Режимы резания при фрезеровании на станках с чпу таблица: Упс! Страница не найдена!
alexxlab | 20.02.1988 | 0 | Разное
таблица, расчеты при обработке, калькулятор, нормативы для алюминия
17.07.2020
При токарной, фрезерной обработке материала на производстве, эффективность этой работы во многом зависит от корректности выставленных настроек инструментария. Поэтому важно провести расчет режимов резания для станков с ЧПУ, чтобы точно избежать возможных проблем. А их может быть масса. Это повреждение самой установки, порча отдельных элементов инструмента, а также лезвийных частей. Пострадать может и материал, что и происходит чаще всего. Поэтому результатом становится полный брак. Любые ошибки также неминуемо сокращают срок службы оборудования.
В принципе, для анализа понадобится изучить множество аспектов. Это и температура предполагаемого объекта, его величина, твердость, планируемая глубина подрезания. И только проведя полную проверку, допустимо приступать к работе. В противном случае это еще и небезопасно для самого сотрудника, осуществляющего процедуру.
Станок токарный ЧПУ, режимы резания
Этот вид инструментов предназначен для качественной обработки различных материалов.
Режущие приспособления также прослужат весь отведенный производителем эксплуатационный срок только в том случае, если при сверлении и подрезании правильно выбрана глубина. Естественно, что работа с металлом при серьезном погружении оказывает гораздо более сильное влияние на износ. Но и в этом варианте допустимо подобрать правильные характеристики и установки, чтобы максимально снизить нагрузку.
Режимы резания для фрезерования на ЧПУ станках позволяют точно рассчитать каждый элемент, проработать до момента притупления весь срок, который и отведен регламентом. Если же не выявить нужные параметры, то возможна бесполезная работа. Ведь режущие части могут прийти в негодность, а сотрудник не поймет этого момента заблаговременно.
Основные параметры
Теперь рассмотрим те характеристики, которые и определяют весь процесс в целом. Понятно, что самые важные аспекты – это скорость вращения шпинделя и подача. Эти два столпа держат на себе процесс. Но они могут сильно разниться, в зависимости от того, насколько глубоко предлагается погружаться в поверхность заготовки.
Сам конечный выбор зависит от сопутствующих факторов.
К ним можно отнести:
- • Охлаждение инструментария. Как известно, при высокой скорости вращения объект сильно разогревается. А это может привести к деформации или даже возгоранию, если речь идет о горючем сырье. Особенно актуально при работе с деревом.
- • Слой. То есть, какую часть поверхности предполагается снимать за проход. И это опять же зависит от всех смежных факторов. Ведь чем больше высота слоя, тем сильнее предполагается нагрузка.
- • Жесткость. Насколько устойчив к механическому эффекту объект.
- • Стратегия работы. Устанавливается на каждом предприятии в индивидуальном порядке.
- • Размер.
Подразумевается величина самой заготовки.
Соответственно, нормативы режимов резания для станков с ЧПУ могут разниться, если учитывать весь комплекс озвученных параметров. Операция по фрезе при работе со сталью или пластмассой занимает разное количество времени. Это логично. Но при некорректном выборе параметром эта цифра по временному диапазону возрастает еще сильнее. Что ставит под угрозу темпы выполнения плана на производстве.
С описанными выше сопутствующими факторами мы немного разобрались. Теперь же перейдем к основным характеристикам, которые и нужно учитывать при анализе.
Глубина
Под этим понятием подразумевается высота слоя, который необходимо снять для выполнения задачи. Не за один проход, а в принципе. Поэтому если подразумевается большая глубина, то понадобится два-три или более повтора. Причем последний из них всегда будет учитываться в меньшей степени. Ведь он фактически является чистовым, то есть направлен на выравнивание поверхности. Первые проходы идут грубым методом, главное — больше снять. А вот чистовой просто правит заготовку, словно прошлись наждачной бумагой.
Параметр глубины строго фиксируется и определяется перпендикулярным замером. Где плоскостью для изучения является сама деталь.
Стоит понимать, что режимы резания алюминия на ЧПУ будут в значительной степени отличаться от той же стали. Ведь жесткость последней выше. И при установке определенной глубине, в первом случае понадобится меньше проходов. Снять стружку с мягкого материала куда легче, можно топить резец намного сильнее.
Подача
В этом случае подразумевается перемещение шпинделя. Вычисляется в миллиметрах. Мы узнаем, какой путь проходит элемент за время равное одной минуте. Этот важный аспект, который имеет простую формулу для выведения. Нам понадобится выявиться подачу на один зуб, а после умножить это число на количественный фактор зубьев в инструменте. А дальше, нужно выявить, сколько оборотов делает фреза за отрезок времени. Он равен минуте, как мы помним. Это значение мы снова умножаем на полученное ранее число.
Получается: А*В*С. Где А – подача на зуб, В – их количество, С – обороты в минуту. Чтобы расчеты не проводить на каждый инструмент и материал отдельно, можно использовать калькулятор режимов резания ЧПУ. Такие программы легко найти на специализированных ресурсах, как в платном, так и в бесплатном виде.
Скорость
Это длительность пути фрезы за минуту. Обозначается уже в метрах. И обычно это справочное стандартное число, которое нужно знать перед работой с заготовкой. Оно зависит от двух моментов. Стойкости самого материала, а также качества фрезы. Указывается обычно в двух вариантах. Штатный и максимальный. Первый предназначается для выявления скорости, при которой срок эксплуатации не снижается выше заявленного производителем. Но обычно ориентируются на второй – это темп, который позволит эффективно выполнять работу, но не подвергать инструмент опасности поломки фрезы.
По уровню КПД именно максимальный параметр лучше всего. Иначе, выбирая режимы резания стали ЧПУ станками (как самого жесткого материала), беспокоясь о сроке годности фрезы, можно сильно увеличить срок выполнения процесса. А это скажется на общих объемах производства. Поэтому не принято экономить в этом моменте.
Все три параметра имеют примерно идентичное значение. Если не брать в расчет один из них, просто не использовать при анализе. То в результате вся работа окажется неэффективной. Так же как и сопутствующие факторы, описанные выше. То есть, только совокупный, комплексный подход может предоставить необходимые результаты. А также нужно всегда ориентироваться на справочные значения, которые предоставляет как производитель, так и свободно распространяются в сети.
Таблица режимов резания при фрезеровании ЧПУ
Прежде чем мы перейдем к конкретному выбору, давайте посмотрим, как выглядит текущий вариант нормативных рекомендаций.
Материал заготовки |
Фреза |
Обороты |
Подача |
Скорость |
Акрил |
Используется спиральная. Почти во всех случаях однозаходная. Но если толщина акрила не превышает 6 мм, то подходит двухзаходная |
18 тысяч |
5 |
1-2 |
Пластик |
Опять же 2-заходная с 1.5 мм |
24 тысячи |
10-20 |
2-3 |
Композит |
Применяется и 1 и 2-заходная. |
От 15 до 18 тысяч |
10-12 |
1-2 |
Дерево |
Зависит от типа работы. Если речь идет про раскрой, то нужна стандартная спиральная. Круглая понадобится, если мы работаем с гравировкой. Ну, а если подразумевается V-образная обработка, то логично подойдет V-гравер. |
Не выше 15 тысяч |
10-15 |
2-3 |
Латунь и бронза |
Сплавная спираль |
15 тысяч |
5 |
1-2 |
Алюминий |
Такая же спиральная, но максимум 2-заходная |
От 15 до 18 тысяч |
12-20 |
1-2 |
МДФ |
Спираль с 1 или 2 заходами |
От 20 до 21 тысячи |
15-20 |
4-5 |
Теперь, когда у нас есть общее представление, мы можем переходить к типу обработки. Стоит помнить, что указанные нормативы имеют значение, только если брать во внимание все озвученные выше моменты. А в первую очередь, характеристики инструмента. Ведь в таблице не учитываются данные по самому агрегату. Его качество зависит от производителя. И ввиду этого принципиально важно подобрать хороший товар. Ясно, что для оптимизации производства все компании стараются искать «золотую середину». Но помните, что часто продукты из этой серии просто не могут долгое время работать с серьезными задачами. Сэкономив, можно сильно потерять в иных факторах. Частая смена деталей, комплектующих, выход из строя до заявленного срока. Покупку лучше совершать у надежного поставщика, который сможет оправдать возложенные на него ожидания. Ведь никакой расчет токарных режимов резания на ЧПУ, анализ и вдумчивый выбор не поможет, если агрегат просто не справляется со своей задачей.
Итак, перейдем к типам работ.
Точение
Это базовый, вместе с тем наиболее простой и весьма эффективный способ обработки детали. Он определяется комплексом из двух фундаментальных элементов. Первый – вращения. Это значит, что чем выше интенсивность, тем сильнее возрастает нагрузка. Но при этом есть и второй способ воздействия – перемещение самого инструмента.
Главным критерием является заявленное качество обработки. При высоком значении процесс серьезно осложняется. Но если подразумевается создание проходных деталей, программирование установки — это легко.
Сверление
Значительная часть заготовок подразумевают наличие различных отверстий. Они могут понадобиться по разнообразным причинам. Часто это функциональные полости, пазы, сквозные проходы для обеспечения задач будущей модели. Но порой это просто способы сцепления, фиксации и сборы всего узла.
Вне зависимости от этих причин, подобные отверстия создаются посредством сверления. Важно учитывать глубину и диаметр. И точно выставлять настройки в соответствии с этими требованиями. В одних случаях, когда это проход для проводки, как вариант, точность не самая важная часть. Ошибка в 1-2 мкм не стоит ничего. А если это функциональный паз, который впоследствии подразумевается как вакуумно-обособленный, то значение становится принципиальным.
Стоит также знать, что часто способ сверления применяется в качестве разрушения заготовки по различным нуждам. И тогда конкретно точность диаметра уже не имеет никакого значения.
Работа такого типа выдвигает и определенные нормативы к инструменту. Чем серьезнее требования к отверстию, тем более высококачественным должно быть оборудование. Точность, мощность, производительность, качество. Сверяются все эти данные, вычисляется, может ли агрегат в принципе выполнять подобную задачу. И лишь после этого происходит программирование установки.
Выбор режимов резания на токарном станке с ЧПУ
Нельзя выбирать только исходя из расчетных сведений таблиц. Разумеется, если все данные по материалу есть, то нормативы имеют место быть. Но их всегда нужно разбирать в условиях техники, имеющийся на производстве. Также стоит рассматривать конкретный тип сырья. ПВХ – это неоднородная группа, как и акрил, даже дерево. Ведь всем параметры, принимаемые к одному материалу, не всегда подходят к другому. Это более твердый материал, не такой деликатный и не подверженный расколу.
То есть, исходить нужно из комплекса аспектов.
Что важно знать
Ошибка в выборе конкретного метода зачастую не критична. Но при этом она всегда влияет на сам станок. И чем чаще будут появляться подобные неточности, тем быстрее он просто перестанет работать.
Также стоит брать в расчет, что ошибки могут возникнуть не только при анализе, но и при программировании. Задачу ставит компьютер, он также может сбоить. Да и человеческий фактор никто не отменял. Лучше перепроверить, чем потом жалеть.
Расчет скорости
Правильный выбор определяет нужное количество оборотов. И это практически единственный параметр, который не содержит точных рекомендаций. Можно было заметить, что в приведенной таблице часто оперируют понятиями «от» и «до», а также «не выше». Значит, допускается весьма серьезная погрешность. И она кардинальным образом на полученный результат влияния не оказывает.
Способы повышения эффективности работы
Существует определенный ряд несложных рекомендаций, способных если не в несколько раз, то на ощутимый процент увеличить результативность. А также сократить потенциальный износ. Что в совокупности ведет к серьезным экономическим выгодам. Особенно если речь идет о цехе, где установлено большое количество оборудования.
- • Если предполагается работа с ПВХ, то выбирать всегда стоит пластик литьевого производства. Ведь он защищен от термического воздействия. Его температура плавления на порядок выше. А, как мы помним, при работе на массе оборотов, под 18 тысяч, заготовка сильно разогревается.
И может быть повреждена.
- • Акрил и алюминий – это два материала, которые тоже не любят термическое воздействие. И обожают греть даже на средних оборотах. Но с ними логичнее всего использовать смазочно-охлаждающую жидкость. Логичнее будет приобрести специальные растворы, которые на современном рынке довольно популярны. Но если хочется сэкономить, а в бухгалтерии отдельной статьи расходов на СОЖ нет, то можно поступить проще. И заменить смазку обычной водой.
- • Пластик и акрил любят фрезы с одним заходом. Как уже стало ясно, материалы не выносят излишнего тепла. А значит, единичный заход позволит без проблем отводить стружку. И давать возможность остывать. В противном случае вполне возможно довести заготовку до плавления.
- • При выборе стратегии обработки всегда рассчитывайте процесс в условиях беспрерывности. Паузы не должны образовываться ни на одном участке. Иначе в совокупности это принесет серьезное снижение продуктивности.
- • Для избегания появления проблемных зон на пластиковой заготовке рекомендуется использоваться встречную фрезеровку.
- • Помните, что последним проходом будет чистовая обработка. Держите ее в памяти. И не пытайтесь запускать фрезу на всю глубину с первого захода. Только в случаях, когда внешний вид поверхности и текстура в принципе не имеют никакого значения.
- • Когда размер заготовки очень мал, всегда нужно работать на минимальных оборотах. Иначе резец просто начнет колоть деталь.
Подведем итоги
Становится понятно, что режимы резания при токарной обработке ЧПУ имеют важное значение. Без их правильного выбора в принципе невозможно грамотно организовать процесс производства. Да и масса сопутствующих моментов тоже оказывают свое существенное влияние. Поэтому перед началом работы с любым материалом стоит провести полный расчет. А также принять во внимание показатели инструмента. Проконсультироваться по тем или иным вопросам, получить помощь в выборе необходимого оборудования вы можете, связавшись со специалистами нашей компании «Сармат» по контактному телефону.
Режимы резания при фрезеровании: таблица, элементы, выбор режимов
Скорость резания
Наиболее важным режимом при фрезеровании можно назвать скорость резания. Он определяет то, за какой период времени будет снят определенный слой материала с поверхности. На большинстве станков устанавливается постоянная скорость резания. При выборе подходящего показателя учитывается тип материала заготовки:
- При работе с нержавейкой скорость резания 45-95 м/мин. За счет добавления в состав различных химических элементов твердость и другие показатели меняются, снижается степень обрабатываемости.
- Бронза считается более мягким составом, поэтому подобный режим при фрезеровании может выбираться в диапазоне от 90-150 м/мин. Она применяется при изготовлении самых различных изделий.
- Довольно большое распространение получила латунь.
Она применяется при изготовлении запорных элементов и различных клапанов. Мягкость сплава позволяет повысить скорость резания до 130-320 м/мин. Латуни склонны к повышению пластичности при сильном нагреве.
- Алюминиевые сплавы сегодня весьма распространены. При этом встречается несколько вариантов исполнения, которые обладают различными эксплуатационными характеристиками. Именно поэтому режим фрезерования варьирует в пределе от 200 до 420 м/мин. Стоит учитывать, что алюминий относится к сплавам с низкой температурой плавления. Именно поэтому при высокой скорости обработки есть вероятность существенного повышения показателя пластичности.
Встречается довольно большое количество таблиц, которые применяются для определения основных режимов работы. Формула для определения оборотов скорости резания выглядит следующим образом: n=1000 V/D, где учитывается рекомендуемая скорость резания и диаметр применяемой фрезы. Подобная формула позволяет определить количество оборотов для всех видов обрабатываемых материалов.
Рассматриваемый режим фрезерования измеряется в метрах в минуту режущие части. Стоит учитывать, что специалисты не рекомендуют гонять шпиндель на максимальных оборотах, так как существенно повышается износ и есть вероятность повреждения инструмента. Поэтому полученный результат уменьшается примерно на 10-15%. С учетом этого параметра проводится выбор наиболее подходящего инструмента.
Скорость вращения инструмента определяет следующее:
- Качество получаемой поверхности. Для финишной технологической операции выбирается наибольший параметр. За счет осевого вращения с большим количеством оборотов стружка получается слишком мелкой. Для черновой технологической операции, наоборот, выбираются низкие значения, фреза вращается с меньшей скоростью, и размер стружки увеличивается. За счет быстрого вращения достигается низкий показатель шероховатости поверхности. Современные установки и оснастка позволяют получить поверхность зеркального типа.
- Производительность труда.
При наладке производства уделяется внимание и тому, какова производительность применяемого оборудования. Примером можно назвать цех машиностроительного завода, где налаживается массовое производство. Существенное снижение показателя режимов обработки становится причиной уменьшения производительности. Наиболее оптимальный показатель существенно повышает эффективность труда.
- Степень износа устанавливаемого инструмента. Не стоит забывать о том, что при трении режущей кромки об обрабатываемую поверхность происходит ее сильный износ. При сильном изнашивании происходит изменение показателей точности изделия, снижается эффективность труда. Как правило, износ связан с сильным нагревом поверхности. Именно поэтому на производственной линии с высокой производительностью применяется оборудование, способное подавать СОЖ в зону снятия материала.
При этом данный параметр выбирается с учетом других показателей, к примеру, глубины подачи. Поэтому технологическая карта составляется с одновременным выбором всех параметров.
Параметры режима резания
Основными характеристиками, которые регулируются в процессе фрезерования и являющиеся составляющими режима резания являются:
- глубина реза – это толщина металла снимаемая за один проход. Выбирается с учетом припуска на обработку;
- ширина реза – показатель ширины снимаемого слоя металла по направлению перпендикулярному направлению подачи;
- подача инструмента – перемещение обрабатываемой поверхности относительно оси фрезы. В расчете режима используются такие показатели как подача на один зуб, в минуту и на один оборот. На величину подачи влияет прочность инструмента и характеристики оборудования.
Глубина резания
Другим наиболее важным параметром является глубина фрезерования. Она характеризуется следующими особенностями:
- Глубина врезания выбирается в зависимости от материала заготовки.
- При выборе уделяется внимание тому, проводится черновая или чистовая обработка. При черновой выбирается большая глубина врезания, так как устанавливается меньшая скорость.
При чистовой снимается небольшой слой металла за счет установки большой скорости вращения инструмента.
- Ограничивается показатель также конструктивными особенностями инструмента. Это связано с тем, что режущая часть может иметь различные размеры.
Глубина резания во многом определяет производительность оборудования. Кроме этого, подобный показатель в некоторых случаях выбирается в зависимости от того, какую нужно получить поверхность.
Мощность силы резания при фрезеровании зависит от типа применяемой фрезы и вида оборудования. Кроме этого, черновое фрезерование плоской поверхности проводится в несколько проходов в случае, когда нужно снять большой слой материала.
Особым технологическим процессом можно назвать работу по получению пазов. Это связано с тем, что их глубина может быть довольно большой, а образование подобных технологических выемок проводится исключительно после чистовой обработки поверхности. Фрезерование т-образных пазов проводится при применении специального инструмента.
Нагрев и смазывание
При повышении температуры и налипании стружки фреза утрачивает свои эксплуатационные характеристики, и работает хуже. Чтобы избежать поломки, нанесения вреда древесине или другим материалами, рекомендуется смазывать рабочие механизмы.
Необходимы к использованию:
- спирт и специальные эмульсии – при резке или сверлении алюминия и цветных металлов;
- мыльная вода – при обработке деталей, в составе которых имеется плексиглас.
При этом необходимо контролировать подачу и ее скорость. Определение оптимальных значений осуществляется в зависимости от материала и его толщины. Для настройки нужного показателя следует пользоваться значениями из таблицы.
Подача
Понятие подачи напоминает глубину врезания. Подача при фрезеровании, как и при проведении любой другой операции по механической обработке металлических заготовок, считается наиболее важным параметром. Долговечность применяемого инструмента во многом зависит от подачи. К особенностям этой характеристики можно отнести нижеприведенные моменты:
- Какой толщины материал снимается за один проход.
- Производительность применяемого оборудования.
- Возможность проведения черновой или чистовой обработки.
Довольно распространенным понятием можно назвать подачу на зуб. Этот показатель указывается производителем инструмента, зависит от глубины резания и конструктивных особенностей изделия.
Как ранее было отмечено, многие показатели режимом резания связаны между собой. Примером можно назвать скорость резания и подачу:
- При увеличении значения подачи скорость резания снижается. Это связано с тем, что при снятии большого количества металла за один проход существенно повышается осевая нагрузка. Если выбрать высокую скорость и подачу, то инструмент будет быстро изнашиваться или попросту поломается.
