Ремонт деталей ручной сваркой и наплавкой: Ремонт деталей сваркой и наплавкой
alexxlab | 01.05.2018 | 0 | Разное
По статистике при восстановлении деталей в 60% случаев используется сварка и наплавка. Сваркой устраняют механические повреждения. Наплавкой восстанавливают изношенные поверхности деталей.
Сущность восстановления сваркой и наплавкой
Оба метода основаны на тепловом воздействии, отличаются только настройки используемого оборудования. Наплавка ― это нанесение на поверхность деталей слоя из сплава основного и присадочного металла. Наплавкой восстанавливают не только геометрические размеры, но также наносят покрытия для повышения жаростойкости, прочности, износоустойчивости и т. д. Процедура выполнятся на поверхности любой формы― от плоской до конической и сферической.
Сварка ― это процесс создания соединения металлических элементов методом плавления или давления. Этим способом заделывают трещины, сколы, отверстия от пробоин, крепят отломившиеся элементы. С такими повреждениями рам, поддонов, кузовов, обоих мостов постоянно сталкиваются при ремонте автомобилей. Сварку также применяют совместно с другими восстановительными процедурами.
Для качественного восстановления деталей сваркой и наплавкой необходимо:
- не допускать сильного смешивания основного металла с наносимым;
- плавить основной металл на минимальную глубину;
- не делать больших припусков на последующую обработку;
- принимать меры по снижению остаточных напряжений и деформации.
Подготовка деталей
Перед восстановлением детали сваркой или наплавкой с поверхности удаляют ржавчину, окалину, грязь металлической щеткой или пескоструйной обработкой до блеска. Обезжиривание выполняют растворителем или нагревом поверхности до 300⁰C. На кромках закрепляемых элементов снимают фаски. У трещин разделывают края под углом 120 — 140⁰, на концах сверлят отверстия диаметром 3 — 4 мм. Глухие трещины углубляют насквозь, чтобы газы при сварке не образовывали поры.
С деталей, которые уже восстанавливались, сначала удаляют остатки нанесенного ранее слоя. Затем проводят процедуру очистки. Если износ не больше 1 мм, с места восстановления снимают слой на глубину 0,5 — 1 мм шлифовальным кругом или резцом. Это обеспечит однородность структуры нанесенного сплава.
Электродуговая сварка и наплавка
Это самая распространенная технология восстановления в промышленности и на дому. Она легко выполняется на обычном сварочном оборудовании. Работу выполняют плавящимися покрытыми электродами и неплавящимися с присадочной проволокой.
Качество конечного результата определяется параметрами электродов. Для ремонта сваркой площадь поперечного сечения стержней выбирают в зависимости от размера повреждения, толщины металла. Для создания слоя с заданными параметрами выбирают марки электродов с легирующими присадками. Они могут содержаться в металле и обмазке стержней.
Наплавку на детали из низкоуглеродистых сталей, которые не подвергались термической обработке, проводят сварочными электродами. Форму изделий из закаленной легированной, высокоуглеродистой стали восстанавливают наплавочными электродами с присадками или стержнями из твердых сплавов. Ими же наносят слои на режущие кромки инструмента для обработки металла.
Важно!
Для предотвращения деформирования, детали из высокоуглеродистой легированной стали предварительно нагревают до 300⁰C.
После окончания работы проводят отпуск для снятия внутренних напряжений в сварочных швах. Для низкоуглеродистой, низколегированной стали предварительный нагрев не требуется.
На цилиндрическую поверхность валики накладывают тремя способами:
- в виде спиралей;
- в форме замкнутых окружностей;
- параллельно оси вращения.
На плоские поверхности наплавляют рядом расположенные широкие валики либо узкие с перекрытием 0,3 — 0,5 по ширине. На место большого износа сначала накладывают слой из низколегированной стали. Наплавку и сварку элементов небольшой толщины выполняют на постоянном токе обратной полярности. Толстостенные детали сваривают переменным или постоянным током с прямой полярностью.
Восстановление деталей в среде защитных газов
Этим способом восстанавливают детали наплавкой и сваркой толщиной от 0,6 мм и валов диаметром до 5 см. Поступающий под давлением к месту сварки газ защищает расплавленный металл от соприкосновения с воздухом. Самые качественные швы получаются в среде аргона или гелия, однако из-за их высокой цены чаще пользуются углекислым газом. В среде азота восстанавливают детали из меди.
При нагреве до высокой температуры из углекислого газа выделяется кислород, который способствует выгоранию углерода, марганца, кремния. Поэтому для работы со сталью применяют сварочную или присадочную проволоку с высоким содержанием этих элементов. Выбор диаметра в диапазоне 0,5 — 2,5 мм зависит от толщины деталей. Наплавку на нержавеющую сталь проводят проволокой из нержавейки, желательно той же марки.
Восстановление в среде углекислого газа выполняют на постоянном токе обратной полярности. Чтобы процесс протекал стабильно, выбирают сварочное оборудование с жесткими характеристиками. Автоматической наплавкой восстанавливают детали диаметром от 10 мм из низкоуглеродистых сортов стали.
Подачу проволоки настраивают так, чтобы не возникали короткие замыкания или обрывы дуги. Скорость наплавки определяется по толщине создаваемого слоя. Валики накладывают с шагом 2,5 — 3,5 мм.
Сварка и наплавка под слоем флюса
Восстановление этим способом проводят электрической дугой, которая горит под расплавленным флюсом. Таким образом, создается эластичная оболочка, защищающая расплавленный металл от соприкосновения с воздухом. Флюсы также поддерживают стабильность горения дуги, раскисляют, легируют, рафинируют наплавляемый металл.
Для сварки и наплавки применяют два вида флюсов:
- Керамические, состоящие из металлических и неметаллических компонентов, что позволяет проводить легирование в большом диапазоне.
- Плавленые не содержат металлических компонентов, поэтому возможности легирования ограничены десятыми долями процента. По сравнению с керамическими видами эти флюсы дешевле, лучше защищают, со швов легче отделяется шлак. Плавлеными флюсами с высоким содержанием кремния пользуются при нанесении слоев из углеродистых, низколегированных сортов стали.

Наплавка под слоем флюса
Наплавку металла под флюсом проводят сварочной проволокой без покрытия. Диаметр (1 — 6 мм) определяют по толщине создаваемого слоя, формы валиков, габаритов деталей. Чтобы увеличить производительность, восстановление ведут ленточными электродами шириной до 10 см или одновременно двумя проволоками с подачей разными механизмами.
Восстановление выполняют на постоянном токе с обратной полярностью. На круглых деталях валики располагают с шагом 2 — 6 диаметра проволоки. Для уменьшения деформации на плоской поверхности наплавку ведут через валик или поочередно на разных участках.
Другие способы восстановления
Также популярны альтернативные методы восстановления:
- Вибродуговая наплавка отличается от обычной электросварки тем, что электрод кроме поступательного движения совершает перпендикулярные колебания частотой 90 — 100 кол/сек. В ходе процесса металл переносится мелкими каплями в сварочную ванну небольшого размера. Этим достигается незначительная глубина проплава, высокая прочность сцепления материала электрода с металлом детали.
- Пламенная наплавка проводится за счет нагрева основного металла и присадочной проволоки струей ионизированного газа, направляемой в рабочую зону соплом горелки.
- Электроконтактную наплавку выполняют методом пластической деформацией после нагрева металла детали и присадочного материала импульсным током. Отличается высокой производительностью (до 150 см²/мин), незначительным термическим воздействием, малым проплавлением.
Перспективными считают способы наплавки (сварки), прошедшие экспериментальную проверку:
- электронно-лучевая;
- высокочастотным током;
- лазерная;
- пропиткой композиционных сплавов;
- взрывом;
- самораспространяющимся высокотемпературным синтезом.
Особенности восстановления деталей из чугуна
Сложность восстановления чугунных деталей связана с тем, что при быстром остывании шов становится чрезмерно хрупким, так как в металле остается много углерода. Поскольку у материалов деталей и швов коэффициенты усадки разные, во время и после окончания сварки образуются трещины. При высокой температуре углерод и кремний выгорают с образованием шлака и газов, которые при быстром остывании остаются внутри швов в виде пор, включений.
Для получения прочных однородных швов восстановление выполняют методом горячей сварки. Деталь предварительно медленно нагревают до 650 — 700⁰C в течение 1,5 — 2 часов в печи. Затем переносят в термос, чтобы температура во время работы не упала ниже отметки 500⁰C. Сварку или нанесение слоя ведут через люк. После окончания восстановления деталь отжигают при 600 — 650⁰C в печи или термосе. Инструкция рекомендует снижать температуру со скоростью 50 — 100⁰C/час.
Обратите внимание!
Если ремонт выполняют газовой горелкой, в качестве присадочного материала применяют стержни из чугуна.
Электросварку проводят чугунными электродами с покрытием, в состав которого входит до 50% графита. Из-за низкой производительности, сложности оборудования, этим способом пользуются редко.
Восстановление холодной сваркой выполняют без предварительного нагрева. Поэтому принимают меры для предотвращения деформирования и образования дефектов. Газовой горелкой чугун плавят медленно, но без перегрева. Электросварку проводят постоянным током обратной полярности, диаметр электродов 3 — 4 мм. Валики при наплавке накладывают вразброс участками по 40 — 50 мм. Прежде чем начать следующий, предыдущий шов охлаждают до 50 — 60⁰C.
В зависимости от решаемых задач для холодной сварки применяют присадочные стержни и электроды:
- чугунные;
- стальные;
- комбинированные;
- пучковые;
- монелевые;
- медно-стальные.
При восстановлении деталей, следует учитывать, что независимо от метода наплавки, нанесенный металл будет неоднороден по механическим параметрам, структуре, химическому составу. Поэтому если деталь работает в условиях больших нагрузок, рекомендуется заменить ее новой.
Технологии сварки и наплавки позволяют эффективно восстанавливать металлические детали, обеспечивая высокую степень надежности и долговечности изделия.
Это подтверждается и практикой использования данных методов при выполнении ремонтных операций в самых разных областях – от починки автомобилей до производства металлопроката. В общем объеме работ по ремонту металлических конструкций восстановление деталей сваркой и наплавкой занимает порядка 60-70%. Наиболее распространена починка стальных блоков цилиндров, моторных валов, картеров, цепных звеньев, лопаток и т. д.
Сварка и наплавка в ремонтно-восстановительных работах
Оба способа основываются на методах термического воздействия с разными параметрами работы подключаемого оборудования. Под сваркой понимается процесс формирования межатомных связей, которые могут использоваться для соединения разных элементов детали, заделки технологических зазоров и устранения мелких дефектов на поверхности. Энергетический потенциал для сварочного процесса обеспечивается за счет общего или местного нагрева заготовки.
К типовым операциям данного рода можно отнести закрепление добавочных или отломанных частей пластин, венцов и втулок. Кроме ремонта изделий с простыми геометрическими формами, возможны и более сложные восстановительные задачи, но в составе с другими технологическими операциями. Например, восстановление резьбы сваркой будет дополняться процедурами механической правки и проточки. К тому же в подобных работах следует соблюдать требования к перегревам вспомогательного инструмента наподобие плашек, которые непосредственно участвуют в коррекции резьбы.
Что касается наплавки, то этот способ подразумевает нанесение дополнительного металлического покрытия на восстанавливаемую поверхность. Новый технологический слой может быть полезен при ремонте изношенных деталей или усиления поверхности в области трения.
Применяемое оборудование
При сварочных работах обязательно используется источник тока, оснастка для удержания детали и направления дуги. Чаще применяют сварочный преобразователь, в состав которого входит двигатель с генератором постоянного тока от 70 до 800 А. Также могут задействоваться выпрямители с трансформаторами тока и пускорегулирующей установкой. Если говорить о расходниках и вспомогательных устройствах, то восстановление деталей сваркой и наплавкой выполняется с подключением удерживающих мундштуков, электродов и систем охлаждения. При наплавке также задействуют деформирующие головки с суппортами и подъемниками, допускающими возможность крепления на станках (токарных или винторезных). Для удаления лишних металлических кромок и слоев применяются специальные резцы.
Требования к подготовке детали
И при сварке, и в процессе наплавки качество выполнения операции в немалой степени будет определяться изначальным состоянием заготовки. Поверхности детали должны быть зачищены от ржавчины, окалины, грязи и жира. В ином случае повышается риск сохранения непроваров, трещин и шлаковых включений. Особое внимание следует уделить обезжириванию от заводских и консервационных масел. Эту процедуру выполняют в горячем растворе, после чего изделие омывается и сушится. Перед восстановлением деталей способом сварки рекомендуется выполнять и пескоструйную обработку, что повышает качество ремонта. Для таких задач используют методы абразивной обработки с подключением компрессорного оборудования, шлифовальных дисков и резцов. Незначительные следы коррозийного поражения можно удалить и ручными металлическими щетками.
Какие электроды используются при восстановлении?
После подготовки основного рабочего оборудования и заготовки можно приступать к выбору электродов. Подбор зависит от вида металла, характера дефекта и требований к слою наплавки. Как правило, в распространенных случаях обломов и трещин используют обычные сварочные электроды с сопротивлением разрыву порядка 4 МПа. Для работы с углеродистыми сталями рекомендуется применять расходники, стержни которых выполнены из проволоки марки Св-08 толщиной 1,5-12 мм. Не стоит игнорировать и характеристики покрытия. Высокий стабилизирующий эффект при восстановлении деталей сваркой и наплавкой обеспечит меловая обмазка электрода типа Э-34. Она будет способствовать устойчивому процессу горения дуги, что позволит сформировать плотный и ровный шов.
Также сегодня используются нестандартные электродные расходники наподобие ленточных и трубчатых порошковых элементов. Обычно они представляют собой свернутые металлические ленты толщиной до 0,8 мм, поверхность которых наполнена различными порошкообразными легирующими смесями на основе ферромарганца, сталинита и др. К таким электродам стоит обращаться, если планируется наделять ремонтируемый участок дополнительными эксплуатационными свойствами.
