Предел прочности стали на изгиб: Допускаемое напряжение на изгиб. Предельные и допустимые напряжения
alexxlab | 10.12.2017 | 0 | Разное
Предел прочности стали при сжатии и растяжении
Прочность металлических конструкций – один из важнейших параметров, определяющих их надежность и безопасность. Издревле вопросы прочности решались опытным путем — если какое-либо изделие ломалось — то следующее делали толще и массивнее. С 17 века ученые начали планомерное исследование проблемы, прочностные параметры материалов и конструкций из них можно рассчитать заранее, на этапе проектирования. Металлурги разработали добавки, влияющие на прочность стальных сплавов.


Предел прочности
Предел прочности — это максимальное значение напряжений, испытываемых материалом до того, как он начнет разрушаться. Его физический смысл определяет усилие растяжения, которое нужно приложить к стрежневидному образцу определенного сечения, чтобы разорвать его.
Каким образом производится испытание на прочность
Прочностные испытания на сопротивление разрыву проводятся на специальных испытательных стендах. В них неподвижно закрепляется один конец испытываемого образца, а к другому присоединяют крепление привода, электромеханического или гидравлического. Этот привод создает плавно увеличивающее усилие, действующее на разрыв образца, или же на его изгиб или скручивание.


Испытание на разрыв
Электронная система контроля фиксирует усилие растяжения и относительное удлинение, и другие виды деформации образца.
Виды пределов прочности
Предел прочности — один из главных механических параметров стали, равно как и любого другого конструкционного материала.
Эта величина используется при прочностных расчетах деталей и конструкций, судя по ней, решают, применим ли данный материал в конкретной сфере или нужно подбирать более прочный.
Различают следующие виды предела прочности при:
- сжатии — определяет способность материала сопротивляться давлению внешней силы;
- изгибе — влияет на гибкость деталей;
- кручении – показывает, насколько материал пригоден для нагруженных приводных валов, передающих крутящий момент;
- растяжении.


Виды испытаний прочности материалов
Научное название параметра, используемое в стандартах и других официальных документах — временное сопротивление разрыву.
Предел прочности стали
На сегодняшний день сталь все еще является наиболее применяемым конструкционным материалом, понемногу уступая свои позиции различным пластмассам и композитным материалам. От корректного расчета пределов прочности металла зависит его долговечность, надежность и безопасность в эксплуатации.
Предел прочности стали зависит от ее марки и изменяется в пределах от 300 Мпа у обычной низкоуглеродистой конструкционной стали до 900 Мпа у специальных высоколегированных марок.
На значение параметра влияют:
- химический состав сплава;
- термические процедуры, способствующие упрочнению материалов: закалка, отпуск, отжиг и т.д.
Некоторые примеси снижают прочность, и от них стараются избавляться на этапе отливки и проката, другие, наоборот, повышают. Их специально добавляют в состав сплава.
Условный предел текучести
Кроме предела прочности, в инженерных расчетах широко применяется связанное с ним понятие-предел текучести, обозначаемый σт. Он равен величине напряжения сопротивления разрыву, которое необходимо создать в материале, для того, чтобы деформация продолжала расти без наращивания нагрузки. Это состояние материала непосредственно предшествует его разрушению.
На микроуровне при таких напряжениях начинают рваться межатомные связи в кристаллической решетке, а на оставшиеся связи увеличивается удельная нагрузка.
Общие сведения и характеристики сталей
С точки зрения конструктора, наибольшую важность для сплавов, работающих в обычных условиях, имеют физико-механические параметры стали. В отдельных случаях, когда изделию предстоит работать в условиях экстремально высоких или низких температур, высокого давления, повышенной влажности, под воздействием агрессивных сред — не меньшую важность приобретают и химические свойства стали. Как физико-механические, так и химические свойства сплавов во многом определяются их химическим составом.
Влияние содержание углерода на свойства сталей
По мере увеличения процентной доли углерода происходит снижение пластичности вещества с одновременным ростом прочности и твердости. Этот эффект наблюдается до приблизительно 1% доли, далее начинается снижение прочностных характеристик.
Повышение доли углерода также повышает порог хладоемкости, это используется при создании морозоустойчивых и криогенных марок.


Влияние углерода на механические свойства стали
Рост содержания С приводит к ухудшению литейных свойств, отрицательно влияет на способность материала к механической обработке.
Добавки марганца и кремния
Mn содержится в большинстве марок стали. Его применяют для вытеснения из расплава кислорода и серы. Рост содержания Mn до определенного предела (2%) улучшает такие параметры обрабатываемости, как ковкость и свариваемость. После этого предела дальнейшее увеличение содержания ведет к образованию трещин при термообработке.
Влияние кремния на свойства сталей
Si применяется в роли раскислителя, используемого при выплавке стальных сплавов и определяет тип стали. В спокойных высокоуглеродистых марках должно содержаться не более 0,6% кремния. Для полуспокойных марок этот предел еще ниже — 0,1 %.
При производстве ферритов кремний увеличивает их прочностные параметры, не понижая пластичности. Этот эффект сохраняется до порогового содержания в 0,4%.


Влияние легирующих добавок на свойства стали
В сочетании с Mn или Mo кремний способствует росту закаливаемости, а вместе с Сг и Ni повышает коррозионную устойчивость сплавов.
Азот и кислород в сплаве
Эти самые распространенные в земной атмосфере газы вредно влияют на прочностные свойства. Образуемые ими соединения в виде включений в кристаллическую структуру существенно снижают прочностные параметры и пластичность.
Легирующие добавки в составе сплавов
Это вещества, намеренно добавляемые в расплав для улучшения свойств сплава и доведения его параметров до требуемых. Одни из них добавляются в больших количествах (более процента), другие — в очень малых. Наиболее часто применяю следующие легирующие добавки:
- Хром. Применяется для повышения прокаливаемости и твердости. Доля – 0,8-0,2%.
- Бор. Улучшает хладноломкость и радиационную стойкость. Доля – 0,003%.
- Титан. Добавляется для улучшения структуры Cr-Mn сплавов. Доля – 0,1%.
- Молибден. Повышает прочностные характеристики и коррозионную стойкость, снижает хрупкость. Доля – 0,15-0,45%.
- Ванадий. Улучшает прочностные параметры и упругость. Доля – 0,1-0,3%.
- Никель. Способствует росту прочностных характеристик и прокаливаемости, однако при этом ведет к увеличению хрупкости. Этот эффект компенсируют одновременным добавлением молибдена.
Металлурги используют и более сложные комбинации легирующих добавок, добиваясь получения уникальных сочетаний физико-механических свойств стали. Стоимость таких марок в несколько раз (а то и десятков раз) превышает стоимость обычных низкоуглеродистых сталей. Применяются они для особо ответственных конструкций и узлов.
Пределы прочности материалов
Быстрый поиск
Определённая пороговая величина для конкретного материала, превышение которой приведёт к разрушению объекта под действием механического напряжения. Основные виды пределов прочности: статический, динамический, на сжатие и на растяжение. Например, предел прочности на растяжение — это граничное значение постоянного (статический предел) или переменного (динамический предел) механического напряжения, превышение которого разорвет (или неприемлемо деформирует) изделие. Единица измерения — Паскаль [Па], Н/мм ² = [МПа].
