Прокатка металла на вальцах: Гибка металла на вальцах. Геометрический расчет в Excel.
alexxlab | 10.02.2023 | 0 | Разное
Гибка металла на вальцах. Геометрический расчет в Excel.
Опубликовано 07 Дек 2013
Рубрика: Механика | 103 комментария
За последнее время ко мне было несколько обращений от читателей блога за помощью в решении одной и той же задачи: как при работе на трехвалковых листогибочных вальцах и профилегибах определить окончательное местоположение среднего ролика (валка)…
…относительно положения крайних роликов (валков), которое обеспечит гибку (вальцовку) заготовки с определенным заданным необходимым радиусом? Ответ на этот вопрос позволит повысить производительность труда при гибке металла за счет уменьшения количества прогонов заготовки до момента получения годной детали.
В этой статье вы найдете теоретическое решение поставленной задачи. Сразу оговорюсь – на практике я этот расчет не применял и, соответственно, не проверял результативность предлагаемого метода. Однако я уверен, что в определенных случаях гибка металла может быть выполнена гораздо быстрее при использовании этой методики, чем обычно.
Чаще всего в обычной практике окончательное местоположение подвижного центрального ролика (валка) и количество проходов до получения годной детали определяется «методом тыка». После длительной (или не очень) отработки технологического процесса на пробной детали определяют координату положения центрального ролика (валка), которую и используют при дальнейших перенастройках вальцев, изготавливая партию этих деталей.
Метод удобен, прост и хорош при значительном количестве одинаковых деталей – то есть при серийном производстве. При единичном или «очень мелкосерийном» производстве, когда необходимо гнуть разные профили или листы разной толщины разными радиусами, потери времени на настройку «методом тыка» становятся катастрофически огромными. Особенно эти потери заметны при гибке длинных (8…11м) заготовок! Пока сделаешь проход…, пока проведешь замеры…, пока перестроишь положение ролика (валка)… — и все сначала! И так десяток раз.
Расчет в Excel местоположения подвижного среднего ролика.
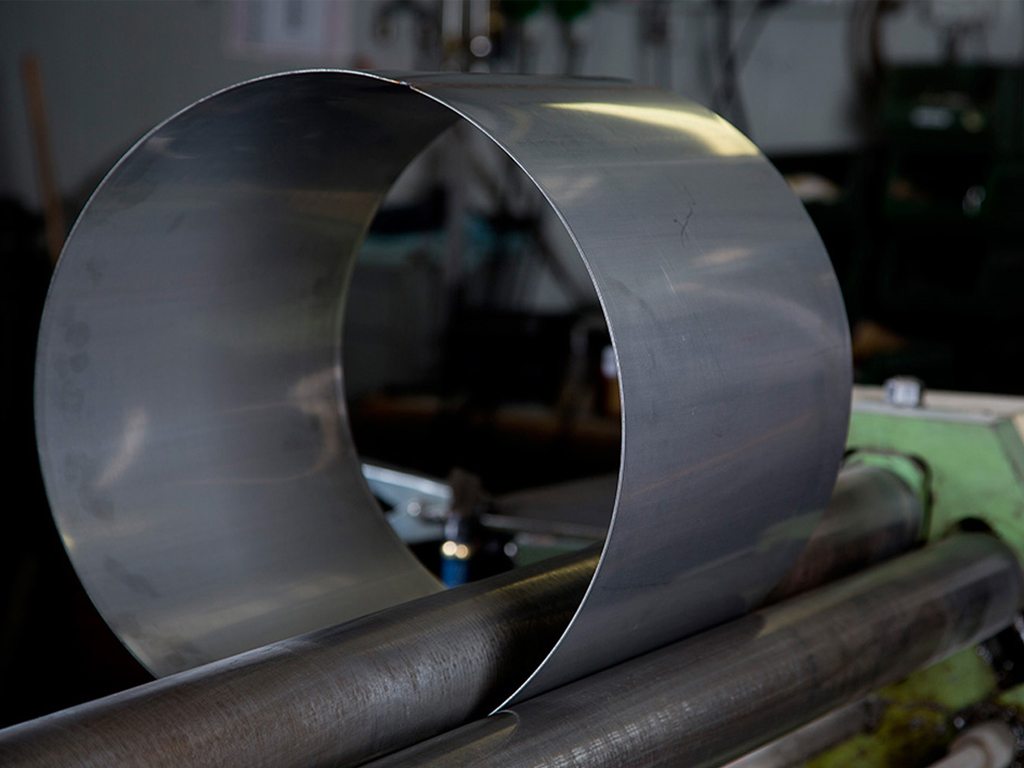
Запускаем программу MS Excel или программу OOo Calc, и начинаем работу!