Ручной дуговой метод сварки и наплавки
При восстановлении поврежденных сварных швов, заделке трещин и запайке герметичных корпусов можно применять ручной метод с графитовыми, угольными или вольфрамовыми электродами. В ходе работы берется пучок стержней с обмазкой и скрепляется проволокой. Окончания необходимо предварительно сварить и вставить в подготовленный держатель. В ходе работы электроды сформируют так называемую блуждающую дугу с широким полем действия. Чем больше площадь поврежденного участка, тем крупнее должен быть пучок. Главная сложность процесса сварки таким способом заключается в необходимости подключения трехфазной сети, поскольку та же наплавка пучком из 5-6 электродов должна производиться на повышенном токе. Таким методом ремонтируют детали из легированных и низколегированных сталей средней и большой толщины.
Метод автоматической наплавки под флюсом
Автоматический процесс наплавки отличается тем, что подача электрода с перемещениями самой дуги по рабочей поверхности полностью механизируются. Флюс, в свою очередь, обеспечивает изоляцию целевой зоны от вредного воздействия кислорода. Метод задействуется для восстановления поверхностей плоских и цилиндрических деталей с глубиной износа до 15 мм. По мере увеличения размера дефекта может применяться несколько слоев наплавки, но в этом случае потребуется ожидание полимеризации каждого предыдущего пласта. Данная технология восстановления деталей сваркой и наплавкой требует подключения источников тока в виде преобразователя или выпрямителя с токарно-винторезным станком. В рабочей зоне формируется покрытие флюса толщиной 1-4 мм, после чего автоматом направляется электродная проволока с дугой. К основным достоинствам этого метода относительно ручной сварки можно отнести минимальные потери металла в результате разбрызгивания. Ручной метод дает в несколько раз больше огарков и угара.
Метод вибродуговой наплавки
В данном случае применяются плавкие электроды, которые в процессе горения дуги вибрируют с короткими замыканиями. Операции подачи и перемещения расходных материалов также автоматизированы. Несмотря на внешнюю сложность процесса, метод довольно простой и не требует применения специальной оснастки. Более того, в конечном счете можно ожидать исключения деформации детали с сохранением твердости без термической обработки. Однако есть и ограничения. Так, вибрационные способы восстановления деталей сваркой и наплавкой подходят для заготовок с диаметром не менее 8 мм или толщиной от 0,5 до 3,5 мм. Теоретически вибродуговая наплавка может выполняться в разных защитных средах с газом или флюсом, но на практике чаще задействуют жидкостную изоляцию – например, кальцинированный раствор соды.
Сварка и наплавка в газовых защитных средах
Этот метод предусматривает подготовку специального баллона со сжатой газовой смесью. Могут использоваться аргоновые и углекислотные газы, направляемые в зону сварки под высоким давлением. Задача смеси также сводится к защитной функции изоляции заготовки от негативного воздействия азота и кислорода в воздухе. Наиболее качественные соединения сваркой в газовых средах получаются при использовании вольфрамовых электродов с отдельным вводом в рабочую зону присадочных материалов. Наплавка осуществляется под постоянным током с обратной полярностью. Процесс может быть механизирован, если применяется электродная проволока, но операции с газоэлектрическими горелками обычно выполняют вручную.
Полуавтоматические способы сварки и наплавки
Оптимальный метод для работы с алюминием и различными сплавами цветмета. Благодаря гибкой настройке параметров оборудования и возможностям использования разных защитных сред оператор может получить при небольшой силе тока качественный шов на заготовке толщиной до 12 мм. Полуавтоматический метод восстановления деталей сваркой производится с помощью вольфрамовых электродов толщиной 0,8-6 мм. Напряжение при этом может варьироваться от 20 до 25 В, а сила тока укладывается в 120 А.
Альтернативная технология восстановления под давлением
Кроме термических способов сварки и наплавки, также применяется широкая группа контактных или холодных методов изменения структуры металлических заготовок. В частности, восстановление деталей сваркой под давлением осуществляется с помощью механических агрегатов с пуансонами. В процессе пластической деформации в точках контакта формируется сварное соединение с определенными параметрами. Конфигурация деформирующего эффекта будет зависеть от характеристик пуансона и техники оказания сжатия.
Заключение
На сегодняшний день не существует более действенных способов коррекции дефектов металлической структуры, чем сварка и наплавка. Другое дело, что в данных сегментах наблюдается активное развитие разных методик реализации технологии на практике. Наиболее перспективным направлением можно назвать восстановление деталей сваркой и наплавкой на автоматизированном оборудовании. Механизация выполнения ремонтных операций повышает производительность процесса, его эргономичность и уровень безопасности для сварщика. Параллельно развиваются и методы высокоточной аргонодуговой сварки с подключением газовых защитных сред. О полной автоматизации в этом направлении пока еще рано говорить, но в плане качества результата эта область является передовой.
Ремонт деталей сваркой и наплавкой » СтудИзба
Эксплуатация и ремонт машин и оборудования НиГ промыслов.
Лекция 10.
6. Ремонт деталей сваркой и наплавкой.
Сваркой называется процесс неразъемного соединения деталей или их отдельных частей вследствие действия сил молекулярного сцепления. При сварке металлов, за исключением холодной сварки, производят местный нагрев соединяемых частей до перехода их в пластическое или расплавленное состояние. Металл шва должен обладать одинаковыми свойствами с основными металлом. Это определяет подбор присадочного материала и режима сварки. На ремпредприятиях нефтегазовой промышленности для ремонта стальных деталей в основном применяют ручную электродуговую и реже ручную газовую сварку. Оборудование, используемое при ремонте деталей сваркой, такое же как и при сварке новых деталей.
Наплавка – процесс нанесения расплавленного металла необходимого состава не поверхность детали, нагретой до температуры плавления. Наплавку применяют для восстановления размеров детали и придания заданных свойств её поверхности путем правильного выбора химического состава и структуры наплавленного металла. Наплавка является разновидностью сварки. однако отличие в том, что при наплавке процесс используется для наращивания на основной металл слоя металла или сплава со свойствами, иногда отличающимися от свойств основного металла. В этой связи к процессу наплавки предъявляются следующие основные требования:
1) Доля основного металла (детали) в наплавленном слое должна быть минимальна.
2) Для сохранения прочности ремонтируемой детали процесс наплавки не должен изменять её исходного химического состава, структуры и напряженного состояния.
3) Наплавленный слой должен обладать достаточно высокой прочностью сцепления с основным металлом.
На практике это решают путем соответствующего выбора технических режимов наплавки, стараясь обеспечить достаточную прочность соединения основного и наплавленного металлов и в то же время в минимальной степени изменить их исходное состояние.
Виды наплавки: ручная и механизированная.Ручная – газовая, электродуговая, аргонно-дуговая. Механизированная – под слоем флюса, в среде защитных газов, вибродуговая, плазменно-дуговая, электрошлаковая, индукционная, наплавка трением.
Наибольшее распространение получили ручная газовая и электродуговая наплавки, автоматическая и полуавтоматическая наплавки электрической дугой под слоем флюса и вибродуговая наплавка.
Выбор наплавляемого материала производят с учетом материала ремонтируемой детали, её форм, размеров, технических требований, условий работы и применяемого вида наплавки. Широко применяется стальная сварочная проволока. Углеродистая и легированная проволоки для восстановления размеров изношенных деталей. Высокохромистые – обеспечивают высокую износостойкость и коррозионную стойкость наплавленного слоя. Широко применяют наплавку перочинной проволокой при наплавке высоколегированных и высокоуглеродистых сплавов. Порошковые проволоки широко используют при наплавке в углеродистом газе и под слоем флюса.
Для ручной газовой электродуговой наплавки используются металлические электроды. регулирование химического состава и свойств наплавленного слоя осуществляется через покрытие или через электродный стержень или комбинированным методом. Для предотвращения появления деформаций и трещин при наплавке применяют предварительный нагрев детали (200-4000С) и другие технологические приемы.
6.1 Ручная газовая сварка и наплавка.
При ручной газовой сварке и наплавке расплавление основного и присадочного материала осуществляется теплом, выделяющимся в процессе сгорания газов (пропанбутановых смесей, ацетилена и др.) в среде кислорода. Качество шва и наплавленного слоя в значительной степени зависит от состава присадочного материала. При сварке следует применять присадочные материалы близкие по химическому составу к материалу ремонтируемой детали. Для защиты металла шва от окисления, а так же для удаления окислов образующихся при сварке применяют флюсы в виде порошка или пасты. Нагрев основного и присадочного металлов при газовой наплавке легко регулируется, что позволяет избежать нежелательного глубокого проплавления основного металла и смешивания его с наплавочным материалом. Толщина наплавляемого слоя обычно колеблется от 2,5 до 4 мм. К недостаткам газовой наплавки следует отнести неравномерность толщины наплавленного слоя.
Сварка чугунных деталей является сложным процессом, что связано с большим содержанием углерода и кремния в чугуне, неоднородностью его структуры и чувствительностью к температурным изменениям. Сварку деталей из чугуна производят с подогревом и без подогрева. При сварке с подогревом деталь нагревают до 650 – 7000С для предупреждения отбеливания чугуна и возникновения остаточных напряжений. При сварке вследствие выгорания углерода и кремния происходит отбеливание чугуна и для получения качественного сварного шва в присадочных материалах должно быть 3 – 3,6 % углерода, 3 – 4 % кремния, 0,5 – 0,8 % марганца.
Особенность сварки деталей из алюминия и его сплавов определяется их свойствами:
1) Низкой (6000С) температурой плавления и большой жидкотекучестью.
2) Высокой теплопроводностью.
3) Способностью окислятся на воздухе с образованием тугоплавкой окисной пленки с температурой плавления 20500 С.
4) Высокой растворимостью водорода в расплавленном алюминии, приводящей к пористости.
Для борьбы с этими явлениями применяют специальные флюсы и технологии сварки.
4.2 Ручная электродуговая сварка и наплавка.
При электродуговой сварке и наплавке источником тепла для расплавления металлов является электрическая сварочная дуга, возникающая между электродом и свариваемым металлом. качество сварного шва и наплавленного слоя определяется диаметром электрода, характеристикой тока, маркой электрода, скоростью сварки, положением шва в пространстве.
При ручной электродуговой сварке и наплавке чаще всего используются металлические электроды, представляющие собой металлический стержень со слоем покрытия, предназначенного для стабилизации дуги горения, защиты расплавленного металла от кислорода и азота воздуха, легирования наплавленного металла. В состав электродных покрытий входят следующие компоненты: стабилизирующие, шлакообразующие, газообразующие, раскисляющие, легирующие и связующие. Электроды изготавливают Ø 1,6-12 мм и длиной 225 – 450 мм. В зависимости от химического состава ремонтируемой детали и требований предъявляемых к сварному шву или наплавленному слою. Для сварки и наплавки применяют типовые электроды определенного назначения. Для наплавки изношенных поверхностей применяют электроды обеспечивающие получение слоя необходимой твердости и высокой износостойкости. Диаметр электрода выбирается в зависимости от толщины наплавляемого слоя и размеров шва. Величина сварочного тока выбирается в зависимости от электрода:
IСВ=(20+4dЭЛ) dЭЛ
IСВ – сварочный ток величина силы;
dЭЛ – диаметр электрода.
Ручную электродуговую сварку и наплавку целесообразно применять при небольшом объеме работ, а также в трудоемких местах. К преимуществам ручной электродуговой сварки и наплавки относится простота и удобство процесса.
Недостатки – низкая производительность, низкая стабильность дуги и невысокое качество.
4.3 Электрическая электродуговая наплавка под слоем флюса.
При указанном виде наплавки электрическая дуга горит под слоем флюса, подаваемого в зону наплавки. В зоне горения дуги оплавляются поверхность детали, электрод и прилегающий слой флюса. Электродная проволока по мере оплавления автоматически подается в зону дуги одновременно с флюсом. При плавлении флюса образуется газовая оболочка, защищающая расплавленный металл от взаимодействия с окружающим воздухом и выгорания легирующих элементов. Флюсовое покрытие способствует сохранению тепла дуги и препятствует разбрызгиванию жидкого металла. Шлаковая корка, образующаяся при остывании, снижает скорость охлаждения наплавленного металла, что создает благоприятные условия для формирования шва. Этим способом можно наплавлять разные поверхности в несколько слоев. Толщина слоя наплавки практически не ограничена. Для питания дуги используется постоянный ток обратной полярности. Наплавку можно производить как на универсальном оборудовании так и на специализированных установках. Для получения требуемых свойств наплавленного металла необходимо вводить в него легирующие элементы.
Преимуществами автоматической наплавки под слоем флюса перед ручной электродуговой являются:
1) Высокая производительность процесса.
2) Высокое качество наплавленного слоя.
3) Возможность регулирования свойств наплавленного слоя.
4) Наличие закрытой дуги, что улучшает условия труда.
5) Лучшее использование эл. энергии и материала проволоки.
Автоматическую наплавку целесообразно применять при ремонте большого числа однотипных деталей, когда требуется наплавить значительный слой металла толщиной 5-40 мм.
4.4 Наплавка в среде защитных газов.
При этом виде наплавки защитный газ, подаваемый в зону наплавки под избыточным давлением, изолирует сварочную дугу и плавильное пространство от кислорода и азота воздуха. наплавку углеродных, легированных сталей и чугуна производят в среде углекислого газа; для высоколегированных сталей применяют аргон. Для наплавки в среде защитных газов применяется серийное оборудование используется постоянный ток. Этот метод применяют, когда затруднена или невозможна подача флюса и удаление шлаковой корки, например при наплавке мелких деталей, внутренних поверхностей и деталей сложной формы. Преимущества: высокая производительность и простота ведения и управления процессом. Недостатки6 сложность работы на открытом воздухе из-за срыва струи углекислого газа под действием ветра и окислительная способность углекислого газа.
