Предел прочности сталь 45: Сталь 45: особенности применения и характеристика
alexxlab | 31.01.2023 | 0 | Разное
Химический состав сталей, %
Сталь | ГОСТ | С | Mn | Si |
Ст4 Сталь45 20ХНЗА | 380—71 1050—60 4543—71 | 0,18—0,27 0,42—0,50 0,17—0,23 | 0,40—0,70 0,50—0,80 0,30—0,60 | 0,12—0,30 0,17—0,37 0,17—0,37 |
Продолжение табл. 1
Сталь | ГОСТ | Cr | Ni | S | Р |
Ст4 Сталь 45 20ХНЗА | 380—71 1050—60 4543—71 | ≤0,3 ≤0,25 0,60-0,90 | ≤0,3 ≤0,25 2,75-3,15 | ≤0,050 ≤0,045 ≤0,025 | ≤0,040 ≤0,040 ≤0,025 |
Сталь марки Ст4,
согласно ГОСТ, имеет следующие свойства
в состоянии поставки (после прокатки
или ковки): (σ в == 420÷540 МПа,σт = 240÷260 МПа;
δ = 21%.
Сталь 45, согласно ГОСТ, в состоянии поставки (после прокатки и отжига) имеет твердость не более НВ 207. При твердости НВ 190— 200 сталь имеет предел прочности не выше 600—620 МПа, а при твердости ниже НВ 180 предел прочности не превышает 550—600 МПа. Для отожженной углеродистой стали отношение σт/σв составляет примерно 0,5. Следовательно, предел текучести стали 45 в этом состоянии не превышает 270—320 МПа.
Сталь 20ХНЗА, согласно ГОСТ, в состоянии поставки (после прокатки и отжига) имеет твердость не более НВ 250. Следовательно, предел прочности при твердости НВ 230—250 не превышает 670— 750 МПа и может быть ниже 600 МПа для плавок с более низкой твердостью. Тогда предел текучести составляет 350—400 МПа, так как σт/σв для отожженной легированной стали 0,5—0,6.
Таким образом, для
получения заданной величины предела
текучести вал необходимо подвергнуть
термической обработке.
Для низкоуглеродистой стали Ст4 улучшающее влияние термической обработки незначительно. Кроме того, Ст4 — как сталь обыкновенного качества имеет повышенное содержание серы и фосфора (см. табл. 1), которые понижают механические свойства и особенно сопротивление ударным нагрузкам.
Для такого ответственного изделия, как вал двигателя, поломка которого нарушает работу машины, применение более дешевой по составу стали обыкновенного качества нерационально.
Сталь 45 относится к классу качественной углеродистой, а сталь 20ХН3А — к классу высококачественной легированной стали. Они содержат соответственно 0,42—0,50 и 0,17—0,23%С и принимают закалку.
Для повышения прочности можно применять нормализацию или закалку с высоким отпуском. Последний вариант
обработки сложнее, но позволяет получить
не только более высокие характеристики
прочности, но и более высокую вязкость.
В стали
45 минимальные
значения ударной вязкости (aн после нормализации составляют
200—300
кДж/м2,
а после закалки и отпуска с нагревом до
500° С
достигают
600—700
кДж/м2.
Так как вал двигателя воспринимает в работе динамические нагрузки, а также и вибрации, более целесообразно применить закалку и отпуск. После закалки в воде углеродистая сталь 45 получает структуру мартенсита. Однако вследствие небольшой прокаливаемости углеродистой стали эта структура в изделиях диаметром более 20—25 мм образуется только в сравнительно тонком поверхностном слое толщиной до 2—4 мм.
Последующий отпуск вызывает превращение мартенсита и троостита в сорбит только в тонком поверхностном слое, но не влияет на структуру и свойства перлита и феррита в основной массе изделий.
Сорбит отпуска обладает более высокими механическими свойствами, чем феррит и перлит.
Наибольшие
напряжения от изгиба, кручения и повторно
переменных нагрузок воспринимают
наружные слои, которые и должны обладать
повышенными механическими свойствам.
Однако в сопротивлении динамическим
нагрузкам, которые воспринимает вал,
участвуют не только поверхностные, но
и нижележащие слои металла.
Таким образом, углеродистая сталь не будет иметь требуемых свойств по сечению вала диаметром 70 мм.
Сталь 20ХНЗА легирована никелем и хромом для повышения прокаливаемости и закаливаемости. Она получает после закалки достаточно однородные структуру и механические свойства в сечении диаметром до 75 мм.
Для стали 20ХНЗА рекомендуется термическая обработка:
1. Закалка с 820—835° С в масле.
При закалке с охлаждением в масле (а не в воде, как это требуется для углеродистой стали) возникают меньшие напряжения, а, следовательно, и меньшая деформация. После закалки сталь имеет структуру мартенсита и твердость не ниже HRC 50.
2. Отпуск 520—530° С. Для предупреждения отпускной хрупкости, к которой чувствительны стали с хромом (марганцем, вал после нагрева следует охлаждать в масле.
