Протяжка проволоки: Механизм протяжки проволоки 4-хроликовый
alexxlab | 20.02.2023 | 0 | Разное
M LORCH
СВАРОЧНЫЕ АППАРАТЫ СЕРИИ M
Серия аппаратов M была специально разработана, чтобы ответить современным требованиям предприятий кузовостроения автопромышленности. Их задачи включают сварку различных металлов и сплавов.
Это гальванизированные стали с различными типами покрытий, которые не могут быть сварены традиционно, так как может быть нарушена коррозионная стойкость всей конструкции. Для исключения этого влияния применяется полуавтоматическая пайка проволочным припоем.
Аппараты серии M позволяют производить пайку начиная с 25 A , что позволяет соединять самые тонкие металлы от 0,5 мм. Минимальное теплововложение минимизирует коробление металла. Кроме того М подкупает простотой управления, сбалансированными диапазонами ступеней напряжения и автоматической настройкой скорости подачи проволоки. Сварочная горелка уже подготовленная к MIG-пайке.
Серия М имеет ряд существенных преимуществ: качественный механизм подачи проволоки; протяжка проволоки без подачи напряжения нажатием кнопки; большие устойчивые колеса; поверхность аппарата можно использовать как подставку; двойное крепление для баллона; защищенный от перегрузки выпрямитель; производительная система охлаждения.
Новый точный 4-х роликовый механизм подачи проволоки, создает равномерный прижим, регулируется еще лучше и гарантирует минимальную деформацию проволоки, точное выравнивание и стабильную подачу. Добавьте к этому новую кнопку включения протяжки проволоки, непосредственно на механизме подачи.
Для протяжки проволоки теперь нет необходимости постоянно включать горелку. Обновленная электроника, новый, более компактный центральный евроразъем горелки, регулируемый тормоз кассеты, также более понятное управление и новый, эргономичный внешний вид.
Комбинированный трансформатор с секционированными обмотками, который, конечно, намотан из высококачественной меди и оптимально согласован. Крепкий диодный выпрямительный блок с защитой от перенапряжения. Ступенчатый переключатель для оптимальных настроек в каждом положении.
Крепкий диодный выпрямительный блок с защитой от перенапряжения. Ступенчатый переключатель для оптимальных настроек в каждом положении.
Электронная логика MIG/MAG сварки, которая управляет сварочным током, подачей проволоки, обратным горением проволоки, подачей газ после сварки и временем сварки точки. Свободно регулируемое время сварки точки.
Принудительное воздушное охлаждение для более высокого рабочего цикла. Термореле, как защита от перегрузок. Горизонтальная установка кассеты с проволокой, подходящая для больших и маленьких кассет без дополнительного адаптера. Сменный кабель «земля» с Евроразъемом. Эргономичное управление с читаемой маркировкой. Корпус из гальванизированной стали с порошковым покрытием. Встроенный держатель газового баллона и соответствие стандартам EN 60974-1a, CE и S.
Сварочными аппаратами
для MIGMAGсварки
серии M сварщики могут выполнять свою работу
качественно и экономично.
Прочность, надёжность и качество
Сварочными аппаратами
для MIGMAGсварки
серии M сварщики могут выполнять свою работу
качественно и экономично.
Оптимальные сварочные параметры
Оптимальные сварочные параметры сразу же настраиваются, а подача проволоки автоматически устанавливается в соответствии с выбранным уровнем напряжения.
Новинка: большие установки серии M-Pro на 250 и 300 A
Новинка: большие установки серии M-Pro на 250 и 300 A в исполнении ControlPro выпускаются сейчас с поворотным и съемным механизмом подачи проволоки и шланг-пакетами различной длины. Это дает вам больше свободы при работе с большими деталями и в ограниченном пространстве. В этом варианте исполнения также присутствуют высококачественный 4-роликовый механизм подачи проволоки, вольтамперный индикатор и устойчивая тележка для газового баллона. Благодаря низкой погрузочной высоте облегчается процедура замены баллона. Тележка подходит для 50-литровых баллонов.
