Протекторная защита от коррозии: Протекторная защита металлов от коррозии
alexxlab | 07.08.1984 | 0 | Разное
Протекторная защита, магниевые протекторы – ООО “СОМЗ”
Как бороться с коррозией металла? С этой проблемой постоянно приходится сталкиваться и на производстве, и в быту.
Особенно важна эта проблема в тех областях производственной деятельности, где высока вероятность различных техногенных катастроф, а так же в нефтегазодобывающей промышленности, в судостроении, на морском флоте и др. Так, например, из-за сквозных коррозионных разрушений днищ резервуаров типа РВС (для отстоя нефти) и промысловых трубопроводов происходят многочисленные разливы нефти, загрязняющие окружающую среду, а также возникает преждевременная необходимость в замене днищ резервуаров, и это при диаметре днища, составляющего, например, для РВС-20 000 почти 50 м.
Коррозия корпусов танкеров (прежде всего старой постройки, не имеющих двойного дна) приводит к утечке нефтепродуктов и балластной воды с остатками перевозимых грузов и продуктами коррозии железа, что так же представляет серьёзную экологическую проблему. На сегодняшний день существует две основные системы противокоррозионной защиты: специальная окраска танков и установка электрохимической протекторной защиты. Как известно, окраска корпуса судна, требующая значительных финансовых затрат, не даёт 100% гарантии защиты от коррозии в морской воде, тем более для судов, длительное время находящихся в эксплуатации. Поэтому наиболее эффективным и экономически выгодным методом является протекторная защита, установка которой не требует специальной подготовки поверхности и крайне проста в исполнении.
Электрохимическая защита металлов от коррозии основана на том, что коррозия металлов прекращается под действием постоянного электрического тока. Поверхность любого металла, гальванически неоднородна, что и является основной причиной его коррозии в растворах электролитов, к которым относятся морская вода, все пластовые и все подтоварные воды. При этом разрушаются только участки поверхности металла с наиболее отрицательным потенциалом (аноды), с которых ток стекает во внешнюю среду, а участки металлов с более положительным потенциалом (катоды), в которые ток втекает из внешней среды, не разрушаются.
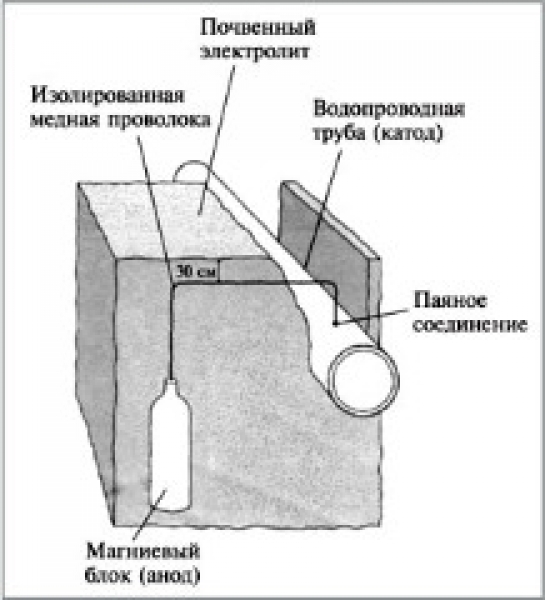
Протекторная защита обычно применяется совместно с лакокрасочными покрытиями. Такое сочетание позволяет уменьшить расход протекторов и тем самым увеличить срок их службы, обеспечить более равномерное распределение защитного тока по поверхности защищаемых конструкций и, компенсировать дефекты покрытия, возникающие в процессе его эксплуатации. Защитный ток идет именно на те участки поверхности металла, где нарушена плотность покрытия, предотвращая коррозию оголившегося металла. При этом на оголенной поверхности металла при его катодной поляризации в воде выпадает катодный солевой осадок, состоящий из нерастворимых солей кальция и магния.
Протекторная защита в состоянии обеспечить полную защиту от коррозии стальныхсооружений и без их окраски. В этом случае должна быть обеспечена более высокая плотность защитного тока на неокрашенной стальной поверхности, что потребует увеличения количества протекторов и усилит их расход. Однако, учитывая трудность нанесения лакокрасочных покрытий, особенно на судах и резервуарах, уже находящихся в эксплуатации, такой способ противокоррозионной защиты с помощью только одних протекторов станет успешным решением.
Поскольку основная масса металлических конструкций делается, как правило, из стали, в качестве протектора могут использоваться металлы с более отрицательным, чем у стали электродным потенциалом. Из основных, их три – цинк, алюминий и магний.
Основное отличие магниевых протекторов – наибольшая разность потенциалов магния и стали, увеличивающая радиус защитного действия, что позволяет использовать меньшее количество магниевых протекторов, чем цинковых и алюминиевых. Кроме того, у магния и магниевых сплавов, в отличие от цинка и алюминия, отсутствует поляризация, сопровождаемая уменьшением токооотдачи. Это определяет основное применение магниевых протекторов для защиты подземных трубопроводов в грунтах с высоким удльным сопротивлением.
Для получения более подробной информации свяжитесь с нами по телефону +7 (342 53) 9-89-98. Наши специалисты будут рады вас проконсультировать.
Протекторная защита от коррозии. Основные способы защиты трубопроводов от коррозии
Любые металлические изделия легко разрушаются под воздействием определенных внешних факторов, чаще всего влажности. Чтобы предотвратить подобные явления, используется протекторная защита от коррозии. Ее задача – снизить потенциал основного материала и тем самым защитить его от коррозии.
Суть процедуры
Протекторная защита строится на основе такого вещества, как ингибитор. Это металл, имеющий повышенные электроотрицательные качества. При воздействии на него воздуха происходит растворение протектора. Вследствие этого основной материал сохраняется, даже если на него оказывается сильное влияние коррозии.
Различные виды коррозии легко победить, если использовать катодные электрохимические методы, к которым относится и протекторная защита. Подобная процедура – идеальное решение, когда у предприятия нет финансовых возможностей или технологического потенциала, чтобы обеспечить полноценную защиту от коррозийных процессов.
Основные преимущества
Протекторная защита металлов от коррозии – это хороший способ защиты любых металлических поверхностей. Использование его целесообразно в нескольких случаях:
- Когда предприятию не хватает производственных мощностей, чтобы использовать более энергозатратные методики.
- Когда требуется защитить малогабаритные конструкции.
- Если требуется защита металлических изделий и объектов, поверхности которых покрыты изоляционными материалами.
Чтобы достичь максимальной эффективности, целесообразно использовать протекторную защиту в электролитической среде.
Когда требуется защита?
Коррозия возникает на любых металлических поверхностях в самых разных сферах – от нефтегазодобывающей промышленности до судостроения. Протекторная защита от коррозии широко применяется в окраске корпусов танкеров. Эти судна постоянно подвергаются воздействию воды, и специальная окраска не всегда справляется с предотвращением реакций влаги с металлической поверхностью. Использование протекторов – простое и эффективное решение проблемы, особенно если суда будут находиться в эксплуатации длительное время.
Большинство конструкций из металла создается из стали, поэтому целесообразно использовать протекторы, имеющие отрицательный электродный потенциал. Основными для производства протекторов являются три металла – цинк, магний, алюминий. Из-за большой разности потенциалов этих металлов и стали радиус защитного действия становится шире, и любые виды коррозии легко устраняются.
Какие металлы используются?
Защитная система строится на основе различных сплавов, в зависимости от специфики использования протекторов, например, среды, в которой он будет использоваться. Протекторная защита от коррозии чаще всего требуется железным и стальным изделиям, но и поверхностям из цинка, алюминия, кадмия или магния она также требуется. Особенность протекторной защиты – в использовании гальванических анодов, которые обеспечивают защиту труб от почвенной коррозии. Расчет подобных установок выполняется с учетом ряда параметров:
- силы тока в протекторе;
- показателей его сопротивления;
- степени защиты, нужной для 1 км трубы;
- количества протекторов на этот же отрезок;
- расстояния, которое имеется между элементами защитной системы.
Плюсы и минусы различных протекторов
На основе протекторов строится защита строительных конструкций от коррозии, трубопроводов разного типа (распределительных, магистральных, промысловых). При этом использовать их нужно грамотно:
- использование алюминиевых протекторов целесообразно для того, чтобы защитить конструкции и сооружения в морской воде и прибрежном шельфе;
- магниевые подходят для использования в слабоэлектропроводной среде, где алюминиевые и цинковые протекторы показывают низкую эффективность. Но их нельзя использовать, если требуется защитить внутренние поверхности танкеров, резервуаров, отстойников для нефти, так как магниевые протекторы отличаются повышенной взрыво- и пожароопасностью. В идеале проекторы на основе этого элемента нужно использовать для внешней защиты конструкций, которые используются в пресной среде;
- цинковые протекторы полностью безопасны, поэтому их можно использовать на любых объектах, даже если на них высокий уровень пожарной опасности.
Если покрытие лакокрасочное
Очень часто требуется обеспечить защиту нефте- или газопровода от коррозии с учетом лакокрасочного покрытия. Комбинация его с протектором – это пассивный способ защиты конструкций от коррозии. При этом эффективность такого мероприятия не так высока, зато достигается следующее:
- нивелируются дефекты на покрытиях конструкций из металлов, трубопроводов, например, отслаивание, появление трещин;
- снижается расход протекторных материалов, при этом сама защита оказывается более долговечной;
- защитный ток равномерно распределяется по металлической поверхности изделия или объекта.
Протекторная защита от коррозии в сочетании с лакокрасочными покрытиями – это возможность распределения защитного тока именно на те поверхности, которые требуют максимального внимания.
О защите трубопроводов
По мере эксплуатации металлические трубы изнутри и снаружи подвергаются воздействию коррозии. Налет появляется вследствие того, что по трубам текут агрессивные вещества, которые вступают в реакцию с материалами. На внутреннее состояние металлических изделий влияет высокий уровень влажности почвы. Если не будет продумана качественная защита строительных конструкций от коррозии, произойдет следующее:
- трубопровод начнет разрушаться изнутри;
- потребуется чаще проводить профилактические осмотры магистралей;
- потребуется более частый ремонт, что скажется на дополнительных тратах;
- потребуется полностью или частично остановить нефтеперерабатывающий или иной другой промышленный комплекс.
Существует несколько способов защиты трубопроводов – пассивные, активные. Также как средство защиты может выступать снижение агрессивности среды. Чтобы защита была комплексной, учитывается тип трубопровода, способ его монтажа и взаимодействие с окружающей средой.
Пассивные и активные методы защиты
Все основные способы защиты трубопроводов от коррозии сводятся к выполнению целого ряда работ. Если говорить о пассивных методах, они выражаются в следующем:
- особом способе укладки, когда сопротивляемость к коррозии продумывается еще на стадии монтажа трубопровода.
Для этого между землей и трубой оставляется воздушный зазор, благодаря которому внутрь трубопровода не попадут ни грунтовые воды, ни соли, ни щелочи;
- нанесении специальных покрытий на трубы, которые будут защищать поверхность от почвенных воздействий;
- обработке специальной химией, например, фосфатами, образующими на поверхности защитную пленку.
Схема защиты на основе активных методов предполагает использование электрического тока и электрохимических реакций ионного обмена:
- электродренажной защиты для борьбы с блуждающими токами;
- анодной защиты, которая замедляет процесс разрушения металла;
- катодной защиты, когда постоянный ток повышает сопротивляемость металлов.
Доводы в пользу протекторной защиты
Как видно, способов повысить защитные характеристики трубопроводов и других металлических изделий немало. Но все они требуют траты электрического тока. Протекторная защита от коррозии трубопроводов – более выгодное решение, так как все процессы окислов прекращаются просто нанесением на поверхности труб из металлов сплавов других материалов. В пользу такого способа говорят следующие факторы:
- экономичность и простота процесса за счет отсутствия источника постоянного тока и применения сплавов магния, цинка или алюминия;
- возможность применения одиночных или групповых установок, при этом схема протекторной защиты продумывается с учетом особенностей проектируемого или уже построенного объекта;
- возможность применения на любых почвах и в условиях морей/океанов, где дорого или невозможно использовать источники внешнего тока.
Протекторную защиту можно использовать для повышения сопротивляемости коррозии различных резервуаров, корпусов судов, цистерн, которые используются в экстремальных условиях.
1.5 Протекторная защита резервуара от коррозии
Электрохимическая защита осуществляется претокторной защитой резервуаров. При протекторной защите поляризация осуществляется присоединением защищаемого резервуара к металлу, имеющему более отрицательный потенциал.
