Расчет скорости коррозии трубопроводов: Расчет скорости коррозии и оценка срока службы трубопроводов
alexxlab | 08.02.2023 | 0 | Разное
| ||||||||||||||||||||||||||||||||||||||||||||||||||||
|
||||||||||||||||||||||||||||||||||||||||||||||||||||
Расчет – скорость – коррозия
Cтраница 1
Определение скорости саморастворения по кривым поляризации. [1] |
Расчет скорости коррозии по методу, описанному выше, оказывается возможным в тех случаях, когда мы имеем дело с исключительно однородными поверхностями. Для неоднородных поверхностей подобные расчеты сопряжены со значительными трудностями. Дело в том, что анодная реакция ионизации металлов протекает, в силу структурных особенностей поверхности сплава, не с одинаковой скоростью в различных точках.
[2]
Расчет скорости коррозии ведут по количеству водорода и уравнению реакции металла с водой. [3]
Водородный корро-зиометр. [4] |
Расчет скорости коррозии в данной работе производится, исходя из объема газа, собранного в бюретке за все время опыта, что дает значение средней скорости. [5]
Кривые термического анализа литьевого углеродно-полимерного материала на основе ре-зольного фенолоформальдегидно.| Зависимость пред прочности при сжатии 6СХ г. [6] |
Дня расчета скорости коррозии материала образцов определяли их поверхность, контактирующую с реагентом, по методу сорбции ме-тиленовой голубой.
[7]
При расчетах скорости коррозии рекомендуется учесть следующее. В этом случае пересчет показателей не требуется. [8]
При расчетах скорости коррозии рекомендуется учитывать следующее. Для вод со значением рН 6 8 ( конденсаты, химически обессоленная, Na -, Н – Na-катиониро-ванная и сырая вода при индексе насыщения / 0) эксплуатационные потери металла практически совпадают с потерями металла, определенными в лабораторных и стендовых условиях. В этом случае пересчет показателей не требуется. [9]
При расчетах скорости коррозии используется построение катодной и анодной поляризационных кривых для образца изучаемого металла. [10]
Графический метод расчета скорости коррозии позволяет в отличие от аналитического рассчитать величину коррозии для весьма сложных случаев, соответствующих реальным условиям протекания коррозионного процесса. [11]
Графический метод расчета скорости коррозии позволяет в отличие от аналитического рассчитать величину коррозии для весьма сложных случаев, соответствующих реальным условиям протекания коррозионного процесса.
[12]
Приведенные основные положения расчета скорости коррозии применимы и для стальных газоходов. [13]
Следующим этапом исследований является расчет скорости коррозии в каждом сечении трубопровода с учетом напряженного состояния и инженерно-геологических особенностей соответствующего участка трассы. Затем формируется прогноз коррозионного износа и малоцикловой усталости для каждого участка трубопровода вдоль трассы. Результаты этого расчета используются для оценки риска аварии на каждом участке трассы. [14]
Для использования этого метода расчета скорости коррозии металлов необходимы накопление и систематизация экспериментального материала по коррозии металлов в различных метеорологических условиях. [15]
Страницы: 1 2 3 4
Материалы – коррозия и допуск на коррозию
Зная ожидаемую общую скорость коррозии и предполагаемый срок службы или срок службы детали, проектировщик может рассчитать дополнительную толщину, необходимую для коррозионной стойкости проектируемого технологического оборудования.
После определения толщины стенки, которая соответствует механическим требованиям, таким как давление, температура и вес оборудования, к толщине стенки добавляется дополнительная толщина, называемая «припуском на коррозию», чтобы компенсировать ожидаемую потерю металла в течение срока службы оборудование. Затем, поскольку глубина проникновения очень велика, поправке на коррозию присваивается коэффициент безопасности, равный двум.
Пример..
Стенка резервуара должна иметь толщину 5 мм по механическим соображениям. Проектировщик определил, что скорость коррозии составит 0,4 мм/год, а ожидаемый срок службы резервуара составит 10 лет. Суммарный припуск на коррозию – это скорость коррозии в год (0,4 мм x 10 лет = 4 мм).
Из соображений безопасности допуск на коррозию удвоен до 8 мм.