Высокое качество серии M-Pro
Качество серии M-Pro также определяется тщательным подходом к оснащению и проектированию аппаратов – от высококачественного трансформатора с оптимально настроенным сварочным дросселем до больших устойчивых колес и прочных ручек. Практичные установки различного уровня мощности и три интеллектуальные концепции управления позволяют аппарату серии M-Pro выполнять конкретные сварочные задачи.
Двойное крепление для газовых баллонов
Для оптимальной безопасности аппараты серии Lorch M оснащаются двойным креплением для газовых баллонов. Поэтому Вы можете безопасно перемещать Ваш источник питания вместе с газовым баллоном (объёмом не более 20 литров).
Сварочные характеристики
Хорошие сварочные характеристики при сварке стали, нержавеющей стали и алюминия.
Режимы работы
Настройки 2-x тактной сварки прихватками, 4-x тактной продолжительной сварки или точечной сварки со свободно регулируемым временем точки.
Благодаря компактному и прочному корпусу со
стабильными колёсами Вы можете без труда поместить аппарат
Lorch M под верстак, или же использовать верхнюю поверхность
аппарата в качестве полки.
Концепция управления
- Концепция управления по принципу “3 шага до сварки”
- С регулировочной автоматикой
- 2-х, 4-х тактовая и точечная сварка
Качественный механизм подачи проволоки с заправкой проволоки без натяжения одним нажатием кнопки в отсеке механизма подачи проволоки.
В комплекте: горелка ML, обратный кабель 25 мм², редуктор
с манометрами расхода и входного давления, газовый шланг,
адаптер шпули K300, сетевой кабель со штекером.
Модель источника | М 222 | М 242 | М 304 |
Сварочный ток, А | 25 -210 | 30 – 230 | 30 – 290 |
Ступени напряжения | 6 | 7 | 12 |
Сварочная проволока | |||
Сталь, мм | 0,6-1,0 | 0,6-1,0 | 0,6-1,2 |
Алюминий, мм | 1,0-1,2 | 1,0-1,2 | 1,0-1,2 |
Продолжительность включения (ПВ) при максимальном токе | |||
ПВ при макс.![]() |
25 | 30 | 30 |
ПВ при макс. токе (40 °C), % | 15 | 20 | 20 |
Аппарат | |||
Сетевое напряжение, В | 1~230 ( 2~400) | 3~400 | 3~400 |
Сетевой предохранитель инерционный, А | 16 | 16 | 16 |
Количество роликов | 2 | 2 | 4 |
Размер (Д x Ш x В), мм | 870х390х610 | 870х390х610 | 870х390х610 |
Масса, кг | 55 | 57 | 67 |
Все пианисты.
