Сплав для пайки – Сплав для пайки, 6 букв
alexxlab | 31.08.2020 | 0 | Разное
Рекомендуем приобрести: Установки для автоматической сварки продольных швов обечаек – в наличии на складе! Сварочные экраны и защитные шторки – в наличии на складе! Алюминий и его сплавы находят широкое применение для изготовления паяных конструкций в авиационной, электротехнической, радиотехнической и ряде других отраслей промышленности. Особенности пайки алюминиевых сплавов определяются такими факторами, как высокая стойкость оксидной пленки, низкая температура солидуса большинства промышленных алюминиевых сплавов, высокая теплоемкость алюминия. Алюминий, обладая большим сродством к кислороду, образует стойкий оксид Аl2O3, находящийся на его поверхности в виде плотной и прочной пленки. Состав и структура оксидных пленок на поверхности алюминиевых сплавов зависят от состава последних. Так, на поверхности алюминиево-магниевых сплавов присутствует смесь оксидов Аl Для высокотемпературной пайки алюминиевых сплавов в качестве флюсов применяют смеси солей хлоридов щелочных и тяжелых металлов с добавками фторидов металлов. Пайку алюминия с указанными флюсами производят припоями на основе алюминия типа силумин, 34А, П425А, В62 и др. Зазор при флюсовой пайке должен быть не менее 0,1…0,25 мм. Высокотемпературная флюсовая пайка алюминия и его сплавов может производиться с применением газопламенного, печного, индукционного и контактного нагрева, а также путем погружения в расплавы флюсов. Для пайки алюминиевых деталей применяют бензовоздушные и газовоздушные горелки. Ацетилено-кислородное пламя непригодно, так как снижает активность флюсов.Для пайки ажурных тонкостенных конструкций из алюминиевых сплавов хорошие результаты обеспечивает печной нагрев. Скорость нагрева для пайки зависит от толщины стенок соединяемых деталей. Температуру печной пайки с применением припоя 34А и флюса 34А поддерживают 550…560 °С; при пайке эвтектическим силумином – 580…600 °С. Применение флюса 34А при печном нагреве опасно ввиду возможности значительного растворения паяемого металла цинком, выделяющимся из флюса; в случае пайки тонкостенных деталей это может привести к сквозному проплавлению. Лучшие результаты дает применение флюсов, в которых хлористый цинк заменен на хлористое олово, хлористый кадмий или хлористый свинец. Это приводит к резкому снижению растворения паяемой поверхности металлом, выделяющимся из флюса. Пайка в солевых ваннах отличается высокой производительностью В связи со значительной температурой пайки (580…620 °С) этим способом паяют сплавы с высокой температурой ликвидуса – АД1, АМц и др. Припои должны быть заранее нанесены на паяемые поверхности в виде покрытия или плакирующего слоя (пайка пластинчатых теплообменников). В случае пайки в солевых расплавах состав флюсовой ванны не должен содержать активных хлоридов типа ZnCl При подготовке поверхности изделий из алюминиевых сплавов к пайке рекомендуется после обезжиривания поверхностей производить их травление в 7…10 %-ном растворе едкого натра при 60 °С с последующей промывкой в холодной воде и обработкой в 20 %-ном растворе азотной кислоты, после чего следует тщательная промывка в проточной горячей и холодной воде и сушка горячим воздухом. Пайку рекомендуется производить не позже чем через 2-3 суток после травления. При пайке погружением в расплав флюса необходим предварительный подогрев изделий до 400…500 °С. Сборку изделий под пайку производят с помощью специальных приспособлений, не взаимодействующих с солевыми расплавами. Приспособления изготовляют из коррозионно-стойких сталей, инконеля, керамики. Своеобразной разновидностью флюсовой высокотемпературной пайки алюминия и его сплавов является реактивно-флюсовая. Флюсы-пасты для этой цели, как правило, содержат до 90 % активных хлоридов. При использовании таких паст наблюдается заметная эрозия основного металла. Для избежания указанного недостатка пайку производят погружением в солевую ванну, в состав которой вводят небольшое количество (в сумме до 1 %) активныххлоридов типа хлористого цинка, хлористого олова, хлористого кадмия и др. В связи с тем что остатки флюсов чрезвычайно коррозионно-активны, особенно при эксплуатации паяных соединений в электропроводящих средах, необходимо сразу же после пайки изделия подвергать тщательной обработке с целью удаления остатков флюсов; с этой целью их промывают в горячей и холодной проточной воде с последующей обработкой в 5 %-ном растворе азотной кислоты или в 10 %-ном растворе хромового ангидрида Однако флюсы могут оказаться и внутри паяного шва, и такая обработка не устранит опасности возникновения очагов коррозии. В этом заключается основной недостаток флюсовой пайки алюминиевых сплавов. Прочностные характеристики паяных соединений при применении наиболее распространенных припоев приведены в табл. 10. 10. Прочность паяных соединений из алюминиевых сплавовНизкотемпературную пайку алюминия и его сплавов припоями на основе олова можно осуществить с применением флюсов на основе высококипящих органических соединений типа триэтаноламина с добавками в качестве активных компонентов борфторидов кадмия и цинка. Применение этих флюсов хотя и обеспечивает удаление оксида алюминия при пайке, но в промышленности они не нашли широкого распространения, так как не обеспечивают получения надежных и герметичных соединений. Кроме того, компоненты легкоплавких припоев в паре с алюминием образуют коррозионно-нестойкие соединения вследствие большой разности нормальных электродных потенциалов. Такие соединения не способны работать в коррозионно-активных средах. Указанные недостатки и затруднения исчезают при использовании технологических покрытий под пайку. В качестве таких покрытий при низкотемпературной пайке алюминия принято использовать медь, никель, серебро, цинк и т.п. Покрытие может быть нанесено электролитически, химически, термовакуумным напылением и другими способами. Наиболее высокое качество сцепления покрытия с основным металлом и коррозионную стойкость паяных соединений обеспечивает применение никельфосфорных покрытий, наносимых на поверхность алюминия химическим способом из специальных гипофосфитных растворов. Оптимальная толщина покрытия 17…25 мкм. После нанесения покрытия деталь подвергают термической обработке в защитной среде (аргон или вакуум) при 200 °С в течение 1 ч, что приводит к повышению прочности сцепления покрытия с поверхностью паяемого металла. Пайка по покрытию легкоосуществима оловянно-свинцовыми припоями с применением канифольно-спиртовых флюсов или флюсов на основе водных растворов хлористого цинка. Коррозионная стойкость таких соединений намного выше стойкости соединений из алюминия, выполненных без защитных покрытий. Соединения из сплавов АМц и Д16. выполненные по никельфосфорному покрытию припоем ПОС61, обеспечивают σср = 30…50 МПа. После годичных испытаний в 3 %-ном растворе поваренной соли прочность соединений снижается лишь на 15…18 %. Коррозионная стойкость соединений, выполненных по медному покрытию, особенно в коррозионно-активных средах, гораздо ниже, чем, по никельфосфорному покрытию; коррозионная стойкость повышается при пайке по цинковым покрытиям и, в частности, по слою цинкового сплава, содержащего 5 % Аl. Слой нанесен на поверхность алюминия методом горячего плакирования. Пайку по цинковому покрытию рекомендуется вести припоем типа ПОСК51 с удалением оксидных пленок механическим способом или с помощью флюса на основе эвтектики NaOH-KOH, вводимой в количестве до 20 % в глицерин. Бесфлюсовую высокотемпературную пайку алюминия можно осуществить в вакууме, в газовых средах без применения защитных покрытий (контактно-реактивным методом). В качестве припоя применяют кремний, медь или серебро, которые наносят на алюминий гальванически, термовакуумным напылением или методом горячего плакирования. Высокое качество паяного соединения получают при пайке в вакууме 10-3 Па и толщине покрытия 10…12 мкм. Пайку алюминия припоями типа силумин осуществляют в специальных газовыхсредах: смесях аргона с парами магния. Такая атмосфера способна при 550…580 °С восстанавливать оксид алюминия и обеспечивать смачивание паяемой поверхности припоями типа силумин. При пайке алюминиевых сплавов в атмосфере паров магния последний переходит из газообразной фазы в расплав. Предел прочности на срез соединений сплава АМг6, выполненных этим способом, 352…358 МПа, а для сплава АМц – 115…125 МПа. Коррозионная стойкость получаемых соединений намного выше, чем при флюсовой пайке. Пайку в защитной атмосфере можно осуществить при использовании самофлюсующих припоев [например, составов (в %): 3 – 15 Si; 0,4 – 1,0 Mg; Аl – остальное, или 7,5-13 Si; 0,3 Сu; 0,1 Mg; 4,5 Р; 0,1 – 3,0 металлов из группы Ni и Со; 0,2 Zn; 0,5 Mn; Аl -остальное]. Пайку этими припоями следует производить в среде аргона, гелия или в вакууме. Бесфлюсовую пайку алюминия припоями типа 34А, силумин (ПСр 5АКЦ) можно производить по предварительно луженой поверхности припоем П200А. Лужение производят механическим способом; толщина слоя 0,03…0,05 мм на сторону. Нагрев под пайку рекомендуется производить в печи в потоке аргона или на воздухе индукционным способом. Прогрессивные способы пайки в вакууме и инертных средах значительно вытеснили пайку с применением флюсов. Пайку в вакууме осуществляют в специальных печах при разрежении 1 * 10-3 Па (в этом случае в камере пайки содержится 3 * 10-7 г/м3 кислорода и 2 * 10-8 г/м3 паров воды). В процессе нагрева с изделия и с внутренней поверхности печи происходит десорбция паров воды и кислорода, что значительно ухудшает состав среды. Для улучшения состава атмосферы применяют распыляемый геттер – магний. При пайке в вакууме с распыляемым геттером получают высококачественные паяные соединения. Недостатком этих печей и способа является сложность удаления после пайки магния, конденсирующегося на стенках печного пространства, нагревателях и теплоотражающих экранах, а также длительность цикла нагрева изделия. Альтернативой способу пайки в вакуумных печах, имеющих внутри камеры экраны и нагреватели, является пайка в аргоне в печах с аэродинамическим подогревом. Внутри рабочей камеры этих печей нет традиционных экранов и нагревателей, а нагрев в них осуществляют вращающиеся колеса с лопатками, и он происходит за счет диссипации энергии газа при его