Содержание никеля в стали в: справочник-сталь тонколистовая,
alexxlab | 04.01.1970 | 0 | Разное
справочник-сталь тонколистовая,
Что такое нержавеющая сталь?
Согласно Европейскому стандарту EN 10020, сталь — железо-углеродистый сплав, содержащий в составе менее 2 % углерода, материалы с более высоким углеродистым содержанием — названы чугуном (Табл. ниже).
Чугун |
Fe + C > 2% |
Углеродистая сталь |
Fe + C < 2% |
Спецсталь |
Fe + C < 2% + (Cr, Ni, Mo, и т.д.,)>5% |
Нержавеющая сталь |
Fe + C<1.2% + Cr>10.5% |
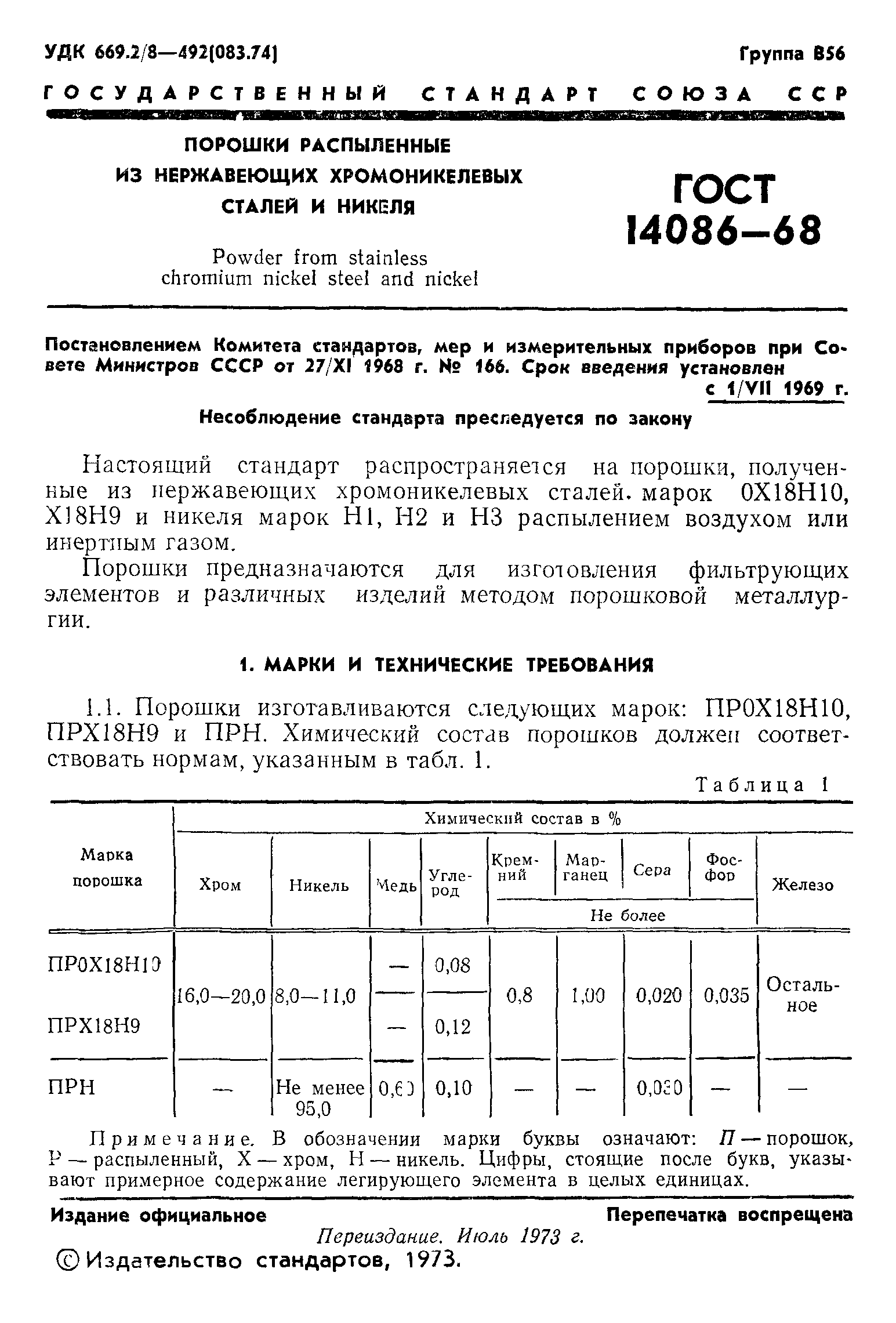
Нержавеющие стали — эту группу коррозиестойких сталей объединяет общая черта — содержание минимум 10.5 % хрома. Также могут присутствовать другие легирующие элементы — Никель, Молибден, Титан, Ниобий и др., так же определяющие свойства стали. Механические свойства и поведение в обслуживании различных типов зависят в первую очередь от их состава. Правильный выбор марки — гарантирует длительный и успешный срок службы стали. Постоянное увеличение использования нержавеющей стали в многих отраслях промышленности связано с ее выдающимися качествами: превосходного сопротивления коррозии, высокой прочности, хорошей свариваемости и легкости при холодной формовке.
Типы нержавеющих сталей
Cотношения между Ni и Cr для различных типов нержавеющих сталей. [PH steels — дисперсионно-упрочненные (закаленные) стали].
Есть пять основных категорий нержавеющей стали, основанных на их микроструктурах – Аустенитные (Austenitic), Ферритные (Ferritic), Дуплексные, Мартенситные (Martensitic), Жаропрочные — (Рис1). Сорта Аустенические — не магнитные и в дополнение к хрому, обычно на уровне на 18 %, содержат никель, который увеличивает сопротивление коррозии. Аустенитные нержавеющие стали — наиболее широко используемая группа нержавеющихсталей. С повышенным содержанием хрома, 20 % — 25 % и никеля, 10 % – 20 %, аустенитные нержавеющие стали – лучше сопротивляются окислению при высоких температурах и могут использоваться в частях печей, топках, муфельных печах: они называются жаропрочными сталями. Ферритные сорта — магнитные, имеют низкое углеродистое содержание и Хром как главный элемент, обычно на и уровне 13 % – 17 %. Дуплексные нержавеющие стали имеют смешанную, ферритно/аустенитную структуру.
Содержание хрома изменяется от 18 % до 28 % и никеля от 4. 5 % до 8 %. Дуплексные сорта находят свое применение в средах, где высокое содержание хлорида. Мартенситные сорта магнитные, содержат обычно 12 % хрома и умеренный уровень углерода. Они — упрочняются, закалкой и отпуском подобно простым углеродистым сталям, и находят поэтому применение главным образом в изготовлении столовых приборов, режущих инструментов и общем машиностроении. Упрочненные стали (Рис. 2) имеют содержание хрома обычно в 17 % с дополнениями никеля, меди и ниобия. Поскольку эти стали могут быть укреплены и хорошо сопротивляются процессу старения, они идеальны для шахтных насосов, шпинделей клапанов и космических компонентов.
Аустенитные и ферритные сорта составляют приблизительно 95 % среди используемых нержавеющих сталей.
Определение Марок
400 Мартенситные марки — Типичный сорт: 410
Хром (12-18 %), магнитный и может быть укреплен обработкой высокой температурой. Типичное использование: крепеж, соединительные детали, промышленные насосы
400 Ферритные марки — Типичный сорт: 430
Хром (12-18 %), “низкий” углерод, магнитный, но не высокая температура обработки. Типичное использование: бытовые приборы, отделка, кухонная утварь
200/300 Ряд Austenitic — Типичный сорт: 304
Хром (17-25 %)/Никель (8-25 %), немагнитный, не укрепленный высокой температурой. Имеет высокую прочность при холодной работе. Дополнения молибдена (до 7 %) могут увеличивать сопротивление коррозии. Типичное использование: пищевое оборудование, химическое оборудование, архитектурные применения
Дисперсионно укрепленные (закаленные) марки — Типичный сорт: 17-4
Хром (12-28 %)/ Никель (3-9 %), с добавлением Меди (3-4%) и Ниобия или Кобальта. Имеют мартенситную или аустенитную структуру. Укрепляются дисперсионным твердением в течение термообработки. Типичное использование: Клапаны, приводы, нефтехимическое оборудование
Дуплексные марки — Типичный сорт: 2205
Хром (18-25 %)/ Никель (4-7 %) и до 4 % молибдена. Более стойкие коррозии под давлением (напряжением), чем аустенитные, и все же достаточно жесткие, чем полностью ферритные сплавы. Типичное использование: Трубопроводы, камеры давления, котлы, силовые передачи, валы.
Выгоды от Нержавеющей стали
Срок службы
Когда рассматриваются полные затраты цикла жизни, нержавеющая сталь — часто наименее дорогой выбор.
Низкие Затраты Обслуживания
Нержавеющая сталь обычно лишь требует периодической очистки, с использованием домашних моющих средств и воды. Поверхности должны быть вымыты повторно водой и протерты. Следует использовать мягкую губку, не применяя абразивных паст.
Простота Изготовления
Современные методы металлообработки подразумевают, что Нержавеющая сталь может быть порезана, сварена, сформована и обработана так же как традиционные стали и другие материалы.
Сопротивление Коррозии
Более низкие сорта сопротивляются коррозии в нормальных атмосферных и водных средах, в то время как более высокие сорта могут сопротивляться коррозии во многих кислотах и щелочах, и некоторых хлористых растворах, присущих окружающим средам, типичных для многих обрабатывающих заводов.
Прочность
Механические свойства Нержавеющих сталей позволяют снизить толщины используемых материалов, таким образом сокращая вес без риска снижения прочностных характеристик. Аустенитные и Дуплексные сорта не теряют прочности и при низких температурах, при учете меньших толщин по сравнению с традиционными сортами. Таким образом достигается существенная экономия по отношению к альтернативным материалам.
Гигиена
Нержавеющая сталь признанна как наиболее гигиеническая поверхность для подготовки пищевых продуктов. Уникальность поверхности Нержавеющей стали в том, что она не имеет пор или трещин для проникновения грязи или бактерий. Это свойство простой очищаемости по отношению к другим поверхностям, делает Нержавеющая сталь первым выбором в строгих гигиенических условиях, например, больницах, общественных кухонь, скотобойнях, пищевого оборудования, перерабатывающих предприятиях АПК.
Эстетический внешний вид
Яркая, легко обслуживаемая поверхность нержавеющей стали обеспечивает привлекательный и современный внешний вид изделий, является идеальной для широкого и растущего диапазона архитектурных и декоративных приложений.
Нержавеющие стали — эту группу коррозиестойких сталей объединяет общая черта — содержание минимум 10.5 % хрома. Также могут присутствовать другие легирующие элементы — Никель, Молибден, Титан, Ниобий и др., так же определяющие свойства стали. Механические свойства и поведение в обслуживании различных типов зависят в первую очередь от их состава. Правильный выбор марки — гарантирует длительный и успешный срок службы стали. Постоянное увеличение использования нержавеющей стали в многих отраслях промышленности связано с ее выдающимися качествами: превосходного сопротивления коррозии, высокой прочности, хорошей свариваемости и легкости при холодной формовке.
Типы нержавеющих сталей
Cотношения между Ni и Cr для различных типов нержавеющих сталей. [PH steels — дисперсионно-упрочненные (закаленные) стали].
Есть пять основных категорий нержавеющей стали, основанных на их микроструктурах – Аустенитные (Austenitic), Ферритные (Ferritic), Дуплексные, Мартенситные (Martensitic), Жаропрочные — (Рис1). Сорта Аустенические — не магнитные и в дополнение к хрому, обычно на уровне на 18 %, содержат никель, который увеличивает сопротивление коррозии. Аустенитные нержавеющие стали — наиболее широко используемая группа нержавеющих сталей. С повышенным содержанием хрома, 20 % — 25 % и никеля, 10 % – 20 %, аустенитные нержавеющие стали – лучше сопротивляются окислению при высоких температурах и могут использоваться в частях печей, топках, муфельных печах: они называются жаропрочными сталями. Ферритные сорта — магнитные, имеют низкое углеродистое содержание и Хром как главный элемент, обычно на и уровне 13 % – 17 %. Дуплексные нержавеющие стали имеют смешанную, ферритно/аустенитную структуру.
Содержание хрома изменяется от 18 % до 28 % и никеля от 4.5 % до 8 %. Дуплексные сорта находят свое применение в средах, где высокое содержание хлорида. Мартенситные сорта магнитные, содержат обычно 12 % хрома и умеренный уровень углерода. Они — упрочняются, закалкой и отпуском подобно простым углеродистым сталям, и находят поэтому применение главным образом в изготовлении столовых приборов, режущих инструментов и общем машиностроении.
Аустенитные и ферритные сорта составляют приблизительно 95 % среди используемых нержавеющих сталей.
