Стали ст3 механические свойства: Сталь 3 – расшифровка и характеристики
alexxlab | 14.05.2023 | 0 | Разное
Механические свойства при растяжении и условия испытания на изгиб углеродистой стали обыкновенного качества в горячекатаном состоянии
Марка стали | Временное сопротивление. Μ Па | Предел текучести, Μ Па для толщин, мм | Относительное удлинение, % для толщин, мм | Изгиб до параллельности сторон (а – толщина образца, d – диаметр оправки) для толщин, мм | ||||||
до 20 | св. 20 до 40 | св. 40 до 100 | св. 100 | до 20 | св. | св.40 | до 20 | св. 20 | ||
не менее | ||||||||||
Ст0 | Не менее 300 | – | – | – | – | 23 | 22 | 20 | d=2,5a | d=3,5a |
Ст2кп | 320-410 | 215 | 205 | 195 | 185 | 33 | 32 | 30 | ||
Ст2пс | 330-430 | 225 | 215 | 205 | 195 | 32 | 31 | 29 | d=l,5a | d=2,5a |
Ст2сп | -“- | -“- | -“- | -“- | -“- | -“- | -“- | -“- | -“- | |
Ст3кп | 360-460 | 235 | 225 | 215 | 195 | 27 | 26 | 24 | ||
Ст3пс | 370-480 | 245 | 235 | 225 | 205 | 26 | 25 | 23 | ||
Ст3сп | -“- | -“- | -“- | -“- | -“- | -“- | -“- | -“- | -“- | -“- |
Ст3Гпс | 370-490 | d=l,5a | d=2,5a | |||||||
Ст3Гсп | 390-570 | 255, | 245 | – | – | 23 | 24 | – | ||
Ст4пс | 410-530 | 265 | 255 | 245 | 235 | 24 | 23 | 21 | d=2,5a | d=3,5a |
Ст4сп | -“- | -“- | -“- | -“- | -“- | -“- | -“- |
| -“- | -“- |
Ст5пс | 490-630 | 285 | 275 | 265 | 255 | 20 | 19 | 17 | d=3,5a | d=4,5a |
Ст5сп | -“- | -“- | -“- | -“- | -“- | -“- | -“- | -“- | -“- | -“- |
Ст3Гпс | 450-590 | 285 | 275 | 265 | 255 | 20 | 19 | 17 |
Сталь поставляют по категориям 1, 2, 3, 4,
5 и 6, в зависимости от количества
гарантируемых характеристик (табл. 6).
Чем больше номер марки стали, тем выше
в ней содержание углерода. Например,
Ст1сп со-. держит 0,06–0,12%С, а Ст6сп –
0,38-0,49%С.
Для строительных конструкций наиболее
широко применяется горячекатаная сталь
по 5-й категории, например, сталь марки
Ст3сп5. Она имеет следующий химический
состав: 0,14–0,22% С; 0,40–0.65% Мп; 0,12–0,30% Si,
менее 0,04% Ρ и менее 0,05% S. Ее механические
свойства в зависимости от толщины
составляют: σH = 370–480 Μ Па, σт ≥ 205 Μ Па, δ5 ≥ 23%, KCU+20 ≥ 34
Дж/см
Ст3сп6, применяемая по 6-й категории в
термически упрочненном состоянии, имея
такой же химический состав как Ст3сп5,
имеет более высокие величины гарантируемых
характеристик прочности и ударной
вязкости: σв = 430 Μ Па, σт ≥
295 Μ Па, δ5 ≥ 16%, KCU-40 ≥ 39 Дж/см2,
KCV0 ≥ 30–34 Дж/см2, KCU после
механического старения ≥ 29 Дж/см2,
испытание на изгиб до параллельности
сторон при d == 5а (а = 21–40 мм).
Для изготовления резервуаров, газгольдеров и других строительных конструкций малых размеров наибольшее применение имеет сталь марки Ст3сп5; для газонефтепроводов малых диаметров (менее 500 мм), изготовляемых из сварных прямошовных и спирально-шовных труб, применяют обычно сталь марок Ст2сп5, Ст3сп5 и Ст4сп5.