Расчет допусков на коррозию
Допуски на коррозию определяются не только проектировщиком, но также и особенно государственными или местными органами. Последние часто имеют многолетний опыт работы с местными условиями и особенно с погодными условиями в соответствующем районе.
Влажность, температура, дождь, ветер, примеси и время намокания металла влияют на скорость коррозии. Коррозия возникает при относительной влажности воздуха от 70 до 80%. Коррозионная реакция возможна, как правило, при температуре выше 0°C и относительной влажности более 80% (поверхность влажная). Примеси воздуха, растворяющиеся в конденсате или дождевой воде, могут ускорить коррозию. Оседание пыли и грязи на поверхности металла ускоряет атмосферную коррозию.
Скорость коррозии выражается в миллиметрах в год поверхностных потерь и используется для обеспечения допуска на коррозию при проектной толщине оборудования, такого как сосуды и трубопроводы.
Операторы часто используют данные, основанные на историческом опыте работы завода, чтобы помочь им определить соответствующие припуски на коррозию. В качестве альтернативы широко доступны диаграммы коррозии, которые показывают скорость коррозии для многих комбинаций конструкционных материалов и технологических жидкостей, и обычно для различных температур процесса предоставляется диапазон значений.
В некоторых случаях, особенно при наличии смеси химических веществ, соответствующие данные могут отсутствовать, и для определения пригодности оборудования могут потребоваться испытания на коррозию. Операторы должны быть в состоянии продемонстрировать использование допусков на коррозию в спецификации и конструкции оборудования. Источники используемых данных должны быть прослеживаемыми.
AMPP – Ассоциация материалов
Защита и эксплуатационные характеристики
Насколько мне известно, в ASME B31.3 не существует допусков на коррозию. Допуски на коррозию обычно устанавливаются конечным пользователем и в некоторой степени основаны на личных предпочтениях и отраслевых традициях. 1,5 мм для трубопровода является общепринятым стандартом, но вы можете установить допуск на коррозию по своему усмотрению, если только государственное или местное агентство не приняло и не заменило B31.3. Чтобы указать трубу, добавьте допуск на коррозию к минимальной расчетной толщине и выберите спецификацию трубы, которая равна или больше минимума + допуск на коррозию.
Ниже приведены две таблицы с рекомендациями по припуску на коррозию
Припуск на коррозию для стальных труб | мм |
Перегретый пар | 0,3 |
Насыщенный пар | 0,8 |
Паровые змеевики в грузовых танках и баках для жидкого топлива | 2,0 |
Питательная вода для котлов в системах открытого цикла | 1,5 |
Питательная вода для котлов в системах замкнутого цикла | 0,5 |
Системы продувки котлов | 1,5 |
Сжатый воздух | 1,0 |
Гидравлическое масло | 0,3 |
Смазочное масло | 0,3 |
Мазут | 1,0 |
Термомасло | 1,0 |
Пресная вода | 0,8 |
Морская вода | 3,0 |
Хладагенты, указанные в Разделе 13 | 0,3 |
Грузовые системы для нефтяных танкеров | 2,0 |
Грузовые системы для судов, перевозящих сжиженные газы | 0,3 |
Примечания. .
- Для труб, проходящих через резервуары, необходимо учитывать дополнительный припуск на коррозию, чтобы учесть внешнюю коррозию.
- Примечание 2. Припуск на коррозию труб, эффективно защищенных от коррозии, может быть уменьшен не более чем на 50 %.
- Примечание 3. Когда коррозионная стойкость легированных сталей подтверждена надлежащим образом, допуском на коррозию можно пренебречь.
Припуск на коррозию для труб из цветных металлов | мм |
Медь | 0,8 |
Латунь | 0,8 |
Медно-оловянные сплавы | 0,8 |
Медно-никелевые сплавы с содержанием Ni менее 10 % | 0,8 |
Медно-никелевые сплавы с содержанием Ni не менее 10 % | 0,5 |
Алюминий и алюминиевые сплавы | 0,5 |
Примечания..
- Допуск на коррозию для других материалов будет специально рассмотрен Обществом.
Если их коррозионная стойкость подтверждена надлежащим образом, допуск на коррозию можно не принимать во внимание.
- Примечание 2. В случае сред с высокой коррозионной активностью Общество может потребовать более высокий допуск на коррозию.