С общими правилами форматирования электронных таблиц, которые применяются в статьях блога, можно ознакомиться здесь.
Прежде всего, хочу заметить, что листогибочные вальцы и профилегибы разных моделей могут иметь подвижные крайние ролики (валки), а могут — подвижный средний ролик (валок). Однако для нашей задачи это не имеет принципиального значения.
На рисунке, расположенном ниже изображена расчетная схема к задаче.
Вальцуемая деталь в начале процесса лежит на двух крайних роликах (валках), имеющих диаметр D. Средний ролик (валок) диаметром d подводится до касания с верхом заготовки. Далее средний ролик (валок) опускается вниз на расстояние равное расчетному размеру H, включается привод вращения роликов, заготовка прокатывается, производится гибка металла, и на выходе получается деталь с заданным радиусом изгиба R! Осталось дело за малым – правильно, быстро и точно научиться рассчитывать размер H. (½)
9. Но деталь с внутренним радиусом изгиба R0 получилась при опущенном верхнем валке на размер Hрасч, а не H0расч!!! Считаем поправку на обратное пружинение x в мм
в ячейке D12: =D9-D11 =3,5
x = Hрасч — H0расч
10. Так как радиусы R и R0 имеют близкие размеры, то можно с достаточной степенью точности принять эту же величину поправки x для определения окончательного фактического расстояния H, на которое необходимо подать вниз верхний ролик (валок) для получения на вальцованной детали внутреннего радиуса R.
Вычисляем окончательную расчетную вертикальную подачу верхнего ролика (валка) H в мм c учетом пружинения
в ячейке D13: =D9+D12 =48,9
H= Hрасч+x
Задача решена! Первая деталь из партии изготовлена за 2 прохода! Найдено местоположение среднего ролика (валка).
Особенности и проблемы гибки металла на вальцах.
Да, как было бы всё красиво и просто – надавил, прогнал – деталь готова, но есть несколько «но»…
1. При вальцовке деталей с малыми радиусами в целом ряде случаев нельзя получить необходимый радиус R за один проход по причине возможности возникновения деформаций, гофр и надрывов в верхних (сжимаемых) и нижних (растягиваемых) слоях сечения заготовки. В таких случаях назначение технологом нескольких проходов обусловлено технологической особенностью конкретной детали. И это не исключительные случаи, а весьма распространенные!
2. Одномоментная без прокаток подача среднего ролика (валка) на большое расстояние H может быть недопустимой из-за возникновения значительных усилий, перегружающих сверх допустимой нормы механизм вертикального перемещения вальцев. Это может вызвать поломку станка. В аналогичной ситуации перегрузки при этом оказаться может и привод вращения роликов (валков)!
3. Концы заготовки, если их предварительно не подогнуть, например, на прессе, останутся прямолинейными участками при гибке на трехвалковых вальцах! Длина прямолинейных участков L чуть больше половины расстояния между нижними роликами А/2.
4. При движении среднего ролика (валка) вниз в сечении заготовки, подверженном изгибу, постепенно нарастают нормальные напряжения, которые вызывают вначале пружинную деформацию. Как только напряжения в крайних верхних и нижних волокнах сечения достигнут предела текучести материала детали σт, начнется пластическая деформация – то есть начнется процесс гибки. Если средний ролик (валок) отвести обратно вверх до начала возникновения пластической деформации, то заготовка отпружинит следом и сохранит свое первоначальное прямолинейное состояние! Именно эффект обратного пружинения вынуждает увеличить размер вертикальной подачи Hрасч на величину x, так как участки заготовки отпружинивают и частично распрямляются, выходя из зоны гибки, расположенной между роликами (валками).
