Сталь h1: – – H1 Stainless Steel
alexxlab | 29.05.2023 | 0 | Разное
Сталь h2/H-1 нержавеющая – Златоустовские ножи и украшенные изделия
Myodo Foundry H-1 нержавеющая сталь
Производитель: Myodo Foundry, Япония
h2 (Myodo) – это настоящая нержавеющая сталь, практически не ржавеющая. Имеет очень мало углерода, только 0,15%, но наличие азота 0,10% улучшает характеристики.
Твердость стали достигает 57-58 HRC (хотя существуют некоторые разногласия относительно твердости на режущей кромке, она может быть выше), что весьма хорошо, учитывая, что в стали очень мало углерода. Сталь используется «как есть» от производителя (подвергается холодному прокату для получения твердого мартенсита) и не требует дальнейшей термообработке у производителя ножей.
Химический состав, %
C | Cr | Mo | N | Ni | Mn | Si | Cu | P | S |
0,15 | 14,0-16,0 | 0,50-1,50 | 0,10 | 6,0-8,0 | 2,0 | 3,00-4,50 | 0,10 | 0,04 | 0,03 |
Существует миф в мире ножей о том, что где-то есть суперсталь с высокими характеристиками, которая не ржавеет. Сталелитейный завод в Японии сделал миф реальностью, создав сталь H-1. h2 имеет режущую кромку, аналогичную многим высококачественным углеродистым сталям, но без риска образования ржавчины или точечной коррозии. С появлением ножей из H-1 ножи из кобальто-хромового сплава исчезли с рынка. Сталь H-1 предлагает коррозионную стойкость кобальтовых сплавов без дополнительных затрат на материалы и производство. H-1 практически революционная сталь.
H-1 была представлена на рынке компанией Benchmade в 2003 году, а вскоре за ними последовал Spyderco. Spyderco широко использует h2 в линейке ножей SALT, которые предназначены для использования в соленой воде. Benchmade позже заменил сталь на X15TN. Хотя сталь является отличным выбором для коррозионностойкого ножа для дайвинга или для использования в агрессивных средах, она все равно не сравнится с S30V или VG-10, когда речь заходит о износостойкости, но будет работать так же хорошо, как и младшая сталь серии 440 – нержавеющая сталь 440A. Работает довольно хорошо, аналогично сталям Aichi AUS-6 и Aichi AUS-8, и в то же время значительно более устойчива к коррозии, что означает, что она превосходит большинство нержавеющих сталей в агрессивных условиях.
По своей сути, h2 – это аустенитная нержавеющая сталь. Аустенитные нержавеющие стали примерно так же стары, как и сама нержавеющая сталь, их разрабатывали немецкие металлурги в период 1909-1912 гг. Они работали над созданием 18% Cr, 8% Ni сталей, которые очень похожи на обычные аустенитные нержавеющие стали, такие как 301, 302 и 304.
Удержание режущей кромки
Из-за относительно низкой твердости, отсутствия карбидов и дельта-феррита износостойкость h2 намного ниже, чем у многих других ножевых сталей. Ожидается, что это приведет к плохому удержанию кромок, что подтверждается сообщениями Spyderco о результатах CATRA. Также сообщалось, что h2 имеет «заоблачное» удержание остроты с серрейторной заточкой, даже лучше, чем другие ножевые стали.
Прочность
Ударная вязкость является достоинством h2. Сталь имеет относительно низкую твердость, содержит мягкий и пластичный феррит и не содержит хрупких карбидов.
Устойчивость к коррозии
Основным преимуществом использования h2 является коррозионная стойкость. Ожидается, что она ниже аустенитных нержавеющих сталей с 18% Cr и 8% Ni, потому что h2 имеет только 15% хрома. Однако 1% молибдена помогает улучшить коррозионную стойкость. Обычно нержавеющая сталь 304 (19 % Cr) является минимально рекомендуемой сталью для соленой воды. Тем не менее, для непрерывного воздействия соленой воды требуется более высокое значение молибдена, поэтому более распространенной является сталь 316, в которой содержание Мо составляет 2-3%. Таким образом, h2 не совсем соответствует уровню тех сталей, которые изготовлены для соленой воды, но поскольку ножи не испытывают непрерывное длительное воздействие соленой воды, то коррозионная стойкость достаточна для большинства применений.
Если вас интересует идеальный рыболовный нож, не проходите мимо. Такая удивительная коррозионная стойкость обходится дорого, так как эта сталь не обладает хорошей износостойкостью, стойкостью режущей кромки.
Ножи из стали h2 Stainless Steel
Включите в вашем браузере JavaScript!
Магазин ножей с характеромКаталог
Бренды ножей
Хиты
Новинки
Товары со скидкой
Доставка и оплата
Контакты
Ножи из стали h2 Stainless Steel отличаются агрессивным стилем и довольно универсальной формой клинка. Такие ножи удобно использовать на охоте и в походах, они комфортно размещаются в руке, обладают мощной и приятной на ощупь рукоятью. Особенно актуальные ножи из стали h2 при плавании и дайвинге – ржавчина на клинке не появляется даже после контакта с соленой водой. Вы гарантировано будете довольны их функциональностью и практичностью!
