Стали ферритные мартенситно: Мартенситно-ферритные стали
alexxlab | 29.12.2022 | 0 | Разное
Мартенситно-ферритные стали
Сеть профессиональных контактов специалистов сварки
Мартенситно-ферритные стали. К этому классу относят стали с частичным γ→α(м)-превращением. Термокинетическая диаграмма у этих сталей состоит из двух областей превращения. При температурах >600оС при низкой скорости охлаждения возможно образование ферритной составляющей структуры. При больщой скорости охлаждения <400oС) наблюдается бездиффузионное превращение аустенита в мартенсит. Количество образовавшегося мартенсита зависит от содержания углерода и скорости охлаждения.
Содержание хрома в мартенситно-ферритных сталях 13 … 14 %, что оптимально по коррозионной стойкости. Такой уровень легирования хромом обеспечивает пассивацию поверхности в агрессивных средах, связанных с нефтехимическим производством; в воде высоких параметров, в том числе с борным регулированием.
Дальнейшее повышение содержания хрома практически без увеличения коррозионной стойкости сталей в указанных средах способствует формированию в их структуре значительного количества ферритной составляющей.
Мартенситно-ферритные стали находят довольно широкое применение для изготовления нефтехимической аппаратуры и энергетического оборудования (табл. 1и 2).
По свариваемости мартенситно-ферритные стали являются неудобными материалами. В связи с неизбежной подкалкой при сварке сварные соединения мартенситно-ферритных сталей склонны к образованию трещин замедленного разрушения. Кроме того, при перегреве в 3ТВ часто наблюдают трещины хрупкого разрушения.
Ударная вязкость металла в 3ТВ сварных соединений 13%-ных хромистых сталей снижается до 10 дж/см2 . В случае низкого содержания δ-феррита последующим термическим отпуском при 700о
С, способствующим распаду структур закалки и выделению карбидов, можно повысить ударную вязкость металла в 3ТВ до 50… 100 Дж/см2 При способах сварки, способствующих значительному перегреву металла в 3ТВ с образованием структуры с большим содержанием о-феррита, термический отпуск мало влияет на ударную вязкость, в результате чего сварные соединения отличаются высокой хрупкостью и не годятся для нагруженных конструкций.
Таблица 1. Мартенситно-ферритные стали: химический состав.
Марка стали | С | Si | Mn | Cr | Ni | Mo | V | S | P | прочих элементов |
15Х12ВНМФ | 0,12..0,18 | ≤0,4 | 0,5..0,9 | 11.0…13,0 | 0,4 …0,8 | 0,5 …0,7 | 0,15…0,30 | ≤0,025 | ≤0,030 | 0,7… 1,1 W |
12Х13 | 0,09..0,15 | ≤0,8 | ≤0,8 | 12,0…14,0 | – | – | Не регламен- тируется |
|||
14Х17Н2 | 16,0…18,0 | 1,5 …2,5 | ||||||||
08ХI4МФ | 0,03.![]() |
0,20…0,45 | 0,8 …1,2 | 12,0…14,0 | – | 0,2 …0,3 | 0,15…0,3 |
Таблица 2. Механические свойства хромистых мартенситно-ферритных сталей, не менее.
Марка стали | σ в, МПа | σ0,2,МПа | δ5, % | ψ,% | KCU, Дж/см2 | Примеры использования |
15Х12ВНМФ | 740 | 590 | 15 | 45 | 60 | Детали паровых, газовых, гидравлических турбин и компрессоров |
12Х13 | 590 | 410 | 20 | 60 | 100 | |
14Х17Н2 | 835 | 635 | 10 | 30 | 50 | Детали внутренних устройств оборудования АЭС |
08ХI4МФ | 450 | 300 | 22 | – | Теплообменники тепловых и атомных электростанций, облицовки хранилищ |
Эффективным способом снижения содержания ферритной составляющей в структуре хромистых сталей является легирование их углеродом и никелем.
Образование большого количества δ-феррита в структуре околошовного металла характерно для 13 … 14%-ных хромистых сталей с <0,1 % С. В участках ОШ3 сварных соединений, нагреваемых до температур, близких к температуре солидуса, количество δ-феррита в структуре может быть подавляющим. Ширина таких участков мало зависит от температуры подогрева при сварке, но возрастает с погонной энергией сварки.
