Сталь 3 содержание углерода: Сталь марки Ст3: характеристики, применение
alexxlab | 22.03.1989 | 0 | Разное
Как отличить сталь 3 от 09г2с
Характеристики высокопрочной сталибез ограничений | сварка производится без подогрева и без последующей термообработки |
ограниченно свариваемая | сварка возможна при подогреве до 100-120 град. и последующей термообработке |
трудносвариваемая | для получения качественных сварных соединений требуются дополнительные операции: подогрев до 200-300 град. при сварке, термообработка после сварки – отжиг |
Марки высокопрочной стали
Сталь является одним из самых важных материалов, который используется практически во всех отраслях промышленности. К высокопрочной стали (в зависимости от области применения) предъявляют различные требования. Марки сталей отличаются по структуре, химическому составу и по своим свойствам (физическим и механическим).
Сталью называют деформируемый сплав железа с углеводом (не более 2 процентов) и примесями других элементов: марганца, кремния, фосфора.
Сталь 20
Сталь конструкционная углеродистая качественная
трубы перегревателей, коллекторов и трубопроводов котлов высокого давления, листы для штампованных деталей, цементуемые детали для длительной и весьма длительной службы при температурах от -40 до 350 град.
СТАЛЬ МАРКИ 3
Углеродистая сталь обычного качества.
Именно такая сталь пользуются наибольшим спросом в строительстве. Причина такой популярности – технологичность, прочность и привлекательная цена. Еще одно преимущество этого сплава – возможность изготавливать из нее изделия, которые выдерживают большую нагрузку и обладают хорошей сопротивляемостью ударам.
Сталь 3 производят по ГОСТ 380-94, согласно ему сталь маркируются буквами «Ст» с порядковым номером от 0 до 6. Чем выше этот номер, тем большее количество углерода содержится в стали. А значит, лучше прочность, но при этом хуже пластические характеристики. Сталь 3 хорошо сваривается, нефлокеночувствительна, не склонна к отпускной хрупкости. Сталь 3 содержит: углерод – 0,14-0,22%, кремний – 0,05-0,17%, марганец – 0,4-0,65%, никель, медь, хром – не более 0,3% , мышьяк не более 0,08%, серы и фосфора – до 0,05 и 0,04%. Количество этих компонентов в сплаве Ст3 не допускается выше указанных значений.
Основа стали – феррит. Его характеристики не позволяют использовать его в чистом виде. Для улучшения показателя прочности феррита сталь насыщают углеродом, добавляют (легируют) хром, никель, кремний, марганец и проводят дополнительное термическое упрочнение.
Сталь 3 выдерживает широкий температурный диапазон при переменных нагрузках. Хорошо сваривается, штампуется в холодном и горячем состоянии, подвергается вытяжке. Применяется без термической обработки.
Свариваемость стали 3
Без ограничений – сварка производится без подогрева и без последующей термообработки. В стали, относящейся к хорошей, содержание углерода составляет менее 0,25%. Они свариваются без образования закалочных структур и трещин в широком диапазоне режимов сварки.
Температура применения
Температура применения стали 3
Минимальная температура применения (температура наиболее холодной пятидневки региона) – минус 30.
Максимальная температура применения – плюс 300.
Качественная среднеуглеродистая сталь.
Такой вид стали применяют для деталей, которые требуют высокой пластичности и сопротивления удару. Качественные углеродистые стали типа 35 изготавливают по ГОСТ 1050-88 и маркируют двухзначными цифрами, которые указывают среднее содержание углерода в сотых долях процента. Например, сталь 35 (0,35 %). Она обладает высокой прочностью (σв = 640…730 МПа, σ0,2 = 380…430 МПа) и относительно низкой пластичностью (δ = 9…14 %, ψ = 40…50 %). Кроме того, этот тип стали не восприимчив к средним напряжениям, обладает стойкостью к деформации и износостойкостью, не подвержен образованию трещин и коррозии. Поэтому именно сталь 35 используют при производстве высокопрочного крепежа и фланцевых соединений. Температурный диапазон: от -40 до +450 градусов Цельсия
Сталь 35 сваривается ограниченно. Способы сварки РДС, АДС под флюсом и газовой защитой, ЭШС. Рекомендуем подогрев и последующую термообработку. КТС без ограничений.
Свариваемость стали 35
Сталь конструкционной марки 35 сваривается ограниченно. С увеличением углерода в стали зона термического влияния и шов закаливаются, увеличивается твердость, сварные соединения становятся более хрупкими и склонными к образованию трещин.
Удовлетворительные стали имеют содержание углерода от 0,25 до 0,35%. Они мало склонны к образованию трещин и при правильных режимах сварки получается качественный шов. Для улучшения качества сварки часто применяют подогрев.
Температура применения стали 35
Минимальная температура применения (температура наиболее холодной пятидневки региона) – минус 40.
Максимальная температура применения – плюс 425.
Сталь легированная, хромистая
Крепежные изделия из стали 35Х обладают высокой конструктивной прочностью, гарантируют надежность конструкции. Кроме того, сталь 35Х хорошо сопротивляется ударным нагрузкам, обладает большим запасом вязкости и высоким сопротивлением усталости. Также, сталь 35Х имеет высокое сопротивление износу, коррозии, трещинам и другим дефектам.
Главное преимущество крепежа из легированной конструкционной стали 35Х перед углеродистыми – это более высокая прочность за счет упрочнения феррита и большей прокаливаемости, меньший рост аустенитного зерна при нагреве и повышенная ударная вязкость. А уровень механических свойств повышен за счет термической обработки.
Свариваемость стали 35x
Температура применения стали 35х
Минимальная температура применения (температура наиболее холодной пятидневки региона) – минус 40.
Максимальная температура применения – плюс 425.
Сталь конструкционная легированная.
Сталь марки 40Х содержит 0,40% углерода и менее 1,5% хрома. Эта сталь довольно трудносвариваема. Поэтому, чтобы получить качественное сварное соединение, необходимы дополнительные операции. При сварке потребуется подогрев до 200-300 градусов, а потом – термообработка путем отжига.
Благодаря добавлению хрома, крепежные изделия из ст.40Х обладают твердостью, прочностью, жаропрочностью и устойчивостью к коррозии. Сталь 40Х рассчитана на значительные нагрузки. Механические свойства стали 40х: предел кратковременной прочности – 570 – 940 МПа, предел пропорциональности – 320 – 800 МПа, относительное удлинение – 13 – 17%, относительное сужение – 35 – 55%, ударная вязкость – 400 – 850 кДж/кв.м.
Плюсы этой марки стали: устойчивость к действию высоких и низких температур и их резким перепадам, могут использоваться под открытым небом и даже в агрессивных, влажных средах. Еще одно неоспоримое преимущество крепежных изделий именно из этой марки стали – это отсутствие необходимости обрабатывать и очищать поверхность.
Свариваемость стали 40x
Ограниченно свариваемая. Рекомендуется подогрев и последующая термообработка.
Температура применения стали 40х
Минимальная температура применения (температура наиболее холодной пятидневки региона) – минус 40.
Максимальная температура применения – плюс 425.
Сталь марки 45 обладает высокой стойкостью и прочностью. Сталь 45 применяют при изготовлении деталей механизмов, используемых при повышенных нагрузках и требующих сопротивления (ударам, трению). Механические свойства этой стали позволяют ей выдерживать значительные перепады температур и другие неблагоприятные климатические воздействия. Эта сталь способна выдержать температурные испытания от 200 до 600 градусов по Цельсию.
При использовании ст. 45 следует помнить, что:
• прочность снижается при нагревании до 200 0С;
• сталь является трудносвариваемой и характеризуется низкой флонекочувствительностью.
Сталь марки 45 — среднеуглеродистая; идеально подходит для изготовления деталей, требующих высокой прочности или высокой поверхностной твердости, а также деталей средненагруженных и не подвергающихся в работе истиранию.
Свариваемость стали 45
Высокоуглеродистую сталь марки 45 рекомендуют соединять контактной сваркой. Ограниченно свариваемые стали имеют содержание углерода от 0,36 до 0,45% и склонны к образованию трещин. Сварка требует обязательного подогрева. При их сварке требуются специальные технологические процессы.
Температура применения стали 45
Минимальная температура применения (температура наиболее холодной пятидневки региона) – минус 40.
Максимальная температура применения – плюс 425.
Сталь конструкционная низколегированная.
Обозначение 09Г2С указывает, что в стали присутствует 0,09% углерода, буква «Г» означает марганец, а цифра 2 – процентное содержание до 2% марганца. Буква «С» означает кремний, содержание кремния менее 1%.
Главное преимущество этой стали – высокая механическая прочность, которая позволяет применять более тонкие детали по сравнению с деталями, изготовленными из других сталей. А значит, детали из стали 09Г2С имеют меньший вес, что экономически более выгодно. Кроме того, еще один плюс этой стали – низкая склонность к отпускной хрупкости.
Свариваемость стали 09г2с
Марка стали 09Г2С широко используется для сварных конструкций. Сварка может производиться как без подогрева, так и с предварительным подогревом до 100-120 градусов по Цельсию. Сварка довольно проста, причем сталь не закаливается и не перегревается в процессе сварки, благодаря чему не происходит снижение пластических свойств или увеличение ее зернистости. При температуре воздуха минус 15 °С и ниже применяют предварительный местный подогрев независимо от толщины стали.
Температура применения стали 09г2с
Минимальная температура применения (температура наиболее холодной пятидневки региона) – минус 70.
Максимальная температура применения – плюс 450.
Сталь. Виды и марки стали. Их применение.
Сталь – это сплав железа и углерода с другими элементами, содержание углерода в нём не более 2,14%.
Наиболее общая характеристика – по химическому составу сталь различают:
углеродистую сталь (Fe – железо, C – углерод, Mn – марганец, Si — кремний, S – сера, P – фосфор). По содержанию углерода делится на низкоуглеродистую, среднеуглеродистую и высокоуглеродистую. Углеродистая сталь предназначена для статически нагруженного инструмента.
легированную сталь – добавляются легирующие элементы: азот, бор, алюминий, углерод, фосфор, кобальт, кремний, ванадий, медь, молибден, марганец, титан, цирконий, хром, вольфрам, никель, ниобий.