Механические свойства стали 20ХНЗА в изделии диаметром до 75 мм после термической обработки:
Предел прочности σв=900—1000 МПа, предел текучести σт = 750—800 МПа , относительное удлинение δ = 8—10 %, относительное сужение ψ = 45—50 %, ударная вязкость
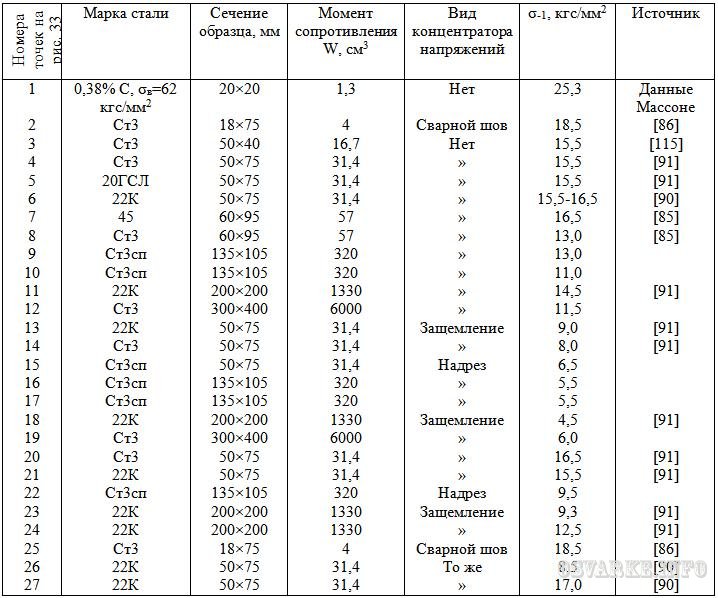
Таким образом, эти свойства обеспечивают требования, формулированные в задаче, для вала диаметром 70 мм.
№ 2. Зубчатые колеса в зависимости от условий работы и возникающих напряжений можно изготавливать из стали обыкновенного качества, качественной углеродистой и легированной с различным содержанием легирующих элементов.
Выбрать, руководствуясь техническими и экономическими соображениями, сталь для изготовления колес диаметром 50 мм и высотой 30 мм с пределом прочности не ниже 360—380 МПа.
Указать термическую обработку колес, механические свойства и структуру выбранной стали в готовом изделии и для сравнения механические свойства и структуру сталей 45 и 40ХН после улучшающей термической обработки.
№ 3. Выбрать сталь для изготовления валов диаметром 50 мм для двух редукторов. По расчету сталь для одного из валов должна иметь предел текучести не ниже 350 МПа, а для другого — не ниже 500 МПа.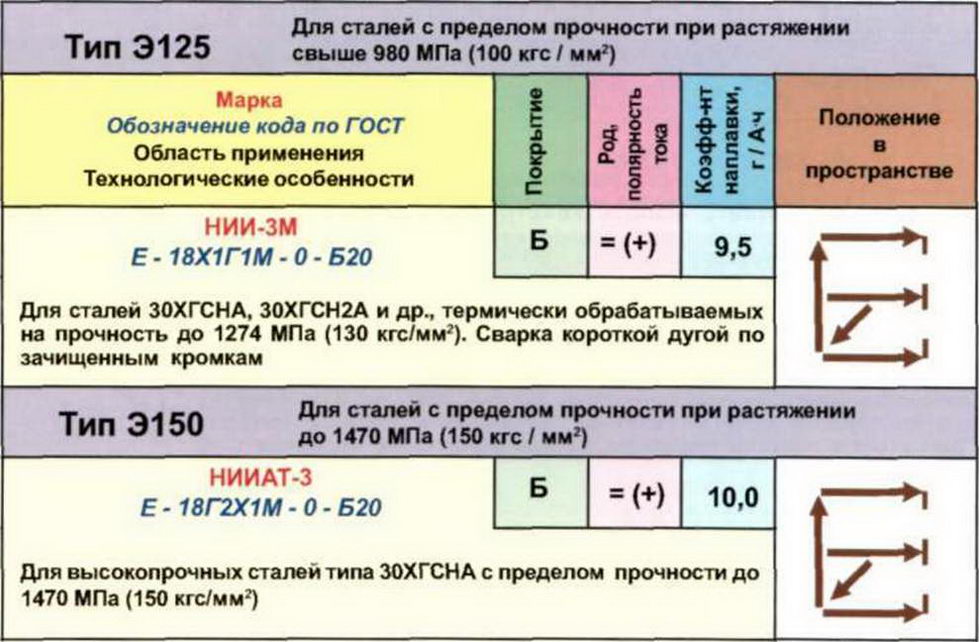
Указать: 1) состав и марку выбранных сталей; 2) рекомендуемый режим термической обработки; 3) структуру после каждой операции термической обработки; 4) механические свойства в готовом изделии.
Можно ли применять углеродистую сталь обыкновенного качества для изготовления валов требуемого сечения и прочности?
№ 4. Коленчатые валы диаметром 80 мм, работающие при повышенных напряжениях, изготавливают на одном заводе из качественной углеродистой стали, а на другом — из легированной стали.
Какую сталь следует применять для этой цели? Указать ее химический состав и марку.
№ 5. Выбрать сталь для изготовления тяжело
нагруженных коленчатых валов диаметром
60 мм: предел
прочности должен быть не ниже
750 МПа.