- За счет снижения показателя подачи повышается и допустимая скорость обработки. При быстром вращении фрезы возможно существенно повысить качество поверхности.
На момент чистового фрезерования выбирается минимальное значение подачи и максимальная скорость, при применении определенного оборудования можно получить практически зеркальную поверхность.
Довольно распространенным значением подачи можно назвать 0,1-0,25. Его вполне достаточно для обработки самых распространенных материалов в различных отраслях промышленности.
Что такое скорость вращения шпинделя и подача?
Скорость вращения — один из основных параметров шпинделя. Он выражается в оборотах в минуту (об/мин) или герцах (Гц). В портальных станках с ЧПУ не используется сложных по конструкции механических коробок передач и скорость регулируется электронными компонентами. С увеличением скорости вращения растет производительность станка и снижается ресурс режущего инструмента. Последнее связано с выделением избыточного количества тепла, которое не успевает рассеиваться. В результате перегрева падает твердость режущих кромок, и они теряют свою остроту.
Скорость подачи, или линейного перемещения, измеряется в миллиметрах в минуту (мм/мин) и влияет на объем снимаемого материала в единицу времени. На портальных станках без механизма вращения заготовки регулируются скорости перемещения портала, каретки и вертикального движения шпинделя. При составлении управляющих программ стараются задать максимально возможные подачи, при этом должно выполняться условие сохранения целостности фрезы. Избыточная скорость приводит к появлению сколов на режущих кромках поломка или деформация хвостовика.
Ширина фрезерования
Еще одним параметром, который учитывается при механической обработки заготовок считается ширина фрезерования. Она может варьировать в достаточно большом диапазоне. Ширина выбирается при фрезеровке на станке Have или другом оборудовании. Среди особенностей отметим следующие моменты:
- Ширина фрезерования зависит от диаметра фрезы. Подобные параметры, которые зависят от геометрических особенностей режущей части, не могут регулироваться, учитываются при непосредственном выборе инструмента.
- Ширина фрезерования также оказывает влияние на выбор других параметров.
Это связано с тем, что при увеличении значения также увеличивается количество материала, который снимается за один проход.
В некоторых случаях ширина фрезерования позволяет получить требуемую поверхность за один проход. Примером можно назвать случай получения неглубоких канавок. Если проводится резание плоской поверхности большой ширины, то число проходов может несколько отличаться, рассчитывается в зависимости от ширины фрезерования.
Подача и скорость фрезы
Величина подачи зависит, в первую очередь от типа обработки – черновая или чистовая. При чистовом резе подача определяется требованиями к качеству поверхности. При черновом необходимо учесть несколько факторов:
- жесткость заготовки, инструмента и станка;
- материал заготовки и фрезы;
- угол заточки фрез;
- мощность привода станка.
Скорость обработки определяется по нормативам, в которых учитывается тип инструмента и материал заготовки. Данный параметр выбирается по стандартной таблице.
Необходимо учесть, что значения в таблице приведены для стандартной стойкости инструмента. Если фреза не соответствует стандартным параметрам, то необходимо учесть поправочный коэффициент который зависит от ширины инструмента (для торцовых фрез), свойств заготовки, угла фрезы и наличия окалины.
Как выбрать режим на практике?
Как ранее было отмечено, в большинстве случаев технологические карты разработаны специалистом и мастеру остается лишь выбрать подходящий инструмент и задать указанные параметры. Кроме этого, мастер должен учитывать то, в каком состоянии находится оборудование, так как предельные значения могут привести к возникновению поломок. При отсутствии технологической карты приходится проводить выбор режимов фрезерования самостоятельно. Расчет режимов резания при фрезеровании проводится с учетом следующих моментов:
- Типа применяемого оборудования. Примером можно назвать случай резания при фрезеровании на станках ЧПУ, когда могут выбираться более высокие параметры обработки по причине высоких технологических возможностей устройства.
На старых станках, которые были введены в эксплуатацию несколько десятков лет назад, выбираются более низкие параметры. На момент определения подходящих параметров уделяется внимание и техническому состоянию оборудования.
- Следующий критерий выбора заключается в типе применяемого инструмента. При изготовлении фрезы могут применяться различные материалы. К примеру, вариант исполнения из быстрорежущей качественной стали подходит для обработки металла с высокой скоростью резания, фреза с тугоплавкими напайками предпочтительно выбирается в случае, когда нужно проводить фрезерование твердого сплава с высоким показателем подачи при фрезеровании. Имеет значение и угол заточки режущей кромки, а также диаметральные размер. К примеру, с увеличением диаметра режущего инструмента снижается подача и скорость резания.
- Тип обрабатываемого материала можно назвать одним из наиболее важных критериев, по которым проводится выбор режима резания. Все сплавы характеризуются определенной твердостью и степенью обрабатываемости.
К примеру, при работе с мягкими цветными сплавами могут выбираться более высокие показатели скорости и подачи, в случае с каленной сталью или титаном все параметры снижаются. Немаловажным моментом назовем то, что фреза подбирается не только с учетом режимов резания, но и типа материала, из которого изготовлена заготовка.
- Режим резания выбирается в зависимости от поставленной задачи. Примером можно назвать черновое и чистовое резание. Для черного свойственна большая подача и небольшой показатель скорости обработки, для чистовой все наоборот. Для получения канавок и других технологических отверстий и вовсе показатели подбираются индивидуально.
Как показывает практика, глубина резания в большинстве случаев делится на несколько проходов при черновой обработке, при чистовой он только один. Для различных изделий может применяться таблица режимов, которая существенно упрощает поставленную задачу. Встречаются и специальные калькуляторы, проводящие вычисление требуемых значений в автоматическом режиме по введенным данным.
Ширина и глубина
Данные параметры имеют важное значение для рационального выбора режима фрезерования. Глубина, как правило, устанавливается на максимально допустимое значение для уменьшения количества проходов. При повышенных требованиях к чистоте и точности обработки применяются черновой и чистовой проходы, соответственно, для съёма основной массы металла и калибровки поверхности. Количество черновых проходов может быть увеличено для повышения качества реза.
Читать также: Ответный фланец что это такое
При выборе глубины также необходимо учесть припуск на обработку. Как правило, несколько проходов применяется при значении припуска более 5 мм. При последнем черновом проходе оставляют около 1 мм на чистовую обработку.
При подборе ширины необходимо учесть, что при одновременной обработке нескольких деталей учитывается общее значение. Выбирая данные значения необходимо учесть и состояние поверхности заготовки. При наличии следов литья, окалины или загрязнений необходимо увеличить глубину реза. В противном случае возможно скольжение зуба, дефекты поверхности, быстрый износ режущих кромок.
При выборе глубины реза существуют следующие типовые рекомендации:
- Чистовая обработка – до 1 мм.
- Черновая по чугуну и стали – от 5 до 7 мм.
- Черновая для разных марок стали – от 3 до 5 мм.
Выбор режима в зависимости от типа фрезы
Для получения одного и того же изделия могут применяться самые различные виды фрез. Выбор основных режимов фрезерования проводится в зависимости от конструктивных и других особенностей изделия. Режимы резания при фрезеровании дисковыми фрезами или другими вариантами исполнения выбираются в зависимости от нижеприведенных моментов:
- Жесткости применяемой системы. Примером можно назвать особенности станка и различной оснастки. Новое оборудование характеризуется повышенной жесткостью, за счет чего появляется возможность применения более высоких параметров обработки. На старых станках жесткость применяемой системы снижается.
- Уделяется внимание и процессу охлаждения. Довольно большое количество оборудования предусматривает подачу СОЖ в зону обработки. За счет подобного вещества существенно снижается температура режущей кромки. СОЖ должна подаваться в зону снятия материала постоянно. При этом также удаляется и образующаяся стружка, что существенно повышает качество резания.
- Стратегия обработки также имеет значение. Примером можно назвать то, что получение одной и той же поверхности может проводится при чередовании различных технологических операций.
- Высота слоя, который может сниматься за один проход инструмента. Ограничение может зависеть от размера инструмента и многих других геометрических особенностей.
- Размер обрабатываемых заготовок. Для больших заготовок требуется инструмент с износостойкими свойствами, который при определенных режимах резания сможет не нагреваться.
Учет всех этих параметров позволяет подобрать наиболее подходящие параметры фрезерования. При этом учитывается распределение припуска при фрезеровании сферическими фрезами, а также особенности обработки концевой фрезой.
Классификация рассматриваемого инструмента проводится по достаточно большому количеству признаков. Основным можно назвать тип применяемого материала при изготовлении режущей кромки. К примеру, фреза ВК8 предназначена для работы с заготовками из твердых сплавов и закаленной стали. Рекомендуется применять подобный вариант исполнения при невысокой скорости резания и достаточной подаче. В тоже время скоростные фрезы могут применяться для обработки с высоким показателем резания.
Как правило, выбор проводится с учетом распространенных таблиц. Основными свойствами можно назвать:
- Скорость резания.
- Тип обрабатываемого материала.
- Тип фрезы.
- Частота оборотов.
- Подача.
- Тип проведенной работы.
- Рекомендуемая подача на зуб в зависимости от диаметра фрезы.
Использование нормативной документации позволяет подобрать наиболее подходящие режимы. Как ранее было отмечено, разрабатывать технологический процесс должен исключительно специалист. Допущенные ошибки могут привести к поломке инструмента, снижению качества поверхности заготовки и допущению погрешностей в инструментах, в некоторых случаях, поломке оборудования. Именно поэтому нужно уделять много внимания выбору наиболее подходящего режима резания.
Особенности фрезерования
Процесс фрезерования является одним их наиболее сложных из всех видов металлообработки. Основной фактор – это прерывистый характер работы, когда каждый из зубьев инструмента входит в кратковременный контакт с обрабатываемой поверхностью. При этом каждый контакт сопровождается ударной нагрузкой. Дополнительные факторы сложности – более одной режущей поверхности и образование прерывистой стружки переменной толщины, что может стать серьёзным препятствием для работы.
Поэтому очень важен правильный подбор режима резания, что позволяет добиться максимальной производительности оборудования. Сюда входит правильный выбор подачи, скорости и силы реза, а также глубины удаляемого слоя что позволяет получить необходимую точность при минимальных затратах и износе инструмента.
Выбор режима в зависимости от материала
Все материалы характеризуются определенными эксплуатационными характеристиками, которые также должны учитываться. Примером можно назвать фрезерование бронзы, которое проводится при скорости резания от 90 до 150 м/мин. В зависимости от этого значения выбирается величина подачи. Сталь ПШ15 и изделия из нержавейки обрабатываются при применении других показателей.
При рассмотрении типа обрабатываемого материала уделяется внимание также нижеприведенным моментам:
- Твердости. Наиболее важной характеристикой материалов можно назвать именно твердость. Она может варьировать в большом диапазоне. Слишком большая твердость делает деталь прочной и износостойкой, но при этом усложняется процесс обработки.
- Степени обрабатываемости. Все материалы характеризуются определенной степенью обрабатываемостью, зависящая также от пластичности и других показателей.
- Применение технологии улучшения свойств.
Довольно распространенным примером можно назвать проведение закалки. Подобная технология предусматривает нагрев материала с последующим охлаждением, после чего показатель твердости существенно повышается. Также часто проводится ковка, отпуск и другие процедуры изменения химического состава поверхностного слоя.
В заключение отметим, что сегодня можно встретить просто огромное количество различных технологических карт, которые достаточно скачать и использовать для получения требуемых деталей. При их рассмотрении уделяется внимание типу материала заготовки, виду инструмента, рекомендуемому оборудованию. Самостоятельно разработать режимы резания достаточно сложно, при этом нужно делать предварительную проверку выбранных параметров. В противном случае может пострадать как инструмент, так и применяемое оборудование.
Рекомендации при выборе режима
Идеально подобрать режим обработки практически невозможно, но есть ряд рекомендаций, которым желательно следовать:
- Диаметр инструмента должен соответствовать глубине обработки. Это позволяет провести обработку в один проход, но для слишком мягких материалов есть риск снятия стружки большей толщины, чем необходимо.
- По причине ударов и вибрации желательно начать с подачи порядка 0,15 мм на зуб и затем регулировать в большую или меньшую сторону.
- Не желательно использовать максимальное количество оборотов, это может привести к падению скорости реза. Повысить частоту можно при увеличении диаметра инструмента.
Определение режима реза производится не только с помощью таблиц. Большую роль играет знание особенностей станка и личный опыт фрезеровщика.
Режимы резания при фрезеровании: таблица, элементы, выбор режимов
Поверхностная обработка заготовок методом фрезерования может проводиться исключительно после разработки технологической карты, в которой указываются основные режимы обработки. Подобной работой, как правило, занимается специалист, прошедший специальную подготовку. Режимы резания при фрезеровании могут зависеть от самых различных показателей, к примеру, типа материала и используемого инструмента. Основные показатели на фрезерном станке могут устанавливаться вручную, также проводится указание показателей на блоке числового программного управления. Особое внимание заслуживает резьбофрезерование, так как получаемые изделия характеризуются довольно большим количеством различных параметров. Рассмотрим особенности выбора режимов резания при фрезеровании подробно.
Содержание
Скорость резания
Наиболее важным режимом при фрезеровании можно назвать скорость резания. Он определяет то, за какой период времени будет снят определенный слой материала с поверхности. На большинстве станков устанавливается постоянная скорость резания. При выборе подходящего показателя учитывается тип материала заготовки:
- При работе с нержавейкой скорость резания 45-95 м/мин. За счет добавления в состав различных химических элементов твердость и другие показатели меняются, снижается степень обрабатываемости.
- Бронза считается более мягким составом, поэтому подобный режим при фрезеровании может выбираться в диапазоне от 90-150 м/мин. Она применяется при изготовлении самых различных изделий.
- Довольно большое распространение получила латунь.
Она применяется при изготовлении запорных элементов и различных клапанов. Мягкость сплава позволяет повысить скорость резания до 130-320 м/мин. Латуни склонны к повышению пластичности при сильном нагреве.
- Алюминиевые сплавы сегодня весьма распространены. При этом встречается несколько вариантов исполнения, которые обладают различными эксплуатационными характеристиками. Именно поэтому режим фрезерования варьирует в пределе от 200 до 420 м/мин. Стоит учитывать, что алюминий относится к сплавам с низкой температурой плавления. Именно поэтому при высокой скорости обработки есть вероятность существенного повышения показателя пластичности.
Встречается довольно большое количество таблиц, которые применяются для определения основных режимов работы. Формула для определения оборотов скорости резания выглядит следующим образом: n=1000 V/D, где учитывается рекомендуемая скорость резания и диаметр применяемой фрезы. Подобная формула позволяет определить количество оборотов для всех видов обрабатываемых материалов.
Рассматриваемый режим фрезерования измеряется в метрах в минуту режущие части. Стоит учитывать, что специалисты не рекомендуют гонять шпиндель на максимальных оборотах, так как существенно повышается износ и есть вероятность повреждения инструмента. Поэтому полученный результат уменьшается примерно на 10-15%. С учетом этого параметра проводится выбор наиболее подходящего инструмента.
Скорость вращения инструмента определяет следующее:
- Качество получаемой поверхности. Для финишной технологической операции выбирается наибольший параметр. За счет осевого вращения с большим количеством оборотов стружка получается слишком мелкой. Для черновой технологической операции, наоборот, выбираются низкие значения, фреза вращается с меньшей скоростью, и размер стружки увеличивается. За счет быстрого вращения достигается низкий показатель шероховатости поверхности. Современные установки и оснастка позволяют получить поверхность зеркального типа.
- Производительность труда.
При наладке производства уделяется внимание и тому, какова производительность применяемого оборудования. Примером можно назвать цех машиностроительного завода, где налаживается массовое производство. Существенное снижение показателя режимов обработки становится причиной уменьшения производительности. Наиболее оптимальный показатель существенно повышает эффективность труда.
- Степень износа устанавливаемого инструмента. Не стоит забывать о том, что при трении режущей кромки об обрабатываемую поверхность происходит ее сильный износ. При сильном изнашивании происходит изменение показателей точности изделия, снижается эффективность труда. Как правило, износ связан с сильным нагревом поверхности. Именно поэтому на производственной линии с высокой производительностью применяется оборудование, способное подавать СОЖ в зону снятия материала.
При этом данный параметр выбирается с учетом других показателей, к примеру, глубины подачи. Поэтому технологическая карта составляется с одновременным выбором всех параметров.
Глубина резания
Другим наиболее важным параметром является глубина фрезерования. Она характеризуется следующими особенностями:
- Глубина врезания выбирается в зависимости от материала заготовки.
- При выборе уделяется внимание тому, проводится черновая или чистовая обработка. При черновой выбирается большая глубина врезания, так как устанавливается меньшая скорость. При чистовой снимается небольшой слой металла за счет установки большой скорости вращения инструмента.
- Ограничивается показатель также конструктивными особенностями инструмента. Это связано с тем, что режущая часть может иметь различные размеры.
Глубина резания во многом определяет производительность оборудования. Кроме этого, подобный показатель в некоторых случаях выбирается в зависимости от того, какую нужно получить поверхность.
Мощность силы резания при фрезеровании зависит от типа применяемой фрезы и вида оборудования. Кроме этого, черновое фрезерование плоской поверхности проводится в несколько проходов в случае, когда нужно снять большой слой материала.
Особым технологическим процессом можно назвать работу по получению пазов. Это связано с тем, что их глубина может быть довольно большой, а образование подобных технологических выемок проводится исключительно после чистовой обработки поверхности. Фрезерование т-образных пазов проводится при применении специального инструмента.
Подача
Понятие подачи напоминает глубину врезания. Подача при фрезеровании, как и при проведении любой другой операции по механической обработке металлических заготовок, считается наиболее важным параметром. Долговечность применяемого инструмента во многом зависит от подачи. К особенностям этой характеристики можно отнести нижеприведенные моменты:
- Какой толщины материал снимается за один проход.
- Производительность применяемого оборудования.
- Возможность проведения черновой или чистовой обработки.
Довольно распространенным понятием можно назвать подачу на зуб. Этот показатель указывается производителем инструмента, зависит от глубины резания и конструктивных особенностей изделия.
Как ранее было отмечено, многие показатели режимом резания связаны между собой. Примером можно назвать скорость резания и подачу:
- При увеличении значения подачи скорость резания снижается. Это связано с тем, что при снятии большого количества металла за один проход существенно повышается осевая нагрузка. Если выбрать высокую скорость и подачу, то инструмент будет быстро изнашиваться или попросту поломается.
- За счет снижения показателя подачи повышается и допустимая скорость обработки. При быстром вращении фрезы возможно существенно повысить качество поверхности. На момент чистового фрезерования выбирается минимальное значение подачи и максимальная скорость, при применении определенного оборудования можно получить практически зеркальную поверхность.
Довольно распространенным значением подачи можно назвать 0,1-0,25. Его вполне достаточно для обработки самых распространенных материалов в различных отраслях промышленности.
Ширина фрезерования
Еще одним параметром, который учитывается при механической обработки заготовок считается ширина фрезерования. Она может варьировать в достаточно большом диапазоне. Ширина выбирается при фрезеровке на станке Have или другом оборудовании. Среди особенностей отметим следующие моменты:
- Ширина фрезерования зависит от диаметра фрезы. Подобные параметры, которые зависят от геометрических особенностей режущей части, не могут регулироваться, учитываются при непосредственном выборе инструмента.
- Ширина фрезерования также оказывает влияние на выбор других параметров. Это связано с тем, что при увеличении значения также увеличивается количество материала, который снимается за один проход.
В некоторых случаях ширина фрезерования позволяет получить требуемую поверхность за один проход. Примером можно назвать случай получения неглубоких канавок. Если проводится резание плоской поверхности большой ширины, то число проходов может несколько отличаться, рассчитывается в зависимости от ширины фрезерования.
Как выбрать режим на практике?
Как ранее было отмечено, в большинстве случаев технологические карты разработаны специалистом и мастеру остается лишь выбрать подходящий инструмент и задать указанные параметры. Кроме этого, мастер должен учитывать то, в каком состоянии находится оборудование, так как предельные значения могут привести к возникновению поломок. При отсутствии технологической карты приходится проводить выбор режимов фрезерования самостоятельно. Расчет режимов резания при фрезеровании проводится с учетом следующих моментов:
- Типа применяемого оборудования. Примером можно назвать случай резания при фрезеровании на станках ЧПУ, когда могут выбираться более высокие параметры обработки по причине высоких технологических возможностей устройства. На старых станках, которые были введены в эксплуатацию несколько десятков лет назад, выбираются более низкие параметры.
