Прочность по роквеллу: таблица, шкала, обозначение и единицы измерения
alexxlab | 02.03.2023 | 0 | Разное
Прочность на разрыв по твердости по Бринеллю Калькулятор
✖В твердости по Бринеллю используется твердый сферический индентор, который вдавливается в поверхность испытуемого металла.ⓘ Твердость по Бринеллю [HB] | Атмосфера ТехническийАттопаскальБармикробарСантиметр ртутного столба (0 °C)Сантиметр водяного столба (4 °C)сантипаскальдекапаскальдесятипаскальДина на квадратный сантиметрэкса паскаль Фемто паскаль Морская вода для ног (15 °C)Вода для ног (4 °C)Вода для ног (60 ° F)ГигапаскальГрамм-сила на квадратный сантиметргектопаскальДюйм ртутного столба (32 ° F)Дюйм ртутного столба (60 ° F)Дюйм водяного столба (4 °C)Дюйм воды (60 ° F)кгс / кв. смКилограмм-сила на квадратный метрКилограмм-сила / кв. миллиметрКилоньютон на квадратный метркилопаскальКило фунт на квадратный дюймКип-сила / квадратный дюймМегапаскальИзмеритель морской водыМетр воды (4 °C)МикробармикропаскальМиллибарМиллиметр ртутного столба (0 °C)Миллиметр воды (4 ° C)миллипаскальнанопаскальНьютон / кв. | +10% -10% |
✖Прочность на растяжение — это максимальное напряжение на инженерной кривой напряжения-деформации.ⓘ Прочность на разрыв по твердости по Бринеллю [TS] |
Атмосфера ТехническийАттопаскальБармикробарСантиметр ртутного столба (0 °C)Сантиметр водяного столба (4 °C)сантипаскальдекапаскальдесятипаскальДина на квадратный сантиметрэкса паскаль Фемто паскаль Морская вода для ног (15 °C)Вода для ног (4 °C)Вода для ног (60 ° F)ГигапаскальГрамм-сила на квадратный сантиметргектопаскальДюйм ртутного столба (32 ° F)Дюйм ртутного столба (60 ° F)Дюйм водяного столба (4 °C)Дюйм воды (60 ° F)кгс / кв. |
⎘ копия |
👎
Формула
сбросить
👍
Прочность на разрыв по твердости по Бринеллю Решение
ШАГ 0: Сводка предварительного расчета
ШАГ 1. Преобразование входов в базовый блок
Твердость по Бринеллю: 200 Килограмм-сила / кв. миллиметр –> 1961329999.99986 паскаль (Проверьте преобразование здесь)
ШАГ 2: Оцените формулу
ШАГ 3: Преобразуйте результат в единицу вывода
689996481.996953 паскаль –>689.996481996953 Мегапаскаль (Проверьте преобразование здесь)
< 4 твердость Калькуляторы
Прочность на разрыв по твердости по Бринеллю формула
Предел прочности = (3.45/9.8067)*Твердость по Бринеллю
TS = (3.45/9.8067)*HB
Корреляция между пределом прочности на разрыв и твердостью по Бринеллю
И предел прочности, и твердость являются показателями сопротивления металла пластической деформации. Следовательно, они примерно пропорциональны. Как показывает практика, для большинства сталей твердость по Бринеллю и предел прочности на разрыв связаны в соответствии с указанным выше соотношением.
Share
Copied!
Производство высокопрочного крепежа в г. Орле
Твердость болтов
Показатели твердости | Класс прочности | |||||||||||
3,6 | 4,6 | 4,8 | 5,6 | 5,8 | 6,8 | 8.8 а | 9.8b | 10,9 | 12,9 | |||
d £ 16с, мм | d > 16с, мм | |||||||||||
Твердость по Виккерсу, HV, F ≥ 98 H | не менее | 95 | 120 | 130 | 155 | 160 | 190 | 250 | 255 | 290 | 320 | 385 |
не более | 220 d | 250 | 320 | 335 | 360 | 380 | 435 | |||||
Твердость по Бринеллю, НВ, F = 30 D2 | не менее | 90 | 114 | 124 | 147 | 152 | 181 | 238 | 242 | 276 | 304 | 366 |
не более | 209 d | 238 | 304 | 318 | 342 | 361 | 414 | |||||
Твердость по Роквеллу, HRC | не менее | – | – | 22 | 23 | 28 | 32 | 39 | ||||
не более | – | – | 32 | 34 | 37 | 39 | 44 |
а Для болтов класса прочности 8. 8 диаметром d £ 16 мм существует повышенный риск повреждения гайки в случае чрезмерной затяжки, приводящей к тому, что создаваемая нагрузка превосходит пробную нагрузку для гайки, установленную в ГОСТ Р 52628.
b Распространяется только на изделия с номинальным диаметром резьбы d £ 16 мм.