По способу производства и содержанию примесей сталь различается:
сталь обыкновенного качества ( углерода менее 0,6%) – соответствует ГОСТ 14637, ГОСТ 380-94. Ст0, Ст1, Ст2, Ст3, Ст4, Ст5,Ст6. Буквы «Ст» обозначают сталь обыкновенного качества, цифры указывают на номер маркировки в зависимости от механических свойств. Является наиболее дешёвой сталью, но уступает по другим качествам.
качественная сталь ( углеродистая или легированная ) – ГОСТ 1577, содержание углерода обозначается в сотых долях % – 08, 10, 25, 40, дополнительно может указываться степень раскисления и характер затвердевания. Качественная углеродистая сталь обладает высокой пластичностью и повышенной свариваемостью.
Низкоуглеродистые качественные конструкционные стали характеризуются невысокой прочностью и высокой пластичностью. Из листового проката стали 08, 10, 08кп изготавливают детали для холодной штамповки. Из сталей 15, 20 делают болты, винты, гайки, оси, крюки,шпильки и другие детали неответственного назначения.
Среднеуглеродистые качественные стали (ст 30, 35, 40, 45, 50, 55) используют после нормализации и поверхностной закалки для изготовления таких деталей, которые обладают высокой прочностью и вязкостью сердцевины (оси, винты, втулки и т. д.)
Стали 60 — стали 85 обладают высокой прочностью, износостойкостью, упругими свойствами. Из них изготавливают крановые колёса, прокатные валки, клапаны компрессоров, пружины, рессоры и т.д.
высококачественная — сложный химический состав с пониженным содержанием фосфора и серы — по ГОСТу 19281.
Также сталь делится по применению :
а) строительная сталь — углеродистая обыкновенного качества. Обладает отличной свариваемостью. Цифра обозначает условный номер состава стали по ГОСТу. Чем больше условный номер, тем больше содержание углерода, тем выше прочность стали и ниже пластичность.
Ст0-3 — для вторичных элементов конструкций и неответственных деталей (настилы, перила, подкладка,шайбы)
Ст3 используют для несущих и ненесущих элементов сварных и несварных конструкций и деталей, которые работают при положительных температурах. ГОСТ 380-88.
Стандартом качества предусмотрена сталь с повышенным количеством марганца (Ст3Гсп/пс, ст5Гсп/пс).
б) конструкционная сталь — ГОСТ 1050
Углеродистые качественные конструкционные стали используются в машиностроении, для сварных, болтовых конструкций, для кровельных работ, для изготовления рельсов, железнодорожных колёс, валов, шестерен и других деталей грузоподъёмников.
Ст20 — малонагруженные детали, такие как валики, копиры, упоры,
Ст35 — испытывающие небольшие напряжения (оси, тяги, рычаги, диски, траверсы, валы),
Ст45 (ст40Х) — требующие повышенной прочности (валы, муфты, оси, зубчатые рейки)
Конструкционные легированные стали используют для гусениц тракторов, изготовления пружин, рессор, осей, валов, автомобильных деталей, деталей турбин и др.
в) инструментальная сталь — применяется для режущего инструмента, быстрорежущая сталь для холодного и горячего деформирования материла, для измерительных инструментов, на производство молотков, долот, стамесок, резцов, свёрлов, напильников, бритв, рашпилей.
У7, У8А (цифра- десятые доли процента по содержанию углерода). Углеродистые стали выпускают качественными и высококачественными. Буква «А» означает высококачественную углеродистую инструментальную сталь.г) легированная сталь — универсальная сталь, содержащая специальную примесь. Содержание кремния более 0,5%, марганца более 1%. ГОСТ 19281-89. Если содержание легирующего элемента превышает 1 – 1,5%, то оно указывается цифрой после соответствующей буквы.
низколегированная сталь — где легирующих элементов до 2,5% (09Г2С, 10ХСНД, 18ХГТ). Низколегированную сталь можно использовать в условиях крайнего севера, от -70 град С. Низколегированную сталь отличает большая прочность за счёт более высокого предела текучести,что важно для ответственных конструкций.
среднелегированная (2,5 -10%),
высоколегированная (от 10 до 50%)
Сталь 09Г2С применяется для паровых котлов, аппаратов и ёмкостей, работающих под давлением и температурой от минус 70, до плюс 450град; её используют для ответственных листовых сварных конструкций в химическом и нефтяном машиностроении, судостроении.
Сталь 10ХСНД используют для сварных конструкций химического машиностроения, фасонных профилей в сдостроении, вагоностроении.
18ХГТ применяют для деталей, работающих на больших скоростях при высоком давлении и ударных нагрузках.
д) сталь особого назначения — сталь с особыми физическими свойствами. Она применяется в электротехничсеской промышленности и точном судостроении.
На свариваемость стали влияет степень её раскисления. По степени раскисления сталь классифицируется:
спокойная сталь (ст3сп) — полностью раскисляется с минимальным содержанием шлаком и неметаллических примесей,
полуспокойная сталь (ст3пс) — по характеристикам качества схожа со спокойной сталью,
кипящая сталь (08кп) — неокисленная сталь с высоким содержанием неметаллических примесей. ГОСТ 1577.
В зависимости от нормируемых характеристик , сталь подразделяют на категории: 1, 2, 3, 4, 5. Категории обозначают химический состав, механические свойства при растяжении, ударную вязкость)
Например, категория 1 — химический состав не нормируемый, категория 3 — нормируется ударная вязкость при температуре +20. Для марки ст0 не нормируется ни химический состав, ни предел текучести.
Марка стали С245 – Ст3пс5
Марка стали С255 — Ст3сп5
Марка стали С235 — Ст3кп2
Марка стали С345 – 09Г2С
© 2001-2019 АО Металлоторг, Все права защищены
металлопрокат, катанка, оцинковка, листы хк, гк, листы оцинкованные холоднокатаные, профильные трубы
Металлоторг – продажа металлопроката
Рекомендованные сообщения
Создайте аккаунт или войдите в него для комментирования
Вы должны быть пользователем, чтобы оставить комментарий
Создать аккаунт
Зарегистрируйтесь для получения аккаунта. Это просто!
Войти
Уже зарегистрированы? Войдите здесь.
Сейчас на странице 0 пользователей
Нет пользователей, просматривающих эту страницу.
Углеродистая сталь: состав, свойства, применение, ГОСТ
- Что собой представляют углеродистые стали
- Классификация по степени раскисления
- Методы производства и разделение по качеству
- Область применения
- Особенности маркировки
Углеродистая сталь благодаря доступной стоимости и высоким прочностным характеристикам относится к широко распространенным сплавам. Из таких сталей, состоящих из железа и углерода и минимума других примесей, изготавливают различную машиностроительную продукцию, детали колов и трубопроводов, инструменты. Широкое применение эти сплавы находят и в строительной сфере.
Калиброванный круг из углеродистой стали чаще всего используется в судостроении и машиностроении
Что собой представляют углеродистые стали
Углеродистые стали, которые в зависимости от основной сферы применения подразделяются на конструкционные и инструментальные, практически не содержат в своем составе легирующих добавок. От обычных стальных сплавов эти стали также отличает и то, что в их составе содержится значительно меньшее количество таких базовых примесей, как марганец, магний и кремний.
Содержание основного элемента – углерода – в сталях данной категории может варьироваться в достаточно широких пределах. Так, высокоуглеродистая сталь содержит в своем составе 0,6–2% углерода, среднеуглеродистые стали – 0,3–0,6%, низкоуглеродистые – до 0,25%. Данный элемент определяет не только свойства углеродистых сталей, но и их структуру. Так, внутренняя структура стальных сплавов, содержащих в своем составе менее 0,8% углерода, состоит преимущественно из феррита и перлита, при увеличении концентрации углерода начинает формироваться вторичный цементит.
Нормы содержания химических элементов в углеродистых сталях
Углеродистые стали с преобладающей ферритной структурой отличаются высокой пластичностью и низкой прочностью. Если же в структуре стали преобладает цементит, то она характеризуется высокой прочностью, но вместе с этим является и очень хрупкой.
Количественное содержание углерода также оказывает серьезное влияние на технологические характеристики металла, в частности на его свариваемость, легкость обработки давлением и резанием. Из сталей, относящихся к категории низкоуглеродистых, изготавливают детали и конструкции, которые не будут подвергаться значительным нагрузкам в процессе эксплуатации. Характеристики, которыми обладают среднеуглеродистые стали, делают их основным конструкционным материалом, используемым в производстве конструкций и деталей для нужд общего и транспортного машиностроения. Высокоуглеродистые стальные сплавы благодаря своим характеристикам оптимально подходят для изготовления деталей, к которым предъявляются повышенные требования по износостойкости, для производства ударно-штампового и измерительного инструмента.
Химический состав углеродистых сталей обыкновенного качества
Углеродистая сталь, как и стальной сплав любой другой категории, содержит в своем составе различные примеси: кремний, марганец, фосфор, серу, азот, кислород и водород. Часть этих примесей, такие как марганец и кремний, являются полезными, их вводят в состав стали на стадии ее выплавки для того, чтобы обеспечить ее раскисление. Сера и фосфор – это вредные примеси, которые ухудшают качественные характеристики стального сплава.
Хотя считается, что углеродистые и легированные стали несовместимы, для улучшения их физико-механических и технологических характеристик может выполняться микролегирование. Для этого в углеродистую сталь вводятся различные добавки: бор, титан, цирконий, редкоземельные элементы. Конечно, при помощи таких добавок не получится сделать из углеродистой стали нержавейку, но заметно улучшить свойства металла они вполне могут.
Классификация по степени раскисления
На разделение углеродистых сталей на различные типы оказывает влияние в том числе такой параметр, как степень раскисления. В зависимости от данного параметра углеродистые стальные сплавы делятся на спокойные, полуспокойные и кипящие.
Более однородной внутренней структурой отличаются спокойные стали, раскисление которых осуществляют, добавляя в расплавленный металл ферросилиций, ферромарганец и алюминий. За счет того, что сплавы данной категории были полностью раскислены в печи, в их составе не содержится закиси железа. Остаточный алюминий, который препятствует росту зерна, наделяет такие стали мелкозернистой структурой. Сочетание мелкозернистой структуры и практически полное отсутствие растворенных газов позволяет формировать качественный металл, из которого можно изготавливать наиболее ответственные детали и конструкции. Наряду со всеми своими достоинствами углеродистые стальные сплавы спокойной категории имеют и один существенный недостаток – их выплавка обходится достаточно дорого.
