Полимерные материалы что это: Полимерные материалы – что это такое и что к ним относится: виды и примеры изделий
alexxlab | 06.03.2020 | 0 | Разное
Что относится к полимерным материалам
Вещества, где блоки элементарного состава соединены, повторяются тысячи, миллионы раз называют полимерами. Вещество характеризуется большим молекулярным весом и возможностью выделить мономер, который называют звеном. Существуют природные и синтезированные ВМС. Если в основе цепи лежит четырехвалентный углерод – вещество органическое. Исключение составляют карбиды, карбонаты, цианиды и соли угольной кислоты.
Природные полимеры
Отдельные радикалы, элементарные молекулы с разорванной связью, в природе образуют кристаллы, смолы, белки, целлюлозные волокна. Если молекулы образованы углеродными связями, вещества относятся к биополимерам. Они образуют цепочку в целлюлозном волокне, сеточку в белке или разветвленную молекулу ДНК.
Кристаллы алмаза, кварца, волокна асбеста относят к природным неорганическим полимерам. Аморфную структуру имеют высокомолекулярные соединения смолы, каучуки.
Синтетические продукты
Природные материалы дороги, запас их ограничен. Человек научился синтезировать высокомолекулярные соединения, отвечающие потребностям, зачастую с новыми свойствами и низкой себестоимостью.
- полимеризация – за счет химических связей радикалов;
- поликонденсация – соединение с потерей определенных атомов;
- химическое модифицирование – изменение состава полимера, придание новых свойств.
Искусственное создание нового вещества возможно при соблюдении условий протекания реакции – температуре, давлении и наличия активных центров. Основная масса мономеров вступит в реакцию синтеза, но структура будет неоднородная по длине и разветвленности цепей. Калибровка – важный этап любого синтеза.
Строение полимерных молекул
Радикалом принято называть первичную молекулу с разорванной двойной связью или цепочку из нескольких молекул, открытую для дальнейшей полимеризации. Важно, чтобы в каждом таком звене был центр силы, притягивающий другой радикал.
- линейная цепь, насчитывающая тысячи звеньев;
- разветвленная структура с сотнями тысяч блоков;
- объемная сеть, где количество радикалов исчисляется миллионами.
Когда соединение происходит за счет химических или координационных связей одного элемента, молекула образует строение гомоцепного типа. Например, полиэтилен, политетрафторэтилен или полиметилакрилат. То есть связь происходит через один химический элемент, какой бы ни была сложной структура звена.
Полимер называют термопластом, если после расплавления он не теряет свойства, подлежат вторичной переработке.
Гетероцепные молекулы собираются, из нескольких радикалов. Они цепляются с разной частотностью, беспорядочно. Такие молекулы относятся к типу реактопластов. После изменения агрегатного состояния, молекулярная решетка вещества меняется.
Структура пластмассы бывает аморфного или кристаллического типа. Вновь полученное вещество может имитировать природный продукт, или превосходить его по свойствам, как получилось с искусственными алмазами.
Искусственный полимерный материал представляет продукт, полученный в результате синтеза одного или нескольких радикалов. Новое вещество обладает устойчивыми характеристиками.
Синтетические пластмассы, смолы, каучуки
Смола – это ВМС, полученный соединение радикалов. В твердом состоянии вещество представляет аморфную массу, от воздействия температуры размягчается. Все известные искусственные полимеры – смолы.
Термопласты и реактопласты
Полимер термопласт, относится к типу А, структура молекулы цепная. Вещество можно его расплавить и заново сформовать. Известные композиции термопластичных смол:
- полиэтиленовая;
- полипропиленовая;
- полихлорвиниловая;
- полистирольная;
- поливинилацетатная;
- полиакрилатная;
- инден-кумароновая.
Пластмасса – материал, образованный смолой, наполнителем, стабилизатором и красителем. Добавки придают продукту нужные свойства, снижают вязкость, обеспечивают долговечность составу. Полимер или смола – это продукт синтеза, а пластмасса – композиционный состав. Оргстекло, поликарбонат и тефлон – термопласты, готовые к употреблению без присадок.
К термоактивным пластмассам относят полимерные материалы, не восстанавливающие свойства после воздействия высоких температур:
- Фенопласт.
- Аминопласт.
- Волокнит.
- Асбестотекстолит.
Смолы – реактопласты
Смолы типа Б получаются в результате реакций поликонденсации или полимеризации в несколько ступеней. Структуры не линейные, получаются в результате соединения компонентов с выделением воды или простых газов. Использовать полимеры можно раз. Они твердеют, при изменении агрегатного состояния разрушаются.
Составы применяются как клеи, добавки в лакокрасочные, строительные, связующие смеси:
- Фенолформальдегидные смолы используют для склеивания пластиков, плит ДСП, в производстве лаков и клеев. К этому виду ВМС относят бакелитовый лак, полимер Б, Полимер ФР-12.
- Аминоформальдегидные смолы находят применение, как связующие для теплоизоляционных материалов, пластиков.
- Полиуретановые смолы – клеи.
- Кремнийорганические смолы характеризуются как гидрофобный материал. Клеи на этой основе не разрушаются от температурных колебаний.
- Эпоксидные смолы используют в виде связующего в строительных смесях. Для склеивания требуется добавка отвердителя.
Искусственные каучуки
Все материалы, относящиеся по признакам к каучукам эластичны. Длинная линейная молекула вещества свернута в комочек. При растягивании она меняет конфигурацию. Такие вещества называют эластомеры. Известны синтезированные каучуки:
- бутадиеновый;
- изопреновый;
- хлорпреновый:
- бутадиенстирольный.
Основной радикал в синтезированном каучуке бутадиен, его изомер, молекула с хлором и стирол.
Вулканизируя сажу путем нагревания состава с добавлением сажи получается резина. Известный материал эбонит – трехмерная структура, полученная в результате вулканизации каучука с порошковой серой.
Синтезированное волокно
Волокна, нити можно получить искусственным путем, преобразуя целлюлозное волокно, полученное в результате химического разложения древесины. Вискозные, ацетатные, штапельные волокна – это искусственный материал.
Синтез позволяет получить структуры, превосходящие натуральные по эластичности, воздухопроницаемости, техническим свойствам. В основе изготовления тканых, нетканых полотен, утеплителей, наполнителей особыми свойствами лежат искусственные смолы.
Виды синтетических волокон:
- Полиамидное, капрон, неустойчив к световому облучению, разрушается от кислот, используется для создания технических высокопрочных тканей.
- Полиэфирное, лавсан используется для бытовых и технических тканей, транспортерных лент, мешков безопасности.
- Полиакрилонитрильное, нитрон, напоминает шерсть, теплостойкие, устойчивы к УФ-лучам.
- Поливинилспиртовое, особо прочное, используется для армирования, текстильной обуви, спортивной одежды;
- Полипропиленовое волокно с хорошей эластичностью используется для изготовления ковров, технических тканей.
- Полиуретановое, спандекс, эластичный материал, по свойствам напоминающий каучук.
- Поливинилхлоридное, совиден, ПВХ волокно – негорючее, химически стойкое, используется для фильтров и защитной одежды.
В производстве используются не только текстильные, но формованные нетканые полотна, разной толщины.
Актуальной стала разработка углеволокна. Композит превосходят металлическую нить по прочности, не меняет объем при изменении температуры, имеет низкий коэффициент трения. Углепластик, легкий и жесткий, технологичный материал, применяется во многих сферах промышленности.
Приглашение к сотрудничеству
Компания «Юнитрайд» готова выполнить заявку на любой из перечисленных видов полимерной продукции. Поставки выполняются с заводов по согласованной логистике и ценам производителя.
