Роквелл бринелль: Таблица твердости по Бринеллю, Роквеллу, Виккерсу, Шору
alexxlab | 15.02.2021 | 0 | Разное
Таблица соответствия HB-HRC
Твёрдость – это сопротивление тела внедрению индентора – другого твёрдого тела. Способы испытания твёрдости подразделяются на статические и динамические.
К статическим относятся способы измерения твёрдости по Бринеллю, Викерсу, Роквеллу, Кнупу; к динамическим – способы измерения твёрдости по Шору, Шварцу, Бауману, Польди, Морину, Граве.
Измерения твёрдости осуществляют при 20±10°С.
Измерение твёрдости по Бринеллю
Бринелля метод [по имени шведского инженера Ю.А.Бринелля (J.A.Brinell)] – способ определения твёрдости материалов вдавливанием в испытываемую поверхность стального закалённого шарика диаметром 2,5; 5 и 10 мм пр нагрузке P от 625 H до 30 кН. Число твёрдости по Бринеллю HB – отношение нагрузки (кгс) к площади (мм2) поверхности отпечатка. Для получения сопоставимых результатов относительной твёрдости материалы (HB свыше 130) испытывают при отношении P:D2=30, материалы средней твёрдости (HB 30-130) – при P:D2=10, мягкие (HB<30) – при P:D2=2,5.
Метод измерения твердости металлов по Бринеллю регламентирует ГОСТ 9012-59 “Металлы. Метод измерения твердости по Бринеллю”: Стандарт устанавливает метод измерения твердости по Бринеллю металлов с твердостью не более 650 единиц. Сущность метода заключается во вдавливании шарика (стального или из твердого сплава) в образец (изделие) под действием усилия, приложенного перпендикулярно к поверхности образца, в течение определенного времени, и измерении диаметра отпечатка после снятия усилия. ГОСТ 9012-59, в частности, определяет требования, предъявляемые к отбору образцов металла для измерения твёрдости по Бринеллю – размер образцов, шероховатость поверхности и др.
Измерение твёрдости по Роквеллу
Роквелла метод [по имени американского металлурга С. Роквелла (S.Rockwell), разработавшего этод метод] – способ определения (измерения) твёрдости материалов (главным образом металлов) вдавливанием в испытываемую поверхность алмазного индентора с углом при вершине 120° (шкалы А и С) или стального закалённого шарика диаметром 1/16 дюйма или 1,588 мм (шкала B. Твёрдость по Роквеллу выражается в условных единицах. За единицу твёрдости принята величина, соответствующая перемещению индентора на 0,002 мм. Испытание методов Роквелла проводят на специальном настольном приборе, снабжённом индикатором, который показывает число твёрдости. ГОСТ 23677-79.
Таблица соответствия HB – HRC (Перевод значений твёрдости)
(соотношение твёрдости по Бриннелю твёрдости по Роквеллу,определяемых методами в соответствии с ГОСТ 8.064-79)
Твердость по Роквеллу | Твердость по Роквеллу | Твердость по Бринеллю | |
HRCэ | HRC | D=10мм HB | Р=3000кг диаметр отпечатка в мм |
– | – | HB 95,0 | 6 |
– | – | HB 100 | 5,87-5,89 |
– | – | HB 111 | 5,60-5,62 |
– | – | HB 115 | 5,51-5,53 |
– | – | HB 116 | 5,49-5,50 |
– | – | HB 120 | 5,41-5,42 |
– | – | HB 125 | 5,31-5,42 |
– | – | HB 130 | 5,22 |
– | – | HB 135 | 5,13 |
– | – | HB 137 | 5,09-5,10 |
– | – | HB 138 | 5,07-5,08 |
– | – | HB 140 | 5,04-5,05 |
– | – | HB 141 | 5,02-5,03 |
– | – | HB 142 | 5,01 |
– | – | HB 143 | 5 |
– | – | HB 143 | 4,99 |
– | – | HB 144 | 4,98 |
– | – | HB 144 | 4,97 |
– | – | HB 145 | 4,96 |
– | – | HB 146 | 4,95 |
– | – | HB 152 | 4,86 |
– | – | HB 161 | 4,72-4,73 |
– | – | HB 164 | 4,68-4,69 |
– | – | HB 167 | 4,64-4,65 |
– | – | HB 170 | 4,60-4,61 |
– | – | HB 174 | 4,55-4,56 |
– | – | HB 179 | 4,49-4,50 |
– | – | HB 185 | 4,42-4,43 |
– | – | HB 197 | 4,29-4,30 |
– | – | HB 198 | 4,28 |
– | – | HB 199 | 4,27 |
– | – | HB 200 | 4,26 |
– | – | HB 201 | 4,25 |
– | – | HB 202 | 4,24 |
– | – | HB 203 | 4,23 |
– | – | HB 204 | 4,22 |
– | – | HB 205 | 4,21 |
HRCэ 20,0 | HRC 17,9 | HB 206 | 4,2 |
HRCэ 20,5 | HRC 18,3 | HB 209 | 4,18 |
HRCэ 21,0 | HRC 19,0 | HB 212 | 4,15 |
HRCэ 21,5 | HRC 19,7 | HB 215 | 4,12 |
HRCэ 22,0 | HRC 20,1 | HB 217 | 4,1 |
HRCэ 22,5 | HRC 20,5 | HB 219 | 4,08 |
HRCэ 23,0 | HRC 20,9 | HB 222 | 4,06 |
HRCэ 23,5 | HRC 21,3 | HB 224 | 4,04 |
HRCэ 24,0 | HRC 22,0 | HB 229 | 4 |
HRCэ 24,5 | HRC 22,4 | HB 231 | 3,98 |
HRCэ 25,0 | HRC 22,8 | HB 234 | 3,96 |
HRCэ 25,5 | HRC 23,6 | HB 239 | 3,92 |
HRCэ 26,0 | HRC 24,0 | HB 241 | 3,9 |
HRCэ 26,5 | HRC 24,4 | HB 244 | 3,88 |
HRCэ 27,0 | HRC 24,8 | HB 246 | 3,86 |
HRCэ 27,5 | HRC 25,6 | HB 252 | 3,82 |
HRCэ 28,0 | HRC 26,0 | HB 255 | 3,8 |
HRCэ 28,5 | HRC 26,4 | HB 257 | 3,78 |
HRCэ 29,0 | HRC 27,3 | HB 263 | 3,74 |
HRCэ 30,0 | HRC 28,1 | HB 269 | 3,7 |
HRCэ 30,5 | HRC 28,6 | HB 272 | 3,68 |
HRCэ 31,0 | HRC 29,0 | HB 275 | 3,66 |
HRCэ 31,5 | HRC 29,4 | HB 278 | 3,64 |
HRCэ 32,0 | HRC 29,9 | HB 282 | 3,62 |
HRCэ 32,5 | HRC 30,3 | HB 285 | 3,6 |
HRCэ 33,0 | HRC 30,8 | HB 288 | 3,58 |
HRCэ 33,5 | HRC 31,6 | HB 295 | 3,54 |
HRCэ 34,0 | HRC 32,1 | HB 298 | 3,52 |
HRCэ 34,5 | HRC 32,5 | HB 302 | 3,5 |
HRCэ 35,0 | HRC 33,0 | HB 306 | 3,48 |
HRCэ 35,5 | HRC 33,8 | HB 313 | 3,44 |
HRCэ 36,0 | HRC 34,3 | HB 317 | 3,42 |
HRCэ 36,5 | HRC 34,7 | HB 321 | 3,4 |
HRCэ 37,0 | HRC 35,2 | HB 325 | 3,38 |
HRCэ 37,5 | HRC 35,6 | HB 329 | 3,36 |
HRCэ 38,0 | HRC 36,0 | HB 333 | 3,34 |
HRCэ 38,5 | HRC 36,5 | HB 337 | 3,32 |
HRCэ 39,0 | HRC 36,9 | HB 341 | 3,3 |
HRCэ 39,5 | HRC 37,8 | HB 350 | 3,26 |