4.5 Вибродуговая наплавка.
Автоматическая вибродуговая наплавка основана на использовании тепла кратковременной электрической дуги, возникающей в момент разрыва цепи между вибрирующим электродом и наплавляемой поверхностью. Отличительной особенностью этого вида наплавки является возможность получения наплавленного слоя малой толщины 0,3 – 0,25 мм, охлаждение поверхности наплавки в результате прерывистого характера процесса, что снижает нагрев детали и остаточные напряжения в ней.
Качество наплавленного слоя во многом зависит от материала электродной проволоки, которую выбирают в зависимости от требуемых механических свойств наплавленного слоя. автоматическую вибродуговую наплавку применяют для наращивания изношенных наружных и внутренних цилиндрических поверхностей (шеек валов, штоков, замков бурильных труб и других деталей). К преимуществам вибродуговой наплавки относятся: возможность получения тонких и прочных покрытий, малая глубина зоны термического влияния, небольшой нагрев детали и незначительное выгорание легирующих элементов электродной проволоки.
4.6 Наплавка металлов трением.
Сущность процесса наплавки металлов трением заключается в плавлении наносимого металла за счет теплоты трения и соединения его с деталью при повышенных температуре и давлении. Наносимый металл или сплав, в гранулированном состоянии, плавится в закрытом пространстве за счет трения о наплавляемую деталь или специальный инструмент. Трение обеспечивается вращением наплавляемой детали или инструмента относительно массы наносимого сплава или металла.
Основным условием для обеспечения плавления наносимого металла или сплава является изготовление инструмента (с помощью которого осуществляется трение) из материала с более высокой температурой плавления по сравнению с температурой плавления наносимого материала. Во избежании прилипания металла или сплава к рабочей поверхности инструмента его изготавливают из соответствующего материала. Основные технологические параметры процесса наплавки трением – это окружная скорость и давление на поверхности трения. Величины этих параметров определяются физическими характеристиками основного и наплавляемого материалов, в особенности коэффициентом трения и температурой плавления материала, а также материала детали и инструмента. Оптимальные значения параметров V=2,5-6 м/с, Р=2-6 кг/мм2. наплавка трением отличается от существующих методов наплавки полезным использованием теплового эффекта трения, отсутствием расплавлением основного и перегрева наплавляемого металлов, отсутствием их перемешивания, образованием металлического соединения между жидким и твердым металлами в условиях всестороннего сжатия и возможностью эффективного использования отходов механической обработки.
Преимущества: стабильность химического состава и сохранение исходных механических свойств в наплавленном слое; получение надежного соединения основного и наплавляемого металлов возможность наплавки комбинированным составом для получения заданных свойств в наплавленном слое; высокая экономичность процесса.
Недостатки: невозможность нанесения металлов более тугоплавких, чем основной металл; ограниченные размеры наплавляемых поверхностей; необходимость изготовления специальных приспособлений для наплавке деталей каждого типа. Процесс наплавки трением целесообразно применять для ремонта изношенных и изготовления биметаллических деталей, а также для поверхностного упрочнения деталей.
7. Ремонт деталей металлизацией.
Процесс металлизации заключается в нанесении расплавленного металла на специально подготовленную поверхность детали распылением его струёй воздуха или газа. Частицы расплавленного металла, ударяясь о поверхность детали, заполняют предварительно созданные на поверхности неровности, в результате чего происходит их механическое закрепление, а так же возникает молекулярное схватывание между наплавляемым и основным металлом. В результате закалки, окисления и наклепа частиц напыляемого металла твердость материала покрытия повышается. Различают газовую, электродуговую, высокочастотную, тигельную и плазменную металлизацию. Напыляемый материал применяется в виде проволоки, ленты или порошка. Наибольшее применение на ремпредприятиях получила электродуговая металлизация. Две электрически изолированные друг от друга электродные проволоки, к которым подведен электрический ток, перемещаются механизмом подачи. При их пересечении возникает ток, и проволоки расплавляются. Струя сжатого воздуха распыляет расплавленный металл на мельчайшие частицы и при скорости 75-200 м/с они наносятся на подготовленную поверхность детали, создавая напыленный слой. Для электродуговой металлизации выпускают стационарные и ручные металлизаторы.
Преимущество электрометаллизации – производительность.
Недостатки: выгорание легирующих элементов, окисление напыляемого металла, низкие механические свойства напыляемого слоя и большие потери металла при напылении.
При газовой металлизации проволоку напыляемого металла расплавляют ацетиленокислородным пламенем, а распыление осуществляется сжатым воздухом или инертным газом. Газовая металлизация обеспечивает получение покрытий высокого качества из-за меньшего выгорания легирующих элементов. Недостаток : необходимость горючего газа, большая стоимость покрытия. Газовая металлизация широко используется для напыления тугоплавких сплавов и металлов, например, титана.
Одним из прогрессивных методов является плазменно-дуговая металлизация. При пропускании эл.тока большой плотности через газовую среду, находящуюся под повышенным давлением, газ ионизируется. Наряду с положительно и отрицательно заряженными ионами в газе содержатся электроны и нейтральные атомы. Такое состояние вещества называется плазмой. Плазма обладает высокой электрической проводимостью и образует вокруг себя магнитное поле, которое заставляет частицы плазмы сжиматься и двигаться узким пучком. Плазменная струя служит интенсивным источником тепла, температура её достигает 150000С.
Схема плазменного металлизатора: между вольфрамовым электродом и соплом горелки создается дуговой разряд, в зону дуги подается инертный газ, который ионизируясь выходит из сопла виде плазменной струи. В зону плазменной струи непрерывно подается напыляемый материал, расплавленные частицы которого увлекаются плазменной струей и с высокой (900 м/с) скоростью напыляются на поверхность детали.
Плазменная металлизация применяется для напыления тугоплавких металлов и соединений ( вольфрам, окиси алюминия, карбиды, бориды и т.д. ).
Преимущества: предотвращается окисление напыляемых металлов; процесс производителен; достигается прочное сцепление напыляемого слоя с металлом детали.
Недостатки: высокая хрупкость напыленного слоя.
После металлизации производят механическую и термическую обработку детали для получения необходимых параметров восстанавливаемой поверхности.
8. Ремонт деталей гальваническим наращиванием.
Гальваническое наращивание металла на поверхность основано на процессе электролиза. Под действием постоянного электрического тока положительно заряженные ионы движутся к катоду, в качестве которого используется восстанавливаемая деталь, на которой выделяется металл и водород. Электролиз металлов может осуществляться с растворимыми и нерастворимыми анодами. Растворимые изготавливают из губчатого железа, меди или никеля в зависимости от вида электролитического процесса; нерастворимые из свинца, платины и других металлов. В комплект оборудования для гальванического наращивания входят: источник постоянного тока, ванны с химически стойкими облицовками, специальные контактные подвесные приспособления, нагревательные устройства, вентиляционное оборудование.
Для восстановления размеров изношенных поверхностей наибольшее применение находят электролитическое хромирование, осталивание, меднение и твердое никелирование.
Хромированиеприменяют для восстановления размеров деталей и получения декоративных, коррозиостойких и износостойких покрытий. Электролитический хром обладает высокой коррозионной стойкостью, низким коэффициентом трения, высокой твердостью, жаростойкостью, высоким пределом текучести. При тщательной подготовке поверхности прочность сцепления хрома со сталью, чугуном, медью и латунью достигает при сдвиге 30кгс/мм2. однако стали с высоким содержанием вольфрама и кобальта, а также высокоуглеродистые стали и высококремниевые чугуны хромировать нельзя, вследствие низкой прочности сцепления. Прочность сцепления резко снижается с увеличением толщины покрытия в связи с ростом остаточных напряжений. После хромирования снимается также усталостная прочность деталей вследствие значительной величины остаточных напряжений в покрытии. Усталостная прочность углеродистых сталей в результате хромирования снижается на 25-40%.
Электрохимическое осаждение хрома отличается от других процессов, как по составу электролита, так и по условиям протекания процесса. Осаждение хрома осуществляется в электролите, содержащем хромовый ангидрид с добавкой серной кислоты.
При хромировании применяют нерастворимые аноды из свинца или сплава свинца с сурьмой. Концентрацию хромового ангидрида в электролите можно изменять в широких пределах, распространение получили горячие электролиты с концентрацией CrO3 от 150 до 350 г/л. Условно хромовые покрытия разделяют на три вида: молочные, блестящие и матовые.
Блестящие покрытия отличаются высокой твердостью, высокой износостойкостью и хрупкостью, имеют на поверхности мелкую сетку трещин.
Молочные – более мягкие и вязкие. Без трещин. По сравнению с блестящими имеют большую износостойкость.
Матовые имеют повышенную твердость и хрупкость, низкую износостойкость, трещины на поверхности.
Для повышения износостойкости применяют пористое хромирование. Оно отличается от твердого дополнительной анодной обработкой (дехромирование) после наращивания хромового покрытия. В результате на покрытии образуется сеть углубленных трещин обеспечивающих большую маслоемкость при работе. Контроль хромового покрытия осуществляется путем наружного осмотра с простукиванием медным молотом.
Преимущества:
§ Высокая прочность сцепления покрытия с основным металлом.
§ Возможность получения покрытия с высокой износостойкостью, с химической тепловой стойкостью.
Недостатки : длительность, сложность, трудоемкость технологического процесса, высокая стоимость.
Хромирование применяют при ремонте штоков насосов, гильз цилиндров ДВС и насосов, гнёзд подшипников, шеек валов и других деталей.
Электролитическое осталивание. При прохождении постоянного тока низкого напряжения через раствор солей железа происходит осаждение на катоде (ремонтируемой детали) электролитического железа. Прочность и твердость осажденного слоя приближаются к аналогичным свойствам среднеуглеродистой стали, поэтому процесс получил название осталивание.
Для осталивания применяют горячие и холодные электролиты. В зависимости от состава электролита и режима осталивания получают мягкие покрытия с твердостью (НВ 120-220) и твердые покрытия с твердостью (НВ 250-600). Прочность сцепления на отрыв покрытия со сталью, медью и чугуном достигает 15 МПа, благодаря чему восстановленная деталь надежно работает при больших нагрузках. Прочность сцепления покрытия с металлом зависит от предварительной подготовки наращиваемой поверхности.
Преимущества:
§ Недефицитность и дешевизна исходных материалов.
§ Выход металла на тонну 75-95%.
§ Скорость осаждения металла и толщина покрытия значительно выше, чем при хромировании. Для твердых покрытий толщина 1-1,2 мм, для мягких 2-3 мм.
§ Механическую обработку покрытия после осталивания производят при обычных процессах резания.
§ Процесс устойчив и может быть автоматизирован.
Недостатки:
§ Высокая коррозионная активность электролита.
§ Сложность технологического процесса.
§ Необходимость частой фильтрации электролита.
Осталивание применяют для наращивания изношенных поверхностей гнезд подшипников, шеек валов, наружных поверхностей бронзовых втулок и т.д.
Меднение. Для меднения деталей применяют два типа электролитов: сернокислые и цианистые, последние токсичны и применяются редко. Аноды при медении применяют растворимые – медные пластины, катодом является ремонтируемая деталь.
На ремпредприятиях меднение применяют при восстановлении размеров бронзовых втулок, вкладышей подшипников, для облегчения приработки трущихся поверхностей и т.п.
Твердое никелирование. Электролитический процесс осаждения никеля называется твердым никелированием. Гальванически осажденный никель порист и имеет пониженную пластичность. Твердость никелированных покрытий составляет 30-60МПа. В зависимости от содержания в электролите получают матовые и блестящие осадки. Процесс ведется при температуре электролита 75-950С. Применяются растворимые аноды из никеля. Вследствие невысокой твердости и малой износостойкости никелирование применяют для восстановления размеров в неподвижных сопряжениях, например, для восстановления посадочных поверхностей деталей под подшипники.
9. Ремонт деталей с применением клеевых соединений.
Склеивание металлов основано на способности некоторых неметаллических материалов образовывать достаточно прочные связи с металлом. Клей для металлов приготавливают на основе термореактивных и термопластичных полимеров. Клей на основе термореактивных полимеров позволяет получить прочные и теплостойкие соединения. Клей на основе термопластичных полимеров позволяет получать менее прочные и с более низкой теплостойкостью соединения.
По внешнему виду клеи для металлов разделяют на жидкие, пастообразные, пленочные и порошкообразные. Они могут быть одно и много консистентными. Выбор клея в каждом конкретном случае должен определятся конструкцией склеиваемого узла, условиями эксплуатации и производительными возможностями предприятия. Физико-механические свойства клеевых соединений металлов зависят от технологии склеивания:
§ Подготовки металлических поверхностей.
§ Приготовления клеевого состава.
§ Технологии нанесения клея на поверхность.
§ Процесса отвердения клея.
Значительное влияние на прочность клеевого соединения оказывают конструктивные факторы и в частности форма и размеры клеевого соединения. На ремпредприятиях склеивание применяют для следующих работ:
§ Соединение частей разрушенных деталей.
§ Заделка трещин, свищей и раковин.
§ Посадка втулок и гнезд взамен запрессовки, приварки и пайки.
§ Восстановление и упрочнение прессовых насадок подшипников.
§ Фиксация сменных деталей.
§ Наложение заплат.
§ Герметизация неплотностей в резьбовых, фланцевых и сварных соединениях.
§ Наклеивание фрикционных накладок.
На практике ремонта бурового и НП оборудования клеи используют для ремонтов резервуаров, трубопроводов и арматуры, насосного и компрессорного оборудования, ДВС. Применение клеевых соединений упрощает технологический процесс ремонта, ускоряет его, снижает стоимость ремонта
Недостатки клеевых соединений:
§ Невысокая температура эксплуатации (до 3000С).
§ Низкая прочность при неравномерном отрыве.