Протекторная
защита резервуаров от почвенной коррозии
осуществляется одиночными и групповыми
(рисунок 4).
а – защита одиночными протекторами; б – защита групповыми протекторными установками.
Рисунок 4 – Схема защиты днища резервуара от почвенной коррозии
Протекторы значительно снижают коррозионный процесс, возникающий как под воздействием почвенных электролитов (повреждение внешней стороны резервуара), так и под воздействием другого электролита – подтоварной воды с растворенными в ней солями хлоридов: магния, натрия, кальция и железа (повреждение внутренней стороны резервуара). При отстаивании нефти и разрушении эмульсии вода вместе с растворенными в ней солями собирается на дне резервуара и вызывает усиленную электрохимическую коррозию днища и нижнего пояса.
Принцип
протекторной защиты основан на следующем:
два электрода: резервуар и протектор,
изготовленного из более электроотрицательного
металла, чем сталь, опущены в почвенный
электролит и соединены проводником.
Так как материал протектора является
более электроотрицательным, то под
действием разности потенциалов происходит
направленное движение электронов от
протектора к резервуару по проводнику.
Таким образом, разрушение металла все равно имеет место. Но не резервуара, а протектора.
Теоретически для защиты стальных сооружений от коррозии могут быть использованы все металлы, расположенные в электрохимическом ряду напряжений левее железа, т.к. они более электроотрицательны. Практически же протекторы изготавливаются только из материалов, удовлетворяющих следующим требованиям:
- разность потенциалов материала протектора и железа (стали) должна быть как можно больше;
ток, получаемый при электрохимическом растворении единицы массы протектора (токоотдача), должен быть максимальным;
отношение массы протектора, израсходованной на создание защитного тока, к общей потере массы протектора (коэффициент использования) должен быть наибольшим.
Данным требованиям в наибольшей степени удовлетворяют магний, цинк и алюминий.
Одна из положительных особенностей протекторной защиты – ее автономность, она может быть осуществлена в районах, где нет электроэнергии.
Протекторную защиту рекомендуется использовать в грунтах с удельным сопротивлением не более 50 Ом.м.
В качестве протекторов для протекторной защиты используются протекторы типа ПМУ (прутковые магниевые протекторы).
Конструкция протекторов ПМУ приведена на рисунке 7, она включает в себя протекторы типа ПМ с подключенным кабелем, помещенные вместе с активатором в хлопчатобумажный мешок.
Прутковые
магниевые протекторы представляют
собой биметаллический пруток с оболочкой
из магниевого сплава и стальным
оцинкованным контактным стержнем
диаметром 4 мм, проходящим по центру
прутка. Форму сечения (круглую,
эллипсовидную) прутковых магниевых
протекторов определяет технология их
изготовления. Прутковые магниевые
протекторы поставляются смотанными на
барабаны или в
бухты.
а – разрез; б – внешний вид.
Рисунок 7 – Конструкция протекторов типа ПМУ
Протекторы ПМ5У, ПМ10У, ПМ20У представляют собой комплект, состоящий из магниевого протектора ПМ5, ПМ’10, ПМ20 с подключенным к нему проводником и порошкообразного активатора, помещенных в хлопчатобумажный мешок активатор, или заполнитель служит для предотвращения образования на поверхности протектора слоя нерастворимых окислов, снижающих его токоотдачу, уменьшения сопротивления цепи “протектор—труба”, а также для поддержания постоянного потенциала. На время складского хранения и транспортировки протектор дополнительно упаковывается в бумажный мешок, который снимается перед установкой его в грунт
Повышение
эффективности действия протекторной
установки достигается погружением его
в специальную смесь солей глины,
называемую активатором. Непосредственная
установка протектора в грунт менее
эффективна, чем в активатор.
Назначение активатора следующее: снижение собственной коррозии, уменьшение анодной поляризуемости, снижение сопротивления растеканию тока с протектора, устранение причин, способствующих образованию плотных слоев продуктов коррозии на поверхности протектора. При использовании активатора обеспечивается стабильный во времени ток в цепи «протектор-сооружение» и более высокое значение коэффициента полезного действия (срока службы протектора).
Широкое распространение получила протекторная защита днища и первого пояса резервуаров от внутренней коррозии. Для этих целей используются магниевые протекторы типа ПМР (рисунок 5).
Рисунок 5 – Протектор типа ПМР
Протектор
типа ПМР представляет собой цилиндр с
отношение высоты к диаметру 0,2–0,4 имеющий
углубление в верхней части в идее
опрокинутого усеченного конуса. Это
сделано для того, чтобы увеличить
поверхность протектора и соответственно
силу тока в начальной период его работы.
В центре протектора впрессована стальная
втулка для обеспечения контакта
протектора с днищем.
Габаритные размеры протектора типа ПМР позволяют монтировать его через нижний люк-лаз.
Сравнительно небольшая высота протектора обеспечивает защиту днища резервуара при низких уровнях подтоварной воды. В зависимости от общей концентрации солей в подтоварной воде применяют определенный тип протектора.
Рисунок – 6 Размещение протекторов на днище резервуара РВС-10000 (2r3=5,5 м, a=2,5 м).
Протектор
монтируют на еще не затвердевшее
покрытие, чтобы он приклеился к днищу.
Зазор между контактной втулкой
протектора и стальным стержнем заливают
лаком или эпоксидной смолой, после этого
контактную втулку приваривают к
стержню.
Для контроля работы защиты один, два протектора устанавливают в качестве контрольных. Контрольный протектор закрепляют на втулке диаметром 6 мм, которую изолируют полихлорвиниловой трубкой. Затем к втулке припаивают проводник сечением 0,75 мм2 (провод ПМВГ), выводят его из резервуара через штуцер с сальниковым уплотнением и присоединяют к контрольно-измерительной панели.
Работу
протекторов контролируют периодическими
измерениями: силы тока, разности
потенциалов днище-электролит (подтоварная
вода) и защитной плотности тока. Силу
тока протектора измеряют, подключая
амперметр в цепь на клеммной панели
или измеряя падение напряжения на
шунте, или калибруя постоянно включенные
в цепь протектора сопротивления. Силу
тока определяют при минимальном и
максимальном уровнях подтоварной воды
один раз в месяц. Результаты измерений
фиксируют в журнале. Отсутствие тока
чаще всего указывает на нарушение
контакта, что может быть при полном
срабатывании протектора. По силе тока
можно судить о средней плотности тока защиты,
а также рассчитывать срок службы
протекторов.
Протекторная защита от коррозии металлических изделий
Суть процедуры
Протекторная защита строится на основе такого вещества, как ингибитор. Это металл, имеющий повышенные электроотрицательные качества. При воздействии на него воздуха происходит растворение протектора. Вследствие этого основной материал сохраняется, даже если на него оказывается сильное влияние коррозии.
Различные виды коррозии легко победить, если использовать катодные электрохимические методы, к которым относится и протекторная защита. Подобная процедура – идеальное решение, когда у предприятия нет финансовых возможностей или технологического потенциала, чтобы обеспечить полноценную защиту от коррозийных процессов.
История открытия
Катодная защита была впервые описана сэром Гемфри Дэви в серии докладов, представленных Лондонскому королевскому обществу по развитию знаний о природе в 1824 году. После продолжительных испытаний впервые катодную защиту применили в 1824 г. на судне HMS Samarang. Анодные протекторы из железа были установлены на медную обшивку корпуса судна ниже ватерлинии, что значительно снизило скорость корродирования меди. Медь, корродируя, высвобождает ионы меди, которые обладают антиобрастающим эффектом. В связи с чрезмерным обрастанием корпуса и снижением эффективности корабля Королевский военно-морской флот Великобритании принял решение отказаться от протекторной защиты, чтобы получить преимущества от антифоулингового эффекта вследствие корродирования меди.
Основные преимущества
Протекторная защита металлов от коррозии – это хороший способ защиты любых металлических поверхностей. Использование его целесообразно в нескольких случаях:
- Когда предприятию не хватает производственных мощностей, чтобы использовать более энергозатратные методики.
- Когда требуется защитить малогабаритные конструкции.
- Если требуется защита металлических изделий и объектов, поверхности которых покрыты изоляционными материалами.
Чтобы достичь максимальной эффективности, целесообразно использовать протекторную защиту в электролитической среде.
Решение задач по химии на покрытие металлов
Задание 284. Если пластинку из чистого цинка опустить в разбавленную кислоту, то начавшееся выделение водорода вскоре почти прекращается. Однако при прикосновении к цинку медной палочкой на последней начинается бурное выделение водорода. Дайте этому объяснение, составив электронные уравнения анодного и катодного процессов. Напишите уравнения протекающей химической реакции.Решение: При опускании пластинки из чистого цинка в раствор разбавленной кислоты, начавшееся выделение водорода вскоре почти прекратится, потому что на пластинке из цинка образуется оксидная плёнка, которая будет препятствовать дальнейшему взаимодействию цинка с разбавленной кислотой. Оксидная плёнка образуется при взаимодействии цинка с кислородом, растворённым в воде по схеме:
Zn + 1/2 O2 = ZnO
Если прикоснуться к цинковой пластинке медной палочкой, то возникнет гальваническая пара цинк — медь, в которой цинк будет являться анодом, а медь – катодом. Это происходит, потому что стандартный электродный потенциал цинка (-0,763 В) значительно отрицательнее, чем потенциал меди (+0,34 В).
Образующиеся ионы Zn2+ будут с имеющимися анионами кислоты давать соль, а ионы водорода Н+, деполяризуясь на медной палочке, Zn – 2 = Zn2+образуют водород, который в виде пузырьков газа выделяется из раствора. Ионно-молекулярное уравнение реакции будет иметь вид:
Молекулярная форма уравнения реакции:
Задание 285. В чем сущность протекторной защиты металлов от коррозии? Приведите пример протекторной защиты железа в электролите, содержащем растворенный кислород. Составьте электронные уравнения анодного и катодного процессов.Решение: Для предотвращения коррозии стальных конструкций применяется протекторная защита: создаётся электрический контакт защищаемой конструкции с протектором – более активным металлом (обычно Zn, Mg, Al или их сплавы). При таком контакте возникает гальваническая пара типа Zn — Fe и коррозии подвергается протектор, а не сама стальная конструкция (трубопровод, корпус корабля и т. п.). Например, корпус корабля защищают протектором – цинковые брусья, которые крепят в нескольких местах днища корабля. Под действием морской воды и кислорода цинк разрушается, а корпус корабля защищается, таким образом, от коррозии. При этом протекают следующие электрохимические процессы:
Анодный процесс: Zn – 2 = Zn2+;Катодный процесс: а) в нейтральной или щелочной среде: 1/2O2 + h3O + 2 = 2OH-; б) в кислой среде: 1/2O2 + 2H+ + 2 = h3O
Таким образом, цинк разрушается, окисляясь до ионов Zn2+, которые с гидроксильными ионами образуют нерастворимый гидроксид Zn(OH)2 или в виде ионов Zn2+ уходит в раствор, если реакция среды кислая. Основной металл остаётся неповреждённым.
Задание 286. Железное изделие покрыли никелем. Какое это покрытие – анодное или катодное? Почему? Составьте электронные уравнения анодного и катодного процессов коррозии этого изделия при нарушении покрытия во влажном воздухе и в хлороводородной (соляной) кислоте. Какие продукты коррозии образуются в первом и во втором случаях?Решение: Железо имеет более электроотрицательный стандартный электродный потенциал (-0,44 В), чем никель (-0,24 В), поэтому железо является анодом, никель – катодом.
Анодный процесс – окисление металла: Fe – 2 = Fe2+
и катодный процесс – восстановление ионов водорода (водородная деполяризация) или молекул кислорода (кислородная деполяризация). Поэтому при коррозии пары Fe — Ni с водородной деполяризацией происходит следующие процессы:
Анодный процесс: Fe – 2 = Fe2+ Катодный процесс: в кислой среде: 2Н+ + 2 = Н2
Продуктом коррозии будет газообразный водород соединение железа с кислотным остатком (соль).