Интересные статьи
Допуск на коррозию, общий
Допуск на коррозию — это мера, используемая при техническом обслуживании.
Допуск на коррозию 3,0 мм означает, что, например, толщина стенки без проблем может быть уменьшена на 3,0 мм.
Имейте в виду, это не означает, что достигнута минимальная толщина стенки и срок службы объекта истек.
Пример.. часть оборудования имеет толщину стенки 10 мм с допуском на коррозию 3,0 мм. При толщине стенки 7,0 мм действие требуется, так как указанный припуск на коррозию полностью израсходован.
Обратите внимание, когда припуск на коррозию израсходован почти полностью.
- Какова скорость коррозии. Является ли это линейным или прогрессивным произошло.
- Какая толщина стены была при строительстве.
- Доступны ли базовые измерения.
- Изменились ли условия процесса.
- Возникла эрозия в сочетании с коррозией.
- Можем ли мы получить следующий период проверки.
- Какая необходима толщина стенки конструкции.
- Должны ли мы сделать перерасчет.
- Контроль толщины стенки в процессе (превентивный контроль).
- Необходимо заменить оборудование при следующем отключении.
- Должен быть тот же материал, что и при возможной замене.
- Измерения толщины стенок достоверны.
Краска и температура могут повлиять на результаты измерения. - Произошел ли спад внутренний или внешний, или их комбинация.
- Может ли оборудование оставаться в эксплуатации или оно должно быть выведено из эксплуатации.
Примечания автора…
Мое мнение о припуске на коррозию
- Джентльмен по имени Аллен Хейзен, блестящий студент-химик Массачусетского технологического института в 1888 году, говорит.
..
«Я чувствую, что обычно не очень выгодно увеличивать толщину стальных пластин из-за этого соображения (а именно, что утолщение пластин не устраняет проблему, а просто продлевает срок службы металла), но что деньги лучше потратить на лучшее покрытие и более тщательный осмотр стальных листов, или, другими словами, на предотвращение питтинга вместо того, чтобы пытаться сделать лист достаточно толстым, чтобы питтинг не проходил через него».
Это заявление г-на Хейзена должно подумать о припуске на коррозию… или нет? - Только после долгих жизненных испытаний, думаю, можно приблизиться к реальности.
Расчеты зависят от сотен факторов и, на мой взгляд, не дают гарантии того, что будет применен надлежащий допуск на коррозию.
Я работал на технологическом предприятии с минимальным сроком службы 15-20 лет.
Спустя 7 лет (вероятнее, раньше) были выявлены первые серьезные проблемы с коррозией, а одной из самых крупных и опытных инжиниринговых компаний завод был спроектирован.
Хорошо, инженерные компании имеют большой опыт и выполнят наилучшую обработку поверхности, но… Если будет найдена правильная спецификация краски, к сожалению, есть много других проблем, которые все еще вызывают коррозию. - Как инжиниринговая компания может гарантировать, что при строительстве нового завода все монтажные швы получат надлежащую обработку поверхности? Нет гарантии !
- Как инжиниринговая компания может гарантировать, что после завершения строительства нового завода вся изоляция будет водонепроницаемой? Нет гарантии !
- Как инжиниринговая компания может гарантировать это… и т.д.
Мы, люди, можем многое, но бессильны против Матери-Природы.
Определение скорости коррозии | Харт Энерджи
Джорджио Г.Дж. Achterbosch, N.V. Nederlandse Gasunie, Гронинген, Нидерланды;
и Lech A. Grzelak, Делфтский технологический университет, Делфт, Нидерланды
Внутритрубные проверки являются частью усилий компании Gasunie по проверке целостности трубопроводов с конца 1970-х годов. Несколько лет назад обнаружение внешней микробной коррозии (ВМК) на одном из трубопроводов высокого давления изменило политику инспекций с проверки произвольно выбранного трубопровода раз в пять лет на программу инспекции всей сети высокого давления (приблизительно 5600 км или 3500 миль) будет завершено через 10-12 лет.