На момент определения подходящих параметров уделяется внимание и техническому состоянию оборудования.
- Следующий критерий выбора заключается в типе применяемого инструмента. При изготовлении фрезы могут применяться различные материалы. К примеру, вариант исполнения из быстрорежущей качественной стали подходит для обработки металла с высокой скоростью резания, фреза с тугоплавкими напайками предпочтительно выбирается в случае, когда нужно проводить фрезерование твердого сплава с высоким показателем подачи при фрезеровании. Имеет значение и угол заточки режущей кромки, а также диаметральные размер. К примеру, с увеличением диаметра режущего инструмента снижается подача и скорость резания.
- Тип обрабатываемого материала можно назвать одним из наиболее важных критериев, по которым проводится выбор режима резания. Все сплавы характеризуются определенной твердостью и степенью обрабатываемости. К примеру, при работе с мягкими цветными сплавами могут выбираться более высокие показатели скорости и подачи, в случае с каленной сталью или титаном все параметры снижаются.
Немаловажным моментом назовем то, что фреза подбирается не только с учетом режимов резания, но и типа материала, из которого изготовлена заготовка.
- Режим резания выбирается в зависимости от поставленной задачи. Примером можно назвать черновое и чистовое резание. Для черного свойственна большая подача и небольшой показатель скорости обработки, для чистовой все наоборот. Для получения канавок и других технологических отверстий и вовсе показатели подбираются индивидуально.
Как показывает практика, глубина резания в большинстве случаев делится на несколько проходов при черновой обработке, при чистовой он только один. Для различных изделий может применяться таблица режимов, которая существенно упрощает поставленную задачу. Встречаются и специальные калькуляторы, проводящие вычисление требуемых значений в автоматическом режиме по введенным данным.
Выбор режима в зависимости от типа фрезы
Для получения одного и того же изделия могут применяться самые различные виды фрез. Выбор основных режимов фрезерования проводится в зависимости от конструктивных и других особенностей изделия. Режимы резания при фрезеровании дисковыми фрезами или другими вариантами исполнения выбираются в зависимости от нижеприведенных моментов:
- Жесткости применяемой системы. Примером можно назвать особенности станка и различной оснастки. Новое оборудование характеризуется повышенной жесткостью, за счет чего появляется возможность применения более высоких параметров обработки. На старых станках жесткость применяемой системы снижается.
- Уделяется внимание и процессу охлаждения. Довольно большое количество оборудования предусматривает подачу СОЖ в зону обработки. За счет подобного вещества существенно снижается температура режущей кромки. СОЖ должна подаваться в зону снятия материала постоянно. При этом также удаляется и образующаяся стружка, что существенно повышает качество резания.
- Стратегия обработки также имеет значение. Примером можно назвать то, что получение одной и той же поверхности может проводится при чередовании различных технологических операций.
- Высота слоя, который может сниматься за один проход инструмента. Ограничение может зависеть от размера инструмента и многих других геометрических особенностей.
- Размер обрабатываемых заготовок. Для больших заготовок требуется инструмент с износостойкими свойствами, который при определенных режимах резания сможет не нагреваться.
Учет всех этих параметров позволяет подобрать наиболее подходящие параметры фрезерования. При этом учитывается распределение припуска при фрезеровании сферическими фрезами, а также особенности обработки концевой фрезой.
Классификация рассматриваемого инструмента проводится по достаточно большому количеству признаков. Основным можно назвать тип применяемого материала при изготовлении режущей кромки. К примеру, фреза ВК8 предназначена для работы с заготовками из твердых сплавов и закаленной стали. Рекомендуется применять подобный вариант исполнения при невысокой скорости резания и достаточной подаче. В тоже время скоростные фрезы могут применяться для обработки с высоким показателем резания.
Как правило, выбор проводится с учетом распространенных таблиц. Основными свойствами можно назвать:
- Скорость резания.
- Тип обрабатываемого материала.
- Тип фрезы.
- Частота оборотов.
- Подача.
- Тип проведенной работы.
- Рекомендуемая подача на зуб в зависимости от диаметра фрезы.
Использование нормативной документации позволяет подобрать наиболее подходящие режимы. Как ранее было отмечено, разрабатывать технологический процесс должен исключительно специалист. Допущенные ошибки могут привести к поломке инструмента, снижению качества поверхности заготовки и допущению погрешностей в инструментах, в некоторых случаях, поломке оборудования. Именно поэтому нужно уделять много внимания выбору наиболее подходящего режима резания.
Выбор режима в зависимости от материала
Все материалы характеризуются определенными эксплуатационными характеристиками, которые также должны учитываться. Примером можно назвать фрезерование бронзы, которое проводится при скорости резания от 90 до 150 м/мин. В зависимости от этого значения выбирается величина подачи. Сталь ПШ15 и изделия из нержавейки обрабатываются при применении других показателей.
При рассмотрении типа обрабатываемого материала уделяется внимание также нижеприведенным моментам:
- Твердости. Наиболее важной характеристикой материалов можно назвать именно твердость. Она может варьировать в большом диапазоне. Слишком большая твердость делает деталь прочной и износостойкой, но при этом усложняется процесс обработки.
- Степени обрабатываемости. Все материалы характеризуются определенной степенью обрабатываемостью, зависящая также от пластичности и других показателей.
- Применение технологии улучшения свойств.
Довольно распространенным примером можно назвать проведение закалки. Подобная технология предусматривает нагрев материала с последующим охлаждением, после чего показатель твердости существенно повышается. Также часто проводится ковка, отпуск и другие процедуры изменения химического состава поверхностного слоя.
В заключение отметим, что сегодня можно встретить просто огромное количество различных технологических карт, которые достаточно скачать и использовать для получения требуемых деталей. При их рассмотрении уделяется внимание типу материала заготовки, виду инструмента, рекомендуемому оборудованию. Самостоятельно разработать режимы резания достаточно сложно, при этом нужно делать предварительную проверку выбранных параметров. В противном случае может пострадать как инструмент, так и применяемое оборудование.
1.6 Свободная таблица режимов резания.
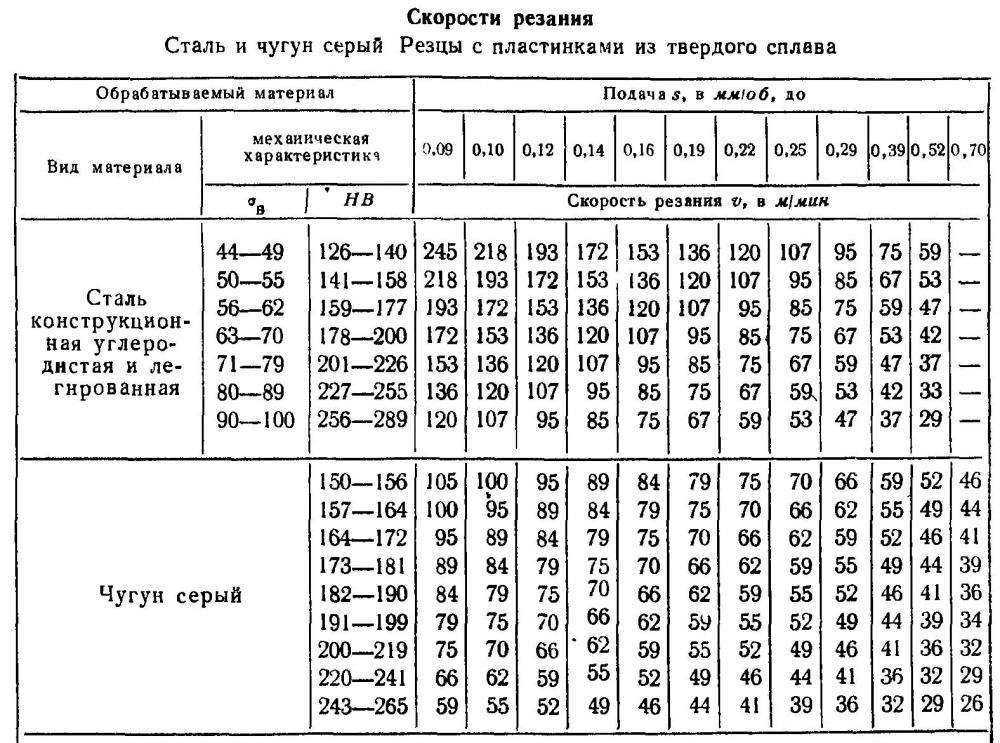
Проектирование привода главного движения металлорежущего станка
курсовая работа
Вид обработки | Инструмент | Элементы режимов резания | |||||||||
D мм | B мм | T мм | Sz мм | T мин | V ммин | n Обмин | Pz Н | Nэфф кВт | |||
Торцовое фрезерование | Фреза торцовая ГОСТ 22085-76 D=80 мм Т5К10 | 100 | 80 | 4 | 0,08 | 180 | 96,7 | 308 | 2948 | 2,13 | |
Торцовое фрезерование | Фреза торцовая ГОСТ 22085-76 D=80 мм Т15К6 | 100 | 80 | 0,5 | 0,03 | 180 | 550 | 1750 | 18,6 | 0,17 | |
Цилиндрическое фрезерование | Фреза цилиндрическая ГОСТ 3752-71 D=80 мм Р6М5 | 80 | 80 | 4 | 0,06 | 180 | 37,7 | 150 | 2820 | 2073 | |
Обработка отрезными фрезами | Отрезная фреза ГОСТ 2679-73 Р:М5 | 20 | 1 | 10 | 0,005 | 60 | 51,2 | 815 | 331,3 | 0,28 | |
Обработка концевой фрезой (паз) | Концевая фреза Р6М5 ГОСТ 17025-71 | 16 | 10 | 20 | 0,04 | 80 | 30,4 | 605 | 2138 | 2,05 | |
Обработка концевой фрезой (плоскость) | Концевая фреза Р6М5 ГОСТ 17025-71 | 16 | 20 | 5 | 0,07 | 80 | 40,9 | 815 | 2050 | 1,97 | |
Обработка трёхсторонней дисковой фрезой | 3-х сторонняя дисковая фреза ГОСТ 1669-78 Р6М5 | 100 | 14 | 10 | 0,07 | 120 | 47,1 | 150 | 1936 | 1,8 |
Предельные частоты режимов резания:
Максимальная мощность резания:
Выбор электродвигателя.
Мощность электродвигателя определяется с учётом наиболее нагруженного режима. Наиболее нагруженным режимом является черновое фрезерование, для которого необходима мощность N = 2,13 kBm.
Мощность электродвигателя определяется по формуле, в которой учтена возможность перегрузки двигателя на 25%:
(2.1)
=2,6 кВт
Согласно приложению 4, стр. 43, [2] Принимаем двигатель двухскоростной 4А132S8/4У3 N = 3,2 /5,3 кВm, 750/ 1500 об/мин.
Делись добром 😉
Логистическая система автоматизированного участка механообработки
2.2.2 Расчет режимов резания для одного технологического перехода и назначение режимов резания по нормативам для остальных технологических переходов
· Расчет режимов резания выполним для операции 015 – точение. Черновое точение Подача и глубина резания при черновом точении выбираются из рекомендуемых значений для стали: S=0,6 мм; t=0,6 мм. Скорость резания при продольном точении: , (2.1) где = 350…
Проект участка механического цеха для изготовления деталей типа корпус с применением станков с ЧПУ. Деталь-представитель: Корпус КЗР 0101108
2.4.2 Определение режимов резания на проектируемые операции. Сводная таблица режимов резания
Аналитический расчет режимов резания. Операция 030. Развернуть отверстие 1 Дано: Станок – 16К20Ф3; Материал заготовки – СЧ20 ГОСТ1412 – 85; Обработка – с охлаждением; D=30,033 мм, d=29,82мм, lрез =103мм…
Проектирование наладки станков с ЧПУ на обработку детали Вал БИПМ.715123.002
1.8 Расчет режимов резания
В дипломном проекте расчет режимов резания на операцию 015, выполняемую на токарном станке с ЧПУ 16К20Т1 и фрезерном станке мод. 6Р13, производим по методике, изложенной в литературе (8) ч.2. Операция 015. Токарная с ЧПУ. Рисунок 1…
Проектирование операций механической обработки основных поверхностей детали авиадвигателя
1.2 Расчет режимов резания
Токарная черновая операция
Поверхность 12 O35 h23 Rz20.
Поверхность 13 O18 h23 Rz20.
1. Устанавливаем глубину резания. Припуск на обработку удаляем за один рабочий проход:
поверхность 12: мм;
поверхность 13: мм. 2…
Проектирование приспособления для фрезерования шпоночного паза
4. Назначение режимов резания, определение сил резания
приспособление фрезерование шпоночный шпиндель Требуется фрезеровать шпоночный паз на валу шириной 10мм и глубиной 5мм, твердость HRC 24, предел прочности = 600 МПа. Выбор фрезы «Фреза шпоночная Р6М5 D102234-0355» диаметр D равен 10мм…
Разработка роботизированного технологического процесса механообработки
11. Определение режимов резания
Рассчитаем режимы резания для поверхности 3 рисунок 9.1(один проход – черновое точение) аналитическим методом по методики, приведенной в источнике [2]. Глубина резания: t=2 мм. Подачу S выбираем, исходя из жесткости и прочности системы СПИД…
Разработка станочного приспособления для обработки детали “Звездочка” на фрезерную операцию
3 Назначение режимов резания, определение сил резания
Требуется нарезать зубья звёздочки с шагом 25,4, числом зубьев 20…
Разработка технологического процесса изготовления детали “Вставка” на станках с программным управлением
2.

Определим подачу F на черновое точение по справочнику. Определим глубину резания t по формуле: t=(Dз-Dд)/(2*i), (6) где Dз- диаметр заготовки; Dд-диаметр заготовки с припуском на чистовое точение; i-число проходов. t=(45-41.5)/2*1=3.5/2=1.75 мм Следовательно, F=0.4-0…
Разработка технологического процесса изготовления детали “Втулка”. Проектирование специальной оснастки
1.10 Расчёт режимов резания, усилий и моментов резания
Расчет режимов резания для выполнения рабочего перехода на вертикально-сверлильном станке. На вертикально-сверлильном станке модели 2Н106П производится сверление отверстияШ4 мм. Глубина обрабатываемой поверхности 4 мм…
Расчет привода главного движения токарного станка
2.1 Выбор режимов резания
На основании таблицы «Режимы резания на токарных станках» /3/ находим скорости резания для обработки заготовок из стали и чугуна.
Для каждого интервала скорости резания находим предельные частоты вращения шпинделя /7/:. ..
Расчет режимов резания металла
1.3 Назначение режимов резания
Глубина резания Учитывая исходные данные – поверхность предварительно обработанная и требуемая шероховатость поверхности Rа = 12,5 мкм, достаточно одного чернового прохода, с глубиной резания t = 5 мм (исходные данные)…
Расчет станка из жаропрочных сплавов
2. Расчет режимов резания
Режимы резания для наибольшей длины обработки L=1000мм и наибольшего диаметра обработки D=500мм, с глубиной резания мм. Обрабатываем только с продольной подачей, используя проходной резец из сплава Т5К10. 1…
Расчеты проектирования станочного приспособления
8. Таблица расчетных данных режимов резания по выбранной операции
Переход 1 фрезеровать три кулачка глубина 25мм. 1. Определяем глубину резания Общая глубина резания t=5мм. Число проходов i=3 2. Определяем подачу. Выбираем фрезу диаметром D=30мм, L=150мм, e=20мм, z=4, Конус Морзе №4. 3. Определяем скорость резания…
Режущие инструменты
1.

Определение габаритных размеров фасонного резца Наименьший допустимый диаметр фасонного резца определяем по формуле (1.1): , (1.1) где d – диаметр оправки для крепления резца; tmax – наибольшая глубина профиля детали; dmax…
Технологический процесс изготовления детали “муфта”
4.3 Расчет режимов резания
Расчет режимов резания на оп.10 – токарная черновая. Режимы резания определяются согласно рекомендациям [11]. При назначении элементов режимов резания учитывают характер обработки, тип и размеры инструмента, материал его режущей части…
Режимы резания для ЧПУ фрезера
Вот советы по выбору инструмента с ЧПУ от механика с ЧПУ, которые помогут вам в выборе инструмента для станков с ЧПУ для ваших компонентов в мастерской с ЧПУ.
Подбор инструмента для обработки с ЧПУ — это искусство, так как станок с ЧПУ может выполнять самые разнообразные операции, такие как токарная обработка резьбы с резьбонарезным профилем или дуговая обработка.
См. «Инструмент 1» на изображении. Если вы провели некоторое время в мастерской с ЧПУ, вы внезапно скажете: о! Это тип инструмента, который в основном используется в станках с ЧПУ.Конечно, это универсальный станок с ЧПУ. Этот инструмент можно использовать для
Теперь посмотрите «Инструмент 2», этот тип инструмента не широко используется. Какие операции обработки может выполнять этот инструмент
Выбор инструмента для ЧПУ для обработки на станках с ЧПУ
- Токарная обработка
- Обработка канавок
- Токарная обработка
- Дуговая обработка
В чем разница, которую может делать «Инструмент 1», но «Инструмент 2» не может справиться с облицовкой, вот и все.Если это единственное отличие, то почему «Инструмент 1» широко используется, тогда «Инструмент 2». На самом деле основной угол режущей кромки составляет . Без сомнения, «Инструмент 2» очень хорошо подходит для прямого токарного станка, мы можем делать еще большие и глубокие разрезы, если диаметр обработки никогда не меняется, но если вы попробуете крутой конус (обработка от меньшего диаметра до большего диаметра) во время обработки тогда этот инструмент не подходит. С другой стороны, «Инструмент 1» делает поворот конуса радостью. То же самое относится к обработке профиля или дуги (если дуга крутая).
Примечание это все мои собственные мысли, у вас может быть другое мнение. Но все это случилось со мной сегодня, я просто попытался обработать большую дугу с помощью «Инструмента 2», и он отказался (завершение работы не было удовлетворительным, и инструмент издавал звук, поскольку он трут, не поворачивается). Операция, которую я хотел сделать, была такой: я хотел обработать дугу с начальным диаметром 40 мм и конечным диаметром 98 мм с длиной дуги 150 мм и радиусом дуги 600 мм, а материал компонента — среднеуглеродистая сталь.И «Инструмент 2» действительно очень хорошо работал, когда я просто применял его к прямому диаметру поворота.
Общие рекомендации по режимам резания:
Для мягкой древесины (сосна, лиственница, липа)
Тип инструмента | Рабочая подача мм/мин | Скорость вращения (об/мин) | Глубина за проход |
Торцевая 6мм | 2500-3500 | 20 000-24 000 | 7,5-8 |
Торцевая 3мм | 1000-1500 | 20 000-24 000 | 4,5 |
Гравер 30° * 0,2 | 800-600 | 20 000-24 000 | 3 |
Для твердой древесины (бук, дуб, фанера)
Торцевая 6мм 3500 | 4500 | 20 000 — 24 000 | 34 |
Торцевая 3мм 2500 | 3000 | 20 000 — 24 000 | 2 |
Гравер 30°х0,2 300 | 600 | 20 000 — 24 000 | 2 |
Для двухслойного пластика
Торцевая 3 мм | 2000 | 12000 | 0.![]() |
Гравер 30°х0,2 | 2000 | 20000 | 0.3 |
Для акрила и полистирола
Торцевая 6 мм | 1000 — 1300 | 10 000 — 12 000 | 3 |
Торцевая 3 мм | 800 — 1000 | 12 000 — 16 000 | 1,5 |
Гравер 30°х0,2 | 300 — 500 | 18 000 — 20 000 | 0,30,6 |
Для ПВХ
Торцевая 6 мм | 1500 — 2000 | 12000 | 8-10 |
Торцевая 3 мм | 1500 — 2000 | 12000-15000 | 4-6 |
Режимы работы ЧПУ — Helman CNC
от Helman Jr.
У каждого станка с ЧПУ есть пара режимов, или я называю это стандартными режимами работы, такими как автоматический режим, режим одиночного блока, MDI (ручной ввод данных) и режим толчкового режима, и там будет больше режимов, но в основном это будут станки с ЧПУ или специальные режимы управления ЧПУ.