вихреобразовании на лопатках специального профиля. Примером использования такого способа нагрева является агрегат, созданный в ОАО «Криогенмаш» для бесфлюсовой пайки алюминиевых изделий в аргоне. Агрегат состоит из термобарокамеры со встроенными аэродинамическими нагревателями (АДН), систем очистки аргона и подачи его в камеру, вакуумирования, контроля и управления процессом пайки и средств загрузки и выгрузки изделия. Рабочая камера агрегата объемом 40 м3 представляет собой гладкий стальной толстостенный цилиндр, внутри которой нет экранов, поэтому она легка и доступна для очистки от конденсирующихся компонентов. Перед напуском каталитически очищенного аргона камера вакуумируется до разрежения 10-3 Па; нагрев камеры до температуры 635 °С с градиентом по газу 3…5 °С осуществляется тремя встроенными АДН общей мощностью 450 кВт. Аэродинамические колеса, вращающиеся с переменной частотой (500, 1000, 1500 об/мин), позволяют регулировать интенсивность нагрева. Теплоотдача от газа к изделию осуществляется путем интенсивной конвекции сильно турбулизированного потока газа, а также теплопроводности по элементам конструкции. По сравнению с вакуумной пайкой, при сопоставимых габаритах и показателях качества изделий, пайка в среде аргона за счет сокращения термического цикла (интенсивный нагрев в газе и выгрузка изделия при 400 °С) является более производительной (на 20 %), менее энергоемкой (на 30 %), а конструкция камеры пайки, не содержащей экранов, облегчает очистку камеры от сконденсированного магния. Качество паяных соединений из алюминиевых сплавов зависит как от выбора эффективного способа предварительной подготовки поверхностей деталей к пайке, включающего удаление жировых загрязнений и «старых» оксидных пленок, так и от состава газовой среды, в которой производится пайка. Для подготовки поверхностей деталей к пайке распространение получили в основном два способа: травление в щелочных растворах и в растворах кислот. Однако эти способы подготовки поверхности нельзя отнести к экологически чистым. Между тем в настоящее время созданы универсальные кислотные и щелочные очищающие средства, представляющие собой водорастворимые, нетоксичные, взрывопожаробезопасные, полностью биоразлагаемые жидкости широкого спектра применения, в составе которых присутствуют поверхностно-активные вещества и компоненты, способные удалять с поверхностей алюминиевых сплавов жировые загрязнения и оксидные пленки. Такие средства в виде концентратов производит, например, российская компания «ЕСТОС». Продукция компании сертифицирована, по гигиеническим показателям допущена к производству на территории России в качестве очищающих средств, в промышленности и в быту. Активность растворов очистителей на основе ортофосфорной кислоты, например ЕС-очиститель фасадов ФФ (ЕС – ФФ), начинается с 10 %-ной концентрации. В отличие от широко распространенных кислотных и щелочных способов подготовки поверхностей деталей обработка в растворе ЕС – ФФ производится при значительно меньшей потере металла (7,0 мкм/мин в NaOH и 0,09 мкм/мин в очистителе ЕС – ФФ). Раствор ЕС – ФФ сохраняет высокую активность после обработки не менее 1,0 м2 на 1 л раствора без корректировки состава. При пайке в вакуумных печах с разрежением в камере пайки 1 * 10-3 Па газовая среда содержит 3 * 10-7 г/м3 кислорода и 2 * 10-8 г/м3 паров воды. При пайке в аргоне содержание паров воды и кислорода на 2-3 порядка выше, что неблагоприятно для пайки Аl-сплавов. Так, в аргоне высшего сорта по ГОСТ 10157-79 содержится 7 * 10-4 г/м3 кислорода. При пайке алюминиевых сплавов припоями типа силумин в таком непроточном аргоне качественных соединений не образуется. Это еще связано и с непрерывным ухудшением атмосферы в процессе пайки за счет термической дегазации паров воды и кислорода с поверхностей изделия, камеры и приспособления. Улучшить состав газовой среды в данном случае можно за счет предварительного и промежуточного вакуумирования камеры до 1 * 10-3 Па, подогрева изделия с приспособлением, дополнительной осушки аргона от паров воды и кислорода и применения нераспыляемого геттера – пористого титана. Например, в процессе пайки в аргоне высокой чистоты (ТУ 6-21-1279) при использовании названных приемов среда для пайки улучшается на порядок и содержит 6 * 10-4 г/м3 кислорода и 1 * 10-4 г/м3 паров воды. Однако в аргоне при пайке сплава АМц эвтектическим силумином даже в такой среде не удается получить стабильное качество соединения. Условия пайки существенно улучшаются, если в паяемом металле или припое содержится магний в количестве не более 1 %. При нагреве в атмосфере аргона алюминиевых сплавов, легированных магнием, магний практически не испаряется, а диффундирует к поверхности детали и способствует разрушению оксидной пленки и улучшению растекания припоя. В результате технологический процесс, включающий каталитическую очистку аргона, двукратное вакуумирование камеры, использование нераспыляемого геттера, ампулирование изделия и подготовку паяемых поверхностей экологически чистыми растворами, реализован при пайке крупногабаритных пластинчато-ребристых теплообменников (ПРТ) длиной 3000 мм и сечением 850 х 1100 мм. Пайка производится при температуре 605 ± 5 °С. Общее время цикла составляет 22 ч. Конструктивно ПРТ представляет собой паяный пакет из проставочных листов толщиной 1…1,5 мм и гофрированной насадки, выполненной из ленты толщиной 0,2…0,7 мм. Припоем служит эвтектический (11,7 % Si) или близкий к эвтектическому силумин, которым с обеих сторон на толщину 80…120 мкм плакирован проставочный лист. Количество припоя, наносимого на паяемые поверхности, должно быть расчетным, поскольку при недостаточной толщине плакированного слоя снижаются качество и прочность соединений, а при избыточной возможно растворение тонкостенных элементов. При пайке крупногабаритных конструкций ПРТ применение сплавов, содержащих магний, для тонкостенной насадки (0,15…0,3 мм) недопустимо, так как проникновение припоя по границам зерен приводит к полной потере ее устойчивости. Поэтому насадку изготавливают из сплава АМц, в качестве материала для брусков используют сплав АД31, содержащий магний, а для проставочных листов применяют сплав АМц, плакированный эвтектическим силумином. Известны способы низкотемпературной пайки без применения флюсов, такие, как абразивная пайка или пайка трением. При этом способе пайки оксидную пленку с поверхности алюминия можно удалить шабером, металлическими щетками, частицами абразива; помогают удалению оксида и первичные твердо-жидкие кристаллы, находящиеся в расплаве припоя. Для лужения алюминия применяют также абразивные паяльники, у которых рабочая часть представляет собой стержень из частиц припоя и абразива. Операция пайки осуществляется уже после абразивного лужения обеспечением плотного контакта по луженым поверхностям при температуре полного расплавления припоя; возможна подпитка шва припоем. Ультразвуковое лужение можно производить с помощью ультразвуковых паяльников и в ультразвуковых ваннах. В связи с тем что при ультразвуковом лужении отмечается сильная эрозия основного металла, лужению этим способом нельзя подвергать изделия с толщиной стенок менее 0,5 мм. Применим также способ абразивно-кавитационного лужения. При этом способе твердые частицы, находящиеся в жидком припое, в ультразвуковом поле оказывают дополнительное абразивное воздействие на металл. При пайке алюминия припоями-пастами на основе галлия в качестве наполнителя паст служат алюминий и сплав алюминия с магнием. Температура пайки 200 … 225 °С, время выдержки 4…6 ч; σв = 30…50 МПа. При пайке луженой поверхности чистым галлием с последующей термической обработкой σв = 28…38 МПа. Паяные швы выдерживают ударные, вибрационные и термоциклические нагрузки, обеспечивают вакуумную плотность не ниже 1 Па и имеют удовлетворительную коррозионную стойкость. Применяют пайку алюминия цинковыми припоями по серебряному покрытию, нанесенному на поверхности пайки предпочтительно термовакуумным напылением с последующей термической обработкой. Разработан ряд технологических процессов, обеспечивающих надежное соединение алюминия с медью и ее сплавами, со сталью, никелевыми и другими сплавами. Основные трудности при осуществлении процесса пайки алюминия с указанными материалами заключаются в следующем: в выборе флюса или газовой среды, обеспечивающей удаление оксидов с поверхностей столь разнородных материалов; в образовании хрупких соединений из-за возникновения интерметаллидов в зоне шва; в наличии большой разности ТКЛР алюминия и перечисленных материалов. Первые две задачи успешно решаются предварительным нанесением на поверхности соединяемых материалов защитных металлических покрытий. Пайку алюминия с медью можно осуществить по никелевому покрытию, нанесенному на алюминий химическим способом. Пайку производят в водороде припоем состава (в %): 49 Ag, 20 Сu, 31 In; температура пайки близка к температуре плавления алюминия. Пайка алюминия с медью и ее сплавами может быть также осуществлена нанесением защитных покрытий типа цинка, серебра и их сплавов на поверхность меди. При этом используют припои на основе олова, кадмия, цинка. Через серебряное покрытие на меди может быть осуществлена контактно-реактивная пайка с образованием в паяном шве хрупкой эвтектики Al-Ag-Cu. Такие паяные соединения могут быть использованы только в ненагруженных конструкциях. Соединение алюминия со сталью, в том числе и с коррозионно-стойкой, облегчается при предварительном лужении поверхности стальной детали легкоплавкими оловянисто-свинцовыми припоями, алюминием и алюминиевыми припоями с применением активных флюсов на основе хлористых и фтористых солей. При пайке алюминия со сталью очень важно строго ограничивать режим из-за опасности образования хрупких интерметаллидов в паяных швах (время выдержки не должно превышать 1…4 мин, температура пайки – заданного предела). Пайка алюминия с титаном возможна только по слою алюминия или олова, нанесенному на поверхность титана путем горячего лужения. См. также: |
www.autowelding.ru
Припои для пайки магниевых сплавов
По сравнению с алюминием трудности пайки магния состоят не только в более активном окислении и образовании окисной пленки, а главное в том, что в состав большинства магниевых сплавов входят низкотемпературные эвтектики системы Mg — А1, Mg—Zn и А1 — Zn.