Определение Марок
400 Мартенситные марки — Типичный сорт: 410
Хром (12-18 %), магнитный и может быть укреплен обработкой высокой температурой. Типичное использование: крепеж, соединительные детали, промышленные насосы
400 Ферритные марки — Типичный сорт: 430
Хром (12-18 %), “низкий” углерод, магнитный, но не высокая температура обработки. Типичное использование: бытовые приборы, отделка, кухонная утварь
200/300 Ряд Austenitic — Типичный сорт: 304
Хром (17-25 %)/Никель (8-25 %), немагнитный, не укрепленный высокой температурой. Имеет высокую прочность при холодной работе. Дополнения молибдена (до 7 %) могут увеличивать сопротивление коррозии. Типичное использование: пищевое оборудование, химическое оборудование, архитектурные применения
Дисперсионно укрепленные (закаленные) марки — Типичный сорт: 17-4
Хром (12-28 %)/ Никель (3-9 %), с добавлением Меди (3-4%) и Ниобия или Кобальта. Имеют мартенситную или аустенитную структуру. Укрепляются дисперсионным твердением в течение термообработки. Типичное использование: Клапаны, приводы, нефтехимическое оборудование
Дуплексные марки — Типичный сорт: 2205
Хром (18-25 %)/ Никель (4-7 %) и до 4 % молибдена. Более стойкие коррозии под давлением (напряжением), чем аустенитные, и все же достаточно жесткие, чем полностью ферритные сплавы. Типичное использование: Трубопроводы, камеры давления, котлы, силовые передачи, валы.
Выгоды от Нержавеющей стали
Срок службы
Когда рассматриваются полные затраты цикла жизни, нержавеющая сталь — часто наименее дорогой выбор.
Низкие Затраты Обслуживания
Нержавеющая сталь обычно лишь требует периодической очистки, с использованием домашних моющих средств и воды. Поверхности должны быть вымыты повторно водой и протерты. Следует использовать мягкую губку, не применяя абразивных паст.
Простота Изготовления
Современные методы металлообработки подразумевают, что Нержавеющая сталь может быть порезана, сварена, сформована и обработана так же как традиционные стали и другие материалы.
Сопротивление Коррозии
Более низкие сорта сопротивляются коррозии в нормальных атмосферных и водных средах, в то время как более высокие сорта могут сопротивляться коррозии во многих кислотах и щелочах, и некоторых хлористых растворах, присущих окружающим средам, типичных для многих обрабатывающих заводов.
Прочность
Механические свойства Нержавеющих сталей позволяют снизить толщины используемых материалов, таким образом сокращая вес без риска снижения прочностных характеристик. Аустенитные и Дуплексные сорта не теряют прочности и при низких температурах, при учете меньших толщин по сравнению с традиционными сортами. Таким образом достигается существенная экономия по отношению к альтернативным материалам.
Гигиена
Нержавеющая сталь признанна как наиболее гигиеническая поверхность для подготовки пищевых продуктов. Уникальность поверхности Нержавеющей стали в том, что она не имеет пор или трещин для проникновения грязи или бактерий. Это свойство простой очищаемости по отношению к другим поверхностям, делает Нержавеющая сталь первым выбором в строгих гигиенических условиях, например, больницах, общественных кухонь, скотобойнях, пищевого оборудования, перерабатывающих предприятиях АПК.
Эстетический внешний вид
Яркая, легко обслуживаемая поверхность нержавеющей стали обеспечивает привлекательный и современный внешний вид изделий, является идеальной для широкого и растущего диапазона архитектурных и декоративных приложений.
Стали содержания никеля – Справочник химика 21
Никель, как и хром, применяется как легирующий элемент в сплавах. В низко- и среднелегированных сталях содержание никеля состав ляет около 3—4%. В нержавеющих, кислотостойких, жаропрочных, немагнитных и других сталях никеля содержится от 8 до 25%, а в некоторых сталях — до 35—80%. Сталь, содержащая 36% N1, 0,5% Мп и 0,5% С, является прекрасным материалом для изготовления различных точных приборов. Содержание никеля в некоторых сталях приведено в табл. 25. [c.304]Известно, что с увеличением в низколегированной стали содержания никеля уменьшается ее сопротивление коррозионному растрескиванию в сероводородсодержащих средах, однако существенное увеличение содержания никеля (до 30 %) делает углеродистые стали весьма устойчивыми против растрескивания, Однозначных данных о влиянии молибдена на стойкость сталей в сероводородсодержащих средах в литературе не обнаружено.
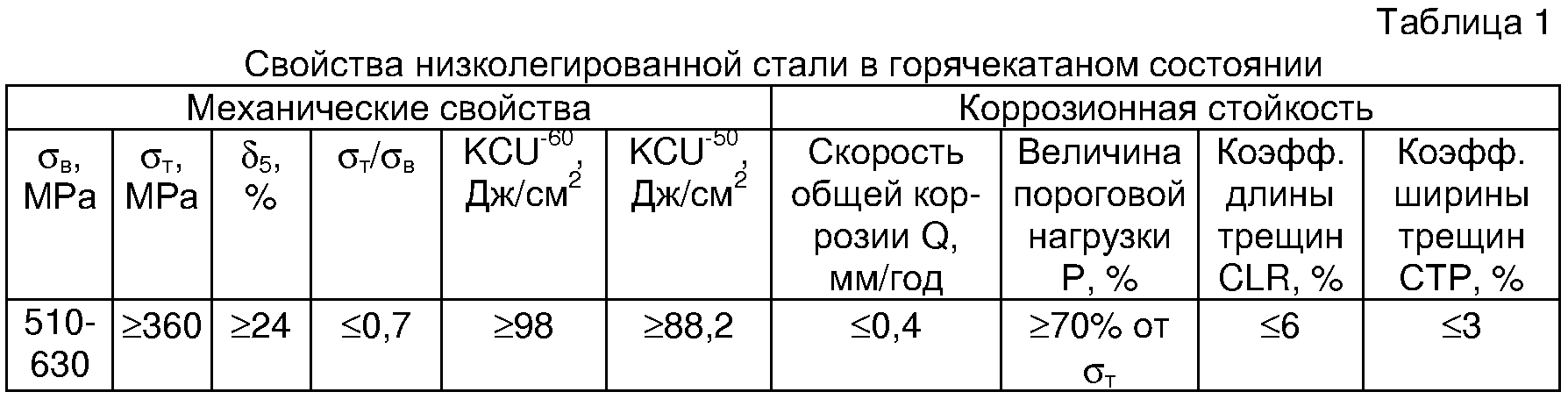
Определяют никель в стали. Содержание никеля около 5 %, осаждение проводят диметилглиоксимом. Весовая форма после высушивания — диметилглиоксимат никеля. При фильтровании через стеклянный фильтрующий тигель масса осадка должна составлять —0,2 г. [c.117]
Пример 3. Найти массу навески стали, необходимой для определения содержания никеля в стали. Содержание никеля составляет около 5%. Осаждают никель диметилглиоксимом. Весовая форма — диметилглиоксимат никеля. При фильтровании через стеклянный фильтрующий тигель масса осадка должна, составлять 0,2 г. [c.99]
Если одновременно присутствует более 12% хрома, то для получения кислотоупорных сталей содержание никеля может быть значительно уменьшено и доведено до 8—12%- Далее стойкость может быть еще более повышена присадкой 2—4% меди, например для защиты от серной кислоты, и при добавке 2—4% молибдена, например для защиты от разбавленной соляной кислоты [188]. [c.69]
При уменьшении в этих сталях содержания никеля в 2 раза с одновременным повышением содержания хрома до 21% кислотостойкость сплавов сохраняется. [c.38]
Непосредственное хромирование и особенно твердое хромирование легированных сталей, которое может потребоваться по соображениям износостойкости, не представляет особых трудностей. По данным Леви низколегированные стали [содержание никеля, хрома не многим более 5% (по массе)] могут быть актированы следующим образом [c.356]
Никель повышает крепость и вязкость сталей. Содержание никеля колеблется от 1,25 до 5%. Никелевые стали широко применяют для изготовления деталей, подвергающихся ударным и переменным нагрузкам. На практике для различных конструкций получили распространение хромоникелевые стали, так как такие стали обладают хорошей твердостью (от присадки хрома) и не хрупки (от присадки никеля), а также хорошо противостоят коррозии. [c.447]
Во время и после второй мировой войны считали, что предела возмоншо-стям эмиссионного спектрального анализа не существует. Полагали, что увеличение рабочего интервала длин волн позволит, помимо металлов, определять галогены и газы считали, что повышением дисперсии спектрографа, созданием сложных электрических источников света, использованием уравнений с большим числом поправочных членов и улучшением фотографических методов измерения интенсивности линий можно будет определить любую концентрацию любого элемента в любой основе. Однако все эти надежды не оправдались. Оказалось, что при содержании элементов выше нескольких процентов точность спектрального метода уже недостаточна для удовлетворения все возрастающих требований промышленности. Так, если в нержавеющей стали содержание никеля по техническим условиям должно составлять 8—9%, производитель, естественно, ради экономии будет ориентироваться на нин ний предел. Следовательно, чем точнее определено содержание никеля, тем ближе можно подойти к 8%, надежно удовлетворяя техническим условиям. [c.147]
Никель повышает механическую прочность и вязкость сталей. Содержание никеля в стали колеблется от 1,25 до 5%. Никелевые стали широко применяются для изготовления деталей, подвергающихся ударным и переменным нагрузкам. Для изготовления различных конструкций нередко используются хромоникелевые стали, обладающие хорошей твердостью (благодаря присадке хрома) и отсутствием хрупкости (вследствие присадки никеля), а также хорошо сопротивляющиеся коррозии. В самолетостроении и автотракторном машиностроении хромоникелевая сталь (1% Сг и 2—3% N1) применяется для изготовления пальцев поршней, шестерен, коллекторов, валов и других деталей двигателя. [c.148]
Примечание. Если в стали содержание никеля около или менее 0,20%, то для испытания берут 5 нл раствора А. При анализе стали можно использовать эталонные раствор , приготовленные в условиях, указанных для определения никеля в растворе чистой соли. Оптическую плотность в этом случав следует измерять используя в качестве нулевого раствора испытуемый раствор стали, в котором не проведена колориметрическая реакция (без добавления к нену диметилглиоксима, щелочи и окислителя). [c.34]
Устойчивые к коррозии материалы | Руководство по выбору материалов
Связаться с экспертомДоступ к экспертным сервисам
Нержавеющая сталь 316
Нержавеющая сталь
Во всех марках нержавеющей стали главными компонентами, отвечающими за коррозионную стойкость и пластичность металла, являются хром и никель. Добавление > 10 % хрома делает сталь нержавеющей, создавая на поверхности слой, содержащий большое количество оксида хрома. Этот слой образуется в результате реакции содержащегося в сплаве хрома с кислородом из атмосферного воздуха. Он придает стали свойство, которое делает ее нержавеющей. Добавление никеля обеспечивает хорошую пластичность и улучшенные свойства формовки и сварки.
Однако не все прутковые заготовки одинаковы. Содержание никеля и хрома в трубных обжимных фитингах и инструментальных кранах Swagelok из нержавеющей стали 316/316L превышает минимальные требования стандартов ASTM для прутков и поковок.
Следует учитывать, что хотя нержавеющая сталь разных марок и не подвержена сплошной коррозии, на ней может возникать местная коррозия.
Для борьбы со:
сплошной коррозией; водородным охрупчиванием; межкристаллитной коррозией
Материал имеет значение
Опасность коррозионного растрескивания под напряжением возрастает при высоких значениях концентрации хлоридов, температуры и растягивающих напряжений. Все марки нержавеющей стали подвержены коррозионному растрескиванию под напряжением. Мы провели испытания фитингов Swagelok для трубок под давлением на устойчивость к SCC и получили превосходные результаты.
Трубные обжимные фитинги и инструментальные краны Swagelok из нержавеющей стали 316 превышают минимальные требования стандартов ASTM.Cплавы 6Mo
Нержавеющая сталь
Сплавы 6-Moly (6Mo) представляют собой супераустенитную нержавеющую сталь, которая содержит не менее 6 % молибдена и имеет значение PREN (коэфф. устойчивости к точечной коррозии) не ниже 40. Сплав 6HN (UNS N08367) содержит на 6 весовых процентов больше никеля (Ni), чем сплав 254 (UNS S31254). Благодаря такому повышенному содержанию никеля сплав 6HN имеет повышенную стабильность с точки зрения формирования нежелательных интерметаллических фаз. Сплав 6HN проявил более высокую коррозионную стойкость в хлоридсодержащих средах по сравнению со сплавом 254.
- Устойчивость к точеной и щелевой коррозии под воздействием хлоридов.
- Устойчивость к коррозионному растрескиванию под напряжением (CSCC) под воздействием хлоридов.
- Предел текучести материала на 50 % выше, чем у аустенитных нержавеющих сталей серии 300.
- Ударная прочность, хорошая обрабатываемость и свариваемость.
- Возможность использования в среде высокосернистого газа (NACE MR0175/ISO 15156)
- Изделия Swagelok из сплава 6-Moly предлагаются из прутков и поковок 6HN (UNS N08367), соответствующих требованиям стандарта NORSOK M-650, регламентирующего поставщиков стали.
Для борьбы со:
сплошной коррозией; местной коррозией; коррозионным растрескиванием под напряжением
Сплав cупердуплексной нержавеющей стали 2507
Нержавеющая сталь
Дуплексная нержавеющая сталь имеет двухфазную микроструктуру, состоящую из зерен аустенита и феррита. Такая структура придает этим материалам сочетание привлекательных свойств, включая прочность, пластичность и коррозионную стойкость.