Режимы работы ЧПУ Режим Jog Режим MDI Автоматический режим Режим одиночного блока
Позволяет узнать, что представляют собой эти режимы ЧПУ и что они делают.
Станок с ЧПУ
Jog Mode
Станок с ЧПУ
Режим Jog является одним из наиболее часто используемых режимов ЧПУ.Режим толчкового режима в основном используется для перемещения каретки станка с ЧПУ (или скольжения станка с ЧПУ), например, перемещения оси станка с ЧПУ, например Ось X Ось Z. Эти перемещения оси могут осуществляться с помощью специальных клавиш для оси или посредством станка с ЧПУ с ручным колесом .
Режим ЧПУ станка с ЧПУ или режим MDA
Режим станка с ЧПУ Режим MDI (ручной ввод данных) или режим MDA (ручной ввод данных автоматически) можно назвать полуавтоматическим режимом. Режим cnc MDI или MDA в основном используется для индексирования инструментов или для выполнения одного блока кода cnc (на некоторых моделях cnc, таких как sinumerik 840D, вы можете выполнять многоблочную программу cnc в режиме MDA).M-коды с ЧПУ могут выполняться в режиме MDI или MDA. Вы даже можете повернуть шпиндель станка с ЧПУ до определенного числа оборотов в режиме MDI или MDA.
Станок с ЧПУ, режим одиночного блока
Программа ЧПУ состоит из программных блоков с ЧПУ . Программные блоки cnc нумеруются, например, N10, N20, N30 и т. Д. В режиме одиночного блока станка с ЧПУ, когда вы нажимаете кнопку цикла пуска на панели управления станка с ЧПУ , будет выполнен только один кадр программы ЧПУ, и каретка станка салазок или станка с ЧПУ остановится, или вы можете сказать, что подача режущего инструмента с ЧПУ будет приостановлена, но помните, что это не означает, что станок с ЧПУ полностью останавливается, будет удерживаться только движение оси станка с ЧПУ, и все другие функции, такие как coolent , будут продолжать течь, а шпиндель будет продолжать вращаться.Короче говоря, режим одиночного блока станка с ЧПУ не повлияет на вращение шпинделя станка, но он будет удерживать подачу инструмента только после выполнения программного блока ЧПУ. И если вы снова нажмете кнопку запуска цикла, будет выполнен следующий программный блок программы ЧПУ, и машина снова будет удерживаться после завершения этого кадра.
Автоматический станок с ЧПУ или автоматический режим
Вы редко встретите станок с ЧПУ производства из Автоматический режим станка с ЧПУ .Наиболее часто используемый режим на станке с ЧПУ (на некоторых элементах управления, таких как Sinumerik 840D, панель управления станка имеет клавишу настройки, которая при выключении станка будет работать только в автоматическом режиме, и вы не сможете изменять режимы). В автоматическом режиме станка с ЧПУ при нажатии кнопки цикла запуска на панели управления станка будет выполнена вся программа ЧПУ. Для работы станка с ЧПУ в автоматическом режиме на некоторых станках с ЧПУ, например, на , необходимо закрыть защитную дверцу станка с ЧПУ .
Программирование ЧПУ
Скорость резания формула автоматизированного расчета
Скорость резания и формула автоматизированного ее расчета поможет определить допустимые скорости резания для различных пар, таких как коррозионно-стойкая и сталь — быстрорежущий инструмент. Если необходимо увеличить скорость резания при токарной обработке, то инструмент из быстрорежущей стали несмотря на его невысокий скоростной диапазон находит широкое применение при работе с коррозионно-стойкими сталями. Он широко используется когда необходимо изготовить токарный резец, концевую фрезу, сверло и другой специализированный инструмент из-за его повышенных прочностных свойств по сравнению с твердым сплавом. На стадии проектирования технологического процесса металлообработки в ручном режиме или в режиме САПР ТП, технолог пользуется рекомендациями справочно-нормативной литературы для того что бы выполнить расчет скорости резания, выбирая аналитический или табличный способ расчета. Следует обратить внимание на тот факт, что определяя скорость резания при токарной обработке для одинаковых условий резания по разным справочникам (см. таблицу) приводит к двух-, трехкратному расхождению ее расчетной величины.
Чаще всего это связано с тем, что различные справочники, используют аналитический расчет скорости резания и приводят в них различное значение скоростного коэффициента Cv в формуле расчета скорости резания (1), в которой учитываются значения принятой стойкости Т, глубины резания t, подачи S и поправочных коэффициентов, определяемых свойствами инструмента Кu и свойствами обрабатываемого металла Кm.
V = (Cv / (Tm * tx * Sy)) * Ku*Km (1)
Следует отметить то обстоятельство, что поправочный коэффициент Кu в формуле (1) для всей гаммы быстрорежущих инструментов Р18, Р12, Р9, Р6М5 и их модификаций принят одинаковым, равным 0,3. Практикой металлообработки отмечено, что режущие свойства различных марок и различных партий поставки быстрорежущих инструментов различаются между собой и это отличие составляет 25-45 % и более.
В ряде справочников определять скорость резания при точении рекомендуется с помощью таблиц и поправочных коэффициентов. Внешне эта формула более удобна для работы в диалоговом режиме с системой ЧПУ, которая способна содержать в памяти (ПЗУ) массивы данных о величинах поправочных коэффициентов. В табличном способе для того чтобы определить допустимую скорость резания есть формула (2):
Vд = Vт · Кv, (2)
где Vт — табличное (матричное) значение скорости резания, м/мин; Кv — коэффициент.
Проблема применения этой формулы для автоматизированного расчета заключается в том, что скорость резания при точении будет определена с использованием коэффициентов невысокой надежности. Как и в случае со скоростным коэффициентом Сv, значения начальной (табличной) скорости Vт в разных источниках различно, различны и значения поправочных коэффициентов, входящих в нее.
Используя табличный и аналитический способы, сложно выполнить точно расчет скорости резания, так как они не в полной мере учитывают допускаемые ГОСТом колебания свойств быстрорежущего инструмента как между марками, так и внутри его марочного состава и колебания физико-механических свойств стальных заготовок в партиях поставки. Это приводит к ошибкам в попытках правильно назначить скорость резания при токарной обработке и как следствие к значительному отклонению действительного периода стойкости от задаваемого.
Недостатком существующих методик определения допустимой скорости резания (при заданной стойкости Т, глубине t, подаче S и постоянных геометрических параметрах режущего инструмента) является то, что в них априорно принимается постоянство режущих свойств быстрорежущего инструмента в партиях поставки внутри их марочного состава и постоянство физико-механических свойств партии поставки стали определенной марки.
В таблице 1 приведен расчет скорости резания, в качестве примера, стали 12Х2Н4А быстрорежущим инструментом с использованием различных справочно-нормативных источников для выбранных условий: стойкость резца Т = 60 мин, глубина резания t = 1 мм, подача S = 0,2 мм/об с применением СОЖ. Геометрия резца: главный угол в плане φ = 45°; вспомогательный угол в плане φ1 = 45°; передний угол γ= 5°; угол наклона режущей кромки γ= 0°; задний угол α = 10°; радиус закругления вершины резца r= 1 мм.
Содержание элементов в стали 12Х2Н4А С=0,12% Cr=2% Ni=4%. Буква А указывает на высокое качество материала.
Химический состав: С — 0,09ч-0,15%; Мп — 0,3-0,6%; Si — 0,17-5-0,37; Сг- 1,25-5-1,65%; Ni — 3,25-3,65; Р — 0,025%; S — 0,025%; Си — 0,3%.
Обладающая физическими свойствами Т0,2 = 1080 Мпа; Тв — 1270
Мпа; 85 = 13%; \|/= 60%; КСИ — 105 Дж/см2; HRС- 39.
Анализируя скорость резания при токарной обработке для одних и тех же условий точения с использованием различных справочников показывает, что расхождения в величине допустимой скорости резания на стадии проектирования технологического процесса токарной обработки коррозионностойкой стали могут достигать двукратной величины и более.
Как правильно рассчитать режим резания при сверлении
При работе сверла на него воздействует та же совокупность сил, что и на токарный резец. Поэтому для расчета режимов резания при сверлении используется аналогичная методика, но со своей геометрией и соответствующими значениями параметров. Силы Рz направлены в противоход главному движению и находятся в прямой зависимости от скорости резания (см. рис. ниже). Силы Рх, Рn и Рл воздействуют на конструктивные элементы сверла и определяют значение осевой силы (Ро), соответствующей силе привода станка.
Главные технологические параметры сверла — осевая сила и крутящий момент. Их определяют расчетным путем с помощью эмпирических формул:
Здесь Ср и См — это константы, значение которых зависит от вида сверления, а также свойств материалов и обрабатываемой детали; D — диаметр сверла и S — подача. Корректирующий коэффициент Кр в данной формуле связан только с характеристиками материала детали.
Режимы резания для фрезы при обработке металлов на станках с ЧПУ
Возможно, вы уже задавались вопросом расчёта режимов резания, но при этом продолжали ломать фрезы и не понимать, что происходит? Почему так? Почему, например, вы уменьшаете подачу, а фреза всё равно работает в неправильном режиме? Звенит, издает нехарактерный звук и, как результат, быстро тупится и ломается. В этой статье вы найдете ответы на интересующие вас вопросы:
- Почему не стоит полагаться на режимы резания из каталогов
- Какие параметры входят в расчёт режимов резания
- Как назначать обороты и подачу по внешнему виду инструмента
- Как работать с различными материалами
- Какой методики расчёта режимов резания придерживаться
Сразу оговорюсь, что в начале статьи будет некоторая вводная информация, предназначенная для общего понимания. Рекомендую читать все по порядку, чтобы не только пользоваться методикой расчёта режимов резания, но и понимать, что откуда берется, и почему именно так. Данная статья в первую очередь рассказывает о расчёте режимов резания для ЧПУ станков, так как на них нет возможности «пощупать» усилие в процессе работы, как это делают на универсальных станках. На ЧПУ оборудовании нужно изначально назначать правильный режим, и только потом вносить небольшие коррективы в пределах ±20%.
Режимы резания из каталогов.
Мы часто слышим вопрос от наших клиентов: «Какие обороты и подачу поставить на ту или иную фрезу?» Можно ответить кратко: «Посмотрите по каталогу производителя!» Но к сожалению, это не является правильной рекомендацией по нескольким причинам:
- Продавец зачастую завышает режимы резания на свою продукцию на 20-40%, чтобы иметь конкурентное преимущество перед другими поставщиками.
- Продавец в большинстве случаев не имеет практического опыта работы с режущим инструментом и различными материалами.
- И самое главное – когда вы соберетесь фрезеровать, каталога под рукой не окажется, а интернет предательским образом отключится!
На что тогда полагаться? На методику расчёта режимов резания, которую мы для вас подготовили! Она является результатом личного опыта работы на фрезерных ЧПУ станках с различными материалами. Возможно, что полученные режимы будут не самыми выигрышными в плане времени обработки, но они точно сохранят ваш инструмент и позволят работать в безопасном для него режиме, что наиболее важно для начинающих операторов ЧПУ!
Параметры режимов резания.
Как видно из рисунка, в режимы резания для фрезы входит 3 параметра:
- S – обороты (частота вращения шпинделя)
- F – подача (скорость, с которой движется инструмент)
- P – величина съема (слой материала, срезаемый фрезой)
Это именно та последовательность, с которой мы производим расчёт режимов резания для фрезы – далее будем её придерживаться. Данные буквенные обозначения используются в том числе и в самой программе на ЧПУ станок. Например, чтобы включить шпиндель на 1500 об/мин по часовой стрелке, мы записываем в программу «S1500 M3». Или, чтобы сделать проход вправо на 50 мм с подачей 300 мм/мин, мы пишем в программе «G1 X50 F300».
Внешний вид инструмента.
Дадим краткую характеристику фрез по внешнему виду, которую следует учитывать при расчёте режимов резания. Рассмотрим три примера:
Данная фреза имеет острые режущие кромки, большой угол завивки винтовой канавки, она 2-х зубая и не имеет покрытия. Все эти факторы свидетельствуют о том, что перед нами инструмент, идеально подходящий для фрезерования цветных металлов, а также вязких материалов (меди, пластиков), которые подвержены сильному нагреву и оплавлению в процессе резания. Такая фреза хорошо подходит для чистовых обработок с небольшими усилиями резания, но не подходит для сталей и черновых обдирок заготовок с большими съёмами.
Данные фрезы имеют более тупые углы заточки режущих кромок, они 4-х зубые (более жесткие) и имеют слой покрытия, уменьшающего трение и увеличивающего твёрдость поверхностного слоя. Всё это свидетельствует о том, что этот инструмент идеально подходит для обработки сталей, они достаточно прочные для работы с большими подачами, подходят в том числе и для черновых обдирок, при этом позволяют достичь хорошей чистоты поверхности.
На этом рисунке мы видим составную фрезу, состоящую из корпуса и твердосплавных пластинок. Как правило, такие фрезы имеют диаметр от 20 мм и более, так как цельный твердосплавный инструмент такого размера становится экономически не выгодным. Предназначение и поведение данных фрез зависит от установленных на них пластинок. Если пластинки без покрытия (блестящие) и имеют остро заточенные режущие кромки, значит, они предназначены для обработки цветных металлов. Если пластинки имеют покрытие и на ощупь кажутся тупыми, то они предназначены для сталей. По опыту использования, покрытие «золотистого» цвета хорошо подходит под нержавеющие стали, а покрытие черного цвета – под обычные конструкционные стали. Фрезы с твердосплавными пластинками «любят» большие подачи.
Вывод: не обязательно заглядывать в каталог или на сайт производителя режущего инструмента и искать у них калькулятор расчёта режимов резания – учитесь идентифицировать фрезы по их внешнему виду. Разновидностей не так много.
Особенности работы с различными материалами.
Здесь мы не будем вдаваться в подробности, а просто дадим список распространённых материалов и опишем особенности работы с ними. Список составлен по принципу от легкообрабатываемых (некапризных) материалов к более сложным.
- Пластики (модулан, капролон, фторопласт) – наиболее легкообрабатываемые материалы. Можно обрабатывать как на высоких, так и на низких оборотах, как с высокими, так и с низкими подачами. На инструмент действуют небольшие силы резания, можно давать большое заглубление. Обращать внимание нужно только на оплавление материала и в случае нагрева снижать обороты.
- Цветные металлы (дюраль, латунь, бронза) – также очень легко обрабатываемые материалы. Обрабатываются на высоких скоростях, стружка сходит легко, не перегреваются, на инструмент действуют небольшие силы резания. Можно обрабатывать без СОЖ (смазочно-охлаждающая жидкость). Режимы резания можно корректировать в большом диапазоне без боязни повредить инструмент.
- Медь, алюминий (мягкие алюминиевые сплавы типа АМГ) – всё то же самое, что и для цветных металлов, но с одной особенностью. В случае превышения скорости происходит резкий нагрев и оплавление материала, что моментально забивает фрезу – она перестаёт резать и сразу ломается.
Для предотвращения этого явления нужно применять СОЖ.
- Конструкционные стали – для них обязательно применение фрез именно под стали с 3/4-мя зубьями и желательно с покрытием. Обработка ведется легко, если станок имеет достаточную жёсткость. Для сталей не стоит применять большие обороты, а также не стоит сильно снижать подачу, так как в этом случае фреза не режет материал, а «зализывает», что приводит к нагреву и ухудшению качества обрабатываемой поверхности. Величина снимаемого материала одним зубом (подача на зуб фрезы) должна быть достаточной.
- Нержавеющая сталь, титановые сплавы – наиболее капризные материалы в обработке. Требуют применения специального инструмента, подходящего для обработки этих материалов. Не «любят» большие обороты и подачу, требуют интенсивного охлаждения СОЖ. Не стоит усердствовать с глубиной врезания и снимать более чем 1/3 от диаметра фрезы.
Методика расчётов режимов резания при фрезеровании.
1. Определяемся с первым параметром – оборотами фрезы (S).
Обороты рассчитываются исходя из оптимальной скорости резания для того или иного материала. Скорость резания – это не обороты! Это скорость, с которой режущая кромка движется относительно материала в метрах в минуту. Скорость резания – это отправная величина для расчёта, но не конечное знание оборотов, которое нам нужно. Условно разделим материалы на цветные металлы и стали, а фрезы на монолитные и с пластинками. Привожу рекомендуемые (подобранные опытным путем) скорости резания.
Монолитные:
- Цветные металлы 120-160 м/мин
- Стали 60-100 м/мин
С пластинками:
- Цветные металлы 180-220 м/мин
- Стали 120-160 м/мин
Формула расчёта скорости резания выглядит так:
Но нас всё-таки интересуют обороты, поэтому выразим S и получим формулу расчёта оборотов шпинделя:
где:
- S – обороты шпинделя (об/мин)
- V – скорость резания (м/мин)
- D – диаметр фрезы (мм)
Точности тут не требуется, полученные обороты можно округлять в любую сторону. Также стоит оговориться, что если Ваш станок не выдает высокие обороты, то не стоит беспокоиться – ставьте те, которые выдает, и работайте. Просто это будет немного медленнее, чем могло бы быть, так как подача будет напрямую зависеть от оборотов – чем меньше обороты, тем меньше будет подача.
Исходя из этих параметров, можно составить таблицу с рекомендациями оборотов для наиболее распространённых диаметров фрез.
2. Определяемся со вторым параметром – подачей (F).
В первую очередь это актуально для концевых монолитных фрез, так как они наиболее подвержены поломке в случае завышения или занижения скорости подачи. Для фрез с твердосплавными пластинками подачу можно брать исходя из расчёта 0.1-0.2 мм на зуб. При этом подача 0.1 мм на зуб будет идеальна для инструмента небольшого диаметра (20-30 мм), а 0.2 мм стоит применять только для более крупных фрез (от 40 мм в диаметре и более).
Для определения скорости подачи воспользуемся простой формулой:
где:
- F – подача (мм/мин)
- D – диаметр фрезы (мм)
- K – коэффициент 0.
006-0.008
- N – количество зубьев фрезы
- S – обороты (об/мин)
Поясняю:
Умножая диаметр инструмента на коэффициент k, мы получаем допустимую подачу на один зуб фрезы. Например, возьмем инструмент диаметром 8 мм – у нас получится 8*0.007 = 0.056 мм/зуб. Если один зуб фрезы будет снимать меньше, то может произойти «зализывание» материала, нагрев и поломка. Если на один зуб будет приходиться больше, то возможна поломка фрезы из-за значительного увеличения сил резания. Далее, подачу на один зуб фрезы мы умножаем на количество зубьев (например, 3 зуба), получаем: 0.056*3 = 0.168 мм/об. Это тот путь фрезы, который она будет проходить за один оборот. Нам остаётся только умножить это значение на ранее выбранные исходя из обрабатываемого материала обороты, и готово! 0.168*5600 = 940 мм/мин.
Таким образом, для обработки цветных металлов 3-х зубой фрезой диаметром 8 мм нам необходимо поставить на нее 5600 об/мин и подачу около 900 мм/мин. Вот и весь расчёт!
3. Определяемся с третьим параметром – величиной съёма (P).
Или, другими словами, глубиной фрезерования. Тут всё просто, достаточно придерживаться правила: 1/3 от диаметра инструмента. Например, для фрезы диаметром 6 мм мы выберем величину съёма 2 мм, а для инструмента диаметром 12 мм допустимая глубина фрезерования составит уже 4 мм.
Но есть и нюансы:
- Если вы работаете только краем фрезы, то глубину фрезерования можно значительно увеличивать. Например, при использовании новомодного высокоскоростного фрезерования инструмент входит в материал на всю глубину режущей кромки, при этом величина перекрытия составляет всего около 5%.
- Если вы работаете с труднообрабатываемыми материалами, то правило 1/3 от диаметра может быть губительным для инструмента, возможно величину съёма придется значительно уменьшить.
- Если у вас скоростной шпиндель и нет возможности поставить на инструмент малые (расчётные) обороты, то ставьте больше, которые станок в состоянии выдать.
Но при этом значительно уменьшайте глубину резания – это убережет фрезу от поломки, а шпиндель от перегрузки.
- Если у вас недостаточно жёсткий станок, то забудьте про большие съёмы по глубине в принципе. Самым оптимальным будет съём по 0.5-1 мм при рабочем диаметре фрезы не более 6 мм.
Заключение:
Для расчёта режимов резания при фрезеровании действуйте следующим образом:
- Определитесь с обрабатываемым материалом и внимательно осмотрите фрезу.