В процессе нагрева эти эвтектики уже при температурах 340—360° С начинают выплавляться и, вступая во взаимодействие с компанентами припоя, вызывают интенсивное растворение основного металла на значительную глубину. Проверить это легко на следующих опытах.
При нагреве двух образцов, поставленных в стык, из которых один из магниевого сплавов марки МА2, а второй из алюминия А00, уже при температуре порядка 380° С происходит пайка без применения каких-либо припоев и флюсов.
Пайка без применения припоев и флюсов легко достигается также при нагреве стыка образцов из магниевых сплавов при сочетании МА2 с МА2, MAl с МА2, МА8 с МА2. Характерно, что такие швы не имеют практической ценности, ибо при незначи — 34 тельной ударной нагрузке они сразу же разрушаются. Разрушение их происходит не по самому шву, а на 1—2 мм отступя от поверхности раздела металлов в глубину того сплава, из которого выплавляются низкотемпературные эвтектики.
Чрезвычайно большая хрупкость этих швов связана с образованием интерметаллических соединений, наиболее хрупкими из которых является Mg4Al3.
Известно [19], что растворимость алюминия в твердом магнии при комнатной температуре составляет 6%, а при эвтектической равной 436° С, — до 12,6%.
Микроструктура сплава магния с содержанием более 3% А1 состоит из зерен твердого раствора, окруженных выделениями интерметаллического соединения Mg4Al3, количество которого увеличивается по мере повышения содержания алюминия.
При 15%’ алюминия в магнии сетка выделения интерметал — лита по границам зерен становится замкнутой, что приводит к повышенной хрупкости сплава. При меньшем содержании алюминия в магнии соединение Mg4Al3 не образует замкнутой сетки и структура сплава представляет однородный твердый раствор.
Наличие в сплаве интерметаллического соединения нежелательно, так как ухудшаются не только технологические свойства, но и коррозионная стойкость сплава.
При выборе состава припоев необходимо также учитывать допустимые и недопустимые контакты.
Допустимыми контактами для магниевых сплавов являются цинк, кадмий, олово или детали из других сплавов, покрытые этими металлами.
Недопустимыми — со сталями; незащищенным алюминием и его сплавами; медью и ее сплавами; никелем; со свинцом.
По литературным источникам [11, 8], для пайки магниевых сплавов используются твердые припои, состав которых приведен в табл. 16.
Таблица 16
Известные припои для пайки магниевых сплавов
|
Перечисленные в этой таблице припои при испытании на растекание, механическую прочность паяного шва, металлографические исследования его структуры, а также способности припоев 3* 35
к оксидированию, в целях защиты от коррозии, дали следующие результаты:
Припои AZ92 с температурой плавления 597° С и AZ125 с температурой плавления 574° С вследствие высоких температур плавления пригодны лишь для пайки Мг и МА1, которые отличаются высокими температурами начала плавления и не содержат в своем составе легкоплавких эвтектик. Небольшой интервал в температурах между началом плавления припоев и основным материалом требует высокой квалификации оператора и не исключает проплава и загорания металла в процессе нагрева и пайки.
Глубина диффузии припоев в основной металл достигает 1 —1,5 мм, в то время как нормальной принято считать глубину диффузии, не превышающую 0,15—0,2 мм. Паяные швы этими припоями наравне с основным металлом (Mr, МА1) принимают оксидирование, обеспечивая хороший декоративный вид паяных узлов и надежную защиту от коррозии.
Припои нельзя применять для пайки тонкостенных (тоньше 1 —1,5 мм) деталей из Мг и МА1 и, кроме этого, они совершенно непригодны для пайки других марок деформируемых магниевых сплавов, ибо, как известно, они имеют в своем составе легкоплавкие эвтектики, о которых говорилось выше и точка плавления их ниже чем у припоев.
Припои № 1 и № 2 с повышенным содержанием алюминия обеспечивают пайку, вернее «заливку», раковин в толстостенных отливках, даже без применения флюсов.
В основе пайки этими припоями лежат рассмотренные выше явления выплавления легкоплавких эвтектик из основного металла с образованием интерметаллического соединения Mg4Al3.
Рассмотрение микрошлифов показывает, что диффузия припоев в толщу основного металла достигает 2—3 мм, а сетка ин — терметаллита Mg4Al3 по границам зерен становится замкнутой, в результате чего швы приобретают хрупкость.
При пайке деталей из МА2 МАЗ, МА5 и др. с толщиной стенок менее 3 мм происходит сквозное проникновение припоев, вызывая искажение чистоты поверхности и конструктивных элементов деталей..
Поэтому припои № 1 и № 2 нельзя использовать собственно для пайки ряда деталей из деформируемых магниевых сплавов, хотя швы хорошо принимают оксидирование.
Наконец, припой с кадмием, медью и магнием при испытании на текучесть и смачиваемость показал самые низкие результаты. Пайка этим припоем происходит при его нагреве на 130—150° С выше точки плавления и сопровождается разъеданием основного металла на глубину 3—4 мм.
Швы, паянные этим припоем, не принимают оксидирования и благодаря наличию в припое значительного количества меди отличаются низкой коррозионной стойкостью.
Для пайки деталей из деформируемых магниевых сплавов в производстве электрорадиоаппаратуры припой оказался непригодным.
Разработка состава припоев для пайки деформируемых сплавов MAI, МА2, МА5, МА8 производилась с учетом следующих требований:
температура плавления припоя должна лежать ниже температуры конца кристаллизации, подвергаемых пайке металлов. Это предотвращает выплавление легкоплавких эвтектик и уменьшает опасность загорания основного металла деталей;
припой должен иметь достаточную жидкотекучесть и способность растворять твердый основной металл деталей с обеспечением глубины диффузии не более 0,2 мм;
припой должен обладать достаточной пластичностью и содержать в своем составе только такие элементы, контакты которых с магнием допустимы;
коррозионная стойкость припоя не должна уступать стойкости основного металла, а для надежной защиты паяных швов припой должен хорошо оксидироваться.
В результате тщательного анализа диаграмм состояния двойных и тройных сплавов магния с другими металлами разработаны, всесторонне проверены и рекомендуются к промышленному освоению припои марок П380Мг, П430Мг, которые в большей мере отвечают всем требованиям, чем припои, предложенные ранее.
Химический состав новых припоев и прочностные характеристики паяных швов приведены в табл. 17 и 18.
Таблица 17
Рекомендуемые припои для пайки магния
|
Таблица 18 Механические свойства швов при пайке в стык
|
Микроструктура припоев состоит из твердого раствора алюминия и цинка в магнии и эвтектики (твердого раствора + MgZn).
