Пружинно рессорная сталь – Рессорно-пружинные стали, применяемые в промышленности
alexxlab | 19.05.2020 | 0 | Разное
Рессорно-пружинные стали, применяемые в промышленности
Автор perminoviv На чтение 6 мин. Опубликовано
Пружинная сталь, марки которой применимы в изготовлении тугих изделий, характеризующихся восстановлением первоначальной формы, при сильном изгибе и значительном скручивании.
Важнейшие детали в производстве механизмов, которые испытывают переменную, повторяющуюся нагрузку, под действием которой происходит сильная деформация. Как только нагрузка прекращается, эти элементы принимают первоначальную форму. В работе этих деталей есть особенность, которая не допускает остаточной деструкции, она должна быть только упругой. К рессорно-пружинным сталям предъявляются завышенные требования при выработке. Разберемся, из какой стали делают рессоры?
Для чего вырабатывают пружинный сплав?
Для выработки деталей могут использовать как легированную сталь, так и углеродистую, они обладают повышенной упругостью, вязкостью, выносливостью и пластичностью. Благодаря свойствам этих видов стали ограничивается упругая деструкция.
Рессорно-пружинные стали доступные, технологичные, имеющие высокий предел релаксационной стойкости.
Интересно: для получения качественных изделий из углеродистой и легированной стали ее закаливают при температуре 420-520 градусов, при этом получается эффект структуры троостита.
Рессорно-пружинные стали сопротивляются непрочному разрушению, и отличаются повышенной пластичностью. Их применяют для выработки изделий с высокой стойкостью к износу, например:
- зажимные цанги;
- тормозной прокат;
- кромки;
- пружины и рессоры;
- упорные шайбочки;
- торсы подшипников;
- фрикционные диски;
- шестеренки.
Марки стали по ГОСТу 14959–79
Это стали с высоким содержанием углерода, но с малым легированием. Госстандарт 14959 обозначает – легированный сплав следующих марок:
- 3К-7 – применяется в выработке проволоки холоднотянутым способом, из которой изготавливают пружины, незакаливаемые;
- 50ХГ – производят рессоры для автомашин и пружины для жд. составов;
- 50ХГА – назначение в производстве как у предыдущей марки рессорно пружинной стали;
- 50ХГФА – выпускают особенные пружины и рессорные детали для машин;
- 50ХСА – пружины специального назначения и небольшие детали для механизмов часов;
- 50ХФА – изготавливают детали с повышенной нагрузкой, с требованиями высочайшей устойчивости и прочности, которые действуют при больших температурах – до 300 градусов.
- 51ХФА – для пружинной проволоки;
- 55С2 — для производства пружинных механизмов и рессор, используемых в тракторостроении, машиностроении, для подвижных составов на ж/д;
- 55С2А – производят авторессоры, пружины для поездов;
- 55С2ГФ – для выработки очень прочных пружин специального направления, авторессор;
- 55ХГР – производят полосовую сталь пружинную, толщина которой варьируется от 3 до 24 мм;
- 60Г – для выработки круглых и гладких пружин, колечки и прочие выработки пружинного типа, обладающих высокой стойкостью к изнашиванию и упругостью, например, скобы, втулки, тамбурины для тормозящих систем, применяемые в тяжелом машиностроении;
Интересно: торсионная сталь, марки 60С2 – пружины высокой нагрузки, фрикционные диски, пружинные шайбочки;
- 60С2А – производят те же изделия, что из стали предыдущего типа;
- 60С2Г – тип рессорной стали, из которой производят тракторные и авторессоры;
- 60С2Н2А – производят ответственные рессоры с высокой нагрузкой на сплав;
- 60С2ХА – для выработки высоконагруженных пружинных продуктов, на которые производится постоянная нагрузка;
- 60С2ХФА – это круглая сталь с элементами калибровки, из которой производят пружины и пластины рессор с высокой ответственностью;
- 65 – изготавливают детали с повышенной прочностью и упругостью, которые эксплуатируются при большом давлении при высоких статистических нагрузках и сильной вибрации;
- 65Г – изготавливают детали, которые будут работать без ударных нагрузок;
- 65ГА – проволока для пружин, прошедшая закалку;
- рессорная сталь марки — 65С2ВА, высоконагруженные рессорные пласты и пружины;
- 68А – закаленная проволока для производства пружинных приспособлений калибром 1.2-5,5 мм;
- 70 – детали для машиностроения, от которых необходима повышенная износоустойчивость;
- 70Г – для пружинных элементов;
- 70Г2 — производят землеройные ножи и пружины для разных отраслей промышленной индустрии;
- 70С2ХА – пружинные элементы для часовых устройств и большие пружины специального назначения;
- 70С3А – пружины с большой нагрузкой;
- марка рессорно пружинной стали 70ХГФА – проволока для выработки пружинных элементов с термообработкой;
- 75 – любые пружинные и другие детали, используемые в машиностроении, на которые оказывается большая нагрузка вибрациями;
- 80 – для выработки плоских деталей;
- 85 – износостойкие детали;
- SH, SL, SM, ДН, ДМ – машинные пружины, работающие при статистических нагрузках;
- КТ-2 – для выработки холоднотянутой проволоки, которая навивается без термической обработки.
Первыми цифрами обозначается среднее содержание углерода в конкретной стали и обозначается она в процентном эквиваленте. После цифр идет литера, обозначающая конкретные легирующие присадки добавлены в сплав, а последнее число – это содержание добавок. Стоит отметить, что если легирующего связующего меньше 1,5%, то число не пишется, содержание больше чем 2,5% обозначается тройкой, промежуточное значение между двумя первыми значениями – прописывается цифрой 2.
Пружинный прокат будь то некорродирующая полоса, листы, шестигранники или квадраты, подразделяются на группы с некоторыми характеристиками:
- химический состав – первоклассная нержавеющая листовая спецсталь, которая нормируется по значениям от 1 до 4Б;
- способ обработки – горячекатаная полоса, поверхность которой обтачивается или шлифуется, калиброванный прокат, кованный, специально отделанный прокат.
Сталь 60с2а пружинная
Нержавеющая пружинная сталь – дешевая, с большой упругостью, выносливостью к износу, при этом у нее нет отпускной хрупкости. Этот сплав не деформируется от механических нагрузок. Эффективно эксплуатируется при повышенной влажности, так как имеет нержавеющее покрытие. Ее применяют при температуре не более 250 градусов, используется для производства изделий из металлопроката.
Из нержавеющей стали производят оборудования в морской промышленности, в медицине, и пищевом производстве. Ее применение в этих отраслях обусловлено коррозиеустойчивой сплава.
Интересно: устойчивость связана с большим содержанием молибдена и хрома. Сплав имеет хорошую сопротивляемость к образованию трещин под большой нагрузкой.
Марка нержавеющей жаропрочной стали используется при выработке тонколистовой прокатки, цельнотянутых труб и различных инструментов пищевой и химической индустрии.
Специфики пружинных сплавов
Высоко- и среднеуглеродистые виды этих сплавов упрочняются путем тонкой хладной деструкции, допускающей внедрение дробеструйных и гидроабразивных способов. При данном виде воздействия усилия остаточного сжатия наводят на плоскость изделий.
Фактически любая рессорная сталь (некорродирующая, без особых противокоррозионных свойств) должна пройти операцию сильного накаливания по сквозистой методике. Поэтому готовая металлопродукция по своему разрезу будет обладать структурой троостита.
