Сплав не содержащий алюминий дюралюминий силумин магналий чугун: Самостоятельная работа “СПЛАВЫ”
alexxlab | 08.02.2023 | 0 | Разное
Сплавы металлов и их применение
Металл является одним из самых необходимых материалов
в промышленности, строительстве, сельском хозяйстве и
иных видах жизнедеятельности человека.
Несмотря на то, что сегодня все более популярным
материалом становится пластик, трубы из него могут
использоваться только в помещениях, а конструкции,
проходящие под землей, можно изготавливать только из
металла.
Чаще всего в промышленности и строительстве используются
не чистые металлы, а их сплавы.
Сплав — это материал, который образуется в
результате затвердения расплава двух или нескольких
металлов.
В состав сплавов кроме металлов могут входить также
неметаллы.
Добавляя в определённом количестве примеси других
металлов и неметаллов, можно получить многие тысячи
материалов с самыми разнообразными свойствами, в том
числе и такими, каких нет ни у одного из составляющих
сплав элементов.
Сплав по сравнению с исходным металлом может быть:
механически прочнее и твёрже,
со значительно более высокой или низкой
температурой плавления,
устойчивее к коррозии,
устойчивее к высоким температурам,
практически не менять своих размеров при
нагревании или охлаждении и т. д.
Сталь является самым востребованным сплавом. Подобный
вывод можно сделать, проанализировав ежегодные объемы
её производства. В большинстве случаев, сталь представляет
собой сплав железа с углеродом, количество которого
достигает двух процентов.
Сплавы стали подразделяются на несколько видов:
малоуглеродистые, уровень углерода в которых не
превышает 0,25%, высокоуглеродистые с содержанием
углерода свыше 0,55% и легированные, дополненные
другими металлами.
Добавленный в сталь хром делает её нержавеющей,
вольфрам делает сталь намного более твёрдой, добавка
марганца делает сплав износостойким, а ванадия —
прочным.
Для того чтобы значение стали в жизни человека стало для
вас более явным, попробуйте вспомнить все металлические
предметы, которые вы использовали за день, — ножи,
кастрюли, бритвы и другое – все они изготовлены из стали.
На втором месте по объему производства находится чугун,
который также представляет собой сплав железа и углерода.
Только в отличие от стали, количество последнего в чугуне
несколько больше. Для придания сплаву прочности в чугун
добавляется кремний.
Особенно широкое распространение чугун получил в
строительстве:
он
используется
для
изготовления
трубопроводной арматуры, крышек люков и других
элементов, основным требованием которых является
прочность. Кроме этого, из чугуна производится и некоторая
посуда: у каждой хозяйки на кухне была или есть сковорода
из чугуна.
Хотя сплавы из алюминия не так распространены, как
материалы, названные выше, некоторые их достоинства
делают их незаменимыми. Прежде всего, сплавы из
алюминия отличает экономичность, легкость в обработке.
Они без труда поддаются ковке, сварке, штампованию, а
также хорошо поддаются обработке на металлорежущих
станках.
Использование алюминиевых сплавов ограничено лишь тем,
что при высоких температурах они теряют ряд своих свойств.
Так, температура 200°С уже является для них высокой,
между тем, как термоустойчивость – это очень важное
свойство металла.
К достоинствам алюминиевых сплавов относится их
безвредность и экологичность, благодаря чему их можно
использовать даже для хранения и перевозки пищевых
продуктов, стойкость к появлению коррозии, высокая
отражательная способность, а также немагнитность.
Наиболее часто алюминиевые сплавы применяются в
пищевой промышленности и машиностроении. Кроме этого,
они необходимы для создания высоковольтных линий и
изготовления
некоторых
архитектурно-отделочных
материалов.
Такие сплавы алюминия как дюралюминий, силумин
незаменимы в самолёто-, вагоно- и кораблестроении.
В приборостроении, при изготовлении строительных
конструкций применяется магналий (сплав алюминия с
9,5—11,5% магния).
Пять тысяч лет тому назад наши предки научились делать
бронзу — сплав олова с медью. Бронза по твёрдости
превосходит оба металла, входящие в её состав.
Сейчас бронзу получают сплавляя медь с другими
металлами.
Алюминиевые бронзы (5—11% А1) обладают высокой
коррозионной стойкостью и золотистым блеском. Они идут
на изготовление лент, пружин, шестерен и художественных
изделий.
Кремнистые бронзы (4—5% Si) обладают высокими
механическими и антикоррозионными свойствами. Они
применяются в химической промышленности для
изготовления сеток, проводов, трубопроводов.
Бериллиевые бронзы (1,8—2,3% Be) способны при быстром
охлаждении с 800° принимать закалку и становятся
твердыми и упругими, как сталь. Их применяют главным
образом при изготовлении часовых механизмов и в точной
механике.
Большинство бронз имеет сложный состав и являются трехили четырех компонентными сплавами.
Сплавы меди, содержащие до 10% цинка, называются
томпаком; при большем содержании цинка (10—40%) —
латунью. Томпак и латунь хорошо прокатываются и
обрабатываются штамповкой и прессованием. Они
применяются для изготовления листов, труб, патронных
гильз и различной арматуры (краны, вентили и др.).
Томпак пластичен, не ржавеет и обладает низкой силой
трения. Томпак хорошо сваривается со сталью и имеет
золотистый оттенок. Литейная латунь предназначена для
создания изделий путём литья. Такой сплав не подвержен
ржавчине, не подвержен деформации.
Добавление в латунь олова резко улучшает ее коррозионную
стойкость («морская» латунь). Сплавы меди с никелем
(иногда с добавлением цинка) обладают значительным
сопротивлением. Некоторые из них, например мельхиор,
применяются для изготовления предметов домашнего
обихода.
Латунь является одним из самых наиболее используемых в
мире сплавов, его даже называют вечным металлом, так как
он практически не подвергается износу.
Сплавы служат незаменимым материалом при изготовлении
особо чувствительных и высокоточных приборов, различного
рода датчиков и преобразователей энергии. Например, на
изготовление сердечников трансформаторов и деталей реле
идёт сплав никеля. Отдельные детали электромоторов
изготавливаются из сплавов кобальта.
Сплав никеля с хромом — нихром, отличающийся высоким
сопротивлением — используется для изготовления
нагревательных
элементов
печей
и
бытовых
электроприборов. Пластинки из сверхтвёрдого победита
(сплав вольфрама и кобальта) применяются для
изготовления металлорежущего и бурового инструмента.
