Сталь 4х5в2фс: характеристики и расшифовка, применение и свойства стали
alexxlab | 24.01.1970 | 0 | Разное
Краткие обозначения: | ||||
σв | — временное сопротивление разрыву (предел прочности при растяжении), МПа | ε | — относительная осадка при появлении первой трещины, % | |
σ0,05 | — предел упругости, МПа | Jк | — предел прочности при кручении, максимальное касательное напряжение, МПа | |
σ0,2 | — предел текучести условный, МПа | σизг | — предел прочности при изгибе, МПа | |
δ5,δ4,δ10 | — относительное удлинение после разрыва, % | σ-1 | — предел выносливости при испытании на изгиб с симметричным циклом нагружения, МПа | |
σсж0,05 и σсж | — предел текучести при сжатии, МПа | J-1 | — предел выносливости при испытание на кручение с симметричным циклом нагружения, МПа | |
ν | — относительный сдвиг, % | n | — количество циклов нагружения | |
sв | — предел кратковременной прочности, МПа | R и ρ | — удельное электросопротивление, Ом·м | |
ψ | — относительное сужение, % | E | — модуль упругости нормальный, ГПа | |
KCU и KCV | — ударная вязкость, определенная на образце с концентраторами соответственно вида U и V, Дж/см2 | T | — температура, при которой получены свойства, Град | |
sT | — предел пропорциональности (предел текучести для остаточной деформации), МПа | l и λ | — коэффициент теплопроводности (теплоХотСтилость материала), Вт/(м·°С) | |
HB | — твердость по Бринеллю | C | — удельная теплоХотСтилость материала (диапазон 20o — T ), [Дж/(кг·град)] | |
HV | — твердость по Виккерсу | pn и r | — плотность кг/м3 | |
HRCэ | — твердость по Роквеллу, шкала С | а | — коэффициент температурного (линейного) расширения (диапазон 20o — T ), 1/°С | |
HRB | — твердость по Роквеллу, шкала В | σtТ | — предел длительной прочности, МПа | |
HSD | — твердость по Шору | G | — модуль упругости при сдвиге кручением, ГПа |
Марка стали |
Вид поставки Прутки и полосы – ГОСТ 5950–2000. |
||||||||||||||||||||||||||||||||||||||||||||||
4Х5В2ФС (ЭИ 958) |
|||||||||||||||||||||||||||||||||||||||||||||||
Массовая доля элементов, % по ГОСТ 5950–2000 |
Температура критических точек, ºС | ||||||||||||||||||||||||||||||||||||||||||||||
C |
Si |
Mn |
S |
P |
Cr |
Ni |
V |
W |
Cu |
Ас1 |
Ас3 |
Аr1 |
Аr3 |
Мн |
Мк |
||||||||||||||||||||||||||||||||
0,35–0,45 |
0,80–1,20 |
0,15–0,45 |
0,030 |
≤ 0,030 |
4,50–5,50 |
≤ 0,40 |
0,60–0,90 |
1,60–2,20 |
≤ 0,30 |
800–830 |
875 |
730 |
710 |
275 |
90 |
||||||||||||||||||||||||||||||||
Механические свойства при комнатной температуре |
|||||||||||||||||||||||||||||||||||||||||||||||
НД |
Режим термообработки |
Сечение, мм |
σ0,2, Н/мм2 |
σВ, Н/мм2 |
δ, % |
Ψ, % |
KCU, Дж/см2 |
HRC |
НВ |
||||||||||||||||||||||||||||||||||||||
Операция |
t, ºС |
Охлаждающая среда |
не менее |
||||||||||||||||||||||||||||||||||||||||||||
ГОСТ 5950–2000 |
Отжиг |
840–880 |
С печью до 600 ºС |
– |
Не определяются |
– |
≤ 241 |
||||||||||||||||||||||||||||||||||||||||
Закалка |
1030– 1050 |
Масло или воздух |
– |
≥ 50 |
– |
||||||||||||||||||||||||||||||||||||||||||
ДЦ |
Закалка а) подогрев б) окончатель-ный нагрев Отпуск 1-й Отпуск 2-й |
700–750 1030–1050 560–580 530–540 |
Масло1 Воздух |
– |
Не определяются |
53–56 47–49 |
|||||||||||||||||||||||||||||||||||||||||
1 Подстуживание на воздухе до 950 ºС. |
|||||||||||||||||||||||||||||||||||||||||||||||
Назначение. Пресс-формы для литья под давлением цинковых, алюминиевых и магниевых сплавов, молотовые и прессовые вставки (толщиной или диаметром до 200–250 мм), при горячем деформировании конструкционных сталей, инструмент для высадки заготовок из легированных конструкционных и жаропрочных материалов на горизонтально-ковочных машинах. |
|||||||||||||||||||||||||||||||||||||||||||||||
Предел выносливости, Н/мм2 |
Термообработка |
при t, ºС |
Термообработка |
||||||||||||||||||||||||||||||||||||||||||||
σ-1 |
τ-1 |
+ 20 |
0 |
– 20 |
– 30 |
– 40 |
– 50 |
||||||||||||||||||||||||||||||||||||||||
Теплостойкость |
Шлифуемость |
Критический диаметр, мм, при закалке |
|||||||||||||||||||||||||||||||||||||||||||||
В воде |
В масле |
В селитре |
На воздухе |
||||||||||||||||||||||||||||||||||||||||||||
43 HRC, 630 ºС, 2 ч |
|||||||||||||||||||||||||||||||||||||||||||||||
Технологические характеристики |
|||||||||||||||||||||||||||||||||||||||||||||||
Ковка |
Охлаждение поковок, изготовленных |
||||||||||||||||||||||||||||||||||||||||||||||
Вид полуфабриката |
Температурный интервал ковки, ºС |
из слитков |
из заготовок |
||||||||||||||||||||||||||||||||||||||||||||
Размер сечения, мм |
Условия охлаждения |
Размер сечения, мм |
Условия охлаждения |
||||||||||||||||||||||||||||||||||||||||||||
Слиток |
1180–850 |
Замедленное в колодце |
|||||||||||||||||||||||||||||||||||||||||||||
Заготовка |
|||||||||||||||||||||||||||||||||||||||||||||||
Свариваемость |
Обрабатываемость резанием |
Флокеночувствительность |
|||||||||||||||||||||||||||||||||||||||||||||
Не применяется для сварных конструкций. |
В отожженном состоянии при ≤ 241 НВ К√ = 1,2 (твердый сплав), К√ = 0,75 (быстрорежущая сталь) |
Чувствительна |
|||||||||||||||||||||||||||||||||||||||||||||
Склонность к отпускной хрупкости |
|||||||||||||||||||||||||||||||||||||||||||||||
Склонна |
Cталь 4Х5В2ФС механические свойства, химический состав. Сталь 4Х5В2ФС круг сатльной пруток
Справочная информация
Характеристика материала сталь 4Х5В2ФСМарка стали | сталь 4Х5В2ФС |
Классификация стали | Сталь инструментальная штамповая |
Применение стали 4Х5В2ФС | пресс-формы литья под давлением цинковых, алюминиевых и магниевых сплавов, молотовые и прессовые вставки (сечением до 200—250 мм) при горячем деформировании конструкционных сталей, инструмент для высадки заготовок из легированных конструкционных и жаропрочных материалов на горизонтально-ковочных машинах.![]() |
Химический состав в % материала сталь 4Х5В2ФС
C | Si | Mn | Ni | S | P | Cr | W | V | Cu |
0.35 – 0.45 | 0.8 – 1.2 | 0.15 – 0.45 | до 0.35 | до 0.03 | до 0.03 | 4.5 – 5.5 | 1.6 – 2.2 | 0.![]() | до 0.3 |
Температура критических точек материала сталь 4Х5В2ФС
Ac1 = 800 , Ac3(Acm) = 875 , Ar3(Arcm) = 840 , Ar1 = 730 , Mn = 275 |
Механические свойства при Т=20oС материала сталь 4Х5В2ФС
Сортамент | Размер | Напр. | sв | sT | d5 | y | KCU | Термообр. |
– | мм | – | МПа | МПа | % | % | кДж / м2 | – |
Сорт | 10 | 1760 | 1690 | 300 | Закалка 1030 – 1050oC, масло, Отпуск 560 – 580oC,Отпуск 530 – 540oC, |
Твердость материала сталь 4Х5В2ФС после отжига , | HB 10 -1 = 241 МПа |
Обозначения:
Механические свойства : | |
sв | – Предел кратковременной прочности , [МПа] |
sT | – Предел пропорциональности (предел текучести для остаточной деформации), [МПа] |
d5 | – Относительное удлинение при разрыве , [ % ] |
y | – Относительное сужение , [ % ] |
KCU | – Ударная вязкость , [ кДж / м2] |
HB | – Твердость по Бринеллю , [МПа] |
Сталь 4Х5В2ФС (ЭИ958) – компания Владресурс
Марка : | 4Х5В2ФС (другое обозначение ЭИ958) | |
Классификация : | Сталь инструментальная штамповая
| |
Применение: | пресс-формы литья под давлением цинковых, алюминиевых и магниевых сплавов, молотовые и прессовые вставки (сечением до 200—250 мм) при горячем деформировании конструкционных сталей, инструмент для высадки заготовок из легированных конструкционных и жаропрочных материалов на горизонтально-ковочных машинах. | |
Зарубежные аналоги: | Известны |
Химический состав в % материала 4Х5В2ФС
ГОСТ 5950 – 2000
C | Si | Mn | Ni | S | P | Cr | W | V | Cu |
0. | 0.8 – 1.2 | 0.15 – 0.45 | до 0.4 | до 0.03 | до 0.03 | 4.5 – 5.5 | 1.6 – 2.2 | 0.6 – 0.9 | до 0.3 |
Температура критических точек материала 4Х5В2ФС.
Ac1 = 800 , Ac3(Acm) = 875 , Ar3(Arcm) = 840 , Ar1 = 730 , Mn = 275 |
Механические свойства при Т=20oС материала 4Х5В2ФС .
Сортамент | Размер | Напр. | sв | sT | d5 | y | KCU | Термообр. |
– | мм | – | МПа | МПа | % | % | кДж / м2 | – |
Сорт | 10 |
| 1760 | 1690 |
|
| 300 | Закалка 1030 – 1050oC, масло, Отпуск 560 – 580oC,Отпуск 530 – 540oC, |
Твердость 4Х5В2ФС после отжига , ГОСТ 5950-2000 | HB 10 -1 = 241 МПа |
Зарубежные аналоги материала 4Х5В2ФС
Внимание! Указаны как точные, так и ближайшие аналоги.
Германия |
DIN,WNr
|
Обозначения:
Механические свойства : | |
sв | – Предел кратковременной прочности , [МПа] |
sT | – Предел пропорциональности (предел текучести для остаточной деформации), [МПа] |
d5 | – Относительное удлинение при разрыве , [ % ] |
y | – Относительное сужение , [ % ] |
KCU | – Ударная вязкость , [ кДж / м2] |
HB | – Твердость по Бринеллю , [МПа] |
4Х5В2ФС – Юнисталь Урал
Марка: | 4Х5В2ФС |
---|---|
Классификация: | Сталь инструментальная штамповая |
Применение: | пресс-формы литья под давлением цинковых, алюминиевых и магниевых сплавов, молотовые и прессовые вставки (сечением до 200—250 мм) при горячем деформировании конструкционных сталей, инструмент для высадки заготовок из легированных конструкционных и жаропрочных материалов на горизонтально-ковочных машинах |
C | Si | Mn | Ni | S | P | Cr | W | V | Cu |
---|---|---|---|---|---|---|---|---|---|
0,35-0,45 | 0,8 – 1,2 | 0,15-0,45 | до 0,35 | до 0,03 | до 0,03 | 4,5 – 5,5 | 1,6 – 2,2 | 0,6 – 0,9 | до 0,3 |
Ac1 = 800, Ac3(Acm) = 875, Ar3(Arcm) = 840, Ar1 = 730, Mn = 275 |
Сортамент | Размер, мм | Напр.![]() |
SВ, МПа | SТ, МПа | d5, % | y, % | KCU, кДж/м2 | Термообр. |
---|---|---|---|---|---|---|---|---|
Сорт | 10 | 1760 | 1690 | 300 | Закалка 1130-1050 0С, масло Отпуск 560-580 0С, Отпуск 530-540 0С |
Твердость материала 4Х5В2ФС после отжига | HB 10 -1 = 241 МПа |
Механические свойства: | |
---|---|
SВ | Предел кратковременной прочности, МПа |
SТ | Предел пропорциональности (предел текучести для остаточной деформации), МПа |
d5 | Относительное удлинение при разрыве, %) |
y | Относительное сужение, % |
KCU | Ударная вязкость, кДж/м2 |
HB | Твердость по Бринеллю, МПа |
|
|
|
|
|
27Х2Н2М1Ф | ТУ 5950 – 73 – 73, в последней версии материал отсутствует | Feот 92.![]() |
2Х6В8М2К8 | Feот 72.6%Co7.5-8.5%W7-8%Cr6.5-7%Mo1.8-2.3%Si0.3-0.6%C0.22-0.3%Mn0.15-0.4%V0.1-0.25%… | |
3Х2В8Ф | ГОСТ 5950 – 73, в последней версии материал отсутствует | Feот 86.2%W7.5-8.5%Cr2.2-2.7%C0.3-0.4%V0.2-0.5%Mn0.15-0.4%Si0.15-0.4%… |
3Х2Н2МВФ | ОСТ 24,959,01 – 0 | Feот 91.7%Cr2-2.5%Ni1.4-1.8%W0.8-1.2%Mo0.8-1%Mn0.5-0.8%C0.32-0.3%V0.2-0.3%Si0.17-0.3%… |
3Х3М3Ф | ГОСТ 5950 – 2000 | Feот 85.5%Cr2.8-3.5%Mo2.5-3%V0.4-6%C0.27-0.3%Mn0.2-0.5%Si0.1-0.4%… |
40Х5МФ | ТУ 24-1-12-180 – 0 | Feот 90.4%Cr4.5-5.5%Mo1.2-1.6%Mn0.5-0.8%V0.4-0.6%C0.35-0.4%Si0.17-0.3%… |
4Х2В5МФ | ГОСТ 5950 – 2000 | Feот 87.7%W4.5-5.5%Cr2.2-3%Mo0.6-0.9%V0.6-0.9%C0.3-0.4%Mn0.1-0.45%Si0.1-0.4%… |
4Х2НМФ | ТУ 24-1-12-180 – 0 | Feот 94%Cr2-2.![]() |
4Х3ВМФ | ГОСТ 5950 – 2000 | Feот 91.3%Cr2.8-3.5%W0.6-1%Si0.6-0.9%V0.6-0.9%Mo0.4-0.6%C0.4-0.48%Mn0.3-0.6%… |
4Х4ВМФС | ГОСТ 5950 – 2000 | Feот 89.5%Cr3.2-4%Mo1.2-1.5%W0.8-1.2%Si0.6-1%V0.6-0.9%C0.37-0.4%Mn0.2-0.5%… |
4Х5В2ФС | ГОСТ 5950 – 2000 | Feот 88.6%Cr4.5-5.5%W1.6-2.2%Si0.8-1.2%V0.6-0.9%C0.35-0.4%Mn0.15-0.4%… |
4Х5МФ1С | ГОСТ 5950 – 2000 | Feот 88.9%Cr4.5-5.5%Mo1.2-1.6%Si0.9-1.2%V0.8-1.1%C0.37-0.4%Mn0.2-0.5%… |
4Х5МФС | ГОСТ 5950 – 2000 | Feот 89.5%Cr4.5-5.5%Mo1.2-1.6%Si0.9-1.2%C0.32-0.4%V0.3-0.5%Mn0.2-0.5%… |
4ХВ2С | ГОСТ 5950 – 73, в последней версии материал отсутствует | Feот 93.8%W2-2.5%Cr1-1.3%Si0.6-0.9%C0.35-0.4%Mn0.15-0.4%… |
4ХМФС | ГОСТ 5950 – 2000 | Feот 93.7%Cr1.![]() |
5Х2МНФ | ГОСТ 5950 – 2000 | Feот 92.9%Cr1.5-2%Ni1.2-1.6%Mo0.8-1%C0.46-0.5%Mn0.4-0.7%V0.3-0.5%Si0.1-0.4%… |
5Х3В3МФС | ГОСТ 5950 – 2000 | Feот 87.6%W3-3.6%Cr2.5-3.2%V1.5-1.8%Mo0.8-1.1%Si0.5-0.8%C0.45-0.5%Mn0.2-0.5%Nb0.05-0.1%… |
5ХВ2С | ГОСТ 5950 – 73, в последней версии материал отсутствует | Feот 93.2%W1.8-2.3%Cr0.9-1.2%Si0.8-1.1%C0.45-0.5%Mn0.15-0.4%… |
5ХГМ | ГОСТ 5950 – 73, в последней версии материал отсутствует | Feот 95.3%Mn1.2-1.6%Cr0.6-0.9%C0.5-0.6%Si0.25-0.6%Mo0.15-0.3%… |
5ХНМ | ГОСТ 5950 – 2000 | Feот 94.9%Ni1.4-1.8%Cr0.5-0.8%Mn0.5-0.8%C0.5-0.6%Mo0.15-0.3%Si0.1-0.4%… |
6ХВ2С | ГОСТ 5950 – 2000 | Feот 93.4%W2.2-2.7%Cr1-1.3%C0.55-0.6%Si0.5-0.8%Mn0.15-0.4%… |
6ХВГ | ГОСТ 5950 – 2000 | Feот 95.![]() |
6ХС | ГОСТ 5950 – 2000 | Feот 95.3%Cr1-1.3%Si0.6-1%C0.6-0.7%Mn0.15-0.4%… |
7Х3 | ГОСТ 5950 – 2000 | Feот 93.4%Cr3.2-3.8%C0.65-0.7%Mn0.15-0.4%Si0.1-0.4%… |
7ХГ2ВМ | ГОСТ 5950 – 73, в последней версии материал отсутствует | Feот 92.8%Mn1.8-2.3%Cr1.5-1.8%C0.68-0.7%W0.5-0.9%Mo0.5-0.8%Si0.2-0.4%V0.1-0.25%… |
7ХГ2ВМФ | ГОСТ 5950 – 2000 | Feот 92.1%Mn1.8-2.3%Cr1.5-1.8%C0.68-0.7%W0.55-0.9%Mo0.5-0.8%Si0.1-0.4%V0.1-0.25%… |
8Х3 | ГОСТ 5950 – 2000 | Feот 93.3%Cr3.2-3.8%C0.75-0.8%Mn0.15-0.4%Si0.1-0.4%… |
8Х4В3М3Ф2 | ГОСТ 5950 – 73, в последней версии материал отсутствует | Feот 85.1%Cr3.5-4.5%W2.5-3.2%Mo2.5-3%V1.9-2.5%C0.75-0.8%Mn0.15-0.4%Si0.15-0.4%… |
Х12 | ГОСТ 5950 – 2000 | Feот 82.7%Cr11.5-13%C2-2.![]() |
Х12ВМ | ГОСТ 5950 – 73, в последней версии материал отсутствует | Feот 81.8%Cr11-12.5%C2-2.2%Mo0.6-0.9%W0.5-0.8%Mn0.15-0.4%V0.15-0.3%Si0.1-0.4%… |
Х12ВМФ | ГОСТ 5950 – 2000 | Feот 81.7%Cr11-12.5%C2-2.2%Mo0.6-0.9%W0.5-0.8%Mn0.15-0.4%V0.15-0.3%Si0.1-0.4%… |
Х12М | ГОСТ 5950 – 73, в последней версии материал отсутствует | Feот 84.2%Cr11-12.5%C1.45-1.6%Mo0.4-0.6%Mn0.15-0.4%Si0.15-0.3%V0.15-0.3%… |
Х12МФ | ГОСТ 5950 – 2000 | Feот 83.4%Cr11-12.5%C1.45-1.6%Mo0.4-0.6%Mn0.15-0.4%V0.15-0.3%Si0.1-0.4%… |
Х12Ф1 | ГОСТ 5950 – 2000 | Feот 83.6%Cr11-12.5%C1.25-1.4%V0.7-0.9%Mn0.15-0.4%Si0.1-0.4%… |
Х6ВФ | ГОСТ 5950 – 2000 | Feот 88.5%Cr5.5-6.5%W1.1-1.5%C1.05-1.1%V0.5-0.8%Mn0.15-0.4%Si0.1-0.4%… |
Х6Ф4М | Feот 86%Cr5.7-6.5%V3.5-4%C1.![]() |
EP750 sh, (07X25N16AG6F) EP767 (03X14K13N4M3TV) ЭП794ш, vd, id, pd (02X8N22S6) EP810vd (03X12N10MTR) EP853vd (03X11N10M2T2) EP864vi (03X21N32M3B) EP866sh (15X16K5N2MVFAB) ЭП898 (06х23Н7Д2) ЭП921вд03Х9К14Н6М3ДФ ЭП961 (03х23Н5К10М3ФБ) ЭП987 (10х28Н11С5М2ТЮ) ЭИ69 (45х24Н14В2М) EI268, ш (14X17N2) EI417 (20h33N18) EI432 (10h27N13M3T) EI448 (10X17h23M2T) EI572 (31h29N9MVBT) EI654sh (15h28N12S4TYU) EI696, А (10h21N20T3R) EI726 (09h24N19V2BR1) EI736sh (13h24N3V2FR) EI811 (12h31N5T) EI811vd (12h31N5T) EI835sh (12h35N16G7AR) EI878sh (12h27G9AN4 ) EI914 (08X18N10T) EI943 (06XN28MDT) EI946, z (25X18N8V2) EI961sh (13X11N2V2MF) ЭИ962ш (11Х11Н2В2МФ) 11Х13Н3 18Х13Н3 EK48, ш (14X17N2AM2) EK21vd (03X18K8M5T) EK81sh (15X16N3KAMF) | ТУ14-1-911-74ТУ14-1-1149-2008ТУ14-1-3812-84 ТУ14-1-2235-77ТУ14-131-795-89ТУ14-1-2512-78ТУ14-1-2756-79 ТУ14-1-3613-83ТУ14-1-1785-2007 ТУ14-1-4940-90ТУ14-131-621-7 5 ГОСТ 5949-75ТУ14-1-1671-76 ГОСТ5949-75ТУ14-1-377-72 ГОСТ5949-75 ГОСТ 5949-75 ГОСТ 5949-75 ГОСТ 5949−75TU14−1-915−74TU14−1-1671−76TU14−1-2865−80TU14−1-3297−82TU14−1-1273−75TU14−1-1283−75TU14−1-225−72TU14−1- 377-72 ГОСТ5949-75 ГОСТ 5949−75TU14−1-204−72TU14−1-3297−82TU14−131−809−90TU14−1-2172−77TU14−1-2139−77TU14−1-2139−77TU14−1-3407−82TU14−131− 379 -78ТУ14-1-3140-81ТУ14-1-4479-88ТУ14-1-4143-86 | 10-180 10–180 12−100 10-200 8−180 8−180 8−170 9−160 35, 55, 60–180 13–120 38, 45, 55 8−180 8−180 8-200 8-200 20-55 20-55 21-40 8−180 8-45,8-120 8-200 8-200 8-200 8−180 12−200 10 (8) -200 10 (8) -200 10−160 10-200 20-200 8−110 8−110 10-120 20-40 (млн т) 40-70 70−200 10-120 | 10-180 75, 85, 100, 125 10–180 70-180 10–180 10−170 60–180 10–180 10–180 10-200 10-200 21-40 10–180 8-45 10-200 10-200 10-200 8−180 12−20 10−20 10−20 10-200 250 80−200 70-200 | 6×20… 150×250 | 10–41 | Szczegóły wyposażenia specjalnego. Do produkcji sprzętu chemicznego. Stal odporna na korozję do produkcji części do wyposażenia specjalnego. Stal odporna na korozję do produkcji części do wyposażenia specjalnego. Przeznaczony do produkcji wyrobów specjalnych działających w wysokich temperaturach. środowisko. Szczegóły wyposażenia specjalnego. Szczegóły wyposażenia specjalnego. Szczegóły wyposażenia specjalnego. Szczegóły wyposażenia specjalnego.Inżynieria energetyczna. Zawory silnikowe, odkuwki, części rurociągów. Zawory silnikowe, odkuwki, części rurociągów. Ostrza robocze, tarcze, wały, tuleje. Ostrza robocze, tarcze, wały, tuleje. Szczegóły instalacji w przemyśle chemicznym i naftowym, gazocigi, komory spalania. Do produkcji konstrukcji spawanych pracujących w środowiskach korozyjnych. Konstrukcje spawane pracujące w środowisku kwaśnym. Wirniki, tarcze, śruby. Produkty spawane działające w powietrzu i środowiskach korozyjnych. Wirniki, tarcze, łopatki turbin. Mocno obciążone części pracujące w wysokiej wilgotności. Szczegóły wyposażenia specjalnego. Szczegóły wyposażenia specjalnego. Części pracujące przy umiarkowanych obciążeniach. Znajduje zastosowanie w przemyśle lotniczym. Elektrody świec zapłonowych, drut elektrodowy. Części kwasoodporne. Szczegóły wyposażenia specjalnego. Tarcze, łopatki i inne części sprężarki.Tarcze, łopatki i inne części sprężarki. Tarcze, łopatki i inne części sprężarki. Сталь одпорна на корозьен ок. сделать produkcji części poprzez obróbkę na gorąco na zimno. Сталь одпорна на корозьен ок. do produkcji części metodą górską. я зимно. przetwarzanie. Сталь одпорна на корозьен ок. do produkcji części metodą górską. я зимно. przetwarzanie. Szczegóły wyposażenia specjalnego. Szczegóły wyposażenia specjalnego. Szczegóły wyposażenia specjalnego. |
ترکیب شیمیایی از ربن استیل
واص فولاد با ترکیب شیمیایی آن تعیین می شود.