Масленое закаливание при температуре 830–880 градусов, совмещаемая с отпуском при 410–480 градусах гарантирует повышения рубежа упругости – главнейшего рабочего свойства вышеперечисленных сталей. Зачастую употребляется и изотермическое закаливание, обеспечивающее не только высокую упругость, но еще и увеличенные данные пластичности, стабильности и вязкости вещества.
Некорродирующая лента и проволока из сплавов 70 и 65 в наибольшей степени часто употребляются для создания машинных пружин. В автотранспортной сфере также динамично используются кремниевые рессорные стали марки пружинной прокатки – 60С2А, 70С3А и 55С2. Они предрасположены к обезуглероживанию, что понижает характеристики их упругости и выносливости. Но за счет присадок хрома, ванадия и определенных составляющих все эти возможные опасности нивелируются.
Сферы применения рессорной прокатки самых ходовых марок стали:
- пружины для любых устройств и агрегатов Машино- и автомобиле-строительной областей – 55С2, 50ХГ, 50ХГА;
- тяжелонагруженные пружины – 60 С2Г, 60С2, 65С2ВА,60С2Н2А;
- износоустойчивые пружины круглые и плоские (употребляется полоса), действующие при повышенных вибрациях – 80, 75,85.
В завершение немного о недостатках
- нехорошей свариваемостью;
- трудность резки.
solidiron.ru
конструкционные, легированные, маркировка и термообработка
Рессорно-пружинные стали – это специальные стали, которые предназначаются для производства различных упругих элементов, в частности пружин и рессор.
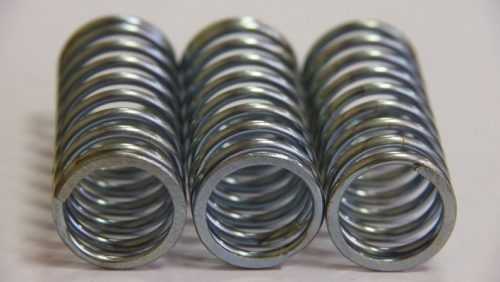
Данный тип материала относится к высоко- и среднелегированным сталям. Главное отличие рессорно-пружинной стали от иных видов – это значительно увеличенный предел текучести данного материала. Другими словами можно сказать, что этот тип обладает высокой степенью упругости, то есть возвращается в исходные состояния и форму после устранения нагрузки. Это параметрическое свойство обусловлено областью применения рессор и пружин. В нормальном режиме работы они постоянно подвергаются сжатию/растяжению или упругой деформации и должны выполнять свои функции даже после большого цикла наложения и снятия деформации. Также данный материал должен обладать хорошей пластичностью и высокой стойкостью к хрупким разрушениям.
Основными легирующими элементами являются кремний, марганец, вольфрам и никель. Эти присадки увеличивают сопротивление пластическим и упругим деформациям путем измельчения зерна сплава. Готовым продуктом можно считать и проволоку, которую в дальнейшем применяют при изготовлении витых и компонованных пружин.
Свойства рессорно-пружинной стали
Основными характеристиками для данного вида сталей является высокое сопротивление упругим деформациям и низкий коэффициент остаточного растяжения. Это связано с недопустимостью увеличения или уменьшения конструкционного размера пружины.
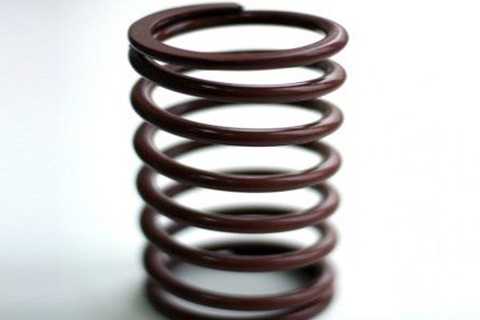
Стальная пружина
Хороших конструкционных и эксплуатационных свойств добиваются, протягивая заранее патентированную проволоку при низких температурах, при этом производят сильную обтяжку материала.
Процесс патентирования ведется в промежутке между двумя вытяжками, сталь нагревают выше температурной точки образования аустенита и затем охлаждают в ванне с расплавом свинца, при этом аустенит переходит в тонкопластинчатый сорбит и увеличивается её механическая прочность.
Для достижения одинаковых физико-химических свойств по всему сечению материала пружинная сталь должна пройти процесс прокаливания сквозной методикой, это обеспечит гомогенную структуру по всему сечению. Особенно важен этот метод для изготовления рессор и пружин большого диаметра, когда неравномерность свойств исходного материала может привести к разрушению готового изделия.
Как для любого другого материала, для рессорно-пружинной стали характерно наличие в составе углерода. В данном случае его содержание может колебаться в пределе 0.50-0.80 % от массы сплава. Дополнительно используют такие легирующие добавки:
- кремний – до 2.5 %;
- марганец – до 1.3 %;
- вольфрам – до 1.3 %;
- никель – до 1.7 %.
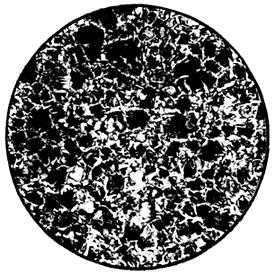
Микроструктура рессорно-пружинной стали
Стоит заметить, что хром и марганец при совместном легировании увеличивают сопротивление стали низким пластичным деформациям. Никель и вольфрам образуют тонкую и однородную структуру карбидной фракции, которая препятствует дислокации.
Рессорно-пружинная сталь очень критична к деформациям наружного слоя материала, так как эти напряжения являются концентраторами возможных дефектов готового изделия.
Закалка данного типа производится при температурах 850 – 880 оС, но после такой термической обработки сталь проявляет слабые упругие свойства из-за образования мартенсита, для повышения данного типа свойств её отпускают при температурах порядка 420-510 оС, что способствует образованию троостита и повышению упругой деформации сплава до предела прочности 1200-1900 МПа и пределу текучести 1100-1200 МПа. При этом проведение закалки изотермически – при постоянной температуре – положительно сказывается на показателях пластичности и вязкости материала.
Стали данного типа обладают хорошими антикоррозионными свойствами из-за наличия в составе сплава таких легирующих добавок как хром и молибден. Это положительно сказывается на длительности эксплуатации и препятствует образованию трещин во время работы.
Стоит отметить так же несколько основных недостатков рессорно-пружинной стали:
- плохая свариваемость – это обусловлено разрушением наружного слоя материала и локальном перегреве детали;
- сложность резки – некоторые трудности возникают при попытках реза такого типа стали, связанно это напрямую с большим сопротивление деформации.
Классификация пружинных сталей
Для начала разберем маркировку такого типа материала, чаще всего она имеет вид «50А2БВГ», где:
50 – содержание углерода в долях процента;
А2 – легирующий элемент №1 и его содержание в процентах;
Б,В,Г – легирующие элементы №2,3,4 и т.д.
Важно! Если после обозначения легирующего элемента не стоит число, значит, его массовое содержание не превышает 1.5%, если число 2 – массовая доля больше 1,5%, но меньше 2,5%, если 3 – массовая доля выше 2,5%.
Например, сталь 50ХГФ – это сплав, в котором содержание углерода составляет 0,50%, и легирующие компоненты хром, марганец и ванадий составляют меньше 1,5%.
Если в маркировке стали есть только цифра, например, ст 50, ст 65 и др., это обозначает, что она относится к углеродистым сталям, а если в названии есть минимум 2 элемента, такая рессорно-пружинная сталь относится к легированным.
Рассмотрим основные классификации данного типа:
- По способу обработки:
- Кованный и горячекатаный.
- Калиброванный.
- Со специальной обработкой наружных поверхностей.
- Горячекатаный круглый с обточенной поверхностью.
- По химическому составу стали:
- Качественная.