Рекомендовать состав и марку стали, режим термической обработки, структуру и механические свойства после закалки и после отпуска.
ЗАДАЧИ ПО ИНСТРУМЕНТАЛЬНЫМ
СТАЛЯМ И СПЛАВАМ
№ 6. Стойкость сверл и фрез, изготовленных из быстрорежущей стали умеренной теплостойкости марки Р12 и обрабатывавших конструкционные стали твердостью НВ 180—200, была удовлетворительной.
Однако стойкость этих сверл резко снизилась при обработке жаропрочной аустенитной стали.
Рекомендовать быстрорежущую сталь повышенной теплостойкости, пригодную для производительного резания жаропрочных сталей, указать ее марку и химический состав, термическую обработку и микроструктуру в готовом инструменте.
Сопоставить теплостойкость стали Р12 и выбранной стали.
Решение задачи № 6
Режущие инструменты
для производительного резания изготовляют
из быстрорежущих сталей, так как эти
стали обладают теплостойкостью. Они
сохраняют мартенситную структуру и
высокую твердость при повышенном нагреве
(500—650° С),
возникающем в режущей кромке.
Однако стойкость инструментов из быстрорежущих сталей, подвергавшихся оптимальной термической обработке, определяется не только их химическим составом, структурой и режимом резания, но сильно зависит от свойств обрабатываемого материала.
При резании сталей
и сплавов с аустенитной структурой
(нержавеющих, жаропрочных и др.),
получающих все более широкое применение
в промышленности, стойкость инструментов
и предельная скорость резания могут
сильно снижаться по сравнению с
получаемыми при резании обычных
конструкционных сталей и чугунов с
относительно невысокой твердостью (до НВ 220—250). Это
связано главным образом с тем, что
теплопроводность аустенитных сплавов
пониженная. Вследствие этого тепло,
выделяющееся при резании, лишь в небольшой
степени поглощается сходящей стружкой
и деталью и в основном воспринимается
режущей кромкой. Кроме того,
эти сплавы сильно упрочняются под режущей кромкой в процессе резания, из-за чего заметно возрастают усилия резания.
Для резания подобных
материалов, называемых труднообрабатываемыми,
мало пригодны быстрорежущие стали
умеренной теплостойкости, сохраняющие
высокую твердость (HRC 60) и
мартенситную структуру после нагрева
не выше
615—620°С.
Для обработки аустенитных сплавов
необходимо выбирать быстрорежущие
стали повышенной теплостойкости, а
именно кобальтовые. Кобальт способствует
выделению при отпуске наряду с карбидами
также и частиц интерметаллидов, более
стойких против коагуляции, и затрудняет
процессы диффузии при температурах
нагрева режущей кромки. Кобальтовые
стали сохраняют твердость HRC 60 после
более высокого нагрева: до
640—645° С.
Кроме того, кобальт заметно (на
30—40%)
повышает теплопроводность быстрорежущей
стали, а следовательно, снижает температуры
режущей кромки из-за лучшего отвода
тепла в тело инструмента. Наконец, стали
с кобальтом имеют более высокую твердость
(до HRC 68 у стали
Р8МЗК6С).
Для сверл и фрез, применяемых для резания аустенитных сплавов, рекомендуются кобальтовые стали марок Р12Ф4К5 или Р8МЗК6С. Термическая обработка кобальтовых сталей принципиально не отличается от обработки других быстрорежущих сталей. Она следующая.
Инструменты
закаливают с очень высоких температур
(1240— 1250°
С для стали Р12Ф4К5 и
1210—1220° С
для стали Р8МЗК6С), что необходимо для
растворения большего количества карбидов
и насыщения аустенита (мартенсита)
легирующими элементами: вольфрамом,
молибденом, ванадием и хромом. Еще более
высокий нагрев, дополнительно усиливающий
перевод карбидов в раствор, недопустим:
он вызывает рост зерна, что снижает
прочность и вязкость. Структура стали
после закалки: мартенсит, остаточный
аустенит
(15—30%) и
избыточные карбиды, не растворяющиеся
при нагреве и задерживавшие рост
зерна. Твердость HRC 60— 62.
Затем инструменты отпускают при 550—560° С (3 раза по 60 мин). Отпуска вызывает: а) выделение дисперсных карбидов и интерметаллидов из мартенсита (дисперсионное твердение), что повышает твердость до HRC 66—69; б) превращает мягкую составляющую — остаточный аустенит в мартенсит; в) снимает напряжения, вызываемые мартенситным превращением.
После отпуска инструменты шлифуют, а затем подвергают цианированию, чаще всего жидкому в смеси NaCN (50%) и Na2C03 (50%) с выдержкой 15—30 мин (в зависимости от сечения инструмента).
Твердость цианированного слоя на глубину 0,02—0,03 мм достигает HRC 69—70; немного (на 10° С) возрастает и теплостойкость. При нагреве для цианирования снимаются также напряжения, вызванные шлифованием. Цианирование повышает стойкость инструментов на 50—80%.
После цианирования
целесообразен кратковременный нагрев
при
450—500° С в
атмосфере пара и с охлаждением в масле;
поверхность инструмента приобретает
тогда синий цвет и несколько лучшую
стойкость против воздушной коррозии.