Полимерные материалы – это… Что такое Полимерные материалы?
материалы на основе высокомолекулярных соединений — веществ, состоящих из однотипных групп атомов, соединенных химическими связями. Основную массу высокомолекулярных соединений получают либо методами химического синтеза из мономеров — продуктов переработки природного сырья (нефти, газа, угля и др.), либо путем переработки природных полимеров (например, целлюлозы, лигнина). В состав П. м. могут входить наполнители, красители, пластификаторы, стабилизаторы и другие добавки, регулирующие функциональные и технологические их свойства. При изготовлении изделий компоненты, входящие в состав П. м., тщательно гомогенизируют до получения однородной пластмассы, из которой прессованием, литьем под давлением, экструзией (формированием изделий путем выдавливания П. м. через профилирующий инструмент), вальцеванием или другим технологическим методом получают готовое изделие или материал, используемый для дальнейшей переработки.
Для медицинских целей используют П. м. общетехнического назначения, а также специальное П. м. медицинского назначения (рис.). Из первых изготавливают строительное и санитарно-техническое оборудование лечебных учреждений, белье, посуду, предметы ухода за пациентами, детали различных приборов, исследовательской и лечебной аппаратуры, инструментов, посуды для аналитических лабораторий и др. Применение П. м. вместо традиционных материалов (металлов, стекла) обусловлено их лучшими технологическими свойствами, комплексом физико-механических характеристик, возможностью переработки в изделия массового выпуска и однократного применения. Помимо общетехнических к этим полимерным материалам предъявляются дополнительные санитарно-гигиенические требования — минимальное выделение в окружающую среду газообразных продуктов, не превышающее ПДК; нерастворимость в моющих растворах; возможность стерилизации дезинфицирующими растворами, газами, УФ-облучением, гамма-излучением и др. Наиболее широко применяются П. м. на основе поливинилхлорида. сополимеров стирола, полипропилена, полиметилметакрилата, полиуретанов, фенол-, мочевино-меламино-формальдегидных смол. Из них выпускают изделия различного назначения, а также плиты, листы, пленки, трубы, тканые и нетканые материалы на основе волокон, пасты, герметики, лаки, клеи. Специальные П. м. медицинского назначения предназначены для непосредственного контакта с живым организмом — в эндопротезах и материалах для восстановительной хирургии, в материалах и изделиях для службы крови, в виде инструментов для внутриорганных исследований, аппаратуры, заменяющей функции сдельных органов, компонентов терапевтических и диагностических средств. Основу таких П. м составляют синтетические и природные высокомолекулярные соединения, не оказывающие на живой организм вредного воздействия. По характеру взаимовлияния с организмом П. м. разделяют на биоинертные, биосовместимые и биоактивные. Биоинертные П. м. (полиэтилен, полипропилен, фторопласт, силиконы, полиметилметакрилат и др.) практически не изменяют своих свойств под влиянием сред живого организма. В виде готовых изделий или материалов их используют для создания искусственных сосудов (полиэтилентерефталат, полипропилен, фторопласт), клапанов сердца (силикон, фторопласт, полипропилен, полиэтилентерефталат), хрусталиков глаз (полиметилметакрилат), частей эндопротезов суставов (полиамиды, фторопласт), в качестве искусственных сухожилий, мышечных связок (полипропилен, полиэтилентерефталат), деталей аппаратов искусственная почка, искусственное сердце — легкое (полиэтилен, полипропилен, полиакрилаты, силиконы, эфиры целлюлозы) и др.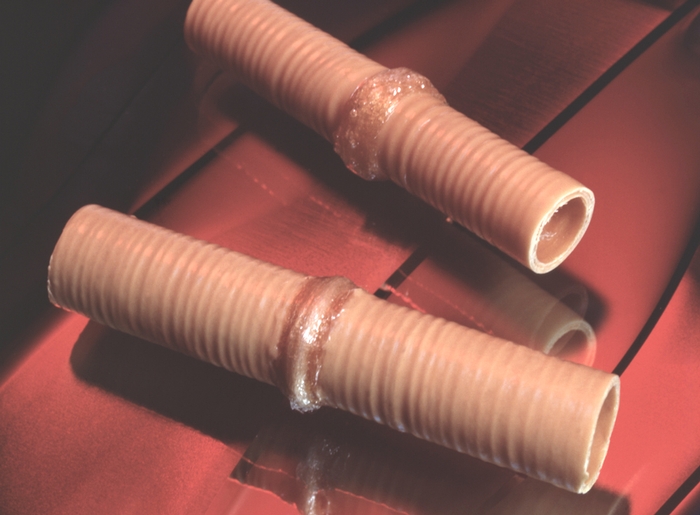
Рис. б). Изделия медицинского назначения из полимерных материалов: протезы трахеи.
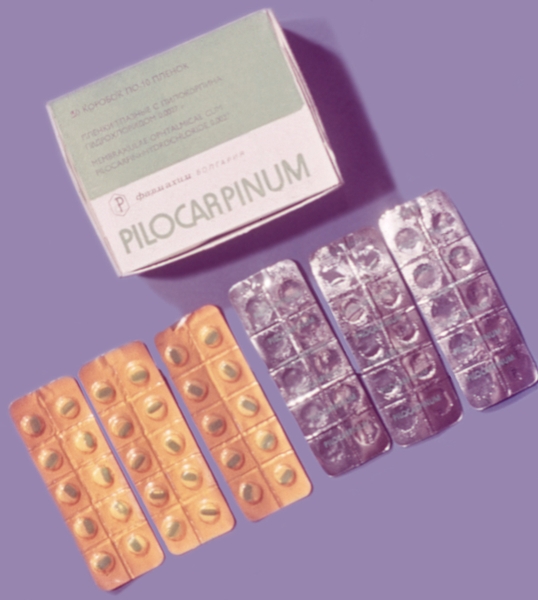
Рис. а). Изделия медицинского назначения из полимерных материалов: упаковка для таблетированных лекарственных средств.
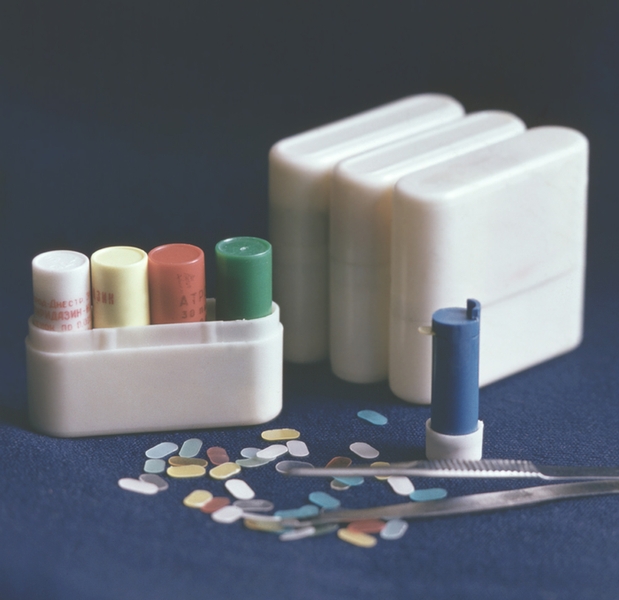
Рис. в). Изделия медицинского назначения из полимерных материалов: глазные лекарственные пленки в пеналах-дозаторах.