При коррозии пары Fe — Ni в атмосферных условиях на катоде происходит кислородная деполяризация, а на аноде – окисление железа:
Анодный процесс: Fe – 2 = Fe2+
Катодный процесс: в нейтральной среде: 1/2O2 + h3O + 2 = 2OH-
Так как ионы Fe2+ с гидроксид-ионами ОН- образуют нерастворимый гидроксид, то продуктом коррозии будет Fe(OH)2. При контакте с кислородом воздуха Fe(OH)2 быстро окисляется до метагидроксида железа FeO(OH), приобретая характерный для него бурый цвет:
4Fe(OH)2 + О2 = 4FeO(OH) + 2Н2О
Так как никель имеет более электроположительный стандартный электродный потенциал, чем железо, то данное покрытие является катодным. При повреждении катодного покрытия (или наличия пор) возникает коррозионный элемент, в котором основной материал в поре служит анодом и растворяется, а материал покрытия – катодом, на котором выделяется водород или поглощается кислород. Следовательно, данное катодное покрытие может защищать железо от коррозии лишь при отсутствии пор и повреждений покрытия.
Когда требуется защита?
Коррозия возникает на любых металлических поверхностях в самых разных сферах – от нефтегазодобывающей промышленности до судостроения. Протекторная защита от коррозии широко применяется в окраске корпусов танкеров. Эти судна постоянно подвергаются воздействию воды, и специальная окраска не всегда справляется с предотвращением реакций влаги с металлической поверхностью. Использование протекторов – простое и эффективное решение проблемы, особенно если суда будут находиться в эксплуатации длительное время.
Большинство конструкций из металла создается из стали, поэтому целесообразно использовать протекторы, имеющие отрицательный электродный потенциал. Основными для производства протекторов являются три металла – цинк, магний, алюминий. Из-за большой разности потенциалов этих металлов и стали радиус защитного действия становится шире, и любые виды коррозии легко устраняются.
Какие металлы используются?
Защитная система строится на основе различных сплавов, в зависимости от специфики использования протекторов, например, среды, в которой он будет использоваться. Протекторная защита от коррозии чаще всего требуется железным и стальным изделиям, но и поверхностям из цинка, алюминия, кадмия или магния она также требуется. Особенность протекторной защиты – в использовании гальванических анодов, которые обеспечивают защиту труб от почвенной коррозии. Расчет подобных установок выполняется с учетом ряда параметров:
- силы тока в протекторе;
- показателей его сопротивления;
- степени защиты, нужной для 1 км трубы;
- количества протекторов на этот же отрезок;
- расстояния, которое имеется между элементами защитной системы.
Технология катодной поляризации
В данном случае используется так называемый наложенный ток. Для его подачи на металлический объект используется внешний проводник (часто) или источник тока (редко). При контакте с электрически активной частицей происходит следующее — частица под действием сил электрического притяжения перемещается к защитному элементу с отрицательным зарядом, где происходит «утилизация» этих частиц.
Последствия такой «утилизации» очевидны — защитный элемент со временем сам покрывается коррозией и приходит в негодность. Поэтому данную технологию очень часто называют методом жертвенного электрода (вместо нашей детали происходит ржавление «электрода-жертвы»).
Помимо силы тока и напряжения при работе с катодной поляризацией нужно учитывать еще один важный параметр — это омическое напряжение. В техническом смысле этот параметр отражает тот факт, что по мере протекания электрического заряда со временем напряжение тока в контуре падает. Само падение происходит из-за того, что протекание катодного тока происходит по контуру с более низким зарядом. В случае правильной сборки контура этот показатель является достаточно маленьким — благодаря этому в контуре будет всегда сохраняться один и тот же ток одинаковой мощности.
Плюсы и минусы различных протекторов
На основе протекторов строится защита строительных конструкций от коррозии, трубопроводов разного типа (распределительных, магистральных, промысловых). При этом использовать их нужно грамотно:
- использование алюминиевых протекторов целесообразно для того, чтобы защитить конструкции и сооружения в морской воде и прибрежном шельфе;
- магниевые подходят для использования в слабоэлектропроводной среде, где алюминиевые и цинковые протекторы показывают низкую эффективность. Но их нельзя использовать, если требуется защитить внутренние поверхности танкеров, резервуаров, отстойников для нефти, так как магниевые протекторы отличаются повышенной взрыво- и пожароопасностью. В идеале проекторы на основе этого элемента нужно использовать для внешней защиты конструкций, которые используются в пресной среде;
- цинковые протекторы полностью безопасны, поэтому их можно использовать на любых объектах, даже если на них высокий уровень пожарной опасности.
Если покрытие лакокрасочное
Очень часто требуется обеспечить защиту нефте- или газопровода от коррозии с учетом лакокрасочного покрытия. Комбинация его с протектором – это пассивный способ защиты конструкций от коррозии. При этом эффективность такого мероприятия не так высока, зато достигается следующее:
- нивелируются дефекты на покрытиях конструкций из металлов, трубопроводов, например, отслаивание, появление трещин;
- снижается расход протекторных материалов, при этом сама защита оказывается более долговечной;
- защитный ток равномерно распределяется по металлической поверхности изделия или объекта.
Протекторная защита от коррозии в сочетании с лакокрасочными покрытиями – это возможность распределения защитного тока именно на те поверхности, которые требуют максимального внимания.
Составные элементы катодной защиты
Есть обязательные составляющие, без которых защита просто не будет функционировать.
Катод и анод
Катодом в нашей схеме защиты является сам автомобиль, он будет служить минусом. Анодом может быть любая металлическая конструкция, пластина и любая поверхность, которая способна проводить электрический ток, даже мокрый асфальт. Без этих двух составляющих электрохимическая защита автомобиля от коррозии просто не будет функционировать.
От некоторых специалистов можно услышать про разность потенциалов и степень защиты, которая определяется этим показателем. Железо будет защищено от коррозии при величине потенциалов в пределах 0,1–0,2 В. На самом деле расстояние, которое находится между анодом и катодом, может достигать нескольких сантиметров и даже метров. Чем больше расстояние между электродами, тем большей должен быть показатель разницы потенциалов. Да и воздух не будет проводить ток небольшого напряжения, разница потенциалов должна быть на уровне киловольта.
Что действительно влияет на эффективность защиты автомобиля, так это площадь анода. Чем она больше, тем катодная защита автомобиля от коррозии будет лучше проявляться.
Электрический ток
Чтобы схема исправно работала, электрический ток между двумя электродами не нужен. Даже если он и возникнет, то будет носить характер побочного продукта. Такой ток может образоваться от мокрого анода, намокших колёс машины и т. д. А проявляться он будет на аккумуляторе, который разрядится быстрее обычного.
Чтобы установка катодной защиты не принесла вреда автомобилю, а работала в нужном нам направлении, потребуется бортовую систему соединить с анодом посредством добавочного резистора. Такое устройство позволит ограничить разряд аккумулятора в том случае, если анод будет замкнут на катоде. Причиной такой ситуации может быть неправильно собранная схема, выход из строя анода, например, полное окисление вплоть до разложения.
О защите трубопроводов
По мере эксплуатации металлические трубы изнутри и снаружи подвергаются воздействию коррозии. Налет появляется вследствие того, что по трубам текут агрессивные вещества, которые вступают в реакцию с материалами. На внутреннее состояние металлических изделий влияет высокий уровень влажности почвы. Если не будет продумана качественная защита строительных конструкций от коррозии, произойдет следующее:
- трубопровод начнет разрушаться изнутри;
- потребуется чаще проводить профилактические осмотры магистралей;
- потребуется более частый ремонт, что скажется на дополнительных тратах;
- потребуется полностью или частично остановить нефтеперерабатывающий или иной другой промышленный комплекс.
Существует несколько способов защиты трубопроводов – пассивные, активные. Также как средство защиты может выступать снижение агрессивности среды. Чтобы защита была комплексной, учитывается тип трубопровода, способ его монтажа и взаимодействие с окружающей средой.
Виды ингибиторов
- для кислых сред;
- от атмосферного влияния;
- против коррозии сероводородной;
- для хранилищ и магистралей с нефтепродуктами;
- для сред нейтральных.
В свою очередь, все группы имеют «внутреннюю классификацию». Например, вещества подразделяются на органические, неорганические и летучие; смешанные, катодные или анодные.
Независимо от своего химического состава, одно и то же средство по-разному ведет себя в той или иной агрессивной среде.
Пассивные и активные методы защиты
Все основные способы защиты трубопроводов от коррозии сводятся к выполнению целого ряда работ. Если говорить о пассивных методах, они выражаются в следующем:
- особом способе укладки, когда сопротивляемость к коррозии продумывается еще на стадии монтажа трубопровода. Для этого между землей и трубой оставляется воздушный зазор, благодаря которому внутрь трубопровода не попадут ни грунтовые воды, ни соли, ни щелочи;
- нанесении специальных покрытий на трубы, которые будут защищать поверхность от почвенных воздействий;
- обработке специальной химией, например, фосфатами, образующими на поверхности защитную пленку.
Схема защиты на основе активных методов предполагает использование электрического тока и электрохимических реакций ионного обмена:
- электродренажной защиты для борьбы с блуждающими токами;
- анодной защиты, которая замедляет процесс разрушения металла;
- катодной защиты, когда постоянный ток повышает сопротивляемость металлов.
Доводы в пользу протекторной защиты
Как видно, способов повысить защитные характеристики трубопроводов и других металлических изделий немало. Но все они требуют траты электрического тока. Протекторная защита от коррозии трубопроводов – более выгодное решение, так как все процессы окислов прекращаются просто нанесением на поверхности труб из металлов сплавов других материалов. В пользу такого способа говорят следующие факторы:
- экономичность и простота процесса за счет отсутствия источника постоянного тока и применения сплавов магния, цинка или алюминия;
- возможность применения одиночных или групповых установок, при этом схема протекторной защиты продумывается с учетом особенностей проектируемого или уже построенного объекта;
- возможность применения на любых почвах и в условиях морей/океанов, где дорого или невозможно использовать источники внешнего тока.
Протекторную защиту можно использовать для повышения сопротивляемости коррозии различных резервуаров, корпусов судов, цистерн, которые используются в экстремальных условиях.
заземления
Электроснабжение УНП2-7-65
Корпуса распределительного щита, установки УНП, компрессора, нагревателя воздуха объединены общим проводом заземления , который выведен на болт заземления, установленный на раме автомобиля с левой стороны. Этот болт должен быть связан с з.
Нагреватель воздуха для УНП2-7-65
2. Проверить подключение заземления к пульту управления. 6.3. Открыть пульт управления. Убедиться в отсутствии влаги или грязи внутри пульта управления и проверить положение ручек выключателей УЗО и автомате «Подогрев»: УЗО должно быть включено (ручка .
Монтаж внутрицеховых трубопроводов
Какие минимальные расстояния допускаются между осями прокладываемых труб? 4. Расскажите о правилах заземления трубопроводов для отвода статического электричества. .
протекторная защита от коррозии
button
В общем друг мой подвязался делать оградку в одно очень неблагоприятное ( в смысле влажности) место.
и возник у нас спор, как защитить столбы от коррозии.
Он бьет кулаком в грудь, что все продумал, и кинет цинковую болванку в воду, что замедлит коррозию конструкции в 10раз…
я с теорией не спорю, но мне кажется что в наших условиях и в пресной воде работать это не будет…
кто что скажет?
draconB76
столбы хоть из чего?
что такое протекторная защита?
carrier
button
но мне кажется что в наших условиях и в пресной воде работать это не будет…
Если обеспечить непосредственный контакт болванки и столба,то теоретически образуется гальванопара. Цинк будет разрушаться,сохраняя сталь. На практике я бы вообще не заморачивался. Коррозия под землёй не так велика как правило.Там кислорода мало. Быстрее корродирет металл на границе заглубления.
button
draconB76
столбы хоть из чего?
столб вроде даже из легированной столи… основание к которому он крепится – сталь3 видимо… но я думаю марка стали тут роли не играет.
draconB76
что такое протекторная защита?
погугли… я так понял что основано на гидролизе, только медленнее
carrier
Если обеспечить непосредственный контакт болванки и столба
ну припаять то не проблема
carrier
На практике я бы вообще не заморачивался. Коррозия под землёй не так велика как правило.Там кислорода мало. Быстрее корродирет металл на границе заглубления.
там не земля. там гораздо хуже. это над водой. иначе я бы и вопрос не поднимал 😊 в земле то скорее я сгнию чем тот столб 😊))
carrier
В воде тоже коррозия слабая. Сильнее ржавеет на воздухе. Корабли по пол века ходят и больше и ничего.К тому же вода пресная.
button
ёперный театр 😊 видимо без фото не объяснить… НАД водой
carrier
button
НАД водой
Загрунтовать,покрасить и забить(на это дело). )))) Причалы и мостки стоят десятками лет и нормально. 😊
button
draconB76
Протектор – уже есть защита.
протекторная защита – нескладушка.
Однако есть вид защиты металла, когда на корпус подаётся заряд. а на дополнительную железяку – противоположный. В итоге разлагается на ионы дополнительная железяка.
