Шероховатости поверхности методы контроля: Измерение шероховатости поверхности – способы и методы. Работа профилометра
alexxlab | 02.05.2023 | 0 | Разное
Методы и средства контроля шероховатости поверхности
Контроль шероховатости поверхности может осуществляться:
1) сравнением (визуально или с помощью микроинтерферометра) реальной поверхности изделия с рабочими образцами
шероховатости, которые имеют стандартизованные значения параметра Ra;
2) измерением параметров шероховатости с помощью щуповых или оптических приборов.
Числовые значения параметров шероховатости определяются либо непосредственно по шкале приборов (профилометров), либо по увеличенному изображению профиля или записанной профилограмме сечения профиля (на приборах – профилографах).
Если в технических требованиях не задано направление измерения шероховатости, то измерения производят в том направлении, где имеется наиболее грубая шероховатость. При механической обработке резанием этому условию соответствует направление измерения, перпендикулярное главному движению при резании (поперечная шероховатость).
Для проведения лабораторной работы используются контактные приборы последовательного преобразования профиля. Эти приборы являются наиболее совершенными для измерения шероховатости поверхности, позволяющими измерить почти все параметры шероховатости, регламентированные ГОСТ 25142 –
82, кроме того, с помощью этих приборов наиболее просто измерять предпочтительный параметр шероховатости Ra.
3.1. Профилометр 283 с унифицированной электронной системой
Профилометр 283 представляет собой контактный щуповой прибор для определения числового значения параметра шероховатости Ra и является высокочувствительным прибором, предназначенным для измерения поверхностей деталей с твердостью не менее НВ 10, сечение которых в плоскости представляет прямую линию.
Принцип действия прибора основан на ошупывании измеряемой поверхности алмазной иглой с радиусом кривизны при вершине 10мкм и преобразовании с помощью механотронного преобразователя механических колебаний иглы в пропорциональные изменения электрического напряжения.
Общий вид профилометра (мод. 283) показан на рис. 4.
Датчик 1 с алмазной ощупывающей иглой закреплен в гнезде штока привода 2. Привод установлен на вертикальной стойке с плитой, на которую устанавливают призму 6 для контролируемой детали.
Привод предназначен для перемещения датчика по измеряемой поверхности и осуществления отсечки шага. Отсечка шага на приводе имеет два значения – 0.8 мм и 0.25мм, соответствующие значениям базовых длин. При отсечке шага
0,25мм скорость перемещения датчика соответствует 0,25мм/с; при отсечке шага 0,8мм – 0,8мм/с; выходные электрические сигналы с датчика поступают на электронный блок 3. Отсчет результатов измерения шероховатости поверхности производится по шкале прибора, которая градуирована по параметру Ra.
3.1.1. Порядок работы на профилометре мод. 283 (рис.4)
Рис. 4. Общий вид профилометра мод. 283
1) установить на призме 6 измеряемую деталь.
2) включить прибор тумблером «сеть». При этом должна загореться сигнальная лампа. Прибор готов к работе через 3-5 мин. после включения в сеть.
3) установить датчик 1, вставленный в привод 2, на измеряемую поверхность детали, при этом, поворачивая маховик стойки 4, добиться совмещения треугольных знаков на штоке и планке привода 7. Застопорить винтом 5 положение датчика.
4) установить на электронном блоке 3 нужный предел измерения, соответствующий заданному параметру шероховатости на чертеже. Переключателем 8 установить заданную отсечку шага, равную базовой длине ℓ.
5) включить нажатием кнопки «пуск» на электронном блоке3 движение датчика по измеряемой поверхности.
После остановки датчика (сигнальная лампа погаснет) отметить значение параметра шероховатости Ra, зафиксированное стрелкой прибора по выбранной ранее шкале.
Для надежной оценки шероховатости рекомендуется измерения повторить несколько раз в различных местах поверхности. Результатом измерения считается максимальное из всех действительных значений Ra, полученных для данной детали.
3.2. Профилограф – профилометр мод. 252
Профилограф – профилометр мод. 252 является контактным высокочувствительным прибором, предназначенным для измерения шероховатости и волнистости поверхности изделий.
Принцип действия прибора основан на ощупывании исследуемой поверхности алмазной иглой с радиусом кривизны при вершине 10 мкм и преобразовании с помощью дифференциального индуктивного преобразователя механических колебаний иглы в пропорциональные изменения электрического напряжения.