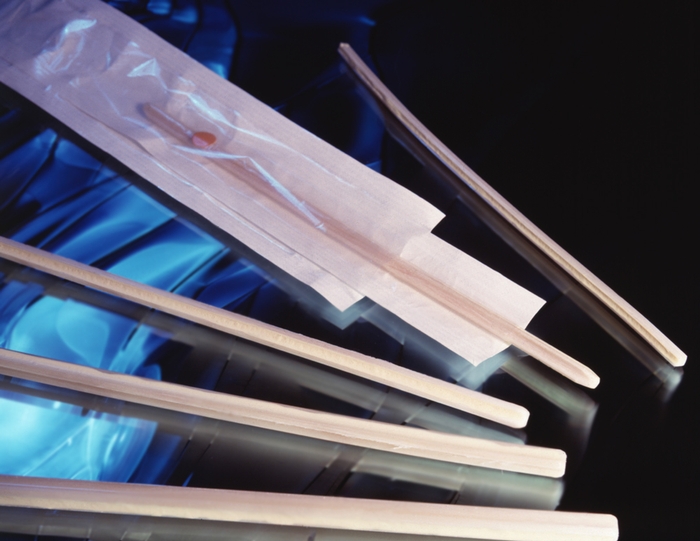
Рис. г). Изделия медицинского назначения из полимерных материалов: штифты для соединения отломков трубчатых костей.
Полимерные материалы Википедия
Полиме́ры (от греч. πολύ «много» + μέρος «часть») — вещества, состоящие из «мономерных звеньев», соединённых в длинные макромолекулы химическими или координационными связями. Полимерами могут быть неорганические и органические, аморфные и кристаллические вещества. Полимер — это высокомолекулярное соединение: количество мономерных звеньев в полимере (степень полимеризации) должно быть достаточно велико (в ином случае соединение будет называться олигомером). Во многих случаях количество звеньев может считаться достаточным, чтобы отнести молекулу к полимерам, если при добавлении очередного мономерного звена молекулярные свойства не изменяются[1]. Как правило, полимеры — вещества с молекулярной массой от нескольких тысяч до нескольких миллионов[2].
Если связь между макромолекулами осуществляется с помощью слабых сил Ван-Дер-Ваальса, они называются термопласты, если с помощью химических связей — реактопласты. К линейным полимерам относится, например, целлюлоза, к разветвлённым, например, амилопектин, есть полимеры со сложными пространственными трёхмерными структурами.
В строении полимера можно выделить мономерное звено — повторяющийся структурный фрагмент, включающий несколько атомов. Полимеры состоят из большого числа повторяющихся группировок (звеньев) одинакового строения, например поливинилхлорид (−CH2−CHCl−)n, каучук натуральный и др. Высокомолекулярные соединения, молекулы которых содержат несколько типов повторяющихся группировок, называют сополимерами или гетерополимерами.
Полимер образуется из мономеров в результате реакций полимеризации или поликонденсации. К полимерам относятся многочисленные природные соединения: белки, нуклеиновые кислоты, полисахариды, каучук и другие органические вещества. В большинстве случаев понятие относят к органическим соединениям, однако существует и множество неорганических полимеров. Большое число полимеров получают синтетическим путём на основе простейших соединений элементов природного происхождения путём реакций полимеризации, поликонденсации и химических преобразований. Названия полимеров образуются из названия мономера с приставкой поли-: полиэтилен, полипропилен, поливинилацетат и т. п.
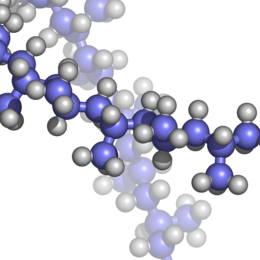
Полимерные покрытия: какие полимеры используются в качестве покрытий, какими достоинствами и недостатками они обладают
Полимерные покрытия применяются для защиты металлических деталей от коррозии и придания им декоративного внешнего вида. Особой разновидностью полимерных материалов являются антифрикционные покрытия, которые не только препятствуют износу деталей, но и выполняют функцию смазки.
Полимерные покрытия предназначены для обработки металлических поверхностей в целях защиты от коррозии и придания декоративного внешнего вида.
В качестве полимерного покрытия могут выступать полиэстер, поливинилденфторид (ПВДФ), пластизол, пурал и др.
Рассмотрим эти материалы, сферы их применения и технологии нанесения подробнее.
Полиэстер
Полиэстер (полиэфир) – наиболее популярный полимер, используемый в качестве покрытия. Он характеризуется высокой стойкостью к УФ-излучению, отличными антикоррозионными свойствами, эластичностью (легко поддается формовке).
Полиэстеровое покрытие выдерживает практически любые температуры – как низкие, так и высокие.
По сравнению с другими видами полимеров полиэстер наиболее доступен по цене.
Не слишком выдающиеся прочностные характеристики материала компенсируются дополнительной обработкой кварцевым песком. Однако стоимость нанесения покрытия при этом возрастает.
Транспортировка изделий с полиэстерово-кварцевым защитным слоем представляет определенные сложности, так как песок может повредить смежные с ним поверхности.
ПВДФ-покрытие
Поливинилденфторид (ПВДФ) применяется для защиты металлов не намного реже, чем полиэстер. Данный полимер состоит из поливинилхлорида (80 %) и акрила (20 %).
ПВДФ образует на деталях блестящий, устойчив к выцветанию слой, поэтому часто используется в качестве декоративного покрытия. Данный материал может придать поверхности глянец, эффект “металлик”, медный или серебристый оттенок.
Поливинилденфторид устойчив к механическому воздействию и обладает наибольшим сроком службы среди всех полимеров. ПВДФ используется для обработки металлических поверхностей, которые эксплуатируются под воздействием агрессивной окружающей среды.
Пластизол
Пластизол, как и ПВДФ-покрытие, обладает отличными декоративными свойствами. По стоимости он является самым дорогим, однако при этом обладает наилучшей устойчивостью к механическим повреждениям.
Пластизол наносится толстым слоем (до 200 мкм) и используется для создания фактурных покрытий, тисненых поверхностей и штампованных рисунков.
Данный материал отлично защищает детали от влаги и коррозии, однако под воздействием очень высоких температур (свыше +80 °С) и прямого УФ-излучения может потерять свои свойства. Именно поэтому его не рекомендуется использовать в южных широтах (в крайнем случае можно применять пластизол светлых тонов с максимальной светоотражающей способностью).
Пурал
Пурал изготавливается на основе полиуретана и модифицированного полиамида. Покрытие из пурала отличается шелковисто-матовой поверхностью, высокой термостойкостью и устойчивостью к резким перепадам температур.
Данный материал не выцветает и не разрушается под действием химически агрессивных сред. Пурал не так устойчив к пластическому деформированию, как пластизол, и стоит дороже, чем полиэстер, однако по соотношению цены и качества является оптимальным вариантом из всех представленных выше.
Наибольшее распространение пураловые покрытия получили при производстве кровельных элементов из оцинкованного металла. Сталь, обработанная пуралом, приобретает красивый внешний вид, высокие антикоррозионные характеристики и устойчивость к УФ-излучению.
Полимерные антифрикционные покрытия
Особой разновидностью полимерных защитных материалов являются антифрикционные твердосмазочные покрытия. Внешне они похожи на краски, однако пигмент в их составе заменяют высокодисперсные частицы твердых смазочных веществ: дисульфида молибдена, графита, политетрафторэтилена и др.
Твердые смазки равномерно распределены в полимерном связующем: эпоксидной, титанатовой, полиуретановой, акриловой, фенольной и других смолах.
Востребованность антифрикционных твердосмазочных покрытий обусловлена их отличными рабочими характеристиками: высокой несущей способностью, широким диапазоном эксплуатационных температур, противозадирными и антикоррозионными свойствами.
