Предел прочности стали 09г2с: Сталь 09Г2С – Сталь конструкционная низколегированная.
alexxlab | 07.03.2023 | 0 | Разное
Легированная сталь 09Г2С: характеристики, применение, твердость, аналоги
При изготовлении различных металлоконструкций, труб и трубопроводной арматуры на российском рынке чаще всего используются две марки стали: ст.20 и 09г2с. Популярность материалов вызвана их эксплуатационными свойствами, хорошей свариваемостью, широким диапазоном рабочих температур.
Стали применяют в машиностроении, нефтегазовом секторе, химической промышленности и других сферах для производства:
- отводов, переходов, тройников и пр. фитингов;
- труб;
- запорно-регулирующей арматуры;
- сварных конструкций;
- машин и прицепов;
- различных деталей.
Несмотря на схожие области применения, стальные марки различаются составом, а, следовательно, технологическими и механическими свойствами. Поэтому материал выбирают, отталкиваясь от государственных и отраслевых стандартов, технических условий и проектной документации.
Характеристика стали 20
Ст. 20 ‒ качественная углеродистая конструкционная сталь, которую используют для производства деталей, работающих при температуре от -40 до +450 °C.
Материал пластичен, не имеет ограничений в сварке, не склонен к отпускной хрупкости, не чувствителен к флокенам. Средняя теплопроводность обеспечивает равномерный нагрев и охлаждение во время транспортировки изделия. После термохимической обработки подходит для изготовления деталей с невысокой прочностью сердцевины при высокой твердости поверхности (шестерни, червяки и пр.).
Химические элементы, входящие в состав марки:
- С (углерод) ‒ 0,17-0,24%.
- Si (кремний) ‒ 0,17-0,37%.
- Mn (марганец) ‒ 0,35-0,65%.
- Ni (никель) ‒ до 0,3%.
- Р (фосфор) ‒ до 0,03%.
- S (сера) ‒ до 0,035%.
- Fe (железо) ‒ ∼98%.
- Концентрация др. элементов, в т.ч. вредных ‒ менее 0,3%.
Допускается снижение содержания кремния при использовании ванадия, алюминия, титана или ниобия. Количество марганца также может быть уменьшено при удовлетворении требований к механическим свойствам.
Легирование стали повышает прочность, стойкость к коррозии, снижает опасность хрупкого разрушения. Основные легирующие элементы: Cr (хром), Ni (никель), Cu (медь), N (азот), V (ванадий), Ti (титан) и пр.
Материал изготавливают волочением, отливкой, ковкой, горячей или холодной деформацией.
Применение
Сталь 09г2с активно используется в судостроительной, транспортной, нефтяной и химической промышленных отраслях. На её основе выполняют сварные соединения сложной конфигурации и изготавливают крепежные детали. Примеры использования:
- Прокладка магистральных трубопроводов
- Возведение жилых и промышленных объектов
- Производство хозяйственной и бытовой техники
Среди других примеров использования такой стали – изготовление технической оснастки, котлов и судов и т.д. Стоит отметить, что широкий температурный диапазон этой стали позволяет использовать её там, где для других материалов есть риск деформации за продолжительный эксплуатационный срок, в частности, для производства тех же котлов, постоянно используемых при высоких температурах.
Характеристика стали 09г2с
Марка 09г2с ‒ конструкционная низколегированная. Ее используют для изготовления деталей и сварных металлоконструкций, работающих под давлением при температуре от -70 до +425 °C, что позволяет выдерживать сильные температурные деформации при длительной эксплуатации. Другими словами, материал морозоустойчив.
Расшифровка:
- 09 ‒ содержание углерода (C) ‒ 0,09%.
- г2 ‒ показывает наличие марганца (Mn) до 2%.
- с ‒ присутствие кремния (Si), отсутствие цифр после «с» определяет его содержание ‒ до 1%.
Химический состав стали не ограничен указанными тремя элементами, он может быть дополнен серой (S), никелем (Ni), фосфором (P), азотом (N) и др. При этом общий процент легирующих добавок не должен превышать 2%.
Свойства:
- не деформируется при эксплуатации;
- выдерживает нагрузки с переменным вектором силы;
- легко подвергается термической обработке;
- пластичная;
- устойчива к образованию флокенов;
- не склонна к отпускной хрупкости;
- не имеет ограничений в свариваемости;
- в сварном шве не образуются микропоры.
Хромистые стали
Хромистые стали имеют коэффициент линейного расширения в среднем от 10 до 13·10-6 град-1. Дополнительно стоит отметить стали ШХ15 и 40Х, значение ТКЛР которых составляет 13,4…15,7·10-6 град-1.