Мартенситно-ферритные стали сваривают, как правило, с предварительным и сопутствующим подогревом (табл. 10.45).
Для низкоуглеродистой стали 08Х14МФ подогрев при сварке не при меняют, так как легирование карбидообразующими элементами снижает эффективное содержание углерода.
Способы сварки и применяемые для мартенситно-ферритных сталей сварочные материалы приведены в табл. 10.46.
Таблица 3. Рекомендации по тепловому режиму сварки мартенситно-ферритных сталей.
Марка стали | Температура подогрева, оС | Продолжительность хранения до термической обработки, ч | Термическая обработка |
15Х12ВНМФ | 300 | не допускается | Отпуск при 700.![]() |
12Х13 | 2 | Отпуск при 700… 720оС | |
14Х17Н2 | 150…250 | не ограничено | Отпуск при 620…640оС |
08Х14МФ | Без подогрева | Не регламентируется | Отпуск при 680… 700оС |
Таблица. Способы сварки, сварочные материалы и механические свойства сварных соединений мартенситно-ферритных сталей.
Марка стали | Способ сварки, сварочные материалы | Механические свойства сварных соединений | |
σв, МПа | KCU, Дж/см2 | ||
15Х12ВНМФ | РДС: – электроды Э-12Х11НМФ КТИ-9 |
735 | 50 |
– электроды Э-11Х15Н25М6АГ2 ЭА-395/9 | 588 | 40 | |
12Х13 | РДС: – электроды Э-12Х13 ЛМ3-1, Э-06Х13Н ЦЛ-41, ЦЛ-51 |
637 | 50 |
– электроды Э-11 Х 15Н25М6АГ2 ЭА-395/9 | 588 | 40 | |
– электроды Э-lОХ25Н13Г2 3иО-8, ЦЛ-25 | 540 | 50 | |
14Х17Н2 | РДС: электроды Э-I0ХI8Н2 АНВ-2. ![]() АДС: проволока Св-08Х 18Н2ГТ, Св-08Х 14ГНТ, флюсы АН-2бс, Оф-б, АНВ-б. АрДС: проволока Св-08Х 18Н2ГТ, Св-08Х 14ГНТ, аргон |
755 | 50 |
08Х14МФ | РДС: электроды Э-l ОХ25Н 13Г2, ЦЛ-25 |
540 | |
АДС: проволока Св-07Х25Н 13, АН-2б |
|||
АрДС: проволока Cb-04Х20Н5МББ |
490 | ||
Св-07Х25Н 13, аргон | 540 |
Copyright. При любом цитировании материалов Cайта, включая сообщения из форумов, прямая активная ссылка на портал weldzone.info обязательна.
Мартенситные и мартенситно-ферритные стали

- вольфрам;
- никель;
- молибден;
- хром.
Рассмотрение такой группы сталей напрямую связано с понятием мартенсита. Это обозначение для игольчатой микроструктуры. Она встречается в чистых металлах, которые проходят процедуру закалки. Также встретить структуру можно и в стали. Одна из отличительных особенностей металлов с такой микроструктурой – склонность к полиморфизму.
Говоря проще – мартенсит представляет собой базовый структурный компонент стали.
История открытия мартенсита связана с именем ученого Марка Мартенса. Он долго изучал различные металлические материалы, а также проблемы, связанные с их износом и накапливанием усталости в процессе использования.
При рассмотрении кристаллической решетки углеродистого раствора выясняется, что она тетрагональная. Решетка делится на составляющие, каждая из которых – это параллелепипед. Ячейка состоит их атомов железа и атомов углерода. Первые располагаются по вершинам, а вторые в центре.
Сама структура неравновесная. В ней сохраняется высокий уровень внутреннего напряжения. Однако материалу это идет только на благо – увеличивается его прочность и устойчивость к длительному использованию.
Ученые долго исследовали особенности повреждения такого типа металла в условиях нагрева. Довольно быстро выяснилось, что в процессе воздействия высоких температур происходит перераспределение атомов углерода. В результате формируются фазы цементита и феррита. В первой содержание углерода составляет 6,7%, во второй не более 0,02%.
