Сталь 20х термообработка: Сталь 20Х: Характеристики, расшифровка марки, состав
alexxlab | 18.01.2023 | 0 | Разное
20Х :: Металлические материалы: классификация и свойства
Сталь 20Х ГОСТ 4543-71
Группа стали – хромистая
Массовая доля элементов, % | ||||||||
Углерод | Кремний | Марганец | Хром | Никель | Молибден | Алюминий | Титан | Ванадий |
0,17-0,23 | 0,17-0,37 | 0,50-0,80 | 0,70-1,00 | – | – | – | – |
Ac1 | Ac3(Acm) | Ac3(Arcm) | Ar1 | Mн |
750 | 825 | 755 | 665 | 390 |
Число твердости, НВ, не более | |
Отожженный или высокоотпущенный прокат | 179 |
Нагартованный прокат | 229 |
Термообработка | Передел текучести σт, Н/мм2 (кгс/мм2) не менее | Временное сопротивление σв, Н/мм2 (кгс/мм2) | Относительное удлинение δ5,% | Относительное сужение ψ, % | Ударная вязкость KCU, Дж/см2 (кгс·м/см2) | ||||||
Закалка | Отпуск | ||||||||||
Температура, оС | Среда охлаждения | Температура, оС | Среда охлаждения | ||||||||
1-й закалки или нормализации | 2-й закалки | ||||||||||
не менее | |||||||||||
880 | 770-820 | Вода или масло | 180 | Воздух или масло | 635(65) | 780(80) | 11 | 40 | 59(6) | 15 |
Твёрдость, НВ, не более | Временное сопротивление σВ, Н/мм2 (кгс/мм2) | Относительное сужение ψ, %, не менее | ||
после отпуска или обычного отжига | после сфероидизи-рующего отжига | |||
Прокат горячекатаный и горячекатаный со специальной отделкой поверхности | Прокат калиброванный и калиброванный со специальной отделкой поверхности | |||
163 | 179 | Не более 550 (56) | 360 – 470 (37 – 48) | 60 |
Твёрдость, НВ, не более | Временное сопротивление σВ, Н/мм2 (кгс/мм2) | Относительное удлинение δ5, % | Относительное сужение ψ, %, | |
Не менее | ||||
Прокат горячекатаный и горячекатаный со специальной отделкой поверхности | Прокат нагартованный калиброванный и калиброванный со специальной отделкой поверхности | |||
– | 207 | 590 (60) | 5 | 45 |
Термообработка | Сечение, мм | КП | Предел текучести, σ0,2 | Временное сопротивление σв, | Относительное удлинение δ5 | Относительное сужение ψ | KCU, Дж/см2 | HB, не более |
МПа | % | |||||||
не менее | ||||||||
Нормализация | до 100 100-300 300-500 | 195 | 195 | 390 | 26 23 20 | 55 50 45 | 59 54 49 | 111-156 |
до 100 100-300 | 215 | 215 | 430 | 24 20 | 53 48 | 54 49 | 123-167 | |
до 100 100-300 | 245 | 245 | 470 | 22 19 | 48 42 | 49 39 | 143-179 143-179 | |
Закалка. | до 100 100-300 | 275 275 | 275 275 | 530 530 | 20 17 | 40 38 | 44 34 | 156-197 156-197 |
100-300 100-300 | 315 345 | 315 345 | 570 590 | 14 17 | 35 40 | 34 54 | 167-207 174-217 |
Температура отпуска, ºС | Предел текучести ,σ0,2 МПа | Временное сопротивление σв, МПа | Относительное удлинение δ5 | Относительное сужение ψ | KCU, Дж/см2 |
% | |||||
Пруток диаметром 25 мм. | |||||
200 300 400 500 600 | 650 690 690 670 610 | 880 880 850 780 730 | 18 16 18 20 20 | 58 65 70 71 70 | 118 147 176 196 225 |
Температура испытания, ºС | Предел текучести ,σ0,2 МПа | Временное сопротивление σв, МПа | Относительное удлинение δ5 | Относительное сужение ψ |
% | ||||
Образец диаметром 6 мм и
