Сталь и медь: Медь — Сталь — Медь « Калужский завод по обработке цветных металлов
alexxlab | 02.04.2023 | 0 | Разное
Медь — Сталь — Медь « Калужский завод по обработке цветных металлов
ТУ 1881-003-75479902-2005 Ленты многослойные марки МСтМ. Технические условияОписаниеМногослойная биметаллическая лента марки МСтМ, изготавливается из низкоуглеродистой стали, плакированной с двух сторон медью.
Состав- Основа – низкоуглеродистая качественная сталь марки 08Ю с химическим составом по ГОСТ 9045.
- Покрытие – медь марки М1 с химическим составом по ГОСТ 859.
Толщина плакирующего слоя h2 и h3 является одинаковой для обеих сторон и составляет от 4 до 6% от толщины готовой ленты. По требованию Потребителя толщина плакирующего слоя может быть до 10% на сторону.
Классификация и сортаментПо состоянию материала:
- мягкое – М
- дрессированное — Д
- полутвёрдое – П
- твёрдое – Т
По виду кромок:
- с обрезной кромкой – О
- без обрезной кромки – Н
Сорт | Толщина H, мм | Допуск по толщине, мм | Ширина B, мм | Допуск по ширине, мм | Длина, мм | Внутренний диаметр рулона Øвнутр.![]() | Масса рулона, кг |
Лента | 0,10 – 0,80 | от (±0,005)до (±0,03) | 6 – 60 | (±0,2) | немерная | 80 / 100 / 200 /300 / 400 | 10 – 100 |
60 – 220 | от (±0,2)до (±0,3) | 50 – 500 | |||||
0,81 – 1,50 | от (±0,03)до (±0,035) | 20 – 60 | (±0,2) | немерная | 300 / 400 / 500 | 10 – 100 | |
60 – 220 | от (±0,2)до (±0,3) | 50 – 500 | |||||
Полоса | 0,50 – 1,50 | от (±0,02)до (±0,035) | 50 – 220 | от (±0,2)до (±0,3) | 1000 – 2000 | — | — |
Для лент с необрезной кромкой допуск по ширине составляет (±1,0) мм.
Возможно изготовление других типоразмеров по согласованному допуску.
Состояние ленты | Временное сопротивление разрыву σB, МПа | Относительное удлинениеδ, % |
Мягкое (М) | 250 ÷ 380 | ≥32 |
Дрессированное (Д) | 280 ÷ 400 | ≥26 |
Полутвёрдое (П) | 290 ÷ 430 | ≥10 |
Твёрдое (Т) | 370 ÷ 510 | ≥4 |
Для производства изделий электротехнической и автомобильной промышленности.
Технология сварки меди и её сплавов со сталью
Обычно сваривают медь со сталью в стыковых соединениях. Швы в таком случае могут быть наружными или внутренними. Выбор зависит от типа и назначения конструкции.
Соединять сталь и латунь лучше всего с помощью газовой сварки. Для соединения стали и красной меди используют электродуговую сварку электродами. Также качественного шва можно добиться с использованием графитовых электродов при соединении под флюсом или же газовой сваркой с помощью флюса БМ-1. Обычно при соединении латуни и стали медь используют как присадку.
Перед процедурой обязательно нужно подготовить кромки металла. При одинаковой толщине деталей подготовка осуществляется тем же способом, как и для черных металлов. Если лист металла имеет толщину менее 3 миллиметров, то разделка не требуется. Если более 3 миллиметров, то требуется скос кромок.
Если вы недостаточно зачистили место сварки или же скос кромок оказался мал, то качество шва будет плохим. Таким образом, при соединении металла с большой толщиной не нужно делать притупление при X- образной разделке.
Как осуществляется сварка меди со сталью?
На деле это довольно сложная задача. Но хороший сварщик с такой задачей все же справится. Используются такие соединения при производстве деталей химической аппаратуры. Один из встречающихся вариантов – это присоединение медного провода к стальной колодке. Показатели качества сварки таких соединений вполне достаточны для своей задачи. Для повышения прочностных характеристик медных изделий в состав вводят до 2% железа. Применять больший объем не рекомендуется, так как прочность начнет снижаться.