§ Склонность к старению при воздействии различных внешних факторов.
Литература:
1) Авербух и др. «Ремонт и монтаж бурового и НП оборудования» Недра, 1976.
Лекция №10. Ремонт деталей сваркой и наплавкой
Сваркой называется процесс образования неразъемного соединения деталей или их отдельных частей вследствие межатомарного взаимодействия или действия сил молекулярного сцепления. Сваркой соединяют металлы и неметаллические материалы, например, стекло, пластмассы и др. При сварке металлов, за исключением холодной сварки, производят местный нагрев соединяемых частей до перехода их в пластическое (сварка давлением) или в расплавленное состояние (сварка плавлением). Стремятся, чтобы металл шва обладал одинаковыми свойствами с основным металлом. Это определяет подбор присадочного материала и режима сварки.
Оборудование, используемое при ремонте деталей сваркой, такое же, как и при сварке новых деталей. Сваркой соединяют отдельные части деталей, заваривают трещины, раковины и устраняют другие дефекты.
Наплавка — процесс нанесения расплавленного металла необходимого состава на поверхность детали, нагретую до температуры плавления, При наплавке нанесенный слой металла прочно соединяется с основным металлом вследствие образования металлической связи.
Наплавку применяют для восстановления размеров детали и придания заданных свойств ее поверхности путем правильного выбора химического состава и структуры наплавленного металла.
Наплавка является разновидностью сварки. Однако наплавочные процессы отличаются от сварочных. При наплавке сварочный процесс используется для наращивания на основной металл слоя металла или сплава со свойствами, иногда отличающимися от свойств основного металла.
В связи с этим к процессу наплавки предъявляются следующие основные требования;
1) для обеспечения заданных физико-механических свойств в наплавленном слое процесс наплавки не должен изменять исходного химического состава и структуры наносимого металла, т.е. при наплавке доля основного металла в наплавленном слое должна быть минимальной;
2) для сохранения прочности ремонтируемой детали процесс наплавки не должен изменять ее исходного химического состава, структуры и напряженного состояния;
3
Виды наплавки


Ручная
Механизированная
















Рисунок 10.1 – Виды ремонта деталей наплавкой
Лекция №10. Ремонт деталей сваркой и наплавкой
Сваркой называется процесс образования неразъемного соединения деталей или их отдельных частей вследствие межатомарного взаимодействия или действия сил молекулярного сцепления. Сваркой соединяют металлы и неметаллические материалы, например, стекло, пластмассы и др. При сварке металлов, за исключением холодной сварки, производят местный нагрев соединяемых частей до перехода их в пластическое (сварка давлением) или в расплавленное состояние (сварка плавлением). Стремятся, чтобы металл шва обладал одинаковыми свойствами с основным металлом. Это определяет подбор присадочного материала и режима сварки.
Оборудование, используемое при ремонте деталей сваркой, такое же, как и при сварке новых деталей. Сваркой соединяют отдельные части деталей, заваривают трещины, раковины и устраняют другие дефекты.
Наплавка — процесс нанесения расплавленного металла необходимого состава на поверхность детали, нагретую до температуры плавления, При наплавке нанесенный слой металла прочно соединяется с основным металлом вследствие образования металлической связи.
Наплавку применяют для восстановления размеров детали и придания заданных свойств ее поверхности путем правильного выбора химического состава и структуры наплавленного металла.
Наплавка является разновидностью сварки. Однако наплавочные процессы отличаются от сварочных. При наплавке сварочный процесс используется для наращивания на основной металл слоя металла или сплава со свойствами, иногда отличающимися от свойств основного металла.
В связи с этим к процессу наплавки предъявляются следующие основные требования;
1) для обеспечения заданных физико-механических свойств в наплавленном слое процесс наплавки не должен изменять исходного химического состава и структуры наносимого металла, т.е. при наплавке доля основного металла в наплавленном слое должна быть минимальной;
2) для сохранения прочности ремонтируемой детали процесс наплавки не должен изменять ее исходного химического состава, структуры и напряженного состояния;
3) наплавленный слой должен обладать достаточно высокой прочностью сцепления с основным металлом.
Рисунок 10.1 – Виды ремонта деталей наплавкой
Для ручной газовой и электродуговой наплавки обычно используют металлические электроды, что объясняется сравнительной простотой процесса наплавки и возможностью широкого регулирования химического состава и свойств наплавленного слоя. Регулирование химического состава и свойств наплавленного слоя осуществляют через покрытие или через электродный стержень, или комбинированным методом. Для предотвращения появления деформаций и трещин при наплавке применяют предварительный нагрев детали в пределах 200—400°С, предварительный изгиб детали в направлении, обратном деформации, погружение детали в воду без смачивания наплавляемой поверхности, наложение наплавляемых валиков в определенной последовательности, высокий температурный отпуск детали после наплавки.
Ручная газовая сварка и наплавка. При ручной газовой сварке и наплавке расплавление основного и присадочного материала осуществляется теплом, выделяющимся в процессе сгорания горючих газов (ацетилена, пропанбутановых смесей и других) в среде кислорода (рис. 5.10). Наиболее распространенным горючим газом, применяемым на ремонтных предприятиях, является ацетилен.
В зависимости от соотношения подаваемых в горелку ацетилена и кислорода можно получить нормальное, науглероживающее и окислительное пламя. Нормальное или, как его часто называют, нейтральное пламя образуется при соотношении кислорода и ацетилена в смеси, равном 1,0—1,2. Нормальное пламя является восстановительным в отношении к свободной закиси железа и в зоне I плавления ограничивает окисление поверхности. При соотношении кислорода и ацетилена, составляющем 0,8—0,9, возникает науглероживающее, а при соотношении, равном 1,2—1,5, окислительное пламя. Выбор сварочного пламени влияет на качество сварного шва или наплавки, а также на производительность процесса.
Сварку деталей из алюминиевых сплавов, а также из стали с содержанием углерода до 0,5% ведут нормальным пламенем. Науглероживающее пламя обычно используют для сварки деталей из серого чугуна и стали с содержанием углерода более 0,5%.
Для сварки деталей из цветных металлов, заварки трещин и раковин небольшой длины в чугунных деталях при толщине стенок 10—15 мм, а также для сварки деталей из малоуглеродистой стали толщиной до 7 мм применяют бензинокислородное пламя и горелку ГКУ-01-55.
Рисунок 10.2 – Ручная газовая наплавка
К недостаткам газовой наплавки следует отнести неравномерность толщины наплавленного слоя.
Электродуговая сварка и наплавка. Ручная электродуговая сварка и наплавка. При электродуговой сварке и наплавке источником тепла для расплавления металлов является электрическая сварочная дуга, возникающая между электродом и свариваемым металлом. Качество сварного шва и наплавленного слоя определяется диаметром электрода, типом и маркой электрода, величиной сварочного тока, напряжением на дуге, родом и полярностью тока, скоростью сварки и положением шва в пространстве.
При ручной электродуговой сварке и наплавке чаще всего используются металлические электроды, представляющие собой металлический стержень, на поверхность которого нанесен слой покрытия, предназначенного для стабилизации горения дуги, защиты расплавленного металла от кислорода и азота воздуха, легирования наплавленного металла. В состав электродных покрытий входят следующие группы компонентов: стабилизирующие, шлакообразующие, газообразующие, раскисляющие, легирующие и связующие. Электроды изготовляют диаметром 1,6—12 мм и длиной 225—450 мм. В зависимости от назначения стальные электроды подразделяются на типы. Тип и марку электродов выбирают в зависимости от химического состава металла ремонтируемой детали и требований, предъявляемых к сварному шву или наплавленному слою.
Диаметр электрода выбирают в зависимости от толщины наплавляемого слоя. При толщине наплавки менее 2 мм рекомендуется применять электроды диаметром 3 мм, а при большей толщине наплавки — электроды диаметром 4—5 мм.
При ремонте закаленных деталей ненаплавляемую часть детали погружают в воду во избежание отпуска. Наплавку легированных сталей производят при большой плотности тока с предварительным подогревом поверхности.
Ручную электродуговую наплавку целесообразно применять при небольшом объеме работ, а также при наплавке труднодоступных мест.
К преимуществам ручной
электродуговой наплавки относятся
удобство и простота процесса.
Недостатки ее — низкая производительность ,
низкая стабильность дуги и невысокое
качество наплавки.
Автоматическая электродуговая наплавка под слоем флюса. При указанном виде наплавки электрическая дуга горит под слоем флюса, подаваемого систематически в зону наплавки. В зоне горения дуги оплавляются поверхность детали, электрод и прилегающий слой флюса. Электродная проволока по мере оплавления автоматически подается в зону дуги одновременно с флюсом. При плавлении флюса выделяется газ и образуется газовая оболочка, защищающая расплавленный металл от взаимодействия с окружающим воздухом выгорания легирующих элементов. Кроме того, флюсовое покрытие способствует сохранению тепла дуги и препятствует разбрызгиванию жидкого металла.
На рис.10.3 представлена схема наплавки под слоем флюса тел вращения. Между поверхностью детали 5 и электродной проволокой 3 возбуждена электрическая дуга. Расплавленная капля металла электрода 3, смещаясь в направлении вращения детали, смешивается е расплавленным основным металлом детали, образуя сварочную ванночку. При остывании образуется наплавленный валик, который покрыт шлаковой коркой 7 и частично неиспользованным флюсом 1.
Наплавка в среде защитных газов. При этом виде наплавки защитный газ, подаваемый в зону наплавки под избыточным давлением, изолирует сварочную дугу и плавильное пространство от кислорода и азота воздуха.
Рисунок 10.3 – наплавка под
слоем флюса
Наплавка в среде защитных газов. При этом виде наплавки защитный газ, подаваемый в зону наплавки под избыточным давлением, изолирует сварочную дугу и плавильное пространство от кислорода и азота воздуха.
Наплавку углеродистых, легированных сталей и чугуна производят в среде углекислого газа; для высоколегированных сталей применяют аргон. При высокой температуре сварочной дуги происходит диссоциация углекислого газа. Образовавшийся атомарный кислород окисляет металл, что приводит к выгоранию железа и других примесей стали. Чтобы прекратить окисление, а также пополнить выгоревшие примеси при наплавке в углекислом газе применяют электродную проволоку, легированную марганцем и кремнием, которые связывают кислород и раскисляют ранее образовавшуюся закись железа. Образующиеся окислы марганца и кремния переходят в шлак.
Наплавку в среде защитных газов применяют, когда невозможна или затруднительна подача флюса и удаление шлаковой корки, например при наплавке мелких деталей, внутренних поверхностей и деталей сложной формы.
Преимуществами наплавки в среде защитных газов являются высокая производительность и простота ведения и управления процессом.
Недостатки ее — сложность работы на открытом воздухе из-за срыва струи углекислого газа под действием ветра и окислительная способность углекислого газа.
Вибродуговая наплавка. Автоматическая вибродуговая наплавка основана на использовании тепла кратковременной электрической дуги, возникающей в момент разрыва цепи между вибрирующим электродом и наплавляемой поверхностью. Отличительной особенностью этого вида наплавки является возможность получения наплавленного слоя малой толщины 0,3—2,5 мм, охлаждение поверхности наплавки в результате прерывистого характера процесса, что позволяет значительно уменьшить нагрев детали, снизить в ней остаточные напряжения и предотвратить ее деформирование.
Автоматическую вибродуговую наплавку применяют для наращивания изношенных наружных и внутренних цилиндрических поверхностей, в частности, шеек валов, штоков буровых насосов, замков бурильных труб и других деталей.
К преимуществам вибродуговой наплавки относятся: возможность получения тонких и прочных покрытий, малая глубина зоны термического влияния, небольшой нагрев детали и незначительное выгорание легирующих электродной проволоки.
Производительность при вибродуговой наплавке выше, чем ручной электродуговой, но ниже, чем при наплавке под флюсом.
Наплавка металлов трением. Сущность процесса наплавки металлов трением, предложенного и разработанного Я.М. Кершенбаумом и Б.А. Авербухом, заключается в плавлении наносимого металла за счет теплоты трения и соединении его с деталью при повышенных температуре и давлении. Наносимый металл или сплав в гранулированном состоянии (в виде стружки) плавится в закрытом пространстве за счет трения о наплавляемую деталь или специальный инструмент. Трение обеспечивается вращением наплавляемой детали или инструмента относительно массы наносимого металла или сплава.
Литература: 2 осн. [43-47], 3 осн. [122-143], 5 осн. [81-148].
Контрольные вопросы:
1. Какие особенности процессов сварки и наплавки?
2. Какие виды сварки и наплавки Вы знаете и объясните их различия в зависимости от технологических процессов?
Износ элементов механизмов происходит неравномерно. При этом из-за небольшого по сравнению с размерами детали повреждения, теряется ее работоспособность. Соответственно ухудшается или прекращается функционирование узла или даже всего механизма.
Из методов реставрации металла восстановление деталей сваркой и наплавкой стоит на первом месте по распространенности. Главных причин две:
- Восстановление исходных свойств элемента.
- Относительная дешевизна.
В статье мы остановимся на практическом применении методик восстановления, применительно к кузовным сварочным работам легковых и грузовых автомобилей.
В чем заключается ремонт?
Процессы сварки и наплавки принципиально отличаются мало. В первом случае расплав используется для соединения частей. Во втором выступает рабочим слоем, который наносят на поверхность детали, с целью восстановления ее первоначальных размеров.
Бывают ситуации, когда эти функции совпадают. Пример — восстановления днища кузова автомобиля, поврежденного коррозией. При этом, сильно разрушенные места заменяются листами металла, трещины и отверстия восстанавливаются наплавкой.
В других случаях, выработка на оси, либо обойме детали кузова полностью реставрируется методом наплавки. Одновременно сваркой может быть устранена (к примеру) трещина на этом же элементе.