- Выберите из таблицы подходящие для нее обороты исходя из материала, типа фрезы и её диаметра.
- По формуле расчёта режимов резания посчитайте необходимую подачу. Для труднообрабатываемых материалов выбирайте коэффициент 0.006, а для легкообрабатываемых – 0.008.
- Определитесь с глубиной фрезерования, учитывая наши рекомендации.
Задача для закрепления:
– необходимо фрезеровать паз шириной 10 мм на глубину 6 мм
– концевой 3-х зубой фрезой диаметром 10 мм
– обрабатываемый материал: сталь
Ответ:
S (обороты) = 2500 об/мин
Кол-во проходов = 2
P (съём) = 3 мм
F (подача) = 525 мм/мин
Скорость подачи и скорость резания: разница в обработке с ЧПУ
- 10 июня 2022 г.
CNC (компьютеризированное числовое управление) обработка представляет собой субтрактивный производственный процесс, в котором используются запрограммированные коды для управления движением оси инструмента. Запрограммированные коды включают все необходимые параметры резания, такие как движение режущего инструмента, скорость вращения шпинделя, подача, число оборотов в минуту и т. д.
Необходимо учитывать эти параметры при разработке изделий для операций обработки с ЧПУ. Эти параметры обеспечивают оптимизацию различных частей процесса обработки с ЧПУ. Срок службы инструмента и энергопотребление будут оптимизированы за счет скорости резания. Время обработки и шероховатость поверхности готовых изделий зависят от скорости подачи.
Следовательно, инженеры и операторы должны знать о скорости резания и подаче, а также о разнице между ними и о том, как рассчитать скорость резания и подачу. Продолжайте читать.
Что такое скорость подачи?
За один оборот шпинделя расстояние, пройденное режущим инструментом, называется скоростью подачи. Ее также можно назвать скоростью зацепления режущего инструмента, а для операции фрезерования она обычно измеряется в дюймах в минуту или миллиметрах в минуту.
Для расточных и токарных операций он может измеряться в дюймах/оборот или миллиметрах/оборот. Изменение скорости подачи будет зависеть от материала заготовки (сталь, дерево, алюминий, нержавеющая сталь и т. д.), материала инструмента (режущий инструмент из быстрорежущей стали, керамика, металлокерамика и т. д.) и других факторов резания, таких как поверхность отделка и характеристики станка с ЧПУ.
Внешний вид обработанных изделий будет зависеть от скорости подачи, поэтому оптимизация скорости подачи имеет решающее значение в процессах обработки с ЧПУ.
Выбор оптимальной скорости подачи
Каждый аспект процесса обработки с ЧПУ напрямую связан со скоростью подачи, от безопасности до производительности, стойкости инструмента и качества продукции. При выборе скорости подачи необходимо учитывать следующие факторы.
Производительность
Для повышения производительности можно увеличить скорость подачи за счет снижения качества поверхности. В другом случае, поддерживая постоянную скорость подачи, можно увеличить скорость резания.
Качество поверхности
Лучшее качество поверхности может быть достигнуто при более низкой скорости подачи. Для черновой обработки можно использовать грубую подачу. Например, скорость подачи можно считать равной 0,01-0,05 мм/об для чистовой обработки и 0,1-0,3 мм/об для черновой обработки.
Ограничение скорости подачи
Доступные станки имеют стержень подачи за подачей в пределах минимального и максимального предела. Для этих станков превышение предела недопустимо, но для обычных токарных станков можно применять только несколько вариантов скорости подачи в пределах диапазона.
Геометрия режущего инструмента
На чистоту поверхности изделий может влиять геометрия инструмента, помимо скорости подачи. Более высокое значение геометрии инструмента может быть предпочтительным, если позволяет геометрия.
Возможности станка
Высокая сила резания и высокие вибрации могут возникать из-за более высокой скорости подачи. Скорость подачи следует выбирать в зависимости от поглощения и передачи больших усилий и вибраций станка.
Что такое скорость резания?
Относительная скорость между режущим инструментом и поверхностью заготовки обычно называется поверхностной скоростью или скоростью резания. Его также можно определить как линейное расстояние в метрах в минуту или футах в минуту, которое материал режущего инструмента перемещает по поверхности заготовки в процессе резания.
Основные параметры обработки с ЧПУ, такие как энергопотребление, температура резания, стойкость инструмента и т. д., будут определяться скоростью резания. Значения скорости резания будут варьироваться в зависимости от различных материалов, таких как высокоуглеродистая сталь, низкоуглеродистая сталь, алюминий и пластик. некоторые инструменты или процессы, такие как инструменты для нарезания резьбы и накатки, будут работать на более низких скоростях резания, чем упомянутые.
Выбор оптимальной скорости резания
Чтобы получить наилучшие результаты от процесса обработки с ЧПУ, необходимо обеспечить оптимальную скорость резания. Оптимальную скорость резания для конкретного процесса обработки с ЧПУ можно предсказать, используя следующие факторы.
Твердость заготовки
Сопротивление материала деформации, вызванной истиранием, вдавливанием и царапаньем, обычно называют твердостью. В процессе обработки необходимо соблюдать определенную осторожность при работе с более твердыми заготовками, так как они могут легко ухудшить характеристики инструмента. При обработке более твердого материала необходимо применять более низкие скорости резания. например, для титана требуется более низкая скорость резания по сравнению со сталью.
Прочность режущего инструмента
При механической обработке прочность режущей кромки инструмента играет решающую роль в допустимых скоростях резания. Например, при обработке для более высоких скоростей резания могут использоваться режущие инструменты, изготовленные из высокопрочных материалов, таких как алмаз и углеродистый борнитрид. С другой стороны, для более низких скоростей резания можно использовать режущие инструменты, изготовленные из быстрорежущей стали.
Стойкость инструмента
При более высоких скоростях резания более мягкие материалы режущего инструмента будут быстро изнашиваться, что приведет к сокращению срока службы инструмента. Еще одним важным фактором для определения скорости резания является то, как долго инженер или оператор хочет работать с этим инструментом. В первую очередь сюда будут входить такие параметры, как стоимость инструмента и количество изготавливаемых деталей. Если эти параметры находятся в допустимых пределах, то можно использовать высокую скорость резания.
Почему скорость и подача важны при обработке?
Скорости и подачи важны при механической обработке, поскольку они определяют скорость удаления материала и его количество.
Скорость и подача могут значительно повлиять на срок службы инструмента.
Разница между скоростью подачи и скоростью резания может определяться решающим фактором, называемым температурой резания, поскольку более высокая температура резания может повлиять на такие параметры, как стойкость инструмента и шероховатость поверхности.
На более мягких материалах (алюминий или смола) неэффективные эффекты скоростей и подач не видны, потому что существует достаточно места для ошибок. Тем не менее, на более твердых материалах (титан или инконель) можно увидеть ложное влияние скоростей и подач, поскольку существует ограниченный диапазон ошибок.
Режущий инструмент быстро сломается, если есть небольшая разница между скоростью и скоростью подачи.
Скорости и подачи являются обязательными для достижения лучшей шероховатости поверхности. Если станок работает с высоким значением скорости инструмента и скорости шпинделя, на поверхности материала появятся следы вибрации.
Разница между скоростью подачи и скоростью резания
Хотя и скорость подачи, и скорость резания влияют на общую производительность станка, на самом деле они относятся к двум разным вещам. Чтобы получить наилучшие результаты от вашего станка с ЧПУ, важно понимать разницу между ними.
1. Основное различие между скоростью подачи и скоростью резания заключается в том, что скорость подачи — это скорость, с которой инструмент проходит через заготовку, а скорость резания — это скорость, с которой движется режущая кромка инструмента.
Другими словами, скорость подачи — это мера того, насколько быстро инструмент перемещается по материалу, а скорость резания — это мера того, насколько быстро инструмент фактически режет.
2. Скорость резания дает образующую и обычно измеряется в м/мин или футах/мин, обозначается Vc. Скорость подачи дает направляющую и обычно измеряется в мм/об или мм/мин, обозначаемых с или f.
3. Во время обработки скорость резания влияет на силу резания и потребляемую мощность. Но скорость подачи не влияет.
4. Скорость резания не влияет на отклонение направления стружки от ортогонального. Однако почти в каждом случае скорость подачи будет влиять на фактическое направление потока стружки.
5. Скорость подачи меньше влияет на температуру резания, износ и срок службы инструмента. Но скорость резки сильно пострадает.
6. Образование гребешков или следов подачи на обработанной поверхности не имеет прямого отношения к скорости резания. Тем не менее, гребешковые метки на поверхности готового изделия будут напрямую зависеть от скорости подачи, и это будет напрямую отражать шероховатость поверхности.
Следующая таблица скорости резания и скорости подачи дает более наглядное представление о различиях.
Parameter | Cutting Speed | Feed Rate |
Generatrix and Directrix | Directrix is генерируется скоростью резания | Generatrix is generated by feed rate |
Units of Motion and S hort F orm | Measured in meters в минуту (м/мин) или футов в минуту (фут/мин) и обозначается Vc | Измеряется в метрах на оборот (mpr) или дюймах на оборот и обозначается буквами s или f |
Chip D irection | No effect on deviating from the orthogonal chip direction | Affect the actual chip flow direction |
Резка F Сила и энергопотребление | Влияние на силу резания и энергопотребление | Не влияет на силу резания и энергопотребление |
Грохота поверхности и гребешки | Не связанные с не менее связанными с скализированной или мариейной машиной | 9018 9018 9018 9018 9018 9018 9018.![]() |
Температура резания, стойкость инструмента и износ инструмента | Сильно затронут | Менее затронут |
Как определить подачу и скорость резания?
В приведенной выше таблице показаны все необходимые параметры, которые используются для определения скорости резания и скорости подачи. Основным требованием для определения скорости резания и подачи является скорость шпинделя. Окончательную подачу можно получить двумя способами: во-первых, путем определения подачи на зуб, а во-вторых, используя эту подачу на зуб, можно определить подачу инструмента.
Прочие важные соображения
Ограничение скорости шпинделя
Для определения скорости фрезы в об/мин потребуется количество футов в минуту (SFM) в зависимости от материала и диаметра фрезы. Иногда, при расчете скорости мельчайших инструментов и/или определенных материалов, расчетная скорость приводит к невозможности.
В таком случае оператор должен запускать инструмент на максимально комфортной для станка скорости и поддерживать требуемую для диаметра стружкообразование. Таким образом, на максимальной скорости машины могут быть достигнуты оптимальные параметры.
Нелинейный путь
Обычно скорости подачи предполагаются как линейное движение, т. е. линейное перемещение. Тем не менее, есть некоторые случаи, когда скорость подачи будет учитываться в дуговой или круговой траектории интерполяции (внешний диаметр или внутренний диаметр). По мере увеличения глубины резания увеличивается угол контакта с инструментом, что приводит к нелинейной траектории. Зацепление инструмента выше для внутренних углов по сравнению с внешними углами.
Взаимодействие скорости резания и подачи
В процессе обработки режущий инструмент сжимает поверхность заготовки и удаляет тонкий слой материала в виде стружки. Относительная скорость между заготовкой и фрезой необходима для передачи требуемой силы сжатия. Первичная относительная скорость была получена за счет скорости резания, что помогает предусмотреть удаление материала.
Чтобы предусмотреть удаление материала с общей поверхности заготовки, фрезе или заготовке должно быть обеспечено другое синхронное движение, известное как движение подачи (различное для разных операций фрезерования) вдоль намеченного направления. Эти одновременные действия скорости подачи и скорости резания вместе с движением подачи удовлетворят основные требования механической обработки.
Заключение
Скорости и подачи необходимы для оптимизации различных частей параметров обработки с ЧПУ, таких как стойкость инструмента, энергопотребление, время и шероховатость. Взаимодействие скорости резания и скорости подачи имеет большое значение для производства деталей, обработанных на станках с ЧПУ. Таким образом, чтобы определить скорость и подачу, инженеры и операторы должны полностью их понимать.
В WayKen наши опытные инженеры и механики могут удовлетворить различные потребности в механической обработке, чтобы обеспечить производство необходимых вам деталей и продуктов. Если вас беспокоят скорости резания и подачи деталей, обработанных на станках с ЧПУ, свяжитесь с нами сегодня. Вы всегда получите наиболее обработанную деталь, которую ожидаете.
Скорость резания и подача совпадают?
Нет, скорость резания и скорость подачи не совпадают. Скорость резания — это скорость, с которой режущий инструмент перемещается по разрезаемому материалу. Скорость подачи — это скорость, с которой разрезаемый материал проходит мимо режущего инструмента.
Что означает SFM в механической обработке?
SFM, также называемая поверхностной скоростью, обозначает поверхностные футы в минуту и является общепринятым измерением скорости резания при механической обработке. Он представляет собой количество футов, которое инструмент может пройти по заготовке за одну минуту. Чем выше SFM, тем выше скорость резания.
Почему инженеры и операторы должны учитывать скорость резания и скорость подачи при обработке с ЧПУ?
Инженеры и операторы должны учитывать скорость резания и скорость подачи при обработке с ЧПУ, поскольку это напрямую влияет на качество готового продукта. Если скорость резки слишком мала, материал не будет резаться чисто, и возникнет риск появления заусенцев или других дефектов.
Фрезерные калькуляторы и формулы – Machining Doctor
На этой странице собраны основные фрезерные калькуляторы и формулы . Каждая тема включает в себя онлайн-калькулятор, формулы и пояснения. Для удобства использования вы можете переключаться между единицами измерения (метрические/имперские) и выбирать, отображать ли все или только калькуляторы (скрыть пояснения и формулы)
На этой странице представлены только элементарные калькуляторы. Для более сложных тем для каждого калькулятора есть отдельная страница. Перейдите на страницу Калькуляторов обработки, чтобы просмотреть полный список.
Выберите калькулятор фрезерного калькулятора
- Скорость резания
- Скорость шпинделя
- подача на зуб
- Подав в таблице
- Скорость удаления металла
.

Тумблер мм/дюйм
Другие калькуляторы
ТеорияСкорость резания — это относительная линейная скорость между кончиком режущей кромки и заготовкой. Это результат произведения между скоростью вращения фрезы (скорость шпинделя) и его окружностью.
\( \large C = 2 \times \pi \times r = \pi \times d \)
\( \large V_c = n \times C \)
Важное примечание: Диаметр (d) должен быть эффективным диаметром, а не диаметром фрезы. Во фрезах 90° оба имеют одинаковое значение. Однако для круглых и фасочных фрез эффективный диаметр зависит от глубины резания и геометрии фрезы. 9
\ 900 огромный \frac{n \times \pi \times d}{1000} \)
Формула в имперских единицах- d – [дюйм]
- n – [об/мин] (оборотов в минуту)
- V c – [SFM] (Поверхностные футы в минуту)
\( \large V_c = \huge \frac{n \times \pi \times d}{12} \)
Скорость шпинделя
Фрезерование
Калькулятор скорости шпинделя и формула .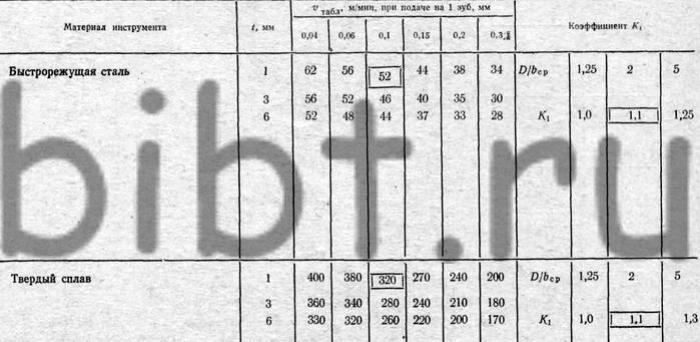
- d – Эфф. диаметр.
- n – Скорость вращения шпинделя.
- С – окружность.
- V c – Скорость резания
Переключатель мм/дюйм
Другие калькуляторы
ТеорияКаталог фрез или наш опыт подсказывают нам, какую скорость резания использовать для данной скорости. С другой стороны, станок с ЧПУ запрограммирован скоростью вращения шпинделя. Поэтому часто нам нужно вычислить число оборотов в минуту по заданной скорости резания либо для программирования, либо для того, чтобы гарантировать, что скорость, с которой мы хотим работать, находится в пределах пределов станка. Он рассчитывается путем деления скорости резания на длину окружности фрезы.
Power Tip – Используйте наш Калькулятор скорости и подачи , чтобы получить рекомендуемую скорость резания на основе десятков параметров!
\( \large C = 2 \times \pi \times r = \pi \times d \)
\( \large n= \huge \frac{V_c}{d} \)
Важное примечание: для получения точных результатов следует использовать эффективный диаметр . Для фрез 90° это просто диаметр фрезы. Однако для круглых фрез и фрез с фаской эффективный диаметр зависит от глубины резания и геометрии фрезы.
- d – [мм]
- n – [об/мин] (Оборотов в минуту)
- V c – [м/мин] \large 0 \\ огромный \frac{1000 \times V_c}{\pi \times d} \) Формула в имперских единицах
- d – [дюйм]
- n – [об/мин] (оборотов в минуту)
- Vc – [SFM] (Поверхностные футы в минуту)
- z – Количество зубьев
- n – Скорость шпинделя [об/мин]
- f z – Подача на зуб [мм или дюйм]
- f n – Подача на оборот [мм или дюйм]
- V f – Подача стола [мм/мин] или [дюйм/мин]
- n – Скорость шпинделя
- z – Количество зубьев
- F z – Подача на зуб
- V f – Подача стола
- z – Количество зубьев
- n – Скорость шпинделя [об/мин]
- f z – Подача на зуб [мм или дюйм] –9045 f
- за оборот [мм или дюйм]
- V f – Подача стола [мм/мин] или [дюйм/мин]
- Сравнение производительности двух наборов режимов резания.
- Оценка требуемой потребляемой мощности.
- a e – Радиальная глубина резания [мм] или [дюйм]
- a p – Осевая глубина резания [мм] или [дюйм]95 V f – Подача стола [мм/мин] или [дюйм/мин]
- Q – Скорость съема металла [мм 3 /мин] или [дюйм 3 /мин]
- Что такое скорость и подача при обработке с ЧПУ?
- Факторы, влияющие на скорости и подачи
- Расчет оптимальных скоростей и подач для процесса обработки
- Часто задаваемые вопросы (FAQ)
- об/мин = число оборотов в минуту: Количество вращений в минуту.
- CS = скорость резания в SFM: Скорость резания в SFM.
- D = Диаметр инструмента в дюймах: Диаметр инструмента в дюймах.
- Глубина и ширина реза.
- Типы фрез.
- Острота режущего ножа.
- Эмбриональные материалы.
- Прочность и однородность зародыша.
- Требуется тонкая обработка.
- Необходимая точность.
- Прочность и твердость станка, устройство удерживает и настраивает инструмент.
- IPM = Скорость подачи в дюймах в минуту: Скорость хода ножа на дюйм в минуту
- F = Подача на зуб: Количество обработки на зуб
- N = Количество зубьев: Количество зубьев
- об/мин = оборотов в минуту: оборотов каждую минуту
- Отсутствие смазки при резке алюминия . Вероятно, это ошибка №1, и с появлением недорогих фрезерных станков с ЧПУ она стала очень распространенной. Ребята, алюминий подходит для режущей кромки ваших концевых фрез. Он буквально хочет химически связать себя или привариться к этому краю. Как только это произойдет, поломка инструмента неизбежна. Лучший способ предотвратить это — использовать какую-либо форму смазочного материала — охлаждающую жидкость или аэрозоль — лучший выбор. Даже опрыскивание резца время от времени баллончиком WD-40 будет работать.
Если вы не можете смазывать, вам нужно найти способ немедленно удалить стружку из разреза и вообще избежать большой глубины резания. Даже в этом случае сварка стружки является бомбой замедленного действия.
- Второй наиболее распространенной ошибкой, с которой я сталкиваюсь у начинающих, является чрезмерное биение . Черт возьми, это даже случилось со мной – я быстро сломал концевые фрезы 5 1/8″, когда пробовал и ошибался, чтобы обнаружить, что у меня плохая цанга ER32. ДОХ! Биение добавляется к стружкообразованию, а слишком большое стружкообразование — это то, что внезапно ломает концевые фрезы. Биение присутствует всегда, вопрос только в степени. Он находится в вашем шпинделе, держателе инструмента и цангах. Вы можете получить ручку на нем, измерив его очень легко. Решение этой проблемы варьируется от простого (замените неисправную цангу) до сложного (получите шпиндель или станок с меньшим биением). Чем меньше фреза, тем меньше допуск на биение. И, к сожалению, чем дешевле станок с ЧПУ и инструменты, тем больше вероятность того, что там будет скрываться биение.
