После сварки термообработка: Термообработка сварных соединений
alexxlab | 02.10.2020 | 0 | Разное
Термообработка после сварки – Справочник химика 21
Термообработка после сварки [c.279]Термическую обработку в заводских условиях можно выполнять по следующим режимам закалка с отпуском и термообработка после сварки нормализация с отпуском и термообработка после сварки только термообработка после сварки Очевидно, что риск неполучения желаемых свойств является наибольшим при первом и наименьшим при последнем режиме термообработки. Поэтому при выборе оптимальным материалом следует считать тот, который требует минимального числа заводских термообработок. Разность температур отпуска стали и термообработки после сварки часто оказывается незначительной. В этом случае для получения наилучшего сочетания прочности и ударной вяз- [c.213]
При термообработке после сварки имеют место следующие проблемы. Так, для получения наилучших характеристик ударной вязкости металла сварного шва температура термообработки должна соответствовать ее верхнему пределу.

Основной металл Метод сварки Сварочный материал Вид термообработки после сварки Ф. [c.86]
При соединении частей вала требуется его термообработка после сварки и проточка наставки после удлинения. [c.161]
Наиболее опасны разрывы трубопроводов или их элементов с низкой ударной вязкостью или не прошедших необходимую-термообработку после сварки, так как при этом может произойти полный разрыв трубопровода по окружности, сопровождаемый интенсивным истечением газов. [c.66]
Эти статьи служат примером важности проблемы свариваемости сталей и обеспечением механических свойств, связанных со сварными соединениями, которые не подвергаются термообработке после сварки. [c.281]
Сварной образец поперечный стыковой шов сварка методом Т16 с использованием электрода. Повторная термообработка после сварки до состояния Тб. Образец анодированный Часть одного образца отсутствовала. 5 С образца сошло 80 % плакировки. Сошло 10 % плакировки. Плакировка толщиной 0,078 мм. Сошло 15 % плакировки. Образец после сварки методом Т и старения. Сварной поперечный стыковой шов сварка с использованием проволоки 7039. ” Плакировка толщиной 0,061 мм. [c.386]
Значительное влияние на выбор металла оказывает характер агрессивной среды [189]. Для ряда сред выбор соответствующего им металла является совершенно обязательным условием для создания работоспособной конструкции. Нередко необходима термообработка после сварки. [c.18]
Перлитные стали могут подвергаться охрупчиванию около концов сварочных трещин в том случае, когда термообработка после сварки проводилась при слишком низкой температуре. В одном широко известном случае [53] охрупчивание такого вида (главным образом в металле шва) привело к хрупкому разрушению сосуда при гидравлич еском испытании.
Исключение образования трещин в результате релаксации остаточных напряжений для толстостенных сосудов высокого давления стало проблемой возрастающей важности и первейшей необходимости. В сосудах давления из перлитной стали образование трещин обычно происходит в процессе термообработки для снятия остаточных напряжений. Не исключена также возможность образования трещин в толстостенных сосудах во время их эксплуатации при высокой температуре, так как для жестких сварных соединений некоторых легированных сталей температура термообработки после сварки в интервале 600— 650° С недостаточна для полной релаксации напряжений.
В процессе производства сосудов давления опасность возникновения таких чешуйчатых трещин появляется во время приварки к толстостенным обечайкам несквозных штуцеров или других деталей. Поскольку использование в толстостенных сосудах сквозных штуцеров связано с риском образования трещин в процессе термообработки после сварки, для сосудов этого класса обычно применяют несквозные штуцера. В то же время для предотвращения чешуйчатых трещин необходимо регламентировать нижний допустимый предел пластичности в направлении толщины листа или применять сталь, подвергнутую вакуумной дегазации.
С одной стороны, термообработка после сварки не только снимает напряжения, но и может уменьшить максимальные значения твердости в зоне термического влияния сварки и неблагоприятное влияние сварки на механические свойства основного материала. С другой стороны, неправильно назначенный режим термообработки может ухудшить свойства стали. В случае аустенитных сталей, где важна коррозионная стойкость, соответствующая термообработка может восстановить способность стали сопротивляться таким видам коррозии, как общая, точечная, и коррозии под напряжением. В то же время выбор неправильной температуры термообработки может привести к выделению карбидов и другим эффектам, снижающим механические свойства, а также коррозионную стойкость. [c.280]
Термообработка до сварки Вид сварки Термообработка после сварки и механические свойства Покрытие Среднее время до разрушения, сутки [c.134]
На коррозионную стойкость хромоникелевых сталей большое влияние оказывают условия термообработки. Наивысшая коррозионная стойкость достигается при закалке на твердый раствор с быстрым переходом зоны температур 500—800° С. При медленном охлаждении или повторном нагреве в интервале указанных температур пересыщенный твердый раствор частично распадается с выделением по границам зерен карбидов хрома. В результате коррозионная стойкость металла резко снижается. Поэтому сварные швы и околошовные зоны аппаратов из нержавеющей стали, не прошедших повторную термообработку после сварки, наиболее подвержены коррозии.
Часть испытания по согласованию с заказчиком может быть снята. Технологические вопросы, касающиеся режимов термообработки, свариваемости, термообработки после сварки и др., решаются в зависимости от выбранной марки стали, условий изготовления трубопровода и режима эксплуатации. В этом случае необходимые рекомендации могут быть получены в специальной литературе 127], [42], [57]. [c.259]
Необходимость термообработки после сварки элементов из вновь вводимых марок легированной стали устанавливается при согласовании применения указанных марок сталей. [c.989]
Акустико-эмиссионная (АЭ) диагностика в настоящее время широко применяется при диагностировании и проведении испытаний оболочковых конструкций.
Были проведены теоретические и экспериментальные исследования по вварке штуцеров в рулонированные сосуды, проведен анализ переходных термических напряжений, срока службы в условиях меняющихся давлений и температур, а также методов термообработки после сварки. Таким образом рулонированные сосуды по конструкции и по качеству изготовления пригодны для применения в любых рабочих условиях.
Предварительный контроль предусматривает проверку качества сварочных материалов, состояния сварочного оборудования. Пооперационный контроль включает проверку качества подготовки и сборки деталей под сварку, соблюдения режимов предварительного подогрева, режимов сварки и порядка выполнения многослойных швов, проведения термообработки после сварки. Контролю внешним осмотром подвергают сварной шов и прилегающую к нему зону шириной 20 мм по обе стороны от шва по всей протяженности сварного соединения. При внешнем осмотре проверяют качество поверхности сварных соединений. В сварных швах не допускаются следующие виды наружных дефектов трещины, подрезы и резкие переходы от основного металла к металлу шва, прожоги, наплавы, незаплав- [c.238]
В деталях сечением более 20 мм, сваренных из аустенитных сталей (за исключением молибденсодержащей стали 316 по стандарту AJSJ и сплава инкаллой с 32% Ni и 22% Сг), существует опасность возникновения трещин в результате релаксации напряжений в процессе термообработки после сварки или в течение эксплуатации при определенном уровне приложенных напряжений [32].
С другой стороны, охрупчивание вследствие деформационного старения может быть устранено или существенно уменьшено термической обработкой после сварки. Это, в свою очередь, значительно снижает риск хрупкого разрушения спокойной раскисленной кремнием и полуспокойной углеродистой и углеродистомарганцевой сталей. Исходя из сказанного, в стандарте В5 1515 для сосудов, подвергающихся после сварки термической обработке, допускаются более низкие рабочие температуры, чем для сосудов, не подвергающихся термообработке после сварки. [c.220]
Поэтому компромиссным решением является использование стали 304 (стандарт ASTM), содержащей 0,08% С (не более). Эта сталь имеет приемлемую коррозионную стойкость во многих окислительных средах. Однако в некоторых европейских стандартах не разрешается применение других материалов, кроме особо низкоуглеродистых и стабилизированных аустенитных сталей. Кроме того, сталь 304 непригодна для использования в плакированных нержавеющей сталью сосудах, подвергающихся термообработке после сварки, так как при этом в нержавеющей стали будет иметь место интенсивное выделение карбидов. [c.224]
Однако использование стабилизирован 1ых сталей оказывается необходимым в любом случае, в том числе и для плакированного листа, если сосуд подвергается термообработке после сварки в обычном интервале температур, поскольку при этом в нестаби-лизированной стали с 18% Сг и 8% N1 происходит выделение карбидов. Стабилизированные стали также предпочитают при выборе материала для службы при высокой температуре вследствие более [c. 241]
В другой методике используется принцип автофреттажа, применяемый ранее для изготовления стволов пушек. Этот принцип заключается в изготовлении нескольких цилиндров, надеваемых один на другой с натягом. Первый цилиндр (внутренний) имеет точно определенные размеры. Его сваривают, а сварные швы контролируют обычными неразрушающими методами. Затем таким же образом изготавливают эторой цилиндр, причем его внутренний диаметр точно устанавливают равным внешнему диаметру внутреннего цилиндра с соответствующим допуском, гарантирующим расчетный натяг. Второй цилиндр затем нагревают до температуры, не превышающей температуры термообработки после сварки, и насаживают на первый цилиндр. Операция, несомненно, требует тщательности и соблюдения допусков на диаметры. Эту операцию можно повторять до тех пор, пока не будет получена требуемая толщина стенки сосуда. При расчете общая толщина стенки определяется таким же образом, как в случае однослойной стенки. [c.279]
Дакворс [15] составил перечень закаленных и отпущенных сталей разных марок, производящихся в 1966 г. , и отметил, что многие из них имеют одинаковые свойства. В Японии, в частности, большое внимание уделяют свариваемости этих сталей, так как во многих случаях сварка будет проводиться на месте монтажа без термообработки после сварки. [c.281]
Эффект смягчения можно наглядно наблюдать на образцах, у которьЕК термообработка после сварки выровняла микроструктуру твердого металла. При растяжении таких образцов вслед за мягкой прослойкой в определенный момент в пластическую стадию вступают приконтактные участки твердого металла, в то время, как вдали от прослойки этот металл продолжает работать упруго. При дальнейшем нагружении, если аг основной металл на всей длине образца. Однако, локализация деформаций в прикон-гактной области твердого металла остается хорошо заметной (рис. 3.5). [c.58]
Химический состав и механические свойства термически улучшенной никелевой стали 12NU9, вязкой при низких температурах, приведены в табл. 240. Сталь I2Nil9 сваривается применяется газовая, электродуговая сварка, а также электродуговая сварка в атмосфере защитного газа. При толщине свариваемой стенки более 10 мм сталь предварительно нагревают до 100—130°С. Термообработка после сварки не допускается. При обработке стали применяется ковка и отпуск при температуре от 1100 до 850°С. [c.443]
Отпуск после сварки — Режимы
Выбор режима подогрева при сварке или отпуска после сварки определяется требованиями отсутствия трещин и обеспечения необходимого уровня механических свойств сварного соединения. Для сварных конструкций из малоуглеродистой стали или хромомолибденовой относительно небольшой толщины — до 10—15 мм — удается обеспечить указанные требования за счет соответствующего выбора термического режима сварки без применения подогрева или отпуска сваренного изделия. При изготовлении сварных конструкций из хромомолибденовых сталей с толщиной свариваемых элементов свыше 15 мм необходим подогрев при температурах 200—400° в зависимости от жесткости изделия и содержания в стали углерода.
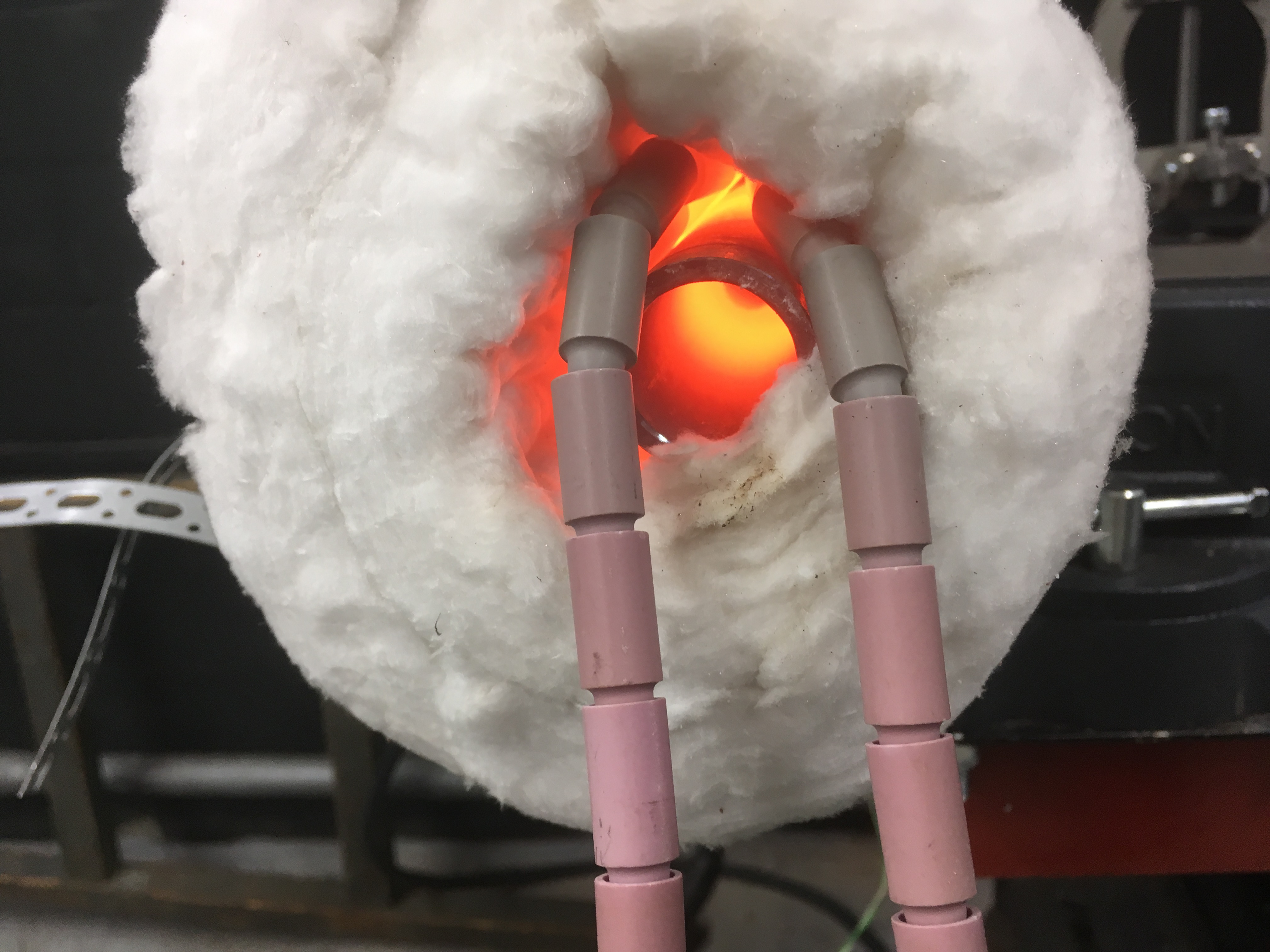
Рис. 9. Механические свойства наплавленного металла КТИ-10 в зависимости от режима отпуска после сварки [3, 15] |
Местный высокий отпуск применяется для крупных деталей в местах, где непосредственно производилась сварка, с целью снижения уровня сварочных напряжений и повышения пластичности металла.
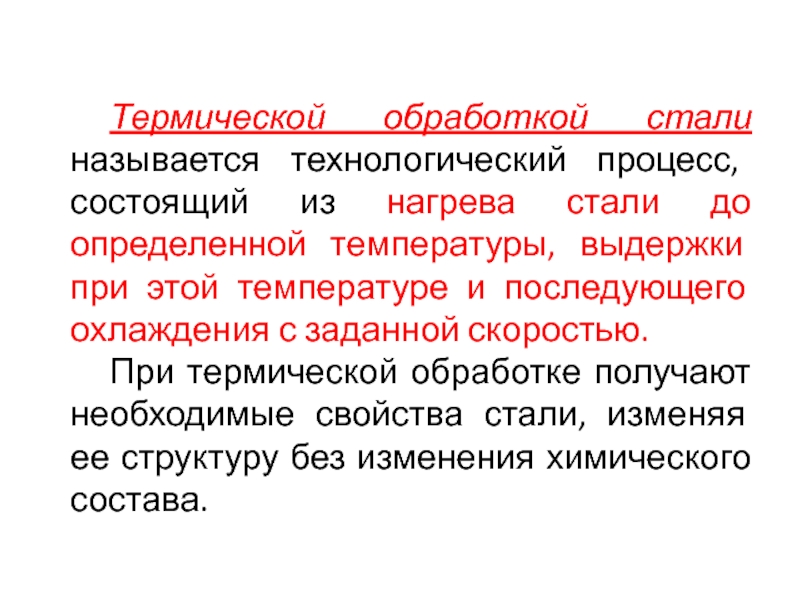
Применение 279 – конструкционная — Износостойкость — Влияние высокочастотной поверхностной закалки 677 – легированная—Механические свойства после цементации, закалки и низкого отпуска 684 — Сварка газовая 202 – малоуглеродистая — Сварка атомно-водородная — Режимы 220 [c.788]
В ряде случаев представляется целесообразным использовать для сварных изделий из перлитных и хромистых сталей режим полной термической обработки закалку с последующим отпуском. При этом обеспечивается наиболее высокая однородность сварного соединения. Данный вид термической обработки может применяться для отливок, подвергаемых крупным заваркам в целях ремонта. На сварку отливка поступает в отожженном состоянии, а после сварки деталь проходит полную термообработку по режиму для основного металла.
