Синтетическая резина: Искусственная и синтетическая резина – презентация онлайн
alexxlab | 18.03.2023 | 0 | Разное
Искусственная и синтетическая резина – презентация онлайн
Похожие презентации:
Сложные эфиры. Жиры
Физические, химические свойства предельных и непредельных карбоновых кислот, получение
Газовая хроматография
Хроматографические методы анализа
Искусственные алмазы
Титриметрические методы анализа
Биохимия гормонов
Антисептики и дезинфицирующие средства. (Лекция 6)
Клиническая фармакология антибактериальных препаратов
Биохимия соединительной ткани
1. Резина
Искусственные исинтетические
Каучуки
—
натуральные
или
синтетические
эластомеры,
характеризующиеся
эластичностью,
водонепроницаемостью
и
электроизоляционными свойствами, из которых путём вулканизации
получают резины и эбониты
Резина (от лат. resina «смола») — эластичный
материал, получаемый вулканизацией каучука
Применяется для изготовления шин для различного транспорта,
уплотнителей, шлангов, транспортёрных лент, медицинских, бытовых и

Получают из натурального или синтетического каучука методом
вулканизации – смешиванием с вулканизирующим веществом (обычно с
серой) с последующим нагревом
История резины начинается с открытием
американского континента. Коренное население
Центральной и Южной Америки, собирая
млечный сок каучуконосных деревьев (гевеи)
получали каучук. Ещё Колумб обратил внимание,
что применявшиеся в играх индейцев тяжёлые
монолитные мячи из чёрной упругой массы,
отскакивают намного лучше, чем известные
европейцам кожаные
Реакция получения натурального каучука
n СН2═ С─СН═СН2 + СН2═ С─СН═СН2
│
│
СН3
СН 3
─[ СН2─С═СН─СН2─СН2─С═СН─СН2]n─
│
│
СН3
СН3
Кроме мячей каучук применялся в быту: изготовления посуды, герметизация
днищ пирог, создание непромокаемых “чулков«, применялся каучук и как клей:
с помощью него индейцы приклеивали перья к телу для украшения. Но
сообщение Колумба о неизвестном веществе с необычными свойствами
осталось незамеченным в Европе, хотя, несомненно, что конкистадоры и
первые поселенцы Нового света широко использовали каучук
По-настоящему Европа познакомилась с
каучуком в 1738 г.

Америки путешественник Ш. Кодамин
представил французской академии наук
образцы каучука и продемонстрировал
способ его получения. Первое время
практического применения в Европе каучук
не получил
Первым и единственным применением в
течение примерно 80 лет было
изготовление ластиков для стирания
следов карандаша на бумаге. Узость
применения каучука обусловливалась
высыханием и твердением каучука
Лишь в 1823 году шотландский химик и изобретатель Чарльз Макинтош
нашёл способ возвращения каучуку свойства эластичности. Он изобрёл
раствором каучука в керосине. Из этой материи стали изготовлять
непромокаемые плащи (получившие по фамилии изобретателя ткани
нарицательное название «макинтош»), галоши, непромокаемые почтовые
сумки
В 1839 году американский изобретатель Чарльз Гудьир
нашёл
способ
температурной
стабилизации
эластичности каучука — смешиванием сырого каучука с
серой и последующим нагревом.

название вулканизация, и, вероятно, является первым
промышленным процессом полимеризации. Продукт,
получаемый в результате вулканизации, был назван
резиной
Процесс вулканизации
После открытия Гудьира резина стала
широко
использоваться
в
машиностроении в качестве различные
уплотнителей
и
рукавов
и
в
зарождающейся
электротехнике,
индустрия которой остро нуждалась в
хорошем изоляционном эластичном
материале для изготовления кабелей
Развивающееся
машиностроение
и
электротехника,
а
позже
автомобилестроение потребляли всё больше резины. Для этого требовалось всё
больше сырья. Из-за увеличения спроса в Южной Америки стали возникать и
быстро развиваться огромные плантации каучуконосов, выращивающие
монокультурно эти растения. Позже центр выращивания каучуконосов
переместился в Индонезию и Цейлон.
После того, как резина стала широко применяться и природные источники каучука
не могли покрыть возросшие потребности стало ясно, что надо найти замену
сырьевой базе в виде каучуконосных плантаций.
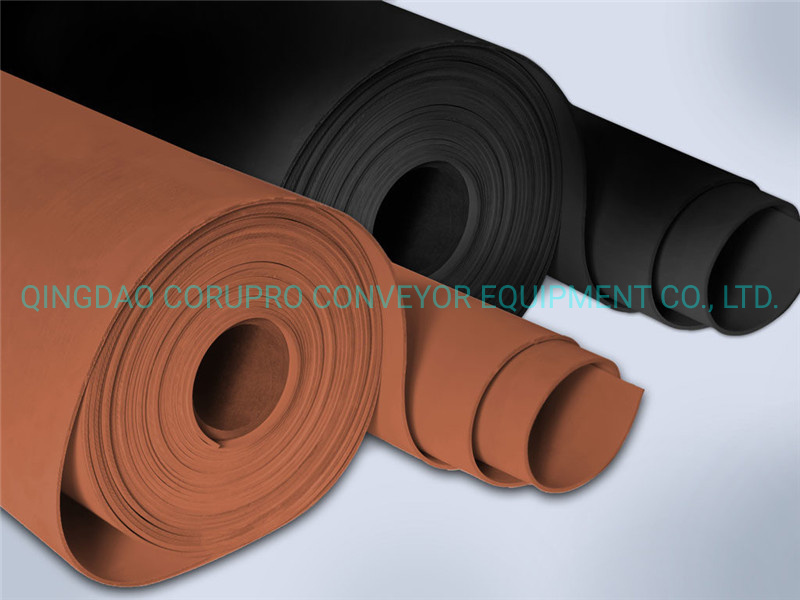
плантациями монопольно владели несколько стран (основной из них была
выращивания каучуконосов и сбора каучука и больших транспортных расходов.