Одна из линий, подверженных влиянию MIC, используется для квалификации свиней MFL от разных поставщиков. В период с 1999 по 2004 год было проведено четыре различных квалификационных захода MFL, в результате которых было проведено 18 раскопок. Скорости коррозии, которые были определены довольно простыми расчетами после каждого прохода скребков, показали значения от 0,2 до 0,3 мм/год в качестве среднего значения для коррозии MIC.
После четвертого прохода скребков (через пять лет после первого) компания Gasunie решила определить скорость коррозии более сложным способом. Статистический анализ был выполнен в сотрудничестве с математическим факультетом Технического университета Делфта. Цель заключалась в том, чтобы использовать данные проходок и раскопок скребков для выделения подходящего подмножества коррозионных дефектов, по которым можно было бы определить скорость коррозии.
Было решено использовать только те дефекты, которые были указаны всеми поставщиками как внешняя коррозия, тем самым исключив дефекты, которые были обозначены как «фрезерный дефект, но, возможно, коррозия». Второй критерий заключался в том, что о дефекте должны были сообщить не менее трех из четырех поставщиков. Эти критерии привели к анализу подмножества из 52 дефектов.
Все сообщенные глубины дефектов были скорректированы на систематическую ошибку, которая была определена по результатам раскопок. Затем скорректированные значения использовались для расчета скорости коррозии с использованием трех подходов. Два из них включали расчет скорости коррозии для каждого дефекта; третья определяла скорость коррозии совокупности дефектов, предполагая линейный во времени рост коррозии. Анализ проводился, начиная с самых простых и заканчивая более сложными моделями. Первый и второй подходы просто основывались на безусловном регрессионном анализе. Третья и последняя модель была основана на беспристрастных измерениях и точности свиней. Средняя скорость коррозии дефектов находилась в диапазоне от 0,12 до 0,24 мм/год. Разделение набора данных на глубокие и мелкие дефекты показало, что средние скорости коррозии для обоих подмножеств, 0,23 мм/год и 0,25 мм/год, существенно не различаются. Это подтверждает одно из предположений о том, что скорость коррозии постоянна.
Осмотры и раскопки
Газотранспортная сеть N.V. Nederlandse Gasunie состоит примерно из 11 600 км (примерно 7 200 миль) стальных трубопроводов (диаметром от 4 до 48 дюймов), которые в основном были построены в середине 1960-х и начале 1970-х годов. . Сеть разделена на часть высокого давления (5600 км, 66-80 бар) и часть среднего давления (600 км, 40 бар). В то время как сеть высокого давления является скребковой, часть среднего давления не имеет средств для запуска и приема интеллектуальных скребков.
До 1999 года у Gasunie не было никаких признаков коррозии на одном из ее трубопроводов. Как регулярные измерения CP, так и наблюдения во время раскопок или изменения маршрута показали, что не существует серьезной проблемы с коррозией. Тем не менее, с 1979 года политика компании заключалась в периодической проверке целостности трубопровода путем запуска интеллектуального скребка через одну из линий высокого давления в среднем раз в пять лет. Результаты этих прогонов скребков подтвердили существующее мнение об отсутствии проблем с коррозией.
В 1999 году 70-км, 36-дюймовый. линия на севере Нидерландов была проинспектирована скребком MFL в рамках программы проверки. Результаты проходки скребка показали 65 признаков внешней коррозии, но отсутствие внутренней коррозии. После тщательной оценки дефектов отделом безопасности было решено, что необходимо раскопать и отремонтировать шесть указателей. Первые раскопки к концу 1999 года привели к неприятному сюрпризу. При раскопках коррозионный дефект оказался полностью отличным от тех немногих коррозионных дефектов, с которыми Гасуни сталкивался в прошлом. Анализ продуктов коррозии и внешний вид дефекта позволил сделать вывод о влиянии на коррозию сульфатредуцирующих бактерий (СРБ). Подобный опыт был получен и на трех других раскопках. Вывод заключался в том, что в четырех из шести раскопок были обнаружены признаки микробной коррозии (MIC). Дополнительные раскопки в 2000 г. также показали MIC.