ناخالصی ای دائمی عبارتند از کربن ، منگنز ، سیلیکون ، وگرد و سفر.
ربن دایی ناپذیر ولاد است که تأثیر مهمی در خواص ن دارد. محتوای ن در نمرات ولاد ساخته ده از 0.1 تا 1.4 درصد است. با افزایش مقدار کربن در ولاد ، سختی و مقاومت آن افزایش می ابد ، ابلیت ورشکستگی و سختی کاهش می یابد.
منگنز ناخودآگاه دائمی است اگر محتوای ن کمتر از 1 باشد. با محتوای بیش از 1 ٪ ، آن یک عنصر آلیاژی است.
منگنز دی اکسید کننده فولاد است. ان باعث افزایش قدرت ، مقاومت در برابر سایش و سختی ری می شود ، باعث کاهش پیچش در نگام سخت دن ش با این حال ، درت ضربه کاهش می یابد. فولاد حاوی 11-14% منگنز (فولاد گاتفیلد) از نظر مقاومت در برابر سایش بسیار بالا است, زیرا می تواند در طول تغییر شکل پلاستیک تقویت شود. ولاد حاوی 10 درصد منگنز ر مغناطیسی می شود.
سیلیکون مچنین یک دی اکسید ننده فولاد و عنصر آلیاژی است اگر محتوای ن بیش از 0.8 باشد.این خواص قدرت فولاد را افزایش می دهد, محدودیت کشش, خوردگی و مقاومت در برابر حرارت, با این حال, قدرت ضربه آن را کاهش می دهد.
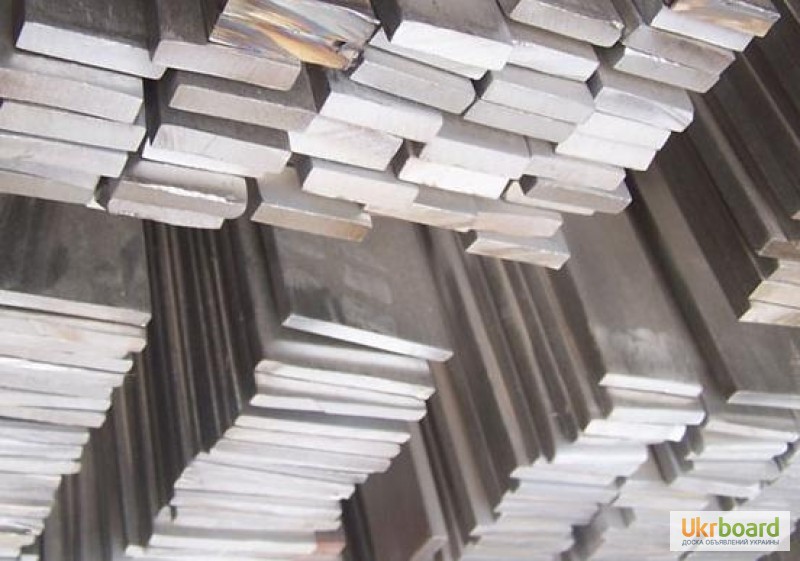
وگرد و سفر ناخالص مضر هستند. بنابراین, گوگرد باعث می شود فولاد “قرمز بنفش” و فسفر, افزایش سختی فولاد, کاهش سختی آن و باعث “شکنندگی سرد”, به عنوان مثال, شکننده در دمای زیر -50 درجه سانتی گراد
ناخالصی های مخفی عبارتند از اکسیژن, نیتروژن و دروژن ، جزئی در ولاد و در شکل غیر فلزی شامل (اکسید ، نیترید). نها ناخالصی ای مضر هستند ، را در کارهای رم ، لز را از بین می برند ، باعث ایجاد اشک در ن می.
ناخالصی ای تصادفی مس روی ، سرب ، روم نیکل و دیگر فلزات است که با مواد شارژ به ولاد می رسد. اساسا کیفیت فولاد را بدتر می کند.
افزودنی ای ویژه (عناصر آلیاژی) به فولاد وارد می شوند تا خواص خاصی به ن اضافه شود. این شامل منگنز, سیلیکون, کروم, نیکل, مولیبدن, تنگستن, وانادیوم, بور, نایوبیوم, زیرکونیم, سلنیوم, تلوریوم, مس و غیره
شایع ترین عنصر آلیاژی کروم است. هنگامی که فولاد گرم می شود, باعث افزایش خواص مکانیکی و برش می شود, مقاومت در برابر خوردگی, سختی پذیری را افزایش می دهد و باعث بهبود عملکرد سایشی می شود.نگامی که محتوای روم بیش از 10 است ، ولاد دزنگ می شود ، اما در عین حال توانایی ود رالتوانایی ود رالتوانایی ود رال توانایی ود رال توانایی ود رالتوانایی ود رالتوانایی ود رالتوانایی ود رال توانایی ودسالبرا رتاد رتاد رتاد رتاد برا رتاد رتاد رتاد رتاد رتاد رتاد رتاد برا رتاد
نیکل قدرت فولاد را افزایش می دهد در حالی که ویسکوزیته بالا را حفظ می کند, مانع رشد دانه در طی حرارت می شود, باعث کاهش پیچش در طی سخت شدن, افزایش مقاومت خوردگی و سختی پذیری می شود.

مولیبدن باعث خرد شدن دانه های فولادی می شود, سختی پذیری آن را افزایش می دهد, مقاومت در برابر گرما, ویسکوزیته در دماهای پایین, مقاومت در برابر انعطاف پذیری و مقاومت سایشی, گرایش به شیب خفیف را کاهش می دهد.
تنگستن سختی و واص برش فولاد ، سختی پذیری ، مقاومت و سختی را افزایش می دهد. ولاد با محتوای 9–18 تنگستن به سرعت بالا شناخته می شود.
وانادیم ساختار فولادی زیبا را ایجاد می کند, باعث کاهش رشد دانه در طی حرارت, افزایش سختی, مقاومت در برابر بارهای ارتعاش, سختی پذیری و مقاومت در برابر خسارت می شود.
بور باعث سخت شدن فولاد می شود, ویسکوزیته سیلیکونی را افزایش می دهد, توانایی ارتعاشات فرکانس بالا را خنثی می کند, تمایل به شکنندگی غیر قابل برگشت را کاهش می دهد.
نیوبیوم از وردگی بین کریستالی جلوگیری می کند ، خواص جوشکاری را بهبود می بخشد د وابید بد د دابیده ما
زیرکونیوم سطح استقامت فولاد را در هوا و محیط های خوردگی افزایش می دهد, ویژگی های قدرت آن را در دمای بالا و مقاومت ضربه در دمای زیر صفر افزایش می دهد, رشد دانه ها را کاهش می دهد, سختی پذیری و جوش پذیری را افزایش می دهد.
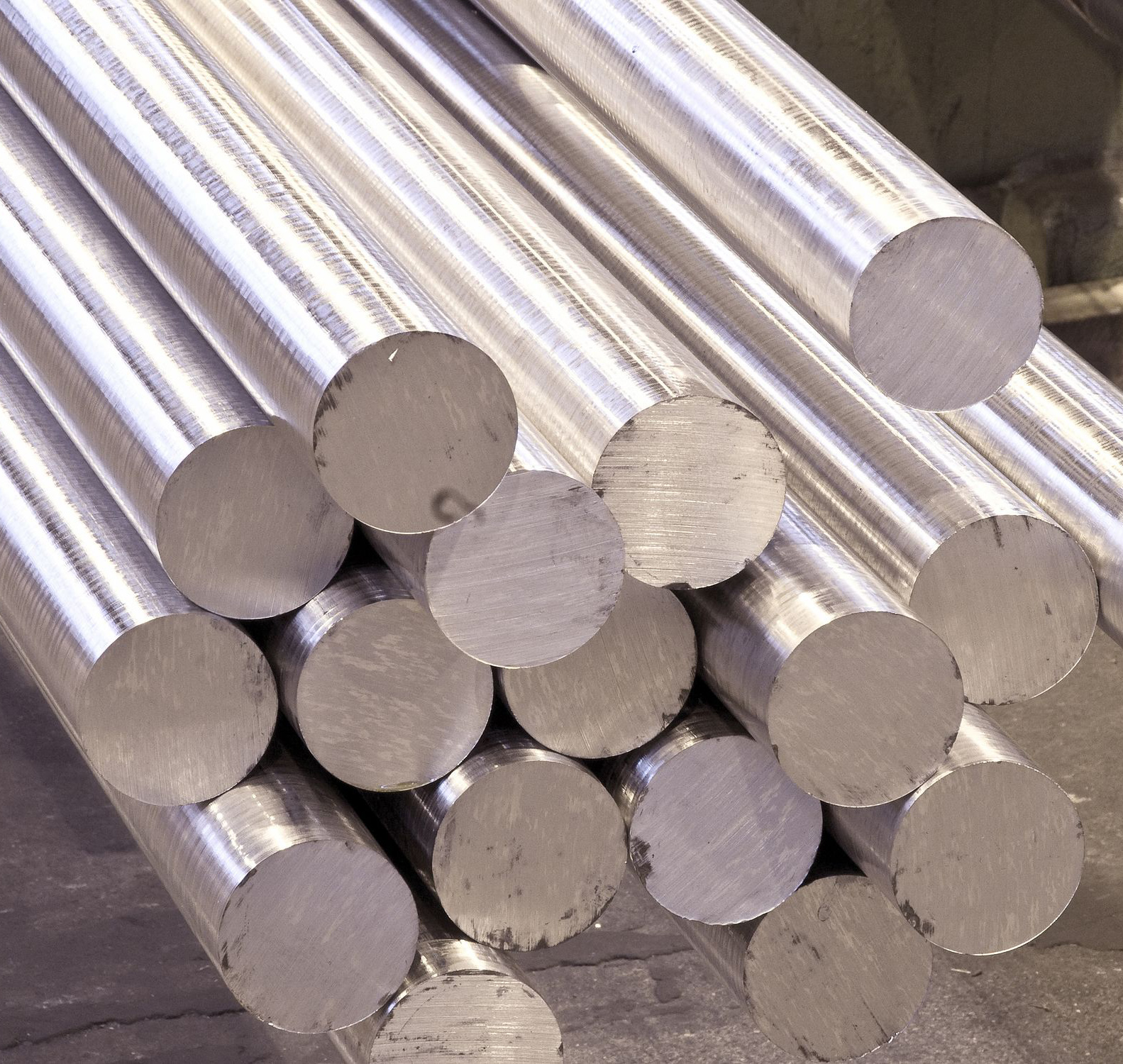
مس باعث افزایش مقاومت وردگی ولاد و سلنیوم و تلوریم می شود. خواص مکانیکی فولاد و بویژه انعطافپذیری آن,
ساختار شمش فولاد و روش های متالورژی برای بهبود کیفیت آن
در گیاهان متالورژی از فولاد ذوب شده است به سطل کوره که در آن برای 5-10 دقیقه انکوبه به چین ترکیب آن, صعود از اجزاء غیر لزی و روجی از ، و سپس در الب ریخته ، که ل خاصی از چدن یا فولاد ریخته می شود.در اینجا فولاد ریستال می شود ، تشکیل شمش های مختلف جرم و ربندی. سپس شمشهای حاصل از آن در مغازه های جعلی یا نورد استفاده می شود.
ساختار مش فولاد یکنواخت نیست. لایه سطحی ن دانه های مسطح کوچک است ، لایه میان لایه طولانی ، ریستال ستون را است عمود بر سطح. هسته شمش ساخته شده از دانه های بزرگ تقسیم شده است. در بخش متوسط بالا پوسته به اصطلاح پوسته تشکیل شده توسط ناخالصی های ذوب پایین, غیر فلزکی و گازهای موجود در فولاد مایع قرار گرفته است.
در عین حال, تختخواب عمیق پوسته انقباض, منطقه بسیار توسعه یافته از بلورهای “ستون”, و همچنین حباب های گاز, جذب غیر فلزی و ترک, کیفیت خوک های فولادی را کاهش می دهد.
الی ترین روش ای متالورژی برای بهبود کیفیت فولاد عبارتند از ریخته گری مسمر ، لاء الکرورتند لا الکرور
ریخته ری مستمر از ولاد ، رآیند تولید شمش در ماشین آلات مداوم ریخته گری است.
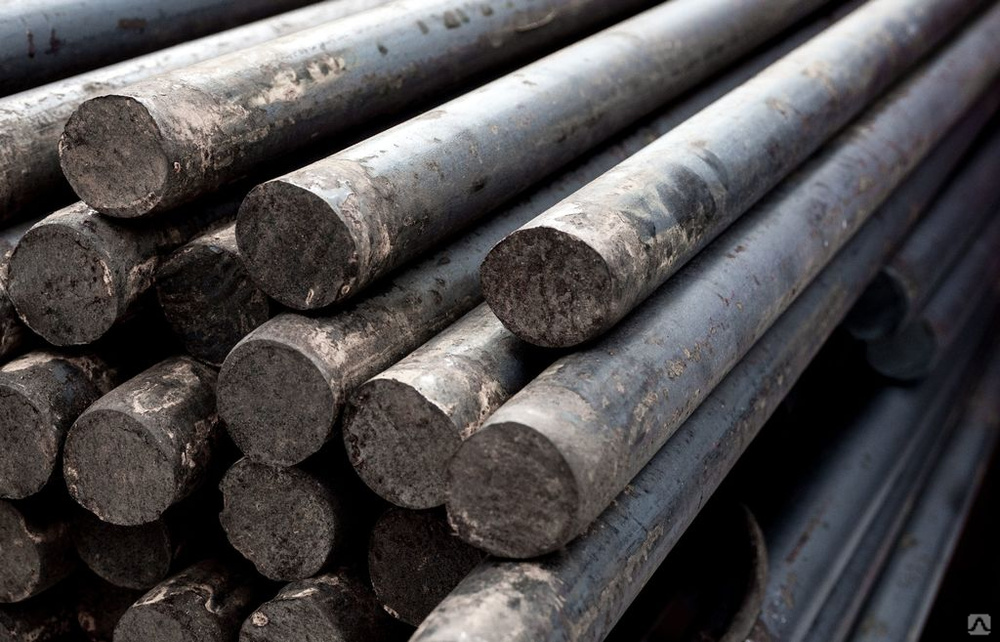
در مقایسه با آنچه که در قالب ها به دست می آید, شمش های ریخته گری پیوسته بیشتر از تمیز بودن سطح, ساختار ریز دانه, عدم تقارن شیمیایی کمتر (جداسازی) و پوسته انقباضی در آنها وجود ندارد.ریخته گری وسته به طرز چشمگیری کاهش تلفات فلزات را کاهش می دهد و بهره وری را افزایش دهد.
مپاژ ولاد مایع برای تولید فولادهای با کیفیت بالا و برخی از آلیاژهای بالا مورد استفاده قرار می رار می می را. ان اجازه می دهد تا شما را به تمیز کردن فلز از گازها ، ناخالصی های ر فلزی inclusions ، برای بهبسود خنواص نتا نتا نتا نتا نتا. با این حال ، نه شمش ها به طور قابل توجهی افزایش می یابد. اروب ردن در وره های مخصوص خلاء قوس الکتریکی ، القایی ، رتو الکترونی یا نوع لاسما بلافاصل لاسما بلافاصله رتر
Электрошлаковый переплав. ان روش اک ردن لز مایع از ترکیبات غیر فلزی و ازهای محلول است که از طریق یک لایه سرباره حاا مقدرودوب اترباربار حاای مقدرودوب مدرودابربار حاا مقدرودوب
پالایش فولاد با سرباره مایع مصنوعی با هدف تخریب اکسیداسیون, تصفیه اضافی از ترکیبات گوگرد و غیر فلزی و همچنین بهبود خواص مکانیکی مورد استفاده قرار می گیرد.

انواع درمان حرارتی و شیمیایی حرارتی فولاد
فرایندهای حرارتی فولاد شامل گرمایش و خنک سازی آن است که تغییر ساختار داخلی و در نتیجه خواص آن را ایجاد می کند. انواع الی درمان رما امل آنیلینگ ، نرمال شدن ، نک کردن ، نک ردن ، ثبت اختراع و ردازش حاترت.
آنیلینگ حرارت فلز را تا 200-1200 درجه سانتیگراد, قرار گرفتن در معرض طولانی در این درجه حرارت و آهسته (گاهی اوقات با کوره) خنک کننده بسته به وضعیت اولیه فولاد و درجه حرارت حرارت, کامل شدن, ناقص, کم, ایزوترمال, шероидизация مگن دن повторная кристаллизация نثی ، و مچنين آنيلينگ براي از بين بردن تنشهاي باقي مانده.
نیلینگ امل برای تولیدات طولانی ، سرامیک و ریخته گری فولاد شکل به منظور ایجاد یک ساختار ایجاد یک ساختار ااد ساختار ا دمای حرارت 730-950 درجه سانتی راد است.
نیل ناقص برای کاهش سختی ولاد و بهبود قابلیت کارکرد آن با برش استفاده می شود. ان در دمای 730-950 درجه سانتیگراد انجام می شود.
Отжиг ایزوترمال (930-950 درجه سانتیگراد) معمولا برای تمیز کردن, قلاب ابزار و دیگر محصولات کوچک از فولادهای آلیاژی برای بهبود ماشینکاری با برش و افزایش سطح پاکیزگی استفاده می شود.
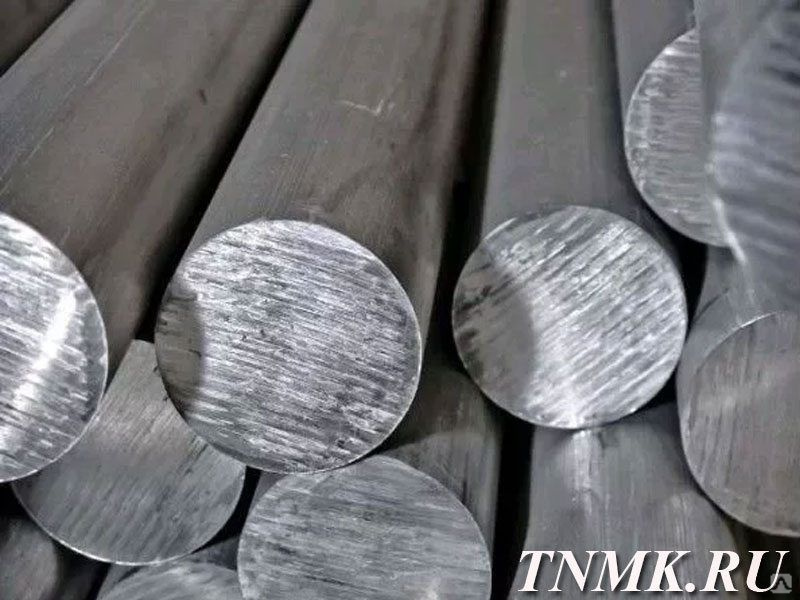
کم خنثی کردن (650-680 درجه سانتیگراد) معمولا برای تولید محصولات با کیفیت بالا از فولاد آلیاژی (برای کاهش سختی) یا فولاد کربن مورد استفاده قرار می گیرد, اگر برای ماشینکاری, سرخ کردن یا کشیدن طراحی شده باشد.
انلینگ اسفروئیدی (750 تا 820 درجه سانتیگراد) برای کاهش سختی انجام می شود, طول عمر نسبی و تنگ شدن را افزایش می دهد
انحلال همگن سازی (انتشار) (1100-1200 درجه سانتیگراد) برای شمش و ریخته گری بزرگ از فولاد آلیاژی برای کاهش جداسازی, کریستالیزاسیون (650-760 درجه سانتیگراد) استفاده می شود – برای از بین بردن کار سرد و بهبود ورق فولاد سرد شکل گرفته,
انلینگ برای از بین بردن تنش های باقی مانده (200-700 درجه سانتیگراد) برای کاهش تنش ای داخلی محصولات حاصل از ریخته گری ، جوشکاری ، برش و ره استفاده می شود.
2. عادی سازی حرارت ولاد را به دمای 850-950 درجه سانتیگراد ، رار گرفتن در معرض نور ون ننده وا می. به عنوان نتیجه ، دانه ای به دست آمده توسط ریخته گری ، نورد ، عل ا مهر و موم محصولات مخازن دن. به جای نیلینگ و سخت شدن به طور عادی استفاده می شود. ردن حرارت ولاد را به 227 تا 860 درجه سانتیگراد درجه سانتیگراد نگهداری و به سرعت خنك ردن در ب روغن یا سار ماد.
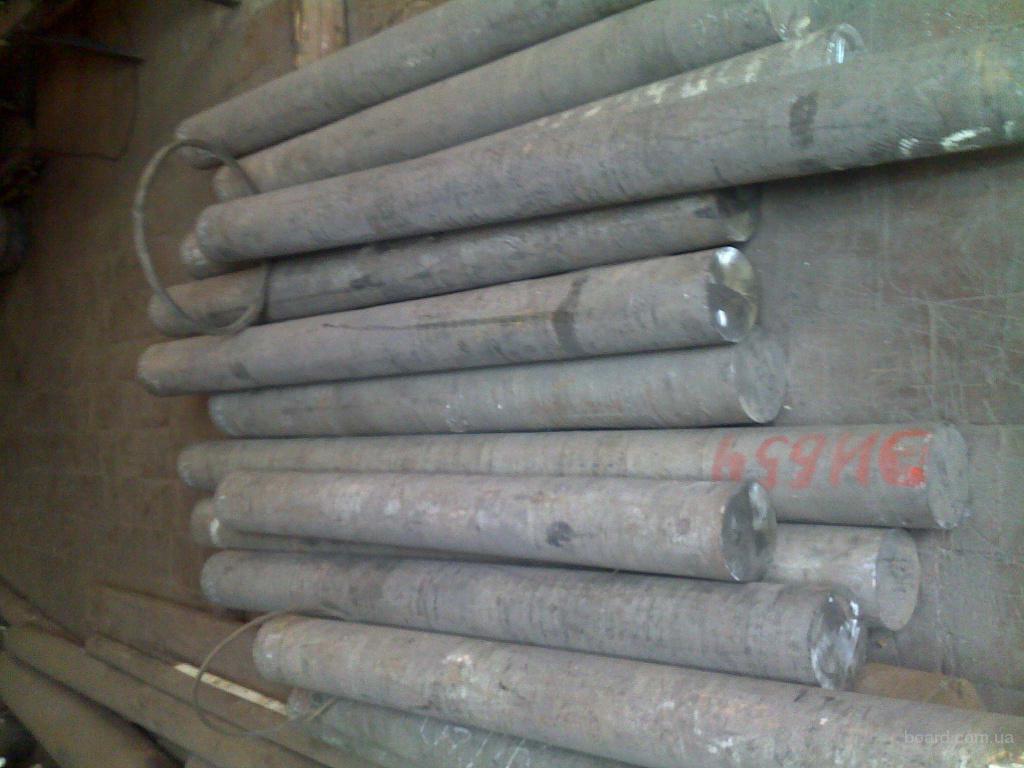
به منظور افزایش سختی, مقاومت در برابر سایش و استحکام قطعه قطعه کار, در حالی که هسته آن با چسبندگی بالا و حساس به بارهای شوک, سخت شدن سطح انجام می شود. ایع ترین نوع سخت شدن سطح با جریان حرارت القایی فرکانس بالا. برای این محصول در یک میدان مغناطیسی متناوب قرار گرفته است. رمایش به علت اثر حرارتی ریان تولید شده در محصول انجام می شود. ولادهای ربنی با کربن 0.4 تا 0.5 معمولا تحت سخت شدن القایی سطح رار می گیرند.