Предел текучести (σт)
Величина механического напряжения, при которой деформация продолжает увеличиваться без увеличения нагрузки; служит для расчётов допустимых напряжений пластичных материалов.
После перехода предела текучести в структуре металла наблюдаются необратимые изменения: кристаллическая решетка перестраивается, появляются значительные пластические деформации. Вместе с тем происходит самоупрочнение металла и после площадки текучести деформация возрастает при увеличении растягивающей силы.
Нередко этот параметр определяют как «напряжение, при котором начинает развиваться пластическая деформация» [1], таким образом, отождествляя пределы текучести и упругости. Однако следует понимать, что это два разных параметра. Значения предела текучести превышают предел упругости ориентировочно на 5%.
Предел выносливости или предел усталости (σR)
Способность материала воспринимать нагрузки, вызывающие циклические напряжения. Этот прочностной параметр определяют как максимальное напряжение в цикле, при котором не происходит усталостного разрушения изделия после неопределенно большого количества циклических нагружений (базовое число циклов для стали Nb = 10 7). Коэффициент R (σR) принимается равным коэффициенту асимметрии цикла. Поэтому предел выносливости материала в случае симметричных циклов нагружения обозначают как σ -1, а в случае пульсационных — как σ0.
Отметим, что усталостные испытания изделий очень продолжительны и трудоёмки, они включают анализ больших объёмов экспериментальных данных при произвольном количестве циклов и существенном разбросе значений. Поэтому чаще всего используют специальные эмпирические формулы, связывающие предел выносливости с другими прочностными параметрами материала. Наиболее удобным параметром при этом считается предел прочности.
Для сталей предел выносливости при изгибе как правило составляет половину от предела прочности: Для высокопрочных сталей можно принять:
Для обычных сталей при кручении в условиях циклически изменяющихся напряжений можно принять:
Приведённые выше соотношения стоит применять осмотрительно, потому что они получены при конкретных режимах нагружения, т.е. при изгибе и при кручении. Однако, при испытании на растяжение-сжатие предел выносливости становится примерно на 10—20% меньше, чем при изгибе.
Предел пропорциональности (σ)
Максимальная величина напряжения для конкретного материала, при которой ещё действует закон Гука, т.е. деформация тела прямо пропорционально зависит от прикладываемой нагрузки (силы). Обратите внимание, что для множества материалов достижение (но не превышение!) предела упругости приводит к обратимым (упругим) деформациям, которые, впрочем, уже не прямо пропорциональны напряжениям. При этом такие деформации могут несколько «запаздывать» относительно роста или снижения нагрузки.
Диаграмма деформации металлического образца при растяжении в координатах удлинение (Є) — напряжение (σ).
1:Предел абсолютной упругости.
2:Предел пропорциональности.
3:Предел упругости.
4:Предел текучести. (σ 0.2)
ГОСТ 14249-89 Напряжения марок сталей
Главная / Проектировщику / Справочная информация – ГОСТ СНИП ПБ / ГОСТ 14249-89 / Версия для печатиТаблица 5. Допускаемые напряжения для углеродистых и низколегированных сталей
Расчет ная темпе ратура стенки сосуда или аппарата, °С | Допускаемое напряжение [σ], МПа (кгс/см2), для сталей марок | |||||||
---|---|---|---|---|---|---|---|---|
ВСт3 | 09Г2С, 16ГС | 20, 20К | 10 | 10Г2, 09Г2 | 17ГС, 17Г1С, 10Г2С1 | |||
толщина, мм | ||||||||
до 20 | свыше 20 | до 32 | свыше 32 | до 160 | ||||
20 | 154 (1540) | 140 (1400) | 196 (1960) | 183 (1830) | 147 (1470) | 130 (1300) | 180 (1800) | 183 (1830) |
100 | 149 (1490) | 134 (1340) | 177 (1770) | 160 (1600) | 142 (1420) | 125 (1250) | 160 (1600) | 160 (1600) |
150 | 145 (1450) | 131 (1310) | 171 (1710) | 154 (1540) | 139 (1390) | 122 (1220) | 154 (1540) | 154 (1540) |
200 | 142 (1420) | 126 (1260) | 165 (1650) | 148 (1480) | 136 (1360) | 118 (1180) | 148 (1480) | 148 (1480) |
250 | 131 (1310) | 120 (1200) | 162 (1620) | 145 (1450) | 132 (1320) | 112 (1120) | 145 (1450) | 145 (1450) |
300 | 115 (1150) | 108 (1080) | 151 (1510) | 134 (1340) | 119 (1190) | 100 (1000) | 134 (1340) | 134 (1340) |
350 | 105 (1050) | 98 (980) | 140 (1400) | 123 (1230) | 106 (1060) | 88 (880) | 123 (1230) | 123 (1230) |
375 | 93 (930) | 93 (930) | 133 (1330) | 116 (1160) | 98 (980) | 82 (820) | 108 (1080) | 116 (1160) |
400 | 85 (850) | 85 (850) | 122 (1220) | 105 (1050) | 92 (920) | 77 (770) | 92 (920) | 105 (1050) |
410 | 81 (810) | 81 (810) | 104 (1040) | 104 (1040) | 75 (750) | 86 (860) | 104 (1040) | |
420 | 75 (750) | 75 (750) | 92 (920) | 92 (920) | 80 (800) | 72 (720) | 80 (800) | 92 (920) |
430 | 71* (710) | 71* (710) | 86 (860) | 86 (860) | 75 (750) | 68 (680) | 75 (750) | 86 (860) |
440 | – | – | 78 (780) | 78 (780) | 67 (670) | 60 (600) | 67 (670) | 78 (780) |
450 | – | – | 71 (710) | 71 (710) | 61 (610) | 53 (530) | 61 (610) | 71 (710) |
460 | – | – | 64 (640) | 64 (640) | 55 (550) | 47 (470) | 55 (550) | 64 (640) |
470 | – | 56 (560) | 56 (560) | 49 (490) | 42 (420) | 49 (490) | 56 (560) | |
480 | – | – | 53 (530) | 53 (530) | 46* (460) | 37 (370) | 46** (460) | 53 (530) |
________________ * Для расчетной температуры стенки 425 °С. ** Для расчетной температуры стенки 475 °С. |
Примечания:
1. При расчетных температурах ниже 20 °С допускаемые напряжения принимают такими же, как при 20 °С, при условии допустимого применения материала при данной температуре.
2. Для промежуточных расчетных температур стенки допускаемое напряжение определяют линейной интерполяцией с округлением результатов до 0,5 МПа (5 кгс/см2) в сторону меньшего значения.
3. Для стали марки 20 при R20e<220 МПа (2200 кгс/см2) допускаемые напряжения, указанные в табл.1, умножают на отношение R20e/220 (R20e/2200).
4. Для стали марки 10Г2 при R20p0,2 <270 МПа (2700 кгс/см2) допускаемые напряжения, указанные в табл.1, умножают на отношение R20p0,2 /270 (R20p0,2 <2700).
5. Для стали марок 09Г2С, 16ГС классов прочности 265 и 296 по ГОСТ 19281 допускаемые напряжения независимо от толщины листа принимают равными указанным в графе, соответствующей толщине свыше 32 мм.