Сталь углеродистую обыкновенного качества применяют также для деталей строительно-монтажных машин. Например, Ст0 Ст1 применяют для изготовления неответственных деталей: опоры, шайбы, прокладки, рамы и т. д.: Ст2 – для изготовления заклепок, анкерных болтов и т. д.
Сталь марки Ст3-применяют для изготовления шкивов, муфт, заглушек, корпусов редукторов и т. д., а также болтов.
Из Ст4 изготовляют крюки, тяги, клинья
и т. д., а также крепежные детали, детали
насосов, компрессоров; из Ст5 – пальцы,
втулки, плашки зажимов, а также болты;
из Ст6 – промежуточные валы, стропы,
ролики передвижных агрегатов, втулки,
шкивы и т. д.
В зависимости от предъявляемых требований
к деталям машин производят их упрочнение.
Ст1, Ст2, Ст3 обычно подвергают
химико-термической обработке (цементации,
цианированию и т. д.) с последующей
закалкой и низким отпуском при 160–180°С,
что позволяет получать высокую прочность,
твердость, износоустойчивость на
поверхностях стальных деталей в сочетании
с пластичной сердцевиной. Ст3, Ст4, Ст5 –
подвергают нормализации или закалке с
высоким отпуском при 550–650°С для улучшения
механических свойств. Закалка с высоким
отпуском позволяет получать наиболее
благоприятное сочетание прочности,
пластичности и вязкости, поэтому такое
упрочнение рекомендуется для деталей
машин, работающих также и в северных
условиях. После термического улучшения,
например, для стали Ст3, гарантируется
KCU
Таблица 6
Электроды для нузкоуглеродистой стали ( постоянный ток)
Электроды для сварки низкоуглеродистых сталей AV-61 2.
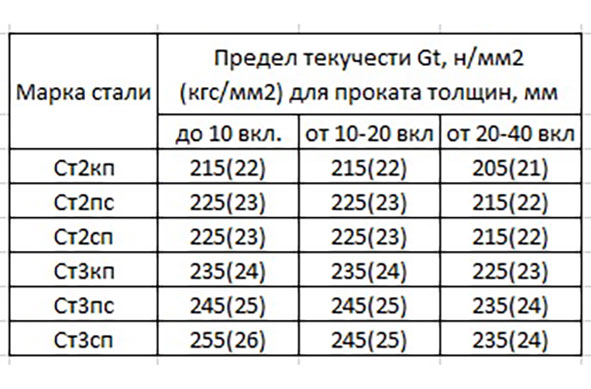
Классификация: |
|
||||||||||||||||||||||||||||
Описание: |
Электроды предназначены для сварки отвественных конструкций из углеродистых и низколегированных сталей. |
||||||||||||||||||||||||||||
Одобрения: | Germanischer Lloyd, DNV, РС (Российский морской регистр судоходства), Сертификат Национальной Системы Сертификации Республики Беларусь (СтБ). Сертифiкат Вiдповiдностi УкрСЕПРО |
||||||||||||||||||||||||||||
Вид покрытия: | Основное с железным порошком. | ||||||||||||||||||||||||||||
Пространственные положения сварки: | Все, кроме “вертикальной вниз”. | ||||||||||||||||||||||||||||
Род тока и полярность: | Постоянный ток обратной полярности. | ||||||||||||||||||||||||||||
Сварочный ток: |
|
||||||||||||||||||||||||||||
Химический состав наплавленного металла (%): |
|
||||||||||||||||||||||||||||
Механические свойства металла шва: |
|
||||||||||||||||||||||||||||
Сварочно-технологические свойства: | Легкое зажигание и повторное зажигание, спокойная и стабильная дуга, легкая отделяемость шлака. ![]() |
||||||||||||||||||||||||||||
Повторное прокаливание перед употреблением: | (300-350)˚С/2 ч. | ||||||||||||||||||||||||||||
Упаковка: |
|
||||||||||||||||||||||||||||
Металлы: | Сталь 16ГС, сталь 17ГС, сталь 09Г2С, сталь 17Г1С, сталь 10Г2С1 (ГОСТ 19282), S235-S355, P235-P355, E-295 (EN 10025, EN 10027-1, EN 10028-2, EN 10028-3). |
||||||||||||||||||||||||||||
Установки: | Котлы горячей воды и паровые котлы, xранилища нефтепродуктов, напорные сосуды, cтроительные конструкции, корпусные части кораблей, cельскохозяйственное оборудование. ![]() |