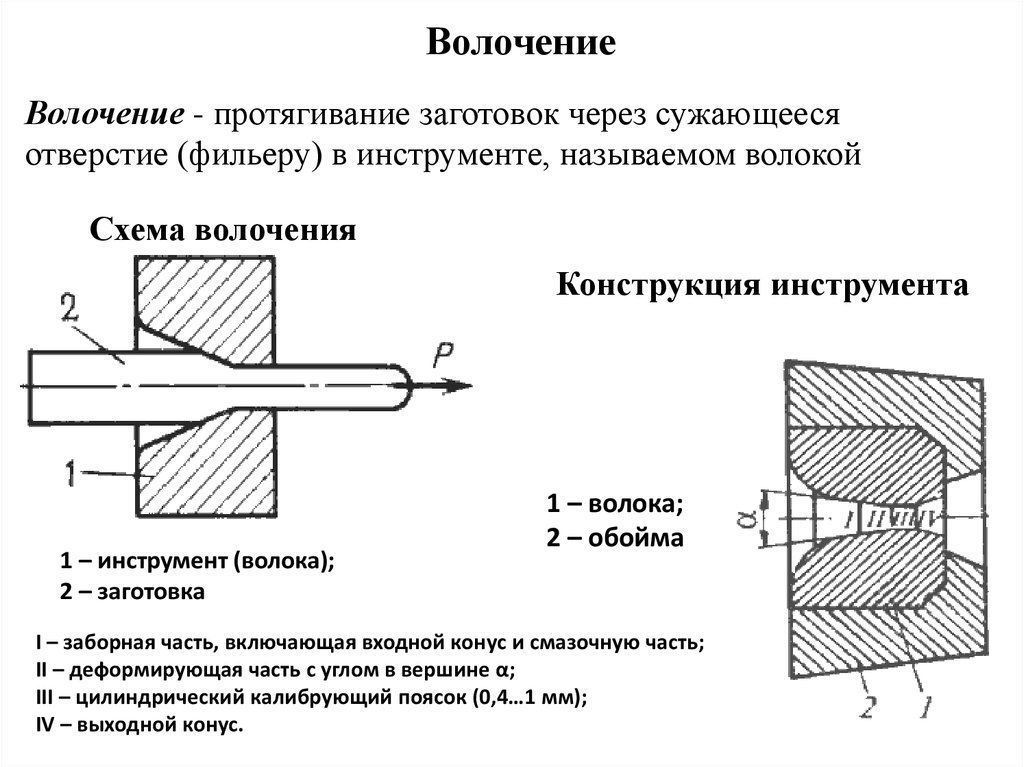
Немного о проволоке и струнах
Естественно, что возникновение, последующее развитие и распространение многострунных, в частности клавишных музыкальных инструментов, исторически связано с производством металлических струн, или, иными словами, с развитием искусства протяжки проволоки.
Насколько известно, человек научился изготовлять металлическую проволоку и струны из нее сравнительно недавно; это требовало большого искусства и опыта, а также механизации способов обработки металла, последняя же была освоена только на сравнительно высоком уровне развития техники. Первое упоминание об изготовлении металлической проволоки найдено во второй книге Моисея (39, 3). Здесь говорится, что искусные мастера Веселиил и Аголиав, разбив золото в листы и вытягивая из него нити, вплетали их в ткани. Однако неизвестно, могла ли употребляться золотая проволока, весьма непрочная и дорогая, в качестве струн для музыкальных инструментов, где требуется, чтобы струны выдерживали значительное напряжение.
Струны древних видов музыкальных инструментов изготовлялись из природных, доступных человеку материалов, не требовавших сложной обработки: это были нити и жгуты из древесной коры и луба, волоса животных, кишки и жилы, наконец, шнуры и нити, свитые из шелка. При прочих достоинствах и удобствах изготовления, обусловленных примитивной техникой, струны из этих материалов обладали достаточной для того времени прочностью, позволяющей их довольно сильно натягивать. Однако их сопротивляемость разрыву была все же довольно ограниченной, а звуки, издаваемые такими струнами, были относительно слабыми и быстро затухающими.
С течением времени, поскольку музицирующий человек желал получать из своих инструментов более сильные и яркие звуки, он должен был обратиться к другим материалам для изготовления струн, обладавшим большей прочностью и сопротивляемостью на разрыв, а также другими физическими качествами. И он неизбежно пришел к использованию для этих целей металлических нитей и проволоки.
Первое исторически надежное известие о волочильных досках для протяжки металлической проволоки в Европе встречается на рубеже XI-XII веков. Это была рукопись монаха Теофила (приблизительно 1100 год). В ней указывается, что из металлической проволоки изготавливаются струны в музыкальных инструментах. Однако систематическое применение металлической проволоки отмечается много позже, примерно с XIV века. Первоначально проволока изготовлялась из мягких, ковких и тягучих материалов – меди и латуни. До XVI века протяжка совершалась примитивным ручным способом; только около 1540 года мастером Рудольфом из Нюрнберга был впервые применен привод от мельничного водяного колеса.