Крошечные фрезы и дешевый ЧПУ — идеальный шторм.
- Использование слишком большого количества канавок в таком материале, как алюминий . Алюминию требуется меньше канавок, потому что он производит более крупную стружку, которая скручивается таким образом, что занимает много места. Требуется больше места между канавками вашей концевой фрезы, а концевые фрезы с меньшим количеством канавок имеют больше места. Придерживайтесь концевых фрез с 2 и 3 канавками, если вы действительно не знаете хитрых способов обмануть это правило.
- Раскалывание и выкрашивание таких материалов, как фанера . Расколы и разрывы уменьшаются за счет правильной скорости и подачи, но это еще не все. См. нашу статью о минимизации сколов и разрывов, чтобы узнать, что является практически библией по обработке фанеры с ЧПУ.
- Насколько вы уверены, что они будут работать в будущем? Кстати, эти таблицы не учитывают болтовню, которая может появляться и исчезать в зависимости от факторов, которые таблицы не фиксируют.
Точный тип державки и вылет инструмента имеют огромное значение. То же самое относится и к конкретному станку (а не только к марке и модели), потому что подшипники каждого шпинделя предварительно нагружены и настроены немного по-разному.
- А как насчет всех переменных, связанных с каждой машиной? Что делать, если в вашем магазине есть несколько видов машин? Столы снова весьма ограничены для решения этой ситуации.
- А как насчет отклонения (подробнее о нем вы узнаете ниже), которое я называю «Бесшумным убийцей инструментов». В большинстве случаев машинисты не знают об отклонении, если они не используют калькулятор подачи и скорости (не таблицы!). Таблицы обычно этого не фиксируют. Предположим, вы используете чужие столы, даже в вашем магазине. Откуда вы знаете, что значения не приводят к отклонению, которое напрасно убьет 25% срока службы вашего инструмента? Если вы не подключите его к калькулятору для перепроверки, вы, вероятно, никогда не узнаете, что происходит.
- 11 Рекомендации по подаче и скорости для облегченных фрезерных станков с ЧПУ: Отлично рассказывается о калькуляторе жесткости и показывает, как выбрать более прочные фрезы для своей работы. Справочник по отклонению инструмента
- : все, что вы хотели знать об отклонении инструмента, и многое другое в этой подробной статье.
- 2 Инструменты для расчета глубины и ширины выреза: Хорошее простое руководство по использованию оптимизатора выреза и мастеров CADCAM.
- При превышении определенного порога ширины резания целесообразно переключиться с попутного фрезерования на обычное фрезерование. Оказывается, хотя большинство пользователей ЧПУ всегда используют попутное фрезерование, они упускают случаи, когда традиционное фрезерование действительно приводит к превосходной геометрии.
Причины отдаленно похожи на те, которые вызывают истончение стружки.
- Сверление глубоких отверстий, где глубина измеряется диаметром инструмента, может быть чем-то вроде черной магии. Есть множество маленьких областей, где один метод работает лучше, чем другой — сверление с просверливанием, параболические канавки, насколько далеко отводиться, как часто отводиться и т. д. — все это играет роль.
- Вы можете существенно изменить правила, если сможете ввести СОЖ высокого давления, и особенно СОЖ через шпиндель.
- Даже точное наведение охлаждающей жидкости с помощью программируемого сопла охлаждающей жидкости может дать вам преимущество.
- То, как кривая мощности вашего шпинделя соответствует соотношению оборотов в минуту и скорости резания вашего инструмента и комбинации материалов, имеет значение. Точка максимального съема материала может быть не идеальной для инструмента. Вместо этого он может быть смещен в сторону, где ваш шпиндель развивает максимальную мощность.
- Существуют своеобразные сочетания мягкого материала и ограничений шпинделя, при которых быстрорежущая сталь может фактически удалить больше материала, чем твердый сплав.
- Припуск по осям X, Y и Z — это количество материала, оставшегося либо на готовой стене (XY), либо на полу (Z) детали, которую необходимо удалить в будущих операциях. Иногда также называется «Запас на вынос».
- Шаг определяет, сколько материала удаляется в радиальном направлении или влево и вправо инструментом каждый раз, когда он проходит в направлении XY.
- Шаг вниз — это количество материала, которое удаляется в осевом или вертикальном направлении при каждом проходе вашего режущего инструмента. Для достижения конечной глубины может потребоваться несколько проходов.
- Верх заготовки обозначает верхнюю поверхность заготовки, используемой для изготовления детали, которую можно использовать в качестве точки отсчета для процессов механической обработки.
- Высота подачи — это высота, на которую позиционируется инструмент перед тем, как начать подачу с рабочей скоростью подачи перед тем, как он войдет в материал, обычно устанавливается на безопасном расстоянии от верха заготовки.
- Высота отвода — это высота, на которую будет отводиться инструмент между перемещениями в рамках одной операции, обычно устанавливаемая на некоторое безопасное расстояние выше высоты подачи.
- Высота зазора — это высота, на которую перемещается инструмент между отдельными операциями, обычно устанавливаемая на 1000 дюймов над верхом заготовки.
- Осевая линия траектории – это траектория, по которой инструмент перемещается по траектории. Необходимо учитывать диаметр инструмента, чтобы гарантировать, что инструмент режет в нужном направлении.
\( \large n = \huge \frac{12 \times V_c}{\pi \times d} \)
Подача на зуб
Калькулятор
подачи на зуб поможет вам рассчитать подачу на основе подачи стола, скорости шпинделя и количества зубьев.Переключатель мм/дюйм
Другие калькуляторы
Теория Подача на зуб представляет собой нагрузку, действующую на одну режущую кромку фрезы (нагрузка стружки). Это хороший показатель для проверки того, подходят ли определенные условия резания (скорость шпинделя и подача стола) для данной геометрии фрезы. Он рассчитывается путем деления подачи стола на скорость вращения шпинделя и количество канавок.
Power Tip – f z равна нагрузке на стружку только при работе фрезой с углом резания 90° при радиальной глубине резания, превышающей радиус фрезы (a e >r). В других случаях можно использовать более высокую подачу в зависимости от коэффициента уменьшения стружки .
Формула (метрическая/дюйм)\( \large f_z= \huge \frac{V_f} {n \times z} \)
Подача стола Калькулятор скорости подачи при фрезеровании.

Переключение мм/дюйм
Другие калькуляторы
ТеорияСкорость подачи фрезерования заготовка, измеренная в [мм/мин] или [дюйм/мин]. Это фактический параметр, который запрограммирован в машине. Однако это не свойство геометрии фрезы, и его необходимо рассчитывать на основе скорости вращения шпинделя и количества зубьев. Основными параметрами, которые мы можем получить из каталога инструментов, являются скорость резания и подача на зуб (загрузка стружки). Исходя из скорости резания, мы можем рассчитать скорость шпинделя с помощью приведенного выше калькулятора. после этого мы можем перейти к следующей формуле
Power Tip . Основным параметром, определяющим подачу стола (V f ), является подача на зуб (f z ). Распространенной ошибкой является использование рекомендуемой по каталогам нагрузки на стружку в качестве подачи на зуб. Однако это предположение верно только при использовании фрезы 90° с радиальной глубиной резания, превышающей радиус фрезы (a e >r). В других случаях вы можете использовать гораздо более высокое значение f z в зависимости от коэффициента утончения чипа 9.0123 .
\( \large f_n = z \times f_z \)
\( \large V_f= n \times f_n \)
\( \normalsize \text {Или напрямую} \)
\( \large V_f= n \times z \times f_z \\)
Скорость съема металла
Калькулятор MRR
определяет объем материала, удаляемого в минуту при определенных условиях резания.
Переключение мм/дюйм
Другие калькуляторы
ТеорияСкорость прокатки металла (MRR) измеряется в кубических дюймах (или кубических мм) в минуту и показывает, сколько материала обрабатывается за одну минуту при наборе условия резки. При фрезеровании это произведение подачи стола, радиальной глубины резания и осевой глубины резания. Узнайте больше в нашем Глубокое удаление металла Страница . MRR используется для двух целей:
\( \large Q = V_f \times a_e \times a_p \)
ПоискНачните печатать и нажмите Enter для поиска
Поиск …Скорости и подачи: руководство для начинающих с таблицей
Каждая операция обработки с ЧПУ требует от вас установки оптимальных скоростей и подач для процесса.
Это два наиболее важных параметра обработки, которые напрямую влияют на качество, эффективность и срок службы инструмента.
Но какие факторы влияют на эти параметры и как определить оптимальные скорости и подачи для процесса?
В этой статье содержится подробное руководство по скорости и подаче операции обработки и объясняется, как рассчитать оптимальные значения.
Что в этой статье?
MellowPine поддерживается читателями. Когда вы покупаете по ссылкам на моем сайте, я могу получить партнерскую комиссию без каких-либо дополнительных затрат для вас.
Что такое скорости и подачи при обработке с ЧПУ?
Скорости и подачи относятся к различным скоростям процесса резания. В то время как скорость резания определяет количество удаляемого материала в футах с поверхности в минуту (SFM), скорость шпинделя — это скорость вращения режущего инструмента/заготовки (об/мин), а скорость подачи — это скорость, с которой режущий инструмент продвигается вдоль заготовки.
Для начала работы с ЧПУ требуется доскональное знание различных параметров, таких как скорость, подача, глубина резания, количество стружки и т. д., которые определяют его функциональность.
Для достижения наилучших результатов каждый процесс обработки с ЧПУ требует определенной комбинации этих параметров.
Как правило, для получения плавных резов рекомендуется высокая скорость с малой подачей, но обработка материала на очень высокой скорости может привести к перегреву и повреждению инструмента.
Аналогично, очень низкая скорость подачи увеличивает время цикла и снижает производительность процесса.
Поэтому важно установить оптимальное значение, обеспечивающее чистый срез с высокой производительностью.
Скоростные параметры станка с ЧПУ состоят из двух типов скоростей: скорости резания и скорости шпинделя.
Скорость резания
Скорость резания — это относительная скорость между заготовкой и режущим инструментом.
Можно определить как скорость, с которой конкретная точка заготовки проходит через режущую кромку.
Скорость резания обычно рассчитывается в метрах в минуту (MPM) или поверхностных футах в минуту (SFM).
Таким образом, скорость резания также можно определить как площадь поверхности, снимаемую режущими зубьями в минуту.
Скорость резания вместе со скоростью подачи и глубиной резания определяет скорость съема материала (MRR) в процессе обработки.
Скорость резания зависит от таких факторов, как материал заготовки, материал режущего инструмента и предполагаемая стойкость инструмента.
Как правило, оптимальную скорость резания инструмента можно определить из справочного руководства, предоставленного производителем.
Эти руководства обычно имеют цветовую кодировку и алфавит для каждой категории материала.
P (синий) для стали, M (желтый) для нержавеющей стали, K (розовый) для чугуна, N (зеленый) для цветных металлов, таких как алюминий, S (коричневый) для жаропрочных сплавов, таких как титановые сплавы, и H (серый) для жаропрочных сплавов.
Скорость вращения шпинделя
Скорость вращения шпинделя определяет количество оборотов, которое режущий инструмент выполняет в минуту (об/мин).
Разницу между скоростью шпинделя и скоростью резания можно понять по тому факту, что два круга разного диаметра, вращающиеся с одинаковыми оборотами, будут преодолевать разные расстояния.
Вращение режущих инструментов разного диаметраКруг большего диаметра имеет сравнительно большую длину окружности, и поэтому каждое вращение большего круга проходит большее расстояние, чем меньшего круга.
В результате, при одинаковой настройке числа оборотов скорость резания (SFM) инструмента большего диаметра больше, чем инструмента меньшего диаметра.
Скорость шпинделя в первую очередь зависит от возможностей вашего станка с ЧПУ, режущего инструмента и типа обрабатываемого материала.
Обычно рекомендуется устанавливать высокие обороты для обработки мягких материалов и низкие обороты для обработки твердых материалов.
Однако обработка материала при слишком высокой или слишком низкой скорости вращения шпинделя может повредить заготовку и резко сократить срок службы инструмента.
Поэтому рекомендуется установить оптимальную скорость для вашего приложения.
Скорость подачи
Скорость подачи — это скорость, с которой режущий инструмент продвигается вдоль заготовки для удаления материала.
Зависит от частоты вращения фрезы, количества канавок режущего инструмента и количества стружки.
Как правило, медленная подача с высокой скоростью вращения обеспечивает чистый рез с высоким качеством поверхности, в то время как высокая скорость подачи может привести к грубому резу со сравнительно плохим качеством поверхности.
Факторы, влияющие на скорость и подачу
Параметры | Связь со скоростью или подачей |
---|---|
Скорость резания | непосредственно пропорциональна скорости шпинделя |
Диаметр инструмента | Обратно пропорционально скорости шпинделя |
Скорость шпинделя | Прямо Проточная до скорости.![]() |
Количество стружки/ Подача на зуб | Прямо пропорциональна скорости подачи |
Параметры обработки и их пропорциональность скорости и подаче
Скорости и подачи процесса обработки напрямую зависят от различных факторов, таких как диаметр режущего инструмента, количество канавок и количество стружки.
Помимо этого, существует множество других факторов, таких как материал заготовки, материал режущего инструмента, жесткость станка с ЧПУ, отклонение инструмента и т. д., которые косвенно влияют на оптимальную скорость и конфигурацию подачи для операции обработки.
Диаметр инструмента
Диаметр инструментаДиаметр инструмента играет важную роль в настройке оптимального числа оборотов.
Инструмент большего диаметра может удалить больше материала, чем инструмент меньшего размера, при той же настройке скорости вращения.
Например, рассмотрим режущий инструмент 1/8″ и режущий инструмент 1/2″, оба вращаются с одинаковой скоростью вращения шпинделя.
Оба инструмента используются для аналогичной операции резания с одинаковым размером и глубиной резания.
Из-за своего большего размера режущий инструмент 1/2″ завершит операцию резания быстрее, чем инструмент 1/8″, независимо от качества резки.
Это связано с тем, что больший режущий инструмент удаляет сравнительно больше материала за каждый оборот.
Поэтому для достижения качественного реза важно учитывать диаметр инструмента при установке оптимальной скорости вращения для процесса.
Количество канавок
Количество канавок на режущем инструментеКоличество канавок (режущих зубьев) инструмента играет важную роль в установке оптимальной скорости подачи.
Режущий инструмент с одним зубом производит одну стружку за один оборот, что означает, что все режущее действие будет выполняться одним зубом.
Принимая во внимание, что в многолезвийной фрезе операция резания выполняется всеми канавками, и, как правило, количество стружки, производимой за один оборот, равно общему количеству канавок.
В результате сила резания равномерно распределяется между различными канавками, что снижает риск повреждения режущего инструмента.
Таким образом, по мере увеличения количества канавок оптимальная скорость подачи также увеличивается.
Нагрузка на стружку
Нагрузка на стружкуНагрузка на стружку, также известная как подача на зуб, может быть определена как толщина стружки, удаляемой в процессе обработки.
Один из самых важных параметров обработки. Расчет оптимальной нагрузки стружки для процесса обработки может помочь установить оптимальную скорость подачи процесса.
По мере увеличения оптимальной нагрузки на стружку значение оптимальной скорости подачи также увеличивается.
Вы можете использовать калькулятор нагрузки на стружку, чтобы найти значение нагрузки на стружку для вашей настройки обработки.
Материал заготовки
Тип материала заготовки также играет важную роль в определении оптимальных скоростей и подач.
Как правило, твердые материалы, такие как металлы, плохо поддаются механической обработке, поэтому для них требуется меньшая скорость подачи, чем для мягких материалов, таких как дерево.
Кроме того, при обработке твердых металлов требуется большее усилие сдвига для выполнения режущего действия, поэтому конфигурация с низким числом оборотов в минуту и высоким крутящим моментом идеально подходит для таких операций.
В то время как мягкие материалы, такие как дерево, относительно легко обрабатываются и требуют высоких оборотов для скольжения режущего инструмента по заготовке.
Режущий инструмент Материал
Фрезы с твердосплавными напайкамиМатериал режущего инструмента определяет его способность выдерживать высокие силы резания.
Твердосплавный режущий инструмент может выдерживать большее усилие, чем инструменты из быстрорежущей стали, и поэтому может использоваться для обработки с более высокой скоростью и конфигурацией подачи.
Жесткость станка
Жесткость станка определяет максимальное усилие резания, которое может быть приложено к заготовке.
Как правило, станок с ЧПУ с жестким шасси может создавать сравнительно большие силы резания.
Принимая во внимание, что станок с менее жесткой конструкцией будет изгибаться под нагрузкой, возникающей из-за высоких сил резания.
Отклонение инструмента
Отклонение инструмента является одним из самых недооцененных параметров, влияющих на качество обработки.
Инструмент с длинным хвостовиком более склонен к отклонению под действием большой силы резания, поэтому его нельзя использовать для конфигураций с высокими скоростями и подачами.
В то время как инструмент с минимальным вылетом имеет очень меньшую возможность отклонения под действием силы резания и может использоваться для приложения сравнительно больших усилий.
Расчет оптимальных скоростей и подач
При расчете скоростей и подач для операции обработки следует учитывать, что оптимальную скорость резания (SFM) можно получить из справочного каталога, предоставленного производителем инструмента.
Точно так же оптимальную стружкообразование режущего инструмента для конкретного материала заготовки можно также получить из каталога инструментов, предоставленного производителем.
Затем вы можете выполнить следующие расчеты, чтобы получить оптимальную скорость вращения шпинделя и скорость подачи для различных операций обработки.
Расчеты для фрезерных операций
Фрезерный станок с ЧПУ, работающий на металлической заготовке.Уравнение для расчета оптимальной скорости шпинделя для фрезерной операции с ЧПУ:
S = (V с x 12)/(π x D)
Где S обозначает скорость шпинделя в об/мин, V с обозначает резку скорость в SFM, а D обозначает диаметр режущего инструмента в дюймах.
Вы также можете рассчитать скорость шпинделя в метрических единицах следующим образом:
S = (V s x 1000)/(π x D)
Где V s обозначает скорость резания в метрах в секунду (м/сек), а D обозначает диаметр инструмента в миллиметрах (мм).
Точно так же вы можете рассчитать оптимальную скорость подачи (в дюймах в минуту), используя следующую формулу:
Скорость подачи = скорость шпинделя x количество зубьев x количество стружки
Необходимо отметить, что произведение умножения количества стружки с количеством канавок дает подачу при резании в дюймах на оборот (IPR).
Следовательно, скорость подачи (IPM) также может быть определена как произведение скорости шпинделя (RPM) и рабочей подачи (IPR).
Расчеты для операций токарного станка
Токарная операция на токарном станкеОперации обработки на токарном станке с ЧПУ отличаются от других операций тем, что вместо вращающегося инструмента токарные станки состоят из вращающейся заготовки.
Таким образом, режущий инструмент токарного станка существенно отличается от фрез или концевых фрез.
Однако расчет скорости и подачи для токарных операций очень похож на фрезерование и сверление, с той лишь разницей, что для расчетов используется диаметр.
Поскольку токарные станки состоят из вращающейся заготовки, мы учитываем диаметр обрабатываемой заготовки (а не диаметр инструмента) для расчета оптимальной скорости вращения шпинделя.
Оптимальную скорость для токарной операции можно рассчитать следующим образом:
S = (V с x 12)/(π x D)
Где S — скорость вращения шпинделя в об/мин, V с — скорость резания в SFM, а D — диаметр резания в дюймах.
Следует отметить, что произведение π на диаметр заготовки или режущего инструмента дает длину окружности.
Таким образом, скорость шпинделя также может быть определена как отношение скорости резания на границе раздела инструмент-заготовка и ее окружности.
Кроме того, токарные инструменты, используемые для токарных операций, в основном являются одноточечными режущими инструментами, поэтому нагрузка на стружку равна рабочей подаче на оборот (в дюймах на оборот).
Скорость подачи (дюйм/мин) = скорость шпинделя (об/мин) x подача на оборот (дюйм/об)
Расчеты для операций сверления
Иллюстрация сверления с ЧПУ Аналогично для операций сверления скорость и подачу можно рассчитать следующим образом.