с Для строительных болтовых соединений предельное значение равно 12 мм.
d Значения твердости, измеренные на конце болтов, винтов и шпилек, должны быть не более 250 HV, 238 НВ или 99,5 HRB.
Твердость гаек
Показатели твердости | Класс прочности | |||||||||
5 | 6 | 8 | 9 | 10 | 12 | |||||
d £ 16, мм | d > 16, мм | d £ 16, мм | d > 16, мм | d £ 16, мм | ||||||
Твердость по Виккерсу, HV | не менее | 130 | 146 | 150 | 170 | 200 | 233 | 188 | 272 | 295 |
не более | 302 | 302 | 302 | 302 | 302 | 353 | 302 | 353 | 353 | |
Твердость по Бринеллю, НВ | не менее | 130 | 146 | 143 | 162 | 193 | 219 | 180 | 258 | 280 |
не более | 286 | 286 | 286 | 286 | 286 | 336 | 286 | 336 | 336 | |
Твердость по Роквеллу, HRC | не менее |
|
|
|
| 11 | 19 | 18 | 26 | 29,2 |
не более | 30 | 30 | 30 | 30 | 30 | 36 | 30 | 36 | 36 |
Шкала твердости Роквелла для испытания на твердость (PDF) – Что такое трубопровод
Твердость материала можно определить как сопротивление этого материала вдавливанию и царапанию. Это характеристика материалов и очень важное свойство материала. Для различных применений требуются твердые материалы, и твердость этого материала количественно определяет это свойство. Чем больше значение твердости, тем тверже материал, и тем сложнее будет создать вмятину при заданной нагрузке. Существуют различные одобренные промышленностью методы определения твердости, такие как твердость по Бринеллю, твердость по Роквеллу, твердость по Виккерсу и т. д. Однако определение твердости по Роквеллу является одним из широко используемых, эффективных и признанных в отрасли методов определения твердости, представленных с использованием твердости по Роквеллу. Весы.
Для выбора материала, контроля процесса и качества, а также приемочных испытаний коммерческих продуктов полезно использовать испытание на твердость по Роквеллу. В этой статье мы узнаем процедуру определения твердости по Роквеллу, соответствующие формулы, стандарты, шкалу твердости по Роквеллу и ее преимущества.
Что такое испытание на твердость по Роквеллу?
Определение твердости по Роквеллу с использованием шкалы твердости по Роквеллу является одним из широко используемых и точных методов определения твердости, распространенных в промышленности. Это испытание легче выполнить по сравнению с испытанием на твердость по Бринеллю или Виккерсу. По имени изобретателей, г-на Хью М. Роквелла и г-на Стэнли П. Роквелла, этот тест на твердость известен как тест на твердость по Роквеллу.
Испытание на твердость по Роквеллу широко используется для тонкой стали, свинца, латуни, цинка, алюминия, цементированных карбидов, железа, титана, медных сплавов и некоторых пластмасс. Этот тест считается одним из простых и быстрых методов определения твердости.
Испытание на твердость по Роквеллу выполняется путем сравнения измерения глубины проникновения индентора при большой нагрузке, известной как основная нагрузка, и при меньшей предварительной нагрузке, известной как второстепенная нагрузка.
Типы испытаний на твердость по Роквеллу
В зависимости от приложения малых и больших нагрузок во время испытания испытания на твердость по Роквеллу подразделяются на две группы. Это:
- Стандартный тест на твердость по Роквеллу , где малая нагрузка составляет 10 кгс, а основная нагрузка составляет 60, 100 или 150 кгс.