Параметры шероховатости поверхности, определяемые профилографом – профилометром мод. 252:
Ra – среднее арифметическое отклонение профиля,
Hmax – высота наибольшего выступа профиля,
Hmin – глубина наибольшей впадины профиля,
tp – относительная опорная длина профиля,n – число шагов неровностей в пределах длины трассы ощупывания при измерении по базовой линии.
3.2.1.Техническая характеристика прибора
Диапазон измерений профилографа – профилометра по параметрам:
Ra, мкм 0,02 ……..250
Hmax, Hmin 0,1……….100 tp, % 0………….100 n 0………….100
3.2.2. Порядок работы прибора при измерении шероховатости поверхности датчиком с опорой на измеряемую поверхность
Использование прибора в качестве профилометра (рис. 5)
1) на стойке 1 размещен мотопривод 2, на котором с помощью специального разъема следует закрепить датчик 4.
2) включить прибор (кнопка 12 на блоке питания 6) и установить ручку переключателя 15 «Род работы» в положение
«ПП» (настройка прибора).
3) установить ручкой 16 мотопривода скорость движения датчика 60 мм/мин, а ручкой переключателя 25 требуемую длину трассы ощупывания.
4) установить ручкой переключателя 26 требуемый предел измерения и ручкой 24 требуемую отсечку шага, равную базовой длине.
5) вращением маховика 18 опустить датчик на измеряемую поверхность, осторожно, чтобы не повредить иглу, при этом
стрелка индикаторного прибора рабочей зоны 27 должна быть приблизительно в середине шкалы.
Примечание: измерение на приборе возможно, когда стрелка индикаторного прибора рабочей зоны находится в пределах шкалы.
3.2.3. Измерение параметра Ra
1) нажать кнопку «Ra» на счетно-решающем блоке 9, после этого кнопку 21 – «пуск» (зеленого цвета) на блоке питания 6 и после остановки датчика снять показания Ra на цифровом табло счетно-решающего блока 9.
Примечание: при загорании индикаторной лампы 28 «перегрузка» переключить прибор ручкой 26 на режим работы с большим пределом измерения; если значащее число на цифровом табло меньше 90, то перевести прибор на режим работы с меньшим пределом измерения.
3.2.4. Измерение параметра «n»
1) произвести выбор предела измерения по значению параметра Ra.
2) нажать кнопку «n» на счетно-решающем блоке 9 и кнопку 21 «пуск», после остановки датчика снять показания «n».
Примечание: при загорании лампы 28 «перегрузка» ручкой переключателя 25 переключить прибор на более короткую трассу ощупывания.
3.2.5. Измерение параметров Hmax, Hmin
1) нажать кнопку Hmax или Hmin на счетно-решающем блоке 9.
2) опустить датчик на измеряемую поверхность (рабочее положение датчика контролировать по отклонению стрелки индикаторного прибора рабочей зоны 27, которая должна находиться в пределах шкалы).
3) для запуска режима измерения нажать кнопку 21 –
«пуск» (зеленого цвета).
Примечание: при первом проходе датчика на цифровом отсчетном устройстве должны быть зафиксированы нули.
4) нажать кнопку 21 вторично и, после остановки датчика, на цифровом табло счетно-решающего блока 9 снять показания Hmax или Hmin.
Примечание: при загорании лампы 28 переключить прибор на больший предел измерения, а если значащее число на цифровом табло будет менее 90, то переключить на меньший предел измерения.
5) нажать кнопку 21 для следующего измерения.
3.2.6. Измерение параметра «tp»
1) измерить значения «Hmax» и «Hmin».
2) нажать кнопку «tp» на счетно-решающем блоке 9; если значащее число на цифровом табло находится в пределах от
90 до 999, то можно приступить к измерению «tp»; если показания Hmax и Hmin получаются в разных пределах измерения, то необходимо установить больший предел.
3) нажать кнопку 21 – «пуск» (зеленого цвета).
Примечание: при первом проходе датчика на цифровом отсчетном устройстве зафиксированы нули.
4) нажать одну из кнопок 29 требуемого уровня сечения профиля.
5) нажать кнопку 21 на блоке питания и после остановки датчика снять с цифрового табло показание «tp» на установленных уровнях.