В некоторых узлах самолётов используются сплавы магния,
очень лёгкие и жароустойчивые. В ракетостроении
применяют лёгкие и термостойкие сплавы на основе титана,
а для производства зеркал и в стоматологии – амальгама
( сплав ртути).
Главным востребованным свойством легкоплавких сплавов
является заданная низкая температура плавления. Это
свойство, в частности, используется для пайки микросхем.
Кроме того, эти сплавы должны иметь определённую
плотность,
прочность
на
разрыв,
химическую
инертность, теплопроводность.
Легкоплавкие сплавы производят из висмута, свинца,
кадмия, олова и других металлов. Такие сплавы используют
в термодатчиках, термометрах, пожарной сигнализации,
например, сплав Вуда.
Сплав натрия с калием (температура плавления –12,5 °С)
используется как теплоноситель для охлаждения ядерных
реакторов.
Применение в чистом виде драгоценных металлов в
ювелирном деле не всегда оправдано и целесообразно из-за
их дороговизны, физических и химических особенностей.
Для придания ювелирным изделиям из золота большей
твёрдости и износостойкости используются сплавы с другими
металлами.
Самая лучшая добавка — это серебро (понижает
температуру плавления) и медь (повышает твёрдость). Из
сплавов золота с 10–30 % других благородных металлов
(платины
или
палладия)
изготавливают
форсунки
лабораторных приборов, а из сплава с 25–30 % серебра —
ювелирные изделия и электрические контакты.
Таким образом, производство металлов и сплавов является
ключевой особенностью современной промышленности. С
каждым годом люди изобретают все больше способов
получения новых материалов, так что вскоре мы наверняка
получим совершенно невероятные соединения, которые
будут сочетать в себе полезные свойства сразу нескольких
групп материалов и химических элементов.
Домашнее задание: параграф 42 (читать)
Металлургическая промышленность. Производство чугуна, стали и алюминия.
Тема урока: Металлургическая промышленность. Производство чугуна, стали и алюминия.
Цель урока: Сформировать понятие о металлургии; изучить основные промышленные способы получения чугуна, стали и алюминия .
Задачи урока:
1.Образовательная: систематизировать знания учащихся о природных соединениях железа и алюминия как основе черной и цветной металлургии ; о научных принципах производства чугуна, стали и алюминия .
2.Развивающая: продолжить формирование навыков самостоятельной работы учащихся с учебником, научно-популярной литературой; развивать познавательную активность учащихся, способствовать выработке навыков наблюдения, умения делать выводы.
3.Воспитательная: содействовать экологическому образованию и воспитанию учащихся; продолжить формирование знаний о целесообразном и экономически обоснованном подходе в химическом производстве веществ и материалов;
Тип урока: урок формирования знаний.
Методы и средства обучения: информационно-коммуникативный; частично-поисковый; эвристическая беседа; современные электронные средства обучения
Оборудование: компьютер, интерактивная доска .
Ход урока:
1.Мобилизирующий момент.
2.Проверка ЗУН:
-Какие способы получения металлов используются в промышленности? Приведите примеры.
-Что такое химическая технология?
-Что является целью химической технологии?
-Что такое промышленная химия?
-Почему технологический процесс, отработанный в химических лабораториях, часто не идёт в заводских условиях?
-Перечислите и объясните общие технологические принципы, применяемые в современных химических производствах.
3.Объяснение материала:
Первые сведения использования металлов в хозяйственной деятельности людей относятся к 4-3 тыс. до н.э. Это время называют медным веком или энеолитом (от лат. аeneus – медный и греч. lithos – камень)
Основное занятие населения – мотыжное земледелие, скотоводство и охота. В это время помимо каменных орудий появляются медные орудия.
Скажите, а в чем преимущество медных орудий труда перед каменными? Это легкая обрабатываемость и легкость в обращении.
Историки считают медный век переходным периодом от каменного к бронзовому веку ( конец 4 начало 3 тыс. до н.э.)
В чем причина того, что постепенно бронза заменила чистую медь и именно из этого сплава начали изготавливать орудия труда и оружие? Медь – металл мягкий и легко деформируется, а бронза более прочная и твердая.
Но со временем и бронза отошла на второй план. Сейчас бронзу используют для производства пружин, шестерней, часовых механизмов, художественных изделий. Бронза – это один из основных материалов скульпторов. Знаменитые Царь-пушка и Царь-колокол также отлиты из сплава меди с оловом.
А вот когда человек научился получать температуру более 1500 С наступила эпоха изделий из железа и его сплавов – чугуна и стали. Это время стали называть железным веком, начало которого датируют с середины 1 тыс. до н.э.
А когда закончился железный век?
Наверное, условно можно сказать, что железный век продолжается и по сей день. Ведь примерно 9/10 из всех используемых металлов и сплавов – это сплавы на основе железа. Ни одна сторона человеческой жизни не обходится на сегодняшний день без использования металлов и сплавов из них.
Учитывая большую значимость металлов, мы должны знать, как же их получают. Поэтому главная цель нашего урока изучить основные промышленные способы получения чугуна, стали и алюминия .(Записываем тему урока)
Что же такое металлургия?
Металлургия ( от греч. metallurgio – обрабатывать металлы) – это область науки, техники и отрасль промышленности, охватывающие все процессы получения металлов, сплавов и прокатных профилей из них.
Металлургия
Чёрная цветная
получение железа и сплавов получение 70 металлов с более ценными
на его основе свойствами
На долю чёрных металлов(железо, марганец, хром) приходится около 90% всей производимой в мире металлопродукции. Среди цветных металлов первое место по размерам производства занимает алюминий.
Я хочу рассказать историю открытия алюминия. Однажды к римскому императору Тиберию пришел незнакомец. В дар императору он преподнес изготовленную им чашу из блестящего, как серебро, но чрезвычайно легкого металла. Мастер поведал, что этот никому не известный металл он сумел получить из глинистой земли. Должно быть, чувство благодарности редко обременяло Тиберия, да и правителем он был недальновидным. Боясь, что новый металл с его прекрасными свойствами обесценит хранившееся в казне золото и серебро, он отрубил изобретателю голову, а его мастерскую разрушил, чтобы никому не повадно было заниматься производством «опасного металла». Спустя полторы тысячи лет в историю алюминия была вписана новая страница. Это сделал талантливый немецкий врач и естествоиспытатель Парацельс Филипп.