- Поверхностная твердость по Роквеллу Испытание , в котором приложенная малая нагрузка составляет 3 кгс, а основные нагрузки составляют 15, 30 или 45 кгс.
Процедура испытания на твердость по Роквеллу
Процедура испытания на твердость по Роквеллу состоит из приложения небольшой нагрузки, за которой следует большая нагрузка. Незначительная нагрузка применяется для установки нулевого положения, из которого будет производиться измерение. Затем прикладывается основная нагрузка, а затем снимается, сохраняя при этом второстепенную нагрузку. Глубина проникновения (d) от нулевой точки отсчета измеряется циферблатом.
Предварительно определенная малая и большая нагрузка прикладывается к испытуемому образцу с помощью алмазного или шарикового индентора. Незначительная нагрузка (от 3 кгс до 10 кгс) снижает эффект отделки поверхности. После этого прикладывается дополнительная или основная нагрузка (от 15 кгс до 150 кгс) на заданное время выдержки. Теперь снимается основная нагрузка и измеряется окончательная глубина вдавливания от положения предварительной нагрузки до положения комбинированной нагрузки, которая преобразуется в число твердости по Роквеллу. Затем предварительную нагрузку снимают и индентор извлекают из образца. См. рис. 1 ниже, на котором поясняется процедура определения твердости по Роквеллу.
Advertisements
Рис. 1: Процедура испытания на твердость по РоквеллуПроцедура испытания на твердость по Роквеллу состоит из следующих шагов:
- Установка образца для испытания на плоскую твердую поверхность.
- Применение незначительной нагрузки для создания небольшого отпечатка (положение нулевой точки).
- Настройка измерительного прибора и измерение начальной глубины вдавливания при незначительной нагрузке.
- Применение основной нагрузки и удержание в течение времени выдержки.
- Снятие основной нагрузки, сохранение второстепенной нагрузки.
- Измерение глубины проникновения из нулевого положения.
- Определение числа твердости по Роквеллу по глубине проникновения.
Формула определения твердости по Роквеллу
Определение твердости по Роквеллу считывается непосредственно с оборудования. Однако существует формула для преобразования измеренной глубины (d) в число твердости по Роквеллу. Число твердости по Роквеллу для материала представляет собой безразмерное число, указывающее значение твердости по определенной шкале Роквелла.
Уравнение для числа твердости по Роквеллу имеет вид
HR=N-(d/s)
Где,
- N и s — масштабные коэффициенты, зависящие от используемого теста. Значение N равно 100 или 130 в зависимости от используемой шкалы твердости Роквелла. Точно так же значение s равно 0,001 мм или 0,002 мм.
- d — глубина проникновения, измеренная от нулевой точки (в мм).
Шкала твердости Роквелла
Шкала твердости Роквелла — это тип шкалы, который показывает твердость материала, измеренную с помощью теста твердости Роквелла. Это безразмерное число. Шкала твердости Роквелла обозначается буквой HR, за которой следует буква, обозначающая любую из возможных шкал. Например, «HRC 96 дюймов для металла означает, что твердость этого металла составляет 96 при измерении по шкале твердости Роквелла C.
Производимая продукция изготавливается из различных материалов. Чтобы приспособить испытания на твердость в этом разнообразном диапазоне, в испытаниях на твердость по Роквеллу используются несколько различных типов инденторов, а также ряд стандартных уровней силы. Каждая комбинация типа индентора и уровней приложенной силы была определена с использованием отдельной шкалы твердости по Роквеллу. Согласно ASTM E 18 существует тридцать (30) различных шкал Роквелла, разделенных на две категории: обычные шкалы Роквелла и поверхностные шкалы Роквелла.
