Резка металла газопламенная – Газовая резка металла: технология, оборудование для разделки
alexxlab | 03.09.2019 | 0 | Разное
Плазменная и газопламенная резка: сравнение технологий
Плазменная резка
- Процесс разработан в середине 50-х годов 20 века.
- Использовался для резки и строжки металла
- Резка токопроводных материалов.
- Воздух или азот – рабочий газ для резки.
- Плавление за счет теплового воздействия плазменной дуги – при газопламенной резки происходит процесс окисления, характерный для углеродистых и низколегированных сталей.
- Использование электрической энергии, плазмообразующий газ (воздух, азот), плазматрон для сжатия дуги.
- Плазменная дуга расплавляет токопроводящий металл и поток воздуха выдувает расплав.
- Без предварительного подогрева.
- Процессы: Нагрев + Удаление расплавленного металла.
Плазма – четвертое состояние вещества
Плазма – газ, нагретый до состояния ионизации и проводимости электрического тока.
- Температура плазмы – 10 000 °С – 14 000 °С
- Сжатый и закрученный поток плазмы расплавляет металл в очень локальной области.
- Расплавленный металл удаляется высокоскоростным потоком плазмы, проходящей через малое отверстие в сопле.
Основные этапы плазменной резки
- Подача сжатого воздуха
- Возбуждение пилотной дуги – между электродом и соплом.
- Перегрев газа.
- Газ выходит из сопла
- Прохождение тока
- Перенос дуги на деталь
Преимущества плазменной резки
- Резка электропроводных металлов
- Простота применения
- Резка сразу без подогрева
- Возможность резки пакета пластин
- Более низкие тепловложения / Очень низкий уровень коробления
- Высокие скорости сварки
- Резка металла с покрытием
- Качественный рез, исключающий дополнительные операции отделки
- Безопасность
Недостатки плазменной резки
- Оборудование более дорогое, включая плазматроны
- Определенный уровень шума и дыма
- Небольшой скос реза (40 – 60 на толщине 25 мм)
Газопламенная резка
- Резка углеродистой и низколегированной стали.
- Химическая реакция: кислород + железо.
- Поток кислорода выжигает металл.
- Поток газа выдувает окалину.
- Процесс: Окисление + Удаление окалины
Основные преимущества плазменной резки. Сравнение с газопламенной резкой
- Резка нержавеющих сталей и алюминиевый сплавов (газопламенная резка – углеродистые стали)
- Производительность
- Низкий уровень тепловложений и как результат – низкий уровень коробления изделия
- Высококачественный рез
- Мобильность – источник плазменной резки + источник сжатого воздуха (компрессор или центральная магистраль)
Рекомендации к источникам питания плазменных резаков в комбинации с резаками серии «AВIPLAS CUT» → |
---|
Поделиться ссылкой:
www.deltasvar.ru
Газокислородная резка металла: технология, виды, условия, процесс
В любой отрасли, изготовляющей, ремонтирующей или перерабатывающей металлические изделия, требуется резать металл. Для чернового раскроя и разборки неразъемных соединений металлических конструкций существует сравнительно несложная и недорогая технология — газокислородная резка металла. Газокислородный способ резания отличается высокой мобильностью. Для работы требуется несложное оборудование, необходимо тщательно соблюдать меры безопасности — способ пожароопасен.
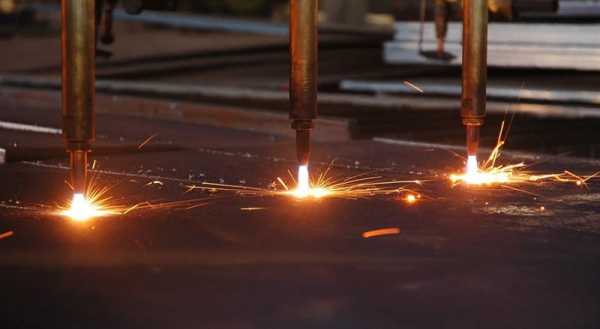
Технология резки газом
Газокислородная резка используется при раскрое стальных сплавов толщиной от 5 до 60 мм. Нагрев и плавление металла происходит за счет тепла, выделяемого при реакции окисления. В ходе реакции полоса металла сгорает с высокой скоростью в узком пучке пламени, направляемом на обрабатываемую поверхность. Продукты сгорания удаляются из зоны резания потоком газа.
При подготовке и проведении процесса газокислородной резки необходимо соблюдать следующие требования:
- Тщательно очистить поверхность по линии разреза и прилегающую к ней зону на 10-15 см. Необходимо удалить следы старой краска, масложировые пятна, смазочные материалы. Наличие таких загрязнений может стать причиной возгорания или даже взрыва. Следует также по возможности зачистить ржавчину. Она выступает в роли теплоизолятора и замедляет резание.
- Со стороны тыльной поверхности разрезаемой детали следует предусмотреть свободное пространство в 5-10 см. Через него должна выходить газометаллическая струя. Если она будет отражаться обратно на деталь, возникнет нежелательная турбулентность газового потока. Это отрицательно скажется на скорости резания и может привести к термической деформации заготовки.
- Нельзя отклонять резак от вертикали более чем на 5°. Это приведет к искажению формы факела, снижению точности реза и качества поверхности.
- Требуется высокая квалификация и значительный практический опыт газосварщика. Только тогда можно гарантировать высокую точность реза и достаточную производительность.

Технология газокислородной резки
Виды резки металла газом
Газокислородная резка имеет несколько разновидностей. Ученые и инженеры разработали эти методы, исходя из особенностей применения в конкретных условиях. Наиболее употребительны следующие методы резки:
- Пропаном. Этот довольно популярный способ применим для титановых, низколегированных сплавов и сталей с низким содержанием углерода. Для углеродистых и высокоуглеродистых сталей он не подходит. Для большей производительности и энергоэффективности пропан могут заменять на метан или ацетилен.