Электроды для сварки низкоуглеродистых сталей AV-61 3.0 мм, вес 1 уп = 2,5 кг
Классификация: |
|
||||||||||||||||||||||||||||
Описание: |
Электроды предназначены для сварки отвественных конструкций из углеродистых и низколегированных сталей. |
||||||||||||||||||||||||||||
Одобрения: | Germanischer Lloyd, DNV, РС (Российский морской регистр судоходства), Сертификат Национальной Системы Сертификации Республики Беларусь (СтБ). Сертифiкат Вiдповiдностi УкрСЕПРО |
||||||||||||||||||||||||||||
Вид покрытия: | Основное с железным порошком. | ||||||||||||||||||||||||||||
Пространственные положения сварки: | Все, кроме “вертикальной вниз”. | ||||||||||||||||||||||||||||
Род тока и полярность: | Постоянный ток обратной полярности.![]() |
||||||||||||||||||||||||||||
Сварочный ток: |
|
||||||||||||||||||||||||||||
Химический состав наплавленного металла (%): |
|
||||||||||||||||||||||||||||
Механические свойства металла шва: |
|
||||||||||||||||||||||||||||
Сварочно-технологические свойства: | Легкое зажигание и повторное зажигание, спокойная и стабильная дуга, легкая отделяемость шлака. ![]() |
||||||||||||||||||||||||||||
Повторное прокаливание перед употреблением: | (300-350)˚С/2 ч. | ||||||||||||||||||||||||||||
Упаковка: |
|
||||||||||||||||||||||||||||
Металлы: | Сталь 16ГС, сталь 17ГС, сталь 09Г2С, сталь 17Г1С, сталь 10Г2С1 (ГОСТ 19282), S235-S355, P235-P355, E-295 (EN 10025, EN 10027-1, EN 10028-2, EN 10028-3). |
||||||||||||||||||||||||||||
Установки: | Котлы горячей воды и паровые котлы, xранилища нефтепродуктов, напорные сосуды, cтроительные конструкции, корпусные части кораблей, cельскохозяйственное оборудование. ![]() |
Электроды для сварки низкоуглеродистых сталей AV-61 4.0 мм, вес 1 уп = 5 кг
Классификация: |
|
||||||||||||||||||||||||||||
Описание: |
Электроды предназначены для сварки отвественных конструкций из углеродистых и низколегированных сталей. |
||||||||||||||||||||||||||||
Одобрения: | Germanischer Lloyd, DNV, РС (Российский морской регистр судоходства), Сертификат Национальной Системы Сертификации Республики Беларусь (СтБ). Сертифiкат Вiдповiдностi УкрСЕПРО |
||||||||||||||||||||||||||||
Вид покрытия: | Основное с железным порошком. | ||||||||||||||||||||||||||||
Пространственные положения сварки: | Все, кроме “вертикальной вниз”. | ||||||||||||||||||||||||||||
Род тока и полярность: | Постоянный ток обратной полярности.![]() |
||||||||||||||||||||||||||||
Сварочный ток: |
|
||||||||||||||||||||||||||||
Химический состав наплавленного металла (%): |
|
||||||||||||||||||||||||||||
Механические свойства металла шва: |
|
||||||||||||||||||||||||||||
Сварочно-технологические свойства: | Легкое зажигание и повторное зажигание, спокойная и стабильная дуга, легкая отделяемость шлака. ![]() |
||||||||||||||||||||||||||||
Повторное прокаливание перед употреблением: | (300-350)˚С/2 ч. | ||||||||||||||||||||||||||||
Упаковка: |
|
||||||||||||||||||||||||||||
Металлы: | Сталь 16ГС, сталь 17ГС, сталь 09Г2С, сталь 17Г1С, сталь 10Г2С1 (ГОСТ 19282), S235-S355, P235-P355, E-295 (EN 10025, EN 10027-1, EN 10028-2, EN 10028-3). |
||||||||||||||||||||||||||||