Таблица 19
Выбор припоев для пайки магниевых сплавов
|
Припои П380Мг и П430Мг, рекомендуемые для пайки магния и его сплавов, следует выбирать с учетом температурного интервала кристаллизации отдельных сплавов и припоев, руководствуясь указаниями табл. 19.
Прочностные испытания образцов из различных магниевых сплавов, паянных припоями П380Мг и П430Мг, показали, что разрушение нахлесточных соединений происходит не по шву, а по основному металлу в переходной зоне. Кроме этого, пайка и связанный с нею нагрев приводят к значительным потерям прочности, которая снижается у сплава МА1 до 50%, а у других магниевых сплавов от 10 до 30%.
Следует напомнить, что при сварке магниевых сплавов потери механической прочности еще более высокие. Поэтому при конструировании сварных и паяных узлов необходимо обязательно учитывать фактор снижения прочности основного металла.
Длительные испытания паяных швов в естественной атмосфере на протяжении двух лет и в камере влажности в течение 40 суток дали положительные результаты.
У всех образцов, где остатки флюсов сразу же после пайки были тщательно удалены, очагов коррозии на паяных швах не обнаружено. Паяные швы с наличием остатков флюса подвергались интенсивной коррозии и разрушались во влажной камере до окончания срока испытаний.
В процессе длительных коррозионных испытаний паяных соединений проводились также замеры переходного сопротивления, изменение которого составило всего 2—7 мком.
Рекомендуемые припои для пайки магниевых сплавов не уступают основному металлу в способности к оксидированию по общепринятой технологии, благодаря чему швы приобретают хороший декоративный вид и дополнительную защиту от коррозии.
hssco.ru
Припои для пайки меди и ее сплавов
В производстве аппаратуры и особенно таких изделий, как волноводы из меди и ее сплавов до последнего времени широкое применение имели лишь серебряные припои (по ОСТ 2982 марок ПСр70, ПСр45 и ПСр25) с относительно высокими температурами плавления, лежащими в интервале 720—780°С. В качестве флюса использовалась бура. Однако с разработкой более совершенных и легкоплавких по сравнению с бурой новых флюсов: тетрафторбораткалиевого, № 209 и № 284 — создались все условия для перехода на припои с пониженными температурами плавления.
Снижение температуры плавления применяемых припоев увеличивает перепад температур между точками начала плавления припоя и самого металла деталей, соединяемых пайкой. В свою очередь это уменьшает опасность проплава тонкостенных латунных деталей и степень их коробления.
Поэтому наряду со стандартными припоями в последние годы получили распространение новые серебряные припои с пониженными температурами плавления, известные под марками ПСр48КН, ПСр40К, ПСр2,5 и др.
Выпуск припоев в виде слитков, зерен и листов, оговоренных ОСТ 2982, в применении к пайке ТВЧ, в соляных ваннах, в инертных и восстановительных средах, где требовалась дозированная подача припоя, создавал значительные неудобства. Даже при пайке газовыми горелками приходилось листовой припой разрезать на прутки с острыми углами и заусеницами, которые при нагреве обгорали, увеличивая потери припоев и одновременно загрязняли швы окислами.
Кроме того, поставка припоев в слитках и листах значительно усложняла для потребителей технологию изготовления дозированных заготовок припоев в виде колец и шайб, которые проще всего изготовлять из калиброванной проволоки серебряных припоев.
В недавно выпущенном взамен ОСТ 2982 новом стандарте на серебряные припои — ГОСТ 8190 — 56 нашли отражение как новые припои с пониженными температурами плавления, так и поставка припоев в виде калиброванной проволоки.
Марки, состав и температурный интервал кристаллизации ряда серебряных припоев по ГОСТ 8190 — 56, наиболее приемлемых в производстве волноводов и других изделий радиотехнической аппаратуры, представлен в табл. 3.
Стандартные серебряные припои*
|
Наряду с температурой плавления при выборе припоя необходимо считаться с его электросопротивлением. В табл. 4 приведены характеристики серебряных припоев по удельному весу и электросопротивлению, которые замерялись на литых образцах.
Удельный вес и удельное электросопротивление
серебряных припоев
Таблица 4
|
Кроме полос, рассмотренные выше припои поставляются в виде проволоки с номинальными диаметрами 0,3; 0,5; 0,8; 1; 1,2; 1,6; 2; 2,5; 3; 3,6; 4 и 5 мм.
Помимо твердых серебряных припоев, при пайке деталей из
Допускаемые отклонения от состава см. ГОСТ 8190—56.
меди и ее сплавов при монтаже аппаратуры очень широко применяются мягкие оловянно-свинцовые припои, характеристики которых в соответствии с ГОСТ 1499 — 54 приведены в табл. 5.
Таблица 5 Мягкие оловянно-свинцовые припои
|
Для пайки монтажных соединений очень выгодно применять трубчатые припои, заполненные внутри канифолевым флюсом, поставка которых предусмотрена указанным выше стандартом. Это позволяет увеличить производительность труда, повысить качество пайки и снизить расход припоев на 20—25 %а флюсов на 40—50%.
Ознакомившись с температурой плавления применяемых твердых и мягких припоев отметим, что зачастую на практике при выборе припоя совершенно не учитывается такой важный фактор, как температурный интервал кристаллизации припоя и его связь с качеством пайки, временем нагрева и расходом энергии на нагрев деталей.
Это легко показать при рассмотрении диаграмм состояния существующих мягких и твердых припоев.
Из рассмотренных ранее условий очевидно, что при использовании, например, мягких припоев системы ПОС температура нагрева деталей и припоя должна не менее чем на 50°С превышать точку начала затвердевания припоя. Этот перегрев необходим для того, чтобы исключить пайку в интервале кристаллизации припоя, когда он имеет две фазы — жидкую и твердую, а его жидкотекучесть ничтожно мала.
Очевидно, при пайке припоем ПОС-ЗО детали и сам припой необходимо нагревать до температуры 300°С, что на диаграмме (рис. 10) будет соответствовать точке 3. После окончания пайки и особенно с момента начала кристаллизации припоя (точка 2, соответствующая 256°С и до полного его затвердевания, точка 1 22
183° С) необходимо предотвращать изделие от толчков и связанных со снятием с приспособления сотрясений, ведущих к образованию — трещин и снижению прочности паяного соединения.
при использовании ПОС-40, начало затвердевания которого наступает при 235° С (точка 2′), а полное затвердевание при 183°С, интервал кристаллизации сужается и температура нагрева под пайку уменьшается до 285° С (точка 3′), но опасность появления трешин от смещения и сотрясения паяного соединения не снимается.
————— ;—■- %Sn Рис. 10. Диаграмма состояния системы олово-свинец. |
‘ Существенное отличие можно наблюдать лишь у припоев эвтектического состава или близких к нему. Для рассматриваемой системы таким припоем является ПОС-61, у которого точки начала и конца затвердевания очень близки, температурный интервал кристаллизации почти отсутствует и это создает ряд технологических преимуществ.
Исключается возможность пайки в интервале кристаллизации припоя, а температура нагрева под пайку по сравнению со всеми другими припоями этой системы будет самой низкой (точка 3″).
При остывании паяных изделий припой почти мгновенно переходит в твердую фазу и опасность в появлении трещин от сотрясений исключается. Более того скорость смачивания и заполнения зазоров припоем, а также степень капиллярного подъема больше при эвтектическом составе припоя, чем при любом другом.
В конечном итоге все это способствует не только снижению температуры пайки, но и сокращению энергетических затрат, времени на нагрев под пайку, а также на выдержку при остывании изделий до полного затвердевания припоя.
Поэтому такие, не указанные в табл. 3, твердые припои, как ПСр44 с температурой начала плавления 650° С, полного расплавления 800° С и ПСр15 с соответствующими температурами 635° С и 810° С, хотя и оговорены в ГОСТ 8190 — 56, не могут считаться приемлемыми с точки зрения только что рассмотренных положений.
Оканчивая рассмотрение твердых и мягких припоев для пайки деталей на основе меди и в соединении их с другими металлами, скажем несколько слов о легкоплавких сплавах и припоях, без которых в ряде случаев нельзя обойтись.
Как правило, получение легкоплавких припоев связано с применением висмута, отличающегося высоким значением удельного электросопротивления. Если для олова оно равно 11,5, а для свинца 18,8, то у висмута электросопротивление составляет 110,8, и при выборе припоя этого нельзя забывать.
Чаще всего в приборостроении используют следующие легкоплавкие припои и сплавы, указанные в табл. 6.
Таблица 6 Легкоплавкие припои и сплавы
|
Анализ припоев, приведенных в табл. 3, 5 и 6, указывает на полное отсутствие припоев с температурами плавления в интервале 300—600° С.
Для пайки меди и ее сплавов вопрос о припоях с температурой плавления именно в этом интервале поставлен сейчас очень остро. Это вытекает из предъявляемых требований к теплостойкости ряда изделий.