3.2.7. Описание прибора
1. Стойка
2. Мотопривод
3. Датчик для измерения отверстий
4. Датчик с опорой
5. Стол
6. Блок питания
7. Блок измерительный
8. Соединительный шланг
9. Блок счетно-решающий
10. Прибор записывающий
11. Приспособление для контролируемой детали
12. Кнопка «включение» на блоке питания
13. Кнопка «реверс» на записывающем устройстве
14. Ручка переключателя вертикального увеличения
15. Ручка переключателя «род работы»
16. Ручка переключателя мотопривода
17. Ручка переключателя скорости движения ленты
18. Маховик
19. Кнопка «включение записывающего устройства»
20. Точная настройка индикатора
21. Зеленая кнопка на блоке питания «пуск»
22. Красная кнопка на блоке питания (аварийная остановка датчика)
23. Кнопка «выключение» на блоке питания
24. Рукоятка переключателя «отсечка шага»
25. Рукоятка переключателя «длина трассы ощупывания»
26. Рукоятка переключателя «предел измерения»
27. Шкала индикатора настройки прибора
28. Индикаторная лампа «перегрузка»
29. Кнопка требуемого уровня сечения профиля
30. Диаграммная бумага
Материал взят из книги Метрология, стандартизация, сертификация (А.И. Аристов)
Методы контроля и измерения шероховатости.
Параметры поверхности определяются только для случая очистки абразивоструйным методом поверхности, ранее неокрашенной или после полного удаления прежних покрытий.
Шероховатость может быть оценена различными методами и измерительными средствами, наиболее распространенными из которых являются:
компараторы (эталоны сравнения) по ИСО 8503-2;
микроскоп по ИСО 8503-3;
профилометр (ил профилограф) по ИСО 8503-4;
метод реплик по стандартам ИСО 8503-5 или NACE RP 0287;
электронные приборы.
Наиболее простым и доступным методом оценки шероховатости является использование компараторов ИСО, технические характеристики которых соответствуют стандарту ИСО 8503-1. Компараторы используются двух типов и представляют собой плоские пластины, разделенные на четыре сегмента с различной строго калиброванной шероховатостью
Процедура определения шероховатости исследуемой поверхности включает в себе следующие действия :
1) Очистка поверхности от пыли и мусора.
2) Подбор компаратора (S или G), соответствующего профилю исследуемой поверхности.
3) Сравнение шероховатости исследуемой поверхности поочередно с четырьмя сегментами компаратора. При необходимости для этого можно использовать лупу с увеличением не более 7. Сравнение производится при расположении компаратора рядом с исследуемым участком поверхности.
4) Определение группы шероховатости исследуемой поверхности:
тонкая – шероховатость между сегментами 1 и 2, но ниже, чем сегмента 2.
средняя – шероховатость между сегментами 2 и 3, но ниже, чем сегмента 3.
грубая – шероховатость между сегментами 3 и 4 , но ниже, чем сегмента 4.
Если шероховатость исследуемого участка ниже нижней границы группы “тонкая”, то она оценивается как “очень тонкая”, если шероховатость выше верхней границы группы “грубая”, то она оценивается как “очень грубая”.
Если визуальная оценка затруднена, то может быть использована осязательная оценка путем легкого “царапания” внутренней поверхностью ногтя пальца поочередно исследуемой поверхности и сегментов компаратора.
В случае сомнений в результате визуальной оценки шероховатости параметры шероховатости могут быть оценены в соответствии со стандартами ИСО 8503-3 (метод с использованием микроскопа) или ИСО 8503-4 (применение прибора с мерительным штифтом).
Параметры
и характеристики шероховатости согласно
ГОСТ 25142 называют совокупность неровностей
поверхности с относительно малыми
шагами, выделенную с помощью базовой
длины. Шероховатость поверхности изделий
независимо от материала и способа
изготовления можно оценивать количественно
одним или несколькими параметрами:
средним арифметическим отклонением
профиля Ra,
высотой неровностей профиля по десяти
точкам Rz,
наибольшей высотой неровностей профиля Rmax,
средним шагом неровностей Sm,
средним шагом местных выступов профиля S,
относительной опорной длиной профиля tp.
Параметр Ra является предпочтительным. Базирование
при измерении шероховатости производится
по средней линии профиля.
Высотные и шаговые параметры шероховатости поверхности.