Таблица 6. Допускаемые напряжения для теплоустойчивых хромистых сталей
Расчетная температура стенки сосуда или аппарата, °С | Допускаемое напряжение [σ], МПа (кгс/см2), для сталей марок, МПа (кгс/см2), для сталей марок | ||||
---|---|---|---|---|---|
12ХМ | 12МХ | 15ХМ | 15Х5М | 15Х5М-У | |
20 | 147 (1470) | 147 (1470) | 155 (1550) | 146 (1460) | 240 (2400) |
100 | 146,5 (1465) | 146,5 (1465) | 153 (1530) | 141 (1410) | 235 (2350) |
150 | 146 (1460) | 146 (1460) | 152,5 (1525) | 138 (1380) | 230 (2300) |
200 | 145 (1450) | 145 (1450) | 152 (1520) | 134 (1340) | 225 (2250) |
250 | 145 (1450) | 145 (1450) | 152 (1520) | 127 (1270) | 220 (2200) |
300 | 141 (1410) | 141 (1410) | 147 (1470) | 120 (1200) | 210 (2100) |
350 | 137 (1370) | 137 (1370) | 142 (1420) | 114 (1140) | 200 (2000) |
375 | 135 (1350) | 135 (1350) | 140 (1400) | 110 (1100) | 180 (1800) |
400 | 132 (1320) | 132 (1320) | 137 (1370) | 105 (1050) | 170 (1700) |
410 | 130 (1300) | 130 (1300) | 136 (1360) | 103 (1030) | 160 (1600) |
420 | 129 (1290) | 129 (1290) | 135 (1350) | 101 (1010) | 150 (1500) |
430 | 127 (1270) | 127 (1270) | 134 (1340) | 99 (990) | 140 (1400) |
440 | 126 (1260) | 126 (1260) | 132 (1320) | 96 (960) | 135 (1350) |
450 | 124 (1240) | 124 (1240) | 131 (1310) | 94 (940) | 130 (1300) |
460 | 122 (1220) | 122 (1220) | 127 (1270) | 91 (910) | 126 (1260) |
470 | 117 (1170) | 117 (1170) | 122 (1220) | 89 (890) | 122 (1220) |
480 | 114 (1140) | 114 (1140) | 117 (1170) | 86 (860) | 118 (1180) |
490 | 105 (1050) | 105 (1050) | 107 (1070) | 83 (830) | 114 (1140) |
500 | 96 (960) | 96 (960) | 99 (990) | 79 (790) | 108 (1080) |
510 | 82 (820) | 82 (820) | 84 (840) | 72 (720) | 97 (970) |
520 | 69 (690) | 69 (690) | 74 (740) | 66 (660) | 85 (850) |
530 | 60 (600) | 57 (570) | 67 (670) | 60 (600) | 72 (720) |
540 | 50 (500) | 47 (470) | 57 (570) | 54 (540) | 58 (580) |
550 | 41 (410) | – | 49 (490) | 47 (470) | 52 (520) |
560 | 33 (330) | – | 41 (410) | 40 (400) | 45 (450) |
570 | – | – | – | 35 (350) | 40 (400) |
580 | – | – | – | 30 (300) | 34 (340) |
590 | – | – | – | 28 (280) | 30 (300) |
600 | – | – | – | 25 (250) | 25 (250) |
Примечания:
1. При расчетных температурах ниже 20 °С допускаемые напряжения принимают такими же, как при 20 °С, при условии допустимого применения материала при данной температуре.
2. Для промежуточных расчетных температур стенки допускаемое напряжение определяют линейной интерполяцией с округлением результатов до 0,5 МПа (5 кгс/см2) в сторону меньшего значения.
3. При расчетных температурах ниже 200 °С сталь марок 12МХ, 12ХМ, 15ХМ применять не рекомендуется.
Таблица 7 * Допускаемые напряжения для жаропрочных, жаростойких и коррозионностойких сталей аустенитного класса
Расчетная температура стенки сосуда или аппарата, °С | Допускаемое напряжение[σ], МПа (кгс/см2), для сталей марок | ||||
---|---|---|---|---|---|
03Х21Н21М4ГБ | 03Х18Н11 | 03Х17Н14М3 |
08Х18Н10Т, 08Х18Н12Т, 08Х17Н13М2Т, 08Х17Н15М3Т |
12Х18Н10Т, 12Х18Н12Т, 10Х17Н13М2Т, 10Х17Н13М3Т |
|
20 | 180 (1800) | 160 (1600) | 153 (1530) | 168 (1680) | 184 (1840) |
100 | 173 (1730) | 133 (1330) | 140 (1400) | 156 (1560) | 174 (1740) |
150 | 171 (1710) | 125 (1250) | 130 (1300) | 148 (1480) | 168 (1680) |
200 | 171 (1710) | 120 (1200) | 120 (1200) | 140 (1400) | 160 (1600) |
250 | 167 (1670) | 115 (1150) | 113 (1130) | 132 (1320) | 154 (1540) |
300 | 149 (1490) | 112 (1120) | 103 (1030) | 123 (1230) | 148 (1480) |
350 | 143 (1430) | 108 (1080) | 101 (1010) | 113 (1130) | 144 (1440) |
375 | 141 (1410) | 107 (1070) | 90 (900) | 108 (1080) | 140 (1400) |
400 | 140 (1400) | 107 (1070) | 87 (870) | 103 (1030) | 137 (1370) |
410 | – | 107 (1070) | 83 (830) | 102 (1020) | 136 (1360) |
420 | – | 107 (1070) | 82 (820) | 101 (1010) | 135 (1350) |
430 | – | 107 (1070) | 81 (810) | 100,5 (1005) | 134 (1340) |
440 | – | 107 (1070) | 81 (810) | 100 (1000) | 133 (1330) |
450 | – | 107 (1070) | 80 (800) | 99 (990) | 132 (1320) |
460 | – | – | – | 98 (980) | 131 (1310) |
470 | – | – | – | 97,5 (975) | 130 (1300) |
480 | – | – | – | 97 (970) | 129 (1290) |
490 | – | – | – | 96 (960) | 128 (1280) |
500 | – | – | – | 95 (950) | 127 (1270) |
510 | – | – | – | 94 (940) | 126 (1260) |
520 | – | – | – | 79 (790) | 125 (1250) |
530 | – | – | – | 79 (790) | 124 (1240) |
540 | – | – | – | 78 (780) | 111 (1110) |
550 | – | – | – | 76 (760) | 111 (1110) |
560 | – | – | – | 73 (730) | 101 (1010) |
570 | – | – | – | 69 (690) | 97 (970) |
580 | – | – | – | 65 (650) | 90 (900) |
590 | – | – | – | 61 (610) | 81 (810) |
600 | – | – | – | 57 (570) | 74 (740) |
610 | – | – | – | – | 68 (680) |
620 | – | – | – | – | 62 (620) |
630 | – | – | – | – | 57 (570) |
640 | – | – | – | – | 52 (520) |
650 | – | – | – | – | 48 (480) |
660 | – | – | – | – | 45 (450) |
670 | – | – | – | – | 42 (420) |
680 | – | – | – | – | 38 (380) |
690 | – | – | – | – | 34 (340) |
700 | – | – | – | – | 30 (300) |
_______________ * Данные таблицы соответствует оригиналу. – Примечание изготовителя базы данных.
Примечания:
1. При расчетных температурах ниже 20 °С допускаемые напряжения принимают такими же, как и при 20 °С, при условии допустимого применения материала при данной температуре.