длиной 30 мм, кованый и нормализованный. | ||||
700 800 900 1000 1100 1200 | 120 63 51 33 21 14 | 150 93 84 51 33 25 | 48 56 64 78 98 – | 89 74 88 97 100 – |
Предел выносливости | Состояние стали |
σ-1, МПа | |
235 295 412 | Нормализация σ0,2=295-395 МПа, σв=450-590 МПа, HB 143-179 Закалка. Цементация. Закалка. Низкий отпуск. σ0,2=790 МПа, σв=930 МПа, HRCЭ 57-63 |
Температура, ºС | Состояние поставки | |||
20 | -20 | -40 | -60 | |
Ударная вязкость KCU, Дж/см2 | ||||
280-286 | 280-289 | 277-287 | 261-274 | Пруток диаметром 115 мм. Закалка. Отпуск |
Расстояние от торца, мм | Примечание | ||||||||||
1,5 | 3 | 4,5 | 6 | 7,5 | 9 | 10,5 | 12 | 13,5 | 18 | Закалка 860 ºС | |
Прокаливаемость | |||||||||||
38,5-49 | 34-46,5 | 29-44 | 24,5-40 | 22-35,5 | 32,5 | 30 | 28,5 | 27 | 24,5 | Твердость для полос прокаливаемости, HRCЭ | |
Количество мартенсита, % | Критическая твердость, HRCЭ | Критический диаметр, мм | |
в воде | в масле | ||
50 90 | 32-36 38-42 | 26-48 12-28 | 8-24 3-9 |
Группа | Величина деформации при холодной осадке | Способ изготовления | Состояние поставки |
50 | До 1/2 первоначальной высоты образца | Горячекатаный | Без термической обработки |
Горячекатаный и калиброванный | Термически обработанный | ||
66 | До 1/3 первоначальной высоты образца | Горячекатаный, калиброванный, горячекатаный и калиброванный со специальной отделкой поверхности | Термически обработанный |
66Т | До 1/3 первоначальной высоты термически обработанного образца с твёрдостью 163 НВ | Горячекатаный | Без термической обработки |
66И | До 1/3 первоначальной высоты термически обработанного обточенного образца | Горячекатаный | Без термической обработки |
Назначение проката | Группа осадки | Допускаемые дефекты | |
Наименование | Максимальная глубина залегания | ||
Для изготовления калиброванного проката (без специальной отделки поверхности) | 50, 66 и 66Т | Отпечатки, рябизна | Половина допуска на размер |
Отдельные мелкие риски | 1/4 допуска на размер, но не более 0,1мм для сечений до 20мм и не более 0,2мм для сечений 20мм и выше | ||
Для изготовления горячекатаного и калиброванного со специальной отделкой поверхности проката | 66И | Отпечатки, рябизна, риски, мелкие раскатанные пузыри и загрязнение | Допуск на размер |
Заменитель
– стали: 15Х, 20ХН, 12ХН2, 18ХГТ.
Температура ковки, ºС:
начала 1260,
конца 750.
Заготовки сечением до 200 мм охлаждаются на воздухе, 201-700 мм подвергаются низкотемпературному отжигу.
Свариваемость – сваривается без ограничений, кроме химико-термически обработанных деталей; способы сварки: РДС, КТС без ограничений.
Обрабатываемость резанием – в горячекатаном состоянии при HB 131 и σв=460 МПа, КV т.в. спл =1,7, КV б. ст =1,3.
Флокеночувствительность – малочувствительна.
Склонность к отпускной хрупкости – не склонна.
Назначение: втулки, шестерни, обоймы, гильзы, диски, плунжеры, рычаги и другие цементуемые детали, к которым предъявляются требования высокой поверхностной твердости при невысокой прочности сердцевины, детали , работающие в условиях износа при трении.