Таким образом защищают от коррозии днища кораблей и подводных лодок. Как подробнее – я не знаю.
андрей евгенич
а не проще изоляцию наложить вот такую http://www.germesizol.ru/page132.html
Gasar
В общем друг мой подвязался делать оградку в одно очень неблагоприятное ( в смысле влажности) место.
и возник у нас спор, как защитить столбы от коррозии.
да не надо выдумывать ничего. корабельная эмаль нужна, и тщательно зачищенная и обезжиренная поверхность.
протекторная – работает на плоскости. в полном контакте с материалом, здесь она никуда совсем.
Каценеленбоген
Протекторная защита…
Гыыыыы.
Пущай сначала строительные перчатки правильно научится надевать.
😀
carrier
Раньше днища машин красили корабельным суриком.Неплохая вещь надо сказать но требовала обновления, так как камнями отбивался.На такой конструкции будет держаться долго.
button
Это фото не совсем корректно. Обычно столб приваривается только с 3х сторон. В любом случае негерметично. Покрасить то покрасят, но ржаветь он изнутри будет. Внутри то не покрасишь. Ну а по поводу перчаток, так их очки одеть не заставишь не то что краги…. хоть так
button
draconB76
Протектор – уже есть защита.
протекторная защита – нескладушка.Однако есть вид защиты металла, когда на корпус подаётся заряд. а на дополнительную железяку – противоположный. В итоге разлагается на ионы дополнительная железяка.
Таким образом защищают от коррозии днища кораблей и подводных лодок. Какподробнее – я не знаю.
В данном случае протектор – это более активный металл. Я на самомо деле тоже за то чтобы ток подвести. Но боюсь что и в этом случае толку не будет
михаил75
draconB76
Однако есть вид защиты металла, когда на корпус подаётся заряд. а на дополнительную железяку – противоположный. В итоге разлагается на ионы дополнительная железяка.
Не путайте анодную и протекторную защиту.
ТС,праследите,где максимальное количество конденсата образуется и припаяйте туда цинковые пластины.Чем толще и длиннее,тем лучше.
anakhoret
протектор расчитывается по площади защищаемого металла.А иде цинк купить?Помница раньше гранулами видел,щас нету…
михаил75
Можно поспрашивать в магазинах,торгующих лодочными моторами,или в сервисных центрах по их ремонту. Или набрать старых карбюраторов и попытаться переплавить.
Ну или в интернетмагазинах.
button
anakhoret
А иде цинк купить?
цинк друг уже купил. если интересно, могу спросить где.
михаил75
ТС,праследите,где максимальное количество конденсата образуется и припаяйте туда цинковые пластины.Чем толще и длиннее,тем лучше.
я хочу шас провести эксперимент на балконе с двумя железками одна с цинком другая без… только вот массу бы вычислить
anakhoret
погуглить-протекторы коррозии.там где-то формула была…
button
ну вот друг гуглил у него получилось что на 5 тонн нужно меньше чем полкило цинка.
ЗЫ кстати тут еще длинна конструкции наверное влияет. а длинна там наверное 40м и 30м
кака
button
ну вот друг гуглил у него получилось что на 5 тонн нужно меньше чем полкило цинка.
Ну вот ещё погуглите такую тему, электрохимическая защита накопительных нагревателей, либо такая же для дюралевых лодок. И там и там применяют магниевые электроды. А так прынцип электохим защиты основан на разнице электрохимических потенциалов защищаемого материала и протекторного электрода. Вот здесь написано об этом, но достаточно много читать надо.
http://www.xumuk.ru/encyklopedia/2/5333.html
А по простому вы имеете защищаемый материал с определённым Э.Х. потенциалом и для его защиты должны взять протектор с более высоким Э.Х потенциалом. И вот за счёт перетекания эл. тока ( я надеюсь вы не забыли электрически их соеденить?) в этой паре протектор начнёт постепенно разрушатся вместо вашей конструкции, тем самым защищая её. И полагаю что протекторный электрод есть расходный элемент который подлежит регулярной замене.Эта защита работает и в пресной воде и просто в сырых помещениях, но ессесвенно с различной эффективностью.
P.S. Вот табличка э.х. потенциалов дабы иметь представление, там так более верхний защищает нижний и чем большая разност потенциалов тем более эффективнее защита.
Стандартные электродные потенциалы металлов, В
Магний
-2,38
Алюминий
-1,66
Марганец
-1,18
Хром
-0,91
Серебро
0,8
Цинк
-0,76
Медь
0,34
Железо
-0,44
Кадмий
-0,4
Свинец
-0,13
button
кака
И вот за счёт перетекания эл. тока ( я надеюсь вы не забыли электрически их соеденить?)
дык у меня забор 😊 он как бы единое целое 😊 точнее 2 части там
кака
button
дык у меня забор он как бы единое целое точнее 2 части там
Ну так и что, объедините забор как бы единое целое в смысле один электрод, и надо на равных(примерно) расстояниях поставить протекторные электроды естественно соединив их электрически с защищаемым забором. Ну и помните что протекторный электрод расходник и требует регулярной проверки его состояния, а на длинной защищаемой цепи они будут расходоватся по разному в зависимости от условий.
P.S. Но в приципе при использовании многоточеной установки протекторов можно и не объединять обе части.
P.P.S. Полагаю использование протекторной защиты не заменяет ещё и применение других защитных мероприятий типа покраски и подобного. А магниевые протекторы можно пошукать в сервисах по ремонту накопительных электроводонагревателей либо в мотолодках, ну и наверняка в Березняковском комбинате металургическом?.
ZavGar
Магниевые протекторы (стержни) продаются там же (в тех же фирмах), что и ТЭНы для бойлеров. Крепление и электрический контакт обеспечиваются стальным стержнем с резьбой (М4?), проходящим по оси протектора.
Остаётся просверлить (в незаметном для постороннего глаза, но очень сыром месте) в защищаемой конструкции отверстие и нарезать резьбу, а потом ввернуть протектор с контргайкой.
Защищаемую конструкцию и место крепления протектора тщательно покрасить, а сам протетор оставить голым и периодически проверять его состояние.
Нектон
Если хотите заморочиться по-научному – поищите протектор магниевый ПМ-10У. Их применяют в газопроводах для защиты от коррозии.
кака
Вот оне и цена и вроде он один всю работу сделаетю
http://www.gazovoz.com/gazovoe…agnieviy-pm-10u
зачем она нужна и какая бывает
Резервуары для нефтяных продуктов и газа должны сохраняться в герметичном состоянии – это одна из основных задач, стоящих перед специализированными предприятиями. Чтобы эксплуатируемое оборудование меньше подвергалось поломкам и авариям, каждую емкость требуется защитить. Делается это с помощью разнообразных средств антикоррозийной защиты.
Причины возникновения коррозии резервуаров
Чтобы понять, как защитить резервуар для нефти от коррозии, нужно знать, из-за чего она возникает. Это естественное явление, причины ее образования могут быть самыми разными:
- влажность в сочетании с перепадами температуры,
- агрессивность продуктов, которые хранятся в емкостях,
- покрасочная технология, которая для них применена.
Коррозия, которая проявляется на резервуарах для нефтепродуктов, при длительной эксплуатации может поражать как внутреннюю его часть, так и внешнюю. Основная причина, по которой коррозия резервуара проявляется на внешней части – это воздействие влажности и других неблагоприятных атмосферных явлений, а внутри емкость разъедается самим продуктом.
Необходимость защиты резервуара от коррозии
Чтобы противокоррозийная защита подземных резервуаров была действительно эффективной, для нее используются специальные защитные средства плюс труд квалифицированных специалистов.
Контролировать состояние защитного слоя необходимо постоянно, выявляя его недостатки и изъяны. Проверка должна проводиться как на внутреннем, так и на внешнем слое, она должна соответствовать всем тем стандартам, на основе которых проводятся специализированные работы. Основная задача защиты от коррозии – это препятствование возникновению коррозийных повреждений в любой части емкости. Обычно такие мероприятия начинаются еще на этапе проектирования, что позволяет значительно увеличить срок эксплуатации хранилища, так что для него изначально используются более толстые металлические листы и антикоррозийная обработка.
Способы защиты резервуаров от коррозии
Чтобы защитить подземную емкость, проводятся мероприятия двух типов. Такому резервуару нужен антикоррозийный слой от двух типов повреждений – почвенной (она же электрохимическая) коррозии и блуждающими токами. Для этого используют три типа защиты:
- протекторную;
- дренажную;
- почвенную.
Наружные поверхности защищаются нанесением на них антикоррозионных покрытий. Это очень эффективный метод, который требует предварительной обработки поверхности емкости. Как покрытие против коррозии используются полимерные ленты, битумно-полимерные или битумно-резиновые мастики.
Чтобы защитить днище резервуара от почвенной коррозии, перед монтажом его защищают с помощью специального гидроизоляционного слоя, а также с этой целью используется протекторная защита от коррозии. В чем она заключается? К днищу резервуара прикрепляется алюминиево-магниевые протекторы, которые находятся на расстоянии полутора метров от него. Эффективной также считается катодная защита.
Как проводится защита от коррозии
Чтобы защитить наружную и внутреннюю часть резервуаров от коррозийных повреждений, в качестве специальный антикоррозийных средств используют лакокрасочные покрытия. Мы обеспечиваем эффективную защиту поверхности стальных емкостей благодаря тому, что используем различные сочетания антикоррозийных составов. Результатом становится общая схема, которая максимально изолирует поверхность. Результат – она эффективно защищена от негативного влияния как окружающей среды, так и эксплуатационных факторов.
Выбор лакокрасочного покрытия напрямую зависит от того, насколько агрессивной является среда и как долго должна эксплуатироваться емкость. В работе по антикоррозионному предохранению наружных поверхностей резервуаров руководствуются требованиями РД 112-РСФСР-015-89 и ИСО 12944.
Протекторная защита емкости от коррозии предполагает использование гальванического метода. Применение такого способа индивидуально, он подходит не под каждый случай.
Протекторная защита резервуара от коррозии
Основывается она на том, что вся емкостная поверхность превращается в один неразрушаемый слой. К поверхности хранилища подключаются электроды металла с отрицательным зарядом, которые и выступают положительными анодами. Они же – протекторы. Чтобы создавался защитный ток, используют гальваническую пару протектор – металл резервуара. Но тут есть и отрицательный момент, который заключается в том, что по прошествии определенного промежутка времени протектор утрачивает свой отрицательный потенциал, то есть по мере его изнашивания эффективность защитного слоя утрачивается.
Наиболее эффективно такая защита работает для предотвращения коррозии локального типа. Ее можно применять как для уже используемых, так и для монтируемых резервуаров, ведь она не только предотвращает, что и замедляет те процессы, которые уже происходят.
Наиболее удачно использовать протекторную защиту в сочетании с пассивной, поскольку она увеличивает срок службы резервуара благодаря более ровному распределению тока по поверхности емкости. Даже если при монтаже и эксплуатации образовались дефекты покрытия, они компенсируются.
Подготовка резервуара к антикоррозийной защите
Перед нанесением антикоррозийной защиты необходимо осуществить подготовку поверхности. Заключается она в следующем:
- слой очищается от сварочных брызг, а также шлака;
- ее избавляют от последствий монтажа, транспортировки;
- с нее убирают следы, оставшиеся после газовой резки, разных острых кромок;
- а также очищают от разных отложений.
Особые требования применяются к местам стыковки металла и сварочным швам. Никаких наплывов и подрезов в этих местах быть не должно, все максимально плавно. Конструктивные элементы должны быть проварены.
Перед тем, как проводить противокоррозийную обработку, все поверхности обязательно обезжириваются. Для внутренних работ можно использовать лакокрасочные и металлизированные материала, а для наружных – только лакокрасочные. Но в обоих случаях срок службы должен составлять не менее 10 лет.
Защита от коррозии – Защита от ржавчины
Коррозия, в том числе ржавчина, является глобальной проблемой, которой уделяется все больше внимания. В условиях устаревающей инфраструктуры риск возрастает и угрожает жизни и имуществу. Слишком часто проблемы игнорируются до тех пор, пока не становится слишком поздно.
Коррозия имеет два аспекта: предотвращение и ремонт. Важным фактором является то, что коррозия необратима… она всегда приводит к ослаблению конструкции. В то время как профилактика работает в будущем, ремонт является наиболее насущной проблемой.