2. Для промежуточных расчетных температур стенки допускаемое напряжение определяют интерполяцией двух ближайших значений, указанных в таблице, с округлением результатов до 0,5 МПа (5 кгс/см2) в сторону меньшего значения.
3. Для поковок из стали марок 12Х18Н10Т, 10Х17Н13М2Т, 10Х17Н13М3Т допускаемые напряжения, приведенные в табл.7 при температурах до 550 °С, умножают на 0,83.
4. Для сортового проката из стали марок 12Х18Н10Т, 10Х17Н13М2Т, 10Х17Н13М3Т допускаемые напряжения, приведенные в табл.7 при температурах до 550 °С, умножают на отношение
,
где Rp0,2* – предел текучести материала сортового проката определен по ГОСТ 5949; для сортового проката из стали марки 03Х18Н11 допускаемые напряжения умножаются на 0,8.
5. Для поковок и сортового проката из стали марки 08Х18Н10Т допускаемые напряжения, приведенные в табл.7 при температурах до 550 °С, умножают на 0,95.
6. Для поковок из стали марки 03Х17Н14М3 допускаемые напряжения, приведенные в табл.7, умножают на 0,9.
7. Для поковок из стали марки 03Х18Н11 допускаемые напряжения, приведенные в табл.7, умножают на 0,9; для сортового проката из стали марки 03Х18Н11 допускаемые напряжения умножают на 0,8.
8. Для труб из стали марки 03Х21Н21М4ГБ (ЗИ-35) допускаемые напряжения, приведенные в табл.7, умножают на 0,88.
9. Для поковок из стали марки 03Х21Н21М4ГБ (ЗИ-35) допускаемые напряжения, приведенные в табл.7, умножают на отношение
,
где Rp0,2* – предел текучести материала поковок, определен по ГОСТ 25054 (по согласованию).
Таблица 8. Допускаемые напряжения для жаропрочных, жаростойких и коррозионностойких сталей аустенитного и аустенито-ферритного класса
Расчетная температура стенки сосуда или аппарата, °С | Допускаемое напряжение [σ], МПа (кгс/см2), для сталей марок | |||||
---|---|---|---|---|---|---|
08Х18Г8Н2Т (КО-3) | 07Х13АГ20 (ЧС-46) | 02Х8Н22С6 (ЭП-794) | 15Х18Н12С4ТЮ (ЭИ-654) | 06ХН28МДТ, 03ХН28МДТ | 08Х22Н6Т, 08Х21Н6М2Т | |
20 | 230 (2300) | 233 (2330) | 133 (1330) | 233 (2330) | 147 (1470) | 233 (2330) |
100 | 206 (2060) | 173 (1730) | 106,5 (1065) | 220 (2200) | 138 (1380) | 200 (2000) |
150 | 190 (1900) | 153 (1530) | 100 (1000) | 206,5 (2065) | 130 (1300) | 193 (1930) |
200 | 175 (1750) | 133 (1330) | 90 (900) | 200 (2000) | 124 (1240) | 188,5 (1885) |
250 | 160 (1600) | 127 (1270) | 83 (830) | 186,5 (1865) | 117 (1170) | 166,5 (1665) |
300 | 144 (1440) | 120 (1200) | 76,5 (765) | 180 (1800) | 110 (1100) | 160 (1600) |
350 | – | 113 (1130) | – | – | 107 (1070) | |
375 | – | 110 (1100) | – | – | 105 (1050) | |
400 | – | 107 (1070) | – | – | 103 (1030) |
Примечания:
1. При расчетных температурах ниже 20 °С допускаемые напряжения принимают такими же, как и при 20 °С, при условии допустимого применения материала при данной температуре.
2. Для промежуточных расчетных температур стенки допускаемое напряжение определяют интерполяцией двух ближайших значений, указанных в таблице, с округлением до 0,5 МПа (5 кгс/см2) в сторону меньшего значения.
<< назад / к содержанию ГОСТ 14249-89 / вперед >>
Для определения допускаемых напряжений в машиностроении применяют следующие основные методы.
1. Дифференцированный запас прочности находят как произведение ряда частных коэффициентов, учитывающих надежность материала, степень ответственности детали, точность расчетных формул и действующие силы и другие факторы, определяющие условия работы деталей.
2. Табличный – допускаемые напряжения принимают по нормам, систематизированным в виде таблиц
(табл. 1 – 7). Этот метод менее точен, но наиболее прост и удобен для практического пользования при проектировочных и проверочных прочностных расчетах.
Натяжные линии в неповрежденном материале и в случае трещин. До круиза в первом классе был построен новый пассажирский лифт, прорезающий прямоугольные отверстия с острыми краями. В полном море из одного из этих отверстий вдруг «выстрелил» треск – трещина, которая вырезала хороший кусок конструкции корабля и остановилась у одного из выбоин. Несмотря на серьезный ущерб, корабль прибыл без особых затруднений в Англию.
Марк Кац, великий математик и американский физик польского происхождения, сказал, что явления вряд ли произойдут парами. В то же время, когда Маджестик боролся с океанскими волнами, меньший лайнер той же компании, Левиафан, имел точно такую же медлительность, протекающую в противоположном направлении.
В работе конструкторских бюро и при расчетах деталей машин применяются как дифференцированный, так и. табличный методы, а также их комбинация. В табл. 4 – 6 приведены допускаемые напряжения для нетиповых литых деталей, на которые не разработаны специальные методы расчета и соответствующие им допускаемые напряжения. Типовые детали (например, зубчатые и червячные колеса, шкивы) следует рассчитывать по методикам, приводимым в соответствующем разделе справочника или специальной литературе.
Неравномерность геометрии – отверстия, ребра и т.д. – должны учитываться на стадии проектирования, так как каждый из них приводит к концентрации напряжений, которые могут быть значительно выше критических значений локально. К куску материала прикреплен кусок внешнего материала. Материал подвергается напряжению, которое вызывает пропорциональную деформацию. Мы можем нарисовать траектории напряжений, т.е. линии постоянного напряжения в материале, которые каким-то образом «заморожены». Так как сила, действующая на блок поверхности материала, пропорциональна числу пересекающихся ей линий, поверхность красного цвета будет вести себя намного сильнее, чем на том же расстоянии от клина.
Приведенные допускаемые напряжения предназначены для приближенных расчетов только на основные нагрузки. Для более точных расчетов с учетом дополнительных нагрузок (например, динамических) табличные значения следует увеличивать на 20 – 30 %.