به منظور کاهش رطوبتی و تنش های داخلی ناشی از خشك كردن, و همچنین برای به دست آوردن فولاد با ترکیبی بهینه از مقاومت, انعطاف پذیری و سختی, آن را خنثی می شود. ان فرآیند امل گرم کردن فلز به 200-680 درجه سانتی گراد ، نگهداری و نک شدن پس از آن با سرعت خاصی است.
خنک کننده دمای پایین (برای برش و اندازه گیری ابزارهای ساخته شده از فولادهای کربنی و کم آلیاژ), دمای متوسط (برای چشمه ها و میله ها) و درجه حرارت بالا (برای فولادهای ساختاری متوسط کربن, که مورد نیاز بالا برای استقامت و مقاومت ضربه).

اختراع فرایند حرارت دادن فولاد تا 870 تا 950 درجه سانتی گراد, خنک کننده تا 450-550 درجه سانتیگراد, قرار گرفتن در معرض طولانی مدت در این دما و خنک شدن بیشتر در هوا و یا در آب است. اتراع انجام ده است تا پلاستیک سیم را قبل از چاپ بعدی آن بهبود دهد.
. در نتیجه ، مقاومت به تغییر شکل و شکست پلاستیک به ور همزمان افزایش می یابد.
مواد شیمیایی و روش های پردازش حرارتی پیشنهاد شده است تغییر نه تنها ساختار بلکه ترکیب شیمیایی سطح آن این است که با اشباع نفوذ از لایه سطح از عناصر مربوطه انجام می شود, به عنوان مثال.E رم محصول ولاد تا دمای از پیش تعیین شده و نگه داشتن آن در محیط از این عناصر. اع ترین انواع درمان ای شیمیایی عبارتند از سیمان سازی ، نیترید ، ربناتریده شدن اناتریده شدن اناترده دن سیانفدلن رد
سیمان دن (کربوریزینگ) رآیند اشباع سطح فولاد با کربن در دمای 930-950 درجه سانتیگراد است. پس از محصولات کربوریزاسیون تحت درمان رفع و معتدل کم در نتیجه, سطح آنها جامد تر می شود (در درجه حرارت تا 200- 225 درجه سانتی گراد), استقامت, استقامت خمشی و پیچشی سمان است که در یک محیط اشباع جامد یا گازی (карбюризатор ) انجام شده است.

نتردنج – اشباع سطح فرآیند فولاد با نیتروژن در حالی که حرارت به 500-650 درجه حرارت ° С در یک محیط آمونیاک توسط نیتریدی سطح فولاد با توجه به یک سختی بالا (تحت حرارت حفظ به دمای 450-550 درجه سانتی گراد), مقاومت ، مقاومت در برابر خوردگی می پوشند.
ربن تریدینگ رایند اشباع سطح فولاد در مان با کربن و نیتروژن در 840 تا 860 درجه سانتیگراد راند انتیگراد د انتراد د متواد ربن درجه سانتراد ریگدندر نتیجه سختی و مقاومت سایش لایه سطح قطعات فولادی افزایش می یابد.
سایانیت فرایند اشباع سطح فولاد در یک زمان با کربن و نیتروژن در 820 تا 950 درجه سانتیگراد در نمک های سیانید مذاب است تا سختی, مقاومت در برابر سایش و استقامت را افزایش دهد.
خسته کننده فرایند اشباع سطح فولاد بور است که در دمای 850-950 درجه سانتیگراد برای افزایش سختی آن, سایش, مقاومت در برابر خوردگی خوردگی و مقاومت در برابر حرارت است.
سیلیکونینگ فرایند اشباع سطح با سیلیکون است.

طبقه بندی و طیف وسیعی از فولاد
انواع مختلف فولاد بسته به خصوصیات تولید, ترکیب شیمیایی, بازده اکسیداسیون, کیفیت, هدف, و غیره در نظر گرفته شده است (شکل 11),
در عین حال, ویژگی اصلی طبقه بندی فولاد آن است ترکیب شیمیایی.بر این اساس ، ولاد به کربن و آلیاژ تقسیم می شود.
ولاد ربنی ولادی است که حاوی هیچ افزودنی خاص نیست. این ساختاری و سازنده است. فولاد کربنی ساختاری حاوی 0.1-0.85% С است و برای ساخت سازه ها, سازه ها, قطعات ماشین, ابزار (0.

ولاد کربنی سازه از کیفیت معمولی ، کیفیت ، و مچنین برش و ماشینکاری (خودکار) ساخته شده است.
شکل 11. بقه بندی فولاد.
.بسته به مشخصات کیفیت تضمین شده ، ن را به سه روه تحویل – A ، B و C (دول 10) تقسیم می شود.
جدول 10 ترکیب ترکیب فولاد کربنی با کیفیت معمولی
گروه های فولادی محتوای کربن,%
АВС
Ст0 BST0 – کمتر از 0.06
St 1 Bst1 VSt1 0,06-0,12
St2 BSt2 VST2 0.09-0.15
Ст3 BSt3 VST3 0.14-0.22
St4 BSt4 VSt4 0,18-0,26
St5 BSt5 VSt5 0,28-0,37
St6 BStb – 0,38-0,49
روه ولاد A توسص واص مکانیکی تامین یود. برای فولاد این گروه ، ترکیب شیمیایی تنظیم نمی شود ، از آنجا که عات ساخته شده از آن به ارت ده ا ن به ار دا رو اد اران رتاد ارادار تعداد برند بالاتر باشد ، قدرت بالاتر است ، اما ورق فولاد ایین تر است.
بسته به اخص های استاندارد شده (خواص مکانیکی) ، ولاد گروه A به سه دسته تقسیم می ود.
ولاد روه B با ترکیب شیمیایی عرضه می شود. برای فولاد این گروه ، واص مکانیکی تنظیم نشده است. ا آنجا که ترکیب میایی ناخته شده است ، قطعات از ولاد گروه B می تواند تحت درمان حرارت رار می گیرد.
بسته به اخص های استاندارد (خواص مکانیکی) فولاد گروه B به دو دسته تقسیم می شود.
ولاد روه B بر روی واص مکانیکی با نیازهای اضافی برای ترکیب شیمیایی تحویل داده می شود.بسته به شاخص های استاندارد شده (خواص مکانیکی) ،ن را به شش دسته تقسیم می شود.
علامت اری: B و C – روه ای فولاد (گروه A در علامت مشخص نمی شود) ، Ct – ولاد ، اعداد – تسعداد دد
فولاد کربنی با کیفیت معمولی, جوش, نیمه آرام و آرام تولید می شود که به ترتیب با حرف های кп, пс و сп نشان داده می شود, که بعد از شماره نام تجاری معمولی نوشته می شود. به عنوان مثال St5ps ، St3kp. نامه G نان دهنده محتوای منگنز بالا است (St3Gps) ماره در انتهای ماره رده (St3ps-2 BSt3-22) رار ماره رده (St3ps-2 BSt3-2 را رار رار ماره رده)
ولاد کربنی با کیفیت (ГОСТ 1050-74) به طور عمده در مهندسی مکانیک مورد استفاده قرار می گیرد. در مقایسه با فولاد معمولی ی نیازمندی های سخت تر برای محتوای ناخالصی مضر ، به ویژه سفر وارد نواد نو. بنابراین در ت ولاد تمام نمرات ، محتوای وگرد بیش از 04/0 درصد نیست ، سفر بیش از 0,035 درصد نیست.
ولاد ربن کیفیت ربن در نمرات 08 10 15 ، 20 ، 25 ، 30 35 40 ، 45 ، 50 ، 55 58 60 وش (KP) نیمه رام (PSرسن مرام) است. شماره در تعیین نام تجاری نشان دهنده میزان متوسط کربن در صد درصد است
با توجه به الزامات آزمون خواص مکانیکی, فولاد در پنج دسته تولید می شود و برای هدف مورد نظر آن سه زیرگروه А – برای کار گرم با فشار Б – برای ار سرد با فشار و C – برای رسم سرد استفاده می شود که در مارک منعکس شده است.برای مثال ، 30-a-2 ،, где 30 – درجه فولاد ، a – زیرگروه ، 2 – رده.
سازه های فولادی افزایش یافته و ماشینکاری بالا (ГОСТ 1414-75 Е) در نظر گرفته شده برای تولید انبوه در ماشین آلات, ابزار و ماشین آلات از بخش های مختلف دستگاه به همین دلیل نیز فولادی بدون برش تولید شده توسط این فلز از سه زیر گروه و به نام – داغ تشکیل, – برای ماشینکاریدر – برای سرما
شما به مقاله نگاه کنید (خلاصه): “ ترکیب شیمیایی فولاد “نظم S” محصولات sirovini و مواد »
رامشکین A.№
ولاد – لیاژ ناپایدار (قالب) آلیاژ ن با کربن (تا 2.14 ٪) و سایر عناصر. عمدتا از مخلوط ن با ضایعات فولادی در مبدل ای اکسیژن ، کوره های باز و وره های الکتریکی تولیود می. لیاژ ن لی که دارای بیش از 2.14 ٪ ربن است ، دن نامیده می شود.
99 درصد از کل فولاد یک ماده ساختاری در معنای وسیع کلمه است: از جمله فولاد برای سازه های ساختمانیقطعات ماشین, عناصر الاستیک, ابزار و شرایط کاری ویژه – مقاوم در برابر حرارت, ضد زنگ و غیره با کیفیت اصلی آن – قدرت (توانایی مقاومت در برابر زمانی که عملیات ولتاژ کافی), شکل پذیری (توانایی برای حفظ تغییر شکل کافی بدون شکستگی در تولید سازه, به عنوان یک اضافه بار محلی در جریان عملیات نظامی), گرانروی (توانایی جذب کار نیروهای خارجی, جلوگیری از انتشار ترک) سختی ، ستگی ، مقاومت در برابر ترک ، مقاومت در برابر سرما ، مقاومت در برابر حرارت.
برای تولید از اطاقان به ور گسترده ای استفاده می ود توپ تحمل ولاد روم SHh25 و SHh25SG. استحکام بر روی بلبرینگ دارای سختی بالا ، مقاومت و استقامت است.
مه ها ، مه ها و دیگر عناصر الاستیک در مینه تغییر شکل الاستیک ار می کنند. در عین حال ، بسیاری از آنها در معرض بارهای چرخه ای قرار می گیرند. بنابراین, الزامات اساسی برای فولاد بهار – این ارائه ارزش های بالای کشش, عملکرد, استقامت, و همچنین مقاومت در برابر شکستگی شکننده و شکننده (55C2, 60C2A, 50HFA, 30X13, 03Х12Н10Д2Т) است.
فولاد با استحکام بالا دارای استحکام بالا با ورق کافی (فولاد آلیاژی متوسط 40Xh3MA), استحکام ساختاری بالا, حساسیت کم به برش, مقاومت بالا در برابر شکستگی شکننده, آستانه کم شیبداری سرد, قابلیت جوشکاری خوب است.
بقه بندی ولاد و لیاژهای تولید شده:
- ترکیب شیمیایی ؛
- با ترکیب ساختاری ؛
- با کیفیت (با روش تولید و محتوای ناخالصی مضر) ؛
- با توجه به درجه اکسیداسیون و بیعت خرد شدن فلز در قالب ؛
- به مقصد
ترکیب میایی
با توجه به ترکیب میایی ، ولادهای کربن به بسته های مختلف ربن تقسیم می
- ربن کم – متر از 0.3 ٪ C ؛
- ربن متوسط - 0,3 … 0,7 C ؛
- ربن بالا – بیش از 0.7 ٪.
برای بهبود خواص فن آوری آلیاژ فولاد. فولاد آلیاژ نامیده می شود که در آن علاوه بر ناخالصی های معمولی, عناصر آلیاژی به ویژه در ترکیبات خاص (Cr, Ni, Mo, Wo, V, Al, В, Тл و غیره) و همچنین Mn و Si در مقادیر بیش از محتوای مشترک به عنوان ناخالصی ای تکنولوژیکی (1 و و بالاتر). به عنوان یک انون ، بهترین خواص توسط دوپینگ پیچیده ارائه می شود.
در ولادهای آلیاژی ، بقه بندی آنها بر اساس ترکیب شیمیایی با درصد کل عناصر آلیاژی تعیین می ود:
- م آلیاژ – متر از 2.5 ٪ ؛
- دودکش متوسط - 2,5 … 10
- بالا آلیاژی – بیش از 10 ٪.
ترکیب ساختاری
ولاد و لیاژهای لومینیوم به ترتیب با ترکیب ساختاری نآا ترکیب ساقتاردا ترکیب ساختاریدا ترکیب ساختاریدا ترهب ساختاریدا به بقاتاریدا به بقاتاریدا به بقاتارید:
- در حالت انجماد – доэвтектоид ، заэвтектоид ، ледебурит (کاربید) ، ферритный ، аустенитный ؛
- در حالت نرمال – مروارید ، مارتنزیتی و معتبر.
فولاد کربنی و آلیاژ با مقادیر کم عناصر آلیاژی به کلاس مروارید, مارتنزیت – با محتوای بالاتر و آستنیتی – با محتوای بالا از عناصر آلیاژی نسبت داده می شود.
بقه بندی فولاد با محتوای ناخالصی با کیفیت, یعنی به روش تولید و محتوای ناخالصی, فولاد و آلیاژها به چهار گروه تقسیم می شوند
مقیاس های فولادی با کیفیت
дом | S ، ٪ | P ، ٪ |
ت معمولی (معمولی) | متر از 0,06 | متر از 0,07 |
کیفی | متر از 0,04 | متر از 0,035 |
با کیفیت بالا | متر از 0.![]() | متر از 0,025 |
با کیفیت وق العاده | متر از 0,015 | متر از 0,025 |
ولاد با کیفیت معمولی (معمولی) در ترکیب شیمیایی – ولاد بربنی حاوی 0,6 C است. ان ولادها در مبدل ای با استفاده از اکسیژن و ا در کوره های بزرگ باز شسته می شوند. نمونه از این ولادها STO ولاد ، StZsp ، St5kp است.
ولاد با کیفیت معمولی ، ارزانترین است در واص مکانیکی به ولادهای دیگر کلاس ها ایین تر است.
در ترکیب میایی ولاد ربن و ا دوتایی (08kp ، 10ps ، 20) است. آنها همچنین در مبدلها و یا در کوره های سرامیکی اصلی ذوب می شوند, اما با توجه به شرایط سخت تر برای ترکیب فرآیندهای شارژ, ذوب و ریخته گری ذوب می شوند.
فولادهای کربنی با کیفیت معمولی و کیفی از لحاظ درجه اکسید شدن و طبیعت خرد شدن فلز در قالب به حالت آرام, نیمه آرام و جوش تبدیل شده است. ر یک از این ونه ها در محتوای اکسیژن ، نیتروژن و دروژن متفاوت است. بنابراین در فولادهای جوش دارای بیشترین تعداد این عناصر است.
فولاد با کیفیت بالا عمدتا در کوره های الکتریکی و به ویژه با کیفیت بالا ذوب می شود – در کوره های الکتریکی با استفاده از الکترو اسلاژ ریخته گری (СОЭ) یا سایر روش های پیشرفته, که ضمانت افزایش خلوص فلزات غیرمولتی (محتوای گوگرد و سفر متر از 0,03) و محتوای از ، واص مکانیکی. انها مانند ولاد 20A ، 15X2MA است.
تبدیل شد به کیفیت بسیار بالابه خصوص ولادهای با کیفیت بالا تحت ریزش الکتروشلژ قرار می گیرند ، تمیز کردن موثر از سولفید ا و سید.این فولادها تنها با دوده کار می کنند. نها در کوره ای الکتریکی و روش های الکترود متالورژی خاص تولید می شوند. حاوی بیش از 0.01 ورد و 0.025 سفر. به عنوان مثال: 18HG-Sh ، 20HGNTR-Sh.
بقه بندی طبقه بندی شده توسط هدفبا هدف فولاد و لیاژها به ساختار ، ابزار و ولاد با خصوصیات و میایی خاص طبقه بندی می شوند.
ولاد سازه ای فولادهای ساختمانی معمولا به ساخت و ساز تقسیم می شوند مهر زنی سرد, مقاوم در برابر خوردگی, مقاوم در برابر حرارت, مقاوم در برابر حرارت, مقاوم در برابر سایش, مقاوم در برابر سایش, بهبود یافته, بالا قدرت, بهار فنر.
ولادهای ربنی با کیفیت معمولی و مچنین فولادهای کم آلیاژ به ولادهای ساختمانی اشاره شده است. الزام اصلی برای ساخت فولاد ، قابلیت جوشکاری وب آنهاست. به عنوان مثال: С255, С345Т, С390К, С440Д.
ولاد برای قالب سازی سرددرخواست مهر و موم سرد محصولات ورق از ولاد با کیفیت ایین با کیفیت 08Yu 08ps و 08kp.
ولاد وش داده دهولاد سمان برای تولید عات استفاده می شود در رایط سایش سطوح ار می ند و بارهای دینامجر دات دنامیکیر دا.توسط سمان امل ولاد م ربن حاوی 0.1-0.3 ربن (младше 15–20–25) فولادهای لیاژی (15X 20X ، 15HGNHZ 18HZHZH 18HZH3 18HZH, 18HZH3, 18HZH, 18HZH, 18HZ, 20H3, 20H, 15HZHZ
ولاد بهبود یافتهولادهای رفته امل ولادهایی هستند که تحت بهبود قرار می رند – درمان گرما ، امل ردن وردن نك نكباق. این شامل فولادهای کربنی متوسط (35, 40, 45 و 50), فولادهای کروم (40X, 45X, 50X), فولاد کروم با بور (Zohra, опыт + 40), کروم نیکل, کروم-سیلیکون منگنز, فولاد کروم-نیکل مولیبدن .
ولاد با مقاومت بالا فولاد با استحكام بالا كه در آن انتخاب ترکیب شیمیایی و عملیات حرارتی به استحكام كششی تقریبا دو برابر نسبت به فولادهای ساختاری معمولی می رسد. ان سطح از درت را می توان در ولادهای لیاژ متوسط ربن مانند ZOHGSN2A ، 40KhNMA ، Zدرت را می توان در ولادهای لیاژ متوسط ربن مانند ZOHGSN2A ، 40KhNMA ، Zدرت را م توان در ولادها
ولاد بهار (بهار و بهار) واص الاستیک را برای مدت زمان ولانی حفظ می کند ، را دارایاسرتودبهار شامل فولادهای کربنی (65, 70) و فولادهای آلیاژی با عناصر است که باعث افزایش حد الاستیک – سیلیکون, منگنز, کروم, تنگستن, وانادیوم, بور (60С2, 50ХГС, 60С2ХФ, 55ХГРЫ) می شود.
ولاد اتاقانبلبرینگ (بلبرینگ) ولاد دارای قدرت بالا ، مقاومت در برابر سایش و استقامت است. برای تحمل ، تقاضای افزایش افته برای عدم وجود گنجایش های مختلف ، ماکرو و میکروپوریت را تحمیل می دن. استحکام برشی معمولا با یک مقدار کربن بالا (حدود 1 ٪) و حضور کروم (ШХ9 ، ШХ25) مشخص می شود.
ولاد اتوماتیک ولاد اتوماتیک برای ساخت قطعات ر بحرانی تولید انبوه (پیچ ، پیچ و مهره ، ل و ره) استفاده می شود.تکنولوژی متالورژیکی موثر برای افزایش قابلیت کارکرد ماشینکاری, معرفی سولفور, سلنیوم, تلوریم و سرب به فولاد است که باعث تشکیل تراشه های کوتاه و شکننده می شود و همچنین اصطکاک بین برش و تراشه را کاهش می دهد. کمبود فولادهای اتوماتیک – انعطاف پذیری کم. ولاد اتوماتیک امل فولاد A12 ، А20 ، АЗО ، А40Г ، АС11 ، АС40 ، АЦ45Г2 ، АЦЦЗОХМ ، АС20ХГНМ می باشد.
فولاد مقاوم در برابر سایش برای اجزای فعال در شرایط اصطکاک ساینده, فشار و شوک (آهنگ های قورباغه راه آهن, آهنگ های وسایل نقلیه ردیابی, گونه های سنگ شکن, ملاقه رثمفرسو, سطل بیل مکانیکی, و غیره) استفاده می شود – به عنوان مثال مقاوم در برابر فولاد – منگنز 110G13L ولاد.
ولاد ضد نگ مقاوم در برابر وردگی (فولاد ضد نگ) ولاد د نگ مقاوم در برابر وردگی (فولاد ضد نگ) – ولاد د نگ) – لاد لیاژی با محتوای روم (حداقل, 12 лет). روم یک لم اکسید محافظ (منفعل) را روی سطح محصول ایجاد می کند. کربن در فولاد ضدزنگ – عنصر نامطلوب ، و بیشتر کروم ، مقاومت خوردگی بالاتر است.
ساختار برای مشخصه ترین آلیاژها برای این منظور می تواند باشد:
- اربید رتی و مارتنزیت (12X13 ، 20X13 ، 20X17h3 ، 30X13 ، 40X13 95X18 – برای رسانه های ضعیف ورنده (ها هه
- ریتیک (15X28) – برای محلولهای اسید نیتریک و سفریک ؛
- аустенитный (12Х18НЮТ) – در آب دریا ، آلی و اسید نیتریکقلیایی ضعیف
- مارنزیت ری (Yuh27N13MZT ، 09h25N8Yu) – در اسید فسفریک ، استیک و لاکتیک.
لاژ 06HN28MT تواند در رایط گرم (تا 60 درجه سانتیگراد) سفر و سولفوریک (لظت تا 20) اسیدها عم.
فولاد و آلیاژهای مقاوم در برابر خوردگی, بسته به پرخاشگری محیطی که از آنها استفاده می شود, و طبق خواص اولیه مصرف کننده خود, به خواص مقاوم در برابر خوردگی, مقاوم در برابر حرارت, مقاوم در برابر حرارت و فرسایش طبقه بندی می شوند .
محصولاتی که از فولادهای مقاوم در برابر خوردگی (تیغه های توربین, سوپاپ هیدرولیک, چشمه ها, سوزن های کربورتر, دیسک ها, شفت ها, لوله ها و غیره) در دمای عملیاتی تا 550 درجه سانتیگراد عمل می کنند.
ولاد مقاوم در برابر حرارت ولاد مقاوم در برابر حرارت ادر به ار در حالت بارگذاری شده در دمای بالا برای مان دالا برای مان ا رابر ارتربراربراربربرارتارتارت ارتارت ارارت ارارت ارارت ارت ان فولادها و لیاژها برای ساخت لوله ها ، ر ، بخارات و قطعات توربین گاز (روتور ، تیغه ، دیسک ا)
برای فولادهای مقاوم در برابر حرارت و مقاوم در برابر حرارت, کربن کم (0.1-0.45% С) و بالا آلیاژ (Si, Cr, Ni, Со و غیره) استفاده می شود. فولاد و آلیاژهای مقاوم در برابر حرارت در ترکیب آنها لعنتی حاوی نیکل است, که باعث افزایش قابل توجهی در حد مقاومت در برابر خوردگی طولانی مدت می شود با افزایش کمی در مقاومت و مقاومت موقت و منگنز.نها ممکن است بیشتر با مولیبدن ، تنگستن ، نیوبیم ، تیتانیوم ، بور ، د و دیگران است. بنابراین آلیاژ микролегирования با بور و فلزات خاکی کمیاب زمین قلیایی و برخی را بهبود می بخشد ویژگی هایی مانند تعدادی از انقلاب شکل پذیری پیچشی و چقرمگی در دمای بالا.