Такого типа структура отражается на характеристиках получаемой стали. В первой фазе ячейка имеет ромбическую структуру, в то время как во второй она становится объемно-центрированной.
В ходе изучения основных параметров материала и его особенностей в использовании, удалось выделить два основных мартенсита. Понимание особенностей таких типов во многом влияет на то, как именно будет понимать сам материал. Выделяют:
Дислокационный мартенсит. В профессиональной литературе и технических текстах также можно встретить название его название как «реечного». Для того чтобы сформировать такую разновидность структурного элемента потребуется сталь трех типов – мало и среднеуглеродистая, а также высоколегированная. При нагреве такой стали до 300 °С наблюдается стремительное мартенситное образование. Привлекает внимание сама форма кристаллов мартенсита. Это рейки (отсюда название реечного), толщина которых варьируется от 0,2 до 2 мкм. При этом все кристаллы оказываются вытянуты в одну сторону. При ближайшем рассмотрении оказывается, что между рейками залегает прослойка аустенита. Однако она настолько тонкая (не превышает 20 нм), что её часто сложно заметить.
Двойниковый. Если второе название дислокационного мартенсита реечный, то двойниковый также называется пластинчатым. Образование такой сетки характерно для углеродистых и легированных сталей. Образование начинается уже при 200 °С нагрева.
Так как выше часто встречалось такое понятие, как мартенситное превращение, необходимо конкретизировать это понятие.
Особенности мартенситного превращения
Мартенситное превращение представляет особо полиморфный процесс. Когда он происходит, в составе кристалла наблюдается упорядоченное передвижение атомов или молекул. Таким образом, их положение относительно друг друга постепенно меняется. Отличаются межатомные расстояния, что становится важной характеристикой рассматриваемого процесса.
Перестройка кристаллической решетки или её деформация приводит к изменению начальной фазы. Величина деформации составляет около 10% или менее (но не больше). На этом фоне энергетический барьер оказывается малым.
Главным условием для того, чтобы превращение оказалось возможным, становится взаимодействие между нестабильной и стабильными фазами. Причем взаимодействие это должно быть упорядоченным. Обращает на себя внимание то, что низкий энергетический потенциал межфазных границ в совокупности с повышенной подвижностью, обуславливается здесь упорядоченным строением таких границ.
Это полностью объясняет то, что лишняя энергия, которая необходима для начала появления кристаллов оказывается не такой значимой, как может показаться на первый взгляд. На практике она сопоставима с энергией исходных дефектов, которые уже присутствуют в первоначальной фазе. При этом устанавливается по-настоящему высокая скорость создания мартенситных кристаллов. К слову, для создания таких кристаллов не требуется тепловой энергии, что также является одной из особенностей самого процесса.
В ходе мартенситных преобразований, проходит модификация атомного порядка компонентов. Это подразумевает постепенное перераспределение и последующее превращение. Сами характеристики кристаллических материалов изменяются, и изготовители могут воздействовать на такие характеристики, увеличивая температуру обработки или же используя набор средств механического взаимодействия с обрабатываемым материалом.
Центральные особенности сталей мартенситного типа
Как уже было сказано, мартенситные стали в своей основе – хромистые. Еще одно отличие – высокий процент содержания в них углерода. Наблюдается и ряд других примесей, определяющих будущую область использования и характеристики конкретного материала. Это молибден, вольфрам, ниобий. На этом список компонентов не ограничивается. При создании такого типа стали удается достичь не только устойчивости к коррозии, но и достаточной жаропрочности для расширения горизонта использования.
У данной разновидности продукции присутствует целый ряд особенностей, среди которых:
Устойчивость к появлению повреждений при соприкосновении с растворами щелочей. В такой ситуации, материал остается устойчивым к появлению коррозии и не изменяет своей структуры. Это наблюдается даже на фоне высокого уровня влажности. Защищенность от повреждения при воздействии высоких температур. Основное условие получение полного спектра положительных качеств использования – правильная закалка материала. Сталь требуется закалять при температуре не ниже 1050 °С. Дополнительное использование после нагрева сорбита и троостита помогает создать по-настоящему устойчивый к жару материал, не меняющий свих свойств при нагреве. Более того, такие стали отличаются способностью к прохождению самозакаливания с попутным увеличением полезных качеств. Низкая пластичность. Это свойство особенно ценно на фоне того, что материал отличается повышенной твердостью. При этом сам материал не теряет своих показателей, даже если в процессе легирования в него будут вводиться дополнительные элементы – пластичность останется на том же уровне. Устойчивость к воздействию воды. Такая особенность помогает создать материал, способный прослужить на протяжении длительного времени даже при соприкосновении с водой. Жидкость не способна разрушить внешний слой защитных материалов на стали и вызвать коррозию.