Если для изделий, работающих при температурах до + 200° С, требования теплостойкости удовлетворяет пайка припоями ПСр2,5 или ПСрЗ, то для изделий с теплостойкостью + 300° С пайка этими припоями уже совершенно непригодна. Остается переход к припоям ПСр40 или ПСр50Кд с температурами плавления выше 600° С, но это не всегда возможно, так как электроизоляционные материалы паяемых деталей рассчитаны на температуру 350—400° С. Более того, применение припоя ПСр40 исключает работу обычными электропаяльниками и требует мощных источников нагрева.
hssco.ru
Пайка различных металлов и сплавов
Изделия, очищенные и подготовленные для пайки, не должны храниться продолжительное время во избежание окисления. Их следует возможно скорее загружать в печь или контейнер с обеспечением защитной среды. Особенное внимание должно быть уделено удалению воздуха при пайке высоколегированных сталей и сплавов, содержащих легкоокисляемые элементы. Удаление воздуха может достигаться вакуумированием или продуванием защитного газа — аргона. При продувании температура должна повышаться постепенно, начиная от комнатной до 800—900 С (1073— 1173 К). Этот процесс требует значительного расход аргона. Вакуумирование более рационально, так как при этом значительно снижается расход аргона. Большое значение при пайке имеет контроль температуры нагрева изделия; перегрев может оказать вредное влияние.
Общее время пребывания припоя в расплавленном состоянии состоит из времени:
t = t1 + t2 + t3
где t1 — время нагрева от температуры плавления припоя до температуры пайки; t2 — время выдержки при пайке; t3 — время охлаждения от температуры пайки до температуры кристаллизации припоя.
В случае взаимодействия припоя с основным металлом t1 и следует, возможно, сокращать. После окончания процесса панки необходимо удалить флюс, очистить окисленные поверхности, устранить наплывы и участки растекания припоя, в особенности в тех местах, которые подлежат последующей обработке. Требование удаления флюса вызвано возможным отрицательным влияние его, например появлением коррозии (в алюминиевых сплавах).
Флюсы (для пайки алюминиевого сплава) удаляют промывкой горячей и холодной водой при условии последующей обработки в растворе хромового ангидрида. Флюсы на основе буры образуют на поверхности твердую корку. Их удаляют механическим путем или погружением деталей в горячую воду. Паяные швы на алюминиевых сплавах обрабатывают металлической щеткой и вторично промывают от флюсов, могущих остаться в порах швов. Растекающийся припой удаляют механическим, химическим или электромеханическим способами.
Для контроля качества паяных соединений применяют разные методы. Существенное значение имеет внешний осмотр швов. Швы проверяются на прочность, плотность, электропроводность. Паяные швы можно контролировать физическими методами: рентгеновским просвечиванием, применением радиоактивных изотопов, прозвучиванием.
Кроме испытания паяных образцов без их разрушения, нередко применяют испытания с доведением их до разрушения. Результаты, полученные при испытаниях до разрушения нескольких образцов, позволяют установить механические свойства серии аналогичных изделий.
К углеродистым и низколегированным сталям относится стали, имеющие температуру плавления 1450—1520 С (1723—1793 К). При низкотемпературной пайке сталей применяются главным образом оловянно-свинцовые припои с активными флюсами. Перед пайкой рекомендуется детали облуживать. Это ускоряет процесс пайки и позволяет обеспечивать высокие механические свойства соединений.
Более часто для пайки сталей применяют высокотемпературные медно-цинковые припои с добавкой серебра (температура плавления 940—700 С (1213—973 К). Однако вследствие легкого испарения цинка эти припои не применяют для вакуумной панки. Их целесообразно использовать при пайке в среде с низкими окислительными свойствами, например продуктов неполного сгорания азотно-водородной смеси с флюсом в виде буры, борного ангидрида и т. д. Для пайки углеродистых сталей в качестве припоя применяют также чистую медь, в особенности при пайке в печах в среде водорода. Медь хорошо растекается, заполняет малые зазоры. При этом прочность соединений превосходит прочность самой меди.
К высоколегированным сплавам относятся коррозионно-стойкие аустенитные стали 0Х18Н9, 12Х18Н9 со стабилизирующими добавками — титаном, ванадием, ниобием и т. д., кислотоупорные хромистые стали Х17, Х25 и другие ферритного класса, жароустойчивые никелевые сплавы, например, имеющие около 80% Ni и др.
Указанные сплавы могут паяться легкоплавкими припоями с применением активных флюсов. Однако пайка легкоплавкими припоями указанной группы сплавов технически нецелесообразна. Рациональнее применять для их соединений высокотемпературные припои (табл. 1).
В соответствии с маркой припоя применяются флюсы с различными составляющими. Некоторые припои при быстром нагреве т. в. ч. теряют свои составляющие.
Высоколегированные сплавы и стали можно паять в среде аргона, водорода, в вакуумных печах, Недостаток пайки в аргоне — не вполне удовлетворительная растекаемость припоя. Для улучшения растекаемости во флюсы вводят добавки, например литий. Пайка в атмосфере водорода требует высокой его чистоты; использование водорода всегда сопряжено с некоторой опасностью взрыва.
Пайка в вакууме дает хорошие результаты при применении припоев, не содержащих легко испаряющихся элементов (цинка и др.). При пайке указанных выше материалов могут возникать поры вследствие испарения некоторых составляющих припоя, например, цинка: непровары в результате неудовлетворительного смачивания расплавленным припоем соединяемых частей или недостаточной очистки поверхностей; трещины при проникновении жидкого припоя между границами зерен основного металла. Особенно часто образуются трещины при пайке медно-цинковыми и медно-серебряными припоями. Применением более высокотемпературных припоев можно избежать растрескивания паяных соединений.
Таблица 1. Состав припоев, %
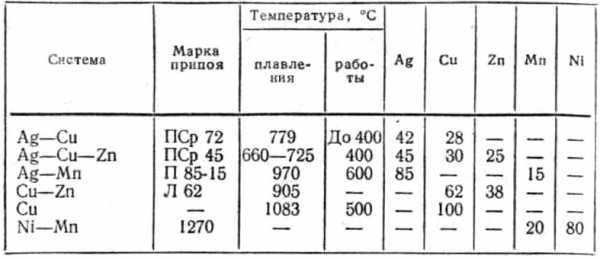
Применение никелевых припоев иногда сопровождается образованием подрезов основного металла в местах перехода к швам. Это происходит вследствие того, что припой этого рода имеет способность растворять основной металл. Чтобы избежать этого явления, следует вести технологический процесс пайки при возможно более низкой температуре.
При помощи пайки хорошо соединяются изделия из чистой меди и медных сплавов. Чистая медь хорошо паяется при нагреве в вакуумных печах, а также в атмосфере хорошо очищенного водорода без каких-либо примесей кислорода. Медно-цинковые сплавы, содержащие 4—38% Zn, при длительном нагреве теряют его (цинк испаряется), поэтому латунные детали перед пайкой целесообразно покрывать медью.
Пайка широко применяется для соединений различных бронз; алюминиевых, содержащих 5—10% Аl; бериллиевых, применяемых в приборостроении и имеющих в своем составе 2—2,5% Be; хромовых, содержащих около 0,5% Сr; оловянных, применяемых при обработке давлением, содержащих олово, а также фосфор и др.
Медь и ее сплавы легко паяются при применении низкотемпературных припоев с использованием канифольных флюсов, не вызывающих коррозии. Нередко перед пайкой поверхности деталей облуживают чистым оловом слоем толщиной 0,005 мм на стали и 0,0075 мм на меди. Низкотемпературные припои не обеспечивают высокой прочности паяных соединений, поэтому рекомендуется пайка в печах высокотемпературными твердыми припоями. Целесообразно применение медно-фосфорных и серебряных припоев и флюсов на основе буры с добавлением фтористых соединений. Алюминиевые бронзы хорошо паяются серебряными припоями с никелем, который препятствует проникновению в припой алюминия и повышает производительность технологического процесса.
Титан и его сплавы паяют в электрических печах, т. в. ч., газопламенным горелками. Наилучшие механические свойства спая достигаются при пайке ТВЧ. Это объясняется тем, что в результате сокращения термического цикла при этом способе пайки отсутствует рост зерна, приводящий к охрупчиванию соединений. При пайке титановых сплавов целесообразно применять серебряные припои, имеющие температуру плавления ниже температуры рекристаллизации титана и выше температуры, требуемой для удовлетворения условий смачивания припоем паяных деталей.
Очень важная задача производства — соединение пайкой различного рода керамических материалов и окислов друг с другом и с металлами. Возможны разные случаи: металлы более тугоплавки, нежели керамика, при этом соединение обеих деталей происходит в твердом состоянии, контакт обеспечивается необходимым давлением, применением покрытий. В последнем случае соединение достигается при температурах ниже температуры плавления каждой из соединяемых деталей.
Особенно благоприятные условия для соединения, когда металлы имеют температуру плавления ниже температуры плавления керамики и в результате своих специфических химических свойств склонны к образованию связи с последней. Гак, например, титан и цирконий имеют большое сродство к кислороду и образуют твердые растворы со многими металлами и окислами. Окислы титана и циркония весьма тугоплавки. При некоторых условиях эти металлы восстанавливают окислы металлов, образующих керамику, и присоединяют к себе освобожденный кислород. Такое восстановление, необходимое для прессовой пайки, следует проводить в условиях вакуума или в среде аргона.