- Высококачественная.
Марка рессорно-пружинной стали дает возможность определить её конструкционные и физико-химические свойства, определить область использования и возможности по механической обработке.
Область использования пружинной стали
Исходя из названия, можно сделать вывод, что данный вид предназначен для использования в областях, связанных с большими упругими деформациями, растяжением, скручиванием. Применяют такую сталь для изготовления всевозможных видов пружин для разнообразного технологического оборудования, полосок стали под рессоры, суппорты и прочее.
Основные области использования:
- производство рессор автомобилей и тяжелой техники;
- производство пружин для технологично оборудования, при этом это относится к пружинам на сжатие и растяжение;
- пружины плоские, цилиндрические, сложные из прутков различных сечений и др.
- упругие элементы тяжелой техники, станкового оборудования;
- пружины тракторной техники и локомотивной техники;
- ножи земельной техники;
- блокировочные и тормозные устройства;
- обоймы подшипников.
Рессора автомобиля
Рассмотрим сводную таблицу самых распространенных марок рессорно-пружинных сталей с указанием их маркировки и области применения:
Маркировка | Основные легирующие компоненты | Эксплуатационные особенности |
50ХГ | Хром, марганец | Рессоры автомобилей, пружины железнодорожной техники |
50ХСА | Хром, кремний, азот | Упругие элементы часовой техники |
55ХГР | Хром, марганец, бор | Штамповка пластин рессор |
60С2 | Кремний | Валы с нагрузкой на скручивание, цанги, подпружиненные шайбы |
60Г | Марганец | Пружинные кольца, бандажи, тормозные башмаки |
65 | — | Детали, работающие в условиях высокого трения |
65С2ВА | Кремний, вольфрам, азот | Рессоры и пружины, работающие под высокой динамической нагрузкой |
70Г2 | Марганец | Ножи для землеройных машин |
70С3А | Кремний, азот | Тяжело нагруженные пружины механизмов |
85 | — | Фрикционные диски с высокой прочностью |
Как видно из таблицы, величина и количество легирующих присадок напрямую отвечают за износостойкость и механическую прочность деталей. Видно, что с повышение содержания углерода от 0,5% до 0,85% увеличивается прочность и упругость материала, хром препятствует образованию ржавчины, вольфрам повышает твердость и красностойкость стали, а марганец увеличивает стойкость к ударам.
Если вы нашли ошибку, пожалуйста, выделите фрагмент текста и нажмите Ctrl+Enter.
stankiexpert.ru
описание, характеристики, марка и отзывы
Рессорно-пружинные стали характеризуются довольно высоким модулем упругости. Этим показателем обладают углеродистые и легированные марки металла.
Легированные и углеродистые материалы
Этот вид материала используют для производства жестких (силовых) упругих элементов. Причиной именно такому применению стало то, что высокий модуль упругости этой стали сильно ограничивает упругую деформацию детали, которая будет произведена из рессорно-пружинной стали. Также важно отметить, что этот тип продукта является высокотехнологичным и в то же время довольно приемлемым по своей стоимости. Кроме использования в авто- и тракторостроении, этот вид материала также широко применяется для изготовления силовых элементов в различных приборах. Чаще всего детали, которые произведены из этой стали, называют одним общим названием – пружинные стали общего назначения.
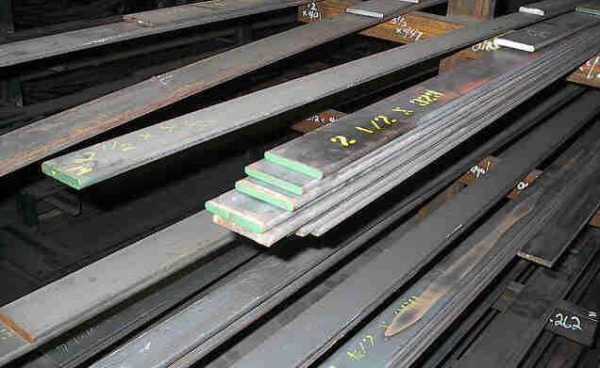
Для того чтобы обеспечить необходимую работоспособность силовых упругих элементов, необходимо, чтобы рессорная сталь обладала высоким пределом не только упругости, но и выносливости, а также релаксационной стойкостью.
Свойства
Для того чтобы удовлетворить такие требования, как выносливость, упругость и релаксационная стойкость, применяются материалы с повышенным содержанием углерода. Процент содержания этого вещества в используемом продукте должен быть в пределах от 0,5 до 0,7 %. Также важно подвергать этот вид стали закалке и отпуску. Проводить эти процедуры необходимо при температуре от 420 до 520 градусов по Цельсию.
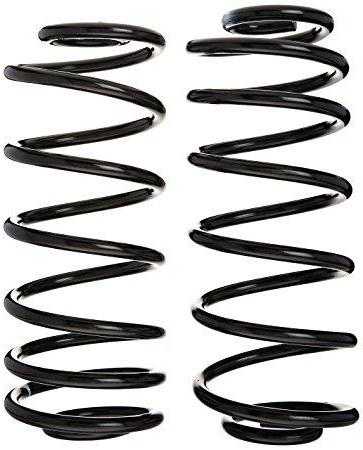
Стоит заметить, что рессорная сталь, закаленная на мартенсит, обладает малым коэффициентом упругости. Он значительно повышается лишь при отпуске, когда образуется структура троосита. Процесс гарантирует повышение пластичности стали, а также вязкости ее разрушения. Эти два фактора важны для того, чтобы снизить чувствительность к концентраторам напряжения, а также увеличить предел выносливости продукта. Можно добавить, что положительными качествами характеризуется также и изометрическая закалка на нижний бейнит.
Ножи
Рессорная сталь для ножа некоторое время являлась наиболее распространенным материалом, особенно среди владельцев автомобилей. Изготовление острых предметов действительно осуществлялось из старых рессор, которые пришли в негодность для использования в транспортном средстве. Применение ножей из такого необычного материала осуществлялось как для различных бытовых нужд, так и для обычной резки продуктов на кухне. Выбор именно на эту деталь пал не случайно. Было несколько причин, почему именно рессорная сталь стала основным материалом для самодельного производства хороших ножей.
Первая причина – это то, что из-за плохого качества дорог такая деталь как рессора, часто и быстро приходила в негодность. Из-за этого у многих автовладельцев этих узлов было в избытке. Детали просто лежали в гаражах. Доступность и стала первой причиной.
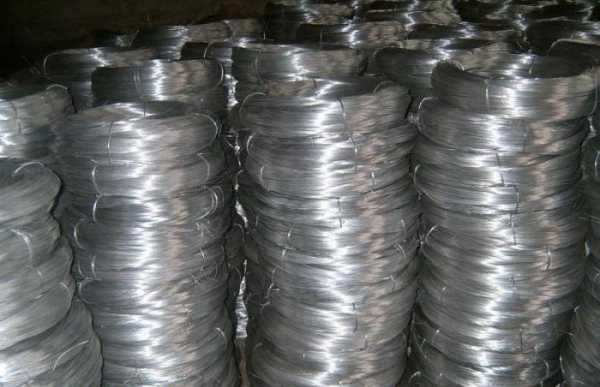
Вторая причина – это конструкция рессоры, которая включала в себя несколько листов углеродистой стали. Именно из этих элементов и можно было изготовить пару добротных ножей.
Третья причина – это высокая эластичность рессорной стали, которая позволяет проводить обработку материала, имея лишь минимальный набор инструментов.