HRCэ 40,0 | HRC 38,2 | HB 354 | 3,24 |
HRCэ 40,5 | HRC 38,7 | HB 359 | 3,22 |
HRCэ 41,0 | HRC 39,1 | HB 363 | 3,2 |
HRCэ 41,5 | HRC 40,0 | HB 373 | 3,16 |
HRCэ 42,0 | HRC 40,5 | HB 378 | 3,14 |
HRCэ 42,5 | HRC 40,9 | HB 383 | 3,12 |
HRCэ 43,0 | HRC 41,4 | HB 388 | 3,1 |
HRCэ 43,5 | HRC 41,9 | HB 393 | 3,08 |
HRCэ 44,0 | HRC 42,4 | HB 398 | 3,06 |
HRCэ 44,5 | HRC 42,9 | HB 403 | 3,04 |
HRCэ 45,0 | HRC 43,3 | HB 409 | 3,02 |
HRCэ 45,5 | HRC 43,8 | HB 415 | 3 |
HRCэ 46,0 | HRC 44,4 | HB 420 | 2,98 |
HRCэ 46,5 | HRC 44,9 | HB 426 | 2,96 |
HRCэ 47,0 | HRC 45,4 | HB 432 | 2,94 |
HRCэ 47,5 | HRC 45,9 | HB 438 | 2,92 |
HRCэ 48,0 | HRC 46,5 | HB 444 | 2,9 |
HRCэ 48,5 | HRC 47,0 | HB 451 | 2,88 |
HRCэ 49,0 | HRC 47,6 | HB 457 | 2,86 |
HRCэ 49,5 | HRC 48,2 | HB 464 | 2,84 |
HRCэ 50,0 | HRC 48,8 | HB 470 | 2,82 |
HRCэ 50,5 | HRC 49,4 | HB 477 | 2,8 |
HRCэ 51,0 | HRC 50,0 | HB 484 | 2,78 |
HRCэ 51,5 | HRC 50,6 | HB 492 | 2,76 |
HRCэ 52,0 | HRC 50,7 | HB 502 | 2,74 |
HRCэ 52,5 | HRC 51,5 | HB 503 | 2,73 |
HRCэ 52,0 | HRC 51,8 | HB 506 | 2,72 |
HRCэ 53,5 | HRC 52,5 | HB 514 | 2,7 |
HRCэ 54,0 | HRC 53,1 | HB 522 | 2,68 |
HRCэ 54,5 | HRC 53,5 | HB 526 | 2,67 |
HRCэ 55,0 | HRC 53,8 | HB 530 | 2,66 |
HRCэ 55,5 | HRC 54,1 | HB 534 | 2,65 |
HRCэ 56,0 | HRC 54,5 | HB 538 | 2,64 |
HRCэ 56,5 | HRC 55,1 | HB 547 | 2,62 |
HRCэ 57,0 | HRC 55,8 | HB 555 | 2,6 |
HRCэ 57,5 | HRC 56,5 | HB 564 | 2,58 |
HRCэ 58,0 | HRC 57,2 | HB 573 | 2,56 |
HRCэ 58,5 | HRC 57,6 | HB 578 | 2,55 |
HRCэ 59,0 | HRC 57,9 | HB 582 | 2,54 |
HRCэ 59,5 | HRC 58,6 | HB 592 | 2,52 |
HRCэ 60,0 | HRC 59,3 | HB 601 | 2,5 |
HRCэ 60,5 | HRC 59,7 | HB 606 | 2,49 |
HRCэ 61,0 | HRC 60,0 | HB 611 | 2,48 |
HRCэ 61,5 | HRC 60,4 | HB 616 | 2,47 |
HRCэ 62,0 | HRC 60,7 | HB 621 | 2,46 |
HRCэ 62,5 | HRC 61,1 | HB 627 | 2,45 |
HRCэ 63,0 | HRC 61,4 | HB 632 | 2,44 |
HRCэ 63,5 | HRC 62,1 | HB 643 | 2,42 |
HRCэ 64,0 | HRC 63,2 | HB 659 | 2,39 |
HRCэ 64,5 | HRC 63,6 | HB 665 | 2,38 |
HRCэ 65,0 | HRC 63,9 | HB 670 | 2,37 |
HRCэ 65,5 | HRC 64,3 | HB 676 | 2,36 |
Задать вопрос
Выбор мер твердости
Форма позволяет выбрать стандартные эталонные меры твёрдости 2-го разряда.
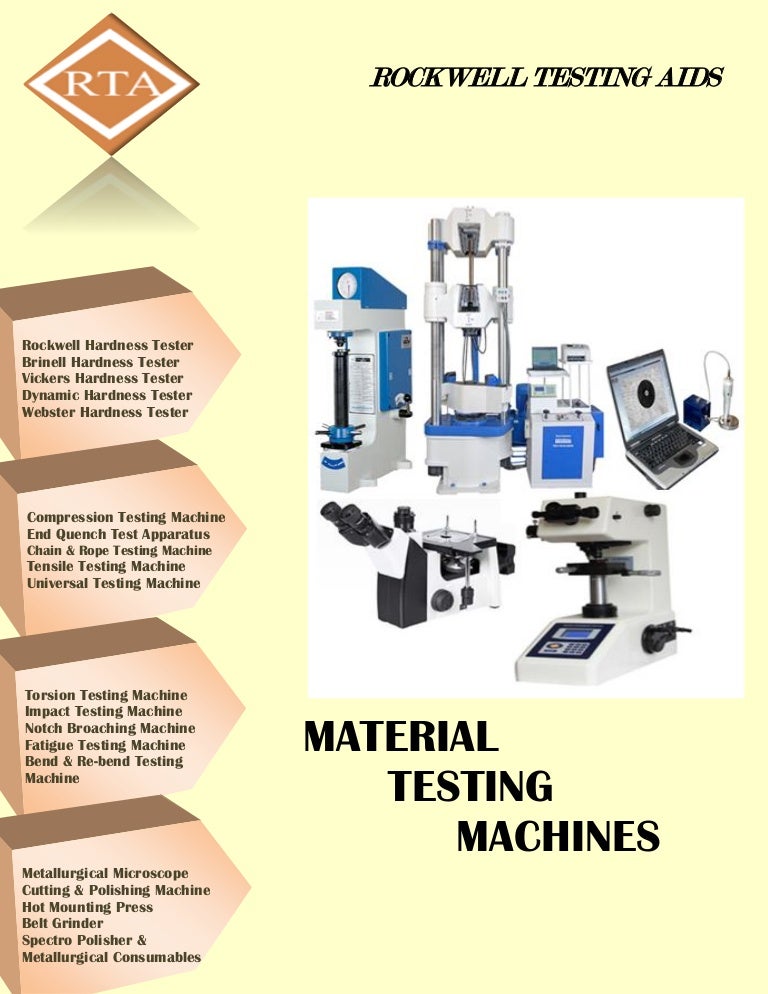
Шкала твёрдости:
Диапазон твёрдости меры:
Нагрузка:
Добавлено в заказ:
–
Перейти к оформлению заказа
В случае необходимости заказа нестандартных эталонных мер твёрдости или эталонных мер твёрдости первого разряда, пожалуйста, напишите нам [email protected] или через форму обратной связи
Обзор шкал твердости: Роквелл, Бринелль
Многообразие различных шкал твёрдости пугает. Бринелль, Шор, Виккерс, Роквелл. У последней, помимо всем известной «подшкалы» С (отсюда и обозначение HRC– HardnessRockwell “C”), есть ещё и другие «подшкалы» «A», «B», «D», «E», «F», «H», «K». И это – не говоря о брате-близнеце – шкале Супер-Роквелла. Казалось бы, зачем так много: вдавили наконечник да посмотрели отпечаток. А какой наконечник? Какой формы? Из какого материала? А с каким усилием вдавливать? А если надо измерять твёрдость тонкой пластины? А если по глубине твёрдость разная? А если образец анизотропен в разных направлениях? А какой геометрический параметр отпечатка измерять?
Если коротко, то разные шкалы как раз и дают ответы на эти вопросы. Если чуть подробнее, то читаем дальше.
Шкала Роквелла.
Здесь остановимся только на самых известных «A», «B» и «С». Остальные используют очень редко, хотя меры твёрдости по таким шкалам мы тоже изготавливаем.
Шкала «A» – внедряется алмазный конус с углом при вершине 120˚ и основной нагрузкой 60 кгс. Пожалуй, самая универсальная «подшкала» из шкал Роквелла, т.к. её максимальная твёрдость соответствует максимальной твёрдости для металлов по шкале HRС (значение 83 HRA примерно соответствует значению 65HRC), а минимальная – минимальной по шкале HRB.
Шкала «B» – внедряется стальной шарик диаметром 1.588 мм при нагрузке 100 кгс. Используется для измерения твёрдости мягких материалов, когда шкала HRC уже «кончилась», т.е. мягче 20 HRC. При этом, будьте осторожны, если надавить таким способом в твёрдый материал, твёрдостью выше 40 HRC, то может «кончиться» уже шарик – повредится при вдавливании. В этом смысле международный стандарт ISO 6508 предусматривает шкалу HRBW. Последняя буква «W» в данном случае обозначает твердосплавный шарик из карбида вольфрама. Его можно вдавливать в твёрдые металлы.
Шкала «С» – внедряется алмазный конус с углом при вершине 120˚, как в шкале HRA, но основная нагрузка – не 60 кгс, а 150 кгс. На практике это даёт возможность стабильного измерения на более шероховатых поверхностях, чем при измерении по шкалам HRAили HRB. C другой стороны, возможности шкалы HRCограничены как твёрдостью – нельзя измерять детали мягче, чем 20HRC, так и толщиной детали. Дело в том, что нагрузка 150 кгс заставляет алмазный индентор вдавливаться глубже, чем нагрузка 60 кгс. При этом есть требование ГОСТа 9013-59 на метод Роквелла: «1.1. Толщина образца (или изделия) должна не менее чем в 10 раз превышать глубину внедрения наконечника после снятия основного усилия». Таким образом, использование шкалы HRA или HRB, за счёт меньших нагрузок, позволяет измерять более тонкие детали.
Полезно иметь в виду
- 1.График зависимости минимальной толщины образца от ожидаемой твёрдости. График взят из ГОСТ 9013-59.