С р е д н е е а р и ф м е т и ч е с к о е о т к л о н е н и е п р о ф и л я Ra — среднее арифметическое из абсолютных значений отклонений профиля в пределах базовой длины:
Ra =
|y(x)|dx;
(3. 3)
Ra = |yi|, (3.4)
где l — базовая длина;
n — число выбранных точек профиля на базовой длине.
О т к л о н е н и е п р о ф и л я у — расстояние между любой точкой профиля и средней линией.
Высота неровностей профиля по десяти точкам Rz — сумма средних абсолютных значений высот пяти наибольших выступов профиля и глубин пяти наибольших впадин профиля в пределах базовой длины.
Н а и б о л ь ш а я в ы с о т а н е р о в н о с т е й п р о ф и л я Rmax — расстояние между линией выступов профиля и линией впадин профиля в пределах базовой длины l.
С
р е д н и й ш а г н е р о в н о с т е й п
р о ф и л я Sm — среднее значение шага неровностей
профиля в пределах базовой длины.
С р е д н и й ш а г м е с т н ы х в ы с т у п о в п р о ф и л я S — среднее значение шага местных выступов профиля в пределах базовой длины.
Числовые значения параметров шероховатости Ra, Rz, Rmax, Sm и S стандартизованы и приведены в ГОСТ 2789.
Как уменьшить или контролировать шероховатость поверхности при традиционной обработке?
Внешний вид, а также некоторые трибологические свойства (связанные с трением, износом и смазкой) твердой поверхности в значительной степени зависят от уровня отделки. Хотя существует множество операций, предназначенных для получения высокообработанной поверхности (например, шлифовка, притирка, хонингование, суперфинишная обработка, NTM и т. д.), использование таких процессов увеличивает затраты и время в производственном графике. Традиционная обработка сама по себе может обеспечить достаточно хорошее качество поверхности, если параметры процесса и другие влияющие факторы контролируются должным образом.
- Формула шероховатости поверхности при точении закругленным инструментом
- Формула шероховатости поверхности при точении острым инструментом
Основная цель обычной механической обработки – получение надлежащих размеров, допусков и хорошего качества поверхности. Каждая операция механической обработки имеет определенные возможности для обеспечения определенного диапазона чистоты поверхности. Хотя для аналитической оценки шероховатости поверхности учитываются лишь некоторые механические и геометрические параметры, в реальных случаях шероховатость может возникать из различных источников. Для улучшения чистоты поверхности (или для уменьшения шероховатости поверхности) требуется точно контролировать все подобные параметры. Ниже обсуждаются различные шаги, которые можно предпринять для улучшения чистоты поверхности при механической обработке.
Параметры, влияющие на шероховатость поверхности при механической обработке, проиллюстрированы с помощью диаграммы «рыбий скелет».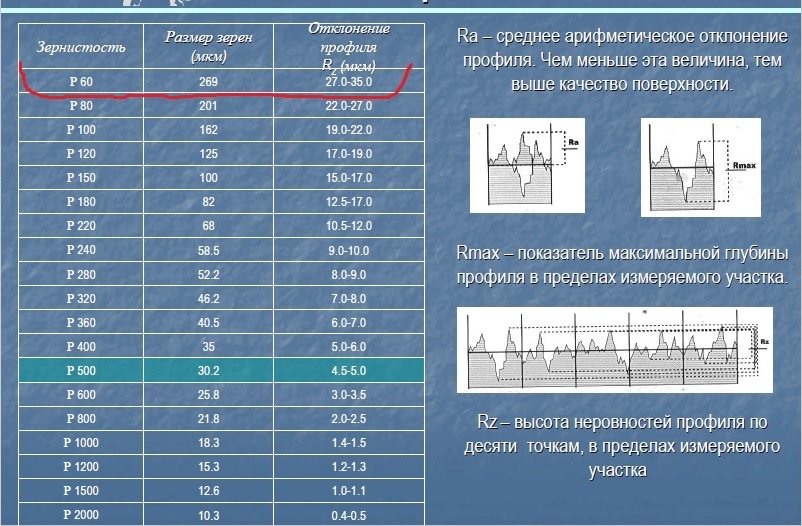
За счет использования режущего инструмента правильной геометрии — При одинаковой скорости подачи и глубине резания закругленный инструмент дает меньшую шероховатость поверхности по сравнению с острым. Таким образом, обеспечив подходящий радиус вершины, можно улучшить качество отделки. Кроме того, инструмент с более низким главным углом режущей кромки (φ) и вспомогательным углом режущей кромки (φ 1 ) может обеспечить лучшую отделку.