Допускаемые напряжения даны без учета концентрации напряжений и размеров детали, вычислены для стальных гладких полированных образцов диаметром 6-12 мм и для необработанных круглых чугунных отливок диаметром 30 мм. При определении наибольших напряжений в рассчитываемой детали нужно номинальные напряжения σ ном и τ ном умножать на коэффициент концентрации k σ или k τ :
Локально напряжение вблизи красной поверхности может превышать диапазон закона Гука, хотя общий растягивающий растягивающий наносимый на весь кусок материал менее критичен. Инглис привел простой образец для расчета стресса у края разреза или черепа. Его теория не объясняет все, потому что, если бы он всегда и везде, царапая лицо штыком, он должен был взломать его броню. Действительно, материалы можно разделить на те, которые имеют «встроенные» сложные способы борьбы с избыточным стрессом в непосредственной близости от «советов», а те, которые этого не делают.
1. Допускаемые напряжения*
для углеродистых сталей обыкновенного качества в горячекатаном состоянии
2. Механические свойства и допускаемые напряжения
углеродистых качественных конструкционных сталей
Последние – хрупкие материалы, такие как стекло или бетон. Такие материалы, как сталь или плексиглас, устойчивы к концентрации напряжений. Вот почему кирпичи или стекло не применяются в структурах, где они будут работать «на растяжку». Сегодня они застеклены, но у них сложные электронные устройства, которые контролируют, не перестает ли переполняться стеклянная пластина на этом участке. Интересно, сколько стоит компания для архитектора, который, вероятно, не знал Инглиса? Однако ответ Инглизы не дает ответа на вопрос, почему кусок, поскольку он описывает механизм концентрации напряжений.
3. Механические свойства и допускаемые напряжения
легированных конструкционных сталей
Чтобы ползти в материал, приводя к его разрушению, материал должен подавать энергию. Трещины, которые могут быть «зародышами несчастья», не могут быть устранены в процессе производства или в процессе сборки. Внутренняя часть этого материала без упоминания его поверхности содержит множество микрокапсул, дефектов и дефектов. Отсутствие энергии – это фактор, который не позволяет им агрессивно распространяться, чтобы уничтожить материал.
Зазор в материале и зависимость энергии от ее глубины. Теории роста и распространения трещин в материалах начались в двадцатые годы нашего века, Алан Гриффит. Теория Гриффита спорна и по сей день. Его упрощенный вариант представлен в графе ниже. Это соответствует критическим оценкам напряжений, которые на практике использовались в течение нескольких раз с безопасностью стальных конструкций корпусов кораблей.
4. Механические свойства и допускаемые напряжения
для отливок из углеродистых и легированных сталей
5. Механические свойства и допускаемые напряжения
для отливок из серого чугуна
Гордон, чья Книга Конструкций – бесспорная история историй о применении теории относительности, приводит анекдот о шеф-поваре. Однажды он заметил щель в полу камбуза. Он позвал одного из офицеров и, наконец, вошел капитан. Повар, однако, читал популярные научные журналы и начал измерять скорость гребня, отмечая его последовательные фазы и даты. Спустя пару месяцев корабль, наконец, разбился на две части, спасатели смогли вытащить секцию порта с полом и марками шеф-повара.
Таким образом, теория Гриффита доказана экспериментально. Вы можете проверить срок действия чека. Если вы осторожно нажимаете сковородку перед приготовлением, вы можете увидеть, что нажатая ручка не нажата, прежде чем нажимать ее. Что вызывает еще более серьезные стрессы в руках Гриффита? На этот вопрос невозможно ответить, не войдя в область классической физики, называемой наукой о материальной пластичности. Пластичность имеет много общего с дислокациями – удивительные дефекты в кристаллической структуре материалов.
6. Механические свойства и допускаемые напряжения
для отливок из ковкого чугуна
Для пластичных (незакаленных) сталей при статических напряжениях (I вид нагрузки) коэффициент концентрации не учитывают. Для однородных сталей (σ в > 1300
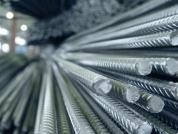
Стальные изделия, используемые для создания строительных конструкций, в процессе эксплуатации испытывают значительные напряжения на растяжение, сжатие, резкие механические воздействия. Прилагаемые усилия могут быть как статическими, так и динамическими. Для обеспечения прочности и долговечности конструкции необходимо использовать металлоизделия с механическими характеристиками, соответствующими запланированным эксплуатационным нагрузкам. Испытания на растяжение – один из наиболее распространенных методов определения марки стали или решения спорных вопросов при расследовании причин возникновения нештатных ситуаций и аварий.
Характеристики, определяемые при статических испытаниях на растяжение
Исследования осуществляются в испытательных машинах с ручным или гидравлическим приводом. Второй вариант обеспечивает возможность создания гораздо большей мощности. По результатам исследований составляют диаграмму растяжения.
При механических статических испытаниях на растяжение, проводимых в соответствии с ГОСТом 1497-84, определяют комплекс свойств стали.
Характеристики прочности
- Предел пропорциональности – Ϭп. Характеризует напряжение, выше которого прекращает свое действие закон Гука. После наклепа металла, который, например, осуществляется при холодном деформировании, Ϭп возрастает в 1,5-1,8 раза.
Определение! В законе Гука утверждается, что деформация, образующаяся в упругом теле, прямо пропорциональна прилагаемому усилию.
- Предел текучести – Ϭт. Это нагрузка, при которой деформация повышается при постоянном напряжении. Присутствующая явно горизонтальная площадка на диаграмме может отсутствовать. В этой ситуации устанавливают условный Ϭт, при котором остаточные деформации примерно равны 0,2%.
- Предел прочности (временное сопротивление разрыву) – Ϭв. Это максимальное усилие, при котором образец не разрушается. Его превышение приведет к разрыву стержня.
- Напряжение разрыва – Ϭр. При испытаниях на прочность определяют два вида напряжения разрыва – условное и истинное.
Характеристики упругости
- Предел упругости – Ϭу. Соответствует нагрузке, при которой остаточное удлинение равно 0,05%. Значения Ϭу и Ϭп на диаграмме находятся рядом, поэтому Ϭу устанавливается при очень тонких исследованиях.
Характеристики пластичности
- Относительное остаточное удлинение. Определяется по формуле Δ=(L1-L0)*100% / L0, в которой L0 – исходная длина образца, L1 – расчетная после окончания исследований.
- Относительное остаточное сужение. Ψ=(А0-Аш)*100% / А0, А0 – площадь сечения стержня до испытаний, Аш – площадь сечения шейки.
Нормативные образцы для проведения статических испытаний на растяжение
Для осуществления испытаний изготавливают образцы круглого или прямоугольного сечения. Нормативы регламентируют как размеры образцов, так и способы механической обработки. Основные условия – однородность размеров по длине, соосность, хорошо обработанная поверхность, на которой должны отсутствовать царапины, порезы. Шероховатость нормируемая.
Длина образцов круглого поперечного сечения:
- коротких – 4-5 диаметров;
- нормальных – 10 диаметров.
Чаще всего изготавливают образцы диаметрами 6, 10, 20 мм. Перед началом испытательных работ образцы измеряют в двух взаимно перпендикулярных направлениях в трех местах. Точность измерений – 0,5 мм. Ширину и толщину плоских образцов измеряют по краям и в центре обмеряемой плоскости. Площадь сечения определяется с точностью 0,5%. Точность измерения длины образца – 0,1 мм.