Строение стального слитка зависит от степени раскисленности стали
Более дешевыми, но и менее качественными являются кипящие углеродистые сплавы, при выплавке которых используется минимальное количество специальных добавок. Во внутренней структуре такой стали из-за того, что процесс ее раскисления в печи не был доведен до конца, присутствуют растворенные газы, которые негативно отражаются на характеристиках металла. Так, азот, содержащийся в составе таких сталей, плохо влияет на их свариваемость, провоцируя образование трещин в области сварного шва. Развитая ликвация в структуре этих стальных сплавов приводит к тому, что металлический прокат, который из них изготовлен, имеет неоднородность как по своей структуре, так и по механическим характеристикам.
Промежуточное положение и по своим свойствам, и по степени раскисления занимают полуспокойные стали. Перед заливкой в изложницы в их состав вводят небольшое количество раскислитилей, благодаря чему металл затвердевает практически без кипения, но процесс выделения газов в нем продолжается. В итоге формируется отливка, в структуре которой содержится меньше газовых пузырей, чем в кипящих сталях. Такие внутренние поры в процессе последующей прокатки металла практически полностью завариваются. Большая часть полуспокойных углеродистых сталей используется в качестве конструкционных материалов.
Ознакомиться со всеми требованиями ГОСТ к углеродистой стали можно, скачав данный документ в формате pdf по ссылке ниже.
Скачать ГОСТ 380-2005 Сталь углеродистая обыкновенного качества. Марки
Скачать
Методы производства и разделение по качеству
Для производства углеродистых сталей используются различные технологии, что сказывается на их разделении не только по способу производства, но и по качественным характеристикам. Так, различают:
- высококачественные стальные сплавы;
- качественные углеродистые стали;
- углеродистые стальные сплавы обыкновенного качества.
Классификация углеродистых сталей
Стальные сплавы, обладающие обыкновенным качеством, выплавляются в мартеновских печах, после чего из них формируют слитки больших размеров. К плавильному оборудованию, которое используется для получения таких сталей, относятся также кислородные конвертеры. По сравнению с качественными стальными сплавами, рассматриваемые стали могут иметь большее содержание вредных примесей, что сказывается на стоимости их производства, а также на их характеристиках.
Сформированные и полностью застывшие слитки металла подвергают дальнейшей прокатке, которая может выполняться в горячем или холодном состоянии. Методом горячей прокатки производят фасонные и сортовые изделия, толстолистовой и тонколистовой металл, металлические полосы большой ширины. При помощи прокатки, выполняемой в холодном состоянии, получают тонколистовой металл.
На современных предприятиях для производства высококачественных сплавов используются электрические дуговые печи
Для производства углеродистых сталей качественной и высококачественной категорий могут использоваться как конвертеры и мартеновские печи, так и более современное оборудование – плавильные печи, работающие на электричестве. К химическому составу таких сталей, наличию в их структуре вредных и неметаллических примесей соответствующий ГОСТ предъявляет очень жесткие требования. Например, в сталях, которые относятся к категории высококачественных, должно содержаться не более 0,04% серы и не больше 0,035% фосфора. Качественные и высококачественные стальные сплавы благодаря строгим требованиям к способу их производства и к характеристикам отличаются повышенной чистотой структуры.
Область применения
Как уже говорилось выше, углеродистые стальные сплавы по основному назначению делят на две большие категории: инструментальные и конструкционные. Инструментальные стальные сплавы, содержащие 0,65–1,32% углерода, используются в полном соответствии со своим названием – для производства инструмента различного назначения. Для того чтобы улучшить механические свойства инструментов, обращаются к такой технологической операции, как закалка углеродистой стали, которая выполняется без особых сложностей.
Сферы применения углеродистых инструментальных сталей
Конструкционные стальные сплавы применяются в современной промышленности очень широко. Из них делают детали для оборудования различного назначения, элементы конструкций машиностроительного и строительного назначения, крепежные детали и многое другое. В частности, такое популярное изделие, как проволока углеродистая, производится именно из стали конструкционного типа.
Используется проволока углеродистая не только в бытовых целях, для производства крепежа и в строительной сфере, но и для изготовления таких ответственных деталей, как пружины. После выполнения цементации конструкционные углеродистые сплавы можно успешно использовать для производства деталей, которые в процессе эксплуатации подвергаются серьезному поверхностному износу и испытывают значительные динамические нагрузки.
Конечно, углеродистые стальные сплавы не обладают многими свойствами легированных сталей (в частности, той же нержавейки), но их характеристик вполне хватает для того, чтобы обеспечить качество и надежность деталей и конструкций, которые из них изготавливаются.
Особенности маркировки
Маркировка углеродистых сталей, правила составления которой строго оговорены пунктами соответствующего ГОСТа, позволяет узнать не только химический состав представленного сплава, но и то, к какой категории он относится. В обозначении углеродистой стали, обладающей обыкновенным качеством, присутствуют буквы «СТ». Пунктами ГОСТа оговаривается семь условных номеров марок таких сталей (от 0 до 6), которые также указываются в их обозначении. Узнать, какой степени раскисления соответствует та или иная марка, можно по буквам «кп», «пс», «сп», которые проставляются в самом конце маркировки.
Цветовая маркировка наносится по требованию потребителя несмываемой краской
Марки углеродистых сталей по ГОСТу и по международным стандартам ИСО
Марки качественных и высококачественных углеродистых сталей обозначаются просто цифрами, указывающими на содержание в сплаве углерода в сотых долях процента. В конце обозначения некоторых марок можно встретить букву «А». Это значит, что сталь обладает улучшенным металлургическим качеством.
Узнать о том, что перед вами инструментальная сталь, можно по букве «У», стоящей в самом начале ее маркировки. Цифра, следующая за такой буквой, указывает на содержание углерода, но уже в десятых долях процента. Буква «А», если она есть в обозначении инструментальной стали, говорит о том, что данный сплав отличается улучшенными качественными характеристиками.
#TITLE# || KOBELCO – KOBE STEEL, LTD. –
Следующая страница
1. Введение
В состав стали, помимо углерода С входит кремний Si, марганец Mn, фосфор Р и сера S. Эти пять элементов называют пятью химическими компонентами стали. Сталь, содержащая 0,3% и менее углерода, называется низкоуглеродистой или мягкой сталью. Сталь, содержащая 0,6% и более углерода, называется высокоуглеродистой сталью. К этому типу относится, например, углеродистая инструментальная сталь. Сталь с содержанием углерода от 0,3% до 0,6% называется среднеуглеродистой сталью. К ней относится машиностроительная сталь. Специальные стали, в состав которых входят те же пять элементов, отличаются от углеродистых сталей более высоким содержанием марганца Mn, кроме того, в зависимости от назначения, в них добавляются такие легирующие элементы, как никель Ni, хром Cr и молибден Mo.
Согласно стандарту JIS, сталь и чугун классифицируются, как показано в Таблице 1, где сталь разделена на нелегированную, специальную и стальную отливку. Специальная сталь, в свою очередь, подразделяется на высокопрочную, инструментальную и сталь специального назначения. Типичные классы прочности среднеуглеродистых и специальных сталей представлены в Таблицах 2~3. В этих таблицах указаны классы прочности AISI/SAE и спецификации ASTM, которые схожи с классами прочности стали по стандарту JIS.
1-я классификация | 2-я классификация | 3-я классификация | Типичные классы JIS (ASTM/AISI/SAE)*1 |
---|---|---|---|
Чугун и сталь | Нелегированная сталь | Стали для строительных сооружений и сосудов под давлением | JIS G3101 : SS, JIS G3103 : SB, JIS G3104 : SV, JIS G3106 : SM (ASTM A36, A204, A285, A31, A283, A529) |
Специальные стали | Углеродистые / легированные стали для строительных сооружений | JIS G4051 : S××C, JIS G4053 : SCr, SMn, SMnC, SCM, SNC, SNCM, JIS G4202 : SACM, JIS G3119 : SBV, JIS G3120 : SQV (AISI/SAE : 1010~1060, 5120~5140, 1522~1541, 4130~4147, 8615~8640, 4320~4340, ASTM A302, A387, A533, A734) | |
Инструментальные стали | JIS G4401 : SK, JIS G4404 : SKS, SKD, SKT, JIS G4403 : SKH (AISI/ASTM : W1−11~1−8, F2, L6, W2, D3~H 19, T1~M42) | ||
Стали специального назначения | JIS G4303~4321 : SUS, SUH, JIS G4805 :
SUJ, JIS G4801 : SUP, JIS G4804 : SUM (AISI : 201~444, 309~446, 52100, 9260~4161, 1212~1144, etc. ![]() | ||
Стальная отливка | Отливка из углеродистой / легированной стали | JIS G5101 : SC, JIS G5102 : SCW (ASTM A27, A216) | |
Отливка из углеродистой / легированной стали для строительных сооружений | JIS G5111 : SCC, SCMn, SCSiMn, SCMnCr,
SCMnM, SCCrM, SCMnCrM, SCNCrM (ASTM A148) | ||
Стальная отливка специального назначения | JIS G5121 : SCS, JIS G5122 : SCH, JIS G5131 : SCMnH (ASTM A743, A744, A351, A297, A447, A608, A128) | ||
Стальная поковка | Поковка из углеродистой стали | JIS G3201 : SF (ASTM A105, A668) | |
Поковка из углеродистой / легированной стали для строительных сооружений | JIS G3203 : SFVA, JIS G3202 : SFVC, JIS G3204 : SFVQ (ASTM A182, A336, A105, A181, A266, A508, A541) | ||
Чугунная отливка | Отливка из серого чугуна | JIS G5501 : FC (-) | |
Отливка из чугуна со сфероидальным графитом | JIS G5502 : FCD (ASTM A536) | ||
Отливка из ковкого чугуна | JIS G5705 : FCMB, FCMW, FCMP (-) | ||
(Примечание) *1.![]() |
2. Основные факторы, которые необходимо учитывать при выборе сварочных материалов
Прежде всего здесь описаны факторы, которые необходимо учитывать при выборе сварочных материалов. Затем речь пойдет о механизме образования трещин и способах их предотвращения. Во-первых, сварочные материалы с высоким содержание диффузного водорода в сварочном металле (такие как электроды ильменитного типа и известково-титановые электроды), никогда не должны применяться для сварки среднеуглеродистых и высокоуглеродистых сталей, а также специальных сталей. Для таких сталей обязательно следует применять сварочные материалы низкоуглеродистого типа.