Мы нашли эту поправку x опытным путем. Обратное пружинение или остаточную кривизну детали можно рассчитать, но это непростая задача. Кроме величины предела текучести материала σт значимую роль при решении этого вопроса играет момент сопротивления изгибу поперечного сечения вальцуемого элемента Wx. А так как часто профили особенно из алюминиевых сплавов имеют весьма замысловатое поперечное сечение, то расчет момента сопротивления Wx выливается в отдельную непростую задачу. К тому же и фактическое значение предела текучести σт часто значительно колеблется даже у образцов, вырезанных для испытаний из одного и того же листа или одного и того же куска профиля.
В предложенной методике сделана попытка уйти от определения обратного пружинения «методом научного тыка». Для пластичных материалов, например алюминиевых сплавов, значение x будет очень небольшим. Для сталей – в зависимости от марки, конечно, немного больше.
Вопросы, касающиеся гибки металла, рассматриваются так же в целом ряде весьма популярных у читателей этого блога статей: «Расчет усилия листогиба», «Расчет длины развертки», «Изготовление гнутого швеллера», «Всё о гнутом швеллере», «Всё о гнутом уголке».
Поделитесь результатами практических испытаний методики со мной и коллегами в комментариях к статье!
Ссылка на скачивание файла: raschet-mestopolozheniia-rolika (xls 32,0KB).
Другие статьи автора блога
На главную
Статьи с близкой тематикой
Отзывы
Прокатка и вальцовка
Вынутый из изложниц слиток имеет определенную форму, которая в дальнейшем изменяется обработкой давлением для получения проволоки, листа и т. д. Предварительно слиток необходимо протравить и тщательно удалить с его поверхности остатки буры и частицы шлака, затем его подвергают ковке (молотком на наковальне), чтобы улучшить пластичность металла. Золотые и серебряные сплавы проковывают в холодном состоянии, платиновые — в горячем. Только после того, как металл хорошо прокован и подготовлен, его можно прокатывать. Перед прокаткой надо очень внимательно осмотреть валки, поскольку каждая крупинка грязи или пыли оставит отпечаток на готовом изделии, что потребует дополнительной обработки.
Прокатывают слиток для уменьшения его толщины и увеличения длины. При листовой прокатке происходит еще уширение полосы, при профильной — уменьшается профиль. Между вращающимися валками слиток обжимается по высоте и вследствие трения между валками и поверхностью слитка продвигается вперед. Однако металл деформируется только на том участке, который подвергается обжатию. Этот участок называется зоной деформации. Разность толщин до и после прокатки называется абсолютным обжатием. Дуга, по которой валок соприкасается с металлом, называется дугой захвата, а угол, соответствующий этой дуге, — углом захвата и чем он больше, тем сильнее степень обжатия. Практикой доказано, что при прокатке сплавов драгоценных и цветных металлов, угол захвата не должен превышать 15-20°, а степень обжатия для серебра проб 875-й и 916-й — 70%, золота пробы 375-й — 50-55%, золота пробы 583-й — 55-60%, белого золота проб 583-й и 750-й (с никелем) — 40%. Необходимо добавить, что давление валков по всему поперечному сечению распределяется неравномерно, и зоны, находящиеся пв краям, деформируются сильнее, чем середина полосы.
При работе на ручных вальцах рекомендуется не давать большое обжатие, тогда лучше обеспечивается плавность прокатки в одном направлении. Кроме того, из-за чрезмерно большого обжатия процесс прокатки часто прерывается, полосу приходится выводить обратно и при этом на ней образуется уступ, ликвидация которого потребует много сил и времени. Заготовку малых размеров размещают на столе целиком, но поскольку подавать ее рукой очень опасно, для подачи ее к валкам пользуются деревянным упором. Конец заготовки вдвигают между валками и опускают верхний валок до получения обжатия необходимой величины.
Продолжая подталкивать одной рукой заготовку в зазор между валками, другой рукой вращают рукоятку привода до тех пор, пока валки не захватят металл, после чего заготовка удерживается и движется с помощью валков. Как правило, необходимый размер заготовки достигается за несколько проходов вперед и назад. Направление прокатки (по отношению к оси заготовки) можно менять только после промежуточного отжига.
Процессы прокатки листового металла и проволоки очень схожи, хотя имеют и некоторые различия. Если листы прокатывают между гладкими валками, то прокатку проволоки производят в ручьевых валках, с ручьями, соответствующими по сечению форме профиля прокатываемой проволоки. При этом заготовка испытывает не только вертикальное давление, но и боковое. Если прокатываемый лист хоть немного расширяется в стороны, то при прокатке проволоки такая деформация недопустима. Прокатывая проволоку, нельзя допускать большого усилия обжатия, а после каждого хода проката проволоку поворачивают на 90° (кантуют) и немного уменьшают расстояние между валками.