Сортировка: по умолчаниюпо размеру скидкипо популярностипо новизнеот дешевых к дорогимот дорогих к дешевым
Показано 1-38 из 38
Нож складной Salt 1 – Spyderco C88SBK, сталь h2 Satin Serrated, рукоять термопластик FRN, чёрный
10 800 руб
Нож складной Ladybug Salt
9 200 руб
Нож складной Ladybug Salt LYLS3
9 200 руб
Складной нож Spyderco Yellow Salt 2 Rust Proof Serrated Blade Yellow FRN Lockback Folding Knife
16 500 руб
Складной нож Salt 2 – Spyderco 88PBBK2, сталь H-1 Black Titanium Carbonitride (TiCN) Plain, рукоять термопластик FRN, чёрный
17 380 руб
Складной нож Salt 2 Black Blade
16 400 руб
Нож складной ManBug Salt Lightweight
11 300 руб
16 200 руб
Товар отсутствует
Нож складной Tasman Salt 7. 0 см
9 670 руб
Посмотреть
Товар отсутствует
Нож складной Tasman Salt Yellow C106PYL
8 430 руб
Посмотреть
Товар отсутствует
Нож складной Salt saver Spyderco
7 530 руб
Посмотреть
Товар отсутствует
Нож складной Snap-It™ Salt SpyderEdge
15 440 руб
Посмотреть
Товар отсутствует
Нож складной Dragonfly 2 Salt, Yellow FRN Handle, SpyderEdge
12 020 руб
Посмотреть
Товар отсутствует
Складной нож Rescue Assist™ Salt Yellow20 000 руб
Посмотреть
Товар отсутствует
Складной нож Salt 1 Black Blade
9 840 руб
Посмотреть
Товар отсутствует
Складной нож Salt 1 – Spyderco C88SBBK, сталь H-1 Black Titanium Nitride Serrated, рукоять термопластик FRN, чёрный
9 490 руб
Посмотреть
Товар отсутствует
Нож складной Atlantic Salt
16 750 руб
Посмотреть
Товар отсутствует
Нож складной Pacific Salt Spyderco
10 690 руб
Посмотреть
Товар отсутствует
Нож складной Pacific Salt, Black Serrated
11 810 руб
Посмотреть
Товар отсутствует
9 140 руб
Посмотреть
Товар отсутствует
Нож с фиксированным клинком Enuff Sheepfoot Salt
21 680 руб
Посмотреть
Товар отсутствует
Нож с фиксированным клинком ARK (Always Ready Knife), SpyderEdge Blade
9 440 руб
Посмотреть
Товар отсутствует
Нож складной Ladybug 3 Hawkbill Salt SpyderEdge
8 450 руб
Посмотреть
Товар отсутствует
Складной нож Spyderco Yellow Salt 2 Folder Knife, H-1 Satin Blade
18 520 руб
Посмотреть
Товар отсутствует
Нож складной Tasman-2 Salt
10 830 руб
Посмотреть
Товар отсутствует
Нож с фиксированным клинком ARK h2
8 660 руб
Посмотреть
Товар отсутствует
Нож складной Tasman Salt
10 830 руб
Посмотреть
Товар отсутствует
Складной нож Spyderco Tasman Salt 2 Black
13 980 руб
Посмотреть
Товар отсутствует
Складной нож Spyderco Tasman Salt 2 Yellow-2
14 540 руб
Посмотреть
Товар отсутствует
Складной нож Spyderco Tasman Salt 2 Yellow Lockback Knife
10 830 руб
Посмотреть
Товар отсутствует
Нож складной Pacific Salt, Black
15 870 руб
Посмотреть
Товар отсутствует
Нож складной Pacific Salt 2 Spyderco, сталь h2 Carbonitride Plain, рукоять термопластик FRN
17 060 руб
Посмотреть
Товар отсутствует
Нож складной Pacific Salt, Serrated
16 400 руб
Посмотреть
Товар отсутствует
Нож складной Pacific Salt, Black Serrated
19 500 руб
Посмотреть
Товар отсутствует
Нож складной Saver Salt Spyderco, сталь H-1, рукоять термопластик FRN
13 980 руб
Посмотреть
Товар отсутствует
Нож складной Dragonfly 2 Salt, Yellow FRN Handle, SpyderEdge
8 430 руб
Посмотреть
Товар отсутствует
Складной нож Salt 1
15 440 руб
Посмотреть
Товар отсутствует
Нож складной Spyderco Atlantic Salt 89SBK, сталь h2, рукоять пластик FRN черный
16 750 руб
Посмотреть
Наш сайт использует файлы cookie. Для продолжения работы с ресурсом ознакомьтесь с политикой конфиденциальности
принять
.
Быстрый заказ
Имя:
Контактный телефон:
Населенный пункт:
Комментарий:
h2 Steel – Как это работает
Спасибо Guns N’ Loaded за то, что вы стали сторонником Knife Steel Nerds Patreon!
Аустенитные нержавеющие стали
По своей сути, h2 — это аустенитная нержавеющая сталь. Аустенитные нержавеющие стали примерно так же стары, как и сама нержавеющая сталь, они были разработаны немецкими металлургами примерно в период времени 1909-1912 гг. Они работали со сталями 18% Cr, 8% Ni, которые очень похожи на обычные аустенитные нержавеющие стали, такие как 301, 302 и 304.
Стали называются «аустенитными», потому что сталь находится в «аустенитной» фазе при комнатной температуре, а не в типичных ферритных или мартенситных фазах при комнатной температуре. Большинство сталей превращаются в аустенит при нагревании до достаточно высокой температуры (например, 1340-1600°F). Аустенит относится к расположению атомов железа внутри стали. Таким образом, когда сталь нагревается до высокой температуры, она самопроизвольно превращается из одного атомного расположения, феррита, с «объемно-центрированной кубической» атомной структурой в аустенит, который представляет собой «гранецентрированную кубическую» структуру. Вот схематические изображения двух различных атомных расположений:
«Элементарная ячейка» объемно-центрированного кубического феррита. Элементарная ячейка представляет собой наименьшее возможное представление кристаллической структуры
Как выглядит элементарная ячейка в увеличенном виде объемно-центрированной структуры феррита
Гранецентрированная кубическая элементарная ячейка аустенита
Увеличенный вид гранецентрированного кубического аустенита
Точная кристаллическая структура феррита и аустенита не так важна, как свойства. Аустенит легко отличить от феррита и мартенсита, потому что он немагнитен. Многие производители ножей используют магнит при термообработке, чтобы узнать, когда сталь превратилась в аустенит. Однако аустенитные нержавеющие стали предназначены для аустенизации при комнатной температуре, поэтому они также немагнитны при комнатной температуре. Они стабилизируют аустенит до комнатной температуры, добавляя различные легирующие элементы, чтобы мартенсит не образовывался во время закалки. Обычно ножевая сталь нагревается до высокой температуры с образованием аустенита, а затем закаливается с образованием твердого мартенсита. Однако различные легирующие элементы снижают температуру образования мартенсита и могут быть снижены до температуры ниже комнатной:
Ms (°C) = 539 – 423*C – 311*N – 30,4*Mn – 17,1*Ni – 12,1*Cr – 7,5*Mo – 7,5*Si
В то время как углерод является лучшим элементом для уменьшения начала мартенсита температуры, это также имеет тенденцию приводить к образованию карбидов. Это означает, что сталь должна быть нагрета до более высоких температур, чтобы растворить все карбиды, или даже до точки, при которой карбиды не будут растворяться без расплавления стали. Карбиды также имеют тенденцию образовываться на границах зерен, если они не охлаждаются достаточно быстро. Из-за высокого содержания хрома нержавеющие стали с углеродом имеют тенденцию к образованию карбидов хрома, а образование этих карбидов приводит к локальному восстановлению хрома «в растворе». Если хром превратился в карбид, он больше не находится в растворе, что способствует коррозионной стойкости. Хром должен находиться в растворе, чтобы сформировать пассивный слой, предотвращающий коррозию. Большее количество хрома в растворе означает более прочный пассивный слой и лучшую коррозионную стойкость. Поэтому добавки углерода обычно избегают в аустенитных нержавеющих сталях из-за потенциального снижения коррозионной стойкости.