Во-вторых, должна учитываться прочность сварочного металла. Среднеуглеродистая и высокоуглеродистая сталь в целом может быть охарактеризована как высокопрочная, ее разрывная прочность зачастую превышает 1000 MPa. При сварке такой высокопрочной стали существует два подхода к выбору сварочных материалов. Один подход отдает приоритет прочности сварочного металла и рекомендует применять такой сварочный материал, которых позволит получить сварочный металл с прочностью, близкой к прочности основного металла. Второй подход отдает приоритет не прочности сварочного металла, а его устойчивости к образованию трещин.
В общем можно сказать, что при прочих одинаковых условиях, устойчивость к образованию трещин в сварном соединении повышается по мере того, как понижается его прочность. Другими словами, чем выше прочность сварочного металла, тем больше риск образования в нем трещин.
Поэтому при выборе сварочных материалов необходимо тщательно изучить вопрос о том, насколько прочность сварочного металла должна быть близка к прочности основного металла. Следует по возможности выбирать сварочные материалы с меньшей прочностью, чтобы снизить риск образования трещин.
В таблице рекомендуемых сварочных материалов дается две рекомендации: для случаев, когда требуется простое соединение деталей, и для случаев, когда сварочный металл должен обладать прочностью, близкой к прочности основного металла.
Хотя в таблице рекомендуемых сварочных материалов это не отмечено, в некоторых случаях рекомендуется использовать сварочные материалы из аустенитной нержавеющей стали марки 309 для сварки среднеуглеродистых и высокоуглеродистых сталей.
Эта рекомендация основана на том, что часто причиной образования трещин в сварном соединении среднеуглеродистой и высокоуглеродистой стали является затвердевание околошовной зоны и диффузный водород в сварочном металле. Конечно, затвердевание околошовной зоны возможно и при использовании сварочных материалов из аустенитной нержавеющей стали. Но отсутствие диффузного водорода в сварочном металле, как считается, повышает устойчивость к образованию трещин наряду со стабильной структурой сварочного металла.
Таким образом, когда невозможно применить предварительный подогрев, а также тогда, когда не стоит проблема термической усталости из-за разницы в термическом коэффициенте расширения, могут быть использованы сварочные материалы из аустенитной нержавеющей стали.
3.Факторы, которые должны быть учтены в отношении соединений разнородных металлов4.Сварные соединения
Верх страницы
Влияние углерода на развитие микроструктуры и твердость нержавеющей стали Fe–13Cr–xC (x = 0–0,7 мас.%)
1. Дюран-Шарр М. Микроструктура сталей и чугунов. Спрингер; Берлин, Германия: 2004. [Google Scholar]
2. Дэвис Дж. Р. Нержавеющая сталь. 2-е изд. АСМ Интернэшнл; Materials Park, OH, USA: 1996. [Google Scholar]
3. Ahmad Z. Principles of Corrosion Engineering and Corrosion Control. 1-е изд. Баттерворт-Хайнеманн; Оксфорд, Великобритания: 2006. [Google Scholar] 9.0003
4. Hougardy H.P., Yamazaki K. Усовершенствованный расчет превращения сталей. Сталь Рез. 1986; 57: 466–471. doi: 10.1002/srin.198600805. [CrossRef] [Google Scholar]
5. Цутияма Т., Тобата Дж., Тао Т., Накада Н., Такаки С. Закалка и разделение низкоуглеродистой мартенситной нержавеющей стали. Матер. науч. англ. А. 2012; 532: 585–592. doi: 10. 1016/j.msea.2011.10.125. [CrossRef] [Google Scholar]
6. Харварт М., Чен Г., Рахими Р., Бирманн Х., Заргаран А., Даффи М., Зупан М., Мола Дж. Легкие нержавеющие стали из алюминиевого сплава, упрочненные B2-(Ni,Fe)Al выпадает в осадок. Матер. Дес. 2021;206:109813. doi: 10.1016/j.matdes.2021.109813. [CrossRef] [Google Scholar]
7. Akhiate A., Braud E., Thibault D., Brochu M. Влияние содержания углерода и термической обработки на микроструктуру и механические свойства мартенситной нержавеющей стали 13%Cr-4%Ni. В: Дэвис Б., редактор. Материалы COM 2014, 53-я ежегодная конференция металлургов; Ванкувер, Британская Колумбия, Канада. 28 сентября – 1 октября 2014 г.; Вестмаунт, Квебек, Канада: Канадский институт горной металлургии и нефти; 2014. [Google Академия]
8. Shen Y.F., Dong X.X., Song X.T., Jia N. Мартенситное превращение в зависимости от содержания углерода в низколегированных TRIP-сталях. науч. Отчет 2019; 9:7559. doi: 10.1038/s41598-019-44105-6. [PMC free article] [PubMed] [CrossRef] [Google Scholar]
9. Суутала Н. Влияние условий затвердевания на режим затвердевания аустенитных нержавеющих сталей. Металл. Транс. А. 1983; 14: 191–197. doi: 10.1007/BF02651615. [CrossRef] [Google Scholar]
10. Ахаван Табатабае Б., Ашрафизаде Ф., Хасанлы А.М. Влияние остаточного аустенита на механические свойства отливок из низкоуглеродистой мартенситной нержавеющей стали. ISIJ Междунар. 2011;51:471–475. doi: 10.2355/isijinternational.51.471. [Перекрестная ссылка] [Академия Google]
11. Амуда М., Акинлаби Э.Т., Мридха С. Справочный модуль по материаловедению и материаловедению. Эльзевир; Амстердам, Нидерланды: 2016. Ферритные нержавеющие стали: металлургия, применение и свариваемость. [Google Scholar]
12. Liu J.H., Binot N., Delagnes D., Jahazi M. Влияние скорости охлаждения ниже Ms на мартенситное превращение в низколегированной среднеуглеродистой стали. Дж. Матер. Рез. Технол. 2021; 12: 234–242. doi: 10.1016/j.jmrt.2021.02.075. [Перекрестная ссылка] [Академия Google]
13. Seo E.J., Cho L., Estrin Y., De Cooman B.C. Взаимосвязь между микроструктурой и механическими свойствами для закалки и разделения (Q&P) обработанной стали. Acta Mater. 2016; 113:124–139. doi: 10.1016/j.actamat.2016.04.048. [CrossRef] [Google Scholar]
14. Пардал Дж. М., Таварес С. С. М., Таварес М. Т., Гарсия П. С. П., Веласко Дж. А. К., Абреу Х. Ф. Г., Пардал Дж. П. Влияние содержания углерода на мартенситное превращение аустенитных нержавеющих сталей, стабилизированных титаном. Междунар. Дж. Адв. Произв. Технол. 2020; 108: 345–356. doi: 10.1007/s00170-020-05138-8. [Перекрестная ссылка] [Академия Google]
15. Вендлер М., Вайс А., Крюгер Л., Мола Дж., Франке А., Ковалев А., Вольф С. Влияние марганца на микроструктуру и механические свойства литых высоколегированных CrMnNi-N сталей. Доп. англ. Матер. 2013; 15: 558–565. doi: 10.1002/адем.201200318. [CrossRef] [Google Scholar]
16. Бернс Х., Гаврилюк В., Шанина Б. Интенсивное междоузельное упрочнение нержавеющих сталей. Доп. англ. Матер. 2008;10:1083–1093. doi: 10.1002/адем.200800214. [CrossRef] [Google Scholar]
17. Бернс Х., Набиран Н., Мухика Л. Отливки из аустенитной нержавеющей стали с высоким содержанием пор. Сталь Рез. Междунар. 2013;84:119–128. doi: 10.1002/srin.201100332. [CrossRef] [Google Scholar]
18. Lee T.-H., Ha H.-Y., Hwang B., Kim S.-J., Shin E. Влияние доли углерода на энергию дефекта упаковки аустенитной нержавеющей стали. Стали. Металл. Матер. Транс. А. 2012;43:4455–4459. doi: 10.1007/s11661-012-1423-y. [CrossRef] [Google Scholar]
19. Брофман П.Дж., Анселл Г.С. О влиянии углерода на энергию дефекта упаковки аустенитных нержавеющих сталей. Металл. Транс. А. 1978; 9: 879–880. дои: 10.1007/BF02649799. [CrossRef] [Google Scholar]
20. Мола Дж., Луан Г., Хуанг К., Ульрих К., Волкова О., Эстрин Ю. Механизмы динамического деформационного старения в метастабильной аустенитной нержавеющей стали. Acta Mater. 2021;212:116888. doi: 10.1016/j.actamat.2021.116888. [CrossRef] [Google Scholar]
21. Chen G., Rahimi R., Xu G., Biermann H., Mola J. Влияние добавки Al на деформационное поведение аустенитной нержавеющей стали Fe–Cr–Ni–Mn–C. . Матер. науч. англ. А. 2020; 797:140084. doi: 10.1016/j.msea.2020.140084. [Перекрестная ссылка] [Академия Google]
22. Огава Т., Кояма М., Тасан С.С., Цузаки К., Ногучи Х. Влияние мартенситной трансформируемости и упрочняемости при динамическом старении на пластичность метастабильных аустенитных сталей, содержащих углерод. Дж. Матер. науч. 2017; 52:7868–7882. doi: 10.1007/s10853-017-1052-3. [CrossRef] [Google Scholar]
23. Talonen J., Nenonen P., Hänninen H. Статическое деформационное старение холоднодеформированной аустенитной нержавеющей стали. В: Акдут Н., Куман Б.С., де Фок Дж., редакторы. Материалы 7-й Международной конференции по высокоазотистым сталям 2004 г., HNS 2004; Остенде, Бельгия. 19–22 сентября 2004 г.; Бад-Гарцбург, Германия: GRIPS Media; 2004. [Google Scholar]
24. Хван А. В., Халльштедт Б., Брокманн К. Термодинамическая оценка системы Fe–Cr–C. Кальфад. 2014;46:24–33. doi: 10.1016/j.calphad.2014.01.002. [CrossRef] [Google Scholar]
25. Kong L., Liu Y., Liu J., Song Y., Li S., Zhang R., Li T., Liang Y. Влияние хрома на перлит- кинетика превращения аустенита в тройных сталях Fe–Cr–C. Дж. Эллой. комп. 2015; 648: 494–499. doi: 10.1016/j.jallcom.2015.06.259. [CrossRef] [Google Scholar]
26. Wieczerzak K., Bala P., Dziurka R., Tokarski T., Cios G., Koziel T., Gondek L. Влияние температуры на эволюцию эвтектических карбидов и M Реакция карбидов 7 C 3 → M 23 C 6 в быстрозатвердевшем сплаве Fe-Cr-C. Дж. Эллой. комп. 2017; 698: 673–684. doi: 10.1016/j.jallcom.2016.12.252. [CrossRef] [Google Scholar]
27. Liu W., Chen C., Tang Y., Long Q., Wei S., Zhang G., Mao F., Jiang Q., Zhang T., Liu M. Термодинамическая оценка и исследование микроструктуры затвердевания в системе Fe–Cr–Ni–C. Кальфад. 2020;69:101763. doi: 10.1016/j.calphad.2020.101763. [CrossRef] [Google Scholar]
28. Zhao Y., Liu W., Fan Y., Zhang T., Dong B., Chen L., Wang Y. Влияние микроструктуры на коррозионное поведение мартенситной нержавеющей стали супер 13Cr. сталь под термической обработкой. Матер. Характер. 2021;175:111066. doi: 10.1016/j.matchar.2021.111066. [CrossRef] [Google Scholar]
29. Шахриари А., Гаффари М., Хаксар Л., Насири А., Хададзаде А., Амирхиз Б.С., Мохаммади М. Коррозионная стойкость мартенситных нержавеющих сталей с содержанием 13% хрома: аддитивное производство CX по сравнению с кованым Ni-содержащим AISI 420. Коррозия. науч. 2021;184:109362. doi: 10.1016/j.corsci.2021.109362. [CrossRef] [Google Scholar]
30. Шнайдер Р., Перко Дж., Рейтхофер Г. Термическая обработка коррозионностойких инструментальных сталей для литья пластмасс. Матер. Произв. Процесс. 2009; 24:903–908. doi: 10.1080/10426910
31. Терри Дж. К. Материалы и дизайн бритв Gillette. Матер. Дес. 1991; 12: 277–281. doi: 10.1016/0261-3069(91)
-R.