Для сварочных работ с помощью графитовых электродов применяется постоянный ток прямой полярности. При этом длина дуги электричества должна быть в пределах от 14 до 20 миллиметров, а напряжение от 40 до 55 вольт. Ток выбирают в зависимости от качества электрода и его диаметра. Обычно он бывает в пределах 300-550 ампер. Флюсы используются точно такие же, как для работы с медью. Их состав можно посмотреть на этой странице. Флюс следует засыпать между разделочными кромками в зону сварки.
Начинать сваривать следует слева. Самый лучший результат достигается при обработке «лодочкой». Осуществляется процесс следующим образом:
- Сначала следует нагреть кромки медного изделия угольным электродом.
- Затем происходит соединение частей в определенном положении присадочного прутка и электрода. Пруток должен быть наклонен против движения под углом 30-40 градусов к металлу. Электрод должен быть наклонен в направлении сварки под углом в 75-85 градусом.
Скорость сварки должна быть 25 сантиметров в час. Соединение меди и чугуна происходит таким же способом.
Для приваривания бронзы с низким содержанием легирующих элементов и толщиной до 1,5 миллиметра к стали до 2,5 миллиметров используется соединение внахлест. При этом используются неплавящиеся электроды из вольфрама и присадочная проволока 1.8 миллиметра. Она подается со стороны. Сама сварка осуществляется в среде аргона в автоматическом режиме. Обработка должна происходить со стороны медного элемента. Сила тока должна при этом составлять 190 ампер, скорость подачи проволоки 70 метров в час, а скорость сварки 28. 5 метров в час. При этом напряжение электрической дуги должно быть 11.5 вольт.
Для присоединения меди или латуни к стальной заготовке применяется стыковая сварка с оплавлением. Этот способ позволяет добиться разной степени оплавления кромок, при этом цветные металлы плавятся меньше. Исходя из этого делают вылеты, равные:
- 3.5 d для стали,
- 1.5 d для латуни,
- 1.0 d для меди.
Где d является диаметром стержней. Если вам требуется применить сварку встык методом сопротивления, то значения вылета должны составлять:
- 2.5 d для стали,
- 1.0 d для латуни,
- 1.5 d для меди.
Приварка шпилек
Часто возникает потребность в присоединении шпилек диаметром 8-12 миллиметров из чистой меди или её сплавов к стали, или наоборот. В таком случае используют постоянный ток обратной полярности. Флюс при этом берется довольно мелкий ОСЦ-45. Подогрев не требуется.
Шпильки из меди или латуни Л62 до 10-12 миллиметров в сечении при силе тока 400 ампер довольно хорошо присоединяются к стальным или чугунным элементам. Латунь ЛС 59-1 не применяют.
Шпильки из стали очень плохо привариваются к меди или латуни. Более-менее нормального результата можно добиться при надевании на конец стальной шпильки кольцо из меди высотой 4 миллиметра и диаметров до 8 миллиметров. Для достижения хороших результатов рекомендуется использовать электроды К-100.
Медь и сталь — в чем разница
13 января 2023 г. 13 января 2023 г. | 11:40
Медь и сталь — самые популярные материалы, используемые в строительстве, производстве и других отраслях промышленности. Правильный выбор зависит от ваших конкретных потребностей и применения, в котором вы используете материал. Давайте посмотрим на некоторые различия между медью и сталью.
Прочность и долговечность
Сталь намного прочнее меди, что делает ее идеальной для применений, связанных с большими нагрузками или требующих большей прочности. Сталь также обладает большей прочностью на растяжение, чем медь, что делает ее устойчивой к изгибу или разрушению под давлением. Для сравнения, медь более пластична и податлива, и ей можно придавать различные формы без разрушения. Это делает его отличным вариантом для приложений, требующих сложных конструкций или компонентов, которыми можно легко манипулировать.
Стоимость и доступность
При сравнении материалов только по стоимости почти всегда выигрывает сталь, поскольку в большинстве случаев она значительно дешевле меди. Однако это будет зависеть от марки стали, которую вы выберете; стали более высокого качества могут быть дороже, чем некоторые сорта меди. Кроме того, если учесть затраты на техническое обслуживание с течением времени (например, на регулярную покраску или защиту от ржавчины с помощью стали), владение стальным изделием выше, чем владение изделием из меди из-за его естественных свойств коррозионной стойкости.
