Серебрение в домашних условиях с помощью анода и катода: ТОП-10 способов посеребрить металл электролитом или провести химическое серебрение с помощью анода и катода дома
alexxlab | 26.01.1992 | 0 | Разное
Как серебрить провода? (часть 2) / Хабр
В предыдущей статье я написал о том, зачем нужны покрытия из драгметаллов в электронной технике. И пообещал, что в следующей публикации раскрою некоторые технологические секреты. Выполняю это обещание. Статья эта посвящена тому, как в домашних условиях нанести серебро на те или иные изделия.
Народные рецепты и их разоблачение
Всякого рода народных рецептов серебрения уйма. Радиолюбители их часто применяют по причине того, что свято верят в полезность серебрения для добротности контуров, стабильности их частоты и т.д. Ну и “раз в военной технике так делали, значит и нам так надо”. О полезности этого в реальности я писал в предыдущей статье.
Пожалуй, лучшим из этих рецептов был такой:
Возьмите отработанный фиксаж и погрузите в него лист засвеченной фотобумаги. Подержав фотобумагу несколько минут, чтобы эмульсионный слой размок, достаньте его из раствора и натирайте им поверхность зачищенного до блеска медного предмета (например, проволоки) до тех пор, пока вся она не покроется равномерным блестящим слоем серебра.
Я этот рецепт опробовал. Он работает, хотя и дает очень тонкое серебряное покрытие. Беда же в том, что вряд ли он способен понизить поверхностное сопротивление и не способен предотвратить окисление меди. Причиной этому является малая толщина и высокая пористость таких покрытий и сильное их загрязнение серой. Это с одной стороны резко снижает проводимость такого серебра, с другой — повышает его химическую активность. Такое серебрение даже паяется неважно, и таким образом, пригодно лишь для серебрения блесен.
Все же этот рецепт — действительно лучший. Он единственный, который дает плотное сцепление серебряного осадка с медью. Но для электроники — бесполезный.
Остальные же, основанные на использовании того же тиосульфатного комплекса (он же — отработанный фиксаж) дают слой, плохо сцепленный с медью и стирающийся даже пальцами.
Некоторые источники предлагают не использовать отработанный фиксаж и засвеченную фотобумагу, а взять нитрат серебра, добавить туда хлорид натрия, отделить осадок хлорида серебра и добавить туда тиосульфат натрия в недостатке (чтобы не произошло полного растворения хлорида серебра), и смешав полученную суспензию с порошком мела, натирать им медный предмет. Суть примерно та же самая, результат тот же.
Рабочий вариант народного рецепта
На самом деле, в данный рецепт нужно внести всего одно изменение — и он превратится в полезный. Нужно убрать из него тиосульфат. Взамен в качестве комплексообразователя вводится винная кислота или ее соль, какой-нибудь хлорид и аммиак, либо хлорид аммония. Рецепт не моего изобретения, но он почему-то малоизвестен. Итак:
Взять 6 г хлорида серебра и добавить к нему 8 г хлорида натрия и 8 г тартрата натрия. Эту смесь перетереть в ступке до однородности. В таком виде ее можно хранить в темноте. Перед использованием к смеси добавляют несколько капель водного аммиака и растирают до состояния пасты. Этой пастой натирают зачищенную до блеска поверхность меди, что приводит к образованию тонкого, но плотного слоя серебра. Этот слой способен защищать медь от окисления и долго сохраняется в среде, не содержащей сероводорода. Покрытие это обладает также хорошей проводимостью и великолепно паяется, так как не загрязнено серой. Более толстое покрытие может быть получено, если предварительно нагреть изделие и пасту до температуры 60-80°С.
Электроосаждение серебра
Электрохимическое осаждение серебра позволяет получить плотные, хорошо электропроводные осадки практически произвольной толщины. Однако в домашних условиях реализовать эту технологию затруднительно. Причиной является то, что качественное серебрение удается провести лишь в электролитах, содержащих цианид-ион, что предопределяет чрезвычайную опасность работы.
Типичный состав электролита для серебрения такой:
10 г хлорида серебра,
40 г цианида калия
40 г бикарбоната натрия
15 г хлорида натрия
70 мл водного аммиака
Вода до 1 л.
Уже страшно? Лично мне да. Я за такую работу не возьмусь даже у себя в лаборатории под тягой и т.д, пока не получу письменное распоряжение от завлаба и не приму все меры безопасности, которые положены при работе с цианидами.
Есть рецепты, в которых цианид замаскирован. Он не вводится в виде цианистого калия или натрия, а образуется при разложении желтой кровяной соли:
40 г хлорида серебра,
20 г гексациано(II)феррата калия (желтой кровяной соли),
30 г карбоната натрия (кальцинированной соды),
Вода до 1 л.
Преимущество одно: при приготовлении мы не контактируем с “живым” цианидом. Но в растворе он все равно есть и раствор опасен для жизни. Кроме того, железо осаждается вместе с серебром, ухудшая его проводимость.
Я даже не указываю плотности тока для этих электролитов. Я их не пробовал и вам не советую. А советую попробовать электролит, опробованный мной и не содержащий цианидов ни в чистом виде, ни в виде комплексных солей. Состав его такой:
6 г йодида серебра,
40 г йодида натрия или эквивалентное по молям к-во йодида калия ,
1-5 г поливинилового спирта,
Вода до 100 мл
Сначала растворяют йодид натрия в воде. В полученном растворе растворяют йодид серебра, при этом образуется комплексная соль Na2AgI3. В конце вносят поливиниловый спирт. Плотность тока 0,3-1 А/дм2 при комнатной температуре. Анод — серебро. В процессе электролиза цвет раствора становится желтым из-за выделяющегося йода. Это нежелательное явление, так как йод реагирует с серебром, загрязняя его слой. Для предотвращения этого нужно по мере пожелтения раствора вводить в него понемногу раствор тиосульфата натрия до исчезновения окраски. Избыток вводить не следует, так как сера в серебре тоже не нужна. Благодаря поливиниловому спирту, осадок получается блестящий. Исключать его не следует, так как без него покрытие получается не просто матовое, а рыхлое. Получить матовое, но плотное покрытие можно добавлением полиэтиленполиамина (отвердитель для эпоксидной смолы), имея в виду его ядовитость.
Есть еще пирофосфатный электролит, мною он был также опробован, но он малоустойчив, требует предварительного серебрения и практически не имеет рассеивающей способности — то есть покрывает серебром катод только со стороны анода.
Вжигание серебра
Этим способом можно получить покрытие из серебра на термостойком стекле или керамике — например, чтобы изготовить термостабильную катушку. Делается вжигание путем нанесения серебросодержащей пасты (это можно делать кистью, через трафарет или иным способом, чтобы получить нужную конфигурацию проводников) на подложку. Пасту можно сделать самостоятельно по следующему рецепту:
Карбонат серебра — 4 вес. ч
Канифоль — 1 в.ч.
Спирт — до нужной консистенции.
Карбонат серебра получается следующим образом: в затемненном помещении (полной темноты не нужно, не должно быть яркого света) к раствору нитрата серебра, взятого в том же количестве, что нужно получить карбонат серебра, и растворенного в 30-50 мл дистиллированной воды в большом стакане, приливается насыщенный раствор бикарбоната натрия. При этом выделяется углекислый газ и образуется много пены, и выпадает желтый осадок, темнеющий на свету. После прекращения выделения газа добавление раствора нужно прекратить и поставить стакан в темное место отстаиваться на 2-3 часа, затем в максимальной степени слить жидкость (осторожно, не взмучивая осадок). После этого осадок следует промыть три раза дистиллированной водой, заливая его ею и давая отстояться, а затем сливая. Далее осадок нужно высушить до сухого состояния в темном месте при комнатной температуре.
Далее порошок карбоната серебра нужно смешать с порошком канифоли и добавить спирт. Паста готова. Использовать ее нужно сразу.
Пасту нужно наносить тонким, но плотным, не просвечивающим слоем, для этого она должна быть достаточно жидкой. В процессе нанесения ее нужно перемешивать, так как она быстро оседает. Лучше, чтобы поверхность, на которое наносится паста, была матовой, шлифованной. Затем изделие с нанесенной пастой помещают в муфельную печь и медленно нагревают от комнатной температуры до 200°С — со скоростью не больше 20°С/час. Дальше можно греть быстрее, и в итоге нужно достигнуть температуры около 800°С (если подложка не позволяет, можно остановиться на 600°С, но качество покрытия и его проводимость будет хуже). Затем при этой температуре нужно выдержать изделие в течение 6-8 часов и выключить печь, дав ей остыть вместе с изделием.
Покрытие получается очень плотное, хорошо проводящее ток и прочно сцепленное с подложкой и выдерживающее пайку мягкими припоями.
Гальваническое меднение металла | Механизмы процесса, методы
Фазлутдинов К.К.