В отличие от обычных полимерных покрытий, антифрикционные выдерживают длительное воздействие химически-агрессивных сред и экстремальных нагрузок. При этом они выполняют не только защитную, но и смазочную функцию, чем также выигрывают у полимеров.
В качестве примера таких материалов можно привести отечественные покрытия MODENGY. Они используются в самых различных отраслях промышленности и автомобилестроения.
Типовыми узлами применения покрытий являются средне- и тяжелонагруженные подшипники, направляющие, зубчатые передачи, детали ДВС (юбки поршней, дроссельная заслонка и пр.), резьбовые соединения и другие пары трения из различных материалов (металлов, резин, пластмасс).
Антифрикционные твердосмазочные покрытия MODENGY наносятся однократно на весь срок службы деталей, что позволяет полностью отказаться от масел и пластичных смазок для дальнейшего обслуживания.
Достоинства и недостатки полимерных покрытий
Полимерные покрытия обладают как неоспоримыми преимуществами, так и явными недостатками.
К достоинствам полимеров можно отнести:
- Эстетичность
- Непроницаемость
- Относительную термостойкость
- Электроизоляционные свойства
- Устойчивость к воде
- Экологичность
- Высокую адгезию
- Большой выбор расцветок
Однако, наряду с положительными сторонами, полимерные покрытия не лишены недостатков. Главный из них – высокая стоимость нанесения, которая складывается из стоимости самого полимера, вспомогательных (грунтовочных) материалов, специального оборудования и пр.
Еще одним минусом полимерных покрытий является сложность их удаления. Они достаточно устойчивы к химикатам, поэтому растворителем удалить полимерный слой не получится. Снять покрытие можно только с помощью специального инструмента.
Существенный недостаток полимеров – невозможность их нанесения без специальных инструментов, которыми располагают только промышленные предприятия или узкие специалисты.
Помимо всего прочего, полимерными составами возможно покрывать не все металлы, а только те, которые проводят электрический ток. Это связано с особым методом нанесения полимеров – путем магнитной индукции.
Нанесение полимерного покрытия
При нанесении полимерного покрытия методом напыления главную роль играет оборудование.
Бак краскопульта имеет положительный заряд, в то время как окрашиваемая деталь заряжается отрицательно. Благодаря этому при контакте полимерного состава с поверхностью изделия возникает явление, схожее с магнитной индукцией при замыкании электрода.
Весь процесс нанесения разделен на этапы, следование которым напрямую влияет на качество конечного результата. При малейших отклонениях от технологии рабочие характеристики полимерного покрытия могут быть сведены к нулю.
На первом этапе работы происходит подготовка поверхности: она тщательно очищается от загрязнений и обезжиривается, те участки, которые обрабатывать не нужно, закрываются.
Далее следует предварительное грунтование изделия, нанесение самого покрытия, возможно лакирование. Все операции происходят в специальной закрытой камере, изолированной от проникновения пыли и других частиц. Одно из главных требований к этой камере – хорошая освещенность, позволяющая специалисту рассмотреть поверхность детали и нанести покрытие с любого ракурса.
Обрабатываемую деталь подвешивают на специальных крюках, подают на нее отрицательный заряд и приступают к нанесению покрытия. Весь процесс занимает достаточно много времени, материал наносится в один слой во избежание неравномерности.
Третий этап – полимеризация. Изделие с покрытием медленно прогревается в специальной камере с максимальной температурой +200 °C. Процесс занимает около 1 часа. Температура и время отверждения зависят от толщины слоя. Важным фактором правильной сушки является медленный и равномерный нагрев печи, во время которого покрытие растекается по детали, проникая во все труднодоступные места.
На последнем этапе изделие охлаждается. Для этого температура в печи постепенно снижается до +100 °C. Нельзя допускать резкого охлаждения камеры, так как на полимерном покрытии могут появиться трещины. Запрещается также открывать печь, так как перепад температуры вызовет те же последствия.
Остывшую деталь извлекают из печи и помещают в камеру для нанесения краски или лака. Данная операция необязательна и имеет, скорее, декоративное значение. Таким образом полимерному покрытию придается дополнительный блеск и глубина.
Антифрикционные твердосмазочные покрытия могут наноситься стандартными методами окрашивания: распылением, окунанием, центрифугированием, трафаретной печатью.
Распыление – наиболее простой способ. Для его реализации понадобится распылительный пистолет с точно настроенными параметрами, источник сжатого воздуха и само покрытие.
Что такое полимер? | MATSE 81: Материалы в современном мире
Щелкните, чтобы увидеть расшифровку «От ДНК к глупой замазке», «Разнообразный мир полимеров».
Что общего у шелка, ДНК, дерева, воздушных шаров и Silly Putty? Это полимеры.
Полимеры настолько важны в нашей жизни, что практически невозможно представить мир без них, но что это за хрень? Полимеры – это большие молекулы, состоящие из небольших единиц, называемых мономерами, связанных между собой, как железнодорожные вагоны из поезда.Поли означает много, моно означает один, а мерс или меро означает части. Многие полимеры сделаны путем повторения одного и того же небольшого мономера снова и снова, в то время как другие сделаны из двух мономеров, связанных в узор.
Все живое сделано из полимеров. Некоторые органические молекулы в организмах маленькие и простые, имеющие только одну из нескольких функциональных групп. Другие, особенно те, которые играют структурные роли или хранят генетическую информацию, являются макромолекулами. Во многих случаях эти макромолекулы представляют собой полимеры.Например, сложные углеводы – это полимеры простых сахаров, белки – это полимеры аминокислот, а нуклеиновые кислоты, ДНК и РНК, которые содержат нашу генетическую информацию, – это полимеры нуклеотидов. Деревья и растения сделаны из полимерной целлюлозы. Это твердый материал, который можно найти в коре и стеблях. Перья, мех, волосы и ногти состоят из белкового кератина, который также является полимером. Это еще не все. Знаете ли вы, что экзоскелеты самого большого типа в животном мире, членистоногих, сделаны из полимерного хитина?
Полимеры также составляют основу синтетических волокон, каучуков и пластмасс.Все синтетические полимеры получают из нефтяного масла и производятся химическими реакциями. Два наиболее распространенных типа реакций, используемых для получения полимеров, – это реакции присоединения и реакции конденсации. Помимо реакций, мономеры просто складываются вместе с образованием полимера. Процесс начинается со свободного радикала, разновидности с неспаренным электроном. Свободные радикалы атакуют и разрывают связи, образуя новые связи. Этот процесс повторяется снова и снова, чтобы создать длинноцепочечный полимер. В реакциях конденсации небольшая молекула, такая как вода, образуется с каждой реакцией удлинения цепи.
Первые синтетические полимеры были созданы случайно как побочные продукты различных химических реакций. Считая их бесполезными, химики в основном их отбрасывали. Наконец, некто по имени Лео Бэкеланд решил, что, может быть, его бесполезный побочный продукт не так уж и бесполезен. Его работа привела к созданию пластика, которому можно было надолго придать форму под действием давления и высоких температур. Поскольку название этого пластика, полиоксибензилметиленгликольангидрид, было не слишком запоминающимся, рекламодатели назвали его бакелитом.Из бакелита делали телефоны, детские игрушки и изоляторы для электрических устройств. С развитием индустрии пластмасс в 1907 году произошел взрывной рост.
Еще один знакомый полимер, Silly Putty, также был изобретен случайно. Во время Второй мировой войны Соединенные Штаты отчаянно нуждались в синтетическом каучуке для поддержки армии. Команда химиков из General Electric попыталась создать его, но в итоге получила липкую мягкую замазку. Это не был хороший заменитель резины, но у него было одно странное качество: он казался чрезвычайно упругим.Так родился Silly Putty!