Установки: | Котлы горячей воды и паровые котлы, xранилища нефтепродуктов, напорные сосуды, cтроительные конструкции, корпусные части кораблей, cельскохозяйственное оборудование. ![]() |
Электроды для сварки низкоуглеродистых сталей UONI-13/55, 3,0 мм, вес 1 уп = 3 кг
Классификация: |
|
||||||||||||||||||||||||
Описание: |
Электроды предназначены для сварки особо ответственных конструкций из низкоуглеродистых и низколегированных сталей, когда к металлу швов предьявляют повышенные требования по пластичности и ударной вязкости, в часности, при работе в условиях пониженных температур. |
||||||||||||||||||||||||
Одобрения: | TÜV, Сертифiкат Вiдповiдностi УкрСЕПРО, Российский морской регистр судоходства (PC), Сертификат Национальной Системы Сертификации Республики Беларусь (СтБ). | ||||||||||||||||||||||||
Вид покрытия: | Основное. | ||||||||||||||||||||||||
Пространственные положения сварки: | Все, кроме “вертикальной вниз”.![]() |
||||||||||||||||||||||||
Род тока и полярность: | Постоянный ток обратной полярности. | ||||||||||||||||||||||||
Сварочный ток: |
|
||||||||||||||||||||||||
Химический состав наплавленного металла (%): |
|
||||||||||||||||||||||||
Механические свойства металла шва: |
|
||||||||||||||||||||||||
Сварочно-технологические свойства: | Легкое зажигание и повторное зажигание, спокойная и стабильная дуга, малое разбрызгивание, хорошая отделяемость шлака, переход без нарезки. ![]() |
||||||||||||||||||||||||
Повторное прокаливание перед употреблением: | (250-300)˚С/1 ч. | ||||||||||||||||||||||||
Упаковка: |
|
||||||||||||||||||||||||
Металлы: | Сталь 10, сталь 15 (ГОСТ 1050), сталь 15К, сталь 16К, сталь 18К, сталь 20К, сталь 22К (ГОСТ 5520), сталь 15Л, сталь 20Л, сталь 25Л (ГОСТ 977), Ст3 (ГОСТ 380), сталь 16ГС, сталь 17ГС, сталь 09Г2С, сталь 17Г1С, сталь 10Г2С1 (ГОСТ 19282), A, B, D, E, A 32/36, D 32/36, E 32/36 и F 32/36, S235-S355, P235-P355, E-295 (EN 10025, EN 10027-1, EN 10028-2, EN 10028-3). ![]() |
||||||||||||||||||||||||
Установки: | Котлы горячей воды и паровые котлы. Напорные сосуды. Строительные конструкции. Корпусные части кораблей. Cельскохозяйственное оборудование. |
Электроды для сварки низкоуглеродистых сталей UONI-13/55, 4,0 мм, вес 1 уп = 5 кг
Классификация: |
|
||||||||||||||||||||||||
Описание: |
Электроды предназначены для сварки особо ответственных конструкций из низкоуглеродистых и низколегированных сталей, когда к металлу швов предьявляют повышенные требования по пластичности и ударной вязкости, в часности, при работе в условиях пониженных температур. |
||||||||||||||||||||||||
Одобрения: | TÜV, Сертифiкат Вiдповiдностi УкрСЕПРО, Российский морской регистр судоходства (PC), Сертификат Национальной Системы Сертификации Республики Беларусь (СтБ).![]() |
||||||||||||||||||||||||
Вид покрытия: | Основное. | ||||||||||||||||||||||||
Пространственные положения сварки: | Все, кроме “вертикальной вниз”. | ||||||||||||||||||||||||
Род тока и полярность: | Постоянный ток обратной полярности. | ||||||||||||||||||||||||
Сварочный ток: |
|
||||||||||||||||||||||||
Химический состав наплавленного металла (%): |
|
||||||||||||||||||||||||
Механические свойства металла шва: |