18.05.2015 (обновленно 11.05.2021)
13970 просмотров
Содержание:
1. Что такое меднение? Назначение и обозначение медного покрытия.
2. Кинетика процесса гальванического меднения.
1. Что такое меднение? Назначение и обозначение медного покрытия.
Меднение — процесс нанесения тонкого слоя металлической меди на изделие для придания ему необходимых свойств.
Медные покрытия широко применяются в основном в качестве подслоя при нанесении многослойных покрытий, а также для улучшения пайки, создания электропроводных слоёв, уплотнения резьбовых соединений, местной защиты стальных деталей при цементации. В редких случаях используются для придания декоративного внешнего вида.
Медь — металл розового цвета с атомной массой 63,5, плотностью 8,9 г/см3, температурой плавления 1083°С, удельным электросопротивлением 0,017*Ом*мм. Медь пластична, твердость медных покрытий 2500-3000 МПа.
Медь интенсивно растворяется в аэрированных аммиачных и цианидных растворах, азотной кислоте, медленнее – в хромовой, слабо – в серной и почти не взаимодействует с соляной кислотой. На воздухе медь легко реагирует с влагой, углекислыми и сернистыми соединениями, окисляется и темнеет.
Стандартный потенциал меди по отношению к ее одновалентным нонам +0,52 В, двухвалентным ионам +0,34 В.
В жестких условиях эксплуатации медь и ее сплавы не должны контактировать с хромом, оловом, сталями, цинком, кадмием, алюминием и магнием.
Характеристики медного покрытия
Обозначение покрытия |
М – стандартное меднение, блеск не нормируется М. М24 – искровзрывозащитное меднение (толщина не менее 24мкм) М. ч – меднение с декоративным чернением (состариванием/патинированием) galvanic copper plating – англ. обозначение |
Толщина |
6-100мкм (оптимально, но возможно осадить большую толщину) |
Микротвердость |
590-1470 МПа (60-150 кгс/мм2) |
Удельное электрическое сопротивление при 18°C |
1,68⋅10-8 Ом⋅м |
Допустимая рабочая температура |
300°C
|
2. Кинетика процесса гальванического меднения.
Для электролитического осаждения меди разработано большое количество электролитов, которые, обычно, разделяют на две группы: кислые и щелочные. Существуют как простейшие, так и достаточно сложные композиции для меднения.
Катодные поляризационные кривые для некоторых из них приведены на рисунке 1.
Рисунок 1 — Катодные поляризационные кривые при меднении из электролитов: 1 — сульфатный; 2 — пирофосфатный; 3 — цианидный ; 4 — цианидный с повышенным содержанием свободных цианидов.
2.1 Процессы в кислых электролитах меднения.
К кислым электролитам относятся сульфатные и фторборатные электролиты. Их основные достоинства – простота состава и устойчивость в эксплуатации, но они обладают низкой рассеивающей способностью. Также из них невозможно непосредственно меднить сталь из-за выпадения контактной меди, а, следовательно, плохое сцепление со сталью слоя меди. Вследствие этого меднение осуществляется после предварительного осаждения медного слоя (3-4 мкм) из щелочных электролитов или после осаждения никелевого слоя (3-5 мкм).
Из кислых электролитов наиболее распространен сульфатный электролит. Основными компонентами сульфатных электролитов являются сульфат меди и серная кислота. Электропроводность нейтральных растворов сульфата меди невелика, поэтому в них добавляют серную кислоту, которая значительно повышает электропроводность растворов температуры перемешивания.
Предполагается, что на катоде разряд двухвалентных ионов меди протекает в две стадии:
Cu2+ + e → Cu+
Cu+ + e → Cu
Замедленной стадией является первая реакция. Доля каждой стадии в общей кинетике меднения зависит от состава электролита и режима электролиза: плотности тока, температуры, перемешивания.
Выход меди по току около 100 %, так как выделения водорода на катоде не происходит, поскольку потенциалы выделения меди имеют более положительные значения, чем потенциалы выделения водорода.
Повышение кислотности электролита способствует уменьшению растворимости сульфата меди, что приводит к снижению верхнего предела допустимой плотности тока. Для увеличения концентрации ионов меди в катодном слое применяют перемешивание. В этом случае кислотность электролитов можно увеличивать. Чем интенсивнее перемешивание, тем выше может быть содержание серной кислоты. Повышение температуры способствует увеличению растворимости сульфата меди: при 25 °С — 23,05 г CuSO4 на 100 г воды; при 100 °С — 73,6 г. Повышенная кислотность способствует получению более мелкокристаллических осадков.
Вблизи анодов наряду с ионами Cu2+ в растворе могут находиться в незначительном количестве ионы одновалентной меди, образующиеся в результате протекания реакции:
Cu + Cu2+ ↔ 2Cu+
При накоплении в растворе ионов Cu+ равновесие будет сдвигаться влево, и металлическая медь будет выпадать в виде осадка.
При недостаточной кислотности раствора сульфат одновалентной меди будет гидролизоваться с образованием Сu(ОН)2 или СuО2
Cu2SO4 + H2O ↔ Cu2O + H2SO4
В результате в электролите будут взвешенные частицы металлической меди и оксида меди, которые, включаясь в катодный осадок, делают его темным, шероховатым, а иногда – рыхлым.
Присутствие серной кислоты способствует протеканию реакций окисления одновалентной меди:
Cu2SO4 + H2SO4 + 1/2О2 → 2CuSO4 + Н2О
Cu2O + 2H2SO4 + 1/2O2 → 2CuSO4 + 2H2O
Таким образом, серная кислота прежде всего нужна для предупреждения накопления ионов Cu+ и гидролиза ее солей.
В сульфатные электролиты меднения иногда вводят поверхностно-активные вещества. Эти вещества вводят для повышения катодной поляризации, что способствует получению более мелкозернистых плотных, иногда блестящих, осадков. Благоприятное действие этих добавок сказывается в том, что они предупреждают образование наростов на краях и выступающих частях деталей. Наилучшими добавками являются декстрин (не более 1 г/л) и фенол или его сульфосоединения (1-10 г/л).
Для получения блестящих медных покрытий предложено большое количество блескообразующих добавок, обеспечивающих зеркальный блеск покрытий, придающих им пластичность и снижающих внутренние напряжения.
При работе с электролитами для получения блестящих медных покрытий особое внимание следует уделять анодам. Анодный процесс растворения меди достаточно сложен и подробно описан в статье.
Взвешенные частицы шлама обычно являются причиной грубого шероховатого осадка. Вообще, медное покрытие особенно склонно к дендритообразованию при меднении с нарушением технологического процесса, к которому относится и присутствие шлама в растворе. Частички шлама становятся при этом центрами кристаллизации и ток, вместо того, чтобы идти на зарождение новых зерен меди, расходуется на обрастание и разрастание этих частиц. Дендриты могут появляться и по другим причинам, одной из которых также является превышение допустимой плотности тока на выступающих частях деталей. Примеры дендритов на медном покрытии приведены на рисунке 2. Пример дендрита на циллиндрическом катоде и поперечный рез такого дендрита приведены на рисунке 3.
Рисунок 2 — Примеры дендритов на медном покрытии.
Рисунок 3 — Пример дендрита на циллиндрическом катоде и поперечный рез такого дендрита.
На качество получаемых блестящих покрытий большое влияние оказывает концентрация ионов Сl–. При пониженной концентрации снижается блеск покрытий и образуются прижоги на острых кромках деталей, при повышенном содержании образуются полосы на покрытиях.
Вредными примесями в медных сульфатных электролитах являются мышьяк, сурьма, некоторые органические вещества, образующие коллоидные растворы, анодный шлам.
Кроме сульфатных, используют фторборатные электролиты. Эти электролиты обладают высокой устойчивостью; получающиеся покрытия плотные и мелкокристаллические, рассеивающая способность электролитов примерно такая же, как у сульфатных. Большая растворимость фторбората меди позволяет применять повышенные плотности тока. Из этих электролитов меднить стальные детали напрямую нельзя; необходим подслой никеля или меди из цианидных электролитов.
2.2 Процессы в щелочных электролитах меднения.
К щелочным электролитам относятся цианидные, пирофосфатные и этилендиаминовые электролиты. Основные достоинства: высокая рассеивающая способность, получение мелкокристаллических осадков, возможность непосредственно меднить стальные детали.
2.2.1 Цианистое меднение.
Довольно распространены цианидные электролиты. Условия осаждения меди из цианидных электролитов существенно отличаются от условий осаждения в кислых электролитах.
В цианидных электролитах медь находится в составе комплексных ионов, степень диссоциации, а, следовательно, и активность ионов меди очень мала. Поэтому потенциал выделения меди в них примерно на 0,9-1,2 В отрицательнее, чем в сульфатных растворах.