Синтетические полимеры изменили мир. Подумай об этом. Можете ли вы представить себе, как прожить один день без пластика? Но не все полимеры хороши. Пенополистирол, например, состоит в основном из стирола, который был определен Агентством по охране окружающей среды как возможный канцероген. По мере производства изделий из пенополистирола или их медленного разрушения на свалках или в океане они могут выделять токсичный стирол в окружающую среду. Кроме того, пластмассы, созданные в результате реакций присоединительной полимеризации, такие как пенополистирол, полиэтиленовые пакеты и ПВХ, долговечны и безопасны для пищевых продуктов, но это означает, что они не разрушаются в окружающей среде.Ежегодно на свалки вывозятся миллионы тонн пластика. Этот пластик не разлагается биологически, он просто распадается на все более мелкие части, влияя на морскую жизнь и в конечном итоге возвращаясь к людям.
Полимеры могут быть мягкими или твердыми, мягкими или твердыми, хрупкими или прочными. Огромное различие между ними означает, что они могут образовывать невероятно разнообразный набор веществ, от ДНК до нейлоновых чулок. Полимеры настолько полезны, что мы стали полагаться на них каждый день. Но некоторые засоряют наши океаны, города и водные пути, оказывая воздействие на наше здоровье, что мы только начинаем понимать.
.8 Свойства полимерных материалов для использования в строительстве
Механические и химические свойства полимерных материалов очень важно знать перед использованием в любом строительстве. Такие материалы все чаще используются в строительстве инфраструктуры, например, в конструктивных элементах, защитных покрытиях и клеях.
Механические и химические свойства полимерных материалов имеют решающее значение для проектировщиков и инженеров, поскольку эти характеристики показывают, подходят ли эти материалы для использования в строительстве.
Высокая прочность или отношение модуля к массе, ударная вязкость, упругость, устойчивость к коррозии, отсутствие теплопроводности (тепловой и электрической), цвет, прозрачность – это свойства, присущие большинству полимерных материалов. Свойства полимерных материалов можно изменить, добавляя стабилизатор или пластификаторы.
Инженеры в основном озабочены механическими свойствами и физико-химическими свойствами, которые определяют долговечность. Механический отклик полимерных материалов может заметно измениться в довольно небольшом температурном диапазоне.
Свойства полимерных материалов
1. Плотность
Плотность полимерных материалов низкая, поскольку они состоят в основном из легких элементов. Плотность полиметилпентана составляет 830 кг на кубический метр, полипропилена (ПП) – 905 кг на кубический метр, а политетрафторэтилена (ПТФЭ) – 2150 кг на кубический метр. Эти плотности значительно ниже, чем у стали, которая составляет 7850 кг на кубический метр.
2. Тепловое расширение
Тепловое расширение полимеров относительно велико.Это необходимо учитывать при разработке и использовании полимерных компонентов, особенно при использовании в сочетании с другими инженерными материалами.
Полимеры могут расширяться за счет изменения суммы в разные стороны благодаря своему составу. Он содержит сильные ковалентные связи вдоль полимерной цепи и гораздо более слабые дисперсионные силы между полимерными цепями.
3. Теплопроводность
Коэффициент теплопроводности (К-фактор) полимеров очень низкий.Это делает его подходящим изоляционным материалом. Полимеры также обладают превосходными электроизоляционными свойствами.
При температуре окружающей среды ненаполненные полимеры имеют удельную проводимость в диапазоне 0,15-0,13 Вт / м ° C, около 240 Вт / м ° C, а у меди – около 385 Вт / м ° C Вт / м ° C.
Твердые полимеры имеют теплопроводность в диапазоне от 0,16 до 0,45 Вт / м / К. У вспененных полимеров теплопроводность составляет всего 0,024 Вт / м / К (ватт на метр на градус Кельвина).
4.Проницаемость
Обычно твердые полимеры не содержат взаимосвязанных пор и могут обычно считается практически непроницаемым. Вот почему полимеры часто используется в качестве защитных покрытий, пароизоляции, герметиков, конопаток составы и защита от газов и паров.
5. Химическая стойкость
Полимер устойчив к воздействию химикатов, что делает его подходящей конструкцией материал в различных обстоятельствах.
6.Прочность
Там есть несколько типов прочности, такие как растяжение, сжатие, изгиб, крутильная и ударная вязкость. На ударную вязкость сильно влияют изменение температуры, ударная вязкость обычно падает с ростом температуры падает.
Прочность полимерного материала составляет на основе молекулярной массы, сшивки и кристалличности. Растяжение прочность полимера повышается с увеличением молекулярной массы. Точно так же большие молекулярная масса обеспечивает высокую прочность.
Кроме того, сшивание уменьшается движения цепей и увеличивает прочность полимера. Кристалличность полимера увеличивает прочность, потому что в кристаллической фазе межмолекулярная связь более значительна.
7. Прочность
Прочность зависит от типа полимера, его состава и структуру, а также синергетический эффект условий воздействия. В долговечность полимера определяет, подходит ли он для внешних строительные приложения
Изменения, которые вызывают ухудшение состояния полимеров в окружающей среде и в конечном итоге определяют их долговечность, сложны и разнообразны.Сложность возникает из-за совместного действия ряда агентов разложения, особенно ультрафиолетового излучения (солнечного света), тепла, кислорода, озона и воды.
Список основных агентов и режимов разложения полимерных материалов приведен в таблице 1.
Таблица 1: Основные агенты и способы разложения полимера
Основные агенты | Режим разложения |
Кислород при умеренной температуре | Термическое окисление |
Кислород при более высокой температуре | Горение |
Кислород + ультрафиолетовое излучение | Фотоокисление |
Вода | Гидролиз |
Только тепло | Пиролиз |
Ионизирующее излучение | Радиолиз |
Микроорганизмы | Биологическая атака |
Кислород атмосферы + вода + солнце радиация | Выветривание Атмосферная деградация |
Эти агенты вызывают физические и химические изменения на молекулярном уровне, и эти изменения различаются от одного полимера к другому.Например,
Полиэтилен подвержен фотоокислению под солнечным светом, если он не стабилизирован преднамеренно поглотителями ультрафиолета, такими как технический углерод. В результате они более устойчивы к атмосферным воздействиям.
Фотоокисление и термическое окисление полимера с кислородом воздуха может вызвать сшивание полимерной цепи с сопутствующим охрупчиванием или разрывом цепочки на мелкие фрагменты. Эти фрагменты растворимы в воде и повторно промываются. наружу, вызывая эрозию поверхности.
Ионизирующее излучение также вызывает молекулярные повреждения полимеров, что приводит к слиянию, сшиванию и разрушению полимерных цепей. Некоторые полимеры разрушаются из-за медленного хрупкого разрушения при напряжениях, значительно меньших нормального напряжения разрушения, когда они подвергаются воздействию определенных конкретных органических веществ.
Это приводит к растрескиванию под воздействием окружающей среды (ESC) в точках локальной концентрации напряжений. Полиэтилен (ПЭ) можно сделать более устойчивым к растрескиванию под напряжением за счет увеличения длины цепи.
8. Токсичность
Некоторые органические мономеры, из которых синтезируются полимеры, признаны токсичными, и при обращении с этими веществами введены строгие меры контроля. Уровни остаточного свободного мономера в термопластах чрезвычайно низки, и эти материалы обычно не считаются опасными.