Высокое содержание хрома улучшает коррозионную стойкость, а также уменьшает мартенситное начало, поэтому простое добавление хрома кажется простым способом получения аустенитной нержавеющей стали. Однако хром также является «стабилизатором феррита». Существует высокотемпературная ферритовая фаза, называемая «дельта-феррит», которую я выделил синим цветом на приведенной ниже диаграмме. Дельта-феррит аналогичен типичному низкотемпературному ферриту, но встречается при высоких температурах.
Фазовая диаграмма 8%Cr железо-углерод, показывающая дельта-феррит (синий), аустенит (красный) и феррит+аустенит (фиолетовый)
Выше указана сталь с содержанием 8 % хрома. Фаза дельта-феррита находится в относительно узком диапазоне очень высоких температур для низкоуглеродистой стали (~ 2350-2750 ° F). Поле аустенитной фазы, напротив, охватывает широкий диапазон температур и содержания углерода. Фиолетовое поле представляет собой комбинацию феррита и аустенита. Однако добавление большего количества хрома, поскольку он является стабилизатором феррита, расширяет фазовое поле дельта-феррита.
12% Cr Фазовая диаграмма железо-углерод
При 12% хрома поле дельта-ферритной фазы значительно расширилось, а поле феррит+аустенит достигло размера, при котором для сталей с очень низким содержанием углерода полное поле аустенитной красной фазы не может быть достигнуто ни при какой температуре. При еще большем количестве хрома область аустенитной фазы очень мала:
Диаграмма фаз железо-углерод 18% Cr
При 18% Cr аустенитная фаза никогда не наблюдается в стали с очень низким содержанием углерода и даже в сталях с содержанием углерода до 0,5 % углерод может лишь частично превратиться в аустенит.
Молибден и кремний также являются стабилизаторами феррита, поэтому они также не помогают сделать сталь аустенитной. Поэтому в аустенитные нержавеющие стали обычно добавляют никель, а иногда и марганец, потому что они уменьшают начало мартенсита и также являются стабилизаторами аустенита. Вот 18% Cr сталь, в которую также добавлено 8% Ni:
18%Cr-8%Ni Диаграмма состояния железо-углерод
После добавления 8% Ni в 18% Cr сталь, фаза дельта-феррита поле теперь чрезвычайно мало, а поле аустенитной фазы намного больше и смещено в сторону более низкого содержания углерода. Поэтому сталь можно нагреть до аустенита перед быстрым охлаждением, чтобы сохранить аустенит при комнатной температуре.
Свойства аустенита и замена никеля
Желательна аустенитная фаза из-за ее очень хорошей пластичности и ударной вязкости. Он также имеет низкий предел текучести, что означает, что операции формовки аустенитной стали относительно просты. В некоторых случаях также желательны немагнитные свойства стали. Никель также улучшает коррозионную стойкость, способствуя «репассивации» при потере пассивного слоя оксида хрома. Это особенно полезно в уменьшении окружающей среды и минеральных кислот. Азот также снижает Ms и стабилизирует аустенит при высокой температуре, но добавление азота в значительных количествах затруднено. И хотя азот с меньшей вероятностью образует нитриды хрома, чем углерод – карбид хрома, избыток азота может привести к образованию нитридов и снижению коррозионной стойкости. О добавках азота в нержавеющую сталь вы можете прочитать в этой статье. Уменьшение содержания никеля желательно, поскольку никель дорог. Частичная замена никеля марганцем используется в некоторых сортах, но полная замена нецелесообразна. Марганец примерно вдвое менее эффективен, чем никель, в расширении поля аустенитной фазы, а пиковый эффект составляет 5% и сужает поле аустенита в больших количествах [1]. Следовательно, Mn может заменить только около 2,5% никеля. И Mn не улучшает коррозионную стойкость, как это делает никель; на самом деле Mn оказывает незначительное негативное влияние на коррозионную стойкость [1]. Однако, в отличие от никеля, марганец действительно улучшает растворимость азота в жидкой стали, и поэтому некоторые стали были произведены с комбинацией марганца и азота вместо никеля. Таким образом, высокое содержание марганца в этих сталях на самом деле связано с добавлением большего количества азота, а не из-за самого марганца. Примерами являются аустенитные нержавеющие стали серии 200, такие как 201, 202 и 205. Азот расширяет поле аустенитной фазы, а также улучшает коррозионную стойкость.
Превращение в мартенсит при холодной обработке
При деформации аустенитных нержавеющих сталей они фактически образуют мартенсит, даже если начальная температура мартенсита ниже комнатной температуры. Мартенсит представляет собой очень прочную/твердую фазу, которая обычно является основной фазой в ножевых сталях. При холодной прокатке, гибке, штамповке и т. д. внутри аустенита образуется мартенсит. Вот изображения нержавеющей стали 301 с возрастающими уровнями «деформации», где вы можете увидеть мартенситные пластины/пластины, формирующиеся по мере деформации стали:
Нержавеющая сталь 301 с увеличивающимся уровнем деформации (указано в процентах), демонстрирующим увеличение мартенсита. Изображения из [2]
Во время холодной обработки стали возникают дефекты атомарного уровня, называемые «дислокациями». Дислокации присутствуют во всех металлах, но плотность дислокаций зависит от различных этапов обработки и термической обработки. Дислокации упрочняют сталь, поэтому чем больше наклепа, тем больше дислокаций и тем прочнее сталь. Прочность металлов определяется поведением дислокаций. О том, что такое дислокации и почему они важны, я написал в этой статье. А про холодную работу вы можете прочитать в этой статье. Вот пример увеличения твердости при холодной обработке инструментальной стали A8 mod:
Данные адаптированы из [3]
Эти дислокации на атомном уровне также могут способствовать образованию мартенсита посредством «гетерогенного зародышеобразования». Новые фазы имеют тенденцию образовываться в благоприятных местах, таких как карбиды, поверхность стали или границы зерен. Дислокации также могут быть благоприятными местами для образования новой фазы, в данном случае мартенсита, поэтому их увеличение может способствовать образованию мартенсита. Это механизм, с помощью которого деформирование аустенитных сталей приводит к образованию мартенсита.
Более низкая температура способствует образованию мартенсита во время деформации, а более высокая температура задерживает образование мартенсита. Аустенит более стабилен при более высоких температурах. На рисунке ниже показано количество образовавшегося мартенсита в зависимости от величины деформации при различных температурах. При 50-80°С (125-175°F) мартенсит практически не образовывался даже при деформации 60% для этой конкретной стали.
Изображение из [4]
Различные аустенитные нержавеющие стали более или менее подвержены превращению в мартенсит во время деформации, в зависимости от состава стали. Влияние состава несколько отличается от влияния, контролирующего температуру начала мартенсита. Распространенным уравнением является предсказание температуры, при которой образуется 50% мартенсита с 30% деформацией в зависимости от состава. Следовательно, количество мартенсита, образующегося при деформации при данной температуре, может быть увеличено за счет более высокого M Д30 .