На основании результатов компания Gasunie пришла к выводу, что более небезопасно предполагать, что другие трубопроводы не подвержены этой проблеме коррозии. Поэтому инспекционная политика была пересмотрена. Было принято решение начать программу внутритрубной инспекции для всех линий высокого давления, которая должна быть завершена примерно за десять лет. Запуская программу проверки, компания поняла, что надежная скорость коррозии имеет первостепенное значение для определения интервала времени повторной проверки ее трубопроводов. Как следствие, скорость коррозии рассчитывалась каждый раз, когда через трубу выполнялся новый проход скребка. Это было сделано путем сравнения заявленных размеров дефекта поставщика А с указанными размерами поставщика В; а затем от А до С, и так далее. Но из-за относительно короткого временного интервала между проходами скребков неопределенность зарегистрированных размеров дефектов является доминирующей и препятствует расчету надежной скорости коррозии. Скорость коррозии, рассчитанная с помощью простого сравнения дефектов, показала средние значения от 0,2 до 0,3 мм/год. Но стандартное отклонение этих значений было того же порядка или даже больше.
Однако после четвертого прогона скребков, который состоялся почти через пять лет после первого прогона, компания Gasunie пришла к выводу, что скорость коррозии можно будет определить с помощью более сложных статистических методов. Из-за давних отношений с математическим факультетом Делфтского технического университета к этому факультету обратились с просьбой помочь проанализировать имеющиеся данные с использованием статистически обоснованных методов.
Первый подход
При первом подходе все дефекты объединяются в один набор данных, и скорость коррозии не рассчитывается для отдельных дефектов, а только для набора данных в целом. Первым шагом было выяснить, есть ли основания для принятия гипотезы о том, что ошибки измерения для всех свиней MFL относятся к одной и той же популяции и имеют нормальное распределение. Так было. Согласно оценке максимального правдоподобия для ошибки измерения параметры равны 0 (среднее) и 0,91 (для стандартного отклонения). Если предположить, что для всех ошибок между ними нет корреляции, то задача нахождения скорости коррозии, связанной со всеми измерениями, эквивалентна марковскому регрессионному анализу Гаусса.
Если также предполагается, что скорость коррозии одинакова во времени (т. е. рост коррозии является линейным), то применение метода наименьших квадратов ошибки (LSE) дает линейное описание роста коррозии в следующей форме: (ВСТАВЬТЕ УРАВНЕНИЕ) Стандартные расчеты дают следующие оценки для неизвестных параметров: (ВСТАВЬТЕ УРАВНЕНИЕ) и (ВСТАВЬТЕ УРАВНЕНИЕ) . Коэффициент эквивалентен измерению скорости коррозии (мм/год), поэтому модель LSE оценила скорость коррозии для калиброванных измерений 0,12 мм/год с доверительным интервалом 95% (0,05, 0,20) (рис. 1).
Затем был рассчитан коэффициент детерминации, чтобы увидеть, насколько хорошо модель соответствует данным. Оценка качества подгонки привела к R 2 = 0,04. Это было неудовлетворительно, так как указывало на то, что корреляция между двумя параметрами практически отсутствует. Согласно модели время зарождения коррозии составляет 20 лет (лет с момента прокладки трубопровода).
Несмотря на то, что оцениваемые параметры находятся в приемлемом диапазоне, этот подход имеет существенные недостатки. В частности, модель:
- Не различает дефекты
- Не учитывает, что часть дефектов исправляется во времени (уменьшение глубины дефекта, что физически невозможно), или для некоторых время возникновения дефектов до монтажа трубопровода
- Предполагается, что все дефекты имеют одну скорость коррозии.
Второй подход
Как отмечалось выше, первый подход имел существенные недостатки. Второй подход предлагает способ борьбы с некоторыми из перечисленных недостатков. Как и ранее, предполагается, что рост коррозии линейен во времени. Вторая модель проверяет, какова скорость коррозии, и анализирует дефекты по отдельности. То есть модель больше не предполагает, что существует только одна скорость коррозии для всех дефектов, а вместо этого рассчитывает скорость коррозии для каждого дефекта. Простой регрессионный анализ, примененный к каждому несмещенному дефекту, показан на рис. 2.9.0003
Из гистограммы, представленной на рис. 2, видно, что во многих случаях простой регрессионный анализ, примененный к каждому дефекту, приводил к отрицательным показателям коррозии. Средняя скорость коррозии по этой модели составляет 0,16 мм/год, что близко к полученному ранее результату. Однако 95-процентный доверительный интервал для скорости коррозии совсем другой: -0,31, 0,54. 95% доверительный интервал содержит отрицательные значения.