При малом количестве цианида аноды пассивируются. При недостаточном количестве свободного цианида, когда происходит пассивация анодов и на них разряжаются ионы ОН– с выделением кислорода, то не весь образующийся кислород выделяется в виде газа, а часть его расходуется на окисление цианида в цианит. Уменьшение содержания цианидов происходит также из-за взаимодействия их с углекислотой воздуха и образования карбонатов (NaCN → Na2CO3 ).
Содержание свободного цианида оказывает на катодный и анодный процессы противоположное влияние: для катодного процесса требуется минимальное содержание цианидов, для анодного – максимальное. При недостатке свободного KCN на анодах образуется зеленоватая пленка CuCN из-за того, что ионы меди не в состоянии перейти в комплексное соединение. Свободная поверхность анода уменьшается, плотность тока растет, и анодное растворение происходит с образованием ионов двухвалентной меди, которые в виде нерастворимого гидрата осаждаются на аноде. При этом аноды пассивируются и наблюдается интенсивное выделение кислорода.
Основными компонентами медных цианидных электролитов являются комплексный цианид меди и свободный цианид натрия. Из приведенных данных видно, что степень диссоциации комплексных ионов очень мала и уменьшается с увеличением содержания CN– в комплексе. Этим, по-видимому, объясняется повышение катодной поляризации при увеличении содержания свободного цианида в электролите.
Содержание меди в электролите во время работы обычно уменьшается вследствие недостаточной растворимости анодов. Снижение концентрации ионов меди в электролитах приводит к образованию пористых осадков. Кроме того, работая с малоконцентрированными медными электролитами, можно применять только пониженные плотности тока.
Постоянным компонентом цианидных электролитов является карбонат. Он накапливается в результате окисления цианида кислородом воздуха, особенно при нагревании:
2NaCN + 2Н2О + 2NaOH + О2 = 2Na2CO3 + 2NH3
Присутствие карбонатов в небольших количествах полезно, поскольку при этом повышается электропроводность электролитов. Однако при их накоплении свыше 70 г/л, а в концентрированных – до 140 г/л аноды проявляют склонность к пассивированию, а покрытия получаются пористыми. Карбонаты можно удалять при помощи хлорида бария и вымораживанием, охлаждая электролит до -5 °С. Следует отметить, что карбонаты натрия легче выпадают в осадок, чем калиевые. Сульфаты существенного влияния на процесс электролиза не оказывают.
Введение в электролит депассиваторов, в качестве которых применяют сегнетову соль KNaC4H4O6•4H2O и роданид калия KCNS, позволяет повысить рабочую плотность тока и устранить пассивацию анодов, но при этом следует одновременно повышать температуру электролита.
Высококонцентрированные по меди электролиты, содержащие депассиваторы, позволяют применять высокие плотности тока (до 10 А/дм2) при повышенной температуре и перемешивании. При этом возможно получить выход по току, близкий к 100 %.
Сульфиды, вводимые в электролит, играют роль восстановителя, предупреждая накопление в ванне ионов меди Cu2+.
Для замены ядовитых цианидных электролитов применяют пирофосфатные и этилендиаминовые электролиты.
2.2.2 Пирофосфатное меднение.
Из пирофосфатных электролитов получают медные осадки с мелкозернистой структурой. При нанесении тонких слоев осадки получаются гладкими, блестящими или полублестящими.
Основные компоненты пирофосфатных электролитов меднения: CuSO4 или Сu2Р2О7 и К4Р2О7 или Na4P2O7. В растворах в присутствии Na4P2O7 образуется комплексная соль Na6[Cu(P2O7)2]; при избытке свободного пирофосфата может образовываться Na2[Cu(P2O7)2]. Константы нестойкости комплексов [Сu(Р2О7)2]6- и [Сu(Р2О 7)2]2- соответственно равны 3•10-3 и 2•10-9.
В щелочных растворах при рН 8 и достаточном избытке свободных ионов Р2О74- медь находится преимущественно в виде шестизарядных комплексных ионов [Сu(Р2О7)2]6-.
В пирофосфатные электролиты вводят NH4NO3, который способствует повышению допустимой катодной и анодной плотностей тока и улучшает качество осадков. Из пирофосфатных электролитов можно получать блестящие осадки. В качестве блескообразующих добавок вводят Na2SeO3 совместно с лимонной или триоксиглутаровой кислотой, 2-меркаптотиазол и другие вещества.
При повышенных плотностях тока может происходить пассивация анодов за счет образования на их поверхности труднорастворимой оксидной или солевой пленки.
Катодный потенциал меди в пирофосфатных электролитах имеет более отрицательное значение, чем в кислых. Большая катодная поляризация объясняется пассивированием поверхности катода вследствие адсорбции ионов Р2О74- или образования оксидных (Сu2О8) и труднорастворимых соединений (Сu2Р2О7) в виде фазовой пленки.
Предполагают, что выделение меди на катоде из пирофосфатных растворов происходит в результате восстановления двухзарядных комплексов:
CuP2O72- + 2e– → Cu + Р2О74-,
образующихся при диссоциации шестизарядных комплексов:
Cu(P2O7)26- ↔ CuP2O72- + Р2О74-.
С повышением температуры ускоряется выделение меди, что связано как с ускорением диффузии комплексных анионов к катоду, так и с облегчением их разряда.
Структура осадков меди из пирофосфатного электролита более мелкая, по сравнению с сернокислымирастворами, с ростом плотности тока она укрупняется (рисунок 4)
Рисунок 4 — Микроизображения покрытия после меднения из пирофосфатного электролита при плотности тока 0,5 А/дм2 (слева) и 1 А/дм2 (справа).
Анодный выход по току в этих электролитах несколько выше катодного, поэтому при корректировке нет необходимости добавлять медные соли. Анодную плотность тока рекомендуется поддерживать в пределах 2-4 А/дм2. При более низкой плотности тока растворение идет недостаточно быстро, при более высокой – на поверхности анодов образуется труднорастворимая оксидная пленка.
Для предотвращения пассивации анодов должно быть достаточное количество свободных анионов Р2

При работе пирофосфатных ванн рекомендуется проводить фильтрацию электролита: для полублестящих осадков – периодически или непрерывно, для блестящих – непрерывно.
Особенностью этилендиаминовых электролитов меднения является возможность непосредственного меднения стальных деталей. Детали в ванну загружают под током плотностью в 3-5 раз превышающей рабочую.
Конец статьи
Понравилась статья? Оцените статью. Всего 1 клик!
Нажмите на звезду
Средняя оценка:
4,50
Всего оценок: 26
Данная статья является интеллектуальной собственностью ООО “НПП Электрохимия”. Любое копирование информации возможно только с разрешения владельца сайта. Размещение активной индексируемой ссылки на https://zctc.ru обязательно.
Статьи от Impgold производителя оборудования, для покрытий
Серебряные покрытия занимают первое место по популярности среди всех покрытий из драгоценных металлов. В ювелирной промышленности, являющейся одним из главных потребителей серебра, одной из основных характеристик является декоративный вид серебряных покрытий, поэтому самый большой интерес представляют электролиты блестящего серебрения. Для гальванического серебрения и нанесенных блестящих серебреных покрытий используются различные электролиты серебрения, наилучшими по качеству из которых, признаны электролиты на основе цианистых комплексов. Данные электролиты имеют высокую рассеивающую способность и состоят из цианистого комплекса серебра, цианида щелочного металла и карбоната этого щелочного металла, который, растворяясь в электролите, повышает его проводимость и способствует образованию более качественных мелко кристаллических осадков.
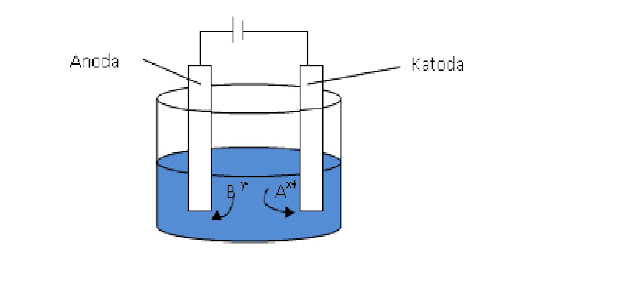
В последние несколько лет разработан целый ряд электролитов, не содержащих свободных цианидов, которые способны заменить цианистые электролиты серебрения. Среди не цианистых электролитов блестящего серебрения можно выделить децианаргентатнороданистый, синеродистороданистый и йодистый электролиты.
Децианаргентатнороданистые и синеродистороданистые электролиты серебрения устойчивы в работе, позволяют получать мелкокристаллические износостойкие серебреные покрытия, ничем не отличающиеся от покрытий, полученных из цианистых электролитов, наличие в составе свободного роданида вместо цианида, позволяет снизить их вредность, а в случае использования децианаргентатнороданистого электролита, значительно повысить рабочую плотность тока (с перемешиванием электролита до 2 А/дм2).
