Сталь для подшипников марка: Стали для подшипников
alexxlab | 11.09.1991 | 0 | Разное
Подшипниковые стали
Сталь подшипниковая нужна для изготовления колец, шариков и роликов подшипников качения. Для подшипников качения требуется сталь, имеющая высокую твердость, износостойкость и сопротивляемость контактной усталости. К таким требованиям подходит высокоуглеродистая хромистая сталь высокого качества, чистая по неметаллическим включениям и карбидной неоднородности.
Сталь подшипниковую изготовляют из марок ШХ4, ШХ15, ШХ15СГ и ШХ20СГ.
Хром увеличивает твердость и износостойкость стали и обеспечивает необходимую прокаливаемость. Легирование кремнием и марганцем проводят для повышения прокаливаемости и применяют для сталей, которые используются для изготовления крупногабаритных подшипников (с толщиной стенки более 10 мм).
Сопротивление контактной усталости напрямую зависит от наличия различных металлургических дефектов (сульфидных и оксидных включений, пористости и др.), которые, попадая на рабочую поверхность, служат концентраторами напряжений, вызывая преждевременное разрушение стали от усталости.
Сталь отожженная горячекатаная, калиброванная и сталь со специальной отделкой поверхности в состоянии поставки должны иметь твердость: 179-207 НВ – для марки ШХ15; 179-217 НВ – для марок ШХ15СГ и ШХ20СГ.
Сталь подшипниковую изготовляют в виде прутков, груб, проволоки. После смягчающего сфероидизирующего отжига она получает структуру мелкозернистого перлита, что обеспечивает удовлетворительную обрабатываемость резанием и хорошую пластичность при холодной штамповке шариков или роликов.
Термообработка деталей подшипника состоит из закалки и низкого отпуска. Механические свойства сталей марок ШХ15 и ШХ15СГ для шарико- и роликоподшипников после закалки и низкого отпуска приведены в таблице.
Таблица
НДС |
Для стали марки ШХ15 |
Для стали марки ШХ15СГ |
||||
Предел прочности при изгибе, МПа |
Предел выносливости при изгибе, МПа |
Ударная вязкость, Дж/см2 |
Предел прочности при изгибе, МПа |
Предел выносливости при изгибе, МПа |
Ударная вязкость, Дж/см2 |
|
50-60 |
3139-3237 |
628 |
35-40 |
3139-3237 |
638 |
40-45 |
61-62 |
2649-2747 |
716 |
25-40 |
2845-2943 |
657 |
30-35 |
63-64 |
2452-2551 |
647 |
20-25 |
2649-2747 |
696 |
25-30 |
Перспективным является применение индукционного нагрева для закалки деталей подшипников качения, что дает возможность получить твердый поверхностный слой с сохранением вязкой сердцевины.
Твердость поверхности деталей подшипника при любом способе закалки должна быть в пределах 61–66 НRС. Последней операцией термической обработки является низкий отпуск при температуре 150–170 °С с выдержкой в течение 2–5 ч. Цель отпуска – уменьшение закалочных напряжений в деталях подшипника. Перед отпуском для снижения количества остаточного аустенита прецизионные (особо точного изготовления) подшипники подвергают обработке холодом с охлаждением до температуры –10.
Подшипники качения – важные детали многих машин и механизмов, поэтому стали для их производства являются конструкционными, по составу и свойствам они близки к инструментальным из-за работы при высоких локальных нагрузках.
Основные требования к подшипниковым сталям следующие.
1. Высокая статическая грузоподъемность. Предельной является нагрузка, при которой допустимые остаточные деформации в зоне контакта между шариком (роликом) и кольцами менее 0,01% диаметра шарика (ролика). Давления в данном случае достигают 4000 МПа. Поэтому выбраны заэвтектоидные, легированные стали с содержанием 1% С и 1,5% Сr (типа ШХ15), обработанные закалкой и низким отпуском для максимальной твердости. В марке стали ШХ15 (ГОСТ 801-78) буква Ш означает «шарикоподшипниковая», а 15 – содержание Сr в десятых долях процента. Сталь содержит 0,95– 1,05% С и 1,30–1,65% Сr.
2. Высокое сопротивление контактной усталости. Оно зависит от количества сульфидных и оксидных включений, а также от содержания водорода, которые понижают долговечность и способствуют ускорению разрушения из-за контактной усталости. Отсюда требования по чистоте в отношении неметаллических включений к карбидной неоднородности. Способ борьбы с неметаллическими включениями – рафинирующие переплавы. Если принять за 100% содержание включений в ШХ15 открытой выплавки, то после обработки синтетическим шлаком в ШХ15-Ш содержание включений уменьшается до 45%, после вакуумнодуговой плавки ШХ15-ВД – до 35%. Использование шлака и вакуумно-дугового переплава ШХ15-ШД обеспечивает уже 25% включений.
3. Подшипники качения испытывают износ от пылевидных частиц грунта, поэтому присутствие в стали Сr благотворно тем, что он увеличивает количество карбидной фазы и позволяет получить твердые специальные карбиды.
4. Размерная стабильность – довольно сильно важный параметров подшипника качения, поскольку изменения размеров приводят к заклиниванию подшипника и его разрушению. Допустимые изменения размеров менее 10~5 мм, они зависят от содержания остаточного аустенита. Чем меньше доля остаточного аустенита, тем лучше, так как при высоких нагрузках может произойти переход его в мартенсит с изменением объема.
Для подшипников специального назначения, работающих в агрессивных средах, применяют коррозионностойкие (нержавеющие) подшипниковые стали. Они содержат 18% Сr и характеризуются хорошей износостойкостью и коррозионной стойкостью. Одна из таких сталей – 95X18, ее термообработка – ступенчатый, из-за низкой теплопроводности, нагрев под закалку 850 °С, затем 1080 °С, охлаждение в масле или струе газа, затем обработка холодом, отпуск 160 °С – 3 ч, НRС 58–60.
Для подшипников, работающих при повышенных температурах применяются дисперсионно-твердеющие стали – высокопрочные стали, как и все подшипниковые, но с высокой устойчивостью к повышенным температурам эксплуатации. Наилучшие механические свойства таких сталей достигаются в результате вторичного твердения.
Из дисперсионно-твердеющей стали 8Х4В9Ф2Ш делают теплостойкие подшипники. При повышении температуры отпуска у данной стали наблюдается провал твердости НRС при 250–400 °С, что соответствует распаду мартенсита. При нагреве выше 400 °С твердость вновь повышается, начинается вторичное твердение, максимум твердости достигается при температуре 500-550 °С.
Рассмотрев подшипниковые стали, можно сделать вывод что существует очень множество нюансов при выборе стали для подшипников, а также многое зависит от назначения подшипников.
Подшипниковая сталь: виды, свойства, применение
- Что такое подшипниковая сталь
- Виды подшипниковой стали
- Сталь для подшипников с обычными условиями работы
- Сталь для подшипников с агрессивными условиями работы
- Свойства шарикоподшипниковых сталей
- Таблица 1 «Химический состав подшипниковых марок стали»
- Таблица 2 «Механические свойства сталей по ГОСТ 801»
- Область применения подшипниковых сталей
В условиях современного инжиниринга производственные механизмы, бытовую технику, приборы и автотранспорт все шире оснащают подшипниками. Такая всесторонняя востребованность обуславливает ужесточение требований к их служебным свойствам. Это, в свою очередь, определяет более строгие критерии отбора материалов для изготовления подшипников и жестко регламентирует свойства, которыми должна обладать подшипниковая сталь, ведь несмотря на различия в конструкции, данные опорные элементы работают в условиях высоких локальных нагрузок, интенсивных вибраций и больших скоростей.
Что такое подшипниковая сталь
Этот термин определяет специальную группу высокоуглеродистых и легированных сталей, используемых для изготовления тел качения, корпусных колец и других элементов подшипников. Как опорные узлы сборной конструкции они испытывают на небольшой контактной площади высокие давления (иногда значительно превышающие 2000 МПа) и критические сжимающие и изгибающие нагрузки. А пластические деформации, возникающие в поверхностном слое металла при работе подшипника, приводят к возникновению остаточных напряжений, которые сильно усложняют картину распределения нагрузок.
- обеспечивать быстроходность кинетических пар;
- характеризоваться высокой твердостью и износостойкостью;
- стойко сопротивляться концентрации усталостных напряжений;
- обладать большим эксплуатационным ресурсом и целым рядом специфических качеств.
Ее химические и физические свойства напрямую определяют качество работы и долговечность этих сборных элементов. А стоимость подшипниковой стали влияет на итоговую себестоимость выпускаемой продукции и рентабельность производства.
Еще в середине прошлого века в инжиниринге использовались в основном шариковые подшипники. В результате за высокоуглеродистыми сталями с повышенным содержанием хрома, которые широко использовались для изготовления подшипниковых тел вращения и колец, закрепилось название «шарикоподшипниковые стали». В наши дни, когда уже применяются игольчатые и роликовые подшипники качения, а также различные подшипники скольжения, термин «шарикоподшипниковые стали» все равно иногда применяется и встречается в технической литературе, изданной до 90-х годов XX столетия.
Чтобы не искажать устоявшиеся технические традиции, согласно ГОСТ 801 на подшипниковые стали маркировка предполагает наличие в самом начале аббревиатуры буквы «Ш». Внимание, этот же символ в конце маркировки указывает, что сталь получена путем электрошлакового переплава.
ДСТУ ISO 683-17 и ГОСТ 801 также предполагают, что на шарикоподшипниковые стали маркировка может включать не только сведения о химическом составе, но и информацию о способе выплавки и термической обработке. По EN 10027 таким сталям присваивается номер 1.35ХХ, а в Японии маркировка содержит буквы SUJ и порядковый номер.
По характеру применения марки сталей для подшипников считаются конструкционными, но химический состав и эксплуатационные качества относят их к инструментальным. Критерии качества и требования, предъявляемые к таким маркам, кардинально отличаются от других машиностроительных, строительных и конструкционных сталей и сплавов. Например:
- крайне важно сохранить твердость подшипниковой стали для узлов, длительное время работающих при повышенных температурах, чтобы обеспечить достаточную статическую и динамическую грузоподъемность. Поэтому особое внимание уделяется составу и способу выплавки, так как неметаллические включения в металле снижают работоспособность и долговечность подшипников;
- отдельно рассматривается структурная нестабильность при низких и высоких температурах и ее влияние на изменение геометрии и точность размеров подшипниковых элементов;
- определяющим фактором является локальное сопротивление усталости металла в зоне контакта элементов качения.
Виды подшипниковой стали
Разнообразные требования к эксплуатационным свойствам и отличающиеся условия работы подшипников обуславливают широкую номенклатуру используемых сталей, поэтому в мировой и отечественной практике используется несколько классифицирующих систем. Например, ДСТУ ISO 683-17 предполагает разделение подшипниковых сталей на пять групп: сквозной прокаливаемости, цементируемые, с индукционной закалкой, нержавеющие и жаростойкие. Но производители и потребители чаще оперируют упрощенной классификацией, основанной на условиях эксплуатации.