Искусство механической протяжки проволоки в XVI веке появилось сначала в Южной Германии, а затем в других европейских странах – Англии, Франции и других. Можно считать, что к XVIII веку было освоено производство более прочной и удобной железной проволоки, но только в 1812 году известный германский фабрикант Фридрих Крупп начал тянуть проволоку и струны из литой тигельной стали. Этот материал позволил применять в музыкальных инструментах достаточно толстые и сильно натянутые струны, способные издавать громкие и полные по тембру звуки. С тех пор производство стальной струнной проволоки получило развитие в разных странах Европы и США, и в настоящее время в большинстве струнных музыкальных инструментов в основном применяются струны из стальной проволоки, как самые прочные и устойчивые в держании приданного им строя.
Тонкая проволока на заказ – Проволока тонкой вытяжки на заказ
Компания California Fine Wire Co. Наши возможности волочения проволоки включают возможность производить проволоку диаметром от 10 микрон до 1 мм с использованием прецизионных волочильных штампов. Качество штампов, используемых в процессе волочения проволоки, напрямую влияет на точность и стабильность конечного продукта. Все наши штампы полируются на месте опытными мастерами, которые гордятся качеством и точностью своей работы.
Все, что мы производим, изготавливается на заказ, что позволяет клиентам выбирать точный сплав, диаметр и метод упаковки, которые лучше всего подходят для их конкретного применения. Алюминий, медь, резистивная проволока и сплавы драгоценных металлов — это лишь некоторые из доступных вариантов материалов. Свяжитесь с нами, чтобы узнать о полном ассортименте доступных сплавов и материалов проволоки. Помимо волочения проволоки по индивидуальному заказу, мы можем перерисовать стандартную продукцию, предоставленную заказчиком, чтобы улучшить округлость проволоки для прецизионных применений. Наш вариант «сверхчистой обработки» обеспечивает наилучшее качество поверхности и соответствует самым жестким допускам по диаметру в отрасли. Прецизионные алмазные штампы используются в процессе окончательного волочения для создания идеальной отделки проволоки.
Нестандартная проволока может быть вытянута в любом количестве и упакована в катушки или нарезана по длине, в зависимости от применения. Время выполнения заказа оценивается в зависимости от задания, и доступны программы управления запасами канбан. Для получения дополнительной информации о наших возможностях точного волочения проволоки см. таблицу ниже или свяжитесь с нами напрямую.
Easy Quote
ХАРАКТЕРИСТИКИ ЧЕРТЕЖА
- Процесс изготовления
Чертеж
Redrawing
Ultra Finishing
- Wire Shape
Round
StrandedDuplex
Ribbon
- Materials
Aluminum
Copper
Nickel
Nickel Alloys
Сплавы проводов сопротивления
Сплавы для термопар
ЗолотоСеребро
Платина
Сплавы платины
Сплавы для герметизации стекла
Bonding Wire
Numerous Additional Options Available
- Finish
Bare
Enamel
PTFECeramic
Plated
- Wire Diameter
0.
0004″ to 0,040″
от 10 микрон до 1,0 мм
Другие размеры по запросу
- Длина проволоки
Длина резки: от 0,122″ до 70023 No Limit on Spooled Lengths
- Flat Wire Width
0.0004″ to 0.10″
10 microns to 2.5 mm
Other Sizes on Request
- Production Volume
Прототип
Низкий объем
Большой объем
- Типичное время выполнения заказа
Расчет на основании работы
- Industry Focus
Aerospace
Defense
ElectronicsMedical
Research & Development
- Industry Standards
ISO 9001 Certified
DFARS
REACHRoHS
ITAR
- Быстрое время обработки.
- Управление высоким крутящим моментом и скоростью.