- Воздушно — дуговая. В дополнение к сгоранию материала в струе кислорода меду заготовками и встроенным в резак электродом возбуждается электродуга. Она плавит металл в районе линии реза, а газовый поток уносит его остатки. Метод не позволяет разрезать толстые изделия, зато дает возможность делать разрезы большой ширины. Это очень полезно при выполнении фасонного раскроя и позволяет существенно снизить трудоемкость операции.
- Кислородно-флюсовая. При данном методе в рабочую область подается флюсовый порошок. Этот компонент участвует в физико-химических процессах и обеспечивает повышенную пластичность и податливость материала во время резания. Способ применим для резания сплавов, на поверхности которых образуются прочные и термостойкие оксидные пленки. Применение флюса позволяет избавиться от них, сместив температурный баланс в зону более высоких температур. Особенно эффективен данный метод для чугунных, медных, бронзовых и латунных изделий, заготовок с высокой степенью зашлакованности и для железобетона.
- Копьевая. Применяется при разборке металлических конструкций, технологических отходов, разделке массивных крупногабаритных заготовок. Струя кислорода пропускается через тонкую стальную трубку — газовое копье. Копье является расходным материалом, оно сгорает в ходе процесса, повышая температуру и эффективность основной реакции и позволяет дополнительно концентрировать режущий факел. В результате скорость разделки существенно возрастает.
Технологически процесс газокислородной резки предполагает ведение резака газорезчиком вручную.
Подача газов управляется одним общим или двумя раздельными запорными вентилями. Применение раздельных вентилей позволяет точно настраивать состав смеси и оперативно перестраивать оборудование для другого вида работ.
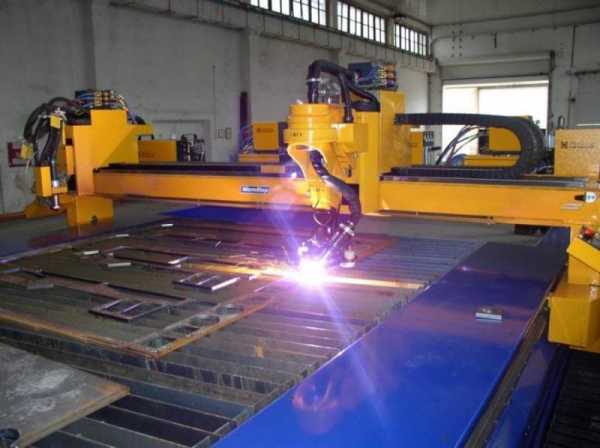
Промышленная газокислородная сварка
Рукоятка резака снабжена тремя патрубками с разъемами. По ним подводится кислород, пропан (или ацетилен) и охлаждающая жидкость. Давление кислорода устанавливается на баллонном редукторе и может достигать 12 атмосфер.
После выполнения поджига в факел резака подается кислород. Сгорание пропана нагревает поверхность заготовки до такой температуры, что начинается химическая реакция его окисления. Она идет настолько интенсивно, что деталь прожигается насквозь струей режущего кислорода и газовый поток выносит сгорающие частицы металла в разрез.
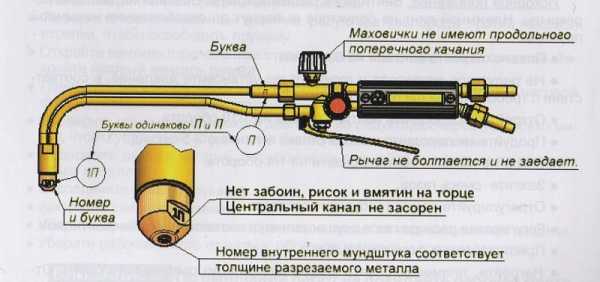
Устройство резака
Условия для газокислородной резки
Для успешного применения газокислородной технологии резки металла следует соблюдать ряд обязательных условий:
- температура плавления (Tплав) материала должна превышать температуру горения (Tвоспл) в кислородной среде. Разница должна составлять не менее 50 °С, чтобы исключить вытекание расплава и неоправданное расширение зоны разреза. Так, для конструкционных сплавов Tплав=1540 °C, а Tвоспл= 1150 °С. С увеличением содержания углерода температура плавления понижается. Это затрудняет резание чугунов и высокоуглеродистых сплавов обычным резаком.
- Tплав разрезаемого материала должна превышать Tплав оксидных пленок на его поверхности. Тугоплавкая оксидная пленка будет препятствовать доступу кислорода к поверхности металла и реакция горения не сможет начаться. Так, оксиды хрома и конструкционная сталь 3 имеют температуры плавления соответственно 2270 и 1540 °С. Выходом из такой ситуации может быть применение флюсового порошка, вступающего в реакцию с оксидной пленкой и преобразующего ее в вещества с более низкой температурой плавления.
- Оксиды, возникающие в процессе резания, должны иметь высокую жидкотекучесть. Если текучесть низкая, то они облепляют кромки линии разреза, препятствуя горению основного материала. Специально подобранный флюсовый порошок также помогает решить эту проблему, повышая текучесть оксидов. Но это приводит к удорожанию процесса.
- Разрезаемый материал должен иметь низкую теплопроводность. В противном случае тепло будет отводиться из рабочей зоны и температуры возгорания металла в месте проведения работы будет не достичь. Реакция не сможет начаться либо будет протекать нестабильно, увеличивая расход газа, снижая точность и качество поверхности реза.
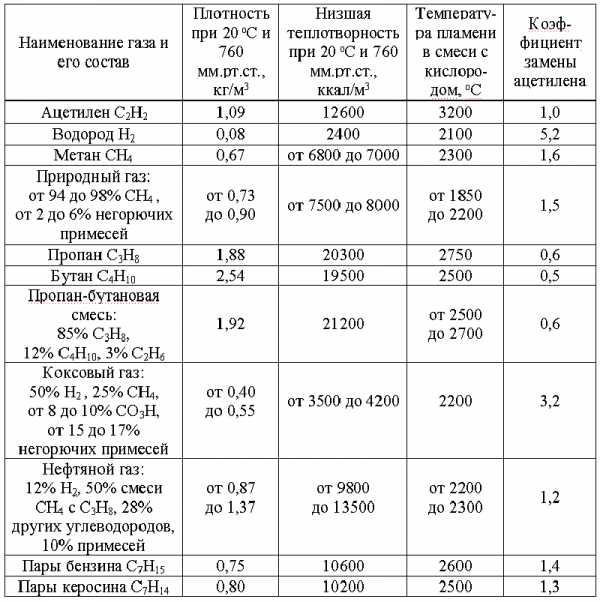
Условия для газокислородной резки
Расход газа при резке металла
Расход газа во время проведения операции зависит от сочетания нескольких факторов.