[c.92]
После сварки и установки крестовин барабан подвергается отпуску для снятия внутренних напряжений по следующему режиму посадка в печь при температуре 450—500° С, нагрев до температуры 600° С по 80° С в час, выдержка при данной температуре 4—8 ч, охлаждение до температуры цеха на воздухе на выкаченной подине печи. [c.336]
При применении в связи с эксплуатационной необходимостью металлов с пониженной свариваемостью проектировать конструкции следует с учетом этого свойства. Для сведения к минимуму неблагоприятных изменений свойств металла сварного соединения и исключения в нем дефектов необходимо применять виды и режимы сварки, оказывающие минимальное термическое и другие воздействия на металл, и проводить технологические мероприятия (подогрев, искусственное охлаждение и др.), снижающие влияние на него сварочных воздействий. Термическая обработка после сварки (нормализация, закалка с отпуском и др.) может в значительной степени устранять неоднородность свойств в сварных заготовках. Прочность зоны сварного соединения может быть повышена механической обработкой после сварки прокаткой, проковкой и др.
[c.288]
Увеличить стойкость сварного соединения против холодных трещин можно, изменяя параметры режима сварки так, чтобы уменьшить скорость охлаждения металла, уменьшая тем самым опасность возникновения хрупкого закаленного участка в зоне термического влияния. Для этого можно выбирать режим сварки с повышенной энергией, увеличивая мощность источника тепла или уменьшая скорость сварки. Применяют подогрев изделия после сварки или сопутствующий подогрев во время сварки, например газовой горелкой, высокочастотным индуктором, либо второй сварочной дугой. Мелкие детали после сварки можно укладывать в ящик с песком, Детали из сталей с плохой стойкостью против холодных трещин подвергают после сварки общей термообработке (отпуску) в печах.
[c.34]
В зависимости от толщины стенки трубных элементов и класса стали сварка швов выполняется с предварительным и сопутствующим подогревом (табл. 3.32). После сварки проводится термическая обработка по режиму высокого отпуска при температуре 630…750 °С с учетом марки стали и толщины стенки трубных элементов. [c.255]
Рис. 31. Влияние термического режима сварки на длительную прочность и пластичность при температуре 565° С металла шва типа Э-ХМФ (электроды ЦЛ-20М) после сварки отпуск при 720—740° С — 5 ч |
В связи с практической невозможностью полного исключения при изготовлении конструкций различного рода зародышевых дефектов, являющихся в дальнейшем при неблагоприятных обстоятельствах очагами развития эксплуатационных тещин, методы лабораторных и стендовых испытаний должны оценивать также влияние возможных дефектов на прочность изделия.
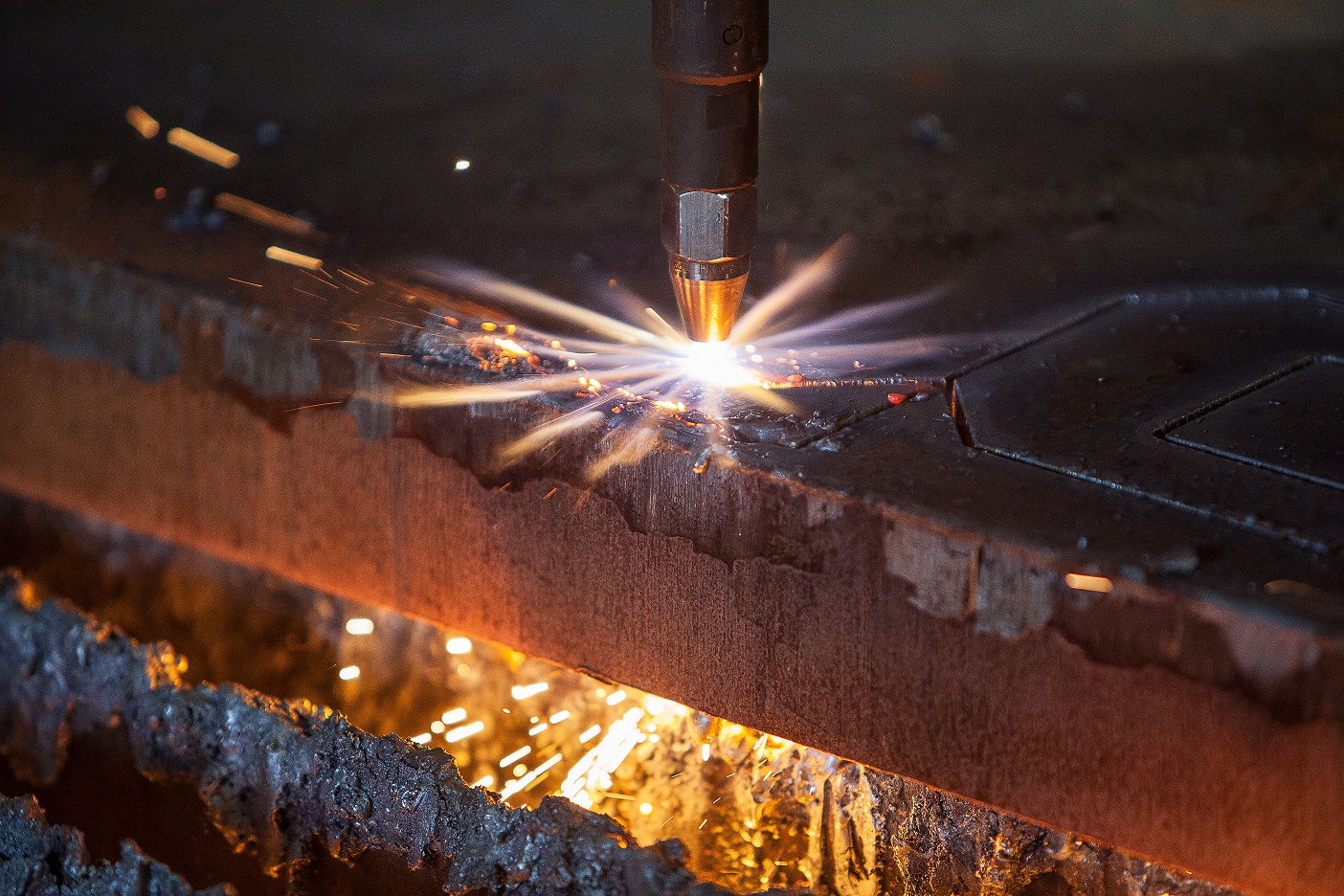
На рис. 101 аналогичные зависимости приведены для швов типов Э-ХМ и Э-ХМФ. Для них также в исходном состоянии после сварки длительная пластичность заметно ниже, чем в отпущенном состоянии. Особо следует обратить внимание на то, что даже при сравнительно небольших отклонениях от оптимального режима отпуска шва типа Э-ХМФ (недоотпуск при 680° С) длительная пластичность шва совсем не повышается, оставаясь на уровне исходного состояния, что наиболее наглядно проявляется при наличии концентратора. Таким образом, для данных составов благоприятное влияние отпуска сказывается лишь при строгом выдерживании установленной температуры отпуска в пределах 730° С.
[c.180]
Образование трещин при высоких температурах в малоуглеродистых и хромомолибденовых швах типа Э-ХМ возможно, как показывает опыт эксплуатации, при наличии в них различного рода дефектов и в первую очередь надрывов в корне шва. В то же время развитие трещин идет относительно медленно и поэтому они обнаруживаются обычно при осмотрах во время капитальных ремонтов. Трещины же в швах типов Э-ХМФ и Э-МФБ даже при сравнительно небольших отклонениях от оптимального режима отпуска (недоотпуске) могут достигать значительного развития, приводя в отдельных случаях к аварийным последствиям. Зародышевые трещины в этих швах могут возникать и непосредственно после сварки в условиях жесткости, при отклонениях от режима подогрева или недоотпуске. Критерием склонности швов к хрупким разрушениям при высоких температурах является величина их длительной пластичности, оцениваемая по результатам испытания образцов на растяжение с постоянной скоростью деформации (и. 14).
[c. 192]
После сварки заготовок из стали 15231 выполняли термическую обработку по режиму закалка с температуры 890° С в воду и отпуск при 550° С (Ов = 97,4 кгс/мм ). Опыты показали, что для высокопрочной стали 15231 предел выносливости образцов с угловым швом (с радиусом галтели в зоне шва / = 10 мм) находится на уровне предела выносливости образцов с поперечным отверстием или шпоночной канавкой. Для стали 11600 (сТв = 60 кгс/мм ) прочность образцов оказалась несколько ниже, чем для образцов со шпоночным пазом или поперечным отверстием. [c.195]
Достаточно высокие значения ударной вязкости у этой стали зависят от режима термической обработки и старения (рис. 272). С понижением температуры испытания она несколько упрочняется, но отпуск при 500° С значительно улучшает ударную вязкость после двойной закалки и после сварки. Сварные изделия после сварки рекомендуется подвергать отпуску для снятия сварочных напряжений и устранения воздействия интервала температур более низкого отпуска (рис. 273) [7091.
[c.467]
После сварки блоков, в зависимости от их габаритов, применяют либо нормализацию с нагревом в печи всего блока по режиму температура нагрева 900— 920° С. охлаждение на воздухе до 250—300° С и последующий отпуск при 630— 650° С в течение 20 ч, либо местную термическую обработку с индукционным нагревом. [c.658]
В соответствии с изменением механических свойств меняются и жаропрочные свойства сварных соединений, оцениваемые по результатам их испытания на длительную прочность. При высокой исходной прочности заготовок и низком отпуске после сварки при 700° С — 5 ч кривые длительной прочности сварных соединений идут выше соответствующих кривых высокоотпущенного состояния (рис. 112, б). По уровню прочности сварные соединения низкоотпущенных вариантов на 10—15% ниже прочности основного металла, обработанного по тому же термическому режиму. При длительности до разрушения в пределах 10 ч изломы проходят пластично при удовлетворительной величине относительного сужения.
При использовании твердости как критерия качества термической обработки следует иметь в виду, что твердость сварных соединений в значительной мере зависит от условий термообработки [12]. Например, при твердости металла шва типа Э-09ХМФ выше НВ 250 (2500 МПа) можно однозначно констатировать, что отпуск после сварки не проводился или его темле-ратура была заметно ниже регламентированной. В то же время если твердость ниже НВ 250, то это еще не говорит о качественном проведении термообработки, так как при чрезмерно высоком подогреве (450—500 °С) пониженная твердость может быть получена и в исходном состоянии. Твердость нялсе НВ 220 свидетельствует о качественном проведении отпуска по установленному режиму. На основании сказанного регламентированная твердость после отпуска должна быть ниже возможной в исходном состоянии при чрезмерно высоком подогреве, поэтому для наиболее ответственных и нагруженных сварных соединений предпочтительнее твердость не выше НВ 220 [12]. [c.171]
Термообработка после сварки различна для разных марок стали. Для отливок из стали ЗОЛ и 35Л при заварке сквозных трещин и вварке усилительных вкладышей обязателен отжиг или высокий отпуск. Для улучшения механических свойств сварного соединения и его обрабатываемости при заварке мелких дефектов на углеродистой стали, содержащей углерода более 0,35%, термическая обработка рекомендуется по режиму для данной стали. Для других сталей, сваренных в термически обработанном состоянии, обязателен отпуск с нагревом до температуры на 50—100° ниже температуры отпуска стали. Для стали 27ГС, 20ХГС и других сталей, склонных к отпускной хрупкости, температура отпуска после сварки должна быть вне области температуры отпускной хрупкости. [c.188]
Термообработка после сварки имеет следующие особенности. При заварке крупных дефектов стали ЛХН2 требуется термическая обработка по режиму для данной стали. После заварки мелких дефектов в термически обработанной отливке обязателен повторный отпуск по режиму для данной стали. Для всякой другой стали рассматриваемой группы, сваренной в термически обработанном состоянии, обязателен отпуск для снятия напряжений с нагревом до температуры на 50—100° ниже температуры отпуска стали. Для стали ЗОХГСА и других сталей, склонных к отпускной хрупкости, температура отпуска после сварки должна быть вне области отпускной хрупкости. [c.189]
Отпуск после сварки кованой стали 15Х1М1Ф должен производиться при температуре 720—740°С. Применение местного отпуска является нежелательным и может допускаться в отдельных случаях при строгом соблюдении установленных режимов. [c.123]Сравнительно широко применяются композитные соединения при сварке сталей одного класса, близких по своим физическим свойствам, но имеющих различный химический состав и механические свойстйа. Однако и в этом случае, как показали исследовании института электросварки им. Патона [23], в сварочных соединениях из низколегированных сталей в зоне сплавления при определенных соотношениях легирующих элементов может наблюдаться концентрационная неоднородность, приводящая к разрушению по зоне сплавления при вибрационной нагрузке. При сварке композитных Соединений возникают вопросы, связанные с выбором электродов, режима подогрева и отпуска после сварки и обеспечения уровня прочностных и пластических свойств таких соединений. Обычно композитные соединения применяются при изготовлении корпусов цилиндров мощных турбин. Корпуса изготавливаются в виде сварных конструкций, в которых области, подвергающиеся действию высоких температур, выполнены из стали 20ХМФ или 15Х1М1Ф, а области, работающие при низких температурах, изготовляются из углеродистой стали 25Л. [c.150]
Подогрев при сварке до 300—350°С, отпуск после сварки при температуре 690—710°С. Полуавтоматическая сварка в среде углекислого газа производится проволокой Св-08ХГСМФА диаметром 3 мм. Сила оварочного тока 350—420 а, напряжение дуги 28—32 в скорость подачи проволоки 100—140 м/н-, расход углекислого газа 1000—1400 л1ч. Сварные соединения, полученные при указанных режимах сварки, обладают вполне удовлетворительными свойствами и аналогичны свойствам соединений, выполненных ручной дуговой сваркой. В табл. 79 приведены результаты механических испытаний сварнолитых соединений, выполненных полуавтоматической сваркой в среде углекислого газа после отпуска при температуре ТЮХ. [c.171]
Однако проведение отжига и отпуска требует наличия сложных нагревательных устройств, точного соблюдения режимов, что в усло-9ИЯХ ремонта деталей не всегда осуществимо. Поэтому в некоторых случаях отжиг и отпуск после сварки или наплавки можно заменить предварительным подогревом изделия, тем более, что предваритель- Ный подогрев изделий из металлов, способных подвергаться закалке, необходим с целью устранения явления закалки и образования микротрещин. Такого рода рекомендации оправдываютсл исследованиями и практикой. [c.41]
С). Однако в ряде случаев, особенно при относительно кратковременной работе установок, обработку заготовок перед сваркой ведут по режиму отпуска при 660—680° С в течение 5 ч. Свойства сварных соединений в этих случаях уступают свойствам основного металла, однако абсолютные значения прочности сохраняются на более высоком уровне, чем для ранее рассмотренных сварных соединений. Так, для сварных соединений стали 15Х12ВМФ (отпуск до сварки по режиму 680″ С — 5 ч, а после сварки по режиму 700° С — 5 ч) предел длительной прочности при 580° С за 10 ч составляет 15 16 кГ1мм . В то же время для сварных соединений, обработанных до и после сварки по режиму высокого от-48 [c.48]
Свойства сварных соединений с точки зрения равнопрочтгости с основным металлом зависят не только от режима термообработки после сваркн, но и от режима термообработки изделия перед сваркой. Так, если отпуск после закалки перед сваркой проводили при температурах ниже тех, которые используют при термообработке [c.269]
Исследованиями установлено, что сварка теплоустойчивых сталей больших толщин должна производиться с применением предварительного и сопутствующего подогрева. Для уменьшения величины остаточных напряжений сварное соединение после сварки должно подвергаться отпуску при температуре, не превышающей температуру отпуска стали до сварки. Во избежание значительного укрупнения зерен и падения ударной вязкости по линии сплавления, сварка должна осуществляться на режимах с ограниченными тепловложе-ниями. Для предотвращения развития диффузионных процессов необходимо стремиться максимально приблизить химический состав шва к составу основного металла. Наилучшие результаты по получению заданного (требуемого) химического состава металла шва определены при легировании через сварную проволоку. [c.121]
Примечание. После сварки сталей 12ХМ и 12МХ необходимо проводить отпуск по режиму, предусмотренному нормативной документацией на термическую обработку. [c.346]
Как показали исследования, остаточные напряжения в сварных соединениях паропроводов из перлитных сталей непосредственно после сварки могут достигать предела текучести металла шва. Однако они редко приводят к повреждениям сварных стыков, если им не сопутствуют дефекты сварки или грубые нарушения установленных режимов сварки. Остаточные напряжения в стыках перлитных трубопроводов снижаются при высоком отпуске, проводимом после сварки. В процессе эксплуатации при высоких температурах они относительно быстро релаксируют. Так, сразу после сварки электродами ЦЛ-14 в сварных стыках паропровода из стали 12МХ одного из котлов ТП-230, на котором в порядке эксперимента не производился отпуск сварных соединений, среднеквадратичные напряжения на внутренней поверхности стыка достигали 16,3 /сГ/жж . После 5 500 ч эксплуатации сварных стыков, не проходивших термической обработки, величина среднеквадратичных напряжений снизилась до 4,4 кГ1мм . [c.201]
Металл перлитного шва в зависимости от его легированности, термического режима сварки и режима отпуска существенно меняет свои свойства. Малоуглеродистые швы обеспечивают необходимые прочность и пластичность непосредственно в исходном состоянии после сварки. Хромомолибденовые швы при наличии подогрева и замедленного остывания конструкций с относительно небольшой толщиной свариваемых элементов также могут иметь необходимые механические свойства непосредственно после сварки,- В то же время при сварке изделий из хромомолибденовых сталей относительно большой толщины (ударной вязкости металла шва. Поэтому указанные сварные конструкции должны после сварки подвергаться обязательному отпуску. [c.27]
На фиг. 10 приведены кривые длительной прочности сварных соединений стали 15ХШ1Ф (электроды ЦЛ-27) при двух уровнях прочности заготовок до сварки. В одном случае сталь перед сваркой термически обрабатывалась на предел текучести при комнатной температуре, равный 40—45 кПмм (нижний уровень прочности для стали) в другом предел текучести заготовки был равен 52—58 кПм.мР. После сварки все образцы прошли отпуск по режиму 720—730 — 5 час. [c.28]