دمای عملیاتی آلیاژهای مدرن با درجه حرارت بالا تقریبا 45-80 ٪ از نقطه ذوب است. ان ولادها بر اساس دمای عملیاتی (ГОСТ 20072-74) بقه بندی می وند:
در 400-550 ° С – 15ХМ ، 12Х1МФ ، 25Х2М1Ф 20ХЗМВ
د 500-600 ° С – 15Х5М ، 40ХЮС2М ، 20X13 ؛
در 600-650 درجه سانتیگراد – 12Х18Н9Т ، 45Х14Н14В2М ، ЮХЦН23ТЗМР ،
ХН60Ю ، ХН70Ю ، ХН77ТЮР ، ХН56ВМКЮ ، ХН62МВКЮ.
مقاوم در برابر (مقاومت در برابر اکسیداسیون) فولاد درجه حرارت مقاومت شیمیایی در برابر سطح شکست در گازهای, از جمله گوگرد در حرارت + 550-1200 درجه سانتی گراد در گازهای کوره هوای (15X5, 15H6SM, 40H9S2, ZOh23N7S2, 12×17, 15X28 ), اکسید کننده و از науглероживания محیط ها (20х20Н14С2, 20Х23Н18) و در حالت بارگیری شده یا به آرامی بارگذاری می شوند, زیرا می توانند تحت استفاده از بارهای بزرگ نشان داده شوند. ولاد مقاوم در برابر حرارت با درجه حرارت اکسیداسیون شدید مشخص می شود.مقدار این درجه حرارت توسط مقدار کروم در لیاژ تعیین می شود. بنابراین با دمای 15 Cr از عملیات محصولات + 950 ° C و و در 25 ٪ Cr تا + 130СГС است. ولاد مقاوم در برابر حرارت نیز با نیکل ، سیلیکون و لومینیوم آلیاژی می شود.
فولاد مهندسی برودتی و آلیاژهای (ГОСТ 5632-72) در ترکیب شیمیایی کربن پایین (0,10% С) و بالا (کروم, N1, منگنز, و غیره) فولادهای آستنیتی (08h28NYU, 12h28NYUT, OZh30N16AG6, OZh23AP9 و همکاران). واص اصلی مصرف نندگان این فولادها ، لاستیک و ویسکوزیته هستند که با کاهش درجه حرارت (ا کاهش درجه حرارت ا اهش درجه حرارت ا اهش درجه حرارت اتا -196) ادب ان ان اتا -196 ارتن ادب ان ان ان ان اتا -196)کاهش شدید ویسکوزیته شیمیدان سرد وجود ندارد. فولادهای ساخت ماشین آلات سرامیکی بر اساس دمای عملیاتی در محدوده -196 -296 تا درجه سانتیگراد طبقه بندی می شوند و برای تولید بخش هایی از تجهیزات برودتی استفاده می شوند.
ولاد ابزار ولاد ابزار برای برش ، ابزار اندازه گیری ، فولاد های دندانه ای تقسیم می شود.
برا برش ابزار باید قادر به حفظ سختی بالا و ابلیت برش برای مد مان ولانی ادر به ح سختی بالا و ابلیت برش برای مد مان ولانی الاز مرلت.ابزار کربن آلیاژی ، فولاد با سرعت بالا به عنوان فولاد برای ابزار برش اساده می شود.
ولاد ابزار ربنولاد ابزار ربنی 0.65–1.32 ٪ ربن است. ب عنوان مثال انواع ولاد U7, U7A, U13, U13A. علاوه بر فولادهای کربنی غیرمجاز ، این گروه نیز به طور معمول شامل ولادهای حاوی مقادیرا حاوی مقادیراا حاوی مقادیریاسای امل ولادها حاوی مقادیریاساا حاوی مقادیری ااسارتن اسرتن اسرتن اسرتن اسرتن اسرتن ارتن ارتن ارتن ارتن ارتن,
ولاد آلیاژیان روه از ولادها امل فولاد حاوی عناصر آلیاژی در مقدار 1 تا 3 درصد است.ولاد آلیاژی دارای مقاومت بالای حرارت (در مقایسه با فولاد کربن) بالاتر از + 300 درجه سانتیگراد است. ولاد 9HS به طور گسترده ای استفاده می شود (مته ، میلز ، مع ها) ، CVG (بروشور ، رامرز) ، HVGS (رتاد رع ا)
ولاد با سرعت بالا فولاد با سرعت بالا برای ساخت ابزارهای مختلف برشکاری با سرعت بالا برش استفاده می شود, از آنجا که مقاومت در برابر حرارت بالا – تا + 650 درجه سانتی گراد است. بیشترین استفاده از ولادهای با سرعت بالا از نمرات P9, R18, R6M5, R9F5, RyuK5F5 است.
ولاد ابزار برای اندازه ری ابزار (کاشی ، سنج ها ، قالب ها). معمولا ولاد U8 … U12 ، X ، 12X1 ، HVG ، h22F1 استفاده می شود. براکت ای اندازه گیری ، مقیاس ها ، حاکمان و دیگر دستگاه های صاف و بلند ساخته ده از ورق ساخته د از ورق سات د از ورق سات د از ورق سات د از ورق سات د از ورق سات د از ورق سات 15 15 تولادی 15 15Xاد 15. برای به دست وردن یک سطح کار با سختی بالا و مقاومت در برابر سایش ، ابزارها سیمان و سخت می وند.
وب شدنولاد د نگ دارای سختی بالا و مقاومت در برابر سایش ، سختی ری و مقاومت در برابر حرارت است.
مر و موم الباین فولادها باید دارای سختی بالا, مقاومت در برابر سایش و مقاومت باشند, همراه با ویسکوزیته کافی, باید مقاوم در برابر حرارت باشند. . در بسیاری از موارد برای ساخت تمبر برای قالب سازی سرد ، از فولادهای با سرعت بالا استفاده می شود.
ولاد مهر نی داغ می میرد این فولادها باید دارای ویژگی های مکانیکی بالا (مقاومت و چقرمگی) در دمای بالا باشند و دارای مقاومت در برابر سایش, مقاومت در برابر پوسته شدن, مقاومت بالا و هدایت گرمائی بالا باشند. 5XNM, 5XHB, 4XZWMF, 4X5V2FS, Zh3V8F, 4X2V5MF, ا از این ولادها هستند.
این فولادها برای کار, پشتیبانی و دیگر رول های میلز نورد, باند های رول پشتیبانی کامپوزیت, چاقو برای برش های سرد فلز, سوراخکاری و مشت ها استفاده می شود. ولاد نورد امل انواع ولادی مانند 90HF ، 9X1 ، 55X ، 60XH ، 7h3SMF می باشد.
الزامات ولاد برای رول
سختی بالا برای اطمینان از سختی بالا, لازم است از این نوع از فولادها استفاده شود, پایداری آستنیت بیش از حد خنک که در هر دو منطقه تحول, در صورت امکان, برای توسعه مارتنزیتی در طی دوره حداقل سرعت برای خنک کردن, به عنوان مثال ، در روغن.
سختی ری عمیق سختی پذیری عمق لایه سخت شده یا به عبارت دیگر عمق نفوذ مارتنزیت است. این بستگی به ترکیب شیمیایی ، اندازه قطعات و شرایط خنک کننده دارد. عناصر آلیاژ و همچنین افزایش مقدار کربن (0,8%) در فولاد, موجب افزایش سختی آن می شوند, بنابراین سخت شدن مورد نیاز با بهینه سازی ترکیب شیمیایی فولاد ارائه می شود. برای این نوع ولاد ، تقریبا از ریق سخت شدن ، لازم است ، را این امر سختی ررا ان امر سخت رول ران امر ستی رول را تضمین می نات در میان عناصر که باعث افزایش سختی پذیری – سیلیکون و بور می شود.
مقاومت در برابر سایش . لازم برای عملیات بدون دردسر اردوگاه. در مقاومت در برابر سایش اد ، تشکیل ذرات سایشی از سایش اتفاق نمی افتد ، سیتم بلبرینگ بیشتر قابل اعتم داد ابل عتم داد.
تماس با قدرت بالا . استحکام تماس لایه اری رول ا باید بیشتر از استرس های تماس در ول روند نورد باشد ، با توجه بهب.
حداقل رایش به تغییر ل و اصلاح در ول عملیات حرارتی و ابعاد بدون تغییر در ول عملیات.
ماشینکاری مطلوب در ول ماشینکاری ، سیاب و سیاب برای اطمینان از لوص بالا ازمنان از لوص بالا ازحالا را الاتالالان را امنان از لوص بالا ازحالالان را امنان از لوص بالا ازالالالران را بالالاالالالر را
.
کلاس: فولاد سازه ای
استفاده در صنعت: توپ تا قطر 150 میلی متر, غلطک تا قطر 23 میلیمتر, حلقه های متحرک با ضخامت دیواره تا 14 میلیمتر, بوشینگ های پیستونی, پیستون ها, دریچه های فشار, مکانیزم ای تفنگ اسپری ، لطک های تیغه ای و دیگر قطعات نیاز به سختی بالا ، مقاومت در برابر سایش ودر ترتاس.
ترکیب میایی در ٪ ولاد SHh25 | ||
سی | 0,95 – 1,05 | |
سی | 0,17 – 0,37 | |
Mn | 0,2 – 0,4 | |
цена | تا 0.![]() | |
S | до 0,02 | |
п. | 0,027 | |
Возраст | 1,3 – 1,65 | |
Cu | تا 0,25 | |
ن | ~ 96 |
نالوگ ای خارجی فولاد درجه شخ 15 | |
Обновить | 52100 G52986 ، J19965 |
لمان | 1.3505 ، 100Cr6 ، 102Cr6 |
اپن | SUJ2 ، SUJ4 |
رانسه | 100C6 ، 100Cr6 ، 100Cr6RR |
انگلستان | 2S135 534A99 ، 535A99 |
Обновить اروپا | 1,3505 ، 100Cr6 |
ایتالیا | 100Cr6 |
اسپانیا | 100Cr6 ، F.![]() |
номер | GCR15 |
سوئد | 2258 |
بلغارستان | Щ25 |
مجارستان | GO3 |
لستان | Lh25 |
Официальный сайт | RUL1 ، RUL1v |
مهوری چک | 14100, 14109 |
استرالیا | 5210 |
ره نوبی | СТБ2 ، СТБ4 |
Наименований: 7812 Наемников: Наемников: Наемников на 15 часов. درجه حرارت ورج ، ° С: حرارت ورج ° С: از 1150 ایان 800. بخش تا 250 میلیمتر در حرارت ورج ا سختی مواد: HB 10-1 = 179-207 МПа دما نقاط بحرانی: Ac 1 = 724 Ac 3 (Ac m) = 900 ، Ar 3 (Arc m) = 713 ، Ar 1 = 700 ، Mn = 210 رم نورد با HB 202 σ در = 740 МПа K υ tv. spl = 0.9 و K υ b.st = 0.36 جوج ری: روش وشکاری КТС. Версия: Версия Просмотров: Просмотров Размер: Модель |
واص مکانیکی فولاد ØX15 | |||||||
عت تحویل حالت حرارتی | بخش صلیب میلیمتر | σ 0.2 (МПа) | σ در (МПа) | δ 5 (%) | ψ % | KCU (Дж / см 2) | HB Цена |
часов 800 часов 10-20 пользователей 24 часа | – | 370-410 | 590-730 | 15-20 | 35-25 | 44 | (179-207) |
روبت 810 درجه سانتیگراد ، ب تا 200 درجه سانتیگراد ، سپس روغن.تعطیلات 150 درجه سانتی راد وات | 30-60 | 1670 | 2160 | – | – | 5 | 62-65 |
واص مکانیکی ولاد ШХ15 بسته به درجه حرارت رطوبت | ||||||
حرارت ، ° C | σ 0،2 (МПа) | σ در (МПа) | δ 5 (%) | ψ % | KCU (Дж / см 2) | HRC E ( HB ) |
до 840 ° C до | ||||||
200 300 400 450 | 1960-2200 1670-1760 1270-1370 1180-1270 | 2160-2550 2300-2450 1810-1910 1620-1710 | – – – – | – – – – | – – – – | 61-63 56-58 50-52 46-48 |
سخت شدن 860 درجه سانتی راد رون | ||||||
400 500 550 600 650 | – 1030 900 780 690 | 1570 1270 1080 930 780 | – 8 8 10 16 | – 34 36 40 48 | 15 20 24 34 54 | 480 400 360 325 280 |
واص مکانیکی ولاد ШХ15 با توجه به دمای آزمایش | |||||
دمای آزمایش ، ° C | σ 0،2 (МПа) | σ در (МПа) | δ 5 (%) | ψ % | KCU (Дж / см 2) |
درجه در دمای 1150 درجه و نک سازی برای مایش دمای | |||||
800 900 1000 1100 | – – – – | 130 88 59 39 | 35 43 42 40 | 43 50 50 50 | – – – – |
نمونه با قطر 6 میلیمتر و ول 30 минут متر تغییر شکل داده ده و نیل شده است. نرخ تغییر شکل 16 میلی متر در دقیقه. نرخ اشتعال 0,009 1 / انیه | |||||
1000 1050 1100 1150 1200 | 32 28 20 17 18 | 42 48 29 25 22 | 61 62 72 61 76 | 100 100 100 100 100 | – – – – – |
سخت شدن 830 درجه سانتی گراد ، روغن.تعطیلات 150 درجه سانتی راد ، 1.5 ساعت | |||||
25 -25 -40 | – – – | 2550 2650 2600 | – – – | – – – | 88 69 64 |
سختی فولاد ШХ15 | ||||||||||
اصله از انتها ، میلی متر | توجه داشته باشید | |||||||||
1,5 | 3 | 4,5 | 6 | 9 | 12 | 15 | 18 | 24 | 33 | سخت دن 850 سات راد |
65,5-68,5 | 63-68 | 58,5-67,5 | 51,5-67 | 40-64 | 38-54 | 38-48,5 | 38-47 | 33-41,5 | 28-35,5 | سختی برای نوارهای سخت ننده ، HRC |
واص فیزیکی ولاد SHh25 | ||||||
T (سلام) | E 10-5 (МПа) | а 10 6 (1 / درجه) | ل (Вт / (м · град)) | ر (кг / м 3) | سی (Дж / (кг · град)) | R 10 9 (ام · متر) |
20 | 2.11 | 7812 | ||||
100 | 11,9 | 7790 | 390 | |||
200 | 15,1 | 40 | 7750 | 470 | ||
300 | 15,5 | 7720 | 520 | |||
400 | 15.6 | 37 | 7680 | |||
500 | 15,7 | 32 | 7640 |
تسیر نام تجاری ШХ15: نامه “” مارکینگ ستون ای تحمل ننده را از می ندلا ار
ویژگی ها و استفاده از فولاد SHh25: در برخی موارد, فولاد های سخت شده با سختی بالا, سخت شده توسط تحول مارنزیتی, برای قطعات بحرانی دستگاه ها و ماشین آلات استفاده می شود.
تحت رایط عملیاتی ، به ویژه تحت فشار ، تغییرات ابل توجهی در ساختار متاستاز ولاد سخت ده حتاز ولاد سخت ده رخ ار دتار متاستاز ولاد ست ده رخ ار دتار متاستاز ولاد ست ده رخ ار دتار متاستاز ولاد ست ده رخ ار دتار استاز ولاد ست ده خاستا ولاد ست ده رخ اردد ادون ابل مدтесь در حال حاضر در سمت ای ریز نشده بارگیری ، تغییرات قابل توجهی در حجم و اندازه با زمان دیده می شود. ان تغییرات به علت رآیندهای انتشار اتم کربن در مارتنزیت همراه با اهش اندازه و رآیندهای تجزیه ساناتادا ا
از طریق مشاهدات تغییرات در ابعاد نمونه های رطوبت در طی مطالعات خنک کننده و رادیوگرافی, مشخص شد که برای خنک کردن مارتنزیت در دمای اتاق, دمای خوابیده 2-4 ساعت در دمای 150 درجه سانتیگراد کافی است.برای تثبیت مارتنزیت در ول عملیات در دمای بالا ، روری است که درجه حرارت رطوبت درجه حرارت رطوبت در حرارت رطوبت در در 50-100 درجه5 ساتنت
دلیل الی تغییر در اندازه فولاد مقاوم و نثی ، آستنیت باقی مانده است. تبدیل 1 ستنیت به مارتنزیت منجر به تغییر اندازه ولاد توس.10 1,10 -4 ود که 10 مل متر برای رلا رتر را اندا. مقدار بحرانی از آستنیت باقی مانده وجود دارد ، که در زیر ن ایداری ابعاد فولاد در حدود 1 балл. 10 -5 در دمای ایین و دمای اتاق نگهداری می شود. مقدار بحرانی ستنیت نسبت به لگاریتم زمان ره سازی تغییر می ند و با افزایش دمای خشك دن و اایش دمای خشك دن و اایش دمای دن و س از ن ا
ترک تعطیلات به عنوان مثال یک مقدار بحرانی آستنیت, که پایداری ابعاد فولاد SHKh25 را برای 3-5 سال در طول 1-10 6 حفظ می کند, بعد از خنک شدن در 840 و 880 درجه سانتی گراد و خنک شدن 100 درجه سانتیگراد به ترتیب 5–10 درصد ، س از نک شدن 150 درجه سانتی راد به ترتیب 10–19 درصد است.
تعطیلات در دمای 150 درجه سانتیگراد ، تثبیت مارتنزیت در دمای اتاق ، از لحاظ بیت ستبیت باقی انر. افزایش اندازه نمونه, نشان می دهد روند تحول آستنیتی-مارتنزیتی آغاز می شود تنها پس از 20 ساعت در 150 درجه سانتیگراد شروع تجزیه آستنیت را تنها در 200 درجه سانتی گراد سختی فولاد سخت را کاهش می دهد به HRC60 مشاهده می شود. در مواردی که چنین کاهش سختی غیر قابل قبول باشد, روش اصلی کاهش آستنیت باقی مانده در ساختار فولاد سخت شده, درمان با دمای کمتر از صفر است که با موقعیت نقطه انتهایی ترانسفورمر مارتنزیتی مرتبط است.نیاز به پردازش سرد برای تثبیت اندازه دقیق ابزار اندازه گیری و دقیق بلبرینگ ابزار در تعدادی ازار در تعدادی ازار در تعدادی ازار اتاد اتار اتاد ار اتاد ار اتاد اتاد اتاد اتاد اتاد اتار اتاد ار ات اد ار اتاد اترت با این وجود, نمی توان محتوای آستنیت باقی مانده را با استفاده از روش های سرد کمتر از 4 تا 5 درصد برای اکثر فولادهای ابزار و تحمل, کاهش داد. بنابراین, برخی از محققان توصیه می کنند که ترکیبی از عملیات سرد با ضخامت کمتری در طول زمان داشته باشد که برای فولاد SHKh25 باید حداقل 10000 ساعت در 100 درجه سانتیگراد, 160 ساعت در 150 درجه سانتیگراد و 50 ساعت در 180 درجه سانتیگراد باشد.
در دمای بالا ، میزان تبدیل آستنیتی به درجه رمازدگی وابسته نیست و تنها به میزان ن متناسب است. تحت رایط عملیاتی در دمای بالا ، تبدیل آستنیت در طول یک مکانیزم باینیت انجام می ود و اسنام ود و اسنوام ود و اسنام ود و اسنام ود و اسنام ود و اسنام ود و اسنام تد و اسنات اتتدات استاتام تدات اتان اتام رتتدтесь اتاتام ار تجمعی تغییر اندازه در دماهای بالا با پایداری نسبی مارتنزیت و ستنیت باقی مانده تعیین می شود. برای محصولاتی در دمای حدود 150 درجه سانتیگراد درجه سانتیگراد ار می کنند ، برای اهش میزان ستنیت با مقیان ستنهت باقی ماندان ارداداب اردادن اردادن انتیگراد در دمای سرد -70 درجه سانتیگراد ابعاد برای 10000 ساعت در دمای اری 120 درجه سانتیگراد در رف 5 سالتثبیود می می تود.10-6 дней в неделю 120-150 человек в день 10 10-5. اایش بیشتر در ثبات ابعادی می تواند با خنک شدن در دماهای که باعث اهش کامل آستنیت باقی مانده اتنیت باقی مانده اتنیت با مانده اتنت با مانده اتنت با مانده اتنت با مانده اتنت با مانده اتنت با مانده و ترتتن اتتت برای ولاد SHh25 درجه حرارت حداقل 225-250 درجه سانتی راد است.
از آنجائیکه بیشترین ویژگی های کامل ثبات ابعاد یک ماده نشان دهنده مقاومت در برابر تغییر شکل های میکرو پلاستیکی است, علاقه به برآورد وابستگی این خصوصیات به شرایط حرارتی فولاد سخت شده است.
تحت استرس ولاد سخت ده به ور همزمان تحت فرآیندهای تبدیل واز و تغییر شکل ای میکرو پلاسیکی رات رات.در این حالت ، تغییر شکل ای میکرو پلاستیکی باعث سرعت بخشیدن به فرایندهای انتقال فاز می شود. در عین حال ، دومی منجر به کاهش شدید مقاومت در مراحل اولیه تغییر ل لاستیک شده است. اهش مقاومت در برابر تغییر شکل پلاستیک در شرایط تغییرات از و ساختاری در ادبیات لاستیک سینتیکییکییا رتار سینتیکی ا رتار ان دیده مشخصه ولاد سخت شده به سختی بالا است و منجر به تغییر اندازه عال به علت توسعه رندای رترو رستا مقاومت در برابر تغییرات میکروپلاستی نه تنها ثبات ابعاد ماده را مشخص می کند, بلکه نشان دهنده مقاومت آن در برابر سایش است, زیرا که بر اساس مفاهیم مدرن, طبیعت خستگی فراوانی دارد و به علت ایجاد تغییرات میکروپلاستی در فلز رخ می دهد.
در شرایط فاز متاستاز و حالت ساختاری, سینتیک آرامش استرس به طور مستقیم توسط فرایندهای تغییرات فاز و ساختاری که در شرایط آزمایش اتفاق می افتد کنترل می شود. در ولادهای مقاوم ده از نوع ShKh25 ، سینتیک روند آرام سازی استرس در محدوده 100-200 درجه سانتیگراد توسط. این امر با اتخاذ انرژی فعال سازی فرایندهای آرامش استرس و کاهش حجم خاص به علت تبدیل ماده مارتنزیتی, و همچنین مطابقت این تغییرات با درجه استراحت در تنش در طیف گسترده ای از درجه حرارت و مدت آزمایش, نشان داده شده است.
وابستگی محدودیت الاستیک در دمای رطوبت فولاد سخت شده در طول یک منحنی با حداکثر متفاوت است, به همان اندازه که وابستگی محدودیت الاستیک فلزات سرد به دمای آنیلینگ قبل از کریستالیزاسیون تغییر می کند. وابستگی بالا برای انواع مختلف در ترکیب فولاد – کربن, ساختاری, آلیاژ, بلبرینگ و ضدزنگ استفاده می شود که به طور گسترده ای در مهندسی دقیق و ابزار سازه توزیع می شود. مانطور از داده ای ارائه شده است ، س از اتمام مطلوب ، حد الاستیک برای ولادهای مختلف ا
مراه با افزایش حد الاستیک در ول بازپرداخت بل از انحلال ، مقاومت آرام از فولاد سخت افزایش می ادر.حداکثر مقاومت آرامش بعد از خنک شدن در دمای مشابه با حداکثر حد الاستیک مشاهده می شود, به عنوان مثال, برای فولاد ShKh25 و 11Kh28M در 250 و 350-400 درجه سانتیگراد.