Определяющим из них является выбранный вид газокислородной резки. Так, воздушно-флюсовый метод при прочих равных параметрах расходует газа меньше, чем кислородно — дуговой.
Кроме того, на расход рабочего газа влияют следующие параметры:
- Навыки газорезчика. Опытный мастер будет расходовать газа на единицу длины реза существенно меньше, чем его начинающий коллега.
- Разрезаемый материал. Термостойкие сплавы требую большего расхода.
- Толщина материала. Чем толще раскраиваемая заготовка или разрезаемое при демонтаже изделие, тем выше будет расход.
- Ширина разреза.
Последним, но не маловажным фактором, влияющим на потребление газа, является общая исправность оборудования и его правильная настройка.
Неисправный вентиль или соединение, неотрегулированная горелка могут не только повысить расход на десятки процентов, но и стать причиной серьезной аварии.
Применение качественных промышленных газов с предписанной технологией степенью очистки от посторонних примесей также повышает производительность и снижает расход.
Преимущества и недостатки технологии
Газокислородная резка обладает целым рядом достоинств, делающим эту технологию экономически эффективной, а в ряде случаев — и просто незаменимой:
- Большая толщина разрезаемого материала.
- Выполнение разрезов любой сложности, в том числе многоступенчатых.
- Кроме сквозного реза, возможен рез на определенную глубину, что позволяет проводить фасонную обработку поверхности.
- Низкая себестоимость операции при достаточном качестве поверхности реза.
- Высокая производительность.
- Высокая мобильность делает метод незаменимым при демонтаже сложных промышленных конструкций и корпусов судов, а также при работе в труднодоступных местах.
Как и любой реально существующей технологии, есть у нее и минусы:
- Требует высокой квалификации и продолжительного набора опыта оператором резака. Начинающим доступны только самые простые операции типа прямого реза тонкого листа.
- Пожароопасность и взрывоопасность. Метод требует проведения ряда подготовительных операций для обеспечения безопасных условий работы и тщательного соблюдения требований безопасности в ходе ее выполнения.
- Невысокая точность раскроя, особенно при ручном резании. Как правило, необходима дополнительная механическая обработка заготовок для приведения размеров и формы в соответствие с чертежом.
- Температурное воздействие на материал может привести к деформациям — короблению, кручению и пр. Это не так важно при демонтаже, но привносит дополнительный риск при раскрое листов.
Стационарные автоматизированные установки плазменной резки металла позволяют побороть большинство недостатков, но лишают процесс мобильности.
Качество резки
Качество газокислородной резки является весьма важным фактором и слабым местом технологии. Чтобы его обеспечить, необходимо контролировать следующие параметры:
- Подача кислорода. Необходимо точно выдерживать этот параметр. Недостаточная подача вызывает неполно окисление разрезаемого материала и накапливанию оксидом в рабочей зоне Переизбыток же охлаждает рабочую зону и выносит из нее тепло, приводя к нестабильности реакции горения.
- Чистота промышленного газа. Применение загрязненного кислорода приводит к скоплению шлаковых масс на нижней стороне разреза, снижению скорости резания и повышенному расходу газа.
- Мощность факела подогрева. Исходя из состава газовой смеси, различают три типа пламени. Окислительное применяется для работы с листом в 3-9 мм. Обычное — для заготовок от 10 до 100 мм. Для более толстого материала используют т.н. науглероживающее пламя подогрева.
- Длина факела. Факел должен быть длиннее, чем толщина детали. Это позволит эффективно выносить продукты горения за пределы рабочей зоны.

Качество резки металла
Опытный мастер должен быть способным одновременно контролировать все указанные параметры.
Скорость резки
Скорость газокислородной резки требуется выдерживать ровно такую, какая предусмотрена технологией.
В случае занижения скорости движения резака происходит перегрев материала и оплавление кромок.
При превышении может начаться частичный или полный непрорез металла, поскольку струя кислорода будет запаздывать и отклоняться.
Контролируют скорость визуально, по направлению факела и искр, вылетающих с тыльной стороны заготовки.
Зависит скорость также и от толщины разрезаемого металла.
Подготовка к резке металла
В ходе подготовительных операций линия резки и околоразрезная зона должны быть зачищены механическим способом от ржавчины, окалины, остатков лакокрасочных покрытий. Масложировые загрязнения следует удалить органическими растворителями.
Присутствие загрязнений в рабочей области приводит к снижению производительности и качества поверхности кромок.
Кроме того, загрязняющие вещества могут вступать в химические реакции при высокой температуре с образованием нежелательных соединений, налипающих на тыльную сторону разреза в виде шлаков.
Подготовка оборудования для газокислородной резки
Заготовку следует надежно закрепить в выбранном положении. Преимущество обычно остается за нижним положением — в нем облегчен доступ к детали и вынос сгоревшего металла с тыльной стороны разреза. Для этого нужно уложить заготовку на специальный раскроечный стол или подложить под нее негорючие подкладки.
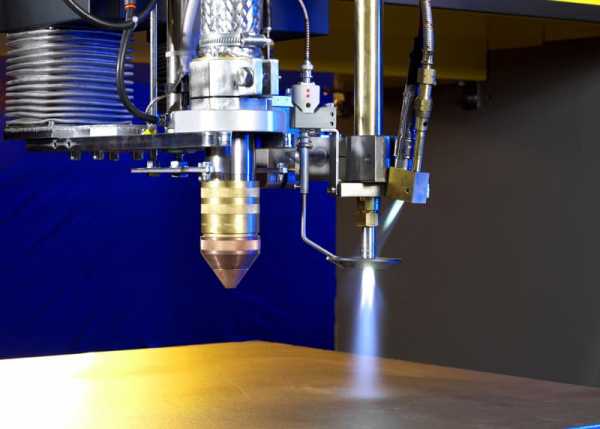
Установка для газокислородной резки металлов
Перед тем как зажечь газокислородный резак
Следует провести полную проверку оборудования:
- Осмотреть горелку, все разъемы, шланги, баллоны и арматуру на предмет отсутствия механических повреждений.
