Потери при резке металла: Отходы при резке металла на заготовки
alexxlab | 05.02.2023 | 0 | Разное
Норма раскроя металла: определение, коэффициент, нюансы расчета
Из этого материала вы узнаете:
- В чем суть технологии раскроя металла
- Какие существуют способы раскроя металла
- Что такое норма раскроя металла
- Как рассчитывается коэффициент раскроя металла
Технологическая операция раскроя металлических листов – одна из самых важных в процессе изготовления конструкций из металла. Чтобы продукция была оптимальной по стоимости и качеству, очень важно соблюдать все режимы этой операции. Конструкторы постоянно предлагают все новые технологии для раскроя профилей и листов из металла. О том, какая должна быть норма раскроя металла, вы узнаете из нашей статьи.
Технология раскроя металла
Создание металлоконструкций начинается с заготовительных этапов, одним из которых является раскрой листового и профильного металла. Именно эта стадия определяет всю дальнейшую работу. Производственные комплексы и машиностроительные предприятия имеют в своем составе цеха, где заготавливают детали будущих конструкций. Эти специализированные подразделения оснащаются разными станками и комплектами оборудования, предназначенного для раскроя.
Под раскроем листового металла следует понимать способ распределения деталей на металлических листах.
По форме заготовки могут быть прямоугольными или с другими очертаниями. Основной задачей конструкторов и технологов является уменьшение количества отходов производства. Существуют возвратные и невозвратные отходы, причем их объемы зависят от применяемых методов раскроя.
Наиболее распространенные способы раскроя металла
1. Метод гильотины
Сегодня на рынке представлено разнообразное оборудование, позволяющее резать металл толщиной 0,45–2,5 мм с помощью простого металлического устройства, для резки листов до 20 мм применяются электрические или пневматические гильотинные ножницы.
Например, недорогая механическая гильотина применяется при раскрое листов металла в строительной отрасли. Ее используют в компаниях, занимающихся производством кровли из оцинкованных листов или металлочерепицы, откосов, сливов, различных доборных элементов.
Различные виды гидравлических, пневматических и электромеханических гильотин находят применение в технологических циклах изготовления листового проката, для отрезания одинаковых листов профиля и при раскрое рулонов из металла. Только нужно учитывать, что гильотина может отрезать исключительно по прямой линии.
Рекомендуем статьи по металлообработке
- Марки сталей: классификация и расшифровка
- Дефекты металлический изделий: причины и методика поиска
2.
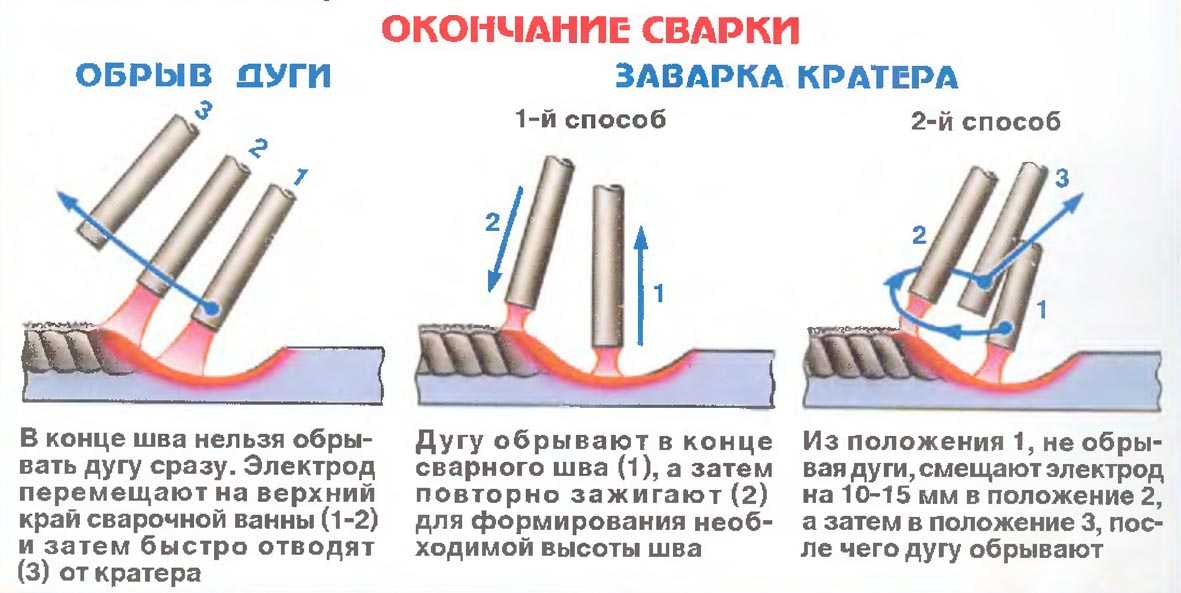
Самым известным и востребованным инструментом, способным справиться с разными задачами, которые, однако, не относятся к высокоточным, можно назвать переносную углошлифовальную машинку «болгарку». На стационарных пилах большого диаметра можно добиться большей точности, поэтому их применяют для выпуска мелких серий деталей из металла. Это оборудование подходит для раскроя металла толщиной до 8 мм. Преимущество подобного вида обработки – в возможности резать материал под разными углами, но для заготовок криволинейной формы такие пилы не используют.