Еще один пример: сварка рамы грузового автомобиля. Здесь свариваются элементы несущего каркаса, где возникли трещины, а наплавляются места выработок в проушинах и пазах крепления узлов, тяг, осей и пр.
Что касается износа железа, выбрать ремонт наплавкой не всегда целесообразно. Если автомобильный завод выпускает необходимые узлы, ремонт может свестись к вырезанию изношенной детали с последующей приваркой новой.
Как правило сварка кузова автомобиля применяется чаще чем наплавка на его деталях. Причина — характер износа, вызванный схожестью причин повреждений при эксплуатации.


Не важно какая это марка: ВАЗ 2109, грузовик «Хюндаи портер», «Лексус» или старенькая «Нива» — основное количество повреждений кузова приходится на коррозию и деформацию листового металла при авариях.
Применяемое оборудование
При всем разнообразии методики работ и инструментального обеспечения, классификация сварки при ремонтах автомобилей сводится всего к двум типам:
- Электрическая, преимущественно дуговая с использованием защитных газов либо флюсов.
- Газовая, с применением ацетилена или пропана.
Электрическая подразделяется на ручную, полуавтоматическую в среде инертных газов, под флюсом и пр.
Существуют и другие способы, например сварка лазерная, трением, диффузионная. Однако для ремонтов автомобилей они практически не используются.
В некоторых случаях используется такая разновидность сварки, как пайка. Применяют ее для ремонта повреждений патрубков из цветных металлов, блоков радиаторов, деталей оборудования рефрижераторов, выполненных из тонкой меди.
Какой сваркой лучше варить кузов автомобиля зависит от характера повреждений, а также особенностей места или детали, которую необходимо восстановить.
На сегодня выполнение основного объема работ осуществляют с помощью электричества. Газосварка, некогда бывшая чуть ли не единственным способом ремонта, на сегодня используется для соединения деталей из тонкого металла.
Кроме того, кислородно-ацетиленовая сварка по-прежнему популярна там, где к кузову крепятся различные тяги, создающие динамические нагрузки.
Из электрических приборов для небольших, ремонтов применяется сварка автомобиля инвертором, обычным ручным сварочным аппаратом. Для тонких работ, требующих высокого качества, а также наплавки используют полуавтоматы с углекислым или инертным газом.
С распространением алюминиевых и титановых сплавов арсенал механиков по ремонту пополнился аппаратами дуговой сварки неплавким электродом в среде инертных газов. С подачей плавящегося присадочного прутка рукой либо автоматически.
Требования к подготовке детали
Качество восстановления во многом зависит от того, насколько правильно мы будем готовить деталь. Это касается сварки, а особенно наплавки.
Металл тщательно зачищают от ржавчины с помощью угловой шлифовальной машины (УШМ), более известной как «болгарка». Либо ручной щеткой. При необходимости снимают фаску или выравнивают.
В ответственных случаях, при наплавке, пайке поверхность обезжиривают.
Хороший эффект дает обработка пескоструйными либо гидроабразивными аппаратами.
Трещины разделывают заточными дисками УШМ на всю глубину, чтобы получить на их месте V-образные канавки. Толстый металл обрабатывают с двух сторон. На их концах для устранения напряжений, предотвращения дальнейшего развития сверлят сквозные отверстия диаметром 4-6 мм.
Перед тем как наплавлять отверстия, их края зенкуют с одной либо двух сторон, при наличии резьбы ее высверливают.
Учитывая, что сварка авто электродом либо газовым пламенем, создает высокую температуру следует позаботится о сохранности примыкающих элементов отделки, эл. оборудования, пластиковых деталей.
Для этого снимают ремонтируемый элемент либо детали, могущие быть поврежденными. Если это по каким-либо причинам невозможно, применяют меры к их защите (закрывают, обкладывают мокрой ветошью).
Используемые электроды
Подбор электродов либо сварочной проволоки осуществляется исходя из трех параметров:
- Вида металла.
- Необходимой толщины детали либо слоя наплавки.
- Уровня ответственности восстанавливаемой детали.
Выполняя кузовной ремонт полуавтоматом с углекислотой используют порошковую сварочную проволоку, омедненную либо простую.
Наплавку слоя с высокими характеристиками по твердости выполняют электродами типа Т-620, с толстой обмазкой включающей графит, карбид бора и пр.
Необходимый диаметр электрода подбирают исходя из толщины свариваемого металла, по специальным таблицам.
Алюминиевые детали соединяют газовой (кислородно-ацетиленовой) либо дуговой сваркой. В последнем случае применяются электроды типа ОЗА-2. При технологии с неплавящимся вольфрамовым электродом, используют в качестве присадки пруток соответствующего алюминиевого сплава.
При наплавке изношенных деталей двигателя для получение легированных покрытий применяют проволоку типа Нп-65, с высоким содержанием углерода. Работы ведут под флюсом, в среде инертных газов.
Способы сварного ремонта кузовов легковых и грузовых автомобилей
Для сварки кузова как легковых авто, так и грузовозов используют самые различные технологии. Принципиально все они сводятся к электрической дуге либо раскаленной струе газа, но при этом нередко имеют существенные технологические отличия.
Ручной дуговой
Для работы применяют аппараты как переменного, так и постоянного тока. К первым относятся сварочные трансформаторы различны типов. Вторые представлены сварочными машинами и генераторами.
Трансформатор дает неустойчивую дугу, требует значительной силы тока на диаметре электрода (эта характеристика называется плотностью тока). При этом растет температура дуги, что чревато прожогом и перекаливанием.
Эта опасность для старых сварочных трансформаторов была актуальной, да и сейчас на вопрос: можно ли варить машину электросваркой, не всегда дают положительный ответ. Как минимум, если речь идет о самодельных устройствах либо обычных сварочных трансформаторах.
Ситуация изменилась с появлением инверторных аппаратов, но для соединения элементов из тонкого металла этот тип соединения применяют ограничено.
Как правило таким способом делают ремонт массивных деталей, наподобие станин или узлов из толстого металла, например — глушителей.


А. Тархомов сварщик со стажем 20 лет: «Современным инвертором кузов заварить можно в большинстве поломок. Разумеется, аппаратом профессионального уровня. Все от сварщика зависит. Не спецу заниматься подобными вещами не стоит категорически».
Автоматическая наплавка под флюсом
Используется достаточно широко для ремонта промышленного оборудования, особенно уникального. Для автомобильных ремонтов распространение невелико обычно, для восстановления путем наплавки деталей вращения (к примеру — распредвала).
Смысл метода заключается в том, что сварочная дуга горит не открыто, а под слоем специального порошка — флюса. Он защищает металл от окисления и соединения с азотом воздуха. Шов или слой наплавки по качеству не уступает исходному металлу, а при использовании специальных электродов может превосходить его по твердости и износостойкости.
Вибродуговой метод
Как и наплавка под флюсом применяется исключительно в заводских условиях, поскольку требует громоздких установок, обеспечивающих точное позиционирование детали.
Смысл заключается в колебательных движениях плавящегося электрода с частотой 100-120Гц, при напряжении 12-18 Вольт. При этом наплавка выполняется крохотными частичками металла с одновременным охлаждением.
В газовых защитных средах
Метод дающий наиболее качественный результат в условиях станций технического обслуживания и ремонтных мастерских.
Сварка либо наплавка ведется в среде инертного газа с помощью неплавящегося электрода (TIG), либо плавким электродом в окружении инертного, либо активного газа (MIG/MAG сварка соответственно).
Позволяет получать соединение, не уступающее выполненному в заводских условиях. Но главное с помощью этого метода автомобилистам впервые стал доступен текущий ремонт деталей, изготовленных из титановых и алюминиевых сплавов, высокопрочных легированных сталей.
Полуавтоматические способы
Один из наиболее популярных на сегодня методов, используемых небольшими мастерскими и частными мастерами.
Процесс ведется на воздухе либо под углекислым газом. В качестве плавящегося электрода используется сварочная проволока нужного состава. Подается она, сматываясь с катушки, по мере необходимости.
При этом даже устройства бытового уровня способны автоматически подстраивать скорость подачи проволоки в зависимости от силы дуги.
Альтернативная технология восстановления под давлением
Для восстановления деталей под давлением наплавка либо сварка не требуется. Деталь лишь предварительно нагревают до пластичности.
Смысл метода в изменении геометрических размеров деталей при их деформации. Различают три основных способа:
- осадка;
- обжатие;
- обсадка.
В первом случае при сжатии цилиндрических деталей типа втулок, с уменьшением высоты уменьшается внутренний диаметр. Обжатием деталь уменьшаю боковыми деформациями, а при обсадке наоборот — увеличивают (см. рисунок фото 8)
В некоторых случаях такие операции дополняют либо предваряют наплавкой.
Особенности сварки рамы грузовых автомобилей
Сварка деталей грузовика и легковой машины принципиально одинакова. Несущественные различия вызваны разной толщиной металла кузова.
Другое дело, когда речь идет о том, как правильно сварить сломанную раму на грузовике воспринимающую нагрузку перевозимого груза, порой весящего не меньше, чем сама машина.
При значительных повреждениях, вызванных авариями либо неправильно эксплуатацией целесообразно вырезать деформированный участок, заменив его целым.
При этом следует использовать исключительно методы, не перекаливающие металл.


Выполняя сварочные работы на каркасах старайтесь спланировать работу так, чтобы швы не располагались поперек сечения. Особенно в местах, где предполагается повышенная нагрузка.
При наплавке трещин их предварительно обрабатывают как рассказывалось в разделе о подготовке. Затем шов зачищают, а участок дополнительно усиливают металлической накладкой.
Категория:
Техническое обслуживание дорожных машин
Публикация:
Восстановление деталей электродуговой сваркой и наплавкой
Читать далее:
Восстановление деталей электродуговой сваркой и наплавкой
При восстановлении деталей ручную электродуговую сварку применяют для заварки трещин, приварки обломанных частей и заплат на пробоины, заплавки изношенных отверстий, наращивания изношенных кулачков и зубьев, а также для устранения повреждений в деталях из алюминиевых сплавов, чугуна и стали.
При ручной электродуговой сварке больше, чем при любом другом процессе, применяемом при восстановлении деталей, качество и производительность процесса зависят от квалификации сварщика, его умения правильно выбрать марку и диаметр электрода, режим сварки, приемы манипулирования концом электрода.
Газовую сварку используют при ремонте кабин и облицовки, а также для заплавки изношенных отверстий, наращивания обломанных ушков. Она основана на использовании теплоты, выделяющейся при сгорании ацетилена или других горючих газов в смеси с кислородом.
Рекламные предложения на основе ваших интересов:
При восстановлении деталей чаще всего в качестве горючего газа применяют ацетилен. Температура ацетилено-кислородного пламени в самой его горячей точке 3000—3150° С. При газовой сварке скорость нагрева и расплавления металла значительно меньше, чем при дуговой, а зона термического влияния значительно больше, поэтому не рекомендуется применять газовую сварку для устранения повреждений в деталях, изготовленных из чугуна.
Дуговая сварка в среде углекислого газа — один из наиболее эффективных процессов для устранения повреждений в тонколистовых стальных деталях. Она все больше вытесняет газовую и ручную электродуговую сварку при ремонте кабин, кузовов и ответственных металлоконструкций. Этот вид сварки отличается высокой производительностью, хорошим формированием сварного шва, легкостью ведения процесса во всех пространственных положениях, концентрацией теплоты в зоне сварки.
Автоматическая наплавка под слоем флюса (рис. 86) обеспечивает наиболее высокое качество наплавленного металла, так как сварочная дуга и ванна жидкого металла полностью защищены от вредного влияния кислорода воздуха, а медленное охлаждение способствует наиболее полному удалению из наплавленного металла газов и шлаковых включений. При автоматической наплавке заданный режим почти не изменяется.
При наплавке под слоем флюса электрическая сварочная дуга горит в закрытой полости из расплавленного минерального вещества (флюса). Флюс предотвращает разбрызгивание жидкого металла, обеспечивает формирование нормального сварного шва, защищает расплавленный металл от действия кислорода и азота воздуха, влияющих отрицательно на свойства наплавленного металла. Электродная проволока из кассеты к месту наплавки подается автоматической головкой.
Рис. 86. Схема механизированной наплавки под слоем флюса:
1 — источник тока для питания дуги, 2 — оболочка из жидкого флюса, 3 — устройство для подвода флюса, 4 — мундштук, 5 — электродная проволока, 6 — электрическая дуга, 7 — шлаковая корка, 8 — наплавленный слой, 9 — наплавляемая деталь, 10 — скользящий контакт
Применение флюса дало возможность использовать голую (без покрытия) электродную проволоку. Ток к проволоке подведен по скользящему контакту 10 на небольшом расстоянии от дуги, что уменьшило длину электрода, по которому протекает сварочный ток. Плотность тока при этом увеличилась в несколько раз, возросла и производительность наплавки. Питание дуги чаще всего осуществляется током от сварочных генераторов или выпрямителей.
Наплавкой под слоем флюса можно восстанавливать изношенные плоские, цилиндрические, резьбовые и другие поверхности деталей. Цилиндрические поверхности деталей, наплавляемые под слоем флюса, должны иметь наружный диаметр свыше 50 мм, так как на меньших сечениях расплавленный флюс и шлак из-за большого разогрева не успевают затвердевать и стекают с деталей. Механизированной наплавкой под слоем флюса восстанавливают катки, колеса, башмаки, валы, ролики, барабаны и др.
Разновидностями электродуговой наплавки под слоем флюса являются более производительная наплавка ленточным электродом, а также сварка и наплавка порошковой проволокой.
Автоматическая наплавка ленточным электродом производится специальным электродом, изготовленным из металлической ленты холодного проката толщиной 0,4—1,0, шириной 20— 100 мм. Благодаря тому, что при этом способе наплавки сварочная дуга непрерывно перемещается по торцу ширины ленты, проплавление основного металла неглубокое и его доля в наплавленном слое составляет 8—10%. Таким образом, влияние наплавки на структуру и механические свойства основного металла незначительно. Химический состав ленты и марку флюса выбирают в зависимости от назначения наплавки.