Количество дефектов, указывающих либо на отрицательную скорость коррозии, либо на время начала коррозии до монтажа трубопровода, равно 16. Один из способов борьбы с отрицательной скоростью коррозии — удалить все выбросы из набора данных. Однако такая обработка нежелательна, так как набор данных на 30% состоит из плохих дефектов. Дальнейшее исследование подтвердило, что скорость коррозии имеет нормальное распределение. Время возникновения коррозии представлено на рис. 3 также в виде гистограммы. Красные полосы указывают время начала вне интервала, определяемого временем монтажа трубопровода (t=0 [год]) и временем последней проверки (t=44,25 [год]). Однако метод наименьших квадратов ошибок приводит к отрицательной скорости коррозии или времени ее возникновения до монтажа трубопровода. Поэтому была разработана альтернатива представленным моделям. Это был третий подход.
Третий подход
Компания TUDelft сконструировала модель таким образом, что должны были соблюдаться следующие ограничения:
- Скорость коррозии должна быть положительной
- Время инициации должно приходиться на срок службы трубопровода.
Модель была основана на оценке максимального правдоподобия, которая, в свою очередь, основывалась на распределениях измерений для функции, описывающей рост коррозии во времени. Модель учитывает информацию о распределении ошибок измерений для каждой конкретной свиньи и в соответствии с этими распределениями присваивает измерениям веса. Кроме того, эта модель также учитывает распределения, полученные в результате процедуры калибровки. Эти распределения используются для присвоения веса свиньям таким образом, чтобы свинья с наименьшим уровнем неопределенности (наименьшее стандартное отклонение для распределения ошибок) получала наибольший вес. Таким образом, естественно, что точная свинья будет влиять на окончательные результаты гораздо больше, чем свинья с более низким уровнем точности.
Предполагая, что функция, связанная с i-м дефектом, является линейной во времени (ВСТАВЬТЕ УРАВНЕНИЕ) , тогда модель Т. Дельфта определяется следующим образом: , связанный с i-м дефектом (количество дефектов 52)
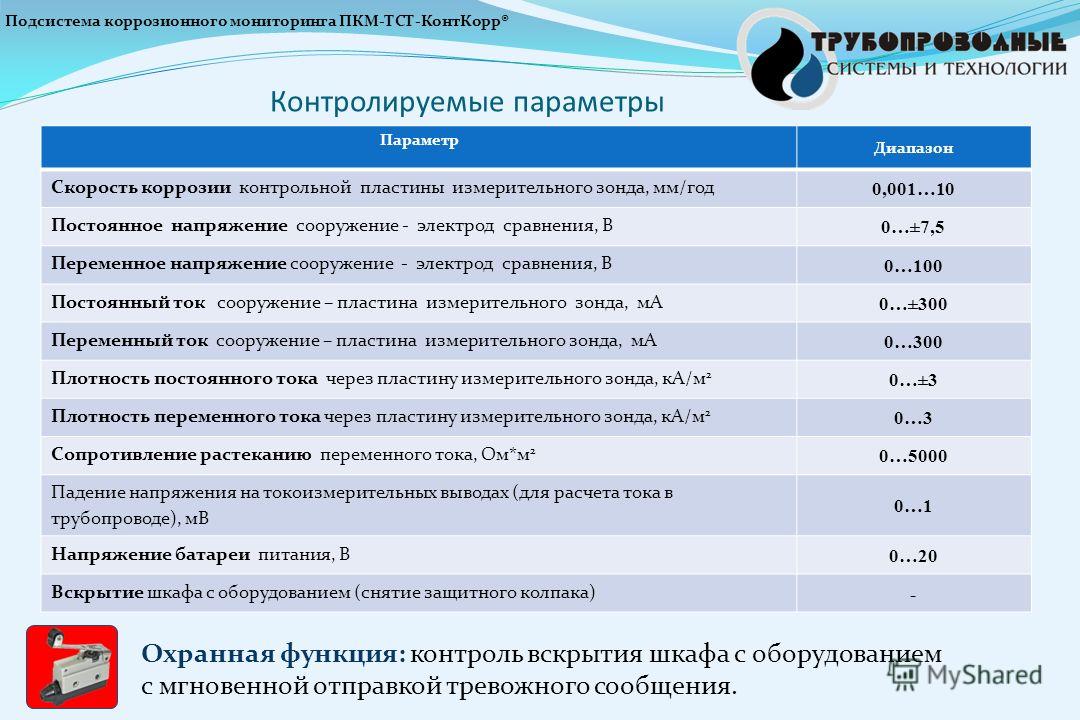
Оценка правдоподобия оптимальна, когда максимизируется следующая функция:
(ВСТАВЬТЕ УРАВНЕНИЯ)
Еще одним преимуществом модели является то, что модель также позволяет проводить анализ недооценки/переоценки для определенных групп дефектов (кластеров). Результаты скорости коррозии, полученные с помощью модели, представлены на рисунке 4. Из-за ограничений выходные данные модели находятся в гармонии с физическими коррозионными свойствами. Ни одна из скоростей коррозии не является отрицательной.