Коэффициенты линейного расширения хромистой стали
Марка стали | Температура, °С | ТКЛР·106 1/град |
Сталь 15Х, 15ХА, 20Х | 100…200…300…400…500…600 | 11,3…11,3…12,3…13,2…13,7…14,2 |
Сталь 30Х | 100…200…300…400…500…600…700…800…900…1000 | 12,5…13…13,4…13,8…14,2…14,6…14,8…12…12,8…13,8 |
38ХА, 40Х | -268…-263…-253…-223…-173…-73 | -0,002…0,02…0,2…1,7…6,6…11,5 |
08Х13 | 100…200…300…400…500…600…700…800 | 10,5…11,1…11,4…11,8…12,1…12,3…12,5…12,8 |
08Х17 | 100…200…300…400…500…600…700…800 | 10,4…10,5…10,8…11,2…11,4…11,6…11,9…12,1 |
12Х13 | 100…200…300…400…500…600…700…800…900…1000 | 10,2…11,2…11,4…11,8…12,2…12,4…12,7…13…10,8…11,7 |
15Х28 | 100…500…600…700…800…900 | 10…11,1…11,3…11,5…12…12,4 |
20Х13 | 100…200…300…400…500…600…700…800 | 10,2…11,2…11,5…11,9…12,2…12,8…12,8…13 |
30Х13 | 100…200…300…400…500…600…700…800…900…1000 | 10,2…11…11,1…11,7…12…12,3…12,5…12,6…10,6…12,2 |
40Х | 100…200…400…600 | 13,4…13,3…14,8…14,8 |
40Х13 | 100…200…300…400…500…600…700…800 | 10,7…11,5…11,9…12,2…12,5…12,8…13…13,2 |
95Х18, 95Х18Ш | 100…200…300…400…500…600…700…800 | 11,7…12,1…12,4…12,9…13,3…11,8…12,1…12,4 |
ШХ15 | 100…200…400…600 | 14…15,1…15,5…15,7 |
Отличия
Стали различаются содержанием химических элементов, что влечет за собой разницу в применении.
Ст20 расширяется под воздействием высоких температур, становится пластичной. При низких температурных значениях становится хрупкой. Является более дешевой маркой в сравнении с 09г2с.
Ст.09г2с сохраняет свои первоначальные характеристики, она более износостойкая. Поэтому ее используют для производства стальных элементов, к которым предъявляются повышенные требования к стойкости и температурным изменениям.
Разновидности
Номенклатура продукции из стали этого типа на российском рынке:
- Сортовой и фасонный прокат (ГОСТы 2590-88, 2591-88, 8239-89 и 8240-97)
- Листы толстого типа (ГОСТы 5520-79, 5521-93 и 19903-74)
- Листы тонкого типа (ГОСТы 17066-94, 19903-74 и 19904-90)
- Полосы (ГОСТы 103-76 и 82-70)
- Кованые поковки и заготовки (гост стали 09г2с 1133-71)
Сталь 09г2с выпускается в виде труб, листов, квадратного проката и круглого профиля, полос. Активно используется эта сталь для производства изделий, к уровню износостойкости которых предъявляются высокие требования – балки, углы, швеллеры.
Многие предпочитают покупать листы 09г2с за счет того, что такая сталь популярна и востребована за счет легкости при сваривании. Кроме того, широкий температурный диапазон этой стали позволяет использовать её там, где для других материалов есть риск деформации за продолжительный эксплуатационный срок.
Основные достоинства
К достоинствам этой стали отнесем следующие:
- Структура способна переносить воздействие низкой температуры без изменения основных эксплуатационных качеств. Именно поэтому металл получил распространение в применении на Крайнем Севере.
- Высокий показатель сопротивления на разрыв и прочность определяет то, что металл может использоваться при изготовлении машин, мостов и других ответственных конструкций.
- Низкие затраты на выполнение монтажных работ характеризуются хорошей свариваемостью.
Для соединения металла не нужно проводить временный нагрев.
- Предел текучести при температуре 355 градусов Цельсия составляет 175 МПа, что позволяет получать изделия сложных конфигураций.
Читать также: Краскопульты для побелки стен и потолков
Допускаемое напряжение на материал этой категории зависит от:
- класса прочности;
- толщины, линейных размеров и иных конфигураций заготовок.
Эквивалент рассматриваемой марки производят более чем в 12 странах. Примером назовем то, что в Германии подобной стали получил название DIN, WNr, в Китае G. B. .
Сравнение с другой маркой стали
Например, для 09г2с и ст3 разница определяется прежде всего содержанием углерода. Для Ст3сп оно в 10-20 раз превосходит того, что имеется в сплаве низколегированной марки.
Ст3сп – относится к углеродистым сплавам. Эта марка стали отличается высокой хрупкостью, быстрым разрушением при низких температурах. Если описываемая марка имеет нижний предел -70 градусов, то объект сравнения всего -20.
4 Выбор стали
4.1 Выбор стали для конструкций и сооружений, производится в зависимости от ответственности конструкций зданий и сооружений, климатического района и условий эксплуатации в соответствии со СНиП II-23-81*.
4.2 Стальные конструкции зданий и сооружений могут изготавливаться из стали углеродистой обыкновенного качества (сортовой и фасонный прокат) по ГОСТ 535, стали углеродистой обыкновенного качества (толстолистовой прокат) по ГОСТ 14637, стали повышенной прочности (толстолистовой, фасонный, сортовой прокат и гнутые профили) по ГОСТ 19281 в соответствии с дополнительными требованиями настоящего стандарта.
4.3 Допускаемая замена стали по ГОСТ 27772 указана в таблице 1. В дополнительных требованиях указаны значения ударной вязкости поперечных образцов для толстолистового проката и продольных образцов – для фасонного проката.
4.4 Расчетные сопротивления сталей, используемых для замены, представлены в таблицах 2-4. Значения расчетных сопротивлений рассчитаны для случаев, когда коэффициент надежности по материалу γm = 1,1; 1,05; 1,025 в соответствии со СНиП II-23-81*.