Режимы дополнительной термообработки после холодной или горячен. реформации (гибки, обжатия, штамповки и др.) и после сварки для разных размеров труб (отпуск, аустениэация, нормализация, время выдержки, зона нагрева) должны устанавливаться совместной инструкцией завода, утвержденной главным инженером и согласованной с основными положениями, разработанными ЦНИИТМАШ. Рекомендуемые режимы дополнительной термообработки указаны в табл. 4.1.3. [c.268]
Для обеспечения пластических свойств металла шва и околошов-ной зоны на уровне свойств основного металла следует выбирать режимы, обеспечивающие получение швов повышенного сечения, применять двухдуговую сварку или производить предварительный подогрев металла до температуры 150…200 °С. Среднеуглеродистые и среднелегированные стали рекомендуется сваривать под флюсом при толщине свариваемого металла не менее 4 мм. Сварку можно вести как на переменном, так и на постоянном токе. Диаметр электродной проволоки выбирают 2…5 мм. При сварке с одной стороны не допускается использование медных и медно-флюсовых подкладок из-за возможности попадания в шов меди и образования вследствие этого горячих трещин. Для увеличения сопротивляемости сварных швов горячим трещинам, а также повышения пластичности и ударной вязкости металла шва используют основные флюсы, такие как АН-26, АН-20, 48-ОФ-10, уменьшающие содержание серы и окисных включений в металле шва. Во избежание пористости и наводоражи-вания швов флюсы перед сваркой необходимо прокаливать при температуре 300…350 °С в течение 2…3 ч, чтобы их влажность не превышала 0,1 %. Конструкционные среднеуглеродистые и среднелегированные стали под флюсом сваривают, как правило, без подогрева. Только в случае сварки жестких узлов и узлов из сталей ЗОХГСА и ЗОХГСНА при большой толщине изделий применяют подогрев до температуры 250…300 °С. После сварки во всех случаях необходим общий отпуск при температуре 600 °С или местный послесварочный отпуск при температуре 300 ° С для предупреждения образования холодных трещин. [c.150]
Свариваемость двухфазных хромоникелевых сталей переходных классов по сравнению с однофазными выше, особенно сопротивляемость образованию трещин и межкристаллитной коррозии. Мартенситно-стареющие коррозионностойкие стали (08Х15Н5Д2Т и др.) могут иметь в зоне сварного соединения ослабленные участки в отношении величины ударной вязкости и стойкости против коррозии. Антикоррозионные свойства сварных соединений восстанавливаются после полной термической обработки. Рекомендуется для этих же целей отпуск перед сваркой при 600—650 °С. Для предотвращения старения металла в зоне сварного соединения в процессе эксплуатации конструкции и последующего снижения его пластических свойств применяют термообработку после сварки (при 600—650 °С). Хромоникелевые стали сваривают практически всеми методами. Режимы стремятся подбирать так, чтобы сварка происходила при малых значениях погонной энергии. Успешно сваривают хромоникелевые стали контактной сваркой. [c.511]
Поэтому во избежание саморастрескивания деталей отжиг или высокий отпуск следует проводить немедленно после сварки. Более подробные данные по режимам термической обработки для других хромистых сталей приведены в табл. 28 с указанием получаемой при этом твердости. Ими можно пользоваться при обработке сварных соединений. [c.719]
Термообработка сварных деталей из низкоуглеродистой стали. ВСтЗпс, ВСтЗсп, 20, 25, 30, 25Л, 20К, 09Г2С, 15ГС, 20ГСЛ, 10ХСНД
Термическая обработка сварных конструкций производится с целью снятия остаточных сварочных напряжений, возникающих в процессе сварки, и улучшения структуры и свойств шва и зоны термического влияния. Термическая обработка должна производиться сразу после окончания сварки, не допускается охлаждения деталей ниже температуры подогрева. При невозможности проведения термической обработки сразу после сварки допускается проводить термический «отдых». Решение о проведении термического «отдыха» принимает мастер. Мастер термического участка (пирометрист) должен знать принцип работы переносных и стационарных пирометрических приборов, температурный режим работы печей, порядок ведения записей и замеров температуры, основные причины возникновения дефектов в пирометрах и способы предотвращения и устранения их, способ смены прогоревших кожухов у термопар.
Подготовка к термообработке: Перед проведением термической обработки детали укладывают горизонтально согласно схемы укладки в специальный поддон, который затем помещается в печь. Допускается другие схемы укладки деталей в печь, если это предусмотрено технологическим процессом. В одну садку должны подбираться близкие по сечению (толщине). Установка сварных конструкций в печах с выдвижным подом и съемными колпаками производиться на подставках или решетки, высота которых должна быть не менее 80 мм. Расстояние между сварными конструкциями, должно быть не менее 50 мм.
Режим термообработки:
- Загрузка в холодную или нагретую не выше 300°С печь.
- Нагрев с производственной скоростью до температуры 300 °С.
- Выдержка при температуре 300±25 °С в течение 1-2 часов.
- Нагрев со скоростью не более 70 °С/час до температуры 590 °С.
- Выдержка при температуре 590 ±25 °С не менее 3-х часов из расчета 1 час на каждые 25 мм наибольшего сечения конструкции.
- Охлаждение в печи со скоростью не более 50 °С/час до температуры 250 °С.
В процессе охлаждения в интервале температур 590-250 °С ЗАПРЕЩАЕТСЯ выдвигать под в печах с выдвижным подом и приподнимать колпак в колпаковых печах.
Температура рабочего пространства в различных зонах печи должна регистрироваться самопишущим прибором в течение всего процесса термической обработки. Снятую с прибора диаграмму мастер термического участка или ответственный за термообработку представляет в отдел технического контроля цеха. Замер и запись фактических
температур режима термообработки производится пирометристом. Запись осуществляется в специальном журнале.
Контроль качества: Сварная конструкция должна поступать на термообработку с сопроводительным документом, заверенным штампом ОТК, удостоверяющим полноту и качество выполнения предыдущих операций .
В процессе термической обработки мастер термического участка контролирует и регистрирует соответствие фактических параметров режима (скорость и время нагрева, температура и продолжительность выдержки, скорость охлаждения, температуру выемки изделия из печи) технологической документации.
По окончании термической обработки, мастер термического участка на сопроводительном документе ставит штамп или делает соответствующею запись о проведении термической обработки, с указанием даты проведения термообработки, № печи, № режима. Результаты контроля должны удовлетворять конструкторской и технологической документации.
Благодарим за поддержку в создании этой статьи компанию Интермост.
Термообработка сварных швов и соединений: процесс выполнения
Различают три разновидности термической обработки деталей. Первая разновидность – это подготовка деталей перед сваркой. Некоторые конфигурации свариваемых изделий (например, трубы больших диаметров) требуют предварительного подогрева до 110 – 120 С0 непосредственно перед сваркой. К некоторым изделиям применяют определенные методы во время сварки. В этой статье мы расскажем, как проводится термообработка сварных швов уже готовых сваренных изделий.1 / 1
Для чего нужна термообработка
В процессе сварки в металле свариваемых деталей происходят разнообразные процессы. Главные из которых это:
- неравномерный прогрев и охлаждение различных зон;
- фазовые преобразования в металле;
- химическое взаимодействие с окружающим пространством.
Все эти процессы приводят к появлению местных напряжений, которые могут стать причиной возникновения трещин и, в тяжелых случаях, привести к полному разрушению изделия. От всех этих неприятностей поможет избавиться термообработка сварных соединений.
Виды обработки
Термообработка может производиться разными способами в различных режимах. В зависимости от химического состава и геометрических размеров изделия используют следующие виды термообработки.
Стабилизирующий отжиг
Изделие нагревается до температуры 970 градусов, и эта температура поддерживается в течение полутора часов. Далее происходит естественное охлаждение. Метод получил широкое распространение при термообработке высоколегированных сталей.
Термический отдых
Этот процесс предусматривает нагрев металла до 300 С0 с последующей выдержкой при этой температуре. Идеальное время выдержки два часа. Кроме снятия напряжения, этот способ снижает количество растворенного водорода в металле шва. Такой метод более всего может пригодиться для обработки изделий с толстыми стенками, где другие методы применить сложно.
Нормализация
Применяется при термической обработке труб малого диаметра. Такие трубы имеют тонкие стенки. В данном случае шов с участком трубы нагревают до 800 градусов и выдерживают около получаса. Таким образом, удается снять только часть напряжений, но это не главное. Главная цель этого вида обработки – придание металлу мелкозернистой однородной структуры.
Высокий отпуск
Подходит для сталей перлитного класса. Время обработки выбирается в пределах нескольких часов. Температуру нагрева доводят до 600 – 700 градусов. Такая обработка решает множество проблем для низколегированных сталей. Остаточное напряжение снимается практически полностью, исчезает закалочная структура.
Аустенизация
Самый высокотемпературный вид. Процессы идут при 1100 градусах в течение 120 – 180 минут. Далее проходит естественное остывание на воздухе. Применяется, в основном, на высоколегированных сталях, придавая им высокую пластичность при незначительных остаточных напряжениях.
Применение различных видов термообработки позволяет повысить прочность сварных швов, увеличить надежность изделий и значительно продлевает срок технической эксплуатации, способствуя повышению коррозионной стойкости металла.
Особенности процесса и применяемое оборудование
Термическая обработка швов требует различных технологий и оборудования. Существует три основных типа оборудования для термической обработки.
Радиационное оборудование – это наиболее простой, а значит, и самый распространенный вид оборудования. Нагрев изделия происходит за счет передачи тепла от нагретой нихромовой проволоки. Между проволокой и изделием прокладывают термостойкий электроизоляционный материал и постепенно увеличивают напряжение на нагревательном элементе (нихромовая проволока). Работа проходит намного быстрее, если нагревательная проволока уже изолирована, и нет необходимости каждый раз изолировать изделие.
Регулировка напряжения может осуществляться различными средствами: от простейших способов переключения отводов на обмотке понижающего трансформатора или устройства гасящих сопротивлений, до высокотехнологичных электронных преобразователей напряжения на тиристорах.
Газопламенное оборудование намного хлопотнее предыдущего вида. Согласитесь, что обеспечить подачу электрического питания намного проще, чем подачу газа. Такие же сложности с регулировкой процесса и контролем параметров. И еще проблематичнее выглядят возможности механизации или автоматизации термообработки сварных швов с применением газопламенного оборудования. Но есть у этого оборудования и одно неоспоримое преимущество – низкая стоимость работ. Это становится понятным при самом приближенном сравнении стоимости электроэнергии и газа.
Индукционные установки
Этот вид термообработки требует специального дорогостоящего оборудования и квалифицированного обслуживания. Промышленность выпускает как переносные индукционные установки, рассчитанные на обработку некрупных деталей в «полевых» условиях, так и многофункциональные гиганты, на основе которых создаются целые производственные участки.
На таких участках используют мощные индукционные установки, вырабатывающие высокочастотное напряжение. Это напряжение подаётся на провода, особым образом расположенные на обрабатываемом изделии. Протекающий в проводах ток, в свою очередь, вызывает появление токов в обрабатываемой детали, которые и разогревают её до нужной температуры.
Индукционные установки используются не только для термообработки сварных швов, но и для разогрева труб в процессе их изгибания. Таким образом, имеется возможность на одной промышленной линии осуществлять разогрев труб перед сваркой, непосредственно сварку труб и термообработку сварных швов. К этому участку обычно примыкает участок приварки фланцев и других деталей.
Необходимо отметить, что все эти процессы легко механизируются и автоматизируются. При наличии необходимого набора датчиков, компьютера и программного обеспечения можно создавать полностью автоматические производственные линии.
Термообработка сварных изделий, металлоконструкций и сварных швов
Д.А. Чичиндаев, А.С. Степанов. / 12.12.2019
Для чего нужна термообработка сварных стыков (швов, соединений, металлоконструкций, изделий и трубопроводов)?
Давайте сперва определим понятие термообработки применимо к сварным изделиям и сварным швам.
Термообработка сварных изделий – это совокупность операций нагрева, выдержки и охлаждения зон сварки (околошовных зон (ОШВ), сварных швов (СВ)) для достижения требуемых параметров и физико-механических свойств сварных швов и, как следствие, сварных изделий.
Для чего проводится термообработка:
Термообработка, как правило, проводится для повышения эксплуатационных характеристик сварных изделий. Она снимает поверхностные и внутренние напряжения в металле, образовавшиеся после сварки.
Показатели качественной термообработки в монтажных условиях:
Сварной шов после сварки имеет, более высокие показатели твердости нежели основной металл. После проведения качественной термообработки показатели твердости сварного шва снижаются до требуемых НТД РФ величин. В монтажных условиях дефектоскописты лаборатории Неразрушающего Контроля при помощи твердомеров производят проверку показателей твердости и контроль соблюдения требуемого НТД РФ диапазона твердости сварного шва.
Основные способы проведения термообработки сварных соединений:
Термообработка после сварки проводится как в заводских условиях, так и на монтаже. В монтажных условиях термообработка сварных стыков и соединений проводится в основном по программе отжига для снятия напряжений (низкотемпературный отжиг или высокий отпуск) двумя способами: радиационный (нагрев производится керамическими ковриками) и индукционный (нагрев производится индуктором, обмотанным вокруг изделия). Оба способа позволяют произвести с заданными параметрами контролируемый подъем температуры до требуемой, провести выдержку температуры и последующее контролируемое охлаждение. В заводских условиях возможно еще использовать печной способ термообработки и иные программы термообработки.
Диапазоны использования радиационного и индукционного методов
Согласно требованиям РТМ-1С, действующим в тепловой энергетике (при выполнении термообработки в других отраслях следует руководствоваться соответствующей Нормативной Документацией) для термообработки трубопроводов со стенками до 50 мм возможно использование как радиационного метода так и индукционного. Для стенок 50 мм и выше – рекомендовано использование индуктивного способа.