- Быстрые разгоны до скорости и торможение до нулевой скорости снова без потери натяжения.
- Различные диапазоны скоростей и требования к крутящему моменту в зависимости от материала.
- Время простоя процесса может быть очень небольшим.
- Из-за скорости проблемы с процессом могут привести к большому количеству брака и потере дохода.
0027
Additional Information
Обзор применения: Волочение проволоки | Производство.
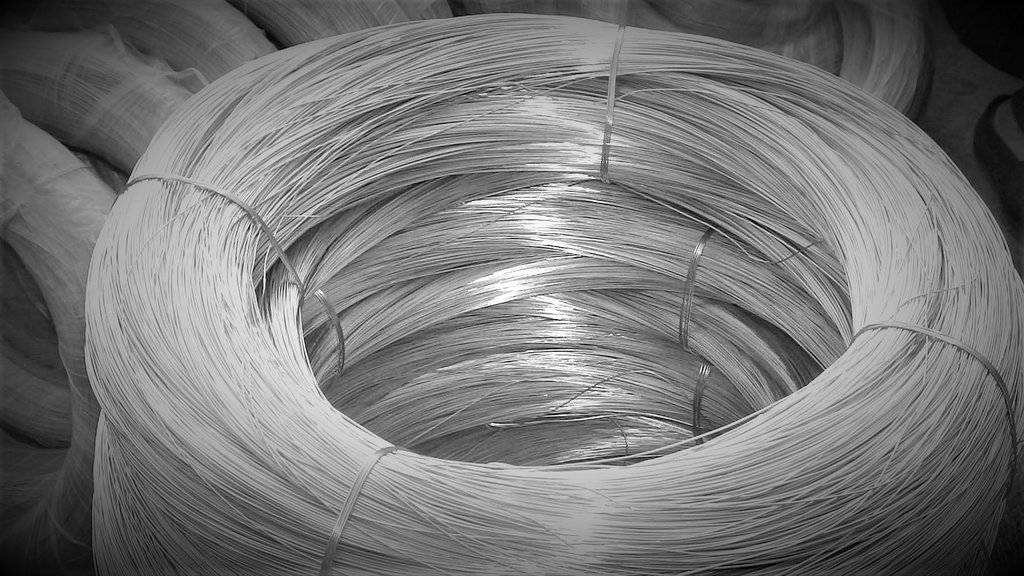
Процесс волочения проволоки практически не изменился за прошедшие годы. Он использует комбинацию матрицы и/или серии матриц для волочения проволоки до выбранного калибра. Тянутая проволока используется во многих областях, помимо того, что мы обычно думаем, как электрические провода и телевизионные кабели. Например, из тянутой проволоки делают пружины любого вида; а также арматура, используемая для строительства во всем мире. Скрепки и скобы сделаны из тонкой тянутой проволоки. Спицы на колесах, проволочные щетки, металлические ручки также изготавливаются из тянутой проволоки. Существуют буквально тысячи готовых изделий, в которых используется тянутая проволока. Чтобы удовлетворить эту постоянно растущую потребность, металлообрабатывающие компании ежегодно протягивают многие миллионы миль проволоки. По этой причине волочение проволоки, хотя процесс волочения не менялся в течение многих лет, является чрезвычайно чувствительным к затратам и конкурентным рынком. В свою очередь, компании, которые производят оборудование для волочения проволоки и технологическое оборудование для волочения проволоки, очень заинтересованы в любом преимуществе производительности или эффективности, которое они могут получить.
Общая схема, показанная ниже, иллюстрирует процесс волочения проволоки. Если используется несколько штампов, они последовательно соединяются друг с другом до тех пор, пока не будет достигнуто требуемое поперечное сечение. Жизненно важно поддерживать непрерывность и знать натяжение и скорость проволоки, когда она проходит через машину. Это обеспечивает постоянное поперечное сечение.