- На слух проверить отсутствие утечки газа. Проверять утечку зажженной спичкой недопустимо.
- Поверить инжекцию.
Осмотр резака
Особо опасной неисправностью, делающей невозможной дальнейшую работу, является обратный удар — распространение пламени в обратном направлении внутрь горелки. Если оператор слышит повторяющиеся хлопки или видит, как пламя втягивается внутрь горелки, он должен немедленно перекрыть подачу пропана, затем кислорода. Горелку следует остудить. Далее необходима прочистка и продувка инжектора, смесительной камеры и форсунок. Все соединения после продувки необходимо подтянуть. Категорически недопустимо:
- Продолжение резки при обратном ударе или нарушении регулировок состава газовой смеси.
- Удержание шлангов в руках или опора их на другие части тела.
- Движение с работающей газокислородной горелкой. При необходимости сменить рабочее место резак следует погасить и вновь разжечь на новом месте.
- Оставлять работающую горелку без присмотра.
Резак
Рабочая зона должна быть не захламлена и обеспечивать свободное перемещение оператора и шлангов.
Резка металла
Работа осуществляется в следующей последовательности:
- прогреть кромку, отклонив резак в сторону детали на 2-3°:
- поставить газокислородную горелку в вертикальное положение и подать кислород;
- снова отклонить резак на 2-3° в сторону реза;
- плавно, без рывков, вести горелку по линии разреза;
- перед окончанием линии немного снизить скорость и дорезать линию до конца.
Перед началом резания следует убедиться в том, что отрезаемый кусок конструкции надежно закреплен и не упадет на оператора или его коллегу
После окончания резки
Правильное завершение операции — это залог безопасности и качества работы. По окончании резания следует:
- Перекрыть подачу кислорода, а затем — горючего газа.
- Закрутить баллонные вентили.
- Открыть вентиль подачи кислорода на горелке и дать газу из шланга уйти в атмосферу, после чего закрутить его.
- Провернуть винт регулировки подачи кислорода, освободив его пружину.
- Очистить форсунки резака от шлаков и нагара.
- Отсоединить горелку от шлангов, свернуть их и подвесить в отведенном месте.
- Убрать газокислородную горелку в отведенное место хранения.
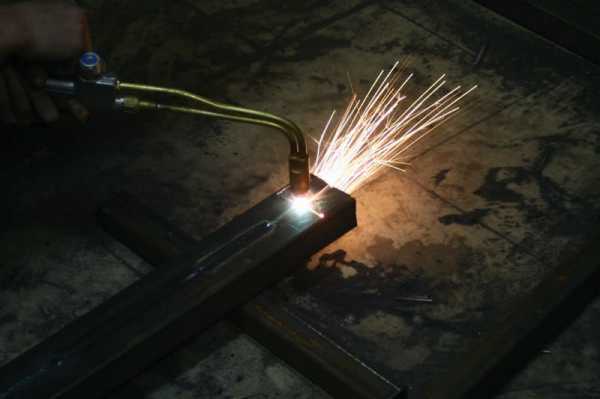
Резка металла газом
Перед тем, как покинуть рабочее место, следует убедиться в отсутствии задымления постороннего запаха и других признаков очагов возгорания.
Деформация материала при резке газом
Термические деформации часто сопутствуют технологическим операциям, связанным с нагревом заготовок до высоких температур. Чаще всего встречается изгиб и коробление.
Для снятия внутренних напряжений, возникших поле газокислородной резки, и восстановления формы деталей, применяют следующие приемы:
- термообработка методом отпуска или отжига;
- правка на правильных вальцах;
- прочное крепление проката перед раскроем и до полного остывания;
- повышенная скорость резания.
Кроме изменения формы, неравномерный нагрев может привести и изменению механических свойств заготовки. Их восстанавливают термообработкой.
Обратный удар при резке газом
Явление обратного удара заключается в изменении направления горения струи газовой смеси. При этом фронт горения втягивается в форсунку и далее начинает распространяться внутри горелки и по шлангам. В наихудшем случае он может привести к взрыву редукторов или даже баллонов с газом. Это серьезная угроза здоровью и жизни сотрудников и сохранности материальных ценностей. Во избежание печальных последствий резак оборудуется обратным клапаном, отсекающим подачу газа при изменении давления.
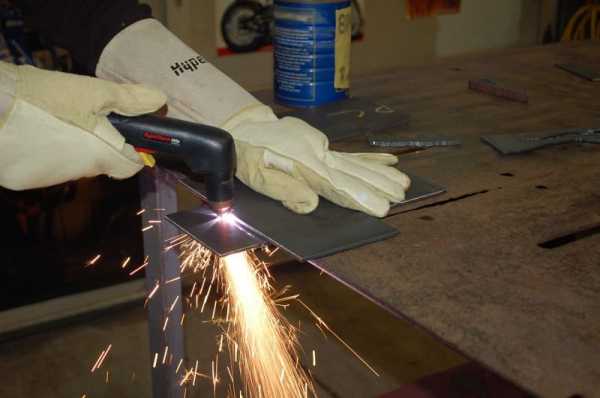
Обратный удар при резке металла
Пропан или ацетилен: что предпочесть?
Для кислородной резки используют несколько подогревающих газов. Наиболее часто применяют пропан. Это объясняется следующими его достоинствами:
- Низкая пожароопасность и взрывоопасность по сравнению с ацетиленом.
- Характерный запах меркаптановых добавок в пропане позволяет легко идентифицировать факт и место разгерметизации и утечки.
- Существенно более низкая стоимость пропана.