Помимо этого, при покупке стоит учитывать высокие показатели водоустойчивости, а также то, что мартенситный металл не так просто обрабатывать с использованием стандартного инструмента для подобных работ.
Особенности обработки и сварки
Одна из проблем, возникающих при использовании такой разновидности стали заключается в правильной сварке. Материал устойчивый к нагреву не так просто сваривать. Сварка возможна только после того, как материал предварительно будет нагрет. Показатели такого нагрева – от 200 до 450 °С. Оптимальный вариант метода сварки – ручная дуговая. Профессионалы рекомендуют использовать особые электроды со специальным покрытием. Также возможно применение и таких типов сварки, как электрошлаковая, под флюсом и дуговая.
Наиболее востребованные марки мартенситной стали
На данный момент в производстве используется большое количество разнообразных марок мартенситной стали. Наиболее востребованные разновидности представлены в таблице ниже.
Марка стали | Особенности состава |
20Х13 | От 12 до 14 % хрома, менее 0,8 % марганца и кремния, от 0,16 до 0,25 % углерода |
10Х12НДЛ | Никеля от 1 до 1,5 % |
18Х11МНФБ | Не более 11,5 % хрома, от 0,5 до 1 % никеля, до 0,21 % углерода, от 0,8 до 1,1 % молибдена |
12Х11В2МФ, 10Х9МФБ, 13Х11Н2В2МФ, 15Х11МФ | Легируются ванадием (от 0,18 до 0,4 %) и молибденом (от 0,35 до 1,1 %) в дополнение к стандартным добавкам. |
Обширное распространение такого типа стали объясняется тем, что она применяется в использовании востребованных предметов. Среди них элементы турбин (роторы, корпуса, диафрагмы, лопатки), элементы насосного оборудования, пружины, хирургический режущий и измерительный инструмент.
Помимо этого, применять перечисленные разновидности стали предпочитают в том случае, если ставится задача создать элементы поверхностей, часто подвергающихся нагреву. К примеру, активно применяется сталь для создания коллекторов, котлов, трубопроводов. Применение стали нашлось и в создании компрессорного оборудования. С помощью таких вариантов создаются различного рода пластины компрессоров. Обширная область применения дополняется высокими эксплуатационными характеристиками, так что заказчик получает проверенный и востребованный материал.
Понимание ферритной, аустенитной и мартенситной нержавеющей стали
Промышленность доверяет нержавеющей стали для обеспечения прочности и коррозионной стойкости своих металлических конструкций. Однако термин «нержавеющая сталь» не передает весь спектр свойств, которыми обладает этот разнообразный металл. Чтобы лучше передать его изменение, нержавеющую сталь можно классифицировать как ферритную, аустенитную и мартенситную нержавеющую сталь.
Нержавеющая сталь обычно состоит из таких элементов, как углерод, никель, молибден, алюминий, медь, титан и не менее 10,5% хрома. Различные варианты нержавеющей стали создаются путем изменения ее химического состава и кристаллической структуры. Эти типы нержавеющей стали предлагают универсальность в свойствах, которые облегчают их использование в широком диапазоне отраслей промышленности. Однако при принятии решения о том, какой тип нержавеющей стали использовать, важно сравнить ферритную, аустенитную и мартенситную нержавеющую сталь.
Ферритная, аустенитная или мартенситная нержавеющая сталь
Выбор правильного типа нержавеющей стали может быть трудным, и это потребует тщательного изучения ваших собственных производственных потребностей, а также преимуществ и металлургических проблем, присущих каждому из них. тип нержавеющей стали. Здесь мы подробно обсудим ферритную, аустенитную и мартенситную нержавеющую сталь.