Сплав супердуплексной феррито-аустенитной нержавеющей стали 2507 отлично подходит для работы в высококоррозионных условиях. В ее состав входят никель, молибден, хром, азот и марганец, что обеспечивает превосходную устойчивость к сплошной, точечной и щелевой коррозии, коррозионному, а также растрескиванию под напряжением при сохранении качества свариваемости.
- Повышенный предел текучести и прочности на разрыв при повышенных номинальных параметрах давления.
- По сравнению с трубками из стали 316/316L с таким же наружным диаметром и номинальным давлением меньшая толщина стенок способствует увеличению потока среды.
- Свариваемость.
- Области применения с температурами до 482 °F (250 °C).
- Более высокая теплопроводность / более низкий коэффициент температурного расширения в сравнении с нержавеющей сталью 316.
- Возможность использования в среде высокосернистого газа (NACE MR0175/ISO 15156)
- Изделия Swagelok из сплава 2507 предлагаются из прутков и поковок, соответствующих требованиям стандарта NORSOK M-650, регламентирующего поставщиков стали.
Для борьбы со:
сплошной коррозией; местной коррозией; коррозионным растрескиванием под напряжением
Сплав 825
Никелевые сплавы
Назначение сплава 825 (Incoloy® 825), в состав которого входят никель, железо, хром и молибден, состоит в том, чтобы обеспечить устойчивость к сплошной, точечной и щелевой коррозии, а также коррозионному растрескиванию под напряжением (SCC) в широком диапазоне рабочих сред.
- Стойкость к межкристаллитной коррозии благодаря стабилизации титаном
- Возможность использования в среде высокосернистого газа (NACE MR0175/ISO 15156)
- Стойкость при использовании в кислотных средах (в т. ч. в серной или фосфорной кислоте).
Для борьбы со:
General Corrosion; Localized Corrosion; Stress Corrosion Cracking; Sour Gas Cracking
Сплав 625
Никелевые сплавы
Назначение сплава 625 (Inconel® 625), в состав которого входят никель, хром и молибден с небольшой добавкой ниобия, состоит в том, чтобы снизить риск межкристаллитной коррозии в широком спектре крайне агрессивных сред.
- Стойкость к воздействию соляной и азотной кислот.
- Прочность и пластичность.
- Стойкость к щелевой и точечной коррозии при высоких температурах.
- Возможность использования в среде высокосернистого газа (NACE MR0175/ISO 15156)
Для борьбы со:
сплошной коррозией; местной коррозией; коррозионным растрескиванием под напряжением; Коррозия под воздействием высокосернистой среды
Сплав C-276
Никелевые сплавы
Сплав C-276 (Hastelloy® C-276) содержит никель, молибден и хром. Высокое содержание молибдена делает этот сплав особо устойчивым к точечной и щелевой коррозии. Он относится к немногим материалам, которые обладают устойчивостью к коррозионным воздействиям влажного газообразного хлора, гипохлорита и диоксида хлора.
- Устойчивость к окислительным и кислотным рабочим средам.
- Пластичность, ударная вязкость и прочность при высоких температурах.
- Устойчивость к щелевой и точечной коррозии, сульфидной коррозии под напряжением (SSC) и межкристаллитной коррозии (IGC)
- Возможность использования в среде высокосернистого газа (NACE MR0175/ISO 15156)
Следует иметь в виду, что данный сплав НЕ рекомендуется использовать в средах с сильной окислительной способностью, таких как горячая и концентрированная азотная кислота.
Для борьбы со:
сплошной коррозией; местной коррозией; коррозионным растрескиванием под напряжением; Коррозия под воздействием высокосернистой среды
Сплав 400
Никелевые сплавы
Сплав 400 (Monel® 400) является медно-никелевым сплавом, который известен своей исключительной стойкостью к плавиковой кислоте, а также к коррозионному растрескиванию под напряжением и точечной коррозии в большинстве видов чистых и технических вод.
- Прочность и коррозионная стойкость в условиях широкого диапазона температур и рабочих сред.
- Сохранение механических свойств при температурах ниже нуля.
Следует иметь в виду, что стоячая морская вода по результатам экспериментов способствует возникновению щелевой и точечной коррозии у данного сплава.
Для борьбы со:
сплошной коррозией; местной коррозией; коррозионным растрескиванием под напряжением; Коррозия под воздействием высокосернистой среды
Титановые сплавы
Стабильная оксидная пленка с надежной адгезией защищает титановые сплавы от коррозии. Эта пленка образуется мгновенно под воздействием воздуха или влаги на поверхность. Следует избегать безводных условий в отсутствие источника кислорода, поскольку в случае повреждения защитная пленка не восстановится.
Титан успешно применяется во многих системах благодаря превосходной коррозионной стойкости в следующих средах:
- хлоридсодержащие растворы и газ с содержанием влажного хлора;
- водные растворы хлоритов, гипохлоритов, перхлоратов и двуокиси хлора;
- естественная и хлорированная морская вода достаточно высокой температуры.
Титан и его сплавы:
- обладают исключительно высокой стойкостью к коррозии, вызванной микроорганизмами;
- высокоустойчивы к кислотам-окислителям различной концентрации и температуры (к распространенным кислотам этой категории относятся азотная, хромовая, хлорная и хлорноватистая кислота [влажный Cl]).
Ограничивающие факторы для применения титана и его сплавов:
- нелегированный титан иногда подвержен коррозии в водных хлоридсодержащих средах при условиях, не прогнозируемых с помощью скорости общей коррозии;
- сухой хлор может подвергнуть титан резкому окислению, вплоть до возгорания;
- титан не подходит для использования с фтористыми газами, чистым кислородом и водородом.
Сочетания компонентов из различных сплавов
В морских установках, в которых фитинги Swagelok из нержавеющей стали 316/316L проявили себя хорошо, а трубки из стали 316/316L подверглись щелевой коррозии в хомутах, возможно, будет экономически выгодно использовать фитинги из стали 316/316L в сочетании с трубками из более коррозионностойкого сплава. В сочетаниях компонентов из различных сплавов используются трубные обжимные фитинги Swagelok из стали 316/316L с трубками из сплавов 254, 904L, 825 или Tungum® (медный сплав UNS C69100).
Повышенное содержание хрома и никеля в стали 316/316L обеспечивает более высокую стойкость трубных обжимных фитингов Swagelok к местной коррозии. Превосходный обхват трубки обеспечивается за счет запатентованной компанией Swagelok конструкции заднего обжимного кольца и шарнирно-цангового способа обжима (hinging-colleting™), при котором достигается низкий крутящий момент и вращение гайки не передается на трубку. Процесс низкотемпературного науглероживания SAT 12, запатентованный компанией Swagelok, применяется для упрочения поверхности задних обжимных колец, что упрощает достижение превосходного обхвата трубок из вышеперечисленных сплавов.
Сочетания компонентов из различных сплавов могут стать экономически эффективным коррозионностойким решением, обеспечивающим следующие преимущества в морских установках:
- содержание никеля и хрома в стандартной нержавеющей стали Swagelok 316, превышающее минимальные требования стандарта ASTM A479, благодаря чему достигается более высокое значение PREN и повышенная стойкость к местной коррозии;
- высокая стойкость к точечной и щелевой коррозии трубок из специальных сплавов;
- низкий риск контактной коррозии за счет позиций 316, 254, 904L и 825 в таблице электродных потенциалов или с учетом длительной успешной эксплуатации фитингов из стали 316/316L с трубками из сплава Tungum.
Как и во всех узлах, в которых используются разные материалы, значения номинального давления для трубок и фитингов из разных сплавов определяются по материалу с самым низким значением номинального давления. Номинальные параметры давления см. в справочнике «Данные по трубкам — сочетания компонентов из различных сплавов», MS-06-117.
С помощью числового эквивалента стойкости к точечной коррозии (Pitting Resistance Equivalent Number, PREN) измеряется стойкость к местной точечной коррозии. Более высокие значения PREN показывают более высокую стойкость материала к точечной коррозии.
Связаться с экспертомДоступ к экспертным сервисам
Чтобы получить больше информации, ознакомьтесь с дополнительными полезными информационными материалами от Swagelok.
> Просмотреть и загрузить подготовленную к печати версию руководства по подбору материалов
Влияние основных легирующих элементов на свойства нержавеющих сталей
Хром (Cr) :
– является основным элементом стали , определяющей её стойкость к окислению (коррозии), хром резко повышает коррозионную стойкость стали при увеличении его в сплаве выше 12,5%, начиная с этой концентрации на поверхности образуется плотная оксидная плёнка Cr2O3
(хром собственно и делает сталь нержавеющей, например стали 20Х13, 30Х13, 40Х13 и т.п)
– при содержании хрома в стали 12—14% теплопроводность стали в 2 раза меньше чистого железа, а электроопротивление возрастает в 3 раза
– обеспечивает повышенную прочность при повышенных температурах, добавка хрома повышает твёрдость и прочность стали, не снижая её пластичности
– снижает ударную вязкость стали
Никель (Ni) :
– основная функция никеля – стабилизация аустенитной структуры стали, такая структура является особо прочной и эластичной.
(минимальное количество никеля способное стабилизировать аустенитную структуру – 8%, именно столько никеля находится в наиболее распространённой импортной стали AISI 304 )
– наличие в стали от 8-10% никеля обеспечивает ей хорошую пластичность и хорошие формовочные свойства
– улучшает свариваемость стали и дополнительно увеличивает сопротивление стали к окислению (коррозии) в районе сварного шва
– никель увеличивает жаропрочность стали (в особенности по отношению к устойчивости к деформации)
– благодаря никелю нержавеющая сталь лучше полируется и более устойчива к царапинам, чем обычные стали
(шлифованные и зеркальные поверхности )
Молибден (Mo) :
– повышает сопротивление стали к окислению (коррозии) при высоких температурах, снижает стойкость сталей к точечной (питтинговой) коррозии
– увеличивает красностойкость, упругость, предел прочности на растяжение
– обеспечивает дополнительное термическое упрочнение
Титан (Ti) :
– повышает прочность стали
– титан добавляют в нержавеющие стали для предотвращения межкристаллитной коррозии
Углерод (C) :
– при увеличении углерода до 0,8% растёт твёрдость и прочность стали, однако приводит к увеличению порога хладноломкости
(например стали 40Х13 и 95Х18 используются для производства ножей)
– чем больше в стали углерода, то она труднее обрабатывается резанием, хуже деформируется и хуже сваривается
(так наиболее распространённые в продаже импортные стали 300-ой серии AISI304/321/316 имеют в своём составе 0,8% углерода, что даёт им большую область применения по сравнению с отечественной сталью 12х18н10т) )
Классификация :: USSA.SU
АУСТЕНИТНАЯ НЕРЖАВЕЮЩАЯ СТАЛЬ
Аустенитная нержавеющая сталь содержит значительное количество хрома и достаточное для образования «аустенитной» микроструктуры количество никеля и марганца, которые и придают этим маркам стали хорошую формуемость, пластичность и коррозионную стойкость (а также делают сталь немагнитной). Типичный состав аустенитной стали содержит 18% хрома и 8% никеля, что соответствует популярной «нулевой» («0») марки, согласно определению Американского института чугуна и стали (AISI). Данная марка известна в России как AISI 304, DIN 1.4301 и соответствует российскому аналогу 08Х18Н9. Аустенитные марки стали отличаются высокой прочностью, имеют коррозионную стойкость в широком диапазоне агрессивных сред и отличаются хорошей технологичность и свариваемостью.
ФЕРРИТНАЯ НЕРЖАВЕЮЩАЯ СТАЛЬ
Ферритные марки нержавеющей стали сходны по свойствам с низкоуглеродистой сталью, но обладают более высокой коррозионной стойкостью. Наиболее распространённые марки ферритной стали содержат в среднем 11% и 17% хрома. Первые обычно применяются в производстве выхлопных систем автомобилей, а вторые – в производстве кухонных приборов, стиральных машин, и архитектурного декора интерьеров.
АУСТЕНИТНО-ФЕРРИТНАЯ НЕРЖАВЕЮЩАЯ СТАЛЬ (ДУПЛЕКСНАЯ)
Стали аустенитно-ферритного класса характеризуются высоким содержанием хрома (18-22%) и пониженным (экономным) содержанием никеля (4-6%, в отдельных случаях до 2%). Дополнительные легирующие элементы – молибден, медь, титан, ниобий. Химический состав этих сталей таков, что соотношение аустенита и феррита после оптимальной термической обработки составляет примено 1:1. Данный класс сталей имеет ряд преимуществ по сравнению с аустенитным сталями: более высокая (в 1,5-2 раза) прочность при удовлетворительной пластичности и сопротивляемости действию ударных нагрузок, большая стойкость против межкристаллитной коррозии и коррозионного растрескивания. Они в основном используются в обрабатывающей промышленности, строительстве и в изделиях, контактирующих с морской водой.
МАРТЕНСИТНАЯ НЕРЖАВЕЮЩАЯ СТАЛЬ
Мартенситные, как и ферритные марки, содержат в среднем от 12% до 17% хрома, однако имеют более высокое содержание углерода. Эти стали применяют преимущественно в термически обработанном состоянии, часто с тщательно шлифованной, а иногда и полированной поверхностью. Они используются при производстве лопастей турбин, столовых приборов и бритвенных лезвий.
