Полировка плоских поверхностей многоступенчатая: Ионная полировка оптических деталей ионным лучом
alexxlab | 17.06.2023 | 0 | Разное
Ионная полировка оптических деталей ионным лучом
Ионная полировка оптических деталей
Компания ВАКТАЙМ проектирует и изготавливает установки ионного лучевого полирования и ионного плазменного травления для обработки поверхностной высокоточной оптики различных диаметров и форм оптического стекла.
Ионная полировка оптических деталей линз, плоских оптических деталей предназначена для точной нано-метровой коррекции оптической поверхности детали. Наши установки для ионного лучевого полирования разработаны специально для улучшения оптических компонентов в кратчайшие сроки. Исправление ошибок после механической полировки оптических деталей, коррекция шероховатости поверхности оптических компонентов, асферизации поверхности и многое другое позволяют выполнять машины для ионной лучевой полировки.
В модельном ряду насчитывается более десятка машин по полировки оптических деталей ионным пучком. Новая технология обработки поверхности и ионная полировка оптических деталей получила широкое распространение в мире в начале 90 годов.
Самая маленькая машина для пилотного производства и ионной полировки, настольного типа позволяет обрабатывать оптические компоненты от 5 мм до менее 1 мм в диаметре с прецизионной точностью до 1 нанометра. Недавно разработанный ионный источник может использовать ионный луч с переменным диаметром около 50-300 мкм как для коррекции и изменения формы поверхности, так и для полировки ионным лучом.
Ионная полировка или шлифовка ионным пучком позволяет добиться невероятных характеристик рабочих поверхностей линз и зеркал. С ее помощью можно получать асферические поверхности с высочайшей точностью формы, при этом шероховатость оптических компонентов при этом снижается до 1 нанометров.
Преимущества ионно-лучевой технологии и метода ионной полировки:
- Высокая точность обработки поверхности
- Возможность получения ювенильных поверхностей, прецизионное качество обработки
- Возможность формирования лучей ионов как инертных и химически активных газов
- Возможность управления энергией ионов в широких пределах
- Точность и простота контроля процесса обработки ионным пучком;
- Высокая однородность и повторяемость обработки без ошибок.
Применение ионно-лучевых технологий для полировки оптических деталей позволяет повысить качество и выход годных выпускаемых приборов, создать новые оптические приборы, изготовление которых другими методами невозможно.
Применение технологии ионной обработки поверхности ионным лучом имеет широкое распространение в технике: от подготовки образцов в просвечивающей электронной микроскопии до систем ионного утонения для высококачественно подготовки зеркал для астрономических телескопов.
Если Вы хотите узнать больше что такое ионная полировка, ионная лучевая полировка поверхности оптических компонентов, то изучите нашу статью по выбору оборудования для подготовки и полировки поверхности изделий для оптики.
Преимущества ионной полировки в вакууме пучком ионов:
- Бесконтактный процесс – никаких следов на поверхности
- Отсутствие индуцированного напряжения на поверхности
- Можно обрабатывать практически любую геометрию
- Большой спектр обрабатываемых материалов
- Низкие затраты на приобретение, в сравнение с машинами для шлифования оптики
- Не требуется применения абразивных паст при шлифовании
- Почти нет изнашиваемых деталей при шлифовании ионной полировкой
- Качество поверхности < λ / 10 до λ/20 достижимо (в зависимости от требования к качеству и скорости процесса)
- Качество поверхности < λ / 100, шр < 1 нм достижимо на диаметре зеркала 3 метра
Полировка поверхности плазмой в вакууме. Ионная полировка.
Если Вы хотите купить установку для ионной полировки оптических деталей, узнать цену установок ионно-лучевой полировки, обратитесь к специалистам данного направления в компании ВАКТАЙМ. Мы предложим Вам оптимальное решение, разработаем технологию и подскажем с оборудованием для полировки ионным лучом.
Компания ВАКТАЙМ проводит подбор оборудования для: ионная полировка, ионная шлифовка оптических деталей в вакууме ионным пучком. Хотите знать больше что такое Ионная полировка, читайте наше статью про ионная полировка больших астрономических зеркал.
Metallographic Polishing – База знаний
Металлографическое полирование, как и металлографическое шлифование, является заключительным этапом в процессе подготовки образцов металлов для последующего анализа. Его цель – исправить деформации, вызванные предыдущими рабочими операциями (во время вырезки заготовок под образцы и резки).