Сталь для подшипников с обычными условиями работы
К этой группе относятся стали общего назначения, рассчитанные на работу без присутствия агрессивных компонентов в окружающей среде и при температурах от -60 до +300°С. В нее включаются такие стали как хромистые, хромомарганцевокремнистые, хромистые и хромомарганцевые с добавкой молибдена. Чаще всего это:
- ШХ15 – высокоуглеродистая хромистая сталь, характеризующаяся высоким сопротивлением контактной усталости и отличной износостойкостью;
- ШХ15СГ – модифицированная низколегированная марка, которая за счет повышенного содержания кремния и марганца лучше прокаливается;
- ШХ20СГ – легированная шарикоподшипниковая сталь с повышенным содержанием хрома, марганца и кремния, предназначенная для изготовления толстых подшипниковых колец;
- 25Х1МФ – марка, легированная молибденом и отличающаяся неплохой свариваемостью и обрабатываемостью.
Сталь для подшипников с агрессивными условиями работы
К этой группе относят высокохромистые стали, способные работать в условиях высокой влажности, агрессивной среды и температур, достигающих +400°С и выше. Они содержат углерод в пределах 1%, сочетают высокую твердость после закалки и низкотемпературного отпуска с достаточно высоким уровнем коррозионной и тепловой стойкостью. В эту группу входят:
- 95Х18-Ш. Сталь, использующаяся для деталей подшипников средних и крупных размеров, эксплуатируемых в условиях агрессивной среды, в том числе в парах азотной кислоты и растворах хлористого натрия;
- 11Х18М-ШД. Это коррозионностойкая и теплостойкая шарикоподшипниковая сталь – маркировка указывает, что она легирована молибденом, который повышает твердость металла и минимизирует негативное влияние водорода. Марка отлично зарекомендовала себя в малогабаритных и миниатюрных приборных подшипниках;
- 8Х4В9Ф2-Ш (ЭИ347) – теплостойкая сталь, обеспечивающая в условия комнатной температуры после стандартной термической обработки твердость в пределах HRC 59…65.
Отлично работает при температурах до +500°С, но из-за присутствия вольфрама склонна к карбидной неоднородности;
- 8Х4М4В2Ф1-Ш – экономнолегированная марка и более дешевый аналог 8Х4В9Ф2-Ш, не уступающий ей в износостойкости и контактной усталости. При этом вязкость 8Х4М4В2Ф1-Ш в 1,5 раза выше.
В мировой практике используются следующие коррозионностойкие подшипниковые стали – X47Cr14, X65Cr14, X108CrMo17, X89CrMoV18-1; и жаростойкие – 80MoCrV42-16, 13MoCrNi42-16-14, X82WMoCrV6-5-4, X75WCrV18-4-1.
Учитывая сложный химический состав, высоколегированные шарикоподшипниковые стали свойства теплостойкости и коррозионной стойкости сочетают с тугоплавкостью и удовлетворительной обрабатываемостью. А вследствие большого количества хрома и углерода в них может возникать ликвация, карбидная неоднородность и структурная полосчастость. По этой причине иногда для производства подшипников используются и другие стали. Например, сталь 20 используется для вкладышей, 50Г2 – втулок, 65Г – корпусов, но так как они не имеют характерные для шарикоподшипниковых сталей свойства, их не принято причислять к таковым.
![]()
Свойства шарикоподшипниковых сталей
Выплавленные путем рафинирующих электрошлаковых переплавов или в электрических печах с вакуумированием или без него шарикоподшипниковые стали свойства должны иметь в соответствии с требованиями нормативной документации. Ключевые параметры – химический состав, геометрические размеры, качество поверхности, параметры макро- и микроструктуры. При этом механические свойства, в отличие от химического состава, в стандартах и технических условиях часто не оговариваются. Отчасти это обусловлено тем, что:
- продукция, выпускаемая по данным стандартам, является полуфабрикатом для изготовления элементов подшипников и приобретает конечный комплекс характеристик после термической обработки готовых изделий;
- некоторые дефекты вызываются нарушениями технологии термической, механической и другой обработки при изготовлении деталей из поковок и проката, не имеющих дефектов, в результате чего получают изделия бракованные или недолговечные;
- подшипниковые стали эксплуатируются в высокопрочном состоянии (после закалки на мартенсит и низкотемпературного отпуска).
Это упраздняет корреляционную связь между контактной усталостной прочностью и механическими свойствами в отожженном состоянии.
Обеспечение особых свойств и повышенной твердости стали для подшипников осуществляется путем введения хрома и других легирующих элементов, а также контролированным процессом раскиления. За счет использования марганца (Mn), кремния (Si) и алюминия (Al) снижается общая газонасыщенность металла, а также минимизируется количество и размер неметаллических включений.
При этом химическая чистота материала нормируется в зависимости от марки стали. А вот глубина обезуглероженного слоя зависит от состояния поставки.
Химический состав подшипниковых марок стали
Марка |
Страна |
Стандарт |
Химический состав |
|||||||||
C |
Si |
Mn |
Cr |
Mo |
Ni |
Cu |
P |
S |
Al |
|||
100Cr6 (1. |
Евросоюз |
EN ISO 683 |
0,93…1,05 |
0,15…0,35 |
0,25…0,45 |
1,35…1,60 |
до 0,10 |
— |
до 0,30 |
до 0,025 |
до 0,015 |
0,05 |
52100 |
США |
AISI SAE, ASTM A295M |
0,93…1,05 |
0,15…0,35 |
0,25…0,45 |
1,35…1,60 |
до 0,10 |
до 0,25 |
до 0,30 |
до 0,025 |
до 0,015 |
0,05 |
GCr15 |
КНР |
GB/T 18254 |
0,95…1,05 |
0,15…0,35 |
0,25…0,45 |
1,40…1,65 |
до 0,10 |
до 0,25 |
до 0,25 |
до 0,025 |
до 0,020 |
0,05 |
SUJ2 |
Япония |
JIS G4805 |
0,95…1,10 |
0,15…0,35 |
< 0,50 |
1,30…1,60 |
до 0,08 |
до 0,25 |
до 0,25 |
до 0,025 |
до 0,025 |
— |
ШХ-15 |
СНГ |
ГОСТ 801 |
0,95…1,05 |
0,17…0,37 |
0,20…0,40 |
1,30…1,62 |
— |
до 0,30 |
до 0,25 |
до 0,027 |
до 0,020 |
— |
ШХ15СГ |
СНГ |
ГОСТ 801 |
0,95…1,05 |
0,40…0,65 |
0,90…1,20 |
1,30…1,65 |
— |
до 0,30 |
до 0,25 |
до 0,027 |
до 0,020 |
— |
ШХ20СГ |
СНГ |
ГОСТ 801 |
0,90…1,00 |
0,55…0,85 |
1,40…1,70 |
1,40…1,70 |
— |
до 0,30 |
до 0,25 |
до 0,027 |
до 0,020 |
— |
95Х18 |
СНГ |
ГОСТ 5632 |
0,90…1,00 |
до 0,80 |
до 0,80 |
17,0…19,0 |
— |
до 0,60 |
до 0,30 |
до 0,030 |
до 0,025 |
— |
X65Cr14 |
Украина |
ДСТУ ISO 683-17 |
0,60…0,70 |
до 1,00 |
до 1,00 |
12,5…14,5 |
до 0,75 |
— |
— |
до 0,04 |
до 0,015 |
— |
Из-за тяжелого режима эксплуатации к подшипниковым маркам стали предъявляют обширный перечень требований. Они должны хорошо прокаливаться и сопротивляться усталостному выкрашиванию, сколам, трещинам, а также характеризоваться:
- высокой износостойкостью;
- малым коэффициентом поверхностного трения;
- повышенным сопротивлением усталости, старению и пластическим деформациям;
- минимально допустимым количеством неметаллических включений и низкой карбидной неоднородностью;
- способностью обеспечить высокую статическую и динамическую грузоподъемность;
- хорошей теплопроводностью и смачиваемостью маслом;
- низким коэффициентом линейного расширения.
Параметры их коррозионной стойкости, так же как немагнитные свойства, могут варьироваться. При этом помимо вышеперечисленных свойств для подшипниковых сталей немаловажны доступная стоимость и обрабатываемость. Последний технологический критерий определяет высокие требования к химическому составу, микроструктуре и твердости металла и определяет способность материала к шлифованию, обработке резаньем и холодной штамповкой.
Механические свойства сталей по ГОСТ 801
Марка стали |
Вид термической обработки |
Твердость HB |
ШХ15 |
Отжиг |
179…207 |
ШХ15СГ |
Отжиг |
179…217 |
ШХ20СГ |
Отжиг |
179…217 |
Область применения подшипниковых сталей
Высокоуглеродистая и хромсодержащая подшипниковая сталь марки ШХ15 и ШХ15СГ широко применяется для изготовления тел вращения, колец и корпусов подшипников, используемых в:
- станках для машиностроения, деревоперерабатывающей и легкой промышленности;
- сталепрокатном, буровом и геологоразведочном оборудовании;
- двигателях внутреннего сгорания и электрических машинах;
- строительной технике;
- электровозах;
- тракторах;
- насосах.
Измерение подшипника штангенциркулем
Сталь подшипниковая выбирается исходя из габаритов и особенностей эксплуатации подшипника. Так, хромистые и хромомарганцевокремнистые марки используются для подшипников, рассчитанных на работу в температурном интервале от -60 до +300°С, но, если предполагается эксплуатация при температурах выше 100°С, детали термообрабатывают. Чтобы обеспечить сквозную прокаливаемость, шарикоподшипниковая сталь ШХ15 используется для колец с толщиной стенки 10…30 мм, для более габаритных уже целесообразно применять марку ШХ20СГ.
Подшипники из высокоуглеродистых марок стали также используются в железнодорожном подвижном составе и ветровых электрогенераторах, рольгангах и грузоподъемных механизмах. Но при производстве подшипников используются не только высоколегированные шарикоподшипниковые стали – примеры: ЭИ-293, ЭИ-336. Это графитизированные стали, обладающие антифрикционными свойствами и высокой твердостью, что позволяет их использовать в мелкосерийном производстве массивных подшипников для изготовления сепараторов с цилиндрическими и фрезерованными окнами, приставными шайбами и цельными окнами для роликов. А сепараторы упорных подшипников для червячных редукторов, патронов и шпинделей металлорежущих станков, крюковых кранов и домкратов могут изготавливаться из обычной стали 20.
НОВАЯ ТЕПЛОСТОЙКАЯ СТАЛЬ ДЛЯ АВИАЦИОННЫХ ПОДШИПНИКОВ
- 2022
- 2021
- 2020
- 2019
- 2018
- 2017
- 2016
- 2015
- 2014
- 2013
№1 | №2 | №3 | №4 | №5 | №6 | №7 | №8 | №9 | №10 | №11 | №12
dx.doi.org/ 10.18577/2307-6046-2019-0-2-17-23
УДК 669.15
Gromov V.I., Kurpyakova N.A., Korobova E.N., Sedov O.V.
НОВАЯ ТЕПЛОСТОЙКАЯ СТАЛЬ ДЛЯ АВИАЦИОННЫХ ПОДШИПНИКОВ
Рассмотрены принципы легирования новой подшипниковой стали, проанализировано влияние неметаллических включений на работоспособность подшипников, исследована карбидная неоднородность в полуфабрикатах (прутках) разного сортамента и рассмотрены методы ее снижения. Проведен сравнительный анализ карбидной неоднородности полуфабрикатов из новой подшипниковой стали с полуфабрикатами того же размера из отечественного аналога – сплава ЭИ347. Показано влияние упрочняющей термической обработки стали на прочность, твердость и теплостойкость.