Поиск альтернативного сырья шёл двумя путями:
Поиск растенийкаучуконосов, которых
можно было бы
культивировать в
субтропическом и
умеренном климате
Производство
синтетических каучуков из
нерастительного сырья
Интенсивно производство синтетических каучуков стало развиваться в СССР,
который стал пионером в этой области. Это было связано с острой нехваткой
резины для интенсивно развивающейся промышленности, отсутствием
эффективных природных каучконосов на территории СССР и ограничение
поставок каучуков из-за рубежа, так как правящие круги некоторых стран
пытались помешать процессу индустриализации СССР. Проблема
налаживания
крупнотоннажного
промышленного
производства
синтетической резины была успешно решена, несмотря на скептицизм
некоторых зарубежных специалистов
Синтетические каучуки стали необходимой альтернативой натуральному
каучуку и придали дополнительные свойства изделиям.
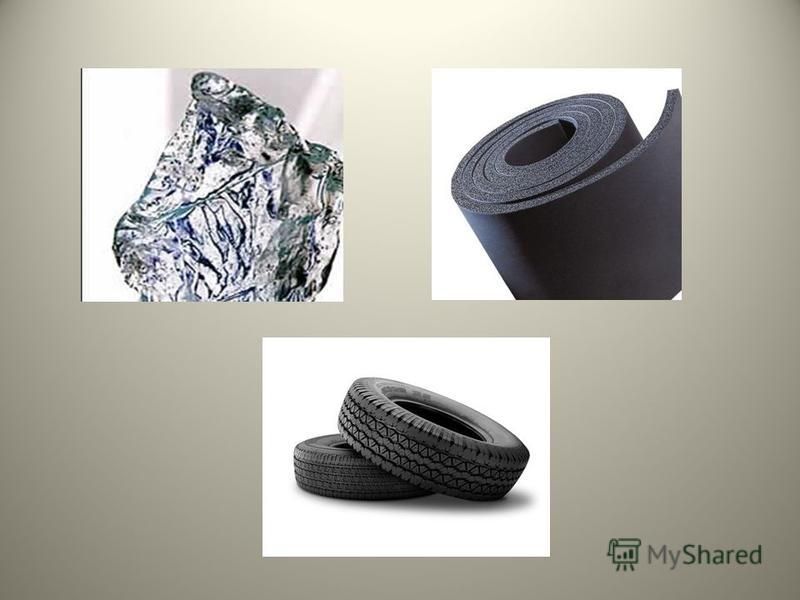
В общем виде их можно разделить на два крупных сегмента: каучуки общего
назначения и каучуки специального назначения
Каучуки общего назначения
Каучуки специального назначения
Бутадиен-стирольный каучук
Хлоропреновый каучук
Бутадиен-метил-стирольный
каучук
Полибутадиеновый каучук
Бутадиен-нитрильный каучук
Бутилкаучук
Уретаны
Этиленпропиленовый каучук
Силиконы
Галогенированные изобутилены
Этиленпропилендиеновый каучук Полисульфидные каучуки
Цис-1,4-полиизопреновый каучук
Каучуки
общего
назначения
используются в тех изделиях, в которых
важна сама природа резины и нет
каких-либо особых требований к
готовому изделию
Каучуки специального назначения
и используются для придания резинотехническому
изделию
(шинам,
ремням, обувной подошве и т.д.)
заданного
свойства,
например,
износостойкости,
маслостойкости,
морозостойкости,
повышенного
сцепления с мокрой дорогой и т.
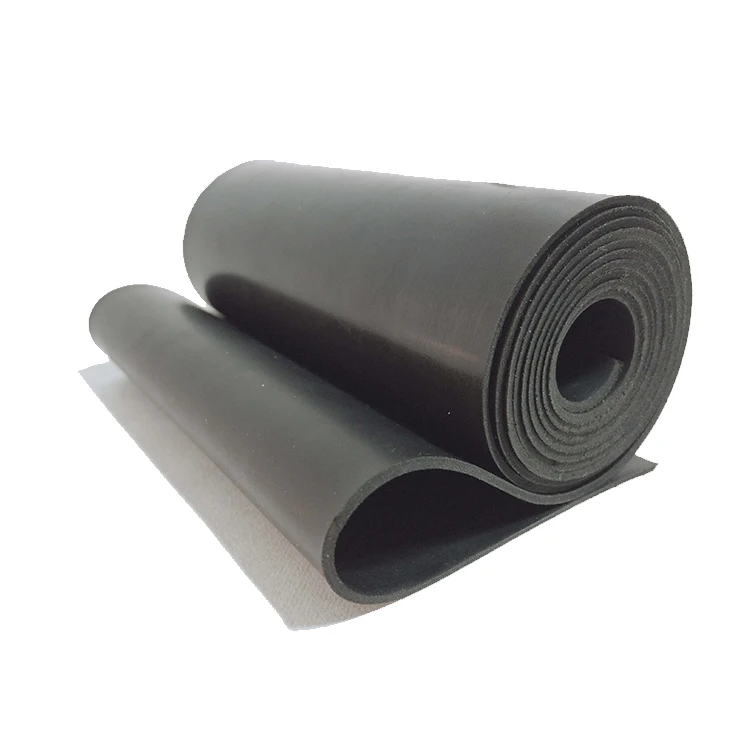
Изопрен
по
износоустойчивости
превосходит натуральный каучук. Изопрен
используют в основном при изготовлении
обуви, перчаток и рукояток некоторых
ножей
Основными свойствами бутадиена
стирольный
являются:
высокая
прочность, сопротивление раздиру,
эластичность и износостойкость
Применяются для большинства
резиновых изделий (в том числе для
изготовления жевательных резинок)
Этот каучук считают лучшим каучуком
общего назначения благодаря отличным
свойствам
высокой
стойкости
к
истиранию и высокому проценту
наполняемости
Основное достоинства резин из
бутилкаучука – стойкость к
действию многих агрессивных
сред, в том числе щелочей,
перекиси водорода, некоторых
растительных масел, высокие
диэлектрические
свойства.
Важнейшая область применения
бутилкаучука – производство шин.