|
||||||||||||||||||||||||
Сварочно-технологические свойства: | Легкое зажигание и повторное зажигание, спокойная и стабильная дуга, малое разбрызгивание, хорошая отделяемость шлака, переход без нарезки. ![]() |
||||||||||||||||||||||||
Повторное прокаливание перед употреблением: | (250-300)˚С/1 ч. | ||||||||||||||||||||||||
Упаковка: |
|
||||||||||||||||||||||||
Металлы: | Сталь 10, сталь 15 (ГОСТ 1050), сталь 15К, сталь 16К, сталь 18К, сталь 20К, сталь 22К (ГОСТ 5520), сталь 15Л, сталь 20Л, сталь 25Л (ГОСТ 977), Ст3 (ГОСТ 380), сталь 16ГС, сталь 17ГС, сталь 09Г2С, сталь 17Г1С, сталь 10Г2С1 (ГОСТ 19282), A, B, D, E, A 32/36, D 32/36, E 32/36 и F 32/36, S235-S355, P235-P355, E-295 (EN 10025, EN 10027-1, EN 10028-2, EN 10028-3). ![]() |
||||||||||||||||||||||||
Установки: | Котлы горячей воды и паровые котлы. Напорные сосуды. Строительные конструкции. Корпусные части кораблей. Cельскохозяйственное оборудование. |
Механические свойства углеродистой стали в зависимости от скорости набора дозы ионов азота и аргона
Механические свойства углеродистой стали в зависимости от скорости набора дозы ионов азота и аргона
- Воробьев В.Л. ;
- Быков П.В. ;
- Баянкин, В.Я. ;
- Шушков А.А. ;
- Вахрушев А.В.
Аннотация
В зависимости от скорость набора дозы при средней плотности ионного тока 10, 20 и 40 мкА/см 2 . Установлено, что усталостная долговечность и микротвердость поверхностных слоев увеличиваются во всем исследованном диапазоне скоростей нарастания дозы. По-видимому, это связано с упрочнением поверхностных слоев в результате генерации радиационных дефектов и радиационно-динамического воздействия быстрых ионов. Образец, облученный ионами аргона при наименьшей из выбранных скоростей набора дозы j av = 10 мкА/см 2 , выдерживает наибольшее число циклов до разрушения.
- Публикация:
Физика металлов и металловедение
- Дата публикации:
- август 2014 г.
- DOI:
- 10.1134/S0031918X14080158
- Биб-код:
- 2014ПММ.
..115..800В
- Ключевые слова:
- ионная имплантация; микротвердость
- ;
- шероховатость поверхности;
- химический состав поверхности;
- усталостная долговечность
Магнитные методы и приборы контроля процесса разрушения ферромагнитных сталей металлоконструкций Оценка остаточного ресурса машин и сосудов, работающих под давлением
Магнитные методы и приборы для контроля процесса разрушения ферромагнитных сталей металлоконструкций Оценка остаточного ресурса машин и сосудов, работающих под давлением·Оглавление ·Материалы Характеристика и испытания | Магнитные методы и Приборы для контроля процесса разрушения ферромагнитных сталей для оценки остаточного ресурса металлоконструкций машин и сосудов, работающих под давлениемМужицкий В.![]() МСИА “Спектр”, г. Москва Попов Б.Е. ОСК “Кран”, Россия Безлюдко Г.Ю. “СНР”, Украина Контакт |
- Предложено использовать магнитный метод для оценки долговечности несущей конструкции из стали. Здесь рекомендуется специальное оборудование для этого метода. Здесь объясняется механизм возникновения и накопления дефектов в связи с поведением реакции коэрцитивной силы H С . Результаты представлены на примере испытаний и исследований кислородного баллона.