Коррозионная стойкость
Медь обладает естественной коррозионной стойкостью благодаря своему оксидному слою, который образуется при контакте с воздухом или водой. Этот слой помогает защитить от дальнейшей коррозии, обеспечивая при этом привлекательную отделку, которая может прослужить много лет без дополнительного обслуживания или обработки. Сталь также обладает некоторой коррозионной стойкостью, но только при покрытии защитными слоями, такими как краска, гальваника или цинкование, и даже в этом случае она может подвергаться коррозии при воздействии агрессивных элементов с течением времени.
Медь лучше проводит электричество
Одним из основных преимуществ меди перед сталью является то, что она лучше проводит электричество. Это означает, что медь можно использовать в электротехнике, где сталь не подходит. Например, медь часто используется в электропроводке из-за ее превосходной проводимости.
Медь долговечнее стали
Еще одним преимуществом меди перед сталью является то, что она более долговечна. Это означает, что медь прослужит дольше, чем сталь, в тех случаях, когда важна долговечность. Например, медные трубы часто используются в сантехнике, потому что они менее подвержены коррозии, чем стальные трубы.
Медь имеет более низкую температуру плавления, чем сталь
Другим преимуществом меди перед сталью является более низкая температура плавления. Это означает, что медь можно использовать там, где плавится сталь. Например, медь можно использовать в электротехнике, где тепло плавит сталь.
Медь более устойчива к коррозии, чем сталь
Еще одним преимуществом меди перед сталью является то, что она более устойчива к коррозии. Это означает, что медь не будет ржаветь так же легко, как сталь. Например, медные трубы часто используются в сантехнике, потому что они менее подвержены коррозии, чем стальные трубы.
Медь немагнитна
Еще одним преимуществом меди перед сталью является то, что она немагнитна. Это означает, что он не будет притягиваться к магнитам, как сталь. Это может быть важно в приложениях, где присутствуют магниты, например, в электродвигателях.
Заключение:
Выбирая между медью и сталью для ваших нужд, учитывайте все факторы, включая прочность и долговечность, стоимость и доступность, а также коррозионную стойкость, прежде чем принимать решение. В зависимости от того, что вам нужно от каждого материала — максимальная прочность или доступность — любой из них может стать отличным выбором для вашего проекта! В конечном счете, оба материала обладают уникальными преимуществами, поэтому вам придется взвесить все варианты, прежде чем выбрать какой-либо из них, чтобы получить наилучший возможный результат для ваших инвестиций!
Абхишек Модак
Абхишек — опытный блогер и отраслевой эксперт, который делится своими взглядами и знаниями по различным темам. Своими исследованиями Абхишек предлагает ценные идеи и советы профессионалам и энтузиастам. Подпишитесь на него, чтобы получить экспертные советы о последних тенденциях и разработках в металлургической промышленности.
Высокопрочная медная сталь для железнодорожных цистерн к мостам
Применение меди в металлургии меди и медных сплавов
Адаптировано из статьи С. Вайнмана, М. Э. Файна и С. П. Бхата
Аннотация | Введение | Результаты | Резюме | Мостовое приложение | Авторы | Ссылки
Аннотация
Разработка сталей с более высокой прочностью и более высокой ударной вязкостью для применения в вагонах-цистернах в течение многих лет была целью улучшения общих характеристик железнодорожных цистерн. За последние десять лет в результате совместных исследований Северо-Западного университета и Ispat-Inland Inc. марки производятся путем воздушного охлаждения после горячей прокатки. Марка NUCu-60 (сверхпрочная криогенная сталь) имеет предел текучести 415 МПа (60 фунтов на квадратный дюйм) и замечательную ударную вязкость при криогенных температурах; более 350 Дж (264 футо-фунта) до –79°С (–110°F). Марка NUCu-70 имеет предел текучести не менее 485 МПа (70 тысяч фунтов на кв. дюйм). Состав марки NUCu-100 такой же, как у NUCu-70. Более высокая прочность достигается закалкой от температуры аустенизации и старением. Обсуждаются механические свойства, а также коррозионная стойкость и сварочные свойства этих сталей. Наконец, сообщается о недавно построенном мосте из этого сплава в Иллинойсе.