3. Обработка на просечном прессе
Просечные прессы, имеющие разную мощность, устанавливают в цехах металлообработки промышленных предприятий. Их применяют для выпуска деталей из алюминия для монтажа металлоконструкций или на завершающем этапе производства просечно-вытяжных листов.
4. Газокислородное оборудование для резки
Высокая производительность этого оборудования делает его одним из самых популярных видов, используемых при раскрое металлических листов. Оно находит применение в большинстве промышленных отраслей, однако режет лист с излишне широким резом, оставляя окалину и неровные края. Также его нельзя применять для резки тонкого листового проката.
Вышеперечисленные методы обладают общим свойством – они одинаково обрабатывают черный и цветной металлы, а также нержавейку. Исключением можно считать обработку алюминиевых листов газокислородным оборудованием.
5. Использование плазмореза при раскрое металлопроката
При раскрое с помощью плазмореза происходит интенсивное нагревание листа электродугой по линии реза и удаление расплавленных частиц потоком плазмы. Высокотемпературная резка металла осуществляется режущим потоком ионизированного газа (в пределах +15 000…+30 000 °С) и поэтому имеет высокую скорость обработки. Этот метод раскроя металла является самым эффективным.
Высокая точность – это не единственное достоинство работы плазмореза, перечислим еще несколько:
- с его помощью можно проводить раскрой сложных деталей, включая шаблонную резку;
- при обработке лист металла не деформируется;
- точность контуров у изделий одного типа, допустимое отклонение линии реза – 0,5 мм;
- метод относится к экологичным и безопасным;
- плазморезом можно обрабатывать черный и цветной металл, нержавейку разной толщины.
Плазменную резку применяют при обработке таких материалов, как:
- алюминиевый прокат, имеющий толщину до 120 мм;
- медь и сплавы (бронза) с толщиной до 80 мм;
- легированная сталь, не превышающая 50 мм в толщину.
6. Лазерное оборудование для раскроя листового металла
Лазерное излучение с точной фокусировкой и высокой плотностью тепловой энергии обеспечивает высокоточный раскрой металла, при этом остается минимальное количество отходов. Технология полностью автоматизирована и роботизирована. Перед работой специалисты подготавливают электронный чертеж с точной разметкой, и далее лазер выполняет раскрой металла согласно заложенной программе.
Лазерная резка имеет нижеперечисленные преимущества:
- возможность изготовления деталей с любым криволинейным контуром;
- соблюдение норм раскроя и экономный расход металла, так как между деталями на листе остаются минимальные зазоры;
- во время резки детали не подвергаются деформации, так как отсутствуют механическое и длительное термическое воздействия, нет цветов побежалости;
- шероховатость минимальная, кромка четко перпендикулярна.
Что значит норма раскроя металла
Что такое норма расхода? Четкая и точная формулировка звучит так: «Это такое количество материала (нас интересует прежде всего металл), которое необходимо для создания единицы продукции».
