Преимущества метода роквелла: Методы определения твердости – Компания «Метротест»
alexxlab | 14.07.2023 | 0 | Разное
Методы определения твердости – Компания «Метротест»
Что такое твердость?
Твердость – это способность материалов сопротивляться проникновению в его поверхность индентора, который должен быть тверже исследуемого образца.
Основные методы определения твердости?
Основными исторически сложившимися определениями твердости являются методы: Бринелля (HB, HBW), Роквелла (HRA, HRB, HRC), Супер-Роквелла (HRN и HRT), Виккерса (HV), Микро-Виккерса (HV) и Шора (HА, НD, НОО и др.).
Во всех перечисленных методах при внедрении индентора происходит пластическая деформация исследуемого образца. Чем больше сопротивление материала пластической деформации, тем на меньшую глубину проникает индентор и тем выше твердость.
Какие исследуемые образцы подвергаются к испытанию методом Бринелля?
По методу Бринелля измеряют твердость более мягких материалов с максимальной твердостью до 650 HBW, например: стали, чугун (кроме белого), медь, мягкие сплавы, черные и цветные металлы, прессованная древесина и фанера при больших нагрузках.
Какие исследуемые образцы подвергаются к испытанию методом Роквелла?
По методу Роквелла измеряют твердость очень твердых и относительно мягких металлов, например: графит и пластмассы, металлы и сплавы после термической обработки при больших нагрузках.
Какие исследуемые образцы подвергаются к испытанию методом Супер-Роквелла?
Метод Супер-Роквелла в отличие от метода Роквелла подходит также для определения твердости алюминиевых сплавов, тонких металлических плит, подшипниковых сталей, толстых защитных покрытий при небольших нагрузках.
Какие исследуемые образцы подвергаются к испытанию методом Виккерса и Микро-Виккерса?
По методу Виккерса позволяют испытывать с высокой твердостью (благодаря использованию алмазного индентора) образцов из твердых сплавов, черных и цветных металлов, тонколистовых сталей, закаленных и не закаленных сталей, литья, полудрагоценных и драгоценных камней, цинкованных, хромированных и луженых покрытий поверхностей при больших нагрузках.
Метод Микро-Виккерса подходит для определения твердости малых образцов или металлической фольги, сталей, керамики, тонких пленок, покрытий, твердых сплавов, тонких закаленных слоев при малых нагрузках.
Какие исследуемые образцы подвергаются к испытанию методом Шора?
По методу Шору измеряют твердость резины и пластмасс, строительных утеплителей, ПВХ, продуктов из натурального каучука, твердых смол, полиэстера, печатных пластин, неопрена, и полиграфических валов.
Как измеряют твердость по методу Бринелля?
Метод измерения твердости по Бринелля описан в ГОСТ 9012-59 и основан на плавном внедрении твердосплавного стального шарика (определенного диаметра) в образец. После окончания испытания с помощью микроскопа измеряют диаметр отпечатка.
Применяют стальные или твердосплавные шарики с диаметрами 2,5 мм; 5 мм; 10 мм (также для определения твердости пластиков и твердых полимерных материалов применяются сферические шарики диаметрами 7,5 и 12 мм).
Как измеряют твердость по методам Роквелла и Супер-Роквелла?
Метод определения твердости по Роквеллу и Супер-Роквеллу в полном соответствии с ГОСТ 9013-59 проводится путем статического внедрения стального шарового индентора диаметром 1,5875 мм или алмазного индентора с углом при вершине 120 градусов с определенным усилием на поверхность исследуемого образца, и измерением глубины отпечатка во время испытания.
Преимущество метода Роквелла.
Преимуществом по Роквеллу является простота метода измерения твердости не требующего замера диаметра отпечатка и поиска твердости по таблице.
Как измеряют твердость по методам Виккерса и Микро-Виккерса?
Метод измерения твердости по Виккерсу и Микро-Виккерсу основан на плавном внедрении правильной четырехгранной алмазной пирамиды (с противоположным углом 136 градусов) в поверхность испытуемого изделия с определенным усилием (P), с последующим измерением диагонали отпечатка и расчета твердости образца по таблицам (ГОСТ 2999-75).
Преимущество метода Виккерса.
Преимущество по методу Виккерсу заключается в том, что возможно измерять твердость очень малых или тонких образцов.
Как измеряют твердость методом Шора?
Метод измерения твердости по Шору заключается во внедрении стального закаленного индентора (с определенной формой) с определенным усилием в поверхность исследуемого образца в соответствии с ГОСТ 263-75, 24622-91, 24621-91, ASTM D2240, ISO 868-85.