№ 7. Выбрать сталь для червячных фрез, обрабатывающих конструкционные стали твердостью НВ 220—240.
Объяснить причины, по которым для этого назначения нецелесообразно использовать углеродистую инструментальную сталь У12 с высокой твердостью (HRC 63—64).
Рекомендовать режим термической обработки фрез из выбранной быстрорежущей стали, приняв, что фрезы изготовлены из проката диаметром 40 мм.
№ 8. Завод должен изготовить долбяки, обрабатывающие с динамическими нагрузками конструкционные стали с твердостью НВ 200—230.
Выбрать марку быстрорежущей стали, наиболее пригодной для этого назначения, рекомендовать режим термической обработки и указать структуру и свойства (для долбяков наружным диаметром 60 мм).
№ 9. Завод изготовлял протяжки из высоковольфрамовой стали Р18.
Указать, можно ли
использовать для протяжек менее
легированную, а следовательно, более
экономичную быстрорежущую сталь.
Выбрать марку стали для протяжек, обрабатывающих конструкционные стали с твердостью до НВ 250, указать ее термическую обработку, структуру и свойства для случаев, когда протяжки изготовляют из проката диаметром 40 и 85 мм.
ЗАДАЧИ ПО цветным металлам И СПЛАВАМ
№ 10. Многие изделия изготавливают из латуни вытяжкой из листа в холодном состоянии. Иногда в изделиях обнаруживаются трещины, возникающие без приложения внешних нагрузок (так называемое «сезонное растрескивание»). На рис. 1 показана деталь после глубокой вытяжки и после растрескивания при вылеживании.
Рис. 1. Растрескивание латунной детали после глубокой вытяжки и вылеживания
Объяснить сущность этого явления и указать способы его предубеждения.
Подобрать марку
латуни, не подверженной сезонному
растрескиванию. Кроме того, описать
структуру, технологические свойства
α и α
+ β’-латуней.
Решение задачи № 10
Латуни в зависимости от содержания цинка и структуры можно разделить на три класса:
1. α-латуни ……. До 39,5% Zn
2. α + β’-латуни ….. От 39,5 до 45,7% Zn
3. β’-латуни ……. От 45,7 до 51% Zn
Увеличение содержания цинка изменяет структуру и свойства латуни (рис. 2).
Увеличение содержания цинка до определенного предела повышает пластичность и прочность. Пластичность достигает максимальных значений при 30—32% Zn, а прочность — при 40%. При дальнейшем увеличении содержания цинка прочность и пластичность снижаются.
Это изменение свойств определяется свойствами соответствующих фаз, образующихся при введении цинка.
α-фаза представляет
твердый раствор типа замещения,
пластичность и прочность которой
возрастают по мере увеличения содержания
цинка.
β’-фаза — твердый раствор на базе электронного соединения с центрированной кубической решеткой и упорядоченным расположением атомов. Эта фаза отличается повышенной хрупкостью и твердостью; поэтому образование β-фазы снижает вязкость и повышает твердость.
Рис. 2. Механические свойства латуни в зависимости от содержания цинка:
а – литая латунь; б — катаная и отожженная латунь
При нагреве выше 450° С β’-фаза превращается в неупорядоченный твердый раствор β, отличающийся большей пластичностью, чем β’-фаза. Из диаграммы состояния видно, что α + β’-латуни приобретают при таком нагреве однородную структуру β-твердого раствора, а следовательно, и большую пластичность.
Эти свойства фаз определяют технологический прогресс изготовления изделий из различных сортов латуни, а также их назначение.
Изделия из α-латуни
изготавливают главным образом холодной
или горячей деформацией; обработка
резанием не дает достаточно чистой
поверхности. Изделия из
α + β’-латуни
изготавливают горячей (прессование,
штамповка) или холодной деформацией
(но без вытяжки) или обработкой
резанием.
В результате последующего отжига прочность сплава понижается, но пластичность возрастает (рис. 3).
Холодная деформация латуни создает в изделии остаточные напряжения. Они возникают и в результате местной холодной деформации (при изгибе деталей, чеканке, развальцовке и т. п.).
Рис. 3. Механические свойства латуни Л68 в зависимости:
а – от степени деформации; б – от температуры отжига
При вылеживании
или эксплуатации в латунных изделиях
иногда возникают трещины. «Сезонное
растрескивание» наблюдается главные
образом в латунях с содержанием более
20% Zn
и отчетливо обнаруживается, например,
в полых изделиях, прутках и т. д. Сезонное
растрескивание усиливается в химически
активных средах, особенно в парах
аммиака, ртутных солях, ртути, мыльной
воде и т. д. Образование трещин является
результатом совместного действия
остаточных напряжений, созданных
холодной деформацией (наиболее опасны
растягивающие напряжения), и химически
активных сред.
Для предохранения от сезонного растрескивания нужен отпуск с нагревом до 200—300° С; это снимает большую часть остаточных напряжений и незначительно снижает прочность.
Но в условиях изготовления и монтажа конструкций с применением развальцовки, гибки и т. д. не всегда возможно избежать возникновения местных, даже незначительных деформаций, а, следовательно, и сезонного растрескивания. В таких случаях применяют более дорогие (и имеющие меньшую прочность), но не склонные к сезонному растрескиванию латуни Л96 и Л90. Латуни Л96 и Л90 обладают высокой теплопроводностью.