Введение
В настоящее время большинство корпусов вагонов-цистерн изготавливается из углеродисто-марганцевой стали TC128B с пределом текучести 50 тысяч фунтов на квадратный дюйм, содержащей более 0,25% углерода и 1% марганца. Эта сталь имеет относительно высокий параметр свариваемости в углеродном эквиваленте. Кроме того, сталь имеет предельные характеристики вязкости разрушения при низких температурах. Для применения в вагонах-цистернах ищут новую, более легко свариваемую сталь с более высокой прочностью и более высокой вязкостью разрушения. Серия высокопрочных сталей (как описано ниже), удовлетворяющих этим требованиям, была разработана в Северо-Западном университете. Это отличные кандидаты на замену стали TC128B в корпусах вагонов-цистерн. Эти стали имеют гораздо более низкое содержание углерода. Упрочнение достигается за счет осаждения меди при охлаждении на воздухе при горячей прокатке. Ni добавляется для предотвращения горячеломкости во время горячей прокатки. Nb и Ti добавляются для контроля размера зерна во время горячей прокатки и сварки. Поскольку стали NUCu в основном ферритные, они не содержат легирующих добавок для повышения прокаливаемости. Первоначальные исследования были проведены с лабораторными плавками.
Более высокая прочность стали позволяет использовать более тонкие секции для снижения веса. Значительно улучшенная свариваемость по сравнению с высокоуглеродистыми сталями должна упростить и снизить стоимость изготовления. Версии стали 60 и 70 ksi используются в горячекатаном состоянии, что снижает затраты на нормализацию.
Результаты
Механические свойства
NUCu-60, как показано в Таблице I, содержит больше Ti, который связывает междоузлия. Плавка стали NUCu-60 была выплавлена в вакууме и подвергнута горячей прокатке в листы толщиной 0,5 дюйма в Ispat Inland. Стали марок NUCu-70 и NUCu-100 были отлиты на Oregon Steel Mills и подвергнуты горячей прокатке на заводе US Steel Company Gary Works. Состав также указан в Таблице I . В то время как предел текучести 70-80 тысяч фунтов на квадратный дюйм был достигнут в горячекатаных и охлаждаемых воздухом стальных листах толщиной до 2 дюймов, для достижения предела текучести 100 тысяч фунтов на квадратный дюйм требовались закалка в воде и старение.
Круглые образцы на растяжение с калибровочным сечением 50,8 мм (2 дюйма) (стандарт ASTM E 8) и образцы Шарпи (стандарт ASTM E 23) подвергали механической обработке в продольном направлении от четверти толщины пластин и испытывали. Было протестировано несколько образцов с очень небольшими отклонениями. Механические свойства сталей приведены в таблице II . Таблица III показывает поглощенную по Шарпи энергию удара сталей.
С | Мн | Си | Медь | Ni | Ти | № | |
NUCu-60 (Испат-Внутренний) | 0,03 | 0,53 | 0,52 | 1,29 | 0,52 | 0,10 | 0,06 |
NUCu-70 и NUCu-100 (OSM/USS) | 0,06 | 0,78 | 0,38 | 1,35 | 0,84 | 0,03 | 0,38 |
Предел текучести МПа (ksi) | UTS МПа (ksi) | Удлинение (%) | |
---|---|---|---|
413(60) | 551(80) | 27 | |
NUCu-70-горячекатаный | 503 (73) | 567 (82) | 32 |
NUCu-70-горячекатаный-нормализованный | 461 (67) | 546 (79) | 36 |
НУКу-100 | 712 (103) | 780 (113) | 26 |
NUCu-60 Горячекатаный (Ref) | NUCu-70 (горячекатаный) | NUCu-70 (горячекатаный, нормализованный) | NUCu-100 | |
---|---|---|---|---|
29 (+07090 24) | > 360 (>264) | |||
0 (+32) | > 360 (>264) | 206 (151) | 257 (188) | 132 (97) |
-12 (+10) | > 360 (>264) | 202 (148) | 255 (187) | 115 (84) |
-23 (-10) | > 360 (>264) | 192 (141) | 242 (177) | 89 (65) |
-40 (-40) | > 360 (>264) | 161 (118) | 233 (171) | 64 (47) |
-62 (-80) | > 360 (>264) | |||
-79 (-110) | > 360 (>264) |
Испытание на ударное разрушение стали NUCu-60 показало ее замечательную динамическую вязкость разрушения; Образцы Шарпи не разрушались до -79°C (-110°F), они изгибались в аппарате Шарпи при взмахе молотка.