4.5 Для элементов сварных узлов рамных конструкций, фланцевых соединений и других, испытывающих растягивающие напряжения в направлении толщины, требуется листовой прокат с гарантией механических свойств при растяжении в направлении толщины по ТУ 14-1-4431-88 и ТУ 14-1-5136-92 и с гарантией сплошности по ГОСТ 22727. Такой же прокат требуется для некоторых жестких сварных соединений угловой, тавровой и крестообразной формы. Испытания на растяжение проводят согласно ГОСТ 28870.
4.6 В зависимости от конструктивного исполнения узла рамных конструкций, фланцевых соединений, уровня действующих растягивающих напряжений в направлении толщины проката, а также расчетной температуры применяются стали 10ХСНДА и 15ХСНДА по ТУ 14-1-5120-92, 09Г2-У – по ТУ 14-1-5136-92, Ст3сп, 09Г2, 14Г2АФ-Ш и др. – по ТУ 14-1-4431-88.
4.7 Для ответственных элементов сварных узлов конструкций, испытывающих растягивающие напряжения в направлении толщины или наводороживание в результате протекания электрохимических процессов коррозии, следует выставлять дополнительные требования по сплошности проката.
4.8 Требования по ультразвуковому контролю сплошности проката устанавливают с использованием классов сплошности (01, 0, 1, 2 и 3) по ГОСТ 22727-88.
Таблица 1
Вид проката | ГОСТ 27772-88 | Сталь на замену | |||||
обозн. норм, докум. | марка стали | толщина проката, мм | класс прочности | дополнительные требования | |||
1 | 2 | 3 | 4 | 5 | 6 | 7 | 8 |
Фасонный прокат | С235 | ГОСТ 535 | Ст3кп2 | до 20 включительно | – | – | по требованию потребителя содержание S ≤ 0,04% Р ≤ 0,03% |
св. | – | см. 1 примечание | |||||
С245 | Ст3пс5 | до 25 включительно | – | см. 2 примечание | |||
Ст3пс3 | св.25 до 30 включительно | – | см. 2 и 4 примечания | см. 3 и 15 примечания | |||
С255 | Ст3сп5 | до 10 включительно | – | – | |||
– | св. 10 до 25 включительно | – | – | ||||
св.25 до 40 включительно | – | см. 4 примечание | |||||
Ст3сп3 | св.25 до 40 включительно | – | см. 4 примечание | ||||
С345-3 | ГОСТ 19281 | 09Г2С-12 | до 10 включительно | 345 | – | см. | |
св. 10 до 20 включительно | 325 | Ударная вязкость КСU-40 ≥ 34 Дж/см2 обеспечена в соответствии с прим.3 к табл.7 ГОСТ 19281 | |||||
св.20 до 32 включительно | 295 | см. 7 примечание | |||||
св.32 до 40 включительно | 265 | ||||||
ГОСТ 6713 | 15ХСНД, 15ХСНД-2 | св.8 до 32 включительно | – | cм. 8 и 16 примечания | |||
С345-4 | ГОСТ 19281 | 09Г2С-15 | до 10 включительно | 345 | см. 9 примечание | см. 6 и 15 примечания | |
св. 10 до 20 включительно | 325 | см. 11 и 12 примечания | |||||
ГОСТ 6713 | 15ХСНД-3 | св. | см. 13 и 16 примечания | ||||
С235 | Ст3кп2 | до 100 включительно | – | – | по требованию потребителя содержание S ≤ 0,04% Р ≤ 0,03% | ||
С245 1) | ГОСТ 14637 | Ст3пс5, Ст3сп5 | от 5 до 25 включительно | – | см. 10 примечание | ||
С255 | Ст3Гсп5 | от 20 до 40 включительно | – | – | |||
Ст3сн5 | от 5 до 25 включительно | – | см. 10 примечание | ||||
от 26 до 40 включительно | – | см. 4 и 10 примечания | см. 3 и 15 примечания | ||||
Ст3Гпс5 | от 5 до 30 включительно | – | см. | ||||
Ст3Гпс3 | св. 30 до 40 включительно | – | см. 4, 5 примечания | ||||
Толстолистовой прокат | С345-3 | ГОСТ 19281 | 09Г2С-12 | до 10 включительно | 345 | см. 6 и 15 примечания 2) | |
св. 10 до 20 включительно | 325 | см. 6 и 15 примечания | |||||
св.20 до 32 включительно | 295 | см. 6, 7 и 15 примечания | |||||
св.32 до 160 включительно | 265 | ||||||
ГОСТ 6713 | 15ХСНД, 15ХСНД-2 | св.8 до 32 включительно | – | см. 8 и 16 примечания | |||
С345-4 | ГОСТ 19281 | до 10 включительно | 345 | см. | см. 6 и 15 примечания | ||
св. 10 до 20 включительно | 325 | – | |||||
09Г2С-15 | св.20 до 32 включительно | 295 | см. 11 примечание | ||||
св.32 до 160 включительно | 265 | ||||||
ГОСТ 6713 | 15ХСНД-2 15ХСНД-3 | св. 8 до 32 включительно | – | см. 13 и 16 примечания | |||
С390 | ГОСТ 19281 | 10ХСНД-15 | до 5 включительно | 390 | см. 6, 9, 14 и 15 примечания | ||
10ХСНД-12 | св. 5 до 40 включительно | 390 | см. 6, 14 и 15 примечания | ||||
ТУ 14-1-5120-92 | 10ХСНДА-3 | св.8 до 50 включительно | 390 | см. |
1) По ГОСТ 27772 для толстолистового проката толщина проката С245 ограничивается 20 мм включительно.