Очень важной задачей является оценка возможного ресурса несущих металлоконструкций, особенно в странах, имеющих более 50% устройств повышенной опасности (краны, грузоподъемные машины, резервуары, котлы и т.д.), которые уже отработали свой срок эксплуатации. жизни, как способ увеличения срока их эксплуатации. Значительная часть задачи оценки состояния конструкций теперь может быть решена с помощью магнитного метода измерения коэрцитивной силы и внедрения системы регистрации нагрузки «СИРЕНА».
Нормы в основу магнитного метода контроля конструкций из ферромагнитных сталей заложены в Межгосударственном стандарте ГОСТ 30415-96, Международном стандарте ИСО 4301 и Методических указаниях “Госгортехнадзора” России РД ИКЦ “Кран” – 007-97. Оборудованием, обеспечивающим этот метод, является специальный магнитный структуроскоп КРМ-СК, разработанный фирмой «СНР» (Харьков) и МНИА «Спектр» (Москва).
Переносной магнитный структуроскоп (измеритель коэрцитивной силы) КРМ-СК-2 с автономным питанием 12В снабжен дополнительным преобразователем с замкнутой магнитной системой, датчиком на эффекте Холла, системой снижения чувствительности к изменению отрыва и обеспечивает регистрацию H С путем анализа полного контура магнитного гистерезиса от 1 до 3000 А/м с погрешностью – не более 5 % при температуре от -20 0 С до +50 0 С
Глубина намагничивания до 40мм. Для испытания труб и резервуаров принято использовать полюсные наконечники, соответствующие их профилям. При необходимости отбраковки металлов по механическим свойствам и состоянию их структуры прибор имеет цифровую, световую и звуковую сигнализацию на низкий и высокий уровень магнитуд Н С . Прибор КРМ-СК-2М имеет возможность подключения к ПК.
В основе метода магнитного диагностирования лежит корреляция между механическими свойствами ферромагнитных материалов и величиной коэрцитивной силы H C , измеряемой при статических и усталостных испытаниях на всех стадиях нагружения вплоть до разрушения. На основе энергетического подхода к анализу намагниченности металла, теоретических исследований упругопластической деформации, увеличения количества дефектов и увеличения величины коэрцитивной силы H C позволяют воспроизвести процесс нагружения металлических образцов в условиях эксплуатации в условиях сложнонапряженного состояния. В сочетании с испытанными образцами метод подобия позволяет определить основные параметры для оценки состояния металлоконструкций по измеренным величинам коэрцитивной силы, соответствующие: пределу текучести – Н С Т , пределу прочности – Н С В , на предел выносливости – Н С N , – с учетом анизотропии механических свойств сталей и сплавов.
На рис.1 представлены зависимости между коэрцитивной силой H C (А/см) и действующими напряжениями s (кг/мм 2 ) при статических испытаниях плоских образцов из сталей Ст3, Ст20, 09Г2С. Так как образцы толщиной 5…10 мм постоянно деформируются в зоне упругости кривой нагружения, то коэрцитивная сила H C пропорционально возрастает в зависимости от приложенного напряжения вплоть до предела текучести – s T . В зоне кривой нагружения, в которой снижается прочность металла, начинается необратимая перестройка доменной структуры металла из-за поворота границ доменов на 90 0 и 180 0 еще. Таким образом, на кривой зависимости H C (s
), а его название — «зуб текучести». В зоне кривой нагружения, в которой нагрузка возрастает при безвозвратных деформациях, коэрцитивная сила H C возрастает одновременно с появлением новой доменной структуры и накоплением активных дефектов в металле. На стадии до разрушения металла увеличение прочности стимулирует окончательную перестройку доменной структуры, увеличивая коэрцитивную силу H C до максимальной в соответствии с сортом стали и сопровождается появлением хрупких микротрещин в местах границ и стыков доменных зерен. После появления и раскрытия магистральной трещины напряжения в зоне развития трещины несколько падают, а также падает коэрцитивная сила H C . Максимум H C B соответствует пределу прочности металла s B .