Полосы прокаливаемости
По требованию потребителя, указанному в заказе, пачки, концы или торцы горячекатаных и кованых прутков, а по согласованию изготовителя с потребителем и калиброванных прутков из стали всех марок в зависимости от группы должны маркироваться краской в соответствии с таблицей
Сортамент, форма размеры и предельные отклонения по размерам проката стали должны соответствовать требованиям:
прокат горячекатаный круглый – ГОСТ 2590-88;
прокат горячекатаный шестигранный – ГОСТ 2879-88;
прокат калиброванный круглый – ГОСТ 7417-75;
прокат калиброванный шестигранный – ГОСТ 8560-78;
профиль холоднотянутый шестигранный – ГОСТ 8560-78
Марка стали 20Х характеристики, расшифровка, применение, свойства, заменители, аналоги, твердость
Содержание
- 1 Заменители
- 2 Иностранные аналоги
- 3 Вид поставки
- 4 Назначение
- 5 Расшифровка стали 20Х
- 6 Применение стали 20Х корпусов, крышек, фланцев, мембран и узла затвора, изготовленных из проката, поковок (штамповок) (ГОСТ 33260-2015)
- 7 Применение стали 20Х для деталей арматуры и пневмоприводов, не работающих под давлением и не подлежащих сварке, предназначенных для эксплуатации в условиях низких температур (ГОСТ 33260-2015)
- 8 Температура критических точек, °С
- 9 Химический состав, % (ГОСТ 4543-71)
- 10 Химический состав, % (ГОСТ 4543-2016)
- 11 Твердость (ГОСТ 4543-2016)
- 12 Механические свойства проката (ГОСТ 4543-2016)
- 13 Механические свойства проката
- 14 Механические свойства поковок (ГОСТ 8479-70)
- 15 Механические свойства в зависимости от температуры отпуска
- 16 Механические свойств при повышенных температурах
- 17 Предел выносливости при n = 107
- 18 Ударная вязкость KCU
- 19 Технологические свойства
- 20 Свариваемость
- 21 Критический диаметр d
- 22 Физические свойства
- 22.
1 Плотность ρ кг/см3 при температуре испытаний, °С
- 22.2 Коэффициент теплопроводности λ Вт/(м*К) при температуре испытаний, °С
- 22.3 Коэффициент линейного расширения α*106, К-1, при температуре испытаний, °С
- 22.4 Удельная теплоемкость c, Дж/(кг*К), при температуре испытаний, °С
- 22.5 Модуль нормальной упругости Е, ГПа, при температуре испытаний, °С
- 22.6 Модуль упругости при сдвиге на кручением G, ГПа, при температуре испытаний °С
- 22.
- 23 Узнать еще
Заменители
Стали 15Х, 20ХН, 12ХН2, 18ХГТ.
Иностранные аналоги
Германия DIN | 20Cr4, 20CrS4 | |
США (AISI, SAE, ASTM) | 5120, 5120H | |
Великобритания (BS) | 207 | |
Япония (JIS) | SCr420, SCr420H |
ВАЖНО!!! Возможность замены определяется в каждом конкретном случае после оценки и сравнения свойств сталей
Вид поставки
Cортовой прокат, в том числе фасонный: ГОСТ 4543—71, ГОСТ 2590-88, ГОСТ 2591-88, ГОСТ 10702-78, ГОСТ 2879-88.
Калиброванный пруток ГОСТ 8559-75, ГОСТ 8560-78, ГОСТ 7417-75, ГОСТ 1051-73.
Шлифованный пруток и серебрянка ГОСТ 14955-77.
Лист толстый ГОСТ 1577—93, ГОСТ 19903—74.
Полоса ГОСТ 82—70, ГОСТ 103—76.
Поковки и кованые заготовки ГОСТ 1133-71, ГОСТ 8479-70.
Трубы ГОСТ 8731-87, ГОСТ 8732-78, ГОСТ 8733-74, ГОСТ 8734-75, ГОСТ 13663-86.
Назначение
Втулки, шестерни, обоймы, гильзы, диски, плунжеры, рычаги и другие цементуемые детали, к которым предъявляются требования высокой поверхностной твердости при невысокой прочности сердцевины, детали, работающие в условиях износа при трении.
Расшифровка стали 20Х
Цифра 20 обозначает, что содержание углерода в стали составляет 0,2%.
Буква Х означает, что в стали содержится хром в количестве до 1,5%.
Применение стали 20Х корпусов, крышек, фланцев, мембран и узла затвора, изготовленных из проката, поковок (штамповок) (ГОСТ 33260-2015)
Марка стали | НД на поставку | Температура рабочей среды (стенки), °С | Дополнительные указания по применению |
20X ГОСТ 4543 | Поковки ГОСТ 8479. ![]() Сортовой прокат Листы ГОСТ 1577, Трубы ГОСТ 8731 | От -40 до 450 | Для сварных узлов арматуры, работающих в неагрессивных средах |
Применение стали 20Х для деталей арматуры и пневмоприводов, не работающих под давлением и не подлежащих сварке, предназначенных для эксплуатации в условиях низких температур (ГОСТ 33260-2015)
Марка стали | Закалка + отпуск при температуре, °С | Примерный уровень прочности, Н/мм2 (кгс/мм2) | Температура применения не ниже, °С | Использование в толщине не более, мм |
20Х | 200 | 900 (90) | -60 | 15 |
ПРИМЕЧАНИЕ
- При термической обработке на прочность ниже указанной в графе 3 или при использовании в деталях с толщиной стенки менее 10 мм температура эксплуатации может быть понижена.