Прокатку фасонной калиброванной (сегментной*; прямоугольной, рисунчатой) проводят за один проход, предварительно прокатав заготовку до нужного сечения. Вальцовка почти не отличается от прокатки, разница только в том, что прокатывается не вся заготовка, а заранее отмеченный участок. Выполняют эту операцию только на вальцах с ручным приводом. Провальцованный участок проверяют после каждого обжатия. В процессе вальцовки необходимо производить промежуточный отжиг заготовки. Делается это каждый раз после уменьшения толщины металла вдвое.
Цитаты и изречения о металлах
Есть люди, что одним щелчком по весам обращают недовешенное железо в полновесное золото.
Бальтасар Грасиан (1601–1658) — испанский прозаик-моралист
“) //–>
Валки для листового металла: определение, типы и применение
Что такое рулоны для листового металла?
Станок для прокатки металлических листов представляет собой тип оборудования, в котором используется рабочий ролик для гибки листового металла. Он может образовывать цилиндрические детали, конические детали и другие детали различной формы.
Это очень важное оборудование для производства листового металла.
Типы валков металлических листов
Прокатный станок является одним из важных видов производственного оборудования, используемого в бытовой технике, сосудах под давлением, ветроэнергетике, кораблестроении, аэрокосмической, военной промышленности, ремонте автомобилей и так далее.
Листопрокатный станок способен сгибать металлический лист в большую дугу или цилиндр, или даже в форму эллипса, квадрата и многосекционную дугу.
Ниже приводится краткий анализ типов и областей применения листовых валков.
Двухвалковый листогибочный станок Верхний ролик двухвалкового листогибочного станка представляет собой жесткий металлический ролик, а нижний ролик представляет собой эластичный ролик, покрытый высокопрочным полиуретановым материалом. Его можно регулировать по вертикали.
При вращении ролика верхний ролик и пластина подачи прижимаются под давлением, а эластичный слой нижнего ролика прижимается к нижнему ролику, вызывая упругую деформацию.
Но из-за того, что объем эластомера является постоянным, давление передается со всех сторон и обеспечивает высокую прочность, равномерное распределение, постоянное действие обратного давления, которое заставляет пластину и жесткий ролик постоянно оставаться рядом, цель состоит в том, чтобы сделать он свернулся в цилиндр с вращением.
Глубина верхнего валика, представляющая собой деформацию упругого слоя, является основным технологическим параметром, определяющим радиус изгиба.
Согласно экспериментальному исследованию, чем больше обжатие, тем меньше радиус изгиба листового металла, но когда величина вдавливания достигает определенного значения, радиус изгиба имеет тенденцию оставаться стабильным, что почти не имеет ничего общего с обжатием при прокатке, это важная особенность технологии гибки листов с двумя валками.
Вальцы двухвалковые листогибочные в основном предназначены для листового металла шириной 2000 мм, толщиной менее 2 мм для круглой прокатки, в основном применяются для серийного производства тонкой тары бытовой техники. Как правило, он может быть оснащен автоматической системой подачи и автоматической системой разгрузки, с высокой степенью автоматизации и высокой производительностью.
Преимущества:
⑴ Не нужно сгибать конец, высокая скорость обработки;
⑵ Можно выполнять высокоточное формование одним движением;
⑶ Даже при штамповке, резке, прокатке металлическая пластина не дает трещин и неравномерной деформации.
⑷ Не создавать складок, не оставлять царапин на поверхности деталей;
⑸ Если увеличить обжатие, изменится даже расстояние между двумя роликами, но диаметр деталей не изменится, поэтому требования к точности не высоки, а использование устройства простое.
Недостатки:
- В связи с тем, что при каждом изменении диаметра изготавливаемой детали необходимо изготавливать направляющее роликовое колесо, он не подходит для многосортного и мелкосерийного производства.
- Не может быть обработан толстой пластиной, максимальная толщина пластины составляет 6 ~ 9 мм.
Существует много видов трехвалковых листогибочных станков, которые можно разделить на механические и гидравлические.