При ступенчатом нагружении и, если H C измеряется после снятия нагрузки с образца, магнитный параметр реагирует только на остаточные напряжения и деформации внутри металла, в зоне упругости H C постоянна и равна начальной величине H c 0 , но после достижения предела текучести возрастает по линейной зависимости. При этом энергия, затрачиваемая на разрушение металла, и максимумы H C B в этих двух случаях примерно равны (одинаковы).
Рис. 1. Данные магнитного контроля плоских образцов из стали Ст3,Ст20,09Г2С в опыте на деформацию с регистрацией данных измерителя коэрцитивной силы непосредственно под нагрузкой и после снятия нагрузки на каждом этапе нагружения. ![]() |
Рис. 2. Магнитные испытания листов стали ВСТ3сп5 на стойкость к разрушению при малоцикловой усталости. |
Энергетический подход, безусловно, может быть использован для анализа усталостного разрушения металла. На рис.2 представлены результаты циклического нагружения плоских образцов из стали ВСтЗсп5. Испытания проводились в цикле «с нуля» с амплитудой, обеспечивающей легкий, нормальный и жесткий режимы работы металлоконструкций подъемных машин в соответствии со стандартом ISO 4301. Это означает, что металл испытывался статической деформацией в начале зоны упругости. кривой нагрузки (сс 0,2 ) – легкий режим, затем в зоне упругопластических деформаций при напряжениях s £ s 0,2 – нормальный режим, а затем при s > s 0,2 – жесткий режим нагружения.
Для оценки общего состояния металлоконструкций лифтового оборудования при его испытаниях и техническом диагностировании достаточно провести анализ распределения величины H C (А/м).

Общий подход к диагностированию напряженно-деформированного состояния и ресурса объектов повышенной опасности магнитным методом в реальных условиях можно рассмотреть на примере кислородного баллона.
Внутренние напряжения в стенках кислородных баллонов можно легко рассчитать, если известны внутреннее давление и толщина стенок. Таким образом, эксперимент по нагружению резервуара давлением воды внутри до разрушения позволяет напрямую связать уровень максимальных действующих напряжений s MAX с величинами коэрцитивной силы H C и определить зависимость, как это представлено на рис.
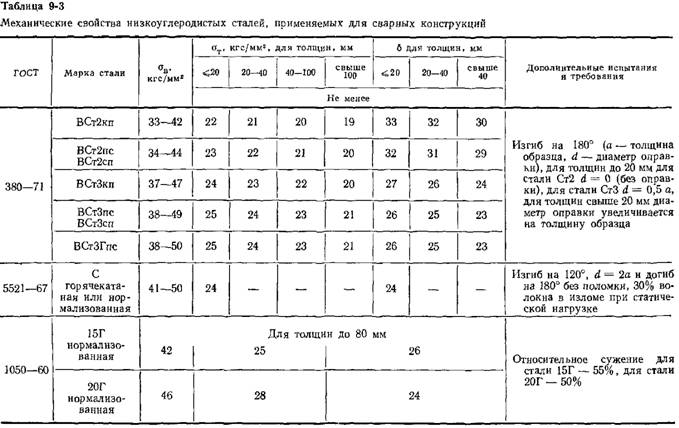
Рис. 3: Магнитный контроль напряженного состояния кислородных сосудов давлением P vn до уничтожения. |
Эта зависимость в основном соответствует классической диаграмме s(e) для деформации стальных образцов. На этой кривой можно выделить зону упругости (I), зону упругопластических деформаций (II), стадию закрепления с последующим разрушением (III). Наклоны на этой кривой могут быть идентифицированы значениями s Т и с B для того металла, из которого изготовлен кислородный баллон, с использованием расчетного значения максимума напряжения s МАКС (P ВН ) внутренней поверхности стенки резервуара. Погрешность определения механических свойств менее 10%.
Рис.![]() |
Таким образом, для каждой стали легко найти H C 0 , H C T , H C B из экспериментальных диаграмм нагружения лабораторных образцов и образцов кислородного баллона, соответствующих различным этапам нагружения металла стенки бака. На практике при решении противоположной задачи можно определить не только максимальные напряжения внутри металла стенки резервуара, используя максимальную и среднюю величины коэрцитивной силы, но и момент перехода металла в зону текучести, что позволит избегать эксплуатации кислородного баллона на этапе, близком к разрушению. К таким же результатам приводит анализ коэрцитивной силы H C , возрастающие по мере циклической загрузки резервуара, так как критические данные H C T и H C B постоянны для каждой стали.