Ацетилен обладает своими достоинствами, которые в определенных обстоятельствах делают его более предпочтительным выбором. В их числе вдвое больший энергетический потенциал. При резке толстых конструкций или при необходимости обеспечить высокую скорость резания это становится определяющим фактором. Однако ацетилен более сложен в обращении, для него строже нормы безопасности и он существенно дороже.
Кроме того, ацетилен издает характерный неприятный запах, и в помещениях ограниченного объема он будет мешать другим работам.
Для работы в установке газокислородной резки не подходит бытовой газ. Там пропан смешан с бутаном, замедляющим или останавливающим процесс первичного нагрева. Промышленный пропан не содержит этой вредной примеси. При снижении температуры ниже 10 °С плотность пропана растет настолько, что изменяется скорость его подачи в горелку. Это приводит к снижению производительности и к повышенному износу деталей и узлов резака.
Кроме подогревающего газа, важно уделять внимание и держать под постоянным контролем узел подачи кислорода. Давление режущего кислорода — свыше 10 атмосфер, и при его утечке можно получить сильные ожоги.
Особенности выполнения ручной резки
Одна из самых распространенных ошибок резчика, приводящая к большому количеству дефектов — это запаздывание струи кислорода. Причинами этого явления служат неравные условия горения по глубине разреза. В средних и нижних слоях заготовки часть энергии факела растрачивается на непроизводительное нагревание соседних областей. Кроме того, часть энергии расходуется на образование окислов. Как следствие, факел отстает от горелки, и фронт разреза вместо вертикального становится наклоненным назад. Если идет раскрой листа и требуется высокая точность разреза, такой порок неприемлем. Для борьбы с этим нежелательным явлением форсунки горелки наклоняют немного назад. Часть факела отражается от фронта разреза, прогрев становится равномерным и обеспечивается требуемая точность, хоть и снижается скорость.
Кроме скорости движения резака, исключительно важна плавность этого движения. Рывки приводят к образованию термических напряжений и, в конечном счете — дефектов структуры. Не менее важно сохранение заданного угла наклона форсунок к разрезаемой поверхности.
Газокислородная резка не подходит для разделки металлов с низкой температурой плавления и высокой теплопроводностью. Детали из алюминия, например, просто расплавятся.
Точность ручной резки повышают с помощью использования шаблонов и лекал из материалов с высоткой температурой плавления.
Их накладывают на подлежащий раскрою лист и плавно обводят контуры горелкой. При этом повышается точность раскроя и качество поверхности среза, снижается и коэффициент отходов.
Механизированная газопламенная резка
Еще больше улучшить точность и коэффициент использования металла позволяют механизированные и автоматизированные установки газоплазменной резки. Их основные достоинства следующие:
- Высокая скорость реза с сохранением точности.
- Ниже требования к квалификации и опыту газорезчика.
- Автоматический контроль и коррекция параметров работы, включая скорость движения, наклон резака, подачу газов, ширину и длину факела. Это позволяет снизить непроизводительные потери металла.
- Входной контроль качества газов. При превышении допустимого содержания примесей установка блокирует работу.
- Совместимость с компьютерными программами оптимизации раскроя заготовок позволяет избежать процедуры разметки. Это повышает коэффициент использования металла и снижает себестоимость раскроя.
- Функция предварительного прогрева листа позволяет снизить термические напряжения в нем и уменьшить коробление. Предварительный прогрев также сокращает время выполнения основной операции.
- Вспомогательные устройства удаляют с поверхности листа шлаки и нагар, причем без остановки основной операции.
Рабочие параметры современных автоматических установок для раскроя достигают:
- скорость резания — до 0,6 метра в минуту;
- ширина разреза- 1-2 мм;
- точность соблюдения размеров — до 1 мм.
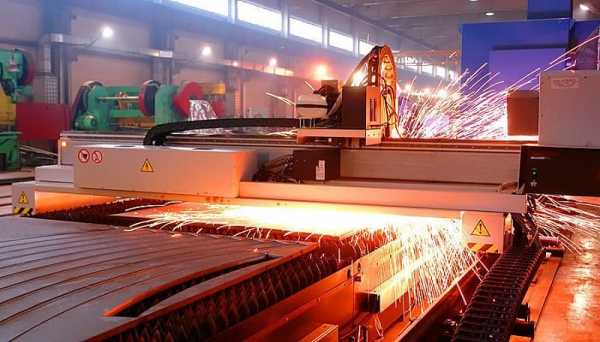
Механизированная газопламенная резка
Имеет автоматическая газокислородная резка и ряд недостатков. Это, прежде всего, ограничения по размеру раскраиваемого листа. Установка строго стационарна и не может использоваться в мобильном варианте, ее монтаж и наладка занимают несколько недель.
Если вы нашли ошибку, пожалуйста, выделите фрагмент текста и нажмите Ctrl+Enter.
stankiexpert.ru
Резка металла газом. Резка на природном газе.
Резка металла газом. Резка на природном газе. 4.63/5 (92.50%) проголосовало 24
Природный газ на многих предприятиях нашел широкое применение в качестве горючего газа для кислородной резки. Благодаря своей высокой теплотворной способности он широко используется в качестве полноценного заменителя ацетилена при кислородной резке стали толщиной до 300 мм и выше, а также для других видов газопламенной обработки металлов.
Содержание метана в природном газе.
Основу природного газа составляет метан, содержание которого в некоторых газовых месторождениях достигает 99%.
Давление природного газа в баллоне.
К местам потребления природный газ поступает по трубопроводам под низким давлением или под давлением 150 кг/см2 в баллонах, окрашенных в красный цвет. В случае отсутствия специальных баллонов для хранения и транспортирования природного газа могут быть использованы обычные кислородные баллоны с измененным вентилем и перекрашенные в красный цвет с соответствующей белой надписью.
Для резки газами — заменителями ацетилена разработаны специальные резаки. Они отличаются от ацетилено-кислородных резаков только размерами выходных отверстий наружного мундштука, смесительной камеры и инжектора, которые должны быть несколько большими.
Резак РЗР-55 для резки металла природным газом.