Если отличить от конструкции, ее можно разделить на наклонную трехвалковую листопрокатную машину, горизонтальную под роликовым движением и геометрическую переменную.
Асимметричный 3-валковый листогибочный станок
Как правило, асимметричный 3-валковый листогибочный станок приводится в действие механическим двигателем.
Верхний и нижний ролики являются фиксированными приводными роликами, однако верхний ролик фиксируется, а нижний ролик может подниматься и вращаться. Нижний ролик в основном работает вместе с верхним роликом, чтобы прижать передний конец металлической пластины. Между тем, боковой ролик, который служит вспомогательным роликом, поднимается вверх, чтобы деформировать изгиб листа. Прокатка верхнего ролика и нижнего ролика реализует круглую прокатку и дуговую прокатку металлического листа.
Асимметричный 3-валковый листогибочный станок применяется для прокатки низкоуглеродистой стали длиной менее 2500 мм и толщиной менее 4 мм в сегмент цилиндра или дуги.
В процессе работы процесс прокатки листов происходит быстро, экономя энергию и снижая себестоимость продукции.
Однако предварительно изогнутый линейный сегмент в два раза толще пластины. И для работы на машине нужны квалифицированные рабочие, технические требования к персоналу выше.
Горизонтальное перемещение нижнего ролика, тип
Горизонтальное перемещение нижнего ролика 3-х валковые вальцы являются наиболее распространенной листопрокатной машиной, которая также является относительно зрелой прокатной машиной как в стране, так и за рубежом. Как правило, он принимает гидравлический привод. Принцип его работы следующий.
Верхний ролик представляет собой силовой ролик с фиксированным вращением, в соответствии с различными технологическими требованиями, два боковых ролика перемещаются по дуге по умолчанию во время рабочего процесса, прижимая металлическую пластину вместе с верхним роликом, и вращение верхнего ролика прекращается. прокатка цилиндра или прокатка конуса.
Как правило, ширина и толщина прокатки могут достигать 4000 мм и 6-40 мм отдельно для 3-валкового листогибочного станка с горизонтальным перемещением нижнего ролика. Самым большим преимуществом является дешевая цена. Однако это требует больших усилий от операторов, поскольку профилирование не может быть завершено за один раз. Линейный участок предварительного изгиба более чем в 2 раза превышает толщину листа.
Листопрокатный станок с изменяемой геометрией
Листопрокатный станок с изменяемой геометрией современное листопрокатное оборудование в стране и за рубежом, способное прокатывать металлические листы толщиной от 20 до 250 мм。
На следующем изображении показан принцип его работы.
Верхний ролик — это приводной ролик, который можно перемещать вверх и вниз. Два боковых ролика являются ведущими роликами, которые могут независимо перемещаться по горизонтали.
Каждое движение ролика может образовывать геометрическую форму. Вот почему его называют листопрокатным станком с геометрическими переменными параметрами.
В процессе обработки реализована горизонтальная подача пластин, предварительное изгибание, отсутствие необходимости в боковом толкающем устройстве и перемещении бокового ролика наружу. Кроме того, резко возрастает способность к изгибу. Предварительно изогнутый линейный отрезок не превышает толщины пластины.
Преимущество:
Можно заменить верхний ролик с другим диаметром, можно оборудовать системой ЧПУ с ПЛК, низкие требования к оператору, почти не имеет линейного сегмента предварительного изгиба, горизонтальная подача, не требует оснащения дорогими боковое толкающее устройство, способное прокатывать коническую заготовку с большим углом, цена ниже четырехвалковых гибочных валков с такой же способностью к изгибу.
Недостаток:
Скорость прокатки немного ниже, чем у 4-валкового листогибочного станка, не может прокатывать многосегментную дугу.
Четырехвалковый листогибочный станок является одним из самых надежных листогибочных станков для обрабатывающей промышленности. Это универсальная машина, которая может прокатывать многосегментную дугу, О-образную форму, квадрат, круг, дугу и т. Д. Она также может быть оснащена системой ЧПУ с диалогом «человек-машина» с высокой степенью автоматизации.
Четыре ролика обычно делятся на механический тип и гидравлический тип, и механический тип четырех роликов используется для прокатки металлического листа толщиной менее 6 мм, а четыре ролика гидравлического типа могут прокатывать до 6-200 мм. толстый лист.