Способ обеспечивает высокую производительность работ: за один проход можно наплавить слой толщиной 2—7 мм и шириной, соответствующей ширине ленты.
Недостатки способа: потребности в ленте различной ширины для наплавки разнотипных деталей; невозможность применения наплавки для валов малых диаметров, шлицевых соединений, внутренних отверстий.Полуавтоматическая сварка и наплавка порошковой проволокой — это сравнительно новый процесс в ремонтном производстве. Сущность способа заключается в том, что в качестве электродного материала применяют специальную проволоку, в состав которой наряду с легирующими элементами введены защитные газо- и шлакообразующие вещества, благодаря чему достигается высокая твердость и износостойкость наплавленного металла. Для наплавки порошковой проволокой используют те же автоматы и полуавтоматы, что и для сварки и наплавки сплошными электродными проволоками под слоем флюса. Наплавку порошковой проволокой рекомендуется применять прежде всего для восстановления деталей с большим износом.
При устранении дефектов в корпусных чугунных деталях (трещин, обломов, пробоин) применяют самозащитную проволоку ПАНЧ-11 без подогрева и дополнительной защиты. По сравнению со специальными никелевыми электродами проволока ПАНЧ-11 обладает высокой стойкостью сварных соединений против околошовных трещин. Заваривают трещины самозащитной проволокой ПАНЧ-11 открытой дугой на постоянном токе прямой полярности участками длиной 20—50 мм с проковкой и охлаждением каждого участка до температуры 50° С. Для сварки рекомендуются полуавтоматы ПДПГ-500, ПДГ-300, А-547У, А-825М в комплекте с выпрямителями ВС-300.
При полуавтоматической сварке чугуна самозащитной проволокой ПАНЧ-11 процесс протекает стабильно, без разбрызгивания металла, сварочный шов формируется без подрезов, наплывов и других наружных дефектов. Металл шва имеет высокую обрабатываемость, плотность и прочность. Этот метод находит все большее применение на ремонтных предприятиях, его можно рекомендовать для холодной заварки трещин длиной до 200 мм, обломов, а также обварки заплат у тонкостенных чугунных деталей.
Вибродуговая наплавка — разновидность автоматической электродуговой наплавки. Она ведется колеблющимся электродом, что дает возможность наплавлять металл при низком напряжении источника тока. Благодаря этому образуется минимально возможная сварочная ванна, мелкокапельный переход металла с электрода на деталь. При вибродуговой наплавке получается достаточно хорошее сплавление основного металла с электродным, небольшой нагрев детали и малая по глубине зона термического влияния. Наиболее широкое применение получила вибродуговая наплавка в среде охлаждающей жидкости.
Принципиальная схема установки для вибродуговой наплавки в среде жидкости показана на рис. 87. К установленной в станок изношенной детали с помощью роликов по направляющему мундштуку подается проволока, которая сматывается с барабана. Одновременно с подачей проволоки от вибратора электроду сообщается колебательное движение частотой 50—100 Гц. Установка вибратора позволяет уменьшить мощность дуги, не уменьшая стабильности процесса. От источника постоянного тока через ролики и мундштук к электроду подводится плюс, а к детали через шпиндель станка — минус.
Рис. 87. Схема установки для вибродуговой наплавки в струе жидкости:
1—индуктивность, 2—генератор, 3—трубопровод, 4 — подающие ролики, 5 — барабан для электродной проволоки, 6 — вибратор, 7 — пружины, 8 — шестеренный насос, 9 — бак-отстойник, 10 — деталь с наплавленным слоем, 11 — зона наплавки, 12 — мундштук
В зону наплавки по трубопроводу непрерывной струей подается жидкость. С детали жидкость стекает в поддон станка, откуда попадает в бак-отстойник и далее насосом по трубопроводам снова подается к детали.
Вибродуговым способом могут наплавляться цилиндрические поверхности диаметром от 15 мм и выше, поверхности изношенных отверстий, подвижных и неподвижных соединений; поверхности под обоймы шариковых и роликовых подшипников; шейки валов, работающих в подшипниках скольжения, не испытывающие ударной нагрузки; шейки в местах прессовых посадок. Вибродуговая наплавка нежелательна для профильных поверхностей в виде резьб, мелких шлиц и т. д. Вибродуговую наплавку можно производить также под слоем флюса и в среде защитного газа.
Способ вибродуговой наплавки и сварки различных материалов в потоке воздуха применяют при восстановлении чугунных деталей. Деталь наплавляют с помощью автоматической вибродуговой головки, а для получения плотных и легко обрабатываемых слоев в зону сварки подают атмосферный воздух. С увеличением подачи воздуха наружная пористость наплавляемого металла уменьшается. Наименьшая пористость получается при расходе воздуха свыше 1600—2000 л/ч.
Рис. 89. Полуавтомат А-547У в комплекте с выпрямителем ВС-300:
1 — баллон с углекислым газом, 2 — подогреватель, 3 — редуктор-расходомер, 4 — держатель со шлангом, 5 — подающий механизм, 6 — сварочный выпрямитель, 7 — пульт управления
Наплавленный металл обладает невысокой твердостью, что позволяет производить токарную обработку слоя обычным инструментом. Для наплавки используют установку, состоящую из токарного станка, источника тока (три выпрямителя ВСГ-ЗА) и автоматической вибродуговой головки.
При наплавке в среде углекислого газа сварочная дуга и расплавленный металл защищаются от вредного влияния воздуха струей углекислого газа, специально подаваемого в зону сварки. Электродная проволока из кассеты непрерывно подается в зону сварки с заданной скоростью. Ток к проволоке подводится с помощью мундштука и наконечника, расположенного внутри газовой горелки, которая подает защитный газ в зону сварки.
Рис. 88. Схема процесса наплавки в среде углекислого газа:
1 — горелка, 2 — электродная проволока, 3 — мундштук, 4 — наконечник, 5 — сопло горелки,6 — основной металл, 7 — сварочная дуга, 8 — сварочная ванна, 9 — шов
Электродная проволока плавится под действием теплотыдуги; электродный металл переходит в сварочную ванну и смешивается с расплавленным основным металлом. В результате сплавления электродного и основного металлов образуется наплавленный валик, прочно соединенный с основным металлом.
При наплавке углекислый газ из баллона (рис. 89) проходит через подогреватель газа, осушитель, редуктор и расходомер (ротаметр). При выходе из баллона углекислый газ расширяется и температура его резко падает. Чтобы исключить резкое охлаждение газа и замерзание содержащейся в углекислом газе влаги, его сразу после выхода из баллона пропускают через подогреватель. Затем углекислый газ попадает в осушитель, представляющий собой цилиндр, заполненный веществом, которое поглощает влагу из углекислого газа (сили- кагель, обезвоженный медный купорос или хлористый кальций).
Наплавка в среде углекислого газа имеет ряд преимуществ перед другими методами наплавки: более высокая производительность труда по сравнению с наплавкой под слоем флюса, высокая экономичность процесса, хорошее качество наплавленного металла; возможность наплавки внутренних поверхностей изделий сложной формы и малых диаметров; улучшение условий труда рабочих. Кроме того, отпадает необходимость в применении различных приспособлений для удержания флюса и расплавленного шлака, как при наплавке под слоем флюса, что позволяет повысить автоматизацию процесса. Недостатки способа наплавки в среде углекислого газа: большие потери металла на разбрызгивание, потребность в применении специальных типов проволоки и особых источников питания.
Сущность процесса электроконтактной приварки стальной ленты заключается в приварке к поверхности деталей стальной ленты мощными импульсами электрического тока. В сварочной точке под действием импульса тока расплавляются металлы присадочного материала и детали. Присадочный материал (стальная лента) расплавляется не по всей толщине, а лишь в тонком поверхностном слое, в зоне контакта с деталью. Слой приваривают ко всей изношенной поверхности регулируемыми импульсами тока при вращательном движении детали со скоростью, пропорциональной частоте импульсов, и поступательном перемещении сварочной головки. Схема процесса приварки ленты приведена на рис. 90.
Для приварки ленты применяют установку 011-1-02, которая позволяет восстанавливать наружные и внутренние цилиндрические поверхности деталей. Технологический процесс целесообразно применять при восстановлении шеек валов под подшипники качения, посадочных отверстий стаканов подшипников и других деталей при износе до 0,4 мм.
Изношенную поверхность предварительно шлифуют, удаляя слой металла толщиной 0,15—0,2 мм. После этого деталь подают на установку. Накладывают на подготовленную поверхность мерный отрезок стальной ленты толщиной 0,4—0,8 мм (в зависимости от величины износа), который прижимают сварочными роликами установки. Материал ленты — средне- и высокоуглеродистые стали марок 45, 50, 65Г и др.
Импульсами тока прихватывают ленту в нескольких местах. Перемещая ролики в крайнее положение, переключают установку на рабочий режим и приваривают ленту.
Рис. 90. Схема процесса электроконтактной приварки стальной ленты:
1 — центры, 2 — восстанавливаемая деталь, 3 — ролики, 4 — лента, 5 — трансформатор, 6 — прерыватель тока
Процесс ведут при подаче жидкости (воды), которая охлаждает ролики сварочной головки и одновременно эффективно отводит теплоту от зоны приварки. При этом твердость восстанавливаемой поверхности увеличивается до HRC.55 и более. Этим достигается совмещение технологий нанесения покрытия и термической обработки. Последующую механическую обработку после приварки ленты производят на круглошлифовальных станках.
Использование электроконтактной приварки стальной ленты взамен вибродуговой наплавки позволяет повысить производительность восстановления деталей в 2,5 раза, снизить расход присадочных материалов в 4—5 раз, трудоемкость работ в 2,5 раза и повысить ресурс детали до уровня новой.
Электроконтактную приварку стальной проволоки применяют преимущественно для восстановления резьбы. Проволоку подают во впадину изношенной резьбы и прижимают контактным роликом. После включения тока ее приваривают. Диаметр проволоки подбирают с таким расчетом, чтобы после ее приварки и осадки металл заполнил впадину между витками восстанавливаемой резьбы и при этом оставался припуск на механическую обработку. Наилучшие результаты получаются в том случае, если диаметр присадочной проволоки равен шагу резьбы или больше его на 5—10%.
Рекламные предложения:
Читать далее: Газопламенное и плазменное напыление и наплавка
Категория: – Техническое обслуживание дорожных машин
Главная → Справочник → Статьи → Форум
Ремонт деталей сваркой
Ремонт деталей сваркой — выбор оборудования
Сварка — часто используемый метод для ремонта. В общем объеме ремонтных работ она занимает 70%. Значит, в этом непростом деле без нее не обойтись никак. Так же как и без инвертора, выбор которого зависит от габаритов и марки материала ремонтируемого.
Если говорить о марке, то выбирать оборудование нужно следующим образом:
• для сталей используют ручную сварку ММА на токе DС.
• для алюминиевых сплавов — инверторы TIG на токе AC.
Вся премудрость технологии сводится к сварке и наплавке.
Подготовка деталей к сварке и наплавке
ремонт распредвала
Уделите этому моменту достойное внимание.
Дефекты типа «скол» необходимо тщательно зачистить металлической щеткой, не желательно оставлять острые кромки, они – концентраторы напряжения. Поэтому кромки нужно скруглить, либо «притупить».
Сварка трещины
Трещины требуют полного удаления путем их разделки (то же с порами, раковинами), иначе оставшаяся внутри и заплавленная снаружи трещина при знакопеременных нагрузках, снова разрастется с выходом на наружный диаметр или поверхность.
При восстановлении деталей наплавкой
«Прохудившиеся» диаметры, требующие наплавки, просто тщательно защищаются металлической щеткой.
Не забывайте, что перед заваркой дефектов алюминиевых сплавов изделия и присадочный материал необходимо протравить в 4-5%-ном растворе едкого натра и 20-25%-ом растворе азотной кислоты, либо зачистить до металлического блеска и немедленно варить.
Какие изъяны устраняют?
Заваривают трещины на платформах и рамах, так же делают заплаты и разнообразные накладки и т.д. и т.п.
Производят восстановление резьб путем наплавки с последующей обработкой и нарезанием резьбы плашкой или метчиком. Соответственно, ремонтируют наружные и внутренние резьбы.
Выбор технологии восстановления деталей
Детали машин ремонтируют автоматической и полуавтоматической сваркой в углекислоте.
Автоматическая представляет собой полностью автономный процесс, нужно только лишь зафиксировать деталь и нажать кнопку, то же касается сварочных роботов.
При проведении ремонтно-восстановительных работ в автосервисе наиболее простой способ – полуавтоматической сварки, когда проволока подается с заданной скоростью, а горелка перемещается вручную вдоль шва. КПД полуавтомата существенно проще по сравнению с ручным инвертором и лучше качество шва. Газ, используемый для защиты: углекислота – активный , существенно окисляет расплавленную углеродистую сталь, а связывает и выводит кислород на поверхность марганец, в большом количестве присутствующий в проволоке 08Г2С. Сварка полуавтоматом в углекислоте идеальна для ремонта пальцев, фланцев карданных валов и т.д.
Популярна в деле ремонта и восстановления так же сварка под флюсом благодаря тому, что она обеспечивает высокую производительность и прочность, обеспечивая надежную защиту ванной. Она и названа так потому, что во время процесса дуга, зажженная между металлом и электродом скрыта под слоем флюса. Таким образом ремонтируют, например, распредвалы.
При небольшом износе на деталях с малым диаметром практикуют восстановление электроимпульсной наплавкой.