Существует несколько различных шкал Роквелла, обозначаемых различными буквами, требующих различных нагрузок или инденторов во время измерения твердости. Таблица твердости по шкале Роквелла для обычных и поверхностных шкал Роквелла представлена в таблицах 1 и 2 ниже:
Символ шкалы Роквелла | Тип индентора/диаметр в случае шарика | Основная нагрузка | Типовое применение | |
HRA | Сфероконический алмаз | 98,07 Н (10 кгс) | 588,4 Н (60 кгс), утонченный карбид, сталь | 9 900|
HRB | Ball, 1,588 мм (¹⁄₁₆ дюймов) | 98,07 N (10 кг) | 980,7 N (100 кг) | Медные все |
HRC | Сфероконический алмаз | 98,07 Н (10 кгс) | 1471 Н (150 кгс) | Сталь, твердый чугун, перлитный ковкий чугун, титан, сталь с глубокой поверхностной закалкой и другие материалы твердостью более 100 по шкале Роквелла B.![]() |
HRD | Сфероконический алмаз | 98,07 Н (10 кгс) | 980,7 Н (100 кгс) | Тонкая сталь и закаленная сталь среднего размера, перлитное ковкое железо. |
HRE | Шар, 3,175 мм (⅛ дюйма) | 98,07 Н (10 кгс) | 980,7 Н (100 кгс) | Чугун, сплавы алюминия и магния, подшипниковые металлы. |
HRF | Шарик, 1,588 мм (¹⁄₁₆ дюйма) | 98,07 Н (10 кгс) | 588,4 Н (60 кгс) | Мягкие металлы и тонкие медные сплавы. |
HRG | BALL, 1,588 мм (¹⁄₁₆ дюймов) | 98,07 N (10 кг) | 1471 N (150 кг) | Mallable Irons, Mopper-Nickel-Alloy-andcincicron. |
HRH | Шар, 3,175 мм (⅛ дюйма) | 98,07 Н (10 кгс) | 588,4 Н (60 кгс) | Алюминий, цинк и свинец. |
HRK | Шарик, 3,175 мм (⅛″) | 98,07 Н (10 кгс) | 1471 Н (150 кгс) | Подшипники из очень мягких или тонких металлов и других материалов.![]() |
HRL | Шарик, 6,350 мм (¼ дюйма) | 98,07 Н (10 кгс) | 588,4 Н (60 кгс) | Подшипники из металлов и других очень мягких или тонких материалов. |
HRM | Шар, 6,350 мм (¼ дюйма) | 98,07 Н (10 кгс) | 980,7 Н (100 кгс) | Подшипники из металлов и других очень мягких или тонких материалов. |
HRP | Шарик, 6,350 мм (¼ дюйма) | 98,07 Н (10 кгс) | 1471 Н (150 кгс) | Подшипники из металлов и других очень мягких или тонких материалов. |
HRR | Шар, 12,70 мм (½ дюйма) | 98,07 Н (10 кгс) | 588,4 Н (60 кгс) | Подшипниковые металлы и другие очень мягкие или тонкие материалы. |
HRS | Шарик, 12,70 мм (½ дюйма) | 98,07 Н (10 кгс) | 980,7 Н (100 кгс) | Подшипниковые металлы и другие очень мягкие или тонкие материалы. |