Как ArmorThane предотвращает коррозию
Коррозия — это повреждение поверхностей и конструкций, вызванное реакцией на ряд элементов и условий. Напыляемые покрытия ArmorThane образуют защитный барьер, который блокирует эти вредные среды, поэтому коррозия не может начаться:
- Вода, дождь, влага
- Морская вода, соленый воздух
- Химические вещества, кислоты, газы
- Истирание и эрозия
- Высокоскоростной поток
- Напряжение, Давление
- Микроорганизмы
- Ухудшение возраста
- Электролиз, Электрический дисбаланс
Коррозионностойкие сплавы и материалы с ингибиторами замедляют повреждение, но недолговечны. По мере того как защитные поверхности стираются в результате износа или физического повреждения, обнажаются лежащие под ними металлы.
Ржавчина является наиболее распространенным результатом и относится к коррозии железа и его сплавов, таких как сталь. Со временем в присутствии кислорода и воды прочные железные конструкции полностью разрушатся. По мере того, как металлическая поверхность стирается и ржавеет, обнажается новый металл; цикл повторяется, оставляя слои только хлопьев. Единственным решением является блокировка этих элементов путем покрытия полимерами ArmorThane до того, как начнется коррозия.
Почему ArmorThane защищает лучше
Краски и лаки обычно используются для покрытия поверхностей, но они обладают очень ограниченными защитными свойствами и со временем ухудшаются без регулярного ухода. Эти тонкие пленки плохо стареют и могут легко трескаться и отслаиваться, оставляя открытые поверхности.
Стандарты толщины поверхностных покрытий устанавливаются поставщиками и спецификациями клиентов, но краски и грунтовки обычно тестируются при толщине 10 мил или меньше. Напыляемые полимеры, естественно, толще, что в двадцать раз превышает толщину промышленных красок, в зависимости от проекта.
Чистые и гибридные полимочевины и полиуретаны ArmorThane были разработаны, чтобы противостоять истиранию, сильным ударам, экстремальным температурам, химическим веществам, воде и многим другим средам для широкого спектра применений. Эти полимеры выдерживают давление и растяжение, не трескаясь, даже при смещении или вибрации основной конструкции. Непроницаемая природа этих материалов создает бесшовный, герметичный барьер. В качестве бонуса аэрозольное покрытие покрывает сложные формы и легко транспортируется на рабочие площадки. Эти факторы делают долгосрочную ожидаемую продолжительность жизни очень рентабельной.
Действия по устранению ржавчины
Существуют разногласия по поводу удаления ржавчины. Одна школа говорит, что ржавчина может быть лишена кислорода и влаги, чтобы остановить ржавчину. Другая мысль заключается в том, что это практически невозможно сделать. Противники указывают на следующие проблемы:
- Ржавчина занимает больше объема, чем исходный металл, вызывая расширение, особенно в окружающем бетоне. Известно, что это состояние вызывает раздвигание соседних суставов. Результатом являются трещины, которые способствуют более быстрому износу и повреждению.
- Многие из методов, направленных на ремонт или предотвращение ржавчины, часто не работают в швах, отверстиях и соединениях, где есть пробелы в обработке.
Они обеспечивают защиту в течение ограниченного времени.
- Если поверхности не полностью загерметизированы или повреждены, такие элементы, как кислород и влага, проникают внутрь.
Согласитесь, что маскировка не работает при ремонте. Простое покрытие ржавчиной может улучшить внешний вид и замедлить износ, но все, что питает ржавчину, будет продолжать разъедать, часто незамеченным. Ослабленное состояние может привести к коллапсу.
Как минимум необходимо удалить рыхлую ржавчину. Существует несколько способов сделать это с помощью абразивно-струйной обработки/шлифовки, кислот, электролиза, преобразователей ржавчины и других методов борьбы с ржавчиной.
Далее необходимо подготовить поверхность. Если покрытие не держится, зазоры вызовут проблемы. Металл должен быть чистым и обезжиренным. Также может потребоваться грунтовка или шероховатость поверхности. Тщательное покрытие полимером ArmorThane — лучший способ создать бесшовный барьер для предотвращения проникновения кислорода и влаги.
Выбор наилучшего полимера
Все продукты ArmorThane прочны и создают герметичный барьер. Однако были разработаны различные полимеры для улучшения защитных свойств в зависимости от поверхности, на которую наносится покрытие, и окружающей среды, такой как атмосферные и промышленные загрязнения, стресс и т. д.
Отрасли, получающие выгоду от полимерных покрытий затраты на коррозию составляют 2,2 триллиона долларов и 3% или более мирового ВВП. Ключевые отрасли, затронутые проблемой, включают:
- Трубопроводы для газа и жидкости
- Переработка нефти
- Автомобильные мосты
- Транспорт
- Морской транспорт, Судоходство
- Питьевая вода
- Канализационные системы
- Производство, Производство
- Пищевая промышленность
- Химические производства
- Хранилище отходов
- Коммунальные услуги
Примеры защиты от коррозии и окисления
Суда и морская техника.
Транспортные контейнеры, подвергающиеся воздействию суровых условий.
Стальные мосты и другая открытая инфраструктура.
Алюминиевые и металлические кровли.
Защитные покрытия для защиты от коррозии
- Ресурсы
- Что такое коррозия
- Защитные покрытия для защиты от коррозии
Промышленные, коммерческие и архитектурные рынки в значительной степени полагаются на покрытия для защиты активов. В общем смысле под покрытиями понимают тонкий слой твердого материала на поверхности, обеспечивающий улучшенные защитные, декоративные или функциональные свойства. Более конкретно, они представляют собой жидкую, сжижаемую или мастичную композицию, которая после нанесения на поверхность превращается в твердую защитную, декоративную или функциональную липкую пленку. Защитные покрытия наносятся на поверхность для защиты подложки от коррозии. Эффективным способом защиты металла от коррозии является физическая изоляция подложки от окружающей среды путем нанесения защитных покрытий.
Покрытия защищают от коррозии одним из следующих способов: они блокируют соединение элементов, необходимых для начала процесса коррозии, активно предотвращают возникновение электрохимической реакции или направляют процесс коррозии в направлении, которое не нанесет вреда имуществу .
См. также учебный центр по защитным покрытиям
Краткая информация
Типы защиты покрытия включают:
- Барьер – защищает, предотвращая контакт воды, кислорода и электролитов с металлом под ним
- Ингибитор — Покрытия, содержащие химические вещества, препятствующие коррозии
- Жертвенный — Наносятся тонкие металлические слои, которые имеют более низкие значения электродного потенциала или имеют более высокие уровни в электрохимическом ряду
- Комбинация
Материалы, обычно используемые в защитных покрытиях:
- полимеры, эпоксидные смолы и полиуретаны для неметаллических покрытий
- цинк, алюминий и хром для металлических покрытий
Нанесение
Покрытия, в том числе краски, могут быть:
- напылением
- сварной
- с покрытием или
- наносится с помощью ручных инструментов (в зависимости от поверхности, окружающей среды и целей применения)
Процесс нанесения защитных покрытий включает:
- подготовку поверхности
- нанесение грунтовки
- полное покрытие
- использование герметика
Информацию, относящуюся к «Проверке покрытий», см. в разделе «Измерение и проверка»
Курсы и сертификаты
Математика для Профессиональных покрытий. Покрытия в сочетании с катодной защитой
Коррозия под изоляцией
Применение промышленных покрытий
Сертифицированный специалист по нанесению покрытий
Борьба с коррозией в индустрии парков развлечений
Основания для парков развлечений Micro-Credential
Обучение специалистов по нанесению покрытий на трубопроводы
Технология морских покрытий – виртуально и лично
Основы защитного покрытия (0103)
Программы аккредитации подрядчиков по покраске QP
Статьи
Экипаж гибких покрытий побеждает тепло на Австралийском сталелитейном заводе
Полный комплект: новое покрытие для защиты резервуаров на химическом заводе
Подготовка к совершенству: стратегии для кровельных подрядчиков
Неутомимая бригада завершает нанесение силиконового покрытия на крышу
Подготовка к совершенству: стратегии поверхности для бетонных покрытий
Проблемы и возможности для подрядчиков по нанесению покрытий, SPF
Покрытие на мосту Трайбека в Нью-Йорке и за его пределами
Советы по нанесению покрытий на строительных площадках в 2020 г.
Систематический подход к анализу сбоев покрытия
Nano неквалифицированное решение для покрытия для оффшорных среда
Советы по работе с промышленными покрытиями, Composites
Веб-трансляции
Систематический подход к анализу сбоев покрытия
Отчеты
Publication 6G186 666. -2010-SG, Подготовка поверхности стальных оснований, загрязненных растворимыми солями, перед нанесением покрытия
NACE 6G197/SSPC-TU 2-1997, Проектирование, монтаж и техническое обслуживание систем покрытий для бетона, используемого во вторичной защитной оболочке
Публикация NACE 02103-2003-SG, Жидкие покрытия для высокотемпературных атмосферных условий
Документы конференции
Обновленная информация о коррозионных характеристиках покрытий CBPC в агрессивной среде мостов Анализ покрытий трубопроводов: обзорное исследование
Сравнение преимуществ экологически чистых съемных покрытий с традиционными продуктами
Низкотемпературные механические свойства пассивных огнезащитных покрытий
Эффективность ремонтных покрытий, наносимых на ржавые стальные поверхности
Испытания покрытий для эксплуатации в морских условиях
Новые достижения в области эпоксидных защитных покрытий
Расчет ожидаемого срока службы и затрат на техническое обслуживание и новое строительство защитных покрытий
Покрытия Дополнительные ресурсы
90Pro Журнал MaterialsPerformance. com: содержит специальный раздел статей о покрытиях и футеровке
MPI (Институт мастеров живописи) Утвержденные краски и покрытия
MPI (Институт мастеров-маляров) Руководства по спецификациям окраски
Поиск сертифицированных подрядчиков SSPC QP
Стандарты
Пакет стандартов подготовки поверхностей швов NACE/SSPC (NACE № 1, 2, 3, 4, 5, 6, 8)
Выбор краски и покрытий
Нанесение краски
ANSI/NACE № 13/SSPC-ASC-1-2016, Квалификация и сертификация специалиста по нанесению промышленных покрытий и футеровки
SP0108, Борьба с коррозией морских конструкций с помощью защитных покрытий
SP0892-2007-SG (ранее RP0892), Покрытия и футеровки поверх бетона для химического погружения и локализации до 30 мил)
TM0104-2004, Оценка системы покрытия резервуаров для балластных вод морских платформ
NACE № 6/SSPC-SP 13-2018, Подготовка поверхности бетона
Металлические и керамические термонапыляемые покрытия для нефтегазодобывающего оборудования
Комитеты по разработке стандартов
AMPP SC 02 Наружные покрытия – атмосферные
Разрабатывает и поддерживает стандарты, руководства и отчеты для покрытий, используемых в средах, подверженных воздействию атмосферы.
AMPP SC 03 Внешние покрытия – заглубленные и погруженные
Разрабатывает и поддерживает стандарты, руководства и отчеты для наружных покрытий материалов, оборудования и конструкций, находящихся в непосредственном контакте с соленой водой, пресной водой или почвой.
AMPP SC 04 Футеровки и внутренние покрытия
Разрабатывает и поддерживает стандарты, руководства и отчеты для футеровок и внутренних покрытий, обычно используемых в специализированных внутренних средах, таких как стальные резервуары, трубопроводы и сосуды, для защиты от коррозии и/или химического воздействия.
AMPP SC 05 Подготовка поверхности
Разрабатывает и поддерживает стандарты, руководства и отчеты по подготовке поверхностей для повышения адгезии к покрытиям и облицовке.
AMPP SC 12 Бетонная инфраструктура
Разрабатывает и поддерживает стандарты, руководства и отчеты для распространения информации об эффективности различных систем защиты от коррозии для строительства и восстановления железобетонной инфраструктуры, а также о методологии оценки армированных и предварительно -напряженные конструкции.
AMPP SC 23 Нанесение, техническое обслуживание и проверка систем покрытий
Разрабатывает и поддерживает стандарты, руководства и отчеты, связанные с процессами и процедурами нанесения, технического обслуживания и контроля.
Кроме того, интересующие технические сообщества AMPP — подготовка поверхности, атмосферные покрытия, бетон, погружение и подземные работы, футеровка (технический подкомитет по покрытиям)
BONDERITE® — решения для защиты от коррозии
Временная защита от коррозии
Коррозия вновь изготовленных изделий или даже во время производства может оказать серьезное влияние на эффективность вашего бизнеса.