- 2.Мало кто учитывает поправки в случае измерения на сферических или цилиндрических поверхностях (приложение 3, ГОСТ 9013-59). А напрасно, они существуют.
Шкала Бринелля.
Самый древний метод измерения твёрдости. Отличие от шкалы Роквелла – измеряется не глубина отпечатка, а диаметр. Поскольку вариантов индентора и нагрузок довольно много, то вместо того, чтобы каждому варианту придумывать название, после твёрдости в HB сразу указываются эти параметры. Например, 105 HB 2.5/62.5/10.
– «105» – понятно, это – число твёрдости в единицах HB
– «2.5» – диаметр шарика в мм (можно от 1 до 10 мм),
– «62.5» – нагрузка в кгс (можно от 5 до 3000 кгс), -
– «10» – время выдержки в нагруженном состоянии в с (почти всегда 10 с, кроме мягких материалов, там до 180 с).
При этом значение твёрдости 105 HBможет быть другим при других параметрах измерения.
Выбор размера шарика и нагрузки зависит от ожидаемой твёрдости и материала (ГОСТ 9012-59, п. 4.6), толщины (ГОСТ 9012-59, приложение 5), качества поверхности (чем больше шероховатость, тем больше должен быть отпечаток), размера отпечатка (ГОСТ 9012-59, п. 4.7), настроения технолога.
Как и со шкалой HRB(W), можно использовать твердосплавный шарик W во всём диапазоне твёрдости (0 – 650 HBW) и нужно при твёрдости более 450 HB.
Используя небольшую нагрузку и маленький диаметр шарика, можно измерять сверхмягкие материалы (даже шкала Роквелла HRB не справится) твёрдостью 0..5 HB 1/10/180. Кстати, мы научились делать меры твёрдости 0..10 HB из оловянного сплава, а также 30..50 HB из алюминиевого.
Пообщаться на данную тему можно по телефону +7(495) 229-75-26 или по электронной почте support@tverdomer. ru
Полезная информация:
1. ГОСТ 9031-75, официальное издание, М.: ИПК Издательство стандартов, 2004
2. ГОСТ 9012-59, официальное издание, М.: Стандартинформ, 2007
3. ГОСТ 9013-59, официальное издание, М.: ИПК Издательство стандартов, 2001
Разница между тестами Роквелла и Бринелля
Все знают, какие предметы твердые, а какие нет.
Это просто то, что люди знают, но не особо задумываются.
Итак, если кого-то из этих людей спросят, как они пришли к такому выводу, им, возможно, придется немного подумать.
Для тех, кто задается вопросом, твердость относится к различной способности данного объекта или материала противостоять вдавливанию при приложении к нему силы.
Твердость объекта следует классифицировать как особенность или характеристику, а не как одно из его свойств, и твердость обычно измеряется путем расчета постоянной площади вмятины, вызванной фиксированной нагрузкой.
Тесты Хардвелла и Бринелля – это два конкретных метода измерения твердости.
[ux_custom_products cat = ”тестер твердости по Бринеллю” продукты = ”” columns = ”4 ″]
Тест БринелляСреди стандартизированных испытаний на твердость метод испытания на твердость по Бринеллю оказался самым первым испытанием, которое широко использовалось.
Обычно он используется для измерения твердости металлических материалов, при этом особое предпочтение отдается грубым материалам.
Также может случиться так, что материал просто непригоден для прохождения других испытаний, поэтому испытание Бринелля останется единственным методом определения твердости.
Чугун – это один из материалов, который требует испытания Бринелля, поскольку он требует относительно большого индентора (как те, что используются в испытаниях Бринелля, например, карбидный шарик).
Однако тест Бринелля не подходит для материалов, которые слишком сильно затвердевают, и закаленная сталь является одним из очевидных примеров.
В дополнение к этому, этот метод также довольно медленный по сравнению с другими тестами и имеет тенденцию оставлять непоправимые отпечатки на металлическом предмете или материале.
Тест Роквелла
Тест Роквелла является более простым из двух методов и, как правило, более точным.
Его можно использовать для тестирования металлов всех видов, включая твердые (в отличие от тестов Бринелля), за исключением обстоятельств, когда внешние факторы играют роль в предотвращении этого.
Также это наиболее часто используемый тест.
Тест Роквелла использует определенные шаги для измерения твердости.
В отличие от теста Бринелля, в нем используется индентор меньшего размера, например алмаз.
Этот индентор используется для приложения небольшой нагрузки (повышенная нагрузка / усилие применяется позже), чтобы избежать разрушения поверхности материала.
Таким образом, он оказывается менее разрушительным методом по сравнению с тестом Бринелля.
Распространять любовь
Проверьте наш тестер твердости для горячей продажи!
Универсальный твердомер VERZUS 700
Универсальный твердомер VERZUS 700
по Бринеллю, Роквеллу и Виккерсу
Электронная нагрузочная ячейка последнего поколения с замкнутым циклом управления. Вибрации и положение твердомера при измерении не оказывают влияния на результат испытания. Твердомер имеет повышенную раму жесткости.
Преобразование результатов в другие шкалы твердости и онлайн статистика одним нажатием кнопки без использования таблиц.
Позволяет проводить все стандартные методы измерения твердости в диапазоне нагрузок от 1 кгс/9.8Н до 250 кгс/2.45 кН. Все процедуры соответствуют или превышают по точности требования стандартов EN/ISO, ASTM и JIS.
Оптическое разрешение считывания 0.1 мкм.
Универсальный твердомер для измерения твердости по методам Роквелла, Супер-Роквелла, Бринеллю, Виккерсу, HVT, HBT и возможностью измерения глубины отпечатка (Rockwell, HBT, HVT, H)
• Все модели включат шкалу измерения твердости ISO 2039
• Модель имеет встроенный электронный микроскоп с выбором объективов и скользящим столом.
• Автоматическая корректировка значений измерений на неровных поверхностях.
• Цветной OLED дисплей, прост в эксплуатации.
• Хранение большого объема информации, ведение статистики результатов измерений, функция калибровки, возможность сохранения программ измерения твердости.
• Принтер с выходом USB-2.
• Большое рабочее пространство.
Технические характеристики VERZUS 700CCD:
Шкалы измерения: Роквелл / Супер-Роквелл, Бринелль, Виккерс, HVT, HBT и измерение глубины отпечатка.
Диапазон измерения твердости по всем шкалам: от 1 кгс/9.8Н до 250 кгс/2.45кН
Нагрузки испытаний: | 1 кгс/9.8Н, 2 кгс/19.6Н, 2.5 кгс/24.5Н, 3 кгс/29.4 Н,4 кгс/39.2 Н, 5 кгс/49 Н, 6.25 кгс/61.29 Н, 10 кгс/98 Н,15 кгс/147 Н, 15.625 кгс/153.2 Н, 20 кгс/196.13 Н, 25 кгс/245.16 Н, 30 кгс/294. |
Нагрузки по Виккерсу: | HV 1 кгс/9.8 Н, 2 кгс/19.6 Н, 3 кгс/29.4Н, 4 кгс/39.2 Н, 5 кгс/49 Н, 10 кгс/98 Н, 20 кгс/196.13 Н, 30 кгс/294.19 Н, 50 кгс/490 Н, 100 кгс/980.7 Н, 120 кгс/ 1176.79 Н, HVT: 50 кгс/490 Н, 100 кгс/980.7 Н |
Нагрузки по Бринеллю: | HB1: 2.5 кгс/24.5 Н,5 кгс/49 Н,10 кгс/98 Н,31.25 кгс/306.45 Н HB2.5: 6.25 кгс/61.29 Н,15.625 кгс/153.2 Н, 31.25 кгс/306.45 Н, 62.5 кгс/612 Н, 187.5 кгс/1838 Н HB5: 25 кгс/245.16 Н, 62.5 кгс/612 Н, 125 кгс/1225 Н, 250 кгс/2.45 кН; HB10: 100 кгс/980.7 Н, 250 кгс/2.45 кН HBT2.5: 62.5 кгс/612 Н, 187.5 кгс/1838Н HBT: 5 кгс/49 Н, 250 кгс/2.45 кН |
Шкалы по Роквеллу: A, B, C, D, E, F, G, H, K, L, M, P, R, S, V, 15N, 30N, 45N, 15T, 30T, 45T, 15W, 30W, 45W, 15X, 30X, 45X, 15Y, 30Y, 45Y
• Индентор измерения твердости пластиков по ISO 2039/1
• Оптическая система RSB: Внешний микроскоп для просмотра измерений твердости по Бринеллю с осветителем LED (Улучшенное качество при минимальном потреблении энергии).
• Дисплей: Цветной, результаты тестирования, ведение статистики, настройки, калибровки и т.д.