В 1825 г. ученый из Дании К.Х. Эрстед (1777 – 1854) стал исследовать глинозем (соединение алюминия с кислородом). Он нагревал смесь глинозема и угля с хлором. Полученный хлорид алюминия он восстанавливал амальгамой калия. В результате получил металл, похожий на олово, но он не провел опыты, подтверждающие чистоту металла.
В 1827 г. эксперименты Эрстеда повторил Ф. Вёлер. Вместо амальгамы он использовал чистый калий. В результате эксперимента он получил 30 г порошкообразного алюминия и исследовал его свойства.
Начались поиски способов его получения. В то время французская администрация императора Наполеона III готовилась к войне против России. Император мечтал из нового открытого металла вооружить своих солдат. Вскоре он дал поручение известному французскому ученому Сен-Клер Девилю найти промышленные способы алюминия. Каким бы могущественным ни был император, его мечта сразу не воплотилась. По поручению императора Наполеона известный французский ученый Сен-Клер Девиль построил первый алюминиевый завод. В основу производства была взята реакция между хлоридом алюминия и металлом натрия. Этот химический метод не дал хорошего выхода алюминия и в течение пяти лет работы было произведено всего 1680 кг алюминия. Полученный таким способом алюминий был равноценен золоту.
В то время не было возможности наладить производство этого металла в большом количестве. Из первого алюминия, полученного на заводе, для императора были изготовлены пуговицы. Оставшийся алюминий был отправлен на выставку.
Современный способ получения алюминия (после чего наладили массовое производство) изобретён американцем И.Холлом и французом П.Эру в 1886 г. Он заключается в электролизе раствора оксида алюминия в растворе криолита.
Технология получения алюминия из руд состоит из 4 производств, связанных между собой технологической цепочкой и производимыми продуктами. Она включает:
1.производство глинозёма
2.производство фтористых солей и криолита
3.производство угольных изделий(электродов и блоков футеровки)
4.производство электролитического алюминия
Производство алюминия
Основным сырьем для производства алюминия служат бокситы, содержащие 32-60% глинозема Al2O3. К важнейшим алюминиевым рудам относятся также алунит и нефелин.
Алюминий получают из оксида алюминия Al2O3 электролитическим методом. Используемый для этого оксид алюминия должен быть достаточно чистым, поскольку из выплавленного алюминия примеси удаляются с большим трудом. Очищенный Al2O3 получают переработкой природного боксита.
Основное исходное вещество для производства алюминия — оксид алюминия. Он не проводит электрический ток и имеет очень высокую температуру плавления(около 2050 oC), поэтому требуется слишком много энергии.
Необходимо снизить температуру плавления оксида алюминия хотя бы до 1000 oC. Такой способ параллельно нашли француз П. Эру и американец Ч. Холл. Они обнаружили, что глинозем хорошо растворяется в расплавленном криолите — минерале состава AlF3.3NaF. Этот расплав и подвергают электролизу при температуре всего около950 oC на алюминиевых производствах. Запасы криолита в природе незначительны, поэтому был создан синтетический криолит, что существенно удешевило производство алюминия.
Гидролизу подвергают расплавленную смесь криолита Na3 [AlF6 ] и оксида алюминия. Смесь, содержащая около 10 весовых процентов Al2O3,плавится при 960 oC и обладает электропроводностью, плотностью и вязкостью, наиболее благоприятствующими проведению процесса. Для дополнительного улучшения этих характеристик в состав смеси вводят добавки AlF3,CaF2 и MgF2. Благодаря этому проведение электролиза оказывается возможным при 950 oC.
Электролизёр -стальная ванна прямоугольной формы внутри выложена огнеупорным кирпичом и блоками из угольной массы. В нижние блоки закругляются расплавленный алюминий – это катод. Над слоем жидкого алюминия находится расплавленный электролит, в который сверху опущен угольный анод, он постепенно сгорает, его наращивают, загружая в алюминиевый кожух анода углеродистую массу . Сверху и со стороны боковых стенок электролит вследствие охлаждения воздухом – застывает, образуя сплошную корку.
При электролизе на катоде выделяется алюминий, а на аноде — кислород. Алюминий, обладающий большей плотностью, чем исходный расплав, собирается на дне электролизера, откуда его периодически выпускают. По мере выделения металла, в расплав добавляют новые порции оксида алюминия. Выделяющийся при электролизе кислород взаимодействует с углеродом анода, который выгорает, образуя CO и CO2
Электролизёр работает непрерывно, но Al2O3 загружают в ванну порциями через 2 суток. Накопившийся алюминий сливают в ковш, из которого предварительно откачивают воздух. Жидкий алюминий по трубе засасывают в ковш, а затем из него разливают по формам.
Казахстан богат алюминиевыми рудами. Однако до второй половины ХХ в. в Казахстане не было ни одного завода по производству алюминия. Огромное богатство оставалось неисследованным и невостребованным. Вообще строительство алюминиевых заводов происходило наряду со строительством электростанций, так как для получения одной тонны алюминия необходимо было затратить 18 тыс. киловатт-часов электроэнергии.
В Казахстане в 2007 г был построен Павлодарский электролизный завод по получению алюминия. На этом заводе используется иртышская вода(Екибастузкая ГРЭС), экибастузский уголь и торгайские бокситы. Электролиз расплава проводится при температуре 1000ºС, пропуская ток силой 60 000А, напряжением 4 -6 В. Для получения одной тонны алюминия расходуется 20 000 кВт/ч электроэнергии. Применяя последние технические достижения, Павлодарский завод выпускает самый дешевый алюминий. Планируется довести производство алюминия до 240 тыс. т в год.
В настоящее время в промышленном масштабе алюминия производится очень много, так как он даёт по свойствам лёгкие, прочные сплавы: силумин, магналий, дюралюминий. Применяют в самолётостроении, автомобилестроении и для производства железнодорожных вагонов. Алюминий – хороший проводник электричества, поэтому применяют в электротехнике. Алюминий легко прокатывается в фольгу толщиной 0,005 мм.