2) ГОСТ 19281 обеспечивает необходимые требования по ударной вязкости для замены сталей, однако в указанном ГОСТ, опубликованном в сборнике «Сталь углеродистая обыкновенного качества и низколегированная» 1998 и 2001 г.г., имеются опечатки в таблице 6 в части требований по ударной вязкости для сталей класса прочности 345.
Примечания:
- Расчетное сопротивление рассчитывается из условия предел текучести σт = 225 МПа.
- Расчетное сопротивление для толщин проката 20…30 мм рассчитывается из условия σт = 235 МПа.
- В прокате, предназначенном для сварных конструкций, массовая доля углерода не должна превышать 0,22%.
- Ударная вязкость КСU-20 ≥ 29 Дж/см2 и после механического старения КСU ≥ 29 Дж/см2 для толщины проката свыше 25 мм.
- Расчетное сопротивление рассчитывается из условия σт = 245 МПа для толщины проката до 20 мм включительно и σт = 235 МПа – для толщины проката свыше 20 до 40 мм включительно.
- Требования по п.п. 2.2.2-2.2.4, 2.2.6, 2.2.8, 2.2.9, 2.2.12 ГОСТ 19281.
- Ударная вязкость КСU-40 ≥ 34 Дж/см2.
- Ударная вязкость КСU-40 ≥ 39 Дж/см2 для толщины проката 8…10 мм включительно и КСU-40 ≥ 34 Дж/см2 для толщины проката 10…32 мм.
- Ударная вязкость КСU-70 ≥ 34 Дж/см2.
- По согласованию потребителя с изготовителем нормы ударной вязкости для толщин 5-9 мм распространяются на прокат толщиной 4-9 мм.
- Ударная вязкость КСU-70 ≥ 29 Дж/см2.
- Ударная вязкость КСU-70 ≥ 29 Дж/см2 для толщин 10. ..11 мм; а для толщин 11. ..20 мм – КСU-70 ≥ 29 Дж/см2 по согласованию изготовителя с потребителем.
- Ударная вязкость КСU-70 ≥ 34 Дж/см2 для толщины проката 8… 10 мм включительно.
- Ударная вязкость КСU20 ≥ 20 Дж/см2.
- Для проката с гарантией свариваемости дополнительно указывают обозначение «св» согласно п.
3.1. ГОСТ 14637 и 19281. Согласно п.3.1.2 ГОСТ 535 в документах о качестве поставляемой стали дополнительно должны быть указания об обеспечении свариваемости – «cв».
- Согласно п.2.2.4. ГОСТ 6713 и п.2.7 ТУ 14-1-5120-92 прокат изготовляют с гарантией свариваемости.
Таблица 2 – Расчетные сопротивления сталей, используемых на замену (при γm = 1,1)
Вид проката | Обозначение нормативного документа | Марка стали | Толщина проката, мм | Расчетное сопротивление | |||||
Ryn, кг/мм2 | Ry, кг/см2 | Rs кг/см2 | Ryn, МПа | Ry, МПа | Rs, МПа | ||||
Фасонный прокат | ГОСТ 535 | Ст3кп | до 20 включит. | 24 | 2180 | 1260 | 235 | 215 | 125 |
св. 20 до 40 включит. | 23 | 2090 | 1210 | 225 | 205 | 120 | |||
Ст3пс | до 20 включит. | 25 | 2270 | 1310 | 245 | 220 | 130 | ||
св. 20 до 30 включит. | 24 | 2180 | 1260 | 235 | 215 | 125 | |||
Ст3сп | до 10 включит. | 26 | 2360 | 1370 | 255 | 230 | 135 | ||
св. 10 до 20 включит. | 25 | 2270 | 1310 | 245 | 220 | 130 | |||
св. 20 до 40 включит. | 24 | 2180 | 1260 | 235 | 215 | 125 | |||
ГОСТ 19281 | 09Г2С | до 10 включит. | 35 | 3180 | 1840 | 345 | 310 | 180 | |
св. 10 до 20 включит. | 33 | 3000 | 1740 | 325 | 295 | 170 | |||
св. 20 до 32 включит. | 30 | 2730 | 1580 | 295 | 265 | 155 | |||
св. 32 до 40 включит. | 27 | 2450 | 1420 | 265 | 240 | 140 | |||
ГОСТ 6713 | 15ХСНД | св. 8 до 32 включит. | 35 | 3180 | 1840 | 345 | 310 | 180 | |
Толстолистовой прокат | ГОСТ 14637 | Ст3кп | до 20 включит. | 24 | 2180 | 1260 | 235 | 215 | 125 |
св. 20 до 40 включит. | 23 | 2090 | 1210 | 225 | 205 | 120 | |||
св. 40 до 100 включит. | 22 | 2000 | 1160 | 215 | 195 | 115 | |||
Ст3пс | от 5 вкл. до 20 включ. | 25 | 2270 | 1310 | 245 | 220 | 130 | ||
св. 20 до 25 включит. | 24 | 2180 | 1260 | 235 | 215 | 125 | |||
Ст3сп | от 5 вкл. до 20 включ. | 25 | 2270 | 1310 | 245 | 220 | 130 | ||
св. | 24 | 2180 | 1260 | 235 | 215 | 125 | |||
Ст3Гсп | св. 20 до 40 включит. | 25 | 2270 | 1310 | 245 | 220 | 130 | ||