• Объективы сменные: 2.5х, 5х, 10х
• Окуляр: 10х (по запросу 15х)
• Время выдержки настраиваемое: от 1 с до 99 с
• Интерфейс: USB-2 (RS-232)
• Разрешение цифрового микроскопа: 0,1 мкм
• Соответствует требования стандартов или превышает требования EN/ISO, ASTM и JIS
• Способ измерения: полностью автоматический (Нагружение, выдержка, разгружение)
Инденторы:
• Шариковый по Бринеллю: 1 мм, 2,5 мм, 5 мм, 10 мм
• Алмазная пирамидка по Виккерсу: 136 °
• Алмазная пирамидка по Роквеллу: 120 °
• Шариковый по Роквеллу: 1/16 “, 1/8”, 1/4 “, 1/2”
• Вертикальный просвет рабочей области: 250 мм
• Горизонтальный просвет рабочей области: 200 мм от центральной линии
• Размеры (ШхГхВ): 290 мм x 588 мм x 845 мм
• Вес: 96 кг
• Требования к питанию: от 100 В до 240 В, 50/60Гц, однофазный
• 2 года гарантии
Варианты модификаций:
VERZUS 700RS (Роквелл/Супер-Роквелл) | Диапазон нагрузок от 1кгс/9.![]() |
VERZUS 700RSB (Универсальный твердомер по шкалам Роквелл/Супер-Роквелл, Бринелль, Виккерс, HVT, HBT) | Диапазон нагрузок от 1 кгс/9.8Н до 250 кгс/2.45кН |
VERZUS 700AS (Универсальный твердомер по шкалам Роквелл/Супер-Роквелл, Бринелль, Виккерс, HVT, HBT) | Диапазон нагрузок от 1 кгс/9.8Н до 250 кгс/2.45кН |
VERZUS 750RS (Твердомер Роквелл/Супер-Роквелл, HVT, HBT) | Диапазон нагрузок от 1 кгс/9.8Н до 187.5 кгс/1838Н |
VERZUS 750CCD (Универсальный твердомер по шкалам Роквелл/Супер-Роквелл, Бринелль, Виккерс, HVT, HBT) | Диапазон нагрузок от 1 кгс/9.8Н до 250 кгс/2.45кН |
Твердомер по Роквеллу, Бринеллю AFFRI RB-DRM
Твердомер находится в Реестре средств измерения Республики Беларусь.
Предназначен для проведения измерений по Роквеллу, Бринеллю. Твердомер оснащен жидкокристаллическим дисплеем, на котором отображается вся информация, полученная на протяжении всего измерительного цикла.
- Создаваемое динамометром усилие не требует использования гидравлического гасителя колебаний и противовесов
- Динамометр системы AFFRI позволяет оператору получать высокоточные измерения даже при условии, что машина находится в зоне вибрации
- С помощью твердомера можно контролировать качество материала в любой стадии процесса производства
- Понятное и простое в управлении программное обеспечение позволяет фиксировать и хранить полученные результаты, производить подсчет
- Возможность подсоединения твердомера к принтеру или компьютеру для передачи данных
- Установка специальных столиков позволяет производить тестирование как плоских, так и круглых образцов
|
Роквелл, Бриннель (Супер Роквелл по спец. |
|
(60-100-150кгс) 588-980-1471 Н (Роквэлл)
Супер-Роквелл.: (15 – 30 – 45 кгс) 147.1 – 294.2 – 441.3 Н |
|
Роквелл: HRC; HRA; HRB; Бринелль: HB Супер Роклвелл: HRN, HRT |
|
Автоматическое |
|
Роквелл: HRC: 20 до <=70 = ±1,5 HRA: 20-<=75 = ±2 >75 – <=88 = ±1,5 HRB: 20 – <=45 = ±4 >45 – <=80 = ±3 >80 – <=100 = ±2 Супер роквелл: HRN: ±1,5 HRT: ±2,5 HB:3% |
|
HB:12-497 HRC:2-68 HRA: 20-85,5 HRB:1-99 HRT:20-93 HRN:20:93 |
|
230В. 200VA |
|
+5-+50 С |
|
Нетто: 85 |
|
34х54х99 |
, калькулятор и тесты по Роквеллу, Бринеллю, Виккерсу и др.
Последние новости : Мы только что добавили новый замечательный калькулятор преобразования твердости в наше программное обеспечение G-Wizard.
Перейти к:
Таблица преобразования и калькулятор твердости
Твердость по Роквеллу
Твердость по Бринеллю
Твердость по Виккерсу
Определение твердости
Твердость – это мера того, насколько хорошо твердый материал сопротивляется постоянному изменению формы при приложении сжимающей силы. Твердость зависит от многих факторов, включая прочность межмолекулярных связей, пластичность, упругую жесткость, пластичность, деформацию, прочность, ударную вязкость и многие другие.
Испытания на твердость: измерение твердости
Обычно твердость измеряется тремя способами:
Устойчивость к царапинам
Скретч испытания твердости основан на идее о том, что более твердые материалы будут царапать более мягкие материалы.
Твердость вдавливания
Типичный твердомер…
меры твердости вдавливанием сопротивление образца к деформации из-за постоянной нагрузки на сжатие от острого предмета.После того, как испытуемый материал подвергается воздействию индентора со специальной нагрузкой и определенными размерами, размеры отпечатка, оставленного на испытуемом объекте, определяют твердость.
Это наиболее распространенный метод испытания на твердость, используемый для ЧПУ и механической обработки, и все шкалы твердости по Роквеллу, Виккерсу, Шору и Бринеллю основаны на твердости при вдавливании.
Твердость отскока
При измерениях твердости по отскоку высота «отскока» молотка с алмазным наконечником, падающего с фиксированной высоты на исследуемый материал, определяет его твердость.
Тест на твердость по Роквеллу (HR)
В испытании на твердость по Роквеллу (значения которого обозначаются аббревиатурой «HR») используется индентор с алмазным конусом или стальным шариком. Индентор вдавливается в исследуемый материал под незначительной нагрузкой, обычно 10 кгс. Когда достигается равновесие (т.е. при этой нагрузке не происходит дальнейшего вдавливания), устанавливается исходное положение. Применяется дополнительная большая нагрузка, увеличивающая проникновение. Удаление основной нагрузки в большинстве случаев приводит к незначительному восстановлению материала.Разница между вдавливанием после этого незначительного восстановления и исходным значением, установленным незначительной нагрузкой, может использоваться для расчета числа твердости по Роквеллу.
Различные шкалы твердости по Роквеллу различаются по типу индентора, а также по основной нагрузке:
Параметры испытаний для различных шкал твердости по Роквеллу…
Тест на твердость по Роквеллу удобно автоматизировать, но он страдает от множества произвольных масштабов и возможных эффектов от опорной наковальни для образца.Методы Виккерса и Бринелля не страдают от этого эффекта.
Испытание на твердость по Бринеллю (BHN)
Испытание на твердость по Бринеллю состоит из вдавливания в исследуемый материал шарика из закаленной стали или карбида диаметром 10 мм, подвергнутого нагрузке 3000 кг. Для более мягких материалов существуют альтернативные весы с нагрузкой 1500 или 500 кг, чтобы избежать чрезмерного вдавливания.
Полная нагрузка применяется в течение 10–15 секунд для чугуна или стали и не менее 30 секунд для других материалов.Диаметр оставшейся вмятины измеряется микроскопом с малым увеличением. Число твердости по Бринеллю может быть рассчитано по диаметру отпечатка. Среднее значение двух измерений, сделанных под прямым углом, используется для диаметра для обеспечения точности.
По сравнению с другими методами испытаний, шарик Бринелля делает самое глубокое и широкое вдавливание, поэтому результаты испытаний усредняют твердость на большей площади. Это может привести к более точным результатам при наличии нескольких структур зерен и других неоднородностей однородности материала.
Испытание на твердость по Виккерсу (HV)
В испытании на твердость по Виккерсу используется алмазный индентор в форме прямой пирамиды с квадратным основанием и углом 136 градусов между противоположными гранями. На индентор действует нагрузка от 1 до 100 кгс. полная нагрузка применяется в течение 10–15 секунд. Две диагонали, оставшиеся на поверхности материала, измеряются с помощью микроскопа и берется их среднее значение. Исходя из этого, рассчитывается площадь наклонной поверхности отпечатка, и на основании этого может быть определена твердость по Виккерсу.
Удивительно, но разные настройки нагрузки дают практически одинаковые числа твердости для однородного материала, что намного лучше, чем произвольное изменение шкалы с другими методами измерения твердости. Преимущества испытания на твердость по Виккерсу заключаются в том, что можно снимать чрезвычайно точные показания, и для всех типов металлов и обработки поверхностей используется только один тип индентора. Недостатком является то, что устройства, снимающие показания, представляют собой большие напольные устройства (не настольные) и стоят дороже, чем устройства Бринелля или Роквелла.
Прочие шкалы твердости
Шкалы твердости по Роквеллу, Бринеллю и Виккерсу являются наиболее распространенными шкалами твердости, но есть и другие:
– Береговой склероскоп
– Кнуп
– Leeb (HLD): Leeb – это испытание на твердость по отскоку, которое было разработано в 1975 году для обеспечения портативного испытания на твердость металлов.
– Твердость Янки: Янка используется исключительно для дерева, но может быть очень полезна при обработке дерева с ЧПУ.