Обработка поверхности – плоский прокат из нержавеющей стали
Вид обработки |
ASTM |
EN10088-2 |
Примечание |
Горячекатаный |
1N |
1E/1D |
Сравнительно грубая матовая поверхность, полученная при горячей прокатке до требуемой толщины с последующим отжигом и удалением окалины. |
Холоднокатаный |
2D |
2D |
Матовая поверхность, полученная при холодной прокатке до требуемой толщины с последующим отжигом и удалением окалины. Также достигается окончательным лёгким проходом через матовые валки. |
Холоднокатаный |
2В |
2В |
Светлая холоднокатаная отделка поверхности достигается тем же способом, что и поверхность D, за исключением того, что после отжига и снятия окалины (травления) производится дрессировка (прокатка с небольшим обжатием на валках с низкой шероховатостью поверх-ности). |
Светлый отжиг |
ВА |
2R |
Отделка типа ВА достигается светлым отжигом в инертной атмосфере после холодной прокатки. |
Шлифовка или матовая полировка |
№4 |
1J/J |
Универсальная светлая полировка посредством обработки сетчатым абразивом с ячейками 10-150 (mesh) после первоначальной шлифовки грубыми абразивами. |
Полировка сатиновым материалом |
№6 |
1К/К |
Мягкая отделка сатиновым материалом с меньшей отражательной способностью, чем при шлифовке (или матовой полировке). Достигается отделкой Тампико (Tampico) с использованием среднегрубого абразива. |
Светлая полировка (зеркальная) |
№8 |
1Р/Р |
Наиболее часто применяемая отделка для достижения высокой отражательной способности (зеркало). Достигается полировкой более мелкими абразивами с последующей полировкой тонким хлопковым материалом. |
Электрополировка поверхности |
– |
– |
Такая поверхность достигается обработкой в электролите. Данный процесс улучшает поверхность, удаляя вкрап-ления и неровности. |
Нержавеющая сталь по ГОСТ – марки, виды и классификации
Коррозионностойкие (нержавеющие) стали – группа легированных сталей, основным легирующим элементом которых является хром с содержанием 12-30%. Помимо хрома, в этих сплавах могут присутствовать: никель, марганец, титан, ниобий и другие добавки. Благодаря такому составу, коррозионностойкие стали, выпускаемые в соответствии с ГОСТом 5632-2014, применяются при производстве деталей машин, элементов конструкций и оборудования, эксплуатируемых в контакте с агрессивными средами (соленой водой, кислотах, щелочах).
Какую функцию выполняют легирующие элементы в коррозионностойких марках?
Основные элементы, присутствующие в составе нержавейки:
- Хром. Повышает устойчивость к различным типам коррозии, твердость, прочность. Незначительно снижает пластичность.
- Никель. Повышает стойкость к коррозии, прочностные характеристики, пластичность, прокаливаемость.
- Марганец. При содержании более 1% увеличивает твердость, износостойкость, стойкость к резким механическим нагрузкам.
- Титан. Повышает прочность, обрабатываемость, коррозионную стойкость, измельчает зерно.
- Ниобий. Улучшает устойчивость к коррозии сварных швов, повышает способность контактировать с кислыми средами.
Типы нержавеющей стали и классификация по структуре
В зависимости от типа внутренней структуры нержавеющие марки разделяют на ферритные, мартенситные, аустенитные и переходные группы.
Хромистые ферритные и мартенситные
Железо и хром образуют ряд твердых растворов. При содержании в стали более 12% хром инициирует появление на стальной поверхности оксидной пленки Cr2O3, обеспечивающей высокую коррозионную стойкость. Хром способствует образованию карбидов. Чем выше содержание углерода, тем активнее он образует карбиды хрома, обедняя твердый раствор этим легирующим элементом. Это приводит к снижению коррозионной стойкости стали. Поэтому нержавейка обычно имеет невысокое содержание углерода – до 0,4%. Примеры хромистых марок – 12Х13, 20Х13, 30Х13 (AISI), 40Х13.
Стали с содержанием хрома до 17% подвергают закалке при +1000…+1050°C. Отпуск для сталей ферритного класса осуществляется при +700…+750°C, мартенситного – +700…+750°C. После закалки и отпуска хромистые стали имеют наиболее высокую коррозионную стойкость.
Ферритные, мартенситные, феррито-мартенситные хромистые марки имеют хорошую коррозионную стойкость в атмосферных условиях и сохраняют хорошие эксплуатационные характеристики в слабоагрессивных средах. Такие сплавы широко используются для производства труб и емкостей, предназначенных для производств, работающих с азотной кислотой, в пищевой индустрии и легкой промышленности. Марки 08Х13 и 12Х13 востребованы при производстве деталей, которые в процессе эксплуатации подвергаются ударным нагрузкам. Нержавеющие стали, например марка 12Х17 (AISI 430), с содержанием хрома 17% и более относятся к ферритному классу. Марки с добавками ниобия, измельчающего зерно и уменьшающего склонность к межкристаллитной коррозии, применяют при производстве медицинского и измерительного инструмента, оборудования для пищевой и химической индустрии.
Хромистые стали, благодаря невысокой стоимости хрома, являются самыми бюджетными коррозионностойкими марками. Они обладают хорошими техническими характеристиками. Их основные недостатки – повышенная хрупкость сварных швов из-за образования при сварке крупнокристаллической структуры и склонность к интеркристаллитной коррозии. Для ликвидации этих проблем в сплав вводят титан, способствующий измельчению зерен. Введение в состав даже небольших количеств молибдена повышает стойкость сплавов к агрессивным кислотам, таким как уксусная и муравьиная.
Хромоникелевые аустенитные стали
Большинство хромоникелевых сталей относится к аустенитному классу. Это 08Х18Н10, 12Х18Н9, 12Х18Н9Т. Никель является аустенитообразующим элементом и играет важную роль в повышении коррозионной стойкости стали. Наиболее востребованные марки нержавеющей стали этого класса – 12Х18Н10Т (AISI 321) и 12Х18Н9 (AISI 304).
Хромоникелевые стали сохраняют высокие рабочие характеристики при повышенных температурах: предел прочности, предел текучести, устойчивость к кислым средам. При нормальных температурах аустенитные стали уступают ферритным маркам по прочности, но более пластичны, имеют более высокую вязкость и хорошо свариваются. Аустенитные стали востребованы для изготовления технологического оборудования производственных предприятий, труб, используемых для передачи агрессивных сред и/или эксплуатируемых при высоких температурах и давлении. Они подходят для получения металлоизделий холодной штамповкой и сваркой.
Стали с более низким содержанием никеля (12Х21Н5Т, 08Х22Н6Т, 15Х28АН) относятся к аустенитно-ферритному классу. Они отличаются сочетанием высокой коррозионной стойкости и прочности. При необходимости повышения кислотостойкости сплав дополнительно легируют медью или комплексом медь+молибден. Пример – 08Х23Н28М3Д3Т. Марка Х21Г7Н5 используется в условиях низких температур.
Аустенитно-мартенситные марки имеют меньшую коррозионную устойчивость, по сравнению с аустенитными, но отличаются повышенной прочностью. Стали переходного класса – 09Х15Н8Ю, 09Х17Н7Ю, 20Х13Н4Г9.
Для экономии легирующих элементов практикуется изготовление двухслойных сталей, получаемых сваркой под давлением. Один слой изготавливают из углеродистых сталей обыкновенного качества типа Ст3 или качественных конструкционных типа марки 10, а второй – из нержавеющей стали, такой как 03Х17Н14М3 (AISI 316).
Маркировка коррозионностойких сталей
Для маркировки нержавеющих сталей в России и странах СНГ используются цифровые и буквенные символы. Буквы указывают, какие элементы, помимо железа и углерода, входят в состав конкретной марки, цифры характеризуют количество углерода и легирующих элементов.
Химические элементы, входящие в состав нержавеющей стали:
- Х – хром. Основной легирующий элемент, обеспечивающий коррозионную стойкость сплава.
- Н – никель. Способствует повышению устойчивости к коррозии, улучшает прочность и пластичность.
- Ю – алюминий. Стабилизирует состав и предотвращает образование посторонних включений.
- М – молибден. Повышает устойчивость к агрессивным кислым средам.
- Б – ниобий. Измельчает зерно, снижает склонность сплава к интеркристаллитной коррозии.
- Г – марганец. Благоприятно влияет на свариваемость.
- Т – титан. Измельчает структуру, препятствует появлению коррозии на границах зерен.
- Ф – ванадий. Повышает пластичность.
Первая цифра, присутствующая в маркировке, указывает на содержание углерода в сотых долях процента. Сам элемент буквой не обозначается. Если легирующий элемент содержится в количестве до 1%, то после его буквенного обозначения цифра не ставится. Если процентное содержание добавки более 1%, то ее содержание указывается целым процентом.
Например, в марке 12Х21Н5Т содержится: 0,12% углерода, 21% хрома, 5% никеля и до 1% титана. При содержании в стали марганца и кремния в количестве до 2% в маркировке их обычно не указывают.
Таблица химических составов нержавеющих сталей популярных марок
Стандарты | Содержание углерода и легирующих элементов, % | ||||||||
ГОСТ | AISI | DIN | C | Mn | Si | Cr | Ni | Mo | Ti |
Мартенситные | |||||||||
20Х13 | 420 | 1.4021 | До 0,2 | До 0,8 | До 0,8 | 12-14 | До 0,6 | – | – |
Ферритные | |||||||||
12Х17 | 430 | 1.4016 | До 0,12 | До 1,0 | До 1,0 | 16-18 | – | – | – |
08Х13 | 409 | 1.400 | До 0,08 | До 0,8 | До 0,8 | 12-14 | – | – | – |
Аустенитные | |||||||||
12Х18Н9 | 304 | 1.4301 | До 0,12 | До 2,0 | До 0,8 | 17-19 | 8-10 | – | – |
08Х18Н10Т | 321 | 1.4541 | До 0,08 | До 2,0 | До 1,0 | 17-19 | 9-12 | – | – |
03Х17Н14М3 | 316S | 1.4435 | До 0,08 | До 2,0 | До 1,0 | 16-18 | 12-14 | 2-3 | – |
AISI 304, 430, 18/8, 18/10…
В чем разница между различными сортами нержавеющей стали (304, 430, 220, и т.д.)? Что означают разные номера маркировки (18/8, 18/10, 18/0, и т.д.)? Нас часто об этом спрашивают, поэтому мы решили написать небольшую статью, посвященную пищевой нержавеющей стали.
“Сорт” нержавеющей стали определяет ее качество, долговечность и термостойкость. Маркировка 18/8, 18/10 и т.д. обозначает состав нержавеющей стали, а именно – соотношение в ней хрома и никеля.
Маркировка пищевой нержавеющей стали
18/8 и 18/10 – два наиболее распространенных сорта нержавеющей стали, используемых для:
Эти сорта также известны как 304 (AISI 304) и входят в серию сортов 300. Первое число, 18, обозначает долю хрома а второе – никеля. Например, нержавеющая сталь 18/8 содержит 18% хрома и 8% никеля.
В нержавеющей стали 304 также содержится не более 0,8% углерода и не менее 50% железа. Хром связывает кислород на поверхности продукта, образуя пленку, защищающую железо от окисления (ржавчины). Никель также повышает коррозионную стойкость нержавеющей стали. Следовательно, чем выше содержание никеля, более устойчива нержавеющая сталь к коррозии. Сталь марки AISI 304 — это аустенитная сталь (сталь, легированная хромом, никелем и марганцем, сохраняющая при охлаждении до комнатной и ниже структуру твердого расплавленного раствора – аустенита) с низким содержанием углерода. Сталь этой марки является наиболее широко используемой из всех марок стали, а её характеристики делают её универсальной в применении. Эта сталь и ее аналог – сталь марки 08Х18Н10 используется для изготовления оборудования для химических и пищевых предприятий и предприятий общественного питания, оборудования для производства, хранения и транспортировки молока, пива, вина и других напитков, а также химреактивов, кухонных и столовых принадлежностей.
Сталь 18/0 содержит незначительное количество никеля (0,75%) и, следовательно, имеет пониженную коррозионную стойкость – она более подвержена ей по сравнению с сортами 18/8 или 18/10. Тем не менее, это – сталь высокого качества. Пищевая сталь 18/0 также известна как сталь 430 и входит в серию нержавеющих сталей 400 которая, в отличие от серии 300, является магнитной.
Пищевые нержавеющие стали серии 200 часто используются для изготовления посуды, кухонных принадлежностей, столовых приборов и контейнеров. Эти стали, как правило, существенно дешевле стали 304 – в серии 200 дорогой никель частично заменен марганцем. Несмотря на то, что изделия из стали 200 так же безопасны, они не так устойчивы к коррозии как сталь марки 304.
У нас можно заказать любую нейтральную мебель из нержавеющей стали.
Использование пищевой нержавеющей стали для столовых приборов
Иногда считают, что сталь 18/10 тяжелее, поэтому менее подходит для столовых приборов. На самом деле, нет никакой разницы между весом столовых приборов из стали 18/8 и 18/10. Никель в столовых приборах из стали 18/10 обеспечивает дополнительную прочность – к примеру, вилки из такой стали плохо гнутся. У столовых приборов из стали 18/10 также более блестящая поверхность.