Преимуществом металлургии Казахстана является наличие собственной минерально-сырьевой базы. Казахстан полностью обеспечивает потребности своей индустрии в сырье, поскольку располагает поистине огромными запасами различных полезных ископаемых. К примеру, оцененные запасы железной руды в стране составляют 16,6 млрд т, что соответствует 6% общемировых запасов данного сырья. Из них около 8,8 млрд т изучены и в настоящее время доступны для промышленной разработки. Производство черной металлургии в основном сосредоточено на предприятиях Карагандинской области (более 60% всей производимой в республике продукции). В области действует крупнейшее предприятие металлургической промышленности Казахстана – Карагандинский металлургический комбинат “Испат-Кармет”, который производит 100% чугуна и готового проката черных металлов и более 90% стали.
Производство чугуна
Сырьем для производства чугуна и стали являются железные руды:
магнетит Fe3O4 (содержит до 72% Fe),
гематит Fe2O3 (содержит до 65% Fe),
лимонит Fe2O3 · nH2O (содержит до 60% Fe),
Доменная печь имеет форму двух усеченных конусов, соединенных основаниями.
Высота доменной печи более 60 м, диаметр – около 10 м.
Стены доменной печи выкладывают из огнеупорного кирпича и снаружи скрепляют стальной оболочкой.
Верхняя часть доменной печи называется колошником, средняя – шахтой, а наиболее широкая – распаром. В самом низу находится горн, имеющий цилиндрическую форму. Внизу горна накапливаются жидкий чугун и шлак, в верхней части горна есть отверстие для вдувания воздуха. Наверху домны имеется автоматическое загрузочное устройство. Внутренний объем печи 5000 м3.
Доменная печь работает в режиме противотока. Сверху в печь непрерывно подается раздробленная до определенных размеров руда и кокс. Снизу вверх движется нагретый газ – восстановитель – монооксид углерода СО: он получается в нижней части домны при сгорании кокса в потоке воздуха, обогащенного кислородом. При сгорании углерода вначале образуется углекислый газ СО2, который проходит через расположенный кокс и превращается с СО. Он восстанавливает железо из оксида железа (III) через промежуточные продукты:
1) С+О2 → СО2;
2) СО2 + С→2СО
3) 3Fe2О3+СО → 2Fе3О4+СО2
4) Fе3О4+СО → 3FeО+СО2
5) FeО+СО → Fе + СО2
В результате получаем чугун – сплав железа, содержащий 3,0 – 4,5 % углерода
Распределение температуры в доменной печи следующее: 1850°С в горне; ≈ 1100°С в распаре; 250-200°С в шахте.
Столь высокая температура в горне обеспечивается экзотермической реакцией горения угля.
Но нельзя ли как-то интенсифицировать все эти процессы?
Производительность доменной печи зависит не только от ее размера, но и от скорости протекания в ней химических процессов.
-Скорость химических реакций увеличивается при повышении концентрации реагирующих веществ. Поэтому железную руду обогащают, т.е. отделять ее от пустой породы, а к вдуваемому в печь воздуху добавлять кислород.
-Скорость химических реакций зависит от поверхности соприкосновения реагирующих веществ. С учетом этого загружаемые в доменную печь руда и кокс должны состоять из кусков определенных размеров. Крупные куски необходимо измельчать, а слишком мелкие укрупнять спеканием, иначе мелкие куски закроют проход газам.
-Скорость реакции зависит от температуры. Для повышения температуры воздух, вдуваемый в печь, предварительно необходимо нагревать в регенераторах.
Чугун хрупок, при ударе ломается. Изделия из него массивны и тяжелы: станины и маховики машин, решетки, крышки люков, трубы, мясорубки, сковородки . Основная часть чугуна используется для передела его в сталь.
Производство стали
Конвертер – большой металлический сосуд грушевидной формы. Изнутри конвертер выложен огнеупорной кладкой.
Загружают конвертор в горизонтальном положении.
Воздух или чистый кислород подается в конвертор под давлением через фурму.
Химизм процесса
Сущность передела чугуна в сталь в конвертере сводится к удалению из чугуна избыточного углерода, кремния, фосфора и серы путем их оплавления, связывания и удаления в виде шлака:
2С+О2 → 2CО
Si+О2 → SiО2
4Р+5О2 → 2Р2О5
S+О2 → SО2
Mn + FeO = Fe + MnO
СаО +SiO₂ = CaSiO₃
Получаем сталь – сплав железа, содержащий менее 2% углерода.
Для поддержания нужной температуры в конвертере не требуется сжигать топливо. Необходимая температура (около 1700°С) достигается в результате экзотермических реакций окисления примесей.
Сталь упруга, поддается ковке и прокатке, прочна. Ее можно ковать и штамповать из нее различные мелкие детали машин, прокатывать в листы. Чем больше в стали углерода, тем она тверже. Наш комбинат производит как твердые, так и мягкие стали. Мягкие стали применяют для изготовления кузовов автомобилей, корпусов холодильников, консервных банок, листов кровельного железа, твердые стали – для изготовления быстрорежущих инструментов.
Для получения высококачественных сталей применяют плавку в электрических печах. В электропечах создается высокая легко регулируемая температура (до 2000° С), что позволяет тщательнее удалить из стали вредные примеси, выплавлять стали с присадкой тугоплавких легирующих элементов (Mo, W и др.), добиваться хорошего раскисления и дегазации. Точная регулировка протекания процесса плавки позволяет получить металл с заданными свойствами.
Однако этот способ более дорогой, чем рассмотренные выше, поэтому в электропечах выплавляют лишь высококачественные стали с особыми физическими и химическими свойствами.
Металлургия – крупный загрязнитель окружающей среды. На ее долю приходится 20% всех промышленных выбросов в атмосферу и сточных вод. Ежегодно металлургические предприятия выбрасывают в атмосферу более 10 млн. тонн вредных веществ, среди которых гигантское количество разнообразных металлов. При открытой добыче руд из хозяйственного оборота изымаются десятки тысяч гектаров земли. Огромные средства расходуются на строительство очистных сооружений и рекультивацию нарушенных земель. При производстве алюминия негативное влияние на окружающую среду оказывают выделяющиеся вредные газы и отходы, так как алюминий относится к токсичным элементам. Безопасность природной среды может быть обеспечена, если будут разработаны новые технологии производства алюминия, очищаться сточные воды, строго контролироваться выбросы соединений алюминия. Можно добывать руду, не нарушая ландшафт, с помощью био- или геотехнологий.
4.Закрепление.