В двух других подходах распределение скорости коррозии было нормальным. Но при использовании третьего подхода все совсем по-другому. Нет оснований отвергать гипотезу о бета-распределении скорости коррозии (с параметрами 1,25 и 3,9).2) (рис. 5). Модель говорит, что все времена инициации находятся в допустимых временных интервалах. Тем не менее, 16 дефектов возникают во время монтажа трубопровода – на рисунке выше они обозначены более светлым синим цветом. Результатом этого является то, что распределение времени инициации является композицией двух распределений, дискретных в 0 и непрерывных в других местах. Непрерывная часть также является бета-распределенной (с параметрами 1,60 и 0,50).
Влияние глубины на скорость коррозии
Чтобы выяснить, оказывает ли глубина дефектов существенное влияние на скорость коррозии, набор данных из 52 несмещенных измерений был разделен на два подмножества. Сначала рассчитывали среднее значение для каждого дефекта. Веса были связаны со стандартными отклонениями ошибок измерения; т. е. точный поросенок имеет наибольший вес. Затем набор данных был разделен на два подмножества, а именно «мелкие» и «глубокие» дефекты, таким образом, чтобы болванка MFL с наименьшим количеством наблюдений имела равное количество измерений в обоих наборах. Для обоих подмножеств применялась модель TUDelft.
Средняя скорость коррозии для глубоких дефектов оказалась равной 0,25 мм/год, для более мелких – 0,23 мм/год. Однако статистически нет оснований отвергать нулевую гипотезу о том, что эти средние значения одинаковы. Отсюда следует, что статистически скорости коррозии глубоких и мелких дефектов существенно не различаются. Гистограммы скоростей для мелких и глубоких дефектов представлены на рисунках 6 и 7. В обоих случаях (мелкие и глубокие дефекты) нет оснований отвергать гипотезу о том, что скорости коррозии зависят от бета-распределения.
Несмотря на то, что количество измерений одинаково в обоих подмножествах, количество дефектов в этих двух наборах неодинаково. Количество неглубоких дефектов по представленному критерию равно 34. Остальные (18) являются глубокими дефектами. Анализ показал, что если набор несмещенных измерений разделить таким образом, что число мелких и глубоких дефектов в обоих подмножествах одинаково, то можно сделать один и тот же вывод об отсутствии существенной разницы в скоростях коррозии.
Выводы
Чтобы надежно определить смещение для устройства для скребков MFL, крайне важно иметь в трубопроводе несколько эталонных дефектов, размеры которых хорошо известны. Затем их можно использовать для калибровки сообщаемых значений MFL. Для описываемого трубопровода количество доступных контрольных точек было ограничено, но все же позволяло оценить погрешность для каждой свиньи. Стало ясно, что между разными поставщиками существуют большие различия: интерпретация, группировка и размер дефектов порождают многочисленные ситуации, в которых неясно, кто из поставщиков прав.