Для предотвращения этого необходимо использовать защиту от коррозии, которая образует барьер между металлической подложкой и агрессивными элементами окружающей среды (например, кислородом, влажностью, солями и температурой). Временная защита от коррозии может также выполнять другие функции, такие как смазка или очистка.
Временная защита от коррозии Объяснение
Коррозия — это постепенное разрушение материалов (в основном металлов) по мере их преобразования в результате химической или электрохимической реакции с окружающей средой в более химически стабильную форму.
Коррозия может проявляться во многих формах: наиболее известной является коричневая ржавчина на стали. На этот процесс сильно влияют условия окружающей среды, такие как кислород, влажность и температура. Поскольку коррозия представляет собой постепенный процесс, она протекает в несколько фаз.
Когда присутствуют «правильные» условия для коррозии, незащищенная стальная поверхность начнет проявлять мгновенную ржавчину в течение нескольких секунд. Это может произойти на линии предварительной обработки между последующими этапами очистки и обработки поверхности. Если обстоятельства не изменятся, коррозия будет продолжаться до полного износа объекта. Для предотвращения коррозии необходимо применять защиту от коррозии; это предотвращает протекание химических и электрохимических процессов, образуя барьер между металлической подложкой и элементами окружающей среды, вызывающими коррозию.
Существует две основные категории защиты от коррозии: постоянная защита от коррозии и временная защита от коррозии. В первую группу входят все методы защиты подложки, по крайней мере, в течение ее предполагаемого срока службы. Это может быть покраска, порошковое покрытие, анодирование (в случае алюминия) и цинкование. Ко второй группе относятся все технологии, обеспечивающие временный защитный слой в процессе производства или транспортировки и складирования.
Области применения временной защиты от коррозии
Межоперационная защита от коррозии (защита в процессе эксплуатации)
Следует избегать мгновенной ржавчины после очистки металлических деталей в производственном процессе. Для этого необходимо учитывать ряд переменных, таких как время между различными этапами, рН на предыдущем этапе, методы нанесения (погружение, распыление, вручную), возможность удаления протектора на следующем этапе, качество воды и скоро. Команда технической поддержки Henkel может работать с клиентами, чтобы помочь найти правильное решение, которое идеально подходит для применения.
Хранение / складирование
Здесь основное внимание уделяется требуемому времени защиты и условиям окружающей среды (часто температуре и влажности). В портфолио BONDERITE есть несколько средств защиты от коррозии со временем защиты от нескольких часов до шести месяцев.
Транспортировка
Условия окружающей среды, в которых хранятся продукты, также имеют решающее значение для временной защиты от коррозии. Проблема, однако, заключается в том, что эти условия часто меняются во время перевозки товаров. Влажность, количество соли (особенно для товаров, перевозимых морем), температура и т. д. могут сильно различаться в течение одной поездки.
BONDERITE ® предлагает полный ассортимент временных средств защиты от коррозии, которые могут обеспечить надежную защиту в этих изменяющихся условиях и совместимость с продуктами защиты от коррозии, такими как технологии VCI (летучий ингибитор коррозии).
BONDERITE
® – Технологии временной защиты от коррозии Компания HENKEL поставляет широкий ассортимент продуктов для временной защиты от коррозии BONDERITE ® . Каждый предназначен для определенной функции; вместе они предлагают клиентам защиту от коррозии, в которой они нуждаются, на протяжении всей обработки, а также во время транспортировки и хранения, чтобы гарантировать, что продукты могут быть доставлены конечным пользователям в идеальном состоянии.
Типы продуктов включают:
- На водной основе – либо на водной основе, либо в виде масляно-водной эмульсии
- На масляной основе поставляется как:
- Защитное масло
- Защитное масло с обезвоживающим средством
- Обезвоживающее средство с защитным маслом
- Обезвоживающий агент-очиститель на основе растворителя
BONDERITE ® Продукты Henkel обеспечивают временную защиту от коррозии почти всех металлических изделий со временем защиты от нескольких часов до шести месяцев. Для получения дополнительной информации и обсуждения ваших конкретных потребностей, пожалуйста, свяжитесь с нашим отделом продаж.
Преимущества BONDERITE ® Временная защита от коррозии
Процессы нанесения покрытий BONDERITE ® обеспечивают выдающиеся характеристики, поскольку они являются инновационными, надежными и устойчивыми. Они обеспечивают клиентам производственные преимущества за счет упрощения процессов нанесения покрытий и повышения коррозионной стойкости. Это позволяет клиентам получать продукцию с более высокой ценностью, отвечая при этом строгим экологическим требованиям сегодняшнего и завтрашнего дня.
Преимущества временной защиты от коррозии BONDERITE®:- Эффективная защита от коррозии
- Продукты с низким содержанием летучих органических соединений или без них (летучие органические соединения)
- Невоспламеняющиеся продукты или продукты с высокой температурой воспламенения
- Ассортимент защитных средств на водной основе
- Экспертиза в области защиты от коррозии и последующих процессов, таких как склеивание, герметизация и покраска, все из одних рук
- Глобальное присутствие Henkel
- Высочайшее качество и отличный сервис
- Техническое обслуживание на местах доступно по всему миру
pdf ( 13,3 МБ )
Свяжитесь с нами
Да №
Наверх
Защита от коррозии – SteelConstruction.

Экономичная защита от коррозии стальных конструкций не вызовет затруднений для обычных применений и сред, если с самого начала будут определены факторы, влияющие на долговечность.
Многие стальные конструкции успешно эксплуатируются в течение многих лет даже в неблагоприятных условиях. Первое крупное железное сооружение, мост в Коулбрукдейле, Великобритания, просуществовало более 200 лет, в то время как о железнодорожном мосту Форт, которому более 100 лет, ходят легенды. Сегодня доступны современные долговечные защитные покрытия, которые при правильном использовании позволяют увеличить интервалы обслуживания и повысить производительность.
Ключ к успеху заключается в распознавании коррозионной активности окружающей среды, воздействию которой будет подвергаться конструкция, и в определении четких и подходящих спецификаций покрытия. Там, где сталь находится в сухом отапливаемом помещении, риск коррозии незначителен, и защитное покрытие не требуется. И наоборот, стальная конструкция, подвергающаяся воздействию агрессивной среды, должна быть защищена высокоэффективной обработкой и, возможно, должна быть спроектирована с учетом технического обслуживания, если требуется продление срока службы.
Оптимальная защитная обработка, которая сочетает в себе соответствующую подготовку поверхности, подходящие материалы покрытия, требуемую долговечность и минимальную стоимость, достигается с помощью современной технологии обработки поверхности.
Содержание
- 1 Коррозия конструкционной стали
- 2 Влияние конструкции на коррозию
- 3 Подготовка поверхности
- 4 Лакокрасочные покрытия
- 5 Металлические покрытия
- 5.1 Горячее цинкование
- 5.2 Металлические покрытия, полученные термическим напылением
- 6 Соответствующие спецификации
- 7 Инспекция и контроль качества
- 8 Каталожные номера
- 9 Ресурсы
- 10 Дальнейшее чтение
- 11 См. также
- 12 Внешние ссылки
- 13 CPD
[вверх]Коррозия конструкционной стали
Основная статья: Коррозия конструкционной стали
Схематическое изображение механизма коррозии стали
Коррозия конструкционной стали представляет собой электрохимический процесс, требующий одновременного присутствия влаги и кислорода. При отсутствии того и другого коррозия не возникает. По сути, железо в стали окисляется с образованием ржавчины, которая занимает примерно в 6 раз больше объема исходного материала, потребляемого в процессе. Здесь показан общий процесс коррозии.
Наряду с общей коррозией могут возникать различные виды локальной коррозии; биметаллическая коррозия, точечная коррозия и щелевая коррозия. Однако они, как правило, не имеют существенного значения для металлоконструкций.
Скорость, с которой развивается процесс коррозии, зависит от ряда факторов, связанных с «микроклиматом», непосредственно окружающим конструкцию, в основном от времени увлажнения и уровня загрязнения атмосферы. Из-за изменений в атмосферных условиях данные о скорости коррозии не могут быть обобщены. Тем не менее, среды можно классифицировать в широком смысле, и соответствующие измеренные скорости коррозии стали дают полезный показатель вероятной скорости коррозии. Дополнительную информацию можно найти в BS EN ISO 129. 44-2 [1] и BS EN ISO 9223 [2] .
Категория коррозионной активности | Низкоуглеродистая сталь Потеря толщины (мкм) a | Примеры типичных сред (только для справки) | |
---|---|---|---|
Внешний вид | Интерьер | ||
C1 очень низкий | ≤ 1,3 | – | Отапливаемые здания с чистой атмосферой, напр. офисы, магазины, школы, гостиницы |
C2 низкий | > 1,3 до 25 | Атмосферы с низким уровнем загрязнения: преимущественно сельские районы | Неотапливаемые здания, в которых может образовываться конденсат, напр. склады, спортивные залы |
C3 средний | > 25 до 50 | Городская и промышленная атмосфера, умеренное загрязнение двуокисью серы; прибрежная зона с низкой соленостью | Производственные помещения с повышенной влажностью и некоторым загрязнением воздуха, напр.![]() |
C4 высокий | > от 50 до 80 | Промышленные зоны и прибрежные районы с умеренным уровнем засоления | Химические заводы, плавательные бассейны, прибрежные суда и верфи |
C5 очень высокий | > 80 до 200 | Промышленные зоны с повышенной влажностью и агрессивной атмосферой и прибрежные зоны с повышенной соленостью | Здания или зоны с почти постоянной конденсацией и высоким уровнем загрязнения |
CX экстремальный | > 200 до 700 | Морские районы с высокой соленостью и промышленные районы с повышенной влажностью и агрессивной атмосферой, а также субтропические и тропические атмосферы | Промышленные зоны с повышенной влажностью и агрессивной атмосферой |
Примечания:
- 1 мкм (1 микрон) = 0,001 мм
- a Значения потери толщины даны после первого года воздействия.
Убытки могут уменьшиться в последующие годы.
- Значения потерь, используемые для категорий коррозионной активности, идентичны значениям, указанным в BS EN ISO 9223 [2] .
[вверх] Влияние конструкции на коррозию
Основная статья: Влияние конструкции на коррозию
Конструкция и детали конструкции могут влиять на долговечность любого нанесенного на нее защитного покрытия. Конструкции, спроектированные с большим количеством мелких конструктивных элементов и крепежных элементов, труднее защитить, чем конструкции с большими плоскими поверхностями. Ключевые вопросы, которые необходимо рассмотреть, включают:
- Доступ для нанесения покрытия и обслуживания
- Избегание ловушек для влаги и мусора
- Предотвращение или герметизация щелей
- Дренаж и вентиляция для минимизации времени увлажнения
- Тщательное управление контактом с другими материалами
Общие рекомендации по предотвращению коррозии за счет надлежащей детализации конструкции можно найти в BS EN ISO 12944-3 [3] , а также некоторые типичные рекомендации и запреты для стальных каркасов. здания показаны ниже.
Примеры детализации зданий
[вверх]Подготовка поверхности
Основная статья: Подготовка поверхности
Стальная балка, выходящая из установки автоматической пескоструйной очистки
Подготовка поверхности — это обязательный первый этап обработки стальной подложки перед нанесением любого покрытия, который обычно считается наиболее важным фактором, влияющим на общий успех защиты от коррозии система.
Характеристики покрытия в значительной степени зависят от его способности должным образом прилипать к материалу подложки. Исходное состояние поверхности стали может варьироваться в зависимости от количества остаточной прокатной окалины и степени начальной ржавчины. Однако, как правило, это неудовлетворительная основа для нанесения современных высокоэффективных защитных покрытий. Существует ряд методов подготовки и степеней чистоты, но, безусловно, наиболее важным и важным методом, используемым для тщательной очистки поверхностей от прокатной окалины и ржавчины, является абразивоструйная очистка. Стандартные степени чистоты для абразивоструйной очистки в соответствии с ISO 8501-1 [4] являются:
- Sa 1 – Легкая струйная очистка
- Sa 2 – Тщательная пескоструйная очистка
- Sa 2½ – Очень тщательная пескоструйная очистка
- Sa 3 – Дробеструйная очистка до визуально чистой стали
Ручная пескоструйная очистка
(Видео предоставлено Corrodere/MPI)
Процесс подготовки поверхности не только очищает сталь, но также обеспечивает подходящий профиль и амплитуду поверхности для нанесения защитного покрытия. Толстослойные лакокрасочные покрытия и металлические покрытия, полученные термическим напылением, требуют грубого угловатого профиля поверхности для обеспечения механического ключа. Это достигается за счет использования абразивных материалов. Дробеструйные абразивы используются для тонкопленочных лакокрасочных покрытий, таких как заводские грунтовки. Разница между дробью и дробью и соответствующими профилями поверхности показана ниже на трехмерных диаграммах, полученных с помощью оборудования для бесконтактной характеристики поверхности.