Е.А. СОЛОМКА 1 , А.И. ЛОБАНОВ 1 , Л.Н. ОРЛОВ 2 , А.А. ГОЛЯКЕВИЧ 2 и А.В. ХИЛКО 2
- 1 Компания «Энергомашспецсталь» Ул. Совхозная, 15, 84306, Краматорск, Донецкая область, Украина
- 2 TM.WELTEC Ltd. Ул. Боженко, 15, 03690, Киев, Украина.E-mail: [email protected]
Опубликовано в “The Paton Welding Journal” 2014 №6-7
В кузнечно-прессовом цехе ООО «Энергомашспецсталь» проводится ремонт и изготовление
приспособление для различных видов кузнечно-прессовых работ
в том числе забастовщики постоянно носят
вне. Чтобы увеличить жизнь и минимизировать сроки
ремонт инструментов, анализ применения существующих
отделочные материалы в наплавке забастовщиков было
осуществляется исходя из условия предоставления
сочетание цены и срока службы инструмента [1—7].Ремонт инструмента кузнечно-прессового оборудования
использование наплавки эффективно благодаря более низкой цене
по сравнению с покупкой новой детали. Dies
и бойки для горячей штамповки и ковки, пресс-формы
и литья под давлением подвергаются тепловым ударам,
высокие удельные давления, износостойкость, что приводит к
в образовании трещин, заусенцев и волосков,
потеря геометрии рабочих поверхностей деталей.
При выборе материала для нанесения
на ремонт штампов головок молотков и
высокоскоростные прессы, металл должен иметь сложный
свойств в зависимости от условий
контакта с горячим металлом.В условиях
быстрой деформации пластичность, устойчивость к
пламенная эрозия и пластическая деформация являются определяющими.
В условиях медленной деформации
повышенные требования к теплу и окислению
Сопротивление дополнительно уточняется [8].
В настоящей работе представлены особенности технологии
ремонтных покрытий ударника самолета и
плоские вставки из стали 5ХНМ изучаются (рисунок
1).
Этот тип светильника используется довольно интенсивно
в печати 31.5 МН силы для производства
часто разнообразная номенклатура продуктов,
что приводит к его быстрому локальному износу. После износа
рабочей поверхности и формирование перекрытий
металл, ударники и вставки подвергаются переточке
рабочей части толщиной около 70 мм
в среднем.
Для ремонта инструмента применение трех
варианты наплавки с использованием электродов разных
тип легирования (ХН65МВ; Стеллой С-О, Стеллой
Ni520-G и ОЗШ-1, ОЗШ-6).После предварительного изучения характеристик и
особенности применения этих расходных материалов
предпочтение отдавалось электродам ОЗШ-
1 и ОЗШ-6, поскольку они не требуют применения
спецтехники и их стоимость ниже. Наплавка производилась с подогревом Рис. 2. Схема расположения наплавленных слоев: 1 – подслой; 2 – прослойка; 3 – рабочий слой
После каждого прохода наносится осажденный слой было проведено. После завершения всплытия забастовщиков отправили в печь для отпуска при 580 ° С. Температура предварительно нагретой печи было 400 ° С, время выдержки составляло 3 ч, скорость нагрев и охлаждение печи составляло 50 ° С / час. Депонированный нападающий и вставка прошли проверку в печати 31.5 МН силы в кузнечно-прессовый цех. Сравнение жизни не депонированного инструмента и депонированного показал последующий:
- не депонированный ударник использовался в работе с 23.11.2011 г. по 25.01.2012 г. и допускал ковку 781,7 т при норме расхода 5,7 кг / т, а рабочая зона бойка требовала перешлифовки;
- депонированный ударник использовался с 25.01.2012 по 07.05.2012 и допускал ковку 2201,13 т при норме расхода 2.1 кг / т, что позволило в 2,8 раза увеличить срок службы инструмента (рис. 3).
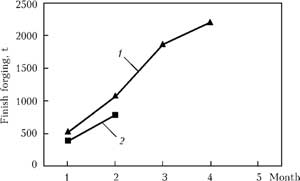
Экономический эффект в среднем 21 000 т / год закончить ковку в прессе силой 31,5 МН составил 98 700 грн.
Для восстановления и укрепления поверхности обеих изношенных частей штампов (ударов, пресс-формы из инструментальных сталей 5ХГМ, 5ХНВ, 5ХНМ, 7Х4, У10А и др.) А также новые, изготовленные из инструментальных и конструкционных марок сталей (45, ст5 и др.), предприятие TM.WELTEC Ltd. разработала порошковую проволоку WELTEC-h560-01 , WELTEC-h560-04 , WELTEC-h560-05 вместо электродов ЦШ-1 (30В8Х4), Ш-1, Ш-16, ЦН-4 (35Г6), ЦН-5, НЖ-2, НЖ-3 (ГОСТ 10051—62).
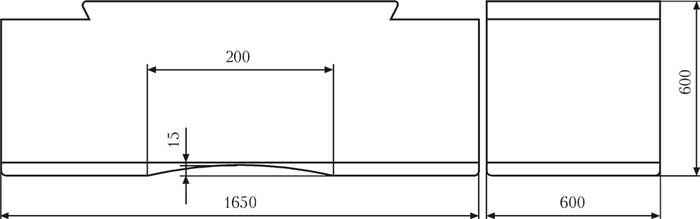
Система легирования порошковых проволок на основе оптимизации легирования наплавленного металла с углеродом, кремнием, марганцем, никелем, хром, молибден, ванадий, вольфрам и титан, благодаря которому получается низкоуглеродистый мартенситная матрица, усиленная дисперсностью карбиды и интерметаллиды, в депонированных металл обеспечен.
Металл, наплавленный порошковой проволокой WELTEC-h560-01 (HRC 38—45) и WELTEC-h560-05 (HRC 48—54) характеризуется высоким износостойкость в условиях эксплуатации штампов для холодной и горячей деформации металлов и удовлетворительно противостоит высокому давлению и шоки.Для всплытия пятен в бороздках матрица, требующая высокой твердости и износостойкости бойков кузнечно-прессового оборудования, рекомендуется использовать провод WELTEC-h560-05 .
Применительно к усилению и ремонту деталей штампов из сталей 5ХНМ, 5ХНВ, 38ХН3М-БА для прессования заготовок из меди, латуни Л63, сплавов ШВ15-1, предпочтительно применять провод WELTEC-h560-04 В (HRC 48—54). Депонированный металл обладает повышенной устойчивостью к «прилипанию» заготовки с рабочей поверхностью матрицы.Всплытие выполняется при постоянном токе реверса полярность с экранированием в смеси газов Ar + + 18% CO 2 .
Провод WELTEC-h560-01 также был успешно применяется для ремонта штампов производства коленчатые валы и шатуны двигателей автомобили «КамАЗ» (Набережные Челны, РФ) (рисунок 5).
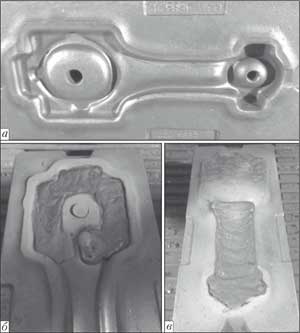
Опыт применения порошковой Провода WELTEC-h560-01 и WELTEC-h560-05 показали, что увеличение эффективности бойка, вставок и умирает достигается увеличением эффективности процесса наплавки, снижение затрат на дополнительные время и особенно снижением потребления отделочного материала. Расход электродов на 1 кг нанесенного металла до 1,8 кг, а для порошковой проволоки – 1,17 кг, при почти равной цене наплавочного материала.
Заключение
1. Применение полуавтоматической электрической дуги наплавка сокращает трудозатраты при ремонте арматуры для кузнечно-прессового оборудования и увеличений продолжительность цикла между ремонтами.2. Применение порошковой проволоки позволяет повышение эффективности наплавочных работ больше чем в 1,5 раза. ,
В принципе, сварочные процессы должны соединять материалы в соответствии с чертежами, основанными на соответствующем сварочном дизайне. Кроме того, важно обеспечить качество сварки, включая внешний вид и прочность сварного шва. На этой странице представлены типичные дефекты поверхности, которые ухудшают качество сварки.
Обязательно прочитайте для всех, кто связан со сваркой! Это руководство включает базовые знания о сварке, такие как типы и механизмы сварки, а также подробные знания, касающиеся автоматизации сварки и устранения неисправностей.Скачать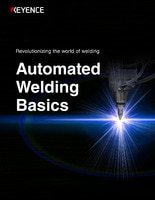
Ямы (открытые дефекты) – это поверхностные дефекты, возникающие, когда газовые полости, образованные внутри металла сварного шва, затвердевают после выхода газа с поверхности валика. Газовые полости, остающиеся внутри валика, являются внутренним дефектом, известным как продувочные отверстия. Причины этих дефектов включают использование неподходящего защитного газа; недостаточный раскислитель; масло, ржавчина, покрытие или другие вещества, прилипшие к поверхности канавки в основном материале; и влага, содержащаяся в материале.
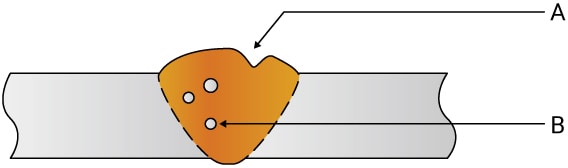
Подрез – это паз на носке сварного шва, образованный основным материалом, выходящим из сварного шва. Типичными причинами являются чрезмерно высокий сварочный ток или скорость сварки. Слишком большая ширина плетения также может быть причиной подреза.
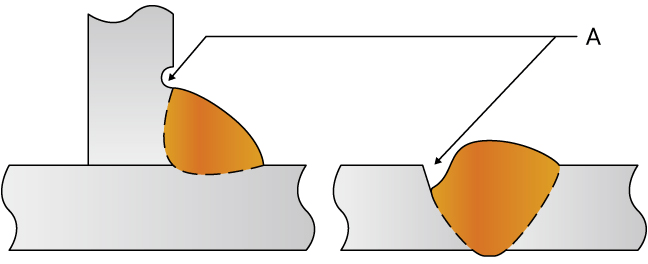
Перекрытие происходит, когда расплавленный металл протекает по поверхности основного материала, а затем охлаждается без слияния с основным материалом. Типичной причиной перекрытия является подача слишком большого количества сварочного металла из-за низкой скорости сварки. Перекрытие в угловых сварных швах вызвано падением избыточного расплавленного металла под действием силы тяжести.Необходимой контрмерой является проверка условий сварки (например, установка более высокой скорости сварки или более низкого сварочного тока).
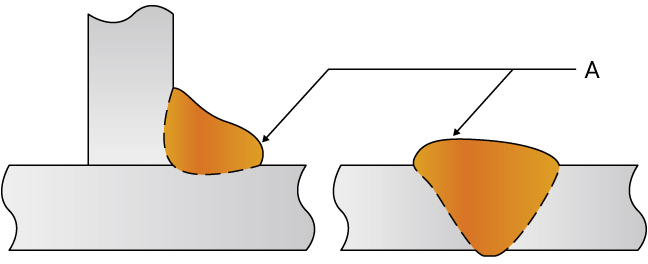
Армирование – это металл сварного шва, который накапливается над поверхностью, превышая требуемый размер в пазу или угловом шве. Типичная причина – высокая скорость сварки (скорость перемещения источника тепла), которая делает недостаточным отложение металла шва в канавке.
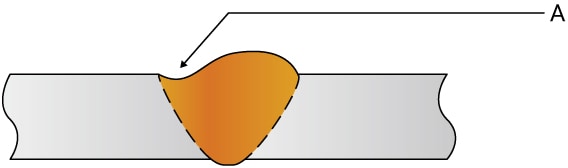
- Недостаточная арматура
Поверхностное растрескивание образует трещины на поверхности горячих сварных швов сразу после сварки.Это широко разделено на растрескивание затвердевания и растрескивание разжижения. Твердение трещины происходит, когда сварка затвердевает. Растрескивание в результате разжижения происходит при многослойной сварке, когда предыдущий сварочный слой расплавляется при последующей сварке. Другая классификация относится к сгенерированному положению и форме трещины, такой как продольное растрескивание, растрескивание носка, поперечное растрескивание, растрескивание кратера и так далее.
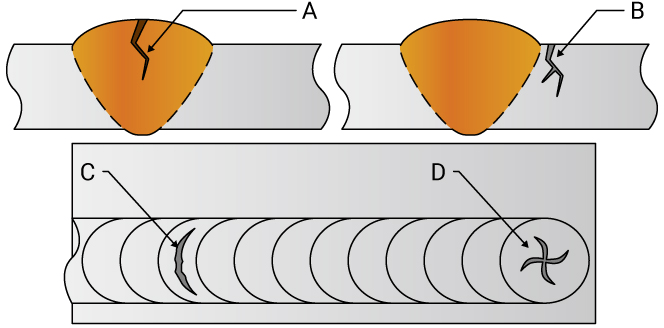
- Продольное растрескивание
- Растрескивание пальца ноги
- Поперечное растрескивание
- Растрескивание кратера
Это дефект, вызванный мгновенным ударом дуги по основному материалу.Другими словами, удар дуги – это место неудачного зажигания дуги, которое не было расплавлено при последующей сварке и осталось на основном материале. Удар дуги может быть причиной растрескивания основного материала.
Подобный дефект может возникать, когда крупные частицы брызг прилипают и остаются на поверхности.
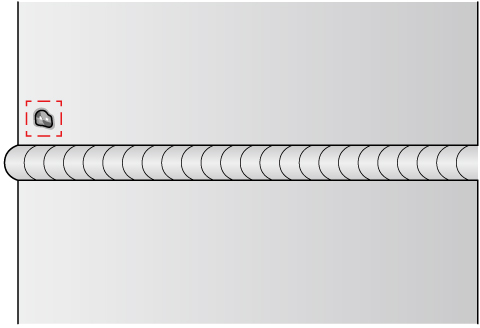
Этот дефект возникает, когда валик изгибается и отклоняется от линии сварки. Возможные причины включают волну или скручивание в автоматически поставляемой сварочной проволоке, которая не корректируется должным образом, или направления линии сварки и скручивания проволоки находятся под прямым углом друг к другу.Этот дефект также может возникать, когда настройки скорости подачи проволоки и сварочного тока не совпадают.