Ключевые слова: теплостойкость, подшипники, карбидная неоднородность, микроструктура, твердость, прочность, легирующие элементы, выплавка, горячая пластическая деформация, термическая обработка, heat resistance, bearings, carbide heterogeneity, microstructure, hardness, strength, alloying elements, smelting, hot plastic deformation, heat treatment.
Введение
Разработка теплостойких сталей для авиационных подшипников – одна из важнейших задач современного материаловедения. Во ФГУП «ВИАМ» исследования по разработке составов, технологий производства полуфабрикатов и термической обработки теплостойких подшипниковых сталей проводятся в рамках «Стратегических направлений развития материалов и технологий их переработки на период до 2030 года» [1–4].
В авиационной технике подшипники работают в сложных условиях. В зоне контакта тел качения и колец подшипников в результате многократно повторяющегося нагружения возникают высокие контактные нагрузки, приводящие к интенсивному изнашиванию. Кроме того, детали испытывают знакопеременные и ударно-вибрационные нагрузки, воздействие коррозионных сред и повышенных температур. Для обеспечения высокой работоспособности и надежности авиационных подшипников, стали, из которых изготавливаются тела качения и кольца, должны иметь:
– высокую прочность и сопротивление пластической деформации;
– высокую износостойкость, которая определяется твердостью, а также количеством и формой специальных карбидов;
– высокое контактное сопротивление усталости, которое зависит от микроструктуры стали и карбидной однородности;
– размерную стабильность;
– хорошую прокаливаемость [5–7].
Подшипниковые стали классифицируются по условиям работы. Различают стали общего назначения, используемые для изготовления деталей подшипников, работающих при температурах от -60 до +300°С в неагрессивных средах, и стали специального назначения для изготовления теплостойких и коррозионностойких подшипников [8].
Опыт изготовления полуфабрикатов из подшипниковых сталей показывает, что для получения повышенного комплекса механических свойств необходимо:
– использование металла высокого качества по газонасыщенности (N2, O2, Н2), чистоте по неметаллическим включениям, отсутствию вредных примесей (As, Pb, Sn), в связи с чем выплавка сталей должна проводиться с применением вакуумных технологий;
– при горячем переделе металла степень его деформации (проработки) должна быть максимально возможной;
– термическая обработка деталей подшипников должна проводиться на специализированном оборудовании, обеспечивающем точное поддержание температуры и исключающем обезуглероживание поверхности.
Для изготовления теплостойких подшипников, работающих в условиях смазки при температуре 200–300°С, а в экстремальных ситуациях – до 500°С, применяют дисперсионно-твердеющие стали, разработанные на основе инструментальных быстрорежущих сталей. За рубежом в основном применяется сталь марки М50, разработанная в США фирмой General Electric Company, которая по способу термической обработки относится к сталям с дисперсионно-карбидным упрочнением. Сталь марки М50 зарекомендовала себя как материал с высокой долговечностью, что объясняется однородностью структуры и отсутствием крупных карбидных включений, негативно влияющих на контактную выносливость. Химический состав стали М50 взят за основу для разработки теплостойких подшипниковых сталей и в других странах. Так, во Франции – это сталь марки 80DCV40, в Германии – марки 80МоCrV4216.
В России для изготовления теплостойких авиационных подшипников используют сталь ЭИ347 (8Х4В9Ф2-Ш), которая обладает высокой прочностью и хорошей твердостью (не ниже 56 HRC) при работе в условиях – до 500°С [8]. Однако в отличие от стали М50, сталь ЭИ347 имеет бо́льшую карбидную неоднородность, что объясняется присутствием в ее составе вольфрама, образующего крупные скопления нерастворимых при нагревах (вплоть до температур плавления) карбидов, которые являются очагами выкрашивания рабочей поверхности подшипников в процессе эксплуатации. Кроме того, крупные сегрегации нерастворимых карбидов при производстве полуфабрикатов из стали ЭИ347 существенно усложняют процесс ковки и исключают прокатку.
Химический состав сталей, чаще всего применяемых для изготовления деталей подшипников, представлен в табл. 1 [8].
Таблица 1
Химический состав сталей для изготовления подшипников качения
Сталь |
Содержание элементов, % (по массе) |
||||||||||
С |
Si |
Mn |
Cr |
P |
S |
Ni |
Cu |
Mo |
W |
V |
|
не более |
|||||||||||
M50 |
0,77–0,85 |
≤0,25 |
≤0,35 |
3,75–4,25 |
0,015 |
0,015 |
0,1 |
– |
4,0–4,5 |
– |
0,9–1,1 |
ЭИ347 |
0,70–0,80 |
≤0,25 |
≤0,25 |
4,0–4,6 |
0,030 |
0,015 |
0,35 |
0,25 |
≤0,80 |
8,5–9,5 |
1,4–1,7 |
80DCV40 |
0,77–0,85 |
0,1–0,4 |
0,1–0,4 |
3,75–4,5 |
0,015 |
0,015 |
0,2 |
0,2 |
3,75–4,5 |
0,25 |
0,9–1,2 |
80МоCrV4216 |
0,77–0,85 |
≤0,25 |
≤0,35 |
3,75–4,25 |
0,015 |
0,015 |
0,1 |
– |
4,0–4,5 |
– |
0,9–1,1 |
Следует отметить, что за рубежом, несмотря на разнообразие разработанных подшипниковых сталей, основным материалом для изготовления авиационных подшипников является сталь М50 и цементуемая сталь марки М50Nil.
Для производства конкурентоспособных теплостойких отечественных подшипников во ФГУП «ВИАМ» создана новая теплостойкая подшипниковая сталь, не уступающая по свойствам стали М50 и превосходящая по карбидной однородности сталь ЭИ347. В табл. 2 приведены сравнительные свойства вышеперечисленных сталей.
Таблица 2
Сравнительные свойства теплостойких подшипниковых сталей
Свойства |
Значения свойств для сталей |
||
новой подшипниковой |
ЭИ347 (Россия) |
М50 (США) |
|
Предел прочности при растяжении, МПа |
2270–2340 |
2100 |
– |
Теплостойкость, °С |
500 |
500 |
500 |
Предел выносливости σ-1, МПа |
650 (на базе 2·107 циклов) |
650 (на базе 107 циклов) |
– |
Ударная вязкость KCU, Дж/см2 |
≥5 |
2 |
>5 |
Плотность, кг/м3 |
7890 |
8300 |
– |
Твердость HRC |
61–63 |
≥60 |
≥60 |
Технологичность полуфабриката |
Прокатка |
Ковка |
Прокатка |
Работа выполнена в рамках реализации комплексной научной проблемы 8. 3. «Высокопрочные наноструктурированные конструкционные стали и диффузионные покрытия, получаемые методами химико-термической обработки» («Стратегические направления развития материалов и технологий их переработки на период до 2030 года») [1].
Материалы и методы
Для исследования механических свойств и микроструктуры новой стали использовали образцы, изготовленные из слитков, поковок (заготовок) и прутков в состоянии до и после термической обработки. Определение химического состава стали проводили в соответствии с ГОСТ Р 55079–2012, ГОСТ 12344–2003 и ГОСТ 12345–2001 на оборудовании фирмы Leco. Металлографические исследования проводили на оптическом микроскопе Olympus GX-51, оснащенном фотокамерой и программой анализа изображений Analysis в соответствии с ГОСТ 8233–56, ГОСТ 1778–70, ГОСТ 5950–2000 и ГОСТ 5639–82 на металлографических шлифах после травления в 4%-ном спиртовом растворе HNO3. Измерение твердости осуществляли на твердомере DuraVision 300 по ГОСТ 9013–59 по методу Роквелла, определение механических свойств – в соответствии с ГОСТ 1497–84, ГОСТ 9454–78 и ГОСТ 25. 502–79 на испытательном оборудовании фирмы Walter+Bai.
Результаты и обсуждение
Состав новой теплостойкой подшипниковой стали разработан на основании опыта ФГУП «ВИАМ» по созданию теплостойких дисперсионно-твердеющих цементуемых сталей и изучения тенденций легирования теплостойких подшипниковых сталей.
Выбрана система легирования, повышающая технологичность стали при пластической деформации и упрочнении. При высоком содержании углерода варьировали содержание основных карбидообразующих элементов: Cr, Mo, W, V, обеспечивающих вторичную твердость стали при отпуске.
Эффект упрочнения при вторичном твердении обусловлен выделением дисперсных карбидов, таких как Ме7С3, Ме23С6 (на базе хрома), Ме2С (молибдена) и МеС (ванадия), а также основного карбида теплостойких сталей М6С (на базе вольфрама и молибдена). Карбид М6С, в котором присутствуют вольфрам и молибден одновременно, в отличие от карбида, где присутствует только вольфрам, имеет меньшие размеры и растворяется при более низких температурах, что благоприятно для снижения балла карбидной неоднородности [8]. В связи с этим при выборе системы легирования в состав стали вводили молибден и вольфрам в различных соотношениях. Для обеспечения мелкозернистой структуры в сталь вводили также ниобий и тантал, которые образуют устойчивые карбиды (NbC, TaC), практически не растворимые в аустените, и являются дополнительными центрами кристаллизации, сдерживающими рост зерна при нагреве под закалку, что положительно влияет на сопротивление хрупкому разрушению и одновременно способствует упрочнению.
Определили также влияние некарбидообразующих элементов (Ni, Mn и Si) на процессы упрочнения и технологичность стали. Никель увеличивает устойчивость аустенита, из которого при отпуске выделяются субмелкодисперсные спецкарбиды, но при содержании ˃0,4% (по массе) никель затрудняет получение при отжиге твердости ≤30 HRC, необходимой для дальнейшей механической обработки полуфабрикатов.
Марганец и кремний использовали как раскислители. Кроме того, кремний вводился как элемент, оказывающий положительное влияние на повышение твердости при дисперсионном твердении в процессе отпуска. Однако его содержание было ограничено, так как известно, что при содержании ˃0,5% (по массе) кремний затрудняет горячую пластическую деформацию, препятствует росту карбидов при отпуске и сдвигает процессы отпуска в сторону более высоких температур.
Содержание углерода варьировали в пределах от 0,7 до 1,0% (по массе). Исследования показали, что количество углерода ˃0,85% (по массе) недопустимо, поскольку в литой микроструктуре слитков обнаружены зернограничные фрагменты эвтектической кристаллизации карбидов. Наличие таких структурных составляющих нежелательно, так как они нерастворимы при нагреве до температуры ковки и тем более до температуры нагрева под закалку.
Выбранная система легирования позволила длительно обеспечить теплостойкость новой стали до 500°С (твердость 61–63 HRC). Необходимо отметить, что разработанная сталь содержит значительно меньшее количество дорогого легирующего элемента вольфрама в сравнении с российским аналогом – сталью ЭИ347 (1 вместо 9% (по массе)), и на 1% (по массе) меньше молибдена, чем зарубежный аналог – сталь М50.