Решите задачу:
Образец сплава железа с углеродом массой 8 г растворили в соляной кислоте. Объём выделившегося водорода составил 0,06 л при нормальных условиях. Какой сплав железа был взят? Определите массовую долю углерода в сплаве.
Глинозем используют для получения алюминия электролизом в расплаве. Выделившийся на аноде кислород окисляет графитовый анод, образуя углекислый газ. Какая масса алюминия было получена, если в результате реакции на аноде собран газ объемом 67,2 л (н. у.)
Если выход железа 92%, то какая масса углерода расходуется для полного восстановления 786 т магнетита(Fe3O4), содержащего 15% примесей
5.Подведение итогов.
6.Рефлексия.
7.Домашнее задание:§8.2, 8.3, упр.6
А1. Сырьем для производства чугуна является:
1.железная руда
2.известняк
3.малахит
4.пирит
А2. Восстановителем железа из железной руды является
1.угарный газ
2.кокс
3.водород
4. все перечисленные вещества
А3. Чугун получают в специальных печах –
1.домна
2.печь обжига
3.мартеновские печи
4.колонна синтеза
А4. Сырьем для производства стали является:
1.железная руда
2.пирит
3.чугун
4.известняк
А5. Роль флюса при доменном производстве выполняет
1.пирит
2.угарный газ
3.известняк
4.уголь
А6. Примеси в железной руде образуют
1.шлаки
2.флюс
3.чугун
4.кокс
А7. Суть доменного процесса
1.образование олеума
2.восстановление металла из руды
3.окисление железа
4.взаимодействие железа с серой
Бланк правильных ответов
| А1 | А2 | А3 | А4 | А5 | А6 | А7 |
1 | Х |
| Х |
|
| Х |
|
2 |
|
|
|
|
|
| Х |
3 |
|
|
| Х | Х |
|
|
4 |
| Х |
|
|
|
|
|
Алюминиевые сплавы или алюминиевые сплавы представляют собой сплавы алюминия, часто с медью, цинком, марганцем, кремнием или магнием. Составы алюминиевых сплавов зарегистрированы в Алюминиевой ассоциации. Многие организации публикуют более конкретные стандарты для производства алюминиевых сплавов, в том числе организация по стандартизации Общества автомобильных инженеров, в частности, ее подгруппы по аэрокосмическим стандартам, Дополнительные рекомендуемые знания
Инженерное использованиеОбзорАлюминиевые сплавы с широким спектром свойств применяются в инженерных конструкциях. Системы сплавов классифицируются по системе нумерации (ANSI) или по наименованиям, указывающим на их основные легирующие компоненты (DIN и ISO). Выбор правильного сплава для данного применения влечет за собой рассмотрение прочности, пластичности, формуемости, свариваемости и коррозионной стойкости, и это лишь некоторые из них. Вопросы гибкостиНеправильное использование алюминия может привести к проблемам, особенно в отличие от железа или стали, которые кажутся интуитивным проектировщикам, механикам или техникам «лучше себя вести». Уменьшение на две трети веса алюминиевой детали по сравнению с железной или стальной деталью аналогичного размера кажется чрезвычайно привлекательным, но следует отметить, что эта замена сопровождается уменьшением на две трети жесткости детали. Таким образом, хотя прямая замена железной или стальной детали копией из алюминия может по-прежнему обеспечивать приемлемую прочность, позволяющую выдерживать пиковые нагрузки, повышенная гибкость вызовет в три раза больший прогиб детали. Если отказ не является проблемой, но чрезмерное изгибание нежелательно из-за требований к точности определения местоположения или эффективности передачи мощности, простая замена стальных труб на алюминиевые трубки аналогичного размера приведет к нежелательной степени изгиба; например, повышенный изгиб при рабочих нагрузках, вызванный заменой стальных труб рамы велосипеда на алюминиевые трубы идентичных размеров, приведет к смещению силовой передачи, а также к поглощению рабочей силы. В таких случаях лучше всего использовать алюминий, изменив размер детали в соответствии с ее характеристиками; например, изготовление велосипедной рамы из алюминиевых труб большего диаметра, чем более толстых стенок. Таким образом можно восстановить или даже повысить жесткость без увеличения веса. [3] Ограничением этого процесса является увеличение склонности к потере устойчивости. Последние модели автомобиля Corvette, среди прочего, являются хорошим примером модернизации деталей для максимального использования преимуществ алюминия. Алюминиевые элементы шасси и детали подвески этих автомобилей имеют большие габаритные размеры для обеспечения жесткости, но они облегчены за счет уменьшения площади поперечного сечения и удаления ненужного металла. В результате они не только такие же или даже более прочные и жесткие, чем стальные детали, которые они заменяют, но и обладают воздушной грацией, которая нравится большинству людей. Прочность и долговечность алюминия сильно различаются не только в зависимости от компонентов конкретного сплава, но и в результате производственного процесса. Эта изменчивость, а также кривая обучения