32. Li J., He T., Zhang P., Cheng L., Wang L. Влияние крупных карбидов на анизотропию механических свойств в мартенситной плавке 11Cr-3Co-3W -стойкая сталь для высокотемпературных лопаток турбин ультрасверхкритических электростанций. Матер. Характер. 2020;159:110025. doi: 10.1016/j.matchar.2019.110025. [CrossRef] [Google Scholar]
33. Са де Соуза Дж.М., Лобато М.К., Гарсия Д.Н., Мачадо П.К. Износостойкость покрытия Fe–Cr–C, нанесенного методом сварки FCAW. Носить. 2021;476:203688. doi: 10.1016/j.wear.2021.203688. [CrossRef] [Google Scholar]
34. Барлоу Л.Д., Дю Туа М. Влияние аустенитизирующей термообработки на микроструктуру и твердость мартенситной нержавеющей стали AISI 420. J. Mater. англ. Выполнять. 2012;21:1327–1336. doi: 10.1007/s11665-011-0043-9. [CrossRef] [Google Scholar]
35. Lei X., Feng Y., Zhang J., Fu A., Yin C., Macdonald D.D. Влияние обращенного аустенита на характеристики точечной коррозии мартенситной нержавеющей стали Super 13Cr. Электрохим. Акта. 2016;191:640–650. doi: 10.1016/j.electacta.2016.01.094. [CrossRef] [Google Scholar]
36. Вендлер М., Хаузер М., Фабричная О., Крюгер Л., Вайс А., Мола Дж. Термическое и деформационное фазовое превращение Fe–15Cr–3Mn–3Ni –0,1N–(0,05–0,25)C аустенитные и аустенитно-мартенситные литые нержавеющие стали. Матер. науч. англ. А. 2015; 645: 28–39.. doi: 10.1016/j.msea.2015.07.084. [CrossRef] [Google Scholar]
37. Ян Х.-С., Бхадешия Х.К.Д.Х. Неопределенности в дилатометрическом определении температуры начала мартенсита. Матер. науч. Технол. 2007; 23: 556–560. doi: 10.1179/174328407X176857. [CrossRef] [Google Scholar]
38. García de Andrés C. Применение дилатометрического анализа к изучению превращений твердой фазы в стали. Матер. Характер. 2002;48:101–111. doi: 10.1016/S1044-5803(02)00259-0. [Перекрестная ссылка] [Академия Google]
39. Bonyár A., Renkó J., Kovács D., Szabó P.J. Понимание механизма цветного травления типа Beraha-I: определение зависящей от ориентации скорости травления, показателя преломления слоя и метод количественного определения угла между нормалью к поверхности направления 〈100〉, 〈111〉 для отдельных зерен. Матер. Характер. 2019;156:109844. doi: 10.1016/j.matchar.2019.109844. [CrossRef] [Google Scholar]
40. Metallische Werkstoffe—Härteprüfung nach Vickers—Teil 1: Prüfverfahren. Бойт Ферлаг ГмбХ; Берлин, Германия: 2018 г. DIN EN ISO 6507-1:2018-07; Немецкий стандарт EN ISO 6507-1:2018. [Академия Google]
41. Хуан К., Яо М., Тимохина И., Шимпф С., Бирманн Х., Волкова О., де Куман Б.С., Мола Дж. Реакции отпуска и перераспределение элементов при отпуске мартенситных нержавеющих сталей. Металл. Матер. Транс. А. 2019;50:3663–3673. doi: 10.1007/s11661-019-05272-3. [CrossRef] [Google Scholar]
42. Хуан К., Волкова О., Бирманн Х., Мола Дж. Дилатометрический анализ растворения карбидов с высоким содержанием хрома в мартенситных нержавеющих сталях. Металл. Матер. Транс. А. 2017; 48:5771–5777. doi: 10.1007/s11661-017-4377-2. [Перекрестная ссылка] [Академия Google]
43. Суутала Н., Такало Т., Моисио Т. Режим однофазной ферритной кристаллизации в сварных швах аустенитно-ферритной нержавеющей стали. Металл. Транс. А. 1979; 10: 1183–1190. doi: 10.1007/BF02811664. [CrossRef] [Google Scholar]
44. Суутала Н., Такало Т., Моисио Т. Ферритно-аустенитный режим затвердевания в сварных швах аустенитной нержавеющей стали. Металл. Транс. А. 1980; 11: 717–725. doi: 10.1007/BF02661201. [CrossRef] [Google Scholar]
45. Бхадешиа Х., Хаником Р. Стали: микроструктура и свойства. Баттерворт-Хайнеманн; Берлингтон, Массачусетс, США: 2017. [Google Scholar]
46. Presoly P., Pierer R., Bernhard C. Объединение измерений HT-LSCM и DSC для характеристики фазовых диаграмм сталей. ИОП конф. сер. Матер. науч. англ. 2012;33:12064. doi: 10.1088/1757-899X/33/1/012064. [CrossRef] [Google Scholar]
47. Chapman L., Day A., Quested P.N. Эталонные материалы для калибровки температур в приборах ДТА/ДСК. Национальная физическая лаборатория; Лондон, Великобритания: 1999. Отчет о NPL CMMT(A)157. [Google Scholar]
48. Гулливер Г. Количественное влияние быстрого охлаждения на состав бинарного сплава. Дж. Инст. Встретились. 1913;9:120–157. [Google Scholar]
49. Scheil E. Bemerkungen zur Schichtkristallbildung. З. Металлкд. 1942; 34: 70–72. [Google Scholar]
50. Кожешник Е. Модель Шейла-Гулливера с обратной диффузией применительно к микросегрегации хрома в сплавах Fe-Cr-C. Металл. Матер. Транс. А. 2000; 31:1682–1684. doi: 10.1007/s11661-000-0179-y. [CrossRef] [Google Scholar]
51. Като Т., Джонс Х., Кирквуд Д.Х. Сегрегация и образование эвтектики при затвердевании стали Fe-1C-1 5-Cr. Матер. науч. Технол. 2003;19: 1070–1076. doi: 10.1179/026708303225004639. [CrossRef] [Google Scholar]
52. Масуми Ф., Джахази М., Шахриари Д., Кормье Дж. Огрубение и растворение γ’-преципитатов во время обработки раствором суперсплава на основе никеля AD730™: механизмы и кинетические модели. Дж. Эллой. комп. 2016; 658: 981–995. doi: 10.1016/j.jallcom.2015.11.002. [CrossRef] [Google Scholar]
53. Масуми Ф., Джахази М., Кормье Дж., Шахриари Д. Кинетика растворения и морфологические изменения γ’ в суперсплаве AD730 TM. Веб-конференция MATEC. 2014;14:13005. doi: 10.1051/matecconf/20141413005. [Перекрестная ссылка] [Академия Google]
54. Масуми Ф., Шахриари Д., Джахази М., Кормье Дж., Дево А. Кинетика и механизмы повторного осаждения γ’ в суперсплаве на основе никеля. науч. Отчет 2016; 6: 28650. doi: 10.1038/srep28650. [Бесплатная статья PMC] [PubMed] [CrossRef] [Google Scholar]
55. Юань Л., Понге Д., Виттиг Дж., Чой П., Хименес Дж.А., Раабе Д. Наномасштабная реверсия аустенита посредством разделения, сегрегации и кинетики замораживание: Пример пластичной стали Fe–Cr–C 2 ГПа. Acta Mater. 2012;60:2790–2804. doi: 10.1016/j.actamat.2012.01.045. [Перекрестная ссылка] [Академия Google]
56. Рахими Р., Волкова О., Бирманн Х., Мола Дж. Термический анализ образования и растворения карбидов с высоким содержанием хрома в нержавеющих сталях, легированных алюминием. Доп. англ. Матер. 2019;21:1800658. doi: 10.1002/адем.201800658. [CrossRef] [Google Scholar]
57. Мола Дж., Луан Г., Хуанг К. , Шимпф К., Рафаджа Д. Эволюция цементита в среднемарганцевых сталях, вызывающая двойникование, пластичность. Материалия. 2018;2:138–147. doi: 10.1016/j.mtla.2018.07.013. [CrossRef] [Google Scholar]
58. Гарсия де Андрес С., Каруана Г., Альварес Л. Контроль карбидов M23C6 в мартенситной нержавеющей стали 0,45C–13Cr с помощью трех репрезентативных параметров термообработки. Матер. науч. англ. А. 1998;241:211–215. doi: 10.1016/S0921-5093(97)00491-7. [CrossRef] [Google Scholar]
59. Garcia C., Alvarez L.F., Carsi M. Влияние параметров термообработки на неравновесные превращения и свойства мартенситных нержавеющих сталей X45Cr13 и X60Cr14MoV. Сварка. Междунар. 1992; 6: 612–621. doi: 10.1080/09507119209548251. [CrossRef] [Google Scholar]
60. Alvarez L.F., Garcia C. Etude des transforms au chauffage continu des aciers inoxidables martensitiques типов Cr13 и CrMoV14. Преподобный Мет. Париж. 1993;90:245–254. doi: 10.1051/металл/1993
245. [CrossRef] [Google Scholar]
61. Mola J., Ullrich C., Kuang B., Rahimi R., Huang Q., Rafaja D., Ritzenhoff R. Аустенитный Fe-15Cr-1Mo, не содержащий никеля и марганца -0.4N-0.3C Сталь: Поведение при растяжении и деформационные процессы между 298 K и 503 K (25 °C и 230 °C) Metall. Матер. Транс. А. 2017;48:1033–1052. doi: 10.1007/s11661-017-3960-x. [CrossRef] [Google Scholar]