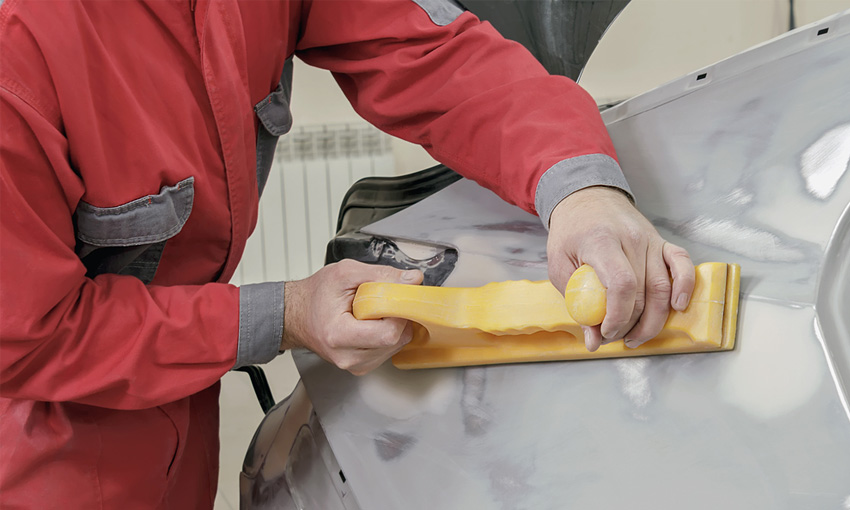
Металлографическая полировка состоит из нескольких этапов, на каждом из которых используется более мелкий абразив, чем на предыдущем. Как правило, делятся на три операции: предварительная полировка, промежуточная полировка и окончательная полировка.
Конечная цель – получить поверхность образца без деформации, царапин и высокой отражающей способности. Для получения точных результатов требуется выбор подходящих расходных материалов, полировальный станок и подходящее руководство по подготовке с индивидуальными настройками инструмента (оптимизированными для соответствующего материала).
QATM – ведущий производитель и поставщик высококачественных расходных материалов для полировки, а также ряда инновационных металлографических полировальных машин, от ручных до полностью автоматизированных моделей. Эксперты по применению QATM объединяют многолетний опыт с тысячами обработанных образцов и будут рады помочь с вашим приложением.
QATM предлагает металлографические шлифовальные / полировальные станки для любых технических требований.
Обзор оборудованияСвяжитесь с нами!
Металлографическая полировка в три этапа
Как правило, отсутствуют действующие правила для металлографического полирования в отношении количества и выбора этапов полирования и градации размеров зерен. Однако существуют предложения по подготовке отдельных материалов или групп материалов, и обычно делается переход между тремя более крупными этапами процесса.
1. Предварительная полировка
Основная цель металлографического предварительного полирования – добиться наилучшего снятия материала в кратчайшие сроки. Хорошая плоскостность шлифовальной поверхности после шлифования может быть сохранена только путем обеспечения того, чтобы алмаз всегда находился в движении, всегда катился, если это возможно. Это раскатывающее движение обеспечивает необходимое удаление излишков материала.
Используемые расходные материалы: алмазы от 15 мкм до 9 мкм / Твердые ткани или ткани с жестким прессованием.
2. Промежуточная полировка
За металлографическим предварительным полированием в большинстве случаев следует металлографическое промежуточное полирование. На этом этапе удаляются деформационные и смазанные слои. Если материал очень твердый, может потребоваться несколько промежуточных этапов полировки.
Используемые расходные материалы: алмаз от 9 мкм до 3 мкм / плотнотканные или слегка ворсовые сукна.
3. Окончательная полировка
Окончательная металлографическая полировка – это последний этап полировки, предназначенный для устранения деформаций и особенно размытия поверхности образца. Этот шаг непростой, но возможный. Однако окончательная полировка не требуется для каждой задачи металлографической полировки.
Используемые расходные материалы: алмаз от 3 мкм до 0,5 мкм / оксидная полировка от 0,1 мкм до 0,06 мкм / ворсистая или флоковая ткань, вспененная для оксидных суспензий
При окончательной металлографической полировке различают чисто механическое удаление алмазной крошкой и химико-механическое удаление, которое достигается с помощью слабощелочных суспензий для окончательной полировки. Когда использовать полирующее средство, нужно определять в каждом конкретном случае.
Металлографическая алмазная полировка
При металлографическом полировании алмазные полировальные средства различаются по форме алмаза. Различают поли- и монокристаллические алмазы.
Полировальные агенты, содержащие поликристаллические алмазы, имеют явные преимущества перед полировальными агентами, содержащими монокристаллические алмазы. Поликристаллический алмаз имеет однородную форму зерна и множество острых краев.
Скорость удаления алмазных полировальных средств зависит от количества и размера алмазных режущих кромок, которые работают одновременно.
