именно поэтому вам захочется придумать альтернативные идеи, если вы не можете поддерживать пресс-фит.
Свободный выбор конструкции с пластиковыми подшипниками
Подшипники скольжения из пластмассы могут быть изготовлены практически любой формы. Ограничения, известные для подшипников из металла/ПТФЭ, такие как толщина листового металла или необходимость в смазочных канавках или смазочных ниппелях, которые могут понадобиться для бронзовых подшипников, не существуют. Кроме того, производственные технологии, такие как литье под давлением, 3D-печать, спекание и механическая обработка прутковых материалов, позволяют исследовать конструкцию деталей с небольшими ограничениями.
Вот несколько вариантов выполнения простых функций предотвращения вращения:
Вариант 1: Функция предотвращения вращения с отверстиями во фланце
Просверливая отверстия во фланце (или выполняя их с самого начала в пресс-форме), простые отверстия во фланце могут служить функцией предотвращения вращения. Просто вставьте несколько винтов внутрь и прикрепите подшипник к корпусу. Сделанный. Однако для больших количеств эта конструкция не слишком хороша, поскольку сборка требует ручного труда и, следовательно, требует больше времени. Кроме того, вам нужно будет учитывать стоимость винтов для каждого подшипника.
Подшипник с фиксирующими отверстиями во фланце
Вариант 2: Элементы предотвращения вращения с простой геометрической посадкой по внешнему диаметру
Даже простые меры могут быть надежными и экономичными решениями для удержания подшипников на месте. Формованная посадка означает, что форма подшипников сама по себе служит защитой от вращения. Вы можете легко добиться этого, изменив круглую внешнюю форму подшипника на что-то с краем или любым другим выступающим элементом. Увеличение стоимости соответствующей пресс-формы для литья под давлением относительно невелико. Однако вы должны учитывать, что вам также потребуется соответствующая форма отверстия в корпусе. Кроме того, для автоматизированной сборки может потребоваться убедиться, что подшипники всегда правильно совмещены с отверстием в корпусе.
Вариант 3: Механическая обработка/обработка отверстия корпуса
начале этого поста уже следует упомянуть как возможный вариант. Иногда может быть дешевле просто еще раз взглянуть на отверстие в корпусе. Может быть, было бы проще просто сделать правильно вынесенное отверстие в корпусе. Обычно достаточно стандартного допустимого отверстия H7.