Ст3Гпс | до 20 включительно | 25 | 2270 | 1310 | 245 | 220 | 130 | ||
св. 20 до 40 включит. | 24 | 2180 | 1260 | 235 | 215 | 125 | |||
ГОСТ 19281 | 09Г2С | до 10 включит. | 35 | 3180 | 1840 | 345 | 310 | 180 | |
св. 10 до 20 включит. | 33 | 3000 | 1740 | 325 | 295 | 170 | |||
св. | 30 | 2730 | 1580 | 295 | 265 | 155 | |||
св. 32 до 160 включит. | 27 | 2450 | 1420 | 265 | 240 | 140 | |||
10ХСНД | до 40 включит. | 40 | 3640 | 2100 | 390 | 355 | 205 | ||
ГОСТ 6713 | 5ХСHД | св.8 до 32 включител. | 35 | 3180 | 1840 | 345 | 310 | 180 | |
ТУ 14-1-5120-92 | 10ХСНДА | св.8 до 50 включит. | 40 | 3640 | 2100 | 390 | 355 | 205 |
Таблица 3 – Расчетные сопротивления сталей, используемых на замену (при γm = 1,05)
Вид проката | Обозначение нормативного документа | Марка стали | Толщина проката, мм | Расчетное сопротивление | |||||
Ryn, кг/мм2 | Ry, кг/см2 | Rs кг/см2 | Ryn, МПа | Ry, МПа | Rs, МПа | ||||
Фасонный прокат | ГОСТ 535 | Ст3кп | до 20 включит. | 24 | 2290 | 1330 | 235 | 225 | 130 |
св. 20 до 40 включит. | 23 | 2190 | 1270 | 225 | 215 | 125 | |||
Ст3пс | до 20 включит. | 25 | 2380 | 1380 | 245 | 235 | 135 | ||
св. 20 до 30 включит. | 24 | 2290 | 1330 | 235 | 225 | 130 | |||
Ст3сп | до 10 включит. | 26 | 2480 | 1440 | 255 | 245 | 140 | ||
св. 10 до 20 включит. | 25 | 2380 | 1380 | 245 | 235 | 135 | |||
св. 20 до 40 включит. | 24 | 2290 | 1330 | 235 | 225 | 130 | |||
ГОСТ 19281 | 09Г2С | до 10 включит. | 35 | 3330 | 1930 | 345 | 325 | 190 | |
св. 10 до 20 включит. | 33 | 3140 | 1820 | 325 | 310 | 180 | |||
св. 20 до 32 включит. | 30 | 2860 | 1660 | 295 | 280 | 165 | |||
св. 32 до 40 включит. | 27 | 2570 | 1490 | 265 | 250 | 145 | |||
ГОСТ 6713 | 15ХСНД | св. 8 до 32 включит. | 35 | 3330 | 1930 | 345 | 325 | 190 | |
Толстолистовой прокат | ГОСТ 14637 | Ст3кп | до 20 включит. | 24 | 2290 | 1330 | 235 | 225 | 130 |
св. 20 до 40 включит. | 23 | 2190 | 1270 | 225 | 215 | 125 | |||
св. 40 до 100 включит. | 22 | 2100 | 1220 | 215 | 205 | 120 | |||
Ст3пс | от 5 вкл. до 20 включ. | 25 | 2380 | 1380 | 245 | 235 | 135 | ||
св. 20 до 25 включит. | 24 | 2290 | 1330 | 235 | 225 | 130 | |||
Ст3сп | от 5 вкл. до 20 включ. | 25 | 2270 | 1310 | 245 | 220 | 130 | ||
св. | 24 | 2180 | 1260 | 235 | 215 | 125 | |||
Ст3Гсп | св. 20 до 40 включит. | 25 | 2380 | 1380 | 245 | 235 | 135 | ||
Ст3Гпс | до 20 включительно | 25 | 2380 | 1380 | 245 | 235 | 135 | ||
св. 20 до 40 включит. | 24 | 2290 | 1330 | 235 | 225 | 130 | |||
ГОСТ 19281 | 09Г2С | до 10 включит. | 35 | 3330 | 1930 | 345 | 325 | 190 | |
св. 10 до 20 включит. | 33 | 3140 | 1820 | 325 | 310 | 180 | |||
св. | 30 | 2860 | 1660 | 295 | 280 | 165 | |||
св. 32 до 160 включит. | 27 | 2570 | 1490 | 265 | 250 | 145 | |||
10ХСНД | до 40 включит. | 40 | 3810 | 2210 | 390 | 375 | 215 | ||
ГОСТ 6713 | 5ХСHД | св.8 до 32 включител. | 35 | 3330 | 1930 | 345 | 325 | 190 | |
ТУ 14-1-5120-92 | 10ХСНДА | св.8 до 50 включит. | 40 | 3810 | 2210 | 390 | 375 | 215 |
Таблица 4 – Расчетные сопротивления сталей, используемых на замену (при γm = 1,025)
Вид проката | Обозначение нормативного документа | Марка стали | Толщина проката, мм | Расчетное сопротивление | |||||
Ryn, кг/мм2 | Ry, кг/см2 | Rs кг/см2 | Ryn, МПа | Ry, МПа | Rs, МПа | ||||
Фасонный прокат | ГОСТ 535 | Ст3кп | до 20 включит. | 24 | 2340 | 1360 | 235 | 230 | 135 |
св. 20 до 40 включит. | 23 | 2240 | 1300 | 225 | 220 | 130 | |||
Ст3пс | До20включительно | 25 | 2440 | 1410 | 245 | 240 | 140 | ||
св. 20 до 30 включит. | 24 | 2340 | 1360 | 235 | 230 | 135 | |||
Ст3сп | до 10 включит. | 26 | 2540 | 1470 | 255 | 250 | 145 | ||
св. 10 до 20 включит. | 25 | 2440 | 1410 | 245 | 240 | 140 | |||