Для правильного выбора алмазного полировального или шлифовального абразива (т.е. моно- или поликристаллического) важно заранее определить его требования. В принципе, хороший результат также может быть достигнут с более дешевым монокристаллическим алмазом, хотя для его получения требуется больше усилий.
Алмазные полировальные средства также различаются по типу материала-носителя. Какой из трех распространенных материалов носителя будет выбран, зависит от требований.
Алмазная паста: высокая концентрация на полировальной ткани, всегда необходима дополнительная смазка Алмазная суспензия: обеспечьте хорошее и равномерное распределение на полировальной ткани, обратите внимание на сегрегацию в случае более длительного периода простоя
Алмазный спрей: обеспечивает хорошее и равномерное распределение на полировальной ткани, всегда требуется дополнительная смазка, более высокий расход из-за дозировки
Расходные материалы для металлографического полирования
Металлографическая оксидная полировка
В металлографии оксидные полировальные агенты используются в основном для окончательной полировки.
Различают суспензии диоксида кремния и оксида алюминия. Оба доступны в виде “готовой к употреблению” водной или спиртовой суспензии. Размер зерна составляет от 0,1 до 0,06 мкм.
Не существует строгих правил применения суспензий. Суспензии на спиртовой основе следует использовать для образцов, подверженных коррозии.
Диоксид кремния: все аустенитные стали, алюминиевые сплавы, титановые сплавы, сплавы драгоценных металлов.
Оксид алюминия: латунь, от низколегированной до нелегированной стали, марки серого чугуна.
С использованием оксидных полирующих агентов может быть достигнуто механическое или химико-механическое удаление, при котором удаляются пятна и слои деформации, которые могут еще присутствовать от предыдущей металлографической полировки; качество этого процесса варьируется от хорошего до очень хорошего.
«Двойное» воздействие также приводит к сокращению времени полировки. Еще одно преимущество перед алмазными добавками – значительно более низкие материальные затраты.
Расходные материалы для металлографического полирования
Салфетки и диски для металлографической полировки
Сукно для металлографической полировки доступно с различной структурой поверхности или из различных материалов (например, шелк, искусственный шелк, шерстяные ткани, флокированные и вспененные пластмассы). Также доступны специально разработанные полировальные диски с интегрированными алмазами.
Металлографическая предварительная полировка обычно проводится на менее эластичных (твердых) тканях с использованием смазки (низкая ударная эластичность важна для сохранения остроты кромок). Если края закруглены слишком мягкой тканью, это отрицательно сказывается на оценке тонких слоев.
При окончательной полировке используйте более эластичное сукно с длинным ворсом и смазочные материалы с более высокой вязкостью.
Эластичность сукна для промежуточной полировки находится между двумя только что описанными крайностями.
Расходные материалы для металлографического полирования
Металлографическая вибрационная полировка
Металлографическое вибрационное полирование позволяет проводить подготовку почти без деформации и царапин на материалах, склонных к деформации. Этот метод также особенно подходит для образцов для анализа EBSD.
При металлографическом вибрационном полировании относительное движение между образцом и полирующей основой, необходимое для удаления остатков образца, достигается за счет вибрирующей рабочей поверхности. Рабочая поверхность подвергается вертикальным колебаниям, на которые накладываются вращательные колебания. Эти комбинированные колебания заставляют образцы, утяжеляемые грузом, двигаться по кругу на рабочем колесе.
Металлографический вибрационный полировщик QPol Vibro автоматически находит наилучшую частоту движения образца по полировальной ткани в зависимости от перемещаемой массы. Благодаря очень щадящему съему материала этот метод особенно подходит для очень мягких и пластичных материалов, таких как медь или медные сплавы, алюминий и алюминиевые сплавы, материалы на основе Ni, а также мягкие стали. Однако такое бережное и, следовательно, очень низкое удаление материала приводит к увеличению времени полировки, иногда значительно превышающему 30 минут.
Вибрационная полировальная машина Qpol Vibro
Советы и рекомендации по металлографическому шлифованию и полировке
Шлифовка и полировка – стандартные методы металлографической подготовки образцов. Опытные знания в области обработки доступны практически для всех материалов. Однако при поиске надлежащей процедуры необходимо учитывать ряд потенциальных источников ошибок. Процедура занимает очень много времени из-за многоступенчатого рабочего процесса, особенно при ручной обработке. С другой стороны, следует ожидать более крупных инвестиций, если требуется более высокая степень автоматизации.
В каждом отдельном случае необходимо оценивать следующие риски:
- Использование абразивных материалов для металлографической полировки может привести к появлению царапин на поверхности образца, особенно если материал содержит фазы с разными значениями твердости. Этого нельзя исключать в случае композитных материалов.
- Края и поверхность кристалла могут быть скруглены.