Компания ООО «ТЭК-Консалтинг» специализируется на проведении термообработки сварных стыков различного диаметра и толщин стенок.
Основные этапы взаимодействия ООО «ТЭК-Консалтинг» с Заказчиком по запросу на проведение операций предварительного подогрева и термообработки:
· Выяснение технических требований Заказчика, заполнение опросного листа, который вы можете скачать по ссылке:
СКАЧАТЬ ОПРОСНЫЙ ЛИСТ на ПРОВЕДЕНИЕ ТЕРМООБРАБОТКИ СВАРНЫХ СОЕДИНЕНИЙ
· Расчет и передача технико-коммерческого предложения в требуемые Заказчиком сроки
· Оперативное согласование и подписание договора с Заказчиком
· При необходимости и по требованию Заказчика – разработка технологии термообработки
· Срочная доукомплектация необходимыми расходными материалами под конкретный проект
· Выезд с оборудованием и аттестованным персоналом Исполнителя на площадку Заказчика
· Исполнение Договора – проведение термообработки сварных стыков в сменном режиме 24/7
· Проведение контроля показателей твердости твердомерами до термообработки и после, протоколирование показателей, ведение журналов термообработки, температура термообработки фиксируется аттестованными регистраторами автоматически с записью на диаграммную ленту
· Подготовка сдаточной документации по требованиям Заказчика, передача Заказчику
ООО «ТЭК-Консалтинг» – строительно-монтажная компания с длительным опытом работ на рынке энергетики в России. Обладая собственным парком оборудования и аттестованными специалистами – операторами термистами, мы в кратчайшие сроки проведем термообработку сварных стыков различного объема и диаметра.
Термообработка
Наша компания проводит работы по термообработке на высококачественном оборудовании компании Weldotherm.
Назначение и виды термообработки сварных соединений.Соединения, выполненные дуговым способами сварки, непосредственно после процесса характеризуются высоким уровнем содержания водорода, неоднородностью структуры и свойств сварного шва, зоны термического влияния, а также наличием в них сварочных напряжений.
Неоднородность структуры соединения зависит, главным образом, от неравномерности нагрева металла при сварке. Металл шва в процессе сварки в расплавленном состоянии имеет температуру выше 1500°С, в то время как соединение со швом участки металла нагреваются в меньшой степени и находятся в твердом состоянии. Прочность и твердость металла шва обычно в 1,5-2 раза превышают эти характеристики в зоне термического влияния и основном металле. Неравномерное значение в сварном соединении имеют и специальные свойства, такие как жаропрочность, хладостойкость, коррозионная стойкость.
Такое неудовлетворительное состояние металла усугубляется действием внутренних напряжений, возникающих в процессе сварки, которые могут достигать значений, близких к пределу текучести (250-350 МПа). Появление этих напряжений обусловлено неравномерностью нагрева различных зон соединения и усадкой металла при охлаждении, структурными изменениями и жесткостью свариваемого изделия.
Внутренние напряжения, возникающие в процессе сварки, опасны тем, что могут вызвать появление трещин в сварных соединениях, особенно, если они изготавливаются из легированных сталей. Кроме того, эти стали при сварке в производственных условиях быстро остывают, что приводит к образованию закалочных структур в шве и зоне термического влияния, также способствующих трещинообразованию.
Одним из основных средств повышения надежности сварных соединений является термическая обработка, процесс которой состоит из трех последовательных этапов: нагрев до определенной температуры с заданной скоростью, выдержка при этой температуре в течение определенного времени и последующие охлаждение с заданной скоростью или подслоем изоляции.
В каждой отрасли промышленности имеет свои нормативно-технические документы по термообработке сварных соединений, которые отражают особенности данного производства.
Классификация видов термообработки.
Предварительный подогрев
Трубы из низкоуглеродистых и низколегированных сталей перлитного класса подогревают (особенно в зимнее время) до 100-200°С, что предохраняет сварное соединение при сварке от быстрого охлаждения, приводящего к возникновению трещин в шве. Различают предварительный подогрев (до начала сварки) и сопутствующий (непосредственно в процессе сварки или во время перерывов в процессе сварки).
Высокий отпуск
При термообработке сварное соединение нагревают до температуры на 20-30°С ниже температуры критической точки Ас1, выдерживают в течение 1-5 ч. и затем медленно охлаждают. При этом на 70-90% снижается уровень сварочных напряжений, происходит структурные изменения в сварном шве и зоны термического влияния, заключающиеся для низколегированных сталей в распаде закалочных структур, что в конечном итоге приводит к заметному снижению твердости и повышению пластичности металла. Высокому отпуску обычно подвергают сварные соединения труб из сталей перлитного класса.
Нормализация
Применяется для сварных соединений, выполненных методами сварки с большой погонной энергией, при которой структура металла сварного соединения становится крупнозернистой с пониженными механическими свойствами.
Сварное соединение нагревают до температуры на 20-30 °С выше температуры критической точки Ас3, выдерживают в течение непродолжительного времени и охлаждают на спокойном воздухе.
Нормализации чаще всего подвергают сварные соединения тонкостенных труб малого диаметра из низколегированных сталей перлитного класса, сваренных газовой сваркой, которые в исходном состоянии (после сварки) имеют крупнозернистую структуру с пониженными пластичными свойствами.
Термический отдых
Сварное соединение нагревают до 250-300 °С и затем выдерживают в течение нескольких часов. При термическом отдыхе уменьшается содержание диффузионного водорода в сварных соединениях, а также несколько снижается уровень сварных напряжений. Отдых обычно назначают для сварных соединений толстостенных конструкций, для которых трудно выполнить термообработку по режиму высокого отпуска.
Сюда можно отнести также термообработку по режиму “дегазации” (нагрев до 200-250 °С с выдержкой 1-2 ч.), которая проводится при ремонте трубопроводов и корпусных конструкций, проработавших в контакте с коррозионноопасными средами.
Аустенизация
Сварное соединение нагревают примерно до 1080-1130 °С, выдерживают в течение 1-2 ч. охлаждают на воздухе. В результате аустенита за счет распада феррита, улучшить механические свойства стали и снизить уровень сварочные напряжений. Аустенизации подвергают сварные соединения трубопроводов из высоколегированных сталей аустенитного класса марок 08Х18Н10Т и др.
Стабилизирующий отжиг
Стабилизирующий отжиг применяют для сварных соединений трубопроводов из высоколегированных сталей аустенитного класса марок 08Х18Н10Т и т.п. Сварное соединение нагревают до 850-870 °С, выдерживают в течение 2-3 ч. и охлаждают на воздухе. Такая термообработка приводит к снижению сварных напряжений на 70-80 % и обеспечивает стабильную структуру, хорошо противодействующую возникновению межкристаллитной коррозии.
Нормализация с отпуском
Полная или восстановительная термообработка применяется для восстановления структуры и свойств сварных соединений различных сталей. При термической обработке сварных соединений теплоустойчивых сталей с целью продления ресурса длительного эксплуатирующихся паропроводов, а так же барабанов. Нормализация обеспечивает получение равномерной аустенитной структуры. При последующем охлаждении происходит превращение аустенита в феррит. Высокий отпуск дает длительную прочность и пластичность сварных соединений.
Все вышеперечисленные виды термообработки сварных соединений возможно производить на индукционном и радиационном оборудовании.
Технологии термообработки.
Принцип индукционного нагрева
Принцип индукционного нагрева легко иллюстрируется с помощью катушки индуктивности с магнитным полем, изменяющимся при изменении силы тока
Поле замыкается внутри катушки, и напряженность зависит от силы тока и количества витков катушки. При помещении металлического предмета внутрь катушки на его поверхности будут возникать вихревые токи, которые вследствие электрического сопротивления металла вызовут нагрев поверхности. Эффект нагрева возрастает с ростом напряженности поля и зависит от свойств материала и расстояния катушки от поверхности.
Наведенный ток будет создавать собственное, противоположное основному поле, что предотвращает проникновение поля катушки в центр предмета. По этой причине вихревые токи будут более активны в области, близкой к поверхности предмета, с понижением силы тока по направлению к центру.
Глубиной проникновения считается уровень, на котором сила тока падает до уровня 37%. С понижением частоты поля глубина проникновения увеличивается. Наложение вихревых токов во внутренних областях предмета вызывает понижение эффективности катушки индуктивности. По этой причине особенно важно выбирать частоту поля в соответствии с габаритами нагреваемого предмета.
Можно установить, что все проводящие материалы нагреваются индукционным методом, вызывая немедленный нагрев в металле.
Преимущества
– быстрота нагрева;
– высокая концентрация и точная локализация энергии при нагреве обеспечивают короткий цикл, высокую производительность, улучшают показатели использования оборудования и материалов и снижают риск деформации при нагреве;
– высокое и однородное качество;
– индукционный нагрев позволяет с легкостью осуществить точное автоматическое управление процессом. Он идеально согласуется с автоматизированным производством и не требует специальной подготовки персонала;
– нагрев только внутри материала;
– непрерывный нагрев производится непосредственно в детали;
– индукционный нагрев позволяет избегать сложного технического обслуживания, измерения, нагрева футеровки печей и их охлаждения. В процессе нагрева не выделяется дым или другие вредные эмиссии, загрязняющие материалы и оборудование. Все это снижает опасность процесса и улучшает рабочие условия;
– пониженные затраты энергии;
В силу самого принципа индукционного нагрева формирование тепла происходит внутри детали и, вследствие этого, процесс более эффективен по затратам энергии, чем другие методы, и количество рассеиваемой энергии исключительно низко.
Применение
– плавка металлов в индукционных электропечах;
– формоизменение: ковка, гибка, прошивка, прессование;
– термообработка: закалка, отжиг, правка, нагрев перед сваркой;
– пайка твердым и мягким припоями;
– спекание металлических порошков и многих других.
Выбор оборудования
Сначала определяют количество необходимой энергии по графику поглощения энергии различными металлами и определяют КПД нагревательной установки.
Для получения значения полной энергии следует разделить потребление энергии на одну тонну данным видом материала на КПД установки.
Далее следует умножить полученное значение на величину требуемого почасового выхода продукции (т/час) для определения потребления энергии.
Термообработка сварных швов: технология и методы проведения
В процессе сооружения конструкций из металла выполняют различные процессы. Так, термообработка сварных швов проводится в процессе работы с металлами и их сплавами. Это позволяет изменить их свойства и структуру. Для термоооброботки сварных соединений используют определенный инструмент, в зависимости от выбранного метода. Зачищенный металл поддается обработке.
Основные способы обработки сварных швов
Зачистка сварных швов после сварки проводится тремя методами:
- Термическая обработка. С помощью этого метода устраняют остаточное напряжение в металле, которое возникает в результате проведения сварки. Термическая обработка сварного шва проводится по местной и общей технологии. В первом случае речь идет о нагреве с дальнейшим охлаждением только сварного соединения. Что же касается общей термообработки, то здесь выполняется прогрев непосредственно всей детали. Этот метод зачастую используют для небольших конструкций.
- Механическая обработка. Суть данного метода заключается в устранении с соединения и прилегающих участков остатков шлаков. Также в процессе обработки производится проверка стыка на прочность. Так, классическим вариантом является зачистка сварных швов с помощью определенных инструментов или постукивание шва. К проверке соединения относятся очень внимательно, так как от этого будет зависеть срок эксплуатации конструкции. Если в результате постукивания возникли трещины, то конструкция отбраковывается, так как прочность соединения нарушено. Что касается остатков шлака, если не выполнить его удаление, то в дальнейшем это приведет к возникновению коррозии участка. Для этого проводится шлифовка сварных швов.
- Химическая обработка. При таком методе выполняется нанесение на соединение защитного покрытия. Это позволяет предотвратить коррозию металла в процессе эксплуатации конструкции. Самым доступным вариантом является использование грунтовочного лакокрасочного вещества.
При выборе метода обработки сварных швов стоит учесть множество факторов. Прежде всего, это касается рациональности способа в том или ином случае. Большое значение имеет и цель использования конструкции. К некоторым изделиям и соединительным швам предъявляются повышенные требования по прочности и надежности.
Термообработка
Зачастую термообработку сварных стыков используют в процессе сооружения трубопроводных магистралей. Для их создания применяют трубы, которые имеют большой внутренний диаметр и значительную толщину стенок. Это обеспечит прочность и надежность системы в процессе эксплуатации. Но, это создает новую проблему – тяжело провести качественное стыкование труб, которые имеют такие геометрические характеристики.
В процессе сварки происходит нагрев небольшого участка изделия. В результате это приводит к возникновению ряда физических процессов, которые неблагоприятно сказываются на эксплуатации конструкции.
Сама же термообработка сварных соединений проводится в несколько этапов:
- Пдготовка изделий к сварке. От того, насколько качественно будет выполнена эта работа, зависит прочность соединения.
- Термообработка места соединения изделий при сваривании.
- Обработка швов после сварки.
Термическая обработка нужна для того, чтобы улучшить сварные свойства металлических конструкций. Но, прежде всего, изделия и швы поддают отжигу и высокому отпуску.
Зачем нужна?
Сварка производится под воздействием электрической дуги, а также присадочного материала с электрода. При этом температура составляет 1500-50000С. В результате такого нагрева на толстом металле возникают различные негативные явления, которые стоит рассмотреть более тщательно:
- В месте соединения сварного и присадочного материала возникает большой перегрев. В результате повышается кристаллизация металла, который имеет крупную структуру. Это значительно понижает его пластичность. Также в процессе нагрева происходит выгорание марганца и кремния. Участок металлического изделия стает жестким и теряет свои первозданные технические характеристики.
- Вблизи шва находится зона закалки, она также испытывает нагрев. Конечно, на нее действует меньшая температура, чем в среде непосредственного соединения присадочного и основного материала. В результате этого в металле происходит закалывание определенных элементов. Участок теряет свою первоначальную пластичность и становится более твердым. Также изменяются показатели материала по ударной вязкости.
- Зона разупрочнения расположена на удаленном расстоянии от места непосредственной сварки металлических изделий. Она поддается воздействию умеренной температуры, которую излучает электронная дуга. Благодаря непродолжительности этого процесса материал сохраняет свою пластичность. Но, что касается прочности, то она несколько понижается.
В результате проведения сварки металла на металл действует остаточное напряжение, которое может привести к деформации. Это может вызвать некоторые сложности при монтаже объемных конструкций. Особенно это касается мест, где будут устанавливаться новые узлы.
Опасность остаточного напряжения заключается в том, что в дальнейшем оно может вызвать образование трещин. В особенности это касается места сварки. Это недопустимо, так как в дальнейшем это приведет к разрушению соединения.
Ситуация ухудшается, когда в процессе эксплуатации конструкции на место сварки действуют высокие температуры. Это приводит к снижению стойкости металла к коррозийным процессам и цикличной прочности. Это касается и способности металла противостоять хрупкости, которая возникает под действием низких температур.
Особенности проведения
Термическая обработка сварных соединений проводится под высокой температурой, значение которой составляет от 700 до 10000С. Благодаря этому можно устранить последствия неравномерного нагрева, которое проводилось во время дуговой сварки. Особенно это касается металлических изделий, которые имеют значительную толщину. В результате обработки шву придают структуру, схожую с остальным материалом.
Термообработка сварных соединений проводится в три этапа:
- Выполняется нагрев участка возле соединения. Для этого используется специальное оборудование, о котором мы поговорим позже.
- Участок или все изделие выдерживается под определенной температурой на протяжении определенного времени.
- На завершающем этапе выполняется планомерное охлаждение материала до нормальной температуры.
Благодаря такому процессу можно устранить остаточные явления после дуговой сварки, выровнять структуру металла, а также снять напряжение, которое часто является причиной его деформации. Процесс выполняется различными способами. Технология его проведения зависит от толщины и типа материала. Обработка проводится не всегда, но есть случаи, когда она просто необходима.
На видео: как происходит процесс термообработки.
Достоинства и недостатки
Обработка стыка термическим методом обладает определенными достоинствами и недостатками. Среди преимуществ можно выделить:
- В результате процесса сварные стыки приобретают новые свойства. В результате этого детали станут более пригодными для эксплуатации в определенных условиях. В особенности это касается защиты металла от коррозии.
- Обработка позволяет устранить некоторые негативные моменты, которые возникли в результате проведения сварных работ.
- Термическая обработка снимает остаточное напряжение, которое возникает в процессе сварки.
Конечно, чтобы достичь такого результата, необходимо правильно подойти к обработке. В особенности это касается соблюдения некоторых правил. Что же касается недостатков данного метода обработки, то среди них выделяют:
- Процесс должен выполнять опытный специалист. Это связано с тем, что обработка путем нагрева необратима. А это значит, что устранить допущенные ошибки при этом практически невозможно.