Абразивная дробь
Зернистый абразив
После абразивоструйной очистки можно проверить дефекты поверхности и изменения поверхности, возникшие в процессе изготовления, например, сварка. Некоторые поверхностные дефекты, появившиеся во время первоначальной обработки стали, могут не оказывать отрицательного влияния на характеристики покрытия в процессе эксплуатации, особенно для конструкций в категориях окружающей среды с относительно низким уровнем риска. Однако, в зависимости от конкретных требований к конструкции, может потребоваться дополнительная обработка поверхности для удаления поверхностных дефектов на сварных швах и кромках срезов, а также растворимых солей для обеспечения приемлемого состояния поверхности для окраски.
[вверх]Лакокрасочные покрытия
Основная статья: Лакокрасочные покрытия
Поперечное сечение многослойной системы окраски
Лакокрасочные покрытия для стальных конструкций разрабатывались на протяжении многих лет в соответствии с промышленным законодательством по охране окружающей среды и в ответ на требования владельцев мостов и сооружений о повышении долговечности. Краска состоит из пигмента, диспергированного в связующем и растворенного в растворителе. Наиболее распространены методы классификации красок либо по их пигментации, либо по типу связующего вещества.
Современная система окраски обычно включает последовательное нанесение красок или, альтернативно, красок, наносимых поверх металлических покрытий, для образования «дуплексной» системы покрытия. Защитные лакокрасочные системы обычно состоят из грунтовки, промежуточных/сборочных слоев и финишных слоев. Каждый «слой» покрытия в любой защитной системе выполняет определенную функцию, и различные типы наносятся в определенной последовательности: грунтовка, промежуточные/сборочные слои в цеху и, наконец, финишное покрытие (или верхнее покрытие) либо в цехе. или на месте.
Предварительные грунтовки используются на металлоконструкциях сразу после пескоструйной очистки, чтобы сохранить реактивно очищенную поверхность в состоянии отсутствия ржавчины в процессе изготовления до тех пор, пока не будет проведена окончательная покраска. Эти типы грунтовки не используются перед нанесением термического напыления покрытий.
Способ нанесения систем окраски и условия нанесения оказывают существенное влияние на качество и долговечность покрытия. Стандартные методы, используемые для нанесения красок на стальные конструкции, включают нанесение кистью, валиком, обычным воздушным распылением и безвоздушным распылением/электростатическим безвоздушным распылением.
Безвоздушное распыление стало наиболее часто используемым методом нанесения лакокрасочных покрытий на стальные конструкции в контролируемых заводских условиях. нанесение кистью и валиком чаще используется для нанесения на месте, хотя также используются методы распыления. Покрытия «полосатые», наносимые на кромки и острые углы, обычно наносятся кистью.
- Безвоздушное распыление на стальные балки моста
Основными условиями, влияющими на нанесение лакокрасочных покрытий, являются температура стали и окружающей среды и влажность. Их легче контролировать в условиях магазина, чем на месте. С появлением современных высокоэффективных покрытий правильное нанесение становится все более важным для достижения намеченных характеристик. Промышленность признала это и ввела схему обучения и сертификации специалистов по нанесению красок (ICATS — Схема обучения специалистов по нанесению покрытий). Регистрация ICATS (или эквивалентная схема, например, Trainthepainter) впоследствии стала обязательным требованием для работы на мостах Highways England и сооружениях Network Rail.
Безвоздушное распыление краски
(Видео предоставлено Corrodere/MPI)
[вверх]Металлические покрытия
Основная статья: Металлические покрытия
Существует четыре широко используемых метода нанесения металлического покрытия на стальные поверхности. Это горячее цинкование, термическое напыление, гальваническое покрытие и шерардизация. Последние два процесса не используются для металлоконструкций, но используются для фитингов, крепежных изделий и других мелких предметов. В целом защита от коррозии, обеспечиваемая металлическими покрытиями, в значительной степени зависит от выбора металла покрытия и его толщины и не сильно зависит от способа нанесения.
[вверх]Горячее цинкование
Стальные элементы извлекаются из обычной ванны для горячего цинкования
Горячее цинкование представляет собой процесс, который включает погружение стального компонента, подлежащего покрытию, в ванну с расплавленным цинком (при температуре около 450 °C) после травления и флюсования, а затем отзыв его. Погруженные поверхности равномерно покрыты цинковым сплавом и слоями цинка, образующими металлургическую связь с подложкой. Полученное покрытие является прочным, прочным, устойчивым к истиранию и обеспечивает катодную (жертвенную) защиту любых небольших поврежденных участков на стальной основе. Типичная минимальная средняя толщина покрытия для стальных конструкций составляет 85 мкм.
Поперечное сечение горячеоцинкованного покрытия
[вверх] Металлические покрытия термическим напылением
Поперечный разрез термически напыленного алюминиевого покрытия
Термически напыленные покрытия из цинка, алюминия и цинко-алюминиевых сплавов могут обеспечить долговременную защиту от коррозии стальных конструкций, подвергающихся воздействию агрессивных сред. Металл в виде порошка или проволоки подается через специальный пистолет-распылитель, содержащий источник тепла, которым может быть кислородное пламя или электрическая дуга. Капли расплавленного металла выдуваются струей сжатого воздуха на предварительно очищенную пескоструйным методом стальную поверхность. Легирования не происходит, покрытие состоит из перекрывающихся пластин металла и является пористым. Затем поры герметизируются путем нанесения тонкого органического покрытия, проникающего вглубь поверхности. Важно, чтобы герметик полностью заполнил все поры в металлическом покрытии.
Адгезия напыленных металлических покрытий к стальным поверхностям считается в основном механической по своей природе. Поэтому необходимо наносить покрытие на чистую шероховатую поверхность, и обычно рекомендуется пескоструйная очистка крупнозернистым абразивом.
Дуговое напыление
(Видео предоставлено Metallisation)
[вверх]Подходящие спецификации
Основная статья: Подходящие спецификации
Общий успех схемы защитного покрытия начинается с хорошо подготовленной спецификации. Это важный документ, предназначенный для предоставления подрядчику четких и точных инструкций о том, что и как следует делать. Спецификация должна быть составлена кем-то с соответствующими техническими знаниями, и в ней должно быть ясно, что требуется, а что является практичным и достижимым. Он должен быть написан в логической последовательности, начиная с подготовки поверхности, проходя через каждую наносимую краску или металлическое покрытие и, наконец, касаясь конкретных областей, например. сварные швы. Он также должен быть максимально кратким, согласующимся с предоставлением всей необходимой информации. Наиболее важными элементами спецификации являются следующие:
- Обработка металла для удаления острых краев, выступов и т. д., а также стальных загрязнений.
- Метод подготовки поверхности и требуемый стандарт.
- Максимальный интервал между подготовкой поверхности и последующим грунтованием или металлическим покрытием.
- Типы используемых красок или металлических покрытий, поддерживаемые соответствующими стандартами.
- Используемый(е) метод(ы) применения.
- Количество наносимых слоев и интервал между слоями.
- Толщина влажной и сухой пленки для каждого слоя.
- Место нанесения каждого слоя (т.
е. магазины или строительная площадка) и требуемые условия нанесения с точки зрения температуры, влажности и т. д.
- Детали для обработки сварных швов, болтовых соединений и т. д.
- Процедуры устранения повреждений и т. д.
Большинство стальных мостов защищены в соответствии с требованиями Highways England и стандартными спецификациями Network Rail. Для других мостов могут быть указаны альтернативные системы и методы покрытия, но должны применяться те же стандарты и принципы надлежащей практики покрытия.
[вверх]Инспекция и контроль качества
Основная статья: Инспекция и контроль качества
Ассортимент приборов для испытаний и контроля
Контроль является неотъемлемой частью контроля качества. Его целью является проверка соблюдения требований спецификации и предоставление клиенту отчета с надлежащими записями. Одним из самых больших преимуществ для инспектора по покрытиям является четкая письменная спецификация, на которую можно без сомнений ссылаться.
Назначение стороннего инспектора с соответствующей квалификацией следует рассматривать как инвестиции в качество, а не просто как дополнительные расходы. Проверка процессов, процедур и материалов, необходимых для нанесения защитного покрытия на стальные конструкции, имеет жизненно важное значение, поскольку серьезную ошибку даже в одной операции нельзя легко обнаружить после выполнения следующей операции, и, если ее не исправить немедленно, это может значительно снизить ожидаемые срок службы до первого технического обслуживания.
[наверх]Ссылки
- ↑ 1.0 1.1 BS EN ISO 12944-2: 2017, Краски и лаки. Защита стальных конструкций от коррозии защитными системами окраски. Часть 2. Классификация сред, BSI
- ↑ 2.0 2.1 BS EN ISO 9223: 2012, Коррозия металлов и сплавов. Коррозионная активность атмосферы. Классификация, определение и оценка BSI
- ↑ BS EN ISO 12944-3: 2017, Краски и лаки. Защита стальных конструкций от коррозии с помощью защитных систем окраски.
Часть 3. Вопросы проектирования, BSI
- ↑ BS EN ISO 8501-1: 2007 Подготовка стальных поверхностей перед нанесением красок и сопутствующих продуктов. Визуальная оценка чистоты поверхности. Степени ржавчины и степени подготовки стальных поверхностей без покрытия и поверхностей после полного удаления предыдущих покрытий, ISO
Ресурсы
- Хенди, Ч.Р.; Айлс, округ Колумбия (2015) Группа стальных мостов: Руководящие указания по передовой практике строительства стальных мостов (6-й выпуск). (стр. 185). SCI
- Руководство 8.01 Подготовка к эффективной защите от коррозии
- Руководство 8.02 Защитная обработка крепежных изделий
- Руководство 8.03 Горячее цинкование погружением
- Руководство 8.04 Металлические покрытия, полученные термическим напылением
- Руководство 8.05 Высокоэффективные лакокрасочные покрытия
- Руководство 8.06 Проверка подготовки поверхности и обработки покрытий
- Стальные здания, 2003 г.
, Британская ассоциация строительных металлоконструкций, ООО.
- Глава 12 – Защита от коррозии
[наверх]Дополнительная литература
- Д.Дикон и Р.Хадсон (2012 г.), Руководство по проектированию металлоконструкций (7-е издание), глава 36 – Коррозия и предотвращение коррозии, Институт стальных конструкций.
- Д.А. Bayliss & D.H.Deacon (2002), Steelwork Corrosion Control (2-е издание), Spon Press
[вверху] См. также
- Коррозия конструкционной стали
- Влияние конструкции на коррозию
- Подготовка поверхности
- Лакокрасочные покрытия
- Стандартные системы защиты зданий от коррозии
- Металлические покрытия
- Соответствующие спецификации
- Инспекция и контроль качества
[наверх]Внешние ссылки
- Британская федерация покрытий
- Ассоциация гальванистов
- Ассоциация исследования красок
- Ассоциация термического напыления и обработки поверхностей
- ИКАТС
- Корродор
- Защита от коррозии
Высокотемпературные коррозионно-стойкие покрытия
Для коррозионно-стойких покрытий компания DECC использует как барьерные, так и защитные типы инженерных покрытий. Эти покрытия прилипают к металлической подложке и обеспечивают дополнительную защиту от соли, химикатов и высокотемпературных агрессивных сред.
Преимущества антикоррозионных покрытий
icon-dashboard
Экономия топлива
увеличивает экономию топлива при применении к определенным автомобильным деталям
. увеличенный срок службы детали
icon-shield
Стойкость
Устойчивость к агрессивным химическим веществам и экстремальным температурам
icon-знак доллара
Экономия средств
Снижение затрат на техническое обслуживание, поскольку срок службы деталей увеличивается
Барьерные покрытия создают однородную пленку, которая предотвращает проникновение внешних элементов на подложку. Другими словами, в барьерном покрытии используется тонкий слой пластичной смолы, который действует как экран, не позволяющий внешним факторам причинить вред детали. Каждое барьерное покрытие содержит защитный слой из пластиковой смолы, который затем соединяется со слоем наполнителя для решения конкретной проблемы. Например, в краске для стен используется красящая добавка, смешанная с пластиковой смолой, и ее можно рассматривать как барьерное покрытие, поскольку она обеспечивает защиту гипсокартона, обеспечивая при этом косметическую привлекательность.