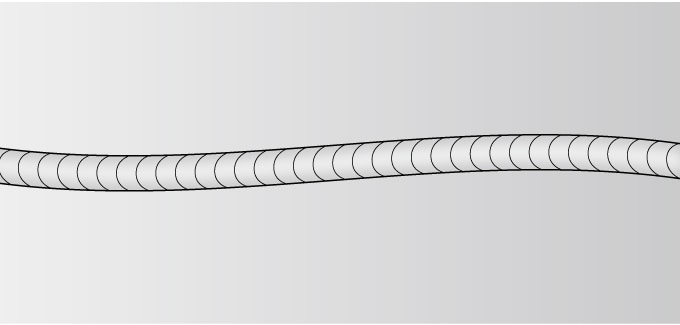
Это состояние, когда части канавки не приварены и остаются открытыми, потому что процесс не может сформировать валик, продолжающийся от начальной точки до конечной точки канавки. Когда этот дефект обнаруживается при сварке робота вокруг начальной или конечной точки, может возникнуть проблема в управлении роботом. Если подача дуги, газа или провода нестабильна, канавка также может оставаться открытой в середине валика.
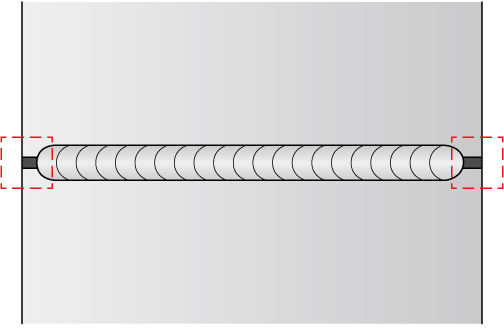
Дом
,Скачать ESAB Руководство по ремонту и техническому обслуживанию …
Руководство по ремонту и техническому обслуживанию Сварочное руководство, второе изданиеXA00086820
Руководство по выбору и применению Расходные материалы Esab по ремонту и техническому обслуживанию
1
Содержание Page 3 4
Предисловие Сокращения строжка – резка – прокалывание Предварительный нагрев и межпроходная температура Управление разбавлением сварочного металла Использование буфера слои и наплавляемые слои Сварка • • • • •
5 6 8 10
чугун «трудно свариваемые стали» разнородные металлы марганцевые стали инструментальные стали и стали для высокотемпературных применений
14 18 22 26 30
Наплавка
34 34 37 38 39
• • • • •
Факторы износа Основной материал Сварочные процессы Типы наплавленного металла с твердым покрытием Руководство по классификации расходных материалов для наплавки в соответствии с DIN 8555 • ESAB для наплавки продукты • Краткое руководство – выбор расходных материалов
40 41 42
Иллюстрированные области применения Расходные материалы – данные о продукте для • • • • • • • •
чугунные буферные слои и наплавляемые слои «трудно свариваемые стали» разнородные металлы марганцевые стали инструментальные стали и стали для высокотемпературных применений твердосплавные цветные металлы
Рекомендуемые температуры предварительного нагрева Сравнительные шкалы твердости Основание Руководство по идентификации металла Индекс применения – алфавитный порядок Продукт – индекс 2
45 Таблица Таблица Таблица Таблица Таблица Таблица Таблица Таблица Таблица
1 2 2 2 3 4 5 6
89 90 91 91 91 93 95 98 105
Таблица 7 108 Таблица 8 109 Таблица 9 110 112 115
Предисловие Каждый день сварщики во всем мире встречают инициалы с расходными материалами, которые они используют.Хорошо для Оскара Кьельберга, основателя Esab AB. Оскар Кьельберг первым изобрел новую сварочную технику, а затем применил покрытый электрод. Эти изобретения – происхождение Esab. Оскар Кьельберг получил квалификацию инженера и несколько лет работал на нескольких шведских пароходах. Именно в этот период в конце 1890-х годов он столкнулся с проблемой, для которой в то время не было эффективного решения. Заклепочные швы на паровых котлах часто протекают. Были предприняты попытки восстановить протекающие соединения с помощью гвоздей, которые были подделаны для получения небольших клиньев, которые затем были вдавлены в суставы.Простая электросварка уже использовалась, но Оскар Кьельберг видел ремонт электросварки, и результаты были неудовлетворительными, поскольку все еще были трещины и поры. Однако он понял, что этот метод может быть разработан и поддерживается ведущими верфями. Оскар Кьельберг организовал небольшую экспериментальную мастерскую в гавани в Гетеборге. На верфях Гетеборга этот метод быстро вызвал большой интерес. Было очевидно, что это может обеспечить огромные преимущества при сварке и ремонте судов.С тех пор эта техника ремонта получила дальнейшее развитие и была внедрена в других сегментах. Сегодня Esab может предложить расходные материалы для ремонта и технического обслуживания большинства материалов и процессов сварки. В этом руководстве вы найдете продукты Esab Repair & Maintenance и ряд приложений, в которых эти продукты используются. Продукты, показанные для каждого применения, являются общими рекомендациями и должны использоваться только в качестве руководства. Дополнительную информацию о продукте см. В Руководстве по сварке ESAB или у местного дилера Esab.
3
Сокращения Rm Rp 0.2 A HRC HB HV aw wh
= предел прочности = предел текучести = относительное удлинение после разрыва = твердость HRC = твердость по Бринеллю = твердость по Виккерсу = после сварки = закаленный
SMAW FCAW GMAW SA
= дуговая сварка в защитном металле (ручная дуговая сварка металлом) = дуговая сварка порошковой проволокой = дуговая сварка металлическим газом = дуговая сварка под флюсом
DC + DC – AC OCV
= постоянный ток – обратная полярность = постоянный ток – прямая полярность = переменный ток = напряжение холостого хода
Химические символы Al BC Cr Co Cu Mn Mo Nb Ni PS Si Sn Ti WV
4
Алюминий Бор Углерод Хром Кобальт Медь Марганец Молибден Ниобий Никель Фосфор Сера Кремний Олово Титан Вольфрам Ванадий
– Резка – Пирсинг Генерал ОК 21.03 – специально разработанный электрод для строжки, резки и пробивки стали, нержавеющей стали, марганцевой стали, чугуна и всех металлов, кроме чистой меди. Покрытие развивает сильную газовую струю, которая сдувает расплавленный материал. Держатель сжатого воздуха, газа или специальных электродов не требуется, так как используется стандартное сварочное оборудование. Канавки очень ровные и гладкие, поэтому сварка может выполняться без какой-либо дополнительной подготовки. Приготовление нержавеющей стали и марганцевой стали, однако, может потребовать небольшого помола.Примечание: электрод не предназначен для производства металла шва. Электрод доступен в 3,25, 4,0 и 5,0 мм.Применения OK 21.03 подходит для строжки при сварке на месте и в тех случаях, когда оборудование для строжки по угольной дуге нецелесообразно. Он отлично подходит для подготовки ремонта в чугуне, поскольку он высыхает и сгорает загрязнения / графит на поверхности и, таким образом, снижает риск растрескивания и пористости при сварке. Выдавливание марганцевой стали является еще одним подходящим применением.
Процедура Используйте в основном постоянный или переменный ток. Для резки и прокалывания рекомендуется DC +. Ударьте дугу, удерживая электрод перпендикулярно заготовке, после чего электрод должен быть направлен в соответствующем направлении, наклонен примерно на 5–10 ° от заготовки и выдвинут вперед. Держите электрод в контакте с заготовкой и перемещайте его, как ручную пилу. Если требуется более глубокий разрез, повторяйте процедуру до тех пор, пока не будет достигнута желаемая глубина. Прокалывать дыры очень легко. Держите электрод в вертикальном положении, зажмите дугу и надавите на электрод, пока он не проникнет в материал.Управляйте электродом распиливающим движением, чтобы увеличить отверстие.
5
Температуры предварительного нагрева и промежуточного прохода Для получения металла сварного шва без трещин наиболее важна температура предварительного нагрева, а также температура промежуточного прохода. Предварительный нагрев снижает: • риск растрескивания водорода • усадочное напряжение • твердость в зоне термического влияния (ЗТВ) • • • • • •
Потребность в предварительном нагреве увеличивается с учетом следующих факторов: содержание углерода в основном материале сплава Содержание основного материала Размер заготовки Начальная температура Скорость сварки Диаметр расходного материала
Как определить температуру предварительного нагрева Состав основного материала должен быть известен для выбора правильной температуры предварительного нагрева, так как температура предварительного нагрева составляет контролируется двумя основными факторами: • содержанием углерода в базовом материале; • содержанием сплава в базовом материале. В основном, чем выше содержание углерода в базовом материале, тем выше требуемая температура предварительного нагрева.Это также верно в отношении содержания сплава, но в несколько меньшей степени. Одним из способов определения температуры предварительного нагрева является расчет углеродного эквивалента, Ceq, на основе химического состава основного материала Ceq =% C +% Mn / 6 + (% Cr +% Mo +% V) / 5 + (% Ni + % Cu) / 15 Чем выше Ceq, тем выше требуемая температура предварительного нагрева. Другим важным фактором, определяющим температуру предварительного нагрева, является толщина и размер компонента. Температура предварительного нагрева увеличивается с увеличением размера и толщины детали.Когда определена правильная температура предварительного нагрева, важно, чтобы эта температура была получена и поддерживалась во время операции сварки. При предварительном нагреве важно время выдержки, чтобы довести весь компонент до необходимой температуры. Как правило, все предварительно нагретые сварочные работы должны медленно охлаждаться. В таблице приведены рекомендуемые температуры предварительного нагрева для ряда различных материалов. 6
Рекомендуемые температуры предварительного нагрева Основной материал Материал наполнителя
Толщина листа мм
Сталь
Легированная легированная сталь Ceq 12% Cr 18/8 Cr / Ni 14% Mn 300–500 HB 200–300 HB ~ 200 HB 250– 500 HB ° C ° C ° C ° C
Низколегированный 200–300 HB
≤20 -> 20 ≤60 -> 60 100
100 150 180
150 200 250
150 250 300
100 200 200
– – –
– – –
Инструментальная сталь 300–450 HB
≤20 -> 20 ≤60 -> 60 125
100 125 180
180 250 300
200 250 350
100 200 250
– – –
– оо
12% Cr сталь 300–500 HB
≤20 -> 20 ≤60 100> 60 200
150 200 250
200 275 350
200 300 375
150 200 250
– 150 200
xxx
Нержавеющая сталь 18/8 25/12 200 HB
≤20> 20 ≤60> 60
– – –
– 100 15 0
– 125 200
– 150 250
– 200 200
– – 100
– – –
Mn сталь 200 HB
≤20> 20 ≤60> 60
– – – –
– – –
– • 100 • 100
xxx
xxx
– – –
– – –
Co-type 6 6 HRC
≤20 100> 20 ≤60 300> 60 400
200 400 400
250 • 450 • 500
200 400 • 500
200 350 400
100 400 400
xxx
o– 100
,Сварка и подготовка поверхности
Благодаря линейке Unitor ™ каждое сварочное применение на борту имеет эффективное решение. Мы считаем, что безопасная сварка – это эффективная сварка, а эффективная сварка ведет к более строгому контролю затрат – сводит время простоя к ремонту до минимума и снижает риски для экипажа, груза и судна.
Все оборудование Unitor ™ спроектировано в полном соответствии с действующими правилами безопасности на море, и мы делаем техническую информацию доступной для конечных пользователей, помогая гарантировать, что оборудование всегда используется правильно и безопасно.
Разработан специально для морской индустрии
Это единственные на рынке сварочные аппараты, разработанные специально для морской промышленности. Некоторые из его новаторских функций включают в себя функцию полной защиты (TP), которая автоматически отключает машину, чтобы предотвратить повреждения, вызванные скачками напряжения или сбоями электроснабжения. Кроме того, функция устройства снижения напряжения (VRD) машины ограничивает напряжение разомкнутой цепи до диапазона 9-13 В, предотвращая несчастные случаи из-за поражения электрическим током.Оба эти новых усовершенствования способствуют безопасной сварке сосуда.
Полностью соответствует требованиям основных классификационных обществ
Изготовленные в полном соответствии с действующими нормами для морского использования, мы постоянно смотрим в будущее на изменения в правилах, чтобы наше оборудование всегда соответствовало требованиям. Ассортимент расходных материалов Unitor ™ является всеобъемлющим, и производство осуществляется в соответствии с четырьмя обществами большого класса (DNV GL, ABS, LR, BV).
Глобальная доступность в 2200 портах
Невозможно предсказать, когда и где возникнет необходимость в обслуживании или ремонте.Но одно можно сказать наверняка: когда это происходит, вам нужно подходящее оборудование под рукой, чтобы выполнить работу эффективно, с минимальным временем простоя. Наша стандартизированная сварочная продукция может быть доставлена через один из 2200 портов, которые мы обслуживаем через нашу глобальную сеть.
Структурированные учебные программы для экипажа
Бортовая сварка происходит в различных, сложных и даже непредсказуемых условиях, и диапазон базовых материалов, которые требуют резки или сварки, как правило, очень широк.Мы помогаем вам подготовиться к этому ряду задач с помощью наших специализированных программ обучения в сотрудничестве с нашими партнерами по всему миру, предлагая наилучшее качество обучения для вашей команды.
Документация – обязательное условие безопасной сварки.
При каждой возможности мы предлагаем поддержку, чтобы убедиться, что продукты Unitor ™ используются правильно и безопасно. Несмотря на то, что оборудование стандартизировано и легко в использовании, оно также подкреплено подробной документацией – руководствами пользователя, руководствами по сварке, селекторами расходных материалов, паспортами продукта, паспортами безопасности, настенными диаграммами для решения проблем и специальной литературой.
Узнайте больше о наших сварочных решениях
,