Резак РЗР-55 предназначен для ручной разделительной резки стали толщиной от 5 до 300 мм с использованием природного газа и некоторых других газов-заменителей, а также пропан-бутановой смеси. Он комплектуется двумя наружными и пятью внутренними мундштуками. Техническая характеристика резака РЗР-55 дана в табл. 1.
Таблица 1
Техническая характеристика резака РЗР-55.
Толщина разрезаемого металла, мм | № мундштука | Давление кислорода, кг/см2 | Скорость резки, мм/мин | Расход кислорода, м3/час | Расход, м3/час | |||
наружного | внутреннего | режущего | подогревательного | природного газа или метана | пропан-бутановой смеси | |||
5-15 | 1 | 1 | 2-2,5 | 430-320 | 2-2,5 | 1,4-1,8 | 1,1 | 0,4 |
15-50 | 1 | 2 | 2,5-3 | 340-190 | 5-10 | 1,7-2,1 | 1,3 | 0,5 |
50-100 | 1 | 3 | 3-4 | 205-125 | 10-15 | 1,7-2,3 | 1,4 | 0,5 |
100-200 | 2 | 4 | 4-7 | 140-90 | 15-26 | 2,1-2,6 | 1,6 | 0,6 |
200-300 | 2 | 5 | 7-11 | 100-85 | 25-40 | 2,5-3,0 | 1,9 | 0,7 |
Характеристика резака типа УР для резки на природном газе.
Чаще всего для работы на природном газе применяют обычные ацетилено-кислородные резаки с рассверленными отверстиями в смесительной камере, инжекторе и в наружных мундштуках. Характеристика резака типа УР для работы на природном газе дана в табл. 2.
При резке металла толщиной от 250 мм и более рекомендуется подачу кислорода в резак осуществлять по двум шлангам — отдельно для подогревательного пламени и режущей струи, при этом давление устанавливается по манометрам на отдельных редукторах.
Таблица 2
Характеристика резака типа УР для резки на природном газе.
Толщина металла, мм | № внутреннего мундштука | Диаметр отверстия, мм | Расход, м3/час | |||
В наружном мундштуке | В смесительной камере | Инжектора | Природного газа | Кислорода для горючей смеси | ||
5—15 | 1 | 6,0 | 3,0 | 1,0 | 1,1 | 1,7 |
15—50 | 2 | 6,0 | 3,0 | 1,0 | 1,3 | 1,9 |
50—100 | 3 | 6,0 | 3,0 | 1,0 | 1,4 | 2,0 |
100—200 | 4 | 7,2 | 3,0 | 1,0 | 1,6 | 2,4 |
200—300 | 5 | 7,2 | 3,0 | 1,0 | 1,9 | 2,9 |
Редуктор для природного газа.
После работы на природном газе нельзя использовать редуктор снова для кислорода без предварительного обезжиривания.
При работе от трубопровода у рабочего места рекомендуется устанавливать предохранительный жидкостный затвор.
При давлении в сети не свыше 0,02 кг/см2 может быть применен специальный постовой затвор ЗГГ-З для городского и природного газа (метана). Устройство и принцип работы его аналогичны затвору низкого давления для ацетилена.
При более высоких давлениях нужно устанавливать затвор закрытого типа. Лучше вместо затвора пользоваться редуктором, который является надежным предохранителем при обратном ударе, и позволяет производить работу в зимнее время на открытом воздухе.
Значительно меньшая температура пламени, создаваемого смесью природного газа и кислорода, по сравнению с температурой ацетилено-кислородного пламени, уменьшает скорость охлаждения кромок, нагреваемых при резке. Поэтому применение природного газа вместо ацетилена особенно целесообразно при кислородной резке легированных сталей, склонных к образованию трещин. Кроме того, резка на природном газе вызывает меньшее науглероживание на поверхности реза. Скорость резки такая же, как и при использовании ацетилена. Время подогрева кромки начала реза — больше.
При пользовании природным газом поверхность реза получается более чистой и качественной, чем при резке ацетиленом. Значительно меньше и деформация металла, что особенно важно при резке малых толщин.
Техника резки на природном газе ничем не отличается от техники резки на ацетилене.
Природный газ менее опасен в отношении образования взрывоопасных смесей с воздухом или кислородом, чем ацетилен, и менее чувствителен к обратным ударам. Однако при кислородной резке с использованием природного газа следует выполнять все правила техники безопасности, относящиеся к газопламенной обработке металлов с применением ацетилена
mechanicinfo.ru
Процессы газопламенной обработки металлов (гом)
Методы газопламенной обработки металлов объединяют свыше 30 технологических процессов (рис. 1.). По своему технологическому назначению они могут быть подразделены на четыре основные группы: резка, соединение, нагрев и напыление материалов. Основой этих процессов является использование концентрированного местного источника нагрева высокотемпературным пламенем. К газопламенным методам примыкают процессы газоэлектрической, в том числе плазменной и газолазерной обработки, при которых теплоносителем служит газ, а источником нагрева — плазменная дуга, лазерный луч и т. д.
Разработано высокопроизводительное автогенное оборудование, которое обеспечивает получение надежных и экономичных металлоконструкций, работающих при сложном нагружении, в широком интервале температур и давлений. Газопламенная обработка повсеместно применяется во многих отраслях народного хозяйства и обладает неоспоримыми преимуществами по сравнению с механической обработкой по производительности труда и капитальным затратам. Наиболее характерные области применения основных газопламенных процессов приведены в табл. 1..
В последние годы внедрение этих процессов непрерывно расширяется. Совершенствуются оборудование и аппаратура для их использования. Современные установки и машины для термической резки и напыления материалов характеризуются высокой степенью автоматизации с использованием программного управления н микропроцессорной техники. Вместе с тем энергетические основы процессов, использующих газовое пламя дли местного нагрева обрабатываемого материала, сохраняются прежними.
Газопламенная обработка преимущественно ведется с применением кислорода и горючих газов (ацетилена и его заменителей). Иногда используются смеси кислорода и паров горючих жидкостей (керосина или бензина). Применяемые при газопламенных процессах горючие газы и кислород подаются к месту работы в сжатом состоянии по газопроводам или в стальных баллонах.