Наука о волочении проволоки
Металлургия — это изучение металла и процессов обработки металлов. Существует определенная скорость изменения характеристик металла, основанная на растяжении и прочности в диапазоне температур при манипуляциях с металлом. Волочение проволоки — это процесс обработки металла, используемый для уменьшения поперечного сечения проволоки путем протягивания ее через ряд фильер.
Процесс волочения проволоки
Сам процесс на самом деле довольно прост. Чтобы начать процесс волочения проволоки, катушка с проволокой помещается в начале машины на катушку. Чтобы пропустить его через машину, конец проволоки должен быть обрезан или сплющен. Он подается через машину и через серию штампов для получения окончательной площади поперечного сечения. На конце машины обычно имеется катушка или намотчик, поэтому готовый продукт представляет собой моток проволоки с желаемой площадью поперечного сечения. Конечным процессом также может быть упаковщик ствола, в котором размещается ствол, а спиральная проволока наматывается непосредственно в ствол с помощью поворотного стола.
Жизненно важно, чтобы температура оборудования не повышалась слишком сильно (в первую очередь из-за энергии, выделяемой при деформации металла), а проволока имела постоянное натяжение и скорость при прохождении через ряд гребенок. Исторически это достигалось исключительно механическими средствами. Однако приводы постоянного тока начали использоваться для работы двигателей на определенных уровнях в зависимости от требуемого металла и поперечного сечения. По мере совершенствования технологий было добавлено программное обеспечение для приложений наматывания, которое поддерживало движение материала с надлежащей скоростью и натяжением, чтобы обеспечить качественный продукт. Это убрало часть механики и перенесло ее на электронные технологии. С внедрением высокопроизводительных/высокоэффективных приводов переменного тока с мощными процессорами для программного обеспечения механическая зависимость от оборудования значительно уменьшилась.
Приводы и процесс волочения проволоки
Как обсуждалось выше, инверторы переменного тока могут использоваться для выполнения широкого спектра функций на машинах для волочения проволоки, поскольку они очень похожи на намоточные машины. Электронный линейный вал, векторное управление и последовательная связь используются на многих из этих современных машин.
Определение программного обеспечения электронного карданного вала
Программное обеспечение электронного линейного вала позволяет синхронизировать один или несколько приводных двигателей с сигналом главного энкодера. Главный энкодер подает импульс на ведомый, в результате чего ведомый дает команду своему двигателю поддерживать определенное положение вала. Ведомый привод отслеживает импульсную обратную связь от ведущего энкодера и своего собственного энкодера. После этого ведомое устройство будет компенсировать любые ошибки положения, регулируя выходную скорость своего двигателя, что приведет к почти идеальному выравниванию между ведущим устройством системы и двигателем ведомого устройства. Ошибка позиционирования не накапливается, поэтому выравнивание всегда будет поддерживаться…
На лотке для проволоки используется главный привод, а остальные – ведомые. Далее в определении программного обеспечения указано:
Следящее устройство также имеет функцию электронного редуктора. Это позволяет ведомому приводу работать в соотношении с ведущим, как если бы они были механически связаны через ремни или зубчатую передачу. Это программное обеспечение включает «улучшенную» связь Modbus. Функция контроля совмещения позволяет следящему приводу принимать регистрационную метку от движущегося продукта и регулировать его угловое положение. Это используется для специальных применений, таких как упаковочные машины, летающие отрезки, этикетки…
Программное обеспечение ELS идеально подходит для проволочного лотка, так как его характеристики, подобные наматывающему устройству, требуют, чтобы проволока двигалась с известным и постоянным натяжением и скоростью. Он должен постоянно приспосабливаться к ошибкам и отслеживанию.
Внедрение приводов переменного тока не только обеспечило очень хорошую производительность, но и дало пользователю возможность не полагаться на механические детали, которые подвержены износу. Поэтому профилактическое обслуживание и рутинные демонтажи значительно сокращаются.