Образцы стали NUCu-70, испытанные в горячекатаном состоянии, имели предел текучести 503 МПа (73 тысячи фунтов на квадратный дюйм) и UTS 567 МПа (82 тысячи фунтов на квадратный дюйм). Удлинение до разрушения относительно велико, 32%. Поглощенная энергия разрушения по Шарпи также высока, 161 Дж (118 фут-фунтов) при -40°C, что намного выше, чем требуется для строительства или применения в цистернах. Нормализация этой стали на 900 ° C увеличивает энергию Шарпи, однако снижает предел текучести до 461 МПа (67 тысяч фунтов на квадратный дюйм) и UTS до 546 МПа (79 тысяч фунтов на квадратный дюйм). Сталь NUCu-70 более чем подходит для использования в вагоностроении в горячекатаном состоянии и с воздушным охлаждением, поскольку прочность и поглощенная по Шарпи энергия удара значительно превышают требования для такого применения.
Когда сталь NUCu с пределом текучести 70 тысяч фунтов на квадратный дюйм была закалена от 900°C и состарена в течение 1 часа. при 525 °C предел текучести увеличился до 712 МПа (103 тысячи фунтов на квадратный дюйм), а предел текучести до 780 МПа (113 тысяч фунтов на квадратный дюйм) с удлинением до разрушения 26 %. Поглощенная энергия разрушения по Шарпи ниже, чем у стали NUCu-70, 64 Дж (47 ft-lb) при -40°C, что является приемлемым значением для высокопрочной стали при такой низкой температуре
Сварка
Из-за очень низкого уровня углерода и отсутствия элементов, используемых для повышения прокаливаемости, таких как хром и молибден, стали NUCu имеют очень низкий эквивалент углерода при сварке. На рис. 1 показана диаграмма Гравилля для прогнозирования свариваемости. Здесь концентрация углерода представлена в зависимости от углеродного эквивалента, рассчитанного как CE = C+(Mn+Si)/6 + (Ni+Cu)/15 + (Cr+Mo+V)/5. Диаграмма Гравилля разделена на три зоны. В зоне I сварные швы, полученные при большинстве условий сварки, не подвержены растрескиванию, в зоне II сварка требует предварительного и последующего нагрева для предотвращения растрескивания, а в зоне III зона термического влияния (ЗТВ) чрезвычайно подвержена растрескиванию. Как видно из Рисунок 1 , сталь NUCu с низким содержанием углерода и углеродным эквивалентом находится глубоко в зоне I и, следовательно, не требует предварительного и последующего нагрева для сварки, сталь TC128B для цистерн с более высоким содержанием углерода и более высоким углеродным эквивалентом попадает в зону I. Зона II близка к границе с зоной III, что свидетельствует о трудностях сварки и склонности ЗТВ к растрескиванию.
Рисунок 1 . Диаграмма свариваемости Graville
Ранее оценивалась сварка нескольких различных плавок стали NUCu-70 без предварительного и последующего нагрева с помощью процесса под флюсом (SAW), а также с помощью ручного процесса в условиях строительного цеха (Trinity Bridge и Arlington Construction Company). Использовались соответствующие расходные материалы. Зона хрупкого термического влияния не образовалась. Сталь также была сварена в сварочной лаборатории Северо-Западного университета без предварительного или последующего нагрева с использованием проволоки LINCOLWELD LA100 и флюса LINCOLNWELD 880M в процессе SAW. Были использованы два значения тепловложения: 1,4 кДж/мм (35 кДж/дюйм) и 3,9 кДж/мм.кДж/мм (98 кДж/дюйм). Таблица IV показывает, что энергия удара, поглощенная по Шарпи, для сварных образцов, включая зону термического влияния, очень высока для «низкой» тепловложения и превышает стандартные требования для высокой тепловложения.