Кроме
того,
бутилкаучук
применяют
в
производстве
различных резиновых изделий,
стойких к действию высоких
температур и агрессивных сред,
прорезиненных тканей
Этилен-пропиленовый
каучук
подходит для производства шлангов,
изоляции,
противоскользящих
профилей, сильфонов
Одной из многочисленных областей
применение являются покрытия для
открытых спортивных и детских
площадок
Эти каучуки имеют два значительных
недостатка.
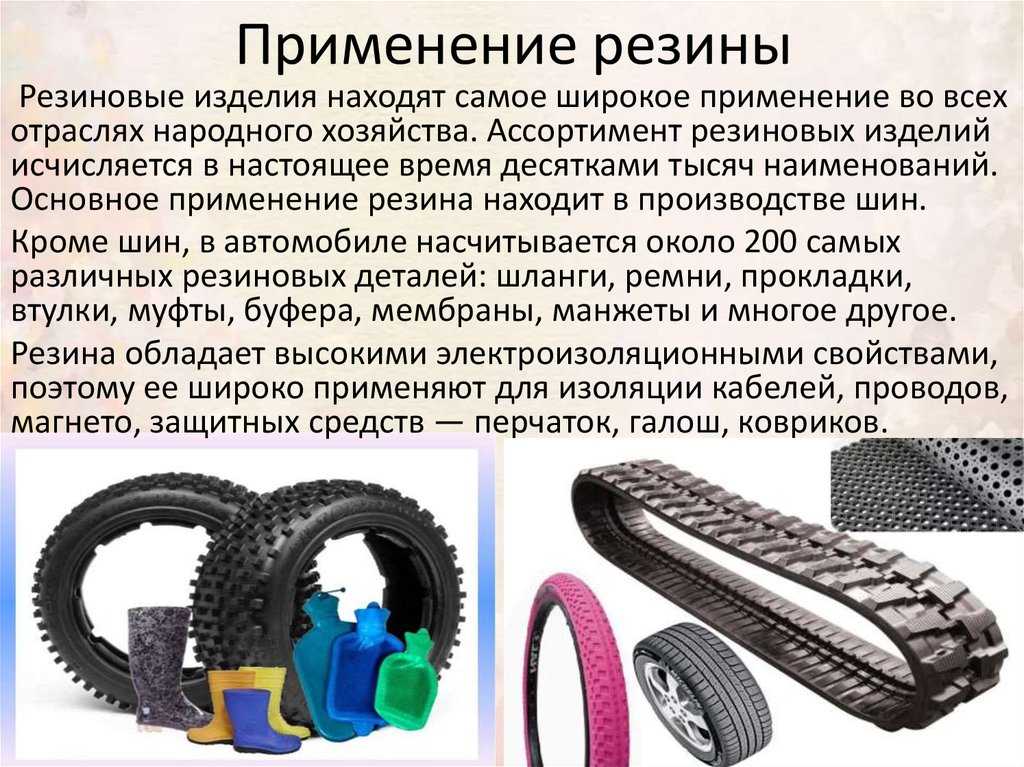
другими простыми каучуками и неустойчивы
[-Ch3-CH=CH-Ch3-]n – [-Ch3-CH(CN)-]m
Бутадиен-нитрильный
каучук
синтетический полимер, продукт
сополимеризации
бутадиена
с
акрилнитрилом
очень хорошая стойкость к маслам и
бензинам
стойкость к нефтяным гидравлическим
жидкостям
стойкость
растворителям
к
углеродистым
стойкость к щелочам и расворителям
широкий диапазон рабочих : от -57°C до
+120°C.
низкая стойкость к озону,
солнечному свету и естественным
окислителям
плохая стойкость к окисленным
растворителям
Хлоропреновый каучук светло-желтая масса
эластичная
Хлоропреновый
каучук
кристаллизуется
при
растяжении, благодаря чему резины на его основе имеют
высокую прочность.
Используется для производства резино-технических
изделий: конвейерных лент, ремней, рукавов,
шлангов,
водолазных
костюмов,
электроизоляционных материалов.
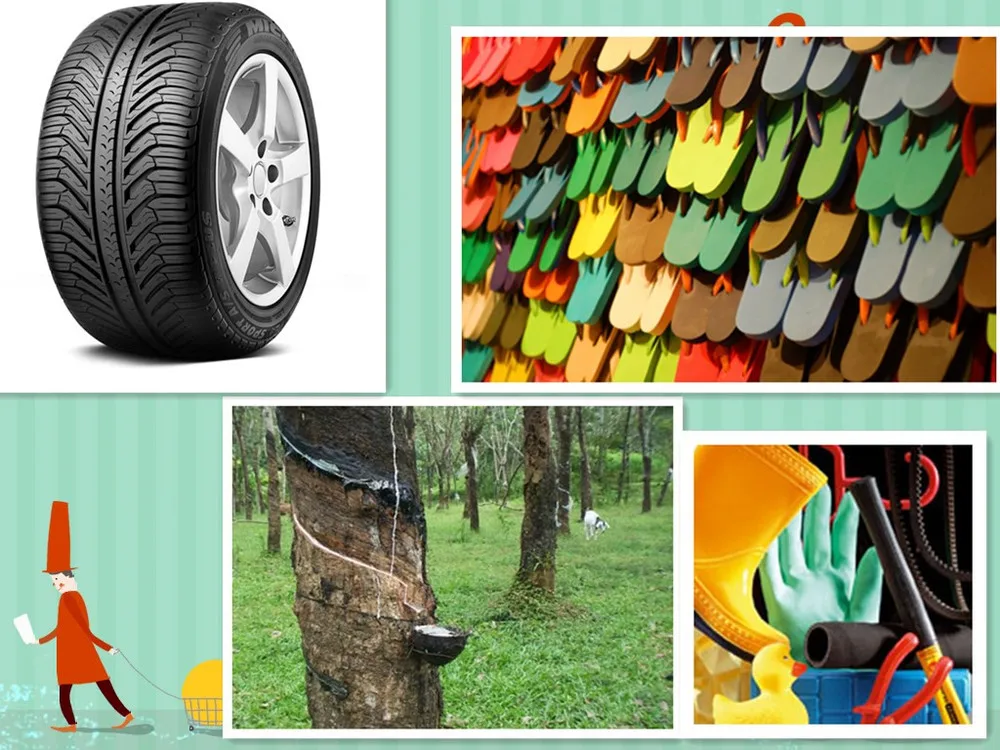
также оболочки проводов и кабелей, защитные
покрытия. Важное промышленное значение имеют
клеи и хлоропреновые латексы
Силоксановые
резины
обладают
комплексом
уникальных
свойств:
повышенными термо-, морозо- и
огнестойкостью,
сопротивлением
накоплению остаточной деформации
сжатия и т. д.