Итак, чтобы производитель выпустил любую деталь, он должен рассчитать норму расхода или количество металла для ее изготовления.
Иногда можно встретиться с одним очень распространенным заблуждением. Часто заказчики рассчитывают на точную норму расхода, чего в принципе не может быть. Количество реально израсходованного металла всегда будет отличаться в большую сторону.
Здесь нет никакого обмана. В любом случае надо понимать, что на расчет нормы раскроя металла влияет множество факторов, и эти цифры всегда будут среднеарифметическими. Расчетная величина не будет соответствовать фактическому количеству материала по той причине, что в разное время его расход отличается.
В этой задаче не так просто разобраться. Очень часто бывает, что на листе могут быть разложены детали самой разной формы, и как тут высчитать, какое количество металла пошло на изготовление конкретного изделия. Мы не берем сейчас тот вариант, когда заготовки имеют простую форму прямоугольника и занимают почти весь лист. Можно много рассуждать на эту тему, главное, вы должны понять, что на величину нормы расхода на одну деталь оказывают влияние следующие факторы:
- количество заготовок, разложенных на листе, и насколько оптимально они разложены;
- будет ли использоваться оставшаяся часть листа для раскроя других деталей.
В разных ситуациях значения могут сильно различаться, даже в несколько раз, особенно если требуется раскрой деталей сложной формы, с выемками и отверстиями.
Расчет нормы при раскрое деталей из профильного металла, например, различные уголков, швеллеров, труб и других изделий, происходит по такому же принципу. Только отличие в значениях не так велико. Ведь при линейном раскрое технология проще, чем при двухмерном. Но и здесь раскладка может меняться, и обрезков бывает достаточно много.
Некоторым особо дотошным любителям точности можно еще указать на нормы ГОСТов, в которых можно увидеть, что существуют определенные допуски и отклонения в размерах и весе деталей каждого наименования. А фактически, если начать перемерять все детали одного типа даже с одного производства, то разницу все равно увидим и в размерах, и в весе. Также не следует забывать о точности измерительных приспособлений. Это касается в первую очередь весов для измерения металла.
Исходя из этого, можно быть совершенно уверенным в том, что, выполняя в соответствии с чертежом раскрой одной и той же детали в разное время, цифры фактического количества металла будут отличаться друг от друга. Дальше уже надо смотреть, как сильно расходятся значения. Нестрашно, если речь идет о допустимых погрешностях измерения. Но нужно учитывать, что влияние оказывают разные факторы, например, тип производства.
О норме расхода можно сказать, что это не характеристика какого-то конкретно произведенного изделия или заготовки, оно относится к общим понятиям. Норматив можно установить еще до момента запуска производства любой детали. Поэтому и нельзя говорить о какой-то абсолютной точности расхода при раскрое металла. Эта величина всегда будет отражением средних значений расходования металла на одну изготовленную деталь.
Коэффициент раскроя металла: норма и другие нюансы
Для учета расходования материалов на производстве используют коэффициент раскроя. Для его расчета нужно разделить общую площадь или длину изготовленных деталей на общую площадь или длину всего использованного металла.
Для расчета норм расхода листовых материалов высчитывают чистую площадь деталей. Вместе с коэффициентом раскроя при Н. р. м. применяют следующие частные показатели: коэффициент использования детали, показатель использования штамповки и др.
На коэффициент Кн влияет выбранная форма заказа металла и использованная технология раскроя.
Расчет различных показателей и норм расхода металла и других расходных материалов необходим для оценки эффективности производства. Всегда определяют и сравнивают цифры по плану и по факту. Основными характеристиками являются значения коэффициентов раскроя и использования, расходного коэффициента выхода продукции или заготовки, коэффициента, определяющего извлечение детали из исходного металла.
При вычислении коэффициента использования берут две цифры − полезный расход металла и норму расхода для производства данной детали − и определяют их соотношение.
К примеру, деталь весит 16 кг, установленная норма раскроя 16 кг, высчитываем значение коэффициента использования – 12 делим на 16, получится 0,75. Из этого становится понятно, что четвертая часть металла или 25 % стали отходами. Также необходимо высчитывать значение расходного коэффициента, для этого берут норму расхода металла или другого материала, принятую для изготовления одной детали, и полезный расход. Этот коэффициент является обратным предыдущему.