- Охлаждающие и смазочные жидкости не должны вступать в реакцию с материалом, так как органические материалы, такие как бумага или волокна, могут разбухать. Если охлаждающая способность недостаточна, материалы образцов подвергаются термической деградации и / или изменениям микроструктуры.
Рынок шлифовального и полировального оборудования очень разнообразен и предлагает подходящие решения для самых разных областей применения. В зависимости от области применения и производительности доступны простые полуавтоматические или полностью автоматические системы шлифовки и полировки. Широкий спектр применения также говорит сам за себя. Тщательно подобранные расходные материалы для шлифовки и полировки в сочетании с подходящими параметрами подготовки позволяют достичь превосходных результатов практически для всех материалов. Механическое шлифование и полировка часто являются единственными методами подготовки, подходящими для керамики, композитных материалов и наполненных / армированных пластиков.
Чтобы помочь пользователю, ниже приведены несколько советов и приемов по шлифовке и полировке.
1. Динамика металлографического полирования и шлифования
Расположение держателя образца по отношению к рабочему диску является особенно важным моментом при полуавтоматической и полностью автоматической металлографической подготовке образцов. Расположение держателя образца, скорость вращения, направление вращения и контактное давление являются важными факторами для долговечности расходных материалов и качества получаемой поверхности.
Если держатель образца расположен слишком близко к центру, результатом будет наиболее неблагоприятная динамика шлифования и полировки (рисунок 1).
Расположение, показанное на рисунке 2, идеально подходит для металлографической подготовки образцов во время шлифовки и полировки. Держатель образца должен немного выступать за край рабочего диска, примерно на 5-10 мм. Тогда образцы по-прежнему перемещаются по полировальной ткани!
2.

В металлографии так называемый “хвост кометы” обычно встречается с неметаллическими включениями, порами и твердыми фазами в мягкой основной матрице, если срез удерживается только в одном направлении шлифовки или полировки во время ручной подготовки. Этот артефакт характерен для больших образцов материала. Для оптимальной металлографической подготовки образцов их следует перемещать таким образом, чтобы избежать образование направленной ориентации.
3. Эффект карандаша
В металлографической полировке «эффект карандаша» – широко распространенный артефакт, образующийся во время подготовки вручную или при однократном нажатии. Поверхность образца сужается к центру, что хорошо видно текстуру на шлифовальной поверхности. Эта проблема возникает при подготовке образцов с однократным давлением.
Причины могут быть:
- Держатель образца с чрезмерно большим отверстием, т.е. у образца слишком большой зазор
- Выбран неправильный диаметр, например, диаметр образца 38 мм (1 ½ дюйма) и держатель образца 40 мм
- Форма образца не адаптирована (слишком высокая, поэтому образец наклоняется вперед и назад)
- Контактное давление слишком низкое, образец начинает неравномерно наклоняться
- Несоблюдение параметров динамики шлифования и полировки
- Образец не цилиндрический (заливочная форма для установки корпуса овальная)
4.

Абразивы и другие полирующие агенты для металлографии, такие как частицы карбида кремния из шлифовальной бумаги, алмазы из алмазных полировальных агентов или оксиды из оксидных конечных полирующих агентов, могут вдавливаться в поверхность во время подготовки металлографических образцов. Это может произойти в следующих ситуациях:
- При сухом металлографическом шлифовании композиционных материалов, состоящих из очень твердых и очень мягких материалов
- В случае чрезмерно высокого давления шлифования или полировки при получении очень мягких материалов и / или композиционных материалов с компонентами мягкой и твердой фаз
- В случае чрезмерно высокой концентрации абразива в сочетании со слишком высоким давлением
- Неправильный подбор крупности шлифовально-полировального средства.
- Когда смазочная пленка разрушается во время полировки. Если добавить слишком мало смазки, образцы могут значительно нагреться
- При использовании смазки с очень низкой вязкостью
- Если выбрана неправильная шлифовальная тарелка или полировальная ткань (слишком жесткая или слишком мягкая), обратите внимание на ударопрочность
- В случае слишком одностороннего движения образца
5.