M D30 (°C) = 413 – 462*(C+N) – 9,2*Si – 8,1*Mn – 13,7*Cr – 9,5*Ni – 18,5*Mo
Некоторые стали предназначены для стимулирования образования мартенсита путем восстановления углерода (304L) или путем восстановления Cr и Ni (301). Образование мартенсита означает, что при холодной прокатке стали можно достичь высокой прочности. Сочетание холодной обработки для повышения прочности за счет образования дислокаций и образования твердого мартенсита означает, что холодная прокатка аустенитных нержавеющих сталей может привести к относительно высоким уровням твердости, по крайней мере, по сравнению с обычными отожженными аустенитными нержавеющими сталями. 301 нержавеющая сталь с 9Сообщается, что 0% холодное обжатие составляет около 55 Rc [5], что аналогично твердости типичных мартенситных сталей в бытовых ножах, но ниже, чем 60+ Rc, характерное для высококачественных ножей. Узнайте о том, что означает твердость по Роквеллу, в этой статье.
h2 Состав стали
Итак, я думаю, у нас наконец-то достаточно предыстории, чтобы добраться до h2. Состав h2 не сильно отличается от других аустенитных нержавеющих сталей, таких как 301 и 302B.
В сталь 302B добавлено большое количество кремния, что способствует «сопротивлению образованию окалины», что означает, что она менее склонна к образованию окалины при высокой температуре во время ковки или других операций. Si в h2 вполне может быть добавлен по той же причине, но добавление даже больше, вероятно, больше, чем необходимо для устойчивости к образованию накипи. H2 также предназначен для достижения высокой твердости после холодной прокатки. Кремний является одним из лучших «упрочнителей твердого раствора», поэтому я думаю, что его можно добавлять для увеличения твердости.
Изображение из [6]
Молибден также увеличивает прочность, однако, вероятно, его добавляют для повышения коррозионной стойкости, в частности, для защиты от точечной коррозии. Существует общее уравнение для прогнозирования стойкости к точечной коррозии, где Mo оказывает более сильное влияние, чем хром. Таким образом, Mo очень хорош для улучшения коррозионной стойкости в растворах хлоридов, таких как соленая вода. Азот также улучшает коррозионную стойкость, но в h2 его очень мало. Я бы не назвал h2 «азотной сталью», потому что многие ножевые стали содержат одинаковое количество азота. Многие спецификации аустенитной нержавеющей стали имеют максимальное содержание азота 0,1%, как и h2, поэтому h2 нередко имеет аналогичное максимальное содержание азота в своем классе стали.
PREN = Cr + 3,3*Mo + 16*N
Содержание никеля также снижено до 7% по сравнению с 302 и 304, как и 301, что способствует образованию мартенсита. Содержание хрома также дополнительно снижено по сравнению с этими сталями до 15%. Это несколько снижает коррозионную стойкость, но способствует образованию мартенсита при холодной прокатке.
Мне также прислали анализ состава h2 от Sandvik на Spydero Salt, он соответствует заявленному составу, за исключением слегка низкого содержания хрома:
Производство стали h2 для ножей
h2 впервые был использован в ножах американского производства компанией Benchmade примерно в 2002-2003 годах, а вскоре после этого компанией Spyderco [7]. Сообщается, что сталь h2, производимая для Spyderco, начинается с заготовки толщиной 7 мм и подвергается холодной прокатке до конечной требуемой толщины [8], до толщины 3 мм для измельчителя Schempp [9] или, вероятно, до 2 мм для легкие папки. Это будет диапазон холодного восстановления 57-71%, не сумасшедшее снижение, но, вероятно, разумное количество для обеспечения надежности процесса. Мартенсит, образующийся при холодной прокатке, естественно «неотпущенный». Они выполняют обработку старением после холодной прокатки, которая закаляет мартенсит. Эта обработка старением фактически увеличивает твердость холоднокатаной стали, если она выполняется в правильном диапазоне температур [10]. В этой статье описан механизм повышения твердости закалкой. Сталь используется как есть от производителя в ножах и не подвергается дальнейшей термообработке [8].
Измерения твердости по h2
Сообщается, что металлурги из тигля измерили твердость по h2 и обнаружили, что она составляет приблизительно 58 Rc в хребте и более твердая на краю, приблизительно 65 Rc [11]. Я не знаю, почему твердость должна быть выше на кромке, поскольку сталь, по-видимому, не «асимметрично» холоднокатана (чтобы предварительно прокатать краевой конус в стали). Были некоторые предположения, что шлифовальные операции приводят к дальнейшему упрочнению (наклепу) кромки, что приводит к повышению твердости. Дальнейшее увеличение твердости будет результатом дальнейшего увеличения доли мартенсита и плотности дислокаций. Однако деформационное упрочнение требует изменения формы, т. е. изгиба, уменьшения поперечного сечения и т. д. Шлифование может привести к поверхностному наклепу самой поверхности, особенно когда шлифовальный станок трет, а не шлифует. Маловероятно, что шлифовка и заточка приведут к достаточному упрочнению для изменения общей кромки. Также сообщается, что шлифовка зубцов приводит к несколько более высокой твердости. Я также не могу придумать причину, по которой шлифовка зубцов может привести к большей деформации. Операция чистого шлифования не приведет к наклепу, и если бы имело место какое-либо значительное упрочнение, они, вероятно, столкнулись бы с такими проблемами, как коробление лезвий и т. д. Поверхностное упрочнение означало бы, что операция шлифования работает неэффективно. Упрочнение требует постоянной деформации, нож должен быть постоянно согнут, или кромка должна быть утончена и т.
Д. За счет удара молотком, изгиба или другого способа деформации. Упругая деформация, такая как изгибание кромки так, чтобы она возвращалась в исходное положение при отпускании, не приводит к деформационному упрочнению. Сообщаемая твердость 65-68 Rc потребует очень большого объема дополнительного наклепа выше 57-58 Rc, и при такой твердости существует большая вероятность растрескивания. Эти типы сталей, как правило, имеют среднее и высокое значение Rc 50 при деформационном упрочнении (холодная прокатка), и случайное увеличение до 65 Rc кажется маловероятным.
Sandvik прислал мне анализ h2 в Spyderco Salt. Они не обнаружили увеличения твердости на краю, фактически они обнаружили снижение. График ниже – это то, что мне прислали, где значение около 55 Rc было 0,4 мм (0,16 дюйма) от края. К сожалению, мне не предоставили рентгеновский снимок, чтобы увидеть расстояния между измерениями. Однако значение Rc стали ~57 сравнимо со значением, указанным выше в Crucible. Возможно снижение твердости на кромке из-за перегрева в результате шлифовки.
Измерения твердости Spyderco Salt, проведенные Sandvik
Микроструктура h2
Sandvik также прислала мне микрофотографии их Spyderco Salt в h2, и сталь имеет интересную микроструктуру. Они сделали снимки в центре лезвия, а также на краю.