Таблицы и калькулятор преобразования твердости G-Wizard
Наше программное обеспечение G-Wizard Calculator включает калькулятор преобразования твердости, потому что он имеет полный набор таблиц преобразования твердости и калькулятор, встроенный прямо на вкладке «Quick Refs»:
Калькулятор преобразования твердости по Роквеллу, Бринеллю, Виккерсу, склероскопу Шора и предел прочности на разрыв…
Калькулятор преобразования твердости особенно удобен.Введите значение «от», выберите единицы «от», введите единицы «до», и G-Wizard выдаст вам значение (если оно есть) в новых единицах твердости. Вот крупный план селектора единиц:
Вот еще кое-что – вы можете получить пожизненный доступ ко всем справочным калькуляторам и материалам, кроме калькулятора каналов и скорости, просто подписавшись на бесплатную пробную версию G-Wizard. Правильно, это совершенно бесплатно, чтобы получить доступ ко всему, просто подписавшись на бесплатную пробную версию, и вы также получите все обновления и обслуживание клиентов на всю жизнь! Кроме того, купите версию за 79 долларов, и вы получите до 1 HP на Feeds и Speeds на всю жизнь.
Так в чем же загвоздка? Почему кто-то платит больше 79 долларов?
Многие любители не платят больше 79 долларов, кстати. Загвоздка – это ограничение мощности шпинделя. При покупке G-Wizard на 1 год за 79 долларов вы получаете 1 год неограниченной мощности шпинделя для подачи и скорости. Когда это истечет, вы получите ограничение мощности шпинделя в 1 л.с. Это ограничение зависит от того, на сколько лет вы подписаны. Вы можете увеличить его в любое время, продлив подписку. Или, если вам не нравятся подписки, вы также можете напрямую использовать продукт.И мы никогда не взимаем плату за обновления или обслуживание клиентов.
Так что давай, дайте G-Wizard бесплатную пробную версию. Вы будете удивлены тем, сколько времени это сэкономит вам на таких вещах, как размеры сверл для метчика, не говоря уже о более длительном сроке службы инструмента, улучшенной чистоте поверхности и более коротком времени цикла, которые вы получите благодаря улучшенным подачам и скоростям.
Таблицы и таблицы преобразования твердости
Rockwell A | Роквелл В | Роквелл С | Роквелл D | Роквелл 15-Н | Rockwell 30-N | Rockwell 45-N | Brinell Std | Бринелл Халтгрен | Вольфрам Бринелля | Виккерс | Склероскоп Shore | Приблизительная прочность на разрыв (psi) |
85.6 | 68 | 76,9 | 93,2 | 84,4 | 75,4 | 1114 | 97 | |||||
85 | 67 | 76,1 | 92,9 | 83,6 | 74,2 | 1060 | 95 | |||||
84,5 | 66 | 75.4 | 92,5 | 82,8 | 73,3 | 1021 | 92 | |||||
83,9 | 65 | 74,5 | 92,2 | 81,9 | 72 | 739 | 940 | 91 | ||||
83,4 | 64 | 73,8 | 91.8 | 81,1 | 71 | 722 | 905 | 88 | ||||
82,8 | 63 | 73 | 91,4 | 80,1 | 69,9 | 705 | 867 | 87 | ||||
82,3 | 62 | 72,2 | 91,1 | 79.3 | 68,8 | 688 | 803 | 85 | ||||
81,8 | 61 | 71,5 | 90,7 | 78,4 | 67,7 | 670 | 775 | 83 | ||||
81,2 | 60 | 70,7 | 90,2 | 77,5 | 66.6 | 613 | 654 | 746 | 81 | 320000 | ||
80,7 | 59 | 69,9 | 89,8 | 76,6 | 65,5 | 599 | 634 | 727 | 80 | 310000 | ||
80,1 | 58 | 69,2 | 89,3 | 75,7 | 64,3 | 587 | 615 | 710 | 78 | 300000 | ||
79.6 | 57 | 68,5 | 88,9 | 74,8 | 63,2 | 575 | 595 | 694 | 76 | 2 | ||
79 | 56 | 67,7 | 88,3 | 73,9 | 62 | 561 | 577 | 649 | 75 | 282000 | ||
78,5 | 55 | 66.9 | 87,9 | 73 | 60,9 | 546 | 560 | 639 | 74 | 274000 | ||
78 | 54 | 66,1 | 87,4 | 72 | 59,8 | 534 | 543 | 606 | 72 | 266000 | ||
77,4 | 120 | 53 | 65,4 | 86.9 | 71,2 | 58,6 | 519 | 525 | 587 | 71 | 257000 | |
76,8 | 119 | 52 | 64,6 | 86,4 | 70,2 | 57,4 | 500 | 508 | 512 | 565 | 69 | 245000 |
76,3 | 119 | 51 | 63,8 | 85.9 | 69,4 | 56,1 | 487 | 494 | 496 | 551 | 68 | 239000 |
75,9 | 118 | 50 | 63,1 | 85,5 | 68,5 | 55 | 475 | 481 | 481 | 542 | 67 | 233000 |
75,2 | 118 | 49 | 62,1 | 85 | 67.6 | 53,8 | 464 | 469 | 469 | 534 | 66 | 227000 |
74,7 | 117 | 48 | 61,4 | 84,5 | 66,7 | 52,5 | 451 | 455 | 455 | 502 | 64 | 221000 |
74,1 | 117 | 47 | 60,8 | 83,9 | 65.8 | 51,4 | 442 | 443 | 443 | 489 | 63 | 217000 |
73,6 | 116 | 46 | 60 | 83,5 | 64,8 | 50,3 | 432 | 432 | 432 | 474 | 62 | 212000 |
73,1 | 115 | 45 | 59,2 | 83 | 64 | 49 | 421 | 421 | 421 | 460 | 60 | 206000 |
72.5 | 115 | 44 | 58,5 | 82,5 | 63,1 | 47,8 | 409 | 409 | 409 | 435 | 58 | 200000 |
72 | 114 | 43 | 57,7 | 82 | 62,2 | 46,7 | 400 | 400 | 400 | 423 | 57 | 196000 |
71.5 | 114 | 42 | 56,9 | 81,5 | 61,3 | 45,5 | 390 | 390 | 390 | 401 | 56 | 1 |
70,9 | 113 | 41 | 56,2 | 80,9 | 60,4 | 44,3 | 381 | 381 | 381 | 390 | 55 | 187000 |
70.4 | 112 | 40 | 55,4 | 80,4 | 59,5 | 43,1 | 371 | 371 | 371 | 385 | 54 | 182000 |
69,9 | 111 | 39 | 54,6 | 79,9 | 58,6 | 41,9 | 362 | 362 | 362 | 380 | 52 | 177000 |
69.4 | 111 | 38 | 53,8 | 79,4 | 57,7 | 40,8 | 353 | 353 | 353 | 361 | 51 | 173000 |
68,9 | 110 | 37 | 53,1 | 78,8 | 56,8 | 39,6 | 344 | 344 | 344 | 352 | 50 | 169000 |
68.4 | 109 | 36 | 52,3 | 78,3 | 55,9 | 38,4 | 336 | 336 | 336 | 335 | 49 | 165000 |
67,9 | 109 | 35 | 51,5 | 77,7 | 55 | 37,2 | 327 | 327 | 327 | 320 | 48 | 160000 |
67.4 | 108 | 34 | 50,8 | 77,2 | 54,2 | 36,1 | 319 | 319 | 319 | 312 | 47 | 156000 |
66,8 | 107 | 33 | 50 | 76,6 | 53,3 | 34,9 | 311 | 311 | 311 | 305 | 46 | 152000 |
66.3 | 106 | 32 | 49,2 | 76,1 | 52,1 | 33,7 | 301 | 301 | 301 | 291 | 44 | 147000 |
65,8 | 105 | 31 | 48,4 | 75,6 | 51,3 | 32,5 | 294 | 294 | 294 | 285 | 43 | 144000 |
65.3 | 105 | 30 | 47,7 | 75 | 50,4 | 31,3 | 286 | 286 | 286 | 278 | 42 | 140000 |
64,7 | 104 | 29 | 47 | 74,5 | 49,5 | 30,1 | 279 | 279 | 279 | 272 | 41 | 137000 |
64.3 | 103 | 28 | 46,1 | 73,9 | 48,6 | 28,9 | 271 | 271 | 271 | 261 | 41 | 133000 |
63,8 | 102 | 27 | 45,2 | 73,3 | 47,7 | 27,8 | 264 | 264 | 264 | 258 | 40 | 129000 |
63.3 | 101 | 26 | 44,6 | 72,8 | 46,8 | 26,7 | 258 | 258 | 258 | 250 | 38 | 126000 |
62,8 | 100 | 25 | 43,8 | 72,2 | 45,9 | 25,5 | 253 | 253 | 253 | 246 | 38 | 124000 |
62.4 | 99 | 24 | 43,1 | 71,6 | 45 | 24,3 | 247 | 247 | 247 | 240 | 37 | 121000 |
62 | 99 | 23 | 42,1 | 71 | 44 | 23,1 | 243 | 243 | 243 | 235 | 36 | 118000 |
61,5 | 98 | 22 | 41.6 | 70,5 | 43,2 | 22 | 237 | 237 | 237 | 226 | 35 | 115000 |
EngArc – L – твердость по Бринеллю и Роквеллу
EngArc – L – твердость по Бринеллю и РоквеллуТвердость по Бринеллю и Роквеллу |
Quick
Число твердости по Бринеллю – получено в результате испытания на твердость по Бринеллю с использованием приведенного ниже уравнения
Тест на твердость – измеряет устойчивость материала к проникновению острым предметом.Общие тесты включают, помимо прочего, тест Бринелля, тест Роквелла, тест Кнупа и тест Виккерса.