Использование пищевой нержавеющей стали для посуды
Нержавеющая сталь является прекрасной альтернативой для посуды из алюминия с тефлоновым покрытием. Тем не менее, на конфорка плиты, жарочная или варочная поверхность из нержавеющей стали сами по себе не обеспечивают оптимальную теплопроводность, поэтому кастрюли и другая посуда, как правило, сделаны из трехслойного материала. Например, в нержавеющей сковороде стали, слой алюминия расположен между двумя слоями стали 18/10, что позволяет теплу равномерно распределяться по всей сковороде. В этих кастрюлях алюминий не вступает в контакт с пищевыми продуктами.
Насколько безопасна нержавеющая сталь?
Нержавеющая сталь является одним из самых распространенных материалов, используемых на кухнях сегодня. Он используется для столовых приборов, посуды, рабочих поверхностей самого разного теплового оборудования. Это прочный, легко поддающийся санитарной обработке и дезинфекции материал, устойчивый к коррозии и действию агрессивных различных кислот, содержащихся в мясе, молоке, фруктах и овощах. Не менее важно, что в нержавеющей стали нет химических веществ, которые могут мигрировать в продукты и напитки.
Мы считаем, что нержавеющая сталь, стекло, чугун, дерево, керамика с эмалью без свинца являются самыми безопасными материалами для использования в кухне. Наша компания предлагает широкий ассортимент изделий из нержавеющей стали.
Прочный, твердый и выносливый: самые разные никельсодержащие легированные стали обеспечивают
Легированные сталивключают широкий спектр материалов на основе железа. Содержание никеля колеблется от очень низкого, ~ 0,3% в некоторых легированных сталях, до 20% в мартенситностареющих сталях. Каждый сплав разработан для некоторого сочетания большей прочности, твердости, износостойкости или ударной вязкости, чем углеродистые стали. Обычно они используются в оборудовании, которое подает мощность, формирует и режет металл, или используются при низких температурах, когда углеродистые стали не обладают достаточной прочностью.Для простоты легированные стали можно разделить на несколько типов с особыми свойствами для конкретных конечных применений. Стали из никелевых сплавов необходимы для изготовления инструментов и оборудования, которые позволяют промышленности производить другие инструменты и оборудование.
Типичный химический состав некоторых известных никельсодержащих легированных сталей
Сталь Тип | Класс (UNS) | К | Ni | Кр | Fe | Прочие | Приложения |
Закаливаемая | AISI 4340 | 0.4 | 1,8 | 0,8 | бал | Пн | Передачи, валы и шасси самолета |
AISI 4320H | 0,2 | 1,8 | 0,5 | бал | Пн | Шестерни и шестерни с поверхностной закалкой для повышения износостойкости, но с прочным сердечником | |
AR450 | 0.26 | 0,70 | 1,0 | бал | Пн | Пластина износостойкая для желобов, футеровок, решеток, баллистических пластин | |
Инструментальная сталь – | A9 (T30109) | 0,5 | 1,5 | 5,0 | бал | Mo, V | Штампы для волочения и формовки, ножницы |
Инструментальная сталь – | P6 (T51606) | 0.1 | 3,5 | 1,5 | бал | Плашки для литья под давлением цинка и пластмассы | |
Высокопрочный | A588 Gr C | 0,1 | 0.35 | 0,5 | бал | Cr, Cu, V | Обеспечивает более высокое соотношение прочности и веса, чем обычная углеродистая сталь, и более высокую стойкость к атмосферной коррозии для использования в строительстве мостов |
Никелевая сталь | 9% никелевая сталь (K81340) | 0,13 | 9,0 | – | бал | Криогенные применения, такие как хранилище СПГ | |
Мартенситностареющая сталь | Maraging 300 (K93120) | 0.03 | 18,5 | – | бал | Co, Mo, Al, Ti | Кожухи ракетных двигателей, планеры, приводные валы, шасси самолетов, литьевые формы, штампы |
Закаливаемая низколегированная сталь
Эти стали относятся к категории черных металлов, которые обладают механическими свойствами, превосходящими простые углеродистые стали.Это достигается добавлением легирующих элементов, таких как никель, хром и молибден, с последующей закалкой (быстрым охлаждением) и отпускной термообработкой. Эти элементы, растворенные в аустените перед закалкой, увеличивают прокаливаемость. Никель дополняет упрочняющий эффект хрома и молибдена и играет важную роль в обеспечении ударной вязкости твердо-мартенситной микроструктуре, которая возникает в результате термообработки с закалкой и отпуском.
Сравнение типичных механических характеристик для AISI 4340 в отожженном, закаленном и отпущенном состоянии с углеродистой сталью AISI 1045
Круглый пруток диаметром 75 мм (3 дюйма) | Предел текучести МПа (тыс. Фунтов на кв. Дюйм) | Предел прочности МПа (тыс. Фунтов на кв. Дюйм) | % |
AISI 4340 отожженный | 588 (86) | 752 (110) | 21 |
AISI 4340 ASTM A434 класс BD | 847 (124) | 963 (141) | 18 |
AISI 1045 нормализованное | 410 (60) | 629 (92) | 22 |
Инструментальная сталь
Инструментальная сталь – это термин, применяемый к множеству высокотвердых, устойчивых к истиранию сталей, используемых для таких применений, как штампы (штамповка или экструзия), резка или резка, изготовление пресс-форм или ударные нагрузки, такие как молотки (личные или промышленные).Их термическая обработка аналогична закаливаемым низколегированным сталям.
Закаленные на воздухе инструментальные стали уменьшают деформацию, вызванную быстрой закалкой в воде, и обладают балансом износостойкости и вязкости.
Инструментальная сталь для пластмассовых форм – это низкоуглеродистые стали, которые подвергаются формованию, а затем науглероживанию, закалке и отпуску до высокой твердости поверхности, что делает их идеальными для форм для литья под давлением и штампов для литья под давлением.
Высокопрочная низколегированная (погодостойкая сталь)
Более мелкозернистая структура этих сталей обеспечивает повышенную прочность по сравнению с обычными углеродистыми сталями.Это более мелкое зерно достигается за счет воздействия на температуру превращения, так что превращение аустенита в феррит и перлит происходит при более низкой температуре во время охлаждения на воздухе. При низком уровне углерода, типичном для сталей HSLA, такие элементы, как кремний, медь, никель и фосфор, особенно эффективны для получения мелкодисперсного перлита.
Добавление хрома, меди и никеля дает стабильный слой ржавчины, который прилипает к основному металлу и является гораздо менее пористым, чем слой ржавчины, который образуется на обычной конструкционной стали.В результате скорость коррозии значительно снижается, что позволяет использовать эти стали без покрытия.
В таблице ниже показаны различия в механических свойствах углеродистой конструкционной стали ASTM A36 и высокопрочной низколегированной конструкционной стали ASTM A588 Grade C.
Разница в механических свойствах углеродистой конструкционной стали ASTM A36 и высокопрочной низколегированной конструкционной стали ASTM A588 класса C
Марка | Предел текучести МПа (тыс. Фунтов / кв. Дюйм) мин. | Предел прочности при растяжении МПа (тыс. Фунтов на кв. Дюйм) мин. | % Относительное удлинение мин |
ASTM A36 | 250 (36) | 400 (58) | 23 |
ASTM A588 Gr C | 345 (50) | 485 (70) | 21 |
Никелевая сталь
Ферритные стали с высоким содержанием никеля, как правило, более 3%, находят широкое применение в областях, связанных с воздействием температур от 0 ° C до -196 ° C.К таким приложениям относятся резервуары для хранения сжиженных углеводородных газов, а также конструкции и оборудование, предназначенные для использования в холодных регионах. Эти стали используют эффект содержания никеля для снижения температуры ударного перехода, тем самым улучшая ударную вязкость при низких температурах.
В углеродистых и большинстве низколегированных сталей при понижении температуры ниже 24 ° C (75 ° F) прочность и твердость увеличиваются, а пластичность при растяжении и вязкость снижаются. Никель улучшает низкотемпературную вязкость, как показано на диаграмме , рис. 1, по результатам удара по Шарпи.
Впервые примененная в резервуарах с жидким кислородом в 1952 году, 9% никелевая сталь с тех пор в основном используется для внутренней оболочки резервуаров для СПГ. Его выбирают вместо аустенитных нержавеющих сталей из-за сочетания высокой прочности и надежной вязкости разрушения при очень низких температурах до -196 ° C.
Узнайте об обычных легирующих агентах
Сталь – это, по сути, железо и углерод, легированный некоторыми дополнительными элементами. Процесс легирования используется для изменения химического состава стали и улучшения ее свойств по сравнению с углеродистой сталью или для корректировки их в соответствии с требованиями конкретного применения.
В процессе легирования металлы объединяются для создания новых структур, которые обеспечивают более высокую прочность, меньшую коррозию или другие свойства. Нержавеющая сталь является примером легированной стали с добавлением хрома.
Преимущества легирующих добавок для стали
Различные легирующие элементы или добавки по-разному влияют на свойства стали. Некоторые из свойств, которые можно улучшить за счет легирования, включают:
- Стабилизирующий аустенит : такие элементы, как никель, марганец, кобальт и медь, увеличивают диапазон температур, в котором существует аустенит.
- Стабилизирующий феррит : Хром, вольфрам, молибден, ванадий, алюминий и кремний могут способствовать снижению растворимости углерода в аустените. Это приводит к увеличению количества карбидов в стали и сокращает диапазон температур, в котором существует аустенит.
- Карбидообразующий : Многие второстепенные металлы, включая хром, вольфрам, молибден, титан, ниобий, тантал и цирконий, образуют прочные карбиды, которые – в стали – повышают твердость и прочность.Такие стали часто используются для производства быстрорежущей стали и инструментальной стали для горячих работ.
- Графитизация : Кремний, никель, кобальт и алюминий могут снизить стабильность карбидов в стали, способствуя их разрушению и образованию свободного графита.
В приложениях, где требуется уменьшение концентрации эвтектоидов, добавляются титан, молибден, вольфрам, кремний, хром и никель. Все эти элементы снижают концентрацию эвтектоида углерода в стали.
Многие области применения стали требуют повышенной коррозионной стойкости. Для достижения этого результата сплавили алюминий, кремний и хром. Они образуют защитный оксидный слой на поверхности стали, тем самым защищая металл от дальнейшего разрушения в определенных средах.
Обычные легирующие агенты для стали
Ниже приведен список часто используемых легирующих элементов и их влияние на сталь (стандартное содержание в скобках):
- Алюминий (0.95-1,30%): раскислитель. Используется для ограничения роста зерен аустенита.
- Бор (0,001-0,003%): агент, повышающий упрочняемость, улучшающий деформируемость и обрабатываемость. Бор добавляется к полностью обезвоженной стали, и его нужно добавлять только в очень малых количествах, чтобы иметь эффект упрочнения. Добавки бора наиболее эффективны в низкоуглеродистых сталях.
- Хром (0,5-18%): ключевой компонент нержавеющих сталей. При содержании более 12 процентов хром значительно улучшает коррозионную стойкость.Металл также улучшает закаливаемость, прочность, реакцию на термическую обработку и износостойкость.
- Кобальт: Повышает прочность при высоких температурах и магнитную проницаемость.
- Медь (0,1-0,4%): чаще всего встречается в качестве остаточного агента в сталях, медь также добавляется для получения свойств дисперсионного твердения и повышения коррозионной стойкости.
- Свинец: несмотря на то, что он практически не растворяется в жидкой или твердой стали, свинец иногда добавляют в углеродистые стали путем механического диспергирования во время разливки, чтобы улучшить обрабатываемость.
- Марганец (0,25-13%): Повышает прочность при высоких температурах, устраняя образование сульфидов железа. Марганец также улучшает прокаливаемость, пластичность и износостойкость. Как и никель, марганец является элементом, образующим аустенит, и может использоваться в аустенитных нержавеющих сталях серии AISI 200 в качестве заменителя никеля.
- Молибден (0,2-5,0%): Обнаруженный в небольших количествах в нержавеющей стали, молибден повышает прокаливаемость и прочность, особенно при высоких температурах.Молибден, который часто используется в хромоникелевых аустенитных сталях, защищает от точечной коррозии, вызываемой хлоридами и серосодержащими химическими веществами.
- Никель (2-20%): еще один легирующий элемент, важный для нержавеющих сталей, никель добавляется в высокохромистую нержавеющую сталь в количестве более 8%. Никель увеличивает прочность, ударную вязкость и ударную вязкость, а также повышает стойкость к окислению и коррозии. Он также увеличивает ударную вязкость при низких температурах при добавлении в небольших количествах.
- Ниобий: обладает преимуществом стабилизации углерода за счет образования твердых карбидов и часто встречается в жаропрочных сталях.В небольших количествах ниобий может значительно увеличить предел текучести и, в меньшей степени, предел прочности сталей, а также иметь умеренное усиление эффекта осаждения.
- Азот: Повышает аустенитную стабильность нержавеющих сталей и улучшает предел текучести таких сталей.
- Фосфор: фосфор часто добавляют с серой для улучшения обрабатываемости низколегированных сталей. Это также добавляет прочности и увеличивает коррозионную стойкость.
- Селен: Повышает обрабатываемость.
- Кремний (0,2–2,0%): этот металлоид улучшает прочность, эластичность, кислотостойкость и приводит к увеличению размера зерен, что приводит к большей магнитной проницаемости. Поскольку кремний используется в качестве раскислителя при производстве стали, он почти всегда присутствует в некотором процентном соотношении во всех марках стали.