S = (V s x 1000)/(π x D)
Где V s обозначает скорость резания в метрах в секунду (м/сек), а D обозначает диаметр инструмента в миллиметрах (мм) .
Скорость подачи (IPM) = Скорость шпинделя (RPM) x подача на оборот (IPR)
Часто задаваемые вопросы (FAQ)
Влияет ли глубина резания на скорость и подачу в процессе обработки?
Да, глубина резания является важным фактором, который влияет на количество стружки и, следовательно, влияет на оптимальную скорость и подачу для процесса обработки. Как правило, по мере увеличения глубины резания оптимальная скорость подачи уменьшается.
Всегда ли рассчитанные скорость и подача обеспечивают идеальные результаты?
Нет. Хотя расчетные скорости и подачи учитывают все возможные переменные, участвующие в процессе, существуют определенные переменные, которые варьируются от одной настройки к другой, такие как жесткость станка, вылет инструмента, вибрации станка и т. д. Таким образом, рассчитанные скорости и подачи не всегда обеспечивают идеальные результаты, и необходимо выполнить пробные запуски и настроить параметры в соответствии с вашей настройкой.
Как рассчитать скорость и подачу для операции сверления, выполняемой на токарном станке?
Операция сверления на токарном станке выполняется с помощью сверла, поэтому оптимальные скорости и подачи для процесса следует рассчитывать по формуле для операций сверления. Однако токарный станок состоит из вращающейся заготовки, и число оборотов в минуту, используемое в расчетах, представляет собой скорость вращения шпинделя патрона.
Как рассчитывается скорость резания при фрезеровании с ЧПУ?
При использовании типов обрабатывающих станков, особенно прецизионных с ЧПУ механическая обработка, расчет скорости фрезерного ножа для разрезаемого материала имеет важное значение, поскольку многие факторы связаны друг с другом, например, твердость материала или твердость фрезерного ножа. Для каждого типа материала потребуется определенная скорость, чтобы можно было точно вырезать размеры, требуемые на чертеже механической обработки.
Скорость резания, также известная как скорость у поверхности, измеряется SFM (футов поверхности в минуту) – это скорость резки на поверхности в минуту. Все режущие инструменты работают по принципу поверхностного метража
Скорость резания определяется как скорость на внешней кромке инструмента, когда он режет. Скорость резки зависит главным образом от типа материала, который вы режете, и типа режущего инструмента, который вы используете. Твердость обрабатываемого материала во многом зависит от предлагаемой скорости резания. Чем тверже рабочий материал, тем медленнее скорость резания. Чем мягче рабочий материал, тем выше предлагаемая скорость резания. Если два режущих инструмента разных размеров вращаются с одинаковой скоростью вращения в минуту (об/мин), , то больший инструмент имеет большую скорость резания. Скорость поверхности, шаг резания поверхности и площадь поверхности напрямую связаны между собой.
С учетом твердости обрабатываемого материала скорость резания может быть указана следующим образом:
Алюминий > Свинец > Железо > Сталь
Судя по твердости режущего инструмента, скорость резания может быть указана как следующим образом:
Углерод > Карбид > > Ветряная сталь
Таблица скорости резки
Тип материала | Скорость резания (SFM) |
---|---|
Низкоуглеродистая сталь | 40-140 |
Среднеуглеродистая сталь | 70-120 |
Высокоуглеродистая сталь | 65-100 |
Легкообрабатываемая сталь | 100-150 |
Нержавеющая сталь, C1 302, 304 | 60 |
Нержавеющая сталь, C1 310, 316 | 70 |
Нержавеющая сталь, C1 410 | 100 |
Нержавеющая сталь, C1 416 | 140 |
Нержавеющая сталь, C1 17-4, pH | 50 |
Легированная сталь, SAE 4130, 4140 | 70 |
Легированная сталь, SAE 4030 | 90 |
Инструментальная сталь | 40-70 |
Чугун – обычный | 80-120 |
Чугун – твердый | 5-30 |
Серый чугун | 50-80 |
Алюминиевые сплавы | 300-400 |
Никелевый сплав, монель 400 | 40-60 |
Никелевый сплав, монель K500 | 30-60 |
Никелевый сплав , инконель | 5-10 |
Сплавы на основе кобальта | 5-10 |
Титановый сплав | 20-60 |
Нелегированный титан | 35-55 |
Медь | 100-500 |
Бронзовый – Обычный | 90-150 |
Бронза – твердая | 30-70 |
Цирконий | 70-90 |
Латунь и алюминий | 200-350 |
Не содержащие кремния неметаллы | 100-300 |
Кремнийсодержащие неметаллы | 30-70 |
Когда вычисляет скорость резания SFM для данного материала и инструмента, можно рассчитать шпиндель, поскольку это значение зависит от скорости резания и диаметра ножа. У нас есть следующая формула:
об/мин = (CS X 4) / D, где:
Скорость очистки можно определить как расстояние, рассчитанное в мм/мин при перемещении работающих на фрезерном станке. Скорость хода может работать независимо от скорости вращения шпинделя, чтобы обеспечить маневренность, а также разумное расположение, чтобы при работе фрезы с различными деталями регулировка становилась проще.
На скорость очистки фрезерного станка влияет ряд факторов:
Скорость перемещения ножа представляет собой количество материала, которое должно быть удалено каждым зубом ножа при его вращении и входе в зону обработки.
Когда режущий нож входит в зону обработки, каждый зуб фрезы входит в зону обработки в равных количествах, образуя стружку одинаковой толщины.
Толщина стружки или плата за обработку на зуб вместе с количеством зубьев режущего ножа составляют основу для определения скорости движения ножа.
Идеальная скорость перемещения ножа для фрезерования измеряется в дюймах в минуту (дюйм/мин) и рассчитывается по следующей формуле:
дюймов/мин = F X N X X об/мин, где:
Таким образом, мы уже можем лучше понять как правильно рассчитать скорость резания при фрезеровании ЧПУ . Чтобы уметь точно обрабатывать виды материалов и детали изделия нужно много тренироваться, чтобы суметь сформировать привычный настрой для правильной работы на станках с ЧПУ.
Пресс-формы VCC , мы специализируемся на точном машиностроении и проектировании изготовления пресс-форм по мере необходимости. Если у вас есть какие-либо вопросы или пожелания по обмену, пожалуйста, немедленно свяжитесь с нами по телефону Hotine/Zalo: 0934 683 166 и Электронная почта: [email protected] или оставьте нам сообщение здесь . Мы свяжемся с вами снова как можно скорее.
Адрес: Лот B2-3-3b, Промышленный парк Нам Тханг Лонг, Тху Фуонг, Бак Ту Лием, Бак Ту Лием, Ханой
7 самых больших ошибок подачи и скорости, которые совершают станки с ЧПУ
Эти 7 ошибок я слышал снова и снова разговаривая с ЧПУ. Есть несколько лучших способов и несколько лучших ответов, которые действительно могут улучшить ваши практики Feeds и Speeds, если вы открыты для них. Исправление фидов и скоростей — один из самых простых способов повышения производительности, который вы когда-либо делали. Не говоря уже о том, что приятно не постоянно уворачиваться от сломанных резаков, LOL.
Не дайте себя обмануть, полагая, что подачи и скорости решают все проблемы!
Когда я слышу от людей, которые ломают инструменты, они почти всегда предполагают, что это результат плохой подачи и скорости. На самом деле, если они используют наше программное обеспечение G-Wizard (хорошо, или какой-то другой калькулятор), они часто злятся на это: «Почему ваше проклятое программное обеспечение ломает так много моих резаков?»
Оказывается, проблема для этих людей редко связана с подачей и скоростью. Они предположили, что, поскольку их концевые фрезы щелкают вправо и влево, это должна быть проблема подачи и скорости, но правда в том, что подача и скорость — это только одна часть головоломки, хотя и важная часть.
Когда я работаю с людьми, имеющими подобные проблемы, я сначала проверяю подачу и скорость. Иногда у них неправильные настройки в G-Wizard или они игнорируют что-то, что он пытается им сказать (например, красные предупреждения об отклонении инструмента), но обычно происходит что-то другое.
Вот наиболее распространенные проблемы, с которыми я сталкивался и которые не связаны с подачей и скоростью:
Если у вас постоянно возникают проблемы, откажитесь от своего первого предположения и проверьте эти другие вещи.
Думать медленнее, значит безопаснее Когда мы хотим быть в безопасности, мы инстинктивно замедляем работу машины. Это просто человеческая природа. Нужно сделать этот громкий шум менее громким, и все будет хорошо, верно?
Не так быстро!
Оказывается, медленная работа может быть наименее безопасной вещью, которую вы можете сделать с точки зрения срока службы инструмента. Происходит какая-то хитрая геометрия, которая запутает вас, если вы о ней не знаете.
Более медленная скорость подачи для данного числа оборотов в минуту приводит к меньшему количеству стружки. Это хорошо, в точку. Но вы можете дойти до того, что количество стружки будет настолько низким, что фреза не сможет эффективно снимать стружку. Вместо этого он начинает тереть или полировать материал вместо того, чтобы аккуратно срезать стружку. Геометрически мы можем увидеть, как это происходит, на следующей схеме:
Фреза вверху может срезать стружку, фреза внизу «стирает» ее…
Представьте, что режущая кромка на самом деле закруглена, а не заканчивается острым концом. – они есть, если смотреть на них под увеличением. Если верхняя часть материала находится над центральной линией режущей кромки, все в порядке, кромка может проникнуть под материал и срезать стружку. Но если она находится ниже этой центральной линии, то режущий инструмент тратит больше времени на надавливание вниз, чем на нарезку вверх. Он пашет по поверхности, пытаясь стереть стружку. Это производит огромное количество тепла, которое, в свою очередь, затупляет резак и усугубляет проблему.
Как узнать, какая минимальная скорость должна быть разрешена? Это непросто, но мы провели здесь исследование, и наш калькулятор G-Wizard предупредит вас о натирании. Если у вас нет G-Wizard, начните беспокоиться о трении, если ваша глубина резания меньше нагрузки на фрезу.
Возьмем альтернативу. Мы мчимся в разрезе, и вдруг раздается шум. Предположим, мы уменьшаем скорость вращения шпинделя, не уменьшая скорость подачи. Очень плохая идея — снижение оборотов при той же скорости подачи увеличивает количество стружки и, скорее всего, сломает фрезу. Всегда сначала уменьшайте скорость подачи!
Вот еще один пример. Входим в рез, возможно, это неприятный отрывочный рез на токарном станке, и вдруг громкий стук. Опять же, наш инстинкт — замедлиться. Но болтовня — это резонансная вибрация. Он с одинаковой вероятностью остановится, если вы ускоритесь или замедлитесь, потому что вы меняете частоту в любом случае, поэтому обязательно попробуйте оба варианта. Chatter на самом деле очень управляем, если вы немного понимаете, как он работает. Глава о Chatter из нашего бесплатного учебного пособия по каналам и скоростям даст вам инструменты, необходимые для того, чтобы очень быстро укротить Chatter.
Игнорирование глубины и ширины резания в пользу подачи и скорости Траектории HSM особенно чувствительны к оптимизации глубины и ширины резания… определяется шириной и глубиной реза, которые вы выбираете? Взятые вместе, эти два фактора определяют, насколько хорошо можно очистить фишки. Наша способность (или неспособность к глубокому резу) очистить стружку определяет, насколько мы должны замедлить резку по сравнению с оптимальными значениями, которые мы могли бы выбрать в противном случае. Современные траектории HSM также очень чувствительны к оптимизации глубины и ширины резания.
Значит, мы должны свести к минимуму и то и другое и радикально увеличить скорость подачи, верно? Не так быстро! Есть плюсы и минусы с обеих сторон — давайте посмотрим на плюсы увеличения глубины или ширины реза.
Большая глубина резания затрудняет удаление стружки, но при этом износ распределяется по большей части канавки, что может иметь решающее значение для срока службы инструмента. Это уменьшает количество ненужных движений, когда мы снова и снова спускаемся вниз, чтобы достичь полной глубины кармана. Это все хорошо, верно? Но большая глубина резания может затруднить вытягивание стружки вверх и из отверстия. Таким образом, чем глубже мы погружаемся, тем больше мы замедляемся, чтобы помочь вытащить фишки.
Теперь больше Ширина реза позволяет быстрее удалять материал, но также усложняет удаление стружки. Худший случай — просверлить отверстие — стружка может только подняться и выйти наружу. Чем меньше ширина реза, тем больше окружность фрезы открыта для воздуха, и стружка может быть выброшена таким образом.
Однако, если мы используем слишком маленькую ширину реза, мы сталкиваемся с явлением, называемым «Радиальное утончение стружки». Это заставляет нас перемещать фрезу быстрее, чем ожидалось, для достижения целевой нагрузки стружки, потому что геометрия небольшой ширины резания странным образом приводит к уменьшению стружки (более подробно это объясняется в нашем курсе «Свободные подачи и скорости»).
Существует гораздо больше факторов, чем те, которые я упомянул. Когда вы выбираете глубину реза и ширину реза, вы фиксируете ряд компромиссов и ограничений для подачи и скорости, о которых вы, вероятно, не знаете. Игра практически выиграна или проиграна благодаря правильному выбору, однако большинство пользователей ЧПУ не выбирают глубину и ширину реза каким-либо сугубо научным способом. Они могут использовать очень причудливые инструменты для выбора подачи и скорости, но если глубина резания и ширина резания не оптимизированы аналогичным образом, вы тратите свое время впустую — вы просто не можете получить наилучшие результаты.
Простые эмпирические правила не могут уловить такие нюансы, но наше программное обеспечение G-Wizard имеет 2 различных инструмента, которые упрощают выбор правильных значений глубины и ширины реза , чтобы остальные расчеты подачи и скорости были учтены. 3 части гармонии. Мне больше всего нравится CADCAM Wizards, потому что это так быстро и просто. Он задает очень мало вопросов и возвращает полный рецепт черновых и чистовых подач и скоростей для всех распространенных CAM-операций (отсюда и название CADCAM Wizards).
Вот видео, показывающее, как они работают:
Мастера CADCAM творят чудеса, проверяя сотни комбинаций с помощью механизма физики резки G-Wizard, чтобы определить наилучший набор компромиссов для целостного рецепта резки. Это не то, что вы можете сделать в электронной таблице или с помощью своего желтого блокнота и научного калькулятора, особенно не так быстро и легко, как CADCAM Wizards делает эту работу.
Обработка подач и скоростей в виде таблиц или баз данных Говоря о CAM, желтых блокнотах, электронных таблицах и научных калькуляторах, я сталкиваюсь со многими программами CAM и ЧПУ, которые хотят просматривать подачи и скорости в виде таблиц или базы данных. Я предполагаю, что они настолько привыкли видеть таблицы в каталогах инструментов, что кажется правильным думать о подачах и скоростях, но это абсолютно один из худших способов думать об этом.
Вот в чем дело: физика подачи и скорости намного сложнее, чем может выразить любой простой набор таблиц. Но производители инструментов должны вам что-то сказать, и, по крайней мере, до недавнего времени они чувствовали, что должны что-то рассказать вам в бумажном каталоге инструментов. Поэтому они упростили его, свели к таблицам и надеялись на лучшее.
Проблема в том, что таблицы не могут точно отразить всю историю. Вы можете видеть ясно как день, что они знают, что не рассказывают всю историю, когда они дают ряд ответов. Я сейчас просматриваю каталог, в котором говорится, что диапазон поверхностной скорости (SFM) для алюминия с их концевыми фрезами должен составлять 500–1000 SFM. Нигде не сказано, как я должен решить, какой именно, но это 2-кратный диапазон. Они не могут быть более точными, потому что таблицы не могут учитывать достаточное количество переменных, чтобы быть очень точными. Нечто подобное мы наблюдаем и с чип-нагрузками.
Если подумать, каждая таблица является двухмерной и поэтому обрабатывает две переменные. G-Wizard учитывает более 50 переменных при расчете подачи и скорости. Каждый из них влияет на результат. Сколько переменных вы рассматриваете? Средняя таблица хороша для 2 переменных. Если вы обрабатываете данные через сложную электронную таблицу Excel, вы можете получить еще несколько. Но каков эффект от тех, которых вам все еще не хватает? Это огромная!
Тогда есть CAM-таблица. Большинство программ CAM хочет создать базу данных о подаче и скорости, которые работали в прошлом. Результаты выглядят точно так же, как таблицы, потому что это все, что есть в базе данных — электронные таблицы.
В этом случае у вас есть таблицы, которые обычно учитывают тип инструмента и материал, и они сообщают вам ширину реза, глубину реза, подачу и скорость, которые работали в прошлом. Большой!
Кроме:
Вы можете попробовать формулы скорости резки в электронной таблице, но это не намного лучше. Есть много подводных камней, связанных с обычными формулами скорости резания.
Я мог бы продолжать в том же духе целую вечность. Хорошие машинисты не используют таблицы или базы данных для определения скорости и подачи. Они используют калькуляторы подачи и скорости. И наши клиенты рассказали нам, почему в прямых цифрах.
Судя по отзывам наших клиентов, эффект от использования калькулятора подачи и скорости может быть очень большим. Они начали с этих более простых методов и сообщают о значительном увеличении своих результатов с помощью G-Wizard:
Вот какие результаты получают наши клиенты от G-Wizard…
Игнорирование отклонения инструментаОтклонение инструмента: Тихий убийца инструментов и производительности?
Это может быть удивительно, но отклонение инструмента может быть самым большим бесшумным убийцей инструментов. Большинство станков с ЧПУ даже не знают, с каким отклонением инструмента они имеют дело при конкретном резе — вам нужно использовать калькулятор подачи и скорости, который сообщит вам эту цифру, прежде чем вы это узнаете. Как только вы это узнаете, вы, вероятно, не будете уверены, что это значит или что это слишком много.
Вот график, показывающий влияние биения инструмента в процентах от нагрузки на стружку и стойкости инструмента:
Помните, что биение (упомянутое выше) и прогиб складываются. Теперь типичная твердосплавная концевая фреза 1/8″ может иметь общий допуск на стружку 0,001″ — тысячную долю дюйма.
Согласно диаграмме, если сумма биения и стружки составляет всего 0,0005 дюйма, или 5 десятитысячных дюйма, мы можем сократить стойкость инструмента до 40%. Довольно чувствительно, а? Права на ошибку не много. И только подумайте, без калькулятора подачи и скорости большинство людей даже не проверяет прогиб.
Позвольте мне дать вам несколько советов о том, как справиться с отклонением инструмента.
Во-первых, хороший Калькулятор подачи и скорости, такой как наш G-Wizard, точно скажет вам, какое отклонение вы получаете, и предупредит вас, когда оно слишком велико.
Во-вторых, это даст вам инструменты для решения проблемы отклонения. В G-Wizard есть калькулятор жесткости, который может помочь вам определить влияние на жесткость диаметра инструмента, вылета и материала (карбид или быстрорежущая сталь). Он имеет оптимизатор резки, который сообщит вам, какую глубину резки вы можете иметь для любой заданной ширины резки, и наоборот. Кроме того, в нем есть мастера CADCAM, которые автоматически прогоняют сотни комбинаций, чтобы найти оптимальное сочетание ширины и глубины резки для максимальной эффективности. Вот несколько полезных советов, которые помогут вам узнать больше об этих инструментах:
Ознакомьтесь с этими статьями и помните, что вы не можете получить подобные инструменты нигде, кроме калькулятора G-Wizard от CNCCookbook.
Неиспользование всех замечательных советовВ школе преподают подачу и скорость как набор простых формул — вот как рассчитать число оборотов в минуту на основе скорости резания и диаметра инструмента. Вот как вы рассчитываете загрузку стружки. Если вам повезет, они обходят те несколько основных формул, которые мы можем найти где угодно (например, в Википедии), и переходят на следующий уровень детализации. Этот следующий уровень детализации сводится к корректировкам, которые необходимо внести в формулы, чтобы они отражали реальность, а не идеал, который является теорией. Например, если ширина резания меньше половины диаметра инструмента, необходимо отрегулировать скорость подачи с учетом радиального утончения стружки.
Следующий уровень детализации добавляет пару десятков дополнительных формул, которые необходимо применить, и кучу новых переменных. Для работы на уровне выпускников, возможно, они перейдут на следующий уровень сложности, который будет включать оптимизацию некоторых из этих переменных относительно друг друга, что G-Wizard делает очень хорошо, что является уникальным в мире каналов и скоростей.