Преимущество метода Шора.
Преимуществом твердомеров по методу Шору является простота в использовании для определения твердости, небольшая масса и габариты.
Твердость по Роквеллу – Словарь терминов | ПластЭксперт
Твердость по Роквеллу
Понятие и общие сведения
В процессе исторического развития материаловедения, появления механизмов и машин у человечества появилась потребность измерять твердость различных материалов и сравнивать их между собой по определенным стандартам. Твердостью в современной технике называют свойство материала, являющееся противоположным пластичности, то есть его способности вытекать из-под нагрузки.
Так, более 100 лет назад в 1908 году австрийским ученым по фамилии Людвиг были описаны теоретические основы метода получения значения твердости материалов при воздействии на них алмазного конуса. А в 1919 году американскими исследователями Хью М. Роквелли Стэнли П. Роквелл были исправлены некоторые практические недочеты метода и запатентована гидромеханическая установка. Именно она и известна по сей день под названием «твердомер Роквелла».Этот твердомер оказался незаменим для неразрушающего контроля твердости высоколегированных и особенно закаленных сталей, применяющихся, например при производстве подшипников.
Измерение твердости по Роквеллу оказалось шагом вперед по сравнению с уже существовавшим на тот момент методом Бриннеля. Этот способ базировался на измерении площади следа на материале, оставленного стальным или карбид-вольфрамовым шариком определенного диаметра. Метод Бринелля, тем не менее,также дожил до сего дня. Обычно он используется для получения значения твердости более мягких материалов, чем метод Роквеллов, например цветных металлов, последний же хорош для закаленной стали. Использование метода Бриннеля характеризуется деформацией рабочего инструмента (шарика), также деформируется и измеряемая поверхность. Из этого следует, что метод Бринелля не соответствует полностью требованиям к неразрушающим способам измерения.
Рис.1. Механизм измерения твердости
Методика измерения и оборудование
Метод определения твердости по Роквеллу подходит для неразрушающего контроля не пластичных материалов, например легированных сталей. В индустрии пластмасс этот метод широко используется для определения твердости рабочих узлов оборудования для переработки полимеров и эластомеров, а также поверхностей технологической оснастки, например прессформ, экструзионного и прочего формующего инструмента.
Метод Роквелла универсален, т.к. обладает тремя шкалами твердости, стандартизированные для определения твердости под тремя нагрузками: в 60, 100 и 150 кгс. Каждой нагрузке соответствует своя измерительная головка или индентор. Рабочим органом каждой головки является конус с углом в 120° и радиусом на вершине в 0,2 мм, выполненный из алмаза. Также применяются калиброванные шарики нескольких стандартных диаметров.
Суть метода заключается в измерении глубины внедрения конуса индентора в образец измеряемого материала. Глубина ввода показывает насколько тот или иной материал способен к сопротивлению внешнему усилию без деформации, то есть образования своего рода валика из выдавленного материала вокруг конуса измерительной головки.
Единицей твердости по Роквеллу при данном методе является числовая величина, не имеющая размера и выражающаяся в числах от 0 до 100. За одну единицу принято движение головки на 0,002 мм.
Всего твердость металла по Роквеллу измеряется по 11 шкалам, обозначаемых латинскими буквами A, B, C, D, E, F, G, H, K, N, T). Они используются для определения твердости в разных парах индентор-нагрузка.
Наиболее часто употребляются шкалы, описанные ниже:
1.
2. Шкала B (HRb) — шарик диаметром 1,588 мм и усилие на инденторе равное 100 кгс, диапазон измерений от 20 до 100 единиц, предназначен для сплавов меди, ковкого чугуна, низкоуглеродистой стали.
3. Шкала C (HRc) — конус и усилие на инденторе равное 150 кгс, диапазон измерений от 20 до 70 единиц, предназначен для высокоуглеродистых сталей после термообработки (закаленных).
При измерении первоначально на конус или шарик прикладывается предварительная нагрузка, позволяющая избавиться от зазоров прибора и оксидной пленки на образце. Эта нагрузка равна 10 кгс для всех трех шкал.
Стационарный твердомер Роквелла выглядит как конструкция в виде рамки, напоминающей букву «П» и состоящая из двух блоков – измерительного и блока установочного перемещения. Они также могут включать в состав двигатель перемещения, цифровую систему измерения, монитор и прочие элементы современного прибора.