- Сера (0,08-0,15%): добавленная в небольших количествах, сера улучшает обрабатываемость, не приводя к жаропрочности. С добавлением марганца жаростойкость дополнительно снижается из-за того, что сульфид марганца имеет более высокую температуру плавления, чем сульфид железа.
- Титан: Повышает прочность и коррозионную стойкость, ограничивая размер зерна аустенита. При содержании титана 0,25-0,60% углерод соединяется с титаном, позволяя хрому оставаться на границах зерен и противостоять окислению.
- Вольфрам: производит стабильные карбиды и измельчает размер зерна для увеличения твердости, особенно при высоких температурах.
- Ванадий (0,15%): подобно титану и ниобию, ванадий может давать стабильные карбиды, повышающие прочность при высоких температурах.За счет создания мелкозернистой структуры можно сохранить пластичность.
- Цирконий (0,1%): увеличивает прочность и ограничивает размер зерен. Прочность можно значительно повысить при очень низких температурах (ниже точки замерзания). Сталь, содержащая цирконий до 0,1%, будет иметь меньший размер зерен и сопротивляться разрушению.
Типы никелевых сплавов – нержавеющие стали, никель-медные сплавы, никель-хромовые сплавы, сплавы с низким коэффициентом расширения
Рассматриваемые темы
Предпосылки
Никелевые сплавы широко используются из-за их коррозионной стойкости, жаропрочности и особых свойств магнитного и теплового расширения.
Основными типами используемых сплавов являются:
Нержавеющие стали
Большинство нержавеющих сталей содержат 8-10% никеля. Во всех случаях работает комбинация хрома с никелем. Нержавеющие стали также полезны в качестве огнестойких материалов, поскольку они сохраняют свою прочность при более высоких температурах, чем конструкционная сталь.
Самая распространенная нержавеющая сталь – это нержавеющая сталь марки 304 с 8% никеля и 18% хрома и остаточным железом. Он используется для таких обычных предметов, как ложки и вилки, кастрюли и кухонные мойки.Если требуется дополнительная коррозионная стойкость, например, для кровли в морских условиях, используется тип 316. Он содержит примерно такое же количество никеля и хрома, что и 304, но с добавлением 3% молибдена. Весы снова железные.
Существует много других видов нержавеющей стали, которые удовлетворяют широкий спектр требований инженеров и архитекторов, например, никелированная сталь (NPS).
Никель-медные сплавы
Эти медно-никелевые сплавы иногда называют NiCu или MONEL или NICORROS и содержат никель с медью и небольшие количества железа и марганца.Типичный медно-никелевый сплав марки 400 (UNS N04400). Эти никелево-медные сплавы содержат минимум 63% никеля, 28-34% меди и максимум 2% марганца и 2,5% железа. Также существует небольшое количество примесей, сохраняемых в ограниченных количествах, чтобы гарантировать, что свойства металла не будут повреждены.
Эти никель-медные сплавы используются там, где требуется более высокая прочность по сравнению с чистым никелем. Никель-медные сплавы имеют более широкий диапазон сред, в которых они устойчивы к коррозии, но для некоторых специализированных применений, таких как сильные щелочные загрязнения, никель или коммерчески чистый никель будут лучше.
Никелево-медные сплавы находят широкое применение в нефтепереработке и судостроении, где требуется длительный срок службы без коррозии. Из-за хорошей теплопроводности никель-медных сплавов они часто используются в теплообменниках, где морская вода является одной из рассматриваемых жидкостей.
Сплавы на основе никеля и хрома
Эти сплавы на основе никеля и хрома широко используются там, где требуется термостойкость и / или коррозионная стойкость. В некоторых членах группы, где условия менее жесткие, часть никеля заменяется железом, чтобы снизить общую стоимость.
Металлы разрушаются при высоких температурах из-за окисления (окалины) и потери прочности. Сплавы этого класса спроектированы таким образом, чтобы противостоять отказу от обоих этих механизмов. Никелевые сплавы не подходят для высокотемпературных сред с высоким содержанием серы.
Там, где коррозионная стойкость значительна, молибден используется в качестве легирующей добавки в сплавах на основе никеля и хрома.
Эта группа сплавов часто продается под торговыми марками, но большинство из них перечислены в единой системе нумерации.Общие торговые наименования: Hastelloy, Incoloy, Inconel, Nicrofer, NiChromM и NiMonic.
Более современные сплавы на основе никеля и хрома в этих группах также имеют широкий спектр дополнительных элементов, добавленных для придания особых свойств – некоторые из них могут быть довольно сложными и требуют очень тщательного контроля над составом и термообработкой.
UNS No | Al | Cr | Co | Fe | Mo | Ni | Nb + Ta | Ti | W | 5 | 5,5 | 16 | 57 | 3,8 |
---|---|---|---|---|---|---|---|---|---|---|---|
N06600 | 15,5 | 8 | 76 | N0 | 21,5 | 9 | 61 | 3,6 | |||
N08800 | 21 | 46 | 32.5 | ||||||||
N07718 | 0,5 | 19 | 18,5 | 3 | 52,5 | 5,1 | |||||
N07090 | 1,5 | 19,5 | 1,5 | 19,5 | 60 | 2,5 |
Номер UNS | Состояние | UTS (МПа) | 0,2 Испытательное напряжение (МПа) | Удлиненное. На 5 см (%) | Твердость (HB) | 1000hr Ruptire Str. 750 ° C (МПа) |
N10276 | Отожженный | 790 | 415 | 50 | 184 | Нет данных |
N06600 | Отожженный | 550-690 | 210- 430 | 55-35 | 120-170 | 38 |
N06625 | Отожженный | 930 | 520 | 45 | 180 | 160 |
N08800 | Отожженный | 520-690 | 210-410 | 60-30 | 120-184 | 70 (700 ° C) |
N07718 | Возрастная закалка | 1350 | 1180 | 17 | 382 | 170 |
Этот список далеко не исчерпывающий, и запросы к производителям никелевых сплавов следует направлять в отношении специализированных высокотемпературных или коррозионных ситуаций.
Все металлы «ползут» под воздействием высоких температур и в заводском виде компоненты могут деформироваться. Эта деформация может привести к поломке. Никелевые сплавы обладают более высокой прочностью и более длительным сроком службы при повышенных температурах, чем большинство сплавов. Это делает их идеальными для таких деталей, как лопатки и диски газотурбинных двигателей. Однако проектировщик должен определить ожидаемый срок службы каждого компонента и использовать при проектировании соответствующую прочность на ползучесть и разрыв.
Сплавы с низким коэффициентом расширения
Существует группа никель-железных сплавов с контролируемым расширением, у которых коэффициент расширения низкий и постоянный в диапазоне температур.
Эти никель-железные сплавы с низким коэффициентом расширения широко используются там, где изменение механических свойств с температурой может быть проблемой, например, в прецизионных пружинах. Эти никелево-железные сплавы также используются там, где требуется уплотнение металл / стекло, называемое сплавами для герметизации стекла.
Одним из примеров является сплав, содержащий 48% никеля и остаточное железо (UNS K94800). Этот сплав имеет следующие коэффициенты расширения:
20-100 ° C: 8,5 x 10 -6 м / м. ° C
20-400 ° C: 8.3-9,3 x 10 -6 м / м. ° C
Этот никелево-железный сплав имеет коэффициент расширения, соответствующий коэффициенту расширения натронно-известкового и мягкого свинцового стекла, и, таким образом, обеспечивает прочное стекло / металлическое уплотнение, которое будет не трескается из-за разного расширения двух материалов. Еще одно такое уплотнение обеспечивается с помощью вытяжных проводов для ламп
Магнитные сплавы
Существует требование к материалам с высокой магнитной проницаемостью, чтобы минимизировать требования к мощности для создания сильного магнитного поля, такого как требуемое в головках магнитофона и для магнитного экранирования. вокруг прецизионных электронно-лучевых устройств отображения.
Эти материалы с высокой проницаемостью представляют собой сложные сплавы на основе никеля с различными вариантами состава. Типичный состав может быть следующим: 70-80% никеля с небольшими количествами молибдена и / или меди и остальное железо. Ожидается, что этот сплав будет иметь максимальную относительную проницаемость от 50 000 до 100 000. Распространенные торговые наименования этой группы – МУ-МЕТАЛЛ и ПЕРМАЛЁЙ.
Также существуют требования к материалам с постоянной проницаемостью в диапазоне плотностей магнитного потока.Это требуется в телефонном оборудовании и электромонтерах, где изменение проницаемости может привести к искажениям. Эти сплавы обычно известны как сплавы PERMINVAR, и их состав составляет около 45% никеля, 30% железа и 25% кобальта.
Торговые наименования и владельцы никелевых сплавов
HASTELLOY – зарегистрированная торговая марка Haynes Intl.
INCOLOY, INCONEL, MONEL и NIMONIC являются зарегистрированными торговыми наименованиями группы компаний INCO.
INVAR – зарегистрированная торговая марка Imphy S.A.
MU-METAL является зарегистрированным товарным знаком Telcon Metals Ltd.
NICORROS и NICROFER являются зарегистрированными торговыми наименованиями Krupp UM GmbH
Источник: Выдержано из Руководства по инженерным материалам, 5 th Edition.
Для получения дополнительной информации об этом источнике посетите Австралазийский институт материаловедения. Сплавы
широко используются из-за их коррозионной стойкости, жаропрочности и особых свойств магнитного и теплового расширения.В этой статье рассматриваются следующие типы сплавов: железо-никель-хромовые сплавы; Нержавеющая сталь; Медно-никелевые сплавы; Никель-хром и др.Влияние химических элементов в стали
Вы когда-нибудь задумывались, что на самом деле означают все эти элементы, перечисленные в протоколе испытаний материалов? Читать дальше!
Углерод
Углерод обычно считается наиболее важным легирующим элементом в стали и может присутствовать до 2% (хотя в большинстве сварных сталей его содержание составляет менее 0,5%). Повышенное количество углерода увеличивает твердость и прочность на разрыв, а также повышает отклик на термическую обработку (способность к закалке).Повышенное количество углерода ухудшает свариваемость.
сера
Сера обычно является нежелательной примесью в стали, а не легирующим элементом. В количествах, превышающих 0,05%, он вызывает хрупкость и снижает свариваемость. Легирующие добавки серы в количестве от 0,10% до 0,30% будут улучшать обрабатываемость стали. Такие типы могут называться «ресульфурация» или «автоматическая обработка». Сплавы для свободной механической обработки не предназначены для использования там, где требуется сварка.
фосфор
Фосфор обычно считается нежелательной примесью в сталях. Обычно он содержится в количестве до 0,04% в большинстве углеродистых сталей. В закаленных сталях это может вызвать охрупчивание. В низколегированные высокопрочные стали можно добавлять фосфор в количестве до 0,10% для повышения прочности и коррозионной стойкости.
Кремний
Обычно только небольшие количества (0,20%) кремния присутствуют в стальном прокате, когда он используется в качестве раскислителя.Однако в стальных отливках обычно присутствует от 0,35 до 1,00%. Кремний растворяется в железе и имеет тенденцию укреплять его. Металл шва обычно содержит примерно 0,50% кремния в качестве раскислителя. Некоторые присадочные металлы могут содержать до 1% для улучшения очистки и раскисления при сварке загрязненных поверхностей. Когда эти присадочные металлы используются для сварки на чистых поверхностях, в результате прочность металла сварного шва будет заметно повышена. В результате снижение пластичности может вызвать проблемы с растрескиванием.
Марганец
Стали обычно содержат не менее 0,30% марганца, поскольку он способствует раскислению стали, предотвращает образование сульфида железа и включений и способствует повышению прочности за счет повышения прокаливаемости стали. В некоторых углеродистых сталях содержится до 1,5%.
Хром
Хром – мощный легирующий элемент в стали. Он сильно увеличивает закаливаемость стали и заметно улучшает коррозионную стойкость сплавов в окислительных средах.Его присутствие в некоторых сталях может вызвать чрезмерную твердость и растрескивание сварных швов и прилегающих к ним швов. Нержавеющие стали могут содержать более 12% хрома.
молибден
Молибден является сильным карбидообразователем и обычно присутствует в легированных сталях в количестве менее 1%. Повышает прокаливаемость и устойчивость к повышенным температурам. В аустенитных нержавеющих сталях он улучшает стойкость к точечной коррозии.
Никель
Никель добавляется в стали для повышения прокаливаемости.Он часто улучшает ударную вязкость и пластичность стали, даже при увеличении прочности и твердости, которые она дает. Его часто используют для повышения ударной вязкости при низких температурах.
Алюминий
Алюминий добавляют в сталь в очень малых количествах в качестве раскислителя. Это также измельчитель зерна для повышения прочности; стали с умеренными добавками алюминия были сделаны с «мелкозернистой практикой».
Ванадий
Добавление ванадия приводит к увеличению прокаливаемости стали.Он очень эффективен, поэтому его добавляют в незначительных количествах. При содержании более 0,05% сталь может иметь тенденцию к охрупчиванию во время обработки для снятия термического напряжения.
Общие определения стали
Слиток железа
Максимум 0,03% углерода, используется для эмалирования, цинкования, глубокой вытяжки листов и полос, отличная свариваемость.
Низкоуглеродистая
Максимум 0,15% углерода, используется для электродов, пластин и профилей, листов, полос, отличная свариваемость.