- Максимальная толщина, указанная в графе 5, обусловлена необходимостью получения сквозной прокаливаемости и однородности свойств по сечению.
Температура критических точек, °С
Ас1 | Ас3 | Аr3 | Аr1 | Mн |
750 | 825 | 755 | 665 | 390 |
Химический состав, % (ГОСТ 4543-71)
С | Si | Mn | Cr | Ni | Cu | S | P |
не более | |||||||
0,17-0,23 | 0,17-0,37 | 0,5-0,8 | 0,7-1,0 | 0,30 | 0,30 | 0,035 | 0,035 |
Химический состав, % (ГОСТ 4543-2016)
Марка стали | Массовая доля элементов, % | |||||||||
С | Si | Mn | Cr | Ni | Mo | Al | Ti | V | B | |
20Х | 0,17-0,23 | 0,17-0,37 | 0,5-0,8 | 0,7-1,0 | — | — | — | — | — | — |
ПРИМЕЧАНИЕ: знак «-» означает, что массовую долю данного элемента не нормируют и не контролируют, если не указано иное.
Твердость (ГОСТ 4543-2016)
- Твердость по Бринеллю металлопродукции в отожженном (ОТ) или высокоотпущенной (ВО) состоянии, а также горячекатаной и кованой металлопродукции, нормализованной с последующим высоким отпуском (Н+ВО), диаметром или толщиной свыше 5 мм должна соответствовать нормам, указанным в таблице
Марка стали Твердость HB, не более 20Х 179 ПРИМЕЧАНИЕ
Твердость калиброванной металлопродукции в отожженном (ОТ) или высокоотпущенном (ВО) состоянии, а также горячекатаной и кованой металлопродукции, нормализованной с последующим высоким отпуском (Н+ВО), может быть на 15 НВ более указанной в таблице выше. - Твердость горячекатаной и кованой металлопродукции, поставляемой без термической обработки, не нормируют и не контролируют.
- Твердость калиброванной металлопродукции и металлопродукции со специальной отделкой поверхности диаметром или толщиной свыше 5 мм, поставляемой в нагартованном состоянии (НГ), должна соответствовать нормам, указанным в таблице ниже.
Марка стали Твердость НВ, не более 20Х 229
Механические свойства проката (ГОСТ 4543-2016)
Марка стали | Режим термической обработки | Механические свойства, не менее | Размер сечения заготовок для термической обработки (диаметр круга или сторона квадрата), мм | ||||||||
Закалка | Отпуск | Предел текучести σт, Н/мм2 | Временное сопротивление σв, Н/мм2 | Относительное | Ударная вязкость КС U, Дж/см2 | ||||||
Температура, °С | Среда охлажде- ния | Темпера- тура, °С | Среда охлаждения | удлинение δ5,% | сужение Ψ, % | ||||||
1-й закалки или нор- мализации | 2-й за- калки | ||||||||||
20Х | 880 | 770— 820 | Вода или масло | 180 | Воздух или масло | 635 | 780 | 11 | 40 | 59 | 15 |
Механические свойства проката
ГОСТ | Состояние поставки, режим термообработки | Сечение, мм | σ0,2, МПа | σв, МПа | δ5, % | Ψ, % | KCU, Дж/см2 | Твердость, не более |
не более | ||||||||
ГОСТ 4543-71 | Пруток.![]() | 15 | 640 | 780 | 11 | 40 | 59 | — |
ГОСТ 10702-78 | Сталь нагартованная -калиброванная и калиброванная со специальной отделкой без термообработки | — | — | 590 | 5 | 45 | — | HB 207 |