Серьезные затруднение пайки керамик с металлами — существенная разница в их температурных коэффициентах расширения, в результате чего в соединениях образуются остаточные напряжения значительной величины. В неблагоприятных случаях, при недостаточной пластичности материалов в них возникают трещины. Для устранения этого явления иногда между соединяемым металлом и керамикой прокладывают пластины из пластичного металла, например молибдена. При пластических деформациях последнего опасность возникновения трещин в керамике значительно уменьшается.
С помощью специальных присадочных металлов можно получать качественные соединения не только однородных элементов, например Al2O3 + Al2O3, но и разнородных. Сплавы, содержащие сильные карбидообразующие элементы — молибден, тантал, титан, цирконий и др., – хорошо смачивают графит.
Также по теме:
Концентрация напряжений. Напряжения и деформации при пайке.
Прочность паяных соединений. Свойства соединений пайкой.
svarder.ru
Сплав Роза Вуда:что это такое,применение,состав,температура плавления
Во время пайки периодически возникают сложные ситуации, когда нужно приблизиться к максимальному проявлению одного из параметров. При работе с тонкими деталями, к примеру, во время ремонта мобильных телефонов и других микросхем, не требуется высокая прочность, а нужна как можно более низкая температура плавления. Естественно, что прочность была бы не лишней, но подобные соединения создаются при помощи твердоплавких металлов и их сплавов, так что их затруднительно применять в такой сфере. Припой сплав Вуда создан как раз для таких целей, чтобы при низкой температуре плавления иметь высокую плотность. Это не единственная область, в которой применяется данный материал.
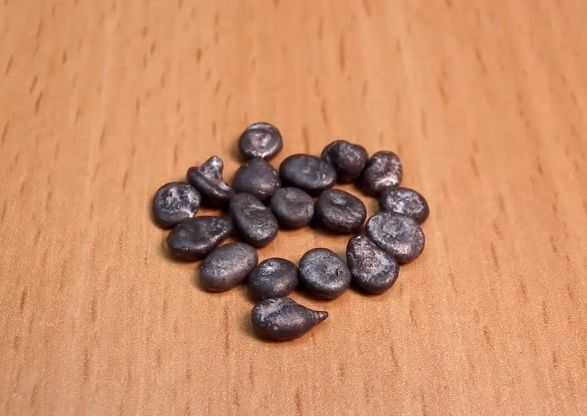
Внешний вид сплава Вуда
Его можно еще встретить в прецизионном литье и при ремонте труб из тонких листов металла. Из него изготавливаются стержни для последующего выплавления различных форм. С его помощью производятся различные тела методом гальванопластики. Помимо этого, он часто используется в лабораториях химической направленности. В технической сфере сплав Вуда применяется для лужения дорожек, которые служат для проведения тока в печатных платах.
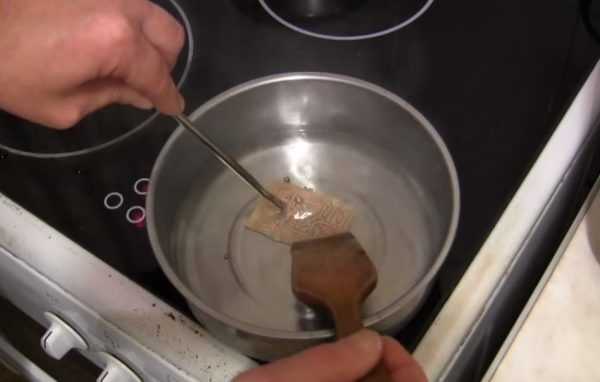
Лужение микросхема сплавом Вуда
Для обыкновенной пайки, где нужна прочность, температурная стойкость и другие механические параметры, его лучше не применять, но для своей сферы он стал уникальным изделием, которое прочно занимает свою нишу. Сплав Вуда производится по ТУ 6 09 4064 87.
Поставляется Сплав Вуда в виде специальных гранул. Это может быть упаковка, в которой содержится 100 грамм, или другой вес, вещества. Такой вариант обусловлен удобством применения. Гранулы имеют серо-черный цвет. При прикосновении паяльника достаточно легко плавятся и прилипают к жалу. Они легки в хранении и не требуют особых условий транспортировки.
Преимущества сплава Вуда
- Одна из самых низких температур плавления, которая ниже ста градусов Цельсия, что позволяет применять для чувствительных к температуре деталей, а также использовать при этом инструменты малой мощности;
- Доступный сплав, который имеет широкое распространение;
- Является незаменимым для многих сфер;
- Обладает высокой плотностью.
Недостатки
- Не может выдерживать высокие температурные нагрузки, благодаря чему сфера его применения ограничивается даже в бытовых условиях;
- Во время эксплуатации оказывается очень чувствительным к механическим нагрузкам, так что даже от небольших ударов может треснуть.
Состав сплава Вуда
Уникальность данного материала состоит в его составе. Здесь нужно не только точное наличие тех или иных элементов, но и соотношение их содержания. Точный и наиболее эффективный состав сплава Вуда выглядит следующим образом:
Химический элемент | Соотношение в составе, % |
Висмут | 50 |
Свинец | 20 |
Кадмий | 12,5 |
Олово | 12,5 |
Технические характеристики сплава Вуда
Главным свойством материала является его легкоплавкость практически при любых условиях, а также достаточно хорошая пластичность. Он может взаимодействовать практически с любыми металлическими поверхностями. Наплавленный металл имеет достаточно высокую плотность, если сравнивать относительно других припоев с низкой температурой плавления. Точные характеристики материала выглядят следующим образом:
Параметр | Единицы измерения | Значение |
Температура плавления | Градусы Цельсия | 72 |
Плотность | кг/м2 | 9720 |
Особенности пайки
«Важно!
Температура плавления припоя является очень низкой, что ведет за собой много других особенностей.»
Сплав Вуда применяется в узкой технической области и при химических операциях. Но чаще всего используют в качестве припоя. Низкая температура предполагает, что нужно использовать слабые паяльники, чтобы не случилось никакого перегрева и состав сохранял вязкость в расплавленном состоянии, так как именно это состояние является лучшим для спаивания.
При работе с мелкими деталями следует использовать тонкое плоское жало инструмента, чтобы не применять слишком большое количество расходного материала. Используя много припоя не обязательно получится хорошее соединение, так как тут больше важна точность. В ином случае может оказаться, что место спайки расплылось, а лишние капли попали на те части схемы, где они не должны быть. Затем нужно будет искать способ как убрать припой с платы. Таким образом, лучше сразу брать минимальные порции.
Несмотря на низкую температуру плавления, сплав Вуда желательно использовать с флюсами, которые подходят для всех легкоплавких материалов. Это сделает качество соединения лучше и уберет даже минимальный риск возникновения проблем при спаивании. Но иногда и сам материал используется для лужения, когда проводится работа с высокотемпературными припоями. Благодаря ему, улучшается схватывание других материалов, а мощный паяльник быстро превратит сплав в жидкое состояние.
Движения должны быть максимально четкими и быстрыми, так как во время использования материал начинает быстро застывать. После нанесения на поверхность, не стоит подвергать жестким проверкам, так как имеется высокий риск повредить застывший припой, даже если соединение сделано качественно. Сплав Вуда оказывается достаточно хрупок, так что вполне достаточно проводить визуальный контроль качества и не подвергать наплавленный металл большим опасностям.
Производители
На рынке преобладают отечественные производители данного материала:
- Уральский завод химических реактивов;
- ЧДА;
- ТинКом.
svarkaipayka.ru
Припой для пайки алюминиевых сплавов и способ его получения
Изобретение относится к области металлургии и может быть использовано при получении припоя для соединения термоупрочняемых алюминиевых сплавов. Припой для пайки алюминиевых сплавов содержит, мас.%: кремний 4-12, германий 4,6-25, стронций 0,003-0,01, церий 0,05-0,15, алюминий – остальное. Припой может дополнительно содержать 0,3-1,0 мас.% магния. Способ получения припоя включает получение слитка, диффузионный отжиг при температуре на 5-10°С выше температуры солидуса в течение 5-24 часов и последующую прокатку. Изобретение обеспечивает повышение прочности паяных конструкций при использовании припоя с пониженной температурой плавления. 2 н. и 2 з.п. ф-лы.
Предполагаемое изобретение относится к области металлургии и может быть использовано при получении припоя для пайки термоупрочняемых алюминиевых сплавов.
В настоящее время известен припой состава (в мас.%): германий 14…52, по крайней мере один элемент из группы: кремний, магний, висмут, стронций, литий, медь кальций, цинк и олово 0…10, алюминий – остальное, а также способ его изготовления методом высокоскоростного охлаждения при литье (патент США №5286314, C21D 1/00, 1994 г.).
Недостатками известного припоя и способа его изготовления является малая номенклатура паяных соединений из-за малой толщины получаемой ленты (толщина 25…85 мкм).