- Для проведения обработки может понадобиться специальное оборудование, для работы с которым нужны определенные навыки. Особенно когда проводится защита сварных швов трубопроводов.
- Процедура должна проводиться в точности с предъявляемыми требованиями.
- В каждом случае подбираются свои параметры обработки.
Если придерживаться определенных правил, то в процессе зачистки стыка не возникнет никаких проблем.
Что подвергают обработке?
Термообработка часто применяется при сооружении трубопроводов различного назначения. В первую очередь это касается труб, которые имеют диаметр более 10 см и толщину стенок 1 см и больше. Процесс выполняется с помощью индукционного нагрева током, частота которого составляет 50 Гц.
Термическая обработка труб довольно проста. Для этого применяют муфельные печи и специальные электронагревательные проволоки, которые имеют достаточную гибкость. Если же изделие имеет толщину не больше 2,5 см, то для обработки используют газопламенный нагрев. Здесь главное равномерно распределить температуру в области соединительного шва.
Термическая обработка проводится не только на кольцевых швах, но и на соединениях, которые имеют другую форму.
При обработке сварных швов стоит учесть толщину и особенности металла. Так, например, если трубопровод изготовляется из стальных труб, толщина стенок которых составляет 45 мм, то процесс необходимо провести сразу после сварки. При этом охлаждение материала не должно достигать 3000С. Это касается и изделия толщиной 25 мм.
Если нет возможности выполнить обработку, то шов защищают теплоизоляционным материалом. При первой же возможности выполняют зачистку. Процесс должен быть проведен в течение 3 суток со дня выполнения сварки.
Параметры проведения процесса
Особенности термообработки напрямую зависят от вида и толщины стали. Так, в случае с хромомолибденовой сталью и ее сплавами процесс проводится индукционным или радиационным методами.
Итак, в зависимости от толщины материала и используемого метода, процесс обработки займет следующее время:
Толщина металла, мм | Радиационный метод, мин | Индукционный метод, мин |
20 | 40 | 25 |
20-25 | 70 | 40 |
25-30 | 100 | 40 |
30-35 | 120 | 60 |
35-45 | 140 | 70 |
45-60 | 150 | 90 |
60-80 | 160 | 110 |
Если проанализировать таблицу, то можно отметить, что обработка металла индукционным методом занимает меньше времени. Это объясняется особенностями проведения процесса.
Какое оборудование используется?
Термическую обработку сварных швов проводят с помощью различных средств. При выборе учитывается толщина металла и возможность использования того или иного оборудования в определенном месте. Сегодня существует три основных метода нагрева околошовного участка. Рассмотрим каждый из них.
Индукционное
На месте устанавливается специальный аппарат, который вырабатывает переменное напряжение высокой частоты. К нему подключается нагревательный элемент, в качестве которого используется гибкий провод. Его наматывают на сварочное соединение, которое предварительно окутывают теплоизоляционным асбестом. Эта технология используется для обработки горизонтальных и вертикальных швов.
Провод наматывается к изолятору вплотную. При этом между витками оставляется зазор толщиной 2,5 см. В результате, с обеих сторон шва покрывается по 25 см изделия. Когда витки будут установлены, согласно всем требованиям и нормам, аппарат включается. При этом учитывается время работы оборудования. Это напрямую зависит от толщины металла. В процессе работы аппарата через витки проходит напряжение, которое создает индукцию, а также нагрев металла.
Для выполнения обработки также широко используют специальные пояса, которые содержат определенное количество проводов. Это позволяет без особых усилий и быстро подготовить изделие к зачистке после сварки.
На видео: индукционный нагрев трубы.
Радиационное
Не меньшей популярностью пользуется радиационный способ обработки сварных швов. В качестве нагревательного элемента используются специальные нихромовые провода. Через них пропускается напряжение, что приводит к их нагреву. Здесь стоит отметить, что в процессе не берет участие индукция. Нагрев материала осуществляется с помощью раскаленной проволоки. Тэны укладываются на основу из теплоизоляционного материала.
Газопламенное
Данный метод является самым дешевым. Для термообработки сварных участков используется ацетиленовая смесь и кислород. Метод используют для обработки материалов, толщина которых составляет не более 10 см. На горелку, заполненную горючей смесью, устанавливается мундштук, который имеет крупные отверстия. Чтобы обеспечить равномерную подачу тепла к обрабатываемой поверхности, на сопло надевают асбестовую воронку. Это позволяет распределить пламя на ширину в 25 см.
При использовании данного способа стоит учесть некоторые особенности. Так, чтобы выполнить качественную термообработку околошовных участков, необходимо нагревать их одновременно. А это значит, что в процессе берут участие сразу две горелки.
Виды термической обработки
Термическое воздействие на соединение сваркой может выполняться несколькими способами. При этом учитывается цель данного процесса. Среди основных методов выделяют:
- Термический отдых. В данном случае материал подвергают нагреву до 3000С. Такая температура поддерживается на протяжении двух часов. В результате процесса происходит снижение водорода в сварочном шве, а также снимается остаточное напряжение. Данный метод зачастую используют к материалам, которые имеют толстые стенки, а также там, где нет возможности применить другие технологии.
- Высокий отпуск. При такой технологии изделие поддают нагреву при температуре до 7000С. Такая обработка длится около трех часов. Время действия тепла на материал напрямую зависит от его толщины. Этот метод позволяет снять остаточное напряжение практически на 90%. Если речь идет об обработке низколегированной стали, то в результате происходит разрушение закалочной структуры и карбиды становятся более крупными. Таким образом, можно достичь повышения пластичности и ударной вязкости. Зачастую эта технология применяется к перлитным сталям.
- Нормализация. Данный метод подразумевает одновременное нагревание материала и сварного шва до температуры в 8000С. При этом термическая обработка не должна превышать 40 минут. С помощью нормализации можно частично снять остаточное напряжение. Но, главным достоинством является то, что в результате обработки получается однородная и мелкозернистая структура. Это в свою очередь улучшает механические свойства шва и околошовных участков. Нормализация зачастую используется на материалах, которые имеют небольшую толщину.
- Аустенизация. Материал разогревается до температуры в 11000С. Термическое воздействие продолжается на протяжении двух часов. После этого материал охлаждается на воздухе. Не рекомендуется выполнять принудительное охлаждение, так как это приведет к снижению прочности металла, а в результате к появлению трещин. Аустенизация используется на высоколегированных сталях. С ее помощью повышается пластичность материала, и снижается остаточное напряжение.
- Стабилизирующий отжиг. Метод используется для обработки материалов с наложенным швом. Он подвергается нагреву температурой в 9700С на протяжении трех часов. По истечению данного времени материал поддают естественному охлаждению на воздухе. С помощью стабилизирующего отжига можно предупредить возникновение межкристаллической коррозии. Зачастую технологию применяют на высоколегированных сталях. Это позволит защитить участки от коррозии.
Термическая обработка применяется на изделиях из различных металлов. С ее помощью повышают их срок эксплуатации. Чтобы правильно провести процесс, необходимо тщательно подойти к выбору рабочей температуры, способа нагрева, а также времени проведения термической обработки. С зачищенными изделиями нужно обходиться очень аккуратно, чтобы не повредить их.
Какой способ выбрать?
Выбор технологии проведения термической обработки сварных соединений напрямую зависит от физико-химических характеристик материала. Об этом свидетельствует марка стали. Особое значение специалисты рекомендуют обратить на выполнение технологических требований. В ином случае качество сварного шва значительно понижается, что в дальнейшем может привести к его полному разрушению.
При выполнении термообработки сварного соединения стоит учесть следующие параметры:
- ширина участка, который будет поддаваться обработке;
- равномерность теплового воздействия на материал, как по толщине, так и по ширине;
- длительность нагревания;
- особенности охлаждения материала после проведения термообработки.
Если учесть все эти особенности, то можно выбрать способ термообработки, который позволит повысить качество соединения. В особенности это касается его прочности.
Контроль температуры
Как уже было сказано, в процессе термообработки необходимо тщательно следить за температурой нагрева. Для достижения этой цели используют специальные средства, такие как термокарандаш и термокраска. При достижении определенной температуры они резко меняют свой цвет. В зависимости от принципа действия, такие терморегуляторы бывают химическими и плавильными.
При достижении определенной температуры, химические регуляторы температуры меняют свой цвет в результате реакции между компонентами. На точность измерения напрямую влияет время термического воздействия на материал, а также колебания давления.
Если нагрев осуществляется на протяжении 3 минут, то погрешность измерений составит не более 100С. Стоит отметить, что изменение оттенка контролеров тепла возникает при критических температурах.
В карандашах и красках второго типа изменение оттенка возникает в результате плавление вещества, которое очень чувствительно к повышению температуры. В отличие от химических термоиндикаторов, эти средства меняются независимо от длительности теплового воздействия. Это позволяет более точно установить температуру нагрева. При этом погрешность составляет не более 20С.
Термоиндикаторы плавления обладают многими достоинствами, среди которых стоит выделить инертность к переменной температуре, разрежению, солнечной радиации, морскому туману и другим негативным факторам окружающей среды, которые могут повлиять на точность измерений.
Термокарандаши и термокраски плавления делятся на два типа:
- Адсорбентные. Индикатор состоит из пигмента в связующем растворе и суспензии вещества, которое чувствительно к повышению температуры во время проведения нагрева материала. В результате теплового воздействия термочувствительное вещество плавится, после чего происходит его адсорбция цветовым пигментом.
- Лаки плавления. Они имеют определенную точку плавления. Вещество наносят непосредственно на обрабатываемую поверхность. Оно быстро высыхает, после чего образуется шероховатая поверхность. В результате достижения определенной температуры она станет глянцевой.
На сегодняшний день производством термоиндикаторов занимаются лакокрасочные заводы. Вместе с этим они предоставляют информацию о критических точках плавления того или иного вещества. Это позволяет значительно повысить качество термической обработки сварных швов.
Другие виды обработки
Зачистку швов осуществляют также механическим и химическим методами. Каждый из них имеет свои особенности проведения. Стоит отметить, что комбинирование этих методов позволяет значительно повысить качество обработки.
Механическая
Обработка проводится с помощью проволочной щетки. Но, такой инструмент используют в труднодоступных местах. В иных случаях для зачистки сварных швов специалисты рекомендуют использовать шлифовальное устройство или болгарку, оснащенную лепестковой насадкой или абразивным кругом.
С помощью механической зачистки можно устранить со сварного изделия заусеницы, окислы и другие новообразования, которые возникли в результате проведения сварочных работ.
Зачистка сварочных швов проводится с учетом некоторых нюансов:
- Особое внимание стоит уделить выбору шлифовального круга. Оптимальным вариантом станет изделие из цирконата алюминия. Особенность этого материала заключается в том, что он обладает высокой прочностью.
- Лепестки круга должны быть изготовлены на тканевой основе. Это связано с тем, что ткань, по сравнению с бумагой, обладает высокой прочностью. При этом стоит учесть, что такие изделия стоят сравнительно недешево.
- Для проведения работ могут понадобиться круги с разными абразивными зернами. Поэтому стоит одновременно приобрести несколько изделий.
- При проведении работ учитывается зернистость круга. Так, если нужно устранить большие окалины, то лучше использовать крупнозернистые насадки. Финишная очистка выполняется мелкозернистыми кругами.
- Зачистка сварных швов в труднодоступных местах осуществляется с помощью специальных инструментов. Борфрезы имеют различные размеры, что позволяет подобрать оптимальный вариант для того или иного участка. Они устанавливаются на шлифовальную машинку.
Химическая
Чтобы достичь максимального эффекта и защитить конструкцию от коррозии, специалисты рекомендуют сочетать механический и химический методы обработки. Для начала осуществляется очистка сварного шва машинкой или щеткой. После этого материал обрабатывают специальными коррозионно устойчивыми веществами, которые позволяют защитить его от негативных факторов окружающей среды.
Химическая обработка осуществляется методом травления и пассивации. Травление применяют до проведения механической шлифовки. Для выполнения процесса используется химический состав, который обеспечивает образование однородного покрытия, защищающее материал от коррозии. Помимо этого, эти вещества позволяют устранить последствия негативного влияния окружающей среды на материал. В особенности это касается мест, где есть скопления окислов хрома и никеля. Именно там чаще всего возникают коррозийные процессы.
Если деталь имеет небольшие размеры, то в процессе обработке она помещается в емкость, заполненную химическим составом. Время проведение в емкости определяется в соответствии с особенностями сварного изделия. В случае с большими изделиями используют местную обработку. Химический состав наносится непосредственно на обрабатываемый участок.
После травления приступают к пассивации сварного соединения. В процессе обработки на зачищенный участок металла наносится состав, который образует пленку. Такое защитное покрытие позволяет защитить изделие от коррозийных процессов.
В результате нанесения состава возникает химическая реакция, которая объясняется довольно просто. Оксиданты взаимодействуют со сталью, что приводит к освобождению свободного металла с поверхности. Это приводит к активации защитной пленки.
На завершающем этапе выполняется очистка сварных соединений от химических веществ. Для этого используется вода. При проведении процесса стоит соблюдать осторожность, так как в отходах после смывки содержатся токсичные вещества, тяжелые металлы и кислоты. Нейтрализовать кислоту можно с помощью щелочи. Оставшуюся жидкость фильтруют. Отработанная вода утилизируется в специально отведенных для этого местах. При этом учитываются законодательные акты по охране окружающей среды.
Обработка конструкций после сварки является весьма ответственным процессом. Работу должен проводить профессиональный мастер. Это обеспечит высокое качество конечного результата. При желании выполнить обработку сварных соединений можно своими руками. Для этого нужно следовать определенным правилам и советам специалистов.
Главное помнить о средствах безопасности. Это касается всех видов обработки. При термической зачистке опасность заключается в использовании высоких температур. С используемым оборудованием нужно обходиться очень осторожно. Это позволит предотвратить возникновение травм. При проведении работ стоит использовать средства индивидуальной защиты.
Зачистка сварных швов (3 видео)
Разные способы обработки (25 фото)
Термическая обработка после сварки (PWHT)
Сварка является неотъемлемой частью эксплуатации и технического обслуживания активов в нефтяной (добывающей, промежуточной, перерабатывающей) и химической промышленности. Хотя он имеет множество полезных применений, процесс сварки может непреднамеренно ослабить оборудование, создавая остаточные напряжения в материале, что приведет к ухудшению свойств материала.
Чтобы обеспечить сохранение прочности материала детали после сварки, регулярно выполняется процесс, известный как Термическая обработка после сварки (PWHT) .PWHT может использоваться для снижения остаточных напряжений, как метод контроля твердости или даже для повышения прочности материала.
Если PWHT выполняется неправильно или вообще игнорируется, остаточные напряжения могут в сочетании с нагрузочными напряжениями превысить конструктивные ограничения материала. Это может привести к сбоям сварки, более высокому потенциалу растрескивания и повышенной восприимчивости к хрупкому разрушению .
PWHT включает в себя множество различных типов потенциальных обработок; два наиболее распространенных типа – последующий нагрев и снятие напряжения:
- Пост-нагрев:
- Водородное растрескивание (HIC) часто возникает, когда во время сварки в материал проникает высокий уровень водорода.Нагревая материал после сварки, можно рассеивать водород из зоны сварки, предотвращая таким образом HIC. Этот процесс известен как пост-нагрев и должен начинаться сразу после завершения сварки. Вместо того, чтобы дать возможность остыть, материал необходимо нагреть до определенной температуры в зависимости от типа и толщины материала. Его следует выдержать при этой температуре в течение нескольких часов в зависимости от толщины материала.
- Снятие напряжения:
- К моменту завершения сварочный процесс может вызвать большое количество остаточных напряжений в материале, что может привести к повышенному потенциалу коррозии под напряжением и растрескивания, вызванного водородом.PWHT может использоваться для снятия этих остаточных напряжений и снижения этого потенциала. Этот процесс включает нагревание материала до определенной температуры с последующим его постепенным охлаждением.
Следует ли подвергать материал PWHT, зависит от ряда факторов, в том числе от его системы легирования или от того, подвергался ли он ранее термообработке. Некоторые материалы действительно могут быть повреждены PWHT, в то время как другие почти всегда требуют этого.
Как правило, чем выше содержание углерода в материале, тем больше вероятность того, что после проведения сварочных работ потребуется PWHT.Точно так же, чем выше содержание сплава и чем выше толщина поперечного сечения, тем больше вероятность, что материал потребует PWHT.