Пруток. Цементация при 920-950 °С, охл. на воздухе; закалка с 800 °С в масле; отпуск при 190 °С, охл. на воздухе | 60 | 390 | 640 | 13 | 40 | 49 | HB 250; HRC5 55-63 |
Механические свойства поковок (ГОСТ 8479-70)
Термообработка | Сечение, мм | КП | σ0,2, МПа | σв, МПа | δ5, % | Ψ, % | KCU, Дж/см2 | Твердость HB, не более |
не менее | ||||||||
Нормализация | До 100 | 195 | 195 | 390 | 26 | 55 | 59 | 111-156 |
100-300 | 23 | 50 | 54 | |||||
300-500 | 20 | 45 | 49 | |||||
До 100 | 215 | 215 | 430 | 24 | 53 | 54 | 123-167 | |
100-300 | 20 | 48 | 49 | |||||
До 100 | 245 | 245 | 470 | 22 | 48 | 49 | 143-179 | |
Закалка+отпуск | 100-300 | 19 | 42 | 39 | 143-179 | |||
До 100 | 275 | 275 | 530 | 20 | 40 | 44 | 156-197 | |
100-300 | 275 | 275 | 530 | 17 | 38 | 34 | 156-197 | |
100-300 | 315 | 315 | 570 | 14 | 35 | 34 | 167-207 | |
100-300 | 345 | 345 | 590 | 17 | 40 | 54 | 174-217 |
Механические свойства в зависимости от температуры отпуска
tотп.![]() | σ0,2, МПа | σв, МПа | δ5, % | Ψ, % | KCU, Дж/см2 |
200 | 650 | 880 | 18 | 58 | 118 |
300 | 690 | 880 | 16 | 65 | 147 |
400 | 690 | 850 | 18 | 70 | 176 |
500 | 670 | 780 | 20 | 71 | 196 |
600 | 610 | 730 | 20 | 70 | 225 |
Примечание: Пруток диаметром 25 мм; закалка с 900 °С, в масле.
Механические свойств при повышенных температурах
tисп. °С | σ0,2, МПа | σв, МПа | δ5, % | Ψ, % |
700 | 120 | 150 | 48 | 89 |
800 | 63 | 93 | 56 | 74 |
900 | 51 | 84 | 64 | 88 |
1000 | 33 | 51 | 78 | 97 |
1100 | 21 | 33 | 98 | 100 |
1200 | 14 | 25 | — | — |
ПРИМЕЧАНИЕ: Образец диаметром 6 мм, длиной 30 мм, кованый и нормализованный; скорость деформирования 16 мм/мин; скорость деформации 0,009 1/с.
Предел выносливости при
n = 107Термообработка | σ-1, МПа |
Нормализация, σ0,2 = 295-395 МПа, σв = 450-590 МПа, HB 143-179 | 235 |
Закалка + высокий отпуск, σ0,2 = 490 МПа, σв = 690 МПа, HB 217-235 | 295 |
Цементация + закалка + низкий отпуск, σ0,2 = 790 МПа, σв = 930 МПа, HRCэ 57-63 | 412 |
Ударная вязкость KCU
Состояние поставки | KCU, Дж/см2, при температуре, °С | |||
+20 | -20 | -40 | -60 | |
Пруток диаметром 115 мм; закалка + отпуск | 280-286 | 280-289 | 277-287 | 261-274 |
Технологические свойства
Температура ковки, °С: начала 1260, конца 750. Заготовки сечением до 200 мм охлаждаются на воздухе, сечением 201-700 мм подвергаются низкотемпературному отжигу.
Обрабатываемость резанием — Kv тв.спл = 1,3 и Kv б.ст = 1,7 в горячекатаном состоянии при НВ 131 σв = 460 МПа.
Флокеночувствительность — малочувствительна.
Склонность к отпускной хрупкости — не склонна.
Свариваемость
Сталь 20Х сваривается без ограничений(кроме химико-термических обработанных деталей). Способы сварки: РДС, КТС без ограничений.