Латуни можно заменить алюминиевой бронзой, не склонной к сезонному растрескиванию и обладающей аналогичными значениями прочности и пластичности.
№ 11. Гребные винты морских пароходов имеют
сложную форму и очень массивны, например
масса винта современного крупного
океанского теплохода достигает
30—50 т.
Наметить схему технологии изготовления винта, учитывая его форму. Исходя из этой схемы и условий работы винта в морской воде, подобрать состав сплава и указать его структуру и механические свойства.
№ 12. Некоторые детали арматуры турбин, котлов гидронасосов и т. п., работающие во влажной атмосфере и изготавливаемые массовыми партиями литьем, имеют сложную форму. В процессе литья должна быть обеспечена максимальная точность размеров.
Указать состав применяемого для этой цели цветного сплава, его структуру и механические свойства; привести способ литья, позволяющий создать требуемую высокую точность с минимальной последующей механической обработкой.
Привести химический
состав стали для форм, применяемых для
литья выбранного сплава, и указать режим
термической обработки, а также
структуру стали в готовом изделии.
№ 13. Многие детали приборов и оборудования, подверженные действию морской воды, изготавливают из цветного сплава путем холодной деформации в несколько операций.
Подобрать сплав, стойкий против действия морской воды, и привести его химический состав.
Указать режим промежуточной термической обработки выбранного сплава и привести его механические свойства после деформации и термической обработки. Сравнить состав стали, стойкой против действия морской воды;
привести режим ее термической обработки, механические свойства и структуру.
№ 14. Трубки в паросиловых установках должны быть стойки против коррозии.
Подобрать марку сплава на медной основе, пригодного для изготовления трубок и не содержащего дорогих элементов; привести состав выбранного сплава.
Указать способ
изготовления трубок и сравнить
механические свойства выбранного
сплава, получаемые после окончательной
обработки, с механическими свойствами
стали, стойкой против коррозии в тех
же средах.
Круг стальной Ст45, диаметр 20 мм
Информация для заказа
Вы можете купить заготовки из стального конструкционного калиброванного круга Ст45 длиной от 50 до 1000 мм.
Номинальный диаметр D круга стального равен 20 мм (квалитет h21, отклонение по диаметру -0,130 мм). Фактическая длина L заготовок из круга строго не меньше указанной в таблице. Может быть больше на 1-5 мм (резка с запасом).
Срок готовности к отгрузке при отсутствии на складе 5 рабочих дней (при оформлении заказа).
Цены за штуку в рублях. Остатки и цены обновлены: 28.01.23 09:45
Код ↑↓ | Модель ↑↓ | m (кг) ↑↓ | L (мм) ↑↓ | Склад ↑↓ | Цена (руб) ↑↓ | Количество |
---|---|---|---|---|---|---|
145009 | Ст45 20 х 50 мм | 0.![]() | 50 | 30 шт | 60 | |
145010 | Ст45 20 х 100 мм | 0.25 | 100 | 30 шт | 90 | |
145011 | Ст45 20 х 150 мм | 0.37 | 150 | 20 шт | 120 | |
145012 | Ст45 20 х 200 мм | 0.![]() | 200 | 20 шт | 150 | |
145013 | Ст45 20 х 300 мм | 0.74 | 300 | 10 шт | 220 | |
145014 | Ст45 20 х 400 мм | 0.99 | 400 | 10 шт | 270 | |
145015 | Ст45 20 х 500 мм | 1.![]() | 500 | 10 шт | 330 | |
145016 | Ст45 20 х 1000 мм | 2.46 | 1000 | 8 шт | 600 |
Корзина: 0 шт на 0 руб
Описание
Круг стальной конструкционный калиброванный Ст45 изготовлен в соответствии с ГОСТ 1050-88. Холоднотянутый. Поверхность ровная и блестящая.
Сталь трудносвариваемая. Может закаливаться термообработкой.
Популярный вариант для изготовления различных изделий, от которых требуется повышенная прочность.
Основные характеристики
Параметр | Значение |
---|---|
Плотность | 7826 кг/м3 |
Температура плавления | 1450—1520 °C |
Предел кратковременной прочности σв | 600 МПа |
Относительное удлинение δ5 | 16 % |
Твердость по Бринеллю HB | 229 |
Химический состав | |||||||||
---|---|---|---|---|---|---|---|---|---|
C: 0,42-0,15 % | Si: 0,17-0,37 % | Mn: 0,5-0,8 % | Ni: до 0,25 % | S: до 0,04 % | P: до 0,035 % | Cr: до 0,025 % | Cu: до 0,025 % | As: до 0,08 % | Fe: 97 % |
Файлы
- ГОСТ 1050-88. Прокат сортовой, калиброванный, со специальной отделкой поверхности из углеродистой качественной конструкционной стали.
Общие технические условия. Скачать (pdf, 842 кБ)
Производитель
- Россия.