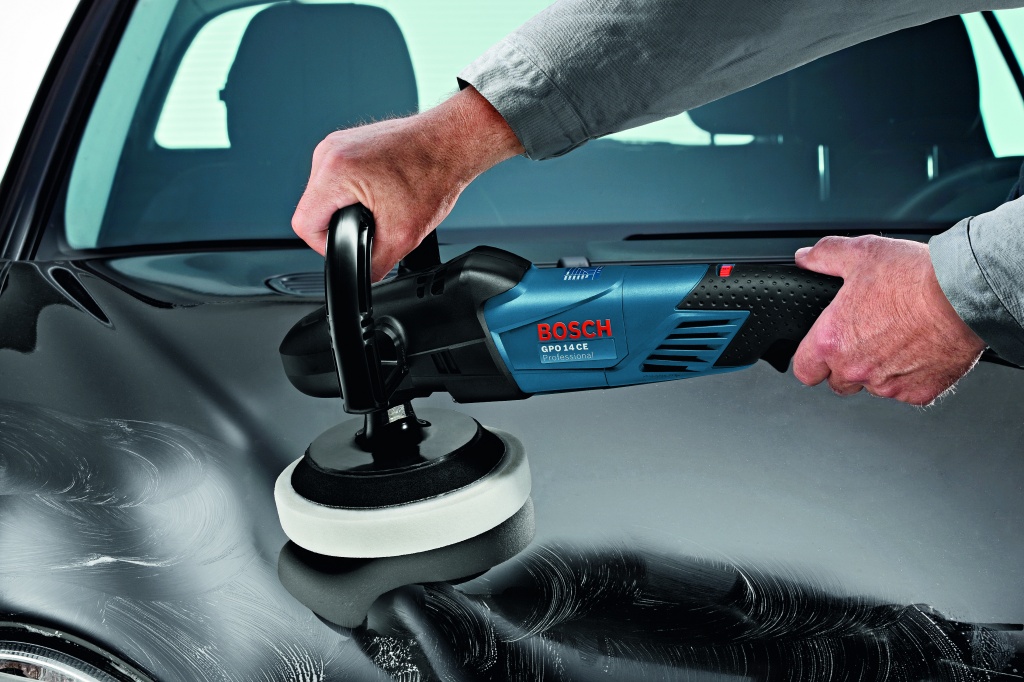
Направление шлифования также может влиять на качество результата металлографической подготовки: при этой ручной подготовке образец слева удерживался на бумаге SiC таким образом, что направление шлифования абразивного зерна велось от стальной части образца (без покрытия) к урочненному материал. Таким образом, хрупкий азотированный слой вдавливается в мельчайшие зазоры между образцом и запрессованной смолой, что приводит к трещинам.
Проблема была решена вращением образца. Нужно было притереть заливочный материал к образцу. Результат (образец справа) не был полностью отполирован, чтобы проблема и решение были четко видны.
DIN 30902: 2016-12 (Термическая обработка черных металлов – Определение под световым микроскопом толщины и пористости композитного слоя азотированных и нитроцементованных деталей) рекомендует обернуть образец алюминиевой или медной фольгой перед запрессовкой, чтобы защитить слой сплава во время запрессовки.
Здесь такой образец показан на первом изображении слева, справа для сравнения развернутый образец. Затем оба образца были установлены в пришлифованное соединение для обеспечения идентичной металлографической подготовки (второе изображение).
Результаты металлографической пробоподготовки показывают, что слой химических соединений на левом изображении имеет неравномерную толщину и имеет сильные сколы. С другой стороны, составной слой на правом изображении однороден и не имеет трещин, поэтому его можно надежно измерить. Важно убедиться, что более толстый белый слой над фактическим клеевым слоем не измеряется, это алюминиевая фольга.
QATM Продукты & Контакты
QATM предлагает широкий спектр инновационных станков для металлографического полирования, от ручных полировальных машин до полностью автоматизированных систем. Прилагаемые расходные материалы для полировки QATM тщательно проверяются и выбираются для идеальной совместимости с нашими станками. Свяжитесь с нами, чтобы получить консультацию, расценки или поговорить с одним из наших специалистов!
Все, что вам нужно знать о полировке. Отделка поверхности
Полировка — это не только наука, но и искусство. Этот метод отделки поверхности металла является одним из лучших способов создания деталей с эстетической привлекательностью. Эти детали не только отлично выглядят, но и работают лучше и служат дольше благодаря полированной поверхности. Металлические поверхности часто имеют тенденцию тускнеть со временем. Обычно это происходит из-за контакта с разлагающими элементами, такими как кислород в воздухе. Контакт с высокой температурой и уровнями износа также имеет тенденцию повреждать поверхности этих металлов.
Однако полированная металлическая деталь защищена от загрязнения и окисления. Он также создает отражающую поверхность, предотвращая коррозию и поддерживая поверхность в отличном состоянии. Полировка поверхности отлично работает с широким спектром металлов, используемых в индивидуальном производстве. В этой статье вы узнаете о различных процессах полировки на производстве. Мы рассмотрим различные преимущества этих процессов и их многочисленные применения. Кроме того, вы узнаете некоторые важные советы, необходимые для адекватного процесса полировки.