Ферритная нержавеющая сталь
Как и все типы нержавеющей стали, ферритная нержавеющая сталь названа в честь микроскопической кристаллической структуры, связанной с металлом: в данном случае это феррит. Он имеет объемно-центрированную кубическую (ОЦК) структуру зерна, которая придает ферритной нержавеющей стали ее магнитные свойства. Поскольку ферритная сталь имеет высокое содержание хрома и низкое содержание углерода, она обладает превосходной пластичностью и формуемостью. Ферритная нержавеющая сталь также обеспечивает хорошую термическую и коррозионную стойкость. По этой причине ферритная нержавеющая сталь подходит для предотвращения коррозионного растрескивания под напряжением в тех случаях, когда высокое воздействие хлоридов представляет собой серьезную проблему.
Аустенитная нержавеющая сталь
Аустенитная нержавеющая сталь является наиболее часто используемым типом нержавеющей стали благодаря ее превосходным механическим свойствам и эстетическому внешнему виду. Сталь обладает высокой коррозионной стойкостью благодаря высокому содержанию хрома. Это делает аустенитную нержавеющую сталь подходящей для тяжелых условий эксплуатации. Наличие аустенита с гранецентрированной кубической (ГЦК) структурой зерна придает аустенитной стали немагнитный характер. Однако можно индуцировать определенный уровень магнетизма и увеличить прочность аустенитной стали посредством холодной прокатки. Холодная прокатка также способствует эстетической привлекательности, обеспечивая превосходную отделку поверхности, поэтому аэрокосмическая, фармацевтическая, пищевая промышленность и многие другие отрасли используют аустенитную нержавеющую сталь для своего применения.
Мартенситная нержавеющая сталь
Мартенситная нержавеющая сталь известна своей прочностью, долговечностью и коррозионной стойкостью. При высоких температурах он имеет ГЦК-структуру аустенита, который при закалке и отпуске может образовывать мартенсит с ОЦК-структурой. Этот мартенсит представляет собой кристаллическую структуру очень твердого железа с различными свойствами в зависимости от содержания углерода. Таким образом, термическая обработка может повысить прочность этой нержавеющей стали. Однако это также затрудняет сварку и изготовление мартенситной стали. Прочность стали делает ее подходящей для компонентов клапанов или турбин, где ключевым требованием является твердость.
В таблице ниже сравниваются свойства ферритной, аустенитной и мартенситной нержавеющей стали.
Properties | Феррит | Austenitic | Martensitic | |
Хромий. | Прочность на растяжение при 20℃ | 400 – 600 МПа | 200 – 600 МПа | 700 – 2000 МПа |
Теплопроводность при 20 ℃ | 11 – 22 Вт/(M.K) | 10 – 25 Вт/(M.K) | 15 – 30 Вт/(M.K) | |
. | 1375 – 1450 ℃ | 1375 – 1450 ℃ | 1370 – 1480 ℃ | |
Modulus of elasticity | 220 GPa | 220 GPa | 200 GPa |
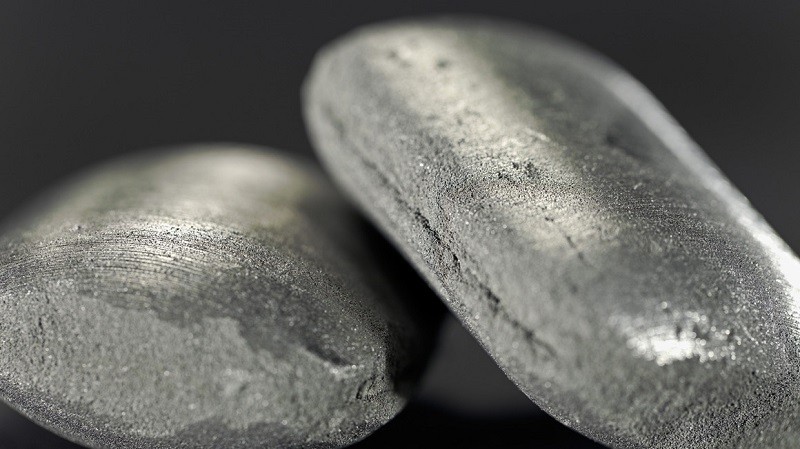
Из-за различных механических свойств и реакций термообработки сварка каждого типа нержавеющей стали требует особого внимания.