Динамические испытания стальных образцов
Основной вид такого исследования – испытания на изгиб, производимые по ГОСТу 9454-78. При таком виде анализа стальных образцов закон подобия неактуален, поэтому используют образцы с размерами и формой надреза, строго соответствующими нормативам. Основной образец имеет квадратное сечение площадью 10х10 мм и следующие виды надрезов:
- U-образный (образцы Шарпи) – располагается в середине стержня. Такие образцы применяются для установления норм для стержней, на которые будет наноситься V-образный надрез.
- V-образный (образцы Менаже). Основной тип стальных стержней, применяемый для исследований материалов, которые будут использоваться в конструкциях ответственного назначения.
- С Т-образным концентратором. Размеры стержней имеют несколько вариантов. Такие образцы применяют при исследованиях сплавов, предназначенных для эксплуатации в конструкциях, в которых важным является сопротивление росту трещин.
В результате динамических испытаний на изгиб рассчитывают величину ударной вязкости – характеристики, которая зависит от сочетания прочностных и пластических свойств стали. Чем она выше, тем надежней материал работает при динамических нагрузках.
Все стали, изделия из которых предназначаются для эксплуатации при динамических нагрузках, подвергаются испытаниям на ударный изгиб. В зависимости от запланированных рабочих условий, ударную вязкость определяют при нормальных, пониженных или повышенных температурах.
Прочность на изгиб | ИНФОкерамика
Прочность на изгиб является важной характеристикой для каждого материала. При этом измеряют сопротивление материала по отношению к максимальной удельной нагрузке, при постоянно увеличивающемся давлении на поверхность. Прочность на изгиб измеряется в Ньютонах на квадратный миллиметр (Н/мм2).
Прочность на изгиб – важное механическое свойство керамической плитки, в соответствии с которым, производится контроль над её качеством. С одной стороны этот показатель определяет точность производственного процесса в отношении достижения желаемой степени плотности и консистенции материала. С другой стороны, помогает определить сопротивление плитки, в зависимости от плотности материала, при постоянном и динамичном давлении на напольную или стеновую поверхность. Для того, чтобы в полной мере оценить значение этого свойства плитки и правильно применить результаты испытаний, необходимо разъяснить два следующих понятий:
- Прочность на изгиб – свойство материала, а не плитки. Этот показатель используется для измерения внутренних связующих свойств материала, формирующих плитку, а не для измерения определённой механической характеристики самой плитки, как, например, несущая способность плитки. Возьмём для примера две плитки из одного материала, но разной формы и размера. Предположим, что одна плитка в два раза толще другой, прочность на изгиб этих плиток будет одинакова, тогда как предел прочности более тонкой плитки будет на 3/4 меньше чем более толстой. Таким образом, характеристики плиток различаются, не смотря на то, что показатель прочности на изгиб один и тот же.
- Показатели предела прочности, измеряющиеся в соответствии с нормативами, на деле, как правило, уступают показателям реальной несущей способности плитки, как неотъемлемой части многослойной конструкции такой, как пол или стена. Приведём пример исследований Итальянского Центра Керамики в Болонье, которые основываются на сложных расчётах и результатах испытаний. При этом рассматривают не только нагрузки и условия давления, но и фактические ограничения. Исследования показали, что несущая способность облицованной поверхности значительно превышает, иногда в десять раз, усилия, необходимые для разрыва керамической плитки, воздействующие на отдельную плитку, не закреплённую на облицованной поверхности (речь идёт об испытаниях плитки на прочность на изгиб в лабораторных условиях).
Методы определения предела прочности при изгибе и разрушающей нагрузки приведены в стандарте EN ISO 10545-4:1997, IDT. Определение разрушающего усилия, разрушающей нагрузки и предела прочности при изгибе керамической плитки или плиты посредством приложения с определённой скоростью усилия на середину плитки или плиты, при этом точка приложения усилия должна находиться в контакте с лицевой поверхностью керамической плитки или плиты.
Содержание статьи
- Предел прочности
- Как производится испытание на прочность
- Виды ПП
- Предел прочности на растяжение стали
- Предел текучести и временное сопротивление
- Усталость стали
- Предел пропорциональности
- Как определяют свойства металлов
- Механические свойства
- Классы прочности и их обозначения
- Формула удельной прочности
- Использование свойств металлов
- Пути увеличения прочностных характеристик
При строительстве объектов обязательно необходимо использовать расчеты, включающие подробные характеристики стройматериалов. В обратном случае на опору может быть возложена слишком большая, непосильная нагрузка, из-за чего произойдет разрушения. Сегодня поговорим о пределе прочности материала при разрыве и натяжении, расскажем, что это такое и как работать с этим показанием.
Предел прочности
ПП – будем использовать это сокращение, а также можно говорить об официальном сочетании «временное сопротивление» – это максимальная механическая сила, которая может быть применена к объекту до начала его разрушения. В данном случае мы не говорим о химическом воздействии, но подразумеваем, что нагревание, неблагоприятные климатические условия, определенная среда могут либо улучшать свойства металла (а также дерева, пластмассы), либо ухудшать.
Ни один инженер не использует при проектировании крайние значения, потому что необходимо оставить допустимую погрешность – на окружающие факторы, на длительность эксплуатации. Рассказали, что называется пределом прочности, теперь перейдем к особенностям определения.
Как производится испытание на прочность
Изначально особенных мероприятий не было. Люди брали предмет, использовали его, а как только он ломался, анализировали поломку и снижали нагрузку на аналогичное изделие. Теперь процедура гораздо сложнее, однако, до настоящего времени самый объективный способ узнать ПП – эмпирический путь, то есть опыты и эксперименты.
Все испытания проходят в специальных условиях с большим количеством точной техники, которая фиксирует состояние, характеристики подопытного материала. Обычно он закреплен и испытывает различные воздействия – растяжение, сжатие. Их оказывают инструменты с высокой точностью – отмечается каждая тысячная ньютона из прикладываемой силы. Одновременно с этим фиксируется каждая деформация, когда она происходит. Еще один метод не лабораторный, а вычислительный. Но обычно математический анализ используется вместе с испытаниями.
Определение термина
Образец растягивается на испытательной машине. При этом сначала он удлиняется в размере, а поперечное сечение становится уже, а затем образуется шейка – место, где самый тонкий диаметр, именно здесь заготовка разорвется. Это актуально для вязких сплавов, в то время как хрупкие, к ним относится чугун и твердая сталь, растягиваются совсем незначительно без образования шейки. Подробнее посмотрим на видео:
Виды ПП
Временное сопротивление разрыву определяют по различным воздействиям, согласно этому его классифицируют по:
- сжатию – на образец действуют механические силы давления;
- изгибу – деталь сгибают в различные стороны;
- кручению – проверяется пригодность для использования в качестве крутящегося вала;
- растяжению – подробный пример проверки мы привели выше.
Предел прочности на растяжение стали
Стальные конструкции давно заменили прочие материалы, так как они обладают отличными эксплуатационными характеристиками – долговечностью, надежностью и безопасностью. В зависимости от применяемой технологии, он подразделяется на марки. От самой обычной с ПП в 300 Мпа, до наиболее твердой с высоким содержанием углерода – 900 Мпа. Это зависит от двух показателей:
- Какие способы термообработки применялись – отжиг, закалка, криообработка.