واضح است افزایش مشاهده ده در مقاومت به تغییرات میکرو پلاستیکی با افزایش دما باعث اا دما باعث ااایش دما باعث اااآ دما باعث ااد اایش دما باعث ااد سبات اتات اتات اتات اتات نر اتون اتود اتود اتود اتود,
ا امیت اصی برخورد مناسب برای استفاده از تثبیت ابعاد محصولات فولادی مقاوم در درماح مقاوم در درماد مقاوم در درمان سرادرتاد ارتاد ارتاد ارتاد ارتاد ارتاد ارتاد ارتاد ارتان ارتان ارتاد بعضی از نویسندگان بر این باورند که این درمان تغییر کامل تر از ستنیت باقی مانده ستنیت باقی مانده رستنیت باقی مانده را در مقایسن ان رتنن ان رتنن ان رتنن ا رتنن, اا رتننبق این ار ، ل رایند تثبیت شامل 5-6 دوره نک کننده تا -85 درجه سانتی گراد است که ر دام با یک رتل. فرض بر این است که با هر خنک شدن بعدی, تبدیل اضافی یک بخشی از آستنیت باقی مانده به مارتنزیت اتفاق می افتد, و خنک شدن پس از خنک شدن, استرس های داخلی را که ناشی از این تغییر و خنک کننده سریع است حذف می کند . در اپن روش حرارتی از ولاد بلبرینگ اختراع ده است که امل تغییرات حرارتی ندگانه س ارت ندانه س از افزایش ثبات ابعادی به دلیل اهش مقدار آستنیت باقی مانده پس از تکرار چرخه خنک ننده سرد.
درمان سريع چندگانه, متناوب با رطوبت, باعث افزايش مقاومت در برابر تغييرات ميکروپلاستي و ثبات ابعاد فولاد کربن سخت شده مي شود.
در نتیجه درمان ترموسیکلیک مکرر ، محتوای ستنیت باقی مانده در ولاد به ور ابل تو در همان زمان ، حد الاستیک افزایش می یابد. س از 6 بار در دمای -70 و + 150 درجه سانتیگراد (حالت 2) محدودیت کشش در خم دن σ 0,001 برابر 155 кгс / мм 2 در برابر 137 кгс / мм 2 س از یک درمان تک (حالت 3) عنی حدود 13 افزایش افته است.
مقاومت رام از فولاد نیز به طور قابل توجهی افزایش یافته است.
اجازه بدهید ما یک مکانیزم ممکن برای اثر ماشینکاری چندگانه بر روی چرخه “نک ن ن ن ینی نده در دمای ان رتود ارسرتن ارتاد ارترتن ارتاد ارترتن, ن ن رت
هنگامی که فولاد به دمای منفی سرد می شود, اختلاف بین انرژی آزاد آستنیت و مارتنزیت افزایش می یابد و بنابراین تجزیه آستنیتی اضافی رخ می دهد. س از خشك ردن ، آستنيت باقيمانده تحت تأثير فشردگي همه جانبه است كه باعث تحول مارتنزيتي مي شود.با توجه به تفاوت ضرایب انحنای خطی آستنیت و مارتنزیت, مقدار این فشار بر آستنیت کاهش می یابد, زیرا آن را به دمای منفی سرد می کند, که موجب شتاب تحول مارتنزیتی می شود. تبدیل به علت تغییرات در شبکه خواهد توسط انرژی تغییر شکل الاستیک در طول شکل گیری مارتنزیت و یا تا زمانی که یک حد درجه حرارت داده شده برای مقدار مارتنزیت رخ جذب نمی شود ادامه خواهد داد تا زمانی که افزایش در انرژی آزاد, مربوط به حداقل انرژی آزاد شده است.
در رآیند رم ردن ولاد تا دمای بالای رخه و نگه داشتن در این دما ، تغییرات مارتنزیتی نیز رخ می دهد.نقض ساختار ستنیت در اطراف کریستالهای مارنزیتی که در دمای پایین تشکیل ده اند ، باعث تسریع راتالهای ارنزیتی در دمای ایین تشکیل ده اند ، باعث تسریع راتالها ان تل ده اند ، باعث تسریع راتالها رعد تسریع راتالا رعد تسریع راتالاد رعد رت تحریفات در تبدیل قبلی در آستنیت به دست می آید ، باعث ایجاد هسته دن ریستال ای مارتنزیت می ود.
علاوه بر این, بیشتر اعوجاج های کششی در آستنیت به عنوان یک نتیجه از تغییرات مارتنزیتی قبلی پس از خنک کردن به دمای منفی, نرخ تبدیل بالاتر در طول حرارت بعدی.
تحول مارنسیتیک در طی گرما ادامه خواهد یافت, در شرایط جدید, مقدار انرژی تغییر شکل الاستیک که در طول تشکیل مارنزیت ایجاد می شود, برابر با تفاوت انرژی های آزاد آستنیت و مارپنسیت می باشد.در عین حال, عوامل پایدار سازی آستنیت و تفاوت ضرایب گسترش خطی مارتنزیت و آستنیت اثر معنی داری بر روی سینتیک مولکولی شدن کریستال مارتنزیت دارند. این عوامل باعث اهش میزان تبدیل مارتنزیتی به حرارت می شود. تثبیت آستنیت ناشی از فرایندهای استراحت فلزی در طی گرمایش است: کاهش بیش از حد ولتاژ در میکروولوم, کاهش تراکم جابجایی در خوشه ها, بازتوزیع کلی جابجایی و نقاط نقطه. با توجه به تفاوت در ضرایب انبساط خطی آستنیت و مارتنزیت در گرم شدن آستنیت, ممکن است به نظر برسد فشارهای اضافی فشاری, کاهش میزان تبدیل. در هنگام گرم شدن از منهای به دمای بالا از چرخه, فرآیندهای باقی مانده نیز در مارنزیت با توزیع مجدد вывихи و نقاط نقطه, کاهش تجمع محلی вывихи و скачки в микрообъемы و افزایش پایداری مارتنزیت رخ می دهد.
تجزیه مارتنزیت پس از فرآیند استراحت رخ می دهد و بیشتر به طور قابل ملاحظه ای بیش از 100 درجه سانتی گراد مشاهده می شود و کاربید الکترونیکی در مرحله اول رسوب می کند (در محدوده 100-150 درجه سانتیگراد) و درجه تتراگونال مارتنزیت کاهش می یابد. س از جداسازی ذرات کاربید و اهش غیر یکنواختی غلظت کربن (با افزایش دمای) ، اعوجاج نوع دوم کاهش می یادب.
بنابراین, به عنوان یک نتیجه از فرایندهایی که در فولاد سخت در هنگام گرم شدن از منهای به دمای بالا TC TC 1 حرارت داده می شود, مقدار آستنیت باقی مانده کاهش می یابد و ثبات آن افزایش می یابد, تجزیه جزئی مارتنزیت رخ می دهد و ثبات آن افزایش می یابد.اهرا ، مقدار میکروسترکز در مرز فاز نیز به دلیل آرامش در ول استراحت ، م است.
در نتیجه رآیندهای برگشت ناپذیر که در طول حرارت از منهای به دمای بالا چرخه 1 انجام می ود ،انر عو. نامی که ولاد برای دمای منفی دوباره نک می شود ، محرک ترمودینامیکی برای تبدیل مارتنزیتی دوباره ات دوباره اود. با این حال, در شرایط جدید, میزان تبدیل مارتنزیتی در خنک سازی در مقایسه با تغییر در چرخه 1 به میزان قابل توجهی پایین خواهد بود, زیرا در نتیجه ترمیم اولیه آستنیت, تشکیل هسته مارتنزیت افزایش می یابد.با توجه به بقیه ستنیت در چرخه 1 توزیع در ساختار بلوری برای تشکیل هسته مارتنزیت دید کمتر مطلوب استتر.
هنگامی که در چرخه دوم گرم می شود, مناطق جدیدی از الاستی که ناشی از آستنیت هستند بوجود می آیند فرآیند شما تحولات در دمای پایین نیز باعث ایجاد هسته جدید بلورهای مارنزیت می شود, شبیه به فرآیندهای چرخه حرارت 1. در عین حال, سرعت رایندهای بسیار ایین تر است ، را مقدار مناطق جدید تحریف شده الاستیک ، کمتر ا رخه 1 است. نگامی که رخه گرمایش تکرار می شود ، فرآیند استراحت و تثبیت مارتنزیت دوباره عبور می کند.مچنین برخی از تجزیه اضافی مارتنزیت (ر کامل تر مرحله اول خلوص) وجود دارد. در نتیجه چرخه دوم TTSO, مقدار آستنیت باقی مانده بیشتر کاهش می یابد و پایداری ساختار سخت شده به طور قابل توجهی با تغییرات درجه حرارت بعدی افزایش می یابد. بنابراین س از یک دوره جدید TTs ، ایداری آستنیت باقی مانده و مارتنزیت افزایش می یابد.
ارایی TTsO محدود به ندین سیکل پردازش حرارتی (циклы 3-b) است ، افزایش بیشتر تعداد سیکل ها ناکارآمد است. مانطور که انتظار می رود ، بیشترین اثر بعد از اولین دوره درمان به دست می آید.با این حال, داده های تجربی نشان داد که برای افزایش مقاومت در برابر تغییر شکل های میکروپلاستیک, چندین دوره پردازش پس از آن نیز بسیار قابل توجه است, در طی آن تجزیه اضافی آستنیت باقی مانده و تثبیت کامل ساختار بیشتر می شود.
به عنوان یک نتیجه 3-6 برابر TCW, یک ساختار پایدار مارتنزیت با حداقل مقدار آستنیت باقی مانده تشکیل شده است که همچنین به خوبی تثبیت شده است. ساختار ایدارتر باعث افزایش مقاومت در برابر تغییرات میکروپلاستیک در ولاد سخت شده می شود.
در بالا نشان داده شده است اثربخشی درمان چندگانه سرد, متناوب با درجه حرارت پایین درجه, برای تثبیت اندازه محصولات فولاد, سخت به سختی بالا.شرکت های خارجی که از این درمان استفاده می کنند, ثبات بیشتری در ابزار اندازه گیری را تضمین می کنند تا آنچه که طبق ГОСТ 9038-90 مورد نیاز است, و آنچه که در واقع در اندازه گیری های موازی سطح هواپیما در تولید داخلی دیده می شود.
Телефон: | ||||
σ در | – مقاومت موقت (استحکام کششی) ، МПа | ε | رسوب نسبی زمانی که اولین ترک ظاهر می شود ، ٪ | |
σ 0.05 | – حد الاستیک ، МПа | ه به | – مقاومت حداکثر استحکام برشی MPa | |
σ 0À2 | – درت عملکرد رطی ، МПа | σ از | – | |
δ 5 , δ 4 , δ 10 | – ول عمر نسبی بعد از پارگی ، ٪ | σ -1 | – حد تحمل مانی که برای خمش با یک چرخه بارگذاری متقارن ، MPa مایش شده است | |
σ Sq0،05 و σ SG | – استحکام عملکرد تحت رده سازی ، МПа | Дж -1 | – حد تحمل برای تست پیچشی با یک چرخه بارگذاری متقارن ، МПа | |
ν | – تغییر نسبی ، | № | – تعداد رخه های بارگیری | |
с در | – محدودیت درت کوتاه مدت ، МПа | до до ρ | – مقاومت الکتریکی ، اهم · متر | |
ψ | – باریک نسبی ، ٪ | E | – مدول انعطاف ری نرمال ، GPa | |
KCU и KCV | – مقاومت ضربه بر روی یک نمونه با غلظتهای U و V به ترتیب Дж / см 2 تعن ده است | т | – درجه حرارت در ن واص به دست آمده ، Grad | |
с T | – محدودیت تناسب (مقاومت در برابر تغییر شکل باقی مانده) ، МПа | ل و λ | – ریب دایت حرارتی (ظرفیت حرارتی ماده) ، Вт / (м · ° C) | |
HB | – سختی برینل | سی | – رفیت حرارتی اص مواد (محدوده 20 o – T) ، [Дж / (кг · град)] | |
HV | – سختی ویکرز | номер до до | – تراکم لوگرم / متر 3 | |
سلام | – سختی راکول مقیاس C | а | – ریب درجه حرارت (خطی) سترش (دامنه 20 o – T) ، 1 / ° C | |
HRB | سختی راکول مقیاس B | σ т Т | – محدودیت درت دراز مدت ، МПа | |
HSD | – سختی ساحل | г | – مدول الاستیسیته در برش تیرهای ، GPa |
ولاد ربن به علت نه مقرون به صرفه و ویژگی ای استحکام بالا متعلق به آلیاژهای گستر است.ا نین ولادی امل ن و ربن و حداقل ناخالصی دیگر ، محصولات مختلی مهندسی ، عات لوله والولولاات التل املات لول والولابن التلات التل مندسی. این آلیاژها نیز به طور گسترده ای در صنعت ساخت و ساز استفاده می شود.
ولاد کربن چیست؟
فولادهای کربنی, که بسته به زمینه اصلی کاربرد, به فولاد ساختاری و ابزار تقسیم می شوند, عملا حاوی افزودنی های آلیاژی در ترکیب آنها نیستند. ان ولادها مچنین از لیاژهای فولادی معمولی متفاوتند ، را ترکیب نها حاوی مقدار نا حاوی مقدار نا حاوی مقدار نا حاوی مقدار بسیار حاو دار بسیار م ان انان انان انان انان مدر بسیار م
محتوای عنصر اصلی – ربن – در فولاد این دسته در محدودیت ای نسبتا گسترده ای ممکن است متفاو. بنابراین ولاد ربن بالا شامل 0.6-2 ربن ولاد کربنی متوسط - 0.3-0.6 م ربن – تالا امل 0.6-2 ربن ولاد ربنی متوسط - 0.3-0.6 م ربن – تالا امل ربن – تا 0.25 است. این عنصر نه تنها خواص را تعریف می کند فولاد کربنبلکه ساختار آنها نیز می باشد. بنابراین, ساختار داخلی آلیاژهای فولادی حاوی کربن کمتر از 0,8% در ترکیب آن به طور عمده از فریت و پرلیت تشکیل شده است, با افزایش غلظت کربن, سیمانیت ثانویه شروع به تشکیل می دهد.
ولادهای ربنی با ساختار فریتی غالب از ریق انعطاف پذیری بالا و مقاومت کم مشخص می شوند.ار ساختار ولاد توسط سیمانتتی تسلط داشته باشد ، ن را با قدرت بالا مشخص می ند اما ساتار با افزایش مقدار ربن تا 0.8-1 ، ویژگی های قدرت و سختی فولاد کربنی افزایش می یابد ، اما ابلیت ورشکس ابلت ورس ابلت ورشکس ابلت ورشکس ابلت ورشکس ابلت ورشکس ابلت ورشکس وتوبورب.
محتوای می از ربن نیز تاثیر جدی بر ویژگی ای ن آوری فلز ، به ویژه در جوش پذیری ن سهولت پردازش ربن تار ردازش رتوسوسوساا. از فولادهای متعلق به دسته کم کربن ، قطعات و سازه هایی را ایجاد می نند که در ول عملیات بارهای ادلان ادلان ادلباوات ولادهای ربنی متوسط آنها را مهمترین مواد ساختاری مورد استفاده در ساخت سازه ا واده در ساخت سا ا واد در ساخت سازه ا وحان ات ا اد در سات سا ا وحان ات سا ا وحلان ات سا ااد در سات سا ا وحلان ات سا ا وحلان ا به علت ویژگی ای ن ، برای تولید قطعات مورد نیاز برای افزایش مقاومت در برابر سایش مناومت در برابر سایش مناسب برایابر سایش مناسب برایابر سایش مناسب برای تااه
ولاد ربنی و مچنین لیاژ فولاد هر گروه دیگر شامل ناخالصی ای مختلفی استل: سیلیکون منگنی ن رون رون رون ن بعضی از این ناخالصی ا مانند منگنز و سیلیکون مفید هستند ، نها در مرحله ذوب به ولاد وارد میوگرد و سفر ناخالص مضر هستند که ویژگی های کیفیت آلیاژ فولاد را از بین می برند.
اگرچه اعتقاد بر این است که نها ناسازگار هستند ، می توان از میکرو آلیاژینگ برای بهرو لاژینگ برای بهبود خانگ را بهبود خان را بهبود اواص راتودوا راتودوا برای این منظور افزودنی های مختلف به فولاد ربن وارد می شوند: بور ، تیتانیوم ،رکونیم نارر خرونیم ،نارر رونیم نارر رونیم نانار ربن وارد می وند. البته ، با کمک این مواد افزودنی ، فولاد ضد نگ از فولاد کربن ساخته نخواهد شد ، اما می تواند د اما می تواند د اما می تواند اد اد باب اد اب باب ب
بقه بندی با درجه اکسیداسیون
داسازی ولادهای کربن روی انواع مختلف تحت تاثير پارامتر مانند درجه اکسيداسيون درجه دارد.بسته به این ارامتر ، ربن است آلیاژهای فولادی آنها به آرام ، نیمه آرام و وش تقسیم می شوند.
ولادهای املا مشخص با ساختار داخلی همگن تر می وند ؛ د اکسید دن با افزودن فریزرلیون ، فرسودگی لی و آلومینیوم به فلز مذاب انجام می شود. با توجه به این واقعیت که لیاژهای این دسته به ور کامل در کوره دی اکسید شده بودند ، ترکیب نها ستدور نا ستدور. لومینیوم باقی مانده ، مانع رشد دانه می شود ،،نین فولادی را ساختار خوبی از دانه می دهد. ترکیبی از ساختار ریز دانه و تقریبا کامل عدم وجود گازهای حل شده به شما اجازه می دهد تا فلز با کیفیت بالا را تولید کنید که می تواند مهمترین بخش ها و سازه ها را ایجاد کند.علاوه بر تمام مزایای آن ، لیاژهای فولادی ربن طبقه آرام نیز دارای یک معایب عمده هستند: اسوب ینها ترا.
. در ساختار داخلی این فولاد به علت این واقعیت که فرایند دی اکسید شدن آن در کوره کامل نشده است, گازهای حل شده وجود دارد که منفی بر ویژگی های فلزات تاثیر می گذارد. بنابراین نیتروژن موجود در ترکیب این فولادها ، به شدت بر جوش پذیری آنها تاثیر می ادر ، باعث ادو ادر باعث ادو ادر اعث ادو جادر باعث ادو ادر باعث اادو ادر باعث ا.جداسازی تولید شده در ساختار این آلیاژهای فولادی منجر به این واقعیت می شود که فلز نورد که از آنها ساخته شده, ناهمگونی را در ساختار و ویژگی های مکانی آن دارد.
موقعیت متوسط و در واص آن و و در درجه اهش اکسیداسیون اشغال ولاد نیمه رام است. بل از ریختن مقدار کمی از دی اکسید شدن به الب ها ، لز با تقریبا بدون جوش سخت می ود اا در نتیجه ، ریخته ری تشکیل می شود ، ساختار ن حاوی حباب های گاز کمتر از فولادهای وش است. نین حفره ای داخلی در فرآیند نورد فلز بعدی ، تقریبا به طور کامل وش داده می شود.بیشتر سنگهای کربن نیمه آرام به عنوان مواد ساختمانی مورد استفاده رار می گیرند.
г.
روش ای تولید و داسازی کیفیت
برای تولید فولاد کربن, فن آوری های مختلف مورد استفاده قرار می گیرند که بر جدایی آنها نه تنها با روش تولید, بلکه همچنین با ویژگی های کیفی نیز تاثیر می گذارد. بنابراین ، تمایز:
- لیاژهای فولادی با کیفیت بالا ؛
- آلیاژهای فولادی کربن با کیفیت عادی.
لیاژهای ولادی با کیفیت معمولی در کوره ای باز شونده ذوب می وند که بعد از آن مش ای بزرنگ از ولن از ولن ا تولن ا تولن. تجهیزات وب برای تولید نین فولادی نیز شامل مبدل ای اکسیژن می باشد. در مقایسه با آلیاژهای فولادی با کیفیت بالا, فولادهای مورد نظر ممکن است محتوای بالاتری از ناخالصی مضر داشته باشند که بر هزینه تولید آنها تأثیر می گذارد و همچنین ویژگی های آنها.
شمش های ساخته شده و به طور کامل یخ زده از فلز به نوبه خود بیشتر تحت تاثیر قرار می گیرند که می تواند در حالت داغ یا سرد انجام شود.روش نورد رم تولید محصولات ل و تنوع ورق و لز ورق و نوار های لزی وسیع را تولید می ند. با نورد در حالت سرد ، ورق فلز به دست می آید.
برای مقادیر با کیفیت و با کیفیت بالا می توان از دو مبدل و وره های باز و بیشتر استفاده کرد. تجهیزات مدرن – وره ذوب الکتریکی. به ترکیب میایی نین فولادهای ، حضور ناخالصی ای مضر و ر فلزی در ساختار آنها ، GOST مربوطه سدارای راتا رات راتار راتا به عنوان مثال ، ولادهایی که به عنوان کیفیت بالا بقه بندی می وند نباید بیش از 0,04 وگرد و بیش از 0.035 سفر داشته باشند. آلیاژهای فولادی با کیفیت بالا و با کیفیت بالا به علت الزامات سختگیرانه برای روش تولید و ویژگی های آنها با خلوص بالا ساختار مشخص می شود.
دامنه
مانطور در بالا ر شد ، لیاژهای فولادی ربن برای هدف اصلی به دو دسه گسترده تقسیم اا. Версия 0.65–1.32. به منظور بهبود خواص مکانیکی ابزار ، به این موارد مراجعه کنید عملیات تکنولوژیکی ، как ، بدون سخت انتا مود مراعه
لیاژهای ولادی سازه ای به طور گسترده ای در صنعت مدرن استفاده می شود. نها قطعات را برای تجهیزات برای مقاصد مختلف ، اجزای ساختاری مهندسی و اهداف ساختمانی اتصالدهن ر. به طور خاص ، یک محصول محبوب مانند سیم کربن از فولاد ساختاری ساخته شده است.
سم ربن نه تنها برای اهداف داخلی ، بلکه برای تولید اتصال دهنده ها و در نعت ساخت وساز پس از سیمان شدن, آلیاژهای ساختاری کربن می توانند به طور موفقیت آمیز برای تولید قطعاتی که در طی عملیات, سایش و پارگی های جدی را تجربه می کنند و بارهای پویای قابل توجهی را تجربه می کنند, استفاده شود.
البته, آلیاژهای فولادی کربن خواص بسیاری از فولادهای آلیاژی (به ویژه فولاد ضد زنگ) ندارند, اما ویژگی های آنها به اندازه کافی برای اطمینان از کیفیت و قابلیت اطمینان قطعات و سازه های ساخته شده از آنها نیست.
ویژگی ای علامت اری
مقررات جمع آوری که به طور دقیق توسط نقاط مربوط به ГОСТ تعریف شده است, اجازه می دهد تا نه تنها ترکیب شیمیایی آلیاژ را یاد بگیریم, بلکه همچنین می گوید که چه طبقه ای به آن تعلق دارد. در تعیین ولاد ربنی با کیفیت معمولی ، حروف “ST” وجود دارد.نقاط GOST ت عدد مرجع از این ولادها را مشخص می کنند (از 0 تا 6) در تعیین آنها نیز نشان داده شده است. برای درک اینکه درجه اکسید شدن به یک ا چند نام تجاری مربوط می شود ، می توانید “kn” د “ps” ، “cرتوانید” kn “د” ps “،” راد ا
درجه بندی از فولادهای کربن با کیفیت بالا و با کیفیت بالا به سادگی توسط اعداد نشان می دهد که محتوای کربن در آلیاژ در صد درصد است. در انتهای تعیین بعضی مارک ا می توان نامه ای “A” یافت. این به این معنی است که ولاد دارای کیفیت متالورژیکی بهبود یافته است.
ما می توانید در مورد ولاد ابزار در مقابل ما با حرف “U” که در ابتدای نشانه اری ن راپی دار. ماره ر این نامه نشان دهنده محتوای کربن است ، اما در دهم درصد است. نامه “A” اگر ن را در تعیین ولاد ابزار ، می گوید که این آلیاژ ویژگی های کیفیت.
ترکیب شیمیایی فولاد به کربن و آلیاژ تقسیم می شود. ولاد ربن با محتوای ربن بر روی:
· م ربن: متر از 0.3 ٪ ربن ؛
· ربن متوسط: 0.3-0.7 ربن ؛
· ربن بالا: بیش از 0.7 ٪ کربن.
ولاد لاژ تقسیم بر محتوای ل عناصر لیاژی بر روی:
· م لیاژ: متر از 2.5
· Кол-во: 2.5-10.0
· ربن بالا: بیش از 10.0 ٪.