при ее использовании, время от времени приобретали алюминий плохую репутацию. Например, высокая частота отказов многих плохо спроектированных ранних алюминиевых велосипедных рам в 1970-х годах подорвала репутацию алюминия в этом использовании. Однако широкое использование алюминиевых компонентов в аэрокосмической и высокоэффективной автомобильной промышленности, где огромные нагрузки выдерживаются с исчезающе малой частотой отказов, показывает, что правильно изготовленные алюминиевые велосипедные компоненты не обязательно должны быть ненадежными по своей сути. Аналогичным образом, использование алюминия в автомобилестроении, особенно в деталях двигателя, которые должны выдерживать тяжелые условия, со временем улучшилось. Инженер Audi, комментируя двигатель V12 мощностью более 500 лошадиных сил (370 кВт) гоночного автомобиля Auto Union 1930-х годов, который был недавно восстановлен на заводе Audi, отметил, что оригинальный алюминиевый сплав двигателя сегодня используется только для садовой мебели и тому подобного. Еще в 1960-х годах алюминиевые головки цилиндров и картер Corvair заработали репутацию из-за отказов и срыва резьбы в отверстиях, даже таких больших, как отверстия для свечей зажигания, чего не наблюдается в современных алюминиевых головках цилиндров. Одним из важных структурных ограничений алюминиевого сплава являются его усталостные свойства. В то время как сталь имеет высокий предел выносливости (теоретически конструкция может выдерживать бесконечное число циклических нагрузок при этом напряжении), предел выносливости алюминия близок к нулю, что означает, что он в конечном итоге выйдет из строя даже при очень малых циклических нагрузках, но при малых напряжениях это может занимать чрезвычайно много времени. Вопросы чувствительности к теплуЧасто также необходимо учитывать чувствительность металла к теплу. Даже относительно рутинная процедура в мастерской, связанная с нагревом, усложняется тем фактом, что алюминий, в отличие от стали, плавится без предварительного свечения красным цветом. Таким образом, операции формования с использованием паяльной лампы требуют определенного опыта, поскольку никакие визуальные признаки не показывают, насколько материал близок к плавлению. Алюминий также подвержен внутренним напряжениям и деформациям при перегреве; склонность металла к ползучести под действием этих напряжений приводит к замедленным деформациям. Например, деформация или растрескивание перегретых алюминиевых автомобильных головок цилиндров обычно наблюдается, иногда спустя годы, как и тенденция сварных алюминиевых велосипедных рам постепенно скручиваться из-за напряжений, возникающих в процессе сварки. Таким образом, аэрокосмическая промышленность полностью избегает тепла, соединяя детали с помощью клея или механических застежек. Напряжения в перегретом алюминии можно снять путем термической обработки деталей в печи и постепенного их охлаждения, т. е. фактически отжигая напряжения. Тем не менее, эти детали все еще могут деформироваться, так что, например, термическая обработка сварных велосипедных рам может привести к смещению значительной части. Если несоосность не слишком велика, охлаждаемые детали могут быть согнуты для соосности. Конечно, если рама правильно рассчитана на жесткость (см. выше), для этого изгиба потребуется огромное усилие. Непереносимость алюминия к высоким температурам не исключает его использования в ракетной технике; даже для использования в конструкции камер сгорания, где температура газов может достигать 3500 К. В двигателе верхней ступени Agena использовалась алюминиевая конструкция с регенеративным охлаждением для некоторых частей сопла, включая термически критическую область горловины; на самом деле чрезвычайно высокая теплопроводность алюминия не позволяла горловине достичь точки плавления даже при сильном тепловом потоке, что привело к созданию надежного легкого компонента. Бытовая электропроводкаИз-за его высокой проводимости и относительно низкой цены по сравнению с медью в 1960-х годах алюминий был представлен в то время для бытовой электропроводки в Соединенных Штатах, хотя многие светильники не были предназначены для использования алюминиевого провода. Но новое использование принесло некоторые проблемы:
Все это привело к перегреву и ослаблению соединений, что, в свою очередь, привело к нескольким пожарам. Затем строители стали опасаться использования проволоки, и во многих юрисдикциях ее использование в очень малых размерах в новом строительстве было запрещено. Еще один способ избежать проблемы с нагревом — обжать алюминиевый провод на короткой «косичке» из медного провода. Правильно выполненный обжим под высоким давлением с помощью надлежащего инструмента достаточно тугой, чтобы уменьшить любое тепловое расширение алюминия. Сегодня для алюминиевой проводки в сочетании с алюминиевыми наконечниками используются новые сплавы, конструкции и методы.