Состав дицианаргентатнородаснитого электролита:
Серебро (в виде KAg(CN)2) – 23-27 г/л
Роданистый калий (KCNS) – 250-270 г/л
Сегнетова соль (NaKC4H4O6) 70-80 г/л
Ализариновое масло (C14H8O4) – 40-45 г/л
Тетрагидрофурфуриловый спирт (C5H10O2) – 70-75 г/л
Сурьма (в виде сурьмяновинокислого калия SbOKC4H4O6) – 11-13 г/л
Катодная плотность тока 0,2-0,4 А/дм2, температура 18-25оС.
Йодистые электролиты серебрения просты в приготовлении, стабильны и безвредны в работе, не требуют фильтрации, частой корректировки, не имеют потерь серебра и дают возможность получать качественные серебреные покрытия с высокой степенью блеска. Недостатком данных электролитов серебрение является небольшой желтоватый оттенок на получаемом серебреном покрытии, а также получение хрупких и шероховатых покрытий при длительной эксплуатации электролита.
Состав йодистого электролита:
Йодистое серебро (AgI) – 50-60 г/л
Йодистый натрий (NaI) – 500-550 г/л
Тиосульфат натрия (Na2S2O3) – 4,0-6,0 г/л
Поливиниловый спирт CH2CH(OH) – 1,0-1,5 г/л
Борная (H3BO3) (или лимонная C6H8O7) кислота – 4,5-6,5 г/л
Катодная плотность тока 0,5-1,5 А/дм2. Температура электролита 18-25*С.
При гальваническом серебрении, серебро обычно наносят на медь или медные сплавы. Если необходимо провести серебрение металлов, то на них перед этим, необходимо сначала нанести медное покрытие. В конечном итоге, серебро лучше всего наносить на медную поверхность. При серебрении металлов, во избежание контактного осаждения серебра, сначала проводят предварительное серебрение, например в электролите следующего состава:
Серебро (Ag в пересчете на металл) 1-2г/л
Железосинеродистый калий (K3[Fe(CN)6]) – 45-60 г/л
Роданистый калий (KCNS) – 85-95 г/л
Температура электролита 18-20оС. Плотность тока 0,1-0,2 А/дм2. Время выдержки 3-4 минуты. Для процесса используют нерастворимые аноды из никеля или стали. Детали опускают в электролит под током. После промывки проводят основное серебрение.
Оборудование для серебрения использующееся для электролитического осаждения серебра, представляет собой источник постоянного или импульсного тока малой мощности, с возможностью регулировки очень малым “шагом” до 0.01 А. В качестве анодов для основного серебрения применяют аноды из чистого серебра. Для предотвращения загрязнения электролита шламом, аноды помещают в чехлы из полипропиленовой ткани. При длительных перерывах в работе аноды вытаскивают из ванны, очищают от шлама и хранят в сухом состоянии.
При серебрении “сложных” сплавов, например алюминия, сначала проводят цинкатную обработку алюминиевой поверхности, затем производят серебрение в три стадии в трех электролитах в каждом из которых содержится более высокая концентрация серебра, чем в предыдущем. Для серебрения алюминия и сплавов на его основе можно использовать процесс химического никелирования. Для этого, алюминиевая деталь или изделие предварительно обрабатывается в электролите следующего состава:
Хлорид никеля (NiCl2) – 30-35 г/л
Ацетат натрия (CH3COONa) – 30-40 г/л
Гипофосфит натрия (Na(PH2O2) – 25-30 г/л
Температура электролита 85-90оС; показатель рН 4-5; выдержка 15-20 минут.
Полученное затем серебреное покрытие, нанесенное по слою химического никеля, обладает даже более высокими физико-химическими свойствами, чем серебреное покрытие, нанесенное по слою меди. Единственным недостатком данного метода, является низкая рассеивающая способность электролита химического никелирования, вследствие этого, сложность или невозможность осаждения никеля в углубленных местах, глубоких полостях, на деталях имеющих сложный профиль поверхности и т.д.
Из-за наличия в воздухе паров серы и ее соединений, на серебреном покрытии со временем образуется сульфид серебра, что приводит к появлению на поверхности серебреного изделия радужных разводов, пятен, которые затем приобретают коричневый оттенок и затем черный цвет. Для очистки серебреного покрытия, изделие, вместе с кусочками алюминия, опускают в 10% раствор соды, в результате чего, выделяющийся водород восстанавливает сульфид серебра до чистого серебра.
Для предохранения покрытия серебра от окисления и образования на нем сернистых пленок, а также для декоративной отделки серебреного покрытия, наиболее простым и эффективным способом является химическое пассивирование в растворе бихроматов. Для этого, серебреную деталь или изделие сначала активируют в растворе кислоты или в щелочи, затем опускают на 20-25 минут в 1% раствор хромпика (K2Сr2O7). Процесс хроматирования ведут при температуре 18-2оС при постоянном перемешивании, рН раствора поддерживают в пределах 3,0 – 4,5 (корректировку рН проводят хромовым ангидридом).
Если внешний вид не играет роли, можно окрасить серебреное покрытие в черный цвет в растворе следующего состава:
Тиосульфат натрия (Na2S2O3) – 18-20 г/л
Натрий сернистый (Na2S) – 40-50 г/л
Серная кислота (H2SO4) – 4-5 г/л
Ацетон (С2Н6О) – 4-5 г/л
Плотность тока 0,05- 0,2 А/дм2, продолжительность обработки 3-5 минут. Полученное серебреное покрытие черного цвета имеет прочное сцепление с основой и обладает высокой износостойкостью.
Для обезвреживания и утилизации отработанного цианистого электролита, его сначала прорабатывают до полного выделения серебра, затем окисляют электролит, вводя в него 0,5 г/л обычной поваренной соли (NaCl), после чего, прорабатывают раствор при плотности тока 1 А/дм2 с нерастворимыми анодами (Внимание! Процесс следует проводить при хорошей вытяжной вентиляции). Через 30 минут в электролит снова добавляют 0,5 г/л соли и снова прорабатывают в течении 30 минут при плотности тока уже 3 А/дм2. Еще через 30 минут снова добавляют такое же количество соли и снова прорабатывают отработанный раствор электролита при плотности тока 6 А/дм2.
Дефекты при серебрении из цианистых электролитов и способы их устранения
Дефект покрытия | Причина возникновения | Способ устранения |
---|---|---|
Отслаивание покрытия (или шелушения), в особенности при последующей полировке | Плохая подготовка поверхности перед покрытием или малая концентрация серебра в электролите | Улучшить подготовку изделия перед покрытием.![]() |
Отслаивание – хрупкое покрытие | Пассивация серебряных анодов, аноды светлые, на катоде выделяется водород | Увеличить количество анодов, откорректировать электролит |
Пятна или потемнение покрытия и потемнение анодов | Недостаток свободного цианистого калия в электролите | Откорректировать электролит по содержанию свободного цианистого калия |
Шероховатость покрытия, темные пятна на покрытии при светлых анодах | Повышенная анодная плотность тока – усиленное растворение анодов, накопление анодного шлама | Отрегулировать анодную плотность тока, отфильтровать электролит, ввести необходимое количество аммиака |
Грубое крупнокристаллическое покрытие, рыхлое, с потемнением | Повышенная катодная плотность тока, близкая к предельной, особенно в момент завешивания | Отрегулировать катодную плотность тока |
Макро пористость покрытия, питтинг в форме блестящих точек или вертикальных полос | Выделение водорода – повышенная плотность тока, задержка пузырьков водорода на поверхности | Отрегулировать плотность тока, ввести перемешивание электролита, покачивание катодных штанг |
Аноды
для серебряного покрытия: вопросы и ответы, проблемы и решения
Finishing. com стал возможным благодаря …
этот текст заменяется на bannerText
(—–)
Запрос предложений: Я хотел бы перейти с анодов из серебряных пластин на аноды в стиле попкорн, чтобы улучшить площадь поверхности. Однако мне нужно руководство по типу материала корзины, который будет использоваться. 9
Эд. примечание: как всегда, любезные читатели: технические ответы на всеобщее обозрение, пожалуйста; коммерческие ответы в частном порядке (да? почему?)
Тесно связанные исторические сообщения, самые старые сначала …
RFQ: Уважаемый сэр;
Мы хотим приобрести СЕРЕБРЯНЫЕ АНОДЫ: 2,990 кг ЧИСТОТА 99,99% Пожалуйста, пришлите предложение для указанного материала.
MANOJ DWIVEDI
TRADING CO./ ПОСТАВЩИК – KANPUR, UP, ИНДИЯ
2005
—-
Ed. примечание: Извините, этот запрос предложения устарел, но технические ответы приветствуются. Пожалуйста, не предлагайте публичные бренды/источники (а? почему?)