62. Huang Q., Schröder C., Biermann H., Volkova O., Mola J. Влияние мартенситной фракции на свойства при растяжении закаленных и разделенных (Q&P) мартенситных нержавеющих сталей. Сталь Рез. Междунар. 2016; 87: 1082–1094. doi: 10.1002/srin.201500472. [CrossRef] [Google Scholar]
63. Sourmail T., Garcia-Mateo C. Критическая оценка моделей для прогнозирования температуры Ms сталей. вычисл. Матер. науч. 2005; 34: 323–334. doi: 10.1016/j.commatsci.2005.01.002. [CrossRef] [Google Scholar]
64. Эндрюс К.В. Эмпирические формулы для расчета некоторых температур превращения. J. Iron Steel Inst. 1965; 60: 721–727. [Google Scholar]
65. Han Y., Li C., Ren J., Qiu C., Zhang Y., Wang J. Изменения сегрегации дендритов в процессе высокотемпературной гомогенизации литой стали h23. ISIJ Междунар. 2019;59:1893–1900. doi: 10.2355/isijinternational.ISIJINT-2019-148. [CrossRef] [Google Scholar]
66. Суутала Н. Влияние марганца и азота на режим затвердевания сварных швов аустенитной нержавеющей стали. МЕТАЛЛ. ПЕР. А. 1982; 13:2121–2130. doi: 10.1007/BF02648382. [CrossRef] [Google Scholar]
67. Хаузер М., Вендлер М., Гош Чоудхури С., Вайс А., Мола Дж. Количественная оценка α’-мартенсита, вызванного деформацией, в Fe–19Cr–3Mn–4Ni–0,15C –0,15N аустенитной стали по магнитным измерениям на месте. Матер. науч. Технол. 2015; 31:1473–1478. дои: 10.1179/1743284714Y.0000000731. [CrossRef] [Google Scholar]
68. Каллити Б.Д. Элементы рентгеновской дифракции. 2-е изд. Аддисон-Уэсли; Рединг, Массачусетс, США: 1978. [Google Scholar]
69. Диксон М. Дж. Значение параметров текстуры в фазовом анализе с помощью рентгеновской дифракции. Дж. Заявл. Кристаллогр. 1969; 2: 176–180. doi: 10.1107/S002188986
81. [CrossRef] [Google Scholar]
70. Вилла М., Хансен М.Ф., Сомерс М. Образование мартенсита в сплавах Fe-C при криогенных температурах. Скр. Матер. 2017;141:129–132. doi: 10.1016/j.scriptamat.2017.08.005. [CrossRef] [Google Scholar]
71. Эузер В.К., Уильямсон Д.Л., Кларк А.Дж., Спир Дж.Г. Ограничение разложения остаточного аустенита в закаленных и отпущенных сталях: влияние быстрого отпуска и кремния. ISIJ Междунар. 2020;60:2990–3000. doi: 10.2355/isijinternational.ISIJINT-2020-263. [CrossRef] [Google Scholar]
72. Хаузер М., Вендлер М., Фабричная О., Волкова О., Мола Дж. Аномальная стабилизация аустенитных нержавеющих сталей при криогенных температурах. Матер. науч. англ. А. 2016; 675: 415–420. doi: 10.1016/j.msea.2016.08.080. [Перекрестная ссылка] [Академия Google]
73. Хаузер М., Вендлер М., Вайс А., Волкова О., Мола Дж. О критической движущей силе деформационного образования α’-мартенсита в аустенитных Cr–Mn–Ni сталях. Доп. англ. Матер. 2019;21:1800676. doi: 10.1002/адем.201800676. [CrossRef] [Google Scholar]
74. Койстинен Д.П., Марбургер Р.Е. Общее уравнение, описывающее степень аустенитно-мартенситного превращения в чистых железоуглеродистых сплавах и простых углеродистых сталях. Акта Металл. 1959; 7: 59–60. дои: 10.1016/0001-6160(59)
-1. [CrossRef] [Google Scholar]
75. Huang Q., de Cooman B.C., Biermann H., Mola J. Влияние мартенситной фракции на стабилизацию аустенита в аустенитно-мартенситных нержавеющих сталях. Металл. Матер. Транс. А. 2016; 47:1947–1959. doi: 10.1007/s11661-016-3382-1. [CrossRef] [Google Scholar]
76. Балби М., Альварес-Армас И., Армас А. Влияние времени выдержки при межкритической температуре на микроструктуру и свойства при растяжении двухфазной ферритно-мартенситной стали. Матер. науч. англ. А. 2018; 733:1–8. doi: 10.1016/j.msea.2018.07.029. [CrossRef] [Google Scholar]
77. Speich G.R., Leslie W.C. Закалка стали. Металл. Транс. А. 1972; 3: 1043–1054. doi: 10.1007/BF02642436. [CrossRef] [Google Scholar]
78. Chen P.C., Winchell P.G. Мартенситная решетка изменяется при отпуске. Металл. Транс. А. 1980; 11:1333–1339. doi: 10.1007/BF02653487. [CrossRef] [Google Scholar]
79. Тейлор К.А., Коэн М. Старение железосодержащих мартенситов. прог. Матер. науч. 1992; 36: 151–272. doi: 10.1016/0079-6425(92)
-5. [Перекрестная ссылка] [Академия Google]
80. Робертс К.С. Влияние углерода на объемные доли и параметры решетки остаточного аустенита и мартенсита. Дж. Мет. 1953; 5: 203–204. doi: 10.1007/BF03397477. [CrossRef] [Google Scholar]
81. Lu Y., Yu H., Sisson R.D. Влияние содержания углерода на отношение c/a мартенсита после закалки в сплавах Fe-C. Матер. науч. англ. А. 2017; 700: 592–597. doi: 10.1016/j.msea.2017.05.094. [CrossRef] [Google Scholar]
82. Патерсон М.С. Рентгеновская дифракция на гранецентрированных кубических кристаллах с дефектами деформации. Дж. Заявл. физ. 1952;23:805–811. дои: 10.1063/1. 1702312. [CrossRef] [Google Scholar]
83. Лободюк В.А., Мешков Ю.Ю., Перелома Е.В. О тетрагональности мартенситной кристаллической решетки в сталях. Металл. Матер. Транс. А. 2019; 50:97–103. doi: 10.1007/s11661-018-4999-z. [CrossRef] [Google Scholar]
84. Краусс Г. Мартенсит в стали: Прочность и структура. Матер. науч. англ. А. 1999; 273–275:40–57. doi: 10.1016/S0921-5093(99)00288-9. [CrossRef] [Google Scholar]
85. Мола Дж., де Куман Б.К. Закалка и разделение (Q&P) Обработка мартенситных нержавеющих сталей. Металл. Матер. Транс. А. 2013;44:946–967. doi: 10.1007/s11661-012-1420-1. [CrossRef] [Google Scholar]
86. Саид-Акбари А., Мозекер Л., Шведт А., Блек В. Характеристика и прогнозирование поведения потока в высокомарганцевых сталях, вызванных двойникованием, пластичность: Часть I. Карты механизмов и работа – Закаливающее поведение. Металл. Матер. Транс. А. 2012; 43:1688–1704. doi: 10.1007/s11661-011-0993-4. [CrossRef] [Google Scholar]
87. Жак П. Дж., Деланне Ф., Ладриер Ж. О влиянии межфазных взаимодействий на механическую стабильность остаточного аустенита в многофазных сталях с пластичностью, вызванной превращением. Металл. Матер. Транс. А. 2001; 32:2759–2768. doi: 10.1007/s11661-001-1027-4. [CrossRef] [Google Scholar]
88. Mola J. Соображения по проектированию формуемых аустенитных нержавеющих сталей на основе процессов, вызванных деформацией: 2. In: Borek W., Tanski T., Brytan Z., editors. Аустенитные нержавеющие стали. ИнтехОткрытый; Риека, Хорватия: 2017. [Google Scholar]
89. Seo E.J., Cho L., Kim J.K., Mola J., Zhao L., de Cooman B.C. Специфические свойства компонентов при закалке и разделении (Q&P) обработанной стали. Матер. науч. англ. А. 2019 г.;740–741:439–444. doi: 10.1016/j.msea.2018.10.082. [CrossRef] [Google Scholar]
90. Huang Q., Shi R., Muránsky O., Beladi H., Kabra S., Schimpf C., Volkova O., Biermann H., Mola J. Нейтронографический анализ разделение напряжений и деформаций в двухфазной микроструктуре с параллельно расположенными фазами. науч. 2020; 10:13536. doi: 10.1038/s41598-020-70299-1. [Бесплатная статья PMC] [PubMed] [CrossRef] [Google Scholar]
91. Kim H.S. О правиле смесей для определения твердости композитов, армированных частицами. Матер. науч. англ. А. 2000; 289: 30–33. doi: 10.1016/S0921-5093(00)00909-6. [CrossRef] [Google Scholar]
Химический состав (требования) для углеродистых легированных сталей, используемых в трубопроводах
, используемых в трубопроводах
Спецификация для бесшовных и сварных черных и горячеоцинкованных стальных труб не более, %

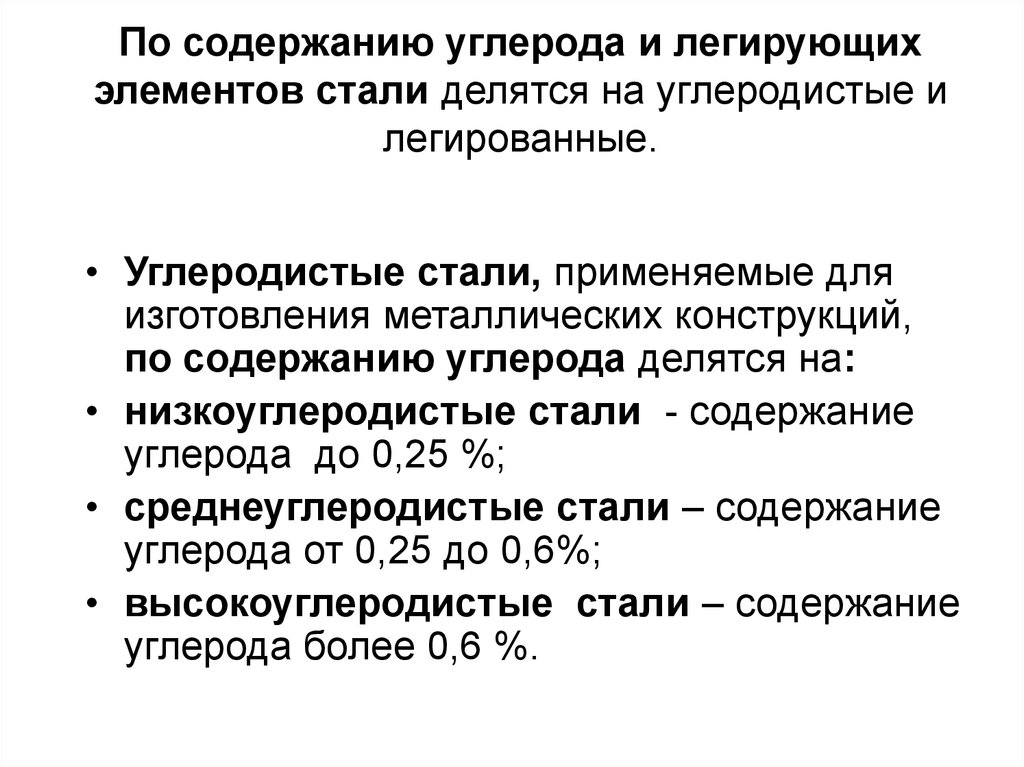
Примечание.