Как правило, полировка подразумевает использование абразивного материала для финишной обработки металлической поверхности. Он направлен на удаление царапин и зазубрин с готовых обработанных деталей, улучшая их блеск и блеск. В результате шлифовки полированной поверхности мы получаем зеркально-блестящее покрытие.
Как упоминалось ранее, процесс полировки отлично подходит для широкого спектра металлических материалов. Тип металла, который вам нужно отполировать, определит процесс полировки металла. Например, для твердых металлов больше подходит автоматическая или роботизированная полировка, а для более мягких металлов может потребоваться ручная полировка и полировка.
Как правило, процесс полировки на производстве состоит из следующих этапов:
Этап №1: Черновая обработкаПроцесс обработки с ЧПУ может включать сварку и соединение, в результате чего на поверхности металла остаются царапины и дефекты. Поэтому возникает необходимость в шероховатости поверхности, чтобы устранить такие дефекты. Этот процесс может быть выборочно выполнен на определенных частях компонента. Рото-орбитальная шлифовальная машина также может помочь придать шероховатость всей поверхности детали. Для шлифования небольших участков могут потребоваться абразивы диаметром около 32 мм с зернистостью от 1500 до 3000. С другой стороны, абразивные диски диаметром 150 мм и зернистостью 1200 или 1500 больше подходят для больших поверхностей.
Этап №2: Полировка По завершении этапа черновой обработки быстрорежущая абразивная паста помогает очистить пораженный участок или всю поверхность детали. Таким образом, в процессе полировки поверхности используются шерстяные береты и полировальные губки, которые помогают распределить абразивную пасту. Губки и береты бывают разной степени жесткости. Таким образом, мы можем добиться различной степени полировки поверхности для прототипов и нестандартных деталей. После процесса полировки салфетка из микрофибры может помочь в эффективной очистке поверхности.
После полировки на поверхности часто остаются нюансы. Таким образом, жизненно важно осветлить поверхность, чтобы восстановить ее первоначальный или даже лучший внешний вид. Процесс осветления также обеспечивает однородность отделки всего компонента.
Шаг № 4: ЗащитаКонечной целью большинства процессов отделки является получение более долговечного и прочного компонента. Поэтому важно защитить окончательную отделку после осветления. Большинство производителей достигают этого, нанося слой защитного воска, что делает окончательную полированную поверхность еще более прочной.
Различные типы полировки поверхности, их плюсы и минусы Существует несколько методов полировки поверхностей нестандартных деталей. Каждый из этих методов имеет свои преимущества и недостатки. Следовательно, ваш выбор метода будет зависеть от нескольких факторов, включая предполагаемое применение продукта, общую стоимость и многие другие. Мы расскажем об этом в последних разделах этого руководства. Давайте рассмотрим доступные методы надежной полировки поверхности.
Этот метод полировки основан на пластической деформации или резке поверхности материала. Затем он получает гладкую поверхность путем удаления полированных выпуклостей. Как правило, материалы, используемые при механической полировке, включают наждачную бумагу, плоские круги, абразивный брусок и т. д. Эти материалы в основном подходят для ручных операций. Однако вспомогательные инструменты, такие как сверхточная полировка и поворотные столы, используются для поверхностей, требующих высококачественной отделки.
Ультраточная полировка заключается в использовании специальных абразивных инструментов и прижатии их к поверхности обрабатываемой детали. Весь процесс происходит при высокоскоростном вращении в полировальной жидкости, содержащей абразивы. Эта технология помогает достичь шероховатости поверхности около 0,008 мкм, что является одним из лучших показателей, которые можно получить для процесса полировки. Этот метод подходит для изготовления форм для оптических линз для литья под давлением.
- Высокая яркость
- Улучшенная поверхностная отделка
- Лучшая чистка поверхности
- Более высокая эстетическая привлекательность
- Пониженная адгезия продукта
- Высокая интенсивность рабочей прослужит долго
- Может подвергаться коррозии
Этот тип полировки поверхности включает предпочтительное растворение выступающей части поверхности материала в химической среде. Цель состоит в том, чтобы получить гладкую поверхность в конце процесса. В процессе химической полировки химический раствор и гальванические пары воздействуют на поверхность металла. Следовательно, происходит образование пассивирующих слоев.
Как правило, химическая полировка имеет прямой результат в сглаживании и полировке микрошероховатостей. Это также приводит к параллельному растворению верхнего слоя детали.
Pros- Workpieces with complex shapes can be polished
- Can work on several parts at the same time
- Less equipment investment
- High efficiency
- Good corrosion resistance
- Это приводит к неоднородной белизне
- Трудно нагревать
- Процесс может выделять вредные материалы
- Трудно регулировать и регенерировать полировальные растворы

Однако, по сравнению с химической полировкой, при электролитической полировке эффект катодной реакции отсутствует. Также эффект полировки в этом случае намного лучше. Этот процесс полировки удаляет излишки материала с металлического компонента. Таким образом, он выравнивает впадины и микровыступы на детали, уменьшает шероховатость поверхности и улучшает ее качество.