Чтобы вычислить значение коэффициента раскроя, нужно определить массу (объем, площадь и длину) всех изготовленных из данного металла деталей и поделить на объем (площадь и т. д.) израсходованного сырья. Например, взято 5 м2 металла, из него произвели 4 м2 заготовок, значение коэффициента 0,8 получим из отношения 4 к 5. Также можно сказать, что уровень расходования составил 80 %.
Чтобы рассчитать значение коэффициента раскроя листов металла qf, нужно найти, как соотносятся между собой общий вес (площадь) деталей BЗ и вес (площадь) исходного листа Вл, формула выглядит так <7Р = Вв Вл.
Для расчета коэффициента раскроя определяют отношение двух величин: первая − полезная площадь используемого сырья, вторая – норма площади для этого количества заготовок.
Задание на изготовление выдается в виде подетальных карт с разметкой всех деталей. Материалы могут быть различные: листы из металла, профиль, пруток, трубы, поковки и отливки, а также пиломатериалы и пластмассы. В отдельном порядке на особых картах определяют разметку для изготовления изделий групповым раскроем.
Карта раскроя представляет собой план-заказ с указанием:
- размеров листовых материалов, наиболее подходящих для вырубки данных деталей;
- габаритов всех будущих деталей, при этом учитываются припуски на обработку;
- количества и веса изделий, веса и характера отходов, а также нормы расхода материалов и коэффициента использования.
Исходя из данных, представленных в подетальных картах, в дальнейшем рассчитывается месячная потребность участков и цехов в материале, составляются цеховые поузловые материальные карты и цеховые карты применяемости материала.
Засоренность или технологические потери металлолома — Портал о ломе, отходах и экологии
Содержание:
- Подготовка металлических отходов
- Засоренность металлолома
- Далее
- Частные случаи переработки
- Переплавка отходов
Сдаваемый металлолом непригоден для промышленного использования без предварительной обработки. Чтобы подготовить отходы металла к переплавке, необходим отдельный технологический процесс приводящий лом в состояние пригодное к применению в металлургии, литейном производстве. На каждом этапе подготовительном и промышленном, неизбежными являются технологические потери металлолома.
Подготовка металлических отходов
Предварительная переработка металлолома зависит от типа металла: цветной или черный, а также определяется видом: трубы, радиаторы; и состоянием: кусковые отходы, цельные, легковесные конструкции.
Еще одним фактором технологических потерь металлолома выступает засор – степень присутствия в отходах неметаллических элементов, а также металлического лома других категорий. Допустимая величина засоренности лома черных металлов указывается отдельно для каждой категории металлолома на пунктах приема. Помимо естественного, существует технологический засор, как следствие переработки металла, резки. Средняя его величина составляет 5%.
к содержанию ↑
Засоренность металлолома
Что такое засоренность? Засоренность, фактически, и есть те самые технологические потери, заложенные при переработки металлолома. То есть, какой-то процент металлолома в любом случае будет потерян при разделки, сортировки, переплавки в печи.
Металлолом в такой партии будет с засором не более 7%
Также процент засоренности металлолома в несколько процентов ставит и сам пункт приема металлолома, который закладывается на грязь, неметаллические материалы и т. д. В данном случае засор устанавливается опытным путем и для каждой партии может быть разным, например:
- если сдается автомобиль на металлолом (полностью в сборе, с колесами, салоном, стеклом и т.д.), то процент засоренности может доходить до 30%;
- если сдаются трубы из земли, в гудроне и грязью внутри, то засор может быть 30-40%;
- принимая холодильники, стиральные машины – засор ставят также не менее 30%;
- зимой может ставиться большой процент засора из-за наличия снега и льда в металле;
- и т.д.
Как же считается засоренность лома? Если говорить честно, то процент засора ставит мастер-приемщик исходя из опыта плюс 1-2 процента для страховки. Минимальный процент засора, который будет установлен абсолютно в любом пункте приема металлолома – это 5%. И на такие категории лома, как чугун, 3А, 5А, 12А – т.е. самые распространенные, засор будет 5-7%, в зависимости от пункта приема лома и состояния металла. На такой вид лома, как железнодорожный металлолом засор ставится не больше 3%.