Серебряные аноды чернеют
В. Мы выполняем процесс серебряного покрытия гаек и болтов, чтобы они не заедали. Наш резервуар устарел, и решение проверяется, и периодически вносятся дополнения, чтобы содержимое не вышло за пределы стандартов, которым мы следуем. В прошлом резервуар работал нормально, но недавно мы столкнулись с проблемой, что АНОД, который состоит из чистого 99% серебра, начинает покрываться черной пленкой во время металлизации. Черный слой на аноде замедляет скорость осаждения, и мы должны вынуть анод из ванны и очистить его абразивной губкой, промыть и снова поставить обратно. Мы должны сделать это 3-4 раза за 15-минутную операцию покрытия. Мы проверили ванну на наличие KCN и AgCN, и их содержание находится в допустимых пределах.
Пожалуйста, предложите какие-либо меры по устранению неполадок/исправлению?.
Мухаммед Наджиб
Сотрудник цеха плазменной резки – Карачи, Пакистан
2007
A. Привет Мухаммад,
Серебряные аноды могут быть доступны с чистотой до 99,97%. Получи это. Смените поставщика, если он не может. 50% вашей проблемы будет решено.
Теперь позаботьтесь о следующих областях:
1. Низкий уровень свободного цианида
2. Низкий pH
3. Больше тока.
Мухаммед, почему вы не упомянули о составе ванны вместо того, чтобы упомянуть «в пределах нормы» — какой предел!
Есть соотношение металла и цианида. Но сначала, пожалуйста, сообщите нам «лимит», который вы поддерживаете! Тогда, может быть, мы вам поможем.
Старайтесь публиковать как можно больше подробностей, а не оставлять все для догадок.
С уважением,
Т.К. Mohan
поставщик процесса нанесения покрытия – Мумбаи, Индия
В. Уважаемый Mohan
Спасибо за ваши предложения. Состав ванны состоит из четырех химических веществ, добавленных в деминерализованную воду. Это цианид калия и серебра = 13 унций веса/галлон, цианид калия = 10 унций веса/галлон, карбонат калия = 4 унции веса/галлон, гидроксид калия = 1 унция. вес./гал.
Галлон — это галлон США = 3,785 литра.
Значение pH равно 12,5 ,
Пределы контроля раствора:
Металл серебра = 6,0–7,5 унций/гал [44,9–56,2 г/л], Текущее значение 6,1 [45,7 г/л],
Цианид калия = 6,0– 9,0 унций/гал [44,9–67,4 г/л], Текущая стоимость 6,5 [48,7 г/л],
Карбонат калия = 4,0–16,0 [30–120 г/л], недавно не проверялось,
Гидроксид калия = 0,5–2,0 [3,74-15 г/л], недавно не проверял.
Мы будем искать серебряный анод 99,97 на нашем местном рынке. Между тем, исходя из деталей ванны, если у вас есть какие-либо другие предложения, сообщите нам об этом.
С уважением
Наджиб
Мухаммад Наджиб [возвращается]
Магазин гальванических покрытий – Карачи, Пакистан
А. Наджиб,
Можете ли вы преобразовать эти конц. в г/л!
Я уезжаю в отпуск. вернусь 15 числа
С уважением,
Т.К. Mohan
поставщик процесса нанесения покрытия – Мумбаи, Индия
—-
Ed. примечание: г/л = унция/галлон x 7,5. Для удобства читателей мы добавили в скобках конверсию к сообщению Мухаммеда.
A. Мухаммед,
Если ваши химические параметры находятся в допустимых пределах, следует соблюдать осторожность в следующих областях.
1. фильтрация раствора
2. качество цианида
3. плотность тока
4. качество воды
5. рН раствора
С уважением,
Uroj Shahnawaz
– Карачи, Пакистан
A. Если эти аноды работали нормально в этом растворе до сих пор, то проблема, скорее всего, в растворе. Поскольку вы указываете, что ток также падает, это звучит так, как будто аноды поляризуются, поэтому, поскольку ваш свободный цианид находится в нижней части вашего диапазона, я бы попробовал добавить пару унций / галлон цианида калия и посмотреть, что произойдет.
Джеффри Уайтлоу
– Порт Мельбурн, Австралия
А. Привет,
Ваши аноды нечистые, они также не отожжены и не протравлены после прокатки. Вероятно, это жир, который выходит каждые 15 минут или около того, так как его можно очистить абразивом. проверьте также рабочее напряжение на шинах.
Deepak Whorra
изделия из серебра – Нью-Дели, Индия
Инертные аноды для серебряного покрытия?
В. Привет. Мы использовали серебряные анодные стержни в нашем серебряном покрытии. Можно ли заменить эти серебряные анодные стержни на инертные аноды? У нас также есть проблема с увеличением содержания карбонатов в нашей ванне. Как нам с этим справиться?
Мэрилу Бакордио
Инженер-технолог – г. Себу, Филиппины
21 апреля 2009 г.
А. Привет, Мэрилу. Серебрение возможно с помощью анодов из нержавеющей стали, а в некоторых магазинах, которые в основном производят тонкие чеканки серебра, используются аноды из нержавеющей стали. Но обычно это менее практично, чем использование серебряных анодов, если вы делаете много гальванопокрытий. Третий вариант — серебряные самородки или «попкорн».
С уважением,
Тед Муни, ЧП
Стремление жить Алоха
finish.com – Пайн-Бич, Нью-Джерси
A. Инертные аноды вызывают образование карбонатов.
Robert H Probert
Robert H Probert Technical Services
Garner, North Carolina
A. Если ваша серебряная ванна изготовлена из натрия, вы можете выморозить карбонаты до определенной степени. Это не аккуратный или полный процесс. Если вы используете ванну на основе калия, я не знаю, как вы избавитесь от карбонатов.
Джеймс Уоттс
– Наварра, Флорида
Сурья
—-
Изд. примечание: см. письмо 473 для хорошего обсуждения вымораживания карбонатов.
A. При использовании ванн на основе цианида калия обработка нитратом кальция снижает содержание карбонатов до желаемого уровня. Fellow Plater – Syracuse, New York, USA A. Аноды из нержавеющей стали вызывают быстрое выделение карбонатов. Не используйте их. Для контроля карбонатов (при использовании серебряных анодов) поддерживайте pH выше 12,5 с помощью гидроксида калия. Джим, Сильвер должен работать не с натрием, а с цианистым калием. Сара Михаэли Тель-Авив-Яффо, Израиль |
A. Я собираюсь обработать нашу ванну для серебряного покрытия, чтобы избавиться от карбоната калия. Я собираюсь использовать продукт под названием Декарбонирующие соли SF20522, поставляемый Macdermid. – Саутгемптон, Хэмпшир, Англия A. Серебряный анод сам по себе является лучшим вариантом, который также снизит себестоимость производства запатентованной серебряной соли или серебряного горшка. Цианид привлечет как плату за конверсию, так и убытки от конверсии! Т.К. Mohan поставщик процесса нанесения покрытия – Мумбаи, Индия |
Очень чистые серебряные аноды в любом случае чернеют
В. Я являюсь поставщиком серебряных анодов для различных компаний, и у меня есть собственный плавильный цех для их изготовления. Но я регулярно получаю жалобы, что после введения анода в ванну через несколько часов из анода выходит какой-то черный компонент. Тигель, который мы используем для плавки серебра, сделан из графита. Используем ли мы правильный тигель или нам следует использовать тигель из карбида кремния? А также, концентрируется ли графит с серебром и приводит ли к загрязнению бака? Или есть какая-то другая причина образования черного цвета? Самое главное тесты показывают чистоту 99,9%.
Даршан Ботра
производитель серебряных анодов – Ченнаи, Тамилнаду, Индия
11 сентября 2011 г.
В. Привет всем,
Когда серебряные аноды помещаются в серебряную ванну (на основе цианида калия), цвет анода становится белым. Через 5 часов или в конце дня серебряные аноды становятся черными. Почему?
Есть ли примеси в серебряной ванне или в аноде?
Предложи мне.
Сурья Нараяна
Инженер-технолог – Тумкур, Карнатака, ИНДИЯ.
23 августа 2014 г.
Серебряный анод через некоторое время чернеет в ванне с хлоридом натрия
В. У меня есть серебряная пластина 0,999 пробы, которая через некоторое время в растворе продолжает чернеть. Он также теряет свою первоначальную массу. Как это можно предотвратить? Так как я хотел бы продолжать обшивку некоторых вещей. Потребуется ли мне в будущем получать новую серебряную пластину 999 пробы?
ishmael smith
– Колумбус, штат Огайо, США
29 июня 2016 г.
A. Привет, Измаил. При серебрении, как и при большинстве других покрытий, анод растворяется в растворе; это источник серебра, которое вы наносите на вещи.
Но я не понимаю “хлорид натрия”. Это приведет к образованию нерастворимого хлорида серебра. Возможно, это была опечатка или автокоррекция, и вы пытались сказать «цианид серебра»?