В виду того, что работоспособность подшипников определяет сопротивление усталости материалов в зоне контакта элементов качения, при разработке технологии изготовления полуфабрикатов большое внимание уделено обеспечению чистоты металла по неметаллическим включениям (особенно сульфидным и оксидным) и карбидной неоднородности: сетке карбидов, строчечным включениям, наличию угловатых карбидов. При наличии большого количества вышеперечисленных включений в процессе передела полуфабрикатов и термической обработки изделий, вследствие различия температурных коэффициентов линейного расширения (ТКЛР) металла и включений, возникают микронапряжения противоположных знаков. При деформационных нагрузках (прокатка, ковка, знакопеременные нагрузки в процессе эксплуатации) неметаллические включения выступают в качестве концентраторов напряжений, а также являются барьером, где скапливаются дислокации. Эти скопления могут стать началом трещин и последующего контактно-усталостного разрушения подшипника [9–11].
Для обеспечения чистоты металла выплавку стали проводили в вакуумно-индукционной печи с последующим вакуумно-дуговым переплавом. В результате чего достигнуто существенное уменьшение загрязненности металла неметаллическими включениями (до 1 балла по ГОСТ 1778–70).
Исследования карбидной неоднородности полуфабрикатов выбранного состава из новой подшипниковой стали проводили на продольных микрошлифах после термической обработки (закалки и высокого отпуска). Как видно из рис. 1, карбиды в прутках из новой стали диаметром 100 мм располагаются в виде узких полос с остатками сильнодеформированной разорванной сетки, что соответствует 5–6 баллу шкалы ГОСТ 5950–2000. Карбиды внутри полос раздробленные. Увеличение степени обжатия при горячей пластической деформации стали с получением прутков диаметром 55 мм снижает карбидную неоднородность стали до 2–3 балла. Карбиды располагаются в направлении прокатки в виде разорванных полос. В прутках диаметром 10 мм карбидная фаза располагается равномерно и соответствует 1 баллу. Угловатые карбиды не обнаружены ни в одном сорте. Таким образом, с увеличением диаметра проката повышается балл карбидной неоднородности, что объясняется меньшим обжатием слитка.
Рис. 1. Карбидная неоднородность (×100) прутков из новой подшипниковой стали диаметром 10 (а), 55 (б) и 100 мм (в)
В связи с этим, помимо оптимизации состава подшипниковой стали, одним из эффективных методов уменьшения карбидной неоднородности является применение для изготовления полуфабрикатов из подшипниковой стали слитков большой массы, поскольку для стали, используемой в виде полуфабрикатов крупного профиля, необходимо достичь степени деформации, достаточной для существенного улучшения условий распределения карбидов. Однако увеличение массы слитка усиливает ликвацию и центральную пористость, поэтому это целесообразно до определенных пределов [9, 12]. На основании проведенного анализа и опыта работы для получения прутков новой теплостойкой подшипниковой стали диаметром до 100 мм с минимальной карбидной неоднородностью выбрана оптимальная масса слитка 600–700 кг.
Сравнение полуфабрикатов из новой стали с полуфабрикатами того же размера из стали ЭИ347 показывает, что распределение карбидной фазы выгодно отличается по строению, количеству и характеру расположения карбидов от распределения карбидной фазы в стали ЭИ347. Так, в структуре прутков из стали ЭИ347 диаметром 100 мм наблюдается деформированная сетка эвтектических карбидов со скоплениями, разорванная в отдельных местах, что соответствует 7–8 баллу по шкале ГОСТ 5950–2000, аналогичный полуфабрикат из новой стали имеет 5–6 балл (рис. 2). Кроме того, в стали ЭИ347, вследствие присутствия в составе повышенного количества вольфрама (9% (по массе)), размер карбидных включений превосходит размер карбидов в новой стали. В микроструктуре стали ЭИ347 присутствуют крупные карбиды угловатой формы, которые снижают контактную долговечность материала. В составе разработанной стали карбиды угловатой формы отсутствуют по причине того, что часть вольфрама заменена на молибден. Молибден и вольфрам замещают друг друга в карбиде в соотношении, равном их содержанию в стали. Такие карбиды обладают значительно меньшей способностью к образованию угловатой формы. Кроме того, имеют меньшие размеры и растворяются при более низких температурах [9].
Рис. 2. Карбидная неоднородность (×100) прутков из стали ЭИ347 диаметром 100 мм
Рис. 3. Микроструктура (×500) образцов прутков диаметром 55 мм из новой подшипниковой стали после упрочняющей термической обработки
В технологию упрочнения теплостойкой стали для подшипников заложены процессы, протекающие при термической обработке быстрорежущих сталей, – это предельно возможное растворение карбидов при нагреве под закалку и перевод в твердый раствор (аустенит) углерода и карбидообразующих элементов. При последующих отпусках происходит выделение субмелкодисперсных карбидов по всему объему зерна, обеспечивающих дисперсионное твердение стали с повышением теплостойкости [9, 13, 14]. Таким образом, упрочняющая термическая обработка новой теплостойкой стали для подшипников обеспечивает в изделиях формирование равномерной мелкозернистой структуры (10 балл) мартенсита отпуска с избыточными карбидами (рис. 3), при которой достигаются высокие значения предела прочности при растяжении σв=2270–2340 МПа, твердости 61–63 HRC и теплостойкости 500°С. Содержание остаточного аустенита в микроструктуре стали составляет ≤2%, тем самым обеспечивается размерная стабильность, что особенно важно для подшипников, установленных в ответственных узлах изделия [15, 16].
Заключения
Во ФГУП «ВИАМ» разработана новая теплостойкая подшипниковая сталь, не уступающая по эксплуатационным характеристикам зарубежному аналогу марки М50 и превосходящая по карбидной однородности и технологичности при горячей пластической деформации отечественную сталь марки ЭИ347.
Применение новой теплостойкой подшипниковой стали для перспективных самолетов и вертолетов взамен стали ЭИ347 позволит повысить контактно-усталостную прочность, надежность и ресурс работы теплостойких подшипников путем повышения чистоты металла и снижения балла карбидной неоднородности. Кроме того, при производстве полуфабрикатов из стали наряду с ковкой возможно применять технологию раскатки, тем самым снизив трудоемкость производства.
ЛИТЕРАТУРА REFERENCE LIST
1. Каблов Е.Н. Инновационные разработки ФГУП «ВИАМ» ГНЦ РФ по реализации «Стратегических направлений развития материалов и технологий их переработки на период до 2030 года» // Авиационные материалы и технологии. 2015. №1 (34). С. 3–33. DOI: 10.18577/2071-9140-2015-0-1-3-33.
2. Каблов Е.Н. Из чего сделать будущее? Материалы нового поколения, технологии их создания и переработки – основа инноваций // Крылья Родины. 2016. №5. С. 8–18.
3. Каблов Е.Н. России нужны материалы нового поколения // Редкие земли. 2014. №3. С. 8–13.
4. Каблов Е.Н. Тенденции и ориентиры инновационного развития России // Сб. научно-информационных материалов. 3-е изд. М.: ВИАМ, 2015. 720 с.
5. Уткин В.М., Никонов А.Г., Прокша Ф.Н. Сравнение норм отечественных и зарубежных нормативных документов на качество шарико- и роликоподшипниковой стали. М.: Черметинформация, 1975. 56 с.
6. Зайцев А.М., Коросташевский Р.В. Эксплуатация авиационных подшипников качения. М.: Транспорт, 1968. 224 с.
7. Громов В.И., Вознесенская Н.М., Покровская Н.Г., Тонышева О.А. Высокопрочные конструкционные и коррозионностойкие стали ФГУП «ВИАМ» для изделий авиационной техники // Авиационные материалы и технологии. 2017. №S. С. 159–174. DOI: 10.18577/2071-9140-2017-0-S-159-174.
8. Спектор А.Г., Зельбет Б.М., Киселева С.А. Структура и свойства подшипниковых сталей. М.: Металлургия, 1980. 264 с.
9. Геллер Ю.А. Инструментальные стали. М.: Металлургия, 1983. 525 с.
10. Крылов С.А., Маркова Е.С., Щербаков А.И., Якушева Н.А. Металлургические особенности выплавки высокопрочной мартенситостареющей стали ВКС-180-ИД // Авиационные материалы и технологии. 2015. №4 (37). С. 14–20. DOI: 10.18577/2071-9140-2015-0-4-14-20.
11. Шпис Х.И. Поведение неметаллических включений в стали при кристаллизации и деформации. М.: Металлургия, 1971. 122 с.
12. Разуваев Е.И., Моисеев Н.В., Капитаненко Д.В., Бубнов М.В. Современные технологии обработки металлов давлением // Труды ВИАМ: электрон. науч.-технич. журн. 2015. №2. Ст. 03. URL: http://www.viam-works.ru (дата обращения: 16.11.2018). DOI: 10.18577/2307-6046-2015-0-2-3-3.
13. Коросташевский Р.В., Зайцев А.М. Авиационные подшипники качения. М.: Оборонгиз, 1963. 340 с.
14. Контер Л.Я. Стали для теплостойких подшипников (обзор). М.: НИИНАвтопром, 1978. Сер.: XII. 78 с.
15. Громов В.И., Кротов В.Н., Курпякова Н.А., Седов О.В., Дорошенко А.В. Влияние остаточного аустенита на структуру и свойства диффузионного слоя стали мартенситного класса после вакуумной цементации // Авиационные материалы и технологии. 2016. №4 (45). С. 3–8. DOI: 10.18577/2071-9140-2016-0-4-3-8.
16. Хенкин М.Л., Локшин И.Х. Размерная стабильность металлов и сплавов в точном машиностроении и приборостроении. М.: Машиностроение, 1974. 255 с.
1. Kablov E.N. Innovatsionnyye razrabotki FGUP «VIAM» GNTS RF po realizatsii «Strategicheskikh napravleniy razvitiya materialov i tekhnologiy ikh pererabotki na period do 2030 goda» // Aviatsionnyye materialy i tekhnologii. 2015. №1 (34). S. 3–33. DOI: 10.18577/2071-9140-2015-0-1-3-33.
2. Kablov E.N. Iz chego sdelat budushcheye? Materialy novogo pokoleniya, tekhnologii ikh sozdaniya i pererabotki – osnova innovatsiy [What to make the future from? Materials of the new generation, technologies of their creation and processing – the basis of innovation] // Krylya Rodiny. 2016. №5. S. 8–18.
3. Kablov E.N. Rossii nuzhny materialy novogo pokoleniya [Russia needs new generation materials] // Redkiye zemli. 2014. №3. S. 8–13.
4. Kablov E.N. Tendentsii i oriyentiry innovatsionnogo razvitiya Rossii [Trends and benchmarks of innovative development of Russia] // Sb. nauchno-informatsionnykh materialov. 3-ye izd. M.: VIAM, 2015. 720 s.
5. Utkin V.M. , Nikonov A.G., Proksha F.N. Sravneniye norm otechestvennykh i zarubezhnykh normativnykh dokumentov na kachestvo shariko- i rolikopodshipnikovoy stali [Comparison of norms of domestic and foreign regulatory documents on the quality of ball and roller bearing steel]. M.: Chermetinformatsiya, 1975. 56 s.
6. Zaytsev A.M., Korostashevskiy R.V. Ekspluatatsiya aviatsionnykh podshipnikov kacheniya [Operation of aircraft rolling bearings]. M.: Transport, 1968. 224 s.