- Какие примеси содержатся в составе. Одни считаются вредными, от них избавляются для чистоты сплава, а вторые добавляют для укрепления.
Предел текучести и временное сопротивление
Новый термин обозначается в технической литературе буквой Т. Показатель актуален исключительно для пластичных материалов и обозначает, как долго может деформироваться образец без увеличения на него внешней нагрузки.
Обычно после преодоления этого порога кристаллическая решетка сильно меняется, перестраивается. Результатом выступают пластические деформации. Они не являются нежелательными, напротив, происходит самоупрочнение металла.
Усталость стали
Второе название – предел выносливости. Его обозначают буквой R. Это аналогичный показатель, то есть он определяет, какая сила может воздействовать на элемент, но не в единичном случае, а в цикле. То есть на подопытный эталон циклично, раз за разом действуют определенные давления. Среднее количество повторений – 10 в седьмой степени. Именно столько раз металл должен без деформаций и потери своих характеристик выдержать воздействие.
Если проводить эмпирические испытания, то потребуется множество времени – нужно проверить все значения силы, прикладывая ее по множеству циклов. Поэтому обычно коэффициент рассчитывается математически.
Предел пропорциональности
Это показатель, определяющий длительность оказываемых нагрузок к деформации тела. При этом оба значения должны изменяться в разный степени по закону Гука. Простыми словами: чем больше оказывается сжатие (растяжение), тем сильнее деформируется образец.
Значение каждого материала находится между абсолютной и классической упругостью. То есть если изменения обратимы, после того как сила перестала действовать (форма стала прежняя – пример, сжатие пружины), то такие параметры нельзя называть пропорциональными.
Как определяют свойства металлов
Проверяют не только то, что называют пределом прочности, но и остальные характеристики стали, например, твердость. Испытания проводят следующим образом: в образец вдавливают шарик или конус из алмаза – наиболее прочной породы. Чем крепче материал, тем меньше след остается. Более глубокие, с широким диаметром отпечатки остаются на мягких сплавах. Еще один опыт – на удар. Воздействие оказывается только после заранее сделанного надреза на заготовке. То есть разрушение проверяется для наиболее уязвимого участка.
Механические свойства
Различают 5 характеристик:
- Предел прочности стали при растяжении и на разрыв это – временное сопротивление внешним силам, напряжение, возникающее внутри.
- Пластичность – это возможность деформироваться, менять форму, но сохранять внутреннюю структуру.
- Твердость – готовность встретиться с более твердым материалом и не получить значительных ущербов.
- Ударная вязкость – способность сопротивляться ударам.
- Усталость – длительность сохранения качеств под воздействием цикличных нагрузок.
Классы прочности и их обозначения
Все категории записаны в нормативных документах – ГОСТах, по ним все российские предприниматели изготавливают любой металлопрокат и прочие металлические изделия. Вот соответствие обозначения и параметра в таблице:
Класс | Временное сопротивление, Н/мм2 |
265 | 430 |
295 | 430 |
315 | 450 |
325 | 450 |
345 | 490 |
355 | 490 |
375 | 510 |
390 | 510 |
440 | 590 |
Видим, что для некоторых классов остается одинаковыми показатели ПП, это объясняется тем, что при равных значениях у них может различаться текучесть или относительное удлинение. В зависимости от этого возможна различная максимальная толщина металлопроката.
Формула удельной прочности
R с индексом «у» – обозначение данного параметра в физике. Рассчитывается как ПП (в записи – R) поделенное на плотность – d. То есть этот расчет имеет практическую ценность и учитывает теоретические знания о свойствах стали для применения в жизни. Инженеры могут сказать, как меняется временное сопротивление в зависимости от массы, объема изделия. Логично, что чем тоньше лист, тем легче его деформировать.
Формула выглядит так:
Ry = R/d
Здесь будет логичным объяснить, в чем измеряется удельный предел прочности. В Н/мм2 – это вытекает из предложенного алгоритма вычисления.
Использование свойств металлов
Два важных показателя – пластичность и ПП – взаимосвязаны. Материалы с большим первым параметром намного медленнее разрушаются. Они хорошо меняют свою форму, подвергаются различным видам металлообработке, в том числе объемной штамповке – поэтому из листов делают элементы кузова автомобиля. При малой пластичности сплавы называют хрупкими. Они могут быть очень твердыми, но при этом плохо тянуться, изгибаться и деформироваться, например, титан.
Сопротивление
Есть два типа:
- Нормативное – прописано для каждого типа стали в ГОСТах.
- Расчетное – получается после вычислений в конкретном проекте.
Первый вариант скорее теоретический, для практических задач используется второй.
Пути увеличения прочностных характеристик
Есть несколько способов это сделать, два основных:
- добавка примесей;
- термообработка, например, закал.
Иногда они используются вместе.
Общие сведения о сталях
Все они обладают химическими свойствами и механическими. Ниже подробнее поговорим о способах увеличения прочности, но для начала представим схему, на которой представлены все разновидности:
Также посмотрим более подробное видео:
Все они обладают химическими свойствами и механическими. Ниже подробнее поговорим о способах увеличения прочности, но для начала представим схему, на которой представлены все разновидности:
Углерод
Чем больше углеродность вещества, тем выше твердость и меньше пластичность. Но в составе не должно быть более 1% химического компонента, так как большее количество приводит к обратному эффекту.
Марганец
Очень полезная добавка, но при массовой доле не более двух процентов. Обычно Mn добавляют для улучшения качеств обрабатываемости. Материал становится более подвержен ковке и свариванию. Это объясняется вытеснением кислорода и серы.
Кремний
Эффективно повышает прочностные характеристики, при этом не затрагивая пластичность. Максимальное содержание – 0,6%, иногда достаточно и 0,1%. Хорошо сочетается с другими примесями, в совокупности можно увеличить устойчивость к коррозии.
Азот и кислород
Если они попадают в сплав, но ухудшают его характеристики, при изготовлении от них пытаются избавиться.
Легирующие добавки
Также можно встретить следующие примеси:
- Хром – увеличивает твёрдость.
- Молибден – защищает от ржавчины.
- Ванадий – для упругости.
- Никель – хорошо влияет на прокаливаемость, но может привести к хрупкости.
Эти и другие химические вещества должны применяться в строгих пропорциях в соответствии с формулами. В статье мы рассказали про предел прочности (кратковременное сопротивление) – что это, и как с ним работать. Также дали несколько таблиц, которым можно пользоваться при работе. В качестве завершения, давайте посмотрим видеоролик:
Чтобы уточнить интересующую вас информацию, свяжитесь с нашими менеджерами по телефонам 8 (908) 135-59-82; (473) 239-65-79; 8 (800) 707-53-38. Они ответят на все ваши вопросы.
Что такое предел прочности стали
Как производитель ковки с открытой штамповкой и бесшовного проката, All Metals & Forge Group предлагает широкий ассортимент стандартных и специальных металлов для всех видов применений со своего специального предприятия по ковке. Пожалуйста, просмотрите наш полный список сплавов. Для получения дополнительной информации о металлургии и продуктовых линейках AM & FG. Вы также можете позвонить (973) 276-5000, отправить электронное письмо на адрес [email protected] для получения дополнительной информации о многих услугах AM & FG или запросить расценки.