Особенности ножей
Существенная причина, по которой именно этот вид стали стал обширно использоваться для производства ножей, – это состав самого продукта. На производстве данный состав получил название рессорно-пружинной стали 65Г. Как следует из названия, этот материал широко используется для производства рессор, пружин, шайб, а также некоторых других деталей. Стоимость именно этой марки стали считается одной из самых низких среди именно углеродистых материалов. Но при этом ее характеристики, то есть прочность, гибкость и ударная вязкость, находятся на высоте. Кроме того, твердость самой стали также увеличилась. Все эти особенности углеродистого металла также сыграли свою решающую роль при выборе материала для создания ножей.
Сталь 65Г
Рессорная сталь 65Г – это конструкционная высокоуглеродистая сталь, которая поставляется в соответствии с ГОСТом 14959. Такая марка относится к группе рессорно-пружинных сталей. Двумя наиболее важными требованиями, предъявляющимися к такому виду стали, являются высокая поверхностная прочность, а также повышенная упругость. Для того чтобы добиться необходимой прочности, в состав металла добавляют до 1 % марганца. Кроме того, чтобы достичь всех требуемых показателей, необходимо провести надлежащую термическую обработку деталей, изготовленных из этой марки.
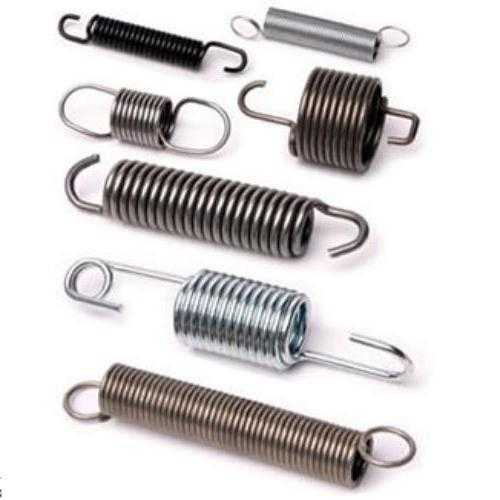
Широкое и эффективное использование данного вида стали обусловлено тем, что она принадлежит к классу экономнолегированных, то есть дешевых. Основными ингредиентами этого продукта стали такие компоненты, как:
- углерод, содержание которого составляет от 0,62 до 0,7 %;
- марганец, содержание которого не превышает от 0,9 до 1,2 %;
- содержание хрома и никеля в составе от 0,25 до 0,3 %.
Другие составляющие, которые входят в состав стали – сера, медь, фосфор и т. д. Это примеси, процентное содержание которых регламентируется государственным стандартом.
Термическая обработка
Существует несколько режимов термической обработки этого типа стали. Любой из них выбирается в соответствии с производственными требованиями, которые предъявляются к готовому продукту. Чаще всего используется два метода термической обработки, которые гарантируют получение необходимых свойств с химической и физической точки зрения. К этим способам относят нормализацию и закалку с последующим отпуском.
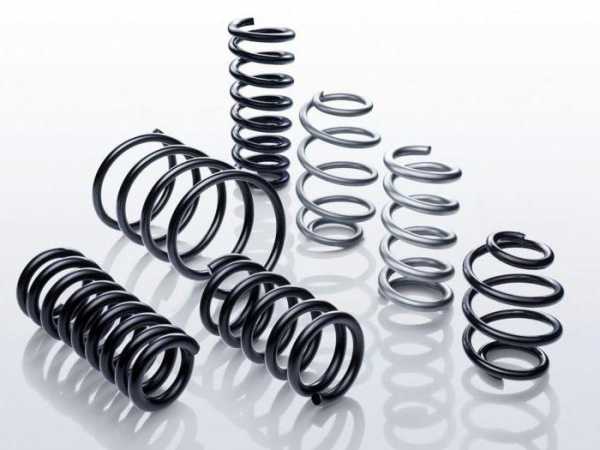
При проведении термической обработки необходимо правильно выбрать параметры температуры, а также времени, которое нужны для проведения операции. Чтобы верно выбрать эти характеристики, следует отталкиваться от того, какая марка стали используется. Так как материал марки 65Г принадлежит к доэвтектидному типу, то в составе этого продукта содержится аустенит, представленный в виде твердой механической смеси с небольшим количеством феррита. Аустенит является более твердым материалом с точки зрения структуры, чем феррит. Поэтому для проведения термической обработки стали 65Г, необходимо создавать более низкий интервал закалочных температур. Учитывая этот факт, подобные показатели для этого вида металла составляют от 800 до 830 градусов по Цельсию.
Режим закалки
Как закалить рессорную сталь? Необходимо создать нужный температурный режим, выбрать правильное время, а также верно рассчитать время и температуру отпуска. Для того чтобы придать стали все необходимые характеристики, которые задаются будущими техническими условиями эксплуатации детали, стоит провести нужную закалку. Для выбора подходящего режима проведения этой процедуры опираются на такие характеристики:
- Важным является не только способ закалки, но и оборудование, которое используется для нагрева стали.
- Подобрать необходимый температурный режим закалки.
- Подобрать подходящий временной промежуток для закалки стали.
- Выбрать нужную среду для проведений процесса закаливания.
- Также важно правильно подобрать технологию охлаждения детали после процесса закаливания.
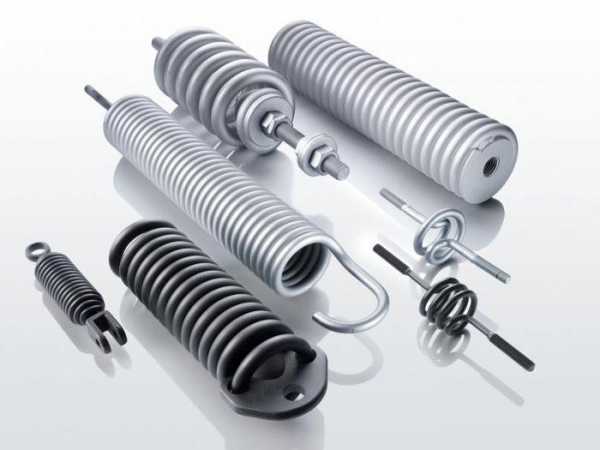
Марки рессорной стали
Поставка стали для изготовления рессоры осуществляется в виде полос. После этого из нее нарезают заготовки, закаливают, отпускают и собирают в виде пакетов. Марки рессорно-пружинной стали, такие как 65, 70, 75, 80 и т. д., характеризуются тем, что их релаксационная стойкость мала, особенно этот недостаток заметен при нагреве детали. Данные марки стали не могут быть использованы для работы в среде, температура которой превышает 100 градусов по Цельсию.
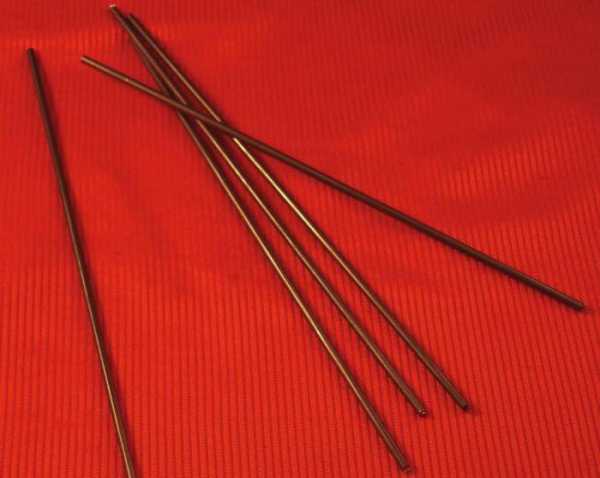
Существуют дешевые кремнистые марки 55С2, 60C2, 70СЗА. Их используют для изготовления пружин или же рессор, толщина которых не будет превышать 18 мм.