Однако при воздействии высокой температуры может происходить частичное пиролитическое разложение с выделением мономера или других летучих и токсичных веществ. С неполимеризованными веществами следует обращаться с особой осторожностью.
Кроме того, возникают проблемы токсичности с некоторыми полимерными добавками, и добавки, разрешенные в составах для контакта с питьевой водой, должны подлежать строгому контролю.
.Динамическое механическое поведение полимерных материалов
1. Введение
Изучение возможностей современных материалов и конструкций для работы в экстремальных условиях было горячей темой исследований на протяжении десятилетий [1–5]. В настоящее время материалы и технологии материалов могут быть адаптированы для применения в строительстве. В последние годы ударопрочные устройства и конструкции привлекают большое внимание из-за инженерных требований безопасности.Они требуют специальных концепций дизайна и оптимизированных свойств материалов. Большинство доступных в настоящее время материалов приводят к увеличению веса и / или объема конструкций и устройств для соответствия требованиям по ударопрочности. Во многих случаях такое увеличение недопустимо при проектировании конструкции. Для решения этой проблемы в материалах используется тенденция к снижению веса и увеличению прочности при разумных затратах. Материальные технологии позволяют удовлетворить эти требования. Они предоставляют возможность разрабатывать современные материалы с высокой специальной прочностью (отношение прочности к весу) и ударной вязкостью для применения в динамических условиях.
Полимерные материалы стали предметом широких исследований в экстремальных условиях из-за их выдающихся характеристик, таких как ударопрочность, зависимость скорости, коррозионная стойкость, низкая плотность, простота формования и так далее. Более того, в некоторых инженерных приложениях они демонстрируют выдающиеся преимущества и заменяют традиционные металлы и неметаллические материалы [1, 2].
Следовательно, понимание динамического механического поведения полимеров необходимо. В частности, исследования полимеров при взрыве, ударе, столкновении и других связанных механических свойствах при ударной нагрузке имеют как теоретическое, так и практическое значение.В этой главе представлена текущая программа исследований динамического механического поведения различных типичных полимеров.
2. Технология определения характеристик
Из-за действия нагрузки с высокой скоростью деформации [6–10] динамическая механическая реакция материалов отличается от таковой при статической нагрузке. Характеристика динамического механического поведения представляет большой интерес для материалов, применяемых при ударах. Для полимеров из-за их низкого волнового сопротивления требуется больше времени для достижения равновесия динамических напряжений во время теста с разделенным стержнем Гопкинсона (SHB) [11, 12], что создает больше трудностей в высокоскоростных механических экспериментах.
Для уменьшения разницы в волновом сопротивлении в испытании SHB используется вязкоупругий ударный стержень [13]. Однако сам вязкоупругий стержень обладает чувствительностью к скорости деформации, что легко приводит к дисперсии и затуханию волны напряжения во время перемещения стержня [14]. Пруток из алюминиевого сплава, по-видимому, эффективен для тестирования полимерных материалов благодаря согласованию волнового сопротивления и более низкой чувствительности к скорости деформации. Для соблюдения условий постоянной скорости деформации и равновесия динамических напряжений необходимо точно рассчитать форму падающего импульса [15].Для удовлетворения этих требований применяется метод формирования импульсов, который, как правило, помещает пластину в конец падающего стержня. Материал пластины может быть медью. Преимущество этого метода формирования импульсов заключается в уменьшении колебаний падающей волны. Путем выбора соответствующей формы и размера образца можно реализовать нагружение с постоянной скоростью деформации и равномерным напряжением в образце [8, 16, 17]. Кроме того, материал с низким волновым сопротивлением в эксперименте SHB сделает сигнал передатчика слабым, что приведет к небольшой разнице между падающим и отраженным сигналами.Полупроводниковый тензодатчик более чувствителен [18], что позволяет обнаруживать слабый сигнал. Таким образом, его можно использовать в эксперименте SHB для тестирования мягких полимерных материалов.
Кроме того, необходимо уточнить методы расчета напряжений, деформаций и скорости деформации испытуемого образца по сигналам, регистрируемым тензодатчиками при испытании SHB. Они основаны на предположении теории одномерных волн напряжений. Две длинные тонкие эластичные стержни в аппарате SHB показаны на рисунке 1, между которыми помещен короткий цилиндрический образец.
Рисунок 1.
Схематическое изображение упругих волн, распространяющихся в аппарате с разрезным стержнем Гопкинсона (SHB) [8].
Когда ударный стержень ударяется о конец падающего стержня, возникает волна сжимающего напряжения, которая немедленно начинает перемещаться по стержню к образцу. Придя к образцу, волна сжимающего напряжения частично отражается обратно к ударной стороне падающего стержня. Остальная часть волны сжимающего напряжения проходит через образец и попадает в передающую планку, что приводит к деформации испытуемого образца [8].При этом акустический импеданс образца должен быть ниже импеданса стержня. Отраженный импульс представляет собой волну растяжения, в то время как прошедший импульс остается в состоянии сжатия. Истории деформации, вызванной волной напряжения, падающего стержня и измерительного стержня регистрируются тензодатчиками A и B, соответственно.
Пока напряжение в двух стержнях остается ниже их пределов упругости, напряжение образца, деформация и скорость деформации могут быть рассчитаны на основе записанных историй деформации падающего стержня и измерительного стержня.Здесь необходимо идентифицировать две важные истории деформации, а именно отраженную волну и прошедшую через образец волна. Кольский [7, 8] применил одномерную теорию волн напряжения для разработки следующего соотношения для расчета инженерного напряжения образца, σS (t):
, в котором E – модуль упругости передающего стержня; A0 – площадь поперечного сечения измерительной шины; AS – площадь поперечного сечения образца перед нагрузкой, а εT (t) – переданная предыстория деформации.
Скорость деформации образца ε′S (t) может быть рассчитана как:
ε′S (t) = dεS (t) dt = −2C0LεR (t) E2, где εR (t) – история отраженной деформации. ; L – длина образца до удара, а C0 – скорость волны в падающем стержне. Отраженная волна представляет собой историю скорости деформации в образце. Таким образом, плоское плато в отраженном сигнале соответствует практически постоянной скорости деформации образца при динамическом нагружении. Скорость волны в падающем стержне, C0, может быть рассчитана на основе теории элементарных колебаний, как показано ниже:
, где E и ρ – модуль упругости и плотность падающего стержня, соответственно.Уравнение (2) может быть интегрировано со временем для получения предыстории инженерных деформаций образца, εS (t), как показано ниже:
εS (t) = – 2C0L∫0tεR (t) E4Таким образом, данные инженерного напряжения образца, деформации и скорость деформации может быть получена из зарегистрированных сигналов тензодатчика в эксперименте SHB.
Однако следует поддерживать равномерную деформацию образца во время эксперимента SHB, чтобы результаты эксперимента могли быть четко задокументированы и интерпретированы для характеристики динамической зависимости напряжения от деформации материала.