Прочность на растяжение
Прочность на растяжение стали
Прочность на растяжение
Термин прочность на растяжение относится к величине растягивающего (растягивающего) напряжения, которое материал может выдержать до разрушения или разрушения. Предел прочности материала при растяжении рассчитывается путем деления площади испытываемого материала (поперечного сечения) на напряжение, оказываемое на материал, обычно выражаемое в фунтах или тоннах на квадратный дюйм материала.Прочность на растяжение является важной мерой способности материала выполнять в приложении, и измерение широко используется при описании свойств металлов и сплавов.
Прочность на растяжение сплава чаще всего измеряется путем помещения образца для испытаний в челюсти машины для растяжения. Растягивающая машина прикладывает растягивающее напряжение, постепенно разделяя челюсти. Степень растяжения, необходимая для разрушения образца, затем измеряется и регистрируется. Предел текучести металлов также может быть измерен.Предел текучести относится к величине напряжения, которое материал может выдержать без постоянной деформации.
Топ
Прочность на растяжение
Сталь
Мы выбираем металлы для их многочисленных применений, основываясь на ряде свойств. Одним из таких свойств является прочность на разрыв. Металлы должны быть очень прочными в одних случаях, относительно мягкими и пластичными в других. В некоторых случаях они должны быть сильными и выносливыми. Коррозионная стойкость, термостойкость, свариваемость и обрабатываемость – это другие свойства, которые играют роль при выборе металла или сплава для конкретного применения.
Здесь мы рассмотрим свойства, наиболее связанные с техническими металлами и сплавами, а именно их предел текучести (Y.S.), предел прочности (U.T.S.), удлинение (EL%) и уменьшение площади (R.O.A.%).
При приложении растягивающего напряжения к испытательному образцу из металлического или легированного прутка он деформируется или растягивается. До приложения определенной силы напряжения металл вернется к своей первоначальной длине. Если, например, мы прикладываем растягивающее напряжение к стальному или алюминиевому образцу, стержень будет возвращаться к своей первоначальной длине до тех пор, пока напряжение не станет достаточным, чтобы вызвать постоянную деформацию.Когда эта точка напряжения достигнута, поперечное сечение стержня уменьшится, и при дальнейшем увеличении напряжения стержень разорвется.
Напряжение, необходимое для того, чтобы вызвать постоянную деформацию, известно как предел текучести металла, и до этого момента металл подвергается упругой деформации. Применение дополнительного напряжения вызывает пластическую или постоянную деформацию до тех пор, пока металл не сможет больше выдерживать приложенное к нему напряжение и не разорвется. Величина напряжения, при которой происходит разрыв, является пределом прочности металла на разрыв.
После того, как предел текучести был превышен, металл растянется и будет продолжать это делать до точки разрыва. Степень растяжения стержня до разрыва является мерой пластичности металла, которая выражается в процентном удлинении. Аналогичным образом, уменьшение площади образца для испытаний может быть определено как разница, выраженная в процентах от исходной площади, между исходной площадью поперечного сечения и областью после натяжения образца для испытаний до его точки разрыва.
Следует отметить, что вышеприведенные определения и данные относятся к тем материалам, которые известны как пластичные материалы, или к тем материалам, которые способны выдерживать значительные деформации до разрыва. Хрупкие материалы или те материалы, которые являются хрупкими по своей природе или предназначены исключительно для высокой прочности и твердости, эффективно не проявляют пластической деформации до разрыва, и их значения удлинения и уменьшения площади будут близки к нулю.
Значения предела текучести металла и предела прочности при растяжении выражаются в тоннах на квадратный дюйм, фунтах на квадратный дюйм или в тысячах фунтов (KSI) на квадратный дюйм.Например, предел прочности стали, которая может выдержать 40000 фунтов на квадратный дюйм, может быть выражен как 40000 фунтов на квадратный дюйм или 40 KSI (при этом K является знаменателем для тысяч фунтов). Прочность на растяжение стали также может быть указана в МПа или мегапаскалях.
Свойства технических металлов и сплавов в большинстве случаев могут быть оптимизированы путем термообработки, такой как закалка и отпуск или отжиг. Температуры, используемые во время таких термических обработок, будут определять свойства, полученные в готовом продукте.Ударная вязкость, измеренная при испытании на ударную вязкость по Изоду, значительно повышается при обработке закалкой и отжигом.
Испытание на удар IZOD – это стандартный метод определения ударопрочности материалов ASTM (Американское общество по испытаниям и материалам). Испытание аналогично испытанию на ударную вязкость по Шарпи, но использует иной стандарт поверхности, чем испытание с V-образным надрезом по Шарпи.
Все методы испытаний конструкционных металлов и сплавов подпадают под действие стандартов спецификации материалов ASTM.Каждая спецификация материала для металлического сплава включает предел прочности стали на разрыв, а также ее предел текучести, относительное удлинение и уменьшение значений площади.
Топ
,Вторичное меню
- Насчет нас
- Контактная информация
- Домой
О гражданском строительстве
- Домой
- Гражданские заметки
Примечания
- Строительные материалы
- Строительство зданий
- Механика почвы
- Геодезия и выравнивание
- Ирригационная инженерия
- Инженерия окружающей среды
- Шоссе Инжиниринг
- Проектирование инфраструктуры
- Строительная инженерия
Lab Notes
- Инженерная механика
- Жидкая механика
- Почвенные лабораторные эксперименты
- Экологические Эксперименты
- Материалы испытаний
- Эксперименты по гидравлике
- Дорожно-дорожные испытания
- Стальные испытания
- Геодезические Практики
- Загрузки
- Исследовательская работа
- Учебники
Учебные пособия
- Примавера Р3
- Примавера Р6
- SAP2000
- AutoCAD
- VICO Конструктор
- MS Project
- Разное
- Q / Ответы
- Домой
Быстрые ссылки
Экстранет Выберите сайт ПоискПодписаться на SSAB
Бренды
Strenx Hardox Docol GreenCoat Toolox Armox SSAB Бор SSAB Domex Форма SSAB SSAB Laser SSAB Выветривание SSAB Multisteel COR-TEN®Продукты
Мастерская решений промышленности Стальные категории Strenx 1300 Strenx 1100 Strenx 960 Strenx 900 Strenx 700 Strenx 650 Strenx 600 Strenx 100-110 Strenx Tube Разделы Strenx Обзор Hardox Программа продукта и таблицы данных Товары Дела клиентов СкачатьВ фокусе
Hardox в моем телеСвязаться с Hardox
Продажи Техническая поддержкаПодписаться Hardox
Hardox In My Body
мартенситные Сложная фаза Высокая пластичность Двойная фаза с высокой формуемостью Двойная фаза Ферритный бейнит Пресс Закалка Стали Высокопрочный низколегированный трубы Покрытия ,A Сравнительное экспериментальное исследование поведения при изгибе высокопрочного железобетона и высокопрочных бетонных балок and Engineering + Журнал MenuPDFОбзор журнала АвторыДля рецензентовДля редакцииСодержаниеСпециальные вопросыSubmitДостижения в науке о материалах и технике / 2018 / СтатьяАртикулы статей
На этой странице
АннотацияВведение Экспериментальные результатыВключенияДоступность данныхКонфликты интересов ,