7. Gromov V.I., Voznesenskaya N.M., Pokrovskaya N.G., Tonysheva O.A. Vysokoprochnye konstrukcionnye i korrozionnostojkie stali FGUP «VIAM» dlya izdelij aviacionnoj tehniki [High-strength constructional and corrosion-resistant steels developed by VIAM for aviation engineering] // Aviacionnye materialy i tehnologii. 2017. №S. S. 159–174. DOI: 10.18577/2071-9140-2017-0-S-159-174.
8. Spektor A.G., Zelbet B.M., Kiseleva S.A. Struktura i svoystva podshipnikovykh staley [Structure and properties of bearing steels]. M.: Metallurgiya, 1980. 264 s.
9. Geller Yu.A. Instrumentalnyye stali [Tool steel]. M.: Metallurgiya, 1983. 525 s.
10. Krylov S.A., Markova E.S., Shcherbakov A.I., Yakusheva N.A. Metallurgicheskiye osobennosti vyplavki vysokoprochnoy martensitostareyushchey stali VKS-180-ID [Metallurgical features of smelting process of high-strength maraging steel VKS180-ID microalloyed by REM] // Aviacionnye materialy i tehnologii. 2015. №4 (37). S. 14–20. DOI: 10.18577/2071-9140-2015-0-4-14-20.
11. Shpis Kh.I. Povedeniye nemetallicheskikh vklyucheniy v stali pri kristallizatsii i deformatsii [Behavior of non-metallic inclusions in steel during crystallization and deformation]. M.: Metallurgiya, 1971. 122 s.
12. Razuvaev E.I., Moiseev N.V., Kapitanenko D.V., Bubnov M.V. Sovremennye tehnologii obrabotki metallov davleniem [Modern technologies of plastic working of metals] // Trudy VIAM: elektron. nauch.-tehnich. zhurn. 2015. №2. St. 03. Available at: http://www. viam-works.ru (accessed: November 16, 2018). DOI: 10.18577/2307-6046-2015-0-2-3-3.
13. Korostashevskiy R.V., Zaytsev A.M. Aviatsionnyye podshipniki kacheniya [Aviation rolling bearings]. M.: Oborongiz, 1963. 340 s.
14. Konter L.Ya. Stali dlya teplostoykikh podshipnikov (obzor) [Steel for heat-resistant bearings (review)]. M.: NIINAvtoprom, 1978. Ser.: XII. 78 s.
15. Gromov V.I., Krotov V.N., Kurpyakova N.A., Sedov O.V., Doroshenko A.V. Vliyanie ostatochnogo austenita na strukturu i svojstva diffuzionnogo sloya stali martensitnogo klassa posle vakuumnoj cementacii [Influence of residual austenite on the structure and properties of diffusion layer of martensitic grade steel after vacuum carburization] // Aviacionnye materialy i tehnologii 2016. №4 (45) S. 3–8. DOI: 10.18577/2071-9140-2016-0-4-3-8.
16. Khenkin M.L., Lokshin I.Kh. Razmernaya stabilnost metallov i splavov v tochnom mashinostroyenii i priborostroyenii [Dimensional stability of metals and alloys in precision engineering and instrument making]. M.: Mashinostroyeniye, 1974. 255 s.
подшипники – ispatguru
подшипники
- Satyendra
- 6 августа, 2020
- 0 Комментарии
- Bainitic Structure, шариковая подшипник, подшипник, опорная сталь, чистота, устаревшая, уточнение сталь, мартенситная структура, неметаллические включения, подшипник качения, упорный подшипник,
Подшипниковая сталь
Оксфордский словарь английского языка определяет подшипник как часть машины, которая позволяет одной части вращаться или двигаться в контакте с другой часть с наименьшим трением». Дополнительные функции включают передачу нагрузки и обеспечение точного определения местоположения компонентов. Подшипник должен выдерживать серьезные статические, а также циклические нагрузки, надежно работая в сложных условиях. Стали хорошо подходят в этом контексте, и во многих их формах представляют собой предпочтительный материал для производства подшипников. Подшипники состоят из тел качения (шарики, цилиндры или бочонки) и колец. Кольца образуют дорожки качения.
Подшипники представляют собой высокотехнологичные, прецизионные элементы машин, которые обеспечивают относительное перемещение компонентов машины с минимальным трением. Они легко и эффективно переносят высокие нагрузки и способны обеспечить высокую точность, надежность и долговечность. Существует несколько типов подшипников, каждый из которых используется для разных целей. К ним относятся шариковые подшипники, роликовые подшипники, упорные шариковые подшипники, упорные роликовые подшипники и конические упорные роликовые подшипники. Поскольку для различных применений требуются подшипники с различными характеристиками, различия между типами подшипников касаются типа нагрузки и способности выдерживать вес. Шариковые подшипники чрезвычайно распространены, поскольку они могут выдерживать как радиальные, так и осевые нагрузки, но могут выдерживать лишь небольшой вес. Роликовые подшипники используют цилиндры вместо шариков и имеют большую несущую способность из-за большего контакта между телами качения и кольцами.
Процесс производства тел качения включает пластическую деформацию с высокой скоростью обжатия исходного литого материала в заготовки квадратного сечения. Деформация способствует разрушению литой структуры и закрытию пористости. Затем заготовки уменьшают в сечении путем дальнейшей прокатки или волочения, термообрабатывают до размягченного состояния и разрезают на отрезки, пригодные для изготовления шаров. Готовые тела качения затем подвергают закалке и отпуску или изотермическому преобразованию до требуемой твердости. Кольца подшипников могут быть изготовлены из бесшовной трубы, полученной методом горячей прокатки и аналогично закаленной с последующей тщательной механической обработкой и шлифовкой до окончательных размеров и чистоты поверхности. Подавляющее большинство тел качения и дорожек качения изготовлено из стали.
Неправильная установка, коррозия, недостаточная смазка и т. д. могут привести к преждевременному выходу подшипников из строя. Однако даже хорошо обслуживаемые подшипники могут со временем выйти из строя из-за усталости контактирующих поверхностей. Широко распространенный вид разрушения состоит из зарождения подповерхностной трещины на ранее существовавшем дефекте в области наибольшего напряжения сдвига под контактной зоной с последующим распространением трещины с образованием в конечном итоге ямки на поверхности. Следовательно, материал, который будет использоваться для производства подшипников, имеет большое значение.
Поскольку подшипник должен выдерживать серьезные статические и циклические нагрузки, надежно работая в сложных условиях, для этой цели хорошо подходят стали. Есть две категории сталей, которые находят применение в большинстве подшипников. Первая категория состоит из тех сталей, которые закалены по всему сечению до мартенситного или бейнитного состояния, а другая категория состоит из тех сталей, которые имеют мягкую сердцевину, но прочные поверхностные слои, нанесенные с использованием таких процессов, как поверхностная или индукционная закалка.
Подшипниковые стали также можно разделить в широком смысле на классы, например, предназначенные для нормальной эксплуатации, эксплуатации при высоких температурах или эксплуатации в коррозионных условиях. Подшипники для нормальных условий эксплуатации, категория, которая включает в себя большинство всех подшипников качения, применимы, когда (i) максимальные температуры составляют порядка 120–150 °C, хотя допустимы кратковременные отклонения до 175 °C. , (ii) минимальная температура окружающей среды составляет около -50 градусов C, (iii) контактные поверхности смазываются такими материалами, как масло, жир или аэрозоль, и (iv) максимальные контактные напряжения по Герцу составляют порядка 2,1 ГПа до 3,1 ГПа. Подшипники, используемые в нормальных условиях эксплуатации, также испытывают воздействие вибрации, ударов, перекосов, мусора и манипуляций. Следовательно, материал изготовления должен обеспечивать ударную вязкость, определенную степень сопротивления отпуску и микроструктурную стабильность при экстремальных температурах. Материал также должен демонстрировать очевидное требование твердости поверхности для сопротивления износу и усталости.
Стали с концентрацией углерода в диапазоне от 0,8 % до 1,1 % и общим содержанием растворенных веществ замещения менее 3 %, изначально предназначенные для станков, исторически доминировали в стали для подшипников. Их можно сделать мартенситными путем закалки в масле или соли при температуре, при которой материал в основном представляет собой аустенит. Затем мартенсит подвергают низкотемпературному отпуску, чтобы сбалансировать противоречивые свойства.
Небольшие подшипники обычно проходят сквозную закалку, т. е. стали обладают достаточной прокаливаемостью, чтобы стать мартенситными по всему сечению подшипника. Это не так с большими подшипниками, где поверхностный слой должен быть науглерожен для получения мартенситного корпуса. В качестве альтернативы большие подшипники могут быть подвергнуты сквозной закалке за счет повышения прокаливаемости стали с использованием более высоких концентраций легирующих элементов.
Традиционно подшипники изготавливаются как из высокоуглеродистой (1 %), так и из низкоуглеродистой (0,2 %) стали. Высокоуглеродистые стали используются либо в состоянии сквозной закалки, либо в состоянии поверхностной индукционной закалки в специальных интегральных конфигурациях подшипников, таких как шпиндель автомобильного колеса. Низкоуглеродистые подшипниковые стали науглероживаются для обеспечения необходимой поверхностной твердости при сохранении других желаемых свойств сердцевины. Параллельная разработка как высокоуглеродистых, так и низкоуглеродистых сталей для подшипников уходит корнями в историю. Первые европейские производители решили использовать знакомые инструментальные стали хромового типа. Американские производители подшипников, с другой стороны, добавили науглероженный корпус к своим подшипникам скольжения из мягкой стали, чтобы соответствовать более высоким требованиям к твердости, предъявляемым к более высоконагруженным подшипникам качения.
Материалы как из высокоуглеродистой, так и из низкоуглеродистой стали выжили, поскольку каждый из них предлагает уникальное сочетание свойств, которое лучше всего подходит для предполагаемых условий эксплуатации. Например, высокоуглеродистые стали (i) могут выдерживать несколько более высокие контактные напряжения, например, возникающие при точечной контактной нагрузке в шарикоподшипниках, (ii) могут подвергаться закалке и отпуску, что является более простой термической обработкой, чем науглероживание, и (iii) могут обеспечивать большую стабильность размеров при экстремальных температурах из-за характерного для них более низкого содержания остаточного аустенита. Науглероженные стали, с другой стороны, обладают (i) большей пластичностью поверхности (из-за содержания в них остаточного аустенита), чтобы лучше сопротивляться эффектам повышения напряжения, вызванным неровностями, смещением и частицами мусора, (ii) более высоким уровнем ударной вязкости сердцевины для сопротивляться разрушению сквозного сечения в тяжелых условиях эксплуатации, (iii) сжимающее остаточное поверхностное напряжение для сопротивления изгибающим нагрузкам, воздействующим на ребра роликоподшипников, и снижать скорость распространения усталостной трещины по поперечному сечению, и (iv) более легкая механическая обработка основной материал в производстве.
В подшипниках качения важно поддерживать достаточную прочность во всей области максимальных внутренних напряжений сдвига. На рис. 1 показано расчетное соотношение между твердостью и пределом текучести при сдвиге, применимое к любому типу стали. Успех данной стали в подшипниках зависит не столько от типа стали, сколько от того, как она обрабатывается. Сопротивление усталости обычно увеличивается с увеличением твердости, и максимальное значение зависит от типа стали. На рис. 1 также сравнивается усталостная долговечность при изгибе углеродистых и науглероженных сталей в зависимости от поверхностной твердости. При усталости при изгибе сочетание сжимающих остаточных поверхностных напряжений с более высокой ударной вязкостью составного сечения дает преимущество науглероженной стали.