С уважением,
Тед Муни, ЧП RET
Стремление жить Алоха
finish.com – Пайн-Бич, Нью-Джерси
В. Привет, Тед Муни. Спасибо, что нашли время ответить на мой вопрос.
Есть ли способ вернуть серебряным тарелкам свой первоначальный вес? Я понимаю, что некоторые из них растворяются, но если я возьму еще одну серебряную пластину и помещу ее в анод, а изношенную вонну возьму в качестве катода, смогу ли я продолжать повторно использовать свои пластины вместо того, чтобы покупать новые. Я просто хотел бы восстановить некоторые пластины.
Есть ли какой-нибудь возможный способ сделать это? Я хотел бы продолжить сервировку вещей для моей жены, так как она хотела бы, чтобы посуда была покрыта металлом. У меня нет возможности покупать больше серебра, когда оно по одному изнашивается.
Измаил Смит [возвращается]
– Колумбус, Огайо, США
А. Привет, Измаил. Вы пытаетесь покрыть серебром другие предметы. Как вы думаете, откуда берется это серебро, которое вы покрываете другими предметами? Это исходит от ваших серебряных тарелок. Вы не можете положить серебро на предметы, не поставив серебро.
Пожалуйста, объясните, какой именно раствор вы используете и в каких условиях вы пытаетесь гальванизировать серебро. Опять же, я не понимаю ссылку на хлорид натрия; вы, конечно, не можете гальванизировать серебро с помощью поваренной соли; для серебряного покрытия требуется чрезвычайно ядовитый цианид, который даже не может быть использован любителем в домашних условиях. Извиняюсь.
С уважением,
Тед Муни, ЧП RET
Стремление жить Алоха
finish.com – Пайн-Бич, Нью-Джерси
Какой анод лучше всего подходит для посеребрения попкорна?
В. Какой анод лучше всего подходит для электроосаждения серебра на медь.
В нашей ванне есть AgCN, KCN и K2CO3.
Серебряный анод дороговат для нас.
Работаем над электрическими элементами.
Большое спасибо,
Мохаммад Заре
– Шираз, Иран
16 декабря 2019 г.
А. Привет Мохаммад. Да, серебро дорогое. Но поставлять его в виде соли для покрытия еще дороже, чем в виде анода. Однако вам не нужно использовать литые аноды; вы можете использовать серебряный «попкорн» в корзинах, если это более доступно и доступно. Удачи.
С уважением,
Тед Муни, ЧП RET
Стремление к жизни Aloha
Finishing.com – Пайн-Бич, Нью-Джерси
A. Количество серебра, нанесенного на заготовку, должно быть заменено, в противном случае раствор покрытия выходит из равновесия и содержание серебра истощается. Самым дешевым источником серебра является металлическое серебро, так как соли серебра стоят примерно в десять раз больше, чем содержание серебра в них.
Тревор Крайтон
Исследователь-практик
Чешам, Бакс, Великобритания
А. Здравствуйте Мохаммад. Тед и Тревор дали несколько отличных советов, они просто хотели упомянуть некоторые преимущества использования анодов типа «попкорн». Серебряные аноды для попкорна имеют большую площадь поверхности в упакованных анодных корзинах из-за их формы. Во-вторых, когда литые аноды становятся тонкими, чтобы сохранить площадь поверхности анода, вы должны либо добавить еще один полный анод рядом с ним, либо вытащить его и сохранить для утилизации. У большинства серебряных пластин есть воронки для корзин, в которые легче добавлять материал для попкорна, чтобы заполнить корзины. Просто что-то рассмотреть.
Марк Бейкер
Пенсионер – Уинстон Салем, Северная Каролина, США
Вопрос, ответ или комментарий в ЭТОЙ теме -или- Начать НОВУЮ тему
Отказ от ответственности: с помощью этих страниц невозможно полностью диагностировать проблему отделки или опасность операции. Вся представленная информация предназначена для общего ознакомления и не является профессиональным мнением или политикой работодателя автора. Интернет в значительной степени анонимен и непроверен; некоторые имена могут быть вымышленными, а некоторые рекомендации могут быть вредными.
Если вы ищете продукт или услугу, связанную с отделкой металлов, проверьте следующие каталоги:
О компании/Контакты Проблемы
Гальваника включает использование электрического тока для покрытия электрода растворенными катионами металлов. В металлургии это одна из самых качественных процедур для получения прочных ровных покрытий на металлических подложках.
Однако гальванопокрытие требует высокого уровня усердия, опыта и точности. Это зависит не только от точных спецификаций электрохимического процесса, но и от тщательной подготовки перед включением выключателя. В результате гальваническое покрытие имеет несколько дефектов из-за сложности процесса.
Общие дефекты гальванического покрытия часто включают проблемы, которые присутствуют до нанесения покрытия, такие как холодные затворы, точечная коррозия, острые края, точки расщепления и грязное производство. Во время нанесения покрытия может произойти отслаивание или потеря адгезии. После того, как покрытие завершено, общие проблемы включают водородное растрескивание, матовые и мутные отложения в покрытии, вздутие и окисление. В этой статье мы объясним, что это за проблемы и как они возникают.
Как и любой сложный процесс, гальванопокрытие следует доверять тем, кто имеет устоявшуюся репутацию в отрасли. Поскольку гальванопокрытие имеет решающее значение для многих отраслей, включая телекоммуникации, оборону, аэрокосмическую промышленность и многие другие, первостепенное значение имеет гарантия того, что надлежащее гальваническое покрытие будет выполнено самой квалифицированной компанией. Это также может быть разочаровывающим процессом, поэтому SPC здесь, чтобы помочь вам пройти через него — от лучших вариантов до полного набора ловушек, которых следует избегать.
Давайте начнем с обсуждения того, какие дефекты могут появиться перед нанесением покрытия.
Перед нанесением покрытия
Поскольку гальваника в значительной степени зависит от предварительной обработки для надлежащего выполнения, многие проблемы, обнаруженные в конечном продукте, на самом деле являются результатом проблем до нанесения покрытия. Вот некоторые из наиболее распространенных источников дефектов предварительного покрытия:
1. Холодные затворы
Холодные затворы являются одним из наиболее распространенных дефектов, обнаруживаемых в материалах, направляемых на гальваническое покрытие. Они являются результатом затвердевания металла на разных стадиях и видны на поверхности металла в виде следов течения или линий.
Более конкретно, холодная резка образуется, когда поток расплавленного металла достигает более холодной поверхности штампа. Из-за разницы температур между расплавленным металлом и холодной головкой происходит быстрое охлаждение расплавленного металла. Это заставляет его затвердевать до полного заполнения формы. Когда поступает следующий поток расплавленного металла, он заполняет оставшиеся зазоры между матрицей и предыдущим потоком.
Проблема здесь в том, что этот новый поток теперь связывается с предыдущим куском закаленного металла, а не весь кусок затвердевает как единое целое. Это вызывает дифференциальное соединение, в результате чего на поверхности объекта появляются линии. Естественно, эти трещины, как правило, находятся в точках, наиболее удаленных от ворот.
Наиболее частая причина этого дефекта — матрица при слишком низкой температуре. В результате деталь имеет неадекватную механическую прочность, так как по этим линиям естественным образом происходит разрушение, когда на деталь оказывается нагрузка.
2. Питтинг
Еще одна распространенная проблема — питтинг, представляющий собой небольшие отверстия на поверхности объекта. Более толстые отложения более подвержены точечной коррозии, так как они увеличиваются в размерах по мере увеличения отложений, а повторно обработанные детали, как правило, проявляют этот дефект больше, чем новые детали.
Источник питтинга связан с поверхностью металла, хотя его конкретные причины могут различаться. В некоторых случаях химические средства подавления дыма могут вызывать точечную коррозию. Это особенно верно, если использовался непостоянный тип средства подавления дыма, хотя в наши дни он реже является источником проблем. Постоянный подавитель дыма хорошего качества сам по себе не вызывает точечной коррозии.
Скорее, точечная коррозия обычно является результатом ошибок, допущенных во время подготовки. Они могут включать в себя неадекватную работу по очистке или дефекты на самом объекте. Перед нанесением покрытия шлифовка, пескоструйная обработка или полировка, которые были выполнены слишком жестко, могут быть виновником и могут привести к появлению мусора на поверхности объекта. Очень маленькие отверстия, окисление на поверхности, микроскопические трещины и кусочки неметаллических материалов также могут вызывать точечную коррозию.
Наконец, точечная коррозия может быть вызвана остатками останова, разрушением трубопровода или футеровки резервуара, обломками проволочных щеток, пескоструйным аппаратом, выгибом шины и такими веществами, как масло, оставшееся после ванны.
3. Острые края
Геометрия объектов играет большую роль в том, как они получают гальваническое покрытие. Сам процесс основан на токе, который запускает реакцию на поверхности детали и притягивает катионы. Определенные геометрические формы приведут к большей привлекательности, чем другие.