Pros- Блеск держится дольше
- Одинаковая внутренняя и внешняя окраска
- Это может помочь с обширным диапазоном MAT
- Низкая стоимость, короткий цикл
- поощряет минимальное загрязнение
- Высокая коррозионная стойкость
- Высокие инвестиции в оборудование
- .
Инструменты и вспомогательные электроды, необходимые для сложных деталей
Электрополировка или электролитическая полировка имеет явное преимущество перед механической полировкой при быстром прототипировании. Он создает гладкую, блестящую, устойчивую к коррозии и износу поверхность на изготовленной по индивидуальному заказу детали.
Другие преимущества электрополировки по сравнению с механической полировкой включают следующее:
- Она уменьшает площадь поверхности материала до микроскопического уровня. Результатом этого является общее снижение адгезии продукта и накопление загрязнения. Кроме того, это позволяет более эффективно очищать готовый продукт.
- Ускоряет удаление заусенцев с материалов. Неотъемлемой характеристикой процесса электрополировки является то, что он имеет большую плотность тока в высоких точках и меньшую плотность в низких точках.
Таким образом, более высокая плотность в верхних точках обеспечивает более быстрое удаление заусенцев. Таким образом, в итоге мы имеем гладкую чистую поверхность.
- Улучшает внешний вид обрабатываемой детали. Надлежащий процесс электрополировки сглаживает и очищает микроскопические поверхности. Полированный металл (в процессе электрополировки) имеет блестящий вид. В этом случае все оставшиеся несовершенства увеличиваются, и визуальный осмотр становится более осуществимым.
Одним из существенных преимуществ полированной поверхности является ее гладкость. То есть нет шансов для залегания грязи или микробов. Следовательно, это позволяет легко очищать деталь до состояния стерильности. Кроме того, эти части, как правило, остаются чистыми.
Более того, полированный металл может адекватно отражать свет. Все это в совокупности предлагает широкий спектр применения процесса полировки в производстве. Таким образом, в таких отраслях, как медицина, аэрокосмическая и электротехническая промышленность, используется полировка нескольких металлических деталей. Применение деталей с полированными поверхностями включает, но не ограничивается следующим:
- Производство медицинского оборудования
- Отражатели и зеркала (например, концентраторы солнечной энергии, безопасные зеркала и т. д.)
- Бампер для пожарных машин
- Крепеж для морского применения
- Пружины и проволочные трещины
Отделка поверхности
Наука об услугах по отделке развивалась с годами, и появилось несколько различных приложений. Полировка имеет свои преимущества и недостатки при быстром прототипировании и мелкосерийном производстве.
Вот некоторые из них:
Плюсы полировки поверхности- Улучшает очищаемость металлической детали
- Повышает устойчивость деталей к коррозии адгезионные свойства детали
- Удаляет румяна с металлической поверхности
- Механически полированные детали могут быть непригодны для применения в условиях высокой чистоты
- Используемые абразивы и другие составы могут оставаться в материале
- Это может быть трудоемким
Конечной целью каждого процесса создания прототипа или мелкосерийного производства является обеспечение конечного результата. продукция соответствует требованиям качества. Отделка поверхности является одним из наиболее важных процессов постпроизводства, обеспечивающим соответствие продукции требуемым стандартам. Мы в RapidDirect понимаем это и готовы воплотить ваше желание прототипирования в реальность.
В RapidDirect у нас есть не только лучшие техники и производственные технологии, но и первоклассная отделка, включая полировку поверхности. Мы работаем с вами, чтобы помочь вам сделать правильный выбор для обрабатываемой детали. Лучшая новость заключается в том, что все наши услуги предоставляются по конкурентоспособным ценам. Загрузите свой файл дизайна сегодня, чтобы получить мгновенную цитату.
Попробуйте RapidDirect прямо сейчас!
Вся информация и загрузки защищены и конфиденциальны.
Лучшие насадки для полировки поверхности изготовленных на заказ деталейНиже приведены советы экспертов, которые помогут обеспечить эффективность процесса полировки:
- Для черновой обработки используйте абразивные диски с полиэфирной пленкой.
Это обеспечит создание соответствующих степеней шероховатости с большей однородностью.
- Не полируйте металлические детали в одном направлении. То есть поможет, если вы будете постоянно менять направления полировки. Это рекомендуется для обеспечения равномерности полировки материалов неравномерной формы и размера.