Рис. 1 Свойства подшипниковых сталей
Характеристики микроструктуры
Высокоуглеродистые подшипниковые стали – В 1950-х гг. высокие температуры. Было высказано предположение, что это также приводит к более высокой твердости при температуре окружающей среды, а также к увеличению срока службы подшипника. Исходя из этого предположения, сталелитейщики стали разрабатывать подшипниковые стали с повышенным содержанием легирующих элементов. Необходимо сравнить эти параметры стали и обработки при испытаниях на усталость тел качения и/или реальных испытаниях подшипников. Стандартные механические испытания, такие как испытания на растяжение и сжатие или испытания на вращающуюся балку, не могут быть соотнесены с результатами усталостной деформации тел качения.
На рис. 2 показана типичная микроструктура закаленной и отпущенной высокоуглеродистой подшипниковой стали, такой как AISI 52100. Матрица представляет собой высокоуглеродистый мартенсит, содержащий первичные карбиды и от 5 % до 10 % остаточного аустенита. Твердость по всему сечению обычно составляет от 60 до 64 HRC. В Таблице 1 приведены составы некоторых высокоуглеродистых подшипниковых сталей. Первые три сорта даны в порядке возрастания прокаливаемости. Их наносят на участки подшипников увеличивающейся толщины, чтобы обеспечить отсутствие немартенситных превращений при закалке. Марка ТБС-9представляет собой подшипниковую сталь с низким содержанием хрома, которая из-за содержания в ней остаточного сплава имеет прокаливаемость, аналогичную AISI 52100. Марка SUJ 1 — это японская марка стали, а марка 105Cr6 — немецкая марка стали, используемая для компонентов подшипников.
Таблица 1 Номинальные составы некоторых подшипниковых сталей | |||||||
Сл. № | Марка | Номинальный состав, % | |||||
Carbon | Manganese | Silicon | Chromium | Nickel | Molybdenum | ||
High carbon bearing steels | |||||||
1 | AISI 52100 АСТМ А 485-10070 | 1.10 | 0.60 | 1.05 | |||
3 | ASTM A 485-3 | 1.02 | 0.78 | 0.22 | 1.30 | 0.25 | |
4 | TBS-9 | 0.95 | 0.![]() | 0.22 | 0.50 | 0.25 maximum | 0.12 |
5 | SUJ 1 | 1.02 | Less than 0.50 | 0.25 | 1.05 | Less than 0.25 | Less than 0.08 |
6 | 105Cr6 | 0.97 | 0.32 | 0.25 | 1,52 | ||
Carburizing bearing steels | |||||||
1 | 4118 | 0.20 | 0.80 | 0.22 | 0.50 | 0.11 | |
2 | 5120 | 0.20 | 0.80 | 0.22 | 0.80 | ||
3 | 8620 | 0.20 | 0.80 | 0.22 | 0.50 | 0.55 | 0.20 |
4 | 4620 | 0.20 | 0.55 | 0.22 | 1.82 | 0.![]() | |
5 | 4320 | 0.20 | 0.55 | 0.22 | 0.50 | 1.82 | 0.25 |
6 | 3310 | 0.1 | 0.52 | 0.22 | 1.57 | 3.50 | |
7 | SCM420 | 0.20 | 0.72 | 0.25 | 1.05 | 0.22 | |
8 | 20MnCr5 | 0.17-0.22 | 1.1-1.4 | 0.4 maximum | 1.0-1.3 |
Fig 2 Microstructure of high carbon and carburizing bearing steels
Науглероженные подшипниковые стали – Науглероживаемые подшипниковые стали имеют пониженное содержание углерода, поэтому термическая обработка обычно приводит к умеренной твердости и высокой ударной вязкости. Высокая твердость поверхности, необходимая для работы подшипников качения, достигается путем диффузии углерода в поверхность, процесс, называемый науглероживанием, перед термической обработкой. Местами сталь представляет собой сплав с высоким содержанием углерода и подвергается термообработке до полной твердости. Полученная структура имеет поверхностный слой с механическими свойствами, эквивалентными свойствам традиционных подшипниковых сталей со сквозной закалкой, и сердцевину, остающуюся низкой твердости, с соответствующей высокой пластичностью и высокой вязкостью разрушения. Поверхностные дефекты (например, выкрашивание) приводят к распространению трещин в прочном сердцевине до того, как они достигнут критического размера. Прочный сердечник предотвращает быстрое и катастрофическое разрушение.
На рис. 2 показаны типичные микроструктуры корпуса и сердцевины науглероженных компонентов подшипника. Микроструктура корпуса состоит из высокоуглеродистого мартенсита с содержанием остаточного аустенита в диапазоне от 15 % до 40 %. Твердость корпуса обычно составляет от 58 HRC до 64 HRC. В сердцевине науглероженных подшипников микроструктура состоит из низкоуглеродистого мартенсита. Он также часто содержит различные количества бейнита и феррита. Твердость сердцевины может варьироваться от 25 HRC до 48 HRC.
В Таблице 1 приведены составы типичных науглероженных подшипниковых сталей. Марки AISI показаны в приблизительном порядке увеличения прокаливаемости или применимости размера сечения. SCM420 и 20MnCr5 — это марки японского и немецкого сплавов соответственно, используемые в науглероженных компонентах подшипников. В дополнение к стандартным маркам стали AISI, подшипниковые стали также могут быть разработаны таким образом, чтобы их прокаливаемость соответствовала требованиям к определенной толщине профиля. Сохранение сплава и более стабильная реакция на термообработку являются преимуществами использования специально разработанных подшипниковых сталей.
Выбор науглероживающей стали для конкретной секции подшипника основывается на методах термической обработки производителя, будь то прямая закалка после науглероживания или повторный нагрев для закалки, а также на характеристиках закалочного оборудования. Важность надлежащей микроструктуры корпуса для способности подшипника сопротивляться питтинговой усталости показана на рис. 3. В частности, наличие перлита в результате несоответствия условий закалки и прокаливаемости корпуса оказывает пагубное влияние.
Рис. 3 Влияние микроструктуры поверхности на поверхностную усталость
Самая популярная подшипниковая сталь содержит около 1 % углерода и 1,5 % хрома. Испытания шарикоподшипников, проведенные Штрибеком в 1901 году на такой стали, показали ее пригодность для применения и, по-видимому, были приняты около 120 лет назад для подшипников компанией Fichtel & Sachs из Швайнфурта в 1905 году и по сей день остаются ключевой сталью в производстве. подшипников с прогрессивным улучшением усталостных характеристик, достигаемым в основном за счет улучшения чистоты по отношению к неметаллическим включениям. Он представляет собой большую часть подшипниковой стали, производимой ежегодно.
Эта подшипниковая сталь соответствует нескольким национальным и международным стандартам. Обычно сталь поставляется в горячекатаном состоянии с перлитной микроструктурой, включающей некоторое количество доэвтектоидного цементита на границах предшествующих аустенитных зерен (рис. 4а). Проэвтектоидный цементит, когда он образует сети на границах аустенитных зерен, является нежелательным, поскольку было показано, что он неблагоприятно влияет на усталостную долговечность контактов качения в ускоренных испытаниях, проведенных с контактными напряжениями, превышающими 5 ГПа. Сетки можно свести к минимуму путем достаточно быстрого охлаждения от конечной температуры горячей деформации или путем отжига для сфероидизации цементита (рис. 4b). Относительно большая концентрация углерода в этой стали ускоряет процесс сфероидизации и является одной из причин успеха этой стали, поскольку она относительно легко поддается мягкому отжигу. После соответствующей механической обработки или формовки компоненты подшипников, изготовленные из стали, подвергаются закалке.
Рис. 4 Микроструктура подшипниковых сталей с 1 % углерода и 1,5 % хрома
Качество подшипниковой стали
единственным наиболее важным фактором в достижении высокого уровня усталостной долговечности подшипников при контакте качения является чистота или отсутствие вредных неметаллических включений в стали. Подшипниковые стали могут быть произведены одним из этих методов, а именно (i) плавка чистой стали в воздухе, (ii) электрошлаковый переплав, (iii) плавка на воздухе с последующим вакуумным переплавом и (iv) вакуумная индукционная плавка с последующей вакуумной дугой. переплавка. Чистота, стоимость и надежность могут увеличиться в зависимости от того, какая практика выбрана.
Чистота подшипниковой стали чаще всего оценивается с помощью микроскопических методов, таких как методы, определенные в ASTM A 295 для высокоуглеродистых сталей и ASTM A 534 для науглероженных сталей. Наихудшие поля, обнаруженные в металлографически подготовленных срезах стали, можно сравнить с рейтинговыми диаграммами (диаграммами J-K) в зависимости от типа включений, таких как сульфиды, оксиды стрингерного типа, силикаты и оксиды глобулярного типа. В Таблице 2 приведены существующие уровни каждого из типов включений, разрешенных для сталей для подшипников, выплавляемых на воздухе. Некоторые производители выпускают подшипники со значительно более низким уровнем содержания неметаллических включений, чем разрешено рейтинговыми таблицами.
Таб.2 Показатели неметаллических включений | |||
Сл. No. | Rating | ASTM A 534-76 (carburizing steel) | |
Thin | Heavy | ||
1 | Type A | 3.0 | 2.0 |
2 | Тип B | 3,0 | 2,5 |
3 | Type C | 2.5 | 1.5 |
4 | Type D | 2.0 | 1.5 |
Bearing steel cleanliness can also be rated by oxygen analysis, the magnetic particle method, and ultra -звуковые методы. Из них ультразвуковой метод показывает лучшую корреляцию с усталостной долговечностью подшипника, когда содержание кислорода в стали составляет менее 20 частей на миллион. Это связано с большим объемом материала, отбираемого методом.
Влияние термической обработки
Важное значение имеет соответствие прокаливаемости и закалки подшипниковой стали. Однако в пределах этого ограничения было обнаружено, что другие параметры термообработки влияют на характеристики подшипников, особенно в неидеальных условиях загрязнения твердыми частицами. Известно, что остаточный аустенит в микроструктуре снижает поверхностную твердость высокоуглеродистых сталей. Пластичность поверхности, выраженная отношением предела текучести к прочности на излом, улучшается за счет увеличения количества остаточного аустенита. Эта улучшенная пластичность часто приводит к улучшению характеристик контактной усталости при качении. Уровень остаточного аустенита может быть повышен за счет добавления азота в кожух или за счет увеличения количества циклов науглероживания. Улучшение характеристик было продемонстрировано для высокоуглеродистых сталей, когда науглероживание увеличило содержание углерода в растворе и содержание аустенита. На рис. 5 показаны улучшенные характеристики стержней из науглероженной стали AISI 52100 по сравнению с ненауглероженными стержнями из того же материала. Было показано, что другие средства повышения пластичности поверхности, такие как оптимизация температуры аустенитизации (рис. 5), регулирование скорости закалки (рис. 5) и аустенитный отпуск для получения полностью бейнитной микроструктуры, улучшают усталостные характеристики высокоуглеродистых подшипниковых сталей. для определенных приложений.