Динамическое равновесие напряжений важно для достоверности эксперимента SHB. Напряжение в образце можно выразить через силу, действующую на каждую торцевую поверхность образца. Когда образец зажат между падающим стержнем и стержнем-передатчиком при динамической сжимающей нагрузке, силы F1 (t) и F2 (t) действуют на образец диаметром DS и длиной LS. Среднюю силу Favg, приложенную к образцу, можно представить как:
Принимая во внимание, что среднее инженерное напряжение на испытуемом цилиндрическом образце составляет:
σavg (t) = Favg (t) 14πDS2E6Здесь силы F1 (t ) и F2 (t), нанесенные на торцевые поверхности образца, от падающего стержня и стержня передатчика соответственно.Эти две силы могут быть выражены в терминах упругих деформаций в падающем стержне и стержне передатчика, соответственно, и могут быть рассчитаны на основе падающих, отраженных и прошедших сигналов, как показано ниже:
F1 (t) = E [εI (t) + εR (t)] πDbar24E7, в котором Dbar – диаметр падающего стержня (и стержня передатчика), а εI (t), εR (t) и εT (t) – истории деформации падающей, отраженной и прошедшей волн, соответственно. Для образца при высокоскоростном нагружении равновесие динамических напряжений должно соблюдаться при постоянной скорости деформации, что означает, что F1 (t) должен быть равен F2 (t), как показано ниже:
Однако в реальном эксперименте SHB , между этими двумя историями силы существует отклонение.Для анализа и количественной оценки отклонения используется критерий равновесия напряжений для сравнения сил (или напряжений), действующих на торцевые поверхности образца. Равичандран и Субхаш [19] ввели параметр R (t) для оценки близости к равновесию напряжений в образце, как показано ниже:
R (t) = | Δσ (t) σavg (t) | = | ΔF (t ) Favg (t) | = 2 | F1 (t) −F2 (t) F1 (t) + F2 (t) | E10, в котором Δσ (t) и ΔF (t) – разности этих двух напряжений и силы, действующие на торцевые поверхности образца соответственно.σavg (t) и Favg (t) представляют собой средние значения этих двух напряжений и сил соответственно (см. уравнения (5) и (6)). Предполагается, что образец находится в состоянии равновесия динамических напряжений, когда значение R (t) меньше 0,05 [8]. Этот общий критерий широко используется для оценки процесса равновесия динамических напряжений в экспериментах SHB.
Путем замены Ур. (7) и (8) в уравнение. (10) параметр R (t) может быть выражен через соотношение между падающей, отраженной и прошедшей волнами, как показано ниже:
R (t) = 2 | F1 (t) −F2 (t) F1 (t ) + F2 (t) | = 2 | εI (t) + εR (t) −εT (t) εI (t) + εR (t) + εT (t) | E11Для образца, находящегося в состоянии равновесия динамических напряжений, силы, приложенные к торцевым поверхностям образца, могут быть выражены двумя деформациями давления стержня, как выражено в уравнениях.(7) и (8). Таким образом, согласно формуле. Из уравнения (11) можно вывести следующее соотношение:
Следовательно, применяя предположение о положительной бегущей гармонической волне и уравнении движения, выражения для инженерного напряжения образца, деформации и скорости деформации могут быть получены в терминах деформации двух стержней давления, как показано в уравнениях. (1), (4) и (2) соответственно. В свою очередь, при равновесии динамических напряжений уравнения. (1), (4) и (2) подходят для использования для расчета инженерного напряжения, деформации и скорости деформации образца.
Поэтому была внедрена технология SHB для экспериментов по динамическому сжатию и растяжению. Это зрелый метод и широко используемый прибор для точного определения динамических механических свойств различных материалов при скоростях деформации от 1000 до 10 000 / с [20].
В этой главе, чтобы охарактеризовать механическую реакцию полимерных материалов с высокой скоростью деформации, в качестве экспериментального оборудования выбран метод SHB. С одной стороны, оборудование SHB может точно определять динамические механические свойства материала при высокоскоростной нагрузке.С другой стороны, его можно хорошо контролировать в лабораторных условиях [20].
.Введение в армированные волокном полимеры – полимеры и композиты: концепции, свойства и процессы
Композит – это любой материал, состоящий из более чем одного компонента. Вокруг вас множество композитов. Бетон – это композит. Он сделан из цемента, гравия и песка и часто имеет внутри стальные стержни для усиления. Эти блестящие воздушные шары, которые вы получаете в больнице, когда болеете, сделаны из композита, который состоит из листа полиэстера и листа алюминиевой фольги, сделанных в виде сэндвича.Полимерные композиты, изготовленные из полимеров или из полимеров вместе с другими видами материалов [7]. Но, в частности, композиты, армированные волокном, представляют собой материалы, в которых волокно, изготовленное из одного материала, внедряется в другой материал.
2.2.1. Полимерные композиты
Полимерные композиты представляют собой любую из комбинаций или композиций, которые содержат два или более материала в виде отдельных фаз, по крайней мере, один из которых является полимером. Комбинируя полимер с другим материалом, таким как стекло, углерод или другой полимер, часто можно получить уникальные комбинации или уровни свойств.Типичные примеры синтетических полимерных композитов включают армированные стекловолокном, углеродом или полимерным волокном, термопластичные или термореактивные смолы, армированный углеродом каучук, полимерные смеси, смолы, армированные диоксидом кремния или слюды, и бетон, связанный или пропитанный полимером, или дерево. Также часто полезно рассматривать в качестве композитов такие материалы, как покрытия (комбинации пигмент-связующее) и кристаллические полимеры (кристаллиты в полимерной матрице). Типичные природные композиты включают древесину (целлюлозные волокна, связанные с лигнином) и кости (минералы, связанные с коллагеном).С другой стороны, полимерные композиции, составленные с пластификатором или очень низкими пропорциями пигментов или технологических добавок, обычно не рассматриваются как композиты.
Обычно цель состоит в том, чтобы улучшить прочность, жесткость или ударную вязкость или стабильность размеров за счет включения частиц или волокон в матрицу или связующую фазу. Вторая цель – использовать недорогие, легко доступные наполнители, чтобы увеличить количество более дорогой или дефицитной смолы; эта цель становится все более важной, поскольку поставки нефти становятся более дорогостоящими и менее надежными.Другие области применения включают использование некоторых наполнителей, таких как стеклянные шарики, для улучшения обрабатываемости, включение частиц сухой смазки, таких как сульфид молибдена, для изготовления самосмазывающегося подшипника и использование наполнителей для снижения проницаемости.
Наиболее распространенные полимерные композиты, армированные волокном, состоят из стекловолокна, ткани, мата или ровинга, залитых в матрицу из эпоксидной или полиэфирной смолы. Армированные термореактивные смолы, содержащие бор, полиарамиды и особенно углеродные волокна, придают особенно высокие уровни прочности и жесткости.Композиты из углеродного волокна имеют относительную жесткость в пять раз больше, чем сталь. Благодаря этим превосходным свойствам эпоксидные и полиэфирные композиты подходят для многих областей применения, таких как компоненты в новых реактивных самолетах, детали для автомобилей, корпуса лодок, корпуса ракетных двигателей и сосуды для химических реакций.
Хотя наиболее впечатляющие свойства проявляются у армированных термореактивных смол, таких как эпоксидные и полиэфирные смолы, значительные улучшения могут быть достигнуты и с многими армированными термопластическими смолами.Поликарбонаты, полиэтилен и полиэфиры входят в число смол, доступных в виде армированных стекловолокном композиций. Комбинация недорогого, одноэтапного производства методом литья под давлением с улучшенными свойствами сделало возможным использование армированных термопластов для замены металлов во многих областях применения в бытовых приборах, инструментах, автомобилях и инструментах.
При разработке других композитных систем возможны различные матрицы; например, полиимидные смолы являются отличными матрицами для стекловолокна и образуют композит с высокими эксплуатационными характеристиками.Потенциальный интерес представляют различные волокна, включая полимеры [такие как поливиниловый спирт], монокристаллические керамические нитевидные кристаллы (такие как сапфир) и различные металлические волокна.