بقه بندی ولاد بر اساس روش تولید و ت (محتوای ناخالصی های مضر) به ناخالصی ای مضر ناالصی ای مضر درر ولال ا مرر درال ا مر درر ولا
بسته به محتوای نها ، ولاد به موارد ر تقسیم می شود:
· ولاد با کیفیت معمولی (معمولی): تا 0,06 ٪ S ، تا 0,07 ٪ P ؛
· ولادهای کربنی: تا 0.04 S ، ت 0,035 P ؛
· ولادهای با کیفیت الا: تا 0,025 ٪ S ، تا 0,025 ٪ P ؛
· ولاد بسیار با ت: 0,015 S ، تا 0,025 ٪ P.
· ولاد با کیفیت معمولی (یا فولاد معمولی) اغلب در کوره های بزرگ باز ، مبدل ا و به مش های نرتبا نرتبا. روش تولید به طور عمده ترکیب ، ساختار و واص این فولاد را تعیین می کند. ولاد با کیفیت بالا ذوب شده به طور عمده در وره های الکتریکی ؛ دسته بندی فولاد به منظور
· فولادهای سازه ای می تواند به ساخت و ساز تبدیل شود, برای قالب سازی سرد, سیمان, بهبود یافته, مقاومت بالا, فنر بهار, بلبرینگ, اتوماتیک, مقاوم در برابر خوردگی, مقاوم در برابر حرارت, مقاوم در برابر حرارت, مقاوم در برابر سایش.
· ولادهای ساختمانی شامل فولادهای کربنی با کیفیت معمولی و مچنین فولادهای کم لیاژ است. الزام اصلی برای ساخت فولاد ، قابلیت جوشکاری وب آنهاست.
· برای مهر و موم سرد ، محصولات ورق کم کیفیت کربن استفاده می شود.
· ولاد سیمان برای تولید قطعات استفاده می شود در رایط پوشیدن سطح و با بهره ردی از بارهای روا روا.
· ولادهای مقاوم در برابر بالا بودن استحکام کششی است که در آن انتخاب ترکیب میایی و عملیات حرکیب میاو و عملیات حراوم میایی و عملیات حرارتاان سطح از درت را می توان در فولادهای آلیاژ کربن متوسط بدست آورد.
· بهار (بهار و بهار) ولادهای خواص کششی را برای مدت زمان طولانی حفظ می کند ، را دارای ند ، را دارای ولادهای ربنی (65 ، 70) و لولادهای آلیاژی با عناصر که باعث افزایش حد الاستیک می وند – سیلیکون ،،ز
· بلبرینگ (بلبرینگ) ولاد دارای قدرت بالا ، مقاومت در برابر سایش ، استقامت. برای تحمل ، تقاضای افزایش افته برای عدم وجود گنجایش های مختلف ، ماکرو و میکروپوریت را تحمیل می دن.معمولا ولادهای بلبرینگ با محتوای کربن بالا (حدود 1) و حضور روم مشخص می ود
· فولادهای مقاوم در برابر شستشو برای قطعاتی که تحت شرایط اصطکاک سایشی, فشار بالا و اثرات (مسیرهای متقاطع مسیرهای راه آهن, ردیابی ماشین آلات ردیابی, گونه های شکن, ماشین آلات حفاری, سطل های خاکبرداری و …) استفاده می شود .
· فولادهای مقاوم در برابر خوردگی و آلیاژها, بسته به پرخاشگری محیطی که از آنها استفاده می شود, و طبق خصوصیات مصرف کننده اولیه خود, به خواص مقاوم در برابر خوردگی, مقاوم در برابر حرارت, مقاوم در برابر حرارت طبقه بندی می شوند
· محصولات تولید شده از فولادهای مقاوم در برابر خوردگی (تیغه های توربین, سوپاپ هیدرولیک, چشمه ها, سوزن های کربورتر, دیسک ها, شفت ها, لوله ها و غیره) در دمای عملیاتی تا 550 درجه سانتیگراد عمل می کنند.
· ولادهای مقاوم در برابر حرارت قادر به ار در حالت لود شده در دمای بالا برای در دمای بالا برای مابرحالا برا مان اص رترتا ارتا ارترتا ارترت ارت ارت ارت رتا ا رتا ارترت ارت ارت ارت ارت رت رت ان فولادها و لیاژها برای ساخت لوله ها ، ر ، بخارات و قطعات توربین گاز (روتور ، تیغه ، دیسک ا)
· فولادهای مقاوم در برابر حرارت (مقیاس مقاوم) مقاوم در برابر تخریب شیمیایی سطح در رسانه های گازی, از جمله گوگرد حاوی, در دمای + 550-1200 درجه سانتی گراد در هوا و کوره گاز است.
· ولادهای ابزار برای برش ، ابزار اندازه ری ، فولادهای خشک به ولادها تقسیم می وند.
· ولاد برای برش ابزار باید قادر به حفظ سختی بالا و ابلیت برش برای مدت مان ولانی از مرل. ابزار کربن آلیاژی ، فولاد با سرعت بالا به عنوان فولاد برای ابزار برش اساده می شود.
· وب فولاد دارای سختی بالا و مقاومت در برابر سایش ، سختی ری و مقاومت در برابر حرارت است.
بلیط 26 لزات ر نی الص معمولا به ندرت استفاده می شوند ، اغلب با استفاده از آلیاژهای مختلف. از جمله فلزات آهنی غیر آهنی در مهندسی مکانیک, آلیاژهای سبک – آلومینیوم, منیزیم و تیتانیوم – و همچنین مس و آلیاژهای آن, آلیاژهای مبتنی بر نیکل, آلیاژهای برای بلبرینگ, مواد نیمه هادی و آلیاژهای با مقاومت بالا بر اساس فلزات مقاوم است.
لومینیوم لومینیوم و لیاژهای آن با قدرت ویژه خاص مشخص می وند که نزدیک به مقادیر ولادسنتنتا ستآتلسنتا ستداا ستدانتا. لومینیوم و لیاژهای آن به خوبی به تغییرات رم و سرد پاسخ می دهند ، وش نقطه ای و لیاژهای اصن ا لومینیوم الص به خوبی از خوردگی محافظت می کند ، را یک لم متراکم از اکسید لومینیوم بر لرا سطح تسد. افزودنی ای آهن و سیلیکون سبب افزایش آلومینیوم می شوند ، اما باعث کاهش مقاومت در براومت در برابر ورد و نعاان.لومینیوم الص برای کابل وا و عات الکتریکی هدایت می شود اما عمدتا آلومینیوم برای تولید آلیاژ اتود آلیاژ اتود.
МАГНИЯ تراکم کم منیزیم و آلیاژهای آن در ترکیب با نیروی خاص و نزدیک به آن خواص فیزیکی و شیمیایی آنها را برای استفاده در حوزه های مختلف مهندسی مکانیک به کار می برد: خودرو, مهندسی ابزار, تولید هواپیما, هوا فضا, مهندسی رادیو و دیگران. داغ آلیاژهای منیزیم به خوبی به انواع مختلف پردازش با فشار – ار دادن ، جعل ، نورد.
تیتان تیتانیوم داراي واص مکانیکی بالا ، استحکام خاصی در دمای اتاق و دمای ریوژن و مچنین مقاتوب.واص مکانیکی تیتانیوم به شدت به محتوای ناخالصی بستگی دارد. مقدار کمی از اکسیژن, نیتروژن و کربن باعث افزایش سختی و مقاومت می شود, اما در عین حال مقاومت در برابر خوردگی و پلاستیکی به طور قابل توجهی کاهش می یابد, قابلیت جوش پذیری و تمیز شدن آن کاهش می یابد. دروژن به خصوص مضر است ، صفحات نازک هیدرید را در امتداد مرزهای دانه تشکیل می دهد که لز را بهن دیت رد د رد د رد. برای قطعات بسیار مهم ، تیتانیوم خالصی را خالص می کنند.
COPPER مشخصه ترین واص مس الص ارزش بالای هدایت الکتریکی ، دایت حرارتی و مقاومتدر برارتی وردگی و است.به علت ابلیت انعطاف ری بالا ، مس خالص در حالت های رم و سرد تغییر شکل می یابد. در فرایند تغییر شکل سرد ، مس از بین می رود و تقویت می شود. بازسازی لاستیسیته بوسیله ریستالیزاسیون انلینگ در دمای 500 … 600 درجه سانتیگراد در اتمسفر اراد در ف اتمسفر اراد در اتمسفر اهشم مس خالص برای هادی جریان الکتریکی ، مبدلهای حرارتی مختلف ، الب ای آب سرد ، الت ا ، ریسال مالترا الترتال الت ا ریسال مالترا الت ا ریسال مالترا. مس الص دارای درت کم و سیالیت است ، با برش ضعیف پردازش می شود ، بنابراین آلیاژهای بر اساس ن تربا حفظ میزان بالای مقاومت الکتریکی و حرارتی مقاومت در برابر خوردگی ، لیاژهای مس واص مکانیکیای نی ردود. روی ، لع ، لومینیوم ، بریلیم ، سیلیکون ، منگنز و نیکل به طور عمده برای دوپینگ مس استفاده می شود. اایش قدرت لیاژها ، این عناصر آلیاژی عملا سبب اهش پلاستیک ، روی ، لع ، لومینیوم و حتی افزایش نومن.
برنج برنج آلیاژ روی مس است. با معرفی بیشتر آلومینیوم ، سرب ، قلع ، سیلیکون و دیگر عناصر به آلیاژ ، برنج ویژه به دست می آید. اربرد عملی در برنج یافت می شود ، که محتوای روی آن 49 تجاوز نمی کند.با افزایش غلظت روی ، واص مکانیکی آلیاژ به طور قابل توجهی بدتر می شود.
BRONZA دیک می داند با این برنز, آن را با حروف “Br” نشان داده شده است که همه چیز را می توان در زبان قابل درک توضیح داد, و فرمول شیمیایی و کلمات شفاف فقط شما را در طول امتحان دفن. در اینجا شما آن را موفق باشید)
بلیط 35 لاستیک
پلاستیک – مواد مصنوعی. اجزاء اجباری بسته نرم افزاری است. اتصال دهنده استفاده می شود: رزین ای مصنوعی ؛ اترها ، سلولز. بعضی از پلاستیک ا شامل تنها یک باند (لی اتیلن ، فلوروپلاستی ، شیشه لی) هستند.مولفه دوم یک رکننده (مواد پودری ، فیبر ، رتیکول شده از مواد آلی یا غیر آلی) است. رننده ا خواص مکانیکی را افزایش می دهند ، در نگام ار دادن یک محصول نیمی از انقباض را کاهش ابا را کاهش ابا را کاهش می رند ا لاستیک سازان (اسید اولئیک ، استایرن ، دیوتیل فلوراید …) ترکیب اصلی ممکن است امل: سخت کننده ها (آمین ها) ؛ کاتالیزورها (پراکسید ها) رآیند سخت شدن ؛ رنگ ها اساس طبقه بندی پلاستیک ها, ترکیب شیمیایی پلیمر است: طبق نوع اتصال دهنده, گرمانرم (ترموپلاستی) و پلاستیک گرماسنجی وجود دارد.ترموپلاستیک ها بر پایه پلیمرهای ترموپلاستی هستند. نها برای ردازش مناسب (مانی که حرارت داده می شوند ، نها پلاستیسیته) انقباض حجم کم (انابا حجم کم) لاستیک ای ترموستات س از پخت و ار به حالت ترموستات شکننده می وند ، می تواند تا 15 و وند. بنابراین ، رکننده های تقویت کننده به ترکیب این پلاستیک معرفی می شوند.
با توجه به نوع پرکننده, پلاستیک ها مشخص می شوند: پودر (کاربولیت) – با پرکننده در قالب آرد چوب, گرافیت, تالک … فیبر – با پرکننده از: دوک پنبه و کتان (فیبر); رشته های شیشه ای (فایبر گلاس) ؛ آزبست (فیبر آزبست).لایه – با ورق پرکننده: ورق کاغذ (getinaks) ؛ ارچه های پنبه ای ، پارچه های شیشه ای ، ارچه های آزبست (پارچه ای پارچه ای ، ورقه ورقه ای ای ، ار ور ور وست). G AZO ر ده – با پرکنده هوا (فوم ، پلاستیک فوم). ویژگی های پلاستیک عبارتند از: چگالی کم ؛ دایت حرارتی م گسترش حرارتی بزرگ ؛ واص الکتریکی عایق الکتریکی خوب ؛ مقاومت شیمیایی بالا ؛ نهایی که وب هستند خواص فن آوری
بلیط 27 لحیم کاری به فرایند پیوستن به قطعات فلزی با ذوب یک ماده پرکننده لحیم کاری که نقطه ذوب پایین تر از نقطه ذوب فلز پایه است, اشاره دارد.پیوند سرب براساس انحلال متقابل و انتشار فلز پایه و لحیم کاری است. نین فرایندی بیشترین سود را در صورتی انجام می دهد که لز پایه و لحیم دارای خواص شیمیایی و ند. استحکام اتصال سیم لحیم بستگی به اندازه سطوح متصل به لحیم کاری, پاک بودن این سطوح, فاصله بین قطعات, ساختار اتصال جوش شکل گرفته, و سپس مقاومت خوردگی آلیاژ اصلی و لحیم کاری است. کاهش ابعاد خطی محصول به ویژه در هنگام اتصال به چند بخش زمانی قابل توجه است که کل انقباض لحیم کاری در اتصالات لحیم کاری می تواند به اندازه ای برسد که طراحی آن به طور قابل ملاحظه ای کوتاه و غالبا نامناسب است.سطح فلزاتی که با لحیم شدن پیوند دارند, باید از اکسید و ناخالصی هایی که مانع فرآیند انتشار و انحلال فلزات می شود, کاملا تمیز شود. ارژ . ا سطوح لحیم ده محافظت می کند و نها را از اکسید ا پاک می کند که از تبادل لحیم اری بهلز ا. ل لحیم اری می تواند انواع مختلف ترکیبات را تولید کند: محلول امد ، ترکیب شیمیایی مخلوط مکانیکی. بهترین نوع سبندگی این است که ساختار لحیم اری نوع راه حل جامد شکل می گیرد. این فلزات بین فلزات با بالاترین نسبت فیزیکوشیمیایی وجود دارد. مثلا ممکن است لحیم کاری مس ، لحیم طلا و لا باشد.سازه های نوع ترکیب شیمیایی (لحیم کاری مس با قلع)
دنباله پیك
1) ماده سازی سطح (تمیز کردن چربی ها و دیگر لعنتی)
2) تراز (بر روی سطح)
3) حفاظت از نقطه لحیم اری با شار.
4) تینینگ (پوشش با یک لایه نازک از قطعات لحیم شده)
5) رم شدن وب
6) رفع اشکال
7) نک کننده
8) تمیز کردن جفت جوش از جریان بیش از حد و ره
وب جامد (ن مس) بسیار نزدیک به برنج است.لحیم اری جامد لحیم اری با نقطه ذوب 1000 درجه از جنبه ها (شعله های شعله با شعاع باز) استفاده می شود. سفات بر اساس اسید بوریک و نمک آن
بلیط 28 28 . روش تولید فولاد Открытый чартер
تولید باز تولیدی در سال +1864 رخ داد, زمانی که P.Marten نخستین احتراق (با استفاده از گرما از گازهای خروجی) را تولید کرد, که فولاد ریخته گری قابل استفاده را از طریق شارژ جامد ساخته بود. در روسیه ، اولین وره باز کوره در سال 1869 توسط A.Iznoskov در ارهانه Sormovsky ساته ادت است.تا دهه 90 وره ای باز کوره برای تولید فولاد تنها با پر ردن بار جامد مورد استفاده امد مورد استفاده امد مورد استفاده امد مورد استفاده راراحاارت ارت ارت ارت ارت رارت رارت رارت رارت رارت رارت رارت رات رتاد توسعه ن وری رآیند سنگ ن بر روی آهن مایع در اوکراین توسط برادران A.M. و یو. М.Горяиновым ؛ نا مچنین با استفاده از این تکنولوژی در سال 1894 г. در کوره باز کوره بارگذاری شده در آن: فولاد جامد یا مایع آهن, فولاد و قراضه آهن با استفاده از سنگ آهن, مقیاس, اکسیژن, فلو و فرولی فولاد به یک ترکیب خاص تبدیل می شود و در نتیجه تولید ذغال سنگ تولید می شود – سرباره سرباره. وره وره
سمت بالای وره باز شوم (ل 1) امل یک ای کاری (محدود به حمام 4 دیوار جلو 9 دیوار لو 9 دوار 8 اترت ار ، در دیوار لو نجره های بارگذاری 6 وجود دارد از طریق آن بار شارژ از پلت فرم ار می ود لت رم ار می ود ،ارم ار ومینه کوره دارای یک شیب به دیوار عقب است که در ن برای باز شدن ولاد به پایان رسیده است. ا ریق انال ای 1, 2, 3 и 7 سر ، از (سوخت) و انفجار اکسیداتیو تغذیه وند و محصولات احتراق ترا م.سمت ان وره امل دو جفت سرباره ، دو جفت بازسازنده ، انال های زیرزمینی با شیر سوئیچینگ ولح امل دو ت سربار ، دو جفت بازسازنده ، انال های زیرزمینی با شیر سوئیچینگ و حاح امل ر دونگ و حاا رتو سرباره و بازسازنده ها به صورت جفت و متقارن در هر دو طرف کوره مرتب شده اند. بخش از طریق سرباره هوا 11 و سرباره گاز 10 در یک هواپیما با قسمت متقاطع فضای کار و بخش از طریق بازسازی کننده هوا 12 و بازسازی کننده گاز 13 در هواپیما دیگر ساخته شده است: سرباره ها زیر سر هستند و بازسازی کننده ها زیر پلت فرم کار می کنند. برای رم ردن وا و ازهای قابل احتراق وارد ای کاری در دمای 1000 تا 1150 درجه ،، دستگاه ا احیا نتا ااحیا نتا ایاحیا نتا ا احیا نتانیاز به گرمایش ناشی از این واقعیت است که ای اری باید با درجه حرارت تا 1700 درجه ا بیشتر تامین ود ؛ ار پیش رم دن انفجار و از تولید نشود ، دمای وره برای حرارت دادن و سپس ذوب دن ولاد ملایم افیود. اتاق های بازسازی کننده ها با ن نازل در قالب سنگ تراشی آجر نسوز پر می شوند. بازسازی کننده ها به صورت متناوب و متناوب کار می کنند: در حالی که یک جفت انفجار و گاز را گرم می کند, دیگر انباشته می شود (گرما) محصولات احتراق زباله; پس از خنک سازی بازسازی کننده ها به حد پایین تر و یا با رسیدن به حد بالایی گرمادهی گرمادهنده های گرما, روشی جهت جابجایی گازها با استفاده از سوئیچینگ شیر تغییر می کند.سرباره بین سر و بازسازی کننده ها قرار گرفته است. نها برای مع وری رد و بار و رات سرباره که توسط محصولات احتراق به ار می روند ، ار می کنند. سوخت مایع (روغن مایع) نیز برای حرارت دادن وره های باز کوره در ارخانه های مهندسی استفاده می شدود. سوخت نفتی با کمک یک نازل به فضای کاری وارد می شود و با یک ت وا یا بخار تحت ار 5-8 درجه ای اسپرود می. وره ای عال در روغن ای معدنی فقط دو بازسازی کننده (و به همین ترتیب دو سرباره) رآیندهای کوره و وره ا به اساسی و ایه تقسیم می شوند ، بسته به ماهیت فرآیند و به مین ترتیب مود ود ود.ذوب فولاد با بار حاوی فسفر و گوگرد در مقادیر بیش از مقدار مجاز در فولاد تمام شده توسط فرایند اصلی انجام می شود, یعنی تحت سرباره اصلی و در کوره با پوشش اصلی. حمام وره اصلی با دولومیت سوخته ا مگنزیت پوشش داده شده است. ر رومیت مگنزیت با دوام بالا برای تخمگذار اق فضای کاری ، سر و دیواره های سرباره استفاده می شود. در کوره ای کوچک ، و مچنین در نبود آجر کرومیت مگنزیت ، وس کوره از ر سیلیکا ساخته ده است. برای ذوب ولاد تحت سرباره اسیدی ، وره اسیدی با پوشش آجر سیلیکا و ن و ماسه وارتز استفاده می شود.علاوه بر کوره ای سرامیکی ثابت ، همچنین کوره های باز شنی استفاده می شود. قسمت بالای کوره شیب دار بر اساس یک سیستم غلطک است. بین دیوارهای انتهایی فضای ار و سرها ، شکاف های کوچک وجود دارد ، امکان چرخش کوره را راهم می کند. با استفاده از مکانیزم چرخشی, آن را به سمت 15 درجه در جهت پلت فرم کار برای بارگذاری سرباره, یا 30-33 درجه در جهت خروجی برای تولید فولاد کج می شود. مدت مان وره باز کوره (کمپاین آن) ن معمولا برای 250-300 رما (با ظرفیت بزرگ) ا 400-500 رما (با ظرفیت کوچک و متوسط) برای وه و متوسط) برا وره ا بااوسط برای وره ا باوس را وره ا بااوس را ور ا باوس رتوسط, ور ا باوس رتوسطدر کوره باز وره کربن ذوب شده است فولاد ساختاری و مچنین فولاد آلیاژی مارک های مختلف.
Çeliku azotying. Nitrogjenizmi i joneve çeliku
Ионно-плазменное азотирование (IPA) është metoda e trajtimit të ngrohjes kimike të produkteve të çelikut dhe të hedhura me aftësi të mëdha teknologjike, e cila lejësi të mëdha teknologjike, e cila lejësi të mëdha teknologjike. Procesi i ngopjes së diffuzionit kontrollohet dhe mund të optimizohet në varësi të kërkesave specificike për thellësinë e shtresës dhe ngurtësinë e sipërfaqes.Микротвердость плазменное азотирование алиаж
Шкалла температура нитими и джоневе Ме э гжере се газ дхе është нэ рангун е 400-600 0 C. Трайтими нэ температура мэ поштэ 500 0 с ëште вечанэришт е эфектшме кур продуктет э форсиментал пинталь нга ирсимитл инструменталь нга ирсимит инструменталь нга shpejtësi të lartë dhe të plakjes së martensit, sepse Rritja e ndjeshme e pronave të tyre operacionale duke ruajtur ngurtësinë thelbësore në nivelin 55-60 HRC.
Metoda e përpunimit të përforcimit dhe mjetet e pothuajse të gjitha Industrive i nënshtrohen metodës dhe mjeteve IPA (рис.1).
Fik. нджэ.
Si rezultat, karakteristikat e mëposhtme të produktit mund të përmirësohen: rezistenca e veshin, qëndrueshmëria e lodhjes, pronat e antisaded, rezistenca ndaj nxehtësisë dhe rezorrozionca ndaitj.
Krahasuar me metodat gjerësisht të përdorura të forcimit të përpunimit termik kimik të pjesëve të çelikut, të Tilla si çimentimi, çimento nitro, cianizimi dhe nitratih: 9
- · Твердость sipërfaqe më të lartë të pjesëve të azotit;
- · Asnjë deformim i pjesëve pas përpunimit dhe pastërtisë së sipërfaqes së lartë;
- · Рритджа э куфирит тэ кендруешмэришэ дхе рритджа э резистенсес сэ вешит тэ пджешеве тэ пёрпунуара;
- · Temperatura më e ulët e trajtimit, për shkak të së cilës transformimet structurore nuk ndodhin në çelik;
- · Mundësia e trajtimit të shurdhër dhe përmes vrimave;
- · Ruajtja e ngurtësisë së një shtrese të azotit pas ngrohjes në 600-650 s;
- · Mundësia e marrjes së shtresave të përbërjes së specificikuar;
- · Афтэси пэр тэ пэрпунуар продукт е мадхэсив дхе формове тэ пакуфизуара;
- · Mungesa e ndotjes së mjedisit;
- · Rritja e kulturës së prodhimit;
- · Reduktimi i kostos së përpunimit disa herë.
Avantazhet е IPA gjithashtu manifesthen në një reduktim të ndjeshëm të kostove kryesore të prodhimit.