Рис. 5 Влияние термообработки на свойства подшипниковой стали 52100
Подшипниковые стали специального назначения
обеспечивают удовлетворительную усталостную долговечность. Низкая коррозионная стойкость этих сталей делает их восприимчивыми к воздействию влаги окружающей среды, а также агрессивных газообразных или жидких загрязнений. Следовательно, при наличии таких условий эксплуатации часто применяются специальные стали.
Некоторые подшипниковые стали подходят для работы при высоких температурах. Эти стали обычно легируют стабилизирующими карбиды элементами, такими как хром, молибден, ванадий и кремний, для улучшения их жаропрочности и сопротивления отпуску. Максимальные рабочие температуры (примерно от 230°C до 300°C) — это температуры, при которых твердость при температуре падает ниже минимума 58 HRC.
Важным применением жаропрочных подшипниковых сталей являются авиационные и стационарные газотурбинные двигатели. Подшипники из стали М50 уже много лет используются в двигателях. Скорости реактивных двигателей постоянно увеличиваются для повышения производительности и эффективности, и, следовательно, подшипниковая сталь, используемая в этих двигателях, должна иметь повышенную ударную вязкость сечения, чтобы выдерживать напряжения, возникающие в результате более высоких центробежных сил. По этой причине большое внимание уделяется науглероживанию жаропрочных подшипниковых сталей, таких как М50-НиЛ и ЦБС-1000М. Прочность сердцевины этих сталей более чем в два раза выше, чем у сталей со сквозной закалкой.
Науглероженные кольца имеют градиент остаточного напряжения при сжатии, в то время как остаточные напряжения при растяжении обнаруживаются в кольцах со сквозной закалкой. Наличие сжимающих остаточных напряжений может способствовать замедлению распространения радиальных усталостных трещин в поперечном сечении дорожек.
Образцы размером по Шарпи были науглерожены, закалены, отпущены и предварительно растрескались на несколько глубин в области кожуха и сердцевины перед испытанием. По мере продвижения трещин внутрь сопротивление разрушению науглероженных композитов значительно улучшается.
В целом, высокотемпературные науглероживаемые стали требуют большей осторожности в процессе науглероживания, чем обычные низколегированные стали науглероживания. Из-за высокого содержания хрома и кремния в жаропрочных сталях всегда необходима некоторая предварительная науглероживание, такая как предварительное окисление, для обеспечения удовлетворительного науглероживания.
Подшипники, которым требуется наивысшая коррозионная стойкость, требуют использования нержавеющих марок с содержанием хрома более 12 %. В настоящее время не существует удовлетворительной технологии науглероживания для этих марок. Таким образом, все коррозионностойкие подшипниковые стали относятся к типу сквозной закалки.
Технические характеристики подшипниковых сталей SMB
(a) Химический состав подшипниковой стали
| Спецификация | С % | Si % | Мн % | П % | С % | Кр % | Мо % | Ni | Твердость |
---|---|---|---|---|---|---|---|---|---|---|
Хром | САЕ52100 100Cr6 SUJ2 | 0,95 ~ 1,10 | 0,15- | 0,50 | 0,025 | 0,025 | 1,30 |
|
| 64 HRc |
Нержавеющая сталь Сталь | АИСИ440К СУС440К X105CrMo17 | 0,95 ~ 1,20 | 1,00 | 1,00 | 0,04 | 0,03 | 16,0 ~18,0 | 0,75 макс. |
| 58 HRc |
КС440 ACD34 С65Cr13 | 0,60 ~ 0,75 | 1,00 | 1,00 | 0,03 | 0,02 | 11,5 | 0,3 макс. |
| 60 HRc | |
AISI420 СУС420 X20Cr13 | 0,26 ~ 0,35 | 1,00 | 1,50 | 0,04 | 0,03 | 12,0 |
|
| 55 HRc | |
AISI304 СУС304 X5CrNi1810 | 0,08 | 0,75 | 2,00 | 0,045 | 0,03 | 18,0 |
| 8,0 | 39 HRc | |
AISI316 SUS316 X5CrNiMo17- | 0,08 | 1,00 | 2,00 | 0,045 | 0,03 | 16,0 | 2,0 | 10,0 | 39 HRc |
(b) Марки стали для подшипников EZO Japan
Компонент | Подшипники из хромистой стали | Подшипники из нержавеющей стали |
---|---|---|
Внутреннее и наружное кольца | САЭ52100/СУДЖ2/100Кр6 | КС440/АКД34/С65Кр13 |
Шарики | САЭ52100/СУДЖ2/100Кр6 | АИСИ440К/СУС440К/С105КрМо17 |
Щит | Стальная полоса SPCC | АИСИ304/СУС304/С5КрНи1810 |
Клетка | Стальная полоса SPCC | AISI304/SUS304/X5CrNi1810 или АИСИ420/СУС420/С20Кр13 |
Это все о стали: важность чистоты стали для подшипников для долгосрочных применений
Автор
Ciprian Radu
RKB BERONGING INDUSTRIONS19191

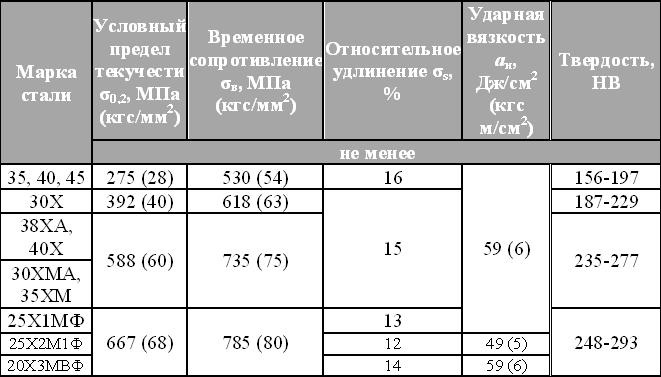
Ключевые слова: Подшипниковая сталь, чистота, усталостная долговечность, термическая обработка, металлография, неметаллические включения
1. Введение надежность большинства промышленного оборудования. В этом отношении выбор правильного материала подшипника и его обработка имеют первостепенное значение.
На протяжении многих лет особые требования к подшипникам качения, т. е. усталостная прочность в контакте качения, сопротивление контактной деформации и износу, ударная вязкость, обрабатываемость и прокаливаемость, предъявлялись к специальной стали, широко известной как подшипниковая сталь [1].
Существует два основных варианта подшипниковых сталей качения [2]:
– стали со сквозной закалкой (табл. 1), у которых после окончательной термической обработки твердость достигает высокого значения 58-64 HRC по всей объем, если компоненты подшипника;
– цементируемые стали (таблица 2), у которых обработка науглероживанием увеличивает содержание углерода до 0,65-1,10 % только в поверхностном слое толщиной 0,7-3,5 мм, где соответствующая закалка и отпуск обеспечивают необходимое высокая твердость 58-64 HRC, в то время как остальная часть материала имеет гораздо более низкую твердость 0f 32-48 HRC, что обеспечивает лучшую эксплуатационную вязкость.
Подходящий выбор стали для изготовления подшипников качения основывается на конкретном промышленном применении подшипника, геометрии, размере, технологии производства и связанных с этим затратах [1].
Одним из основных факторов, определяющих усталостную долговечность подшипников качения, является однородность и чистота стали. Данную сталь можно считать чистой, если содержание в ней примесей, таких как фосфор, сера, кремний и алюминий, очень низкое. Эти примеси в сочетании с кислородом образуют неметаллические включения [4].
Если бы две группы одинаковых подшипников качения были изготовлены из материалов одного типа, но из разных партий, что означает возможное разное содержание неметаллических включений, то можно было бы ожидать значительной разницы в распределении фактической усталостной долговечности [5]. ]. Существующие неметаллические включения действуют как концентраторы напряжения, способные инициировать микротрещины во время повторяющихся контактных напряжений, создаваемых нагрузкой качения в поверхностном слое дорожек качения. В конечном итоге эти микротрещины могут пробить поверхность дорожки качения, и со временем может произойти выкрашивание, что приведет к полному выходу подшипника из строя (рис. 1) [6].
Для получения соответствующего класса чистоты необходимо контролировать и улучшать широкий спектр рабочих процессов в процессе производства стали, таких как раскисление и добавки, вторичная металлургическая обработка и литье [3].
2. Выбор подшипниковой стали RKB для длительного срока службы
Как уже отмечалось, чистота стали играет решающую роль в разработке высококачественных подшипников с превосходными эксплуатационными характеристиками.
В связи с тем, что для обеспечения требуемой твердости, высокой устойчивости к контактной деформации и износу, а также хорошей размерной стабильности, подшипники RKB в основном изготавливаются из высокоуглеродистой хромистой стали SAE 52100 со сквозной закалкой, как показано в таблице 1. Чтобы гарантировать Премиальное качество своей продукции Группа RKB регулярно и тщательно проверяет химический состав стали, особенно верхние пределы содержания кислорода (таблица 3).
Для подшипников с большими размерами поперечного сечения используется сталь SAE 52100/A для улучшения прокаливаемости, имеющая более высокое содержание марганца, кремния и хрома. Сталь SAE 52100/A аналогична сталям 100CrMnSi6-4 или GCr15SiMn [7] и имеет уменьшенное количество удлиненных сульфидов.
Для специального промышленного применения группа RKB может использовать цементируемую сталь SAE 9315, которая представляет собой никель-хром-молибденовую сталь (таблица 2) [7].
Цементируемые стали RKB, цементированные на необходимую глубину и поверхностную твердость 58-64 HRC, имеют более мягкую (32-48 HRC) энергопоглощающую сердцевину, которая при ударных нагрузках обеспечивает лучшие характеристики, чем дается сквозной закалкой подшипниковых сталей [2].
Стали RKB со сквозной и цементируемой закалкой производятся в прутках с помощью ряда процессов:
- электропечная плавка
- печное рафинирование и дегазация
- непрерывное литье
- нагрев и рафинирование
- горячая прокатка/ковка и отжиг.
Для выявления дефектов материала до начала производственного процесса стальные прутки выборочно подвергаются неразрушающему контролю, наиболее часто используется ультразвуковой метод.
Последним достижением RKB Group и ее поставщика стали в этой области является новая улучшенная версия стали со сквозной закалкой под названием RKB Type. Протокол RAV, химический состав которого аналогичен стали SAE A485. Этот инновационный протокол особенно подходит для производства подшипников качения класса RKB Victory Line.
Для соблюдения ограничений, налагаемых последними международными стандартами в отношении неметаллических включений, т.е. чистоты, сталь RKB Type.RAV подвергается строгому процессу очистки, называемому электрошлаковым переплавом с вакуумной дегазацией или VAC-ESR (рис. 2). .
Процесс VAC-ESR дает значительные преимущества с точки зрения макро- и микроструктуры стали, что приводит как к повышению надежности продукции, так и к снижению потребности в техническом обслуживании. Эти преимущества связаны с [1]:
- глубокое обессеривание,
- рафинирование и равномерное распределение неметаллических включений,
- мелкозернистая структура,
- отсутствие усадочных дефектов и макросегрегации.
Как показано на рис. 3, преимущества, предлагаемые сталью RKB Type.RAV для наших подшипников, очевидны с точки зрения термической обработки, процессов тонкой шлифовки и проверки, износостойкости и коррозионной стойкости, простого процесса монтажа, базового номинального срока службы и срока службы. затраты цикла (рис. 3).