Вся информация о засоре изложена в ГОСТ 2787-75 лом черных металлов -показатели качества вторичных металлов по их составу, степени чистоты, габаритам и массе должны соответствовать требованиям, указанным в таблице ГОСТа.
Никакой формулы для расчета засора нет, вот часть информации из ГОСТа:
Определение засора цветного лома также осуществляется с помощью ГОСТа в данном случае на помощь придут документы ГОСТ 1639-2009 и ГОСТ Р 54564-2011.
Также смотрите статью – ГОСТ Р 54564-2011 — описание и отличие от ГОСТ 1639-2009.
к содержанию ↑
Далее
Подготовка к переплавке происходит с учетом происхождения металлолома. Также она зависит от конкретного состояния отходов, производясь одним из следующих способов:
- пакетирование;
- резка;
- дробление;
- переплав;
- термическое измельчение.
При необходимости отдельно выполняется процедура пиротехнического контроля, распространенная для контроля степени безопасности отходов цветных металлов.
к содержанию ↑
Частные случаи переработки
Предварительная переработка позволяет снизить уровень технологических потерь металлолома во время его переплавки. Например, пакетирование понижает расходы на угар. Данный вид обработки металлических отходов является одним из наиболее распространенных. Он используется при обработке:
- проволоки, стружки;
- бытового лома;
- прочих металлоконструкций.
Используемые специализированные прессы сжимают отходы металлов одновременно в трех плоскостях, производя прочные компактные пакеты.
см. статью – Лом черных металлов плотность
Дробление используется для переработки стружки, а также списанных автомобилей. В последнем случае эффективность дробления вызвана тем, что позволяет сепарировать отходы цветных и черных металлов, что также снижает процент технологических потерь.
Резка металлолома газом
Огневая и механическая резка используются при разделке крупногабаритного лома. Второй вариант, с применением гидравлических ножниц обладает наибольшей эффективностью. Его производительность на порядок превосходит огневую резку, тогда как процент расходов минимален. Огневое разрезание металлов выполняется электродуговым способом или с помощью горелок: газовых или керосиновых. Электродуговая резка более производительная, однако характеризуется высоким уровнем потерь – до 20%, тогда как данная величина при использовании горелок не превышает 3%.
к содержанию ↑
Переплавка отходов
Основными видами технологических потерь металлолома при его нагреве выступают угар и окалина.
Наблюдаемое снижение массы металла в результате угара может достигать 5% от исходной величины и зависит от продолжительности нагрева. Для понижения эффекта от угара используется интенсификация нагрева металла, сокращающая время переплавки. Оптимальный температурный режим определяется конструкцией оборудования, а также формой заготовок.
индукционная плавка стали
Окалина – следствие окислительных процессов на поверхности металла. Потери в этом случае достигают 3% исходной массы и существенно возрастают вследствие неравномерного нагрева.
Чтобы компенсировать угар и окалину при переплавке используют такие методики, как нагрев в нейтральной среде. Также эффективными способами снижения потерь является индуктивный и контактный нагрев, позволяющие минимизировать их до уровня 0,5%.
где тратится 15,9% сырья?
В производстве листового металла традиционные производственные процессы начинаются с металлических листов с помощью машин для штамповки и лазерной резки. Образующийся при этом брак может достигать 15% и более: детали, вложенные в листы, оставляют каркас, используемый в качестве опоры, который впоследствии необходимо утилизировать.
В этой статье я покажу, как внедрить альтернативные и современные производственные технологии, которые начинаются непосредственно с металлических рулонов, представляя реальный случай, когда один производитель имеет сэкономил 95 200 евро в год на сырье, внедрив линию штамповки / лазера с подачей рулонов всего для 10 изделий из своего производства.
Я также покажу, как адаптировать правило Парето для определения правильных статей, на которых следует сосредоточиться, отраслей и типов продуктов, которые получают выгоду от этой экономии, понимания производственной логистики и размера производственных партий.