HRV | Шарик, 12,70 мм (½ дюйма) | 98,07 Н (10 кгс) | 1471 Н (150 кгс) | Подшипники из металлов и других очень мягких или тонких материалов.![]() |
Символ шкалы Rockwell | Тип Индентера/Диаметр в случае мяча | Незначительная нагрузка, N (KGF) | Незначительная нагрузка, N (KGF) | Minor Lop, N (KGF) | . , N (KGF) | Типичное использование | ||
15N | Сфероконический бриллиант | 29.42 (3) | 147,1 (15) | с аналогичным калибровочный материал. | ||||
30N | Сфероконический алмаз | 29,42(3) | 294,2 (30) | Аналогичен шкалам A, C, D в таблице 1, но для более тонкого калибровочного материала. | ||||
45N | Сфероконический алмаз | 29,42(3) | 441,3 (45) | Аналогичен шкалам A, C, D в таблице 1, но для более тонкого материала.![]() | ||||
15T | Шар; 1,588 мм (1/16 дюйма) | 29,42(3) | 147,1 (15) | Аналогичен шкалам B, F, G в таблице 1, но для более тонкого калибровочного материала. | ||||
30T | Шар; 1,588 мм (1/16 дюйма) | 29,42(3) | 294,2 (30) | Аналогичен шкалам B, F, G в таблице 1, но для более тонкого калибровочного материала. | ||||
45T | Шар; 1,588 мм (1/16 дюйма) | 29,42(3) | 441,3 (45) | Аналогичен шкалам B, F, G в таблице 1, но для более тонкого калибровочного материала. | ||||
15 Вт | Шар; 3,175 мм (1/8 дюйма) | 29,42(3) | 147,1 (15) | Очень мягкий материал | ||||
30 Вт | Шар; 3,175 мм (1/8 дюйма) | 29,42(3) | 30 (294,2) | Очень мягкий материал | ||||
45 Вт | Шар; 3,175 мм (1/8 дюйма) | 29,42(3) | 45 (441,3) | Очень мягкий материал | ||||
15X | Шарик; 6,35 мм (1/4 дюйма) | 29,42(3) | 147,1 (15) | Очень мягкий материал | ||||
30X | Шарик; 6,35 мм (1/4 дюйма) | 29,42(3) | 30 (294,2) | Очень мягкий материал | ||||
45X | Шарик; 6,35 мм (1/4 дюйма) | 29,42(3) | 45 (441,3) | Очень мягкий материал | ||||
15Y | Шарик; 12,70 мм (1/2 дюйма) | 29,42(3) | 147,1 (15) | Очень мягкий материал | ||||
30 лет | Шар; 12,70 мм (1/2 дюйма) | 29,42(3) | 30 (294,2) | Очень мягкий материал | ||||
45Y | Шарик; 12,70 мм (1/2 дюйма) | 29,42 (3) | 441,3 (45) | Очень мягкий материал |
.
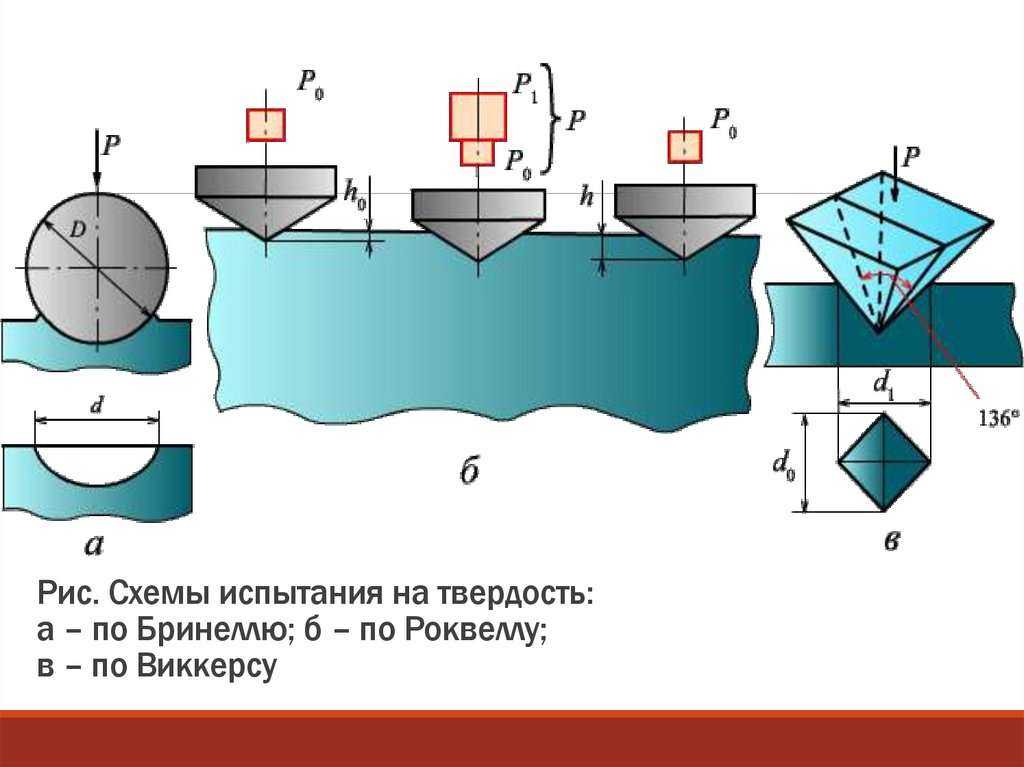
- тип материала для испытания на твердость
- толщина материала для испытания
- площадь или ширина материала для испытания
- ограничения каждой шкалы твердости Роквелла
- однородность материала для испытания.