Рис.2. Современный прибор для измерения твердости
Процесс определения твердости проводят при температуре от 18 до 23 градусов С и относительной влажности от 70 до 80 процентов. К исследуемому образцу предъявляются следующие требования: устойчивость на приборе, шероховатость поверхности Ra=2,5 или выше. Образец должен проходить термообработку вместе с деталями партии, к которой он относится.
Преимущества и недостатки
Неоспоримым преимуществом метода, предложенного Роквеллами, является универсальность и применимость к большому количеству и широкому диапазону материалов, прежде всего практически ко всем металлам.
Также можно отметить прочие его достоинства:
– существует возможность применения метода определения твердости по Роквеллу к готовым изделиям ввиду отношения его к неразрушающим;
– можно применять метод для контроля различных по степени кривизны поверхностей, в том числе цилиндрические детали или детали с кривизной R3;
– возможность измерения твердости листов с толщиной от 0,3 мм по Роквеллу;
– определение твердости проводится быстро, максимальное время измерения составляет 1-2 минуты с тестом контрольного образца;
– результат получается в удобном для считывания и обработке виде.
Недостатками метода «твердость по Роквеллу» считают не такую высокую точность измерений и возможный существенный их разброс по образцу, как можно получить по методам Бриннеля или Виккерса. Тем не менее, этот минус не такой значительный, учитывая описанные выше его достоинства.
Каковы преимущества и недостатки метода Роквелла?
Введение
Твердость является не физическим свойством, а характеристикой материала. Тем не менее, важно проверять твердость объектов при производстве, чтобы повысить производительность производственных продуктов.
Если вы хотите измерить твердость стальных объектов в процессе проявки, но не знаете, как выполнить какой-либо тест, тогда лучшим вариантом будет твердость по Роквеллу.
Испытание на твердость по Роквеллу — это простое испытание на твердость. Прочтите статью, чтобы узнать о самом простом тесте на твердость.
I. Почему важен тест на твердость по Роквеллу?
Испытание на твердость по Роквеллу применяется во всем мире для применения экспериментального испытания на твердость при вдавливании. Испытание по Роквеллу — это быстрый процесс, очень экономичный и неразрушающий тест (вызывающий лишь незначительные вмятины на материале образца). Испытание на твердость по Роквеллу — простой процесс, поэтому его может выполнить любой человек без специальной подготовки или навыков. Результаты испытаний могут помочь в выборе материала, контроле качества и проведении приемочных испытаний промышленной продукции. Испытание на твердость предоставляет информацию о характеристиках объекта, таких как предел прочности при растяжении, пластичность и износостойкость.
II. Каковы преимущества / преимущества метода Роквелла?
Испытание на твердость по Роквеллу имеет следующие преимущества:
- В начале испытания нет необходимости в предварительной подготовке образца, например, шлифовке поверхности и т. д.
- Может использоваться для неразрушающего контроля.
- Исполнитель может считывать результаты невооруженным глазом, нет необходимости в каком-либо оптическом оборудовании, таком как микроскоп.
- Объект тестирования также можно использовать для других функций.
- Испытание на твердость по Роквеллу — это быстрый процесс, занимающий меньше времени, а также требующий меньших затрат для проведения испытания по сравнению с другими испытаниями на твердость, например, испытанием по Бринеллю, Кнупу или Виккеру, для проведения которых требуется дорогостоящее оборудование.
III. Каковы ограничения/недостатки метода Роквелла?
Измерение твердости по Роквеллу также имеет некоторые недостатки:
- Получение точного результата в этом методе измерения твердости затруднено, потому что, если у вас есть незначительная ошибка измерения глубины, весь ваш расчет может пойти не так.
- Трудно найти различия между материалами при увеличении твердости.
- Зона, где проводится тест, должна быть чистой и не должна содержать никаких загрязнений, например, инородных тел, любых частиц, масла или окалины, чтобы результат теста был точным и точным.
- Влияние индентора на результат теста непредсказуемо, например, индентор установлен, но его острие недостаточно острое.
IV. Тест с алмазными конусами
При проведении теста на твердость с алмазными конусами эталонная глубина составляет 0,2 мм. Испытание на твердость с помощью алмазного конуса применяется, когда объект образца очень твердый, например, из твердой или закаленной стали.
В процессе определения твердости по Роквеллу с алмазным конусом, вариант С или объект находится под испытательной нагрузкой 1373 Н = 140 кп. Здесь преднатяг всего 98 Н = 10 кп. Но количество острых тестов может быть изменено в соответствии с заявкой.