Спасибо, что поделились этой статьей. Перейдите по ссылке, чтобы получить дополнительную информацию о линиях пробивки рулонов и лазерной резки.
Пример из практики: Elleci Spa и влияние сырья на себестоимость продукцииСамый простой способ объяснить, как рулонное производство влияет на конечный результат, — показать, как одной компании удалось получить прибыль от перемещения 10 изделий из листа. сматывать питаемые линии.
Elleci Spa – производитель с более чем 40-летним опытом производства листового металла: они работают в северной Италии, и их производственные мощности расширяются от револьверной пробивки до систем лазерной резки, листогибочных прессов и листогибочных станков, профилегибочных и штамповочных линий, линий с подачей рулонов. линии пробивки и лазерной резки, системы роботизированной сварки и завод порошковой окраски. Они предоставляют своим клиентам комплексное обслуживание, включая проектирование деталей для производства, производство, сборку и упаковку продукции с оригинальной упаковкой клиента.
Следующие данные предоставлены компанией Elleci и взяты из расчета окупаемости инвестиций в линию пробивки рулонов и лазерной резки.
Прежде всего, Elleci выбрала товары, которые с учетом их годового количества легко поместились бы в линию подачи в рулонах. Вот подборка из 10 кодов и годовых объемов производства за одну смену.
На втором этапе они проанализировали, сколько деталей помещается в лист стандартного размера.
Следовательно, Elleci рассчитал количество брака для каждого изделия. Elleci обрабатывает рулоны с точной шириной детали, поэтому количество брака составляет от 2 до 3%. На следующем рисунке показано, как оптимизируется материал в листе стандартного размера и в рулоне, нарезанном по ширине.
При производстве прямоугольного изделия на листе стандартных размеров детали укладываются на поверхность металлического листа. Однако их позиционирование должно учитывать ограничения, связанные с положением захватов, а оптимизация материала зависит от размера листа и продукта.
Когда мы работаем с катушкой стандартного размера, у нас внезапно появляется возможность оптимизировать длину, чтобы она соответствовала точному количеству прямоугольников.
Максимальная оптимизация материала происходит в третьем случае, когда панели укладываются в рулон, разрезанный точно по размеру панели.
Сравнительная таблицаВ случае Elleci изделия из листа имеют следующий процент брака:
В среднем при производстве этих 10 кодов из листа брак составляет 15,9% . В следующей таблице представлен процент брака по каждому изделию.
В рулонном производстве Elleci имеет крошечный 2-3% брак: в результате экономия материала составляет 78,8 тонн за одну смену, что соответствует 47600 евро. Имея станок для работы в две смены, Elleci имеет общий доход в размере 95 200 евро в год 90 006 только за счет экономии сырья.
В этом конкретном случае Elleci использует в своей мастерской различные технологии для управления производством: револьверные пробивные прессы, системы лазерной резки, перфорационные и лазерные линии с подачей рулонов.
При принятии решения о том, какой продукт запускать из рулона, важно искать изделия с более высокими производственными циклами и правильной геометрией.
Можно применить правило 80/20 к производству листового металла: «есть 20% изделий, которые используют 80% листового металла, обработанного в цехе». Именно на этих изделиях следует сосредоточиться, чтобы рассмотреть вопрос о переносе их на линию по производству рулонов.
В остальных 80% изделий используется только 20% листового металла: это детали с меньшими производственными циклами, меньшими количествами и большей изменчивостью, где предпочтительнее работать с листами.
Elleci — мастерская по изготовлению листового металла со средними и крупными производственными циклами: на самом деле ее деятельность больше напоминает OEM, чем мастерскую.
Фактически, компании, которые больше всего могут извлечь выгоду из преимуществ высокой производительности и экономии материалов на линиях с подачей рулонов, являются OEM-производителями: благодаря их более высокой специализации можно сосредоточить и управлять 80% производства непосредственно из рулонов. .
Размер партий также важен. При работе на собственной производственной линии можно организовать производство партиями более 400-500 деталей: таким образом можно полностью перерабатывать рулоны — наиболее эффективный способ работы с системами производства рулонов.