св. | 24 | 2340 | 1360 | 235 | 230 | 135 | |||
ГОСТ 19281 | 09Г2С | до 10 включит. | 35 | 3410 | 1980 | 345 | 335 | 195 | |
св. 10 до 20 включит. | 33 | 3220 | 1870 | 325 | 315 | 185 | |||
св. 20 до 32 включит. | 30 | 2930 | 1700 | 295 | 290 | 165 | |||
св. 32 до 40 включит. | 27 | 2630 | 1530 | 265 | 260 | 150 | |||
ГОСТ 6713 | 15ХСНД | св. 8 до 32 включит. | 35 | 3410 | 1980 | 345 | 335 | 195 | |
Толстолистовой прокат | ГОСТ 14637 | Ст3кп | до 20 включит. | 24 | 2340 | 1360 | 235 | 230 | 135 |
св. 20 до 40 включит. | 23 | 2240 | 1300 | 225 | 220 | 130 | |||
св. 40 до 100 включит. | 22 | 2150 | 1240 | 215 | 210 | 120 | |||
Ст3пс | от 5 вкл. до 20 включ. | 25 | 2440 | 1410 | 245 | 240 | 140 | ||
св. 20 до 25 включит. | 24 | 2340 | 1360 | 235 | 230 | 135 | |||
Ст3сп | от 5 вкл. до 20 включ. | 25 | 2270 | 1310 | 245 | 220 | 130 | ||
св. | 24 | 2180 | 1260 | 235 | 215 | 125 | |||
Ст3Гсп | св. 20 до 40 включит. | 25 | 2440 | 1410 | 245 | 240 | 140 | ||
Ст3Гпс | до 20 включительно | 25 | 2440 | 1410 | 245 | 240 | 140 | ||
св. 20 до 40 включит. | 24 | 2340 | 1360 | 235 | 230 | 135 | |||
ГОСТ 19281 | 09Г2С | до 10 включит. | 35 | 3410 | 1980 | 345 | 335 | 195 | |
св. 10 до 20 включит. | 33 | 3220 | 1870 | 325 | 315 | 185 | |||
св. | 30 | 2930 | 1700 | 295 | 290 | 165 | |||
св. 32 до 160 включит. | 27 | 2630 | 1530 | 265 | 260 | 150 | |||
10ХСНД | до 40 включит. | 40 | 3900 | 2260 | 390 | 385 | 220 | ||
ГОСТ 6713 | 5ХСHД | св.8 до 32 включительно | 35 | 3410 | 1980 | 345 | 335 | 195 | |
ТУ 14-1-5120-92 | 10ХСНДА | св.8 до 50 включит. | 40 | 3900 | 2260 | 390 | 385 | 220 |
Влияние равноканального углового прессования на трибологические свойства низкоуглеродистой стали (Fe-0,09C-0,64Si-,26Mn)
Журнал поверхностных инженерных материалов и передовых технологий Vol. 05 No.01 (2015), ID статьи: 52938, 3 страницы
10.4236/jsemat.2015.51003
Влияние равноканального углового прессования на трибологические свойства малоуглеродистой стали (Fe-0,09C-0,64Si-,26Mn)
Мордовской П.Г., Яковлева С.П., Махарова С.Н.
Департамент материаловедения, Институт им. В.П. Ларионов Институт физико-технических проблем Севера СО РАН, Якутск, Россия
Электронная почта: [email protected]
Авторские права © 2015 принадлежат авторам и Scientific Research Publishing Inc. Лицензия (CC BY).
http://creativecommons.org/licenses/by/4.0/
Поступила в редакцию 6 ноября 2014 г.; пересмотрено 9 декабря 2014 г.; принято 22 декабря 2014 г.
АННОТАЦИЯ
В работе представлены результаты равноканального углового прессования (РКУП) и последующей термической обработки (ТО) как метода повышения износостойкости металлических материалов в условиях фрикционного скольжения. В работе исследовано влияние РКУП и ТО на микроструктуру и механические свойства низкоуглеродистой стали.
Ключевые слова:
Низкоуглеродистая сталь, равноканальное угловое прессование, ультратонкие и наноструктуры, термообработка, износ
1. Введение существенно влияет на структуру и свойства материала [1] . В условиях РКУП заготовка пропрессовывается через стальную матрицу, имеющую два канала одинакового сечения, пересекающихся под углом Ф, обычно равным 90˚. Образец механически обрабатывают для плотного прилегания к стенке канала. Большинство научных исследований о влиянии РКУП описывают изменение структуры и механических свойств цветных металлов и их сплавов [2]-[4]. В настоящее время практика промышленного применения РКУП требует более полной информации о поведении материала в трибологических условиях.
Цель: исследование трибологических свойств низкоуглеродистой стали с ультра- и наноструктурами, сформированными методами РКУП и низкотемпературного отжига.