Стандарты определения твердости по Роквеллу
Широко используемые стандарты, регламентирующие методологию измерения твердости по Роквеллу:
- ASTM E18 для металлов
- ISO 6508 для металлов,
- ASTM D785 для пластмасс
- ISO 2039 для пластмасс
Прибор для определения твердости по Роквеллу
Для определения значений твердости материалов доступен широкий ассортимент приборов для определения твердости по Роквеллу. Он может варьироваться от ручного и полуавтоматического до полностью автоматического продвинутого. См. рис. 2 ниже, на котором представлены основные компоненты типичной машины для определения твердости по Роквеллу.
Факторы, влияющие на точность и надежность определения твердости по Роквеллу
Существуют различные параметры, влияющие на точность, прецизионность и надежность метода определения твердости по Роквеллу. Это:
- Испытательная машина Rockwell: Результаты испытаний могут отличаться в зависимости от оборудования, оператора и условий окружающей среды. Таким образом, необходимо убедиться, что состояние машины и установка образца оператором правильные.
- Наличие грязи или жира в зоне контакта.
- Поверхность образца: Состояние поверхности должно быть хорошего качества, чтобы получить более точные и воспроизводимые результаты испытаний.
- Навыки оператора: оператор должен обладать высокой квалификацией в надлежащих методах ремонта и тестирования.
В противном случае результаты испытаний могут существенно различаться.
Типичные значения твердости по Роквеллу
В следующей таблице (Таблица 3) приведены некоторые типичные значения твердости по Роквеллу
Материал | Значения твердости по Роквеллу |
Very Hard Steel | HRC 55 to HRC 66 |
Axes | HRC 45 to HRC 55 |
Brass | HRB 55 to HRB 93 |
Hard Impact Steel Blades | HRC от 52 до HRC 55 |
Преимущества определения твердости по Роквеллу
Определение твердости по Роквеллу дает значительные преимущества по сравнению с другими жесткими методами испытаний, как указано ниже:
- Тест твердости по Роквеллу напрямую отображает значения твердости.
Таким образом, для определения значения твердости расчетов не требуется.
- Это быстрый, надежный и надежный метод с небольшой площадью отступа.
Тест на твердость по Роквеллу и тест на твердость по Бринеллю
Детали теста на твердость по Бринеллю и основные различия между тестом на твердость по Роквеллу и тестом на твердость по Бринеллю опубликованы в отдельной статье. Пожалуйста, нажмите здесь, чтобы перейти к этой статье .
Присоединяйтесь к нам в TelegramОпределение твердости по Роквеллу
Твердость — это характеристика материала, а не фундаментальное физическое свойство. Он определяется как сопротивление вдавливанию и определяется путем измерения постоянной глубины вдавливания. Проще говоря, при использовании фиксированной силы (нагрузки) и данного индентора, чем меньше отпечаток, тем тверже материал.
Значение твердости при вдавливании получают путем измерения глубины или площади вдавливания с использованием различных методов испытаний.
Метод определения твердости по Роквеллу , как определено в ASTM E-18, является наиболее часто используемым методом определения твердости.
Тест Роквелла, как правило, проще в выполнении и более точен, чем другие методы определения твердости. Метод испытаний Роквелла используется для всех металлов, за исключением случаев, когда структура испытуемого металла или состояние поверхности вносят слишком много изменений; где отступы будут слишком большими для приложения; или когда размер или форма образца запрещают его использование.
Метод Роквелла измеряет постоянную глубину отпечатка, вызванного действием силы/нагрузки на индентор. Во-первых, к образцу прикладывается предварительное испытательное усилие (обычно называемое предварительной нагрузкой или небольшой нагрузкой) с помощью алмазного или шарикового индентора. Эта предварительная нагрузка разрушает поверхность, чтобы уменьшить влияние отделки поверхности. После выдержки предварительного испытательного усилия в течение заданного времени измеряют базовую глубину вдавливания.
После предварительной нагрузки добавляется дополнительная нагрузка, называемая основной нагрузкой, для достижения общей требуемой испытательной нагрузки. Эта сила удерживается в течение заданного времени (времени выдержки), чтобы обеспечить упругое восстановление. Эта большая сила затем высвобождается, возвращая усилие к предварительной нагрузке. После выдержки предварительного испытательного усилия в течение заданного времени измеряется окончательный отпечаток. Значение твердости по Роквеллу получается из разницы между базовым и конечным измерениями вдавливания. Это расстояние преобразуется в число твердости. Предварительное испытательное усилие снимают, а индентор извлекают из образца.