Подводимая теплота кДж/мм (кДж/дюйм) | Поглощенная энергия удара по Шарпи (Дж (фут-фунт)) при температуре испытаний, °C (°F): | |||
---|---|---|---|---|
24 (75) | -12 (10) | -23 (-10) | -40 (-40) | 241 (176) | 242 (177) | 224 (164) | 187 (137) |
3,9 (98) | 206 (151) | 70 (51) | 79 (58) | 52 (38) |
Повторные испытания G-BOP, проведенные в Центре исследований и технологий стали США с использованием тепловложения 1,4 кДж/мм (35 кДж/дюйм) и низкого содержания водорода AWS E7018 и E9Электроды 018 без предварительного и последующего нагрева не показали трещин металла сварного шва в сварных швах или опорных плитах.
Компания Stupp Bridge, Боулинг-Грин, Кентукки, недавно провела квалификационные испытания процедур (PQR) SAW без предварительного и последующего нагрева с использованием электродов Lincoln LA85 и флюса MIL800-HPNi. Подвод тепла составил 2,36 кДж/мм (60 кДж/дюйм). В испытаниях на разрушение при -30°C (-22°F) средняя энергия удара, поглощенная по Шарпи, составила 124 Дж (91 фут-фунт). Требование стандарта Американского общества сварщиков составляет 34 Дж (25 футо-фунтов) при этой температуре.
Коррозионная стойкость
Медь значительно улучшает коррозионную стойкость стали в морской и внутренней среде 6, 7 , а высокое содержание меди в стали NUCu эффективно снижает потерю веса в ускоренных испытаниях на атмосферостойкость.
На рис. 2 сравнивается потеря массы стали NUCu с потерей веса стали A36 и некоторых атмосферостойких сталей в стандартных ускоренных испытаниях SAE J2334, проведенных Таунсендом в Bethlehem Steel Corporation 7 . Потеря толщины стали A36 была на 133% больше, чем у стали NUCu. Потери толщины атмосферостойкой стали A588 и стали HPS70W A709 были на 69% больше, чем у стали NUCu. С использованием существующих баз данных были установлены индексы коррозии, и индекс для стали NUCu намного ниже, чем для любой другой конструкционной стали 6, 7, 8 .
Рисунок 2 . Коррозионная потеря конструкционной и атмосферостойкой стали
(данные ускоренных автомобильных испытаний по стандарту SAE J2334, проведенных в Bethlehem Steel Corporation компанией Townsend 7 )
Эти же марки стали были покрыты эпоксидной краской Carboguard 890 (фирма Carboline), нанесены царапины и затем испытаны в камере соляного тумана (D1654-92 Standard 9 , 49,97 г/л солевого раствора). Степень коррозии измеряли после выдержки при 35°C в течение 3 недель. Результаты испытаний показаны на рис. 3 . Ширина областей коррозии, прилегающих к царапинам, была измерена и показана на рис. 4 . Вновь сталь NUCu демонстрирует наилучшую коррозионную стойкость; корродированные поверхности в местах царапин A36, A588 и HPS 70W A709стали были на 93%, 52% и 54% соответственно шире, чем у стали NUCu.
Рисунок 3 . Окрашенные стальные панели после 3 недель выдержки при 35°C в камере соляного тумана
(слева направо: A36; A588; ASTM HPS 70W; сталь NUCu)
Рисунок 4 . Ширина коррозионных царапин на окрашенных стальных панелях через 3 недели при температуре 35°C в камере соляного тумана
Резюме
Информация, представленная в этом документе, показывает, что NUCu 70, в частности, имеет преимущества перед сталью TC128B, используемой в настоящее время в производстве цистерн. Более высокая прочность должна привести к снижению веса. Более высокая ударная вязкость разрушения снижает риск хрупкого разрушения, особенно при низких температурах. В то время как требуемое легирование меди и никеля увеличивает стоимость стали, нормализация не требуется; Сталь NU-Cu используется в горячекатаном состоянии. Гораздо лучшая свариваемость, как показано положением на диаграмме Гравилля, должна значительно снизить затраты на изготовление. Предварительный нагрев или последующий нагрев могут быть устранены. Плюсом также является лучшая атмосферостойкость и коррозионная стойкость. Если важным фактором является выдающаяся стойкость к ударному разрушению при очень низких температурах, Supertough NUCu 60 является кандидатом. Для приложений с еще более высокой прочностью NUCu 100 может быть предпочтительным сплавом.