Ссылки- Фундерберк, Р. Скотт, 1998. «Ключевые концепции: термообработка после сварки». Инновации в сварке Том XV, № 2.
- Ахмед Халил, Кришан Дж., 2002. «Термическая обработка после сварки – примеры из практики», Информационный бюллетень BARC, специальный выпуск ко Дню основателя, стр. 111-115.
Это определение неполное? Вы можете помочь, внося в него свой вклад.
Связанные темы
Инструменты темы
Поделиться темой
Внести вклад в определение
Мы приветствуем обновления этого определения Integripedia от сообщества Inspectioneering.Щелкните значок ссылку ниже, чтобы открыть форму, которая позволит вам внести изменения в определение и отправить их Инспекционному персоналу.
Способствовать определениюТермическая обработка после сварки – обзор
Аустенитные стали
Термическая обработка аустенитных сталей после сварки необходима для обеспечения удовлетворительной работы в некоторых условиях, но может также вызвать другие проблемы.Краткое описание ситуаций, требующих термической обработки, и проблем, связанных с этим, приведено в Таблице 3.1.
Таблица 3.1. Проблемы, требующие термообработки аустенитных нержавеющих сталей
Тип материала | Устойчивость к механической обработке | Растрескивание при повторном нагреве | Трансгранулярная коррозия под напряжением | Межкристаллитная коррозия под напряжением | Распад сварного шва | Сигма-выделение | Повреждение линии ножа |
---|---|---|---|---|---|---|---|
304 | ✓ | ✓ | ✓ | ✓ | & gt; 0.06% C | ✗ | ✗ |
304L | ✓ | ✓ | ✓ | ✗ | ✗ | ✗ | ✗ |
316 | ✓ | & gt; 0,1% Nb | ✓ | ✓ | > 0,06% C | ✗ | ✗ |
316L | ✓ | > 0,1% Nb | ✓ | ✗ | ✗ | ✗ | ✗ |
321, 347 | ✓ | ✗ # | ✓ | ✗ | ✗ | ✗ | ✓ |
309, 310 | ✓ | ✓ | ✓ | ✓ | ✗ | Литой,> 0.1% C | ✗ |
18/37 (литье) | ✓ | ✗ | ✓ | ✓ | ✗ | ✗ | ✗ |
308, 309 металла сварного шва | ✓ | ✗ | ✓ | ✗ | ✗ | ✗ | ✗ |
Применимо HT | 400–450 ° C 550–650 ° C 850–950 ° C 950–1050 ° C Медленное охлаждение | 950 –1050 ° C Быстрое охлаждение | 850–1050 ° C Медленное охлаждение | 950–1050 ° C Быстрое охлаждение | 950–1050 ° C Быстрое охлаждение | 950–1050 ° C Быстрое охлаждение |
Из-за Чем выше коэффициент теплового расширения аустенитной стали по сравнению с ферритной сталью, проблемы деформации могут быть более серьезными в аустенитных сварных деталях.В тех случаях, когда после сварки должна выполняться обработка с узкими допусками, может потребоваться обработка для частичного снятия напряжения, например, при 550–650 ° C или даже 400–450 ° C, чтобы предотвратить деформацию во время обработки, как обсуждается ниже. Выбор температур для послесварочной термообработки конструкций из аустенитной нержавеющей стали для снятия остаточных напряжений не так прост, как для ферритных сталей, в правилах дается мало рекомендаций.
Основными причинами термической обработки аустенитных нержавеющих сталей являются (i) снятие напряжений и (ii) повторное растворение вредных осадков.Степень снятия напряжения зависит от применяемой температуры, например, большая часть напряжения может сниматься при температуре выше 950 ° C, тогда как около 35% снимается при температуре 550–650 ° C. 17 Снятие напряжения должно сопровождаться медленным охлаждением, но следует отметить, что в диапазоне температур 850–550 ° C это приведет к некоторой форме выпадения осадков. Для повторного растворения осадков требуется температура выше 1000 ° C с последующим быстрым охлаждением, которое приводит к повторному возникновению остаточного напряжения. Следовательно, большая часть снятия напряжения аустенитных сталей – это компромисс.Кроме того, использование самых высоких температур приводит к провисанию неподдерживаемых конструкций, что является дополнительным осложнением.
Проблема растрескивания при повторном нагреве может возникать в некоторых аустенитных сталях. 18 Это может произойти, если закрепленные сварные детали из чувствительных сталей нагреваются, например, до 850 ° C в течение коротких периодов времени (возможно, менее одного часа) или до более низких температур в течение длительного времени, например, до 500 ° C в течение примерно 1000 час. Склонность к растрескиванию увеличивается с ограничением соединений и, следовательно, становится больше для толстых сварных деталей, чем для тонких.Было обнаружено, что все обычные аустенитные стали подвержены этой форме растрескивания после сварки, за исключением стали типа 316 с содержанием Nb <0,1%. Сталь типа 347 особенно восприимчива. Эту проблему можно предотвратить путем термообработки сварного шва при температуре 950–1050 ° C, чтобы уменьшить выпадение осадков, способствующих растрескиванию. Требуется быстрый нагрев через области более низких критических температур.
Наличие остаточных напряжений при сварке приводит к увеличению риска коррозионного растрескивания под напряжением в аустенитных сварных деталях в определенных средах, 9 см. Рис.3.8. Все обычные относительно низколегированные аустенитные нержавеющие стали страдают от межкристаллитного коррозионного растрескивания под напряжением в хлоридных или гидроксидных средах.
3.8. Коррозионное растрескивание под напряжением в сварных деталях из аустенитной нержавеющей стали.
Концентрация хлорид-ионов, достаточная для того, чтобы вызвать растрескивание, может составлять всего одну часть на миллион в насыщенной кислородом воде, тогда как в случае гидроксильных ионов необходимы концентрации около 40%. Следовательно, во время производства следует принимать меры предосторожности, чтобы исключить контакт с веществами, несущими хлорид-ионы, даже в том, что касается контроля типа растворителя, используемого в маркерах.Коррозионное растрескивание под напряжением происходит только при наличии растягивающего напряжения, поэтому, если общие напряжения уменьшаются за счет снятия остаточных напряжений, склонность к растрескиванию может быть значительно снижена или устранена. Это требует термической обработки для снятия основной части остаточных напряжений и требует температур 800–1050 ° C с последующим медленным охлаждением.
Вторая форма коррозионного растрескивания может возникать в некоторых аустенитных сталях в умеренно / умеренно окислительных средах. Эта форма атаки ускоряется под действием напряжения и происходит по межзерновому механизму, когда на границах зерен происходит выделение богатого хромом (Fe, Cr) 23 C 6 . 19 Обычно это происходит при воздействии температур в диапазоне 500–850 ° C в процессе эксплуатации или во время сварки. Сталь, в которой возникло это состояние, считается «сенсибилизированной» к межкристаллитной атаке. Чувствительность является результатом обеднения хрома, прилегающего к границам зерен. Этого можно избежать, проводя термообработку при температуре около 950 ° C или выше, чтобы осадки возвращались обратно в твердый раствор, с последующим быстрым охлаждением для предотвращения повторного осаждения на границах зерен.При локальной термообработке нержавеющих сталей необходимо соблюдать осторожность, поскольку температурный градиент по обе стороны от нагретой ленты будет подвергать материал воздействию температур в критическом диапазоне для осаждения.
Связанная с этим проблема, которая может возникнуть в аустенитных изделиях непосредственно после сварки в средах с незначительным / умеренным окислением, – это «распад сварного шва». Это форма преимущественной межкристаллитной атаки в ЗТВ сварного шва. Это также вызвано выделением на границах зерен карбидов с высоким содержанием хрома в области ЗТВ, нагретой до температур от 500 до 850 ° C.Восприимчивые материалы следует подвергнуть послесварочной термообработке до температуры выше 950 ° C, чтобы карбиды перешли в раствор.
Проблемы с выделением карбидов в стабилизированных марках, например, типов 321 и 347, в значительной степени решаются путем добавления элементов (Ti и Nb), которые образуют карбиды, предпочтительно, чем хром. Однако на установках нефтепереработки, где могут образовываться политионовые кислоты, иногда требуется стабилизационная термообработка (например, при 850–920 ° C для типа 347) для устойчивости к межкристаллитному воздействию. 19
Вторым средством преодоления сенсибилизации является снижение уровня углерода в стали. Широко доступны низкоуглеродистые аустенитные марки (304L, 316L) с содержанием углерода, равным или менее 0,03% C, что в значительной степени устраняет проблемы коррозии / коррозии под напряжением, связанной с выделением карбидов. Фактически, при современных методах производства стали уровни углерода в деформируемых аустенитных нержавеющих сталях, как правило, значительно ниже, чем в предыдущие годы, а проблемы, связанные с выделением карбидов, особенно во время сварки, встречаются гораздо реже, чем, скажем, 30 лет назад.
Еще одна трудность, которая может возникнуть в результате термообработки после сварки, – это «повреждение ножевой линии». Это происходит предпочтительно в области границы плавления сварных деталей из стабилизированных сталей, например типов 321 и 347, после термообработки в диапазоне температур 550–750 ° C в течение более одного часа. Эта атака требует очень специфической окислительной среды, такой как кипящая азотная кислота, и не является широко распространенной проблемой. Этого не происходит, если уровень углерода ниже 0,03%.Для восприимчивых материалов и подходящей среды термообработку при необходимости следует проводить при температуре выше 750 ° C.
При длительной эксплуатации при высоких температурах (около 500–850 ° C) возможно образование хрупкой интерметаллической фазы, известной как сигма-фаза. 20 Время и температура, при которых это происходит, различаются для разных марок аустенитной стали, но в целом это происходит во время эксплуатации при 650–850 ° C в течение периодов от 10 часов для стали марки 304 до 1000 часов для стали типа 310.
Сигма-фаза, как правило, не присутствует в ЗТВ или металле сварного шва сварных конструкций, а также маловероятна при кратковременной термообработке после сварки полностью аустенитного материала, поскольку это время обычно слишком короткое. Однако его можно обнаружить во время термообработки металлов сварных швов, содержащих значительное количество остаточного δ-феррита (например, металлы сварных швов типов 308, 309), поскольку образование сигмы из феррита происходит значительно быстрее, чем из аустенита. Последние разработки аустенитных нержавеющих сталей 18Cr – 8Ni показывают, что образование сигма-фазы можно замедлить, изменив химический состав.Сигма-фаза, вероятно, мало повлияет на свойства при повышенных температурах, но может вызвать заметное охрупчивание, когда сварная деталь остыла после работы до температуры окружающей среды. Тепловой удар из-за быстрого охлаждения может вызвать растрескивание хрупких конструкций.
Аналогичные проблемы могут возникать при высокотемпературной эксплуатации высокоуглеродистых литых аустенитных материалов основных составов 25/20 или 18/37. В этих материалах возможно обширное осаждение карбидов и сигма-фазы при температурах в диапазоне 500–850 ° C в течение времени менее 1 часа, что делает материал хрупким от комнатной температуры до примерно 750 ° C.
Это наиболее тяжелая ситуация при высоком содержании углерода около 0,4% и становится менее серьезной при содержании углерода порядка 0,1%. Обработка раствором при 1250 ° C может быть использована для возврата карбидов в раствор для восстановления исходного состояния материала, но повторное осаждение быстро произойдет во время эксплуатации в диапазоне 500–850 ° C. Кованые материалы аналогичного состава по отношению к хрому и никелю обычно имеют более низкое содержание углерода, и этой проблемы не возникает.За исключением случаев, когда требуется высокий уровень углерода для высокотемпературной прочности, наиболее подходящим подходом к использованию аустенитных нержавеющих сталей, где требуется термообработка, является выбор одной из марок с низким содержанием углерода.
Зачем нужна термообработка после сварки
Термическая обработка после сварки (PWHT) используется для уменьшения напряжения в куске металла после того, как он подвергся сварке. Сварка – бессильный процесс во многих отраслях промышленности, особенно в обрабатывающей.Это полезно при производстве стали и металлических компонентов. В процессе сварки используются очень высокие температуры. Это заставляет металл расширяться. Когда металл остывает, он дает усадку. В результате в металле остается много напряжений. PWHT перераспределяет это напряжение, вызванное сваркой.
Важность послесварочной термообработки
PWHT необходим, чтобы сделать металл более прочным. Он предохраняет металл от растрескивания под воздействием напряжения во время сварочной операции.Этот процесс также дает следующие преимущества:
- PWHT увеличивает пластичность и снижает твердость металла.
- Поскольку он снижает твердость, вероятность поломок, связанных с напряжением, также сводится к минимуму.
- Металл становится менее хрупким.
- Этот процесс обеспечивает большую стабильность размеров.
- PWHT снижает риск водородного растрескивания (HIC).
Меры предосторожности и рекомендации
Хотя PWHT чрезвычайно полезен для применения и срока службы продукта, следует позаботиться о том, чтобы выбранный метод работал в пользу конкретного металла.
- Следует учитывать, подвергался ли основной металл термообработке ранее.
- Некоторые сплавы и металлы могут растрескиваться при PWHT. Таким образом, необходимо учитывать систему сплава.
- Температура PWHT никогда не должна превышать температуру отпуска сплава или металла.
- Присадочный материал, используемый для сварки, также претерпевает несколько изменений при термообработке. Также следует учитывать совместимость наполнителя.
Продолжительность и диапазон температур PWHT зависит от всех вышеперечисленных факторов.
Термическая обработка после сварки имеет решающее значение для надлежащего функционирования и надежности металла и применения. Это необходимо для увеличения срока службы большинства металлов. PWHT – один из наиболее важных процессов, используемых при производстве стали.
Что инспектор по сварке должен знать о предварительном нагреве и термообработке после сварки
При сварке некоторых основных материалов и для некоторых условий эксплуатации может потребоваться предварительный нагрев и / или термообработка после сварки.Эти типы термической обработки обычно требуются для обеспечения надлежащей целостности сварного шва и обычно предотвращают или устраняют нежелательные характеристики в готовом сварном шве. Любая форма термообработки является дорогостоящей, поскольку требует дополнительного оборудования, дополнительного времени и дополнительных операций. По этим причинам термическую обработку следует проводить только после тщательного изучения преимуществ, которые она может предложить. В некоторых случаях термическая обработка будет обязательной, как в случае тяжелых профилей из низколегированных сталей, тогда как в других случаях она будет оправданной мерой предосторожности против преждевременного выхода из строя.
Существует ряд причин для включения этих термических обработок в процедуру сварки, и мы рассмотрим некоторые из наиболее распространенных.
Предварительный нагрев
Предварительный нагрев, как определено в Стандартных условиях сварки AWS, – это «тепло, прикладываемое к основному металлу или подложке для достижения и поддержания температуры предварительного нагрева». Температура предварительного нагрева определяется тем же документом, что и «температура основного металла в объеме, окружающем точку сварки, непосредственно перед началом сварки.При многопроходной сварке это также температура непосредственно перед началом второго и последующих проходов » (Температура между проходами).
Предварительный нагрев может выполняться с использованием газовых горелок, кислородно-газового пламени, электрических одеял, индукционного нагрева или нагревания в печи. Для достижения хороших результатов важно, чтобы нагрев был равномерным по всей области стыка. Интенсивный неравномерный нагрев мало полезен для замедления охлаждения и может быть вредным, вызывая более высокие остаточные напряжения, деформацию или нежелательные металлургические изменения в основном материале.Если указан предварительный нагрев, все сварное соединение должно быть равномерно нагрето по толщине материала до желаемой минимальной температуры. Чтобы получить равномерную температуру по толщине материала, желательно приложить источники нагрева к одной стороне поверхности материала и измерить температуру материала на противоположной стороне. Когда нагревание и измерение температуры должны проводиться с одной и той же поверхности, инспектор должен убедиться, что нагрета не только поверхность материала.Важно следить за тем, чтобы вся толщина материала была нагрета до однородной температуры. Помимо установки температуры предварительного нагрева, для некоторых приложений может потребоваться ограничение температуры между проходами. Эта информация должна быть указана в спецификации процедуры сварки. Если указана температура между проходами, область сварного шва должна быть проверена перед нанесением следующего сварного шва. Сварка не может продолжаться, если измеренная температура превышает максимальные условия между проходами, указанные в процедуре сварки.Перед тем, как продолжить сварку, сварной конструкции необходимо дать остыть до указанного верхнего предела температуры между проходами.