2. Экспериментальный
2.1. Материалы
Исследования проводились на широко используемой в России стали 09Г2С. Химический состав 09Г2С: Fe-0,09C-0,64Si-1,26Mn-0,007P-0,003S-0,08Cr-0,1Ni-0,02Al-0,14Cu-0,002V-0,01Nb-0,013 Ти. Образцы 09Г2С диаметром 20 мм и длиной 100 мм прессовали для РКУП при 20°С. РКУП проводилась двумя циклами прессования по маршруту Bc (поворот на 90° после каждого сжатия) с углом пересечения каналов Φ = 90°; после РКУП образцы подвергались термической обработке (ТО): кратковременному низкотемпературному отжигу при 350°С и 450°С с выдержкой 1 час [5] . После РКУП и ТО были подготовлены образцы для трибологических испытаний в виде бруска размерами: 5×10×5 мм с шероховатостью Ra 2,9.0006
Исследования микроструктуры проводились с использованием сканирующего электронного микроскопа JEOL JSM-6480LV. Трибологические испытания проводились на машине трения с площадью контакта 5×5 мм. Испытания на сухое трение скольжения проводились на стальном листе твердостью 50 – 52 HRC, путь трения – 560 м, нагрузка – 150, 225, 300 и 375 Н [6].
3. Результаты и обсуждение
3.1. Микроструктура
Микроструктура исходного материала была ферритно-перлитной, размер зерен феррита колеблется в пределах 4,35 мкм (средний диаметр -10 мкм). Предыдущие исследования [5] стали 09Г2С после РКУП показал, что его микроструктура состоит из распределений в деформированной ферритной матрице карбидов диаметром ~300-500 нм. Средний размер ферритных участков, свободных от карбидной фазы, составляет около 5 мкм, что более чем в 2 раза меньше среднего размера зерен феррита-оригинала.
На рис. 1 представлена микроструктура стали после РКУП и ТО: средний размер ферритных участков уменьшается, продолжается процесс диспергирования карбидов, сопровождающийся их сфероидизацией и диспергированием. В пластинчатых перлитных группах при деформации наблюдается изменение расстояний между пластинами; в ферритовых пластинах происходит образование ячеистой структуры, вытянутой вдоль оси скольжения в виде вторичной системы скольжения, пластины из карбида цемента постепенно истончаются и дробятся.
3.2. Механические свойства
Механические свойства образцов при растяжении представлены в табл. 1. Как видно из табл. 1, РКУП вызвал почти трехкратное увеличение предела текучести σ T и предела прочности σ B по сравнению с исходным состоянием. Сближение этих показателей характерно для стали в высокопрочном состоянии. Резкий рост прочности происходит за счет интенсивного рассеивания. Наибольшие значения прочности получили образцы, обработанные в следующих режимах: РКУП при 20°С и нагреве до 350°С, РКУП при 20°С без ТО и РКУП при 350°С без ТО соответственно.
3.3. Трибологические свойства
Трибологические свойства ферритно-перлитной стали определяются комплексом физико-
Таблица 1. Механические свойства стали 09Г2С после различных видов обработки.
Рис. 1. Микроструктура после холодного РКУП с увеличением (а) ×10000; (б) ×20 000; после холодного РКУП и отжига при 350°С; (в) ×10 000; (г) ×20 000; после холодного РКУП и отжига при 450°С; (д) ×10 000; (е) ×20 000.
Характеристики в зависимости от количества и дисперсности структурно-свободного феррита, размера и формы карбидных частиц, деформационного поведения, сопротивления возникновению микротрещин. Для повышения износостойкости необходимо применять химическую, термическую и механическую обработку, вызывающую повышение твердости, оптимальное распределение дисперсных частиц карбидной фазы, микролегирование и др.
В табл. 2 приведены результаты трибологических испытаний при сухом трении с различные значения нормальной нагрузки. Износ образцов в исходном состоянии и после РКУП при нагрузке 150 и 225 Н низкий. Рост нагрузки до 300 Н приводит к значительному увеличению износа сырья за счет перехода к адгезионному схватыванию.
При нагрузке 375 Н массовый износ образцов воздуха снижается вследствие изменения режима трения, что повышает способность материала сопротивляться растрескиванию и образованию частиц износа, но в образце после РКУП и при отжиге при 450°С произошло однократное увеличение износа до величины 260 мг, что соответствует изменению характера трения с микрорезания на адгезионное схватывание. При испытаниях в зонах фактического контакта под нагрузкой происходит укрепление более мягкого рисунка за счет увеличения плотности дислокаций и образования вторичной фрагментарной структуры поверхностного слоя.
Таблица 2. Массовый износ при сухом трении скольжения.
между образованием и разрушением вторичных структур механического и химического происхождения, т.е. может наблюдаться неравномерный во времени циклический износ поверхности трения из-за специфики упругого деформирования поверхностных слоев тел.
Лучшую износостойкость показала сталь, обработанная по режимам РКУП и ТО. Высокая износостойкость стали с УМЗ и наноструктурой, сформированной РКУП ТО, обусловлена особенностями трибологического разрушения объемно-деформированного материала. После РКУП наблюдается текстурирование зерен феррита вдоль оси заготовки, совпадающей с осью канала матрицы, что должно сказываться на структуре образуемой поверхности трения в зависимости от направления трибопары. При трибообработке деформированной стали в поверхностном слое происходят следующие процессы: разрушение (фрагментация) зерен феррита, текстурирование ферритных полос и перераспределение карбидов по линии скольжения; также можно наблюдать больший эффект таких вещей, как зернограничное скольжение и вращение крупных зерен в УМЗ и наноструктурированных материалах. Воздействие трибопарного нагрева частично вызывает рекристаллизацию зерен в поверхностном слое материала. Меньший размер зерна должен обеспечивать более равномерный снос частиц износа с поверхности трения по сравнению с исходным крупнозернистым материалом. Дальнейшее движение частиц износа по поверхности трения должно вызывать меньшее разрушение поверхности трения, т. е. уменьшается влияние абразивного износа, а также «выдолбления» поверхности трения частицами износа.