Поскольку неопределенность измерения инструмента MFL является доминирующей по сравнению с ростом коррозии в период времени между проходами скребка, очень сложно определить достоверную скорость коррозии для каждого дефекта. Но, предполагая аналогичный процесс коррозии (MIC) для каждого дефекта, основываясь на оценке сигналов MFL, исторических измерениях CP и результатах раскопок, в сочетании с предположением о линейном росте коррозии, можно было рассчитать реалистичную скорость коррозии. для этого трубопровода. В зависимости от используемого подхода было получено значение средней скорости коррозии 0,12 мм/год (подход 1), 0,16 мм/год (подход 2) или 0,24 мм/год (подход 3). Цифры для 95% верхних предельных значений составляли соответственно 0,20 мм/год, 0,54 и 0,62 мм/год.
Для каждого из заявленных дефектов поставщика А оценивалась вероятность того, что это дефект MIC или нет. Опыт раскопок, специфическая картина сигналов MFL для дефектов MIC и положение часов дефектов были использованы для принятия этого решения о вероятности MIC. Судя по дефектам, о которых сообщил поставщик А, было установлено, что 15% дефектов, вероятно, не были дефектами MIC. Если мы предположим, что этот процент справедлив и для 52 дефектов, возникших в результате процесса сопоставления, можно сделать вывод, что подавляющее большинство дефектов в этой линии вызвано микробным влиянием. Следовательно, скорость коррозии во многом определяется этим коррозионным процессом. Если мы сравним это значение со значениями, которые часто указывают для МПК, равными 0,4 мм/год или выше, то полученное значение находится в более низком диапазоне. Неофициальные контакты с другими передающими компаниями, также имеющими опыт работы с внешними ВПК, подтверждают справедливость этого значения.
Предположение о линейности процесса коррозии было подтверждено анализом двух подмножеств: глубоких и мелких дефектов. Для обоих подмножеств была рассчитана аналогичная средняя скорость коррозии: 0,23 мм/год и 0,25 мм/год. Разница не существенна.
Теперь, когда скорость коррозии определена, Gasunie должна будет решить, как использовать эти значения для расчета интервала повторной проверки для этой линии. Расчет, вероятно, будет выполняться детерминированным образом для каждого дефекта с учетом погрешностей измерения и неопределенности скорости коррозии.
Еще один момент, который необходимо решить, это вопрос о том, можно ли использовать эти значения и для других строк. В настоящее время проводится анализ результатов 40 проходов скребков, чтобы выяснить, имеют ли другие трубопроводы аналогичные коррозионные характеристики. Для тех линий, которые имеют аналогичное распределение коррозии, представляется реалистичным использовать аналогичные скорости коррозии для расчета интервалов повторных проверок.
Еще одно интересное применение этих скоростей коррозии — программа прямой оценки (DA) компании Gasunie. В этой программе частоты отказов рассчитываются на основе предположений о распределении и скорости коррозии. Следовательно, надежные значения скорости коррозии имеют первостепенное значение для качества этой программы.
Будущая работа
С момента открытия MIC компания Gasunie искала возможности создания модели коррозии для MIC на основе параметров почвы. До сих пор не было возможности определить соответствующие параметры и соотнести их с размерами дефектов. Но поразительно, что MIC часто концентрируется в определенных частях трубопровода или в определенных частях Нидерландов.
В сети есть определенная область, где две линии, находящиеся на расстоянии примерно 50 метров друг от друга, имеют концентрации MIC в пределах одного километра. И на аналогичных линиях, проходящих на расстоянии 300 метров параллельно этим линиям, MIC не обнаружен. Недавние усилия были сосредоточены на этой области, чтобы выяснить, почему существуют эти различия. Данные свидетельствуют о том, что различия в типах коррозии могут быть вызваны очень локальными различиями в почве. Прошлым летом на рассматриваемом трубопроводе было проведено еще восемь раскопок. Информация, полученная о типах коррозии и размерах дефектов, будет использоваться для проверки сделанных до сих пор предположений и для дальнейшей калибровки результатов скребков.
Благодарности
Авторы выражают признательность своим коллегам из Gasunie, в том числе Робберту ван дер Шееру, Асиму Сагламу, Карине Кутровски, Роберту Куику, Питу ван Мастригту, Витце Слотердейку, Полу Весселиусу и Эрику Джагеру; и профессора Роджер М. Кук, профессор Томас А. Маццуки и Даниэль Левандовски из TUDelft. Основано на документе, представленном на Международной конференции по трубопроводам ASME IPC 2006, 25-29 сентября 2006 г.