- Суммарный состав этих пяти элементов не должен превышать 1,00%.
ASTM A105
Спецификация поковок из углеродистой стали для трубопроводов
Состав, % | |||||
Элт | С | Мн | П | С | Си |
0,35 макс. | 0,6 1,05 | 0,035 макс. | 0,04 макс. | 0,1 0,35 | |
Состав, % | |||||
Элт | Медь | Ni | Кр | Пн | В |
0,4 макс. ![]() | 0,4 макс. (1) | 0,3 макс. (1-2) | 0,12 макс. (1-2) | 0,08 макс. |
Примечания..
- Сумма меди, никеля, ниобия, молибдена и ванадия не должна превышать 1,00%.
- Сумма ниобия и молибдена не должна превышать 0,32%.
Примечание.. Для каждого сокращения на 0,01% ниже установленного максимума углерода (0,35%), допускается увеличение содержания марганца на 0,06% сверх указанного максимума (1,05%) до максимального значения 1,35%.
ASTM A106
Спецификация бесшовных труб из углеродистой стали для эксплуатации при высоких температурах
Состав, % | |||||
Элт | C макс. | Мн | P макс. | S макс. | Si мин. |
гр. А | 0,25 (1) | 0,27 0,93 | 0,035 | 0,035 | 0,1 |
гр.![]() | 0,30 (2) | 0,29 1,06 | 0,035 | 0,035 | 0,1 |
гр. С | 0,35 (2) | 0,29 1,06 | 0,035 | 0,035 | 0,1 |
Состав, % | |||||
Элт | Cr макс. (3) | Cu макс. (3) | Мо макс. (3) | Ni макс. (3) | В макс. (3) |
гр. А | 0,4 | 0,4 | 0,15 | 0,4 | 0,08 |
гр. Б | 0,4 | 0,4 | 0,15 | 0,4 | 0,08 |
гр. С | 0,4 | 0,4 | 0,15 | 0,4 | 0,08 |
Примечания..
- Для каждого сокращения на 0,01% ниже указанного максимума углерода допускается увеличение содержания марганца на 0,06% выше указанного максимума, максимум до 1,35%.
- Если иное не указано покупателем, для каждого сокращения на 0,01% ниже указанного максимума углерода допускается увеличение содержания марганца на 0,06% выше указанного максимума, максимум до 1,65%.
- Сумма этих пяти элементов не должна превышать 1%.
ASTM A216
Спецификация для стальных отливок, углеродистых, пригодных для сварки плавлением, для работы при высоких температурах
Состав, % макс. | |||||
гр. | С | Мн | П | С | Си |
WCA UNS J02502 | 0,25 (1) | 0,70 (1) | 0,04 | 0,045 | 0,6 |
ВКБ УНС Дж03002 | 0,30 (2) | 1,00 (2) | 0,04 | 0,045 | 0,6 |
ВКЦ UNS J02503 | 0,25 (3) | 1,20 (3) | 0,04 | 0,045 | 0,6 |
Состав, % не более | |||||
гр.![]() | С | Мн | П | С | Si |
WCA UNS J02502 | 0,25 (1) | 0,70 (1) | 0,04 | 0,045 | 0,6 |
ВКБ УНС Дж03002 | 0,30 (2) | 1,00 (2) | 0,04 | 0,045 | 0,6 |
ВКЦ UNS J02503 | 0,25 (3) | 1,20 (3) | 0,04 | 0,045 | 0,6 |
Примечания..
- Для каждого уменьшения содержания углерода на 0,01% ниже указанного максимального содержания углерода допускается увеличение содержания марганца на 0,04% выше указанного максимума, но не более чем на 1,10%.
- Для каждого уменьшения содержания углерода на 0,01 % ниже указанного максимального содержания углерода допускается увеличение содержания Mn на 0,04 % сверх указанного максимума, но не более чем на 1,28 %.
- Для каждого уменьшения содержания углерода на 0,01 % ниже указанного максимального содержания углерода допускается увеличение содержания марганца на 0,04 % сверх указанного максимума до максимум 1,40 %.
ASTM A234
Спецификация трубопроводной арматуры из кованой углеродистой и легированной стали для эксплуатации при умеренных и высоких температурах
Состав, % | |||||
гр. | С | Мн | P макс. | S макс. | Си |
WPB (1 2 3 4 5) | 0,3 макс. | 0,29 1,06 | 0,050 | 0,058 | 0,1 мин |
ДПК (2 3 4 5) | 0,35 макс. | 0,29 1,06 | 0,050 | 0,058 | 0,1 мин |
WP1 | 0,28 макс. | 0,3 0,9 | 0,045 | 0,045 | 0,1 0,5 |
WP12 CL1 | 0,05 0,2 | 0,3 0,8 | 0,045 | 0,045 | 0,6 макс. |
WP12 CL2 | 0,05 0,2 | 0,3 0,8 | 0,045 | 0,045 | 0,6 макс. ![]() |
WP11 CL1 | 0,05 0,15 | 0,3 0,6 | 0,03 | 0,03 | 0,5 1,0 |
WP11 CL2 | 0,05 0,2 | 0,3 0,8 | 0,04 | 0,04 | 0,5 1,0 |
WP11 CL3 | 0,05 0,2 | 0,3 0,8 | 0,04 | 0,04 | 0,5 1,0 |
WP22 CL1 | 0,05 0,15 | 0,3 0,6 | 0,04 | 0,04 | 0,5 макс. |
WP22 CL3 | 0,05 0,15 | 0,3 0,6 | 0,04 | 0,04 | 0,5 макс. |
РП5 КЛ1 | 0,15 макс. | 0,3 0,6 | 0,04 | 0,03 | 0,5 макс. |
РП5 КЛ3 | 0,15 макс. | 0,3 0,6 | 0,04 | 0,03 | 0,5 макс. ![]() |
WP9 CL1 | 0,15 макс. | 0,3 0,6 | 0,03 | 0,03 | 1,0 макс. |
WP9 CL3 | 0,15 макс. | 0,3 0,6 | 0,03 | 0,03 | 1,0 макс. |
WPR | 0,2 макс. | 0,4 1,06 | 0,045 | 0,05 | |
WP91 | 0,08 0,12 | 0,3 0,6 | 0,02 | 0,01 | 0,2 0,5 |
WP911 | 0,09 0,13 | 0,3 0,6 | 0,02 | 0,01 | 0,1 0,5 |
Состав, % | |||||
гр. | Кр | Пн | Ni | Медь | Другие |
WPB (1 2 3 4 5) | 0,4 макс. | 0,15 макс. | 0,4 макс. ![]() | 0,4 макс. | В 0,08 макс. |
ДПК (2 3 4 5) | 0,4 макс | 0,15 макс. | 0,4 макс. | 0,4 макс. | В 0,08 макс. |
WP1 | 0,44 0,65 | ||||
WP12 CL1 | 0,8 1,25 | 0,44 0,65 | |||
WP12 CL2 | 0,8 1,25 | 0,44 0,65 | |||
WP11 CL1 | 1,0 1,5 | 0,44 0,65 | |||
WP11 CL2 | 1,0 1,5 | 0,44 0,65 | |||
WP11 CL3 | 1,0 1,5 | 0,44 0,65 | |||
WP22 CL1 | 1,9 2,6 | 0,87 1,13 | |||
WP22 CL3 | 1,9 2,6 | 0,87 1,13 | |||
РП5 КЛ1 | 4.![]() 6. | 0,44 0,65 | |||
РП5 КЛ3 | 4. 6. | 0,44 0,65 | |||
WP9 CL1 | 8. 10. | 0,9 1,1 | |||
WP9 CL3 | 8. 10. | 0,9 1,1 | |||
WPR | 1,6 2,24 | 0,75 1,25 | |||
WP91 | 8. 9,5 | 0,85 1,05 | 0,4 макс. | V 0,18 0,25 Nb 0,06 0,1 N 0,03 0,07 Al 0,02 макс. (6) Ti 0,01 макс. (6) Zr 0,01 макс. (6) | |
WP911 | 8. 9,5 | 0,9 1,1 | 0,4 макс. | (6)0451 Ti 0,01 макс. (6) |
Примечания..