Они применяются в весьма важных
областях техники, а относительно
высокая их стоимость окупается более
длительным сроком эксплуатации по
сравнению с резинами на основе
углеводородных каучуков
English Русский Правила
Синтетическая резина – Большая Энциклопедия Нефти и Газа, статья, страница 1
Cтраница 1
Синтетические резины менее, чем естественные резины, подвержены разбуханию в присутствии масла и большинства растворителей. [1]
Синтетические резины широко применяют для изготовления уплотнений, препятствующих утечке масла из картеров зубчатых редукторов.
Синтетическая резина хуже естественной по сопротивляемости разрыву, но меньше набухает при соприкосновении с маслом, чем естественная. [3]
Синтетические резины значительно более устойчивы к действию ультрафиолетовых лучей. Свет не оказывает заметного влияния на поверхность дерева, но продолжительная эксплуатация деталей, изготовленных из дерева, при облучении их ультрафиолетовыми лучами может привести к некоторым изменениям поверхностных слоев древесины. [4]
Синтетическая резина СКН-40 ( бутадиеннитрильный каучук) также относится к бензостойким материалам и может применяться для облицовкл резервуаров. [5]
Размеры канавок для динамических уплотнений топливных систем.![]() |
Обычные синтетические резины или смеси буна N, буна S, неопрен, бутил, каучук и натуральная резина обладают характеристиками, позволяющими изготовлять детали формовым способом с использованием стандартного оборудования. Однако разработанные совсем недавно синтетические резины, а также большинство силиконовых материалов, имеют на 3 – 5 % большую усадку, чем стандартные резины. В этих случаях О-образные кольца, отформованные из новых материалов на имеющемся оборудовании, имеют размеры на 3 – 5 % меньше, чем предусмотренные стандартом. Материалы с большой усадкой – это силиконы, витон, фтористые силиконы и полиакрилаты. [7]
Разрыв синтетической резины происходит значительно легче, чем естественной. [8]
Марка синтетической резины, которая берется для тканево-резиновых манжет, зависит от рабочей среды и температуры. Наиболее обычными базовыми полимерами являются полихлоро-прен, буна N, буна S, бутил и витон. Полихлоропрен и буна N применяются для уплотнения масел, буна S – для воды, бутил – при уплотнении сложных эфиров фосфорной кислоты. Витон используется в условиях высоких рабочих температур.
[9]
Конструктивные варианты манжетных уплотнений. [10] |
Уплотнения из синтетических резин могут работать в масляной среде при окружных скоростях на поверхности трения до 20 м / сек. Однако применять высокие скорости и температуры без крайней необходимости не рекомендуется, так как это снижает надежность уплотнения. [11]
Вращающийся скребок для труб большого диаметра фирмы Дженерал. [12] |
Шары из синтетической резины изготавливаются полыми. В корпусе устанавливается клапан /, через который закачивается жидкость с таким расчетом, чтобы диаметр шара превысил на 2 % внутренний диаметр трубы.
[13]
Уплотнения из синтетических резин могут работать при окружных скоростях на поверхности трения до 20 м / сек, а в отдельных случаях и до 25 м / сек. В зависимости от сорта резины они могут быть пригодны также для работы при температурах на поверхности трения выше 150 С. Так, например, манжеты из силиконовой резины допускают при скорости 25 м / сек температуру 180 С. [14]
Коэффициент трения синтетической резины по металлу обычно увеличивается с увеличением скорости. От чистоты уплотняемой поверхности коэффициент трения зависит мало, но чистота поверхности существенно влияет на износ уплотнителей. [15]
Страницы: 1 2 3 4
Программа синтетического каучука США – Национальный исторический памятник химической промышленности
Посвящен 29 августа 1998 г. Акронскому университету в Акроне, штат Огайо, и следующим корпорациям-участникам: The Firestone Tire & Rubber Company, The BF Goodrich Company, The Goodyear Tire & Резиновая компания, Стандартная нефтяная компания Нью-Джерси, Резиновая компания Соединенных Штатов.
Памятный буклет (PDF)
Когда в начале Второй мировой войны прекратились поставки натурального каучука из Юго-Восточной Азии, Соединенные Штаты и их союзники столкнулись с потерей стратегического материала. При поддержке правительства США консорциум компаний, занимающихся исследованиями и производством каучука, объединился в уникальном духе технического сотрудничества и стремления производить синтетический каучук общего назначения GR-S (государственный каучук-стирол) в промышленных масштабах. В Акроне и других местах США эти компании в сотрудничестве с сетью исследователей в государственных, академических и промышленных лабораториях разработали и произвели в рекордно короткие сроки синтетический каучук в количестве, достаточном для удовлетворения потребностей США и их союзников во время Второй мировой войны.
Содержимое
- Quest for Synthetic Rubber
- История натурального каучука
- Первые исследования синтетического каучука
- Истоки производства синтетического каучука в США
- Реакция США на кризис с поставками каучука во время Второй мировой войны: компания Rubber Reserve
- Партнерство промышленности, академических кругов и правительства решает кризис предложения каучука
- Дополнительное чтение
- Обозначение достопримечательности и благодарность
- Процитировать Страница
В поисках синтетического каучука
Поиск материалов, которые могут заменить природные вещества, уже давно является проблемой для химиков. К 1914 году натуральные красители из растений были заменены синтетическими красителями, полученными из каменноугольной смолы, целлулоид заменил слоновую кость, а бакелит заменил шеллак на основе насекомых. Тем не менее, эти продукты были произведены в относительно небольших масштабах.