Критический диаметр
dКритическая твердость HRC3 | Количество мартенсита, % | d, мм, после закалки | |
в воде | в масле | ||
32-36 | 50 | 26-48 | 8-24 |
38-42 | 90 | 12-28 | 3-9 |
Физические свойства
Плотность ρ кг/см
3 при температуре испытаний, °ССталь | 20 | 100 | 200 | 300 | 400 | 500 | 600 | 700 | 800 | 900 |
20Х | 7830 | 7810 | 7780 | — | 7710 | — | 7640 | — | — | — |
Коэффициент теплопроводности λ Вт/(м*К) при температуре испытаний, °С
Сталь | 20 | 100 | 200 | 300 | 400 | 500 | 600 | 700 | 800 | 900 |
20Х | 42 | 42 | 41 | 40 | 38 | 36 | 33 | 32 | 31 | — |
Коэффициент линейного расширения
α*106, К-1, при температуре испытаний, °С20-100 | 20-200 | 20-300 | 20-400 | 20-500 | 20-600 | 20-700 | 20-800 | 20-900 | 20-1000 |
10,5 | 11,6 | 12,4 | 13,1 | 13,6 | 14,0 | — | — | — | — |
Удельная теплоемкость
c, Дж/(кг*К), при температуре испытаний, °С20-100 | 20-200 | 20-300 | 20-400 | 20-500 | 20-600 | 20-700 | 20-800 | 20-900 | 20-1000 |
496 | 508 | 525 | 537 | 567 | 588 | 626 | 706 | — | — |
Модуль нормальной упругости Е, ГПа, при температуре испытаний, °С
Сталь | 20 | 100 | 200 | 300 | 400 | 500 | 600 | 700 | 800 | 900 |
20Х | 216 | 213 | 198 | 193 | 181 | 171 | 165 | 143 | 133 | — |
Модуль упругости при сдвиге на кручением G, ГПа, при температуре испытаний °С
Сталь | 20 | 100 | 200 | 300 | 400 | 500 | 600 | 700 | 800 | 900 |
20Х | 84 | 83 | 76 | 74 | 71 | 67 | 62 | 55 | 50 | — |
1,7027, 20cr4, AISI 5120, 20H-сталь-хардинг.
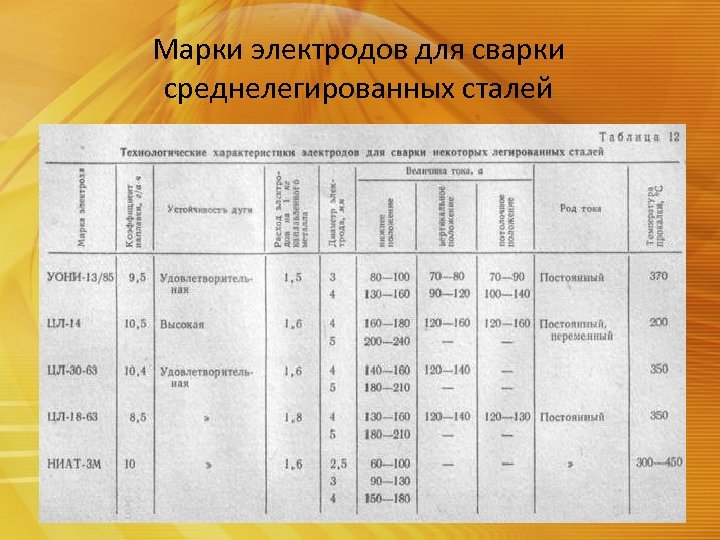

20H, 1.7027, 20Cr4, 5120, 20Ch – описание шпиндели, штифты, распределительные валы и втулки. Свариваемая, обрабатываемая и поддающаяся резке сталь.
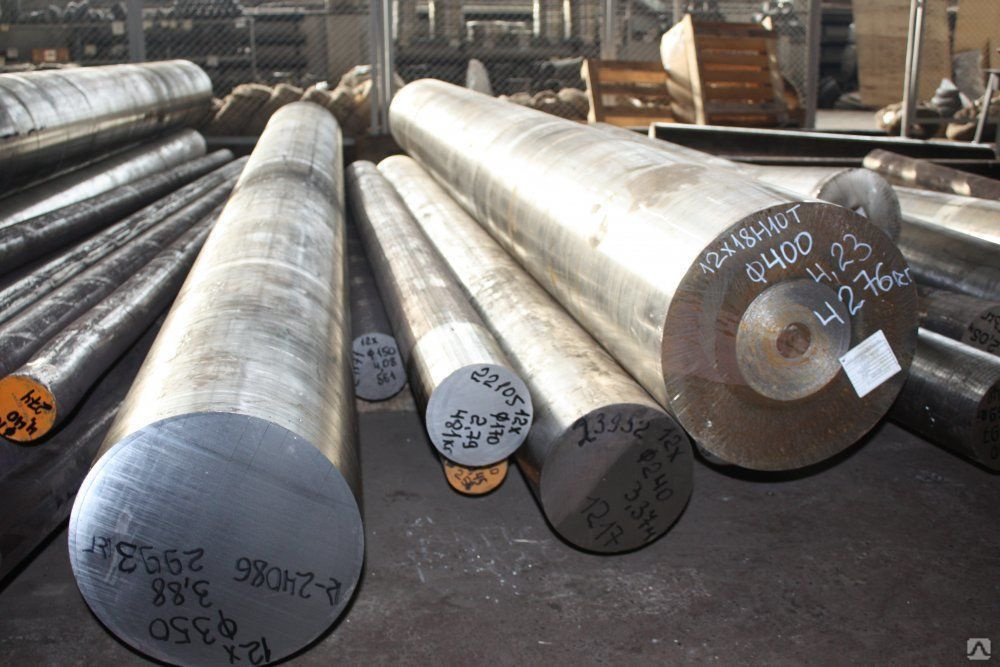
Физические и механические свойства
Здесь Вы можете найти механические свойства выбранных сплавов. Несмотря на сходство, они явно различаются.