Сварка ферритной нержавеющей стали связана с рядом проблем, включая возможную потерю пластичности и ударной вязкости, а также рост зерна. Для решения этих задач сварщики должны:
- Сваривать тонкие секции, предпочтительно менее 6 мм, чтобы уменьшить общую значимость потери прочности в компоненте.
- Установите межпроходную температуру от 100 до 120 ℃, чтобы ограничить рост зерна.
- При сварке секций толщиной более 6 мм предварительно прогрейте при низких температурах, чтобы уменьшить напряжение и избежать образования трещин в соединении.
- Используйте низкоуглеродистую аустенитную сталь, а также расходные материалы на основе никеля для повышения прочности сварного шва.
Аустенитная нержавеющая сталь, с другой стороны, легче сваривается, чем другая нержавеющая сталь. Однако нельзя не учитывать возможность охрупчивания и растрескивания. Чтобы обеспечить качество сварки, следуйте этим советам по сварке.
- Убедитесь, что максимальная межпроходная температура составляет 150 ℃, а тепловложение менее 50 кДж/дюйм, чтобы избежать таких проблем, как горячее растрескивание.
- Используйте присадочный материал с низким содержанием углерода для повышения прочности сварного шва.
- В зависимости от требуемого уровня феррита расходные детали с содержанием феррита 3-5 процентов могут помочь предотвратить горячее растрескивание.
Мартенситная нержавеющая сталь обладает повышенной прокаливаемостью, что также делает ее менее пластичной. Внезапный нагрев от сварки и внезапная закалка могут привести к образованию трещин. Чтобы противостоять этому:
- Используйте процесс с низким содержанием водорода, такой как сварка в среде инертного газа (MIG) или сварка вольфрамовым электродом в среде инертного газа (TIG), чтобы свести к минимуму проблему водородного растрескивания.
- Чтобы избежать закалки в околошовной зоне, предварительно подогрейте металл, чтобы уменьшить разницу температур и улучшить контролируемое и медленное охлаждение.
- Убедитесь, что присадочный металл соответствует основному металлу.
Уникальный химический состав и металлургические свойства ферритной, аустенитной и мартенситной нержавеющей стали требуют различной обработки при сварке. Прежде чем приступить к какой-либо операции, производители должны понимать сложность металла и требования, которым он может подвергаться в своей рабочей среде. Только после понимания различных требований к ферритной, аустенитной и мартенситной нержавеющей стали отрасли могут оптимизировать свои сварочные процессы, чтобы повысить производительность и рентабельность работы.
Компания Arc Machines, Inc. является ведущим поставщиком передовых технологий сварки, которые могут обеспечить наилучшие результаты при сварке нержавеющей стали. Чтобы узнать больше о нашей продукции и обсудить любые вопросы, касающиеся ферритной, аустенитной или мартенситной нержавеющей стали, обращайтесь по телефону [email protected] . Чтобы разработать индивидуальное решение, свяжитесь с нами , чтобы договориться о встрече.
Что такое нержавеющая сталь – аустенитная, ферритная, мартенситная, дуплексная и осажденная нержавеющая сталь
Интересные факты Менеджер по маркетингу · 24 октября 2019 г. · комментарии выключены
В настоящее время сталелитейная промышленность оказывает большое влияние на коммерческий рынок. Отклонение в отрасли оказывает огромное влияние на различные сегменты рынка. Все категории стали имеют различные характеристики с точки зрения различных химических и механических свойств. Из нескольких категорий нержавеющая сталь является одной из премиальных групп, которая на данный момент имеет самые высокие темпы роста на рынке. Основной причиной более широкого использования нержавеющей стали является ее коррозионная стойкость, долговечность и возможность вторичной переработки. Он чрезвычайно универсален по своей природе из-за его исключительных механических свойств, таких как высокая формуемость, структурная прочность и ударопрочность. Он имеет минимальное содержание хрома 10,5%. Это семейство имеет несколько подкатегорий: аустенитные, ферритные, мартенситные, дуплексные и дисперсионно-твердеющие. Эти подкатегории обладают различными химическими и механическими свойствами, что дает производителям наилучший выбор для выбора конкретного материала в соответствии с требованиями их применения. Механические свойства являются мерой реакции материала на внутреннюю и внешнюю приложенную силу и играют огромную роль при выборе материала. Важными свойствами, которые необходимо учитывать при выборе материала, являются предел текучести, предел прочности при растяжении, относительное удлинение, уменьшение площади, твердость и ударная вязкость.