Благодаря этому принципу, когда ток проходит через объект с острым краем, плотность тока в этой точке увеличивается. Распределение тока имеет первостепенное значение для правильного гальванического покрытия. Вот почему на ранних этапах следует проявлять осторожность, чтобы уменьшить острые края, резьбу или изгибы. В противном случае ток может накапливаться в одной области детали и притягивать чрезмерное количество покрытия.
Когда на острой кромке скапливается слишком много покрытия, в результате может получиться хрупкий слой, который легко ломается. Большинство производителей исправляют острые края путем шлифовки и удаления заусенцев с края, пока он не станет более мягким. Обычное эмпирическое правило заключается в закруглении всех краев до тех пор, пока их радиус не будет составлять от 0,4 до 0,8 миллиметра.
4. Точки расщепления
Спайность — это расщепление твердого тела вдоль структурной плоскости. При гальванике это может вызвать проблемы со структурной жесткостью. Точки спайности образуются в процессе литья под давлением.
5. Нечистое производство
Одним из самых простых способов гарантировать проблемы с гальванопокрытием является наличие на объекте грязной поверхности. Это может быть результатом производственных проблем, обращения, загрязнения или загрязнения оборудования. Высококвалифицированный специалист по гальванике осмотрит объект на предмет надлежащей чистоты.
Гальваническое покрытие притягивает покрытие к поверхности объекта с помощью тока. Однако каким бы мощным ни был ток, между поверхностью предмета и самим покрытием должно произойти окончательное сцепление. Если между этими двумя есть какая-либо примесь, адгезия будет неполной. Результатом неизбежно будет покрытие, которое отделяется от объекта. Это может привести к волдырю или ломкой области.
После покрытия
Ниже приведены распространенные дефекты, возникающие после нанесения покрытия:
1. Потеря адгезии
Есть ли способ гарантировать адекватную адгезию?
Этот вопрос очень важен, так как потеря адгезии является одной из наиболее распространенных причин поломки деталей отделки, которая служит как декоративным, так и утилитарным целям. Слишком часто вину возлагают на гальваническое покрытие. На самом деле, это редко происходит из-за покрытия, а скорее из-за поверхности под ним. Каждый раз, когда поверхность покрывается антиадгезионными составами, оксидами, легирующими веществами или маслами, адгезия материала покрытия может быть нарушена.
Поверхность под покрытием должна быть «активной», то есть она должна быть готова к нанесению покрытия. Система предварительной обработки является частью линии нанесения покрытия и состоит из предварительного замачивания в щелочной жидкости, электроочистки, травления в кислоте, раскисления, процедуры удаления окалины с использованием химикатов, ультразвуковой очистки и активации ударов. Они различаются в зависимости от линии покрытия и ее различных функций.
Ни одна из этих предварительных обработок не может длиться бесконечно долго на линии гальванического покрытия, а срок их службы ограничен интенсивностью используемого использования. Из-за этого срок действия одной или нескольких предварительных обработок может истечь, и объект не будет должным образом обработан перед гальванопокрытием. Примеры сбоев могут включать истощенный химический процесс, предназначенный для удаления определенного ингибитора адгезии, или включения свинца, которые не удаляются должным образом с подложки.
Несколько факторов помогают гальванопластике предотвратить появление дефектов:
- Сообщите металлисту, какой сплав используется. Знание точного сплава продукта может быть разницей между безупречной работой по гальваническому покрытию и работой с дефектами. Например, латунь 360 может содержать до 5 процентов свинца, а латунь 260 — 0 процентов свинца.
Оба сплава широко используются, но техника нанесения покрытия для каждого из них разная. В частности, каждая латунь нуждается в различной предварительной обработке, чтобы стать достаточно активной. Если производитель не знает, с каким типом сплава он имеет дело, это маловероятно.
- Менее мощные масла легче удалить. Как правило, те масла, которые помечены как органические, то есть масла, полученные из живых источников, таких как животные и овощи, можно без особых проблем удалить с предметов, прошедших предварительную обработку. Однако воск и смазки, сделанные из силикона, труднее удалить, и они с большей вероятностью останутся, несмотря на попытки очистки. По возможности заранее продумайте процесс нанесения покрытия и используйте масла или смазки, которые легче удалить.
- Обязательно проводите термообработку в инертной среде. Использование инертной среды для термообработки дороже, но компромисс заключается в том, что она требует значительно меньше предварительной обработки и, как результат, может уравнять или сэкономить деньги.
В противном случае бригаде по предварительной обработке может потребоваться пескоструйная обработка, чтобы избавиться от накипи, образовавшейся в результате термической обработки. Это может увеличить стоимость гальванических работ на порядок.
- Убедитесь, что вы используете гальванические материалы. Высококачественные материалы имеют первостепенное значение для конечного продукта гальванического покрытия. Они стоят дороже, но, как это часто бывает в производстве, более высокая цена легко компенсируется простотой покрытия и отсутствием брака. Более высокая стоимость связана с дополнительным уровнем заботы о том, чтобы на поверхности не было металлических включений или остатков.
2. Растрескивание после нанесения покрытия — водородное растрескивание
С самого начала современной индустриальной эры водород представлял проблему для тех, кто занимается отделкой металлов. Он имеет тенденцию делать металлы хрупкими, заставляя их ломаться и разрушаться. При гальванике водород часто может проникать в детали без ведома производителя.
Поскольку водородное охрупчивание обычно проявляется после завершения процесса, когда деталь подвергается нагрузке, эту проблему трудно выявить, пока она не возникнет. Инженеры справляются с этим, принимая несколько мер на протяжении всего процесса. К ним относятся запекание для снятия напряжения и дробеструйная обработка объекта, которые повышают прочность и минимизируют вероятность водородного разрушения.
3. Тусклые и мутные отложения в гальваническом покрытии
Одним из неприятных дефектов является тусклое или мутное пятно на покрытии. Это может иметь несколько возможных причин:
- Химический дисбаланс: При погружении объекта в ванну недостаточное количество добавки Dura Additive или чрезмерное количество сульфата, хромовой кислоты или загрязняющих веществ может привести к тусклым или мутным отложениям в конечном продукте.
- Неправильная температура: Температура ванны должна быть между 130 и 140 градусами по Фаренгейту.
Используйте воздушную мешалку, чтобы поддерживать постоянную температуру во всей ванне, и старайтесь оставаться в пределах двух градусов по Фаренгейту.
- Неправильная плотность тока: Плотность тока должна быть равна двум ASI, и отклонение от этого уровня может вызвать тусклость или туманность.
- Неправильное распределение тока: Если аноды не находятся на надлежащем расстоянии от объекта, ток не будет течь правильно. Используйте соответствующие аноды, чтобы решить эту проблему.
- Неправильный выпрямитель Функция: Выпрямитель должен работать правильно, чтобы избежать тусклых отложений. Выполните тесты для поиска необходимого ремонта.
- Недостаточный предварительный нагрев: Недостаточно горячие детали могут выйти из строя. Убедитесь, что они полностью нагрелись до температуры ванны.
- Interrupted Current: Детали, покрытые без прерывания тока, как правило, дают наилучшие результаты.
- Недостаточное ополаскивание: Процесс ополаскивания должен быть тщательным, чтобы убедиться, что все чистящие средства и химические вещества отсутствуют на объекте перед нанесением покрытия.
- Деталь слишком высока в растворе: Объект, помещенный не менее чем на 4 дюйма ниже верхней части раствора, будет получать надлежащий ток.
- Загрязнение органическими соединениями: На ванне может образоваться поверхностная пена из органических веществ, которая затем может прилипнуть к поверхности объекта.
4. Вздутие покрытия
Волдыри возникают, когда газ расширяется из пор объекта. Эти газы обычно представляют собой водород или азот, и они попадают на поверхность объекта из-за смазки, нанесенной на штамп. Когда объект нагревается, газы расширяются и давят на покрытие, заставляя его вздуваться в виде волдыря. В качестве альтернативы, нахлест, который частично остается на поверхности, может привести к отрыву покрытия.
5. Окисление в гальваническом покрытии
Одной из основных причин покрытия является предотвращение окисления объекта. Поэтому само собой разумеется, что сам объект способен окисляться до нанесения покрытия. Окисление на поверхности объекта может привести к плохой адгезии и отслоению покрытия после завершения процесса.
Свяжитесь с Sharretts Plating Company для консультации
Гальваника — это процесс, требующий навыков, опыта и соответствующего оборудования. SPC является отраслевым лидером в области консалтинга по гальваническим покрытиям. Имея почти столетний опыт работы в гальванической промышленности, мы готовы помочь нашим клиентам получить наилучшие результаты по оптимальной цене.
Наша аккредитация включает в себя то, что мы являемся первой компанией, получившей награду за лучшую производственную практику от Военно-морского ведомства США, первой сертифицированной по стандарту ISO 9000, получившей аккредитацию QS и стандарты TS 16949 Tier 1 и Tier 2 по управлению качеством в автомобильной промышленности.