Мостовое приложение
Департамент транспорта Иллинойса (IDOT) недавно объявил о завершении строительства нового моста в Лейк-Вилла, Лейк-Каунти (Иллинойс), построенного из инновационной высокопрочной стали, разработанной инженерами-исследователями Северо-Западного университета.
Рисунок 5 . Новый мост на Лейк-Вилле в Лейк-Каунти, построенный из медной стали, разработанной в Северо-Западном университете
Около 500 тонн стали из медного сплава, известной как высокоэффективная конструкционная сталь ASTM A 710 Grade B, было использовано при строительстве 430-футового пролета, по которому проходит Illinois Rt. 83 над путями Канадской национальной железной дороги. «IDOT в восторге от возможностей, предоставляемых этим новым типом экономичной высокопроизводительной стали, разработанной прямо здесь, в Иллинойсе», — сказал секретарь IDOT Тимоти В. Мартин. «Эта сталь не только прочная, жесткая и простая в изготовлении, но и противостоит погодным условиям лучше, чем обычная сталь, а это означает, что ее не нужно красить. Это упрощает строительство и значительно снижает долгосрочные затраты на техническое обслуживание».
IDOT находится в процессе подачи заявки в Американское общество по испытаниям и материалам (ASTM) и Американскую ассоциацию государственных служащих автомобильных дорог и транспорта (AASHTO) на определение этой стали в качестве стандарта для строительства мостов. Единственное предыдущее использование было при восстановлении моста Поплар-стрит через реку Миссисипи в районе Метро-Ист.
Сталь имеет прочность 70 000 фунтов на квадратный дюйм (psi) по сравнению с 50 000 psi у обычно используемой конструкционной стали. Его также легко сваривать, и испытания показали, что он обладает высокой ударной вязкостью при низких температурах. Кроме того, высокое содержание меди придает сплаву гораздо лучшую стойкость к атмосферной коррозии, чем у других высокопроизводительных сталей.
«Мы разработали эту сталь девять лет назад, и ее применение ожидалось уже давно», — сказал Моррис Э. Файн, почетный профессор материаловедения и инженерии Северо-Западного университета, разработавший новый сплав вместе со своим коллегой, профессором-исследователем Семеном Вайнманом и при ключевой поддержке Северо-Западного института инфраструктурных технологий (ITI). «Эта сталь экономически эффективна, потому что ее переработка дешевле, чем у конкурирующих конструкционных сталей той же прочности, у нее лучшая устойчивость к атмосферным воздействиям и ее легче сваривать».
«Мы рады видеть, что наша сталь используется в этом новом мосту, и надеемся, что сталь будет использоваться в других мостах в Иллинойсе, а также в других штатах», — сказал Вайнман, профессор-исследователь материаловедения и инженерии в Северо-Западном университете.
«Уже более полувека профессор Файн является одним из выдающихся мировых лидеров в области материаловедения, — сказал Дэвид Шульц, директор ITI. «Институт инфраструктурных технологий рад и горд тем, что поддержал его команду в разработке высокопрочной стали, используемой в мосте Route 83. Мы надеемся и дальше помогать ему «расширять границы» все более прочных и экономичных сталей».
Мост Лейк-Вилла был построен компанией Dunnet Bay Co. по контракту на сумму 5,75 миллиона долларов. Проектировщиком моста была компания Graef Schloemer and Associates of Chicago. Сталь была произведена компанией Mittal Steel USA в Коутсвилле (Пенсильвания) и изготовлена на заводе Industrial Steel Construction в Гэри (Индиана). IDOT получила федеральные средства для оплаты стали через Федеральный фонд исследований инновационных мостов.
Надзор за проектом для IDOT осуществлял инженер-резидент Марио Бьондолилло. Ключевую роль в проекте для IDOT также сыграл Крис Хахин, главный исследователь и инженер-металлург отдела. По оценкам IDOT, отказ от покраски стали позволил сэкономить 300 000 долларов. Новый мост заменил сооружение 19 века.29. Строительство велось поэтапно, чтобы обеспечить движение транспорта по ул. 83.
Авторы
Проф. Семен Вайнман и проф. Моррис Э. Файн
Проф. С. Вайнман и проф. М. Э. Файн: Факультет материаловедения и инженерии, Северо-Западный университет, 2220 Campus Drive, Evanston, IL 60208-3108.