- Фитинги, изготовленные из стержня или пластины, могут содержать максимум 0,35 углерода
- Фитинги, изготовленные из поковок, могут содержать не более 0,35 углерода и не более 0,35 кремния без минимального количества.
- Для каждого сокращения на 0,01% ниже указанного максимума углерода будет разрешено увеличение содержания марганца на 0,06% сверх указанного максимума, но не более чем на 1,35%.
- Сумма меди, никеля, ниобия и молибдена не должна превышать 1,00%.
- Сумма ниобия и молибдена не должна превышать 0,32%.
- Применяется как для анализа плавки, так и для анализа продукта.
Мягкая сталь: определение, свойства и варианты использования
- 24 февраля 2022 г.
Мягкая сталь — это сталь, которая сочетает в себе железо и углерод. Благодаря присутствию железа он приобрел хорошие магнитные свойства. Мягкая не легированная сталь. Из-за большего количества углерода его химический состав сильно отличается от других элементов или других сталей, поскольку мягкая сталь имеет хорошее качество поверхности, и вы можете увеличить твердость ее поверхности различными способами. Давайте узнаем больше об этом материале.
Что такое мягкая сталь?
Сталь в основном состоит из железа. В зависимости от различного содержания углерода различают низкоуглеродистую сталь (также называемую мягкой сталью или простой углеродистой сталью), среднеуглеродистую сталь и высокоуглеродистую сталь.
В следующей таблице показаны различия и характеристики трех типов стали:
Содержание углерода (% масс.) | Микроструктура | Characteristics | Examples | |
Low-carbon steel (Mild steel) |
Less than 0.25 |
Pearlite, ferrite | Soft, cheap, очень пластичный, легко поддается механической обработке и сварке | AISI105, AISI 316L, Q195, Q215, Q235, 08F, 15Mn, 20Mn |
-9009 Средняя углеродистая сталь0003 | 0,25 до 0,60 | Martensite | . | |
Высокоуглеродистая сталь (углеродная инструментальная сталь) | от 0,60 до 1,25 | Pearedit0003 | T7, T7A, T8Mn, T8MnA, AISI440C |
Согласно приведенной выше таблице, мягкая сталь — это тип стали, который содержит 0,05–0,25 % углерода. Благодаря своей пластичности и пластичности материал легко формуется и обрабатывается. Детали из мягкой стали, как правило, очень подходят для штамповки, ковки. Мягкая сталь широко используется в инструментах, автомобильных кузовных деталях, строительстве и инфраструктуре.
Как производится мягкая сталь?
Процесс производства мягкой стали (низкоуглеродистой стали) аналогичен процессу производства других углеродистых сталей. Эти процессы со временем менялись, и в настоящее время они более эффективны и дешевле, чем раньше. В современных производственных процессах производство мягкой стали из чистого железа или железной руды включает три основных этапа.
1. Первичное производство стали
В этом процессе железо смешивают с углем и известью и нагревают в доменной печи. В современном первичном производстве стали используются современные печи, такие как кислородная печь или электродуговая печь. Последний обычно используется производителями в развитых странах, а стальные детали, которые выходят из электродуговой печи , отличаются высоким качеством.
2. Вторичное производство стали
Целью вторичного производства стали является, главным образом, снижение содержания углерода (меньше углерода) до желаемой степени и добавление других легирующих элементов для улучшения свойств стали. На этом этапе в основном контролируется и контролируется термообработка и охлаждение печи.
3. Литье и первичная формовка
Как только сталь в печи достигает определенного содержания углерода и механические свойства улучшаются в определенной степени, сталь должна быть разлита в форму, которая называется литьем, а некоторые говорят чугун, что не так. . Во время этого процесса жидкая форма стали будет отверждена и сформирована в различные геометрические формы. Эти кристаллические структуры литой стали впоследствии будут разрезаны на более мелкие детали.
Литая сталь имеет множество дефектов и несовершенств. Применяется первичный процесс формования, называемый горячей прокаткой. После горячей прокатки сталь приобретает большую прочность, пластичность, свариваемость и т. д.
4. Вторичное формование
Вообще говоря, существует процесс вторичного формования, такой как обработка на станках с ЧПУ, холодная прокатка, порошковое покрытие, цементация или гальваническое покрытие для дальнейшего улучшения механических и химических свойств или эстетики мягкой стали. стальные детали. В этих процессах надлежащим образом наносится металлическое покрытие, такое как цинковое покрытие или любой другой тип углеродистой стали.
Механические свойства низкоуглеродистой стали
Как видно из приведенной выше таблицы, низкоуглеродистая сталь имеет более низкое содержание углерода, чем другая углеродистая сталь. Мягкая сталь имеет простое содержание углерода 0,25%.
Мягкая сталь обладает высокой ударной вязкостью, отличной пластичностью и свариваемостью, хорошей ковкостью с возможностью холодной штамповки. Благодаря этим свойствам обработка низкоуглеродистой стали на станке с ЧПУ проще, чем обработка на станке с ЧПУ других типов стали.
Основным недостатком мягкой стали является то, что она имеет относительно низкую прочность на растяжение, что означает, что она легче ломается, чем другие типы стали.
К счастью, процесс термической обработки, называемый науглероживанием, можно использовать для повышения прочности на растяжение. Науглероживание — это процесс поверхностного упрочнения, при котором мягкая сталь нагревается до определенной температуры, а затем сталь охлаждается, в результате чего сталь закаляется на поверхности, сохраняя сердцевину стали мягкой и пластичной.
Применение мягкой стали
Широко используется мягкая сталь. Типичные применения – обычные аппаратные средства, кухонная утварь, медицинские инструменты, машины, строительство, инфраструктура и т. д.
1. Строительство и инфраструктура
Мягкая сталь обладает хорошей прочностью на растяжение для изготовления каркасов в строительных проектах. Он соответствует сейсмическим и ветровым требованиям, не может быть скомпрометирован червями и насекомыми, а мягкая сталь устойчива к эрозии и огнестойкости, что идеально подходит для использования в строительстве.
2. Машиностроение
Высокая прочность, пластичность и твердость низкоуглеродистой стали делают ее предпочтительной для производства комплектующих к машинам. Благодаря низкому содержанию углерода сталь можно обрабатывать, резать, прессовать, формовать и формовать без разрушения.
3. Посуда
Благодаря очень низкому содержанию углерода низкоуглеродистая сталь не ржавеет, благодаря чему посуда долгое время остается чистой и острой. Мягкая сталь более термостойкая, чем другие материалы, может использоваться в качестве антипригарного материала и более полезна для здоровья, чем алюминиевая посуда.
4. Трубопроводы
Поскольку низкоуглеродистая сталь чрезвычайно пластична, трубы из низкоуглеродистой стали очень популярны при изготовлении различных видов труб и столбов. Мягкая сталь может использоваться в качестве материалов, безопасных для пищевых продуктов, поэтому она идеально подходит для транспортировки воды, напитков и природного газа в стальных трубах. Кроме того, благодаря низкому содержанию углерода трубы, которые используются на открытом воздухе, не ржавеют и не подвергаются воздействию холода в суровых условиях. По сравнению с пластиковыми трубами трубы из мягкой стали более экологичны и служат намного дольше. Его также можно вырезать прямоугольной формы.
Варианты использования мягкой стали
AISI 316L с низким содержанием углерода – всего 0,03 % – это обычно очень широко используемая мягкая сталь. Работая с различными компаниями на протяжении многих лет, мы обнаружили, что производители медицинских инструментов любят использовать этот материал. Для изготовления прототипов или изготовления стальных деталей небольшого объема обработка с ЧПУ обычно является выбором номер один. Детали из стали 316L, обработанные на станках с ЧПУ, часто не требуют обработки поверхности или какого-либо процесса термообработки. Детали из мягкой стали с ЧПУ могут использоваться в качестве конечных продуктов, а не только прототипов. В других распространенных продуктах, таких как рыболовные инструменты, также используется много стали AISI 316L.
Обработка низкоуглеродистой стали с ЧПУ и мелкосерийное производство
Почему люди часто жалуются, что сталь трудно обрабатывать с помощью ЧПУ? Обрабатываемость стали в основном зависит от содержания в ней углерода. Высокоуглеродистые стали трудно обрабатывать в основном из-за их неуступчивости и внутреннего напряжения.
Однако мягкие стали трудно обрабатывать, потому что они слишком мягкие. Стружка, появившаяся в процессе ЧПУ-обработки, имеет тенденцию прилипать и накапливаться, это приводит к увеличению времени на очистку стружки и возможному повреждению режущих инструментов. Идеальное количество углерода для легкой обработки составляет около 0,20%.
Например, некоторые низкоуглеродистые стали слишком мягкие, что вызывает проблемы со скоплением стружки. Есть один способ, который мы иногда используем: сначала цементируем мягкую сталь. Цементная закалка или поверхностная закалка делает мягкую сталь закаленной снаружи, что делает сталь мягкой внутри, что устраняет проблемы накопления стружки, а поскольку сердцевина стали все еще мягкая, когда возникает внешнее напряжение. во время процесса обработки, применяемого к материалу, мягкость или пластичность мягкого перегонного куба будет поглощать напряжение и делать деталь неспособной сломаться.
Для мелкосерийного производства деталей из низкоуглеродистой стали лучше всего подходит обработка с ЧПУ. Мягкая сталь, используемая для обработки с ЧПУ, — это то, что мы называем «блочным материалом», имеет хорошее качество и разумную цену. Обработка с ЧПУ выполняется очень быстро по сравнению с литьем и литьем. Для литья и литья первоначальные затраты времени и средств на изготовление форм очень велики. При мелкосерийном или мелкосерийном производстве деталей из мягкой стали общая стоимость, как правило, намного дешевле, чем при литье и формовании, поскольку вам не нужно изготавливать формы.
Долгосрочное производство мягкой стали: литье и литье
Если необходимо производить большие объемы деталей из мягкой стали, распространенный метод называется литьем или формованием (расплавленная сталь). Литье металлов под давлением (MIM), которое похоже на литье пластмасс под давлением, представляет собой процесс впрыскивания жидкой формы металла в форму, жидкий металл будет отвержден и затвердеет в форме. После извлечения из формы стальные детали грубо формируются. Существуют процессы пост-обработки для дальнейшего улучшения эстетики формованных деталей.
Как и при литье пластмасс под давлением, при проектировании форм и деталей MMI конструктор должен учитывать такие вопросы, как углы уклона, извлечение из формы, усадка, допуски и т.