В зависимости от металлургических свойств материала и / или желаемых механических свойств свариваемого компонента, предварительный нагрев и температура между проходами могут оцениваться по разным причинам. Например, процедура сварки низкоуглеродистой стали, которая имеет низкое содержание углерода, относительно низкую закаливаемость и используется там, где нет особых требований к обслуживанию, может учитывать минимальную температуру предварительного нагрева и промежуточного прохода в зависимости от толщины материала.В процедурах сварки, используемых для термообрабатываемых низколегированных сталей и хромомолибденовых сталей с требованиями к ударной нагрузке, обычно указываются минимальные и максимальные требования к температуре предварительного нагрева и промежуточного прохода. Эти низколегированные материалы могут иметь высокую закаливаемость и подвержены водородному растрескиванию. Слишком быстрое охлаждение этих материалов или их перегрев может серьезно повлиять на их эксплуатационные требования. При сварке никелевых сплавов мы в первую очередь озабочены тепловложением во время операции сварки.Подвод тепла в процессе сварки, а также температура предварительного нагрева и промежуточного прохода могут серьезно повлиять на эти материалы. Высокая погонная энергия может привести к чрезмерному растворению состава, выделению карбидов и другим вредным металлургическим явлениям. Эти металлургические изменения могут способствовать растрескиванию или потере коррозионной стойкости. Процедуры сварки некоторых алюминиевых сплавов, таких как термообрабатываемые, серии 2ххх, 6ххх и 7ххх, часто связаны с общим снижением тепловложения. Для этих материалов максимальная температура предварительного нагрева и промежуточного прохода контролируется, чтобы минимизировать влияние отжига и старения на зону термического влияния (HAZ) и, как следствие, потерю прочности на разрыв.
В критических случаях необходимо точно контролировать температуру предварительного нагрева. В этих ситуациях используются регулируемые системы нагрева, и к ним прикрепляются термопары для контроля нагреваемой детали. Эти термопары подают сигнал на блок управления, который может регулировать источник питания, необходимый для нагрева. Используя оборудование этого типа, можно контролировать нагреваемую деталь с очень жесткими допусками.
Некоторые из причин предварительного нагрева: :
a) Удаление влаги из области сварного шва: Обычно это выполняется путем нагрева поверхности материала до относительно низкой температуры, чуть выше точки кипения. воды.Это высушит поверхность пластины и удалит нежелательные загрязнения, которые в противном случае могут вызвать пористость, водородное охрупчивание или растрескивание из-за введения водорода во время процесса сварки.
b) Для снижения температурного градиента: Во всех процессах дуговой сварки используется высокотемпературный источник тепла. Между локализованным источником тепла и холодным свариваемым материалом возникает резкая разница температур. Эта разница температур вызывает дифференциальное тепловое расширение и сжатие, а также высокие напряжения в зоне сварки.Уменьшение перепада температур путем предварительного нагрева основного материала сведет к минимуму проблемы, связанные с деформацией и чрезмерным остаточным напряжением. Если предварительный нагрев не выполняется, между областью сварного шва и основным материалом может возникнуть большая разница в температуре. Это может вызвать быстрое охлаждение, что приведет к образованию мартенсита и вероятному растрескиванию при сварке некоторых материалов с высокой прокаливаемостью.
Термическая обработка после сварки
По разным причинам и для разных материалов используется ряд различных типов термообработки после сварки.
a) Термическая обработка после сварки чаще всего используется для снятия напряжений. Целью снятия напряжения является устранение любых внутренних или остаточных напряжений, которые могут присутствовать в процессе сварки. Снятие напряжения после сварки может быть необходимо для снижения риска хрупкого разрушения, предотвращения последующей деформации при механической обработке или устранения риска коррозии под напряжением.
b) Для некоторых легированных сталей может потребоваться термический отпуск для получения подходящей металлургической структуры.Эта обработка обычно выполняется после охлаждения сварного шва, но при определенных обстоятельствах может потребоваться выполнить эту обработку до его охлаждения, чтобы предотвратить растрескивание.
c) Очень грубые сварные конструкции стали, например, полученные с помощью электрошлакового процесса сварки, могут потребовать нормализации после сварки. Эта обработка улучшит крупнозернистую структуру, снизит напряжения после сварки и удалит все твердые зоны в зоне термического влияния.
г) Сплавы с дисперсионным твердением, такие как термообрабатываемые алюминиевые сплавы, иногда требуется подвергнуть термообработке после сварки для восстановления своих первоначальных свойств.В некоторых случаях используется только обработка старением, хотя полная термообработка на твердый раствор и обработка искусственным старением обеспечат лучшее восстановление свойств после сварки.
Когда сварочные операции включают предварительный нагрев и / или термообработку после сварки, важно, чтобы инспектор по сварке понимал эти требования, чтобы убедиться, что они выполняются правильно и с точки зрения соответствующих спецификаций и / или правил процедуры сварки. требования.
Исследование и объяснение термической обработки после сварки
Сварные швы часто подвергаются термообработке после сварки.(PWHT) Есть разные причины для этого и различные методы термообработки после сварки. Есть также определенные риски, связанные с PWHT. На этой веб-странице мы рассмотрим использование PWHT.
Во первых
мы рассмотрим различные виды термической обработки, а затем соотнесем
их при сварке.
The WelderDestiny Compass: еженедельная подписка на электронный журнал
Вы можете посмотреть прошлые выпуски “The WelderDestiny Compass”, щелкнув здесь.
Виды термической обработки
Два
различные материалы при воздействии одного и того же термического цикла потенциально могут
имеют существенно разные результаты по материалам. Термические обработки
поэтому обычно описывается с точки зрения воздействия, которое они окажут на
материал, а не тепловой цикл. Однако есть исключения из этого
правило.
Ниже
список типичных термообработок:
- Отжиг: Обычно это относится к обработке, необходимой для получения материала мягкое и безударное состояние. Для большинства материалов, например углеродистой стали, это будет означать очень высокую температуру, а затем очень сильное охлаждение. медленно до комнатной температуры.
- Закалка Anneal: Здесь снова делается попытка добиться «мягкой» структуры, но медленной круто было бы вредно для материала. Типичным для этого будет 300 серия нержавеющих сталей. (Также называется аустенитной нержавеющей сталью). нержавеющие стали не претерпевают существенных фазовых превращений в большая часть материала во время цикла термообработки, но может привести к образованию локально вредных фаз или частиц, когда он хранится в каком-то промежуточном температурные диапазоны в течение длительных периодов времени.Чтобы этого не случилось, материал быстро охлаждается (закаливается) от высокой температуры. (Обычно 1050 ° C) Это сокращает время, в течение которого материал остается при температуре. диапазон 500 – 850 ° C, где может наблюдаться образование границ зерен карбиды, которые серьезно снижают коррозионную стойкость материала. Этот вредный процесс называется сенсибилизацией.
- Решение Обработка: Основная цель этой термической обработки – убедиться, что все различные легирующие элементы равномерно распределены по материалу, и «Растворяется» в материале, насколько это возможно.Это часто выполняется на отливки, потому что процесс затвердевания во время отливки имеет тенденцию приводить к материал, имеющий относительно большие различия в некоторых легирующих элементах в разных частях конструкции. Как правило, бывают области с высоким концентрация одних элементов и низкие концентрации других элементов. От повышение температуры до точки, при которой происходит большая диффузия, эти неравномерные концентрации легирующих элементов выровняются. Определенные фазы (например, карбиды) также будут «растворяться» (переходить в раствор) материалом при эти высокие температуры.Чтобы сохранить как можно больше легирующих элементов в раствора, некоторые материалы обычно закаливают после обработки раствором. В этом случае это очень похоже на закалочный отжиг, описанный выше.
- Закалка Закалка: Для достижения высокой твердости некоторых материалов, таких как углеродистые стали и низколегированные стали, материал можно нагревать до температуры, выше которой фаза трансформации происходят в материале. (Обычно 950 ° C для углеродистой стали.) затем материал быстро охлаждается (закаливается) с образованием некоторых метастабильных фаз (для например, мартенсит), что обеспечивает высокую твердость материала.Когда материалы подвергаются закалке, они также обычно становятся хрупкими.
- Закалка: Для смягчения материала, который уже был затвердевшим в результате предыдущего нагрева. цикла (например, закалка), вы можете снова увеличить температуру материал до точки, ниже которой он начинает испытывать объемную фазу превращений (обычно нагревают до 650-700 ° C) и выдерживают там в течение промежуток времени. Во время этого цикла отпуска затвердевший мартенсит превращается в закаленный мартенсит не такой твердый и хрупкий, как закаленный мартенсит, но по-прежнему очень силен и вынослив.
- Закалка и Temper: Это комбинация двух описанных циклов термообработки. выше.
- Напряжение Разгрузка: При пластической деформации пластичных металлов они заканчиваются. с большим количеством остаточных напряжений в материале. Сварка также приводит к эти остаточные напряжения вокруг сварного шва. Увеличивая температуру металла предел текучести металла снижается. (Предел текучести – это напряжение, при котором материал начинает пластически деформироваться.) Когда доходность прочность снижается из-за высокой температуры ниже уровня остаточного напряжения, тогда материал «расслабится». Это снимает стрессы, которые были захвачены в материале в результате деформационных или сварочных работ. Углерод Стали обычно снимают напряжение при температуре около 600 ° C. На это температура, остаточное напряжение обычно снижается примерно до 30% от предела текучести. прочность материала при комнатной температуре. Основная причина стресса облегчение обработки состоит в том, что она улучшает вязкость разрушения компонентов.Это также снижает вероятность определенных механизмов коррозии, таких как стресс. Коррозионное растрескивание. (SCC)
- Нормализация: Обычно это выполняется с углеродистыми сталями, чтобы обеспечить безнапряженную, мелкую зернистая структура. Это достигается за счет взятия температуры выше температура, при которой происходит фазовое превращение в массе материала (обычно температура около 950 ° C), а затем дать ему остыть на неподвижном воздухе. От применяя эту обработку к обычным углеродистым / углеродистым марганцевым сталям, они будут разработать структуру, которая представляет собой очень хороший компромисс между прочностью и жесткостью.Это очень типичная термообработка стальных отливок, поковок и другие стали для получения мелкозернистой структуры.
- Осадки Отверждение: В некоторых материалах образуются очень мелкие частицы. внутри их структуры, если их температура повышена и поддерживается там в течение время. Эти маленькие частицы называются осадками. Наличие этих мелкие частицы укрепляют материал. Типичные осадки Цикл отверждения следующий: Температура материала доведена до точка, где будет проводиться «обработка раствора».Тогда материал «Закаливают», чтобы не образовывался осадок. Далее температура снова повышается (но до температуры ниже температуры раствора) который затем способствует образованию осадков. Это называется «старением». лечение. Важно отметить, что если температура слишком высока или слишком долго держаться на приподнятом уровне в течение этой части цикла, тогда материал будет «Старше возраста». Престарелый материал будет иметь меньшую твердость и прочность, чем тот, который был должным образом выдержан.Точно так же, если температура или время старения слишком низкий, то материал будет «не выдержанным», что снова приведет к меньшая твердость и прочность. Недостаточное старение – меньшая проблема, потому что вы можете просто увеличьте температуру снова, чтобы продолжить старение, до оптимального результат достигнут. Старение – гораздо более серьезная проблема, потому что это может быть только исправлено повторным выполнением всего цикла. (Из обращения с раствором.)
- Термомеханически Контролируемый процесс: (TMCP) Строго говоря, это не термическая обработка, как такие, но я думаю, что это хорошее место, чтобы обсудить это в ближайшее время.В TMCP сталь деформируется (например, прокатывается), одновременно испытывая температуры, которые недостаточно высоки, чтобы вызвать полные фазовые превращения и рекристаллизации, но не настолько низко, чтобы приводить только к холодной штамповке. Каждый сталелитейный завод имеет свою собственную последовательность температур и деформация для получения прочного материала, легко свариваемого. Стали TMCP имеют тенденцию иметь низкоуглеродные эквиваленты, оставаясь при этом очень прочными и выносливыми.
Есть
некоторые другие более специализированные термические обработки, которые иногда используются
при очень особых обстоятельствах, но для наших целей перечисленные выше
будут основными видами термической обработки, на которые следует обратить внимание.
Влияние сварки на материалы
Fusion
сварка связана с температурами, достаточно высокими, чтобы расплавить материалы,
присоединился. Таким образом, они вводят тепловой цикл, который приводит к
материалы, близкие к сварному шву, нагреваются до температур, близких к температуре плавления
точки, а материалы, находящиеся далеко от сварного шва, практически не увеличивают
температура.Другими словами, существует температурный градиент, испытываемый
материалы, которые варьируются от температуры окружающей среды до температуры плавления.
г.
часть основного металла, структура которого изменилась под воздействием тепла сварки
известна как зона термического влияния (HAZ) сварного шва. Материал, на котором
температура была недостаточно высокой, чтобы существенно повлиять на
материал просто называют основным материалом. Участок, оплавленный из-за
операция сварки называется наплавленным металлом.
г.
структура металла сварного шва будет зависеть от состава основного металла,
состав присадочного металла и эффекты, вызванные тепловым циклом. Как
по общему правилу мы можем выбрать присадочный металл, чтобы получить желаемый результат в пределах
металл шва. Однако с точки зрения композиции мы ничего не можем сделать, чтобы
зона термического влияния. (HAZ) Единственный эффект, который мы имеем в управлении
Структура ЗТВ предназначена для управления тепловым циклом.
Это
также должно быть очевидно, что тепловой цикл в ЗТВ будет иметь
значительное влияние на термическую обработку материала перед сваркой
операция.Например, некоторая часть ЗТВ основного металла углеродистой стали
будет повышена до температуры, выше которой происходят фазовые превращения в
стали. (Это называется критической температурой, и для обычных углеродистых сталей
это около 720 ° C.)
Когда
в последующем его охлаждают, снова будут фазовые превращения. Если
скорость охлаждения достаточно высокая, тогда мы можем испытать некоторую закалку
упрочнение в этой области, что приводит к твердой хрупкой структуре. Если охлаждение
достаточно медленный, то мы испытаем тепловой цикл, похожий на
нормализующая термическая обработка.Если скорость охлаждения очень низкая, то тепловая
Цикл будет напоминать цикл отжига стали.
Это
означает, что за счет изменения количества энергии, используемой при сварке, (также называемой
подводимой тепловой энергии) наряду с предварительным нагревом и последующим нагревом могут быть
достигается как в металле шва, так и в зоне термического влияния сварного шва.
Некоторые
материалы, такие как низколегированные стали, почти всегда приводят к закалке
структура внутри ЗТВ при сварке. Затем им требуется дополнительный нагрев после сварки.
Лечение (PWHT) для достижения желаемого результата.В случае нашего примера с
из низколегированной стали, они почти всегда нуждаются в закалке для достижения
подходящая прочная и жесткая микроструктура.
Некоторые
материалы достигают значительной прочности в результате холодной обработки.
Под холодной обработкой понимается пластическая деформация металла при температуре
ниже которого деформированные зерна металла будут рекристаллизоваться. Это лечение
приводит к увеличению прочности холоднодеформированного материала.
Когда
сварка холоднодеформированного (также называемого деформационным упрочнением) материала, части
ЗТВ будет испытывать достаточно высокие температуры, чтобы вызвать перекристаллизацию и
фазовые изменения.Это устранит холодную работу и потенциально уменьшит
прочность материала в ЗТВ значительно. Обратите внимание, что термообработка после сварки не может
обратить этот эффект вспять.
Это
разупрочнение часто наблюдается при сварке упрочненных алюминиевых сплавов. В
ЗТВ всегда будет значительно слабее, чем холодно обработанный основной металл. В
единственный способ эффективно справиться с этим эффектом – спроектировать компонент в
таким образом, чтобы сварной шов находился в области с меньшим напряжением, или основание
металл делается толще, чем требуется, вокруг области сварного шва, чтобы компенсировать
потеря силы.
г.
Другой способ упрочнения алюминиевых сплавов – это
осадочное твердение. Опять же, термический цикл сварки вводит
область в ЗТВ, которая не выдерживается, (Температура была достаточно высокой, чтобы вернуться
осаждается в раствор, после чего следует гашение из-за высоких скоростей охлаждения
обычно связаны со сваркой.) и области, которая изношена. (Температура
был выше, чем требуется для оптимального старения, но недостаточно для возврата осадков
в раствор.) Таким образом, сварка с дисперсионным твердым покрытием (также называемая состаренной)
материалы приведут к снижению прочности ЗТВ. Для небольших компонентов это
возможно подвергнуть весь компонент дисперсионному твердению
цикл, но в большинстве случаев, как правило, ничего нельзя сделать
чтобы исправить это снижение прочности в ЗТВ осажденного твердого
материал.