К более качественным маркам стали можно отнести 50ХФА, 50ХГФА. Если сравнивать с кремнемарганцовыми и кремнистыми материалами, то при отпуске температура намного выше – около 520 градусов. Из-за такой процедуры обработки эти марки стали характеризуются высокой теплостойкостью, а также малой чувствительностью к надрезу.
fb.ru
Производство и применение пружинной стали
При производстве пружинной стали получается материал с большим пределом текучести. Благодаря этому свойству все изделия, изготавливаемые из этого материала, способны принимать исходную форму даже после скручивания или значительного изгиба. Именно для производства упругих изделий, не испытывающих остаточную деформацию, и предназначаются эти материалы.
Сферы использования
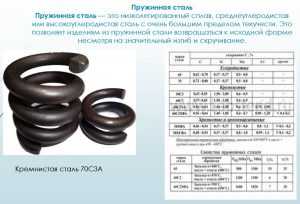
Пружинная сталь — это низколегированный сплав
Из пружинной стали изготавливается широкий ассортимент изделий и деталей, используемых в транспортных средствах, агрегатах и заводском оборудовании. Торсионы и рессоры, которые можно встретить в подвесках автомобилей и бронетехники, изготавливаются из стали марок 55C2, 60C2A и 70C3A. С недавнего времени для этих же целей стала использоваться сталь марки 50ХФА. Из нее же обычно изготавливаются клапана для пружин.
Детали для транспортных средств – не единственная сфера, в которой применяется пружинная сталь. Материалы из этой категории используются для изготовления отмычек, пружин для фрикционных дисков, а также для разного рода механизмов, в том числе производственных. Для тех или иных изделий и пружин подходит сталь определенных марок. Между ними есть большие отличия в плане важных эксплуатационных характеристик:
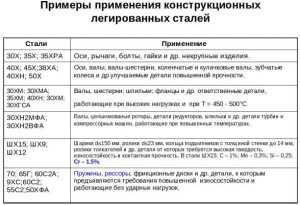
Примеры применения конструкционных легированных сталей
- 50ХГФА – применяются для создания часовых пружин;
- 55C2 – рессоры и пружины, используемые в подвеске транспортных средств;
- 60Г, 65 – для изготовления износостойких и вибростойких пружин, упорных шайб;
- KT-2 – для проката холоднокатаной проволоки.
Существуют и другие многочисленные марки, причем многие из них способны взаимозаменять друг друга. Например, сталь марки 68 может применяться вместо 65ГА, а сталь марки 70(Г) отлично заменяет 60Г. В ГОСТ можно обнаружить таблицы, в которых приведены все существующие марки с их режимами обработки и свойствами.
Состав и производство
Для сборки пружин и механизмов на их основе используется сталь, в состав которой входит от 0,5% до 0,75% углерода. В случае если содержание этого элемента превышает отметку 0,7%, материал называется инструментальной сталью. Это твердый и высокопрочный материал для изготовления разных инструментов. А также он применяется с целью создания пружин, максимально устойчивых к механическим воздействиям.
Углерод – не единственный элемент, оказывающий влияние на важные характеристики стали для пружин. При производстве металла в его состав намеренно вводятся легирующие компоненты в следующих концентрациях:
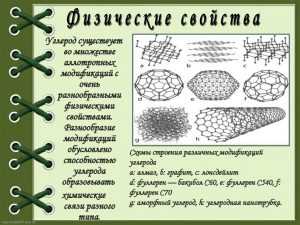
Углерод
- никель – до 1,7%;
- вольфрам – до 1,2%;
- хром – до 1,2%;
- ванадий – до 0,25%;
- марганец – до 1,25%;
- кремний – до 2,8%.
Важнейшим этапом производственного процесса является измельчение зерна. В результате сопротивляемость готового металла мелким пластическим деформациям значительно увеличивается. Это положительным образом сказывается на релаксационной стойкости пружин, которые изготавливаются из высоколегированных сталей.
Современные методы изготовления сплавов для создания пружин позволяют производить материалы с любым исполнением, любой поверхностью и диаметром, если речь идет о пружинной проволоке. Строго соблюдаются как отечественные, так и международные стандарты, определяющие эксплуатационные характеристики стали. Кроме того, осуществляется тщательный контроль качества за каждым этапом создания пружинных сплавов.
Маркировка
Маркировка стали для производства пружинных изделий довольно простая, но при этом информативная. По обозначению можно понять состав материала, которым определяются все его эксплуатационные свойства. Маркировка расшифровывается в направлении слева направо. Она включает в себя следующие позиции:
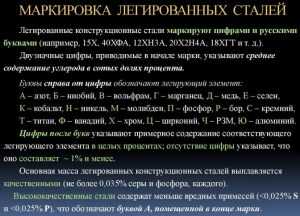
Маркировка стали
- первая позиция из двух цифр выражает массу углерода в сотых долях процента;
- вторая позиция из одной или нескольких букв указывает название легирующего элемента;
- третья позиция показывает округленную до целого значения долю легирующего элемента.
В случае если доля легирующего элемента в металле составляет менее 1,5%, в маркировке она не указывается. По обозначению можно легко понять, к какому виду принадлежит металл. Например, пружинная сталь марок 65, 70, 75, 80 и 85 относится к категории углеродистых. Материалы, в маркировке которых присутствует минимум две позиции, причисляются к легированным, так как в их составе высокая концентрация легирующих элементов.
Характеристики
Основными свойствами материалов для изготовления стальных тормозных лент, пружин и прочих изделий, являются высокая текучесть и упругость. Значительное увеличение упругости достигается путем закалки сплава в масле при высоких температурах в диапазоне от +820 °C до +870 °C. После закаливания обязательно проводится отпуск в диапазоне температур от +400 °C до +480 °C. Если есть необходимость в повышении таких свойств металла как прочность, вязкость и пластичность, на производстве прибегают к изотермическому закаливанию.
На основании характеристик материала для создания пружин выделяются следующие группы металлов:
Таблица расчетных значений сопротивления стали
- по химическому составу – обычный, нержавеющий, легированный металл;
- по способу обработки – калиброванный, горячекатаный, кованый прокат, со специальной отделкой.
Металлы, идущие на изготовление пружин, обязательно проверяются и нормируются по химическому составу. В этом случае прокат классифицируется по категориям. Всего существует 14 категорий, которые обозначаются маркировкой от 1 до 4Б включительно. По некоторым характеристикам нормирование не выполняется. Например, металлы категорий 1, 1A, 1Б не нормируются на наличие обезуглероженного слоя и прокаливаемость.
Основные требования
К ключевым характеристикам пружинного проката предъявляются строгие требования ГОСТ. Основной список технических требований регламентируется ГОСТ 14959-79. В нем содержится перечень как углеродистых, так и легированных марок стали. Там же описаны требования по отношению к маркировке, упаковке, правилам транспортировки, хранения и применения проката из пружинных сталей.
Перечень некоторых требований:
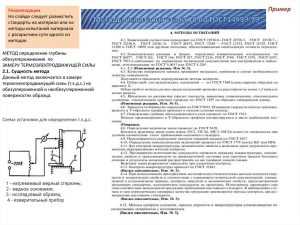
ГОСТ 14959-79
- максимальная массовая доля меди – 0,2%, остаточное содержание никеля – не более 0,25%;
- сталь марки 51ХФА может использоваться исключительно для изготовления упругой проволоки;
- максимальная массовая доля серы и фосфора в стали марки 60С2Г – не более 0,06%.