Натуральный каучук, напротив, имел огромное экономическое и военное значение. Автомобили, ключевой элемент американской общественной жизни, не могли двигаться без резиновых шин, и к 19В 30-е годы автомобильная промышленность США быстро выросла до размеров, не имеющих себе равных. Современная нация не может надеяться защитить себя без каучука. На постройку военного самолета ушло полтонны каучука; танку нужно было около одной тонны, а линкору – 75 тонн. Каждому военнослужащему требовалось 32 фунта резины для обуви, одежды и снаряжения. Шины были необходимы для всех видов транспортных средств и самолетов.
Американская резиновая промышленность стала крупнейшей и самой технологичной в мире. К концу 1930-х годов Соединенные Штаты использовали половину мировых запасов натурального каучука, большая часть которого поступала из Юго-Восточной Азии.
Нехватка натурального каучука, вызванная началом Второй мировой войны, побудила правительство США приступить к реализации программы по быстрому и крупномасштабному производству заменителя этого важного материала. Существовала реальная опасность, что война будет проиграна, если американские ученые и технологи не смогут заменить почти миллион тонн натурального каучука синтетическим заменителем в течение 18 месяцев.
Чтобы сотворить это промышленное и научное чудо, правительство США объединило усилия с каучуковыми компаниями, молодой нефтехимической промышленностью и университетскими исследовательскими лабораториями. Получившаяся в результате программа синтетического каучука стала выдающимся научным и инженерным достижением. Благодаря партнерству правительства, промышленности и научных кругов производство синтетического каучука в США увеличилось с 231 тонны каучука общего назначения в год в 1941 г. до 70 000 тонн в месяц в 1945 г.
Воздействие на резиновую промышленность оказалось необратимым. Сегодня 70 процентов каучука, используемого в производственных процессах, является синтетическим и является потомком синтетического GR-S общего назначения (государственный каучук-стирол), производимого Соединенными Штатами в таком большом количестве во время Второй мировой войны.
Вернуться к началу
История натурального каучука
Натуральный каучук известен на протяжении веков. Французский исследователь Шарль-Мари де ла Кондамин сообщил в 1745 году, что южноамериканские индейцы использовали его для изготовления обуви и бутылок. Его получают в основном из латекса каучукового дерева, произрастающего в Южной Америке.
Резина получила свое название после появления в Европе и использования ее для стирания карандашных следов. Вскоре его назвали (индийским) «каучуком».
Первым основным применением каучука была ткань для воздушных шаров, ткань, покрытая каучуком, растворенным в скипидаре. В 1823 году Чарльз Макинтош, используя нафту, лучший растворитель, склеил липкую резиновую ткань и ткань вместе, чтобы сделать плащи.
Хотя резина привлекла внимание публики, возникли проблемы. Резина сильно замерзала зимой и плавилась летом. В начале 1830-х годов был большой спрос на товары, изготовленные из этой водостойкой резинки, но «резиновая лихорадка» резко закончилась из-за неудач продукции.
Чарльз Гудиер открыл способ вулканизации натурального каучука, чтобы сделать его более полезным. Работая на кухонной плите в 1839 году, он смешал каучук с серой и свинцовыми белилами. Этот процесс, вулканизация, сделал резину более устойчивой к изменениям температуры и ускорил рост резиновой промышленности.
К 1910 году азиатские каучуковые плантации, зародившиеся из семян, привезенных из бассейна Амазонки, вытеснили каучук с диких деревьев Южной Америки и стали основным источником растущего рынка.
Вернуться к началу
Ранние исследования синтетического каучука
Майкл Фарадей в 1829 году показал, что каучук имеет эмпирическую формулу C 5 H 8 . В 1860 году Гревилл Уильямс получил жидкость с той же формулой путем перегонки каучука; он назвал это «изопреном». Технология синтетического каучука началась в 1879 году, когда Гюстав Бушарда обнаружил, что при нагревании изопрена с соляной кислотой образуется каучукоподобный полимер. Однако Бушарда получил изопрен из натурального каучука; первый по-настоящему синтетический каучук был изготовлен Уильямом Тилденом три года спустя. Тильден получил изопрен путем крекинга скипидара, но процесс его превращения в каучук занял несколько недель. В 1911 Фрэнсис Мэтьюз и Карл Харрис независимо друг от друга обнаружили, что изопрен может полимеризоваться быстрее с помощью натрия.
В 1906 году ученые компании Bayer в Германии приступили к реализации программы по производству синтетического каучука. К 1912 году они производили метиловый каучук, полученный путем полимеризации метилизопрена. Метиловый каучук производился в больших масштабах во время Первой мировой войны, когда блокада остановила импорт натурального каучука в Германию. Поскольку метиловый каучук был дорогой и некачественной имитацией, в конце войны его производство было прекращено.
На протяжении 1920-х годов исследования синтетического каучука находились под влиянием колебаний цен на натуральный каучук. Цены в целом были низкими, но ограничения на экспорт натурального каучука из Британской Малайи, введенные британцами в 1922 году, в сочетании с последующим повышением цен вызвали создание скромных программ исследований синтетического каучука в Советском Союзе, Германии и Соединенных Штатах между 1925 г. и 1932.
Исследователи из I.G. Farben, немецкого конгломерата, в который входила Bayer, сосредоточились на натриевой полимеризации мономера бутадиена для производства синтетического каучука под названием «Buna» («bu» для бутадиена и «na» для натрия, химического вещества). символ натрия). Они обнаружили в 1929 видно, что Buna S (бутадиен и стирол, полимеризованные в эмульсии) в смеси с сажей значительно прочнее натурального каучука.