Давным-давно люди, живущие в Южной и Центральной Америке, использовали латекс натурального каучука, полиизопрен для изготовления таких вещей, как перчатки и ботинки, а также резиновые мячи, которые они использовали для игр, которые очень напоминали современный баскетбол. Он взял два слоя хлопчатобумажной ткани и вложил их в натуральный каучук, также известный как полиизопрен, в результате чего получился трехслойный сэндвич, подобный тому, который вы видите справа (помните, хлопок состоит из натурального полимера, называемого целлюлозой).Из этого получились хорошие плащи, потому что, в то время как резина делала их водонепроницаемыми, слои хлопка делали их удобными для ношения, чтобы сделать материал, обладающий свойствами обоих компонентов. В этом случае мы сочетаем водостойкость полиизопрена и комфорт хлопка.
Современные композиты обычно состоят из двух компонентов: волокна и матрицы. Волокно – чаще всего стекло, но иногда кевлар, углеродное волокно или полиэтилен. Матрица обычно представляет собой термореактивный материал, такой как эпоксидная смола, полидициклопентадиен или полиимид.Волокно заделано в матрицу, чтобы сделать матрицу более прочной. У композитов, армированных волокном, есть два преимущества. Они прочные и легкие. Часто они прочнее стали, но весят намного меньше. Это означает, что композиты можно использовать для облегчения автомобилей и, следовательно, более экономичного расхода топлива.
Распространенным армированным волокном композитом является Fiberglas TM . Его матрица состоит из реакции полиэфира с двойными углерод-углеродными связями в его основной цепи и стирола.Поливаем смесью стирола и полиэстера массу из стекловолокна.
Стирол и двойные связи в полиэфире реагируют путем свободнорадикальной винильной полимеризации с образованием сшитой смолы. Стекловолокно застревает внутри, где действует как усиление. В Fiberglas TM волокна не выстраиваются в определенном направлении. Это просто запутанная масса, как вы видите справа. Но мы можем сделать композит более прочным, выровняв все волокна в одном направлении.Ориентированные волокна делают с композитом некоторые странные вещи. Когда вы натягиваете композит в направлении волокон, композит становится очень прочным. Но если вы потянете его под прямым углом к направлению волокна, он совсем не будет прочным [8-9]. Это не всегда плохо, потому что иногда нам нужно, чтобы композит был прочным только в одном направлении. Иногда изделие, которое вы делаете, будет испытывать нагрузку только в одном направлении. Но иногда нам нужна сила более чем в одном направлении. Поэтому мы просто направляем волокна более чем в одном направлении.Мы часто делаем это, используя тканую ткань из волокон для усиления композита. Тканые волокна придают композиту хорошую прочность во многих направлениях.
Полимерная матрица скрепляет волокна. Рыхлый пучок волокон не принесет особой пользы. Кроме того, хотя волокна прочные, они могут быть хрупкими. Матрица может поглощать энергию, деформируясь под нагрузкой. То есть матрица добавляет композиту прочности. И, наконец, хотя волокна обладают хорошей прочностью на разрыв (то есть они прочные, когда вы их тянете), они обычно обладают ужасной прочностью на сжатие.То есть они прогибаются, когда вы их раздавливаете. Матрица придает композиту прочность на сжатие.
Не все волокна одинаковы. Сейчас может показаться странным, что стекло используется в качестве арматуры, ведь стекло действительно легко разбить. Но по какой-то причине, когда стекло превращается в крошечные волокна, оно действует совсем иначе. Стекловолокно прочное и гибкое.
Тем не менее, существуют более прочные волокна. Это хорошо, потому что иногда стекло оказывается недостаточно прочным и жестким.Для некоторых вещей, например деталей самолетов, которые подвергаются сильной нагрузке, вам нужно разорвать причудливые волокна. Когда стоимость не имеет значения, вы можете использовать более прочные, но более дорогие волокна, такие как Kevlar TM , углеродное волокно. Углеродное волокно (Spectra TM ) обычно прочнее, чем Kevlar TM , то есть может выдерживать большее усилие, не ломаясь. Но Kevlar TM имеет тенденцию быть жестче. Это означает, что он может поглощать больше энергии, не ломаясь. Он может немного растягиваться, чтобы не сломаться, больше, чем углеродное волокно.Но Spectra TM , который представляет собой разновидность полиэтилена, прочнее и жестче, чем углеродное волокно и Kevlar TM .
Для разных работ требуются разные матрицы. Ненасыщенные системы полиэфир / стирол являются одним из примеров. Они подходят для повседневного использования. Кузова Chevrolet Corvette изготавливаются из композитных материалов с использованием ненасыщенных полиэфирных матриц и стекловолокна. Но у них есть недостатки. После затвердевания они сильно усадятся, очень легко впитывают воду, а их ударная вязкость низкая.
2.2.2. Биокомпозиты
В течение многих десятилетий в сфере жилищного строительства древесина использовалась в качестве основного строительного материала для каркасов современных американских домов. Американская лесная промышленность произвела рекордные 49,5 миллиардов досковых футов пиломатериалов в 1999 году и еще 48,0 миллиардов дощатых футов в 2002 году. В то время как производство пиломатериалов находится на пике, доля домовладельцев достигла рекордного уровня 69,2%, с более чем 977 000 дома были проданы в 2002 году. Поскольку на жилищное строительство приходится одна треть от общего объема использования пиломатериалов хвойных пород в Соединенных Штатах, существует растущий спрос на альтернативные материалы.Использование опилок не только является альтернативой, но и повышает эффективность использования побочных продуктов. Древесно-пластиковые композиты (ДПК) – это относительно новая категория материалов, охватывающая широкий спектр композиционных материалов, в которых используются связующее на основе органических смол (матрица) и наполнители, состоящие из целлюлозных материалов. Новые и быстро развивающиеся биокомпозитные материалы представляют собой высокотехнологичные продукты, обладающие одним уникальным преимуществом – древесный наполнитель может включать в себя опилки и древесные отходы. Следовательно, для производства биокомпозитов не требуются дополнительные древесные ресурсы.Отходы, которые традиционно требуют денег за правильную утилизацию, теперь становятся полезным ресурсом, позволяя переработке быть как прибыльной, так и экологически безопасной. Использование биокомпозитов и WPC быстро увеличивалось во всем мире, и конечные пользователи этих композитов в строительстве, автомобилестроении и мебельной промышленности. Одной из основных проблем, связанных с использованием биокомпозитов, является воспламеняемость двух основных компонентов (связующего и наполнителя). Если бы был добавлен антипирен, это потребовало бы, чтобы адгезия волокна и матрицы не нарушалась антипиреном.Задача состоит в том, чтобы разработать композит, который не будет гореть и сохранит свои механические характеристики. Вместо органических матричных соединений можно использовать неорганические матрицы для повышения огнестойкости. Древесные композиты на неорганической основе состоят из минеральной смеси в качестве связующей системы. Такие неорганические связующие системы включают гипс и портландцемент, оба из которых обладают высокой устойчивостью к огню и насекомым. Основным недостатком этих систем является то, что максимальное количество опилок или волокон, которое может быть добавлено, невелико.Одним относительно новым типом неорганической матрицы является алюмосиликат калия, экологически чистое соединение, изготовленное из природных материалов. Федеральное управление гражданской авиации изучило возможность использования этой матрицы в коммерческих самолетах из-за ее способности выдерживать температуры до 1000 ºC без образования дыма, а также способности углеродных композитов выдерживать температуры 800 ºC и поддерживать 63% своей исходная прочность на изгиб. Матрицы из алюмосиликата калия совместимы со многими распространенными строительными материалами, включая глиняный кирпич, кладку, бетон, сталь, титан, бальзу, дуб, сосну и ДСП [10].
.