92.
Удлинение и сокращение площади – это свойства, которые также играют важную роль при выборе материала. Они также оцениваются с помощью испытаний на растяжение и предел текучести. Оба коэффициента определены в процентных формах. Удлинение – это отношение конечной длины к исходной длине образца. Конечная длина представляет собой разницу между длиной, полученной после разрушения, и исходной длиной образца. Уменьшение площади представляет собой отношение конечной площади поперечного сечения к исходной площади поперечного сечения образца. Конечная площадь поперечного сечения представляет собой разницу между первоначальной площадью поперечного сечения и наименьшей площадью поперечного сечения образца после разрушения.
Твердость – это мера сопротивления материала деформации или вдавливанию. Проверка относится к неразрушающему методу контроля. Обычно его определяют методами испытаний по Бринеллю и Роквеллу. Измеряется в BHN, HRB и HRC.
Прочность – это способность образца поглощать энергию до разрушения. Его определяют двумя методами: Шарпи и Изода. Наиболее распространенным методом, используемым в промышленности, является тест Шарпи с V-образным надрезом. Измеряется в джоулях. Скорость поглощения энергии высока для прочных материалов и очень мала для хрупких материалов.
Аустенитная нержавеющая сталь семейства имеет самое широкое применение на коммерческом рынке. В целом в нем присутствует не менее 16% содержания хрома. Он также содержит большое количество никеля, который улучшает различные свойства, такие как технологичность и коррозионная стойкость. Они немагнитны по своей природе. Они обладают гораздо лучшими свойствами, такими как предел текучести и прочность на растяжение, чем углеродистая сталь. Предел текучести аустенитной нержавеющей стали составляет 35-50% от предела прочности при растяжении, но в мягкой стали предел текучести имеет более высокую долю предела прочности при растяжении, то есть 65-70%. Прочность на растяжение и предел текучести также можно увеличить в большей степени при выполнении операций холодной обработки давлением. Эти материалы обладают способностью упрочняться до очень высокого уровня прочности по сравнению с обычными материалами. У них более высокие значения удлинения, что означает, что они обладают отличной формуемостью. Они обладают чрезвычайно хорошей ударной вязкостью и ударной вязкостью при комнатной температуре, но снижаются при отрицательных температурах. Кроме того, значение ударной вязкости материала будет уменьшаться при выполнении холодной обработки.
Ферритные нержавеющие стали обычно содержат от 10,5 до 18% хрома. В нем очень мало углерода. Эти марки являются магнитными по своей природе и имеют плохую свариваемость. Они обладают умеренной коррозионной стойкостью и не подвержены коррозии под напряжением. По сравнению с аустенитным семейством холодная обработка оказывает на них очень меньшее воздействие. Значения растяжения и текучести увеличиваются в меньшей степени после наклепа. Стандартные ферритные марки обладают вязкостью при комнатной температуре, однако с понижением температуры вязкость снижается.
Мартенситные нержавеющие стали имеют почти такой же уровень содержания хрома, как и ферритные. Однако они имеют относительно высокое содержание углерода, т.е. 0,1-1%. Они также являются магнитными и термообрабатываемыми. В состоянии отжига они имеют почти те же механические свойства, что и ферритная нержавеющая сталь. Для улучшения свойств они должны пройти процесс QT (закалка и отпуск). Благодаря процессу QT улучшаются такие свойства, как ударная вязкость и удлинение материала, а также почти такой же уровень прочности и твердости.
Дуплексные нержавеющие стали — единственное семейство сталей, которые содержат как аустенитную, так и ферритную микроструктуру. Они содержат 18-28% хрома, 4,5-8% никеля и 2,5-4% молибдена. Они обладают высокой устойчивостью к коррозии и воздействию галогенидов. Вот почему они используются в теплообменниках, химических резервуарах и нефтеперерабатывающих заводах. Они имеют более высокие значения предела текучести и предела прочности, чем аустенитные и ферритные марки.