Вернуться к началу
Истоки производства синтетического каучука в США
Благодаря своим рабочим отношениям с I. G. Farben гигантская нефтяная компания Standard Oil of New Jersey (Jersey Standard) была важным посредником в трансатлантических перевозках технологии синтетического каучука. В начале 1930-х годов химики Jersey Standard начали исследования и разработки по производству бутадиена из нефти. Их работа включала дегидрирование — реакцию, которая удаляет атомы водорода из молекул углеводородов. Открытие катализаторов для ускорения реакции, наряду с процедурами очистки и модификациями процессов, позволило наладить крупномасштабное производство бутадиена. Компания под руководством Фрэнка А. Ховарда заключила соглашения с I. G. Farben и через Совместную американскую исследовательскую компанию обменивалась технической информацией по синтетическому каучуку и другим разработкам. Jersey Standard также имела ограниченные права на разработку Buna S и управляла патентами в Соединенных Штатах после начала войны в Европе в 1919 году.39. Поскольку GR-S похож на Buna S, эта технология оказалась решающей для решения каучукового кризиса, с которым столкнулись Соединенные Штаты во время Второй мировой войны.
В Соединенных Штатах в исследованиях и разработках по производству универсального заменителя натурального каучука доминировала большая четверка каучуковых компаний: The Firestone Tire & Rubber Company (Bridgestone/Firestone, Inc.), The B. F. Goodrich Company, The Goodyear Tire & Rubber Company и United States Rubber Company (Uniroyal Chemical Company, Inc.). Их коллективные технические знания сыграли важную роль в успешном завершении программы синтетического каучука.
Результатом работы двух русских ученых, работавших в United States Rubber Company, Александра Д. Максимова и Ивана Остромисленского, стали патенты 1920-х годов на эмульсионную полимеризацию бутадиена, а также стирола. Ученые компании BF Goodrich под руководством химика Уолдо Л. Семона построили экспериментальную установку производительностью 100 фунтов в день для сополимеризации бутадиена с метилметакрилатом для производства каучука для шин. Полученный продукт «Америпол» был представлен в 1940. Рэй П. Динсмор из Goodyear запатентовал «Chemigum», синтетический каучук, производимый в Акроне, штат Огайо, в том же году. Джеймс Д. Д’Ианни, также работавший в Goodyear, провел обширные исследования по синтезу различных мономеров, которые можно было бы полимеризовать с бутадиеном. Джон Стрит руководил программой Firestone по полимеризации бутадиена и стирола и построил экспериментальный завод по производству синтетического каучука для производства шин. Тем не менее, натуральный каучук оставался основой производства в США.
Наверх
Реакция США на кризис поставок каучука во время Второй мировой войны: компания Rubber Reserve
Президент Франклин Д. Рузвельт хорошо знал об уязвимости США из-за их зависимости от поставок натурального каучука под угрозой, и в июне 1940 года он сформировал Rubber Reserve Company ( РКР). RRC поставил задачи по накоплению каучука, экономии использования каучука в шинах путем установления ограничений скорости и сбору резинового лома для утилизации.
Начало Второй мировой войны отрезало США доступ к 90 процентов поставок натурального каучука. В то время в Соединенных Штатах был запас около одного миллиона тонн натурального каучука, уровень потребления около 600 000 тонн в год и не было коммерческого процесса производства синтетического каучука общего назначения. Мероприятия по сохранению, восстановлению и накоплению запасов не могли заполнить пробел в потреблении каучука.
После прекращения поставок натурального каучука RRC призвала четыре крупные каучуковые компании производить 400 000 тонн синтетического каучука общего назначения в год. 19 декабря, 1941 г., Jersey Standard, Firestone, Goodrich, Goodyear и United States Rubber Company подписали соглашение о патентах и обмене информацией под эгидой RRC.
Ситуация стала еще более критической, так как потребность в каучуке для военных нужд возросла. Поскольку запасы каучука истощались и возникали конфликты по поводу наилучшего технического направления, Рузвельт в августе 1942 года назначил Комитет по обследованию каучука для расследования и вынесения рекомендаций по разрешению кризиса. В комитет, возглавляемый финансистом Бернардом М. Барухом, также входили ученые Джеймс Б. Конант, президент Гарвардского университета, и Карл Т. Комптон, президент Массачусетского технологического института.
В удивительно короткий срок, всего в один месяц, комитет Баруха вынес свои рекомендации, две из которых имели решающее значение для разрешения каучукового кризиса: назначение директора по каучуку, который имел бы полную власть над поставками и использованием каучука, и немедленное строительство и эксплуатация 51 завода по производству мономеров и полимеров, необходимых для производства синтетического каучука. Уильям М. Джефферс, президент Union Pacific Railroad, был первым директором по каучуку, Брэдли Дьюи, президент Dewey and Almey, был заместителем, а Люциус Д. Томпкинс, вице-президент United States Rubber Company, помощником заместителя. .
Вернуться к началу
Партнерство между промышленностью, академическими кругами и правительством решает кризис предложения каучука
Технология, выбранная для производства синтетического каучука, была основана на исследованиях Buna S, поскольку Buna S можно смешивать с натуральным каучуком и измельчать на тех же машинах, и потому что сырье (мономеры) было доступно. Эта резина особенно подходила для изготовления протекторов шин, поскольку устойчива к абразивному износу; и он сохранял более четкие отпечатки в формах, каландрах и экструдерах, чем натуральный каучук. Однако синтетический каучук было труднее изготовить, он имел меньшую липкость и требовал большего количества клея для изготовления шины, чем натуральный каучук. Эти проблемы необходимо было решить для производства надежной резины общего назначения.
26 марта 1942 года представители компаний и правительства США согласовали «общий рецепт» производства каучука GR-S. Рецептура состояла из мономеров бутадиена (75%) и стирола (25%), персульфата калия в качестве катализатора или инициатора, мыла в качестве эмульгатора, воды и модификатора додецилмеркаптана. Поскольку для GR-S требуются другие условия смешивания, ускорители, антиоксиданты, типы и количества технического углерода, чем для натурального каучука, руководители программы поняли, что для решения существующих и потенциальных проблем производства GR-S потребуется программа исследований и разработок.