Обозначения сплавов Кованые и литые алюминиевые сплавы используют разные системы идентификации. Кованый алюминий идентифицируется четырехзначным числом, которое идентифицирует легирующие элементы, за которым следует тире, буква, определяющая тип термической обработки, и число от 1 до 4 цифр, определяющее конкретный отпуск, например. Деформируемые сплавыМеждународная система обозначения сплавов является наиболее широко принятой схемой обозначения деформируемых сплавов. Каждому сплаву присваивается четырехзначный номер, где первая цифра указывает на основные легирующие элементы.
Пределы состава кованого алюминиевого сплава (% веса)
| 0,10 | 9000 2 9000.35.00620,05 | 0,15 | остаток | ||||||||||||||||||||||||||||||||||||||||||||||||||||||||||||||||||||||||||||||||||||||||||||||||||||||||||||||||||||||||||||||||||||||||||||||||||||||||||||||||||||||||||
5083 | 0.40 | 0.40 | 0.10 | 0.40-1.0 | 4.0-4.9 | 0.05-0.25 | 0.25 | 0.15 | 0.![]() | 0,15 | остаток | |||||||||||||||||||||||||||||||||||||||||||||||||||||||||||||||||||||||||||||||||||||||||||||||||||||||||||||||||||||||||||||||||||||||||||||||||||||||||||||||||||
5086 | 0.40 | 0.50 | 0.10 | 0.20-0.7 | 3.5-4.5 | 0.05-0.25 | 0.25 | 0.15 | 0.05 | 0.15 | remainder | |||||||||||||||||||||||||||||||||||||||||||||||||||||||||||||||||||||||||||||||||||||||||||||||||||||||||||||||||||||||||||||||||||||||||||||||||||||||||||||||||||
5154 | 0,25 | 0,40 | 0,10 | 0,10 | 3,1-3,9 | 0,15-0,35 | 0,20 | 0,15-0,35 | 0,20 | Остаток | ||||||||||||||||||||||||||||||||||||||||||||||||||||||||||||||||||||||||||||||||||||||||||||||||||||||||||||||||||||||||||||||||||||||||||||||||||||||||||||||||||||
5454 | 0.25 | 0.40 | 0.10 | 0.50-1.0 | 2.4-3.0 | 0.05-0.20 | 0.25 | 0.20 | 0.05 | 0,15 | остаток | |||||||||||||||||||||||||||||||||||||||||||||||||||||||||||||||||||||||||||||||||||||||||||||||||||||||||||||||||||||||||||||||||||||||||||||||||||||||||||||||||||
5456 | 0.25 | 0.40 | 0.10 | 0.50-1.![]() | 4.7-5.5 | 0.05-0.20 | 0.25 | 0.20 | 0.05 | 0.15 | остаток | |||||||||||||||||||||||||||||||||||||||||||||||||||||||||||||||||||||||||||||||||||||||||||||||||||||||||||||||||||||||||||||||||||||||||||||||||||||||||||||||||||
6005 | 0,6-0,9 | 0,35 | 0,10 | 0,10 | 0,40-0,6 | 0,10 | 0,10 90-0,6 | 0,10 | 0,10 990-0,6 | 0,10 | 0,10 9.Остаток||||||||||||||||||||||||||||||||||||||||||||||||||||||||||||||||||||||||||||||||||||||||||||||||||||||||||||||||||||||||||||||||||||||||||||||||||||||||||||||||||||
6005A | 0.50-0.9 | 0.35 | 0.30 | 0.50 | 0.40-0.7 | 0.30 | 0.20 | 0.10 | 0.05 | 0.15 | остаток | |||||||||||||||||||||||||||||||||||||||||||||||||||||||||||||||||||||||||||||||||||||||||||||||||||||||||||||||||||||||||||||||||||||||||||||||||||||||||||||||||||
6060 | 0.30-0.6 | 0.10-0.30 | 0.10 | 0.10 | 0.35-0.6 | 0.5 | 0.15 | 0.10 | 0.![]() | 0,15 | остаток | |||||||||||||||||||||||||||||||||||||||||||||||||||||||||||||||||||||||||||||||||||||||||||||||||||||||||||||||||||||||||||||||||||||||||||||||||||||||||||||||||||
6061 | 0.40-0,8 | 0,7 | 0,15-0,40 | 0,15 | 0,8-1,2 | 0,04-0,35 | 0,8-1,2 | 0,04-0,35 |
2,
2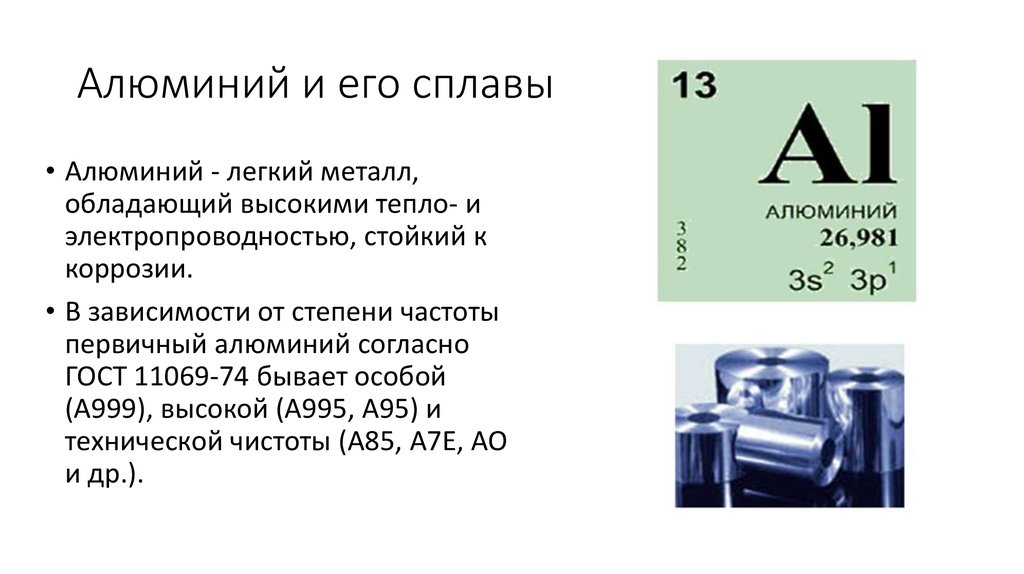
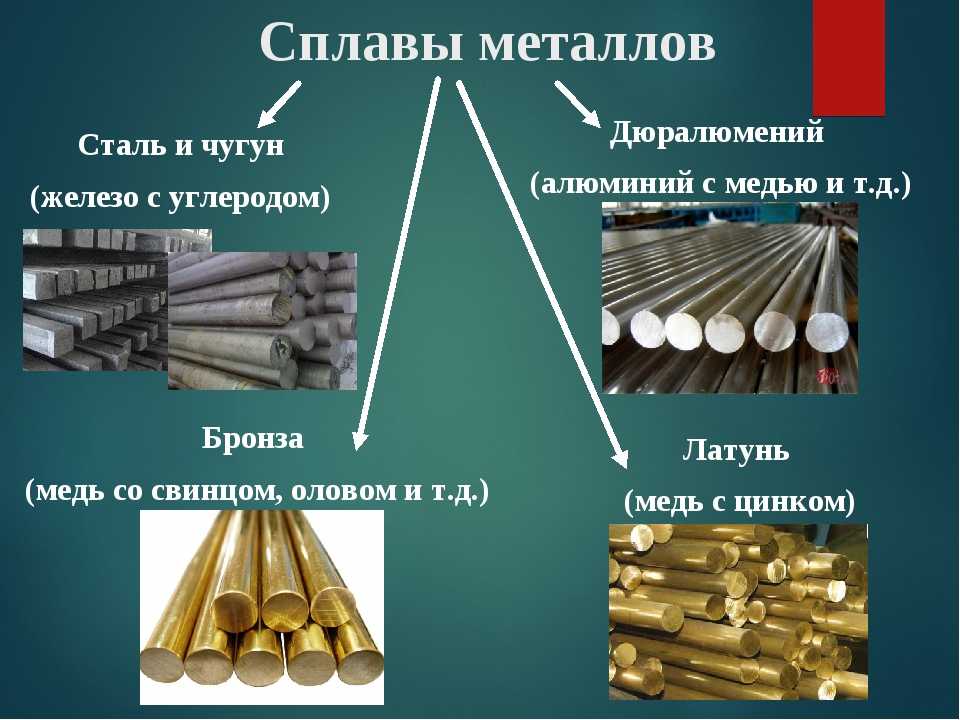


“Другие” ограничения применяются ко всем элементам, независимо от того, существует ли для них столбец таблицы или нет, для которых не указано другое ограничение. сплав 6005A имеет еще один предел, не указанный выше: соотношение марганца и хрома должно находиться в диапазоне 0,12-0,50.
Литейные сплавы
Алюминиевая ассоциация (АА) приняла номенклатуру, аналогичную номенклатуре деформируемых сплавов. Британский стандарт и DIN имеют разные обозначения. В системе AA вторые две цифры показывают минимальный процент алюминия, т.е. 150.x соответствуют минимум 99,50% алюминия. Цифра после запятой принимает значение 0 или 1, обозначая отливку и слиток соответственно [4] . Основные легирующие элементы в системе AA следующие:
- Серия 1xx.x минимум на 99% состоит из алюминия
- Серия 2xx.x, медь
- Серия 3xx.x кремний, медь и/или магний
- Кремний серии 4xx.x
- Серия 5xx.x магний
- Цинк серии 7xx.x
- Банка серии 8xx.x
- Серия 9xx.x Разное
Именованные сплавы
- Дюралюминий (медь, алюминий)
- Magnox (магний, алюминий)
- Zamak (цинк, алюминий, магний, медь)
- Силумин (алюминий, кремний)
Обзор использования
Общие аэрокосмические сплавы
Это алюминиевые сплавы, которые уже давно используются в самолетах и других аэрокосмических конструкциях. [5]
- 7075 алюминий
- 6061 алюминий
- 6063 алюминий
- 2024 алюминий
- 5052 алюминий
Прочие аэрокосмические сплавы
В настоящее время производятся, но менее широко используются алюминиевые сплавы для аэрокосмических применений.