Чтобы получить опыт, на который вы можете положиться, обратитесь в SPC за консультацией по гальваническим покрытиям.
Электролитическая ячейка против гальванической ячейки
Ячейка — это устройство, способное производить электрическую энергию в результате химических реакций или использовать электрическую энергию для осуществления химической реакции. Таким образом, клетки можно разделить на две основные категории: одни производят электрическую энергию в результате химических реакций, а другие используют электрическую энергию для осуществления химической реакции. В то время как первый называется гальваническим или гальваническим элементом, последний является электролитическим элементом.
Электролитическая ячейка и гальваническая ячейкаЭлектролитические и гальванические ячейки работают по-разному. В следующей таблице перечислены основные различия между электролитическими элементами и гальваническими элементами.
Электролизеры | Гальванические элементы |
Способствует несамопроизвольным реакциям, в которых электрическая энергия внешнего источника преобразуется в химическую энергию.![]() | Способствует самопроизвольным реакциям, в которых химическая энергия превращается в электрическую. |
Оба электрода погружены в один и тот же раствор электролита. | Полуклетки соединены соляным мостом. |
Катод — это отрицательный электрод, а анод — это положительный электрод. Под действием внешнего источника электроны движутся от анода к катоду. | Катод — это положительный электрод, а анод — отрицательный электрод. Электроны по-прежнему текут от анода к катоду. |
Однако обе ячейки содержат две полуячейки для чистой окислительно-восстановительной реакции с восстановлением и окислением. В обеих ячейках происходит окисление на аноде и восстановление на катоде.
Что такое электролитическая ячейка? Электролитическая ячейка представляет собой устройство, предназначенное для использования электрической энергии и обеспечения неспонтанной окислительно-восстановительной реакции. Таким образом, электрическая энергия преобразуется в химическую энергию в процессе электролиза.
Итак, что такое электролиз?
Процесс прохождения электрического тока от внешнего источника в раствор электролита называется электролизом.
Электролитическая ячейка подходит для электролиза определенных соединений, таких как вода, при электролизе образуются газообразные водород и кислород.
Компоненты электролизераНа следующей схеме электролизера показаны основные компоненты электролизера (см. рис. 1).
Электролизер состоит из следующих основных частей:
- Бак : Электролизер имеет электролитический бак, изготовленный из непроводящего материала, такого как бакелит или стекло.
- Электролит : Раствор для электролиза (электролит) заливается в бак. Электролит может быть в виде раствора или расплавленного состояния.
- Электроды : Ячейка состоит из двух металлических/графитовых стержней, погруженных в электролит и подключенных к батарее.
Стержень, подключенный к положительной клемме, действует как анод , а тот, что подключен к отрицательной клемме, действует как катод .
На заметку
|
Разложение хлорида натрия — самый простой пример понимания того, как работает электролитическая ячейка. Если вы расплавите хлорид натрия, чтобы получить жидкость, и пропустите электрический ток через расплавленную соль, она разложится.
Расплавленный NaCl ионизируется с образованием твердого натрия и газообразного хлора. Когда электрический ток протекает через расплавленный хлорид натрия, положительные ионы натрия движутся к отрицательному катоду, а отрицательные ионы хлорида притягиваются к положительному аноду. Поскольку атомы хлора не могут существовать независимо друг от друга, они объединяются, образуя молекулы хлора. Полуреакции можно выразить следующим образом:
На катоде:
Na + + e – → Na
На аноде:
Cl – – e – → Cl (первичное изменение)
Cl + Cl → Cl 2 (вторичное изменение)
Суммарную реакцию процесса можно записать, как показано ниже:
2NaCl (2NaCl l) → 2Na (s) + Cl 2 (g)
Законы электролиза ФарадеяМайкл Фарадей широко изучал электролиз и установил зависимость между количеством вещества, осажденного на электроде, и количеством прошедшего через него электричества. электролит. Он сформулировал два количественных закона, упрощающих расчеты на основе электролиза.
Первый закон электролиза Фарадея Согласно закону, вес металла, осажденного на катоде, прямо пропорционален количеству использованного электричества.
W ∝ Q
W = ZQ
С момента z = электрохимический эквивалент = эквивалентный вес/ постоянная Фарадея
Фарадея = 96500
Q =
Формула может быть написана следующим образом:
W = ZIT
.
Вт = (экв. вес × i × т)/ 96500
2-й закон электролиза ФарадеяСогласно второму закону, если одно и то же электричество (по количеству) проходит через разные электролиты, соединенные последовательно, то вес металла, осажденного на катоде, прямо пропорционален к своему эквивалентному весу.
Вт ∝ Экв. вес
w1 / w2= E1 / E2
Пример решения Пример 1: Если через водный раствор медного купороса в течение часа пропускают ток силой 0,2 ампера, какая масса меди накопится на катоде? Решение: t= 1 час = 60×60 секунд = 3600 с Ток = i = 0,2 А Атомная масса меди = 63,5 Валентность меди в медном купоросе = 2 Таким образом, эквивалентная масса меди = атомная масса / валентность Эквивалентная масса = 63,5/2 Эквивалентная масса = 31,75 Электрохимический эквивалент меди можно рассчитать следующим образом: Z = уравнение масса / 96500 Z = 31,75 / 96500 Z = 3,29 × 10 -4 г/Кл Согласно первому закону электролиза Фарадея масса меди будет равна .![]() Вт = Зит Вт = 3,29×10-4×0,2×3600 Вт = 0,2369 г Ответ: На катоде накопится 0,2369 г меди по массе. |
Проверьте свои знания: Вопрос 1: Как долго вы будете пропускать ток силой 4 ампера через раствор нитрата серебра, чтобы покрыть металлическую поверхность площадью 50 см 2 толщиной слоя 0,005 мм? Учитывая плотность серебра 10,5 г/см 3 |
Электролитическая ячейка находит применение в различных полезных процессах, таких как покрытие некоторых металлов для предотвращения их коррозии. Ниже приведены некоторые полезные области применения электролизера:
1. Извлечение и рафинирование металлов
Рафинирование металлов включает извлечение нечистых металлов из руды.
Анод: Руда служит анодом.
Электролит: Соль металла становится электролитом.
Катод: Отложения чистого металла на катоде.
Создание электролизера для извлечения и рафинирования металлов используется для нескольких металлов, таких как медь, цинк и другие. По мере того, как чистый металл откладывается на катоде, он удаляется с катода. Анод продолжает сжиматься в процессе, и нечистый анод заменяется, чтобы продолжить процесс.
2. Химическое производство
Электролизом производятся химические вещества, такие как каустическая сода, перманганат калия, хлор, персульфат аммония, кислород, водород и многое другое в больших масштабах.
Некоторые процессы, такие как электролиз рассола, дают несколько полезных продуктов. Основным продуктом, собирающимся на катоде, является каустическая сода, тогда как на одном полюсе (на аноде) выделяется хлор, а на другом (на катоде) выделяется водород.
3. Электролитическое восстановление металлов из соединений
Алюминий получают из бокситов с помощью электролизера. Бокситы высокого качества содержат до 70% оксида алюминия, кремнезема и оксида железа. Сначала на катоде собирается оксид алюминия, а затем соответствующая обработка помогает получить чистый алюминий за счет восстановления оксида алюминия. Процесс дает чистый алюминий до 99,5%.
4. Гальваническое покрытие
Процесс покрытия металла другим, обычно для следующих целей, называется гальванопокрытием:
- Чтобы добавить больше ценности
- Украшение
- Защита от коррозии
- Ремонт
- Промежуточный производственный процесс
При гальванопокрытии объект, на который наносится гальваническое покрытие, служит катодом, а металл, наносимый на него, — анодом. Электролит также содержит осаждаемый металл. Часто катод окружен набором анодов или вращается с постоянной скоростью вокруг анода, чтобы обеспечить равномерное покрытие. Покрытие золотом и серебром выполняется по той же схеме.
Часто задаваемые вопросы Q1. Каковы критерии образования продуктов при электролизе?
В основе электролиза лежат два критерия:
- Вещество с более высоким стандартным восстановительным потенциалом предпочтительно восстанавливается на катоде.
- Вещество с более низким стандартным восстановительным потенциалом преимущественно окисляется на аноде.
Q2. Что такое жертвенная защита?
Протекторная защита — это процесс защиты металла за счет другого, более активного или электроположительного металла, нанесенного на его поверхность. Часто это делается с помощью электролиза; типичным примером является гальванизация железа. В этом процессе тонкий слой цинка наносится на железное вещество, чтобы защитить его от коррозии.
Q3. Где используются электролизеры?
Электролитические элементы имеют широкий спектр применения, например, гальваническое покрытие металлов, отделение чистой формы металла от его металлических соединений, перезарядка аккумулятора и многое другое.