Роберт Р. Уильямс из Bell Telephone Laboratories организовал и координировал исследования в области каучуковой промышленности, в которых участвовали Национальное бюро стандартов, Bell Labs и такие крупные исследовательские университеты, как Университет Иллинойса, Университет Миннесоты и Университет штата Нью-Йорк. Чикаго. Первое из многих заседаний Комитета по исследованию сополимеров состоялось 29 декабря 1942 года в Акроне, штат Огайо, для обмена последней информацией между организациями, работающими над различными аспектами исследований синтетического каучука. Помимо представителей правительства, крупных компаний и университетов, в работе приняли участие представители Columbian Carbon Company, Школы прикладных наук Кейса (ныне Университет Кейс Вестерн Резерв), Принстонского университета и Университета Акрона. Принадлежность участников этой встречи свидетельствует о широком участии в программе. На более поздних встречах присутствовали представители Phillips Petroleum, General Tire, Polymer Corporation и Корнельского университета.
В ходе совместных усилий компании поделились результатами более 200 патентов. Участвующие американские ученые и инженеры улучшили процесс полимеризации, произвели модификаторы, которые позволили существующему технологическому оборудованию уравнять производительность натурального каучука, определили марки технического углерода для конкретных применений и модифицировали производство бутадиена для повышения эффективности. Лаборатории университета разработали более совершенные аналитические методы для улучшения контроля качества и провели фундаментальные исследования механизма полимеризации GR-S и химической структуры каучука. Академические и промышленные участники разъяснили факторы, влияющие на скорость полимеризации, молекулярную массу полимера и весовое распределение.
У каучуковых компаний были технологии и ответственность за строительство заводов по производству синтетического каучука. Правительство предоставило не менее важную составляющую — капитал. У. И. Берт, инженер BF Goodrich, возглавлял комитет, который спроектировал и построил первый государственный завод GR-S. Уолтер Пиггот, также из Goodrich, возглавлял инженерный комитет по производству GR-S.
По стране было разбросано несколько заводов, одни по полимеризации, другие по производству мономеров. Первые заводы были построены и введены в эксплуатацию в рекордно короткие сроки — девять месяцев.
Firestone произвела первый тюк синтетического каучука в рамках программы 26 апреля 1942 года, за ним последовали Goodyear 18 мая, United States Rubber Corporation 4 сентября и Goodrich 27 ноября. В 1942 году эти четыре завода произвели 2241 тонну синтетического каучука. . К 1945 году Соединенные Штаты производили около 920 000 тонн синтетического каучука в год, 85 процентов которого составлял каучук GR-S. Из этих 85 процентов четыре основные компании производили 547 500 тонн в год (70%).
Продолжались исследования после окончания войны 19 августа45. Синтетический каучук был усовершенствован и, после того как заводы военного времени снова служили во время Корейского конфликта, стал неотъемлемой частью каучуковой промышленности. Производство GR-S вернулось в частные руки в 1955 году, когда правительство продало заводы. По мере того, как 20-й век подходит к концу, резиновая промышленность выросла до международного предприятия стоимостью 60 миллиардов долларов с примерно 15 000 предприятий, работающих в Соединенных Штатах. Синтетический каучук является жизненно важной частью транспортной, аэрокосмической, энергетической, электронной и потребительской промышленности.
Вернуться к началу
Дополнительная литература
- История химии каучука, науки о полимерах и инженерии полимеров (Акронский университет)
Наверх
Обозначение ориентира и признание
Обозначение ориентира
Американское химическое общество присвоило Программе США по синтетическому каучуку статус национального исторического химического памятника на церемонии, состоявшейся 29 августа 1998 г. в Акронском университете в Акроне, штат Огайо. Дополнительные плакетки были вручены пяти перечисленным ниже компаниям, участвовавшим в разработке каучука GR-S. Текст мемориальной доски, посвященной программе, гласит:
Когда в начале Второй мировой войны прекратились поставки натурального каучука из Юго-Восточной Азии, Соединенные Штаты и их союзники столкнулись с потерей стратегического материала. При поддержке правительства США консорциум компаний, занимающихся исследованиями и производством каучука, объединился в уникальном духе технического сотрудничества и стремления производить синтетический каучук общего назначения GR-S (государственный каучук-стирол) в промышленных масштабах. В Акроне и других местах США эти компании в сотрудничестве с сетью исследователей в многочисленных государственных, академических и промышленных лабораториях разработали и произвели в рекордно короткие сроки синтетический каучук, достаточный для удовлетворения потребностей США и их союзников во время Второй мировой войны. :
The Firestone Tire & Rubber Company
The B.F. Goodrich Company
The Goodyear Tire & Rubber Company
Standard Oil Company of New Jersey
United States Rubber Company
Program, 1939-1945», созданной Американским химическим обществом в 1998 году в рамках программы «Национальные исторические химические памятники».

Национальные исторические химические памятники Американского химического общества. Программа синтетического каучука США. http://www.acs.org/content/acs/en/education/whatischemistry/landmarks/syntheticrubber.html (по состоянию на месяц, день, год).
Наверх
Вернуться на главную страницу National Historic Chemical Landmarks .
Дополнительная информация: О программе Landmarks .
Примите меры: Назначьте достопримечательность и свяжитесь с координатором NHCL .
Мы были бы слепы, если бы не видели предпринимаемые в настоящее время усилия многих компаний принять участие в развитии новой крупной отрасли с огромными послевоенными возможностями». Комитет, 10 сентября 1942 г.
Резина | Тропические растения, нефть и природный газ
грузовые шины извлекаются из пресс-форм
Посмотреть все СМИ
- Ключевые люди:
- Тан Ченг Лок
Пол В.
Личфилд Генри Николас Ридли Джованни Баттиста Пирелли Карл Дитрих Харрис
- Связанные темы:
- полиизопрен латекс вулканизация гуттаперча поролон
Просмотреть весь связанный контент →
Резюме
Прочтите краткий обзор этой темы
каучук эластичное вещество, полученное из экссудации некоторых тропических растений (натуральный каучук) или полученное из нефти и природного газа (синтетический каучук). Из-за своей эластичности, устойчивости и прочности резина является основным компонентом шин, используемых в автомобильных транспортных средствах, самолетах и велосипедах. Более половины всего производимого каучука идет на автомобильные шины; остальное идет на механические детали, такие как крепления, прокладки, ремни и шланги, а также на потребительские товары, такие как обувь, одежда, мебель и игрушки.