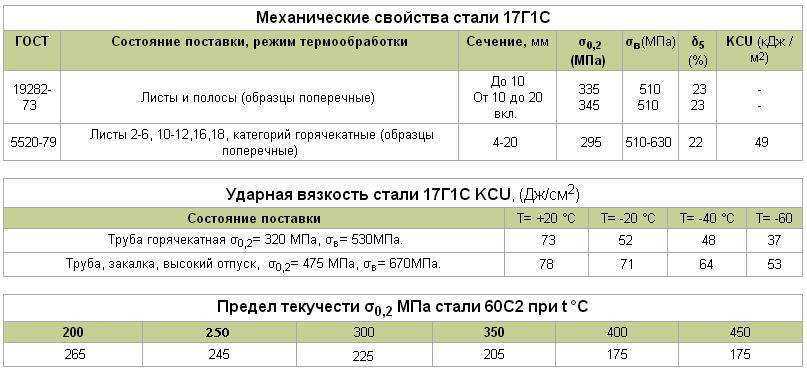
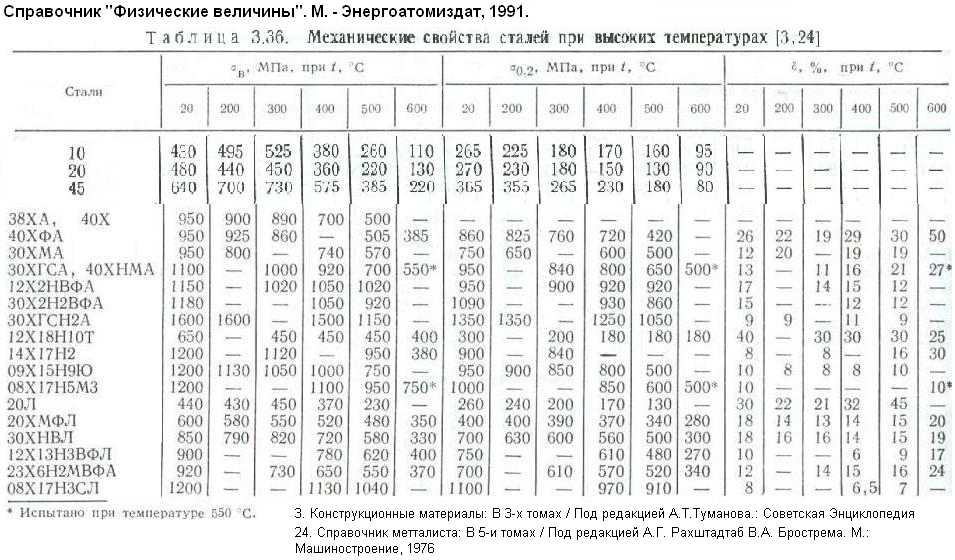
Статистический анализ распределения Н С в стенках 800 кислородных баллонов, работающих более 30 лет, позволяет определить критерии браковки баллонов и выявить более 2,5% баллонов, работающих в критическом режиме эксплуатации, которые были необходимы для вывода их из эксплуатации, рис.5.
Рис. 5: Схема распределения дефектов и коэрцитивной силы на поверхности стены. |
- В.Ф. Мужицкий, Б.Е.Попов, Г.Ю.Безлюдько, В.В. Зарудный, Е.А. Левин, Дефектоскопия, 1996, N 3, с.12-19.
- Л.А.Крутикова, В.Ф.Мужицкий, Б.Е.Попов, Г.Ю.Безлюдко. Сборник тезисов 7-й Европейской конференции по неразрушающему контролю. Копенгаген, май 1998 г., стр. 351.
- ГОСТ 30415-96. Межгосударственный стандарт (Россия, Украина, Казахстан, Белоруссия) «Сталь.