Низкоуглеродистая сталь
Максимум 0,15-0,30% углерода, используется для изготовления профилей, листов и стержней, хорошая свариваемость.
Средний углерод
Максимум 0,30-0,50% углерода, используется для деталей машин, хорошая свариваемость – может потребоваться предварительный и последующий нагрев.
Высокоуглеродистый
Максимум 0,50–1,00% углерода, используется для пружин, штампов, рельсов, плохая свариваемость – трудно сваривать без предварительного нагрева и последующего нагрева.
Спасибо Американскому обществу сварщиков за предоставленную информацию, использованную в этом ресурсе.
Аустенитная нержавеющая сталь с низким содержанием никеля
Наиболее распространенными сортами нержавеющей стали являются марки 304 и 316, которые особенно популярны, поскольку их аустенитная микроструктура обеспечивает превосходное сочетание коррозионной стойкости, механических и физических свойств и простоты изготовления.
Аустенитная структура является результатом добавления примерно 8-10% никеля. Не только никель образует аустенит; другие элементы, которые используются таким образом, – это марганец, азот, углерод и медь.
Стоимость никеля и его добавок в нержавеющую сталь
Стоимость обычных нержавеющих сталей в значительной степени определяется стоимостью ингредиентов. Стоимость хрома, который является основным «нержавеющим ингредиентом», невелика, но добавление элементов, которые улучшают коррозионную стойкость (особенно молибдена) или модифицируют производственные свойства (особенно никель), значительно увеличивает стоимость.
Стоимость никеля колебалась от 5000 долларов США или 6000 долларов США в 2001 году до 15 000 долларов США за тонну в 2004 году.
Аналогичным образом, стоимость молибдена резко возросла с примерно 8000 долларов США за тонну в 2001 году до примерно 50 000 долларов США за тонну в 2004 году.
Эти затраты напрямую влияют на два наиболее распространенных сорта: 304 (18% Cr, 8% Ni) и 316 (17% Cr, 10% Ni, 2% Mo). Воздействие наиболее остро ощущается в сплаве 316, стоимость которого выше 304.
Другие марки, такие как дуплекс 2205 (22% Cr, 5% Ni, 3% Mo) и все более высоколегированные нержавеющие стали. стали также затронуты.
Относительные затраты на ингредиенты показаны на Рисунке 1, но они сильно меняются, а иногда и быстро с течением времени. Эти затраты были правильными в конце 2004 года.
Легирующие добавки – марганец, заменяющий никель
Суть легирующих элементов в том, что они достигают определенных изменений коррозионной стойкости или микроструктуры (что, в свою очередь, влияет на механические и производственные свойства. ).
Хром используется для достижения коррозионной стойкости, а молибден добавляет к этому.
Распространенной оценкой коррозионной стойкости марок нержавеющей стали является эквивалент сопротивления питтингу (PRE), который обычно оценивается как PRE =% Cr + 3,3 x% Mo + 16 x% N. Красивое уравнение, но, к сожалению, только руководство.
PRE дает руководство по ранжированию марок, но не является предиктором устойчивости к какой-либо конкретной коррозионной среде. Очевидно, что стойкость к точечной коррозии может быть увеличена за счет молибдена, а также за счет добавок хрома или азота.Они намного дешевле молибдена. Несмотря на высокий фактор PRE, азот имеет ограниченное влияние на коррозионную стойкость из-за низкой растворимости, т.е. <0,2%.
Микроструктура стали в значительной степени определяется балансом между элементами, формирующими аустенит, и элементами феррита.
Со стороны формирователя аустенита углерод, марганец, азот и медь – все возможные альтернативы никелю. Все эти элементы дешевле никеля.
Как и в случае с PRE, формулы эквивалентности Ni служат руководством, но не раскрывают всей истории; каждый элемент действует немного по-разному, и невозможно полностью удалить никель и заменить его, например, медью или азотом.
Марганец действует как аустенитообразователь, но не так эффективен, как никель, а хромомарганцевые стали имеют более высокую скорость деформационного упрочнения, чем очевидно эквивалентные хромоникелевые стали.
Углерод является очень мощным аустенитным образцом, но имеет лишь ограниченную растворимость в аустените, поэтому имеет ограниченную ценность в стали, предназначенной для того, чтобы быть полностью аустенитной.
Хотя никель не признается формулой PRE, он оказывает положительное влияние на устойчивость к некоторым агрессивным средам, которые марганец не дублирует.
Между элементами также может быть синергия. Добавление азота имеет двойной эффект: образование аустенита и повышение стойкости к питтинговой коррозии. Марганец сам по себе является сильным образующим аустенит, но он также увеличивает растворимость азота.
Рост сталей “серии 200”
Таким образом, марганец является жизнеспособной альтернативой никелю, начиная от незначительного добавления до почти полной замены.
Разработка аустенитных марок с высоким содержанием марганца впервые произошла около пятидесяти лет назад, во время одного из (нескольких) предыдущих периодов высокой стоимости никеля.
В то время некоторые марки Cr-Mn-Ni были достаточно развиты, чтобы им были присвоены номера марок AISI Ü 201 (17% Cr, 4% Ni, 6% Mn) и 202 (18% Cr, 4% Ni, 8% Mn). ) являются альтернативами хромоникелевых марок 301 и 302 с высоким содержанием марганца и все еще включены в спецификации ASTM в качестве стандартных марок.
Их потребление в последующие десятилетия было низким по сравнению с их эквивалентами Cr-Ni. Причины неэффективного использования этих более дешевых марок стали:
- Очень высокая скорость наклепа (в некоторых случаях это может быть преимуществом).
- Немного худший внешний вид поверхности Ü считается неприемлемым для определенных применений.
- Дополнительные производственные затраты Ü, в частности, более высокий износ огнеупоров при плавке.
- Коррозионная стойкость в некоторых средах ниже по сравнению с марками Cr-Ni.
Дополнительная проблема заключается в том, что аустенитный лом Cr-Ni и Cr-Mn-Ni является немагнитным независимо от содержания никеля, но торговцы ломом оценивают лом на основе предполагаемого содержания никеля.
Это может дестабилизировать рынки лома.В результате снижение затрат (из-за более низкой стоимости ингредиентов) в целом было недостаточным для перехода приложений от традиционных марок Cr-Ni.
Принятие решений часто происходило из-за технических преимуществ серии 200 в нишевых приложениях, а не из-за затрат.
Некоторые новые претенденты
В последнее десятилетие появилось несколько новых претендентов в группе Cr-Mn-Ni аустенитных сплавов. Основные разработки проводились в Индии, и основным применением была кухонная утварь, в частности кухонная утварь.
Очень высокая скорость деформационного упрочнения марок с низким содержанием никеля / высоким содержанием марганца была приемлемой до определенного момента для данного применения, но для уменьшения этой проблемы также были внесены добавки меди.
Индия была плодородной площадкой для разработки и производства этих сортов из-за местных экономических факторов.
Другие азиатские страны также стали сильными рынками, а в последнее время также стали производителями. Китайский рынок особенно силен, и в Китае существует значительный спрос на марки Cr-Mn-Ni, часто называемые нержавеющими сталями серии «200».
Другие центры производства – Тайвань, Бразилия и Япония. Разработка сплава привела к появлению ряда аустенитных марок с содержанием никеля от 1% до 4% и марганца более 9%. Ни одна из этих марок пока не включена в ASTM или другие международно признанные стандарты.
Производство этих аустенитных марок с низким содержанием никеля росло очень быстрыми темпами. Последние данные, опубликованные Международным форумом по нержавеющей стали (ISSF), показывают, что в 2003 году 1.5 миллионов тонн (7,5% мировой нержавеющей стали) было именно этого типа. В Китае эта доля оценивается в 25% в 2004 году.
Проблемы все еще существуют, и крупномасштабная конверсия Cr-Ni применений в марки Cr-Mn-Ni- (Cu) маловероятна.
Основная проблема заключается в отсутствии контроля uns недобросовестные поставщики, неверно представляющие продукт с низким содержанием никеля как сорт 304, что приводит к некоторым нарушениям коррозии при эксплуатации и ухудшению качества лома из-за загрязнения материалом с низким содержанием никеля.
По состоянию на начало 2005 г. будущее неясно. Хотя кажется логичным, что должно быть место для аустенитных марок с низким содержанием никеля, практические проблемы могут означать, что выборщики марок вместо этого предпочтут либо продолжать использовать более дорогие марки Cr-Ni, либо искать более дешевые альтернативы среди ферритных марок. или дуплексные сорта.
Кредиты
ASSDA благодарит г-на Питера Мура, менеджера по техническим услугам Atlas Specialty Metals, за вклад в эту статью.
Эта техническая статья была опубликована в журнале «Австралийская нержавеющая сталь» № 32 – зима 2005 г. и представляет собой выдержку из раздела «Выбор сорта» Справочного руководства Австралии по нержавеющей стали 2005 г.
Чтобы заказать копию этого важного технического ресурса для индустрии нержавеющей стали, загрузите форму заказа с веб-сайта ASSDA – www.assda.asn.au или позвоните в офис ASSDA по телефону 07 3220 0722.
Типы Никелевые сплавы и их свойства
Никель – это универсальный металл, который в изобилии содержится в земной коре и ядре.Никель, впервые обнаруженный и выделенный шведским химиком и минералогом Акселем Фредриком Кронштедтом, обладает несколькими желательными свойствами, которые делают его полезным в промышленности. Во-первых, никель очень пластичен и ценен как легирующий элемент, изменяющий свойства других металлов. Например, марки нержавеющей стали могут быть созданы путем добавления никеля для производства сплавов, которые обладают коррозионной стойкостью и высокотемпературной стойкостью, что делает их идеальными для использования на химических предприятиях, где можно ожидать воздействия едких веществ.
Эта статья будет посвящена обзору различных типов широко доступных никелевых сплавов. Определение сплава в случае никелевых сплавов – это тот, в котором никель является основным элементом (т.е. имеет самую высокую концентрацию всех металлов в сплаве).
Свойства никеля
Никель, химический символ которого – Ni, имеет серебристо-белый цвет и является первичным элементом с гранецентрированной кубической кристаллической структурой. Он является магнитным при комнатной температуре и имеет температуру Кюри 253 o ° C (487 o F).В таблице 1 ниже приведены некоторые другие ключевые физические свойства и характеристики никеля.
Таблица 1 – Характеристики и свойства никеля (Ni)
Характеристика | Значение |
Атомный номер | 28 |
Атомный вес | 58,69 |
Температура плавления | 1453 или С |
Температура кипения | 2730 o C |
Вторичная переработка / восстановление | Есть |
Плотность | 8.90 г / см 3 @ 25 o C |
Температура Кюри | 253 или С |
Звукоизоляция | 4900 м / с при комнатной температуре |
Коэффициент теплового расширения | 13,4 мкм / (м- o K) |
Коэффициент теплопроводности | 90.9 Вт / (м – o K) |
Удельное электрическое сопротивление | 69,3 нОм-м при 20 o C |
Модуль Юнга | 200 ГПа |
Модуль объемной упругости | 180 ГПа |
Модуль сдвига | 76 ГПа |
Коэффициент Пуассона | 0.31 |
Твердость по шкале Мооса | 4,0 |
Твердость по Виккерсу | 638 МПа |
Распространенные типы никелевых сплавов
Никель легко сплавится с большинством металлов, таких как медь, хром, железо и молибден. Добавление никеля к другим металлам изменяет свойства получаемого сплава и может использоваться для получения желаемых характеристик, таких как, например, улучшенная стойкость к коррозии или окислению, повышенные характеристики при высоких температурах или более низкие коэффициенты теплового расширения.
В разделах ниже представлена информация о каждом из этих типов никелевых сплавов.
Никель-железные сплавы
Никель-железные сплавы используются там, где желаемым свойством является низкая скорость теплового расширения. Инвар 36 ® , также продаваемый под торговыми марками Nilo 6 ® или Pernifer 6 ® , демонстрирует коэффициент теплового расширения, который составляет примерно 1/10 от коэффициента теплового расширения углеродистой стали. Эта высокая степень стабильности размеров делает никель-железные сплавы полезными в таких приложениях, как прецизионное измерительное оборудование или стержни термостатов.Другие сплавы никель-железо с еще более высокими концентрациями никеля используются в приложениях, где важны магнитомягкие свойства, таких как трансформаторы, индукторы или запоминающие устройства.
Никель-медные сплавы
Никель-медные сплавы очень устойчивы к коррозии в соленой или морской воде и поэтому находят применение в морских приложениях. Например, Monel 400 ® , также продаваемый под торговыми марками Nickelvac ® 400 или Nicorros ® 400, может найти применение в морских трубопроводных системах, валах насосов и клапанах для забортной воды.В этом сплаве минимальная концентрация 63% никеля и 28-34% меди.
Никель-молибденовые сплавы
Никель-молибденовые сплавы обладают высокой химической стойкостью к сильным кислотам и другим восстановителям, таким как соляная кислота, хлористый водород, серная кислота и фосфорная кислота. Химический состав сплава этого типа, такого как сплав B-2 ® , имеет концентрацию молибдена 29-30% и концентрацию никеля 66-74%. Применения включают насосы и клапаны, прокладки, сосуды под давлением, теплообменники и трубопроводные изделия.