Уравнение
Ниже приводится уравнение для числа твердости по Бринеллю:
HB = |
|
где F – приложенная нагрузка в килограммах, D – диаметр индентора в миллиметрах, а D i – диаметр отпечатка в миллиметрах.
Детали
Тест на твердость измеряет сопротивление проникновению твердого предмета в поверхность материала. Было разработано множество тестов на твердость, но наиболее часто используемые – это тест Роквелла и тест Бринелля.
Что касается испытания на твердость по Бринеллю, твердый стальной шар (обычно диаметром 10 мм) вдавливается в поверхность материала. Диаметр оттиска, обычно от 2 до 6 мм, измеряется, и число твердости по Бринеллю (сокращенно HB или BHN) рассчитывается по приведенному выше уравнению.Число твердости по Бринеллю может быть получено всего за несколько минут практически без подготовки образца и без разрушения компонента, но оно обеспечивает близкое приближение к пределу прочности при растяжении.
| |||||
Тест Бринелля | Тест Роквелла |
В испытании на твердость по Роквеллу используется стальной шарик малого диаметра для мягких материалов и алмазный конус, или Brale, для более твердых материалов.Глубина проникновения индентора автоматически измеряется испытательной машиной и преобразуется в число твердости по Роквеллу (HR). Используются несколько вариантов теста Роквелла. Тест Rockwell C (HRC) используется для твердых сталей, тогда как тест Rockwell F (HRF) может использоваться для алюминия.
Числа твердости используются, прежде всего, в качестве основы для сравнения материалов, спецификаций для производства и термообработки, контроля качества и корреляции с другими свойствами материалов.Твердость хорошо коррелирует с износостойкостью. Материал, используемый для дробления или измельчения руды, должен быть очень твердым, чтобы гарантировать отсутствие эрозии или истирания материала твердыми исходными материалами. Точно так же зубья шестерни трансмиссии или системы привода транспортного средства должны быть достаточно твердыми, чтобы зубья не изнашивались. Обычно обнаруживается, что полимерные материалы исключительно мягкие, металлы имеют промежуточную твердость, а керамика – исключительно твердые.
Также испытания по Виккерсу (HV) и Кнупу (HK) относятся к испытаниям на микротвердость; они образуют такие маленькие углубления, что для проведения измерения требуется микроскоп.
Твердость по Роквеллу
Испытания твердости по Роквеллу описываются стандартным методом определения твердости ASTM E-18, измерения выполняются быстро и легко, они имеют хорошую воспроизводимость, а испытательная машина для них проста в использовании. Фактически, число твердости считывается прямо с циферблата. Шкалы твердости по Роквеллу обозначены как A , B , C , … и т. Д. Инденторы описываются как ромб, шарик диаметром 1/16 дюйма и ромб для шкал A , B и C соответственно, где прилагаемая нагрузка составляет 60, 100 или 150 кг.Таким образом, шкала Rockwell B , обозначенная как R B , использует нагрузку 100 кг и индентор № 2, который представляет собой шар диаметром 1/16 дюйма. В шкале Rockwell C R C используется алмазный конус, который является индентором № 1, и нагрузка 150 кг. Полученные таким образом числа твердости являются относительными. Следовательно, твердость R C = 50 имеет значение только по отношению к другому числу твердости с использованием той же шкалы.
Твердость по Бринеллю
Твердость по Бринеллю – еще один широко используемый тест.При испытании вдавливающий инструмент, через который прикладывается сила, представляет собой шарик, а показатель твердости H B определяется как число, равное приложенной нагрузке, деленной на площадь сферической поверхности вмятины. Таким образом, единицы измерения H B такие же, как единицы измерения напряжения, хотя используются редко. Проверка твердости по Бринеллю занимает больше времени, так как H B необходимо рассчитывать на основе данных испытаний. Основным преимуществом обоих методов является то, что они в большинстве случаев неразрушающие.Оба они эмпирически и напрямую связаны с пределом прочности испытуемого материала. Это означает, что при желании прочность деталей может быть проверена по частям в процессе производства.
Для сталей соотношение между минимальным пределом прочности и числом твердости по Бринеллю для 200 ≤ H B ≤ 450 составляет:
S u = 0,495 H B kpsi = 3,41 H B МПа
Аналогичные соотношения для чугуна могут быть получены из данных, предоставленных Krause.Данные 72 испытаний серого чугуна, произведенного на одном литейном заводе и разлитого в два размера испытательных стержней, представлены в виде графиков. Минимальная прочность, определенная ASTM, на основании этих данных составляет:
Eq1 S u = (0,23 H B – 12,5) kpsi = (1,58 H B – 86) МПа
Уолтон показывает диаграмму, по которой можно определить минимальную прочность по SAE. Результат:
S u = (0.2375 H B -16) тыс. Фунтов на кв. Дюйм
, что более консервативно, чем значения, полученные из уравнения 1.
Связанные
▪ L – Таблицы преобразования твердости по Бринеллю-Роквеллу: ссылка1, ссылка2
|
|
Магнитный твердомер по Бринеллю и Роквеллу – QualiMag-RB
Портативные твердомеры по Бринеллю и Роквеллу QualiMag-RB разработаны на основе твердомера Qualimag-R по Роквеллу и соответствуют методам испытаний твердомеров по Бринеллю и Роквеллу и работают как твердомеры по Бринеллю и Роквеллу. Портативные твердомеры по Бринеллю и Роквеллу QualiMag-RB используются для испытания отливок, поковок, сталей и цветных металлов, а также деталей, изготовленных из всех видов металлических материалов при различных видах термической обработки.Он способен испытывать готовые и полуфабрикаты металлических заготовок различных размеров и форм с использованием различных наковальней. Принцип и точность тестирования соответствуют соответствующему международному стандарту ISO 6508, 6506 и американскому стандарту ASTM E110.
Характеристики
- Используются для испытаний отливок, поковок, сталей и цветных металлов, а также деталей из всех видов металлических материалов в условиях термической обработки.
- Позволяет испытывать готовые и полуфабрикаты металлических заготовок различных размеров и форм с использованием различных наковален.
- Отслеживаемый стандартный блок твердости. Индентор проверяется стандартным твердомером по Роквеллу.
- Принцип и точность испытаний соответствуют международному стандарту ISO 6508, 6506 и американскому стандарту ASTM E110.
Технические характеристики
Арт. | Описание |
Начальная испытательная сила по Роквеллу | 10 кг |
Общее испытательное усилие по Роквеллу | 60 кг, 100 кг, 150 кг |
Испытательная сила Бринелля | 62.5 кг, 125 кг, 187,5 кг |
Индентор Роквелла | Индентор с алмазным конусом 120 °, шарик из твердого сплава 1,588 мм |
Тестовый шар Бринелля | Шарик из твердого сплава Ф2,5 мм |
Ошибка индикации | в соответствии с ISO и ASTM |
Ошибка повторяемости | в соответствии с ISO и ASTM |
Разрешение теста | Роквелл 0.5HR Brinell 0,005 мм (диаметр вдавливания) |
Испытательный полигон | Твердость по Роквеллу HRC, HRB, HRA |
Диапазон применения | Rockwell для изделий или полуфабрикатов из обычных металлов, включая сталь, медь, алюминий, науглероженный слой, твердый сплав и т. Д. Бринелль для отливок, поковок, стального сырья, цветных металлов |
Переуступка
ПереуступкаФормулы преобразования твердости для стали
Для 10Роквелла – Бринелля (ожидаемая ошибка +/- 10%)
из «Испытания на твердость при вдавливании» автор В.Э. Лисахт, стр.134Для 40Для 30Бринелля = 7300 / (130 – Роквелл B)
по Бринеллю = 3710 / (130 – Роквелл E)
Бринелля = (1520000 – 4500 C по Роквеллу) / (100 – C по Роквеллу) 2
Для 40Бринелля = (25000 – 10 (57 – Роквелл C) 2 ) / (100 – Роквелл C) 2
От твердости до предела прочности (ожидаемая погрешность +/- 15%)
из «Испытания на твердость при вдавливании»
автор В.Э. Лисахт, стр.134
Для 82Для 10Предел прочности на разрыв (psi) = (4750000 – 12000 Rockwell B) / (130 – Роквелл B)
Предел прочности на разрыв (psi) = 10 5 (7000-10 Rockwell C) / (100 – Роквелл С) 2
Для Бринелля <175Для Бринелля> 175Предел прочности на разрыв (psi) = 515 по Бринеллю
Предел прочности на разрыв (фунт / кв. Дюйм) = 490 по Бринеллю
Глубина проникновения до твердости
от
«Испытание на твердость по Роквеллу» Д.К. Ван Акен
Rockwell B = 130 – глубина проникновения (мм) / 2 ммRockwell C = 100 – глубина проникновения (мм) / 2 мм
Rockwell Test – обзор
2.1 Факторы, влияющие на выбор испытаний на твердость
Выбор конкретного метода испытаний для определения твердости определяется несколькими факторами.К ним относятся: размер и форма заготовки, степень плоскостности заготовки, диапазон твердости испытуемого материала, состояние поверхности заготовки, характер испытуемого материала (однородный или неоднородный), влияние следов вдавливания, количество идентичных деталей, подлежащих испытанию, и доступность оборудования.