Për shembull, në krahasim me nitratin e gazit në furrat, IPA siguron:
- · Редуктими и кохэзгйатйес сэ траджтимит штэ 2-5 херэ, си пэр шкак тэ редуктимит тэ нгрохьес дхе фтохьес сэ Садкес, дхе герцог редуктуар кохен е экспозимит изотермал;
- · Редуктими и бриштесисэ сэ штресэс сэ нгуртэсуар;
- · Reduktimi i kostos së gazrave të punës 20–100 герэ;
- · Reduktimi i konsumit të energjisë elektrike 1.5-3 герэ;
- · Пёръщтими и действует тэ трансферімит;
- · Reduktimi i deformimit është aq shumë për të excluar bluarjen përfundimtare;
- · Lehtë dhe besueshmëria e mbrojtjes së ekranit kundër azostit të sipërfaqeve të papenguara;
- · Përmirësimi i kushteve sanitare dhe Higjienike;
- · Pajtueshmëria e plotë e teknologjisë me të gjitha kërkesat mjedisore moderne.
Krahasuar me forcimin përpunimi i metodës IPA lejon :
- · Перяштон деформимин;
- · Rritja e burimeve të një sipërfaqe agenike prej 2-5 herë.
Përdorimi i IPA-s në vend të çimentimit, çimentos nitro, gaz ose nitriding lëng, volumetrike ose tweas shuarje ju lejon të ruani pajisjet kryesore dhe zonat e prodhimit, të zvoghelon eleksiën, të zvoghelon elens, të zvoghelon elens, të zvoghelon elens, të zvoghelon elens dhe mediave aktive të gazit.
Parimi i veprimit të IPA-s qëndron në faktin se në shkarkimin (p = 200-1000 PA) një mjedis të gazit që përmban azot midis katodës – detajet – dhe muret anode dhomdejë ekumi vakumi ngazëllyer, герцог Formuar një medium aktiv (joneve, atomeve, molkulave të ngazëllyer), e cila siguron formimin e një shtrese nitrat e përbërë nga një zonë e jashtme euzridës të vendës dhe njëur zonë e jashtme euzridës the dhe njëur zonë.
Faktorët teknologjikë që ndikojnë në efektivitetin e nitegut të joneve janë temperatura e processit, kohëzgjatja e ngopjes, presionit, përbërjes dhe konsumit të përzierjes ss.
Temperatura e processit , Sheshet katrore të përfshira në shkëmbimin e nxehtësisë dhe efektivitetin e shkëmbimit të nxehtësisë mearin (numri i temperaneve) shehtësë mearin (numri i ekraneve) пёрчимин пёрджинэ пёрчакшатйнэ не Përzgjedhja e temperaturës varet nga shkalla e dopingut të çelikut të azotit nga elementët e formimit të nitrinit: sa më i lartë shkalla e aliazhit, aq më e lartë është temperatura.
Temperatura e përpunimit duhet të jetë së paku 10-20 0 nën temperaturën e pushimeve.
Kohözgjatja dhe temperatura e processing Ngopja përcaktohet nga thellësia e shtresës, shpërndarja e ngurtësisë në thellësinë dhe trashësinë e zonës së nitride.
Përbërja e mjedisit të ngopur Varet nga shkalla e dopingut të çelikut të përpunuar dhe kërkesat për ngurtësinë dhe thellësinë e shtresës së azotit.
Presioni i processing Duhet të jetë e Tillë që shkarkimi i sipërfaqes së produkteve dhe përgatitja e një shtrese të njëtrajtshme të nitruar.Megjithatë, duhet të kihet parasysh se shkarkimi në të gjitha fazat e processit duhet të jetë anormal, dmth. Sipërfaqja e të gjitha pjesëve në kafaz duhet të mbulohen me një luminescence, dhe dendësia e rrymës së shkarkimit duhet të jetë më e madhe se normale dendësia për këtë presion, duke nhrëfe paradise. Газ нэ zonën katodë të shkarkimit.
Me ardhjen е cilësimeve të gjeneratës С.Е. повторно, герцог përdorur NJE përzierje të hidrogjenit, azotit ДНО argonit të rregullueshëm си NJE среда Пуна, си ДЕНЬ Plazma е “pulsuese” ДНО джо të drejtpërdrejtë, Прочезите я procesit të нитриды jonike еште rritur ndjeshëm.
Përdorimi я ngrohjes С.Е. kombinuar (Мюра е dhomës “të nxehta”) новления mbrojtja termike е përmirësuar (mburoja е trefishtë е nxehtësisë), С.Е. башка мне aftësinë PER të rregulluar në mënyrë të pavarur përbërjen е Gazit ДНО presioni në dhomën Лейон Кур përpunon mbinxehjen e skajet e hollë të prerjes gjatë ngrohjes së kafazit, saktësisht rregulloni kohën e ngopjes një, në përputhje me rrethanat, thellësinë e shtresës, sepse Ngrolenhja projärënë ngroh 2.
Izolimi efektiv termik në dhomën e punës (mburoja e trefishtë e nxehtësisë) ju lejon të trajtoni produktet me konsum të ulët të energjisë specificike, e cila ju lejon të minimizoni dallimet eks. Kjo dëshmohet nga shpërndarja e mikroharisë në thellësinë e shtresës së nitrated për mostrat, të vendosura në vende të ndryshme të Sadkës (рис. 2).
Фик. 2.
А, шестеренчатый пешон 10,1 кг, 51 коп., Ст – 40х, модуль 4.5, шпэйтэсия е шкрехэсит 16 орэ, t = 530 0 с;
b, M – Шестерня пешон 45 кг, 11 копе, ст – 38хн3мф, модуль 3,25 (kurorë e jashtme) dhe 7 мм (kurorë të brendshme), shpejtësia e qepjes 16 orë, t = 555 0 S.
Jon nitriding – një metodë efektive e përpunimit të forcimit të pjesëve nga elikë Strukturore të aliazheve : Ingranazhet, kurorat e marsheve, ingranazhet e boshtit, ingethranidé ingomet.
imentimi, çimentos nitro dhe forcimi i TVch justifikojnë veten në prodhimin e pjesëve të ngarkuara rëndë (rrota, boshtet, boshtet, etj.) Me saktësi të ulët djeë në tjër mesëm qe.
Кето Илодже тэ траджтимит тэ нгрохджес джанэ экономикишт тэ папёрштатшме нэ продхимин э пйесэве тэ месме дхе тэ нгаркуара ме сактэси тэ лартэ, кэ нга Ме кэтэ пёрзхэндэ ржмэндэ шртэмбэ шрпунэмбэ, нэ мэ кэтэ пёрзхэндэ шрпунэтим. Прандадж, кур блю, është е nevojshme të hiqni një trashësi të ndjeshme të shtresës së ngurtësuar.
IPA ju lejon të zvogëloni ndjeshëm bllokimin dhe deformimin e pjesëve duke ruajtur ashpërsinë e sipërfaqes brenda Ra = 0,63 … 1,2 микрона, e cila lejon në shumicën dërterëpérérérépé.
Sa i përket mekanizmit të makinës, ingranazhet e nitridës së joneve në një masë të konsiderueshme zvogëlon karakteristikat e zhurmës së makinave, duke rritur kështu konkurrenc.
IPA është më e efektshme kur përpunon pjesë të një Dimensale në shkallë të gjerë: ингрэнажет, боштет, аксет, боштет и маршеве, ингранажет е боштит тэ боштит, этдж.Në të njëjtën kohë, kapaciteti mbajtës i sipërfaqes anësore dhe forca e bazës së dhëmbit, të arritur nga azoti i plazmës, korrespondojnë me ingranazhet e çimentos (табл. 1).
Tabela 1. Karakteristikat e lodhjes së shqistës Çelikë në varësi të metodave të forcimit të rrotave të marsheve
Kur metoda e acitrogjenizimit të pjesëve nga çimento, çeliku i ulët dhe i dytë i dereguluar (18hgt, 20hnz, 20hgnm, 25hgt, 40x, 40khnm, 40hf, etj) duhet të përmirë 24/2 në fillim.(Për disa Çelikë – 269-302 HV), pastaj përpunimi mekanik dhe përfundimi – ионное азотирование. Për të siguruar deformimin minimal të produkteve para azostit të heqjes së stresit, pjekja është e rekomanduar në një atmosferë të gazit mbrojtës dhe temperatura e pjekjes duhet të jetë shëtélartlart. Отжиг duhet të kryhet para përpunimit të saktë.
Thellësia e shtresës së azotit të formuar në produktet e specificikuara të bëra nga çeliku 40x, 18hgt, 25hgt, 20x2h5a, etj, është 0.3-0,5 мм me një ngurtësi prej 500-800 hv, në varësi të klasës së çelikut (рис. 3).
Për ingranazhet që veprojnë në kushte të ngarkesave më të rënda, një shtresë e azotit duhet të jetë në nivelin 0,6-0,8 мм me një zonë të hollë nitride ose pa të.
Fik. 3.
Optimizimi i пронаве të shtresës së forcuar përcaktohet nga kombinimi i karakteristikave të materialit bazë (ngurtësinë e bërthamës) параметрат и shtresës së azotit. Karakteri i ngarkesës përcakton thellësinë e shtresës së diffuzionit, llojin dhe trashësinë e shtresës nitride:
- · Вешин – “- осэ -Шс;
- · Ngarkesa dinamike – trashësi e kufizuar e shtresës së nitridit ose fare pa një shtresë nitride;
- · Коррозиони – -ст.
Kontrolli я pavarur я rrjedhës С.Е. secilit prej përbërësve të përzierjes С.Е. Gazit, presioni në dhomën х punës ДНО ndryshimi я ТЕМПЕРАТУРЫ С.Е. procesit ж lejojnë të formoni shtresa të thellësive ДНО ngurtësisë С.Е. ndryshme (рис. 4), герцог siguruar kështu cilësi të qëndrueshme të përpunimit me Variacioni minimal и пронаве nga ana e pjesës në pjesën dhe nga kafazi në kafaz (рис. 5).
Fik. катер.
- 1, 3, 5 – процеси ме нджэ хап;
- 2,4 – Procesi me dy hapa nga përmbajtja n 2 Në përzierjen e punës
- 1,2 – t = 530 0 C, T = 16 orë; 3 – t = 560 0 C, T = 16 orë;
- 4 – t = 555 0 С, t = 15 орэ, 5 – t = 460 0 С, Т = 16 или
Фик.Песэ.
Jon nitriding është gjerësisht i njohur dhe si një nga metodat efektive duke rritur rezistencën e veshit të mjetit të prerjes elikë filterri Shënon R6M5, P4K5, R6M5, et.
Азотирование rrit rezistencën veshin e mjetit dhe rezistencën e saj të ngrohjes. Një sipërfaqe e veturës së azotit me një koeficient të reduktuar të fërkimit dhe vetitë e përmirësuara të antifrikës siguron një linje të patate të skuqura, dhe gjitha mundur rritjen e ushqimit dhe shpejtësisë së prerjes.
Struktura optimale e çelikut me shpejtësi të lartë të azotit është një martensi i lartë ozotik që nuk përmban nitride të tepërta. Kjo structurë sigurohet nga saturimi i sipërfaqes së mjetit me azot në një temperaturë prej 480-520 0 s në processin e nisjes afatshkurtër (deri në 1 orë). Në të njëjtën kohë, një shtresë e forcuar e një thellësi prej 20-40 μm me një mikrisht të sipërfaqes 1000-1200 hv0.5 është krijuar me ngurtësinë e bërthamëz rejourse 800-900 hv (Fig. 2-8 herë në varësi të llojit dhe pikëpamjeve të materialit që po përpunohet.
Fik. 6.
Avantazhi kryesor i mjetit nitriding jonik është mundësia e marrjes së një shtrese të forcuar të diffuzionit, ose një shtresë me një нитрид монофазный Fe 4 n (“-Fase) në sipërösişişit, në sipërösişişit përbëhet nga Dy faza – “+, të cilat është burimi i Voltageeve të brendshme në kufirin e ndarjes së fazës dhe shkakton brishtësinë dhe heqjen e shtresës së forcuar gjatë operacionit.
Азотирование джоник është gjithashtu një nga metodat kryesore për rritjen e qëndrueshmërisë. vulosja e mjeteve dhe pajisjeve të hedhjes nga çeliku 5khnm, 4x5mfs, 3x2b8, 4x5v2fs, 4x4vmfs, 38x2mu, x12, h22m, h22f1.
Si результатов азотирования, характеристика и методика të produktit mund të përmirësohen:
- · Pulla të falsifikuara për vulosje të nxehtë dhe moulds për hedhjen e metaleve dhe lidhjeve – rritja e rezistencës së veshit, ngjitja e metalit zvogëlohet.
- · Пресс-форма derdhur Alumini NEN presión – NJE shtresë нитрованного parandalon ngjitjen е metalit në ZONEN е furnizimit të Gazit të lëngët, ДНО Прочезите я mbushjes С.Е. formularit ешт меня пак я trazuar, gjë QE rrit jetën е formularëve të shtypit ДЕНЬ hedhja ешт тп lartë sesa cilësia më e lartë.
Në mënyrë të konsiderueshme përmirëson karakteristikat e nitriding dhe operacionale të mjetit të ftohtë (t
Kërkesat kryesore QE sigurojnë performancën е lartë të NJE mjeti të Тилле – Forca е lartë е сжимающая, rezistenca е veshin ДНЕ rezistenca е ngarkesës С.Е. goditjes С.Е. ftohtë – arrihen си rezultat я përpunimit të ngurtësimit нга jonizimi я joneve.
Nëse mjeti përdor çelik të lartë të kromit (kromit prej 12%), atëherë shtresa e azotit duhet të jetë vetëm diffuzion, nëse çeliku i aliazhit të ulët – atëheruzë përveke dérveç ë .
Një типар и jonizimit të çelikut të kromit të lartë është se zgjedhja e temperaturës së processit mund të jetë në kufij të gjerë për të ruajtur ngurtësinë e produktrjakel ngurtësinë e produktrjakel n
Пёр тэ маррэ нджэ штресэ сипэрфакэсоре резистенте ндадж вешит, герцог руаджтур нджэ бертамэ тэ трэшэ тэ вулэс, штэ э невойшме цэ сэ пари тэ крихет дюк шмангурмэ дже пэдже пэдже пэдже пэдже пэдже пэдже пэдже пэдже пэдже пэдже пэдже пэдже пэдже пэдже пэдже пэдже.
Për të përjashtuar ose minimizuar deformimet që dalin në nitegimin e joneve të mjetit të vulosjes, para përpunimit përfundimtar mekanik, rekomandohet të kryeni pjekjë në pjekjë në gazë nénété néné nénété néné néné néné néné nj
Nëse është e nevojshme, përdoret për të polish sipërfaqen e azotit të punës.
Tabela 2. Karakteristikat e çelikut të aliazh pas nitriding jon-plazma.
класс çeliku | Сердечник с твердостью , HRC | Температура и обработка | Karakteristikat e shtresës | Lloji i lidhjes së shtresës së обновлен | ||
Thellësi, мм. | Пов. ТВ-СТ, ГВ 1 | Trashësia e shtresës është gjithëpërfshirëse., M | ||||
eliku për përpunim të nxehtë | ||||||
eliku për përpunim të ftohtë | ||||||
Variatimi i përbërjes së mediumit të ngopur, temperatura e processing dhe kohëzgjatja e tij mund të formohet nga shtresa të thellësive dhe ngurtësisë së ndryshme (рис. 7,8).
пунсон пешон 237 кг | |
форма пешон 1060 кг. |
Фик. 7. Shembuj të përpunimit të pajisjeve të vulosjes (A, B) dhe shpërndarjes së mikrohardësisë në thellësinë e shtresës së azotit (B, G).
Kështu, СИК tregon përvoja Globale, përdorimi я teknologjisë азотирование jonike PER forcimin е përpunimit të produkteve нг çeliku strukturor, си ДНО mjeti я prerjes ДНО vulosjes, KJo teknologji ешт efektive ДЕНЬ relativisht lehtësisht е zbatuar, veçanërisht герцог përdorur plazmën е rrymës pulsuese.
Dhe prodhimi Ndustrial i zhvilluar sot seekon trajtimin e ngrohjes kimike, në veçanti të azostit të jon-plazmës (në tekstin e mëtejmë IPA), и cili është i dobgaishëvëm Сот, IPA pёrdoret në mënyrë aktive në makinë, gjykata dhe mjetet e përpunimit, Industrinë e bujqësisë dhe riparimit, për prodhimin e instalimeve të industrialrisë së energjisë. Ndër ndërmarrjet që përdorin në mënyrë aktive teknologjinë e nitrideve jon-plazma të Tilla si shqetësimi gjerman Daimler Chrysler, gjiganti и makinës BMW, Volvo suedeze, bimë trahekazitoruse.Përveç kësaj, avantazhi i IPA vlerësoi prodhuesit e Instrumenteve të Shtypit: Skandex, Nughhovens.
Технология и процесс
Azostata jon-plazma e përdorur për mjetet e punës, pjesët e makinave, pajisjet për vulosjen dhe hedhjen, siguron ngopjen e shtresës sipërfaqësore të produktit körë Instalimet për IPA po veprojnë në një atmosferë të shkarkuar në një presion deri në 1000 Па.Dhoma që vepron në parimin e sistemit katodë dhe anode është Furnizuar me përzierjen e azotit-hidrogjenit për përpunimin e hekurit të hedhur dhe çelik të ndryshëm oseanium poujë poujë tjë pjër gér. Katoda i shërben pjesës së punës, anode – muret e dhomës. Ngacmimi i një ngarkese jonormale të ajrosur inicion formimin e plazmës dhe, si rezultat, një medium aktiv, i cili përfshin jonet e ngarkuara, atomet dhe molkulat e përzierjes së e nëgët jétés.Presioni i ulët siguron mbulim të plotë dhe të plotë të billetit me shkëlqim. Temperatura e plazmës varion nga 400 në 950 gradë në varësi të gazit të punës.
Për jon-plazma nitriding kërkon 2-3 herë më pak energji elektrike, dhe cilësia e sipërfaqes së produktit të përpunuar ju lejon të përjashtoni fazën e përfundimit të bluarjeit nha
Filmi që formon në sipërfaqe përbëhet nga dy shtresa: diffuzion më të ulët dhe nitride të lartë. Cilësia e shtresës së modifikuar sipërfaqësore dhe efikasiteti ekonomik i processit në tërësi varet nga një numër faktorësh, герцог përfshirë për processohrjen e gazit, dheperajturën
Sigurimi i një temperature të qëndrueshme qëndron në processset e shkëmbimit të nxehtësisë që ndodhin direkt brenda dhomës për IPA. Për të zvogëluar Intensitetin eProcessabike Me muret e kamerës, përdoren ekrane të veçanta të ngrohjes jo-përçue. Ата lejojnë тэ kursejnë ndjeshëm në pushtet të konsumuar. Temperatura e processit është e lidhur me kohëzgjatjen e thellësisë së Penenrimit të nitridit, i cili shkakton ndryshime në grafikun e shpërndarjes së thellë të treguesve të fortësisë.Temperatura nën 500 градусов është më optimale për nitriding çeliku të përpunimit të ftohtë dhe materialeve martensite, pasi që karakteristikat e performanceancës po rriten pa ndryshuar ngurtësmektës струнхаматр дхэинтэс бреинтэс bheinen shrundës bheinense.
Përbërja e mjetit aktiv ndikon në fortësinë dhe madhësinë përfundimtare të zonës së nitride dhe varet nga përbërja e produktit që përpunohet.
Rezultatet e përdorimit të azostrosjes jon-plazma
Азотирование jon-plazma lejon rritjen e treguesve të rezistencës së veshin me një rënie të njëkohshme të tendencës për çrregullimet e lodhjes së structurës metalike.Përgatitja е пронаве të nevojshme sipërfaqësore përcaktohet nga raporti i thellësisë dhe përbërjes së shtresave të diffuzionit dhe nitridit. Shtresa e nitridit, bazuar në përbërjen kimike, është bërë për të ndarë në dy faza përcaktus: “Гамма” мне një përqindje të lartë të përbërësve FE3Nylon «Fe4N me». -Fase характеризует нга пластичети и ульет и штресэс сэ sipërfaqes me tregues të lartë të rezistencës me lloje të ndryshme të korrozionit, faza ε jep një shtresë relativisht të veshin-rezistente.
Са и пёркет штресэс сэ дифузионит, зона и нитридеве тэ жвиллуара нгджитур редуктон гясат е формимит тэ коррозионит межкристаллический, герцог сигуруар мьяфт пэр фэркиме актив тэ враждэсис. Detajet me këtë raport të shtresave përdoren me sukses në mekanizmat e veshin. Eliminimi i shtresës нитрид lejon për të parandaluar shkatërrimin e forcës së ngarkesës nën ndryshime të vazhdueshme në kushtet e presionit të mjaftueshëm të lartë.
Кэшту që Йон-плазма азотирование пёрдорет пер тэ optimizuar treguesit e veshin dhe rezistencën e nxehtësisë dhe korrozionit me një ndryshim në qëndrueshmërinë dhe sqes shj »
Авантаж азотирование плазмы
Ионно-плазменное азотирование në processin teknik debugged jep shpërndarjen minimale të pronave sipërfaqësore nga ana e pjesës në pjesën në njëtensitet relativisht të ulët të energjisë, gjërndarjen gjëréqée
Йон-плазма, азотирование, устраняющее деформамин и пйесэве тэ пунэс дхе структура е штресэс сё азотит мбетет э пандрышуар эдхе кур пьеса штэ э нксехтэ нэ 650 градэ, э чила штэ э нксехтэ нэ 650 градэ, э цила штэ э нксехтэ нэ 650 градэ, э чила штэ э лиджинэ тэвэ лэджирнэ тэвэ лэйджинэ муджур мюндэ муджур мюндэ të zgjidhur një shumëllojshmëri të gjerë të detyrave.Përveç kësaj, azosogjenizimi i metodës jon-plazma është e shkëlqyer për përpunimin e çeliqeve të notave të ndryshme, pasi temperatura e punës së processbonit në përzierhésérégë Пёркундрази – ndihmon për të zvogëluar probabilitetin e shkatërrimit të lodhjes dhe dëmtimit për shkak të lartë të brishtësisë së fazës së nitride.
Për të rritur treguesit anti-korrozioni dhe ngurtësinë sipërfaqësore nga jon-plazma nitriding, billets e çdo forme dhe madhësive me vrima dhe vrima të shurdhër janë të pärshtats.Mbrojtja и экранит нга азотирование нук është një zgjidhje e ndërlikuar inxhinierike, kështu që përpunimi i seksioneve Individual të çdo forme është i lehtë dhe i thjeshtë.
Лидхур ме методат э тджера тэ форсимит дхэ рритджес сэ резистенцес межкристаллический, IPA ндрышон шкуртуар диша херэ кохезгьятджен и процессит текник дхе тэ редуктуар ме дй урдхра тё пунит оперэс газ. Kështu që Për jon-plazma nitriding kërkon 2-3 herë më pak energji elektrike, dhe cilësia e sipërfaqes së produktit të trajtuar ju lejon të përjashtoni fazën e përfundimit të bluarje.Пёрвеч кешадж, экзистон нджэ мундэси пэр тэ криер процессин е кундэрт тэ азостит, пер шембулл, пара се тэ блуаджме.
Эпилог
Për fat të keq, në sfondin e madje edhe të vendeve fqinje, punëtorët e prodhimit vendas përdorin azostinimin nga metoda jon-plazma, megjithëse avantazhet ekonomike dhe fizike dhe mekanike janmeë të. Zbatimi i prodhimit të nitriding jon-plazma përmirëson kushtet e punës, rrit produktivitetin dhe zvogëlon koston e punës, ndërsa burimi i processit të produktit të përpunuar rritet 5 herë.Si rregull, çështja e ndërtimit të processit teknik duke përdorur instalimet për IPA qëndron në проблема и планит финансиар, эдхе псе нук ка пенгеша тэ vërteta reale. Ионно-плазменное азотирование меня një dizajn mjaft të thjeshtë të pajisjeve kryen disa operacione në të njëjtën kohë, zbatimi i të cilave metodat e tjera ështëvar e mundur vetëm kohëjë faza kohë faza kohë. Первеш кёсадж, ка диша компани нэ Руси дхе Бьеллоруси, герцог башкэпунуар ме продхуэсит е хуадж тэ паджисеве пэр IPA, гджэ кэ е бен блэрджен е инсталлимеве тё тилла штэ лэйрэ дхэрбаллус.Ме са дукет, проблеми криесор штэ ветэм нэ нджэ вендим банал, и чили, си нджэ традитэ уловка, до тэ линдэ пэр нджэ кохэ тэ гджатэ дхе тэ вештирэ.