Известен также припой, состоящий из (в мас.%): кремний 8…10; германий 3,5…4,5; магний 0,5…0,8; марганец 0,3…0,5; стронций 0,05…0,1; алюминий – остальное (А.с. СССР №476951, В23К 35/28, С22С 21/02, 1975 г.), прототип.
Недостатком данного припоя является высокая температура плавления, исключающая возможность его использования для соединения высокопрочных алюминиевых сплавов, малая номенклатура паяных соединений, низкий срок службы изделий.
Известен способ получения припоя, включающий отливку слитка с последующей его прокаткой (А.с. СССР №671962, В23К 35/28, С22С 21/10, 1979 г.), прототип.
Недостатком данного способа является получение припоя с высокой температурой плавления, что не позволяет использовать его для соединения высокопрочных алюминиевых сплавов, и, как следствие, низкий срок службы получаемых изделий.
Предлагается припой для пайки алюминиевых сплавов, состоящий из алюминия, кремния, германия, стронция и церия при следующем соотношении компонентов (в мас.%): кремний 4…12; германий 4,6…25; стронций 0,003…0,01; церий 0,05…0,15; алюминий – остальное.
Припой дополнительно содержит магний в количестве 0,3…1 мас.%.
Предлагается способ получения припоя для пайки алюминиевых сплавов, включающий отливку слитка, его диффузионный отжиг при температуре на 5…10°С выше температуры солидус припоя в течение 5…24 часов и последующую прокатку.
После горячей прокатки дополнительно проводят холодную на окончательную толщину листа до 0,1 мм.
Предлагаемый состав припоя отличается от прототипа тем, что он дополнительно содержит церий в количестве 0,05…0,15 мас.% и компоненты взяты в следующем соотношении (в мас.%): кремний 4…12; германий 4,6…25; стронций 0,003…0,01; церий 0,05…0,15; алюминий – остальное.
Припой дополнительно содержит магний в количестве 0,3…1 мас.%.
Предлагаемый способ получения припоя отличается от прототипа тем, что слиток перед прокаткой подвергают диффузионному отжигу при температуре на 5…10°С выше температуры солидуса в течение 5…24 часов.
После горячей прокатки дополнительно проводят холодную на окончательную толщину листа до 0,1 мм.
Задачей изобретения является повышение эксплуатационных характеристик и увеличение номенклатуры паяных соединений из алюминиевых сплавов, а также увеличение срока службы получаемых конструкционных материалов.
Технический результат – понижение температуры плавления припоя и повышение прочности паяных конструкций.
Предлагаемый припой и способ его изготовления позволяют провести растворение неравновесных фаз и получить сплав равновесного фазового состава с измельченной структурой, что повышает прочность соединений, снижает температуру плавления припоя, позволяет проводить пайку высокопрочных алюминиевых сплавов с низкой температурой солидус, и, как следствие, увеличивать прочность изделий и срок их эксплуатации.
Пример.
Было получено 3 слитка припоя, содержащего (в мас.%): кремний 9, германий 12, церий 0,1, стронций 0,005, алюминий – остальное. Отливка сплавов осуществлялась путем расплавления сплава Al-12Si и растворением в нем технического германия, стронция и церия, которые вводились в расплав в виде лигатур. Отливку слитков припоя осуществляли при температуре 700°С. Температура солидуса – 451°С. Диффузионный отжиг полученных слитков проводили в течение 24 часов при температуре 460°С, что соответствует 9°С выше температуры солидус. После этого слитки припоя подвергали горячей прокатке, получая припой в виде листов, толщиной 0,8 мм. Один из прокатанных листов также подвергали холодной прокатке до толщины 0,1 мм.
Для пайки изделия из сплава АВч использовался припой в виде тонкой фольги, толщиной 0,1 мм. Пайка проводилась в печи в воздушной атмосфере с использованием флюса 34А. Прочность полученного паяного образца на разрыв составляла 180 МПа, разрушение происходило по основному материалу.
Для печной пайки изделия из сплава АД31 в вакууме использовали припой толщиной 0,8 мм. Пайка проводилась в печи со степенью разрежения 10-2…10-3 Па в присутствии паров магния. Прочность полученных образцов составляла 176 МПа, разрушение происходило по основному материалу.
Проводились испытания припоя-прототипа. Пайка изделия из сплава АВч проводилась в печи в воздушной атмосфере с использованием флюса 34А. Прочность полученных соединений составляла 80 МПа.
Таким образом, предлагаемое изобретение позволяет повысить прочность паяного соединения в 2…2,5 раза и, как следствие, повысить срок службы изделия в 2…2,5 раза.
1. Припой для пайки алюминиевых сплавов, содержащий алюминий, кремний, германий, стронций, отличающийся тем, что он дополнительно содержит церий при следующем содержании компонентов, мас.%:
Кремний | 4-12 |
Германий | 4,6-25 |
Стронций | 0,003-0,01 |
Церий | 0,05-0,15 |
Алюминий | Остальное |
2. Припой по п.1, отличающийся тем, что он дополнительно содержит 0,3…1 мас.% Mg.
3. Способ получения припоев для пайки алюминиевых сплавов, включающий отливку слитка и его прокатку, отличающийся тем, что перед прокаткой слиток припоя по п.1 или 2 подвергают диффузионному отжигу при температуре на 5-10°С выше температуры солидуса в течение 5-24 ч.
4. Способ по п.3, отличающийся тем, что осуществляют горячую прокатку слитка, после которой проводят холодную прокатку на толщину 0,1 мм.
findpatent.ru
Сплав для пайки на основе циркония
Изобретение может быть использовано для пайки элементов тепловыделяющих сборок ядерных реакторов, преимущественно, при изготовлении дистанционирующих решеток, сформированных из трубных заготовок. Сплав содержит компоненты в следующем соотношении, мас.%: железо 4,0-6,0, бериллий более 3,0-4,0, ниобий 0,9-1,1, медь 4,0-8,0, олово 1,0-3,0, хром 0,2-1,0, висмут + мышьяк 0,0001-0,0018, сера 0,0001-0,0015, цирконий и неизбежные примеси остальное. Дополнительно сплав может содержать германий в количестве 0,25-2,5 мас.%. Сплав обеспечивает повышение коррозионной стойкости при одновременном повышении сопротивления ползучести, а также уменьшение температуры плавления и снижение образования интерметаллидов железа в паяном шве. 1 з.п. ф-лы, 1 табл.
Область техники, к которой относится изобретение
Изобретение относится к металлургии сплавов, а именно к сплавам для пайки на основе циркония, и предназначено для использования во многих областях промышленности, в частности в ядерной энергетики для пайки циркония и его сплавов, особенно для пайки элементов тепловыделяющих сборок ядерных реакторов, преимущественно при изготовлении дистанционирующих решеток, которые формируются из ячеек, сформированных из трубных заготовок.
Уровень техники
Из множества различных методов получения неразъемных соединений в машиностроении, в частности в реакторостроении, большое значение придается технологическому процессу пайки. Возможность получения соединений в скрытых и малодоступных местах конструкций; изготовление тонкостенных изделий с большой плотностью расположения паяных соединений; необходимость соединить разнородные материалы и детали с большой разницей толщин; зависимость температуры процесса от влияния температуры нагрева на свойства конструкционного материала; возможность совмещения термообработки с термическим циклом пайки и пр. определяют преимущество пайки перед другими методами соединения, в частности перед сваркой. В связи со значительным увеличением количества новых материалов, усложнением конструкции изделий, высокими требованиями к надежности и прочности соединений материалов конструкций ставится задача расширения теоретических и технологических исследований в области номенклатуры припоев, методов их получения, способов пайки, режимов термической обработки паяемых материалов, разработки оснастки и др.
Пайка имеет ряд значительных преимуществ перед сваркой благодаря:
– возможности соединять детали без расплавления основного металла, без нарушения геометрических размеров изделия, в любых сочетаниях металлов;
– формированию соединения практически одновременно по всем поверхностям контакта, а не последовательно, как при сварке;
– получению (формированию) качественного физического шва при соединении деталей в различных пространственных положениях;
– возможности совмещения операций пайки и термической обработки при использовании одного и того же нагревательного оборудования.
Известен сплав для пайки на основе циркония, содержащий (80-90)% циркония, (5,5-15)% железа, 1,5% германия, (1-3)% хрома и 2,5% бериллия (Понимаш И.Д., Орлов А.В., Рыбкин Б.В. Вакуумная пайка реакторных материалов, М., Энергоатомиздат, 1995, с.115-125). По результатам длительных коррозионных (гидродинамических) испытаний и механическим свойствам сплав показал хорошую пригодность для пайки дистанционирующих решеток тепловыделяющих сборок. Пайку ячеек данным припоем проводили следующим образом. Сборку ячеек с вертикальными зазорами устанавливали в печи на припой, где далее ее нагревали до температуры пайки. При пайке припой затекал в зазоры под действием капиллярных сил. Припой полностью заполнял зазоры с образованием галтелей. Время выдержки при температуре пайке, равной температуре затекания, составляло 1 минуту. Однако данный припой имеет высокую температуру плавления (930-1020)°С и, соответственно, температуру пайки (960-1030)°С.