Большая часть микроструктуры выглядит как мартенсит, имеющий шероховатый и пластинчатый или пластинчатый вид, как показано ниже при большем увеличении. Есть также некоторые продолговатые элементы с белым травлением, которые для меня выглядят как дельта-феррит:
Дельта-феррит иногда присутствует в аустенитных нержавеющих сталях, поскольку при медленном затвердевании расплавленной стали происходит ликвация. Легирующие элементы будут диффундировать друг к другу, образуя локализованные области с большим или меньшим содержанием данного элемента. Когда хром и другие стабилизаторы феррита разделяются на определенные области, феррит стабилизируется и сохраняется при более низких температурах. Кремний также является стабилизатором феррита, поэтому высокое содержание кремния в h2, вероятно, также затрудняет избегание дельта-феррита. Феррит не особенно желателен в ноже из-за его низкой твердости; феррит может снизить прочность кромки.
Сохранение кромки
Из-за относительно низкой твердости, отсутствия карбидов и дельта-феррита износостойкость стали h2 намного ниже, чем у многих других ножевых сталей. Ожидается, что это приведет к плохому удержанию краев разреза, что подтверждается отчетами Spyderco об удержании краев CATRA [12]. Также сообщалось, что у h2 превосходное удержание режущей кромки с зазубренными краями, даже лучше, чем у других ножевых сталей. Я уверен, что удержание края значительно лучше по сравнению с простыми краями. Тем не менее, я не знаю, что насчет h2 может привести к лучшему удержанию кромки, чем у других сталей с зазубренной кромкой. Предложения об эффектах закалки работы не имеют для меня смысла. Тем не менее, утверждения, которые я видел, несколько неясны относительно того, что имеется в виду, кроме хорошего удержания зазубренной кромки, относится ли это к уровню увеличения между гладкими и зазубренными кромками или к сравнению удержания зазубренной кромки из стали h2 с удержанием гладкой кромки из других сталей. 12].
Прочность
Вышеупомянутые эффекты, которые приводят к плохому удержанию края, вероятно, означают, что прочность хороша для h2. Сталь имеет относительно низкую твердость, содержит мягкий и пластичный феррит и не содержит хрупких карбидов. Поэтому я ожидаю, что прочность h2 будет высокой.
Коррозионная стойкость
Основным преимуществом использования h2 является коррозионная стойкость. Ожидается, что он будет на ступеньку ниже аустенитных нержавеющих сталей с 18% Cr и 8% Ni, потому что h2 содержит только 15% Cr. Однако 1% Mo, вероятно, помогает улучшить коррозионную стойкость. h2 продвигается за его устойчивость к коррозии в ножах, используемых в соленой воде. Обычно нержавеющая сталь 304 (19% Cr) — минимальная рекомендуемая сталь для воздействия соленой воды, особенно версия с низким содержанием углерода. Однако для постоянного воздействия соленой воды требуется более высокое содержание Мо, поэтому чаще встречается 316, в которой 2-3% Мо. Так что h2 не совсем до уровня тех сталей, которые сделаны для соленой воды, но так как ножи не видят непрерывных длинных – при длительном использовании в соленой воде коррозионная стойкость достаточна для большинства применений.
Однако по сравнению с обычными ножевыми сталями коррозионная стойкость стали h2 является звездной. Одним из основных преимуществ является наличие небольшого количества карбида или его отсутствие. Общей проблемой нержавеющих сталей является «сенсибилизация», когда сталь локально восстанавливается хромом вокруг карбидов, особенно тех, которые образуются на границах зерен. H2 практически не имеет этой проблемы, особенно по сравнению с большинством ножевых нержавеющих сталей, наполненных карбидом хрома. Практически весь ~15% Cr в h2 находится в растворе, что способствует коррозионной стойкости. Я оценил количество хрома в растворе для всех основных нержавеющих сталей для ножей и обнаружил, что h2 выше, чем у всех, кроме Vanax, но позже я провел повторную оценку с помощью другого программного пакета и обнаружил, что первая оценка была завышена для Vanax. Следовательно, h2 содержит столько же или больше Cr в растворе, чем практически любая другая ножевая сталь. Это в сочетании с отсутствием карбида означает, что это очень хороший выбор для обеспечения высокой коррозионной стойкости.
Резюме
Мне пришлось рассказать много об аустенитных нержавеющих сталях, чтобы вообще обсудить h2, а это тема, которую трудно представить в таком небольшом объеме. И мне пришлось дать много ссылок на статьи по другим базовым понятиям, потому что было бы слишком много пояснений для них всех в рамках этой статьи. Так что, надеюсь, объяснения h2 имеют смысл. На самом простом уровне h2 представляет собой аустенитную нержавеющую сталь, которая была подвергнута холодной прокатке, чтобы получить твердый мартенсит. Он был разработан, чтобы поддерживать эту микроструктуру за счет пониженного содержания Cr и Ni, а прочность дополнительно повышается за счет добавок Mo и Si. Эта комбинация состава и обработки приводит к твердости около 57 Rc, хотя есть некоторые разногласия по поводу твердости на кромке. Сохранение кромки относительно плохое, но ударная вязкость хорошая, а коррозионная стойкость h2 отличная.
[1] Писториус П. К. и М. Дю Туа. «Аустенитные нержавеющие стали с низким содержанием никеля: металлургические ограничения». В 12-й междунар. Конгресс ферросплавов, состоявшийся 9 июня 1993 г., стр. 6-9. 2010.
[2] Хаушилд, П., В. Давыдов, Дж. Драгокупил, М. Ланда и П. Пилвин. «Характеристика вызванного деформацией мартенситного превращения в метастабильной аустенитной нержавеющей стали». Материалы и дизайн 31, №. 4 (2010): 1821-1827.
[3] Гасеми-Нанеса, Хади, Мохаммад Джахази, Маджид Хейдари и Том Левассер. «Влияние вызванных деформацией микропустот на механическое разрушение мартенситной инструментальной стали AISI A8-Mod». В Протоколы конференции AIP , том. 1896, нет. 1, с. 020021. Издательство AIP, 2017.
[4] Ангел, Т.Дж. «Формирование мартенсита в аустенитных нержавеющих сталях». Журнал Института чугуна и стали 177 (1954): 165-174.
[5] Johannsen, D.L., A. Kyrolainen, and P.J. Ferreira. «Влияние обработки отжигом на формирование аустенитных нержавеющих сталей AISI 301 с размером зерна нано/субмикрон». Металлургические и материальные сделки A 37, no. 8 (2006): 2325-2338.
[6] Пикеринг, Ф. Б. «Высокопрочные низколегированные стали — десятилетие прогресса, микролегирование 75». Proceedings, Union Carbide Corp, New York 9 (1975).