Основными химическими компонентами каучука являются эластомеры, или «эластичные полимеры», большие молекулы, похожие на цепи, которые могут растягиваться на большие длины и при этом восстанавливать свою первоначальную форму. Первым распространенным эластомером был полиизопрен, из которого изготавливают натуральный каучук. Натуральный каучук, образующийся в живом организме, состоит из твердых частиц, взвешенных в жидкости молочного цвета, называемой латексом, которая циркулирует во внутренних частях коры многих тропических и субтропических деревьев и кустарников, но преимущественно 9.0217 Hevea brasiliensis , высокое дерево хвойных пород, происходящее из Бразилии. Натуральный каучук был впервые научно описан Шарлем-Мари де Ла Кондамин и Франсуа Френо из Франции после экспедиции в Южную Америку в 1735 году. Английский химик Джозеф Пристли дал ему название «каучук» в 1770 году, когда обнаружил, что им можно стирать карандаши. Метки. Большой коммерческий успех пришел к нему только после того, как в 1839 году Чарльз Гудиер изобрел процесс вулканизации.
Натуральный каучук и сегодня продолжает занимать важное место на рынке; его устойчивость к накоплению тепла делает его ценным для шин, используемых на гоночных автомобилях, грузовиках, автобусах и самолетах. Тем не менее, он составляет менее половины промышленно производимого каучука; остальное — каучук, полученный синтетическим путем с помощью химических процессов, которые были частично известны в 19 веке.го века, но не применялись в коммерческих целях до второй половины 20 века, после Второй мировой войны. К наиболее важным синтетическим каучукам относятся бутадиеновый каучук, бутадиен-стирольный каучук, неопрен, полисульфидные каучуки (тиоколи), бутилкаучук и силиконы. Синтетические каучуки, как и натуральные каучуки, могут быть усилены вулканизацией, улучшены и модифицированы для специальных целей путем армирования другими материалами.
Основные свойства полимеров, используемых для производства основных товарных каучуков, приведены в таблице.
Викторина «Британника»
Строительные блоки предметов повседневного обихода
тип полимера | температура стеклования (°C) | температура плавления (°С) | термостойкость* | маслостойкость* | сопротивление изгибу* | типичные продукты и области применения |
---|---|---|---|---|---|---|
*E = отлично, G = хорошо, F = удовлетворительно, P = плохо.![]() | ||||||
полиизопрен (натуральный каучук, изопреновый каучук) | −70 | 25 | п | п | Е | шины, пружины, обувь, клеи |
стирол-бутадиеновый сополимер (стирол-бутадиеновый каучук) | −60 | п | п | г | протекторы шин, клеи, ремни | |
полибутадиен (бутадиеновый каучук) | −100 | 5 | п | п | Ф | протекторы шин, обувь, конвейерные ленты |
акрилонитрил-бутадиеновый сополимер (нитриловый каучук) | от −50 до −25 | г | г | Ф | прокладки топливных шлангов, ролики | |
изобутилен-изопреновый сополимер (бутилкаучук) | −70 | −5 | Ф | п | Ф | покрышки, оконные рейки |
этилен-пропиленовый мономер (EPM), этилен-пропилен-диеновый мономер (EPDM) | −55 | Ф | п | Ф | гибкие уплотнения, электрическая изоляция | |
полихлоропрен (неопрен) | −50 | 25 | г | г | г | шланги, ремни, пружины, прокладки |
полисульфид (тиокол) | −50 | Ф | Е | Ф | уплотнения, прокладки, ракетное топливо | |
полидиметилсилоксан (силикон) | −125 | −50 | г | Ф | Ф | уплотнения, прокладки, хирургические имплантаты |
фторэластомер | −10 | Е | Е | Ф | Уплотнительные кольца, уплотнения, прокладки | |
полиакрилатный эластомер | от -15 до -40 | г | г | Ф | шланги, ремни, уплотнения, ткани с покрытием | |
полиэтилен (хлорированный, хлорсульфированный) | −70 | г | г | Ф | Уплотнительные кольца, уплотнения, прокладки | |
стирол-изопрен-стирол (SIS), стирол-бутадиен-стирол (SBS) блок-сополимер | −60 | п | п | Ф | автомобильные детали, обувь, клеи | |
Смесь EPDM-полипропилен | −50 | Ф | п | Ф | обувь, гибкие чехлы |
Каучуковое дерево
В промышленных масштабах натуральный каучук получают почти исключительно из Hevea brasiliensis, дерева, произрастающего в Южной Америке, где оно растет в диком виде до высоты 34 метров (120 футов). Однако выращиваемое на плантациях дерево вырастает только до 24 метров (80 футов), потому что углерод, необходимый для роста, также является важным компонентом каучука. Поскольку только атмосферный углекислый газ может поставлять растению углерод, этот элемент необходимо распределять между двумя потребностями, когда дерево находится в активном производстве. Кроме того, с листвой, ограниченной верхушкой дерева (для облегчения постукивания), потребление углекислого газа меньше, чем у дикого дерева. Другие деревья, кустарники и травянистые растения производят каучук, но поскольку ни одно из них не сравнится по эффективности с Hevea brasiliensis, Промышленные ботаники сосредоточили свои усилия исключительно на этом виде.
При выращивании гевеи , соблюдаются естественные контуры земли, деревья защищены от ветра. Покровные культуры, посаженные рядом с каучуковыми деревьями, удерживают дождевую воду на склоне и помогают удобрять почву, фиксируя атмосферный азот. Также используются стандартные методы садоводства, такие как выращивание в питомниках выносливых подвоев и прививка к ним, ручное опыление и вегетативное размножение (клонирование) для получения генетически однородного продукта.