Вопросы и комментарии
Углеродистая стальC45 — поставляется в Великобританию компанией West Yorkshire Steel Ltd
C45 Поставщики пластин или прутков для газопламенной резки с доставкой по всей Великобритании. C45 — это среднеуглеродистая сталь, обладающая приемлемой прочностью на растяжение. Поставляемый в холоднотянутом или горячекатаном состоянии, свойства при растяжении могут варьироваться, но составляют примерно 500-800 Н/мм². Этот сорт может подвергаться пламенной или индукционной закалке для получения хорошей поверхностной твердости с умеренной износостойкостью. C45 широко используется для компонентов , которые требуют лучших свойств, чем у низкоуглеродистой стали, но не оправдывают затраты на легированную сталь. Доступный на складе в барах, C45 может быть разрезан по вашим требованиям. Мы также предлагаем плиты газопламенной резки, нарезанные по вашим размерам и нормализованные.

Мы приветствуем запросы на экспорт углеродистой стали. Свяжитесь с нашим офисом продаж и ознакомьтесь с нашей политикой доставки для получения дополнительной информации.
Альтернативные марки углеродистой стали, которые мы поставляем
EN3 | EN8 | EN9 | EN32 | EN43 | 070М20 | 080М40 | 070М55 | 080А15 | С275 | С355 | Key Steel
Форма поставки
West Yorkshire Steel является акционером и поставщиком круглого, квадратного и плоского проката из углеродистой стали C45. Стержни можно распилить до нужной длины на 1 или несколько частей. West Yorkshire Steel поставляет стальные профили, вырезанные пламенем, марки C45, поверхность которых при необходимости может быть отшлифована. Может поставляться шлифованный стальной стержень C45, обеспечивающий прецизионную шлифовку стального стержня с жесткими допусками.
Свяжитесь с нашим опытным отделом продаж, который поможет вам с вашим запросом на среднеуглеродистую сталь C45.
- Плита
- Квартира
- Диаметр
Нажмите на заголовки ниже для получения дополнительной информации
C45 широко используется во многих общетехнических приложениях. Типичные области применения включают инструменты, валы, гайки, болты, шатуны, винты, ролики.
Углерод | 0,42-0,50% | Фосфор | 0,045% макс. |
Марганец | 0,50-0,80% | Сера | 0,045% макс. |
Кремний | 0,15-0,40% |
West Yorkshire Steel является поставщиком стальных профилей C45. Поскольку при газовой резке листа C45 может образоваться твердая кромка, этот сорт обычно нормализуется после газопламенной резки. Профили, вырезанные пламенем, могут быть отшлифованы Lumsden или прецизионно отшлифованы.
Прецизионно отшлифованные плоские заготовки / измерительные пластины могут поставляться длиной 500 мм / 1000 мм. Нестандартные размеры могут быть изготовлены примерно за 2-3 недели.
Тщательно нагрейте сталь, затем доведите температуру до 1100°C для ковки. Не ковать ниже 850°C. После ковки медленно охлаждают, желательно в печи.
Медленно нагреть до 680-710°C, хорошо пропитать. Медленно остудить в печи.
Медленно нагрейте компонент до 820-860°C и дайте ему полностью нагреться. Закалка в масле или воде.
Отпуск сразу после закалки, пока инструменты еще теплые. Повторно нагрейте C45 до температуры отпуска, затем выдержите в течение одного часа на каждые 25 миллиметров общей толщины (минимум 2 часа). Охладите на воздухе. Для большинства применений температура отпуска составляет 550-660°C.
Мы рекомендуем вам связаться с вашим поставщиком сварочных материалов, который предоставит вам полную помощь и информацию по сварке стали C45.
Температуры термообработки, включая скорость нагрева, охлаждения и время выдержки, будут варьироваться в зависимости от таких факторов, как форма и размер каждого компонента из стали C45. Другие соображения во время термической обработки включают тип печи, закалочную среду и оборудование для транспортировки заготовок. Пожалуйста, проконсультируйтесь со своим поставщиком услуг по термообработке для получения полного руководства по термообработке углеродистой стали C45.
Углеродистая сталь C45 доступна с сертификатом литья и анализа или сертификатом мельницы BS EN 10204 3.1. Пожалуйста, запрашивайте при размещении любых заказов.
Углеродистая сталь C45 поставляется в соответствии с нашей регистрацией ISO 9001:2015.
Пруток из углеродистой стали CK45 | CK45 Ковка | CK45 Круглый
CK45 Стальной круглый пруток, CK45 Производители стального круглого проката, CK45 Поставщики стали, CK45 Stockist, CK45 Дилеры стали, CK45 Дистрибьюторы стали, CK45 Оптовые торговцы, торговцы сталью CK45, дистрибьюторы стального квадрата CK45, стальной плоский пруток CK45, стальные компании CK45 рядом со мной.