До сих пор широко используется выработка ацетилена в передвижных генераторах на месте производства работ. Наиболее распространенными процессами газопламенной обработки являются газовая сварка и кислородная резка. Они сохраняют свое значение для некоторых видов металлообработки, несмотря на успешное развитие электродуговых методов сварки и резки.
Газовая сварка широко используется при сварке стали малой толщины, чугуна, цветных металлов и сплавов. Кислородная резка применяется на поточно-механизированных линиях для высокопроизводительного раскроя листового проката в судостроении, машиностроении и других отраслях металлообработки. Ручная кислородная резка до сих пор повсеместно используется для разделки металла в цеховых условиях, при ремонте, монтаже и в строительстве.
Рис 1. Структура процессов газопламенной обработки
Таблица 1. Области применения основных процессов газопламенной обработки металлов.
Процесс | Область применения |
Ручная кислородная резка | Разделительная резка низкоуглеродистой и низколегированной стали толщиной 3- 300 мм Разделительная резка низкоуглеродистой стали толщиной от 300 до 800 мм Разделительная резка скрапа. лома и низкоуглеродистой стали толщиной до 200 мм Разделительная резка высоколегированной стали Поверхностная зачистка местных дефектов на заготовках из низкоуглеродистой и низколегированной стали |
Машинная кислородная резка | Заготовительная прямолинейная резка Точная фигурная вырезка заготовок и деталей из листовой низкоуглеродистой стали толщиной до 100 мм Обрезка торцов труб в цеховых и полевых условиях (диаметром от 194 до 1420 мм) Резка стали большой толщины (до 2000 мм) Разделительная резка блюмсов и слябов на установках непрерывной разливки стали Сплошная поверхностная зачистка блюмсов и слябов в потоке прокатки |
Машинная плазменная резка | Точная фигурная вырезка заготовок и деталей из листовой низкоуглеродистой высоколегированной стали толщиной до 80 мм и алюминия толщиной до 100 мм |
Машинная лазерная резка | Точная фигурная вырезка деталей и заготовок из листов |
Газовая сварка | Сварка стали малой толщины, чугуна, цветных металлов и сплавов |
Ручная газопламенная пайка | Пайка легкоплавким и тугоплавкими припоями, низкотемпературная пайкосварка чугуна чугунными припоями |
Машинная газопламенная пайка | Механизированная высокопроизводительная пайка деталей из медных сплавов |
Ручная газопламенная пайка | Наплавка цветных металлов и твердых сплавов на стальные и чугунные изделия |
Газопорошковая наплавка | Тонкослойная наплавка износостойких покрытий из порошковых твердосплавных материалов |
Газопламенный нагрев, правка и очистка | Нагрев до 300°С изделий из черных и цветных металлов и неметаллических материалов, а также для оплавления поверхности битумной гидроизоляции Правка металлоконструкций до и после сварки Пламенная очистка поверхности металла от ржавчины, окалины и краски |
Газопламенное напыление покрытий | Нанесение покрытий из цинка, алюминия, стали и других материалов для защиты металлоконструкций от коррозии, повышения износостойкости деталей и восстановления их размеров Нанесение покрытий из порошков цинка и термопластических материалов с температурой плавления до 800°С для защиты от коррозии и уплотнения поверхностей Нанесение покрытий из самофлюсующихся твердых сплавов, оксида алюминия и других материалов для повышения износостойкости деталей
|
oitsp.ru
Газоплазменная резка металла, станки газоплазменной резки с ЧПУ, газоплазменные машины и установки
Сейчас все большее количество производственных и строительных компаний обзаводятся участками плазменной резки. Газопламенная резка металла обеспечивает качественное и быстрое разрезание металлических заготовок, выполнение многочисленных производственных процессов упрощается.
Сравнивая два способа резки металла: с помощью отрезного диска и высокотемпературным воздействием, следует отметить, что для второго характерны более высокие скорость и качество получаемой поверхности. Особенно это проявляется при работе с твердыми сплавами, к примеру, с высоколегированными сталями.
В этом случае твердость материала и режущего инструмента разнится незначительно, что приводит и к низкому качеству реза, и к быстрому износу инструмента. При резке плазмой таких проблем не возникает, поскольку твердость материала не играет никакой роли. Газоплазменная резка листового металла может использоваться для любых сплавов, в том числе и цветных металлов. При этом для разных материалов требуется менять только электроды и сопла.
Процесс газоплазменной резки металла
Суть процесса заключается в том, что газоплазменный станок генерирует дугу, которая расплавляет разрезаемый металл за счет высокой температуры и выдувает жидкий расплав напором плазмы. Для резки существует две схемы создания плазмы, первая из которых заключается в использовании наконечника сопла в качестве электрода. При этом обрабатываемый материал не включается в цепь. В результате получается независимый поток плазмы, которым разрезается заготовка.
Вторая схема предполагает включение заготовки в цепь. Таким образом, плазменная дуга зажигается между электродом и обрабатываемым металлом. Резка металла производится электрической дугой и плазменным столбом.
Второй способ резки является более эффективным с точки зрения использования энергии, поскольку мощность дуги используется в виде разрядов, находящихся за пределами наконечника. Поэтому для обработки металлических сплавов, способных проводить электрический ток, используется эта схема. Плазменная резка с независимой дугой применяется ограниченно, в основном для неметаллических материалов.
Газоплазменные станки с ЧПУ
Любая установка газоплазменной резки металла имеет такие элементы:
− источник питания;
− компрессор;
− горелка;
− зажим.
Небольшие установки имеют совмещенный компрессор и источник плазмы. Это удобно при использовании аппарата на удаленной строительной площадке, поскольку позволяет обходиться минимальным количеством оборудования. С другой стороны, мощность таких устройств ограничена, поэтому их сфера использования заключается в резке заготовок небольшой толщины.
В ручных станках оператор самостоятельно перемещает горелку
для резки заготовки. Для промышленности это неэффективно, поэтому используются станки газоплазменной резки с ЧПУ, которые имеют рабочий стол и механизм для перемещения горелки.