Некоторые требования к пружинной стали могут не соблюдаться. Например, вышеупомянутый ГОСТ допускает изменение концентрации марганца в составе сплава по желанию заказчика. Однако это действие допустимо только для тех пружинных сплавов, в составе которых нет таких легирующих элементов как никель и хром. А также не рекомендуется сильно отклоняться от таблиц, в которых указаны допустимые концентрации элементов.
Особенности сталей
Рессорно-пружинная сталь – ряд марок, в процессе создания которой применяется метод пластической холодной деформации. Для реализации этого метода могут использоваться дробеструйные и гидроабразивные технологии. Специфические методы, используемые при производстве пружинных металлов, наделяют сплав не только положительными, но и отрицательными качествами. К минусам таких материалов можно отнести:
- сложность разрезания – этот процесс возможен, однако затрудняется обработка готовых изделий;
- плохая свариваемость – металлы для производства пружин совсем не предназначены для сваривания.
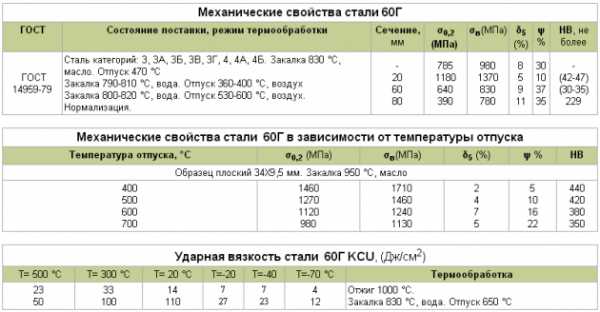
Сталь 60Г — рессорно-пружинная
Отдельно надо выделить такую разновидность металлов как коррозионностойкая сталь. Это марка специального назначения, главной ее особенностью является высокая устойчивость к коррозионному разрушению. С целью наделения материала такими характеристиками в его состав добавляют легирующие элементы – никель и хром. Содержание никеля варьируется от 9 до 12%, а хрома – от 13 до 27%, в зависимости от необходимых свойств.
В целом пружинный металл пользуется высокой востребованностью, даже несмотря на некоторые недостатки. Применение таких материалов не ограничивается пружинами, фрикционными дисками и рессорами. Сталь используется и в фортепианных струнах, для проката проволоки и других целей.
Видео по теме: Как изготавливают сверхпрочные пружины
promzn.ru
Пружинные стали
Казанский Государственный Технический Университет им. А. Н. Туполева
Институт авиации, наземного транспорта и энергетики
Кафедра: «Материаловедение и структура образующих технологий»
Дисциплина: «Материаловедение ч.2»
Курсовая работа
Тема: «Пружинные стали»
Выполнена:
Проверил:
Елабуга , 2009 г.
План:
1. Описание
2. Применение
3. Маркировка и основные характеристики
4. Особенность вальцовки пружинной стали
5. Основные требования, предъявляемые к рессорно-пружинной стали
6. Характеристика материала 68А
7. Литература
Описание:
Пружинная сталь — сталь, предназначенная для изготовления упругих элементов (пружин, рессор и т.д.)
Работа пружин, рессор и тому подобных деталей характеризуется тем, что в них используют только упругие свойства стали. Большая суммарная величина упругой деформации пружины (рессоры и т. д.) определяется ее конструкцией — числом и диаметром витков, длиной пружины. Поскольку возникновение пластической деформации в пружинах не допускается, то от материала подобных изделий не требуется высокой ударной вязкости и высокой пластичности. Главное требование состоит в том, чтобы сталь имела высокий предел упругости (текучести). Это достигается закалкой с последующим отпуском при температуре в районе 300—400° С. При такой температуре отпуска предел упругости (текучести) получает наиболее высокое значение, а то, что эта температура лежит в интервале развития отпускной хрупкости I рода, в силу отмеченного выше обстоятельства не имеет большого значения.
Пружины, рессоры и подобные им детали изготавливают из конструкционных сталей с повышенным содержанием углерода (но, как правило, все же более низким, чем у инструментальных сталей) — приблизительно в пределах 0,5—0,7% С, часто с добавками марганца и кремния. Для особо ответственных пружин применяют сталь 50ХФ, содержащую хром и ванадий и обладающую наиболее высокими упругими свойствами. Термическая обработка пружин и рессор из легированных сталей заключается в закалке от 800—850° С (в зависимости от марки стали) в масле или в воде с последующим отпуском в районе 400—500° С на твердость НRС 35—45. Это соответствует ст в = 1304-1600 кгс/мм2 .
Иногда такой термической обработке подвергают детали конструкций большой длины и с тонкими стенками, которые должны обладать высокими пружинящими свойствами. В этом случае применяют сталь ЗОХГС; после закалки и отпуска при 250° С она будет иметь прочность (ав ) 160 кгс/мм2 , но вязкость (ад ) всего лишь 5 кгс-м/см2 , а пластичность (б) 7% и (ф.) 40%. Часто пружины изготавливают из шлифованной холоднотянутой проволоки (так называемой серебрянки). Наклеп (нагартовка) от холодной протяжки создает высокую твердость и упругость. После навивки (или другого способа изготовления) пружину следует отпустить при 250—350°С для снятия внутренних напряжений, что повысит предел упругости. Для изготовления серебрянки применяют обычные углеродистые инструментальные стали У7, У8, У9, У10.
На качество и работоспособность пружины большое влияние оказывает состояние поверхности. При наличии трещин, плен и других поверхностных дефектов пружины оказываются нестойкими в работе и разрушаются, вследствие развития усталостных явлений в местах концентрации напряжений вокруг этих дефектов. Кроме обычных пружинных материалов, имеются и специальные, работающие в специфических условиях (повышенные температуры, агрессивные среды, и т. д.).
Общая характеристика: сталь рессорно-пружинная, малочувствительна к флокенообразованию, склонна к отпускной хрупкости при содержании Mn≥1%, не применяется для сварных конструкций. Плотность при 20°С – 7,81х10³кг/м³. Модуль нормальной упругости при 20°С – 215 Гпа. Удельная теплоёмкость при 20-100°С – 490 Дж/(кг·°С)
Они работают в области упругой деформации металла под воздействием циклических нагрузок. Поэтому они должны иметь высокое значение предела упругости, текучести, выносливости при необходимости пластичности и высоком сопротивлении хрупкому разрушению.
Пружинные стали содержат С = 0,5 – 0,75% , Si до 2,8%, Mn до 1,2%, Cr до 1,2%, V до 0,25%, Bе до 1,2%, Ni до 1,7%. При этом происходит измельчение зерна, способствующее возрастанию сопротивления стали малым пластическим деформациям, а следовательно, ее релаксационной стойкости. Широкое применение на транспорте нашли кремнистые стали 55С2, 60С2А, 70С3А. Однако они могут подвергаться обезуглероживанию, графитизации, резко снижающим характеристики упругости и выносливости материала. Устранение указанных дефектов, а также повышение прокаливаемости и торможение роста зерна при нагреве достигается дополнительным введением в кремнистые стали хрома, ванадия, вольфрама и никеля. Для изготовления пружин также используют холоднотянутую проволоку (или ленту) из высокоуглеродистых сталей 65, 65Г, 70, У8, У10 и др.. Применяются также пружины специального назначения из мартенситных сталей 30Х13А, мартенситно – стареющих 03Х12Н10Д2Т, аустенитно-мартенситных 09Х15Н8Ю и других сталей и сплавов. Стали закаливают с температур 830 – 880°С и отпускают на тростит (380 – 550°С).