Никель-хромовые сплавы
Никель-хромовые сплавы ценятся за их высокую коррозионную стойкость, жаропрочность и высокое электрическое сопротивление. Например, сплав NiCr 70/30, также обозначаемый как Ni70Cr30, Nikrothal 70, Resistohm 70 и X30H70, имеет температуру плавления 1380 90 980 o 90 981 ° C и удельное электрическое сопротивление 1,18 мкОм-м. Нагревательные элементы, такие как тостеры и другие электрические нагреватели сопротивления, используют никель-хромовые сплавы. Когда они производятся в форме проволоки, они известны как проволока из нихрома ® .
Никель-хром-железные сплавы
Сплавы никель-хром-железо объединяют эти элементы для получения сплавов, стойких к окислению и высокотемпературной коррозии. Сплав 800, продаваемый под торговыми марками Incoloy 800 ® , Ferrochronin ® 800, Nickelvac ® 800 и Nicrofer ® 3220, используется в компонентах печей, таких как трубы для крекинга нефтехимических печей, а также в качестве материала для обшивка электронагревательных элементов. Эти сплавы обычно также ценятся за их оптимальные свойства ползучести и разрыва при высоких температурах.В состав этих сплавов обычно входит 30-35% никеля, 19-23% хрома и минимум 39,5% железа. Высокая концентрация железа привела к реклассификации этих сплавов как нержавеющих сталей.
Никель-хром-молибденовые сплавы
Применяя аналогичные никель-молибденовые сплавы, никель-хром-молибденовые сплавы также обеспечивают высокую коррозионную стойкость, особенно в отношении восстанавливающих кислот, таких как соляная кислота и серная кислота. Одним из наиболее известных из этих сплавов является сплав C-276, также продаваемый под торговыми названиями Hastelloy C276 ® , Nickelvac ® HC-276, Inconel ® 276 и Nicrofer ® 5716.Этот сплав используется в облицовках, воздуховодах и скрубберах для контроля загрязнения, а также в компонентах химической обработки, таких как теплообменники, испарители или реакционные сосуды. Состав этого сплава в основном состоит из никеля с 15-17% молибдена, 14,5-16,5% хрома, 4-7% железа, 3-4,5% вольфрама и меньшими концентрациями других элементов, таких как марганец.
Никель-хром-кобальтовые сплавы
Эти никелевые сплавы добавляют хром и молибден, чтобы добавить сплаву предел прочности при ползучести.Сплав 617 является примером, продаваемым под торговыми марками Inconel 617 ® и Nicrofer ® 617, который имеет состав 20-24% хрома, 10-15% кобальта и 8-10% молибдена с минимальным содержанием никеля. содержание 44,5%. Эти сплавы применяются в компонентах промышленных печей, газовых турбинах, опорах каталитических решеток для производства азотной кислоты и на объектах по производству ископаемого топлива.
Никель-титановые сплавы
Никель-титановые сплавы обладают сохранением формы и свойствами памяти формы.Формируя форму из этого сплава при более высокой температуре и деформируя его из этой сформированной формы при более низкой температуре, сплав запомнит исходную форму и преобразовывается в эту форму после нагревания до этой так называемой температуры перехода. Регулируя состав сплава, можно изменять температуру перехода. Эти сплавы обладают сверхэластичными свойствами, которые могут быть использованы для обеспечения, помимо прочего, амортизатора от повреждений в результате землетрясения для защиты каменных зданий.
Форм-факторы никелевого сплава
Поставщики никелевых сплавов предлагают их в различных форм-факторах, которые обычно включают:
Другие варианты формы материала, такие как кованые кольца, заготовки или блоки, могут быть доступны у поставщиков по запросу.
Общие торговые наименования сплавов никеля
Ниже в таблице 2 приведены некоторые из наиболее распространенных торговых наименований типов никелевых сплавов, продаваемых на рынке.
Таблица 2 – Распространенные типы никелевых сплавов и торговые наименования
Имя | Тип сплава | Альтернативные торговые наименования |
Никель 200 | 99% + чистый никель | Никель 99.2 |
Никель 201 | 99% + чистый никель | Никель 201, LC Никель 99,2 |
Монель 400 ® | Никель-медь | Никельвак ® 400, Никоррос ® 400 |
Монель R405 ® | Никель-медь | |
Монель K500 ® | Никель-медь | |
Инконель 600 ® | Никель-хром-железо | Никельвак ® 600, Феррохронин ® 600 |
Инконель 601 ® | Никель-хром-железо | Pyromet ® 601, Nicrofer ® 601 |
Инконель 617 ® | Никель-хром-кобальт | Nicrofer ® 617 |
Инконель 625 ® | Никель-хром-железо | Chornin ® 625, Altemp ® 625, Nickelvac ® 625, Haynes ® 625 Nicrofer ® 6020 |
Инконель 718 ® | Никель-хром-железо | Nicrofer ® 5219, Alvac ® 718, Haynes ® 718, Altemp ® 718 |
Инконель X750 ® | Никель-хром-железо | Haynes X750 ® , Pyromet ® X750, Nickelvac ® X750, Nicorros ® 7016 |
Инколой 800 ® | Никель-хром-железо | Феррохронин ® 800, Никельвак ® 800, Nicrofer ® 3220 |
Инколой 825 ® | Никель-хром-железо | Nickelvac ® 825, Nicrofer 4241 ® |
Хастеллой C22 ® | Хром-молибден-вольфрам | Инконель ® 22, Nicrofer ® 5621 |
Хастеллой C276 ® | Никель-хром-молибден | Никельвак ® HC-276, Инконель ® 276, Nicrofer ® 5716 |
Хастеллой B2 ® | Никель-хром-молибден | Нимофер ® 6928 |
Хастеллой X ® | Никель-хром-железо-молибден | Nickelvac ® HX, Nicrofer ® 4722, Altemp ® HX, Inconel ® HX |
Vascomax ® C250 | Никель-кобальт-молибден | Maraging C250 ™, Maraging 250 ™ |
Vascomax ® 300 | Никель-кобальт-молибден | Maraging 300, Maraging C300 ® и Vascomax ® C300 |
Vascomax ® C350 | Никель-кобальтовая сталь | Maraging C350 ™ |
Рене ® 41 | Никель-хром | |
Мультиметр ® N155 | Никель-хром-кобальт | |
Waspaloy 25 ™ | Никель-кобальт | |
Инвар 36 ® | Никель-железо | Нило 6 ® , Пернифер 6 ® |
Инвар 42 ® | Никель-железо | Нило 42 ® |
Резюме
В этой статье представлен краткий обзор наиболее распространенных типов никелевых сплавов и их использования.Для получения информации о других продуктах обратитесь к нашим дополнительным руководствам или посетите платформу Thomas Supplier Discovery Platform, чтобы найти потенциальные источники поставок или просмотреть подробную информацию о конкретных продуктах.
Источники:
- https://www.nickelinstitute.org/about-nickel/nickel-alloys/
- https://www.magellanmetals.com/nickel-alloys
- https://www.unifiedalloys.com/resources/tech-data/uns-reference/
- http://www.nickelalloys.eu/uploads/4/4/1/8/44185717/nicr7030-2019.pdf
- http://www.specialmetals.com/assets/smc/documents/alloys/incoloy/incoloy-alloy-800.pdf
- http://megamex.com/hastelloy-c-276-c276-nickel-alloy.htm
Уведомления о товарных знаках:
Торговые наименования, торговые марки и зарегистрированные торговые марки никелевого сплава, упомянутые в этой статье, являются собственностью соответствующих владельцев, как показано ниже:
- Hastelloy ® – зарегистрированная торговая марка Haynes International.
- Monel ® , Inconel ® , Ni-Span ® , Nimonic ® , Incoloy ® , Nilo 6 ® и Nilo 42 ® и являются зарегистрированными товарными знаками Special Metals Corporation.
- Waspaloy 25 ™ является товарным знаком United Technologies / Pratt & Whitney.
- Pernifer 6 ® , Nimofer ® и Nicorros ® являются зарегистрированными товарными знаками ThyssenKrupp-VDM, Германия.
- Nitronic ® , 15-7 MO, 15-5 PH, 17-4 Ph, 17-7 PH, PH 13-8 MO являются зарегистрированными товарными знаками AK Steel Corporation.
- Maraging C250 ™, Maraging 250 ™, Maraging 300, Maraging C300 ® , Maraging C350 ™, Rene, Nickelvac ® , Nicrofer ® и Vascomax являются зарегистрированными товарными знаками компании Allegheny Technologies (ATI), Pittsburgh, PA
- Invar 36 ® – зарегистрированная торговая марка Carpenter Technology Corporation.
- Инвар ® – зарегистрированная торговая марка Arcelor Mittal.
Больше от Metals & Metal Products
Обработка никеля | Британника
Обработка никеля , подготовка металла для использования в различных изделиях.
Хотя никель (Ni) больше всего известен своим использованием в чеканке монет, он стал гораздо более важным для многих промышленных применений, которые обязаны своим значением уникальной комбинации свойств.Никель имеет относительно высокую температуру плавления 1453 ° C (2647 ° F) и гранецентрированную кубическую кристаллическую структуру, которая придает металлу хорошую пластичность. Никелевые сплавы обладают высокой устойчивостью к коррозии в самых разных средах и способны выдерживать широкий диапазон высоких и низких температур. В нержавеющих сталях никель улучшает стабильность защитной оксидной пленки, которая обеспечивает коррозионную стойкость. Его основной вклад связан с хромом в аустенитных нержавеющих сталях, в которых никель позволяет сохранять аустенитную структуру при комнатной температуре.Современные технологии сильно зависят от этих материалов, которые составляют жизненно важную часть химической, нефтехимической, энергетической и смежных отраслей.
История
Никель использовался в промышленности в качестве легирующего металла почти за 2000 лет, прежде чем он был выделен и признан новым элементом. Еще в 200 г. до н. Э. Китайцы сделали значительное количество белого сплава из цинка и медно-никелевой руды, найденной в провинции Юньнань. Сплав, известный как pai-t’ung , экспортировался на Ближний Восток и даже в Европу.
Позже горняки в Саксонии наткнулись на то, что выглядело как медная руда, но обнаружили, что при ее переработке был получен только бесполезный шлакоподобный материал. Они посчитали это заколдованным и приписали дьяволу «Старый Ник». Таким образом, он стал известен как купферникель (медь Старого Ника). Именно из этой руды, изученной Акселем Фредриком Кронштедтом, был выделен никель и признан новым элементом в 1751 году. В 1776 году было установлено, что pai-t’ung , теперь называемое никель-серебром, состоит из меди, никель и цинк.
Получите подписку Britannica Premium и получите доступ к эксклюзивному контенту. Подпишитесь сейчасСпрос на нейзильбер был стимулирован в Англии примерно в 1844 году развитием гальваники серебра, для которого оно было признано наиболее желательной основой. Несколько позже было разработано использование чистого никеля в качестве коррозионно-стойкого гальванического покрытия; оба эти использования по-прежнему важны.
Небольшие количества никеля производились в Германии в середине 19 века. Более значительные суммы поступили из Норвегии, а небольшая часть – из шахты в Гэпе, штат Пенсильвания, в Соединенных Штатах.Новый источник, Новая Каледония в южной части Тихого океана, был введен в производство около 1877 года и доминировал до разработки медно-никелевых руд в районе Медно-Клифф-Садбери, Онтарио в Канаде, который после 1905 года стал крупнейшим в мире источником никеля. . К концу 1970-х годов производство в Советской России превысило производство в Канаде. К началу 21 века Китай стал мировым лидером по производству никеля, за ним следуют Россия, Япония, Австралия и Канада.
Канадские руды представляют собой сульфиды, содержащие никель, медь и железо.Наиболее важным минералом никеля является пентландит (Ni, Fe) 9 S 8 , за которым следует пирротин, обычно от FeS до Fe 7 S 8 , в котором часть железа может быть заменена никелем. . Халькопирит, CuFeS 2 , является доминирующим минералом меди в этих рудах, с небольшими количествами другого минерала меди, кубанита, CuFe 2 S 3 . Также присутствуют золото, серебро и шесть металлов платиновой группы, и их извлечение важно.Кобальт, селен, теллур и сера также могут быть извлечены из руд.
Другими важными классами руд являются латериты, которые являются результатом длительного выветривания перидотита, изначально содержащего небольшой процент никеля. Выветривание в субтропическом климате удаляет большую часть вмещающей породы, но содержащийся никель растворяется и просачивается вниз и может достигать концентрации, достаточно высокой, чтобы сделать добычу рентабельной. Из-за этого метода образования отложения латерита обнаруживаются вблизи поверхности в виде мягкого, часто глинистого материала, с концентрацией никеля в пластах в результате выветривания.Гарниерит, (NiMg) 6 Si 4 O 10 (OH) 8 , силикат никеля и магния, самый богатый никелем, но никелевый лимонит (Fe, Ni) O (OH) · n H 2 O, составляет основную часть латеритов. Месторождения Новой Каледонии относятся к типу гарниерита, и множество других месторождений латерита разбросаны по всему миру, что создает широкий спектр проблем, связанных с добычей, транспортировкой и извлечением. Содержание никеля в латеритах широко варьируется: например, на заводе Le Nickel в Новой Каледонии руда, доставленная на плавильный завод в 1900 году, содержала 9 процентов никеля; в настоящее время он составляет от 1 до 3 процентов.
Поскольку никель содержится в двух радикально разных типах руды, неудивительно, что методы его добычи различаются.