Проблемы приложения для волочения проволоки включают:
Резаки
Многие компании, поставляющие оборудование для волочения проволоки, также поставляют периферийное оборудование. После волочения проволоки необходимо обрезать ее до определенной длины. ЧРП с электронным линейным валом очень хорошо выполняет эту функцию. За режущим диском имеется главный привод с замкнутым контуром и ведомый привод. Главный привод должен поддерживать точное натяжение и скорость в сочетании с ведомым приводом.
Упаковщики для бочек
Упаковщик для проволочных бочонков представляет собой узел, который может быть размещен непосредственно на лотке для проволоки, или спиральная проволока может быть доставлена на другую станцию. В функции упаковки ствола ствол помещается на вращающийся поворотный стол. Проволока непрерывно подается в нижнюю часть ствола и отбрасывается. Обычно на барабанном упаковщике имеется два двигателя: один для укладки проволоки, а другой для вращения поворотного стола. Поскольку этот процесс намного медленнее и не зависит от натяжения, а лишь умеренно зависит от скорости, небольшой привод с разомкнутым контуром соединен с векторным приводом с замкнутым контуром для поворотного стола. Существует также версия этой сборки только для проигрывателя. В этом случае устанавливается только один привод переменного тока.
Намотчики и намотчики
Намотчики часто устанавливаются в конце волочильных станков. Моталки представляют собой отдельные машины, наматывающие проволоку и конечные изделия различного сечения и прочности. Их единственная цель – намотать или намотать конечный продукт для отправки. Намотчики могут использоваться для намотки очень больших кабелей на высоких скоростях, и их мощность достигает 1000 л.с. Спулеры вроде меньше и не выше 50 л.с. Хотя они выполняют ту же функцию, намотчики выглядят меньше, чем моталки, и в отрасли называются таковыми.
Application Requirements
Wire Applications | Voltages | HP Range | Duty | Software | |||
Волочение проволоки | 230/460/575 В | 5-100 л.с. | Непрерывная тяжелая работа; 40 град С N1; Прилагается | Электронный линейный вал | |||
. 40 град С N1; Прилагается | |||||||
Пэкерз баррелей | 230/460/575V | 20-40HP | 20-40HP 9797 | 20-40HP 97979797 | 9000; 40 град С N1; В комплекте |
| |
Фрезы | 230/460/575 В | 5-75 л. | 9000; 50 град С N1; Прилагается | Электронный приводной вал |
Функции привода Подходит для процесса волочения проволоки
В приведенной ниже таблице показаны особенности и преимущества использования частотно-регулируемых приводов для намотки.
Drives Products | Features | Benefits |
Yaskawa A1000 or G7 Drives | PID Control Mode | Line velocity контроль и постоянство диаметра могут быть достигнуты с помощью ПИД-режима приводов с датчиками положения танцора, датчиками скорости или датчиками диаметра. |
Управление включением/выключением охлаждающего вентилятора | Управление количеством включений и выключений приводного вентилятора увеличивает срок службы охлаждающего вентилятора и снижает потребность в техническом обслуживании. | |
Векторное управление потоком и режим управления крутящим моментом | Управление как крутящим моментом, так и постоянным натяжением возможно при использовании векторного управления с обратной связью и режима управления крутящим моментом. | |
Нулевой режим сервопривода | Функция Zero Servo в замкнутом контуре Flux Vector предотвращает провисание проволоки, устраняя необходимость в механическом тормозе. | |
Торможение с помощью кинетической энергии (KEB) | Функция торможения KEB может замедлить приложение до остановки без повреждения нагрузки, даже при отключении питания. Простое движение по инерции до остановки может привести к налипанию или разрыву проволоки. | |
Определение крутящего момента | Обнаружение недостаточного крутящего момента определяет обрыв провода, чтобы привод мог автоматически немедленно остановить приложение. |