- Используйте полировальную пасту очень экономно. Добавление слишком большого количества полировального состава на полировальный круг приведет к образованию жирных пятен на заготовке.
- Абразивный материал должен быть в идеальном состоянии. То есть он не должен быть ни слишком твердым, ни слишком жидким.
- Для полировальных машин часто подходит низкая рабочая скорость около 900 об/мин.
- Избегайте перегрева поверхности и используйте быстрорежущие пасты.
- Удалите следы смазки на компоненте сухой мягкой тканью из микрофибры
- Нанесите немного полировальной пасты, но как можно чаще.
- По возможности рекомендуется полировать поперек царапин или следов, а не вдоль них.
- Удалите любой лак с поверхности металлического компонента, если он есть, перед полировкой
- Всегда не забывайте надевать подходящее защитное снаряжение. Процесс полировки поверхности может быть довольно опасным, если вы не защищены.
- Для каждого цвета полировальной пасты должен быть свой уникальный полировальный круг. Не смешивайте полировальные составы с разными свойствами на одном и том же полировальном круге.
- Если вам необходимо использовать разные полировальные пасты с одним полировальным кругом, вы можете удалить остатки пасты, прижав проволочную щетку к вращающемуся кругу.
- Закрепление сверла в тисках поможет вам полировать небольшие предметы более эффективно и легко.
- Используйте хороший восковой полироль для защиты уже отполированного металла.
Какова основная цель процесса полировки? 9№ 0008
Полировка помогает создать блестящую и гладкую поверхность изготовленных на заказ деталей. Это помогает улучшить внешний вид деталей, предотвращая коррозию (удаляя окисление), улучшая очищаемость и уменьшая адгезию деталей. Полировка поверхности также оставляет чистую поверхность материала со значительными отражающими свойствами. Все это направлено на то, чтобы детали соответствовали ожиданиям клиентов.
Что такое полировальные составы?
Как правило, полировальные составы представляют собой абразивы. Эти абразивы состоят из полирующего порошка, смешанного с жирами и восками, в результате чего получается брусок или лепешка. Эти абразивы сглаживают металлические поверхности и помогают наносить чистую полированную отделку.
В чем разница между полировкой и полировкой?
Полировка и полировка — два наиболее распространенных процесса отделки в обрабатывающей промышленности. Оба метода отделки поверхности включают в себя сглаживание поверхностей компонентов для улучшения их физических свойств и эстетики. Однако полировка предполагает использование абразивов, прикрепленных к полировальному кругу. С другой стороны, полировка не предполагает приклеивания абразивов на основе зерен к кругу. Это позволяет легко и быстро снимать/заменять абразив с круга.
Полировка поверхности придает блеск поверхности ваших изделий. Это улучшает качество и производительность таких продуктов различными способами. В этой статье мы обсудили различные области применения полировки, а также ее преимущества. Предоставленные советы также помогут вам получить максимальную отдачу от процесса полировки на производстве. В RapidDirect мы всегда готовы предложить вам лучшие услуги по полировке ваших нестандартных деталей. Благодаря нашему опыту ваша продукция будет соответствовать точным спецификациям. Свяжитесь с нами сегодня, и давайте приступим к работе.
Конструирование химико-механической полировки. (Книга) | ОСТИ.ГОВ
- Полная запись
- Другие сопутствующие исследования
Аннотация не предоставлена.
- Авторов:
- Снеговски, Джеффри Джозеф
- Дата публикации:
- Исследовательская организация:
- Национальная лаборатория Сандия. (SNL-NM), Альбукерке, Нью-Мексико (США)
- Организация-спонсор:
- самофинансирование
- Идентификатор ОСТИ:
- 1574644
- Номер(а) отчета:
- ПЕСОК2016-3854Б
638702
- Номер контракта Министерства энергетики:
- АК04-94АЛ85000
- Тип ресурса:
- Книга
- Страна публикации:
- США
- Язык:
- Английский
Форматы цитирования
- MLA
- АПА
- Чикаго
- БибТекс
Снеговски, Джеффри Джозеф.
Конструирование для химико-механической полировки. . США: Н. П., 2016.
Веб.
Копировать в буфер обмена
Снеговски, Джеффри Джозеф. Конструирование для химико-механической полировки. . Соединенные Штаты.
Копировать в буфер обмена
Снеговски, Джеффри Джозеф. 2016.
«Проектирование для химико-механической полировки». Соединенные Штаты. https://www.osti.gov/servlets/purl/1574644.
Копировать в буфер обмена
@статья{osti_1574644,
title = {Проектирование химико-механической полировки.},
автор = {Снеговски, Джеффри Джозеф},
abstractNote = {Аннотация не предоставлена.},
дои = {},
URL-адрес = {https://www.