Для выбора наиболее подходящего метода испытаний важно иметь некоторое представление о диапазоне твердости испытываемого материала.В большинстве случаев обоснованное предположение может быть сделано на основе состава материала, маршрута обработки (прокат, ковка, литье, поверхностная закалка, детали порошковой металлургии и т. Д.) И применяемой термической обработки. Идеальная форма заготовки для испытания на твердость – это квадратный блок достаточного размера, чтобы можно было сделать требуемый вид вдавливания. Иногда идеальных форм не существует. Поэтому при испытаниях по Роквеллу и Бринеллю рекомендуется использовать различные наковальни. Как правило, обычные тесты Бринелля и Роквелла не рекомендуются, если размер заготовки превышает 16 кг.Портативные методы, такие как склероскоп и ультразвуковое тестирование, могут использоваться для тестирования крупных компонентов на месте. В этих методах правильное состояние поверхности имеет решающее значение для получения точных результатов. Многие методы испытаний очень чувствительны к плоскостности образца. Чтобы получить точные показания с помощью приборов Бринелля, Роквелла, склероскопа и обычных микротвердомеров, тестируемая поверхность должна иметь плоскостность, по крайней мере, в пределах 2–3 °, то есть около 90 ° от направления движения индентора.Регулируемые приспособления часто используются для приведения плоской поверхности в нужное положение. Необходимость регулярных испытаний ряда таких же больших и тяжелых деталей также может повлиять на выбор методов и приемов испытаний. Степень гладкости поверхности, необходимая для получения точных результатов, напрямую зависит от размера индентора. Хотя более гладкая поверхность очень желательна для любого метода тестирования, тест Бринелля, который включает в себя большое вдавливание, может быть проведен и считан с разумной степенью точности, когда покрытие сопоставимо с типами чистовой обработки или грубой шлифовки.При испытаниях по Роквеллу предпочтительны полированные поверхности. При испытаниях по Виккерсу и склероскопу требования к отделке намного более жесткие и требуют отделки поверхности, эквивалентной той, которая используется для микроскопических исследований при большом увеличении. Следы, оставленные при испытании на твердость вдавливанием, могут варьироваться от диаметра> 4 мм, как в испытании Бринелля, до микроскопических следов, оставшихся после испытания на микротвердость при малой нагрузке. Испытания по Бринеллю приводят к появлению больших вмятин, которые могут выступать в качестве участков для зарождения трещин.Следы, оставленные склероскопом или микротвердомерами на готовом продукте, обычно не вызывают возражений.
Твердомеры по Роквеллу следует регулярно проверять по калиброванной стороне стандартных испытательных блоков, чтобы обеспечить калибровку испытательной машины и оценить повреждение индентора (если таковое имеется). Инденторы проверяются с помощью теневого графа или аналогичного инструмента, который легко обнаруживает недостатки. Не следует использовать дефектный индентор. Правильная проверка тестера предполагает как минимум пять считываний; среднее значение должно находиться в пределах допусков, нанесенных на стороне испытательного блока, чтобы гарантировать, что тестер находится в процессе калибровки.Если среднее значение пяти показаний выходит за эти пределы, следует отметить разницу между этим средним значением и средним значением блока испытаний. Эта ошибка может быть временно компенсирована при оценке результатов. Однако дальнейшая компенсация неисправности тестера не допускается.
Национальный институт стандартов технологий (NIST) прилагает значительные усилия для установления стандартов для испытаний на твердость и для обеспечения большей совместимости стандартов США со стандартами, используемыми в других частях мира (Ellis 1998).Хотя испытание на твердость по Роквеллу основано на отслеживаемых параметрах, значения твердости сами по себе в настоящее время являются эмпирическими. Чтобы сделать значения твердости более абсолютными, необходимо разработать согласованные стандарты с международным участием. Первичные блоки, соответствующие требованиям NIST, были изготовлены и откалиброваны с использованием первичного грузопоршневого манометра. Новые блоки, отслеживаемые NIST, имеют гораздо более жесткие допуски (до 0,1) по сравнению с тестовыми блоками HRC Rockwell типа ASTM. Три значения твердости охватываются 300 стандартными эталонными материалами (SRM), выпущенными NIST на данный момент, т.е.е., 63 HRC, 45 HRC и 25 HRC. Другие типы тестовых блоков для Роквелла и других методов могут быть предоставлены NIST в будущем. NIST SRM доступны только по практически непомерно высокой цене, и аккредитованные NIST поставщики работают над производством вторичных тестовых блоков с использованием вторичных машин и измерений на основе первичных блоки. Стандартизация инденторов NIST не продвигается необходимыми темпами из-за отсутствия соглашения о том, как измерить геометрию алмаза. Однако для проверки индентора можно использовать стандарт ASTM E 18.Инденторы должны отправляться пользователями своему поставщику каждые два года для повторной аккредитации, которая основывается на размерной проверке. Переписывание ASTM E 18 продолжается. Страны с лабораториями, занимающимися разработкой испытаний на твердость, включают: Япония (Национальная исследовательская лаборатория метрологии, NRLM), Германия (Materialprüfungsanstalt, MPA), Италия (Институт метрологии, IMGC), Великобритания (NAMAS), Китай (Национальный институт метрологии, NIM), Австралии и Бразилии.
Испытание на твердость неоднородных материалов, таких как чугун, твердые сплавы и детали порошковой металлургии, представляет несколько трудностей.Измерения твердости серого чугуна отражают композитные значения материала матрицы и графита; эти значения меньше, чем у материала матрицы. Для большинства типов чугуна твердость матрицы более точно определяется испытаниями по Бринеллю, чем испытаниями Роквелла, хотя оба требуют корректировки для получения истинной твердости матрицы. Тест на микротвердость – самый точный метод определения твердости чугуна. На рисунке 1 показана взаимосвязь между наблюдаемыми показаниями HRC и значениями микротвердости для различных серых чугунов с различными углеродными эквивалентами.Эквивалент углерода (CE) = Общий углерод + (% Si +% P) / 3. Разница между измеренными и рассчитанными значениями микротвердости уменьшается по мере уменьшения эквивалента CE и сужается при более низких уровнях твердости. Прежде чем использовать таблицу преобразования для определения точных результатов, необходимо знать CE проверяемого чугуна. Детали из порошковой металлургии (P / M) демонстрируют более широкие вариации при испытаниях на твердость по сравнению с деформируемыми аналогами. Проникновение индентора в поры и группы пор, присутствующие в деталях из P / M, приводит к этому изменению.В таких случаях следует снять не менее пяти последовательных измерений; Кроме того, следует отбросить любые высокие или низкие показания. Из-за разнообразия составов и плотностей, встречающихся в частях P / M, рекомендации по подходящим методам испытаний являются трудными, но испытание по Роквеллу с различными масштабами является предпочтительным методом. Микротвердость пористых материалов может быть измерена инденторами Кнупа или алмазной пирамиды при нагрузках 100 г и более. Индентор Кнупа является предпочтительным, потому что он делает неглубокую выемку и не нарушается, проникая в нераскрытые поры, в то время как инденторы в форме алмазной пирамиды часто встречаются со скрытыми порами.Испытания на микротвердость и измерение эффективной глубины корпуса покрываются стандартом MPIF 37 Федерации металлической порошковой промышленности (MPIF).
Рис. графит типа 3 (воспроизведено с разрешения Американского общества металлов из Справочник по металлам , 9-е изд. Введение в термообработку чугунов, Термическая обработка , 1981, Vol.4, стр. 527).
Проверка твердости пластиков (полимеров) – сложная задача. Поскольку деформация пластмассы зависит от времени, а при испытании на твердость под нагрузкой пластмассовый материал продолжает течь, фактор времени необходимо учитывать на разных этапах испытаний. Основным стандартом является ASTM D 785. Вариант стандартного теста Роквелла – альфа-число твердости по Роквеллу в процедуре B стандарта ASTM D 785 – часто используется для тестирования пластмасс. Твердомер довольно часто используется для измерения твердости практически всех типов пластиков, каучуков и резиноподобных материалов.Несколько типов твердомеров подходят для всего диапазона твердости, в то время как специальные инструменты доступны для тестирования уплотнительных колец и очень тонких материалов. Некоторые твердомеры описаны в стандарте ASTM D 2240.