Properties | Grade | ||||
---|---|---|---|---|---|
PN | ISO | GOST | ISO | ||
20H | 20Cr4 | 20Ch | 1.7027 | ||
Yield strength: | R m | > 640 МПа | > 850 МПа | > 637 МПа | – |
Прочность на разрыв: | R m | > 780 MPa | 820-1170 MPa | > 784 MPa | – |
Wydłużenie: | A 5 | 11 % | 9 % | 11 % | – |
Udarność KCU, 20°C: | KCU2 J/cm 2 | 60 J/cm 2 | KU: 25J/cm 2 | 59J/cm 2 | – |
Twardość po odprężaniu: | HB | < 179 HB | < 197 HB | < 179 HB | < 197 HB |
Механические свойства после закалки
- Диаметр D: 11 мм0006
- Удлинение A: мин 9 %
- Ударная стоимость Ku: min 25 J
- Прочность на растяжение RM: 750-1100 МПа
- Прочность урожая Re: Мин 490 МПа
- .
Мин 9 %
- Ударная стоимость Ku: Min 25 J
- Прочность на растяжение RM: 670-1020 МПа
- Устойчивая к выходу. Ударная вязкость КУ: мин. 25 Дж
Heat treatment and plastic working
Following parameters are recommended for working and heat treatment
Treatment | Grade | |||||||
---|---|---|---|---|---|---|---|---|
PN | ISO | GOST | ISO | |||||
20H | 20Cr4 | 20Ch | 1.7027 | |||||
Закалка | Temperature | 880℃ | 860-900℃ | 880℃ | 860-900℃ | |||
Cooling | oil, water | – | oil, water | – | ||||
Придерживание | Температура | 180 ℃ | 150-200 ℃ | 180 ℃ | 150-200.![]() | – | воздух, масло | – |
Мы доставляем этот стальной сплав AS:
- , полосы и оттенки 97777777777777779 29 29 29 29 29 29 29 29 29 29 29 29 29 29 279. , аналоги и др. обозначения:
- быстрая и бережная резка образцов
- быстрая установка с получением плоской поверхности
- быстрая и бережная шлифовка/полировка
20Х, 20Ч, 20Ч-Ш, 20Cr, 1.7027, 20Cr4, SCr22, SCr420, B21, 5120, C41201, 20Ch-PV
Металлографическая пробоподготовка термообработанных материалов
Термическая обработка, зародившаяся в бронзовом веке, получила дальнейшее развитие для обработки железа (кузнечное дело) около 800 г. до н.э., достигнув своего пика в производстве дамасской стали в начале 10 века н.э.
Железо было преобразовано в сталь путем добавления углерода, что придало сплаву новые свойства, такие как повышенная твердость. Было исследовано большое количество сплавов железа и различных элементов, что привело к разработке новых типов стали, подходящих для многих различных применений. Еще одним способом изменения свойств стали является термическая обработка, например отжиг. Поскольку время играет решающую роль в этом процессе, были разработаны диаграммы температура-время. На сегодняшний день многие диаграммы зависимости температуры от времени были оценены для производства лучшей стали для конкретного применения. Эти диаграммы показывают корреляцию между временем и теплом и соответствующей структурой (аустенит, мартенсит, бейнит) обработанной стали. Термическая обработка в основном производится в закалочных цехах. Материалы, обрабатываемые в закалочных установках, в основном одинаковы, и воспроизводимые, надежные и сопоставимые результаты являются обязательными. Для эффективного управления технологическим процессом необходимо протестировать большое количество образцов. Из-за такой высокой пропускной способности процесс пробоподготовки должен быть простым и быстрым.