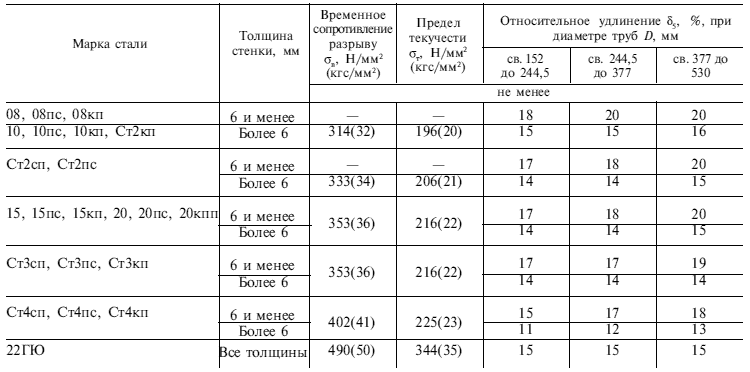
Введение класса: Углеродистая сталь CK 45 подходит для средненапряженных деталей больших размеров (тяжелые кованые детали) и сложных форм в автомобилестроении и машиностроении (например, корабельные валы, детали трансмиссии, колеса). узлы). Самая низкая температура применения. -25 °C, благоприятная ползучесть до 480 °C.
Марка Применение: Подходит для изготовления различных прочных режущих инструментов с износостойкостью, ударопрочностью. Усовершенствованный штамп для штамповки, штамп для резьбы, прочность и сложная форма штампа и т. д. Индустрия режущего инструмента: скребок, зубчатый нож, железные ножи, сверла и т. д.
Кузнечная промышленность: штамповка
Винтовая промышленность: пресс-формы для штамповки головок, такие как зубья, пуансон.
Эквивалентные марки:
США | немецкий | Япония | Китай | ИСО |
АСТМ А681 | DIN 17350 | ДЖИС Г4403 | ГБ/т 1299 | ИСО 4957 |
1045 | СК45 | С45К | 45 | C45E4 |
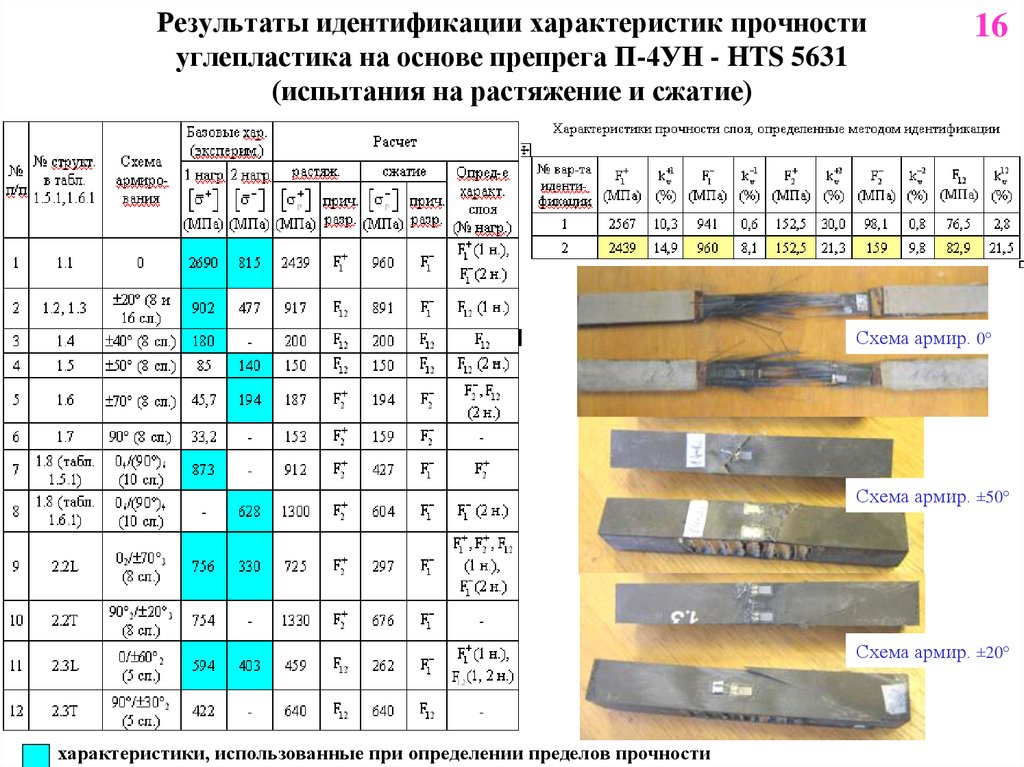
Химический состав: В следующей таблице показан химический состав стали CK45:
Элемент | С | Си | Мн | Р | С |
Содержание(%) | 0,42-0,5 | 0,4 | 0,5-0,8 | 0,04 | 0,03 |
Механические свойства:
Модуль упругости | 217 ГПа при – 100 °C |
Удлинение | 4–8 % при 20 °C |
Коэффициент Пуассона | 0,29 [-] при 20 °C |
Модуль сдвига | 75 – 80 ГПа при 20 °C |
Прочность на растяжение | 580 – 770 МПа при 20 °C |
Предел текучести | 330 – 640 МПа при 20 °C |
.

Закалка: Закалка этой марки осуществляется с температуры аустенизации 1475-1550ºF (800-845ºC) и закалки в масле или воде.
Пламенная и индукционная закалка может осуществляться путем быстрого нагрева до желаемой глубины корпуса и закалки в воде или масле. За этим должна следовать закалка при температуре 300–400ºF (150–200ºC), чтобы уменьшить напряжения в корпусе, не влияя на его твердость. При такой обработке можно получить поверхностную твердость Rc 58. Специалирование: Температура парики / ℃: 552 После твердых твердых изделий HRC или выше: 201-269hb.