- Какой инструмент обеспечивает более гладкую поверхность при точении – закругленный или острый?
Путем уменьшения скорости подачи — Шероховатость поверхности пропорциональна скорости подачи. Таким образом, используя более низкую скорость подачи, можно улучшить чистовую обработку. Однако в таком случае необходимо пожертвовать скоростью съема материала (MRR), и, таким образом, производительность снизится.
Исключая вероятность образования BUE — Нарост на кромке (BUE) развивается и прочно прилипает к кончику инструмента. Это изменяет геометрию инструмента, ограничивает плавный сход стружки, увеличивает силу резания и вызывает вибрацию. Все такие последствия могут привести к образованию шероховатых поверхностей. Таким образом, за счет снижения вероятности образования BUE (например, за счет использования охлаждающей жидкости, правильного угла наклона инструмента и т. д.) можно улучшить чистоту поверхности.
Путем уменьшения вибрации — Вибрация в станке может вызывать колебания глубины резания, скорости подачи и силы резания. Такие небольшие колебания масштаба могут ухудшить качество обрабатываемой поверхности. Таким образом, использование виброгасителей, надлежащая передача вибрации и изоляция станка от пола могут улучшить чистоту поверхности.
За счет снижения скорости износа инструмента — Изношенный инструмент может серьезно повредить обрабатываемую поверхность. Материал, совместимый с инструментом, может сохранять свою форму в течение более длительного времени. Использование соответствующей охлаждающей жидкости также помогает снизить скорость износа за счет контроля температуры резания.
Существует несколько других тривиальных факторов, влияющих на качество поверхности при механической обработке. К таким факторам относятся (i) качество необработанной поверхности, включая шероховатость поверхности, трещины, пустоты и т. д. (ii) однородность обрабатываемого материала, (iii) прерывистое движение скользящих частей станка, (iv) эксцентриситет заготовки или инструмента. , (v) люфт в движущихся элементах, (vi) модификация наконечника инструмента и т. д. Таким образом, при правильном контроле этих факторов в соответствии с требованиями качество поверхности также может быть улучшено.
- Книга: Достижения в технологии производства XV Д. Т. Фама, С. С. Димова и Т. О’Хагана (Professional Engineering Publishing Limited).
- Материалы: К. С. Умашанкар, Б. Дж. Мануджеш и Н. А. Джнанеш; Повторяющийся квалификационный анализ — инструмент для анализа чистоты поверхности во время обработки; Достижения в области машиностроения; 2010.
- Книга: Механическая обработка и станки А. Б. Чаттопадхьяя (Wiley).
- Книга: Резка металла: теория и практика А. Бхаттачарьи (Новое центральное книжное агентство).
Приборы и методы измерения шероховатости поверхности – mechutopia
Введение
Профилометры.Существует множество инструментов и методов, используемых для измерения шероховатости поверхности.
С инженерной точки зрения наиболее важными из них являются:
Обработка нержавеющей стали: вызов…
Пожалуйста, включите JavaScript
Обработка нержавеющей стали: проблемы, решения и 10 советов от профессионалов. | 2023
- Инструменты с наконечниками, работающими от электричества
- Оценка поверхности на ощупь и измерение того, насколько хорошо она работает с инструментами
- Существует несколько видов световых интерференционных микроскопов
- Изготовление копий на поверхности
1-й и 2-й из этих методов показывают серию профилей на поверхности .
Электрические точечные устройства
На этих устройствах есть рычаг. На рукоятке алмазный наконечник. Этим наконечником маркируется вся поверхность образца. Электрические сигналы отправляют информацию о том, как наконечник перемещается вверх и вниз, на дисплей или принтер.
A) Устройство с E-Core
Устройство с E-Core.На рисунке расстояние между концами сердечника (E) изменяется, когда рычаг на конце сердечника (Fe), который находится между двумя полюсами магнита, перемещается вверх и вниз. Это изменение делает амплитуду электрических сигналов больше или меньше. При необходимости элемент интерфейса увеличивает мощность этих сигналов. Создав систему фильтрации, можно печатать по прямой линии.