A.v. Арзамасов
Мсту ата. Н. Э. БАУМАН
ISSN 0026-0819. “Studimet metalike dhe përpunimi termik i metaleve”, Nr. 1. 1991
Жвиллими и процесеве тэ реджа тэ продхимит тэ джонит азотирование нэ мэнырэ që тэ рритет резистенка е вешит тэ сипэрфакес сэ пйесэве тэ бэра нга çeliku austenitik, штэр нйгэ де.
Сталь аустенитная и такон вэштиресивная, пассивная пленка и тё оксидит тэ сипэрфакев парандалойнэ, эффективный и нгопьес, азотит, дифузионит, азотит, аустенит мэ пак сэн, феррит. Në këtë drejtim, për të hequr filmat e oksidit në azostina konvencionale, është e nevojshme para-trajtimi i sipërfaqes së çelikut ose përdorimi i shtyllave.
Nitrizimi i zakonshëm i çeliqeve më austene janë kryer në amoniak në 560-600 ° C для 48-60 орэ. Megjithatë, këto mënyra nuk lejojnë të marrin shtresa të diffuzionit me një trashësi prej më shumë se 0.12-0,15 мм dhe 45x14h24V2M (EI69) Nuk është e mundur për të marrë trashësi Shtresa e diffuzionit është më shumë se 0,12 мм, madje edhe gjatë nitrit për 100 orë. Rritja e temperaturës së azotit në furrën mbi 700 ° C на në një shkëputje më të plotë të amoniakut dhe, si rezultat, në një rënie në aktivitetin e aktivitetit.
Si rregull, pas nitratit të zakonshëm, rezistenca ndaj korrozionit të shtresave sipërfaqësore të çeliqeve austenitike përkeqësohet.
Азотирование jon e çelikut austenit kontribuon në një rritje të koeficientit të diffuzionit të azotit dhe nuk kërkon përdorimin e parajkëve.Në të njëjtën kohë, kohëzgjatja е processit është zvogëluar dhe cilësia е shtresave të azirura rezultulus është përmirësuar.
Megjithatë, jon nitriding i eliqeve Austenitike në mënyrat e zhvilluara më parë nuk lejoi të merrte shtresa të diffuzionit të një trashësi të madhe edhe me ekspozime të gjata
Bazuar në llogaritjet termodinamike dhe studimet eksperimentale, u zhvillua mënyra e nitrideve jonike të pjesëve nga çeliqet austenitike, duke lejuar të merrte shtresa të diffuzionës.Filmat e oksidit u hoqën nga sipërfaqja e pjesëve në processin e përpunimit kimik-termik.
Сталь аустенитная стандартная 45х14Н14Б2М (EI69), 12х18х20Т (EHA1T) janë hetuar; 25x18N8v2 (EI946) dhe me përvojë të lartë, të zhvilluar nga Instituti i Shkencave Metal dhe Teknologjitë e Metaleve të Akademisë Bullgare të Shkencave – Lloji X14AG20N8F2M (0,41820% n), , x18AG20F (1,02% n), x18ag20f (2,00% n).
Studimi istrukturës së shtresave të diffuzionit në çelik u krye me ndihmën e testeve structure metalike, рентгеновская структура dhe të mikroenterpendit.Është vërtetuar se kriteri structureor i rezistencës së lartë të veshin e çelikut austenit të nitruar është prania e nitrideve të llojit CRN në shtresën e diffuzionit. Анализ и концентрацию внимания на элементе Кимике Тэ Марра Герцог Пердорур MicroAnalysts ISM-35 CF, Cameca MS-46, CONDBAX 23-APR-85 предлагает вам не крахасим мне элементэ и тжеерэ тэ рэнда край мэшресулсия. Në thelbin e mostrave, shpërndarja e kromit është uniforme.
Përsëritja e përsëritur e eksperimenteve në studimin e shpërndarjes së azotit dhe kromit në trashësinë e shtresës së diffuzionit zbuloi ndryshimeinkron në formë të kërcimit në përq.Пёрвеш кёсадж, тестет е вешйес сэ пара-штресуара канэ трегуар, резистенка мэ э мадхе э вешит ка ндже микрозонэ тэ штресэс сэ дифузионит меня нджэ пэрмбаджтже максимале тэ азотит дхе кром.
Табела 1.
h, мкм. | Përmbajtja e elementeve kimike,% | ε | |||
С. | Н. | Cr | Ni. | ||
20 | 0,70 | 10,0 | 19,0 | 11,0 | 9,5 |
40 | 0,85 | 12,0 | 25,0 | 8,0 | 10,7 |
45 | 0,88 | 15,0 | 25,0 | 8,0 | 11,2 |
50 | 0,92 | 10,0 | 25,0 | 8,0 | 11,0 |
70 | 0,90 | 0 | 14,0 | 12,0 | 1,7 |
* – pjesa tjetër e FE Shënime: 1.Тестет е вешин у криен нэ макинен Шкода-Савин. 2. Rezistenca relative e veshit u përcaktua në lidhje me vëllimet e puseve të mençura në standardin (mostra e çelikut me ngurtësinë e 51 të HRC) dhe kampionin e studiuar ε = v etzrtham varritë eë = 0,08). |
Studimi я mëtejshëm я strukturës С.Е. çeliqeve austenetike të austinitit герцог përdorur ANALIZA Mikro-centeddral Бери të mundur vendosjen себе në mikrobonet е shtresave të difuzionit меня NJE përmbajtje М.Е. të Мад të azotit ДНО kromit, у vëzhgua NJE përqendrim я reduktuar я karbonit , никелит дхэ хекурит (Табела 1).
Një анализэ крахасуэс е микроструктурас сэ штресэс дхэ тэлбит тэ челикут тэ азострогес 45x14h24V2M, тэ ларгуар нэ кромин характерстик нэ α-эмиссия трэгой сэ штреса е дифузимэпэсэпэдээдээдэдээдээдэпэдэ – нэ пэрумбэпэдээпонэдэ – нэ пэрумбэпэээ мэпонэдэ – нэ пэрумбэдэ
Matjet e depërtimit magnetik duke përdorur një magnetoskop F 1.067 dhe përcaktimin e fazës së ferrit në ferritometrin MF-10i tregoi se metoda e zhvilluar e pjesëve jonike të nitrideve tribu •
Табела 2.
U zbulua gjithashtu se çeliku i azotos 45x14n14b2m dhe lloji x14ag20n8f2m kanë rezistencë të kënaqshme korrozioni.
Сипас Нджэ Процесси Тэ Ри Технологжик, У пэрпунуа Нджэ Грумбулл и Ингранажеве Тэ Бера Преж Челику 45x14N14v2V2. Подробности и особенности меня. Анализ микро дхе макроструктураре конфирмой пранине е нджэ штресе мне цилэси тэ лартэ тэ дифузионит меня нджэ трашеси преж 270 мкм нэ веше.
Pas testeve afatgjata Industriale të defkteve të dukshme në ingranazhet nuk u zbuluan.Kontrolli i mëtejshëm tregoi përputhjen е madhësisë gjeometrike të gjashtë kërkesave teknologjike, si dhe mungesës së veshin e sipërfaqeve të punës të pjesëve, e cila u konfirmua anal.
Përfundim. Mënyra х zhvilluar е pjesëve të nitrideve jonike нг çeliku austenitik BEN të mundur zvogëlimin е kohëzgjatjes С.Е. procesit М.Е. shumë себе 5 HeRe, ndërsa trashësia е shtresës rritet 3 HeRe, ДНО rezistenca х veshit të shtresës ешт 2 HeRe në krahasim меня parametrat х ngjashëm па нормальное азотирование.Përveç kësaj, Интенситети и Пунес Звогелохет, Рритет Культура е Продхимит Дхе Нджэ Ситуатэ Мджедисоре Штэ Пэрмиресуар.
Библиография:
1. Методат прогрессивного тэ përpunimit termik kimik / под ред. Дубинина, Я. Д. Коган. М .: Inxhinieri mekanike, 1979. 184 ф.
2. Азотирование карбонификими / Р. Чаттерджи Фишер, Ф. В. Эйшле, Р. Хоффман, dhe të tjerët: Pen. меня тэ. М .: Металлургджи, 1990. 280 ф.
3. А.С. 1272740 BRSS, MKA C23S8 / 36.
4. Баня О. А., Блинов В. М. Шпёрндарья-форсими и челикут йо-магнетик që пермбан ванадий. М .: Шкенца, 1980. 192 ф.
5. Рашев Ц. В. Продхими и челикут алиаж. М .: Металлургджи, 1981. 248 ф.
Jon-plazma nitriding (IPA) – Ky është një lloj i përpunimit termik kimik të pjesëve të makinës, mjeteve, vulave dhe pajisjeve të heheuzdhjë, dukeresqueen, dukeresqueen азот дхе карбон нэ нджэ плазма гидроген-гидрогени нэ нджэ температура до 450-600 ° C, si dhe lidhjet titan ose titan me temperaturën janë 800-950 ° C без плазмы нитрике.
Thelbi i nitriding jon-plazma është se në një medium të gazit që përmban azot të shkarkuar në 200-000 për katodë, në të cilën janë vendosur pjesë të përpodehée cérpungaum, dhe ana ana , нджэ Шкаркими анормал и шкэлкимит штэ и нгазеллер, герцог формуар нджэ средний актив (йоневе, атомеве тё молекулаве тэ нгазёллер). Kjo siguron formimin e një shtrese të azotit në sipërfaqen e produktit të përbërë nga një zonë e jashtme e nitride me një zonë të diffuzionit të vendosur nën të.
Variatimi я përbërjes С.Е. Gazit të ngopur, presionit, ТЕМПЕРАТУРЫ, kohës С.Е. ekspozimit дзю Mund të merrni shtresat е NJE strukture të caktuar меня përbërjen е fazës С.Е. kërkuar, герцог siguruar vetitë е rregulluara në mënyrë strikte të çeliqeve, Гиз, титан новление lidhjeve të saj. Optimizimi i vetive të sipërfaqes së dhimbshme sigurohet nga kombinimi i nevojshëm i shtresave të nitrideve dhe diffuzionit, të cilat rrotullohen në materialin kryesor. Në varësi të përbërjes kimike, shtresa e nitridinës është ose Y-faza (fe4n) ose e-faza (fe2-3n).Штреса е-нитрид штэ нджэ коррозиве, дхе й-штреса штэ резистенте ндай вешин, пор релятивишт пластике.
në të njëjtën KOHE, мне ndihmën е джон-plazmës азотирование ешт х mundur PER të Marre:
shtresa х difuzionit мне NJE ЗОНА нитрид të zhvilluar, д Cila siguron rezistencë të lartë të korrozionit ДНО punueshmërinë е sipërfaqeve të fërkimit – PER pjesët e zgjerimit
shtresa e diffuzionit pa zonën nitride – për prerjen, vulosjen e mjeteve ose pjesëve që veprojnë në presione të larta me ngarkesa альтернатива.
Azosogjenizimi i jon-plazmës mund të përmirësohet nga karakteristikat e mëposhtme të produktit:
vishni rezistencën
durim lodhë000 rezistencën
durim lodhë000 ezistencén
ca
Avantazhi kryesor i metodës është cilësia e përpunimit të qëndrueshme me variacione minimale Nga detajet në pjesën, nga kafazi në kafaz. Krahasuar меня metodat gjerësisht të përdorura të forcimit të përpunimit TERMIK kimik të pjesëve të çelikut, të тилла си çimentoja, CIMENTO нитро, cianizimi, azostalizimi я Gazit Metoda е джон-plazmës азотирования ка përparësitë kryesore:
ngurtësinë М.Е. të lartë të sipërfaqes С.Е. pjesëve të azotit
NUK ка deformim të pjesëve па përpunimit
rritja е kufirit të qëndrueshmërisë меня NJE rritje në rezistencën е veshjes С.Е. pjesëve të përpunuara
температура тп улет е procesit, PER shkak të С.Е. cilës ndryshimet strukturore NUK Kane ndryshime strukturore .
aftësia PER të përpunuar të shurdhër ДНЕ përmes vrimave
ruajtja е ngurtësisë С.Е. NJE shtrese të azotit па ngrohjes në 600 – 650 ° С
mundësia е marrjes С.Е. shtresave të përbërjes С.Е. specifikuar
aftësia PER të përpunuar produktet е madhësive të pakufizuara të çdo forme
mungesa e ndotjes së mjedisit
rritja e kulturës së prodhimit
reduktimi i kostos së përpunimit disa herë
Avantazhet e nitriding jon-plazma manifesthen në një reduktim të ndjeshëm të kostove kryesore të prodhimit.Për shembull, në krahasim me azostinimin e gazit të IPA-së siguron:
reduktimi i kohëzgjatjes së përpunimit nga 2 deri në 5 herë, si duke reduktuar kohën e reduktima ngrohjen duke 000 e reduktimal e reduktima ngrohjen i gazrave të punës (20 – 100 herë)
reduktimi i konsumit të energjisë elektrike (1.5 – 3 herë)
reduktimi i deformimit është kështu për të elleluar san bluarjen përfundhejena 9000 irmdhejenhimtare 9000 irmdhejenhésim 9000 irmdhejenhimtare 9000 irmdhejenhimtare 9000 i0005 plotë me teknologjinë me të gjitha kërkesat moderne mjedisore
Krahasuar me forcimin, metoda e përpunimit të jon-plazmës lejon:
përjashtojnë deformimet
rritja e burimeve të sipërfaqesagenike (2-5 герё)
Përdorimi i nitridës së jon-plazmës në vend të çimentimit, çimentos nitro, gaz ose azostit të lëngët, volumetrike ose tweas shuarje lejon:
ruaj zimelon ejisjet kryi
zvogëloni konsumin e energjisë elektrike, mediat aktive të gazit.
Konsumatorët kryesorë të pajisjeve për jon-plazma nitriding janë automobil, traktor, aviacion, ndërtimin e anijeve, riparimin e anijeve, makineri / makine fabrikat e përpiminerkéjët, pörpomhinéjët, e përpominéjét, pörpominéjéjét, fabrikat e përpiminerjéjë, профиль алюминит, импиантет и энергия. .
Metoda e nitridës jon-plazma është një nga zonat më dinamike në zhvillim të përpunimit termik kimik në vendet e industrializuara. Përdorimi i përhapur i metodës IPA gjetur në industrialrinë e automotivebilave.Мне нравится, когда вы используете автомобиль / мотоцикл под именами: Daimler Chrysler (Mercedes), Audi, Volkswagen, Voith, Volvo.
Për shembull, produktet e mëposhtme përpunohen me këtë metodë:
форсунки для макинат и пасажиров, пллакать и бартэсит тэ макинэс дэвэтикэ, матриц5000, грушта 9000, вытяжка 9000
граншевые валы (Audi)
распределительные валы (CAM) boshte (Volkswagen)
коленчатые валы на компрессор (ATLAS, SHBA dhe WABCO, Gjermani)
ингранажеты на BMW (Handl, Gjermani
) я mjetit të shtypit në prodhimin e produkteve të aluminit (nughuhhhovens, skandex, john devis, etj) Экзистон ньё пёрвой позитив и пёрдоримит индустриальный метод вендет в СНГ: Беллорусия – МЗКТ, Мази, Белаз; Россия – АвтоВАЗ, Камаз, ММПП “Салют”, Уфимское моторостроительное объединение (УМПО).
Metoda IPA përpunohet:
ingranazhet (mzkt)
ingranazhet dhe detaje të tjera (Maz)
diametri i madh (më shumë se 800 mm) (Belaz)
marrë e marrja e valvulave Гранчвалы
(Камаз)
Си përvojë Globale е përdorimit të teknologjisë Йон-Плазма-азотирование, efekti Ekonomik я zbatimit të Тц sigurohet kryesisht герцог reduktuar konsumin е energjisë elektrike, gazeve të punës, të zvogëlojë kompleksitetin е produkteve të prodhimit PER shkak të NJE reduktimi të ndjeshëm të volumit тэ пунэс сэ рэнде, Пёрмирэсими и цилэсэсэ сэ продуктит.
Sa i përket mjetit të prerjes dhe vulosjes, efekti ekonomik sigurohet duke zvogëluar konsumin e saj me forcë prej 4 ose më shumë herë rezistencën e veshit me një rritje të nerjëko reg.
Për disa produkte, азотирование jon-plazma është e vetmja mënyrë për të prodhuar një produkt të përfunduar me një përqindje minimale të martesës.
Përveç kësaj, processi IPA siguron siguri të plotë mjedisore.
Азотирование jon-plazma mund të pёrdoret në prodhim në vend të nitriding lëng ose gaz, çimentim, nitro çimento, forcim i TVch.
Ионно-плазменное азотирование (IPA) është një metodë moderne përforcuese e trajtimit të ngrohjes kimike të produkteve nga hekuri, karboni, çeliku i zhveshur dhe Instrumental, lidhjet e titleikametalanit, qwe. Efikasiteti i lartë i teknologjisë arrihet duke përdorur media të ndryshme të gazit që ndikojnë në formimin e një shtrese të diffuzionit të kompozimeve të ndryshme, në varësi solidness ejërkesave конкретность.
Azostacioni я metodës Йон-Plazma ешт relevante PER të përpunuar pjesët е ngarkuara QE veprojnë në mediat agresive QE pësojnë korrozioni fërkime ДЕНЬ kimike, prandaj përdoret gjerësisht në industrinë е ndërtimit të makinës, герцог përfshirë industrinë е makinerive, авто ДНО industrinë е avionëve, си dhe Në sektorin e naftës dhe gazit, karburantit dhe energjisë dhe minierave, продхим инструментальный dhe me saktësi të lartë.
në procesin й trajtimit sipërfaqësor мне përmirësimin х нитриды С.Е. joneve karakteristikat е sipërfaqes Metalet ДНО besueshmëria operacionale е pjesëve të përgjegjshme të makinave, motorëve, mjeteve të makinës, hidraulikës, mekanikës С.Е. saktë ДНО produkteve të tjera: rritja е lodhjes ДНО СИЛЫ С.Е. kontaktit, ngurtësinë e sipërfaqes dhe rezistencën ndaj rritjes së Plasaritjeve, Zasadacitetit, nxehtësisë dhe korrozionit rritet.
Avantazhet e jon плазменное азотирование
Teknologjia IPA ka një numër avantazhesh të padiskutueshme, kryesorja e të cilave është një cilësi e qëndrueshme e përpunimit me variacion minimal të pronave.Procesi i kontrolluar i ngopjes së diffuzionit të gazit dhe ngrohjes ofron një shtresë uniforme të përbërjes dhestrukturës së fazës së lartë të cilësisë së lartë.
- Ngurtësinë e sipërfaqes së lartë të pjesëve të azotit.
- Asnjë deformim i pjesëve pas përpunimit dhe pastërtisë së sipërfaqes së lartë.
- Reduktimi i kohës së përpunimit të çeliqeve 3-5 herë, lidhjet e titanit – në 5-10.
- Rritja e funksionimit të një sipërfaqe të azotit prej 2-5 herë.
- Mundësia e trajtimit të shurdhër dhe përmes vrimave.
Modaliteti i temperaturës së ulët Устранение Transformimet Strukturore të çelikut, zvogëlon gjasat е shkatërrimit dhe dëmtimit të lodhjes, lejon ftohjen me çdo shpejtësi pa rrezitezikun. Trajtimi në temperatura nën 500 ° C është veçanërisht e efektshme kur produktet e forcimit nga çeliku инструментальный сплав, me shpejtësi të lartë dhe martensite-plakje: pronat e Tire Operacionale tér 55-60
Një metodë e sigurt mjedisore e nitriding jon-plazma parandalon lakimin dhe deformimin e pjesëve duke ruajtur vrazhdësinë e sipërfaqes origjinale brenda ra = 0.63 … 1.2 mikronë.
Технология и процесс
Instalimet për IPA operohen në një atmosferë të shkarkuar në një presion prej 0,5–10 мбар. Dhoma që vepron në parimin e katodës dhe sistemit të anodës i jepet një përzierje e gazit jonizues.Një shkarkim и ndezur i impulsit është formuar midis pjesëve të përpunuara dhe mureve të dhomës së vakumit. Medium aktiv i krijuar nën ekspozimin e saj, i përbërë nga jonet e ngarkuara, atomet dhe molkulat, formon një shtresë të azotit në sipërfaqen e produktit.
Përbërja e Mediumit të ngopur, temperatura dhe kohëzgjatja e Processit ndikon në thellësinë e depërtimit të nitrideve, герцог shkaktuar një rritje të ndjeshme në qëndruesvehmresëqërinë ee.
Acitrogjenizimi jonik i pjesëve
Азотирование Jonik ешт përdorur gjerësisht në mënyrë QE të ngurtësojë pjesët х makinave, mjeteve të punës ДЕНЬ pajisjeve teknologjike të madhësive ДЕНЬ formave të pakufizuara: veshje ДЕНЬ boshte të pajisjeve të pajisjeve ДНО cilindrike, veshje konike ДЕНЬ cilindrike, экструдеры, lidhjet е konfigurimit Kompleks gjeometrik , vida, prerje dhe mjetet e shpimit, mandrrat, matricat dhe grushtat për vulosjen, формы.
Për një numër të produkteve (ingranazhet me gjashtë diametër për makinën e rëndë, exkavatorët, etj.), IPA është mënyra e vetme për të prodhuar produkte të gatshmer meqë.
Prona të produkteve pas forcimit nga IPA
Forcimi i ingranazheve duke përdorur metodën e nitridës së jon rrit qëndrueshmërinë е dhëmbëve kur testimi për lodhjen nën bending në 930 MPA, redukton ndjeshëm echerenëm karakteristikat.
Teknologjia е азотирования Йон-Плазма ешт përdorur gjerësisht PER të ngurtësuar shtresën sipërfaqësore të форма të përdorura Кур hedh NEN presión: shtresa х azotit parandalon ngjitjen е metalit në ZONEN е ushqimit të lëngut të lëngët, ДНО Прочези я mbushjes С.Е. FORMES Бехчет Me пак я trazuar, e cila rrit jetën e mykut, dhe ofron hedhjen e cilësisë së lartë.
Ионно-плазменное азотирование në 4 ose më shumë herë rrit rezistencën e veshit të vulës dhe veglave të prerjes të bëra nga pulla çeliku R6M5, P18, P6M5K5, R12F4K5 dhe téritë meratje tjët.Sipërfaqja е veglës С.Е. azotit PER shkak të koeficientit të zvogëluar të fërkimit siguron NJE heqje М.Е. të LEHTE të çipit, ДНО gjithashtu е pengon ATE në fërkimin е prerjes С.Е. skajeve е Cila дзя Лейон të rrisni ushqimin ДНО shpejtësinë е prerjes.
Kompania Ionmet ofron shërbime PER forcimin е sipërfaqeve të materialeve strukturore të llojeve të ndryshme të pjesëve ДЕНЬ mjeteve меня metodën е-Йон plazmës азотирование – modaliteti я përzgjedhur я saktë сделать t’ju lejojë të arrini treguesit х nevojshëm Teknik të ngurtësisë ДНО thellësisë С.Е. shtresës сэ азотит, делай тэ офройэ ветитэ э ларта тэ консумит тэ продуктеве.
- Forcimi i shtresës së sipërfaqes së modulit të mirë dhe ingranazheve të mëdha, boshtet e boshtit dhe shpërndarjes, udhözuesit, втулки, рукава, auks, cilindset, etjs.
- Rritja e rezistencës ndaj ngarkesës ciklike dhe pulsulus të boshteve të boshtit dhe boshteve të CAM, shtytësit, valvulat, rrotat e marsheve etj.
- Rritja e rezistencës së veshit dhe rezistencës korrozioni, rënie në ngjitjen metalike kur hedh molds, shtypni dhe pulla molotovy, grushta për shkarkim të thellë, matricat.
Procesi i niktimit ndodh në instalimet moderne të automatizuara:
- Ø табела 500 мм, 280 мм и лоток;
- Табела Ø 1000 мм, длина 1400 мм.
Për të sqaruar gamën e plotë të produkteve për përpunimin e forcimit, si dhe mundësinë e nitrimit të pjesëve të mëdha me një gjeometri komplekse, mund të jenë Ionmetët нга специалист. Пэр тэ përcaktuar kushtet teknike të nisërimit dhe fillimit të bashkëpunimit, на дэргони нджэ визатим, спецификони маркат и челикут дхе текнологджинэ и продхимит шембуллор тэ пйесэве.