Если вы тестируете тонкие листы, то возникает риск вздутия объекта на противоположной стороне теста. Это происходит из-за большой силы, приложенной в процессе испытаний, и приводит к неточным измерениям. Для преодоления этого риска используется вариант А с меньшим испытательным усилием, равным 490 Н. При необходимости можно использовать и другой вариант D с испытательным усилием 883 Н = 90 кп.
V. Испытание с твердосплавными шариками
Испытание на твердость по Роквеллу применяется с твердосплавными шариками для испытания более мягких материалов, таких как конструкционная сталь или латунь, потому что при испытании мягкого материала алмазными конусами это может привести к очень глубокому проникновению в материал, который выйти далеко за пределы указанной глубины 0,2 мм. При использовании твердосплавного шарика указанная эталонная глубина увеличивается до 0,26 мм. Распределение степеней твердости на разных стадиях остается одинаковым и составляет 0,002 мм.
Измерение твердости твердосплавными шариками имеет результаты, лежащие в пределах теоретического диапазона от 0 (на этапе полной глубины вдавливания) до 130 (на этапе отсутствия глубины вдавливания).
Основное отличие испытаний с твердосплавными шариками от алмазных конусов заключается в варианте B и варианте F. Твердосплавные шарики имеют диаметр 1,5875 мм или 1/16 дюйма в испытании на твердость. Преднатяг установлен на 98 Н = 10 кп. Испытательная нагрузка в варианте В 883 Н, в варианте F 490 Н.
Вывод
В этой статье мы кратко объяснили процесс определения твердости по Роквеллу и его применение, значение, преимущества и недостатки. Понимание методов испытаний на твердость позволяет производителям разрабатывать четкие и точные спецификации и устранять задержки, вызванные предоставлением слишком малой информации. Имейте в виду, что перед проведением любого теста на твердость проверьте инденторы на наличие повреждений, которые могут повлиять на результаты. Чтобы узнать больше о тестах на твердость по Роквеллу или различных тестах на твердость, посетите наш веб-сайт и получите бесплатную консультацию.
Преимущества и недостатки разрушающих методов определения твердости по Роквеллу
Оставить сообщение
Методы разрушающего испытания на твердость по Роквеллу:
В тесте на твердость по Роквеллу мерой твердости является не поверхность вмятины, а ее глубина. Индентором служит либо твердосплавный шарик, либо закругленный алмазный конус с углом при вершине 120° и радиусом при вершине 0,2 мм. Глубину вдавливания можно считывать непосредственно с циферблатного индикатора через траекторию движения испытательной машины.
Рисунок вверху: Алмазный конус для определения твердости по Роквеллу
В тесте на твердость по Роквеллу индентор вдавливается в испытуемый материал. Глубина вдавливания служит мерой твердости!Процесс измерения теста Роквелла выполняется в три этапа. Сначала индентор помещается на испытуемую поверхность с так называемой предварительной нагрузкой F0, равной 98 Н. Таким образом можно компенсировать влияние возможных процессов схватывания в образце и любого зазора в измерительном приборе. После кратковременного приложения предварительного испытательного усилия циферблатный индикатор устанавливается на ноль (опорный уровень). Затем можно определить фактическое значение твердости.
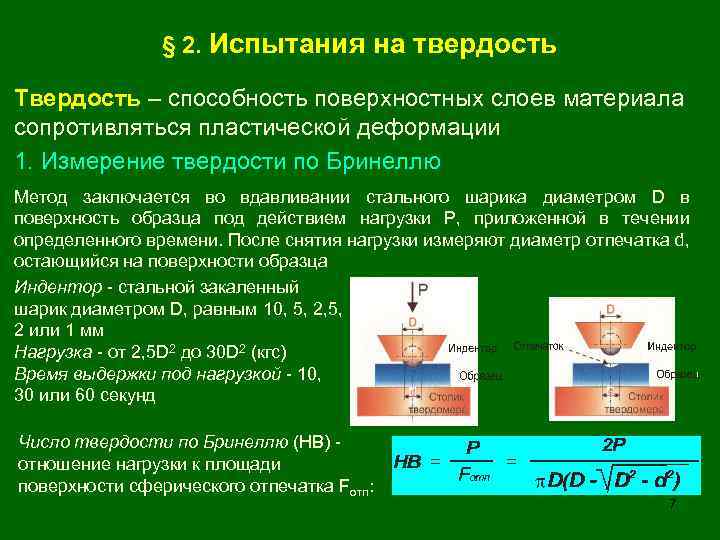
Рисунок выше: Процедура определения твердости по Роквеллу
Фактическая испытательная нагрузка F1 прикладывается в дополнение к предварительной нагрузке, и индетор проникает в материал с общей силой F=F0+F1. Устанавливаемая испытательная нагрузка берется из таблиц в зависимости от индентора и испытуемого материала.