Защитные покрытия содержат определенные элементы, такие как алюминий или цинк, которые защитно окисляются, чтобы гарантировать, что подложка не подвержена коррозии. Покрытия, устойчивые к солевому туману, некоторые из которых выдерживают более 1000 часов, также могут предотвратить гальваническую коррозию при контакте разнородных металлов друг с другом. Жертвенные покрытия, по сути, обманывают ржавчину, заставляя ее разъедать покрытие, а не металлические слои под ним. Это происходит потому, что алюминий или, в некоторых случаях, цинк добавляют в эпоксидную смолу в процессе производства покрытия.
На протяжении более 50 лет компания DECC усердно работала над тем, чтобы предоставить нашим клиентам самые надежные варианты нанесения защитного покрытия. Мы стремимся предоставить решения для каждой из уникальных потребностей наших клиентов, независимо от сложности поставленной задачи.
Компания DECC полностью оборудована и готова решить вашу проблему эффективным и недорогим решением.
Acheson
Смазочные материалы Emralon 310, Molydag 250 и Molydag 254 обеспечивают коррозионную стойкость различных компонентов.
Doerken
Все покрытия Doerken предназначены для защиты от коррозии.
Dow Corning
Большая часть линейки Molykote обеспечивает превосходную защиту от коррозии.
Lord Corporation
Chemlok 6254 является предпочтительным покрытием DECC, которое используется для процесса соединения резины с металлом, а также обладает коррозионной стойкостью. Мы также используем Chemlok 6260 для аналогичных проектов.
The Magni Group
DECC — это аппликатор, одобренный компанией Magni. Все покрытия Magni были разработаны специально для защиты компонентов от коррозии.
Whitford
DECC — одобренный Whitford аппликатор. Многие покрытия Xylan разработаны с учетом защиты от коррозии в качестве главного приоритета.
Коррозионностойкие покрытия компании DECC обеспечивают эффективную защиту от многих различных форм коррозии.
Атмосферная коррозия
Этот термин используется для описания любых коррозионных причин, которые могут присутствовать в атмосфере внутри или вне помещений. Несколько факторов могут работать вместе, чтобы вызвать атмосферную коррозию. ИСО 9223 стандарта оценивают коррозионную активность окружающей среды от C1 (наименее агрессивная) до CX (наиболее агрессивная). Эта классификация может помочь определить, какие материалы могут или не могут быть подходящими для применения и окружающей среды, но атмосферная коррозия может произойти, даже если будут приняты меры предосторожности. Состояние поверхности может усилить атмосферную коррозию: грубые поверхности склонны собирать грязь и другие твердые частицы, что в конечном итоге может привести к коррозии, в то время как гладкие поверхности менее восприимчивы.
Щелевая коррозия
Щелевая коррозия, образующаяся в ограниченном пространстве с ограниченным содержанием кислорода, обычно поражает фланцы, резьбовые соединения и другие механические соединения в оборудовании и машинах. Растворенные ионы металлов и ионы хлора проникают в эти щели с низким содержанием кислорода, создавая большие неглубокие области коррозии.
Науглероживание
Некоторые металлы и сплавы могут науглероживаться в высокотемпературных средах, где присутствуют монооксид углерода, диоксид углерода, метан или другие углеводородные газы. Эффекты науглероживания могут сильно различаться в зависимости от количества углерода и кислорода в атмосфере, рабочей температуры и состава металла. В дополнение к внешней коррозии, науглероживание также может вызвать охрупчивание и, в крайних случаях, разрушение материала, приводящее к образованию глубоких ямок и отверстий.
Гальваническая коррозия
В любой потенциально агрессивной среде, где два разнородных металла вступают в повторяющийся механический контакт, может возникнуть гальваническая коррозия. Такие материалы, как углеродистая и оцинкованная сталь, медь и латунь, очень восприимчивы к этому разрушительному процессу. При гальванической коррозии металл с более низким потенциалом положительного электрода обычно более подвержен воздействию, а скорость коррозии может быть очень высокой и быстродействующей. И барьерные, и защитные покрытия от компании DECC обеспечивают эффективное решение проблемы гальванической коррозии.
Высокотемпературная коррозия
Высокотемпературная атмосфера, богатая кислородом, серой или галогенами, может вызывать сильные коррозионные реакции. Эти «восстановительные» среды могут воздействовать на алюминий, кремний, хром и другие металлы и сплавы. Специальные высокотемпературные покрытия от DECC могут защитить большинство металлических поверхностей от коррозионных реакций при повышенных температурах.
Межкристаллитная коррозия
Хотя современные металлы с пониженным содержанием углерода, как правило, невосприимчивы к межкристаллитной коррозии, она по-прежнему представляет опасность для любого материала, содержащего углерод. Фактором, провоцирующим межкристаллитную коррозию, являются высокие температуры выше 1000°F (550°C). Термическая обработка металлов — отличный способ предотвратить этот тип коррозии; Компания DECC предлагает ряд термобарьерных покрытий для защиты нетермообработанных материалов.
Окисление
Обычно называемое ржавлением, окисление происходит, когда железо подвергается воздействию кислорода в окружающей среде, и, следовательно, это, возможно, наиболее распространенная форма коррозии. Колебания температуры могут ускорить процесс окисления. На поверхности образуются чешуйки ржавчины из оксида железа, которые парадоксальным образом могут обеспечить защиту от дальнейшего окисления. Однако ржавчина также может проникать глубоко в металлические материалы. Существует ряд методов предотвращения окисления, от простой окраски поверхности до специальных антикоррозионных покрытий DECC.
Точечная коррозия
Питтинговая коррозия, как правило, локализованная, образует дискретные язвы на незащищенных металлических поверхностях. Каждая ямка воздействует на очень небольшую площадь поверхности, но скорость коррозии высока и часто быстро действует. Существует ряд потенциальных причин точечной коррозии, в том числе воздействие морской воды, технологические растворы с высоким содержанием хлоридов, окислительные химикаты и многое другое. Все эти факторы могут усугубляться повышенными температурами и средами с низким pH.
Сульфидация
Сульфидирование похоже на окисление, но вызывается воздействием соединений серы в технологических газах, а не кислорода. Никелевые сплавы особенно подвержены сульфидированию и могут быстро разрушаться. Часто образуются сульфидные отложения, похожие на отложения ржавчины, но они не обеспечивают той защиты, которую обеспечивают оксидные отложения. DECC применяет систему фенольных смол к дизельным компонентам, чтобы решить эту проблему.
Равномерная коррозия
Как следует из названия, равномерная коррозия представляет собой постоянное разрушение на большой части незащищенной металлической поверхности, часто на всей поверхности. Равномерная коррозия обычно происходит в рабочей среде с постоянной температурой и химическим воздействием и обычно происходит с постоянной, хотя и постепенной, скоростью. От него обычно легче защититься, чем от локализованных процессов коррозии.
Растрескивание и усталость
Хотя технически это не коррозия, растрескивание и усталость все же очень вредны для металлов и сплавов. Как правило, вызванное сочетанием механического напряжения и коррозионных факторов окружающей среды, растрескивание может очень быстро распространяться и вызывать более быстрый выход из строя, чем одна только коррозия. Коррозионная усталость обычно вызывается комбинацией циклических нагрузок и коррозионных факторов и может быстро снизить усталостную прочность материала. Антикоррозионное покрытие от DECC поможет бороться с коррозионными факторами, которые приводят к чрезмерному растрескиванию и усталости.
Связанные статьи
Просмотреть все
Ищете больше? Ознакомьтесь с нашими последними новостями и статьями
Подробнее
ISO 12944 – Защита стали от коррозии с помощью защитной краски
Сталь является одним из наиболее часто используемых металлов, благодаря своей надежной опоре и свойствам нержавеющей стали является одним из самых распространенных материалов в промышленности. на планете. Однако, как черный металл, он подвержен коррозии при одновременном воздействии влаги и кислорода. Когда железо в стали окисляется, оно занимает примерно в шесть раз больше объема исходного материала, что может резко нарушить его структуру. Защита стали от коррозии необходима для обеспечения ее долговечности, и эта задача стандартизирована в соответствии с ISO 129.44.
ISO 12944 Стандарт
ISO 12944 касается системы защитной окраски, которая может предотвратить коррозию углеродистой или низколегированной конструкционной стали. Эта система покрытия задерживает коррозию металла, потому что она может изолировать поверхность стали от местного микроклимата, который ее окружает и в противном случае может вызвать ржавчину. ISO 12944 состоит из восьми частей, каждая из которых либо посвящена конкретным соображениям, либо подробно описывает этап процесса.
Все части ISO 12944
ISO 12944-1:2017 – Краски и лаки – Защита стальных конструкций от коррозии с помощью систем защитной окраски – Часть 1: Общее введение не определяет конкретную процедуру, а дает основу, необходимую для использования сводных документов. Он устанавливает область действия стандарта, указывая, что его следует использовать только для предотвращения коррозии, а не для защиты соответствующей поверхности от других воздействий, таких как микроорганизмы, химические вещества, механическое воздействие и пожары.
Создание на основе этого, ISO 12944-2: 2017 – Краски и лаки. Защита стальных конструкций от коррозии с помощью защитных систем окраски – Часть 2: Классификация сред классифицирует основные среды, которым может подвергаться конструкционная сталь. Это определяет категории атмосферной коррозии на основе потери массы, описывает категории окружающей среды для конструкций, погруженных в воду или заглубленных в почву, и дает информацию о некоторых особых коррозионных нагрузках.
В качестве начального этапа процедуры нанесения защитной краски, ISO 12944-3:2017 – Краски и лаки. Защита стальных конструкций от коррозии с помощью систем защитной окраски – Часть 3. Конструктивные соображения требуют, чтобы стальные конструкции были спроектированы таким образом, чтобы не только обеспечить их общую поддержку, но и облегчить облегчают приготовление, нанесение и уход за защитной краской. Поскольку определенные формы конструкции более подвержены коррозии, рекомендуется, чтобы проектировщик связался со специалистом по коррозии на самом раннем этапе процесса, чтобы конструкция не подверглась коррозии до нанесения.
ISO 12944-4:2017 – Краски и лаки – Защита стальных конструкций от коррозии с помощью защитных систем окраски – Часть 4: Типы поверхности и подготовка поверхности определяет ряд типов поверхностей стальных конструкций и устанавливает требования, касающиеся их подготовки к нанесению краска. Эти требования гарантируют отсутствие на поверхности каких-либо вредных веществ, которые могут ограничить адгезию грунтовки к стали.
ISO 12944-5:2019 — Краски и лаки — Защита стальных конструкций от коррозии с помощью систем защитной окраски — Часть 5: Системы защитной окраски фокусируется на другом основном компоненте защищаемой конструкции: самой системе окраски. В этой части описываются различные типы красок и материалов для покрытий и даются рекомендации по их выбору на основе классификации сред и поверхностей, установленной предыдущими частями сводного стандарта.
Последним разделом, помогающим выбрать систему окраски, является ISO 12944-6:2018 – Краски и лаки – Защита стальных конструкций от коррозии защитными системами окраски – Часть 6: Методы лабораторных испытаний. В этом документе рассматриваются процедуры лабораторных испытаний, используемые для определения эффективности конкретной системы защитной окраски. Одним из обсуждаемых методов, помогающих в выборе системы окраски, является искусственное старение, предназначенное для оценки надежности антикоррозионного покрытия с течением времени.
ISO 12944-7: 2017 — Краски и лаки — Защита стальных конструкций от коррозии с помощью систем защитной окраски — Часть 7: Выполнение и надзор за окрасочными работами — касается фактического нанесения системы защитной окраски на стальную конструкцию и содержит требования на его исполнение, кроме управления краской и рабочими. Рекомендуется подготовить стальную основу к нанесению системы окраски в соответствии с указаниями, изложенными в предыдущих шести частях стандарта.
И, наконец, для более широкого руководства, охватываемого этой серией стандартов, ISO 12944-8:2017 – Краски и лаки – Защита стальных конструкций от коррозии с помощью систем защитной окраски – Часть 8: Разработка спецификаций для новых работ и технического обслуживания обеспечивает средства, с помощью которых защищенная сталь может поддерживаться в течение всего срока ее службы.
Сосредоточенный на определенной группе конструкций, последний стандарт в этой серии, ISO 12944-9: 2018 — Краски и лаки — Защита стальных конструкций от коррозии с помощью систем защитной окраски — Часть 9: Системы защитной окраски и методы лабораторных испытаний для морских и связанных с ними сооружений, определяет эксплуатационные требования к системам защитной окраски для морских сооружений.