Имеют высокий предел текучести. Отношение предела текучести к пределу прочности 0,8−0,9. Для листовых рессор и пружин подвесок применяют кремнистые и марганцовистые стали 50ХГ, 50Г2, 05Г, 55С2 и др. Для торсионных валов используются стали 45ХНМФА, G0C2A, 70СЗА.
Для повышения усталостной прочности деталей, работающих при высоких колебательных нагрузках, необходимо обеспечить в поверхностном слое создание остаточных сжимающих напряжений. С этой целью применяют заневоливание пружин, заневоливание и чеканку торсионных валов, обкатку роликами, пластическую осадку и дробеструйную обработку листовых рессор. Легированная рессорно-пружинная сталь, термообработанная до твердости HRC 45—50, имеет предел усталости при кручении 190 МПа. После дробеструйной обработки предел усталости увеличивается до 350 МПа (3500 кгс/см2).
Применение:
Пружины, рессоры, упорные шайбы, тормозные ленты, фрикционные диски, шестерни, фланцы, корпусы подшипников, зажимные и подающие цанги и другие детали, к которым предъявляются требования повышенной износостойкости, и детали, работающие без ударных нагрузок.
Виды поставляемой продукции: в горячекатаном состоянии (без термообработки) с твёрдостью не более НВ285; в высокоотпущенном состоянии – не более НВ241
Маркировка и основные характеристики:
Марки пружинных сталей:
Основные механические свойства рессорно-пружинной стали после специальной термической обработки.
mirznanii.com
характеристики, свойства, марки, ГОСТ. Изделия из пружинной стали
Начать стоит с того, что любая пружина, рессора и другие подобные элементы эксплуатируются в условиях жесткой и постоянной упругой деформации. Кроме этого, большинство деталей подвергается еще и циклическим нагрузкам. Именно по этим причинам к пружинной стали предъявляются высокие требования по упругости, текучести, выносливости, пластичности, а также важно наличие необходимого сопротивления к хрупкому разрушению.
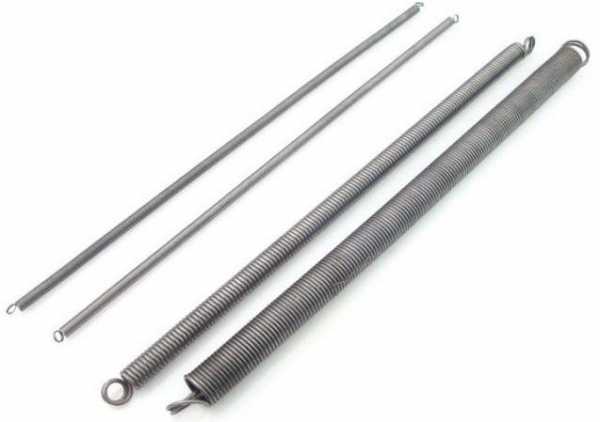
Состав
В состав стали, которая подходит для производства пружин и рессор входит от 0,5% до 0,75% углерода. Дополнительными требования к содержанию легирующих элементов при производстве следующие:
- содержание кремния в пружинной стали до 2,8%;
- содержание марганца до 1,2%;
- легирование хромом достигает 1,2%;
- содержание ванадия до 0,25%;
- легирование вольфрамом до 1,2%;
- содержание никеля до 1,7%.
Также здесь важно добавить, что при производстве стали осуществляется процесс измельчения зерна, который способствует возрастанию сопротивления металла к малым пластическим деформациям. Это, в свою очередь, увеличивает релаксационную стойкость изделия из пружинной стали.
Применение
Довольно широкое применение в транспортных средствах нашли изделия из таких марок стали, как 55С2, 60С2А, 70С3А. Но здесь нужно знать, что этот материал подвержен таким дефектам, как обезуглероживание или графитизация. Эти недостатки опасны тем, что они сильно снижают характеристики упругости, а также прочности материала. Для того чтобы избежать этих дефектов и их негативного влияния на пружинную сталь, в нее и добавляют те элементы, которые были указаны выше.
Лучшими показателями в отличие от кремнистой разновидности сплава обладает марка 50ХФА. Этот вид материала стал больше всего использоваться для изготовления автомобильных рессор. Также этот тип стали очень часто используется для производства клапанов пружин, так как он не подвержен обезуглероживанию. Но тут стоит добавить, что она обладает малой прокаливаемостью.
Работа пружин
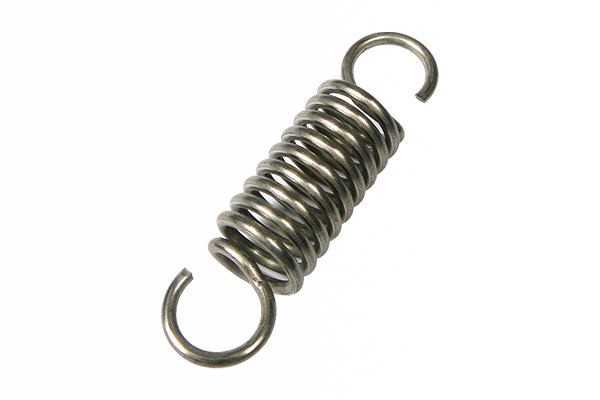
Здесь важно понимать, что работа любой пружины, рессоры или любой другой детали из пружинной стали характеризуется только тем, что используются лишь упругие свойства материала. Суммарная величина их упругости определяется особенностями конструкции. Решающим показателем здесь будет количество витков, их диаметр, а также длина самого изделия. Еще один важный момент, который необходимо отметить – это пластическая деформация. Это в пружинах чаще всего не допускается, а потому от материала, который используется для производства пружин, не требуется наличия высокой ударной вязкости или показателя пластичности. Основное требование – это параметр упругости. Верхний предел этой характеристики должен быть довольно велик. Для того чтобы достичь требуемого параметра, сталь подвергают закалке под воздействием высоких температур, а после проводят отпуск материала при температуре в 300-400 градусов по Цельсию.
Свойства
Основное свойство пружинной стали – это текучесть(упругость). Максимальный показатель этого параметра достигается только при температурах, указанных выше. Однако если отпускать материал при таких градусах, то отпускная хрупкость окончательного продукта будет находиться в первом роде. Как уже говорилось ранее, ударная вязкость не имеет принципиального значения.
Еще одно из свойств стали касается ее состава. Оно выражается в том, что содержание углерода в ней больше, чем в других сплавах. Хотя, если сравнивать с инструментальной сталью, все же меньше.
Для обычного процесса легирования используют марганец и кремний. Для более ответственных пружин или рессор в качестве добавок применяют хром и ванадий. Эти два элемента придают им повышенную упругость. Можно добавить, что для достижения наилучших эксплуатационных свойств сталь часто подвергают закалке в масле или воде.
Виды и марки стали
Марки пружинной стали делятся на множество различных групп. Существуют материалы общего назначения. К ним относят марки 65, 70, 75, У9А. Из этого продукта изготавливают пружины для машин с небольшим сечением. К особым свойствам этих деталей можно отнести их пониженную релаксационную стойкость.
Кремнистые стали марок 55С2, 60С, 60С2 применяются для создания таких элементов, как пружины и рессоры, использующиеся в автомобильной, автотракторной промышленности, а также в железнодорожной промышленности. Тут важно добавить, что эти элементы склонны к обезуглероживанию. Каких-либо особых свойств у этой стали не имеется.
Еще одна разновидность стали – это комплексно легированная. Данный продукт выпускается под марками 50ХФА и 60С2ХФА. К использованию этого материала прибегают в том случае, если необходимо создать пружины или рессоры для важных деталей. Стойкость к температурному воздействию у этого материала составляет до +300 градусов Цельсия.