В некоторых случаях производство может быть переведено на 100% подачу в рулонах; в других случаях линии подачи листов и линии подачи рулонов дополняют друг друга, чтобы обеспечить работу с партиями разного размера.
Современная отрасль обработки металлов давлением вынуждена стремиться к оптимизации во всех аспектах своей деятельности. Бережливое производство побуждает нас выявлять потери и максимально сокращать их, будь то незавершенное производство, неэффективные процессы и информационные потоки или бесполезные и избыточные процедуры, которые не создают ценности для клиента.
Традиционные станки для штамповки и лазерной резки генерируют процент брака, который может достигать 15% и более, в то время как линии с рулонной подачей работают с браком всего от 2 до 3%. Имея возможность избежать этих 15% отходов, современные компании не могут позволить себе упустить .
Производители листового металла и OEM-производители, в частности, имеют большое преимущество: анализируя свои изделия и количества с помощью правила Парето, можно сразу определить изделия для перехода на производство в рулонах. В этих изделиях используется до 80 % сырья, поэтому поточное производство из рулонов дает наибольшую экономию.
В моей последующей статье я покажу, как Elleci зарабатывает более 196000 евро в год благодаря экономии сырья в сочетании с высокой скоростью производства системы пробивки рулонов/лазера.
Кредиты: Я хочу поблагодарить Джорджио Томаселлу (генеральный директор Elleci) за то, что он поделился и разрешил использовать информацию, представленную в этой статье
Резка конструкционной стали по длине; Чистые факты об инструментах и процессах сдвига
Рис. 1: Для однократной резки требуется прижимное устройство на стороне подачи материала ножниц. |
При производстве конструкционной стали первым процессом обычно является резка по длине. Обычно используются следующие методы: распиловка (холодная распиловка или ленточная распиловка), обжиг (плазменный или газокислородный) и резка ножницами.
Резка обычно ограничивается различными деталями из конструкционной стали. Он не используется на более крупных элементах конструкции, потому что требуемое усилие и получаемое в результате качество резки ограничивают экономическую и практическую осуществимость. Структурные элементы, которые являются практическими кандидатами на резку, включают:
• Уголок 8 дюймов и меньше
• Швеллер 12 дюймов и меньше
• Плоская заготовка 12 дюймов и меньше
• Балки S 5 x 10 дюймов, M 4 x 13 дюймов, W 4 x 13 дюймов
Инструмент для резки
Инструментальная сталь, такая как S-7, обычно используется для изготовления оснастки или ножей. Ножи обрабатываются с соблюдением требуемых допусков, а затем подвергаются термообработке до твердости от 52 до 56 по шкале Роквелла C (HRC). При термообработке они немного меняют форму. Операция шлифовки возвращает ножи в заданный допуск на чистовую обработку.
Набор инструментов состоит из неподвижного ножа и подвижного ножа. Рабочий зазор между неподвижным ножом и подвижным ножом должен составлять 10 процентов от толщины материала конструктивного элемента.
Процессы резки
В настоящее время для резки различных элементов конструкционной стали используются два процесса резки. Они бывают одинарными и двойными. Стрижка одинарными. В процессе однократной резки используется одно фиксированное лезвие и одно подвижное лезвие. Прижимное устройство на стороне подачи материала ножниц удерживает материал в правильном положении во время процесса резки (см. 9).0005 Рисунок 1 ).
Двойной рез. Процесс двойной резки однозначно отличается от процесса резки, используемого для резки листового или пруткового проката. При двойной стрижке используются три режущих инструмента: верхнее или подвижное лезвие действует как пробойник; два нижних или фиксированных ножа действуют как штамп (см. , рис. 2, ). Верхнее (подвижное) лезвие создает потерю материала, равную толщине лезвия за каждый цикл.
Заготовка поддерживается с обеих сторон верхним ножом, поэтому прижим материала не требуется. Поскольку верхнее лезвие действует как пробойник, минимальная длина среза не может быть меньше толщины верхнего лезвия.