Наиболее близким по технической сущности и достигаемому результату к настоящему изобретению является сплав для пайки на основе циркония, содержащий железо, бериллий, ниобий, медь, олово и хром (Плющеев А.Н., Калин Б.А., Федотов В.Т. и др.. Разработка аморфного ленточного припоя для пайки дистанционирующих решеток, “Сб. докладов VI Российской конференции по реакторному материаловедению” (Димитровград, 11-15 сентября 2000 г.) т.3.42, г.Димитровград, НИИАР, 2001, с.254-267). Известный припой содержит 5,5% железа, 2,5% бериллия, 1% ниобия, 8% меди, 2% олова и 0,4% хрома. Высокое содержание меди позволяет наиболее сильно понизить температуру плавления сплава. Для нейтрализации вредного влияния меди сплав легирован оловом и хромом, ниобий вводиться в количестве 1% для того, чтобы не обеднять циркониевый сплав Э110 по ниобию. Проведенные в течение 1000 часов коррозионные испытания паяных ячеек в дистиллированной пароводяной смеси при температуре 350°С и давлении 16,5 МПа показали достаточно высокую стойкость паяных соединений. Однако испытания более чем 1000 часов выявили некоторое снижение коррозионной стойкости при одновременном снижении сопротивления ползучести. Кроме того, известный сплав обладает относительно высокой температурой плавления ~800°С, в то время как для пайки циркония и его сплавов предпочтительно иметь температуру плавления ниже, поскольку температура ~800°С является критической в том плане, что при пайке при этой температуре в основном металле происходит изменение структуры за счет фазовых переходов, что резко ухудшает коррозионные свойства основного металла и его пластичность.
Сущность изобретения
Задачей настоящего изобретения является разработка и создание сплава для пайки на основе циркония, обладающего улучшенными эксплуатационными характеристиками.
В результате решения данной задачи возможно получение технических результатов, заключающихся в том, что повышается коррозионная стойкость при одновременном повышении сопротивления ползучести, а также уменьшается температура плавления сплава и снижается образование интерметаллидов железа в паяном шве и улучшается структура паяного шва.
Данные технические результаты достигаются тем, что сплав для пайки на основе циркония, содержащий железо, бериллий, ниобий, медь, олово и хром, дополнительно содержит висмут, мышьяк и серу при следующем соотношении компонентов, мас.%:
Железо 4,0-6,0
Бериллий Более 3,0-4,0
Ниобий 0,9-1,1
Медь 4,0-8,0
Олово 1,0-3,0
Хром 0,2-1,0
Висмут + мышьяк 0,0001-0,0018
Сера 0,0001-0,0015
Цирконий остальное
Отличительная особенность настоящего изобретения заключается в том, что сплав дополнительно содержит висмут, мышьяк и серу, а также выбраны новые диапазоны содержания отдельных компонентов. В частности, изменено содержание бериллия в сторону увеличения, среднее содержание меди уменьшено. Действительно, как известно, с одной стороны, увеличение содержания меди приводит к уменьшению температуры плавления, но совершенно незначительно. Так с увеличением содержания меди от 8% до 12% температура солидуса сплава понижается всего на 5 градусов; с дальнейшим увеличением концентрации меди, несмотря на снижение температуры солидуса, начинает возрастать температура ликвидуса сплава и, соответственно, увеличивается температурный интервал плавления. Именно поэтому для одновременной реализации вышеуказанных технических результатов предложено повысить содержание бериллия с одновременным введением новых присадок. Конкретные диапазоны содержания компонентов сплава по настоящему изобретению были определены экспериментально. Уменьшение содержания железа менее 4,0% и бериллия менее 3,0% приводит к увеличению температуры плавления сплава. Увеличение содержания железа выше 6,0% приводит к исчезновению в структуре сплава активной альфа-цирокониевой фазы, снижению капиллярных свойств припоя и ухудшению качества пайки. Содержание бериллия более 4,0% незначительно уменьшает температуру сплава, но при этом повышается действие его токсичности, а также образуется большое количество хрупких интерметаллидов. Снижение содержания меди менее 4,0% также увеличивает температуру плавления сплава, а содержание меди более 6,0% ухудшает качество паяного соединения и снижает его коррозионную стойкость. Температура плавления сплава в соответствии с настоящим изобретением составляет ~750-760°С. При суммарном содержании висмута и мышьяка менее 0,0001% и серы менее 0,0001% их влияние на коррозионную стойкость и сопротивление ползучести практически отсутствует. При суммарном содержании висмута и мышьяка более 0,0018% и серы более 0,0015% значительно ухудшается структура описываемого сплава. Ниобий введен для того, чтобы не обеднять основной сплав (как известно, в ядерном реакторостроении используются сплавы с содержанием ниобия 0,9-1,1%). Хром и олово введены для уменьшения вредного действия меди и азота и улучшения качества паяного шва.
Кроме того, сплав в соответствии с настоящим изобретением дополнительно содержит германий в количестве 0,25-2,5 мас.%, что предотвращает образование интерметаллидов железа в паяном шве.
Сведения, подтверждающие возможность осуществления изобретения
Для приготовления сплава-припоя использовали следующие элементы:
– цирконий металлический иодидный, ТУ 95-46-76;
– ниобий Нб-1, ГОСТ 16099-70;
– железо: порошок железный ПЖ-0, ГОСТ 9849-74;
– бериллий горячепрессованный чистотой 99,98%;
– медь, ГОСТ 859-78.
Перед плавкой предварительно были изготовлены лигатуры Zr-5 мас.% Be и Zr-50 мас.% Nb. Выплавку слитков проводили в дуговой печи МИФИ-9 шестикратным переплавом с использованием лигатур, чистого циркония и железа. Для предотвращения разбрызгивания или рассыпания при плавке навески при приготовлении заворачивались в ниобиевую фольгу толщиной 50 мкм, вес которой также входил в общий вес навески.
Полученные сплавы для пайки, составы которых приведены в Таблице, использовали для соединения ячеек дистанционирующих решеток, выполненных из циркониевого сплава.
Таблица | |||
КОМПОНЕНТ | СОСТАВ СПЛАВА | ||
1 | 2 | 3 | |
Железо | 4,0 | 4,9 | 6,0 |
Бериллий | 3,6 | 4,0 | 3,05 |
Ниобий | 1,0 | 1,1 | 0,9 |
Медь | 8,0 | 4,0 | 5,9 |
Олово | 2,1 | 3,0 | 1,0 |
Хром | 1,0 | 0,2 | 0,6 |
Висмут + мышьяк | 0,0018 | 0,0001 | 0,0009 |
Сера | 0,0001 | 0,0008 | 0,0015 |
Германий | 1,2 | 2,5 | 0,25 |
Цирконий и неизбежные примеси | остальное |
Главным критерием в оценке годности паяного соединения является характер разрушения, т.е. отрыв по металлу свидетельствует о годности паяного соединения. Как показали исследования, усилие до отрыва паяных образцов, полученных с использованием сплавов для пайки по настоящему изобретению, лежит в пределах 51-58 кГс, что более чем в два раза превышает усилие на отрыв сварных соединений. Разрушение всех образцов происходило по основному металлу.
Коррозионные испытания длительностью до 6500 часов проводили в автоклавах емкостью 1 дм3 в дистиллированной пароводяной смеси при температуре ~350°С и давлении ~16,5 МПа (168 кгс/см2). Состояние поверхности образцов контролировали визуально, принимая во внимание, что оксидная пленка черного цвета свидетельствует о хорошей коррозионной стойкости, а серые оттенки и цвета побежалости свидетельствуют о плохих коррозионных свойствах образцов.
Проведенные испытания показали, что паяные соединения, полученные с использованием сплавов для пайки и отожженные при температуре 580°С в течение 6 часов, после коррозионных испытаний имеют черную оксидную пленку, свидетельствующую о повышении коррозионной стойкости.
Из последних исследований: паяные решетки получаются более жесткие по сравнению со сварными – это упрощает сборку ТВС.. Показаны повышенные в (1,5-2 раза) механические свойства паяных ЦДР по сравнению со сварными, что создает определенные запасы для оптимизации конструкции ЦДР.
Кроме того, как показало сравнение микроструктур сварных и паяных решеток, после коррозионных испытаний материал зоны пайки слабо гидрируется, причем гидриды имеют тангенциальных характер выделений, в отличие от сварных, где наблюдаются радиальные выделения гидридов, а как известно, радиальные гидриды ухудшают механические свойства.
1. Сплав для пайки на основе циркония, содержащий железо, бериллий, ниобий, медь, олово и хром, отличающийся тем, что дополнительно содержит висмут, мышьяк и серу при следующем соотношении компонентов, мас.%:
Железо 4,0-6,0
Бериллий более 3,0-4,0
Ниобий 0,9-1,1
Медь 4,0-8,0
Олово 1,0-3,0
Хром 0,2-1,0
Висмут + мышьяк 0,0001-0,0018
Сера 0,0001-0,0015
Цирконий и неизбежные примеси остальное.
2. Сплав по п.1, отличающийся тем, что дополнительно содержит германий в количестве 0,25-2,5 мас.%.
findpatent.ru