4. Заключение
Полученные результаты показывают, что при низкотемпературном отжиге при 350°С и 450°С РКУП можно использовать как технологию снижения износа при трении скольжения, если не превышена критическая нагрузка. Тогда нагрузка больше, чем предел прочности материала.
Литература
- Валиев Р.З. и Александров И.В. (2000) Наноструктурные материалы, полученные в результате интенсивной пластической деформации. Логотипы.
- Жа, М., Ли, Ю.-Дж., Матисен, Р., Бьёрге, Р. и Ровен, Х. Дж. (2014) Микроструктура, изменение твердости и термическая стабильность бинарного сплава Al-7Mg, обработанного методом РКУП с промежуточным отжигом . Труды Общества цветных металлов Китая, 24, 2301-2306.
- Ю, Х., Ли, Ю.Л. и Ли, Л. (2014) Влияние измельчения зерна на вязкость разрушения и механизм разрушения магниевого сплава AZ31. Procedia Materials Science, 3, 1780-1785. http://dx.doi.org/10.1016/j.mspro.2014.06.287
- Шаери М.Х., Салехи М.Т., Сейедейн С.
Х., Абуталеби М.Р. и Парк Дж.К. (2014) Микроструктура и механические свойства сплава Al-7075, обработанного равноканальным угловым прессованием в сочетании с обработкой старением. Материалы и дизайн, 57, 250-257. http://dx.doi.org/10.1016/j.matdes.2014.01.008
- Яковлева С.П., Махарова С.Н. и Борисова М.З. (2009) Формирование наноразмерных структурных элементов в стали 09Г2С при низкотемпературном отжиге после интенсивной пластической деформации. Сборник статей III Международной конференции «Деформация и разрушение материалов и наноматериалов», Москва, 2004, Вып. 1, 256-257.
- Яковлева С.П., Махарова С.Н., Мордовской П.Г., Борисова М.З. и Винокуров Г.Г. (2011) Износостойкость и поверхность трения легированной стали с различной зернистостью. Металлургического машиностроения, 4, 26-29.
Microsoft Word – 007_YIT_ITEE06
%PDF-1.4 % 1 0 объект > /OCG [6 0 R 7 0 R] >> /Тип /Каталог /Акроформ 8 0 Р /Метаданные 9 0 R /Страниц 10 0 Р >> эндообъект 11 0 объект > эндообъект 2 0 объект > эндообъект 3 0 объект > эндообъект 4 0 объект > эндообъект 5 0 объект > эндообъект 6 0 объект > /Вид > /Элемент страницы > /Печать > >> /Тип /ОКГ /Имя (Водяной знак) >> эндообъект 7 0 объект > >> /Тип /ОКГ /Имя (верхние/нижние колонтитулы) >> эндообъект 8 0 объект > /Шрифт > >> /DA (/Helv 0 Tf 0 г ) >> эндообъект 90 объект > ручей приложение/pdf
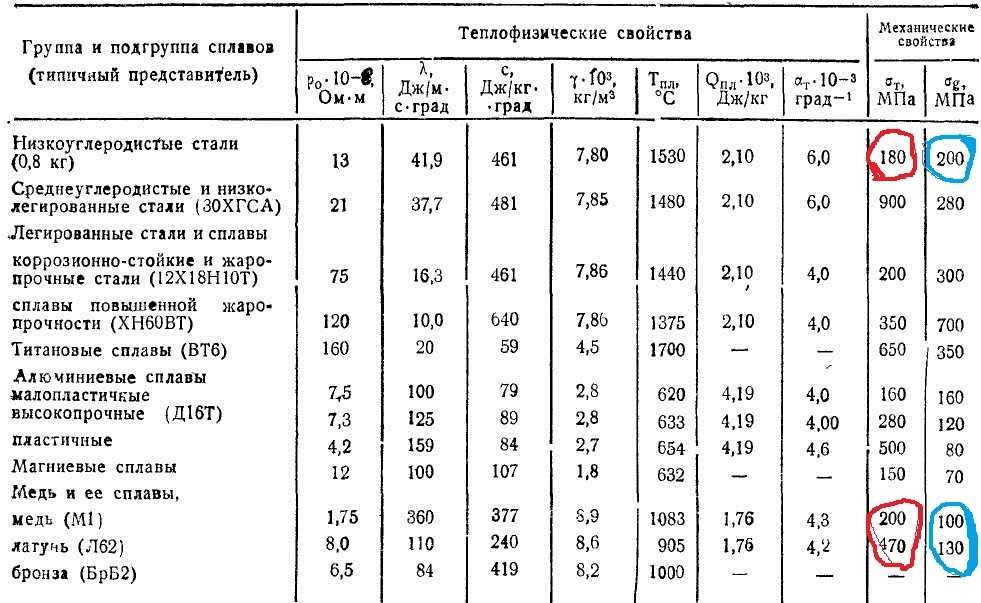