[7] https://www.bladeforums.com/threads/h2-steel-100-corrosion-proof.239015/
[8] https://forum.spyderco.com/viewtopic.php?f= 2&t=72555&p=1120610
[9] https://forum.spyderco.com/viewtopic.php?t=75399
[10] Rathbun, R.W., D.K. Matlock, and J.G. Speer. «Деформационное старение аустенитных нержавеющих сталей, содержащих мартенсит, вызванный деформацией». Scripta materialia 42, вып. 9 (2000).
[11] https://forum.spyderco.com/viewtopic.php?t=58227&start=20
[12] http://www.cliffstamp.com/knives/forum/read. php?5,71943
Нравится:
Нравится Загрузка…
h3 Steel – h2 продолжение
Background
Недавно Spyderco Byte анонсировала замену стали h2 – h3. H2 известна как сталь с очень высокой коррозионной стойкостью, используемая в основном в линейке ножей Spyderco Salt. У меня есть предыдущая статья о дизайне h2 и о том, как он «работает», которую вы можете прочитать здесь. У меня возникло искушение переписать большие куски этой статьи здесь, потому что h2 — одна из самых неправильно понятых ножевых сталей, но я попытаюсь выделить несколько основных моментов без особых объяснений, и я надеюсь, что вы прочтете предыдущую статью, чтобы понять о чем я:
h2 — «аустенитная» нержавеющая сталь. Эта категория сталей включает такие марки, как 301, 302 и 304, и наиболее известна тем, что используется в изделиях, не связанных с ножами, таких как кастрюли и сковороды. Хотя они используются в ножах для масла, я полагаю. Они обладают очень высокой коррозионной стойкостью и отличной формуемостью, а также немагнитны. Сорта не известны своей высокой твердостью, которая обычно требуется для ножевых сталей. Однако аустенитные нержавеющие стали при холодной обработке превращаются в твердый мартенсит. Степень превращения стали в мартенсит зависит от ее состава и температуры холодной прокатки стали. Более низкие температуры приведут к большему превращению в мартенсит при меньшей холодной обработке. Существует много моделей и уравнений для прогнозирования того, насколько легко сталь превратится в мартенсит, но нет единого мнения о том, как это прогнозировать, из-за сложности моделирования поведения. Одним из измерений является температура, при которой 50% мартенсита образуется при 30% деформации. Вот уравнение для предсказания этой температуры:
M D30 (°C) = 413 – 462*(C+N) – 9,2*Si – 8,1*Mn – 13,7*Cr – 9,5*Ni – 18,5*Mo
Таким образом, для стали, предназначенной для быть превращенным в мартенсит посредством холодной прокатки, мы хотим, чтобы температура M D30 была относительно высокой, чтобы при холодной прокатке при комнатной температуре он почти на 100% преобразовывался в мартенсит (без растрескивания). Это обеспечивает относительно высокую твердость стали h2 в готовых ножах, которая измеряется в диапазоне 55-58 Rc.
У меня есть состав h2, сообщенный Spyderco, а также фактические измерения стали, независимо выполненные Sandvik:
состав h2 в сравнении с двумя другими, в чем-то похожими аустенитными нержавеющими сталями:
Измерения состава Sandvik для h2:
Этот процесс холодной прокатки аустенитной нержавеющей стали сильно отличается от большинства ножевых сталей, которые обычно нагревают до высокой температуры для превращения в аустенит, а затем быстро закаливают для превращения в мартенсит, а не подвергают холодной прокатке. Температуры, при которых стали превращаются в мартенсит, выше комнатной температуры, тогда как если аустенитную нержавеющую сталь закалить до комнатной температуры, она останется аустенитной, потому что мартенсит образуется только при температурах ниже комнатной.
h3 Сталь
Итак, со всей этой предысторией (надеюсь, вы читали статью h2, на которую я дал ссылку), мы можем посмотреть, что Spyderco сообщила об изменении h3. Я буду цитировать Spyderco Byte, а затем объяснять, о чем они говорят.
Азот
«Ключевым компонентом Pacific Salt и всех оригинальных ножей Spyderco Salt Series является сталь
H-1. Сталь H-1, разработанная корпорацией Myodo в Японии, представляет собой радикально отличающийся сплав, сочетающий исключительную коррозионную стойкость и ударную вязкость обычной аустенитной нержавеющей стали с повышенным уровнем твердости, что позволяет ей хорошо работать в качестве материала для лезвий ножей. В отличие от традиционных сталей на углеродной основе, в H-1 используется азот, чтобы создать стальные свойства. Азот, как и углерод, представляет собой небольшой атом и обладает аналогичной способностью влиять на изменения в ферритной структуре железа. Однако, в отличие от углерода, он не увеличивает уязвимость стали к коррозии».
Здесь они описывают природу h2 как аустенитной нержавеющей стали с твердостью выше обычной. Однако затем они объясняют это тем, что h2 имеет добавку азота. Однако это не совсем точно. h2 имеет содержание азота, указанное как 0,1%. Если бы это действительно было содержание азота, то оно вносило бы небольшой вклад в жесткость. Тем не менее, это довольно низкое количество азота в любом случае. Сталь с 0,1% азота не достигла бы уровня твердости ножевой стали. Даже максимальные количества углерода (0,15%) и азота (0,1%) сделают h2 по существу «мягкой» сталью, а не инструментальной сталью. Вместо этого именно холодная обработка превращает структуру в мартенсит, что придает ей более высокую твердость, а не азот. На самом деле существуют аустенитные нержавеющие стали с повышенным содержанием азота, чтобы частично заменить содержание никеля для стабилизации аустенита. Это «200 серия» аустенитных нержавеющих сталей. Азот не увеличивает твердость, и эти стали в их типичном виде являются аустенитными и не обладают высокой твердостью. Но также типично для аустенитных нержавеющих сталей иметь максимально допустимое содержание углерода и азота, особенно углерода, потому что этот элемент может привести к образованию карбида и снижению коррозионной стойкости.
Но где-то часть «max» спецификации h2 для C, N и Mn была утеряна, что, по-видимому, привело к некоторой путанице в отношении природы стали.
Фосфор, сера и старение
«Помимо азота, уникальный состав сплава H-1 также включает хром, марганец, молибден, никель, фосфор и серу. Этот точно настроенный рецепт элементов позволяет подвергать их дисперсионному твердению во время производства. В этом процессе, также называемом возрастным упрочнением, используется контролируемое нагревание для повышения предела прочности и предела текучести материала. Однако настоящий секрет твердости H-1 заключается в превращении остаточного аустенита в твердый мартенсит как в процессе прокатки стали, так и в последующей обработке материала для создания готовых лезвий».