Испытания керамики на твердость проводились поверхностными методами по Виккерсу, Кнупу и Роквеллу (Quinn 1998). Твердость по Кнупу чаще упоминается в США, чем где-либо в мире, из-за наличия стандартов ASTM C730 для стеклокерамики, C849 для керамических изделий белого цвета и C1326 для современной керамики с 9.8 Н (1 кгс). При низких нагрузках вдавливания проблемы возникают из-за зависимости твердости от нагрузки и погрешности измерения из-за небольшого размера вдавливания. При более высоких нагрузках возникают проблемы с растрескиванием и отслаиванием; в некоторых случаях эти проблемы делают невозможным достоверное измерение. Эффект размера вдавливания, при котором твердость уменьшается с увеличением нагрузки вдавливания, обнаруживается как для твердости по Кнупу, так и по Виккерсу. Постоянная твердость достигается при нагрузках от 5 до 100 Н в зависимости от керамики. На рис. 2 показаны некоторые из распространенных серьезных проблем, связанных с измерением твердости керамики.В случае керамики заметная погрешность может быть вызвана малейшим ударом о твердомер или стол, на который он был помещен, когда индентор находится в контакте с образцом. кончик кончика – и слишком часто определение размера отступа становится неточным. Кроме того, поскольку твердость обратно пропорциональна квадрату диагональной длины отпечатка, любая ошибка измерения длины удваивается. Для данной нагрузки в керамике развиваются сравнительно меньшие диагонали, чем в большинстве металлов; это увеличивает неопределенность измерения.Исследование, спонсируемое циклическим проектом Versailles Advanced Materials and Standards (VAMAS), показало, что различия в воспроизводимости значений твердости керамики могут достигать 15%. Чтобы получить оптимальные результаты, вдавливание должно быть больше микроструктурных элементов, и предпочтительно использовать 10 или более вдавливаний хорошей геометрии для разумной надежности. Предварительный стандарт Европейского комитета по стандартизации (CEN), CEN ENV 843-3, имеет методы твердости по Кнупу и Виккерсу, а также шкалы А и N по Роквеллу.Стандарт твердости керамики ISO, разрабатываемый Техническим комитетом TC 206 Fine ceramics, будет включать твердость как по Кнупу, так и по Виккерсу.
Рис. 2. Проблемы, связанные с испытанием твердости керамики, включая (а) метод перекрестия, (б) растрескивание вдавливания, (в) влияние размера вдавливания, (г) удар или вибрацию, (д) пределы оптического разрешения (воспроизведено с разрешения [ правообладатель] из Adv. Mater. Processes , 1998, 154 , 23–7).
Encore Metals – Преобразование твердости
Преобразование твердости
Приблизительные соотношения между твердостью по Бринеллю, Роквеллу, Шору, Виккерсу и Фирту и пределом прочности на разрыв S.Углеродистые и легированные конструкционные стали A.E.
С | А | 15-Н | 30-Н | ВИКЕРС | КНООП | BRINELL | |
150 кг Брайе | 60 кг Брайе | 16 кг N Braie | 30 кг N Braie | 10 кг 136 * Алмаз | 500 гр. и старше | 3000 кг 10 мм Шарик | Прибл. Прочность на растяжение Прочность тысяч фунтов / кв. Дюйм |
Роквелл | Rockwell Поверхностное | Роквелл | Роквелл | Виккерс | Кнуп | Бринелл ** (Стандартный шар) | |
68 67 66 65 64 | 85.6 85,0 84,5 83,9 83,4 | 93,2 92,9 92,5 92,2 91,8 | 84,4 83,6 82,8 81,9 81,1 | 940 900 865 832 800 | 920 895 870 846 822 | – – – – – | неточный и только для сталь |
63 62 61 60 59 | 82.8 82,3 81,8 81,2 80,7 | 91,4 91,1 90,7 90,2 89,8 | 80,1 79,3 78,4 77,5 76,5 | 772 746 720 697 674 | 799 776 754 732 710 | – – – – – | 351 |
58 57 56 55 54 | 80.1 79,6 79,0 78,5 78,0 | 89,3 88,90 88,3 87,9 87,4 | 75,7 74,8 73,9 73,0 72,0 | 653 633 613 595 577 | 690 670 650 630 612 | 615 595 577 560 543 | 338 325 313 301 292 |
53 52 51 50 49 | 77.4 76,8 76,3 75,9 75,2 | 86,9 86,4 85,9 85,5 85,0 | 71,2 70,2 69,4 68,5 676,6 | 560 544 528 513 498 | 594 576 558 542 526 | 525 512 496 481 469 | 283 273 264 255 246 |
48 47 46 45 44 | 74.7 74,1 73,6 73,1 72,5 | 84,5 83,9 83,5 83,0 82,5 | 66,7 65,8 64,8 64,0 63,1 | 484 471 458 446 434 | 510 495 480 466 452 | 451 442 432 421 409 | 238 229 221 215 208 |
42 40 38 36 34 | 71.5 70,4 69,4 68,4 67,4 | 81,5 80,4 79,4 78,3 77,2 | 61,3 59,5 57,7 55,9 54,2 | 412 392 372 354 336 | 426 402 380 360 342 | 390 371 353 336 319 | 194 182 171 161 152 |
32 30 28 26 24 22 20 | 66.3 65,3 64,3 63,3 62,4 61,5 60,5 | 76,1 75,0 73,9 72,8 71,6 70,5 69,4 | 52,1 50,4 48,6 46,8 45,0 43,2 41,5 | 318 302 286 272 260 248 238 | 326 311 297 284 272 261 251 | 301 286 271 258 247 237 226 | 146 138 131 125 119 115 110 |
B 100 кг Шар 1/16 “ | F 60 кг Шар 1/16 “ | 30-T 30 кг Шар 1/16 “ | A 60 кг и старше | Knoop 500 Gr. | Br’L 3000 кг | Предел прочности |
Брей | Брей | Брей | Брей | Шарик 10 мм | Тысяч фунтов. | |
Роквелл | Роквелл | Rockwell Поверхностное | Роквелл | Кнуп | Бринелл | за кв.дюйм |
100 99 98 97 96 | – – – – – | 83,1 82,5 81,8 81,1 80,4 | 61,5 60,9 60,2 59,5 58,9 | 251 246 241 236 231 | 240 234 228 222 216 | 116 114 109 104 102 |
95 94 93 92 91 | – – – – – | 70.8 79,1 78,4 77,8 77,1 | 58,3 57,6 57,0 56,4 55,8 | 226 221 216 211 206 | 210 205 200 195 190 | 100 98 94 92 90 |
90 89 88 87 86 | – – – – – | 76.4 75,8 75,1 74,4 73,8 | 55,2 54,6 54,0 53,4 52,8 | 201 196 192 188 184 | 185 180 176 172 169 | 89 88 86 84 83 |
85 84 83 82 81 | – – – – – | 73.1 72,4 71,8 71,1 70,4 | 52,3 51,7 51,1 50,6 50,0 | 180 176 173 170 167 | 165 162 159 156 153 | 82 81 80 77 73 |
80 79 78 77 76 | – – – – – | 69.7 69,1 68,4 67,7 67,1 | 49,5 48,9 48,4 47,9 47,3 | 164 161 158 155 152 | 150 147 144 141 139 | 72 70 69 68 67 |
75 74 72 71 68 | 99,6 99,1 98,0 96,8 95,6 | 66.4 65,7 64,4 63,1 61,7 | 46,8 46,3 45,3 44,3 43,3 | 150 147 143 139 135 | 137 135 130 125 121 | 66 65 63 61 59 |
66 64 62 60 58 | 94,5 93,4 92,2 91,1 90,0 | 60.4 59,0 57,7 56,4 55,0 | 42,3 41,4 40,4 39,5 38,6 | 131 127 124 120 117 | 117 114 110 107 104 | Даже для стали отношение прочности на разрыв к твердости является неточным , если не определено для конкретного материала . См. ASTM A370 |
56 54 52 50 48 | 88.8 87,7 86,5 85,4 84,3 | 53,7 52,4 51,0 49,7 48,3 | 37,7 36,8 35,9 35,0 34,1 | 114 111 109 107 105 | 101 * 87 * 85 * 83 * 81 | |
46 44 42 40 38 | 83,1 82,0 80,8 79,7 78,6 | 47.0 45,7 44,3 43,0 41,6 | 33,3 32,4 31,6 30,7 29,9 | 103 101 99 97 95 | * 79 * 78 * 76 * 74 * 73 | |
36 34 32 30 | 77,4 76,3 75,2 74,0 | 40,3 39,0 37,6 36,3 | 29,1 28.2 27,4 26,6 | 93 91 89 87 | * 71 * 70 * 68 * 67 |
Все значения относительной твердости на этой карточке являются средними значениями испытаний на различных металлах, различные свойства которых не позволяют установить точные математические преобразования. Эти значения соответствуют таблицам 1 и 2 ASTM E 140 для неаустенитных сталей. Перед интерпретацией значений преобразования твердости рекомендуется ознакомиться со стандартами ASTM E 140, E 10, E18, E92, E110, E384 и A 370 (включая испытания на твердость металлов).
* Тесты по Бринеллю 101 проводились с использованием всего лишь 500 кг иода и 10-миллиметрового шара.
** Вышеупомянутые испытания Brinell 451 HB проводились с твердосплавным шариком 10 мм.
.