В зависимости от индентора (алмазный конус или твердосплавный шарик) безразмерное значение твердости HR можно определить по следующим формулам:
HRC, HRA=100−h/0,002 Твердость по Роквеллу для алмазного конуса
HRB,HRF=130− h/0,002 Твердость по Роквеллу для твердосплавного шарика
Испытание алмазными конусами
Для алмазных конусов значение твердости получено из эталонной глубины 0,2 мм. В зависимости от того, насколько проникший индентор достигает этой эталонной глубины, материалу присваивается соответствующая твердость. Полное проникновение индентора на заданную глубину, очевидно, означает очень мягкий материал; этому присваивается значение твердости 0. Однако, если алмазный конус вообще не проникает в материал, это означает, что материал чрезвычайно твердый, которому присваивается полное значение твердости 100. Шкала имеет четное деление 0,002 мм (2 мкм), так что достижение половины эталонной глубины также соответствует половине максимального значения твердости (значение твердости по Роквеллу 50). Таким образом, при использовании алмазных конусов шкала Роквелла делится на 100 степеней твердости.
Метод испытаний с алмазным конусом особенно подходит для очень твердых материалов, таких как закаленные или отпущенные стали. Не считая спецпроцедур, предварительная нагрузка составляет 98 Н (10 кп). Фактическая тестовая нагрузка может варьироваться в зависимости от приложения.
В варианте процесса C образец подвергается испытательной нагрузке 1373 Н (140 кПа). Однако, особенно при тестировании тонких листов, существует риск того, что материал будет выпячиваться только на противоположной стороне из-за высокого испытательного усилия, что исказит результат измерения. По этой причине для испытания алмазного конуса был введен вариант А, который работает с уменьшенным испытательным усилием 490 Н (50 кп). Кроме того, существует менее распространенный вариант D, в котором значение твердости определяется с помощью испытательной нагрузки 883 Н (90 кп). Для его определения также используется уравнение (HRC, HRA).
Обратите внимание, что на практике твердость по Роквеллу не определяется по приведенному выше уравнению, а считывается непосредственно по калиброванной шкале.
Рисунок вверху: Индикатор часового типа для определения значения твердости по Роквеллу
Испытание твердосплавными шариками
Однако при испытании относительно мягких материалов алмазный конус проникал бы в материал слишком глубоко и находился бы за пределами эталонной глубины 0,2 мм. Поэтому мягкие поверхности проверяются твердосплавными шариками, а эталонная глубина увеличивается до 0,26 мм. Однако сохраняется деление степеней твердости с шагом 0,002 мм. Это приводит к значениям твердости в теоретическом диапазоне от 0 (полная глубина вдавливания до 0,26 мм) до 130 (глубина вдавливания отсутствует) при использовании твердосплавных шариков.
При использовании твердосплавного шарика для определения твердости основное различие проводится между вариантами процесса B и F. В отличие от испытания с алмазным конусом, они подходят для более мягких металлов, таких как конструкционная сталь или латунь. Шарик имеет диаметр 1,5875 мм (=1/16 дюйма). Во всех вариантах процесса предварительная нагрузка составляет 98 Н (10 кПа). Процедуры снова отличаются только фактической тестовой нагрузкой. В варианте B испытательная нагрузка составляет 883 Н (90 кПа), а в варианте F испытательная нагрузка составляет 490 Н (50 кПа). Из-за меньшей испытательной нагрузки вариант процесса F особенно подходит для очень мягких материалов, таких как медь или тонкие листы.
Сопоставимость значений твердости
Значения твердости, полученные при разных вариантах процесса, нельзя сравнивать друг с другом. Кроме того, значение твердости, полученное при определенном методе обработки, должно находиться в определенном диапазоне. Для значений вне этого диапазона метод следует изменить, поскольку индентор либо слишком сильно, либо слишком слабо проник в материал.
HRC: от 20 до 70
HRA: от 20 до 88
HRB: от 20 до 100
HRF: от 60 до 100
Преимущества и недостатки
Преимуществом определения твердости по Роквеллу является относительно короткое время испытаний и хорошая автоматизация, поскольку измеренные значения определяются непосредственно по глубине отпечатка без оптического измерения под микроскопом. Поэтому этот процесс особенно подходит для автоматизированного производства.
Недостатком процесса Роквелла является относительно небольшой диапазон глубины.