Здесь в статье упоминается, что именно холодная прокатка приводит к более высокой твердости h2, поэтому я не имею в виду, что Spyderco совершенно неправильно понимает природу стали. Однако это еще один случай «максимума» состава, поскольку фосфор и сера упоминаются как часть «точно настроенного рецепта». Фосфор и сера являются примесями в стали. Есть определенные стали, в которые для обрабатываемости добавляется сера, но h2 не входит в их число. Сталелитейная компания сообщает Spyderco о количестве фосфора и серы, но это просто для того, чтобы показать, в какой степени компания гарантирует максимальное содержание этих элементов. Они не добавляются для дисперсионного твердения/старения. Упрочнение при старении производится на стали после завершения ее холодной прокатки. Это делается путем нагревания стали до промежуточной температуры и образования некоторых небольших выделений, которые увеличивают прочность.
Холодная обработка и шлифование
«H-1 начинается с листа толщиной 7 мм и постепенно раскатывается до требуемой конечной толщины — обычно 3,0 мм или 2,5 мм, в зависимости от модели Spyderco. Экстремальные сжимающие усилия этого процесса прокатки превращают часть аустенита стали в твердый мартенсит, увеличивая общую твердость материала без ущерба для его ударной вязкости или коррозионной стойкости. Механические процессы, используемые для придания формы и шлифовки готового лезвия, дополнительно повышают его твердость за счет избирательного превращения дополнительного аустенита в мартенсит. В результате получается лезвие с превосходной режущей кромкой, невероятно прочное и гибкое, а также чрезвычайно устойчивое к коррозии».
Интересно, что Spyderco сообщает о степени холодной обжатия, которую видит h2, которая составляет 57-64% в зависимости от конечной толщины заготовки. В статье также упоминается дальнейшее образование мартенсита во время заточки ножей, что я ранее высказывал скептически. Когда компания Sandvik измерила микротвердость ножа h2, они обнаружили немного более низкую твердость вблизи кромки (~55 Rc), где произошло большее шлифование.
Компания Sandvik обнаружила падение твердости рядом с кромкой ножа h2
Логистические проблемы с h2
«Не секрет, что пандемия COVID-19 оказала далеко идущее влияние на все аспекты мировой промышленности и экономики. Являясь третьим по величине производителем стали в мире, Япония особенно сильно пострадала и была вынуждена реструктурировать свою сталелитейную промышленность. Одним из последствий этого изменения является то, что H-1 больше не будет производиться. Однако там, где есть вызов, есть и возможности. Благодаря тесному сотрудничеству с нашими партнерами-производителями в Японии компания Spyderco помогла разработать новую сверхкоррозионностойкую сталь с соответствующим названием H-2.
Проще говоря, H-2 использует проверенный временем состав сплава и производственные процессы H-1 и совершенствует их еще больше. В результате получается сталь, которая сохраняет все исключительные качества оригинала, но при этом легко обрабатывается».
Здесь нет полной конкретики относительно того, был ли h3 разработан для облегчения производства оригинальной сталелитейной компанией (Myodo) или новая разработка была сделана вместе с новым производителем, потому что Myodo больше не могла производить больше h2 . Упоминание «партнеров-производителей» наводит меня на мысль, что на смену Myodo нужен был новый производитель.
Поэлементный анализ
Затем в статье приводится разбивка элементных изменений между h2 и h3, которые мы можем обсудить: карбидов и увеличивает уязвимость стали к коррозии. Уменьшение количества углерода в H-2 еще больше снижает этот риск и, следовательно, помогает повысить его коррозионную стойкость.

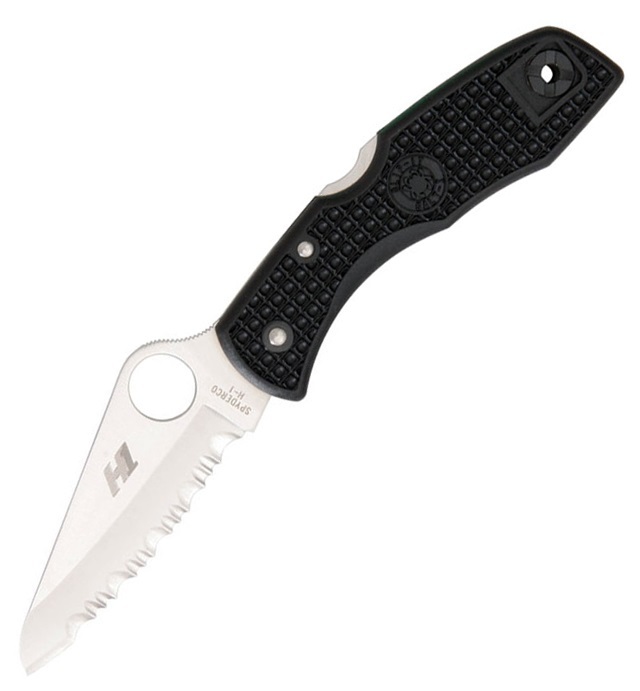
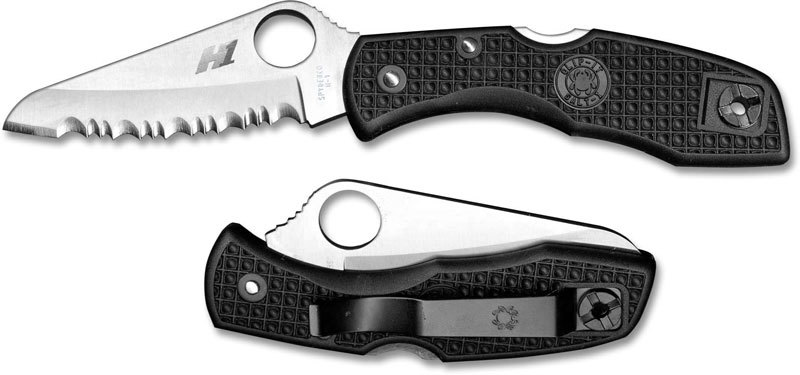
Комментарии выше – это то, что Spydero сообщил об изменениях в составе. Некоторые из этих описаний того, что элементы делают в стали, несколько не связаны со сталью, но я не хочу повторять их все. Например, сера указана как добавленная для более высокой обрабатываемости, но также указано, что ее содержание составляет 0,001%, что является чрезвычайно низким уровнем, для достижения которого сталелитейная компания должна использовать специальные производственные процессы. Они явно не специально добавили. Таким образом, нет никаких причин упоминать об улучшении обрабатываемости, поскольку для этой цели ничего не добавляется. Иногда я думаю, что разговоры о влиянии различных элементов могут внести путаницу, а не упростить вещи, поэтому я несколько критически отношусь к этому. Я писал об опасности такого обсуждения стальных элементов в этой статье о статьях с рейтингом стали. Но это обычный способ обсуждения элементов стали даже многими металлургами, поэтому я не могу слишком критиковать.