Предварительные испытательные нагрузки (преднагрузки) варьируются от 3 кгс (используется в «Поверхностной» шкале Роквелла) до 10 кгс (используется в «Обычной» шкале Роквелла). Суммарные испытательные усилия колеблются от 15-150 кгс (поверхностные и обычные) до 500-3000 кгс (макротвердость).
Иллюстрация метода испытаний
A = Глубина, достигнутая индентором после приложения предварительной нагрузки (небольшая нагрузка).
B = Положение индентора при полной нагрузке, малая плюс большая нагрузка.
C = Конечное положение, достигнутое индентором после упругого восстановления материала образца.
D = Измеренное расстояние, представляющее разницу между предварительной нагрузкой и положением большой нагрузки. Это расстояние используется для расчета числа твердости по Роквеллу.
Можно использовать различные инденторы: конические алмазные с круглым наконечником для более твердых металлов и шариковые инденторы диаметром от 1/16 дюйма до 1/2 дюйма для более мягких материалов.
При выборе измерительной шкалы Роквелла общим правилом является выбор шкалы, допускающей наибольшую нагрузку и индентор без превышения определенных рабочих условий и с учетом условий, которые могут повлиять на результат испытания. Эти условия включают образцы, толщина которых меньше минимальной глубины вдавливания; отпечаток образца, который падает слишком близко к краю образца или другой оттиск; или испытание на цилиндрических образцах.
Кроме того, испытательный вал должен находиться в пределах 2 градусов отвеса, чтобы обеспечить точную нагрузку; не должно быть отклонений образца или тестера во время приложения нагрузки из-за таких условий, как грязь под образцом или на подъемном винте. Важно поддерживать чистоту поверхности и удалять обезуглероживание от термической обработки.
Листовой металл может быть слишком тонким и мягким для проведения испытаний по заданной шкале Роквелла без превышения минимальной толщины и возможного повреждения испытательного окна. В этом случае можно использовать алмазную наковальню, чтобы последовательно воздействовать на результат.
Другим особым случаем при испытании холоднокатаной листовой стали является то, что закалка может создать градиент твердости в образце, поэтому каждое испытание измеряет среднее значение твердости по глубине вмятины. В этом случае любой результат теста Роквелла будет подвергнут сомнению, потому что часто существует история испытаний с определенной шкалой на конкретном материале, к которому операторы привыкли и могут функционально интерпретировать.
Ссылка..www.hardnesstesters.com
Стандартная шкала твердости Роквелла
Символ шкалы Роквелла | Тип диаметра индентора в случае шарика | Незначительная нагрузка | Основная нагрузка | Типичное применение |
HRA | Алмаз сферической формы | 98,07 Н (10 кгс) | 588,4 Н (60 кгс) | Твердые сплавы, тонкая сталь и мелкозернистая цементируемая сталь |
ХРБ | Шар, 1,588 мм (1/16 дюйма) | 98,07 Н (10 кгс) | 980,7 Н (100 кгс) | Медные сплавы, мягкие стали, алюминиевые сплавы, ковкий чугун и т.![]() |
HRC | Алмаз сферической формы | 98,07 Н (10 кгс) | 1471 Н (150 кгс) | Сталь, твердый чугун, перлитный ковкий чугун, титан, сталь с глубокой поверхностной закалкой и другие материалы твердостью более 100 по шкале Роквелла B. |