Рис. 4: Для деталей с однородным профилем одним лезвием можно обрабатывать детали разных размеров. |
Толщина материала. Толщина верхнего лезвия — это максимальная толщина материала, который можно разрезать с помощью этой конфигурации инструмента. Например, если инструмент с двойной режущей кромкой используется для резки плоского материала толщиной до 1 дюйма, то толщина верхнего лезвия должна быть не менее 1 дюйма. Это лезвие толщиной 1 дюйм создает потерю материала или пропил в 1 дюйм для каждого цикла сдвига, независимо от толщины материала.
Потеря материала может быть критическим фактором, в зависимости от применения. Например, если длина готовой детали составляет 20 футов, а толщина верхнего ножа составляет 1 дюйм, потери материала в процессе резки с двойным резом составляют незначительные 0,4 процента от общей длины. Когда вырезаются детали длиной 10 дюймов, потери материала составляют 10 процентов от общей длины.
Передний угол. Верхнее лезвие ножниц с двойным резом может использовать передний угол, который уменьшает поперечное сечение, срезаемое за один раз. Уменьшение разрезаемого поперечного сечения существенно снижает требуемый тоннаж.
Искажение, возникающее в результате использования переднего угла, отражается в заготовке или отходах (см. Рисунок 3 ). Способность удерживать все искажения внутри заготовки позволяет получить исключительно плоскую готовую деталь. Однако, поскольку в этом процессе материал срезается постепенно, требуется более длинный ход, чем при обычной или однократной резке.
Швеллеры для резки, двутавровые балки
Однородный профиль плоских поверхностей и уголков делает их идеальными для резки — один набор инструментов подходит для различных размеров (см. Рисунок 4 ).
Рис. 5: Для деталей с неоднородным профилем для каждой детали требуется уникальный набор режущих инструментов. |
Однако это не тот случай, когда приложение включает каналы или двутавровые балки. При изменении глубины швеллера или двутавра изменяется и расстояние от одной полки до другой. Различное расположение полок и высота стенки в случае двутавровой балки диктуют уникальную геометрию оснастки для каждого размера сечения (см.0005 Рисунок 5 ).
В дополнение к глубине балки или канала вес на фут также влияет на поперечное сечение элемента. Эти различия в глубине и весе требуют использования уникального набора верхних и нижних ножей для каждого размера и веса швеллера и балки.
Допустимые отклонения в конструктивных сечениях
К сожалению, проблема согласования профилей ножей с разрезаемым сечением не ограничивается размером и весом сечения. Во время прокатки сырья валки, используемые сталелитейным заводом, изнашиваются. Этот износ приводит к тому, что сечения немного превышают заданные размеры элемента. Небольшие отклонения в допусках фрезерования являются нормальными и считаются приемлемыми.
Понимая динамику допусков прокатного стана, разработчики однозаходной оснастки для швеллеров и двутавровых балок должны предусмотреть отверстие для прокатываемого профиля каждого размера и веса. К сожалению, этот допуск станка является переменным, и требуемое отверстие инструмента, чтобы учесть этот допуск, отрицательно влияет на качество резания.
Рис.![]() Инструмент с двойным вырезом для швеллеров и некоторых двутавровых балок включает гидравлически регулируемую боковую наковальню. |
Оснастка с двойной насечкой для швеллеров и некоторых двутавровых балок уникальным образом решает эту проблему допусков фрезерных станков. Эти наборы штампов включают гидравлически регулируемую боковую наковальню (см. , рис. 6, ). Эта конструкция не только вмещает ряд каналов (от 4 до 12 дюймов), но и ее конструкция с гидравлическим боковым зажимом решает проблему допусков фрезерных станков.
Этот набор регулируемых штампов обеспечивает плотное прилегание боковых упоров к фланцам элемента при каждом ходе и компенсирует любой допуск прокатки прокатного стана.
Работа с гаммой
Типы станков, инструментов и опций, доступных для резки элементов из конструкционной стали, охватывают весь спектр от простых до сложных, чтобы приспособиться к различным сценариям резки. Выбор процесса — одинарная резка или двойная резка, передний угол или отсутствие переднего угла или использование другого метода, такого как распиловка или газопламенная резка, — который лучше всего соответствует критериям применения, требует сначала определения стоимости и технических ограничений готовой детали.