- 2090 алюминий
- 2124 алюминий
- 2195 алюминий – сплав Al-Li, используемый в сверхлегком внешнем баке космического корабля “Шаттл”
- 2219 алюминий
- 2324 алюминий
- 6013 алюминий
- 7050 алюминий
- 7055 алюминий
- 7150 алюминий
- 7475 алюминий
Морские сплавы
Эти сплавы используются в судостроении и судостроении, а также в других морских и прибрежных применениях, чувствительных к соленой воде. 9 Судостроение из алюминия , Стивен Ф. Поллард, 1993, International Marine, ISBN 0-07-050426-1
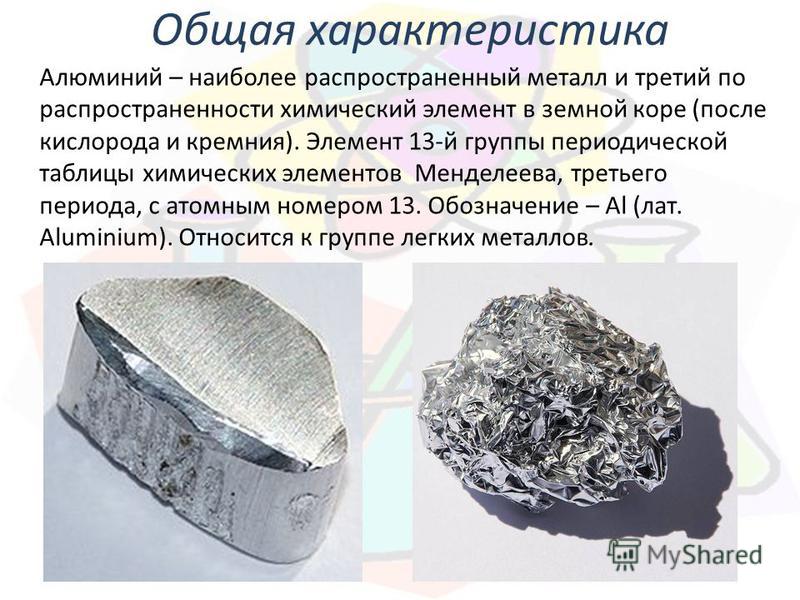
Алюминий и алюминиевые сплавы | Арнольд Магнитные Технологии
Легкий и универсальный материал
Тонкокатаный алюминий и алюминиевые сплавы от Arnold Precision Thin Metals (PTM) универсальны и легки и используются для упаковки различных электротехнических изделий и других приложений. Алюминий часто является лучшим решением, когда желательными характеристиками являются малый вес, хорошая проводимость и высокая формуемость. Чтобы удовлетворить эти потребности, PTM предлагает своим клиентам алюминиевые полосовые материалы различной толщины и состава сплава.
Ключевые приложения и используют
- батареи
- Кабельные и компонентные экранирование
- Упаковка
- Pharmaceutical, Cosmetics
Доступны в All All Gradess и Tempers
. алюминиевых марок в различных состояниях.

Четырехзначная схема нумерации деформируемых и литых сплавов Международной системы обозначений сплавов обеспечивает быструю справку для нужд вашего применения.
СЕРИЯ 1000
Практически чистый алюминий с содержанием алюминия не менее 99% по весу, может подвергаться деформационному упрочнению.
СЕРИЯ 2000
Легированный медью, может подвергаться дисперсионному твердению до прочности, сравнимой со сталью. Ранее называвшиеся дюралюминием, они когда-то были наиболее распространенными аэрокосмическими сплавами, но были подвержены коррозионному растрескиванию под напряжением и все чаще заменяются серией 7000 в новых конструкциях.
СЕРИЯ 3000
Легирован марганцем и может подвергаться деформационному упрочнению.
СЕРИЯ 4000
Сплав кремния. Также известен как силумин.
СЕРИЯ 5000
Сплав магния.
СЕРИЯ 6000
Легированы магнием и кремнием, легко поддаются механической обработке и могут подвергаться дисперсионному твердению, но не до такой высокой прочности, которой могут достичь сплавы серий 2000 и 7000.
СЕРИЯ 7000
Легированный цинком, может подвергаться дисперсионному твердению до самой высокой прочности любого алюминиевого сплава.
СЕРИЯ 8000
Легированные другими элементами, не включенными в другие серии. Например, алюминиево-литиевые сплавы.
РАЗМЕРЫ
Каждый из них доступен в различных толщинах и размерах, показанных ниже:
Толщина | Максимальная ширина | 5mm) as rolled edge 17.0” (431.8mm) with a slit edge”> |
---|---|
0,00039″ – 0,0001″ (0,0099 – 0,0025 мм) | 4,25 дюйма (107,95 мм) с закругленной кромкой 4,0 дюйма (101,6 мм) с щелевой кромкой |
СОСТАВ СПЛАВА ОБЫЧНО ПРЕДЛАГАЕМЫХ МАРОК
Состав указан в весовых процентах (мас.%).
Grade | Al | Si | Fe | Cu | Mg | Mn | Cr | Zn |
---|---|---|---|---|---|---|---|---|
1050 | 5 min”> | 0,25 | 0,4 | 0,05 | — | — | — | — |
1100 | 0 min”> | 0,95 Si+Fe | 0,05 – 0,20 | — | — | — | — | — |
2024 | 7 – 93.0″> | 0,5 | 0,5 | г. 3,8 – 4,9 | 1,2 – 1,8 | 0,30 – 0,9 | — | — |
5052 | 7 – 96.5″> | 0,25 | 0,4 | 0,1 | 2,2 – 2,8 | — | 0,15 – 0,35 | — |
6061 | 8 – 97.16″> | 0,40 – 0,8 | 0,7 | 0,15 – 0,40 | 0,8 – 1,2 | — | — | — |
7075 |