Портальные газоплазменные машины
Портальные газоплазменные машины обладают высокой точностью и обеспечивают весьма качественную резку металла. Точность обеспечивается за счет жесткой конструкции, которая позволяет перемещать горелку с минимальным отклонением от заданной траектории. По точности такие станки уступают только лазерным установкам, но намного дешевле их.
Газоплазменная машина портального вида позволяет выполнить раскрой листов с высокой скоростью. Крайне удобно то, что станок выполняет однотипную работу самостоятельно, что значительно увеличивает производительность при массовом и крупносерийном производстве.
sibirsvarka.ru
Газопламенная резка – Большая Энциклопедия Нефти и Газа, статья, страница 3
Газопламенная резка
Cтраница 3
При газопламенной резке металлов вместо горелок применяются резаки, которые отличаются от сварочных горелок наличием добавочного кислородопро-пода и конструкцией мундштука, в котором через центральное отверстие вытекает чистый, так называемый режущий кислород, а через концентрично расположенные отверстия – горючая смесь для подогрева металла. [31]
При газопламенной резке листов из углеродистых и низколегированных сталей металл нагревается до температуры выше точки плавления; при этом происходит его интенсивное сгорание в струе газового окислителя. Окислителем служит технически чистый кислород. [32]
Под газопламенной резкой ( чаще ее называют кислородной) понимают способ разделения металла по прямому или криволинейному контуру. Метод основан на использовании для нагрева смеси горючих газов с кислородом и экзотермической ( с выделением тепла) реакции окисления металла. [33]
Когда применяется газопламенная резка или электросварка, сечение реза должно находиться на расстоянии не менее 250 мм от сечения разрушения, причем последнее не должно подвергаться каким-либо дополнительным воздействиям. [34]
Применяется также газопламенная резка, выполняемая при помощи ацетилено-кисло-родных и керосино-кислородных резаков, а также с применением заменителей ( пропан, бутан и-т. [35]
Станки для газопламенной резки в большинстве случаев предназначены для выполнения прямых и косых резов на трубах, резки секторов для сварных отводов, а также для фасонной отрезки штуцеров и вырезки отверстий в трубах. Резка может производиться как со скосом, так и без скоса кромок под сварку. [37]
Оборудование для газопламенной резки значительно дешевле гильотинных ножниц и кромкострогальных станков. [38]
Горючим для газопламенной резки могут быть ацетилен, бензин, керосин. Температура пламени ацетилена 3100 – 3800 С, бензина 2500 – 2600 С, керосина 2000 С. Применяют также другие газы с температурой пламени не ниже 1800 С. [39]
При выполнении газопламенной резки металла с помощью жидкого топлива ( керосина, бензина или их смеси) наполнять бачок горючим разрешается не более чем на 0 75 его емкости. [40]
Особые преимущества полуавтоматической и автоматической газопламенной резки по сравнению с ручной должны быть учтены при проектировании серийных и массовых работ по вырезке деталей и по разделке кромок с применением копирующих механизмов. [41]
Резаки предназначены для газопламенной резки металла. [43]
Кроме станков для газопламенной резки труб, применяемых только на трубопроводных заводах и в мастерских, имеется большое количество различных конструкций переносных приспособлений для газопламенной разделительной и фасонной резки. Примерами таких приспособлений могут служить механизированный газовый резак ТР-2, предназначенный для разделительной резки труб Dy от 190 до 350 мм; труборез ГРВ-2 для разделительной резки труб Dy от 108 до 450 мм с креплением из велосипедной цепи; машина Спутник для труб Dy от 194 до 1100 мм; переносная головка ПГР-2 для вырезки отверстий Dv от 50 до 400 мм под штуцера в трубах Dy от 150 до 500 мм. [44]
Страницы: 1 2 3 4
www.ngpedia.ru
Преимущества газоплазменной резки металлов
- Подробности
- Опубликовано 26.03.2018 10:55
Технологические разработки позволили разработать инновационные решения для промышленных процессов, связанных с резанием металла. Примером может служить газоплазменная резка. Характеризуемый точностью и скоростью, этот вид резки набирает популярность. Он эффективен не только для тонких и толстых листов металла. Можно также прорезать ржавый, окрашенный или грязный металл. Газопламенная резка имеет много преимуществ, благодаря чему используется во многих отраслях промышленности. В этом процессе резания используется газовая струя, выпущенная с большой скоростью, чтобы резать металл толщиной до шести дюймов при очень высоких температурах.
Преимущества газопламенной резки многочисленны:
Скорость резки. Роботизированные плазменные резаки в пять раз быстрее, чем работа традиционными ручными резаками, и способны разрезать до 500 дюймов в минуту.
Широкий диапазон материалов и толщины – роботы для плазменной резки могут делать точные разрезы в различных металлах и толщинах. Плазменные резаки используют азот, что позволяет им резать сталь, алюминий и другие металлы.
Простота использования. Для работы с резаками требуется некоторая подготовка и практика для эффективного использования. Но плазменные резаки просты в использовании и не требуют большой подготовки для обработки. Если эти инструменты используются в отрасли, это позволит сэкономить затраты на обучение сотрудников. Плазменные резаки обычно удобны и просты в эксплуатации. Даже новый пользователь может сделать почти идеальную резку с первой попытки.
Безопасность. В процессе используется газ, который не является легковоспламеняющимся, устраняя некоторые из опасностей, связанных с безопасностью, с процедурами газовой резки.
Экономичность. Плазменная резка является экономически эффективным применением – она дешевле, чем лазерная или водоструйная резка.
Сохраняет материалы в прохладном состоянии. Несмотря на то, что процесс происходит при высоких температурах, роботизированные системы плазменной резки могут удерживать поверхность материалов прохладными. Это предотвращает деформацию и повреждение краски и других покрытий.
Эти многочисленные преимущества дополняют данный метод резки, который не только сократит производственные и трудовые затраты, но и улучшит качество вашего продукта.
- < Назад
- Вперёд >
myelectro.com.ua