Физические свойства:
Количество | Значение | Блок |
Тепловое расширение | 10 – 10 | е-6/К |
Теплопроводность | 25 – 25 | Вт/м.К |
Удельная теплоемкость | 460 – 460 | Дж/кг.К |
Температура плавления | 1450 – 1510 | °С |
Плотность | 7700 – 7700 | кг/м 3 |
Удельное сопротивление | 0,55 – 0,55 | Ом.![]() |
Термические свойства: Коэффициент теплового расширения α 1,08E-5 1/K при -100 °C Thermal conductivity λ 41.7 W/(m·K) at 20 °C Thermal diffusivity α diff 11.6 mm²/s at 20 °C
Forging Properties: Сначала предварительный нагрев до 552 ℃, затем нагрев до температуры ковки. Затем выдержите при 820–870 °C, тщательно прогревая. Затем начните ковать, температура ковки не ниже 560 ℃. После ковки медленно остудить.
Снятие стресса: Нормализация: 840-870 ° C ANDELING: ANDELING: nealing: .

Плотность: Плотность 7,8 г/см³ при 20 °C
Обрабатываемость: Обрабатываемость хорошая, на 80 % выше, чем у сплава AISI 1112, используемого в качестве 100 % обрабатываемой стали. Сварка: Города снабжения: Ахмедабад, Амараватхи, Амбаттур, Бангалор, Белгаум, Шеннай, Шитт, Коимбат, Дорор, Дорор, Дорор, Дорор, Дорор, Дорор, Дороре, Дороре, Дороре, Дороре, Дороре, Дороре, Дороре, Дороре, Дорор, Малор, Малор, Малор, Малор, Малор, Малор, Малор, Малор, Малор, Малор, Малор, Малор, Марант, Малор, Марант, Малор, Марант, Малор, Марант, Малор, Мейраб, Мейраб, Мейраб, Мейраб, Маран. , Тутикорин, Мадурай, Андхра-Прадеш, Карнатака, Пудучерри, Керала, Тамил Наду, Телангана, Салем, Танджавур, Тричи, Эроде, Веллор, Ранипет, Сивакаси, Карур, Хосур, Нагеркойл, Канчипурам, Караикуди, Нейвели, Куддалор, Кумбаконам, Тируваннамалай , Поллачи, Раджапалаям, Гудиятам, Пудукоттай, Ваниямбади, Амбур, Нагапаттинам, Тривандрам, Виджаявада, Гунтур, Тирупати, Назаратпет, Какинада, Курнул, Кадапа, Низамабад, Махабубнагар, Каримнагар.
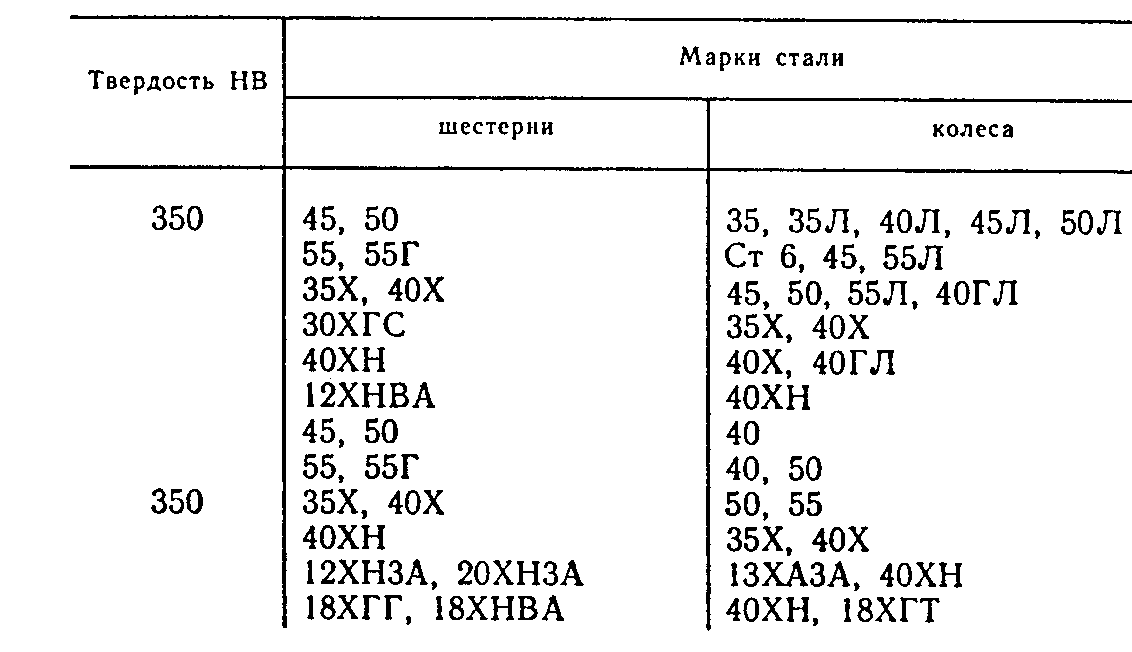