На следующем рисунке показан принцип работы 4-валковой листогибочной машины.
Верхний ролик вращается, приводной ролик фиксируется, а нижний ролик может перемещаться как вверх, так и вниз. В основном он работает вместе с верхним роликом для зажима металлической пластины. Два боковых ролика перемещаются вверх и вниз в наклонном направлении. Функция заключается в позиционировании и формовании пластин.
Принцип работы четырехвалкового листогибочного станка на рынке одинаков, разница только в конструкции. Некоторые боковые ролики имеют планетарную дуговую направляющую, а другие имеют линейную направляющую.
До 2003 года 4-валковые листогибочные машины в основном использовали линейные направляющие. После этого планетарная дуговая направляющая выходит на рынок.
Некоторые производители придерживаются линейной направляющей, пусть даже с высокой стоимостью, но это удобно в обслуживании. Он также имеет большое преимущество при прокатке листового металла из высоколегированного сплава или материала из титанового сплава.
Однако я думаю, что для металлического листа с пределом текучести менее 500 МПа разница не слишком велика. А стоимость использования с планетарной дуговой направляющей будет намного ниже.
Преимущество:
Он может удовлетворить весь спектр прокатки листового металла, высокая степень автоматизации может быть оснащен автоматическими устройствами подачи вверх и вниз.
Недостаток:
Прямая линия предварительного изгиба более чем в 1,5 раза превышает толщину листа.
В дополнение к указанным выше обычным листовым валкам существуют специальные валки, такие как вертикальные валки, усиленные барабанные валки, корабельные валки и т. д.
Чем отличается формование листового металла от…
Если вам интересно, чем штамповка листового металла отличается от прокатки, читайте дальше, чтобы узнать!
Опубликовано Беном Брауном в понедельник, 28 февраля 2022 г.
Основное отличие состоит в том, что в то время как прокатка заставляет металл течь в другую форму, формование листового металла работает, вызывая деформацию материала в целом с минимальным воздействием на зерно. структуру или толщину материала.
Что такое процесс формовки листового металла?
Формование листового металла обычно происходит при комнатной температуре. Это процесс, при котором куски листового металла изменяются и переформировываются без удаления какого-либо исходного материала — прокатка, а также ковка и экструзия работают по-разному, потому что они прилагают силы к материалу, чтобы заставить его течь в новую форму. При формовании листового металла создается сила, вызывающая деформацию металла, что затем делает металл более ковким, поэтому его можно сгибать, растягивать и складывать в огромное разнообразие различных и часто очень сложных конструкций.
Формовка и гибка – в чем разница?
Гибка и формовка не отличаются друг от друга. Гибка – это разновидность формовки металла, где формовка – это разновидность изготовления металла. Поняв критические различия между ними, вы решите, какой процесс является оптимальным для вашего проекта.
Процессы прокатки, формовки и экструзии могут выполняться при температуре выше комнатной, при этом формование листового металла в большинстве случаев происходит при комнатной температуре. Размер зерна также, вероятно, будет улучшаться во время прокатки, ковки и экструзии (хотя и не всегда во время экструзии), когда размер зерна материала не улучшается во время формовки листового металла.
Прокатка и ковка
Прокатная ковка — это процесс, направленный на уменьшение площади поперечного сечения и изменение размеров нагретых прутков, заготовок или плит. Это достигается за счет пропускания материала между двумя приводными валками, вращающимися в противоположных направлениях. Каждый рулон имеет по крайней мере один совпадающий оттиск.
Прокатка включает пропускание металла между валками для уменьшения толщины материала до заданного размера. В этом процессе используются молот и наковальня или отбойный молоток в более крупных машинах. Прокатка может быть горячая или холодная. Холодный метод часто используется, если желаемый результат состоит в том, чтобы сделать металл более жестким или твердым.
Прокатка и экструзия
Экструзия работает для создания различных компонентов в процессе, который проталкивает или вытягивает материал через фильеру желаемого поперечного сечения.
Таким образом можно обрабатывать множество различных материалов, включая алюминий, полимеры и керамику. Экструзия может быть как горячей, так и холодной.
Высококачественные профилегибочные станки от ООО «Роллформинг»
Если вы ищете профилегибочный станок для своего бизнеса, просмотрите профили от ООО «Роллформинг» сегодня.