Но есть еще один уровень знаний. Как только мы поймем, как взаимодействуют все эти различные переменные и формулы (или как только мы позволим нашему Калькулятору Подачи и Скорости позаботиться об этом), мы поймем, что мир Подачи и Скорости далеко не однороден. Это запутанный ландшафт со множеством интересных тупиков, переулков и кварталов. Мы говорили о явлении трения выше. Это одна интересная область, которую вы достигаете, если позволяете нагрузке на стружку падать слишком низко по сравнению с остротой инструмента. Есть много других. Вот несколько примеров:
Я могу продолжать в том же духе некоторое время. Существуют буквально сотни этих маленьких самородков, ожидающих, когда ЧПУ обнаружит и воспользуется ими. Вы видите их в каталогах инструментов, в которых упоминаются десятки из них. Другие вы должны открыть для себя сами, экспериментируя с комбинациями. Некоторые из них настолько тонкие, что вы никогда не найдете их, если вам не поможет программное обеспечение, которое дьявольски старается максимизировать комбинации.
Когда я впервые начал свое путешествие, результатом которого стал G-Wizard, одной из самых больших моих проблем было выяснить, как мне запомнить все эти полезные маленькие правила. Их было так много, и каждый раз, когда я открывал каталог инструментов, вываливалось все больше. В конце концов я сдался и решил, что хочу, чтобы программное обеспечение запоминало эти вещи для меня. Он должен дать мне лучшие подсказки и подсказки, как только он увидит, в каком районе я нахожусь, благодаря введенным параметрам. Так родилась функция «Советы G-Wizard».
Воспользуйся всеми этими самородками. Пролистайте технические разделы ваших каталогов инструментов — для этого они и существуют. Или получите цифрового помощника, такого как G-Wizard, который запомнит их для вас и напомнит, когда они применимы. Я просмотрел около 250 каталогов инструментов, прочесывая их в поисках советов, которые можно добавить в G-Wizard. Я все еще взволнован, чтобы пройти следующий, который я тоже получаю!
Выбор «достаточно хороших» подач и скоростейДа ладно, этого действительно достаточно для вашего фейерверка?
Многие считают, что то, что они делают для Feeds and Speeds, достаточно хорошо. В конце концов, вы не ломаете слишком много инструментов, вы зарабатываете деньги на механообработке, и рез звучит хорошо, разве этого недостаточно?
Обычно только Новички проявляют желание хорошо решить проблему, потому что у них еще нет решения, которое, по их мнению, работает. Но у новичков будет свой единственный вкус «достаточно хорошего», который проявляется в форме настойчивого требования бесплатных инструментов. Для экспертов, чтобы изменить то, что они делают, они должны либо быть той редкой высококонкурентной породой, которая всегда жаждет большего преимущества, либо они должны получить работу с новыми материалами или инструментами, с которыми они не знакомы.
Но вот в чем дело: на самом деле несложно сделать лучше, а преимущества от улучшения могут быть весьма значительными практически для любого пользователя ЧПУ. Мы путешествовали по некоторым из менее посещаемых дорог Feeds и Speeds в обсуждении выше. Я надеюсь, вы видите, что, возможно, многое не учитываете, если не пользуетесь сложным калькулятором подачи и скорости.
Электронных таблиц и таблиц недостаточно. Они могут серьезно снизить поломку инструмента, но при этом остается много возможностей для дальнейших ценных улучшений. Если срок службы инструмента сокращается вдвое (и это, по словам наших клиентов, является типичным улучшением), вы, вероятно, этого не замечаете. Инструменты работают довольно долго, прежде чем сломаться, НО ОНИ МОГУТ ПРОЙТИ НАМНОГО ДАЛЬШЕ!
Если у вас хорошая отделка поверхности, вы, вероятно, не думаете об этом. Тем не менее, если бы вы могли улучшить его, вы могли бы сэкономить много времени, сократив объем работы, которая выполняется после того, как деталь снята со станка. Кроме того, есть время, которое вы тратите на работу, которая занимает больше времени, чем следует, или время, потраченное на борьбу с справочниками, каталогами инструментов, калькуляторами и электронными таблицами. Время, которое можно было бы использовать с большей пользой.
У меня есть люди, которые говорят мне, что им не нужно ничего лучше, потому что они слышат хорошую подачу и скорость. Вы можете услышать действительно очень плохие подачи и скорости, но не слышно хорошие подачи и скорости . Диапазон комбинаций, которые ваше ухо скажет вам как хорошие, намного шире, чем оптимальные комбинации. Если бы вы могли слышать хорошую подачу и скорость, вы могли бы купить компакт-диски для тренировки слуха, и такие компании, как Boeing, заставили бы всех своих машинистов слушать их. Чтобы получить хорошую работу, вам придется пройти тест на слух. Но ничего из этого не существует.
Любители часто говорят мне, что не могут позволить себе такой инструмент, как G-Wizard. Они купили или построили машину как минимум за 1000 долларов и, возможно, намного больше. Они покупают фрезы для этого станка, и средняя цена фрезы составляет значительную часть годовой подписки на G-Wizard (хорошо для шпинделя мощностью 1 л.с. на всю жизнь!). Если они спасли хотя бы один катер в течение этого года от безвременной кончины, они в основном заплатили за это. И они, безусловно, чаще всего ломают резаки и больше всего нуждаются в помощи. Вы узнали все, что вам нужно было знать, и сломали только 1 фрезу в процессе?
Они считают, что время бесплатно и не стоит экономить. Тем не менее, у них есть много проектов, которые они хотели бы реализовать, и не хватает времени, чтобы сделать их все.
Как для профессионалов, так и для любителей, улучшение каналов и скорости — один из самых дешевых и простых способов повышения производительности.
Дополнительная ошибка: Думаете, что можете настраивать подачу и скорость на слух
Вы слышите хорошую подачу и скорость?
О, если бы это было так просто!
Многие механики старой школы утверждают, что вы можете услышать, когда подача и скорость правильные, но вот реальность:
Слышны только очень плохие подачи и скорости, и то только иногда.Что это значит?
Что ж, если разрез звучит плохо, то почти наверняка так оно и есть. Но если это звучит хорошо, это может быть довольно плохо. Проблема в том, что существует множество факторов, которые на самом деле не издают никаких отличительных звуков. Слишком большое отклонение может радикально сократить срок службы инструмента задолго до того, как это сильно повлияет на звук резания. То же и с выбегом.
Слишком малая нагрузка на стружку вызывает трение, что опять-таки отрицательно сказывается на сроке службы инструмента, а звук практически отсутствует.
Посредственные скорости и подачи оставляют много денег и срока службы инструмента на столе, но они не кажутся заметно отличными от действительно превосходных скоростей и подачи.
Я мог бы продолжать, но, возможно, небольшой мысленный эксперимент послужит лучше. Подумайте о том, что произошло бы, если бы вы могли слышать подачу и скорость. Если бы это было правдой, вы могли бы купить наборы компакт-дисков, предназначенные для «тренировки слуха» машинистов. Они проигрывали примеры хороших и плохих сокращений. Крупные производители будут давать всем начинающим машинистам специальные тесты на скорость и слух. Потому что зачем нанимать кого-то, кто не слышит разницы между хорошей и плохой подачей и скоростью?
Реальность такова, что вы не можете купить компакт-диски для тренировки слуха машинистов, и магазины не проверяют слух машинистов таким образом.
Заключение
Вот и все: 7 типичных ошибок при подаче и скорости плюс 8-я дополнительная ошибка. Избегайте их, и вы на пути к лучшей подаче и скорости. И хорошая новость заключается в том, что теперь, когда вы знаете, что это такое, их легко избежать!
Присоединяйтесь к более чем 100 000 пользователей ЧПУ! Раз в неделю бесплатно получайте наши последние записи в блоге прямо на вашу электронную почту. Кроме того, мы предоставим вам доступ к некоторым замечательным справочным материалам по ЧПУ, включая:
10 траекторий фрезерования для вашего первого проекта 2D-обработки с ЧПУ
Эта деталь, которую вы только что обработали, находится в пределах допуска? В мире производства это либо да, либо нет. Точность обработки требует учета некоторых сложных переменных, включая размер ваших элементов, имеющиеся у вас инструменты и возможности вашего станка. Все эти переменные объединяются с помощью траекторий для успешного производства деталей в пределах допуска. В этой статье основное внимание будет уделено тому, как спланировать свой первый проект 2D-обработки с 10 траекториями фрезерного станка с ЧПУ. Узнайте больше о Fusion 360 Machining Extension здесь.
обычно подразделяются на 2D, 3D, 4-осевые и 5-осевые. Однако термин 2D немного вводит в заблуждение, так как эта траектория использует ось Z для позиционирования инструмента по глубине. Например, на изображении ниже у нас есть призматическая деталь, все элементы которой находятся на разных высотах в плоскости XY. Мы можем быстро расположить наш инструмент на глубину по оси Z, а затем обработать элемент, перемещаясь по осям X и Y.
Многие начинающие операторы станков с ЧПУ с трудом планируют свои траектории, особенно по мере того, как элементы становятся все более сложными. Иногда этот процесс решения проблемы очевиден. Для карманов используется операция 2D-кармана, для фасок используется фрезерование фаски и т. д.
Но потом вы попадаете на сложные вопросы, на которые нет таких черно-белых ответов. Как вы собираетесь обрабатывать отверстие в центре верхней детали? Вы можете использовать траекторию сверления, контура или круглого кармана. И какие из этих элементов нужно обрабатывать сверху, а какие снизу? Ответ на эти вопросы требует некоторых фундаментальных знаний о траекториях.
Каждая траектория инструмента имеет уникальное поведение и вариант использования. Ознакомьтесь с приведенными ниже траекториями, с которыми вы столкнетесь в Fusion 360 и других CAM-решениях.
Траектория | Применение |
Торец | Чистовая обработка торца детали. |
Контур | Обработка петель, открытых карманов, стыковых шрифтов, ласточкиного хвоста, наборов ключей или распилов. |
Фаска | Удаление заусенцев и создание фасок с помощью конической фрезы или центрирующего сверла. |
Филе | Создание скруглений с помощью инструмента скругления углов. |
Карман | Черновая или чистовая обработка карманов различных форм и размеров.![]() |
Фреза для обработки пазов | Обработка прямых или дуговых пазов. |
Сверление | Создание точечных, резьбовых, сверлильных или развернутых отверстий. |
Отверстие | Просверливание отверстий, обычно более 0,75 дюйма в диаметре. |
Резьбовая фреза | Обработка внутренней резьбы диаметром более 0,75 дюйма, фрезерованной наружной резьбы любого размера или нестандартной резьбы. |
Существует также некоторый жаргон траекторий, с которым вы захотите познакомиться. Вы найдете ссылки на приведенные ниже термины почти в каждом программном пакете CAM.
Все эти термины и типы траекторий объединяются при планировании процесса 2D-обработки. Посмотрите приведенный ниже пример того, как мы можем спланировать обработку простой призматической детали.
Шаг | Траектория | Комментарии |
1 | Торец | Черновая и чистовая обработка до самой высокой плоской поверхности детали. |
2 | 2D Contour | Обработка внешней стороны детали. |
3 | 2D Contour | Обработка вне круглой бобышки. |
4 | 2D карман | Черновая обработка и чистовая обработка круглого кармана. |
5 | Слот Мельница | Фрезерование дуговых пазов.![]() |
6 | Фреза для круглых карманов | Обрабатывает центральные сквозные отверстия. В зависимости от размера здесь также может работать дрель. |
7 | Фаска | Использует 2D-контур и фрезу для создания фаски для создания угла 45°. |
8 | Скругление | Использует 2D-контур и инструмент скругления углов для создания скругления. |
9 | Центровочное сверло | Предварительное сверление отверстий для предотвращения дрейфа сверла и создания фаски. |
10 | Сверло | Просверливает отверстия. |
11 | Фреза для круглых карманов | Станки с цековкой. |
CDC регулирует траекторию инструмента с учетом износа инструмента, который может привести к неточностям в детали. Это в основном выровняет ваш инструмент либо немного влево, либо вправо от первоначально запрограммированной траектории. Вы можете найти значение компенсации, вычитая фактические размеры из желаемых размеров элемента детали.
Мы всегда рекомендуем активировать CDC, когда инструмент находится вдали от детали. Это позволит наклонному движению CDC полностью проявиться, прежде чем он соприкоснется с вашим материалом. Правильная реализация CDC для точной обработки 2D-элементов является важной частью успешной практики обработки. Проверьте с помощью системы управления станком и программного обеспечения CAM, чтобы убедиться, что вы понимаете, как вводить значение компенсации.
Только что составленный план использует 10 различных траекторий фрезерования. Знание того, как использовать каждый из них, и понимание их ограничений является ключом к успеху в обработке. В разделах ниже мы подробно рассмотрим каждую траекторию, а также некоторые рекомендации, которые следует учитывать.
1 — Облицовка Вы будете использовать торцовку в начале процесса обработки, чтобы удалить лишний материал вплоть до самой верхней плоской грани детали. Мы рекомендуем использовать торцевую фрезу для большинства деталей. Это обеспечит самые высокие скорости съема материала.
Траекторию нужно начинать на достаточном расстоянии от детали, чтобы торцевая фреза не врезалась в материал заготовки. Расстояние от центра инструмента должно равняться радиусу инструмента плюс некоторый зазор.
Мы рекомендуем планировать черновые проходы на основе срезов материала заготовки, толщина которых может варьироваться до 0,05 дюйма. По сути, планируйте наихудший размер материала с максимальной высотой и дополнительными черновыми проходами. Это гарантирует, что ваш инструмент не соприкоснется со слишком большим количеством материала за один раз, что часто приводит к поломке.
2 – 2D-контурирование 2D-контурирование используется для черновой и чистовой обработки наружных стенок детали. Рассмотрите возможность использования компенсации диаметра фрезы (CDC) для элементов с высокими допусками, чтобы учесть износ инструмента и отклонение материала. Если вы решите использовать CDC, начните траекторию с детали, чтобы CDC можно было полностью задействовать до контакта с материалом.
При обработке стен обязательно увеличьте глубину резания полных стен немного ниже нижней стенки, не прорезая стол станка или губки тисков. Таким образом, когда вы снимаете припуск с задней стороны детали, нет необходимости пытаться выровнять другой контур с ранее обработанными элементами, что может быть сложно и неточно. Кроме того, рассмотрите возможность выполнения чистового прохода на всю глубину на высоких стенах. Это гарантирует, что стены будут прямыми, а не конусообразными.
Всегда рекомендуется оставлять постоянный припуск при черновой обработке стенок детали. Это гарантирует, что чистовой проход удаляет постоянное количество материала, поможет обеспечить равномерное давление резания на инструмент и повысит точность обработки детали.
3 – Выемка Выемка карманов может использоваться для удаления лишнего материала из кармана любой формы, например, из спирального кармана ниже.
При выполнении чернового прохода кармана мы рекомендуем оставлять постоянную толщину на стенках и дне кармана. Затем они могут быть равномерно удалены в процессе отделки.
Специальные концевые фрезы для черновой обработки с зубцами для дробления стружки являются одними из лучших типов инструментов для удаления материала. Тем не менее, они дают плохую чистовую обработку по сравнению со стандартными концевыми фрезами. Окончательный чистовой проход стандартной или чистовой концевой фрезой улучшит чистоту поверхности.
Если позволяет место, используйте винтовое движение при погружении в карман. Если это невозможно, вы можете использовать концевую фрезу с центральной режущей кромкой или просверлить направляющее отверстие и использовать его как точку входа для погружения. Обязательно уточните у производителя вашего инструмента оптимальные подачи и скорости для плунжерного фрезерования.
Наконец, при планировании траектории инструмента начинайте с центра кармана и выходите в направлении против часовой стрелки. Инструмент будет использовать попутное фрезерование при обработке кармана, что обеспечивает лучшие условия резания на жестких станках с ЧПУ.
Пазы можно обрабатывать различными методами, включая контурную обработку, вырезание карманов или специализированные операции фрезерования пазов. Мы рекомендуем всегда использовать инструмент меньше, чем ширина паза, чтобы максимизировать удаление материала и обеспечить адекватную эвакуацию стружки. При планировании траектории движения инструмента наилучшие результаты даст движение с наклоном.
5 – Отверстие ТраекторииОтверстие используют спиральное движение для вырезания круглых элементов, таких как отверстия диаметром более 0,75 дюйма или круглые бобышки. Медленное снижение траектории инструмента удерживает инструмент постоянно включенным, не перегружая его, и обеспечивает ровную поверхность.
6 — Фрезерование фаски Фрезерование фасок отлично подходит для чистовой обработки 2D-элементов. Одним из наиболее распространенных производственных травм в мастерских являются порезы рук при снятии деталей со станка. Снятие острых кромок с помощью фаски помогает избежать порезов рук, а операторам обеспечить безопасность и продуктивность.
Вот рекомендуемая формула для установки глубины резания:
(tool_radius – tool_tip_radius) – ширина фаски – зазор
Эта формула удерживает режущую кромку инструмента, что обеспечивает лучшие условия резания, что увеличивает срок службы инструмента и улучшает качество поверхности. Значение зазора не позволит срезу выйти за пределы внешнего диаметра инструмента. Убедитесь, что радиус вашего инструмента достаточно велик, чтобы оставить некоторое пространство по обе стороны от реза, чтобы вы не отрезали непосредственно по внешнему диаметру или по диаметру кончика.
7 — Радиусное фрезерование Радиусное фрезерование использует 2D-контурную траекторию для создания внешнего скругления. Для использования 2D-траектории требуется радиусная фреза, но вы можете добиться аналогичных результатов с помощью шаровой мельницы и 3D-контурной траектории.
Вы можете использовать центральное сверление для создания конической формы на лицевой стороне детали. Центровочные сверла обычно короче и толще стандартных спиральных сверл, поэтому они создают точные конусы, которые помогут удерживать более поздние сверла в центре во время их работы и предотвращают их «ходьбу» или перемещение по поверхности детали. При планировании конического выреза мы рекомендуем засверлить достаточно глубоко, чтобы он соответствовал диаметру окончательного просверленного отверстия. Если вы хотите получить фаску на последнем отверстии, засверлите немного больше диаметра сверла.
9 — Сверление Сверление позволяет быстро создавать отверстия, удаляя материал вертикально. Просверленные отверстия можно оставить простыми сквозными, утопленными, расточенными или с резьбой. Цикл Peck Drill можно использовать для более глубоких отверстий, при которых инструмент слегка втягивается, чтобы сломать стружку, способствуя эвакуации стружки и минимизируя поломку инструмента.
При настройке программы ЧПУ убедитесь, что вы знаете желаемое конечное состояние для каждого отверстия. Если это сквозное отверстие, просверлите его достаточно глубоко, чтобы острие сверла очищалось, когда оно входит в заготовку. Вы также захотите включить припуск на прорыв, чтобы предотвратить отбортовку или заусенцы.
10 – Нарезание резьбы Нарезание резьбы в ранее просверленных отверстиях путем согласования подачи и скорости с шагом резьбы. Ваша установка CAM рассчитает скорость подачи на основе скорости резания и числа витков на дюйм (TPI) метчика. Убедитесь, что вы просверлили отверстие подходящего размера для вашего крана. Если отверстие слишком маленькое, существует риск поломки метчика внутри отверстия. Если он слишком большой, нити не будут формироваться должным образом.
Обязательно используйте соответствующую смазку при нарезании резьбы, независимо от того, оснащена ли ваша машина автоматической подачей охлаждающей жидкости или вручную смажьте кончик метчика маслом перед началом операции. Мы также рекомендуем нарезать отверстия размером менее 6 вручную, так как меньшие метчики легче ломаются. Обе эти рекомендации помогут избежать ненужной поломки инструмента.
При настройке программы ЧПУ не забудьте добавить глубину метчика, учитывающую как кончик, так и начальную конусность метчика, и убедитесь, что отверстие достаточно глубокое для размещения метчика. Для старых станков с ЧПУ также может потребоваться большая высота подачи, чтобы шпиндель мог достичь полной скорости, прежде чем погрузиться в материал.
Знание того, как эффективно планировать проект 2D-обработки с ЧПУ, начинается с понимания типов ваших траекторий. Типичная работа с ЧПУ начинается с облицовки материала самой высокой плоской поверхностью детали. Оттуда вы можете очерчивать стороны и начинать работать над дополнительными функциями и мелкими деталями.