Стандартная термообработка после сварки (PWHT)
Пока
теоретически возможно выполнение любой из описанных термических обработок.
ранее как термообработка после сварки (PWHT) практически не использовалась
дело. Типичными являются следующие термические обработки после сварки:
- Напряжение Relieve: Сварка вызывает высокие остаточные напряжения в металлах в регионе. вокруг сварного шва. Это может привести к снижению характеристик вязкости разрушения и восприимчивость к механизмам коррозии, таким как коррозионное растрескивание под напряжением.(SCC) Снятие напряжения, вероятно, является наиболее часто выполняемой термообработкой после сварки, особенно на углеродистые стали и углеродистые марганцевые стали. Снятие стресса – это обычно код требование к оборудованию, работающему под давлением, более определенной толщины. (Каждый код имеет различные правила для определения того, когда требуется снятие напряжения.) Для углерода стали, снятие напряжений обычно составляет около 580 ° C – 650 ° C. Обратите внимание, что лечение для снятия стресса в более высоком диапазоне может уменьшить прочность стали TMCP.Если для сталей TMCP требуется термообработка после сварки, она должна предпочтительно делать в нижней части диапазона.
- Темперамент: Для низколегированных сталей и других материалов, которые естественно твердеют при сварке, a почти всегда требуется вспыльчивость. Температура отпуска может варьироваться в широких пределах, но для низколегированных сталей обычно составляет около 700–750 ° C. (Некоторые закаленные и закаленные микролегированные стали могут иметь значительно более низкий отпуск Обратите внимание, что при использовании температуры отпуска после термообработки выше этой основного металла ослабит основной металл.Поэтому отпуск после термообработки шва Рекомендуется быть примерно на 30 ° C ниже, чем состояние основного металла.
- Нормализация: Большинство крупных конструкций сложной формы не подлежат нормированию. PWHT. Причина в том, что материал становится настолько слабым при замачивании. температура (обычно 950 ° C для углеродистой стали), что он не может поддерживать конструкции и приводит к катастрофическому короблению и деформации. Нормализационная термообработка после сварки поэтому выполняется только на довольно простых компонентах, которые можно легко поддерживается.Типичным примером может быть сварной выпуклый конец для сосуда высокого давления, перед приваркой к самому сосуду.
Риски, связанные с термообработкой после сварки
Сообщение
Термическая обработка сварного шва (PWHT) сопряжена с риском. Ниже приведен список потенциальных
проблемы, которые могут возникнуть при выполнении термообработки после сварки.
- Убыток прочности: Чрезмерное время или слишком высокая температура для снятия напряжения после сварки термообработка может привести к снижению прочности материала.Закалка также может привести к снижению прочности закаленных и закаленные материалы. Поэтому время и температура должны быть хорошими. контролируется.
- Искажение или коллапс: Температуры снятия напряжений или отпуска приводят к получению материала что значительно снижает прочность при повышенных температурах. Если элемент конструкции испытывает некоторую нагрузку на него, то в процессе послесварочной термообработки цикл он может согнуться или деформироваться. Это могло иметь катастрофические и высокие затраты. последствия.Поэтому важно убедиться, что все конструкции подверженные воздействию высоких температур, должным образом поддерживаются. Кроме того, если один часть конструкции испытывает значительно более высокие температуры, чем другие разделы, разница в тепловом расширении также может привести к серьезным искажения конструкции. Такая ситуация обычно возникает, когда кожухотрубные теплообменники подвергаются термообработке для снятия напряжений после сварки, когда температура оболочки повышается и понижается намного быстрее, чем трубки.Важно следить за тем, чтобы не было чрезмерных температур. градиенты или различия во время операции термообработки после сварки. Для этого необходимо иметь достаточное количество термопар, прикрепленных к компонентам, чтобы гарантировать недопустимость температурных градиентов не бывает. В некоторых печах также могло быть потенциальное попадание пламени в некоторые места на судне. Это могло, это может локально увеличить температуру до значений выше фазового превращения температура, (более низкая критическая температура), что приводит к неожиданным фазовым изменениям а также изменения громкости.Они могут не только снизить механические свойства, но и привести к деформации. Чтобы этого не произошло, там должны быть эскизы загрузки печи, показывающие, как будет происходить попадание пламени предотвращены, и также должны быть размещены термопары в местах ближе всего к горелкам газовых или мазутных печей.
- Охрупчивание или растрескивание: Некоторые плавки материал может содержать микроэлементы, которые делают его восприимчивым к «закалке». охрупчивание ». (Обычно хром) Во время операции термообработки после сварки некоторое количество интерметаллических могут образовываться очень хрупкие фазы, приводящие к значительному и потенциально катастрофическое охрупчивание компонента или конструкции.Для обеспечения что этого не произойдет, материалы следует закупать с испытанием на образцы, которые были подвергнуты моделированию цикла термообработки после сварки. Некоторые стальные компоненты могут также иметь некоторое количество остаточного аустенита в своих структурах из-за их предыдущие термические обработки. После термообработки после сварки этот остаточный аустенит может превратиться в мартенситоподобная структура, хрупкая. Коды обычно требуют, чтобы окончательный контроль и неразрушающий контроль (NDT) должны быть выполнены после термообработки после сварки. операции, чтобы обнаружить любые дефекты, которые образовались во время операции PWHT.Твердость Испытания после термообработки после сварки также помогают определить, не произошло ли затвердевания. произошла во время послесварочной термообработки. (Обратите внимание, что не все механизмы охрупчивания связаны с более высокой твердостью металла.)
Методы термообработки после сварки
Есть
это 3 типичных метода применения тепла для термообработки после сварки. Это следующие методы:
- Печь: При термообработке после сварки в печи весь компонент обычно помещен в печь, и температурный цикл применяется ко всему составная часть.Очевидно, это означает, что компонент или структура не должны быть такими. большой, что не помещается в топку. Также компонент необходимо переместить в где находится топка. Для работ по техническому обслуживанию или для длинных, громоздких форм компонентов, это часто непрактично. Основное преимущество этого вида термообработки после сварки это переменное расширение, вызванное чрезмерными температурными градиентами (разные температуры в различных частях компонента) можно свести к минимуму. К при этом важны скорости нагрева и охлаждения, так как более толстые секции будут обычно требуется больше времени для нагрева или охлаждения, чем для более тонких секций.
- Внутренний обжиг: В этом методе компонент изолирован снаружи, а тепло вводится внутрь компонента, пока весь компонент не нагреется до необходимой температуры. Тепло обычно вводится газовыми горелками. горелки. Очевидно, это подходит только для компонентов «полого» типа, таких как сосуды под давлением. К тому же это довольно дорогой вариант, связанный с рисками. с соответствующей изоляцией и защитой от пламени горелок.
- Местное внешнее нагревание: Этот метод термообработки после сварки подходит для удлиненных компонентов, которым требуется только нагревание на определенных участках, а не весь компонент.Это типично для кольцевых сварных швов на трубопроводы или закрывающие сварные швы на длинных сосудах высокого давления. В этом методе какой-то элемент вводит тепло снаружи компонента (иногда элементы размещаются внутри и снаружи для обеспечения равномерного нагрева) обычно в обвязка по всей окружности компонента. Подходящая изоляция сохраняет тепло из-за потери тепла с поверхности из-за конвекции и излучения. Однако тепло теряется из-за теплопроводности к неотапливаемым частям составная часть.Поэтому важно контролировать температурные градиенты от области, испытывающие PWHT, до областей, которые все еще остаются «холодными». Если это не так Если все сделано аккуратно, переменное тепловое расширение может фактически привести к появлению остаточных напряжения в зонах, прилегающих к зоне термообработки после сварки, которые можно просто переместить проблему из одного места в другое.
Источники тепла для термообработки после сварки
В зависимости
Что касается метода применения тепла во время термообработки после сварки, существует ряд различных терминов.
источники.Типичные источники тепла:
- Газ или нефть Горелки: Обычно используются в больших печах или при выполнении внутренний обжиг компонента. Основная проблема в том, что горелки потенциально может столкнуться с компонентами, что приведет к возникновению «горячих точек», где температура слишком высока по сравнению с остальной частью компонента. Печь поэтому планировку необходимо тщательно спланировать, чтобы убедиться, что это не случаться. Как правило, дополнительные термопары применяются в области, где возможно попадание пламени во время термообработки после сварки.
- Электрооборудование Нагревательные элементы сопротивления: Они часто используются для местной термообработки после сварки. составные части. Они имеют форму матов, имеющих электрическое сопротивление. проволока «сплетена» через керамические бусины. Эти «тепловые шарики» затем прикрепляются к поверхность, подлежащую послесварочной термообработке. Часто их просто держат на месте при помощи стальной проволоки. При использовании этих нагревательных элементов элементы размещается на поверхности металла, а вокруг снаружи, чтобы сохранить тепло.
- Индукционный нагрев: В этом источнике тепла элемент (часто просто кабель, намотанный на трубу) имеет высокую частоту через него проходит переменный электрический ток. Этот переменный ток приводит к возникновению магнитного поля вокруг элемента. Магнитное поле в свою очередь приводит к образованию вихревых токов в металле. Затем вихревые токи приводят к резистивный нагрев в металле. По сути, металл, подвергающийся воздействию тепла после сварки. лечение фактически является нагревательным элементом. (Это работает почти так же, как индукционные плиты для приготовления пищи.) У этого источника тепла есть номер преимуществ. Во-первых, это обычно приводит к гораздо более быстрому нагреву. чем использование горелок или электрических нагревателей сопротивления. Второе преимущество заключается в том, что нагревательные спирали можно устанавливать вокруг внешней стороны изоляции. который помещается напротив металла, чтобы удерживать тепло. Это означает, что элементы не подвергаются воздействию высоких температур, поэтому система более надежна. Третье преимущество состоит в том, что эта система в целом более энергоэффективна, чем Метод электрического резистивного нагрева.Есть и недостатки. Во-первых, сильные магнитные поля могут мешать некоторым контрольно-измерительные приборы, а также есть некоторые опасения относительно долгосрочной безопасности аспекты. Если у вас есть кардиостимулятор, вы, скорее всего, не захотите вешать вокруг этого типа оборудования во время его работы. Другой недостаток – что если что-то пойдет не так с элементом управления, это будет намного проще материал должен быть сильно перегрет до того, как оператор поймет, что система вышла из-под контроля.Это можно смягчить, убедившись, что есть достаточно «запасных» термопар, так как проблема чаще всего возникает при управлении термопарами. вылететь из компонента.
Кодекс требований к термообработке после сварки
Как
Как правило, производственные нормы определяют, когда требуется термообработка после сварки, а
особый цикл термообработки после сварки. Они также обычно устанавливают требования с точки зрения
методы, которые можно использовать, а также максимальные скорости нагрева и охлаждения и
максимально допустимые температурные градиенты.Примеры таких кодов: ASME
VIII, BS 5500 или AS 4458 для сосудов под давлением и ASME B31.3 или AS 4458 для
трубопровод.
Есть
также другие руководящие принципы и рекомендуемые практические документы, которые помогают в
обеспечение правильного выполнения послесварочной термообработки. Широко используемый документ в этом
Следует учитывать AWS D1.10, рекомендуемый для местной термообработки труб после сварки.
Заключение по послесварочной термообработке
Сообщение
Термическая обработка сварных швов (PWHT) сама по себе является специализированной областью со многими
технический персонал, специализирующийся на эксплуатации оборудования и печей для послесварочной термообработки.Если ты
заинтересованы в такой работе, тогда найдите компанию в
в вашем районе, где выполняется такая работа, и посмотрите, могут ли они предложить вам работу. Большинство
в большинстве случаев эти компании также предоставят вам необходимое обучение.
для работы со своим конкретным оборудованием.
Другой
техническая проблема заключается в сравнении различных циклов PWHT. Поскольку это
немного технически подробный предмет, я рассмотрел его на веб-странице его
собственный. Нажмите здесь, чтобы увидеть, насколько разные
циклы термообработки можно сравнить.
The WelderDestiny Compass: еженедельная подписка на электронный журнал
Вы можете посмотреть прошлые выпуски “The WelderDestiny Compass”, щелкнув здесь.
Исследование влияния термообработки после сварки на сталь, прокатываемую для трубопроводов с термо-механическим контролем | IPC
Практические варианты прокладки новых или измененных трубопроводов часто ограничены, что в некоторых случаях может привести к строительству трубопроводов в потенциально сейсмических или оползневых зонах.Дизайнеры выступили за использование толстостенных труб в этих областях; с потенциальным требованием к термообработке кольцевого шва после сварки (PWHT) для снижения остаточных напряжений и закалки любых твердых микроструктур, образующихся во время строительной сварки.
Большая часть высокопрочных толстостенных труб производится с использованием стального листа с термомеханической обработкой (TMCP). Принято считать, что эти стали не предназначены для последующей термообработки и могут иметь некоторое ухудшение своих механических свойств при повторном нагреве выше критических температур.В ряде стандартов, спецификаций и технических публикаций признается влияние PWHT на механические свойства листа TMCP, но дается ограниченное руководство по тому, как это повлияет на свойства. Другие относятся непосредственно к вредному воздействию, например BS 4514-1, в котором говорится, что «при проведении PWHT может потребоваться проверка свойств трубы и сварных соединений, подвергшихся термической обработке» и EN10208-2, в котором говорится «Последующий нагрев материала TMCP выше 580 ° C может снизить прочность».
Реакция на PWHT двух сталей для трубопроводов TMCP, используемых в газотранспортной сети Великобритании, была исследована, чтобы подтвердить, происходит ли ожидаемое ухудшение свойств, и попытаться количественно оценить масштаб любого эффекта. Испытываемым материалом трубы был L450MB и L555MB (эквивалентный классу API5L X65 и X80) с размерами 1219 мм × 25,4 мм и 1219 мм × 22,9 мм соответственно, изготовленных с использованием процесса UOE и дуговой сварки под флюсом. Кольцевые сварные швы были изготовлены с использованием ручного процесса сварки металлической дугой в Национальном центре технического обслуживания трубопроводов сети в Великобритании.
Параметры PWHT были выбраны так, чтобы представлять верхний предел температурного и временного диапазонов, доступных в существующих стандартах и литературе, теоретически проверяя наихудший сценарий с точки зрения любого возможного вредного воздействия.
Проект включал подробную программу испытаний трубы, продольного и кольцевого сварных швов как в состоянии после сварки, так и после послойной термообработки. В документе описаны проведенные испытания и полученные результаты.
Механические свойства труб обоих сортов соответствуют минимальным требованиям соответствующих спецификаций после термообработки.Однако наблюдался общий вредный эффект PWHT, наиболее значительный для материала L555MB и особенно для продольного шва. Величина любого эффекта считается функцией химического состава материала, параметров TMCP, сварочных материалов и параметров PWHT. PWHT на материалах труб TMCP должна быть ограничена. Если невозможно избежать PWHT, следует провести испытания конкретного материала, чтобы четко определить величину любого ухудшения свойств при предлагаемой температуре PWHT и тепловом цикле.
Нержавеющая сталь и PWHT – Термическая обработка после сварки – AMARINE
Большинство сварных деталей из аустенитной нержавеющей стали не требуют термообработки после сварки. Для тех, кто это делает, температура термообработки должна отражать конкретную проблему, которая решается.
Необходимость термической обработки сварных соединений из аустенитной хромоникелевой стали в любом виде во многом зависит от условий эксплуатации. Для некоторых применений термическая обработка используется для придания максимально возможной степени коррозионной стойкости, например, путем обработки раствора для гомогенизации композиции или стабилизации, чтобы минимизировать риск сенсибилизации во время последующего воздействия повышенных температур.
В других применениях для снятия напряжений может использоваться термическая обработка. Это может обеспечить большую стабильность размеров деталей, подлежащих механической обработке, или снизить склонность к растрескиванию под напряжением (SCC) / растрескиванию при повторном нагреве. Для стабильности размеров достаточно низкотемпературной обработки при температуре около 400 ° C, дающей частичное снятие напряжений. Для устойчивости к SCC может оказаться целесообразным использовать обработку при более высоких температурах, около 1000 ° C, чтобы снять большую часть внутреннего напряжения.Тяжелые секции некоторых нержавеющих сталей (например, стабилизированные марки, такие как тип 347), работающие в диапазоне температур ползучести, могут растрескиваться при повторном нагреве, и снятие напряжений (> 950 ° C) – единственный гарантированный способ избежать этой проблемы.
Для полного отжига на твердый раствор (> 1000 ° C), если требуется быстрое охлаждение в течение части цикла охлаждения, чтобы избежать недопустимого осаждения, следует отметить, что это создаст новые напряжения значительной величины.