S.P. Bhat : Ispat-Inland, Отдел исследований и разработок Ispat Inland, 3001 East Columbus Drive, East Chicago, IN 46312.
Ссылки
1. M.E. Fine et al., International Symposium on Low Carbon Steel for 90s (Cincinnati, OH, ASM International, 1993), 511.
2. S. Vaynman et al., Materials for the New Millennium, Proceedings of the Fourth Materials Engineering Conference (New York, NY, ASCE, 1996), 1551.
3. С. Вайнман, И. Усландер и М. Э. Файн, Труды 39-й конференции по механической обработке и обработке стали (Индианаполис, Индиана, МКС, 1997), 1183.
4. С. Вайнман, М. Е. Файн, Международный симпозиум по стали для сборных конструкций , (Цинциннати, Огайо, ASM International, 1999), с. 59.
5. С. Вайнман и др., Микролегированные стали 2002 (Чикаго, Иллинойс, ASM International, 2002), 43.
6. С. Вайнман и др., «Оценка атмосферной коррозии высокопрочных низколегированных сталей», Металл. Trans ., 28A(1997), 1274-1276.
7. Х. Таунсенд, пенсионер из Bethlehem Steel Company, частное общение.
8. Стандарт ASTM G 101-01 для оценки стойкости низколегированных сталей к атмосферной коррозии.
9. ASTM D 1654-92 Стандартный метод испытаний для оценки окрашенных образцов или образцов с покрытием.
Также в этом выпуске:
- Высокопрочная медная сталь для железнодорожных цистерн к мостам
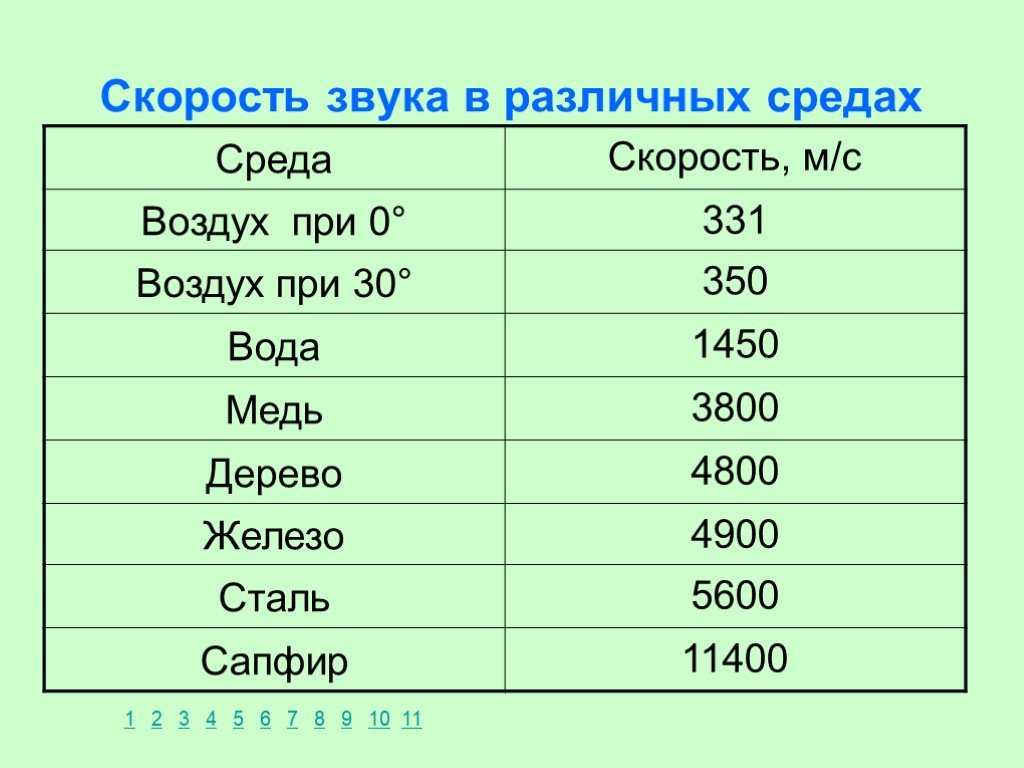