Углерод и азот
Другая проблема с элементами, описанными выше, заключается в том, что для h2 указаны диапазоны, в то время как для h3 указан очень конкретный процент. Производитель стали не может гарантировать 13,73% хрома и 2,63% кремния в каждой плавке h3. Они имеют некоторый внутренний диапазон состава сплава. Иногда общедоступный диапазон составов шире «фактического» диапазона, допустимого производителем. Так в статье написано, что углерод уменьшился с 0,15 до 0,09%, но измерение h2 по Sandvik составило 0,10% углерода. Так что вполне возможно, что содержание углерода вообще не изменилось. Они используют методы, аналогичные h2, для достижения относительно низкого содержания углерода, чтобы избежать образования карбида для хорошей коррозионной стойкости. То же самое с азотом, содержание которого описывается как сниженное с 0,10 % до 0,06 %, но опять же это аналогично измерению Sandvik 0,05 % с h2. Это максимальные допустимые значения для h2 (макс. 0,15% углерода и макс. 0,1% азота) и конкретные измеренные значения для h3 (0,09% углерода и 0,06> азота). Поэтому я не думаю, что содержание азота действительно уменьшилось. По крайней мере, я думаю, мы можем сказать, что углерод и азот очень похожи между h2 и h3.
Хром
Диапазон значений h2 составляет 14–16 %, а значение h3 составляет 13,73 %. Вероятно, наиболее вероятно, что содержание хрома составляет 13,5 или 14% для h3 с некоторыми допустимыми пределами, например, 13-15% хрома. Это может немного снизить коррозионную стойкость h3, но, вероятно, это компенсируется повышенным содержанием молибдена. Интересно, что когда Sandvik измерил содержание хрома h2, оказалось, что его содержание составляет всего 13,8%. Я не уверен, была ли это особенно бедная хромом теплота h2, какая-то ошибка измерения или и то, и другое.
Медь
Описано добавление 0,17% меди. Однако это относительно низкий уровень меди, и неясно, действительно ли это намеренное добавление. Нержавеющая сталь и инструментальная сталь обычно изготавливаются из переработанной стали, которая содержит некоторое количество меди. Относительно вероятно, что сталелитейная компания просто сообщила о полученном уровне меди, а не заявила о прибавке.
Марганец
h2 указан как имеющий 2% Mn, однако для многих аустенитных нержавеющих сталей характерно максимальное содержание 2% Mn. И Sandvik измерил Mn h2 как около 1%, что имеет смысл. Тем не менее, это по-прежнему означает, что h3 имеет более низкое содержание Mn около 0,3%, что является более типичным уровнем, используемым для ухода за серой. Сульфид марганца менее вреден для стали, чем сульфид железа. Марганец может частично заменить более дорогой элемент никель для стабилизации аустенита в этих типах сталей.
Молибден
Содержание Mo увеличено с ~1% в h2 до ~2,25% в h3. Молибден особенно хорош для улучшения «сопротивления точечной коррозии» в соленой воде. Он укрепляет слой оксида хрома в нержавеющих сталях для повышения коррозионной стойкости. Это помогает поддерживать коррозионную стойкость за счет снижения содержания хрома и помогает в условиях соленой воды.
Никель
Содержание никеля также было увеличено с ~7% до ~8,25%. Это более типичное количество для аустенитных нержавеющих сталей, хотя это представляет определенный интерес, поскольку содержание никеля, вероятно, было уменьшено в h2 по сравнению с другими сталями, чтобы обеспечить его превращение в мартенсит во время холодной прокатки.
Кремний
Содержание кремния снижено с ~3,75% до ~2,5%. В статье о h2 я отметил, что это странно высокое значение для кремния, и, возможно, оно было добавлено, потому что кремний обладает высоким упрочняющим эффектом. Поэтому будет интересно посмотреть, приведет ли это уменьшение содержания кремния к снижению твердости h3 по сравнению с h2. Кремний также является сильным «стабилизатором феррита», и на микрофотографиях h2, сделанных Sandvik, было обнаружено некоторое количество феррита. Феррит представляет собой мягкую фазу в стали (железо при комнатной температуре полностью состоит из феррита) и не очень желателен в стали с h2. Уменьшение содержания Cr и Si и увеличение содержания Ni вполне могло быть сделано для того, чтобы избежать феррита.
Светло-серые «прожилки» феррита в h2
M D30 Температура
Все эти изменения в составе также влияют на стабильность аустенита и, следовательно, на то, насколько легко он превращается в мартенсит при холодной прокатке. Температура M D30 несколько ниже с h3 в соответствии с уравнением, но несколько выше в соответствии с JMatPro, программным пакетом, который прогнозирует поведение стали. Похоже, что они сбалансировали состав, чтобы сохранить аналогичные характеристики трансформации между h3 и h2 во время холодной прокатки.
Как сравнить свойства h2 и h3?
Конечно, без измерения свойств двух сталей мы можем только строить догадки. Но мы можем сделать несколько общих утверждений.
Коррозионная стойкость
Я думаю, что уменьшение содержания Cr с увеличением содержания Mo, вероятно, приводит к одинаковой коррозионной стойкости двух материалов, но, возможно, к улучшению с h3. Это зависит от конкретной среды; Мо особенно хорошо помогает, например, в соленой воде.
Вязкость
Прочность h2 высокая из-за относительно низкой твердости и полного отсутствия карбидов. Карбиды представляют собой твердые, хрупкие частицы, которые повышают износостойкость, но снижают ударную вязкость. Таким образом, можно было бы ожидать, что h3 будет таким же, потому что в нем отсутствуют карбиды, как и в h2. Большинство других сталей для ножей содержат карбиды для повышения износостойкости, но они снижают ударную вязкость этих сталей.
Износ кромки
Когда дело доходит до удержания кромки от износа, отсутствие карбидов в классах h2 и h3 означает, что это в значительной степени зависит от твердости стали. h2 имеет низкую износостойкость, потому что карбидов нет, а h3 останется прежним.
Твердость и деформация краев
Сопротивление деформации краев контролируется прочностью, которая сильно коррелирует с твердостью. Как упоминалось выше, более высокая твердость также способствует износостойкости. Таким образом, это будет большой вопрос с h3, достигнет ли он того же уровня твердости, что и h2. Я полагаю, что они бы не использовали h3, если бы он не достиг такого же уровня твердости. Но, возможно, уменьшение на 1-2 Rc все же будет считаться приемлемым, я не знаю. Как я упоминал в разделе о M D30 , я ожидаю, что мартенситное превращение во время холодной прокатки будет сходным между h2 и h3, но снижение содержания Si может привести к снижению твердости. Мне интересно посмотреть, где заканчивается твердость ножей h3.
Выводы и резюме
Развитие h3, по-видимому, произошло по необходимости из-за доступности, а не необходимости улучшения его свойств, хотя это, конечно, не означает, что свойства нельзя улучшить.