ХРД | Алмаз сферической формы | 98,07 Н (10 кгс) | 980,7 Н (100 кгс) | Тонкая сталь и сталь средней цементации, а также перлитный ковкий чугун |
ОПЧ | Шар, 3,175 мм (1/8 дюйма) | 98,07 Н (10 кгс) | 980,7 Н (100 кгс) | Чугун, алюминиевые и магниевые сплавы и подшипниковые металлы |
хорватских рупий | Шар, 1,588 мм (1/16 дюйма) | 98,07 Н (10 кгс) | 588,4 Н (60 кгс) | Отожженные медные сплавы и тонкий мягкий листовой металл |
ХРГ | Шар, 1,588 мм (1/16 дюйма) | 98,07 Н (10 кгс) | 1471 Н (150 кгс) | Ковкие чугуны, медно-никелево-цинковые и мельхиоровые сплавы |
HRH | Шар, 3,175 мм (1/8 дюйма) | 98,07 Н (10 кгс) | 588,4 Н (60 кгс) | Алюминий, цинк и свинец |
кун | Шар, 3,175 мм (1/8 дюйма) | 98,07 Н (10 кгс) | 1471 Н (150 кгс) | Подшипниковые металлы и другие очень мягкие или тонкие материалы |
Кулоны | Шар, 6,350 мм (1/4 дюйма) | 98,07 Н (10 кгс) | 588,4 Н (60 кгс) | Подшипниковые металлы и другие очень мягкие или тонкие материалы |
HR | Шар, 6,350 мм (1/4 дюйма) | 98,07 Н (10 кгс) | 980,7 Н (100 кгс) | Подшипниковые металлы и другие очень мягкие или тонкие материалы |
ХРП | Шар, 6,350 мм (1/4 дюйма) | 98,07 Н (10 кгс) | 1471 Н (150 кгс) | Подшипниковые металлы и другие очень мягкие или тонкие материалы |
Рубль | Шар, 12,70 мм (1/2 дюйма) | 98,07 Н (10 кгс) | 588,4 Н (60 кгс) | Подшипниковые металлы и другие очень мягкие или тонкие материалы |
ХРС | Шар, 12,70 мм (1/2 дюйма) | 98,07 Н (10 кгс) | 980,7 Н (100 кгс) | Подшипниковые металлы и другие очень мягкие или тонкие материалы |
ВРС | Шар, 12,70 мм (1/2 дюйма) | 98,07 Н (10 кгс) | 1471 Н (150 кгс) | Подшипниковые металлы и другие очень мягкие или тонкие материалы |
Основной принцип и практическая процедура определения твердости по Роквеллу
Типичные значения твердости по Роквеллу
Символ шкалы Роквелла | Тип диаметра индентора в случае шарика | Малая нагрузка, Н (кгс) | Основная нагрузка, Н (кгс) | Типичное применение |
15Н | Алмаз сферической формы | 29.![]() | 147,1 (15) | Аналогичен шкалам A, C, D в таблице 1, но для более тонкого калибруемого материала |
30Н | Алмаз сферической формы | 29.42(3) | 294,2 (30) | Аналогичен шкалам A, C, D в таблице 1, но для более тонкого калибруемого материала |
45Н | Алмаз сферической формы | 29.42(3) | 441,3 (45) | Аналогичен шкалам A, C, D в таблице 1, но для более тонкого калибруемого материала |
15Т | Мяч; 1,588 мм (1/16 дюйма) | 29.42(3) | 147,1 (15) | Аналогичен шкалам B, F, G в таблице 1, но для более тонкого калибровочного материала |
30Т | Мяч; 1,588 мм (1/16 дюйма) | 29.42(3) | 294,2 (30) | Аналогичен шкалам B, F, G в таблице 1, но для более тонкого калибровочного материала |
45Т | Мяч; 1,588 мм (1/16 дюйма) | 29.![]() | 441,3 (45) | Аналогичен шкалам B, F, G в таблице 1, но для более тонкого калибровочного материала |
15 Вт | Мяч; 3,175 мм (1/8 дюйма) | 29.42(3) | 147,1 (15) | Очень мягкий материал |
30 Вт | Мяч; 3,175 мм (1/8 дюйма) | 29.42(3) | 294,2 (30) | Очень мягкий материал |
45 Вт | Мяч; 3,175 мм (1/8 дюйма) | 29.42(3) | 441,3 (45) | Очень мягкий материал |
15Х | Мяч; 6,35 мм (1/4 дюйма) | 29.42(3) | 147,1 (15) | Очень мягкий материал |
30X | Мяч; 6,35 мм (1/4 дюйма) | 29.42(3) | 294,2 (30) | Очень мягкий материал |
45Х | Мяч; 6,35 мм (1/4 дюйма) | 29.42(3) | 441,3 (45) | Очень мягкий материал |
15 лет | Мяч; 12,70 мм (1/2 дюйма) | 29.![]() |