B) Устройство катушки
Устройство катушечного типа. На рисунке показано устройство с катушкой. Катушка надевается на вершину алмаза. Когда магнит помещается между катушками, создается магнитное поле в вертикальном направлении. Концы двигаются вверх и вниз вместе с катушкой. Когда алмазный наконечник движется вверх и вниз, магнитное поле меняется. Сила этого магнитного поля равна высоте и длине поверхности. Или равно количеству перемещений алмазного наконечника. В местности, где работает устройство, частота может быть не чувствительна. Схема коррекции (Rc) используется для выделения нежелательных частот.
(Примечание. Магнитная часть катушки усиливает магнитный поток катушки.)
C) Устройство с пьезоэлектрическим кристаллом
Устройство с пьезоэлектрическим кристаллом. На рисунке показано пьезоэлектрическое устройство. Когда к пьезоэлектрическому элементу прикладывается сила, он создает напряжение. Ромбовидная ручка крепится к стеклу шпилькой. Со скользящей подушечкой алмазный наконечник касается поверхности. Когда наконечник перемещается вверх и вниз, он создает напряжение, которое воспринимается как сигнал и отправляется на индикатор или записывающее устройство. Изменение напряжения настраивается для измерения степени шероховатости поверхности. В яме применяется небольшое усилие. Используется максимальное пиковое усилие.
Оценка поверхности на ощупь и с помощью механических устройств
– Оценка поверхности на ощупь
Идея этого метода заключается в сравнении. Контроль ногтей можно проводить вдоль поверхности. Для сравнения используются тестовые блоки со значениями шероховатости в серии (N). Свойства трения поверхности используются, чтобы судить о том, как она ощущается. Поскольку оценка вращающихся поверхностей на ощупь приведет к большим различиям, для контроля следует использовать электрические устройства с острыми алмазными наконечниками (Ra).
Созданы механические инструменты, способные измерять методом прикосновения. Их наносят на поверхности, которые были отшлифованы, отполированы, притерты, отшлифованы или отшлифованы с помощью этих инструментов. Значения (Ra) читаются как эквиваленты серии N.
– Принцип работы устройств
Когда тонкая металлическая поверхность ребра вдавливается в область, подлежащую оценке, она либо скользит, либо изгибается, в зависимости от двух факторов.
Когда угол меньше критического угла, ребро немного перемещается по поверхности. По мере увеличения угла плавник начнет изгибаться, как на картинке. Когда поверхность очень гладкая, критический угол большой. Этот угол меняется в зависимости от того, насколько шероховатая поверхность. На фото вы можете увидеть, как устройство выглядит вживую. Сквозь прозрачную крышку виден плавник, прикрепленный к поверхности. При достижении критического угла серия N на стрелке индикатора показывает значения шероховатости поверхности (Ra). Калибровка прибора (Ra) выполняется на закаленных образцах размером 0,1 и 0,4 мкм.
Устройство измерения глубины со шкалой
Показатель грубой шероховатости (Rz) должен быть определен для среднеарифметических значений выше 5,0 м. (Ра). Большинство измерительных приборов для электричества ниже этого значения.
Устройство глубины предназначено для токарных, фрезерованных и экструдированных деталей, среди прочего. Параметр (Rz) становится более важным, чем параметр (Ra) на этих поверхностях. Преимущество прибора в том, что он может делать измерения быстро и не требует графиков.
Прибор состоит из индикаторного циферблата со стержнем (стержнем) внутри. В зависимости от того, круглая или плоская поверхность, алмазный наконечник можно зафиксировать в двух или трех точках. Сначала устройство устанавливается обратно в стандартный блок. Затем, нажав на измеряемую область, можно было ввести холмы. Затем наконечник затягивают и снимают показания. Не менее 4 раз этот процесс повторяется снова. Его среднее равно сразу (Rz). Если вы хотите (Ra), вы делите найденное значение (Rz) на (4). Rz = 4Ra – значение шероховатости. Около 15% людей толерантны. Мы не должны забывать, что мы не должны слишком доверять этим фактам. Rz можно умножить на 7 (Ra).
Измерение шероховатости поверхности с помощью световых интерференционных микроскопов
При правильном изменении оптической системы метод создания теней можно также использовать для измерения шероховатости поверхности как на плоских, так и на изогнутых поверхностях.