2.1 Преимущества термической обработки
Имея правильный химический состав и мелкозернистую структуру, сталь RKB Type.RAV использует специальную термическую обработку для достижения надлежащей твердости 58-64 HRC, равномерной по всей площади сечения. компоненты подшипника.
2.2 Преимущества тонкого шлифования
Более высокое содержание неметаллических включений в стандартной стали SAE 52100 проявляется в первую очередь как недостаток в процессе тонкого шлифования, когда более мягкая стальная матрица, окружающая твердые хрупкие неметаллические включения, частично удаляется . При удалении включений с поверхности стали образуются пустоты или ямки (рис. 4). Кроме того, при эксплуатации подшипника эти пустоты могут реагировать как инициаторы микротрещин, что в конечном итоге может привести к полному выходу подшипника из строя. Наоборот, сталь РКБ Тип.РАВ, благодаря своей высокой степени чистоты, значительно снижает вероятность образования таких полостей.
2.3 Преимущества износостойкости
Специфическая структура RKB Type.RAV способствует распространению любого повреждения подшипника в четыре раза медленнее, чем в подшипниках из стандартной стали.
Наши подшипники из стали RKB Type.RAV менее восприимчивы к загрязнениям, а это означает, что вмятины, вызванные посторонними твердыми частицами, не вызовут преждевременных усталостных повреждений.
Высокая коррозионная стойкость стали марки РКБ Тип.РАВ подтверждена испытанием погружением в раствор хлористого натрия (рис. 5). Как легко заметить, на поверхности стандартной подшипниковой стали SAE 52100 наблюдается повышенная ржавчина по сравнению с образцом из стали RKB Type. RAV. Фактически стандартная подшипниковая сталь содержит крупные эвтектические карбиды, которые действуют как инициаторы трещин и снижают содержание хрома в мартенситной матрице (рис. 6а).
Сталь RKB Type.RAV, наоборот, не имеет эвтектических карбидов, а состоит из мелкодисперсных карбидов и прочного мартенсита, повышающих коррозионную стойкость (рис. 6b).
2.4 Преимущества процесса монтажа
Как известно, неправильный процесс монтажа может повредить подшипник качения (рис. 7) [8]. Благодаря более стабильной структуре стали РКБ Тип.РАВ возможный перегрев, возникающий при неправильном монтаже, не влияет на задействованные несущие элементы.
Сталь RKB Type.RAV имеет более мелкое зерно, что повышает прочность материала и его способность выдерживать большие нагрузки и удары. Кроме того, более высокая прочность специальной подшипниковой стали RKB защищает компоненты подшипника от повреждения прямыми ударами, которые могут возникнуть при неправильном монтаже.
2.5 Преимущества номинального срока службы
Для проверки качества подшипниковой стали, используемой RKB, по сравнению со сталями, поставляемыми другими производителями, было проведено испытание на контактную усталостную долговечность. Были выбраны пять ведущих поставщиков стали, и одному из них мы обязали соблюдать протокол подшипниковой стали серии RKB JX80X для обеспечения высочайшей надежности в критических условиях. Образцы материалов для испытаний были отожжены и изготовлены в виде шайб, закалены в электропечи с газовой защитой при температуре от 835 до 845 °C и, наконец, отпущены при температуре от 150 до 160 °C в течение 3 часов.
Оценка проводилась на приборе Test Life Prediction с максимальным контактным напряжением 4508 МПа и 2040 об/мин. Каждая из пяти испытательных групп содержала 16 испытуемых образцов. Для каждой группы испытания проводились до усталостного разрушения всех образцов группы.
Подшипниковая сталь премиум-класса RKB Type. RAV в соответствии с нашими высокими стандартами качества показала превосходство над другими материалами.
Статистические значения, приведенные в таблице 4 и изображенные на рисунке 8, указывают на то, что испытательные образцы, изготовленные из нашей стали, имеют самые высокие значения как номинального, так и среднего срока службы.
2.6 Преимущества затрат на срок службы
В компании RKB, используя нашу специальную подшипниковую сталь Type.RAV, мы преследуем цель разработки индивидуальных решений проблем для клиентов в самых разных областях применения, особенно там, где ранее использовавшаяся прокатная сталь Материалы подшипников достигли своего предела, стандартные подшипники необходимо заменять довольно часто, а время простоя всей системы, включая систему затрат, должно быть сокращено. Если сравнить инвестиции и капитальные затраты на подшипники RKB и стандартные подшипники, наши затраты немного выше (рис. 9).). Однако эти затраты довольно быстро окупаются за счет затрат на эксплуатацию и техническое обслуживание. Поэтому, благодаря надежности наших подшипников, обеспечиваемой чистотой и качеством изготовления нашей стали, наши клиенты получают экономическую прибыль.
Как известно, термообработка подшипников качения чередует операции нагрева и охлаждения в контролируемых атмосферных условиях для придания материалам желаемых характеристик, таких как твердость, высокая прочность на растяжение, улучшенная обрабатываемость. , правильный размер зерна и сниженное остаточное напряжение. Термические циклы, обеспечивающие эти специфические свойства материала, включают фазы отжига, науглероживания (только для цементируемых сталей), закалки, отпуска и снятия напряжений (дополнительный отпуск) [1; 2].
Помимо этих обычных обработок, RKB может выполнить две дополнительные термообработки:
- Бейнитная обработка (HB) и
- Обработка для стабилизации размеров (S1, S2, S3, S4).
Блок-схема упомянутых термообработок представлена на рисунке 10.
Бейнитная обработка RKB может применяться к кольцам подшипников, изготовленным из стали SAE 52100, если их толщина не превышает 17 мм. RKB может применить обработку HB к внутреннему кольцу (RKB HB3), наружному кольцу (RKB HB 2) или к обоим кольцам (RKB HB1).
Термическая обработка RKB HB3 или RKB HB2 выполняется, когда техническое применение требует процесса монтажа с посадкой с большим натягом между внутренним/наружным кольцом и валом/корпусом. Эти термообработки значительно снижают внутренние напряжения, создаваемые предыдущими термическими циклами, которые в сочетании с чрезмерной посадкой с натягом могут привести к растрескиванию внутреннего/наружного кольца.
Термическая обработка RKB HB1 выбирается, когда для технического применения требуется одновременная посадка с высоким натягом между внутренним кольцом и валом и наружным кольцом и корпусом. За счет снижения уровня напряжения частота растрескивания снижается в обоих кольцах и достигается более длительный срок службы.
Кроме того, если толщина колец не превышает 17 мм, на оба кольца подшипников, изготовленных из стали SAE 52100, можно также нанести обработку для стабилизации размеров RKB. RKB может проводить обработку для стабилизации размеров при рабочих температурах до
350 °C, что соответствует RKB S4. Однако чем выше размерная стабильность, тем ниже твердость, что отрицательно сказывается на сроке службы подшипника.
Для колец толщиной более 17 мм обработка для стабилизации размеров RKB не может быть правильно применена ко всему объему материала, в то время как обработка бейнитом RKB может быть выполнена правильно.
Кроме того, если кольца толще 17 мм, для подшипников RKB можно использовать сталь SAE 52100/A. В этом случае бейнитная обработка RKB не может быть применена к кольцам подшипников из-за высокого содержания кремния и марганца, которые повышают твердость и снижают ударную вязкость за пределами допустимых пределов. Напротив, все обработки RKB для стабилизации размеров могут быть точно применены к кольцам подшипников, изготовленным из SAE 52100/A.
Для критических/жестких применений группа RKB использует сталь SAE A485.RAV или RKB Type.RAV с обеими специальными термообработками, независимо от толщины кольца.
Кроме того, RKB Group может применять к своей продукции две специальные термохимические обработки:
- Противоизносная обработка (AWT) и
- Фосфатная обработка (PT).
Группа RKB использует противоизносную обработку для снижения как трения, так и износа контактирующих поверхностей, работающих в смешанных или даже граничных режимах смазки. Противоизносная обработка снижает риск преждевременного выхода подшипника из строя и продлевает срок его службы.
Слой сульфида железа толщиной 3-6 мкм, благодаря противоизносной обработке, представляет собой пористое и рыхлое вещество, которое поглощает больше смазочного масла. Он обеспечивает наличие смазочной пленки между телами качения и дорожками качения, тем самым уменьшая трение и износ контактирующих поверхностей (рис. 11). Вследствие чрезмерных нагрузок или больших ускорений и торможений упруго-гидродинамическая пленка может нарушиться, но благодаря самосмазывающемуся слою сульфида железа подшипники с противоизносной обработкой RKB могут корректно функционировать в режиме граничной смазки. без абразивного износа.
Наоборот, для подшипников без противоизносной обработки режим граничной смазки предполагает повышенное трение и, что еще важнее, интенсивный абразивный износ, способный ускорить выход подшипника из строя.
Фосфатирование — это термохимическая обработка, используемая RKB Bearing Industries для защиты от коррозии подшипников качения, предназначенных для работы в агрессивных средах. Обработку фосфатом можно наносить на оба кольца подшипника (PT1), только на наружные кольца (PT2), внутренние кольца (PT3) или на оба кольца подшипника и тела качения (PT4).
4. Многоуровневый контроль качества подшипниковой стали RKB
Группа RKB постоянно совершенствует свои знания в области подшипниковой стали посредством научных исследований, проводимых ее техническим отделом. Непрекращающееся сотрудничество группы компаний RKB со своим поставщиком стали позволило нашим сталям со сквозной и цементированной закалкой дополнительно снизить содержание кислорода и неметаллических включений, обеспечив высокую чистоту и лучшее сопротивление усталости в контакте качения.
Контроль качества, осуществляемый RKB в отношении своей стали и готовой продукции, осуществляется на многоуровневой основе посредством неразрушающих испытаний, контроля химического состава, оценки макро- и микроструктуры, измерений механических свойств и окончательного отчета для отслеживания (рис. 12). ).
Одной из важнейших задач, которую должен выполнять отдел контроля качества RKB, является правильная количественная оценка чистоты стали. С этой целью для оценки макровключений используется синий тест на излом, а для оценки микровключений – метод оптической микроскопии. Эти методы позволяют проводить объемную оценку и дают статистически значимое количество включений.
Чтобы прояснить различия между стандартной подшипниковой сталью и специальной подшипниковой сталью RKB Type.RAV, мы оценили их с металлографической точки зрения. Мы исследовали площадь приблизительно 112 мм2 на наличие неметаллических включений в соответствии с ASTM E3 и ASTM E45
. На рис. значительно выше в стандартной подшипниковой стали, чем в специальной подшипниковой стали RKB. Оценка общей длины неметаллических включений заключалась в осмотре продольного (параллельного линиям потока материала) разреза. Как видно из рисунка 15, общая длина у стандартной стали оказывается намного больше, чем у стали RKB Type.RAV.
5. Выводы
Номинальный срок службы подшипников с идеальной внутренней геометрией, правильным монтажом и стандартными условиями эксплуатации в конечном счете определяется качеством сталей, используемых в производственном процессе.
Чтобы выполнить требования последних международных стандартов в этой области, RKB Group постоянно проводит исследования и разработки в области качества стали для подшипников качения, особенно в отношении чистоты, термической и химической обработки и соответствующего контроля процесса. Равновесие между этими факторами привело к увеличению усталостной долговечности подшипников качения производства RKB.