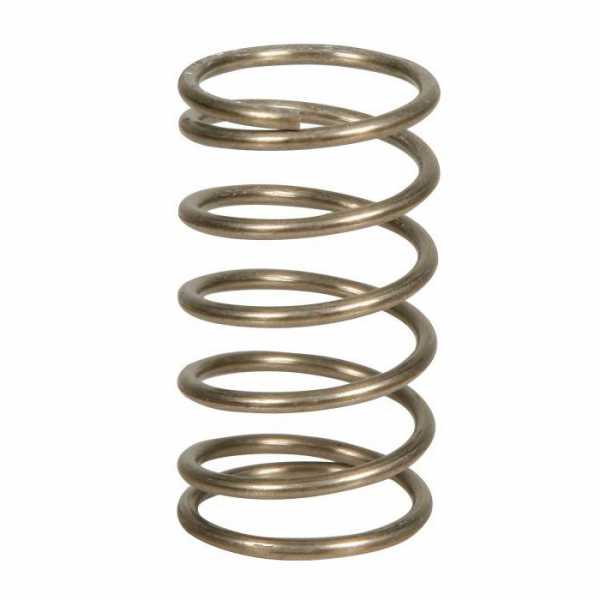
Можно выделить также стали специального назначения. К ним принадлежат такие продукты мартенситного класса 30Х13, 40Х13. Они используются для производства обычных пружин или рессор, однако обладают особыми свойствами. Характеристика пружинной стали этой марки состоит в том, что у нее повышенная стойкость к коррозии, повышенная жаропрочность (до 550 градусов Цельсия), а также выраженные магнитные свойства.
Требования по ГОСТ
Для пружинных сталей, как и для другой самой разнообразной продукции, был принят ГОСТ. Он устанавливает все правила, касающиеся материала. К примеру, там описаны следующие технические требования.
- Массовая доля такого вещества, как медь не должна превышать 0,2%. А остаточное количество никеля не должно быть выше, чем 0,25%.
- Для такой марки стали, как 60С2Г, существует отдельное требование, которое гласит, что суммарная массовая доля серы и фосфора не должна быть выше 0,06%.
- Такая марка стали, как 51ХФА по ГОСТ предназначается лишь для производства пружинной проволоки.
- ГОСТ пружинной стали также предписывает, что по индивидуальному заказу потребителя массовая доля, содержащегося в стали марганца, может быть уменьшена, несмотря на предписания, которые указываются в таблице, имеющейся в том же документе. Это при условии, что сплав не подвергался легированию хромом и никелем.
Коррозионностойкая сталь
Одна из марок стали специального назначения отличается тем, что у нее имеется повышенная стойкость к коррозии. Для того чтобы максимально повысить сопротивляемость материала к разрушающему ее процессу, в него добавляют и хром, и никель в количестве от 13 до 27% и от 9 до 12% соответственно. Другими словами, эти продукты относятся к группе высоколегированных сталей.
Основным аустенитообразующим элементом в таком продукте является никель. В то время как марганец, к примеру, влияет на образование аустенита слабее, эффект от его использования ниже практически в два раза. Если необходимо еще сильнее расширить аустенитную область, то можно использовать такие вещества, как углерод или азот.
fb.ru
Рессорно-пружинная сталь
Сталь, обладающая высоким пределом упругости (текучести).Для получения высоких упругих характеристик рессорно-пружинные стали подвергают закалке с последующим среднетемпературным отпуском для получения в структуре троостита. Для достижения более высоких эксплуатационных характеристик используют стали, легированные кремнием, хромом и ванадием.
Характерным признаком рессорно-пружинных сталей является наличие в них углерода в количестве 0,5…0,8 %. По составу эти стали могут быть как углеродистыми, так и легированными. Рессорно-пружинные стали, прежде всего, должны обладать высоким пределом текучести, что обеспечивает высокие упругие свойства. Это достигается закалкой с последующим средним отпуском. Температура отпуска должна выбираться в пределах 350–500 °С (иногда, в зависимости от состава и назначения может доходить и до 600 °С). Кроме того, они должны обладать высоким пределом выносливости и достаточно высоким пределом прочности. А вот пластичность этих сталей должна быть пониженной (5–10 % по относительному удлинению и 20–35 % по относительному сужению). Это связано с тем, что в рессорах и пружинах не допускается пластическая деформация.
Углеродистые стали используются для изготовления пружин небольшого сечения, работающих при невысоких напряжениях. Закалка этих сталей проводится в масле. В таблице 1 приведены режимы термической обработки, механические свойства (минимальные) и предел выносливости (расчетный) для углеродистых сталей.
Примечание
- Предел выносливости вычислен по формулам: σ-1 = 0,29σВ + 79,2 и σ-1 = 0,45σ0,2 + 95,4.
- К недостаткам углеродистых пружинных сталей следует отнести невысокий предел упругости и невысокую прокаливаемость. Критический диаметр этих сталей при закалке в масле не превышает 25 мм.
Примечаниe
- Для сталей марок 50С2, 55С2 и 60С2 отжиг может быть заменен высоким отпуском.
- Для сталей 50С2 и 55С2 закалку можно проводить в воде.
К недостаткам этих сталей следует отнести их склонность к обезуглероживанию и образованию поверхностных дефектов в процессе горячей обработки, приводящих к снижению предела выносливости. В целях предотвращения образования указанных дефектов, кремнистые стали дополнительно легируют хромом, марганцем, ванадием, никелем и вольфрамом.
Режимы термической обработки кремнистых рессорно-пружинных сталей приведены в таблице 2.
Сталь 60С2ХА идет для изготовления крупных пружин ответственного назначения. При закалке в масле она прокаливается на глубину до 50 мм. Недостатком этой стали является ее склонность к обрыву в процессе волочения.
Стали марок 60С2Н2А и 60С2ХФА обладают более высокой прокаливаемостью (до 80 мм) и применяются для изготовления пружин особо ответственного назначения. При этом сталь 60С2Н2А обладает наилучшим сочетанием технологических и эксплуатационных свойств. Общий недостаток кремнистых рессорно-пружинных сталей заключается в их повышенной чувствительности к внешним поверхностным дефектам (царапины, риски, забоины), играющим роль концентраторов внутренних напряжений, вследствие чего снижается предел выносливости. Поэтому в настоящее время в практике широко применяются бескремнистые рессорно-пружинные стали.
При одной и той же концентрации углерода, что и у кремнистых сталей, кремний в них заменяется следующими возможными сочетаниями легирующих элементов: хром + марганец, хром + ванадий, хром + марганец + ванадий, хром + марганец + бор. Например, 50ХГ, 50ХФ, 50ХГФ, 55ХГР. Эти стали обладают повышенной вязкостью и менее чувствительны к надрезу. ля повышения эксплуатационных характеристик, особенно для пружин, работающих при длительных знакопеременных нагрузках, назначают обдувку поверхности пружин дробью. Возникающие при этом в поверхностном слое напряжения сжатия приводят к повышению предела выносливости.
Наиболее высокие механические и эксплуатационные характеристики можно получить в процессе холодной протяжки предварительно патентированной проволоки, диаметром до 2 мм из углеродистой стали, подвергавшейся высоким степеням обжатия (70–90 %).
Процесс патентирования проводится между протяжками. Он заключается в нагреве проволоки на 50–100 °С свыше точки Ас3 с последующим охлаждением в ванне с расплавленным свинцом. Температура расплава должна составлять 450–550 °С. В результате такой термической обработки происходит изотермический распад аустенита с образованием тонкопластинчатого сорбита.
sl3d.ru