Кроме того, подготовка должна привести к отличной плоскостности образца, чтобы обеспечить простой и безошибочный контроль поверхности.
Современный нож из дамасской стали
QATM предлагает продукцию для всех областей применения в области материалографии
Обзор продукцииСвяжитесь с нами!
Материалографический процесс подготовки
Как следствие всех этих требований, метод подготовки должен включать:
Использование станков для резки мокрым абразивом QATM дает преимущество быстрой и щадящей резки за счет выбора функции CareCut, которая снижает нагрев во время резки и поддерживает деформацию при низкой массе. Это облегчает последующую быструю подготовку образца с незначительной степенью деформации и отсутствием или минимальными структурными изменениями. Чтобы получить плоскую поверхность и высокое удержание кромки, наш модульный пресс для горячей запрессовки, использующий Epo black в качестве монтажной массы, отвечает требованиям высокой производительности, хорошего удержания кромки и плоской поверхности. Несколько методов шлифовки и полировки могут быть применены к образцам из промышленной области, и методы подготовки, обсуждаемые здесь, дадут обзор методов, используемых в этой области.
Метод 1
Этот метод хорошо зарекомендовал себя в течение длительного времени. Из-за твердости термообработанных образцов срок службы SiC Paper довольно короткий, что приводит к относительно высоким затратам на расходные материалы.
Подготовка следующая:
Шаг | Средний | Смазка/подвеска | Скорость (об/мин) | Держатель образца направления | Одинарная нагрузка (Н) | Время (мин) |
Шлифование | Карбид кремния, P180 | вода | 300 | По часовой стрелке | 30 | До самолета |
Шлифование | Карбид кремния, P320 | вода | 300 | По часовой стрелке | 30 | 1:00 |
Шлифовка | Карбид кремния, P600 | вода | 300 | По часовой стрелке | 30 | 1:00 |
Шлифование | Карбид кремния, P1200 | вода | 300 | По часовой стрелке | 30 | 1:00 |
Полировка | ИОТА | Диаметр полный, 3 | 150 | По часовой стрелке | 30 | 5:00 |
Способ 2
Плоское шлифование камнем обеспечивает быструю и экономичную подготовку. Но это требует вложений в специальную машину. Тем не менее, общее время подготовки сокращается, так как нет необходимости менять SiC-бумагу. Кроме того, можно использовать алмазные притирочные диски, которые имеют длительный срок службы.
Ступенька | Средний | Смазка/подвеска | Скорость (об/мин) | Держатель образца направления | Одинарная нагрузка (Н) | Время (мин) |
Шлифование | Камень, P100 | вода | фиксированный | По часовой стрелке | 30 | До самолета |
Предварительная полировка | Галакси Контеро H | Полный диаметр, 9 мкм | 150 | Против часовой стрелки | 30 | 4:00 |
Полировка | ИОТА | Полный диаметр, 3 мкм | 150 | По часовой стрелке | 30 | 4:00 |
Чтобы избежать инвестиций в новый станок, можно использовать алмазные шлифовальные круги для плоского шлифования, что дает преимущество использования стандартного шлифовального и полировального оборудования.
Метод 3
Шлифовальный круг Galaxy очень жесткий и позволяет получать ровные поверхности даже при изменении твердости поверхности образца.
Шаг | Средний | Смазка/подвеска | Скорость (об/мин) | Держатель образца направления | Одинарная нагрузка (Н) | Время (мин) |
Шлифование | Галактика красная | вода | 300 | По часовой стрелке | 30 | До самолета |
Предварительная полировка | Галакси Контеро H | Полный диаметр, 9 мкм | 150 | По часовой стрелке | 30 | 5:00 |
Полировка | ИОТА | Полный диаметр, 3 мкм | 150 | По часовой стрелке | 30 | 4:00 |
Феррит-перлит, травление 3% нитала, светлое поле 20x
Мартенитная структура после термообработки, травление 3% нитала, светлое поле 20x
Заключение
В закалочных цехах требования к подготовке образцов включают короткое время подготовки, высокую производительность, надежные результаты с хорошей плоскостностью образца для определения твердости или исследования поверхности.